
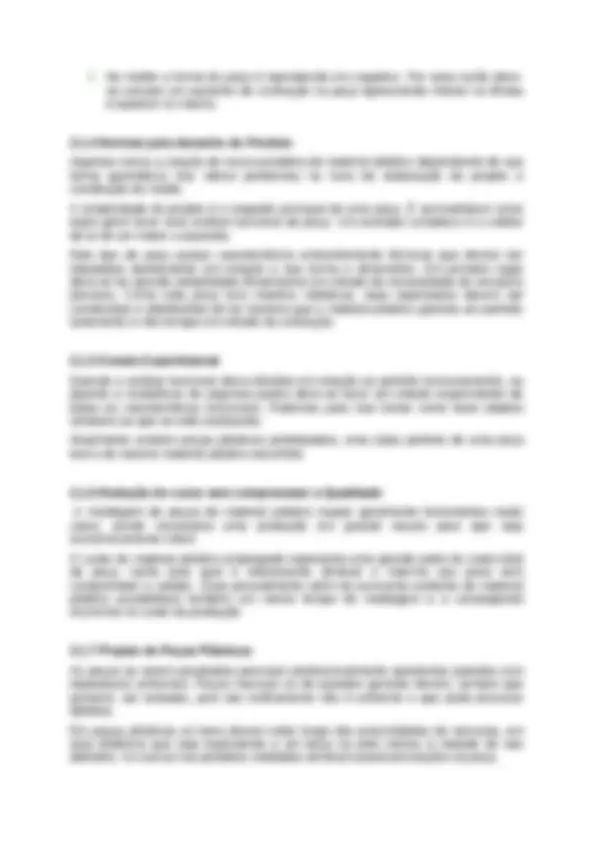
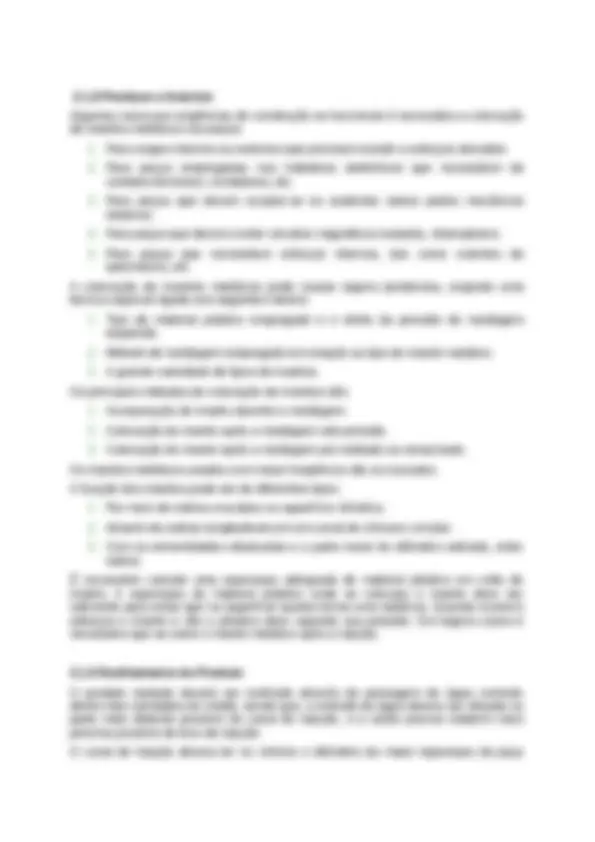
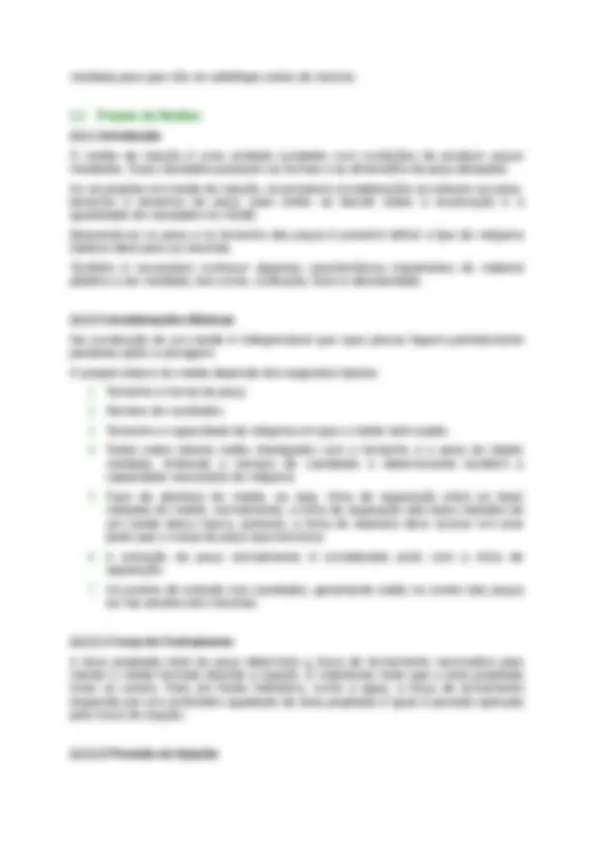
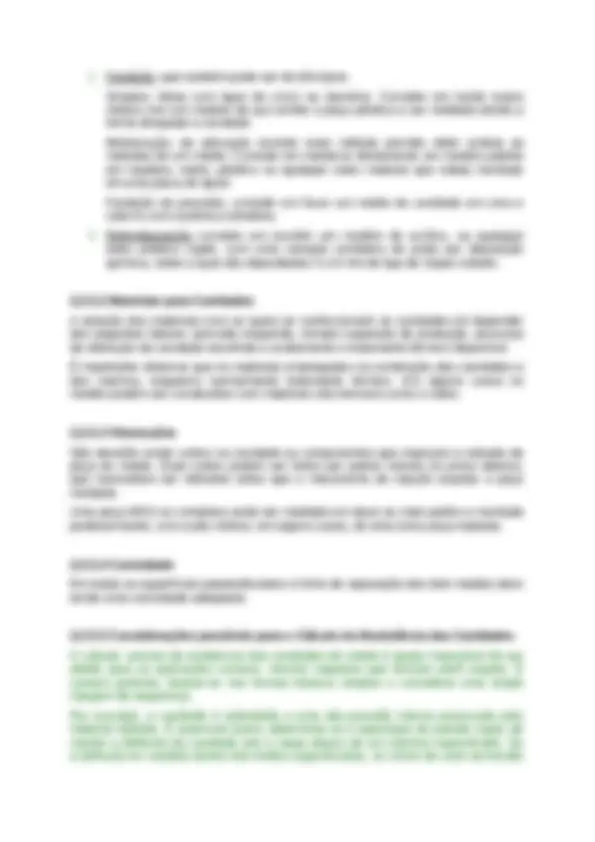
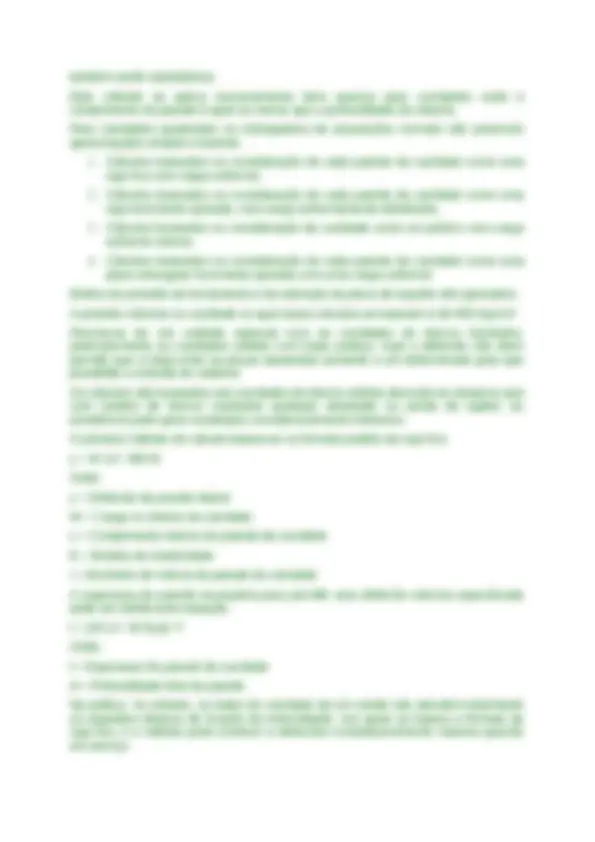
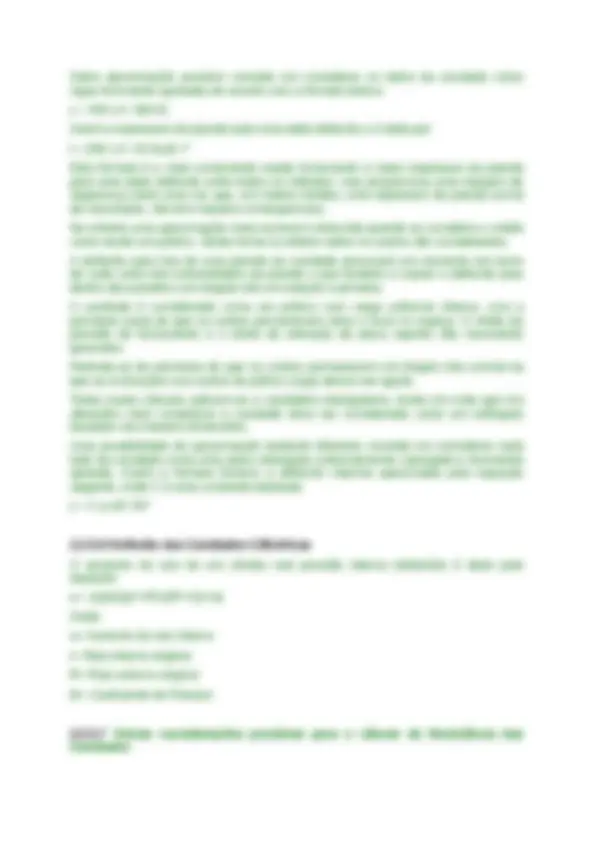
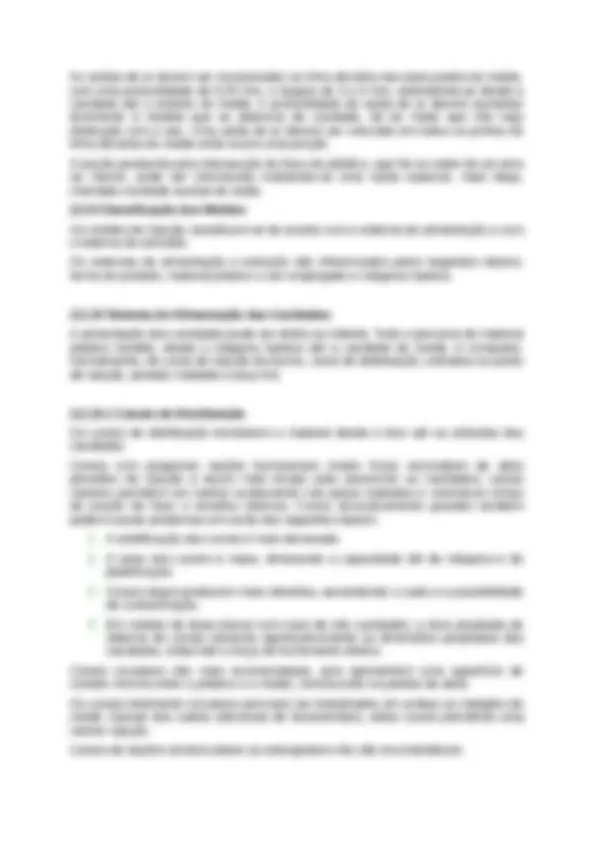
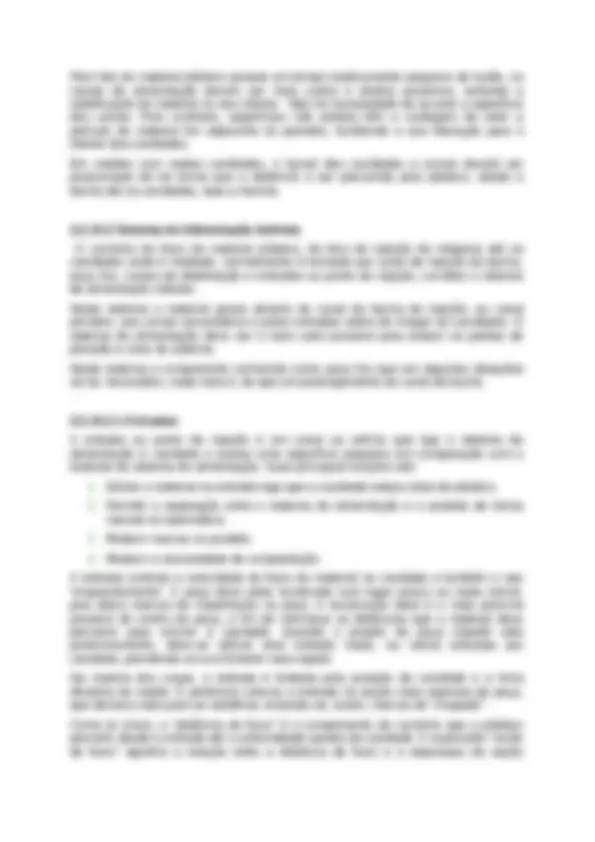
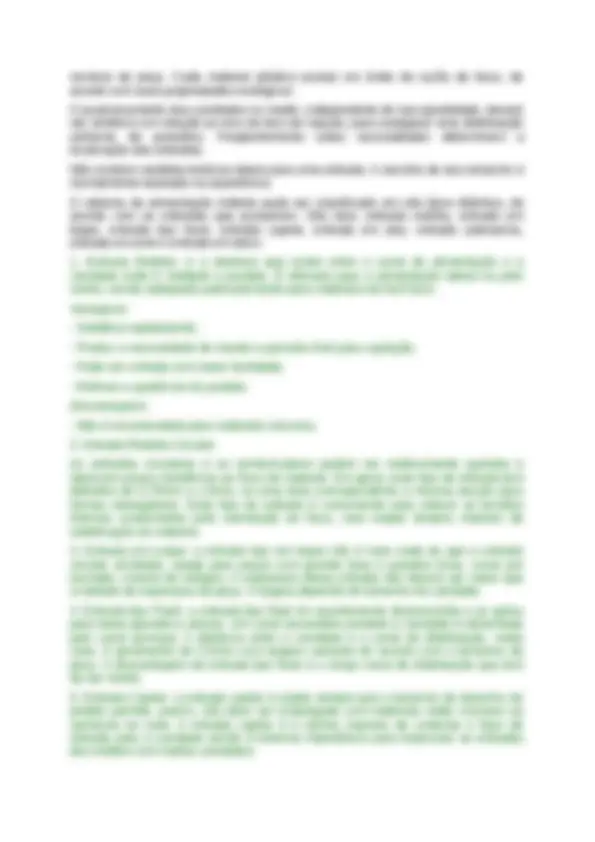
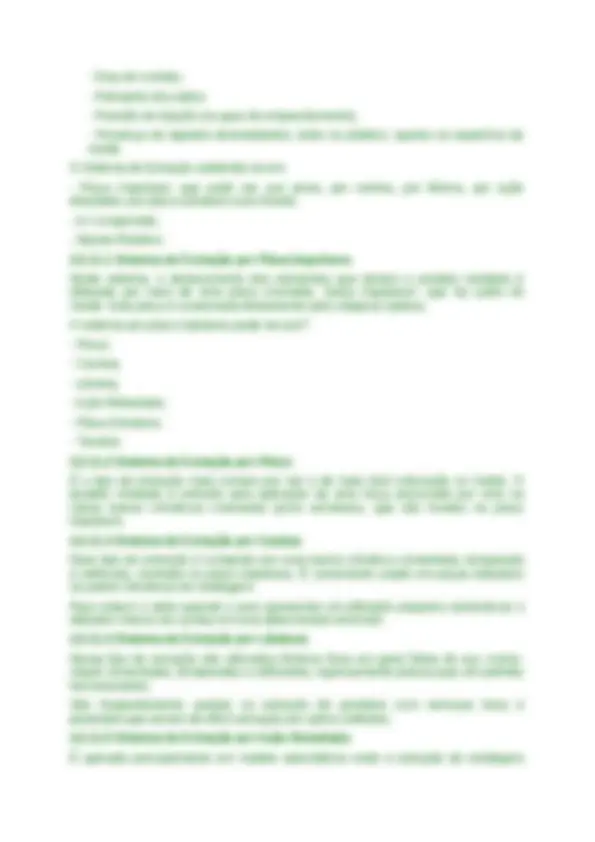
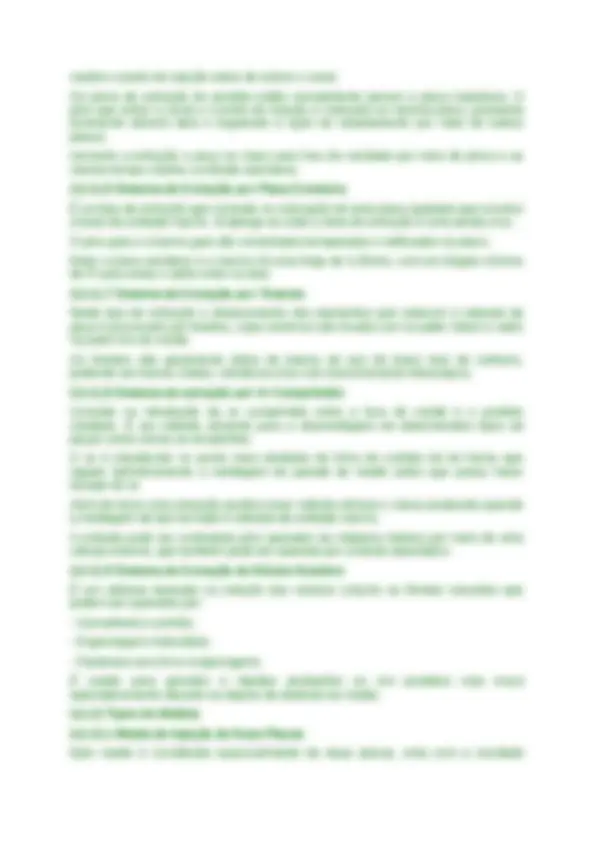
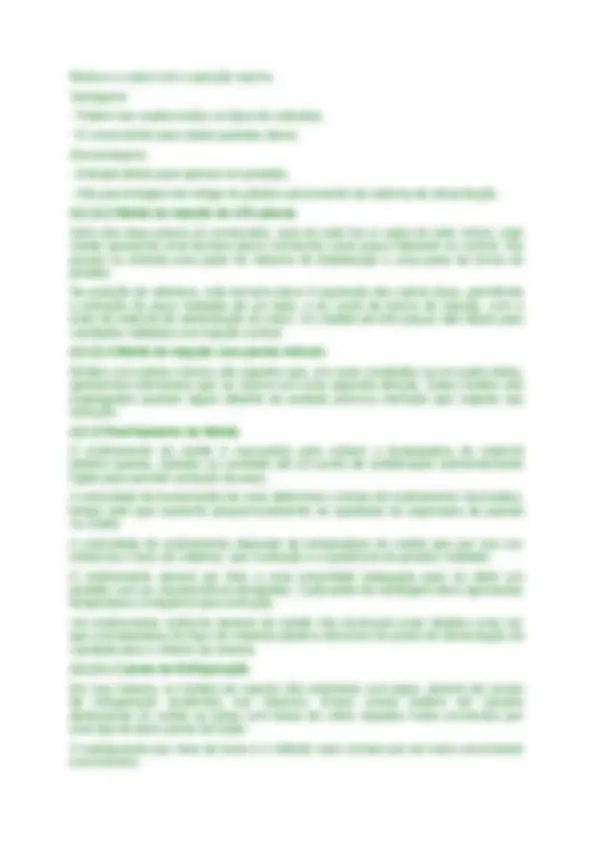
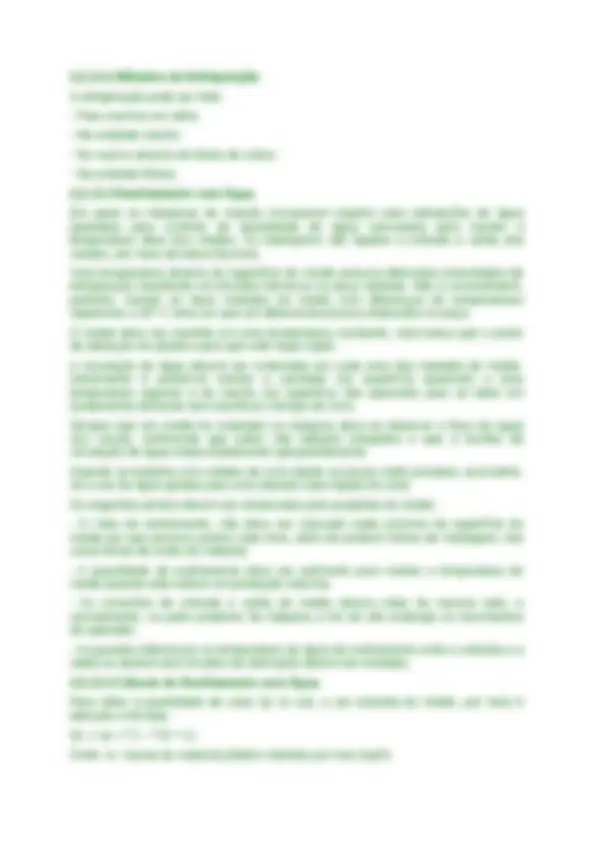
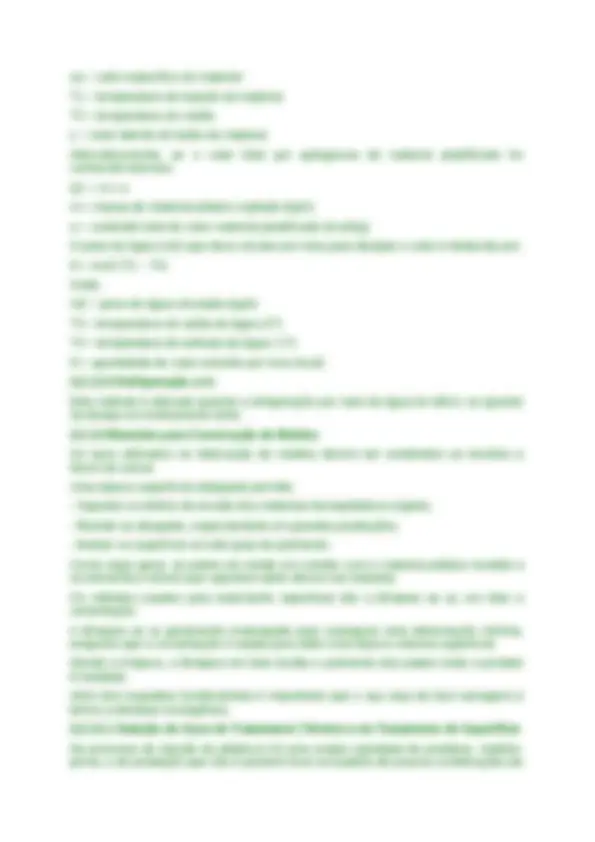
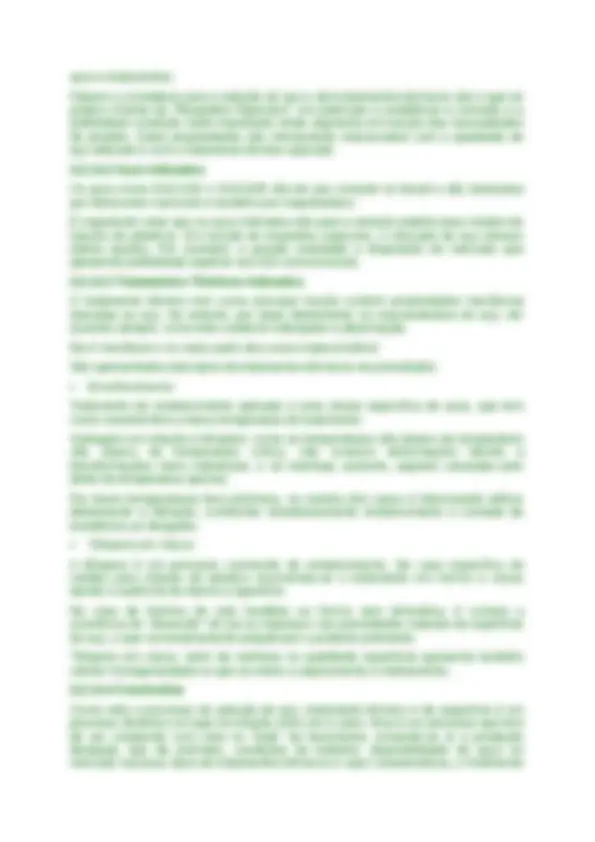
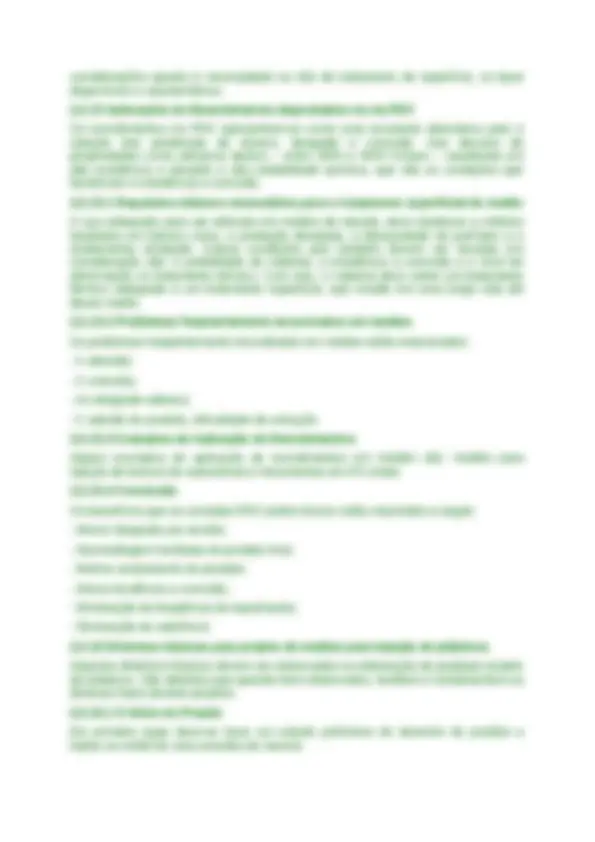
