
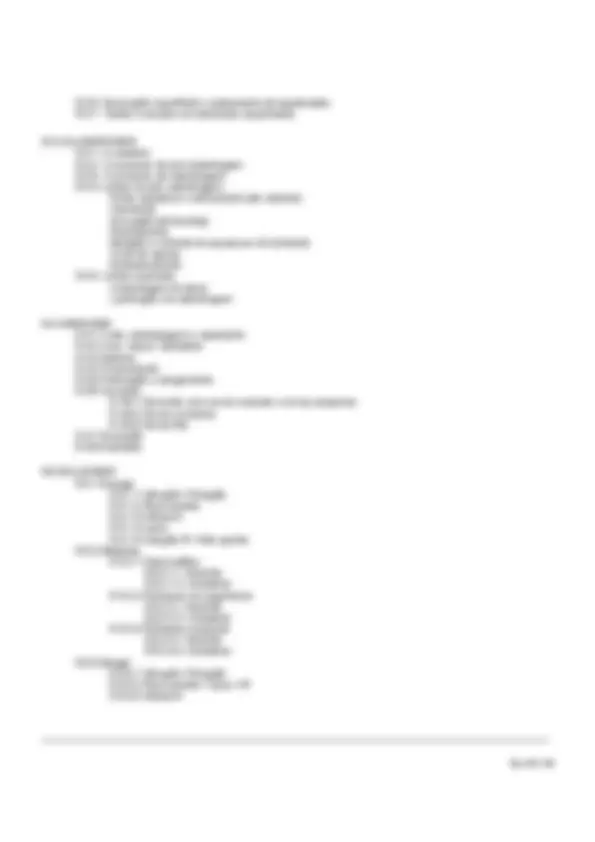
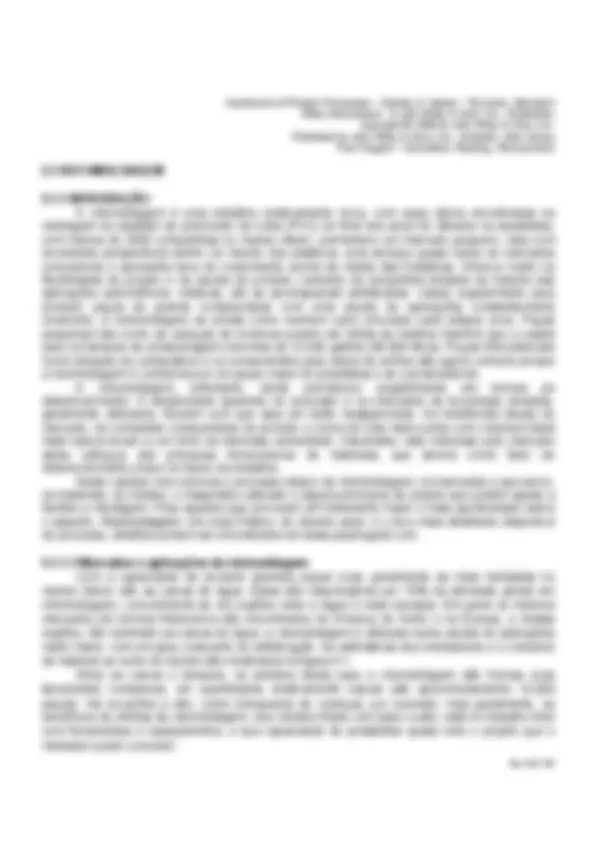
