
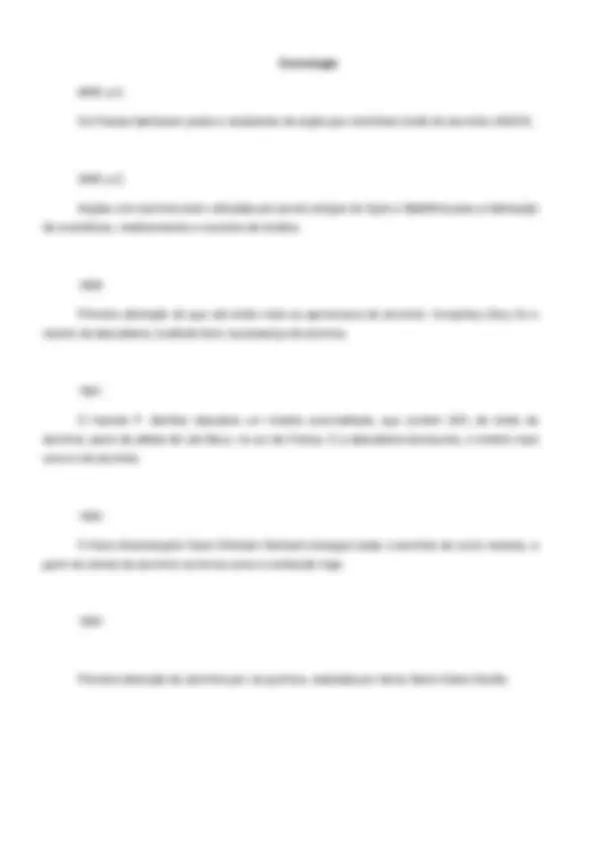
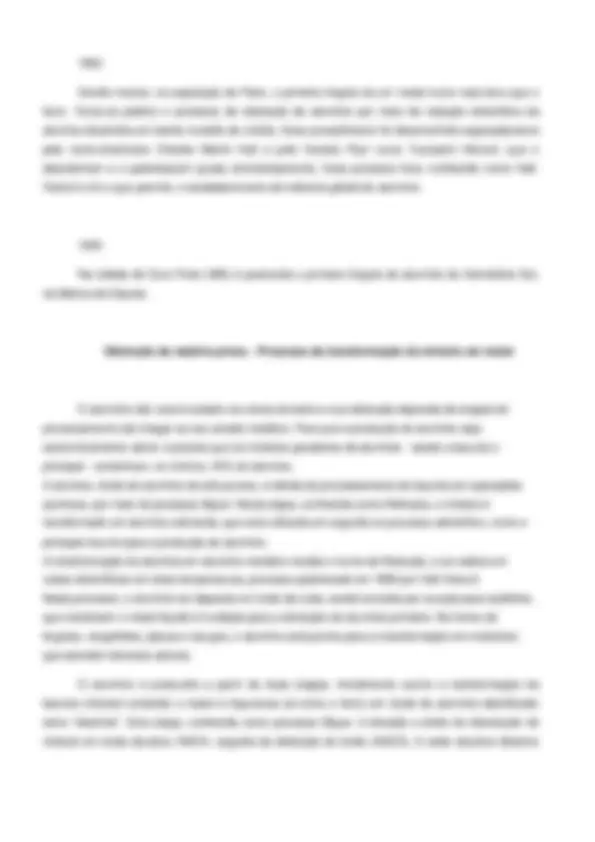
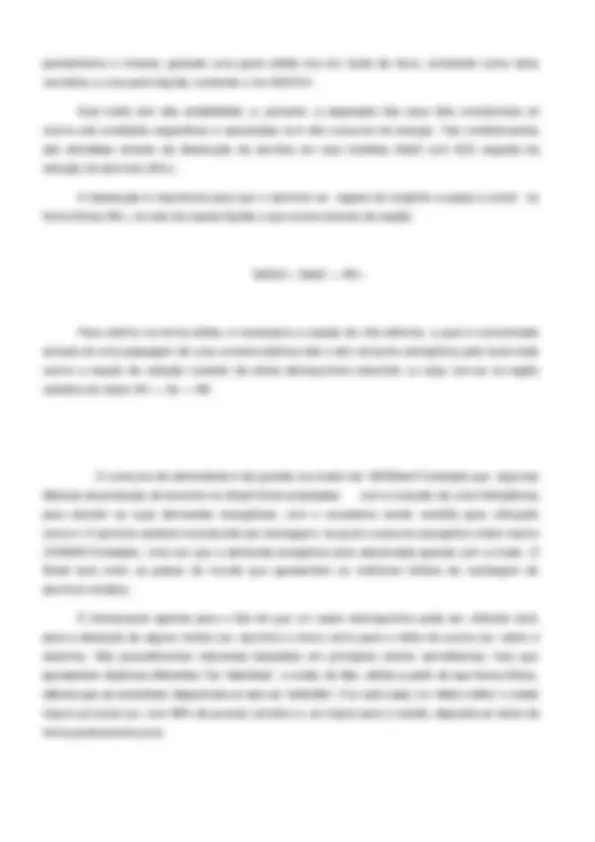
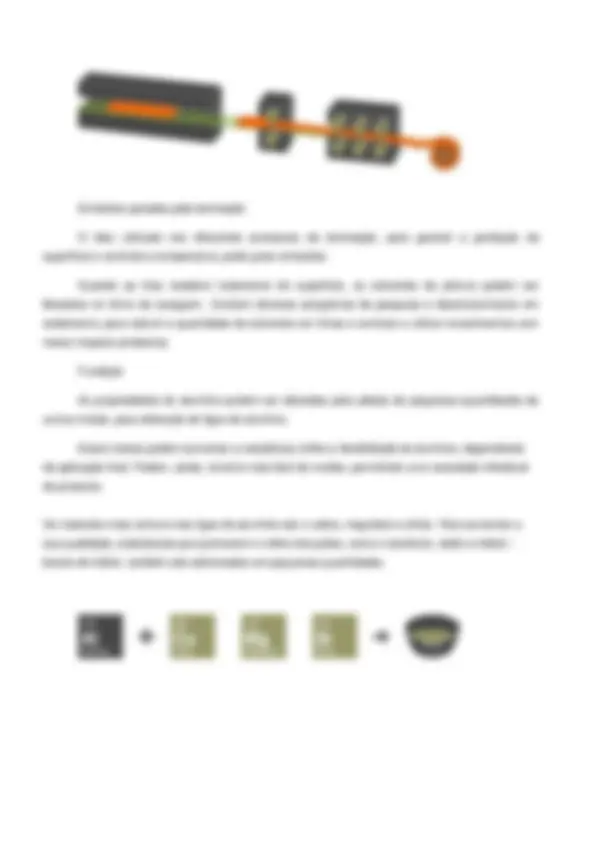
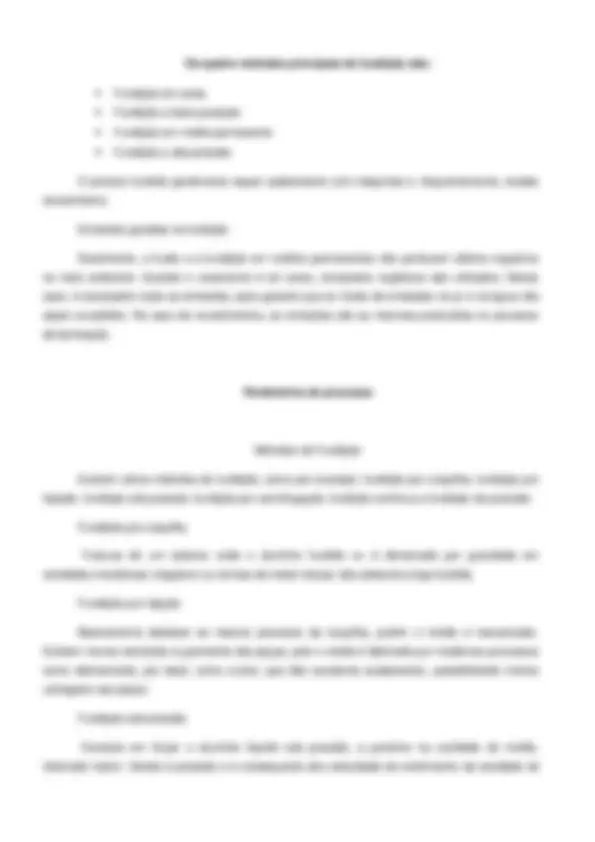
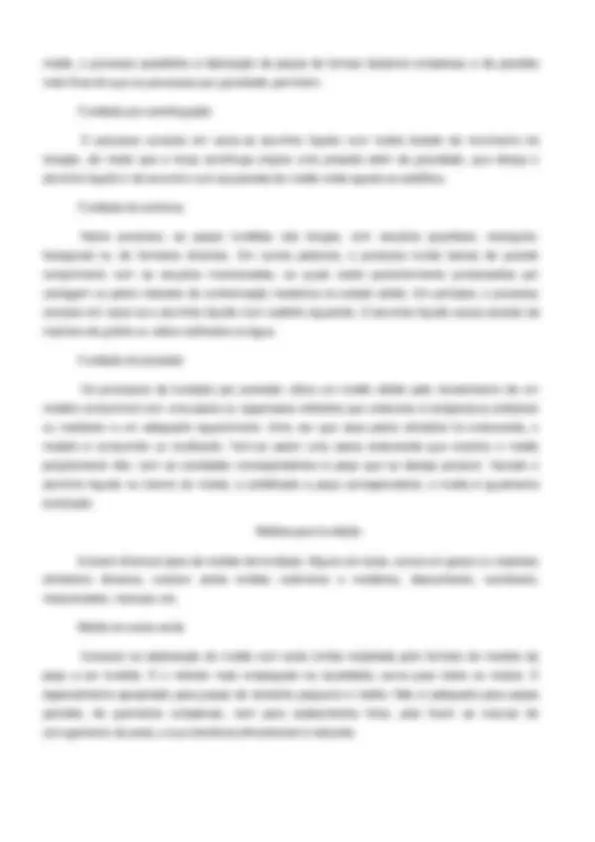
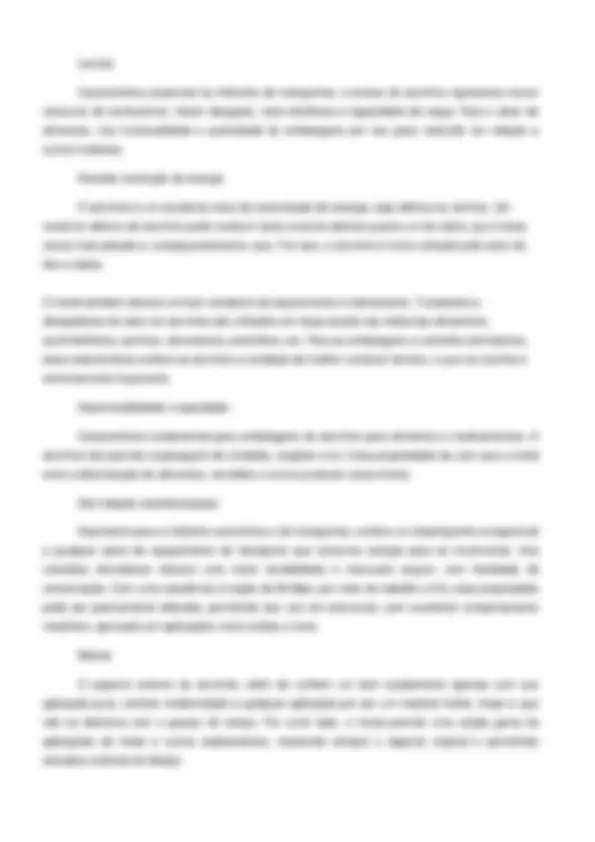
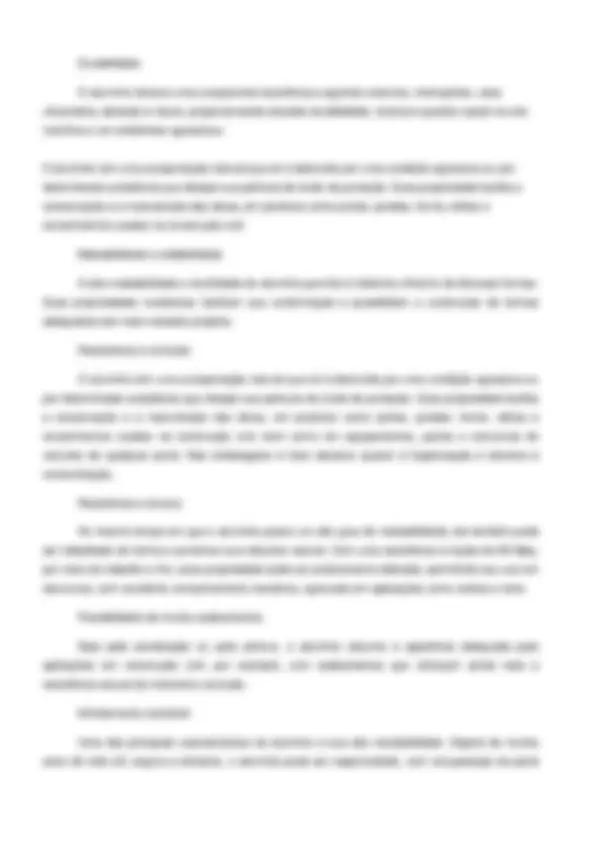
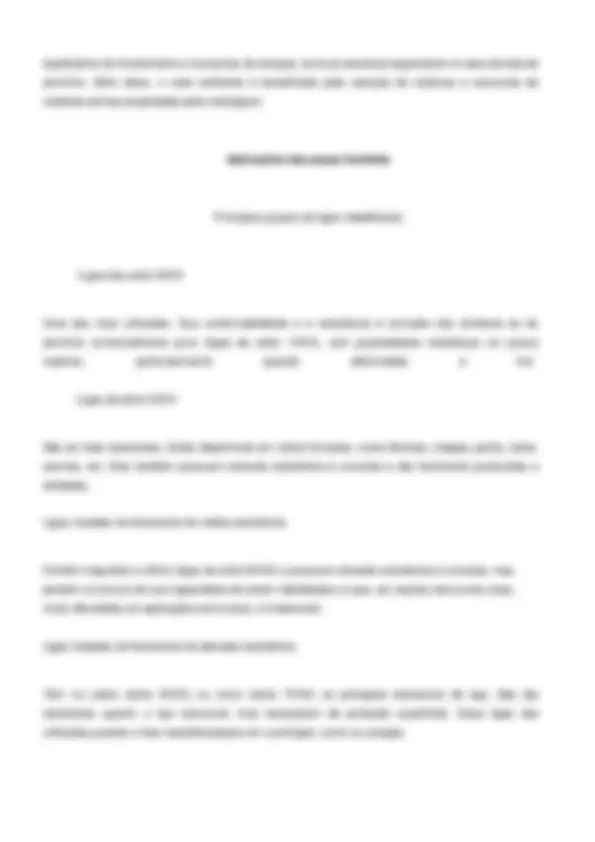
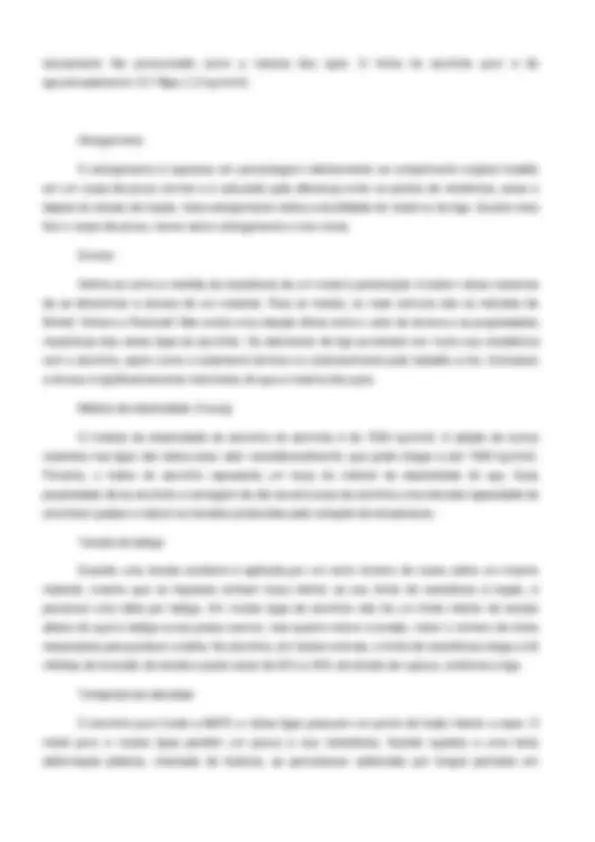
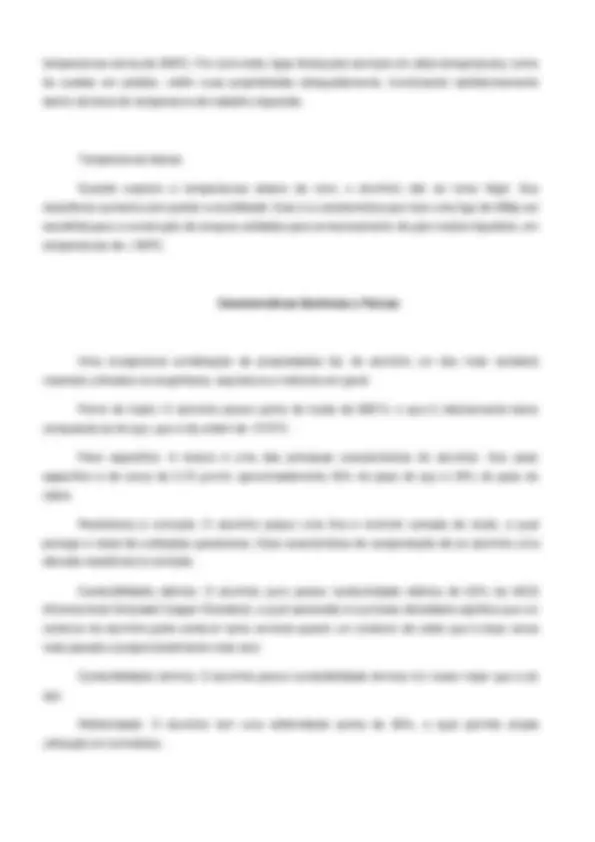
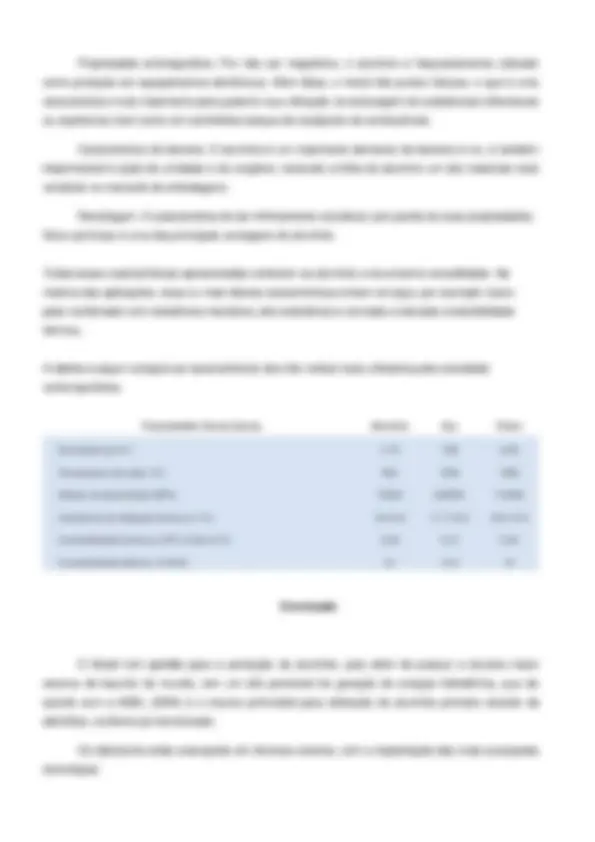
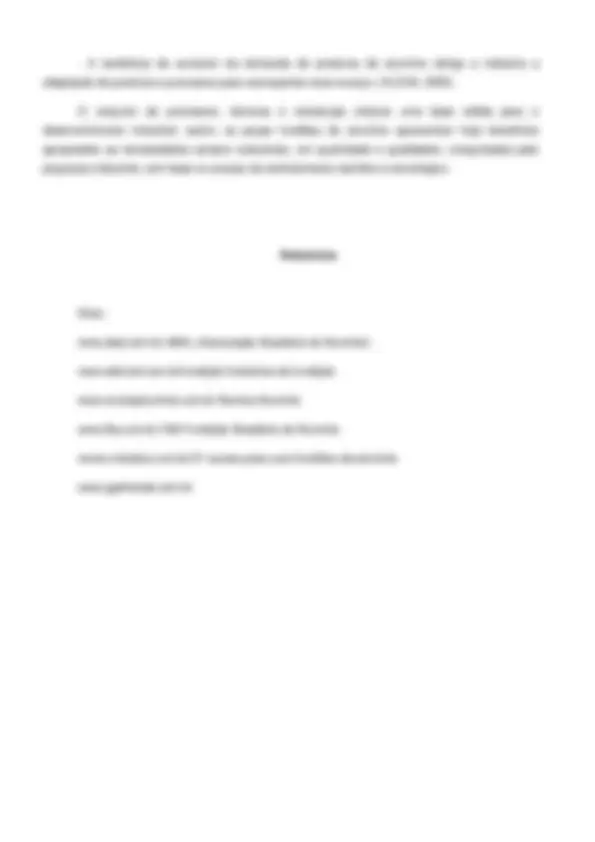
Estude fácil! Tem muito documento disponível na Docsity
Ganhe pontos ajudando outros esrudantes ou compre um plano Premium
Prepare-se para as provas
