
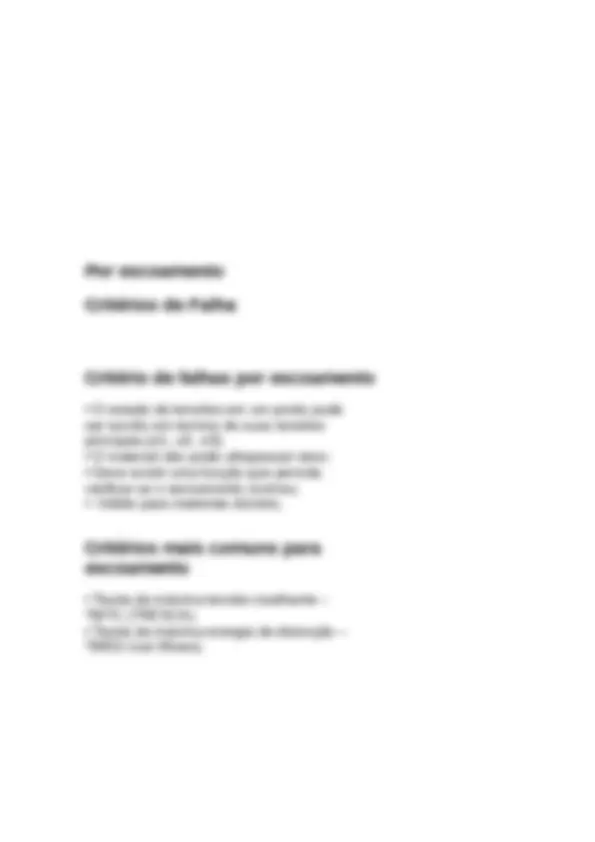
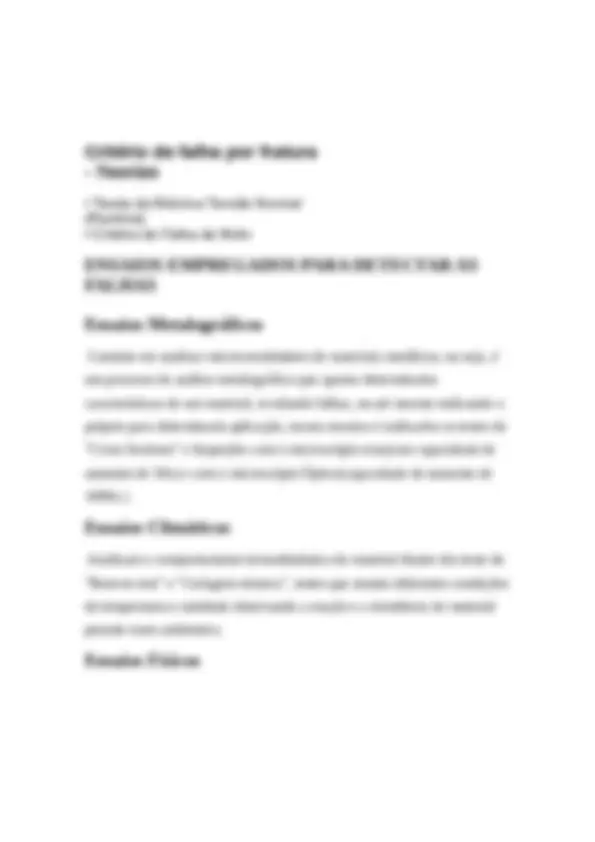
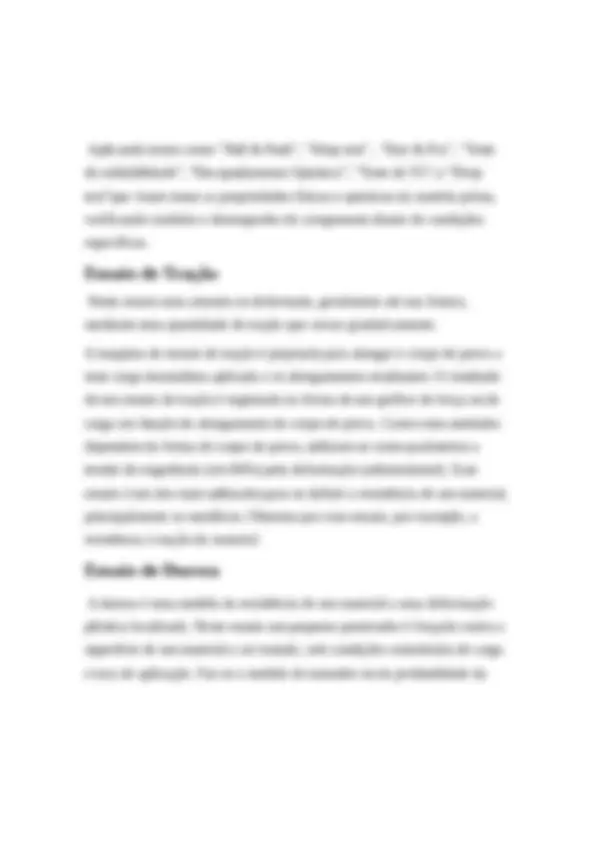
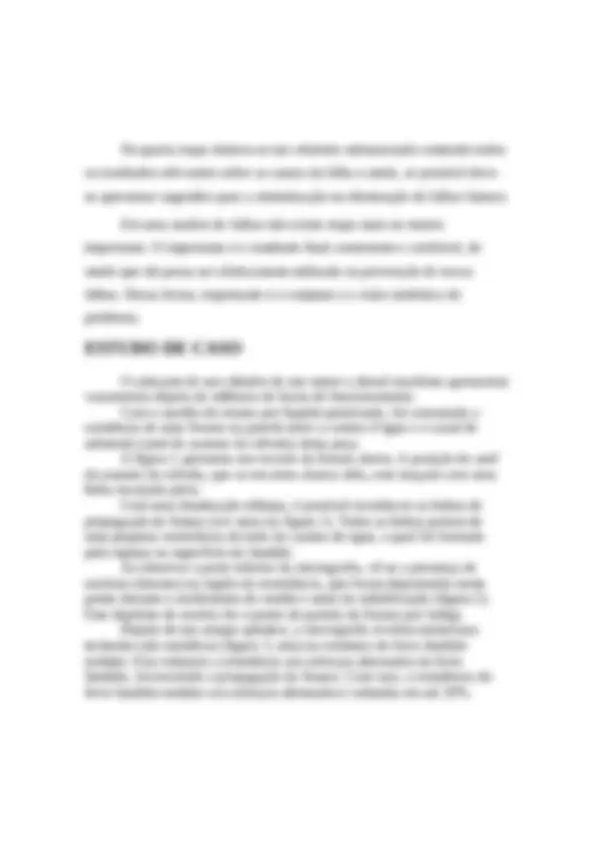
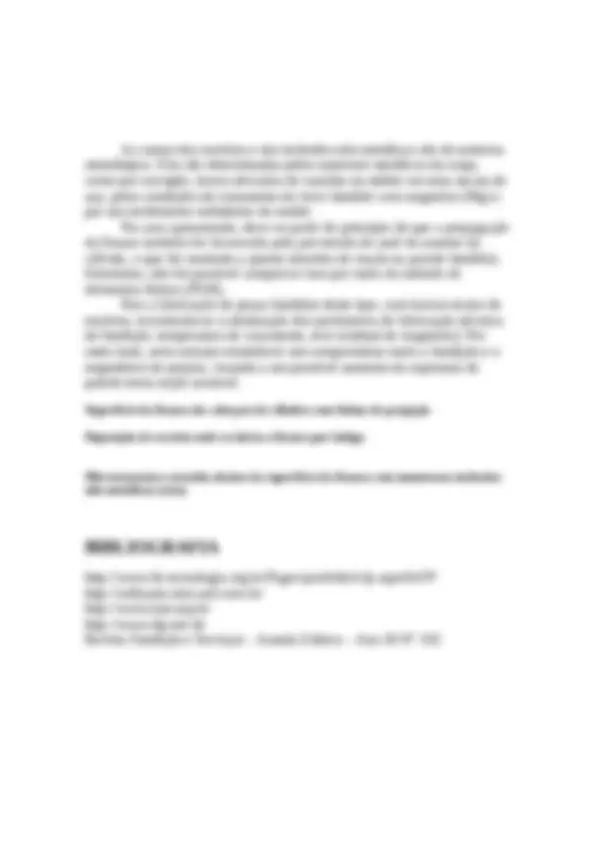
Estude fácil! Tem muito documento disponível na Docsity
Ganhe pontos ajudando outros esrudantes ou compre um plano Premium
Prepare-se para as provas
Estude fácil! Tem muito documento disponível na Docsity
Prepare-se para as provas com trabalhos de outros alunos como você, aqui na Docsity
Os melhores documentos à venda: Trabalhos de alunos formados
Prepare-se com as videoaulas e exercícios resolvidos criados a partir da grade da sua Universidade
Responda perguntas de provas passadas e avalie sua preparação.
