
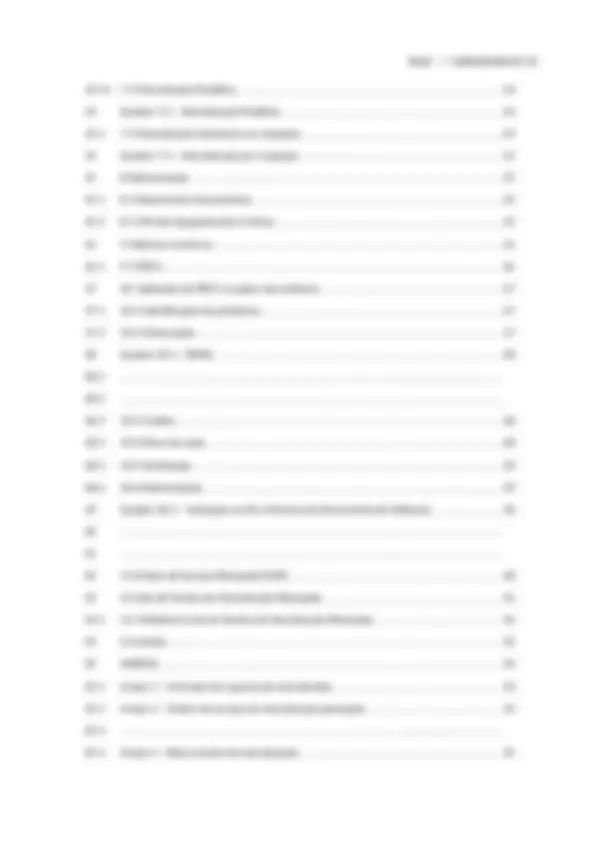
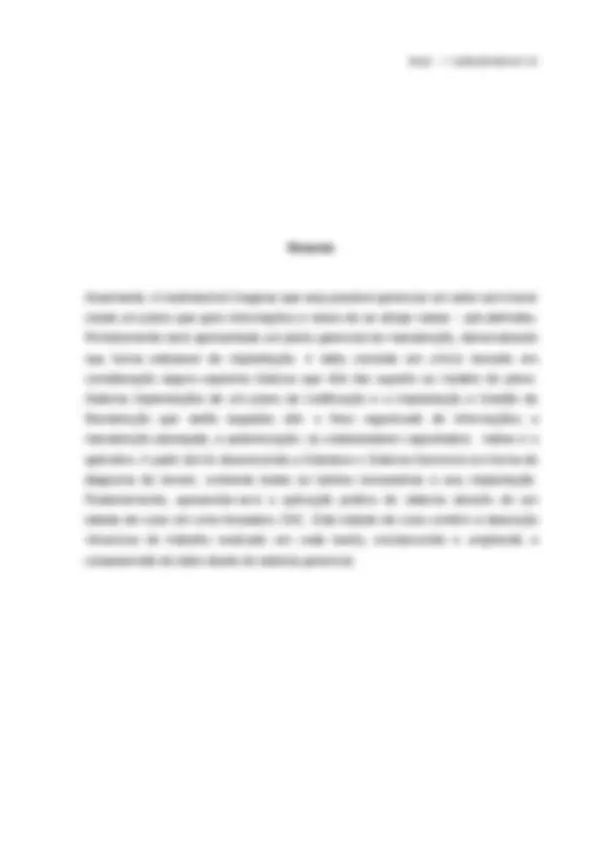
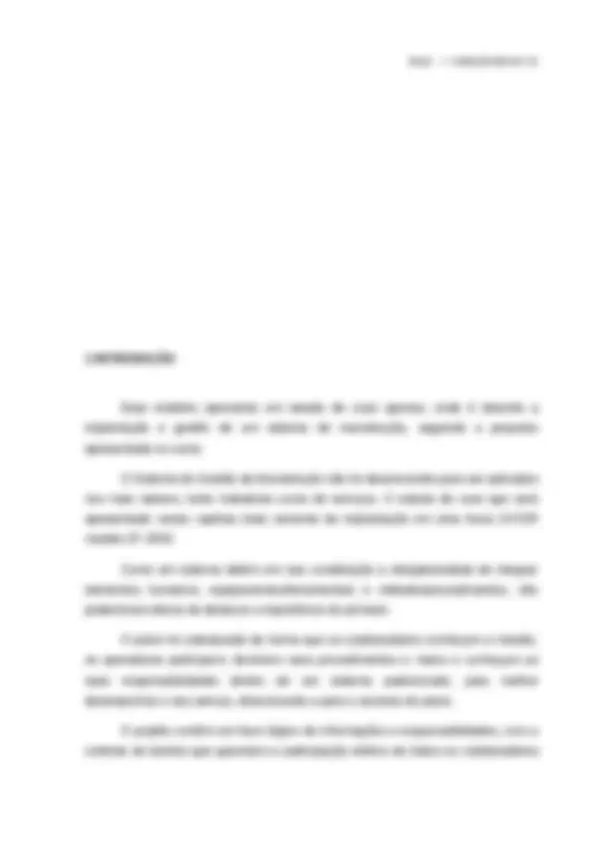
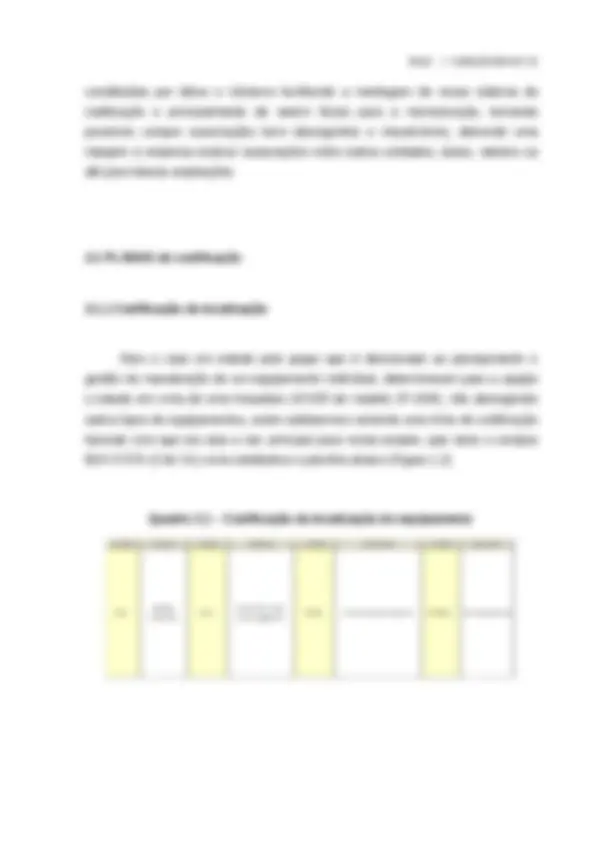
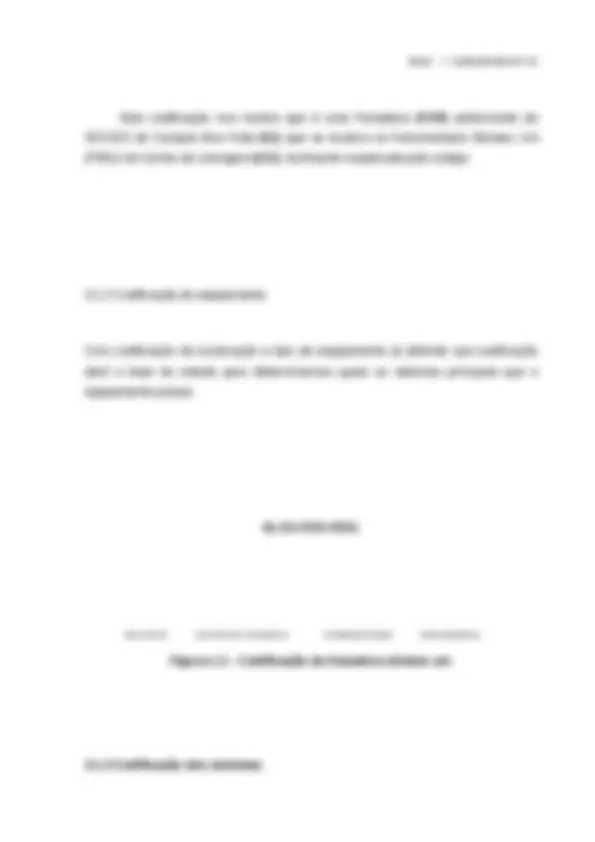
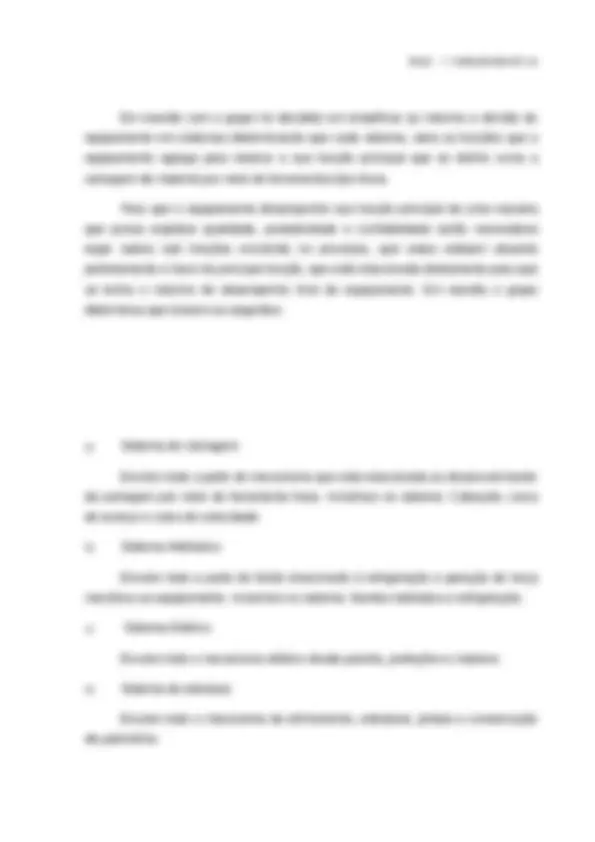
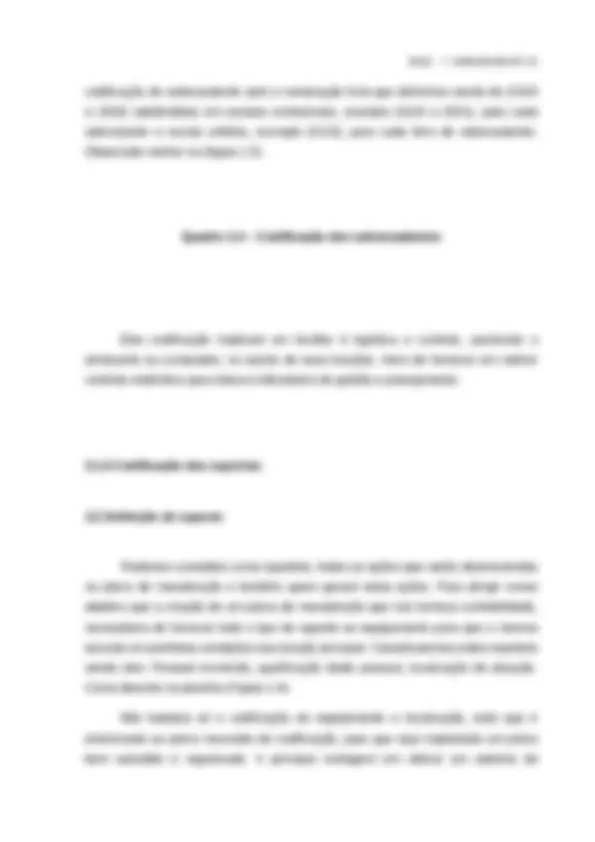
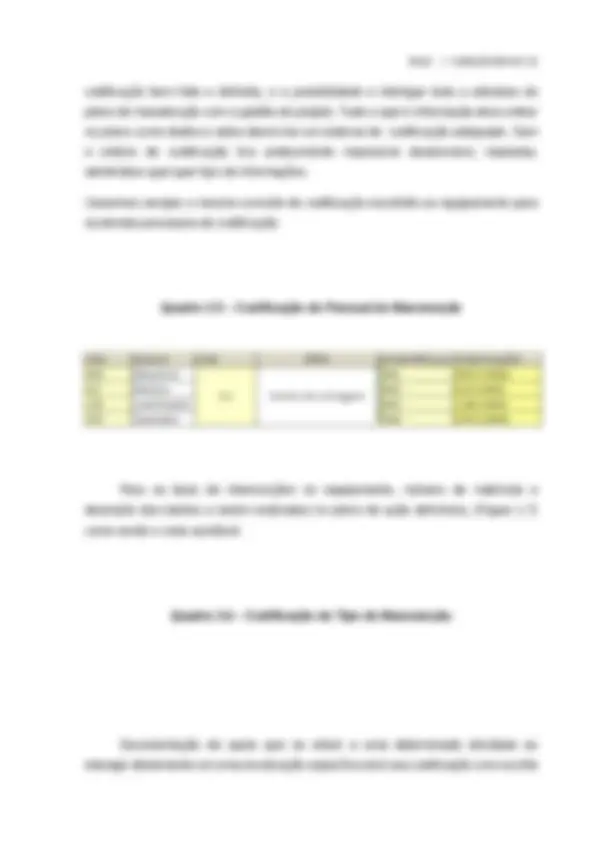
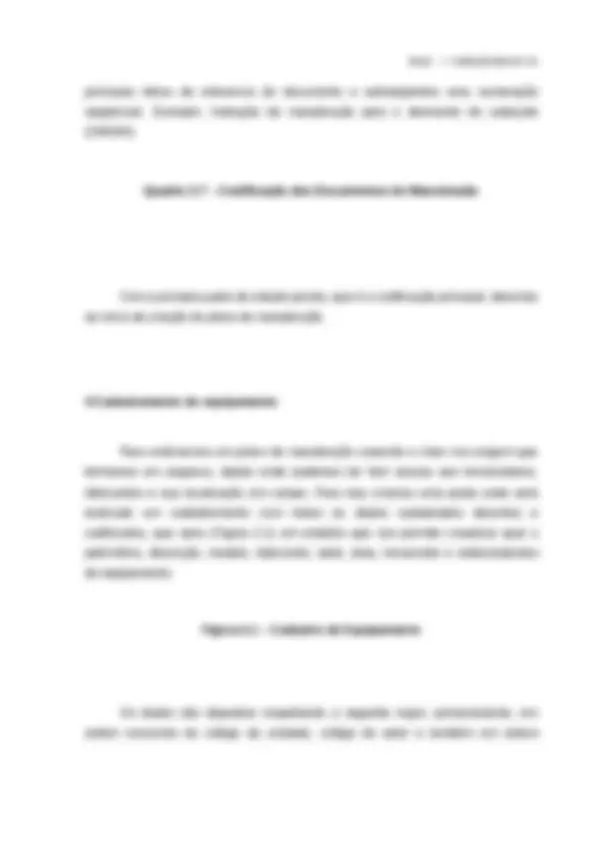
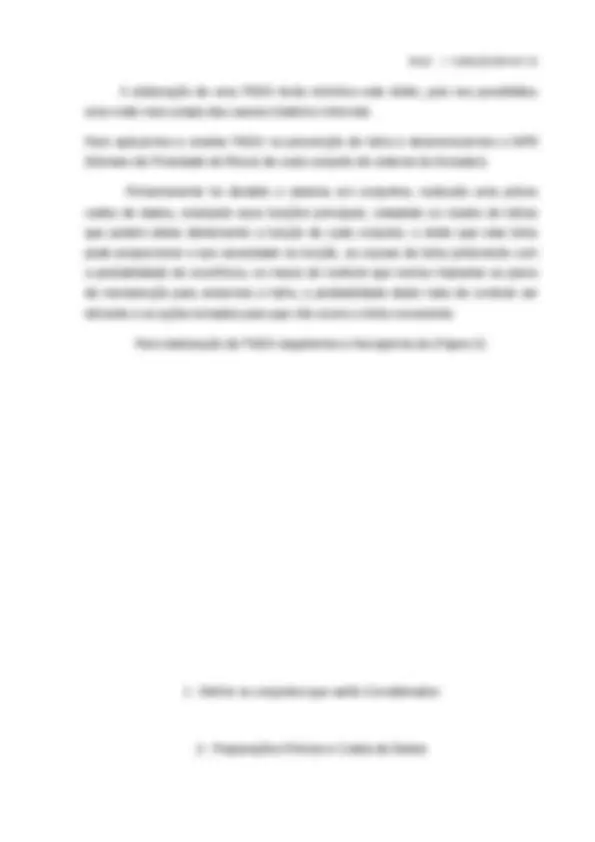
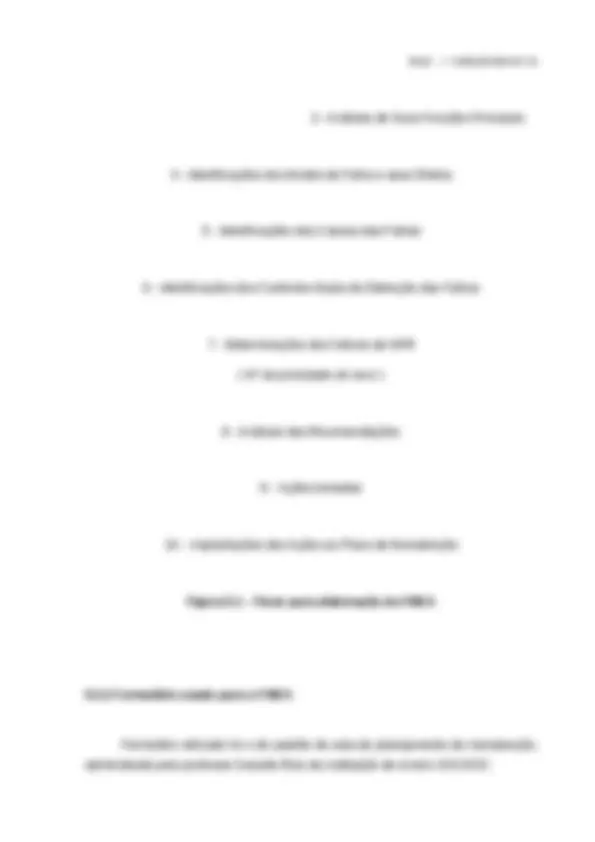
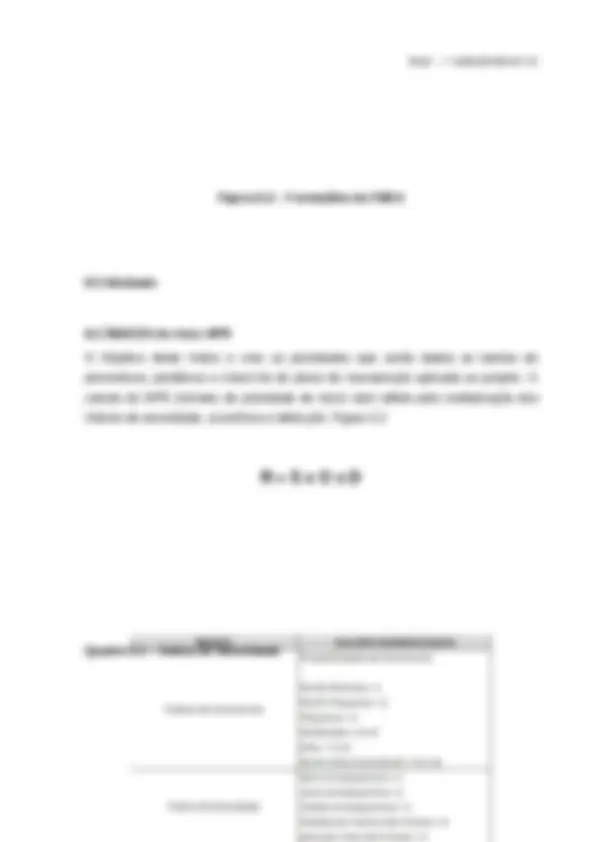
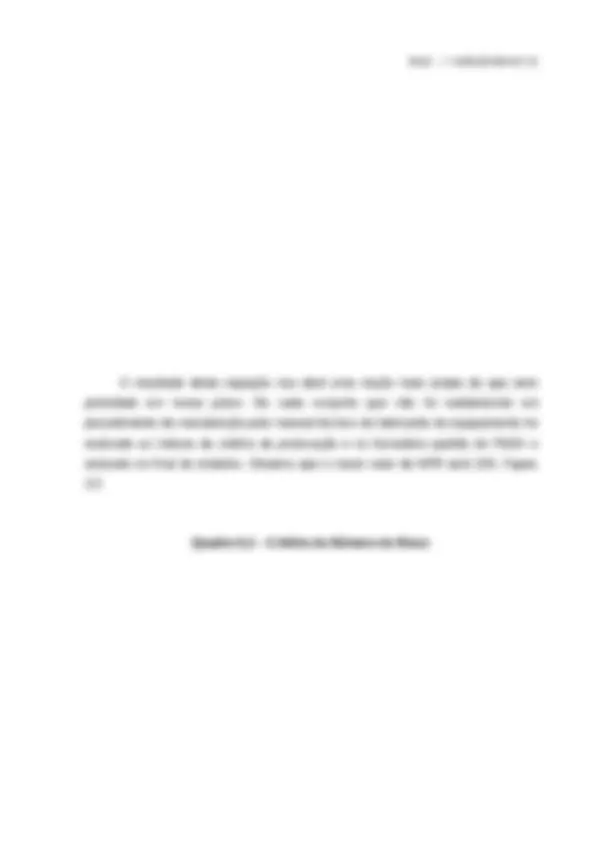
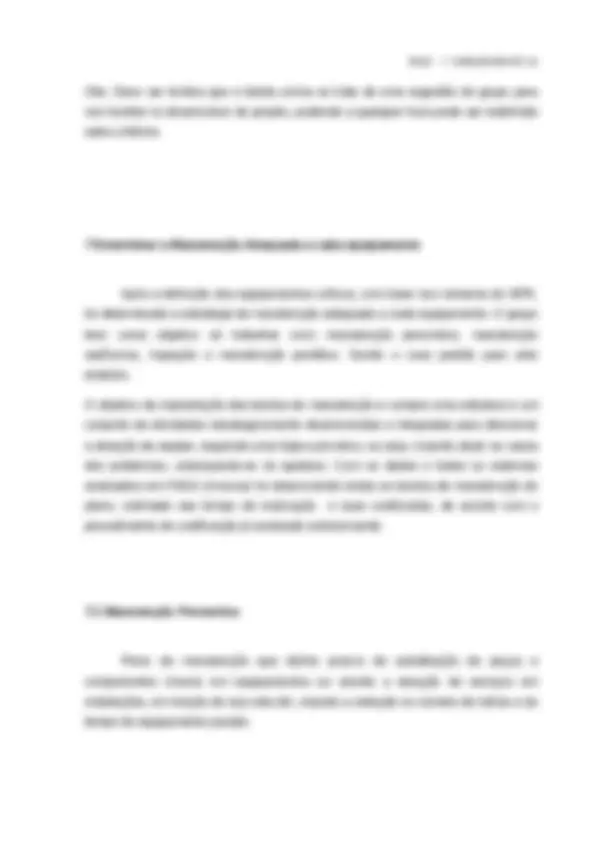
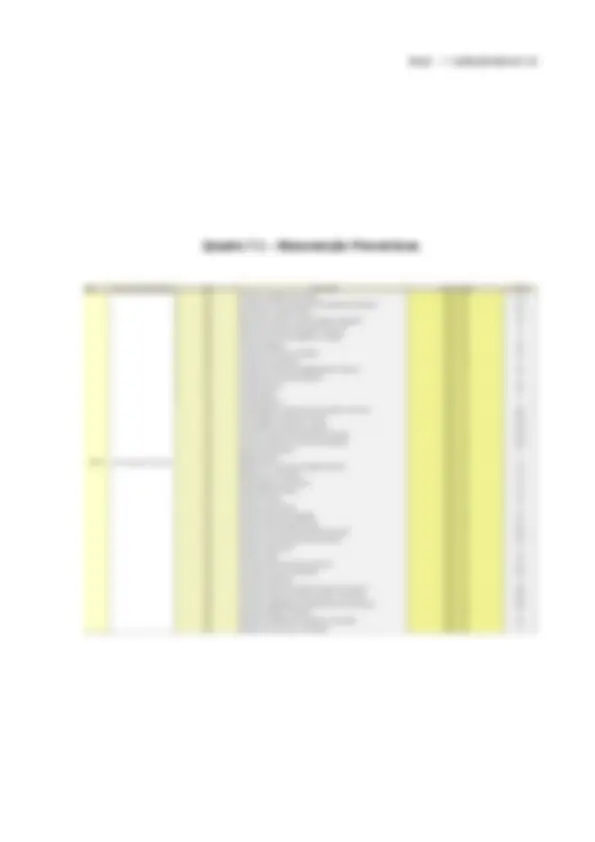
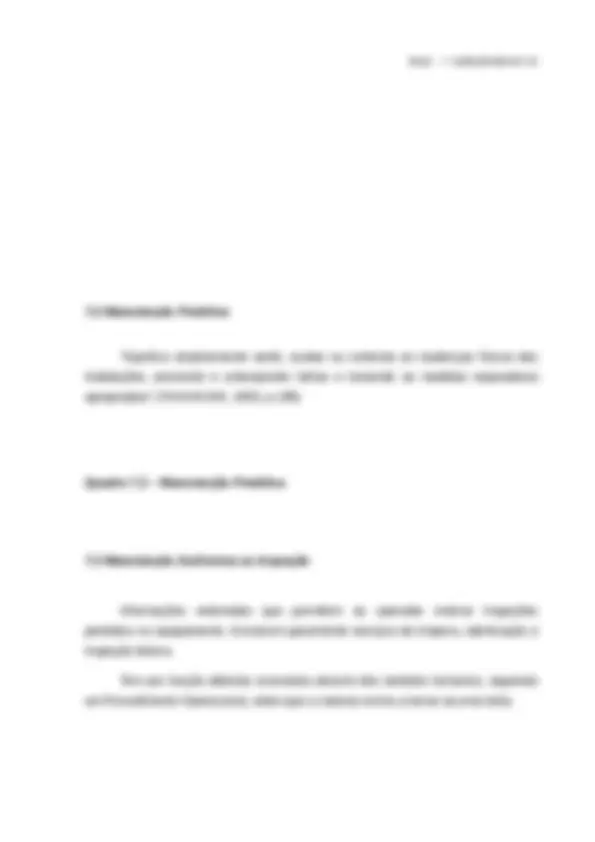
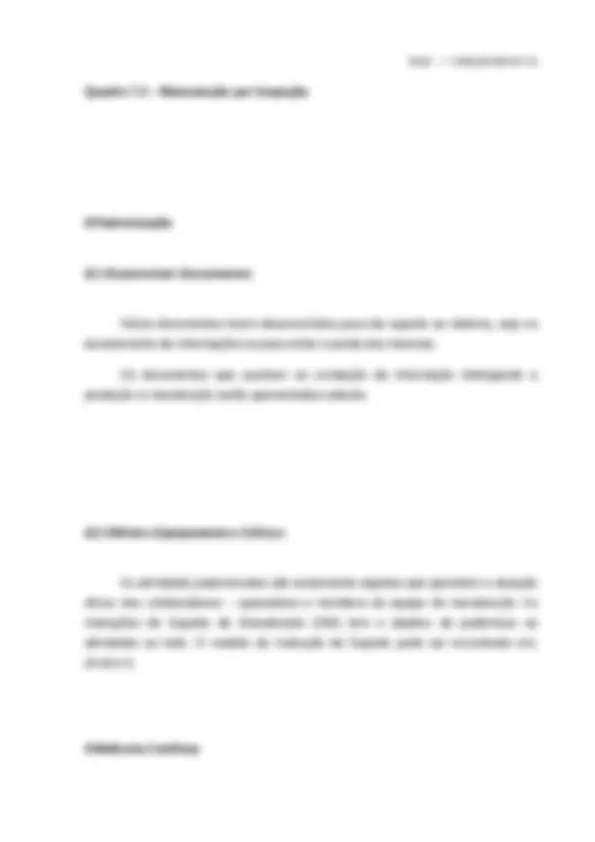
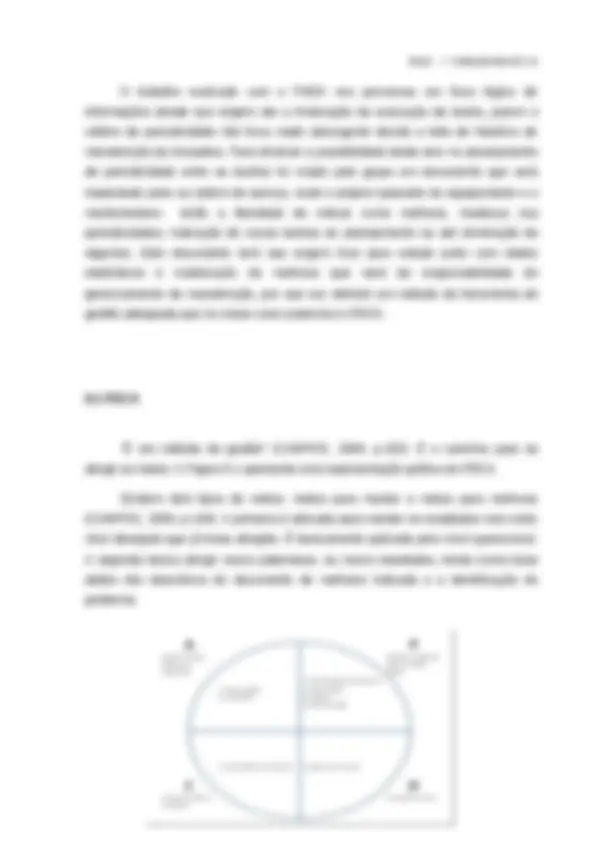
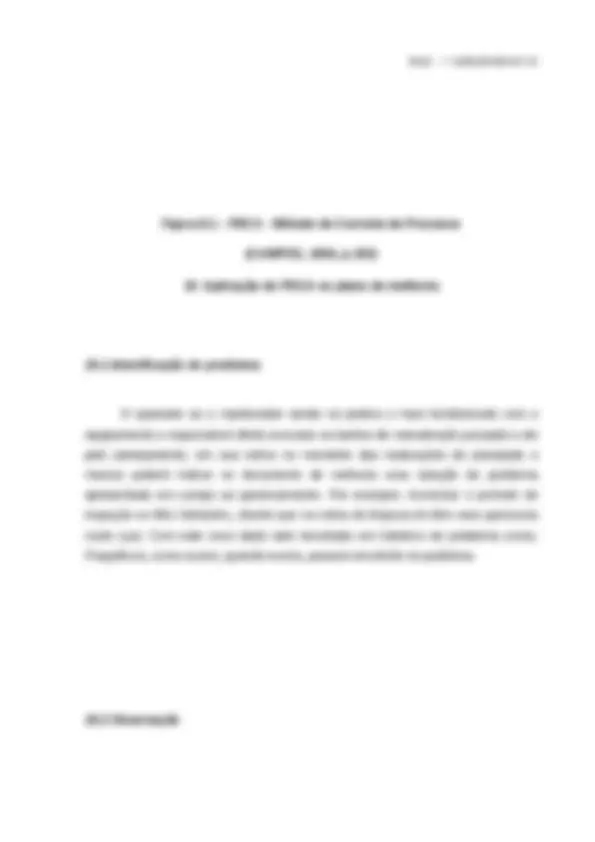
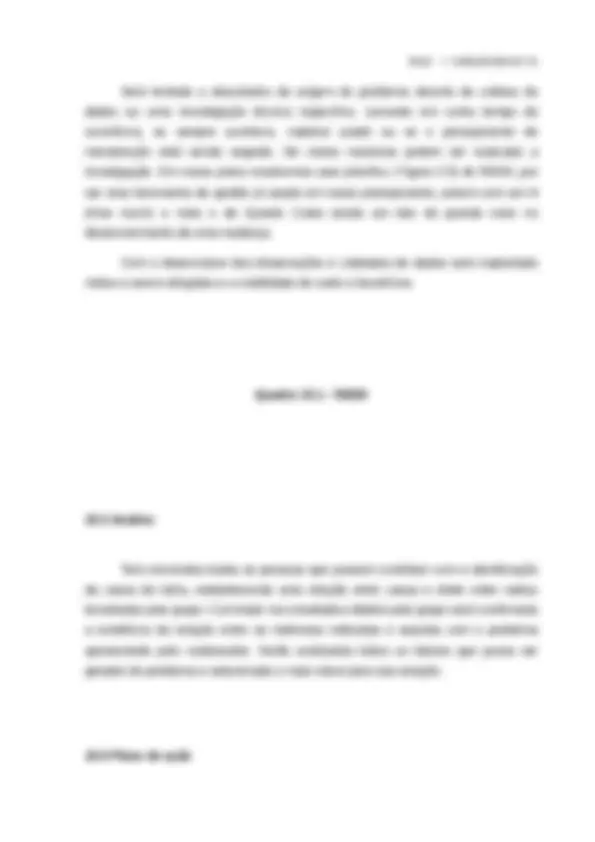
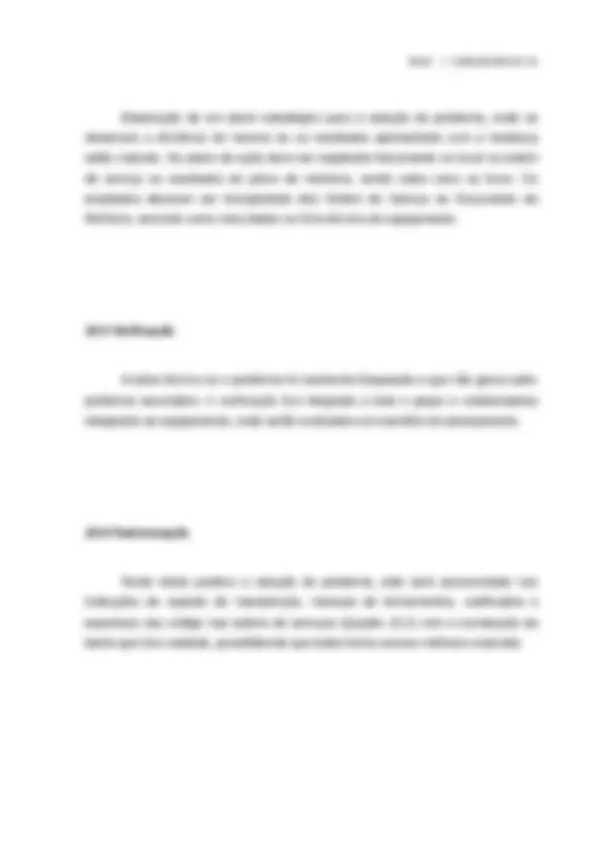
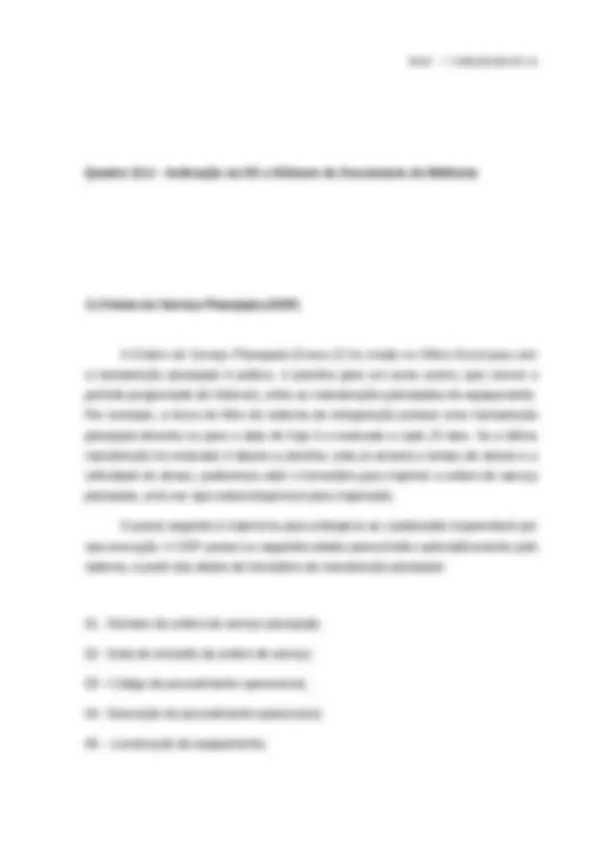
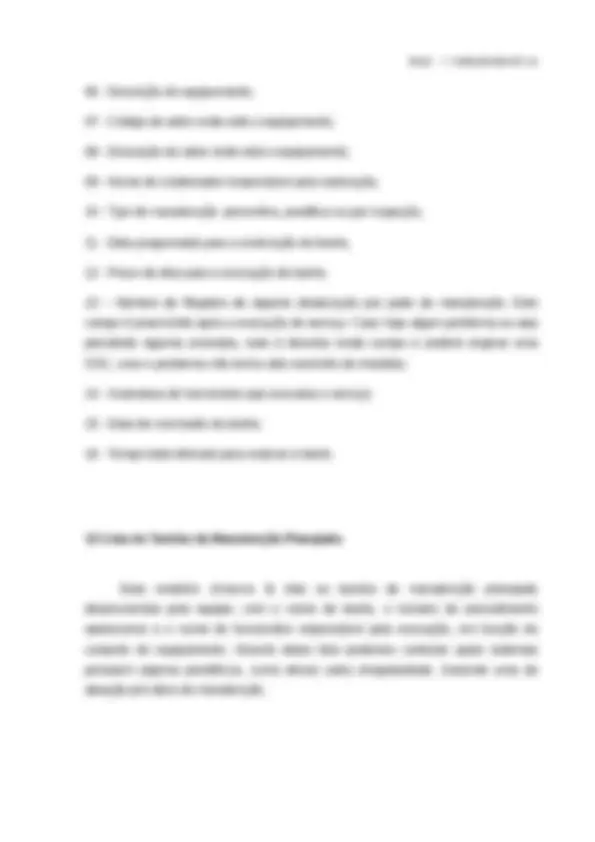
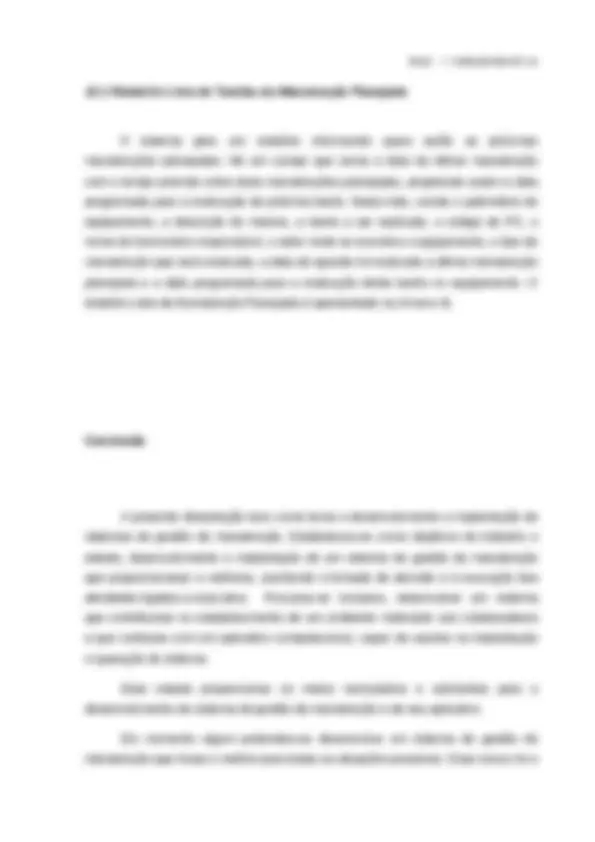
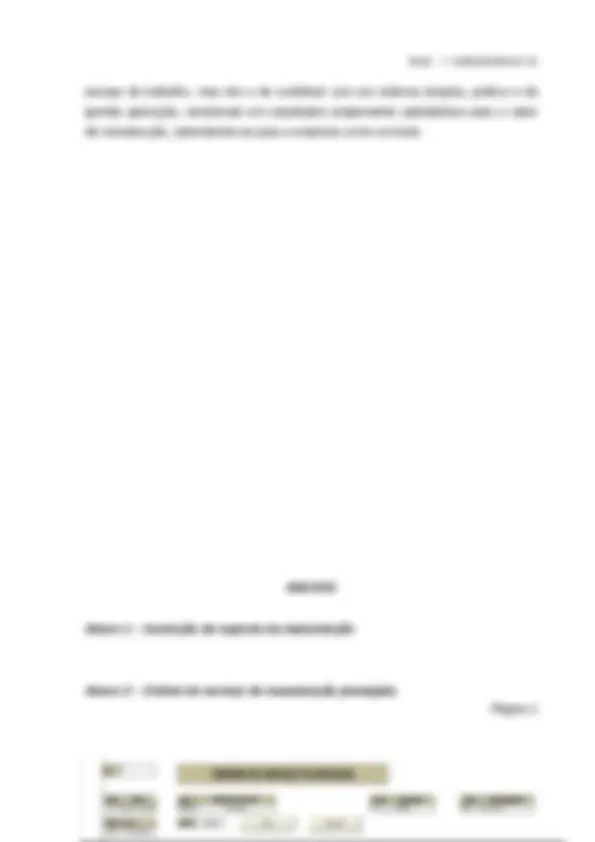