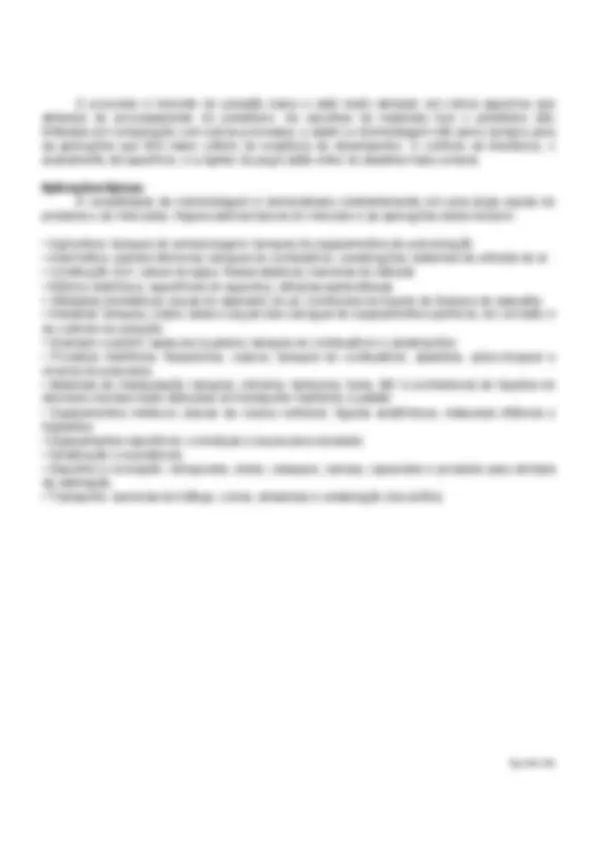
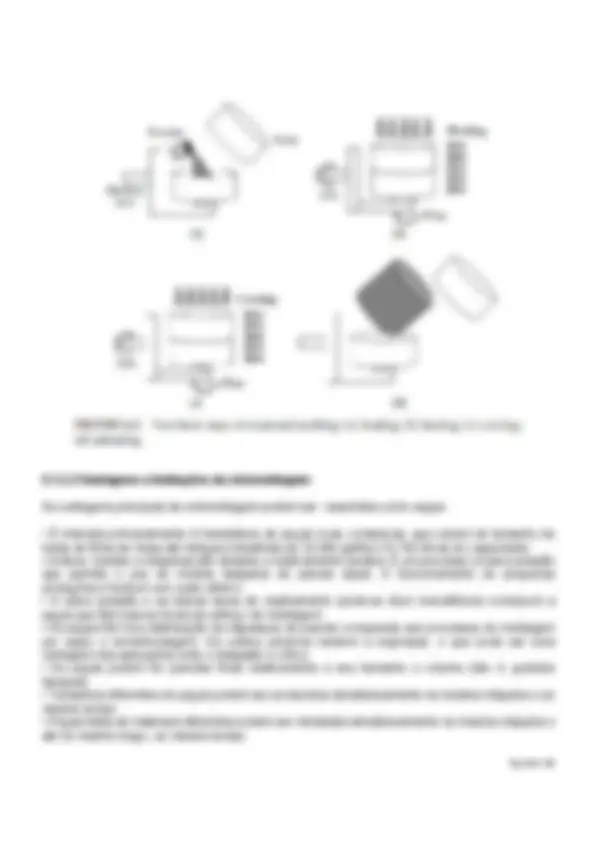
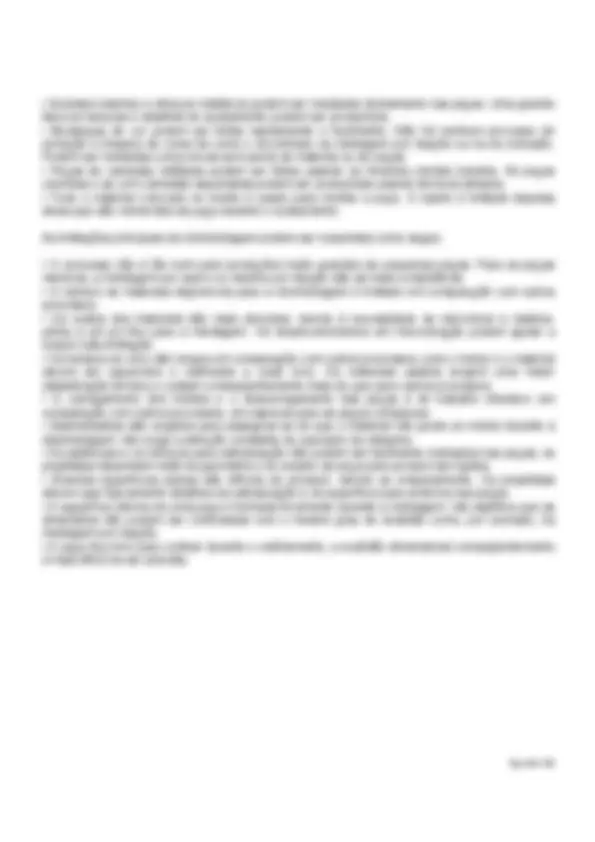
