
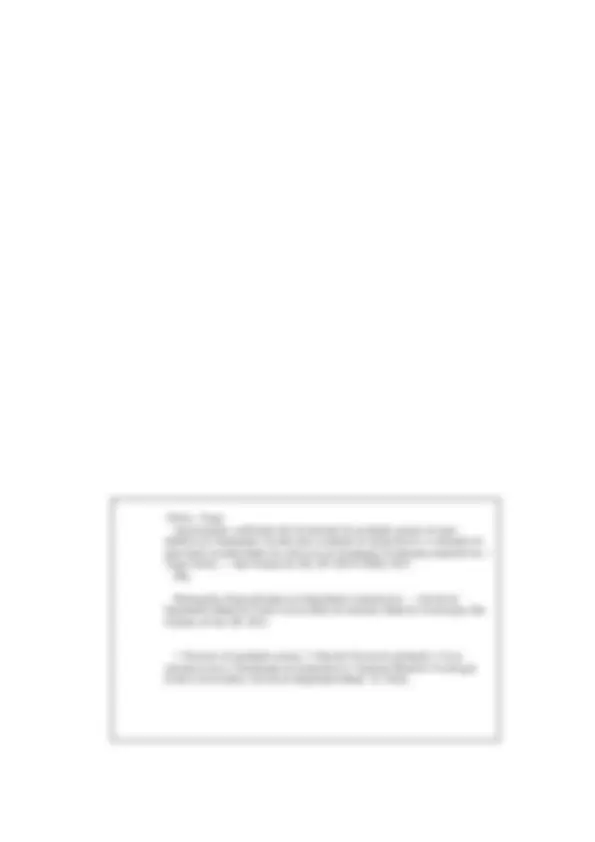
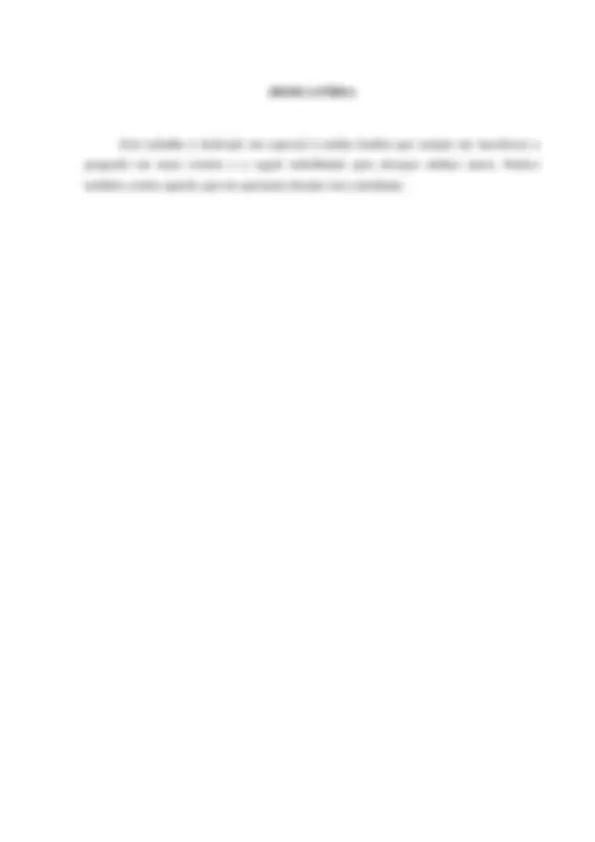
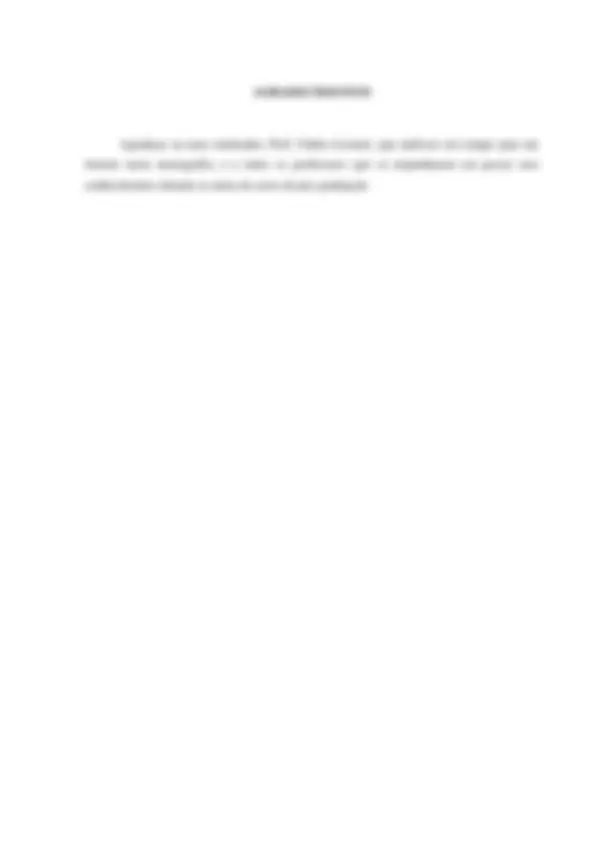
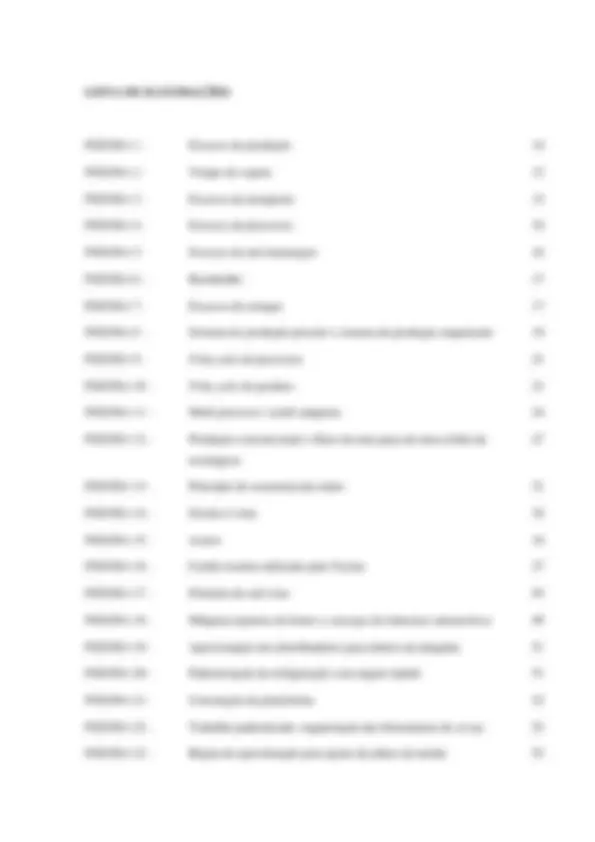
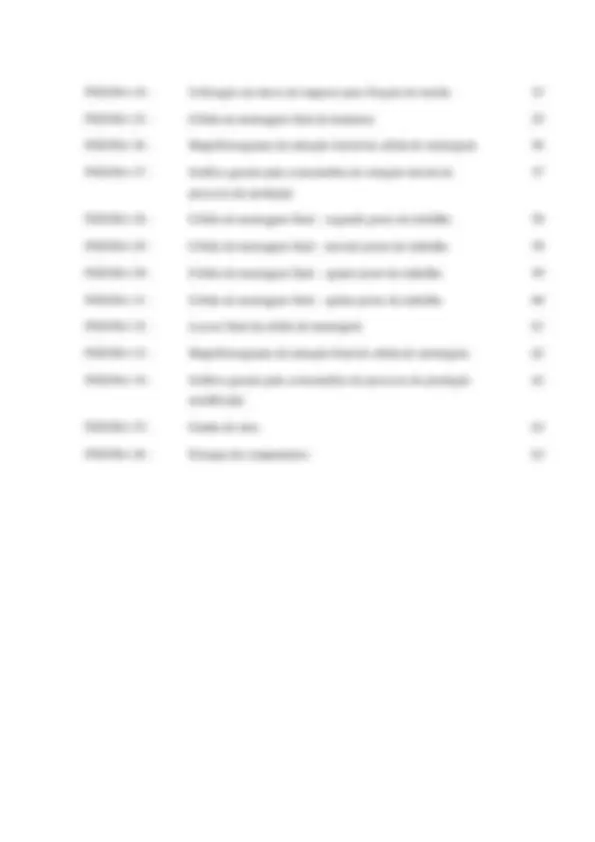
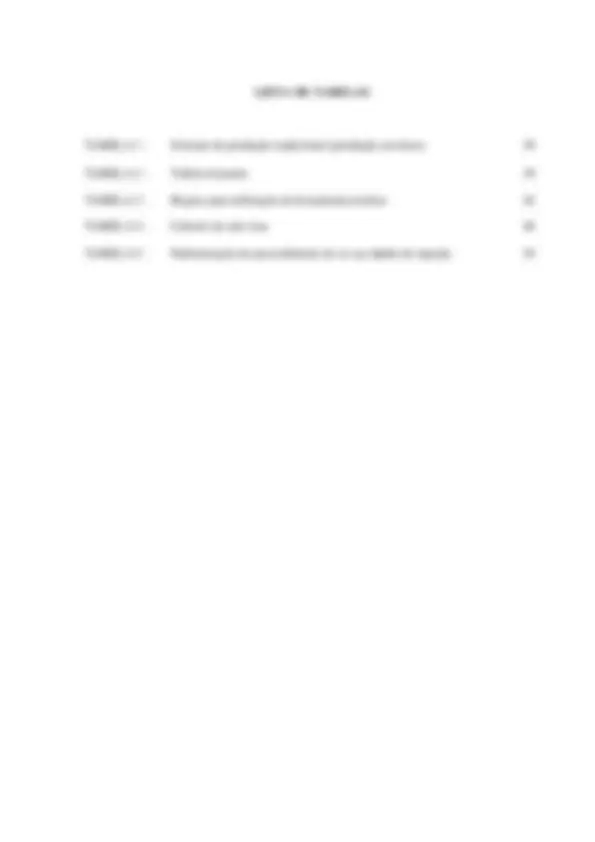
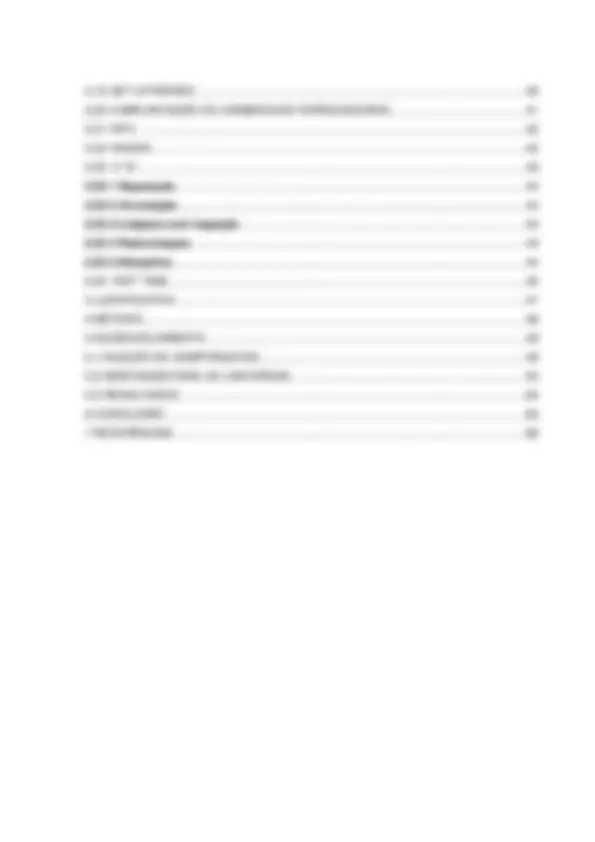
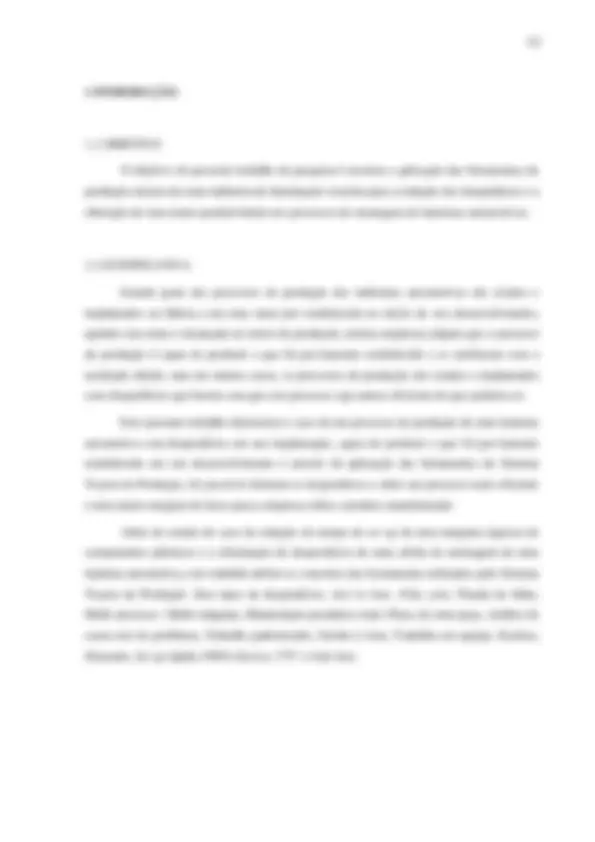
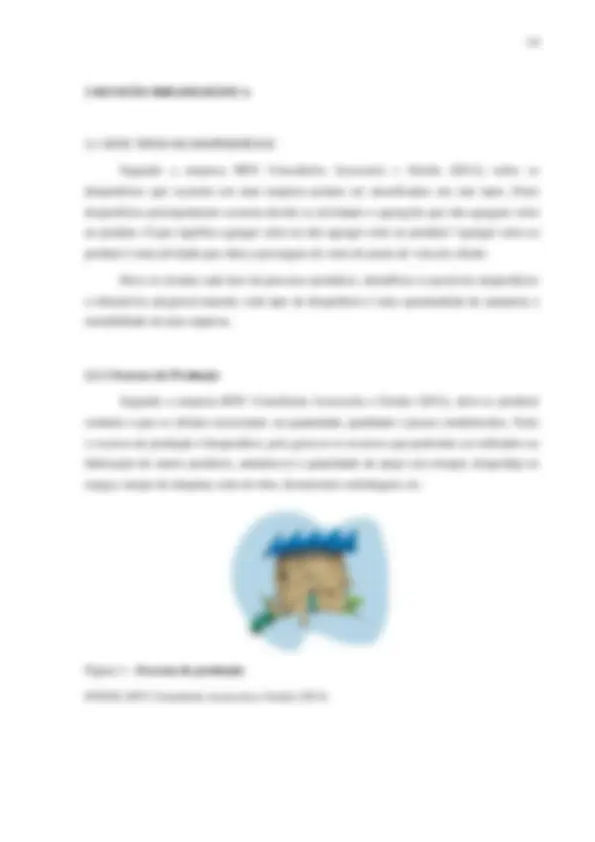
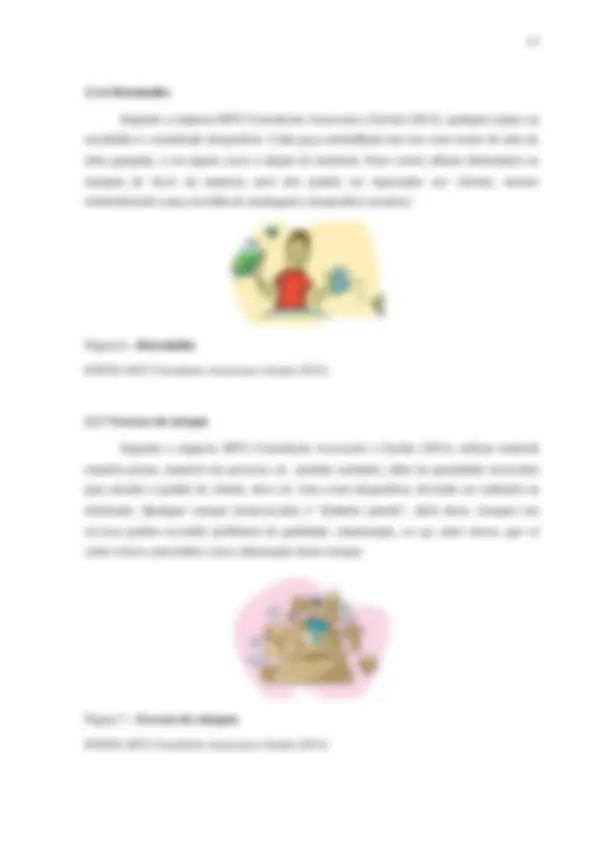