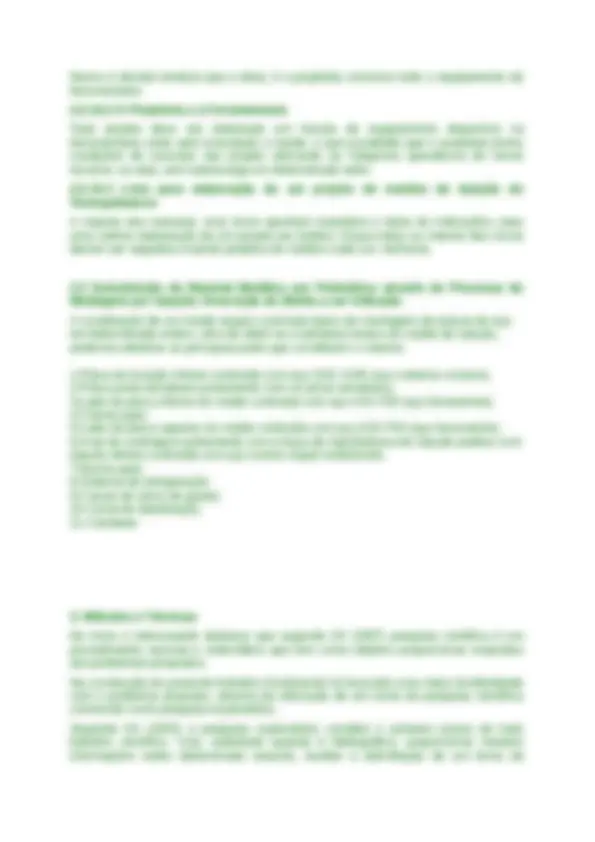
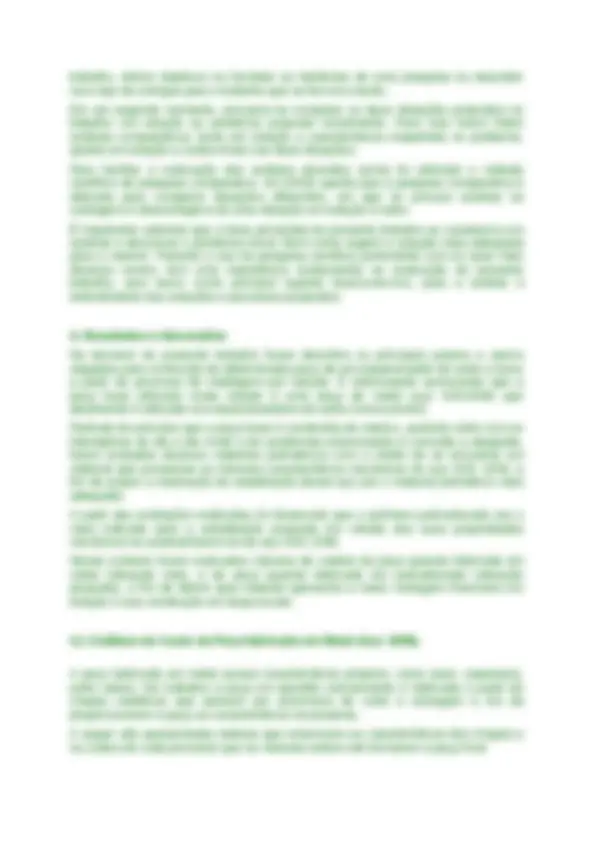
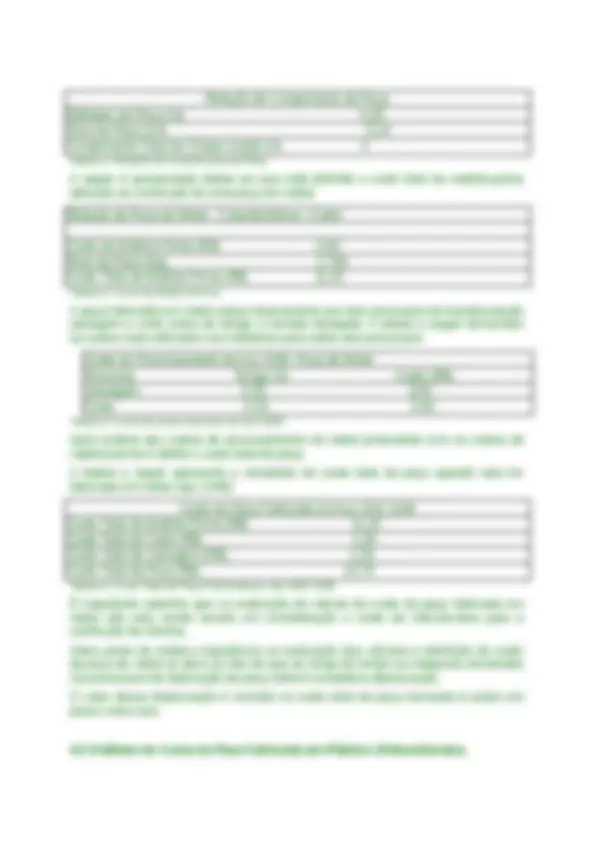
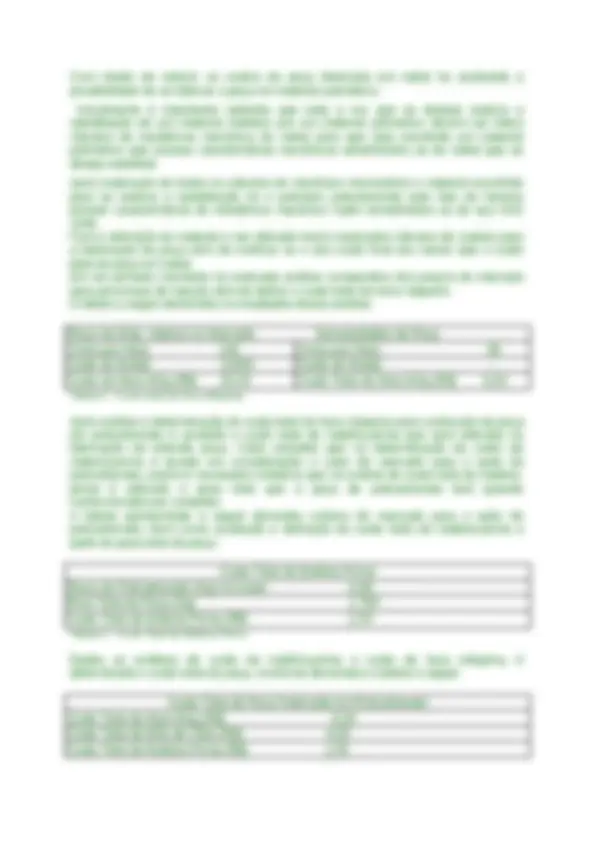
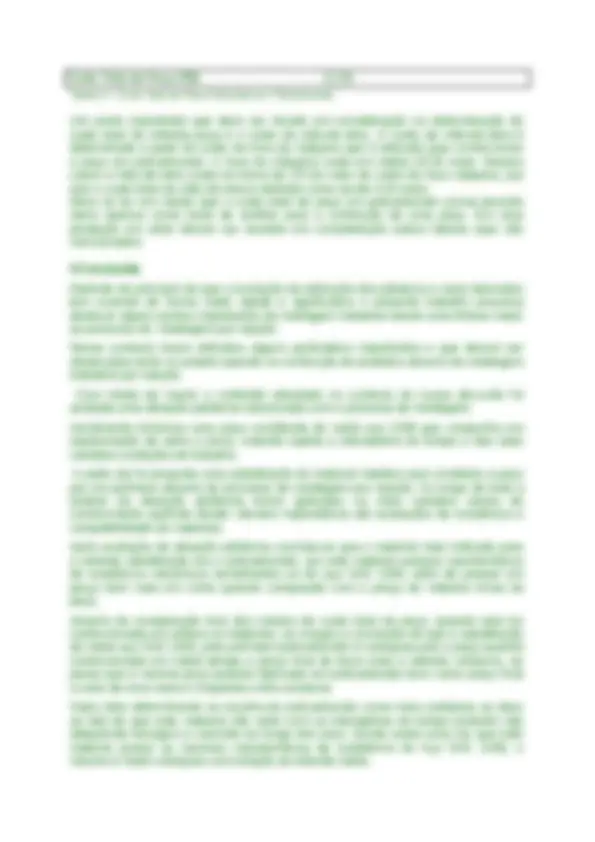
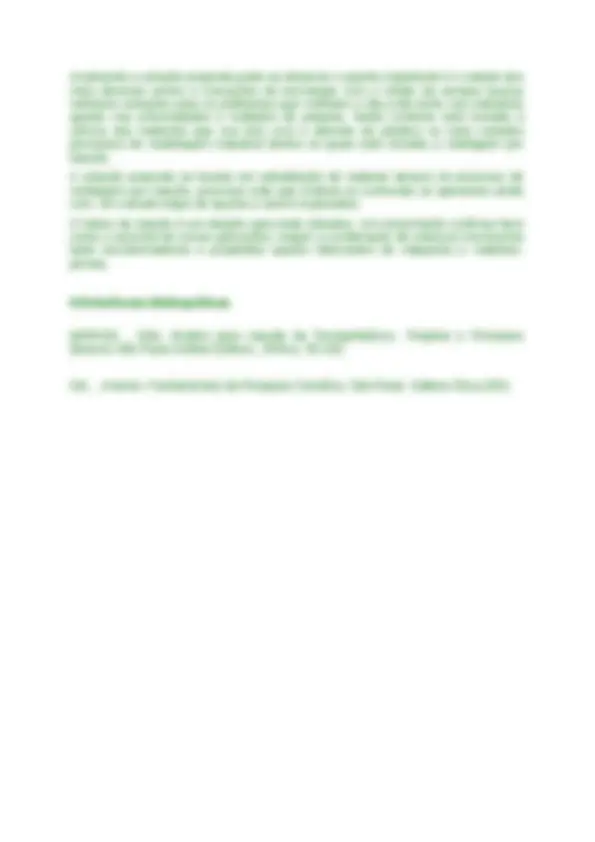
Estude fácil! Tem muito documento disponível na Docsity
Ganhe pontos ajudando outros esrudantes ou compre um plano Premium
Prepare-se para as provas
Estude fácil! Tem muito documento disponível na Docsity
Prepare-se para as provas com trabalhos de outros alunos como você, aqui na Docsity
Os melhores documentos à venda: Trabalhos de alunos formados