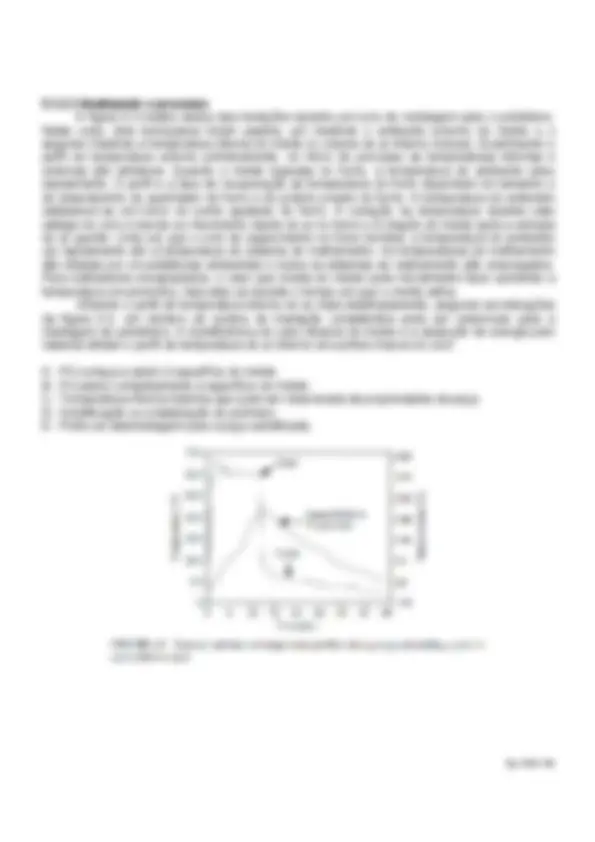
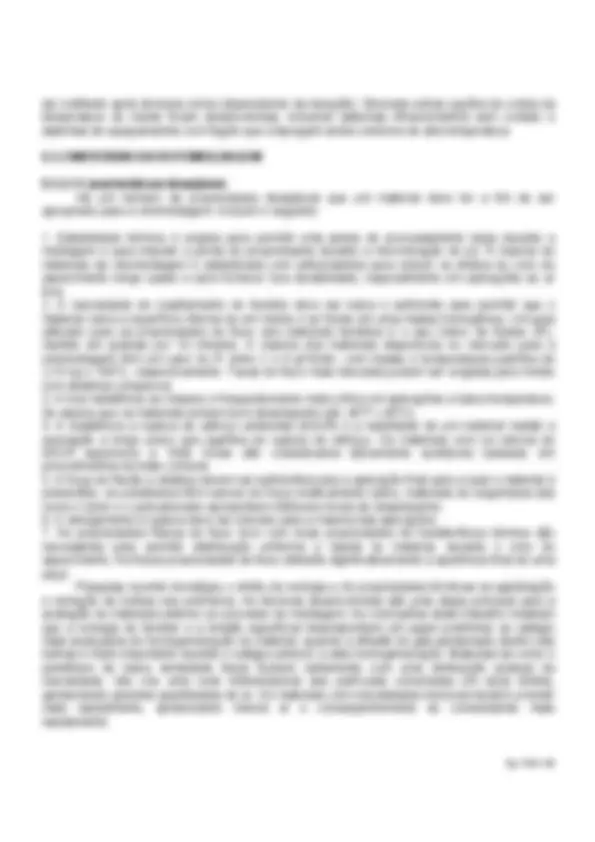