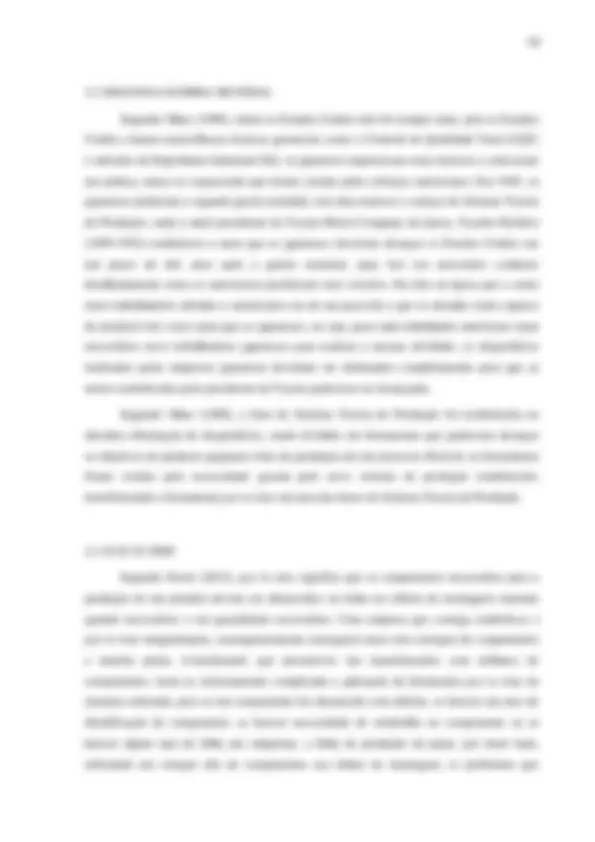
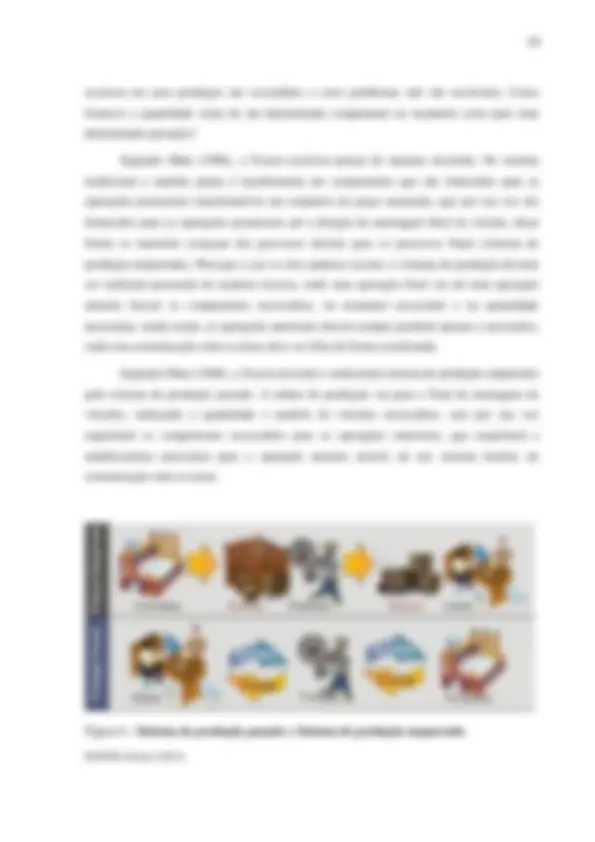
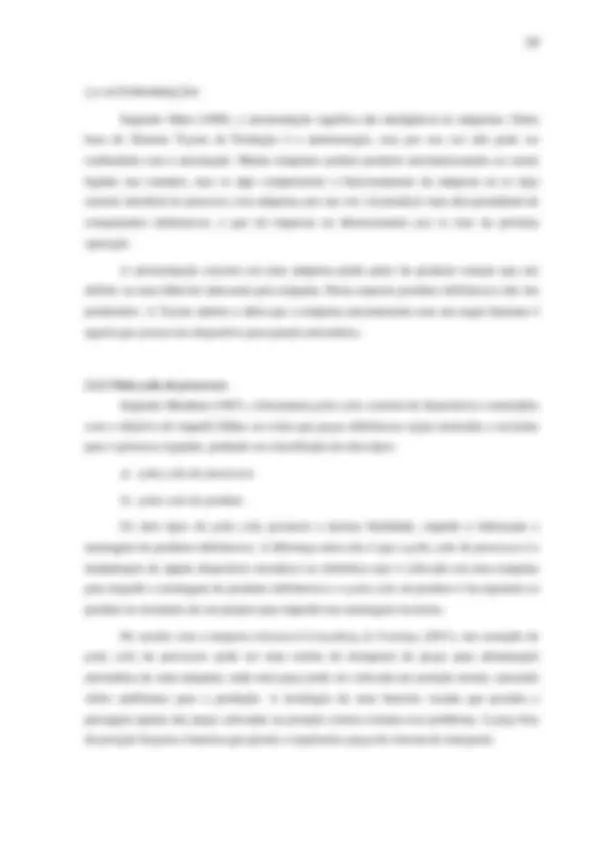
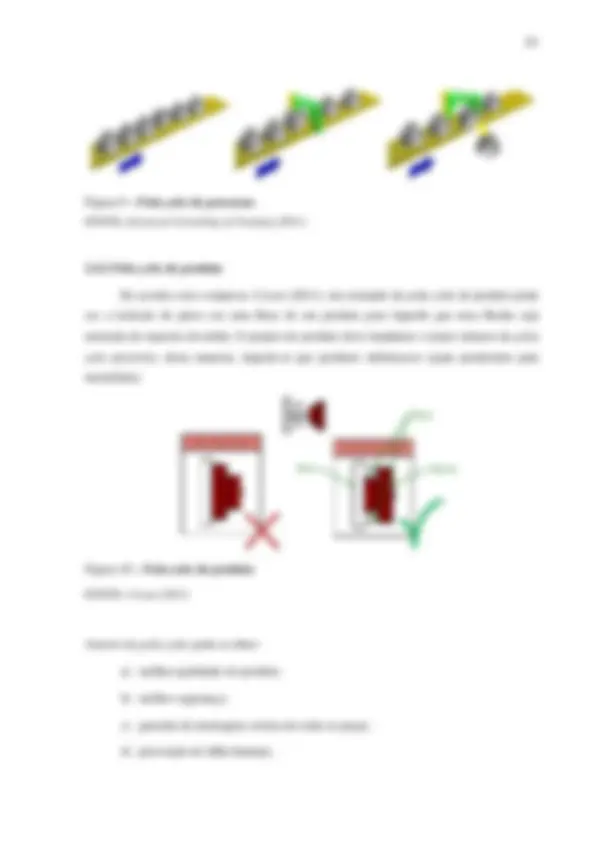
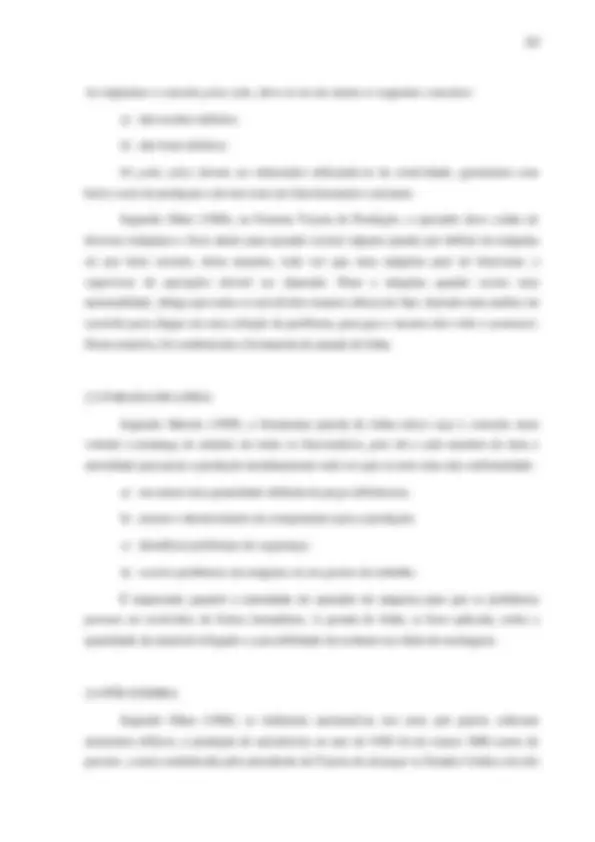
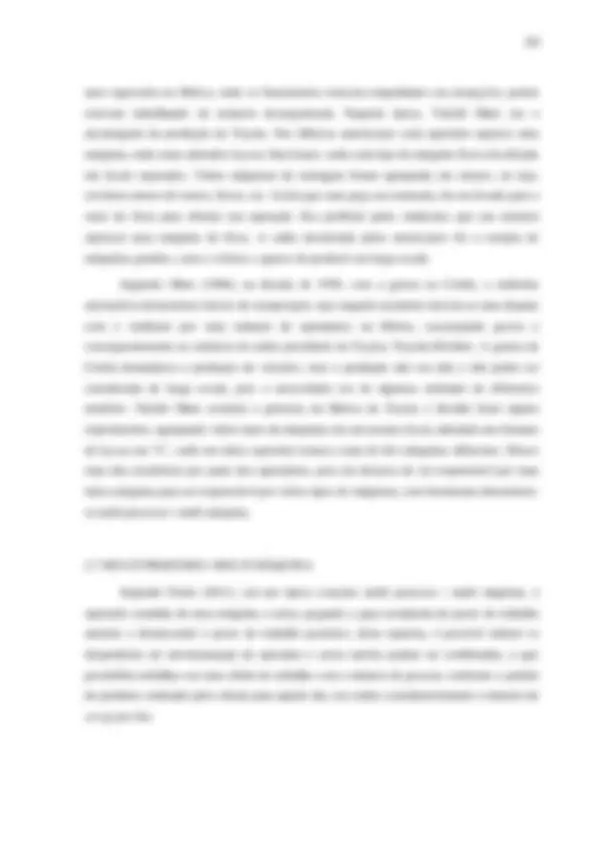
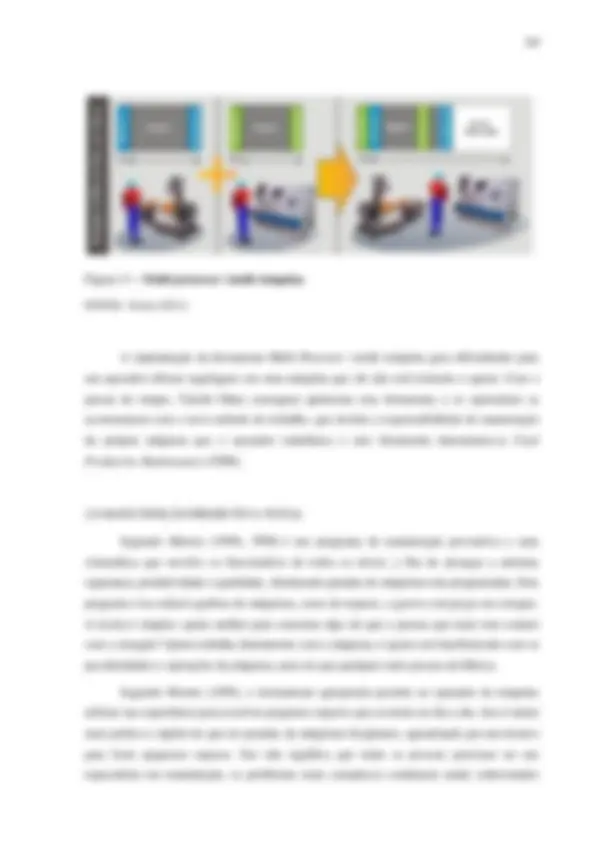
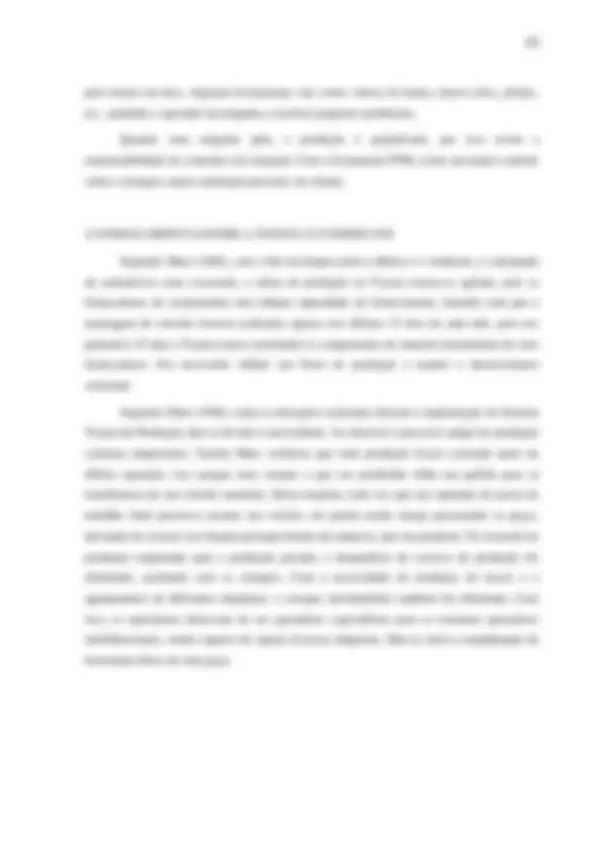
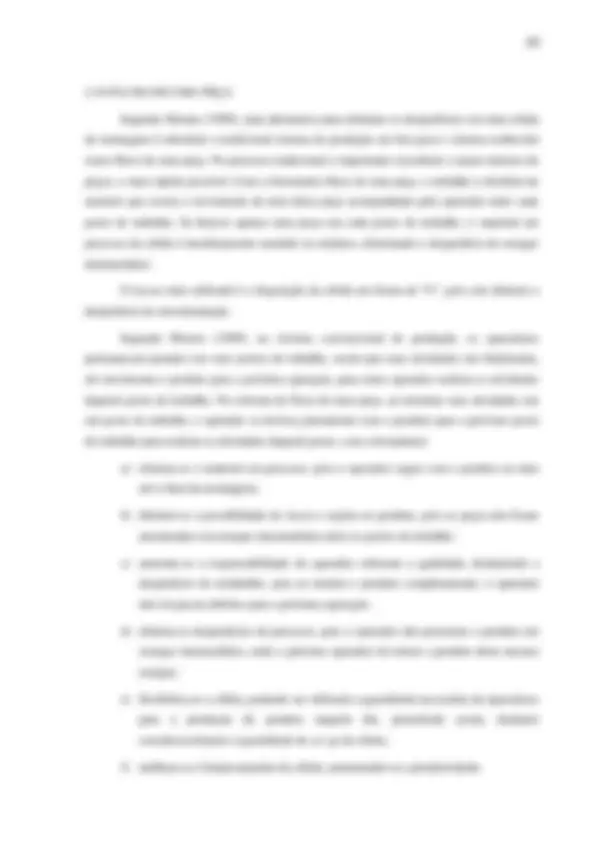
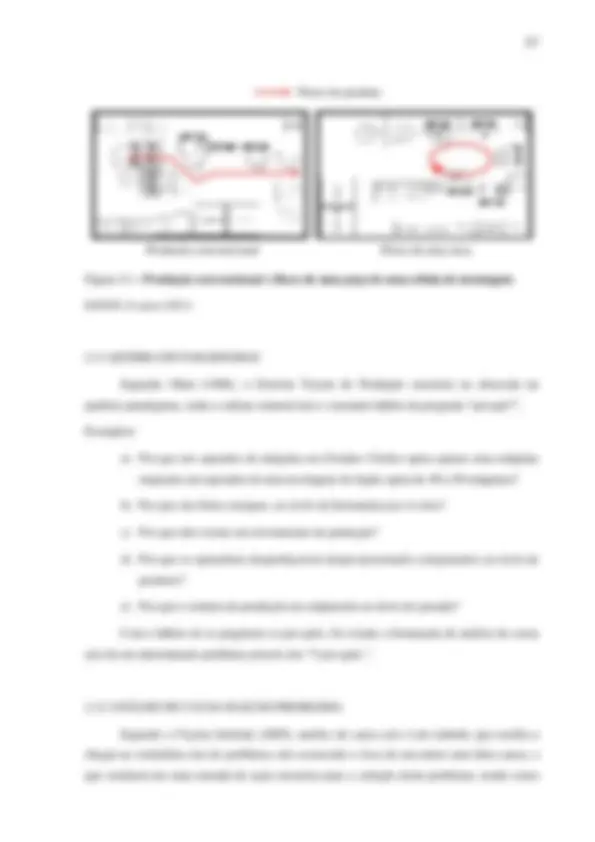