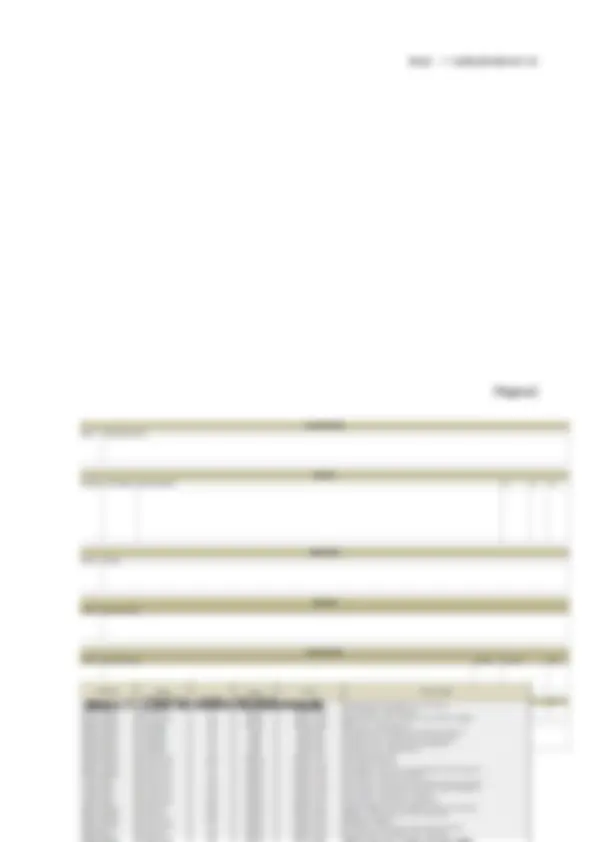
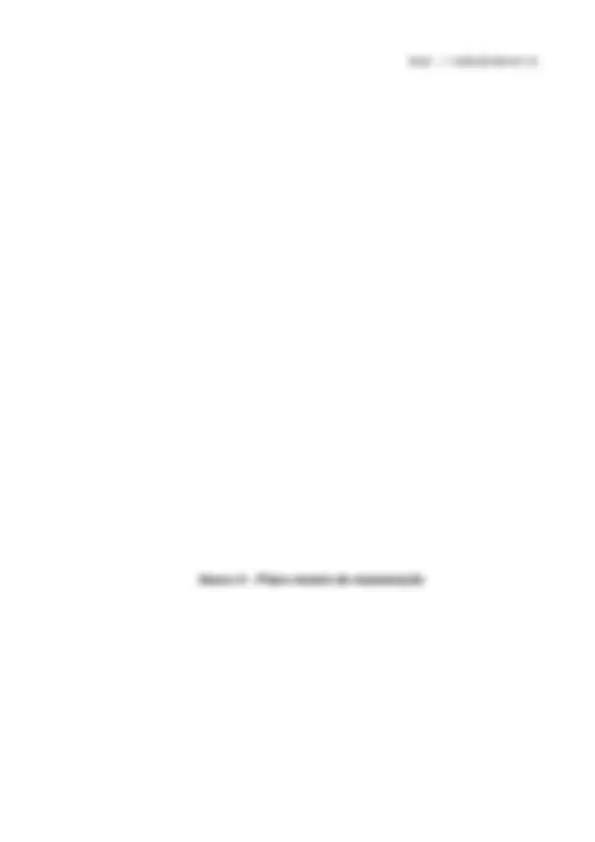
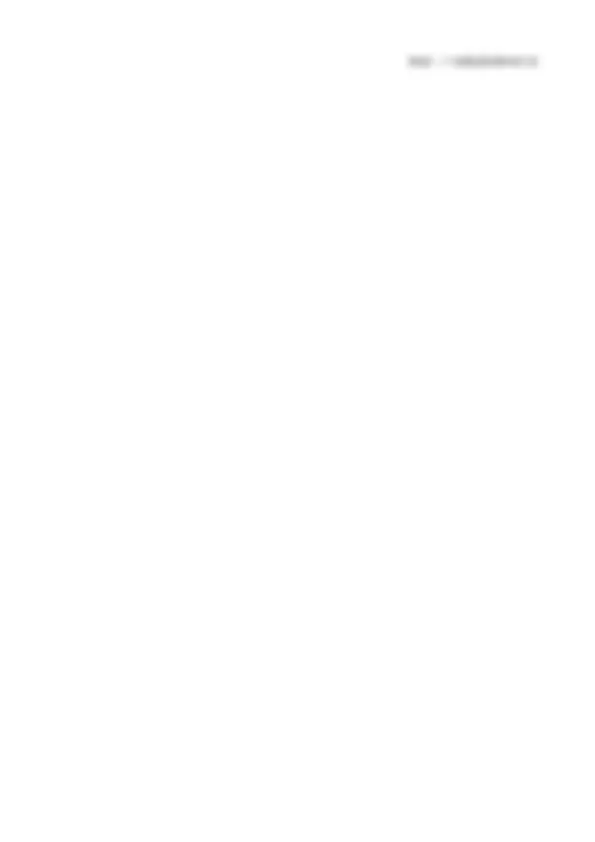
Estude fácil! Tem muito documento disponível na Docsity
Ganhe pontos ajudando outros esrudantes ou compre um plano Premium
Prepare-se para as provas
Estude fácil! Tem muito documento disponível na Docsity
Prepare-se para as provas com trabalhos de outros alunos como você, aqui na Docsity
Os melhores documentos à venda: Trabalhos de alunos formados
Prepare-se com as videoaulas e exercícios resolvidos criados a partir da grade da sua Universidade
Responda perguntas de provas passadas e avalie sua preparação.
Ganhe pontos para baixar
Ganhe pontos ajudando outros esrudantes ou compre um plano Premium
Comunidade
Peça ajuda à comunidade e tire suas dúvidas relacionadas ao estudo
Descubra as melhores universidades em seu país de acordo com os usuários da Docsity
Guias grátis
Baixe gratuitamente nossos guias de estudo, métodos para diminuir a ansiedade, dicas de TCC preparadas pelos professores da Docsity