Ganhe pontos para baixar
Ganhe pontos ajudando outros esrudantes ou compre um plano Premium
Comunidade
Peça ajuda à comunidade e tire suas dúvidas relacionadas ao estudo
Descubra as melhores universidades em seu país de acordo com os usuários da Docsity
Guias grátis
Baixe gratuitamente nossos guias de estudo, métodos para diminuir a ansiedade, dicas de TCC preparadas pelos professores da Docsity
Trabalho sobre Teoria das Falhas em resistencia dos materiais
Tipologia: Trabalhos
1 / 9
Esta página não é visível na pré-visualização
Não perca as partes importantes!
A metodologia de Análise do Tipo e Efeito de Falha, conhecida como FMEA (do inglês Failure Mode and Effect Analysis), é uma ferramenta que busca, em princípio, evitar, por meio da análise das falhas potenciais e propostas de ações de melhoria, que ocorram falhas no projeto do produto ou do processo. Este é o objetivo básico desta técnica, ou seja, detectar falhas antes que se produza uma peça e/ou produto. Pode-se dizer que, com sua utilização, se está diminuindo as chances do produto ou processo falhar, ou seja, estamos buscando aumentar sua confiabilidade.
Esta dimensão da qualidade, a confiabilidade, tem se tornado cada vez mais importante para os consumidores, pois, a falha de um produto, mesmo que prontamente reparada pelo serviço de assistência técnica e totalmente coberta por termos de garantia, causa, no mínimo, uma insatisfação ao consumidor ao privá-lo do uso do produto por determinado tempo. Além disso, cada vez mais são lançados produtos em que determinados tipos de falhas podem ter conseqüências drásticas para o consumidor, tais como aviões e equipamentos hospitalares nos quais o mau funcionamento pode significar até mesmo um risco de vida ao usuário.
Apesar de ter sido desenvolvida com um enfoque no projeto de novos produtos e processos, a metodologia FMEA, pela sua grande utilidade, passou a ser aplicada de diversas maneiras. Assim, ela atualmente é utilizada para diminuir as falhas de produtos e processos existentes e para diminuir a probabilidade de falha em processos administrativos. Tem sido empregada também em aplicações específicas tais como análises de fontes de risco em engenharia de segurança e na indústria de alimentos.
A norma QS 9000 especifica o FMEA como um dos documentos necessários para um fornecedor submeter uma peça/produto à aprovação da montadora. Este é um dos principais motivos pela divulgação desta técnica. Deve-se, no entanto implantar o FMEA em uma empresa, visando-se os seus resultados e não simplesmente para atender a uma exigência da montadora.
Consiste em analisar microconstituíntes de materiais metálicos, ou seja, é
um processo de análise metalográfico que aponta determinadas
características de um material, revelando falhas, ou até mesmo indicando o
próprio para determinada aplicação, nesses ensaios é realizados os testes de
“Cross Sections” e Inspeções com o microscópio ersa(com capacidade de
aumento de 50x) e com o microscópio Óptico(capacidade de aumento de
1000x ).