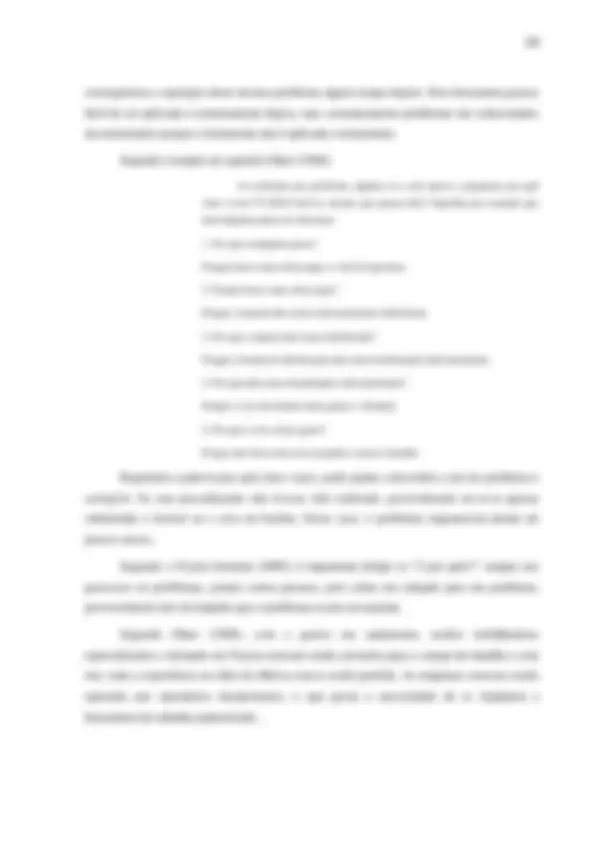
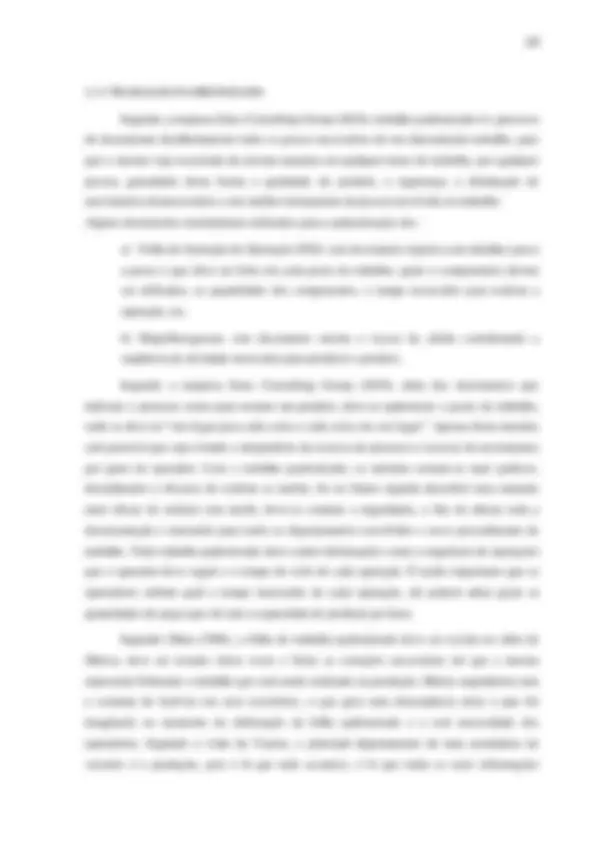
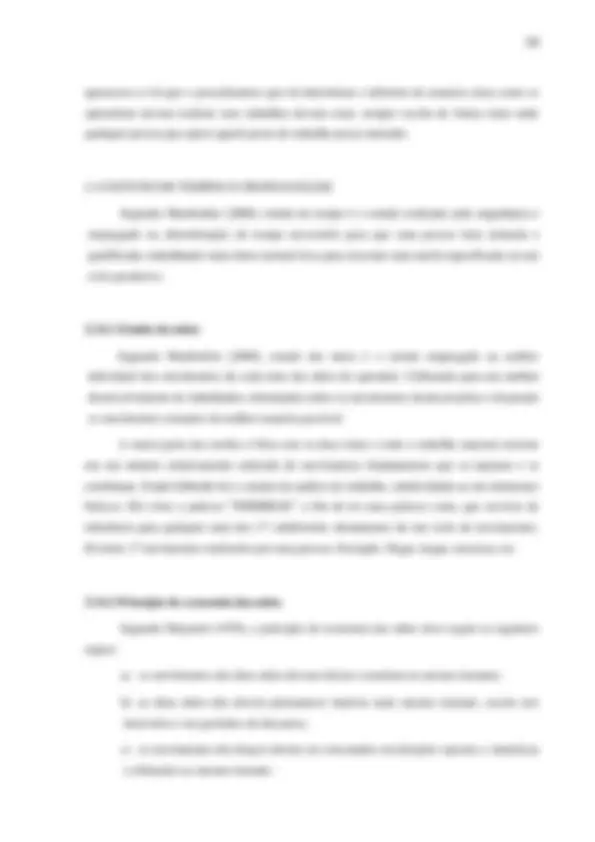
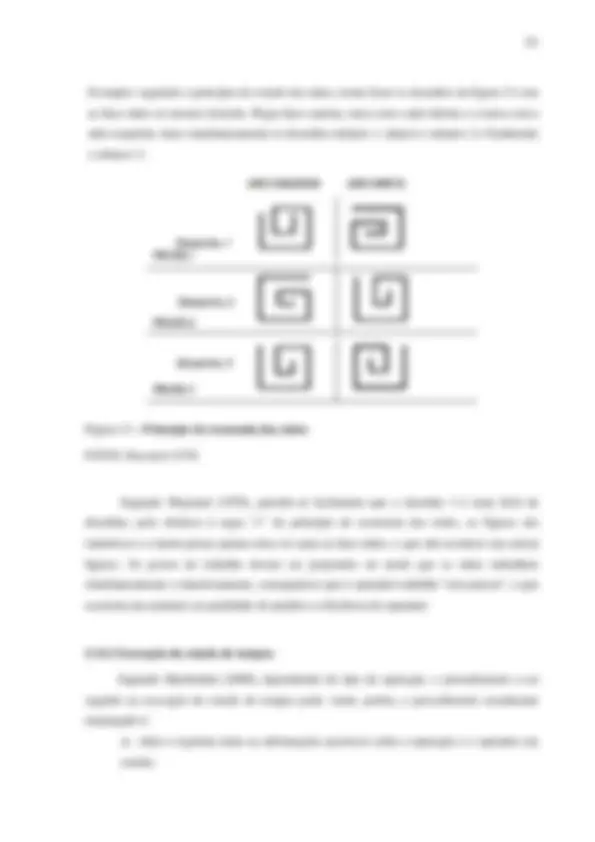
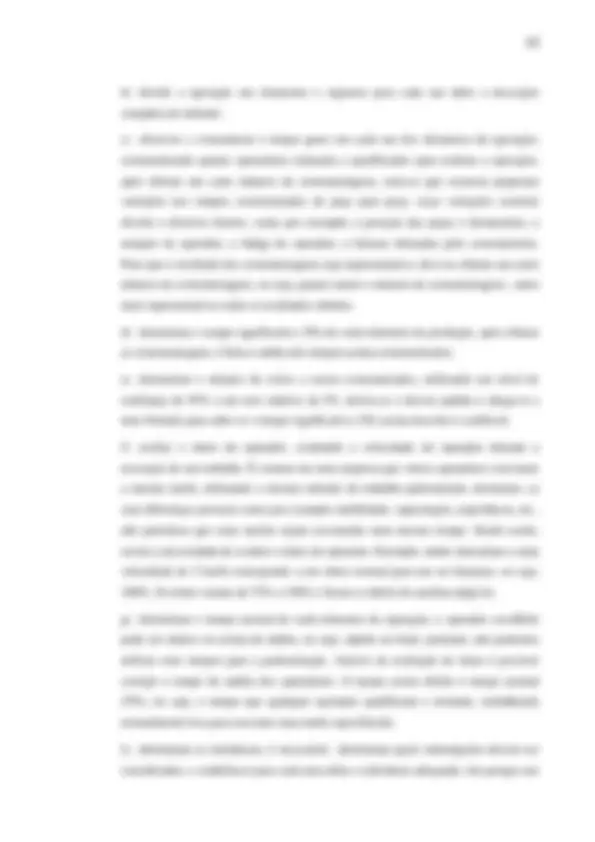
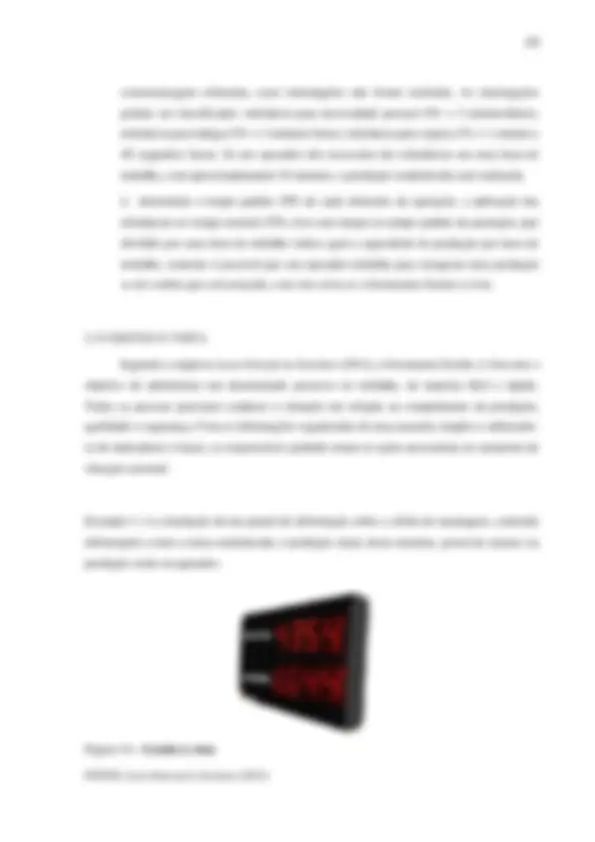
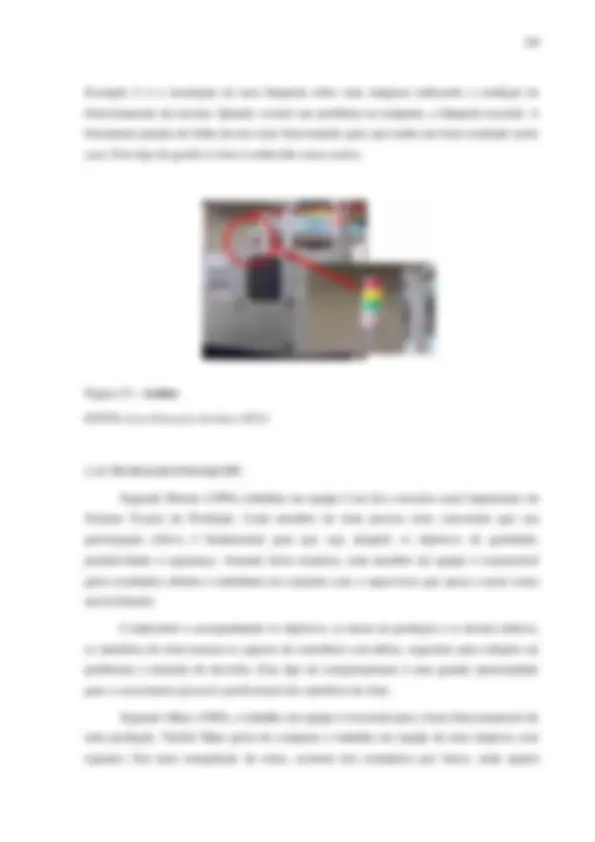
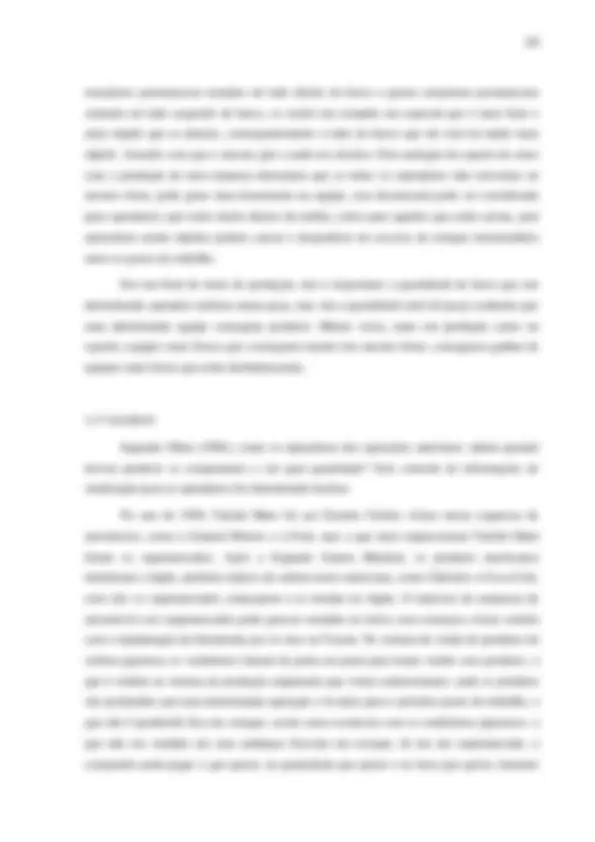
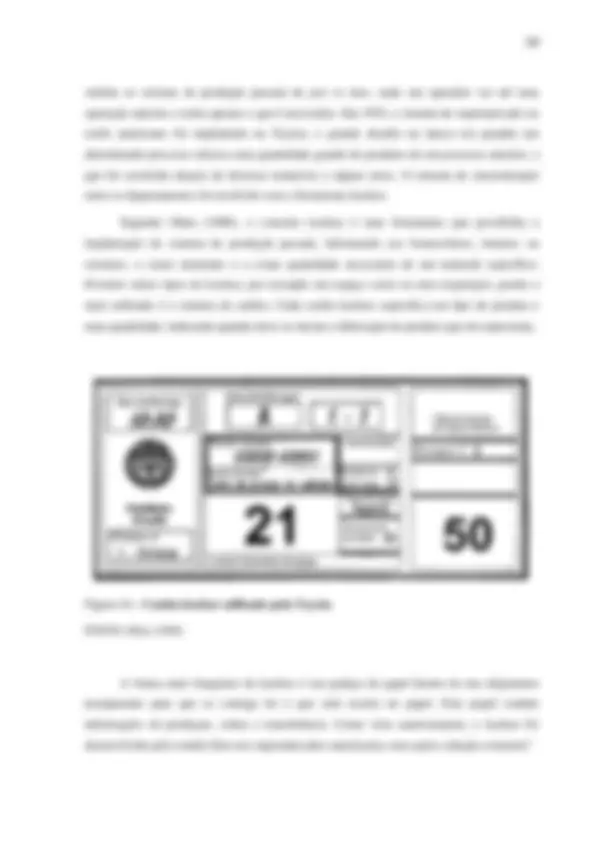

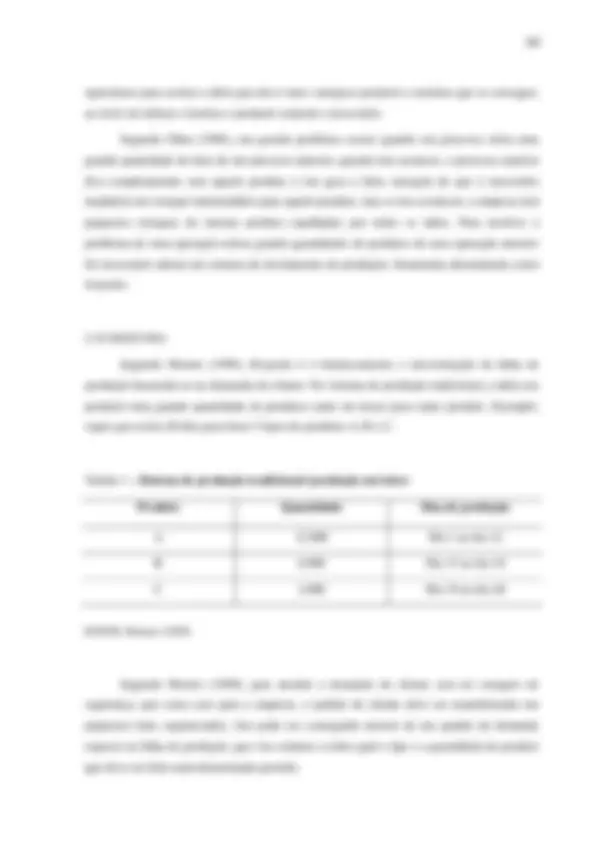