Estude fácil! Tem muito documento disponível na Docsity
Prepare-se para as provas com trabalhos de outros alunos como você, aqui na Docsity
Os melhores documentos à venda: Trabalhos de alunos formados
Prepare-se com as videoaulas e exercícios resolvidos criados a partir da grade da sua Universidade
Responda perguntas de provas passadas e avalie sua preparação.
Ganhe pontos para baixar
Ganhe pontos ajudando outros esrudantes ou compre um plano Premium
Comunidade
Peça ajuda à comunidade e tire suas dúvidas relacionadas ao estudo
Descubra as melhores universidades em seu país de acordo com os usuários da Docsity
Guias grátis
Baixe gratuitamente nossos guias de estudo, métodos para diminuir a ansiedade, dicas de TCC preparadas pelos professores da Docsity
Saiba sobre a história do alumínio, desde sua primeira aparição até a produção industrial atual. Descubra os processos de obtenção, as aplicações principais e as principais características desse material leve e versátil.
O que você vai aprender
Tipologia: Trabalhos
1 / 21
Esta página não é visível na pré-visualização
Não perca as partes importantes!
Instituto Federal de Educação, Ciência e Tecnologia Sul-rio-grandense
Campus Sapucaia do Sul Curso de Bacharelado em Engenharia Mecânica
Sapucaia do Sul, 5 de outubro de 2015
Fundição do alumínio
Introdução ao alumínio
É um dos primeiros processos industriais utilizados na produção de artigos de metal. A fundição em alumínio pode ser feita por gravidade, com uso de areia ou molde metálico, e sob pressão, (alta ou baixa). Além desses há também processos especiais, com cera perdida e tixofundição.
As peças fundidas de alumínio têm suas principais aplicações na área automotiva e de transportes. Como exemplo, podem-se citar blocos de motor, cabeçotes, caixas de câmbio, carcaças e rodas para automóveis e veículos pesados, entre outros.
As peças de alumínio podem ser produzidas a partir dos seguintes processos:
Fundição em areia; Fundição em Coquilha; Fundição sob pressão; Tixofundição.