Plano de manutenção em uma fresadora ZAYER modelo ZF-2000
Tipologia: Notas de estudo
1 / 36
Esta página não é visível na pré-visualização
Não perca as partes importantes!
6 ........................................................................................................................................
9 ........................................................................................................................................
Resumo
Atualmente, é inadmissível imaginar que seja possível gerenciar um setor sem haver criado um plano que gere informações e meios de se atingir metas – pré-definidas. Primeiramente será apresentado um plano gerencial da manutenção, demonstrando sua forma estrutural de implantação. A idéia consiste em criá-lo levando em consideração alguns aspectos básicos que irão dar suporte ao modelo do plano. Sistema implantações de um plano de codificação e a Implantação e Gestão da Manutenção que serão seguidos são: o fluxo organizado de informações; a manutenção planejada; a padronização; os colaboradores capacitados; metas e o aplicativo. A partir dai foi desenvolvida a Estrutura o Sistema Gerencial em forma de diagrama de árvore, contendo todas as tarefas necessárias a sua implantação. Posteriormente, apresentar-se-á a aplicação prática do sistema através de um estudo de caso em uma fresadora CNC. Este estudo de caso contém a descrição minuciosa do trabalho realizado em cada tarefa, esclarecendo e ampliando a compreensão do leitor diante do sistema gerencial.
Esse relatório apresenta um estudo de caso apenas, onde é descrita a implantação e gestão de um sistema de manutenção, seguindo a proposta apresentada no curso.
O Sistema de Gestão da Manutenção não foi desenvolvido para ser aplicados nos mais setores, tanto industriais como de serviços. O estudo de caso que será apresentado nesse capítulo trata somente da implantação em uma fresa ZAYER modelo ZF-2000.