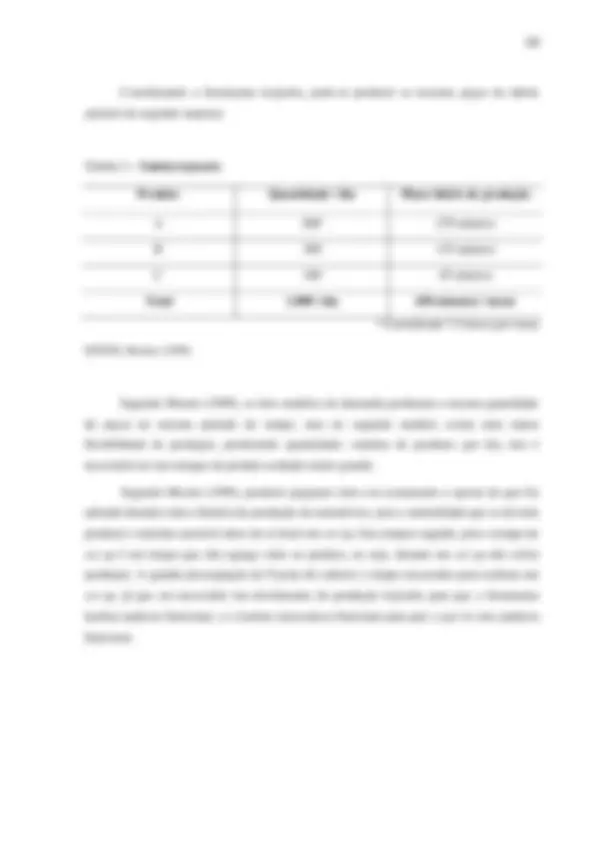
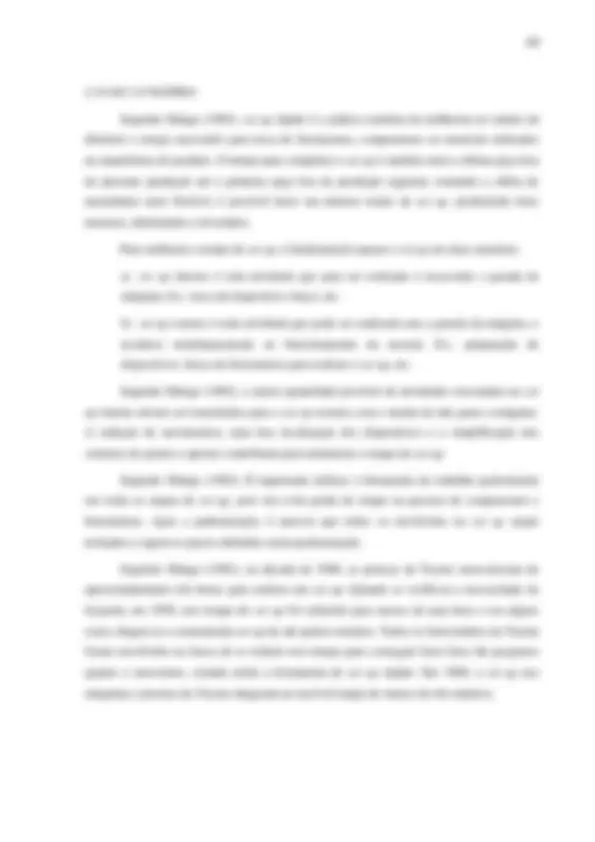
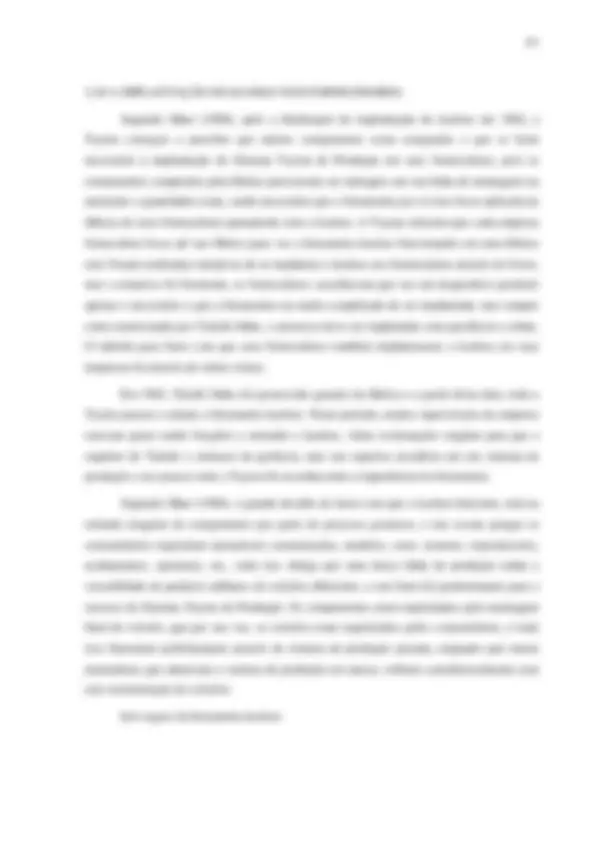
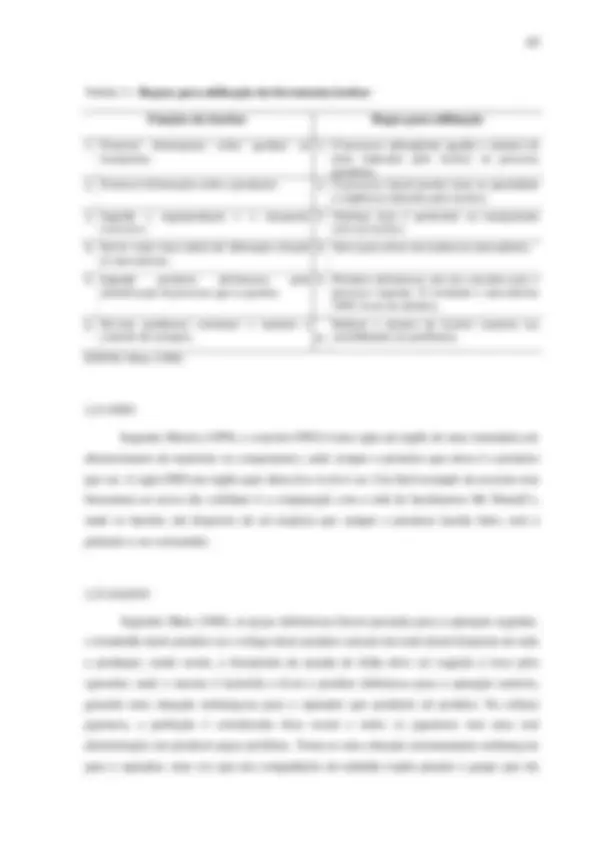
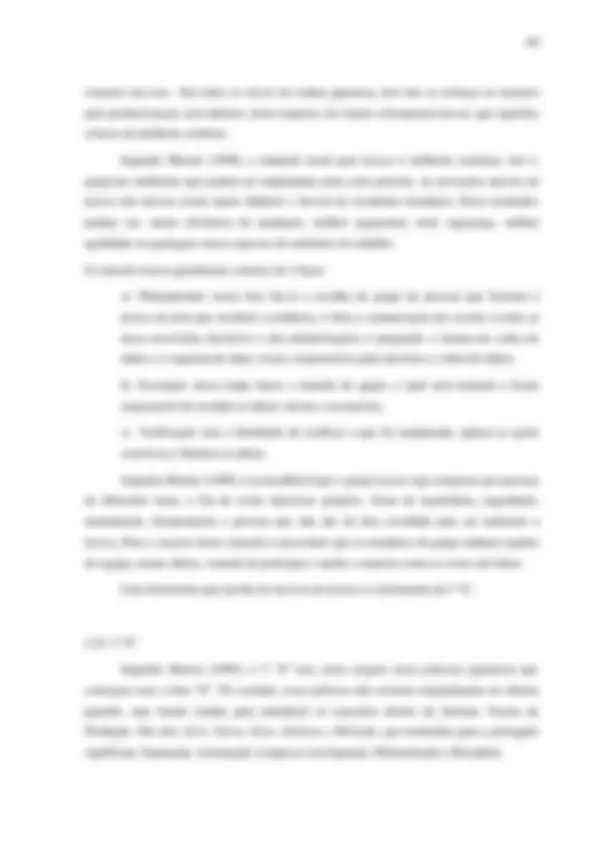
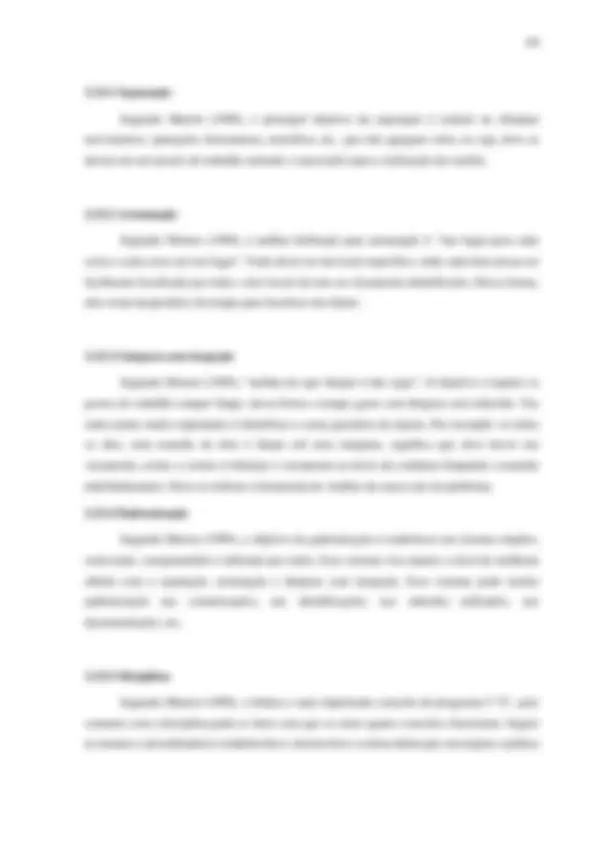
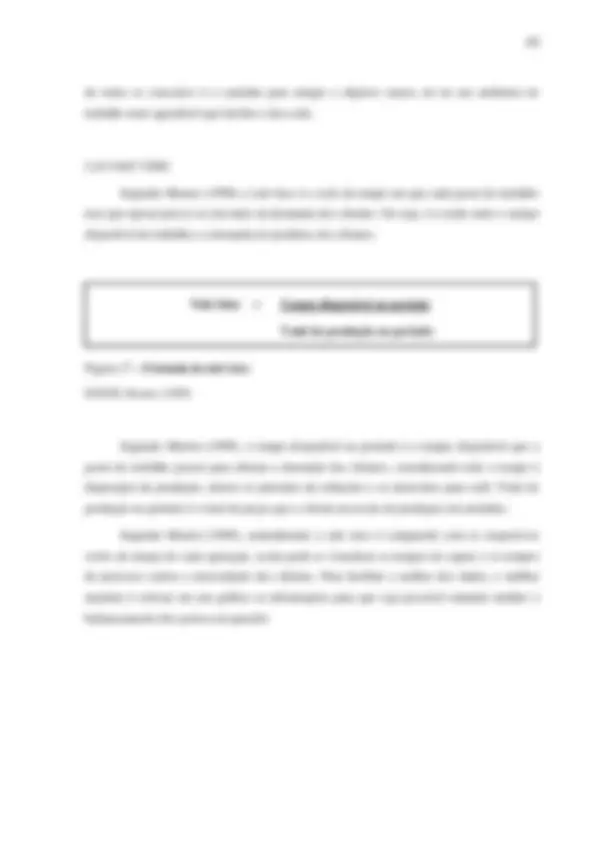
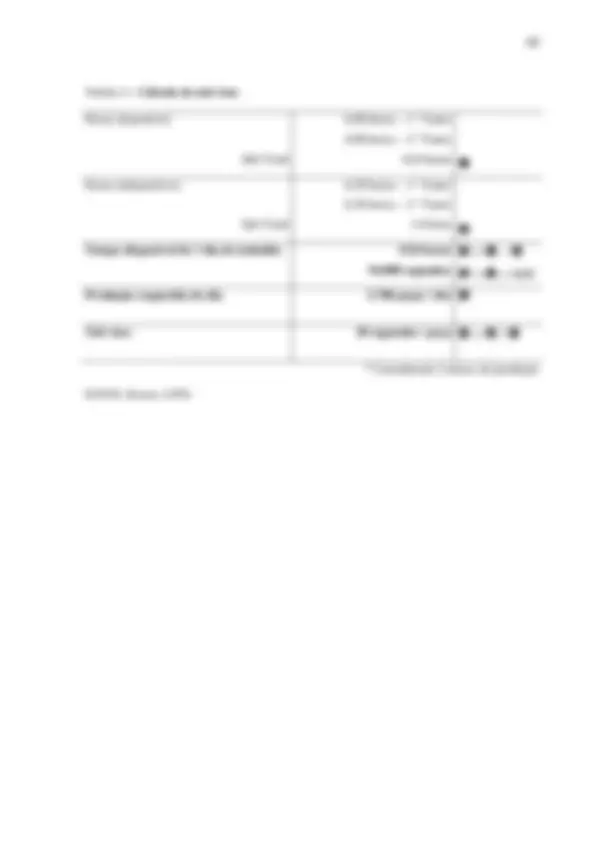
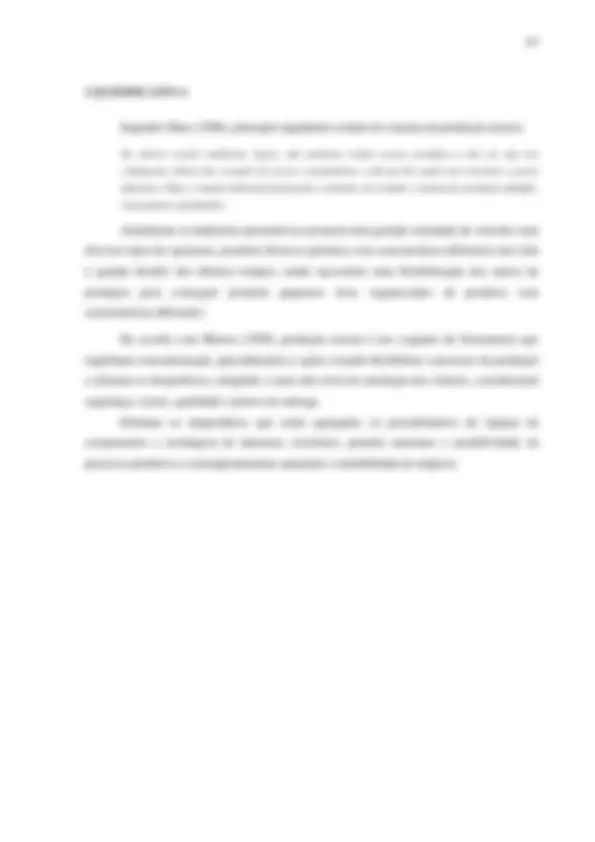
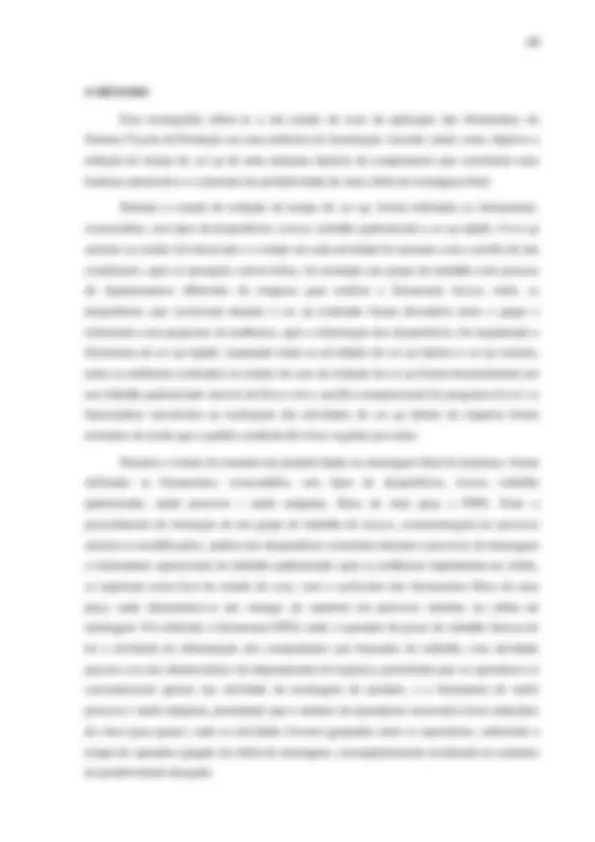