História do alumínio
O alumínio, apesar de ser o terceiro elemento mais abundante na crosta terrestre, é o metal mais jovem usado em escala industrial. Há sete milênios, ceramistas da Pérsia já produziam seus vasos com um tipo de barro que continha óxido de alumínio, que hoje conhecemos como alumina. Trinta séculos mais tarde, egípcios e babilônios usaram outra substância contendo alumínio na fabricação de cosméticos e produtos medicinais.
Sua cronologia mostra que, mesmo nas civilizações mais antigas, o metal dava um tom de modernidade e sofisticação aos mais diferentes artefatos. Não obstante, durante seus primeiros usos, nada se sabia sobre o metal na forma como o conhecemos hoje, já que o alumínio só começou a ser produzido comercialmente há cerca de 150 anos.
Deville mostra, na exposição de Paris, o primeiro lingote de um metal muito mais leve que o ferro. Torna-se público o processo de obtenção de alumínio por meio da redução eletrolítica da alumina dissolvida em banho fundido de criolita. Esse procedimento foi desenvolvido separadamente pelo norte-americano Charles Martin Hall e pelo francês Paul Louis Toussaint Héroult, que o descobriram e o patentearam quase simultaneamente. Esse processo ficou conhecido como Hall- Heróult e foi o que permitiu o estabelecimento da indústria global do alumínio.
Na cidade de Ouro Preto (MG) é produzido o primeiro lingote de alumínio do Hemisfério Sul, na fábrica da Elquisa.
Obtenção da matéria prima – Processo de transformação do minério em metal
O alumínio não ocorre isolado na crosta terrestre e sua obtenção depende de etapas de processamento até chegar ao seu estado metálico. Para que a produção do alumínio seja economicamente viável, é preciso que os minérios geradores de alumínio - sendo a bauxita o principal - contenham, no mínimo, 30% de alumina. A alumina, óxido de alumínio de alta pureza, é obtida do processamento da bauxita em operações químicas, por meio do processo Bayer. Nesta etapa, conhecida como Refinaria, o minério é transformado em alumina calcinada, que será utilizada em seguida no processo eletrolítico, como o principal insumo para a produção de alumínio. A transformação da alumina em alumínio metálico recebe o nome de Redução, e se realiza em cubas eletrolíticas em altas temperaturas, processo patenteado em 1886 por Hall-Heroult. Neste processo, o alumínio se deposita no fundo da cuba, sendo extraído por sucção para cadinhos, que transferem o metal líquido à fundição para a obtenção do alumínio primário. Na forma de lingotes, vergalhões, placas e tarugos, o alumínio está pronto para a transformação em indústrias que atendem diversos setores.
O alumínio é produzido a partir de duas etapas. Inicialmente ocorre a transformação da bauxita (mineral contendo o metal e impurezas tal como o ferro) em óxido de alumínio identificado como “alumina”. Esta etapa, conhecida como processo Bayer, é elevada a efeito de dissolução do mineral em soda cáustica, NAOH, seguida da obtenção do óxido (Al2O3). A soda cáustica dissolve
parcialmente o mineral, gerando uma parte sólida rica em óxido de ferro, conhecido como lama vermelha, e uma parte líquida, contendo o íon Al(OH)4-.
Este óxido tem alta estabilidade, e, portanto, a separação dos seus dois constituintes só ocorre sob condições especificas e associadas com alto consumo de energia. Tais condicionantes são atendidas através da dissolução da alumina em sais fundidos (NaCl com KCl) seguida da redução do alumínio (Al3+).
A dissolução é importante para que o alumínio se separe do oxigênio e passe a existir na forma iônica Al3+, no seio da massa líquida o que ocorre através da reação:
2al2o3 = 3alo2- + Al3+
Para obtê-lo na forma sólida, é necessária a cessão de três elétrons, a qual é concretizada através de uma passagem de uma corrente elétrica (dai o alto consumo energético) pelo local onde ocorre a reação de redução (catodo) da célula eletroquímica industrial, ou seja, tem-se na região catódica do reator Al³+ + 3e- = Al
O consumo de eletricidade é tão grande (na ordem de 18000kwh/Tonelada) que algumas fábricas de produção de alumínio no Brasil foram projetadas com a inclusão de uma hidroelétrica para atender as suas demandas energéticas, com o excedente sendo vendido para utilização comum. O alumínio também é produzido por reciclagem, na qual o consumo energético é bem menor (700kWh/Tonelada), uma vez que a demanda energética esta relacionada apenas com a fusão. O Brasil esta entre os países do mundo que apresentam os melhores índices de reciclagem de alumínio metálico.
É interessante apontar para o fato de que um reator eletroquímico pode ser utilizado tanto para a obtenção de alguns metais (ex: alumínio e zinco) como para o refino de outros (ex: cobre e estanho). São procedimentos industriais baseados em princípios teórico semelhantes, mas que apresentam objetivos diferentes. Na “eletrólise”, o metal, de fato, obtido a partir de sua forma iônica, cátions que se encontram disponíveis no seio do “eletrólito”. Por outro lado, no “eletro-refino” o metal impuro já existe (ex: com 98% de pureza) constitui e, ao migrar para o catodo, deposita-se neste de forma praticamente pura.
O alumínio vem substituindo o cobre como metal preferido para tubulações em trocadores de calor e condicionadores de ar.
Emissões geradas pelo processo de extrusão
Após a extrusão, as seções são resfriadas e temperadas, recebendo, quando necessário, tratamento de superfície. Esses tratamentos de superfície podem gerar emissões, porque o banho eletrolítico, ao quais os perfis da extrusão são submetidos para ganhar uma camada protetora, contém compostos de alumínio. Os efluentes dos banhos podem ser minimizados se forem selecionados tratamentos adequados para limpar as emissões que entram em contato com a água e o ar.
Laminação
O alumínio pode ser processado a quente ou a frio. O alumínio é um metal muito maleável, podendo ser laminado de 60 cm a 2-6 mm. Como produto final, as folhas de alumínio podem ter a espessura de até 0,006 mm e continuar impermeáveis à luz, aroma ou sabor.