Analisam o comportamento termodinâmico do material diante dos teste de “Burn-in test” e “Ciclagem térmica”, testes que simula diferentes condições de temperatura e umidade observando a reação e a resistência do material perante esses ambientes;
Aplicando testes como “Pull & Push”, “Drop test” , “Dye & Pry”, “Teste
de soldabilidade”, “Decapsulamento Quimico”, “Teste de TG”,e “Drop
test”que visam testar as propriedades físicas e químicas da matéria prima,
verificando também o desempenho do componente diante de condições
específicas.
Neste ensaio uma amostra se deformada, geralmente até sua fratura,
mediante uma quantidade de tração que cresce gradativamente.
A maquina de ensaio de tração é projetada para alongar o corpo de prova a
uma carga instantânea aplicada e os alongamentos resultantes. O resultado
de um ensaio de tração é registrado na forma de um gráfico de força ou de
carga em função do alongamento do corpo de prova. Como estas unidades
dependem da forma do corpo de prova, utilizam-se como parâmetros a
tensão de engenharia (em MPa) pela deformação (adimensional). Esse
ensaio é um dos mais utilizados para se definir a resistência de um material,
principalmente os metálicos. Obtemos por esse ensaio, por exemplo, a
resistência à tração do material.
A dureza é uma medida da resistência de um material a uma deformação
plástica localizada. Neste ensaio um pequeno penetrador é forçado contra a
superfície de um material a ser testado, sob condições controladas de carga
e taxa de aplicação. Faz-se a medida do tamanho ou da profundidade da
Nesta análise, são utilizadas técnicas para determinação da composição
química da amostra. Feita esta determinação, compara-se o resultado com
uma norma específica ou com uma especificação fornecida pelo cliente.
Vemos, então, se a composição encontrada está dentro ou fora do
especificado para aquele material. Caso esteja fora da especificação, iremos
analisar se isso teve alguma implicação direta ou indireta para a causa da
falha.
Primeiro passo: coleta de dados, sobre o componente e seu contexto
no sistema que se insere. Pontos importantes: exame preliminar e uma
documentação fotográfica inicial detalhada do componente, pois durante as
análises ele é manuseado constantemente e é partido em várias amostras, o
que altera sua forma original.
A segunda etapa consiste na analise das evidencias. São feitos nesta
etapa os testes mecânicos, as analises micro e macroestruturas e são
analisados os mecanismos da fratura.
Em terceiro, formula-se uma hipótese que é validada de acordo com
os resultados da etapa anterior.
Na quarta etapa elabora-se um relatório substanciado contendo todos
os resultados relevantes sobre as causas da falha e ainda, se possível deve-
se apresentar sugestões para a minimização ou eliminação de falhas futuras.
Em uma analise de falhas não existe etapa mais ou menos
importante. O importante é o resultado final consistente e confiável, de
modo que ele possa ser efetivamente utilizado na prevenção de novas
falhas. Dessa forma, importante é o conjunto e a visão sistêmica do
problema.
O cabeçote de um cilindro de um motor a diesel marítimo apresentou vazamentos depois de milhares de horas de funcionamento. Com o auxilio do ensaio por liquido penetrante, foi constatada a existência de uma fissura na parede entre a camisa d’água e o canal de admissão (anel do assento da válvula) desta peça. A figura 1 apresenta um recorte da fissura aberta. A posição do anel do assento da válvula, que se encontra abaixo dela, está maçada com uma linha tracejada preta. Com uma iluminação oblíqua, é possível reconhecer as linhas de propagação da fissura (ver setas na figura 1). Todas as linhas partem de uma pequena reentrância do lado da camisa de água, a qual foi formada pela ruptura na superfície do fundido. Ao observar a parte inferior da micrografia, vê-se a presença de escórias (drosses) na região da reentrância, que foram depositadas neste ponto durante o enchimento do molde e antes da solidificação (figura 2). Este depósito de escória foi o ponto de partida da fissura por fadiga. Depois de um ataque químico, a micrografia revelou numerosas inclusões não-metálicas (figura 3, seta) na estrutura do ferro fundido nodular. Elas reduzem a resistência aos esforços alternados do ferro fundido, favorecendo a propagação da fissura. Com isso, a resistência do ferro fundido nodular aos esforços alternados é reduzida em até 20%.