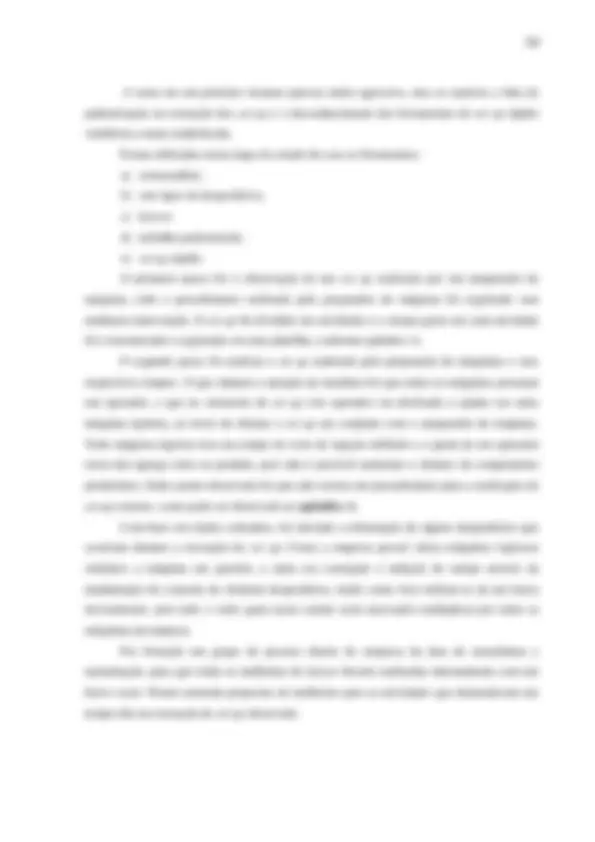
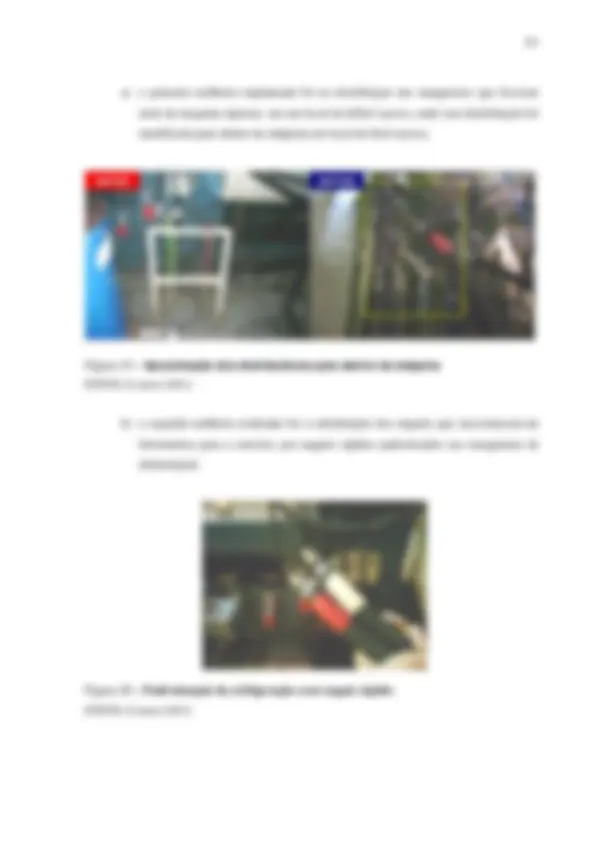
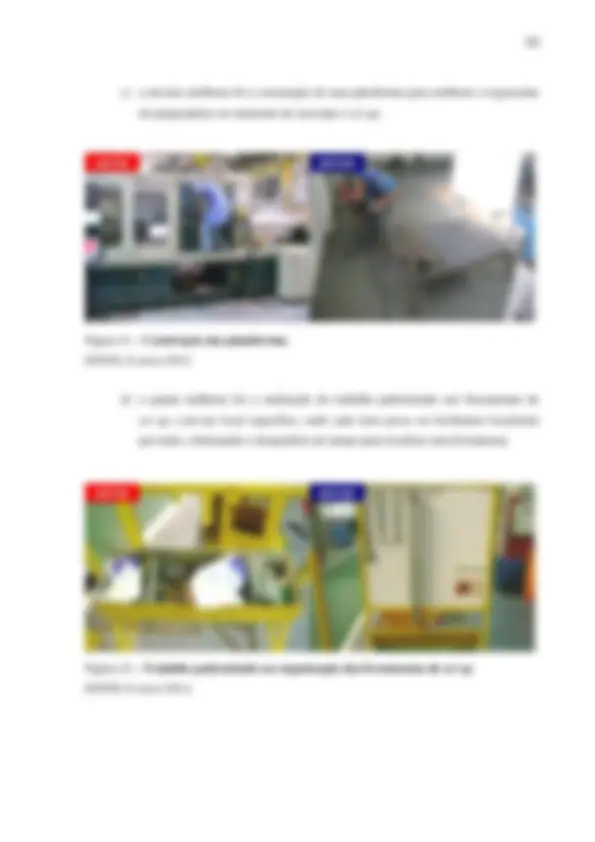
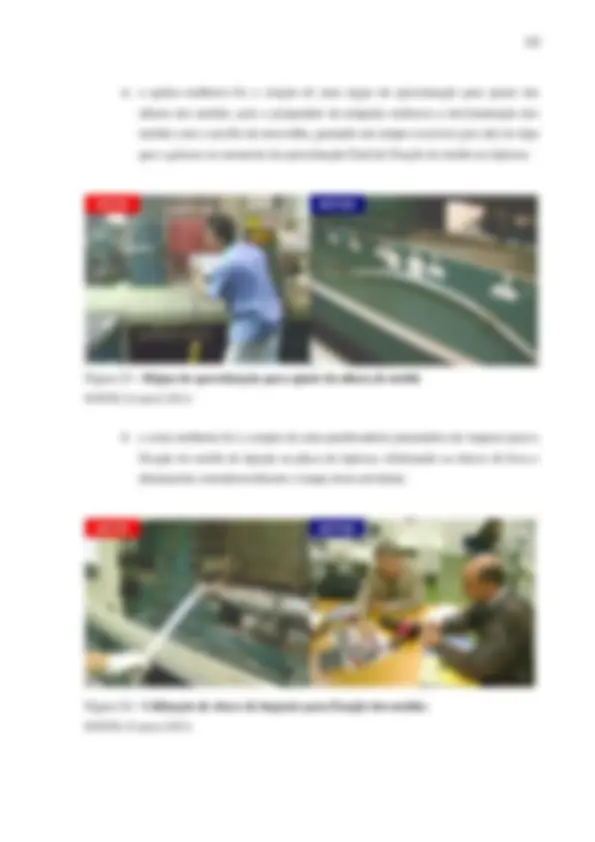
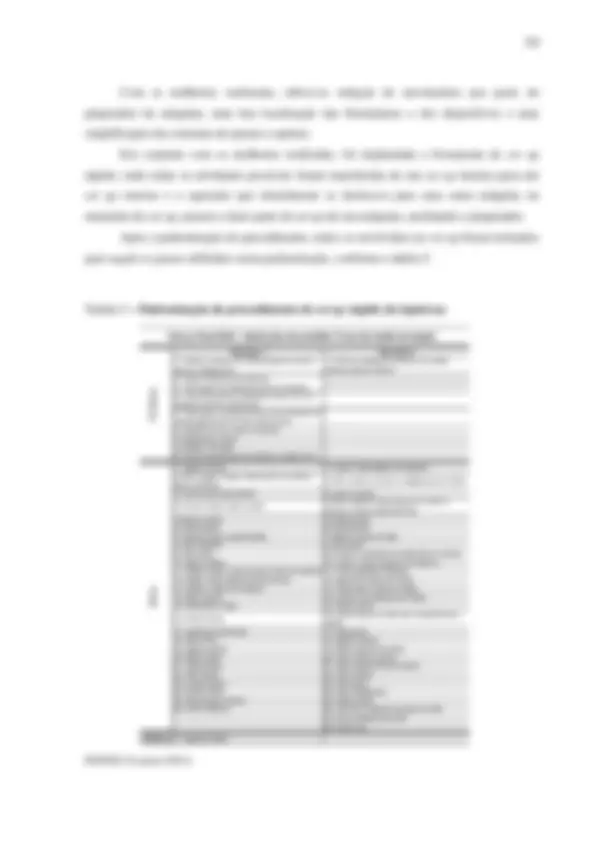

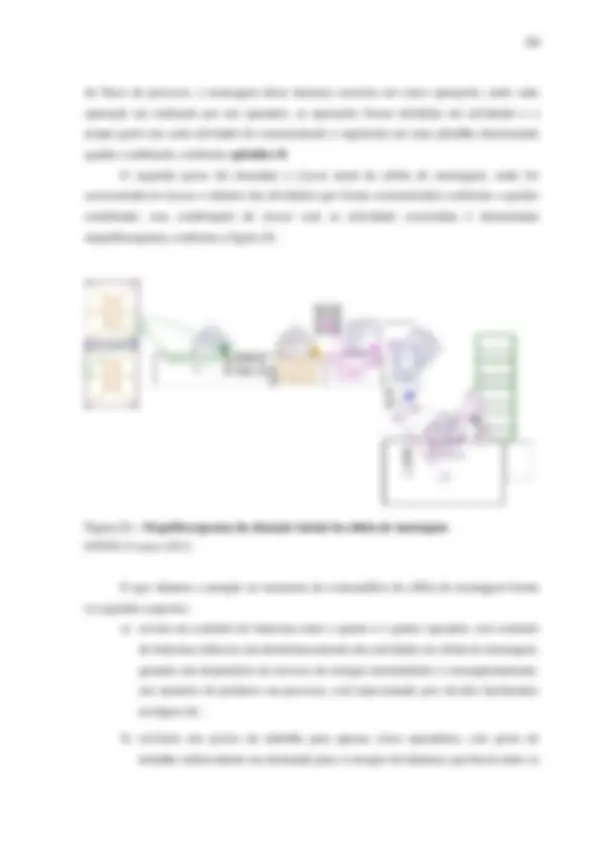
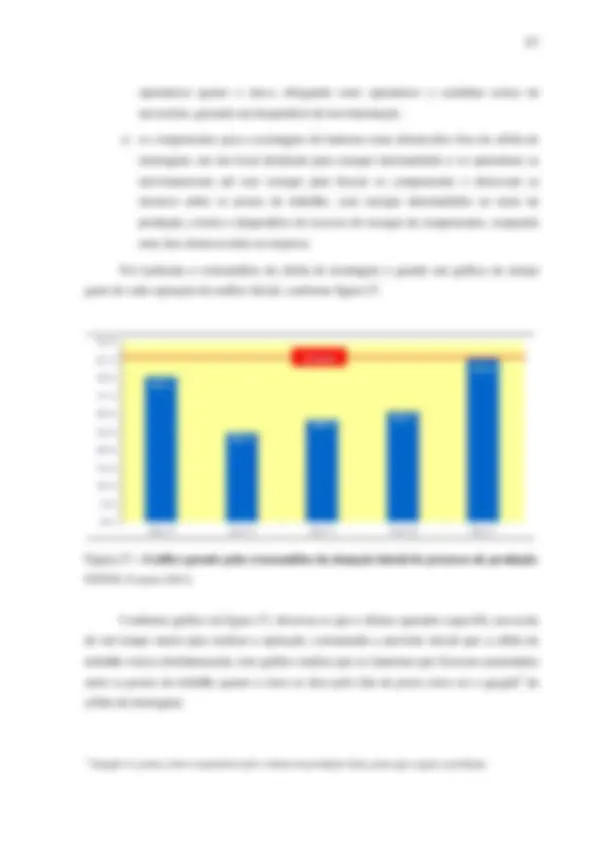
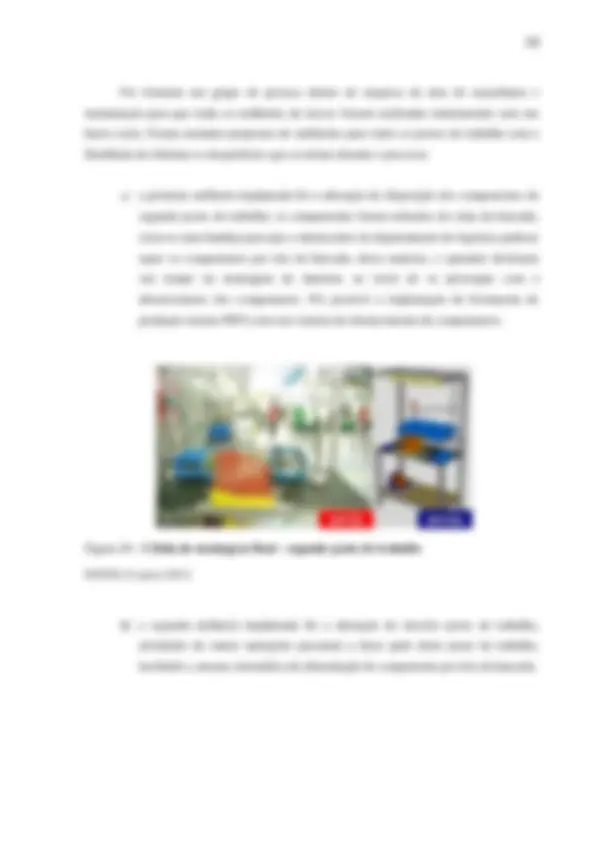
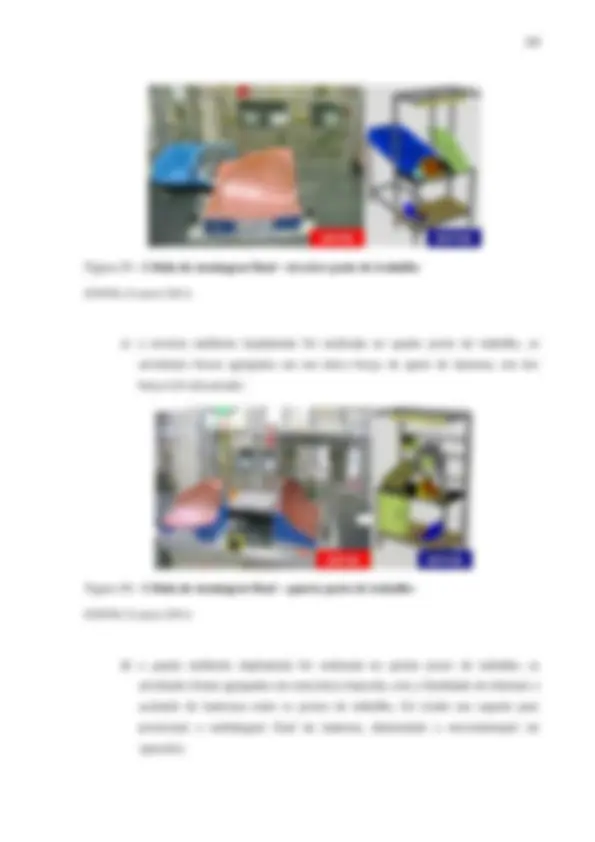
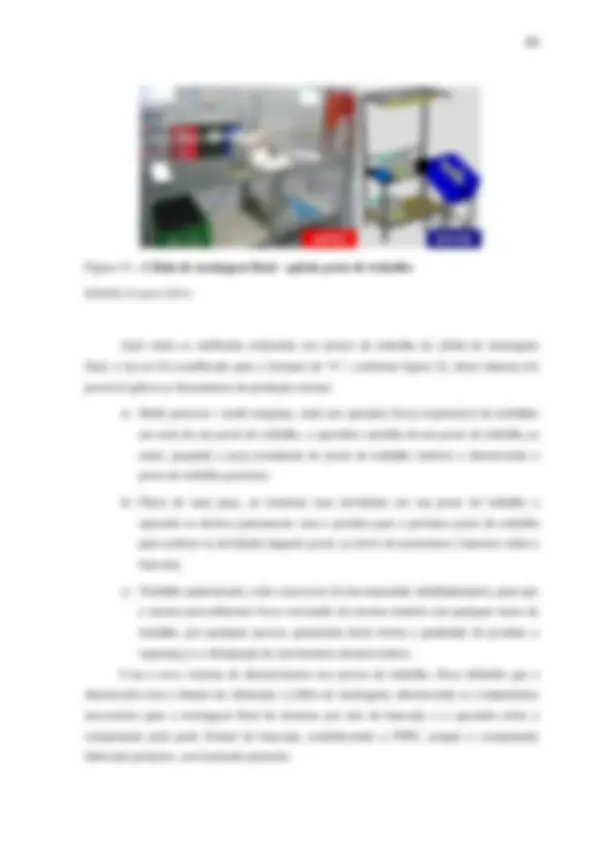