O alumínio, por si só, forma uma camada protetora, que o torna altamente resistente à corrosão. Há, ainda, uma série de tipos de tratamento de superfície que incrementam essas propriedades.
Emissões geradas pela laminação
O óleo utilizado nos diferentes processos da laminação, para garantir a perfeição da superfície e controlar a temperatura, pode gerar emissões.
Quando as tiras recebem tratamento de superfície, os solventes da pintura podem ser liberados no forno de secagem. Existem diversos programas de pesquisa e desenvolvimento em andamento, para reduzir a quantidade de solventes em tintas e vernizes e utilizar revestimentos com menor impacto ambiental.
Fundição
As propriedades do alumínio podem ser alteradas pela adição de pequenas quantidades de outros metais, para obtenção de ligas de alumínio.
Esses metais podem aumentar a resistência, brilho e flexibilidade do alumínio, dependendo da aplicação final. Podem, ainda, torná-lo mais fácil de moldar, permitindo uma variedade infindável de produtos.
Os materiais mais comuns nas ligas de alumínio são o cobre, magnésio e silício. Para aumentar a sua qualidade, substâncias que promovem o refino dos grãos, como o estrôncio, sódio e titânio / boreto de titânio, também são adicionados em pequenas quantidades.
molde, o processo possibilita a fabricação de peças de formas bastante complexas e de paredes mais finas do que os processos por gravidade, permitem.
Fundição por centrifugação
O processo consiste em vazar-se alumínio líquido num molde dotado de movimento de rotação, de modo que a força centrífuga origine uma pressão além da gravidade, que obriga o alumínio líquido ir de encontro com as paredes do molde onde aquele se solidifica.
Fundição de continua
Neste processo, as peças fundidas são longas, com secções quadrada, retangular, hexagonal ou de formatos diversos. Em outras palavras, o processo funde barras de grande comprimento com as secções mencionadas, as quais serão posteriormente processadas por usinagem ou pelos métodos de conformação mecânica no estado sólido. Em princípio, o processo consiste em vazar-se o alumínio líquido num cadinho aquecido. O alumínio líquido escoa através de matrizes de grafite ou cobre resfriados na água.
Fundição de precisão
Os processos de fundição por precisão utiliza um molde obtido pelo revestimento de um modelo consumível com uma pasta ou argamassa refratária que endurece à temperatura ambiente ou mediante a um adequado aquecimento. Uma vez que essa pasta refratária foi endurecida, o modelo é consumido ou inutilizado. Tem-se assim uma casca endurecida que constitui o molde propriamente dito, com as cavidades correspondentes à peça que se deseja produzir. Vazado o alumínio líquido no interior do molde, e solidificado a peça correspondente, o molde é igualmente inutilizado.
Moldes para fundição
Existem diversos tipos de moldes de fundição. Alguns em areia, outros em gesso ou materiais refratários diversos, existem ainda moldes cerâmicos e metálicos, descartáveis, recicláveis, mecanizados, manuais, etc.
Molde em areia verde
Consiste na elaboração do molde com areia úmida modelada pelo formato do modelo da peça a ser fundida. É o método mais empregado na atualidade, serve para todos os metais. É especialmente apropriado para peças de tamanho pequeno e médio. Não é adequado para peças grandes, de geometria complexas, nem para acabamentos finos, pois ficam as marcas de corrugamento da areia, e sua tolerância dimensional é reduzida.
Molde em areia seca
Este tipo de molde se consolida em altas temperaturas (entre 200 e 300°C). Este método utilizado para aumentar a resistência mecânica e a rigidez da forma de fundição. Este processo permite a modelação de peças de grandes dimensões e geometrias complexas. A precisão dimensional é boa e o acabamento superficial é bom, pois o corrugamento das peças causado pela areia é bem menor.
Molde mecânico
Atualmente, ao invés da conformação em areia de forma convencional por compactação manual, usa-se um tipo molde mais compactado chamado de molde mecânico. Trata-se de um sistema desenvolvido para que o material de conformação do molde seja comprimido através de equipamento pneumático ou hidráulico cujas cavidades mecânicas (negativo) ou formas recebam o metal com maior tamanho densidade ou pressão, de forma a suportar os esforços sem que ocorram desmoronamentos durante o preenchimento. Este sistema foi desenvolvido para resolver as deficiências da utilização dos moldes em areia verde, menos resistente.
Moldes para micro fusão
O modelo em cera é pré-aquecido, portanto derreterá e escorrerá para fora do molde, ficando desta forma a cavidade pronta para receber o material fundido.
.A principal vantagem deste sistema é a ausência de machos e de superfícies de junta, ficando a peça com acabamento fino e precisando de pouca usinagem principal.
Coquilha x fundição em areia
A peça fundida em coquilha possui um custo final menor por peça, pois a fundição em areia varia em função das quantidades no que interfere pouco no coquilhamento.
A produção é maior e mais rápida no coquilhamento. Possui uma qualidade superior em acabamento. As peças podem ser fundidas em buchas, insertos e postiços.
Na mesma ferramenta é possível alterar os diâmetros dos furos ou dimensões das buchas e insertos sem alterar o molde, apenas alterando o postiço do molde.
A fabricação de pequenas quantidades para teste ou amostras não depende de programação de produção.
Leveza
Característica essencial na indústria de transportes, a leveza do alumínio representa menor consumo de combustível, menor desgaste, mais eficiência e capacidade de carga. Para o setor de alimentos, traz funcionalidade e praticidade às embalagens por seu peso reduzido em relação a outros materiais.
Elevada condução de energia
O alumínio é um excelente meio de transmissão de energia, seja elétrica ou térmica. Um condutor elétrico de alumínio pode conduzir tanta corrente elétrica quanto um de cobre, que é duas vezes mais pesado e, consequentemente, caro. Por isso, o alumínio é muito utilizado pelo setor de fios e cabos.
O metal também oferece um bom ambiente de aquecimento e resfriamento. Trocadores e dissipadores de calor em alumínio são utilizados em larga escala nas indústrias alimentícia, automobilística, química, aeronáutica, petrolífera, etc. Para as embalagens e utensílios domésticos, essa característica confere ao alumínio a condição de melhor condutor térmico, o que na cozinha é extremamente importante.