Prepare-se com as videoaulas e exercícios resolvidos criados a partir da grade da sua Universidade
Responda perguntas de provas passadas e avalie sua preparação.
Ganhe pontos para baixar
Ganhe pontos ajudando outros esrudantes ou compre um plano Premium
Comunidade
Peça ajuda à comunidade e tire suas dúvidas relacionadas ao estudo
Descubra as melhores universidades em seu país de acordo com os usuários da Docsity
Guias grátis
Baixe gratuitamente nossos guias de estudo, métodos para diminuir a ansiedade, dicas de TCC preparadas pelos professores da Docsity
O presente trabalho visa descrever alguns parâmetros básicos e técnicos para o desenvolvimento tanto de projetos quanto de peças produzidas apartir de moldes, bem como, demonstrar através de um estudo a substituição de metal por polímero, através de um molde de injeção, em de parte de um equipamento agrícola chamado esparamador de uréia a lance.
Tipologia: Notas de estudo
1 / 30
Esta página não é visível na pré-visualização
Não perca as partes importantes!
Eduardo Bortolin (FAHOR) eb000867@fahor.com.br
Everton Freddi (FAHOR) ef000909@fahor.com.br
João Guilherme Weiller (FAHOR) jw000868@fahor.com.br
Leandro Vianna Fernandes (FAHOR) lf000809@fahor.com.br
Resumo
No contexto atual a evolução tecnológica esta cada vez mais presente tanto no campo quanto na cidade. Um dos processos industrais em que ocorreu uma cresente e continua evolução aos longos dos anos foi à moldagem industrial. Apartir disso o presente trabalho visa demonstrar alguns parâmetros importantes deste processo desde o projeto até a confecção de moldes. Na mesma linha de ação o presente trabalho irá fazer uma descrição desse processo através de um projeto de produto, onde será feita a substituição de material metálico, por material polimérico, em um equipamento agrícola chamado esparamador de uréia a lance, visando assim avaliar as possíveis vantagens econômicas da utilização dos processos de moldagem, na confecção deste equipamento agrícola.