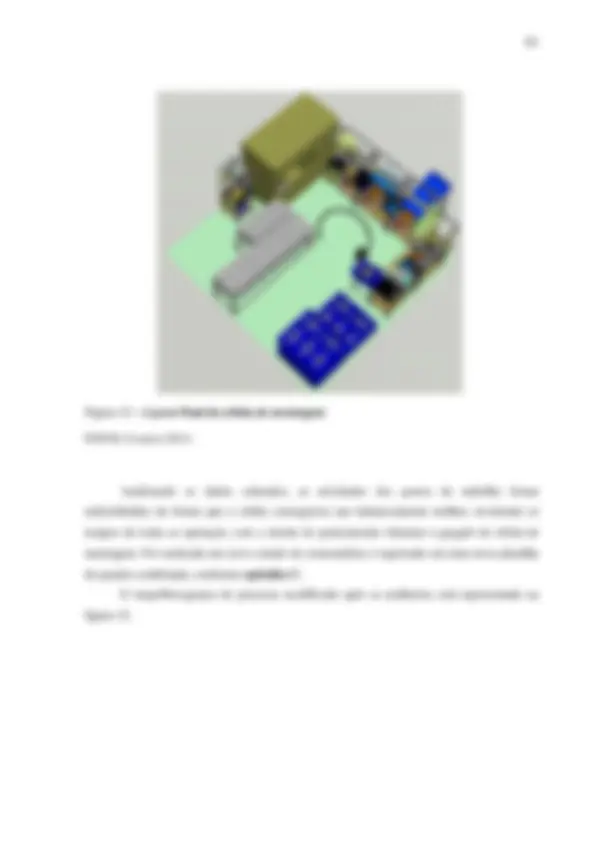
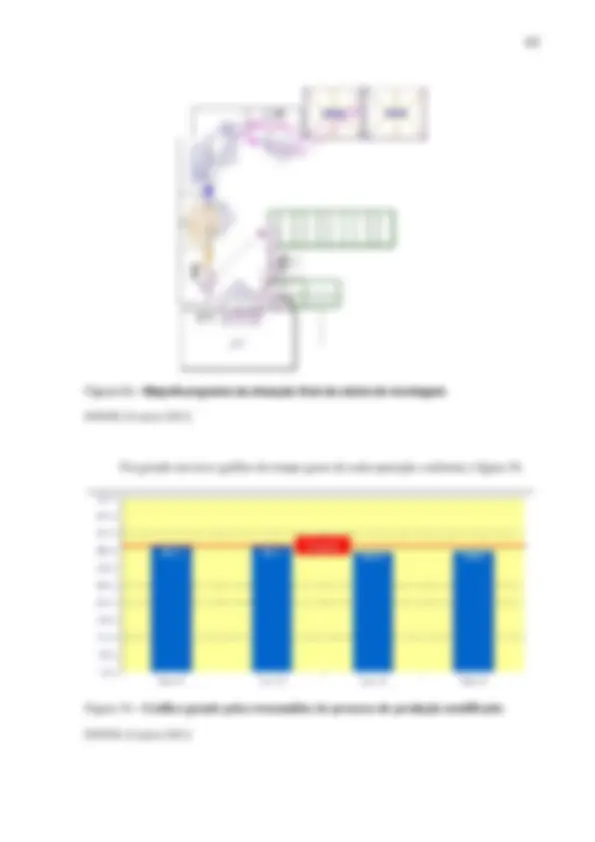
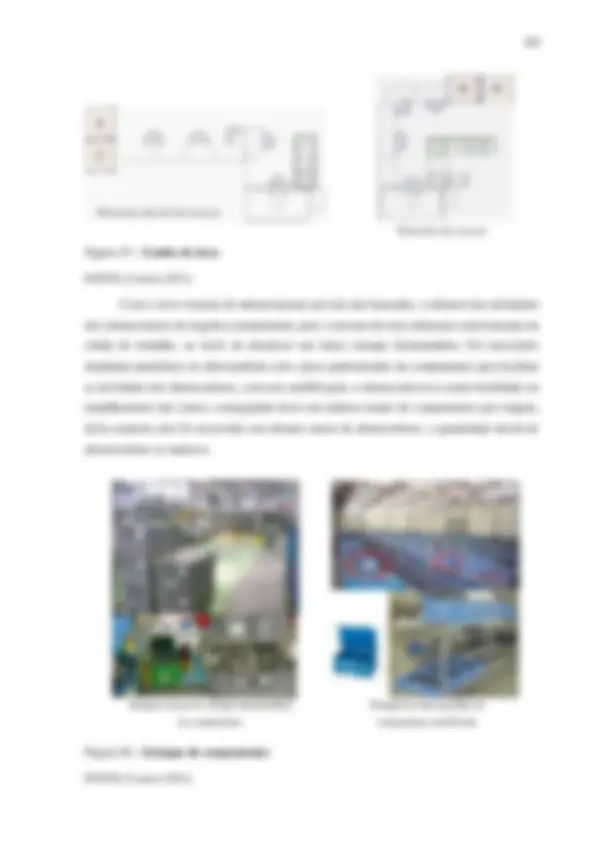
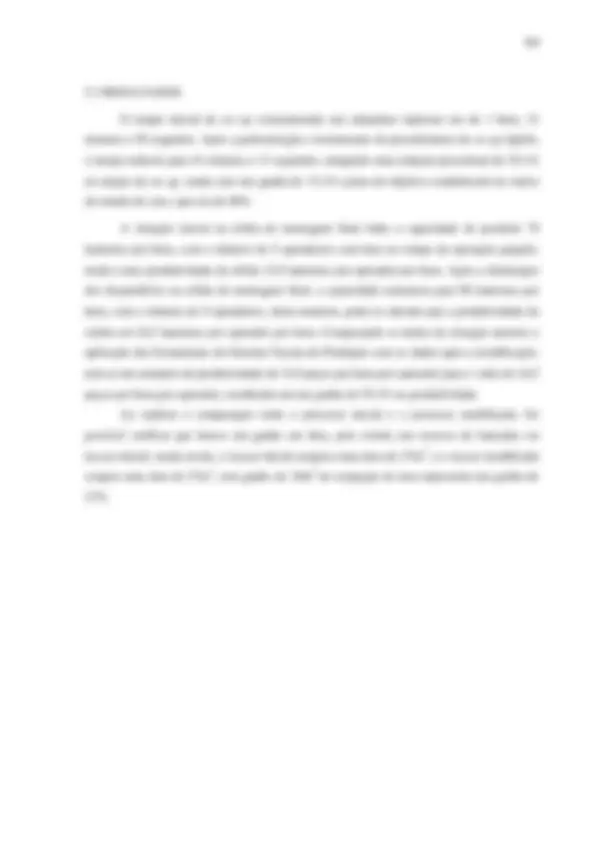
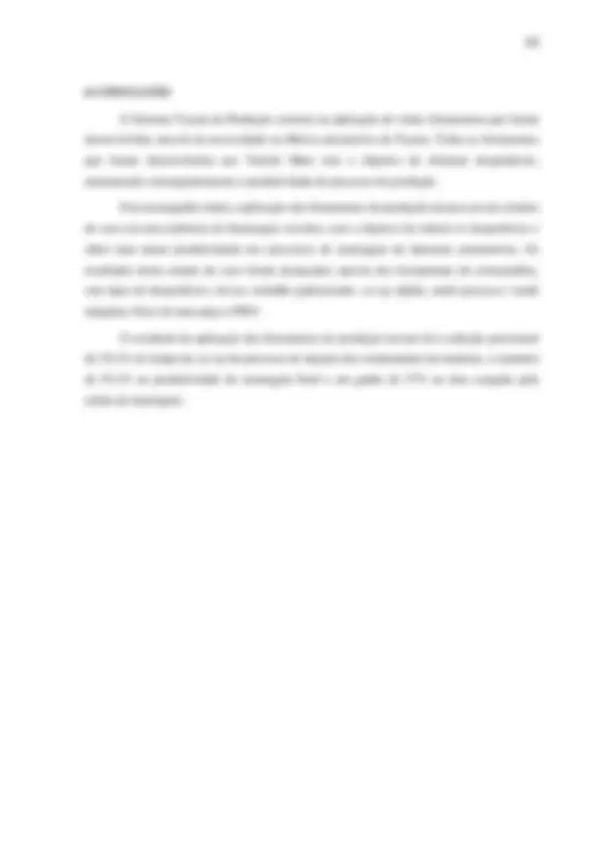
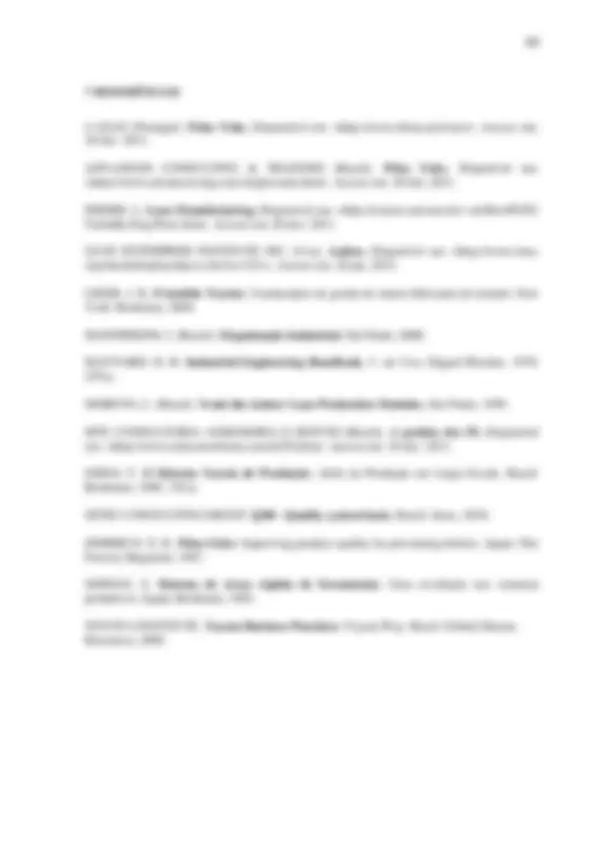
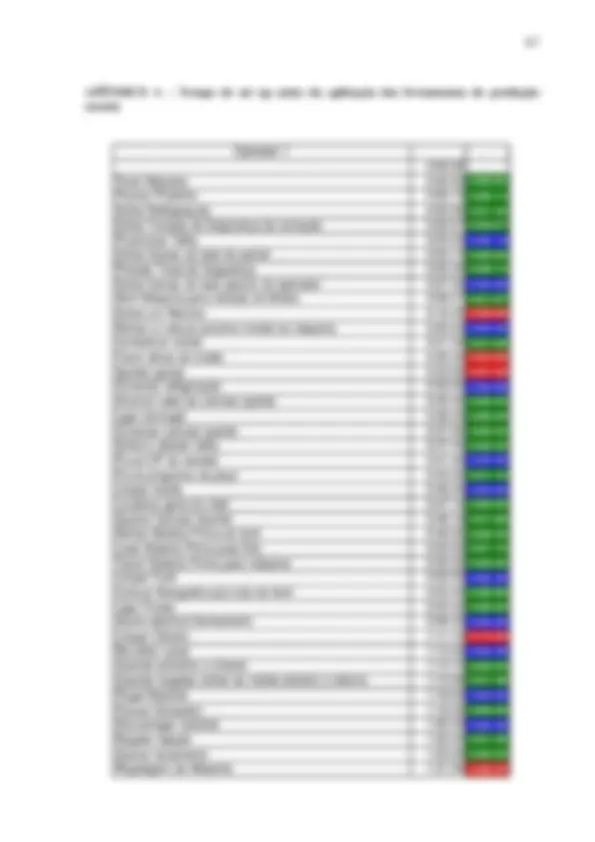

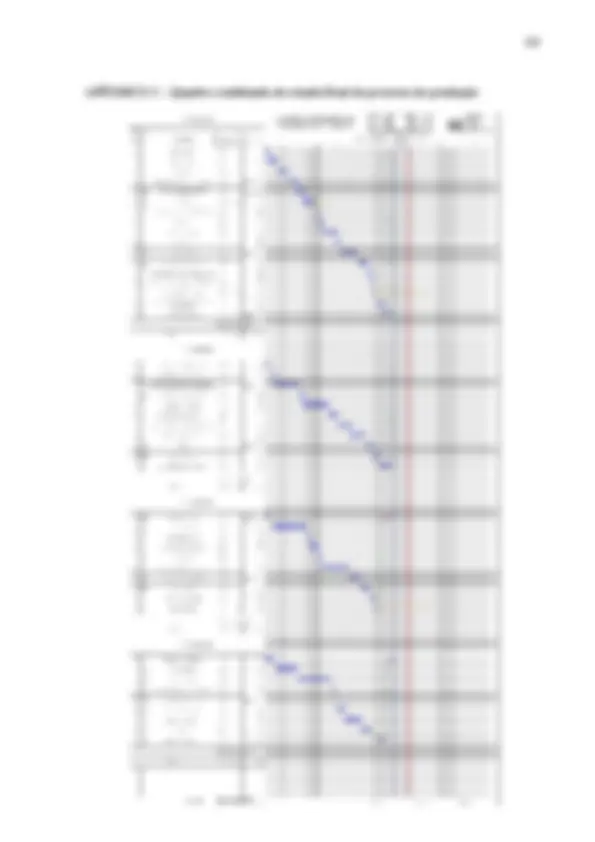
Estude fácil! Tem muito documento disponível na Docsity
Ganhe pontos ajudando outros esrudantes ou compre um plano Premium
Prepare-se para as provas
Estude fácil! Tem muito documento disponível na Docsity
Prepare-se para as provas com trabalhos de outros alunos como você, aqui na Docsity
Os melhores documentos à venda: Trabalhos de alunos formados
Prepare-se com as videoaulas e exercícios resolvidos criados a partir da grade da sua Universidade
Responda perguntas de provas passadas e avalie sua preparação.