Como um sistema detém em sua constituição a obrigatoriedade de integrar elementos humanos, equipamentos/ferramentais e métodos/procedimentos, não poderíamos deixar de destacar a importância do primeiro.
O plano foi estruturado de forma que os colaboradores conheçam a missão, os operadores participem; dominem seus procedimentos e meios e conheçam as suas responsabilidades dentro de um sistema padronizado, para melhor desempenhar o seu serviço, direcionando-o para o sucesso do plano.
O projeto contém um fluxo lógico de informações e responsabilidades, com o controle de tarefas que garantam a participação efetiva de todos os colaboradores
Quadro 2.1 – 5W1H do Planejamento do Sistema Gerencial da Manutenção
3 Codificação e critérios definidos
Nada podemos fazer para a implantação do plano de manutenção na fresadora se não for estabelecido um sistema de codificação com critérios bem definidos tais como; a empresa que o equipamento pertence, a área que se localiza, o setor em que esta operando, sua função neste setor, os sistemas que estão relacionados ao comprometimento de sua função principal, os conjuntos e subconjuntos de cada sistema. Partindo da divisão estrutural principal (Figura 1.1) a instituição SOCIESC, que será base para a implantação de outras divisões estruturais, estabelecendo coligações com os critérios relacionados à estruturação principal da SOCIEC, sendo outras subdivisões como: definições de sobressalentes, critério de criticidade, tipos de manutenções, tarefas realizadas pela manutenção, status operacionais, ferramentas de controle e gestão de manutenção e as responsabilidades técnicas.
Figura 3.1 – Diagrama principal
Após o grupo ter definido a estruturação principal foram estabelecidas as codificações das raízes de onde veio se tornar a base principal para as demais. Ficou determinado que usassem codificações do tipo alfanuméricos que são
constituídas por letras e números facilitando a montagem de nosso sistema de codificação e principalmente de serem fáceis para a memorização, tornando possíveis compor associações bem abrangentes e visualizáveis, deixando uma margem à empresa realizar associações entre outras unidades, áreas, setores ou até para futuras ampliações.
3.1 PLANOS de codificação
3.1.1 Codificação de localização
Para o caso em estudo pelo grupo que é direcionado ao planejamento e gestão da manutenção de um equipamento individual, determinaram para a equipe o estudo em cima de uma fresadora ZAYER de modelo ZF-2000, não abrangendo outros tipos de equipamentos, assim adotaremos somente uma linha de codificação fazendo com que ela seja a raiz principal para nosso projeto, que seria o campos BOA VISTA (Cód. 01) como estabelece a planilha abaixo (Figura 1.2).
Quadro 3.1 – Codificação da localização do equipamento
Em reunião com o grupo foi decidido em simplificar ao máximo a divisão do equipamento em sistemas determinando que cada sistema, seria as funções que o equipamento agrega para realizar a sua função principal que se define como a usinagem de material por meio de ferramentas tipo fresa.