Palavras chave : Moldagem, Equipamento Agrícola, Polímeros, Substituição de Materiais.
1. Introdução
Na década de 1940 a utilização de peças injetadas de material plástico restringia-se a alguns produtos de no máximo alguns poucos gramas. Com o cresimento do mercado desses produtos devido a sua alta aplicabilidade houve ao longo dos anos uma constante evolução, tanto que atualmente, temos moldes com áreas projetadas de até 1m², e peças plásticas produzidas apartir de moldes pesando até 20 kg.
Em paralelo a essa evolução que ocorreu no processo de moldagem industrial a agricultura brasileira também passava por um período de mudanças. Nesse período houve um enorme advento de novas tecnologias, e novos modelos de máquinas agricola no país. Na sua grande maioria essas máquinas eram quase que totalmente compostas de metal e aço. Porém hoje em dia, em virtude de questões financeiras, cada vez mais se trabalha em busca de novas alternativas de materiais que possam substituir os metais, e ao mesmo tempo fazer com que o equipamento agrícola não seja prejudicado em virtude disso.
Apartir da análise dessas considerações, o presente trabalho visa descrever alguns parâmetros básicos e técnicos para o desenvolvimento tanto de projetos quanto de peças produzidas apartir de moldes, bem como, demonstrar através de um estudo a substituição de metal por polímero, através de um molde de injeção, em de parte de um equipamento agrícola chamado esparamador de uréia a lance.
2. Revisão da Literatura
2.1 Projeto de Produtos
2.1.1 Introdução
Para se obter um bom desempenho da peça, evitando-se inconveniências posteriores que provoquem um aumento de custo, é necessário que os seguintes fatores sejam analisados:
2.1.2 Características Técnicas e Aparência do Produto
Há produtos normalmente utilizados em eletroeletrônica, que requerem somente características técnicas, aplicações mecânicas e conjuntos de peças não visíveis, não exigindo, portanto maiores preocupações com a aparência.
Por outro lado existem produtos que não necessitam de dimensões rígidas, mas cuja aparência é bastante importante, tais como, brinquedos, utilidades domésticas, adornos, etc.
2.1.3 Desenho de Produto e Desenho de Molde
Considerando que o molde é a ferramenta que dará as dimensões e a forma do produto faz-se necessário um estudo criterioso das dimensões das cavidades, levando em consideração a contração do material a ser utilizado.
2.1.3.1 Contração
Na produção de peças de material plástico a contração é muito importante devendo ser atentamente considerada, pois refletirá nas dimensões do produto moldado, além de influir sobre os seguintes itens:
2.1.8 Postiços e Insertos
Algumas vezes por exigências de construção ou funcionais é necessária a colocação de insertos metálicos nas peças:
A colocação de insertos metálicos pode causar alguns problemas, exigindo uma técnica especial ligada aos seguintes fatores:
Os principais métodos de colocação de insertos são:
Os insertos metálicos usados com maior freqüência são os roscados.
A fixação dos insertos pode ser de diferentes tipos:
É necessário calcular uma espessura adequada de material plástico em volta do inserto. A espessura do material plástico onde se colocara o inserto deve ser suficiente para evitar que na superfície oposta forme uma saliência. Quando ocorrem esforços o inserto e não o plástico deve suportar sua pressão. Em alguns casos é necessário que se usine o inserto metálico após a injeção.
2.1.9 Resfriamento do Produto
O produto injetado deverá ser resfriado através da passagem de água corrente dentro das cavidades do molde, sendo que, a entrada da água devera ser situada na parte mais distante possível do canal de injeção, e a saída precisa estarem mais próxima possível do bico de injeção.
O canal de injeção devera ter no mínimo o diâmetro da maior espessura da peça
moldada para que não se solidifique antes da mesma.
2.2 Projeto de Moldes
2.2.1 Introdução
O molde da injeção é uma unidade completa com condições de produzir peças moldadas. Suas cavidades possuem as formas e as dimensões da peça desejada.
Ao se projetar um molde de injeção, as primeiras considerações se referem ao peso, tamanho e desenho da peça, para então se decidir sobre a localização e a quantidade de cavidades no molde.
Baseando-se no peso e no tamanho das peças é possível definir o tipo de máquina injetora ideal para as mesmas.
Também é necessário conhecer algumas características importantes do material plástico a ser moldado, tais como, contração, fluxo e abrasividade.
2.2.2 Considerações Básicas
Na construção de um molde é indispensável que suas placas fiquem perfeitamente paralelas após a usinagem.
O projeto básico do molde depende dos seguintes fatores:
2.2.2.1 Força de Fechamento
A área projetada total da peça determina a força de fechamento necessária para manter o molde fechado durante a injeção. É importante notar que a área projetada inclui os canais. Para um fluído hidráulico, como a água, a força de fechamento requerida por um centímetro quadrado da área projetada é igual à pressão aplicada pela rosca de injeção.
2.2.2.2 Pressão de Injeção
do gás e do ar precisam ser bem observadas para que a peça possua a qualidade adequada.
2.2.4 Bucha de Injeção
Também chamada de bucha do canal de injeção, é um componente do molde através do qual o fluxo de material plástico procedente da máquina injetora penetra até as cavidades do molde.
O canal de injeção do molde é afunilado. O afunilamento padrão é 10 mm por 300 mm. O orifício da bucha do molde deve ter no mínimo três mm de diâmetro, com um comprimento menor possível.
Na injeção com cavidade única, o diâmetro do canal de injeção na entrada da cavidade deverá ser de aproximadamente o dobro da espessura da peça. Se for pequeno poderá ocorrer delaminação do material ou calor excessivo nesse ponto. Um diâmetro muito grande por sua vez requer um ciclo maior para permitir a solidificação do canal de injeção.
2.2.4.1 Características da Bucha
Ela é feita de aço cromo-níquel, constituída de um assento esférico, ou em ângulo, onde é alojado o bico do cilindro de injeção.
O furo da bucha que forma o canal de injeção é quase sempre redondo, polido, e cônico, para facilitar o fluxo de material e a extração do canal. A conicidade varia entre 2º a 5º.
2.2.4.2 Dimensões
O comprimento da bucha de injeção deve ser o mais curto possível para que o resfriamento seja rápido e os ciclos de injeção curtos.
Geralmente o comprimento da bucha é de 5 a 10 vezes o do diâmetro, o que permite um bom rendimento.
2.2.5 Cavidades
2.2.5.1 Introdução
A cavidade de moldagem é normalmente composta por duas partes: a unidade fêmea que modela a parte externa da peça, e o núcleo ou unidade macho, que configura sua parte interna.
A cavidade pode ser obtida por:
Simples; feitas com ligas de zinco ou alumínio. Consiste em fundir esses metais com um modelo de aço similar a peça plástica a ser moldada dando a forma desejada a cavidade.
Metalização; de utilização recente esse método permite obter ambas as metades de um molde. Consiste em metalizar diretamente um modelo padrão em madeira, metal, plástico ou qualquer outro material que esteja montado em uma placa de apoio.
Fundição de precisão; consiste em fazer um molde da cavidade em cera e cobri-lo com cerâmica refratária.
2.2.5.2 Materiais para Cavidades
A seleção dos materiais com os quais se confeccionará as cavidades irá depender dos seguintes fatores: precisão requerida, número esperado de produção, processo de obtenção da cavidade escolhida e acabamento e tratamento térmico disponível.
É importante observar que os materiais empregados na construção das cavidades e dos machos, requerem normalmente tratamento térmico. Em alguns casos os moldes podem ser construídos com materiais não-ferrosos como o cobre.
2.2.5.3 Obstruções
Não deverão existir cortes na cavidade ou componentes que impeçam a retirada da peça do molde. Esse cortes podem ser feitos por partes móveis ou pinos laterais, que necessitam ser retirados antes que o mecanismo de injeção expulse a peça moldada.