Ganhe pontos para baixar
Ganhe pontos ajudando outros esrudantes ou compre um plano Premium
Comunidade
Peça ajuda à comunidade e tire suas dúvidas relacionadas ao estudo
Descubra as melhores universidades em seu país de acordo com os usuários da Docsity
Guias grátis
Baixe gratuitamente nossos guias de estudo, métodos para diminuir a ansiedade, dicas de TCC preparadas pelos professores da Docsity
Um estudo de caso sobre a aplicação de ferramentas de produção lean em uma indústria de iluminação veicular, com o objetivo de reduzir desperdícios e obter maior produtividade na montagem de lanternas automotivas. Como as ferramentas do sistema toyota de produção, como o sistema just-in-time, poka-yoke, parada de linha e eliminação de desperdícios, foram utilizadas para melhorar o processo de produção, eliminar desperdícios e obter um processo mais eficiente e rentável.
Tipologia: Notas de estudo
1 / 70
Esta página não é visível na pré-visualização
Não perca as partes importantes!
São Caetano do Sul 2012
Monografia apresentada ao curso de pós-graduação em Engenharia Automotiva, da Escola de Engenharia Mauá do Centro Universitário do Instituto Mauá de Tecnologia para obtenção do título de especialista.
Orientador: Prof. Cleber Lorenzi
São Caetano do Sul 2012
Este trabalho é dedicado em especial à minha família que sempre me incentivou a progredir em meus estudos e a seguir trabalhando para alcançar minhas metas. Dedico também a todos aqueles que me apoiaram durante esta caminhada.
Agradeço ao meu orientador, Prof. Cleber Lorenzi, que dedicou seu tempo para me instruir nesta monografia, e a todos os professores que se empenharam em passar seus conhecimentos durante as aulas do curso de pós graduação.
In 1945, the Japonese lost World War II, this date marked the beginning of the Toyota lean production system, where Toyota Motor Company’s president at that time, Toyoda Kiichiro, set the goal that the Japonese should reach the United States in a period of three years after the war ends.Wastage made by the Japonese company should be completely eliminated so that the goals established by the president of Toyota could be achieved. The Toyota lean production system was developed by necessity, as the United States managed to lower the costs of their vehicles, producing according to the traditional system of mass production developed by Frederick Taylor and Henry Ford in the early twentieth century. The system developed by Taylor basically consists of large scale production batches of a single type of vehicle, specializing the sectors of the plant, while the Toyota lean production system is to cut costs, to eliminate waste and to produce small batches of various models of vehicles. In 1950, with the war in Korea, the automotive industry showed signs of recovery, however began a dispute with the union for a reduction in the number of operators at the plant, causing atrikes and consequently the resignation of Toyota’s president, Toyoda Kiichiro. After the resignation of the president, Taiichi Ohno took over the management of Toyota and decided a inverted way of thinking, he created the Toyota lean production. The basis of this system was the reversal of the traditional production system pushed by the pull production system, where all the tools were created by the need generated by the new production system stablished, with a focus on eliminating waste in a progressive way, with the objective of producing small batches production of various types of products. This paper discibes the application of lean production tools in a case study inside a vehicular lighting industry, in order to reduce waste and achieve higher productivity in the process of assembling automotive rear lamps. The results of this case study were achieved with a reduction of 55.1% in the set up time of the injection process of the components of the rear lamp, an increase of 55.1% in the productivity of final assembly and a 27% gain in the area occupied by the call assembly.
Keywords: Process of lean production. Toyota production system. Lean manufacturing. Waste disposal.
FIGURA 12 - Produção convencional x fluxo de uma peça de uma célula de montagem
LER Lesões por Esforços Repetitivos CQT Controle de Qualidade Total EI Engenharia Industrial TPM Total Productive Maintenance (Manutenção Produtiva Total) PCP Planejamento e Controle da Produção TS Tempo Significativo TN Tempo Normal TP Tempo Padrão WIP Work in process (Material em processo) FIFO First In First Out (Primeiro a Entrar Primeiro a Sair) FIO Folha de Instrução de Processo
13
O objetivo do presente trabalho de pesquisa é mostrar a aplicação das ferramentas de produção enxuta em uma indústria de iluminação veicular para a redução dos desperdícios e a obtenção de uma maior produtividade nos processos de montagem de lanternas automotivas.
Grande parte dos processos de produção das indústrias automotivas são criados e implantados na fábrica com uma meta pré estabelecida no início de seu desenvolvimento, quando esta meta é alcançada no inicio da produção, muitas empresas julgam que o processo de produção é capaz de produzir o que foi previamente estabelecido e se satisfazem com o resultado obtido, mas em muitos casos, os processos de produção são criados e implantados com desperdícios que fazem com que este processo seja menos eficiente do que poderia ser.
Este presente trabalho demonstra o caso de um processo de produção de uma lanterna automotiva com desperdícios em sua implantação, capaz de produzir o que foi previamente estabelecido em seu desenvolvimento e através da aplicação das ferramentas do Sistema Toyota de Produção, foi possível eliminar os desperdícios e obter um processo mais eficiente e uma maior margem de lucro para a empresa sobre o produto manufaturado.
Além do estudo de caso da redução do tempo de set up de uma máquina injetora de componentes plásticos e a eliminação de desperdícios de uma célula de montagem de uma lanterna automotiva, este trabalho define os conceitos das ferramentas utilizadas pelo Sistema Toyota de Produção: Sete tipos de desperdícios, Just in time , Poka yoke , Parada de linha, Multi processo / Multi máquina, Manutenção produtiva total, Fluxo de uma peça, Análise de causa raiz do problema, Trabalho padronizado, Gestão à vista, Trabalho em equipe, Kanban , Heijunka , Set up rápido, FIFO, Kaizen , 5“S” e Takt time.
15
2.1.2 Tempo de espera
Segundo a empresa MTU Consultoria Assessoria e Gestão (2012), pode-se facilmente perceber este tipo de desperdício quando observa-se um operador parado esperando pelo término do ciclo de uma máquina, por uma manutenção ou mesmo aguardando componentes.
Figura 2 – Tempo de espera
FONTE: MTU Consultoria Assessoria e Gestão (2012)
2.1.3 Excesso de transporte
Segundo a empresa MTU Consultoria Assessoria e Gestão (2012), entende-se que toda vez que um material é transportado de um lado para o outro, seja dentro de um mesmo setor, de uma máquina para outra, ou de um setor para o outro, está ocorrendo o desperdício de transporte, que deve sempre ser reduzido ao máximo, pois a mão de obra utilizada no transporte não está agregando valor ao produto. Uma esteira, calha ou até mesmo a aproximação das máquinas podem eliminar a atividade de transporte e o operador que executa a atividade de transporte pode executar outra atividade.
Figura 3 – Excesso de transporte
FONTE: MTU Consultoria Assessoria e Gestão (2012)
16
2.1.4 Excesso de processos
Segundo a empresa MTU Consultoria Assessoria e Gestão (2012), toda vez que um material é processado durante um tempo maior do que o necessário ou quando executa-se uma operação desnecessária, ocorre o desperdício de processo. Um bom exemplo é embalar e desembalar a mesma peça durante o processo, o tempo gasto para embalar e desembalar o produto não agrega valor ao produto.
Figura 4 – Excesso de processos
FONTE: MTU Consultoria Assessoria e Gestão (2012)
2.1.5 Excesso de movimentação
Segundo a empresa MTU Consultoria Assessoria e Gestão (2012), o desperdício de movimentos refere-se aos movimentos desnecessário que uma pessoa realiza para que um processo seja realizado. Uma das maneiras de eliminar os movimentos desnecessários é a aproximação dos materiais no posto de trabalho. O beneficio não será apenas um aumento de produção, mas também haverá uma diminuição de LER (Lesões por Esforços Repetitivos), além de diminuir a fadiga que é considerada nas tolerâncias de cronoanálise, pois o desgaste para executar uma atividade será menor se os componentes necessários para um operador executar uma atividade estiver próximo ao seu corpo.
Figura 5 – Excesso de movimentos
FONTE: MTU Consultoria Assessoria e Gestão (2012)
18
Segundo Ohno (1988), imitar os Estados Unidos não foi sempre ruim, pois os Estados Unidos criaram maravilhosas técnicas gerenciais como o Controle de Qualidade Total (CQT) e métodos de Engenharia Industrial (EI), os japoneses importavam estas técnicas e colocavam em prática, nunca se esquecendo que foram criadas pelos esforços americanos. Em 1945, os japoneses perderam a segunda guerra mundial, esta data marcou o começo do Sistema Toyota de Produção, onde o atual presidente da Toyota Motor Company da época, Toyoda Kiichiro (1899-1952) estabeleceu a meta que os japoneses deveriam alcançar os Estados Unidos em um prazo de três anos após a guerra terminar, para isto era necessário conhecer detalhadamente como os americanos produziam seus veículos. Era dito na época que a razão entre trabalhadores alemães e americanos era de um para três e que os alemães eram capazes de produzir três vezes mais que os japoneses, ou seja, para cada trabalhador americano eram necessários nove trabalhadores japoneses para realizar a mesma atividade, os desperdícios realizados pelas empresas japonesas deveriam ser eliminados completamente para que as metas estabelecidas pelo presidente da Toyota pudessem ser alcançadas.
Segundo Ohno (1988), a base do Sistema Toyota de Produção foi estabelecida na absoluta eliminação de desperdícios, sendo dividido em ferramentas que pudessem alcançar os objetivos de produzir pequenos lotes de produção em um processo flexível, as ferramentas foram criadas pela necessidade gerada pelo novo sistema de produção estabelecido, transformando a ferramenta just in time em uma das bases do Sistema Toyota de Produção.
Segundo Freire (2012), just in time significa que os componentes necessários para a produção de um produto devem ser abastecidos na linha ou células de montagem somente quando necessários e em quantidades necessárias. Uma empresa que consiga estabelecer o just in time integralmente, consequentemente conseguirá zerar seus estoques de componentes e matéria prima. Considerando que automóveis são manufaturados com milhares de componentes, torna-se extremamente complicada a aplicação da ferramenta just in time de maneira ordenada, pois se um componente for abastecido com defeito, se houver um erro de identificação de componente, se houver necessidade de retrabalho no componente ou se houver algum tipo de falha nas máquinas, a linha de produção irá parar, por outro lado, utilizando um estoque alto de componentes nas linhas de montagem, os problemas que
19
ocorrem em uma produção são escondidos e estes problemas não são resolvidos. Como fornecer a quantidade exata de um determinado componente no momento certo para uma determinada operação?
Segundo Ohno (1988), a Toyota resolveu pensar de maneira invertida. No sistema tradicional a matéria prima é transformada em componentes que são fornecidos para as operações posteriores transformá-los em conjuntos de peças montadas, que por sua vez são fornecidos para as operações posteriores até a direção da montagem final do veículo, desta forma os materiais avançam dos processos iniciais para os processos finais (sistema de produção empurrado). Para que o just in time pudesse ocorrer, o sistema de produção deveria ser realizado pensando de maneira inversa, onde uma operação final vai até uma operação anterior buscar os componentes necessários, no momento necessário e na quantidade necessária, sendo assim, as operações anteriores devem sempre produzir apenas o necessário, onde esta comunicação entre as áreas deve ser feita de forma coordenada.
Segundo Ohno (1988), a Toyota inverteu o tradicional sistema de produção empurrado pelo sistema de produção puxado. A ordem de produção vai para o final da montagem de veículos, indicando a quantidade e modelo de veículos necessários, esta por sua vez requisitará os componentes necessários para as operações anteriores, que requisitará a matéria-prima necessária para a operação anterior através de um sistema kanban de comunicação entre as áreas.
Figura 8 – Sistema de produção puxado x Sistema de produção empurrado
FONTE: Freire (2011)