Para que o equipamento desempenhe sua função principal de uma maneira que possa englobar qualidade, produtividade e confiabilidade serão necessárias reger outras sub funções envolvida no processo, que estas estejam atuando perfeitamente a favor da principal função, que está relacionada diretamente para que se tenha o máximo de desempenho final do equipamento. Em reunião o grupo determinou que fossem as seguintes:
a) Sistema de Usinagem
Envolve toda a parte do mecanismo que esta relacionada ao desenvolvimento da usinagem por meio da ferramenta fresa. Incluímos no sistema: Cabeçote, caixa de avanço e caixa de velocidade.
b) Sistema Hidráulico
Envolve toda a parte de fluído relacionado à refrigeração e geração de força mecânica ao equipamento. Incluímos no sistema: Bomba hidráulica e refrigeração.
c) Sistema Elétrico
Envolve todo o mecanismo elétrico desde painéis, proteções e motores. d) Sistema de estrutura Envolve todo o mecanismo de alinhamento, estrutural, pintura e conservação de patrimônio.
Todos os sistemas foram adotados como sub função primordial para o equipamento fresadora realize sua função principal.
Após a divisão em sistema do equipamento, determinamos que a melhor codificação, seria em dotarmos as três principais letras de cada descrito do sistema, para que pudéssemos criar uma codificação gerando melhor caracterização e visibilidade e acrescentamos juntos dois números deixando margens as futuras ampliações (Figura 1.4). Como exemplo, o Sistema de Usinagem Numero Um, ficou codificado em SDU01.para os sub conjuntos adotaremos a mesma regra excluído a codificação em número, por não ser necessário, já que neste estudo não foi encontrado sub conjuntos iguais para exercer a mesma sub função.
Quadro 3.2 – Codificação dos sistemas
3.1.4 Codificação dos conjuntos
Para os conjuntos adotaremos a mesma regra excluída a codificação em número, por não ser necessário, já que neste estudo não foi encontrado conjuntos iguais para exercer a mesma sub função.
codificação do sobressalente será a numeração final que definimos sendo de ( a 1500) subdivididos em escalas centesimais, exemplo (0100 a 0201), para cada subconjunto e escala unitária, exemplo (0115), para cada item de sobressalente. Observado melhor na (figura 1.5).
Quadro 3.4 – Codificação dos sobressalentes
Esta codificação implicará em facilitar à logística e controle, auxiliando o almoxarife ou comprador, no auxilio de suas funções. Alem de fornecer um melhor controle estatístico para futuros indicadores de gestão e planejamento.
3.1.6 Codificação dos suportes
3.2 Definição de suporte
Podemos considera como suportes, todas as ações que serão desenvolvidas no plano de manutenção e também quem gerará estas ações. Para atingir nosso objetivo que a criação de um plano de manutenção que nos forneça confiabilidade, necessitaria de fornecer todo o tipo de suporte ao equipamento para que o mesmo execute em perfeitas condições sua função principal. Classificaremos estes suportes sendo eles: Pessoal envolvido, qualificação deste pessoal, localização de atuação. Como descrito na planilha (Figura 1.6).
Não bastaria só a codificação do equipamento e localização, tudo que é relacionado ao plano necessita de codificação, para que seja implantado um plano bem sucedido e organizado. A principal vantagem em utilizar um sistema de
codificação bem feita e definida, e a possibilidade e interligar toda a estrutura do plano de manutenção com a gestão do projeto. Tudo o que é informação deve entrar no plano como dados e estes devem ter um sistema de codificação adequado. Sem o critério de codificação fica praticamente impossível desenvolver, implantar, administrar qual quer tipo de informações.
Usaremos sempre o mesmo conceito de codificação escolhido ao equipamento para os demais processos de codificação:
Quadro 3.5 – Codificação do Pessoal de Manutenção
Para os tipos de intervenções no equipamento, número de matrícula e descrição das tarefas a serem realizadas no plano de ação definimos, (Figura 1.7) como sendo o mais aceitável.
Quadro 3.6 – Codificação do Tipo de Manutenção
Documentação de apoio que se referir a uma determinada atividade ou interagir diretamente em uma localização específica terá sua codificação com as três
crescente de equipamento. O relatório apresenta todos os equipamentos cadastrados e suas respectivas unidades e setores.
5 Desenvolvimento do plano de manutenção
5.1 Sistemática do Plano de Manutenção
A sistemática do plano de Manutenção engloba, em sua estrutura, um conjunto de atividades estrategicamente desenvolvidas pelo grupo e integradas nas ordens de serviços para direcionar a atuação da equipe, seguindo uma lógica pró-ativa, ou seja, visando atuar na causa dos problemas, antecipando-se às quebras.
Estabelecer e garantir um fluxo lógico das informações desde a sua origem até a finalização da execução do serviço.
5.2 Programação da Manutenção Planejada
A programação da manutenção planejada foi elaborada pelo grupo utilizando o próprio manual do fabricante onde registrado nele as principais ações preventivas a serem tomada e sua periodicidade. Porem, neste caso, o manual do fabricante adquirido pelo grupo só apresentou como plano de preventiva, os períodos de lubrificações e tipo de lubrificante. Como a intenção do grupo era a criação de um plano mais completo e confiável tivemos então a necessidade de nos baseamos um ponto de partida concreto e para isso decidimos umar a ferramenta de gestão FMEA. A decisão tomada nos facilitou muito, pois como já tínhamos sub divididos o equipamento em sistemas e conjuntos nos bastou definir as funções principais de cada conjunto e utilizar a ferramenta de uma maneira mais clara possível. só consiste em definir os conjuntos dos sistemas, a tarefa a ser realizada, a sua periodicidade, o tipo de intervenção, o responsável pela tarefa, o tempo da realização da tarefa, a data da última manutenção planejada, situação da programação das tarefas, status de operação do equipamento, inserção de
melhorias e a criação das documentações padrões como; Ordem de serviço da manutenção, check list diários, plano mestre anual de manutenção, instruções de suporte e formulário de proposta de melhoria.
5.3 Apresentação do FMEA
Define FMEA ( Failure Mode and Effect Analysis ) como um método de análise de produtos ou processos usados para identificar todos os possíveis modos potenciais de falha e determinar o efeito de cada um sobre o desempenho do sistema (produto ou processo), mediante um raciocínio basicamente dedutivo (não exige cálculos sofisticados). É, portanto, um método analítico padronizado para detectar e eliminar problemas potenciais de forma sistemática e completa.
O manual complementar FMEA da QS9000 descreve como um grupo sistemático de atividades, comprometidos com:
5.3.1 Implantação do FMEA
Uma das dificuldades encontradas na elaboração da FMEA reside no fato de que o grupo não possuir uma base histórica de manutenção do equipamento para uma avaliação mais objetiva. Com isso, torna-se difícil a determinação dos índices de ocorrência e detecção.
3 - Análises de Suas Funções Principais
4 - Identificações dos Modos de Falha e seus Efeitos
5 - Identificações das Causas das Falhas
6 - Identificações dos Controles Atuais de Detecção das Falhas
7 - Determinações dos Índices de NPR ( Nº de prioridade de risco )
8 - Análises das Recomendações
9 – Ações tomadas
10 – Implantações das Ações ao Plano de Manutenção
Figura 5.1 - Fluxo para elaboração da FMEA
5.3.2 Formulário usado para o FMEA
Formulário utilizado foi o de padrão da aula de planejamento de manutenção, administrado pelo professor Geraldo Reis da instituição de ensino SOCIESC
Figura 5.2 – Formulário de FMEA
6 Criticidade
6.1 ÍNDICES de risco NPR
O Objetivo deste índice e criar as prioridades que serão dadas as tarefas de preventivas, preditivas e check-list do plano de manutenção aplicada ao projeto. O calculo do NPR (número de prioridade de risco) será obtido pela multiplicação dos índices de severidade, ocorrência e detecção. Figura 3.
Quadro 6.1 – Índice de Severidade