Impermeabilidade e opacidade
Característica fundamental para embalagens de alumínio para alimentos e medicamentos. O alumínio não permite a passagem de umidade, oxigênio e luz. Essa propriedade faz com que o metal evite a deterioração de alimentos, remédios e outros produtos consumíveis.
Alta relação resistência/peso Importante para a indústria automotiva e de transportes, confere um desempenho excepcional a qualquer parte de equipamento de transporte que consuma energia para se movimentar. Aos utensílios domésticos oferece uma maior durabilidade e manuseio seguro, com facilidade de conservação. Com uma resistência à tração de 90 Mpa, por meio do trabalho a frio, essa propriedade pode ser praticamente dobrada, permitindo seu uso em estruturas, com excelente comportamento mecânico, aprovado em aplicações como aviões e trens.
Beleza
O aspecto externo do alumínio, além de conferir um bom acabamento apenas com sua aplicação pura, confere modernidade a qualquer aplicação por ser um material nobre, limpo e que não se deteriora com o passar do tempo. Por outro lado, o metal permite uma ampla gama de aplicações de tintas e outros acabamentos, mantendo sempre o aspecto original e permitindo soluções criativas de design.
Durabilidade
O alumínio oferece uma excepcional resistência a agentes externos, intempéries, raios ultravioleta, abrasão e riscos, proporcionando elevada durabilidade, inclusive quando usado na orla marítima e em ambientes agressivos.
O alumínio tem uma autoproteção natural que só é destruída por uma condição agressiva ou por determinada substância que dissipe sua película de óxido de proteção. Essa propriedade facilita a conservação e a manutenção das obras, em produtos como portas, janelas, forros, telhas e revestimentos usados na construção civil.
Maleabilidade e soldabilidade
A alta maleabilidade e ductilidade do alumínio permite à indústria utilizá-lo de diversas formas. Suas propriedades mecânicas facilitam sua conformação e possibilitam a construção de formas adequadas aos mais variados projetos.
Resistência à corrosão
O alumínio tem uma autoproteção natural que só é destruída por uma condição agressiva ou por determinada substância que dissipe sua película de óxido de proteção. Essa propriedade facilita a conservação e a manutenção das obras, em produtos como portas, janelas, forros, telhas e revestimentos usados na construção civil, bem como em equipamentos, partes e estruturas de veículos de qualquer porte. Nas embalagens é fator decisivo quanto à higienização e barreira à contaminação.
Resistência e dureza Ao mesmo tempo em que o alumínio possui um alto grau de maleabilidade, ele também pode ser trabalhado de forma a aumentar sua robustez natural. Com uma resistência à tração de 90 Mpa, por meio do trabalho a frio, essa propriedade pode ser praticamente dobrada, permitindo seu uso em estruturas, com excelente comportamento mecânico, aprovado em aplicações como aviões e trens.
Possibilidade de muitos acabamentos
Seja pela anodização ou pela pintura, o alumínio assume a aparência adequada para aplicações em construção civil, por exemplo, com acabamentos que reforçam ainda mais a resistência natural do material à corrosão.
Infinitamente reciclável
Uma das principais características do alumínio é sua alta reciclabilidade. Depois de muitos anos de vida útil, segura e eficiente, o alumínio pode ser reaproveitado, com recuperação de parte
Tabela das Ligas de Alumínio Trabalháveis Liga Características Aplicações 1050 1100
Alumínio comercialmente puro, muito dúctil no estado recozido, indicado para deformação a frio. Estas ligas têm excelente resistência à corrosão, a qual é crescente com o aumento da pureza da liga
Equipamentos para indústrias alimentícias, químicas, bebidas, trocadores de calor ou utensílios domésticos.
1350 Alumínio 99,5% de pureza, com condutibilidade mínima de 61% IACS.
Barramentos elétricos, peças ou equipamentos que necessitem de alta condutibilidade elétrica. 2017 2024 2117 2219
Ligas de AlCu, com elevada resistência mecânica, alta ductibilidade, média resistência à corrosão e boa usinabilidade.
Peças usinadas e forjadas, indústria aeronáutica, transporte, máquinas e equipamentos.
3003 Ligas de AlMn, com boa resistência à corrosão, boa conformabilidade e moderada resistência mecânica. São ligas de uso geral.
Carrocerias de ônibus e de furgões, equipamentos rodoviários e veículos em geral, reboques, vagões, utensílios domésticos, equipamentos para indústria química e alimentícia, telhas, cumeeiras, rufos, calhas, forros, construção civil e fachadas. 4043 4047
Ligas de AlSi utilizadas em varetas de solda. Soldagem das ligas das séries 1XXX, 3XXX e 6XXX. 5005 5052 5056
Ligas de AlMg são dúcteis no estado recozido, mas endurecem rapidamente sob trabalho a frio. Alta resistência à corrosão em ambientes marítimos. Em geral a resistência mecânica aumenta com os teores crescentes de Mg.
Carrocerias de ônibus e de furgões, equipamentos rodoviários e veículos em geral, estruturas solicitadas, reboques, vagotilde;es ferroviários, elementos estruturais, utensílios domésticos, equipamentos para indústria química e alimentícia, telhas, cumeeiras, rufos, calhas, forros, construção civil, fachadas e embarcações. 6053 6061 6063 6351
Ligas de AlMgSi, tratáveis termicamente com excelente resistência mecânica na têmpera T6.
Carrocerias de ônibus e de furgões, equipamentos rodoviários e veículos em geral, estruturas solicitadas, reboques, vagões ferroviários, elementos estruturais, utensílios domésticos, equipamentos para indústria química e alimentícia, telhas, cumeeiras, rufos, calhas, forros, construção civil, fachadas e embarcações. 7075 7178
Ligas de AlZn, tratáveis termicamente, alta resistência mecânica, boa resistência à corrosão e boaconformabilidade.
Peças sujeitas aos mais elevados esforços mecânicos em indústria aeronáutica, militar, máquinas e equipamentos, moldes para injeção de plástico e estruturas.