Uma peça difícil ou complexa pode ser moldada em duas ou mais partes e montada posteriormente, com custo inferior, em alguns casos, de uma única peça injetada.
2.2.5.4 Conicidade
Em todas as superfícies perpendiculares á linha de separação dos dois moldes deve existir uma conicidade adequada.
2.2.5.5 Considerações possíveis para o Cálculo da Resistência das Cavidades
O cálculo preciso da resistencia das cavidades do molde é quase impossível de ser obtido para as aplicações comuns, mesmo naquelas que tenham perfil regular. É comum portanto, basear-se nas formas básicas simples e considerar uma ampla margem de segurança.
Por exemplo, a cavidade é submetida a uma alta pressão interna provocada pelo material injetado. É essencial assim, determinar-se a espessura da parede capaz de manter a deflexão da cavidade sob a carga abaixo de um máximo especificado. Se a deflexão for mantida dentro dos limites especificados, os níveis de calor da tensão
Outra aproximação possível consiste em considerar os lados da cavidade como vigas livremente apoiadas de acordo com a fórmula básica: y = 5W L4 / 384 EI Assim a espessura da parede para uma dada deflexão y é dada por:
t = [5W L4 / 32 Eyd] ¹/³ Esta fórmula é a mais comumente usada fornecendo a maior espessura da parede para uma dada deflexão entre todos os métodos. Isso proporciona uma margem de segurança maior uma vez que, em muitos moldes, uma espessura da parede acima da necessária, não tem maiores consequencias. No entanto uma aproximação mais racional é oferecida quando se considera o molde como sendo um pórtico. Desta forma os efeitos sobre os cantos são considerados. A deflexão para fora de uma parede da cavidade provocará um momento em torno de cada canto das extremidades da parede o que tenderá a causar a deflexão para dentro das paredes com ângulo reto em relação a primeira. A cavidade é considerada como um pórtico com carga uniforme interna, com a premissa usual de que os cantos permanecem retos e fixos no espaço. O efeito da pressão de fechamento e o efeito de retenção da placa suporte são novamente ignorados. Partindo-se da premissa de que os cantos permanecem em ângulo reto conclui-se que as inclinações nos cantos do pórtico (viga) devem ser iguais. Todos esses cálculos aplicam-se a cavidades retangulares, tendo em vista que em situações mais complexas a cavidade deve ser considerada como um retângulo baseado nas maiores dimensões. Uma possibilidade de aproximação bastante diferente consiste em considerar cada lado da cavidade como uma placa retangular uniformemente carregada e livremente apoiada. Assim a fórmula fornece a deflexão máxima aproximada pela equação seguinte, onde C é uma constante tabelada: y = C p d4 / Et³
2.2.5.6 Deflexão das Cavidades Cilíndricas
O aumento do raio de um cilindro sob pressão interna (deflexão) é dado pela equação: u = {(rp/E)[(r²+R²)/(R²-r²)]+m}
Onde: u= Aumento do raio interno
r= Raio interno original R= Raio externo original
M= Coeficiente de Poisson
2.2.5.7 Outras considerações possíveis para o cálculo de Resistência das Cavidades
As dimensões das paredes das cavidadesdevem ser calculadas para oferecer resistência contra a força de fechamento do molde e da pressão de injeção do material plastificado no interior da cavidade.
A linha de abertura do molde está sujeita a impactos repetitivos pela ação de fechamento da máquina injetora. Se a pressão de injeção for baixa para injetar determinadas peças isso poderá ser desprezado. Mas para evitar tais problemas é necessário calcular adequadamente a força de fechamento, selecionar o material para confecção do molde para resistir a tensão de compressão (tração), e calcular a respectiva área de contato na linha de abertura do molde.
Para determinar a força de fechamento para o molde deve-se multiplicar a área projetada da moldagem pela pressão de injeção ou algo equivalente.
A pressão de injeção depende de vários fatores, como fluidez do material, temperatura de plastificação, temperatura do molde, entre outros.
Como regra bastante prática e próxima pode-se dar um valor médio de pressão de injeção de 300 a 1100 Kg/cm².
2.2.5.8 Dimensionamento do tamanho e do material para base de Molde
O tamanho da base do molde é determinado por colocação das cavidades, sistema de alimentação das cavidades, sistema de extração utilizado, sistema de controle da temperatura, sistema de acionamento de engrenagens (quando utilizado), colunas, buchas, guias ou dispositivo específicopara os moldes.
Depois de calculada a dimensão necessária do molde, é preciso acrescentar a largura e o comprimento final deste, para a fixação. Com as dimensões finais verifica-se a disponibilidade de bases padronizadas e se satisfazem as condições de layout das cavidades.
2.2.5.9 Dimensionamento dos Calços
De uma maneira geral, na construção de moldes, os calços formam um U para o sistema de ejeção das peças. A pressão de injeção pode causar deflexão nas placas suportes das cavidades suportadas pelos calços. Além disso, essa deflexão causará rebarbas nos produtos. Para evitar esse problema, são colocados alguns suportes em locais estratégicos que não interfiram com os pinos de extração e retorno. Para determinação dos calços e suas distâncias, a fórmula de viga bi-apoiada pode ser adotada.
2.2.5.10 Alinhamento das duas metades de um Molde
A colocação da bucha guia com a coluna guia de um molde permite um desalinhamento máximo de 0,006 cm e um mínimo de 0,004 cm.
Na pratica essas tolerâncias são menores, e podem ser medidas, dependendo do caso, pela colocação de cada metade do molde em posição fixa, e movimentando a outra metade contra um relógio comparador. Mesmo que os cálculos sobre o desalinhamento possam estar dentro da tolerância requerida, é indicado incorporar outros recursos para assegurar o alinhamento.
As saídas de ar devem ser incorporadas na linha divisória das duas partes do molde, com uma profundidade de 0,05 mm, e largura de 3 a 6 mm, estendendo-se desde a cavidade até o exterior do molde. A profundidade de saída de ar deverá aumentar levemente á medida que se distancia da cavidade, de tal modo que não haja obstrução com o uso. Uma saída de ar deverá ser colocada em todos os pontos da linha divisória do molde onde ocorra uma junção.
A junção produzida pela intersecção do fluxo do plástico, que flui ao redor de um pino ou macho, pode ser minimizada instalando-se uma saída especial, mais larga, chamada cavidade auxiliar de solda.
2.2.9 Classificação dos Moldes
Os moldes de injeção classificam-se de acordo com o sistema de alimentação e com o sistema de extrusão.
Os sistemas de alimentação e extração são influenciados pelos seguintes fatores: forma do produto, material plástico a ser empregado e máquina injetora.
2.2.10 Sistema de Alimentação das Cavidades
A alimentação das cavidades pode ser direta ou indireta. Todo o percurso do material plástico fundido, desde a máquina injetora até a cavidade do molde, é composto, normalmente, de canal de injeção da bucha, canal de distribuição, entradas ou ponto de injeção, produto moldado e poço frio
2.2.10.1 Canais de Distribuição
Os canais de distribuição transferem o material desde o bico até as entradas das cavidades.
Canais com pequenas seções transversais (muito finos) necessitam de altas pressões de injeção e levam mais tempo para preencher as cavidades; canais maiores permitem um melhor acabamento nas peças injetadas e minimizam linhas de junção de fluxo e tensões internas. Canas excessivamente grandes também podem causar problemas em razão dos seguintes fatores:
Canais circulares são mais recomendados, pois apresentam uma superfície de contato mínima entre o plástico e o molde, minimizando as perdas de atrito.
Os canais totalmente circulares precisam ser trabalhados em ambas as metades do molde. Apesar dos custos adicionais de ferramentaria, estes canais permitirão uma melhor injeção.
Canais de seções semicirculares ou retangulares não são recomendáveis.