Propriedades dos fundidos
Propriedades Mecânicas
As propriedades mecânicas são determinadas por ensaios rotineiros de amostras selecionadas como sendo representativas do produto. Estes ensaios mecânicos são normalmente destrutivos de modo que não devem ser efetuados em produtos acabados, pois alteram suas condições de funcionalidade. Obtêm-se corpos-de-prova de amostras que tenham sido elaboradas do mesmo modo que o produto, exceto no caso de peças fundidas e forjadas. Os ensaios de peças fundidas são feitos em corpos-de-prova do mesmo vazamento do metal da peça fundida e elaborados ao mesmo tempo. Com as peças forjadas, os ensaios, geralmente, são feitos em pedaços cortados do mesmo metal da peça.
Os valores das propriedades mecânicas podem dividir-se em dois grupos:
Valores garantidos: parâmetros mínimos estabelecidos pelas especificações
Valores típicos: obtidos por meio de dados estatísticos propiciados por ensaios rotineiros, que garantem que o material obedece às especificações.
Principais Propriedades dos Alumínios:
É um dos primeiros processos industriais utilizados na produção de artigos de metal. As propriedades do alumínio e a tecnologia moderna oferecem excelentes condições, com controles científicos adequados, para que se possa produzir grandes quantidades de peças mantendo uma qualidade uniforme. O mercado conta com excelentes ligas de alumínio que proporcionam uma grande variedade de propriedades para as peças fundidas. As principais são:
Baixa temperatura de fusão Alta condutividade térmica Forte tendência a oxidação Baixa densidade Elevado coeficiente de dilatação.
Limite de resistência à tração
É a máxima tensão que o material resiste antes de haver sua ruptura. Calcula-se dividindo a carga máxima (em quilogramas) aplicada durante o ensaio, pela seção transversal em milímetros quadrados do corpo-de-prova. Para o alumínio puro recozido, essa razão é de aproximadamente 48MPa (4,9 kg/mm2). O valor aumenta em função da liga, do trabalho a frio e do tratamento térmico (quando possível).
Limite de Escoamento
Consiste na tensão em que o material começa a deformar-se plasticamente e que para o alumínio é de 0,2% do comprimento original medido em um corpo-de-prova normal. É importante definir este grau de deformação permanente porque as ligas de alumínio não possuem limite de
temperaturas acima de 200ºC. Por outro lado, ligas feitas para serviços em altas temperaturas, como às usadas em pistões, retêm suas propriedades adequadamente, funcionando satisfatoriamente dentro da faixa de temperatura de trabalho requerida.
Temperaturas baixas
Quando exposto a temperaturas abaixo de zero, o alumínio não se torna frágil. Sua resistência aumenta sem perder a ductilidade. Esta é a característica que leva uma liga de AlMg ser escolhida para a construção de tanques soldados para armazenamento de gás metano liquefeito, em temperaturas de – 160ºC.
Características Químicas e Físicas
Uma excepcional combinação de propriedades faz do alumínio um dos mais versáteis materiais utilizados na engenharia, arquitetura e indústria em geral.
Ponto de fusão: O alumínio possui ponto de fusão de 660°C, o que é relativamente baixo comparado ao do aço, que é da ordem de 1570°C.
Peso específico: A leveza é uma das principais características do alumínio. Seu peso específico é de cerca de 2,70 g/cm3, aproximadamente 35% do peso do aço e 30% do peso do cobre.
Resistência à corrosão: O alumínio possui uma fina e invisível camada de óxido, a qual protege o metal de oxidações posteriores. Essa característica de autoproteção dá ao alumínio uma elevada resistência à corrosão.
Condutibilidade elétrica: O alumínio puro possui condutividade elétrica de 62% da IACS (Internacional Annealed Copper Standard), a qual associada à sua baixa densidade significa que um condutor de alumínio pode conduzir tanta corrente quanto um condutor de cobre que é duas vezes mais pesado e proporcionalmente mais caro.
Condutibilidade térmica: O alumínio possui condutibilidade térmica 4,5 vezes maior que a do aço.
Refletividade: O alumínio tem uma refletividade acima de 80%, a qual permite ampla utilização em luminárias.
Propriedade antimagnética: Por não ser magnético, o alumínio é frequentemente utilizado como proteção em equipamentos eletrônicos. Além disso, o metal não produz faíscas, o que é uma característica muito importante para garantir sua utilização na estocagem de substâncias inflamáveis ou explosivas, bem como em caminhões-tanque de transporte de combustíveis.
Característica de barreira: O alumínio é um importante elemento de barreira à luz, é também impermeável à ação da umidade e do oxigênio, tornando a folha de alumínio um dos materiais mais versáteis no mercado de embalagens.
Reciclagem: A característica de ser infinitamente reciclável, sem perda de suas propriedades físico-químicas é uma das principais vantagens do alumínio.
Todas essas características apresentadas conferem ao alumínio uma extrema versatilidade. Na maioria das aplicações, duas ou mais destas características entram em jogo, por exemplo: baixo peso combinado com resistência mecânica; alta resistência à corrosão e elevada condutibilidade térmica.
A tabela a seguir compara as características dos três metais mais utilizados pela sociedade contemporânea:
Propriedades físicas típicas Alumínio Aço Cobre Densidade (g/cm³) 2,70 7,86 8, Temperatura de fusão (°C) 660 1500 1083 Módulo de elasticidade (MPa) 70000 205000 110000 Coeficiente de dilatação térmica (L/°C); 23.10- 6 11,7.10- 6 16,5.10- 6 Condutibilidade térmica a 25°C (Cal/cm/°C) 0,53 0,12 0, Condutibilidade elétrica (%IACS) 61 14,5 10
Conclusão
O Brasil tem aptidão para a produção do alumínio, pois além de possuir a terceira maior reserva de bauxita do mundo, tem um alto potencial de geração de energia hidrelétrica, que de acordo com a ABAL (2004) é o insumo primordial para obtenção do alumínio primário através de eletrólise, conforme já mencionado.
Os fabricante estão avançando em diversos setores, com a implantação das mais avançadas tecnologias