Pelo fato do material plástico possuir um tempo relativamente pequeno de fusão, os canais de alimentação devem ser mais curtos e diretos possíveis, evitando a solidificação do material no seu interior. Não há necessidade de se polir a superfície dos canais. Pelo contrário, superfícies não polidas têm a vantagem de reter a película do material frio adjacente ás paredes, facilitando a sua liberação para o interior das cavidades.
Em moldes com muitas cavidades, o layout das cavidades e canais deverá ser posicionado de tal forma que a distância a ser percorrida pelo plástico, desde a bucha até as cavidades, seja a mesma.
2.2.10.2 Sistema de Alimentação Indireta
O caminho do fluxo do material plástico, do bico de injeção da máquina até as cavidades onde é moldado, normalmente é formado por canal de injeção da bucha, poço frio, canais de distribuição e entradas ou ponto de injeção, constitui o sistema de alimentação indireta.
Neste sistema o material passa através do canal da bucha de injeção, ao canal primário, aos canais secundários e pelas entradas antes de chegar às cavidades. O sistema de alimentação deve ser o mais curto possível para reduzir as perdas de pressão e calor do sistema.
Neste sistema o componente conhecido como poço frio que em algumas situações se faz necessário, nada mais é, de que um prolongamento do canal da bucha.
.
2.2.10.2.1 Entradas
A entrada ou ponto de injeção é um canal ou orifício que liga o sistema de alimentação à cavidade e possui uma superfície pequena em comparação com o restante do sistema de alimentação. Suas principais funções são:
A entrada controla a velocidade do fluxo do material na cavidade e também o seu “empacotamento”. A peça deve estar localizada num lugar pouco ou nada visível, pois deixa marcas de imperfeição na peça. A localização ideal é o mais próximo possível do centro da peça, a fim de minimizar as distâncias que o material deve percorrer para encher a cavidade. Quando o projeto da peça impedir este posicionamento, deve-se utilizar uma entrada maior, ou várias entradas por cavidade, permitindo um enchimento mais rápido.
Na maioria dos casos, a entrada é limitada pela posição da cavidade e a linha divisória do molde. É preferível colocar a entrada na seção mais espessa da peça, que demora mais para se solidificar, evitando-se, assim, marcas de “chupado”.
Como já vimos, a “distância de fluxo” é o comprimento do caminho que o plástico percorre desde a entrada até a extremidade oposta da cavidade. A expressão “razão de fluxo” significa a relação entre a distância de fluxo e a espessura da seção
Devido as suas pequenas dimensões, a entrada capilar se solidifica rapidamente permitindo ciclos curtos de tensões reduzidas.
A principal desvantagem é que, quanto maior a entrada mais veloz se tornará o fluxo do plástico fazendo com que parte da energia cinética seja convertida em calor e, e casos extremos causando queima ou degradação do material.
2.2.10.2 Sistema de Alimentação Direta
Neste sistema o material plástico flui diretamente do canal da bucha de injeção para a cavidade. É classificado de acordo com os tipos de entrada de injeção que podem ser:
Esse sistema é utilizado em moldas de injeção para moldagem de produtos simples, com alta escala de produção, onde o funcionamento automático do molde livra o produto do sistema de alimentação.
2.2.10.3 Injeção com Sistema de Câmara Quente
O que é câmara quente: é um conjunto de elementos eletromecânicos que, quando
instalados em moldes de injeção de termoplásticos, mantém em seu interior o canal de injeção em estado plástico de fusão controlada.
Vantagens da utilização dos Sistemas de Câmara Quente:
Há uma grande melhoria no processo de injeção pelos seguintes pontos:
cisalha o ponto de injeção antes de extrair o canal.
Os pinos de extração do produto estão normalmente presos a placa impulsora. O pino que extrai o canal e o ponto de injeção é colocado na mesma placa, passando livremente através dela e regulando a ação de retardamento por meio de outras placas.
Iniciando a extração a peça se move para fora da cavidade por meio de pinos e ao mesmo tempo cisalha a entrada submersa.
2.2.11.6 Sistema de Extração por Placa Extratora
É um tipo de extração que consiste na colocação de uma placa ajustada que envolve a base da unidade-macho. Emprega-se onde a área de extração é uma aresta viva.
O pino guia e a bucha guia são cementados temperados e retificados na placa.
Entre a placa extratora e o macho há uma folga de 0,25mm, com um ângulo mínimo de 5º para evitar o atrito entre os dois.
2.2.11.7 Sistema de Extração por Tirantes
Neste tipo de extração o deslocamento dos elementos que realizam a retirada da peça é provocado por tirantes, cujos externos são fixados um na parte móvel e outro na parte fixa do molde.
Os tirantes são geralmente feitos de barras de aço de baixo teor de carbono, podendo ser barras chatas, cilíndricas e/ou com funcionamento telescópico.
2.2.11.8 Sistema de extração por Ar Comprimido
Consiste na introdução de ar comprimido entre a face do molde e o produto moldado. É um método eficiente para a desmoldagem de determinados tipos de peças como caixas ou recipientes.
O ar é introduzido no ponto mais afastado da linha de contato de tal forma que separe definitivamente a moldagem da parede do molde antes que possa haver escape do ar.
Além de fazer uma extração positiva esse método elimina o vácuo produzido quando a moldagem de tipo fechado é retirada da unidade macho.
A entrada pode ser controlada pelo operador da máquina injetora por meio de uma válvula externa, que também pode ser operada por controle automático.
2.2.11.9 Sistema de Extração de Núcleo Rotativo
É um sistema baseado na rotação dos núcleos (macho ou fêmea) roscados que podem ser operados por:
É usado para grandes e rápidas produções ou em produtos cuja rosca automaticamente durante ou depois da abertura do molde.
2.2.12 Tipos de Moldes
2.2.12.1 Molde de Injeção de Duas Placas
Este molde é constituído essencialmente de duas placas, uma com a cavidade
fêmea e a outra com o punção macho.
Vantagens:
Desvantagens:
2.2.12.2 Molde de injeção de três placas
Além das duas placas já conhecidas, uma do lado fixo e outra do lado móvel, este molde apresenta uma terceira placa conhecida como placa flutuante ou central. Ela possui na entrada uma parte do sistema de distribuição e uma parte da forma do produto.
Na posição de abertura, esta terceira placa é separada das outras duas, permitindo a extração da peça moldada de um lado, e do canal da bucha de injeção, com o resto do sistema de alimentação do outro. Os moldes de três placas são ideais para cavidades múltiplas com injeção central.
2.2.12.3 Molde de injeção com partes móveis
Moldes com partes móveis são aqueles que, em suas cavidades ou em parte delas, apresentam elementos que se movem em uma segunda direção. Estes moldes são empregados quando algum detalhe do produto provoca retenção que impede sua extração.
2.2.13 Resfriamento do Molde
O resfriamento do molde é necessário para reduzir a temperatura do material plástico quente, injetado na cavidade até um ponto de solidificação suficientemente rígido para permitir extração da peça.
A velocidade de transmissão de calor determina o tempo de resfriamento necessário, tempo este que aumenta proporcionalmente ao quadrado da espessura da parede no molde.
A velocidade do resfriamento depende da temperatura do molde que por sua vez influencia o fluxo do material, sua contração e a aparência do produto moldado.
O resfriamento deverá ser feito a uma velocidade adequada para se obter um produto com as características desejadas. Cada parte da moldagem deve apresentar temperatura compatível para extração.
Um resfriamento uniforme através do molde não alcançará esse objetivo uma vez que a temperatura do fluxo do material plástico decresce do ponto de alimentação da cavidade para o interior da mesma.
2.2.13.1 Canais de Refrigeração
Em sua maioria, os moldes de injeção são resfriados com água, através de canais de refrigeração existentes nos mesmos. Esses canais podem ser furados diretamente no molde ou feitas com tubos de cobre alojados neste envolvidos por uma liga de baixo ponto de fusão.
O resfriamento por meio de furos é o método mais comum por ser mais conveniente e econômico.