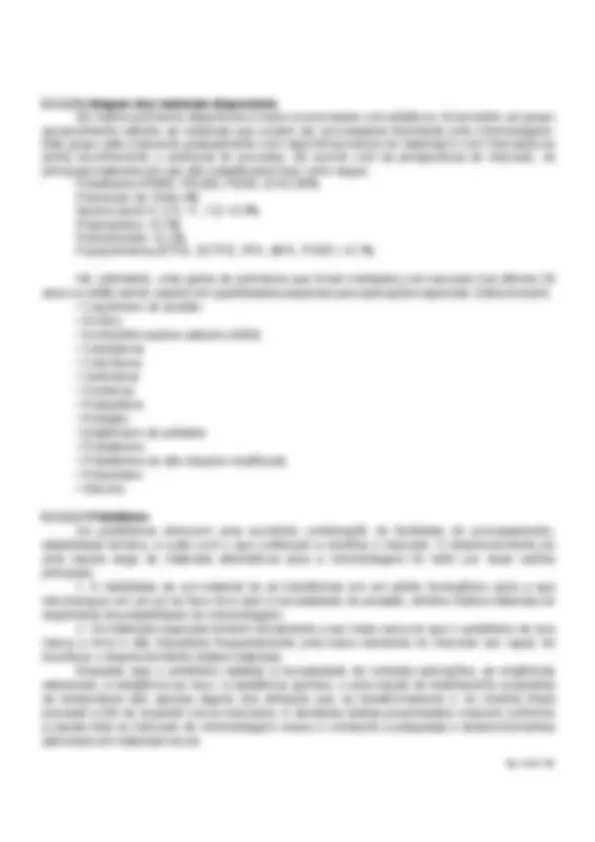
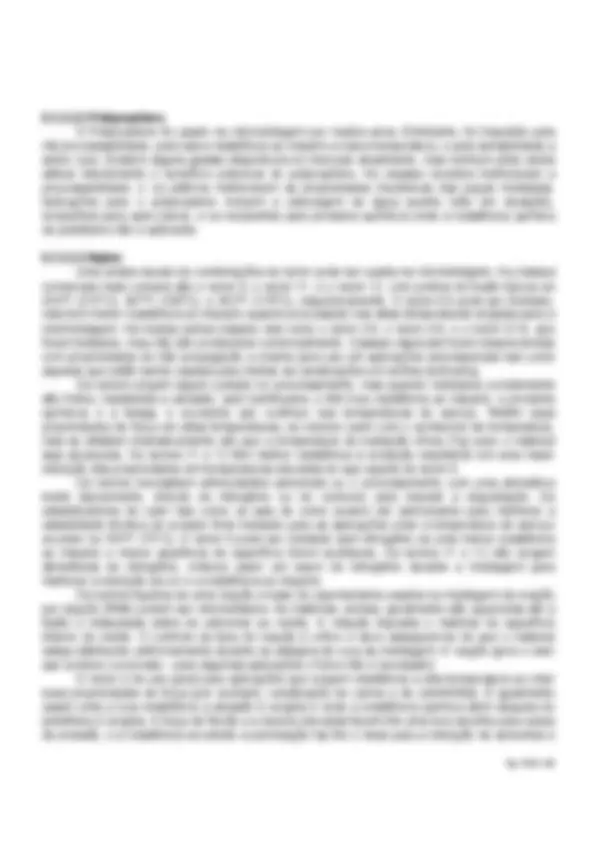
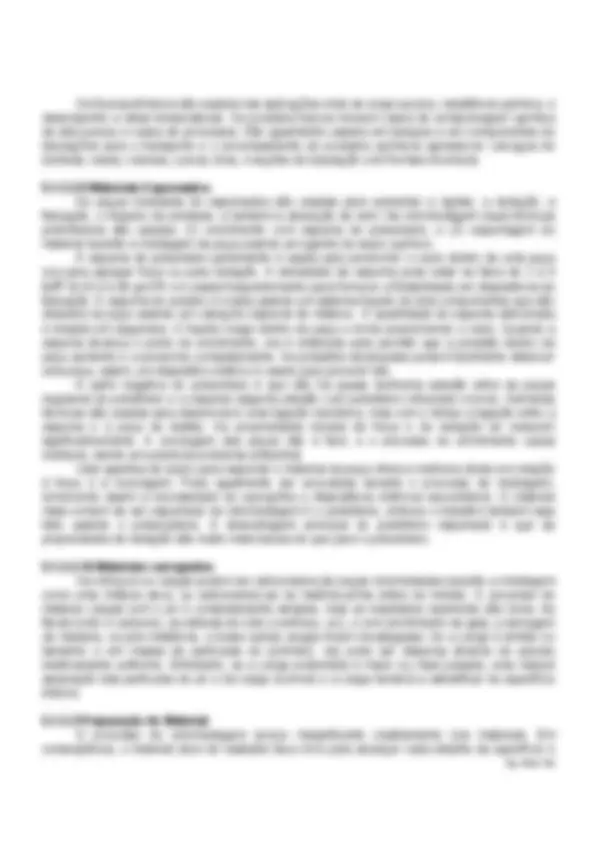
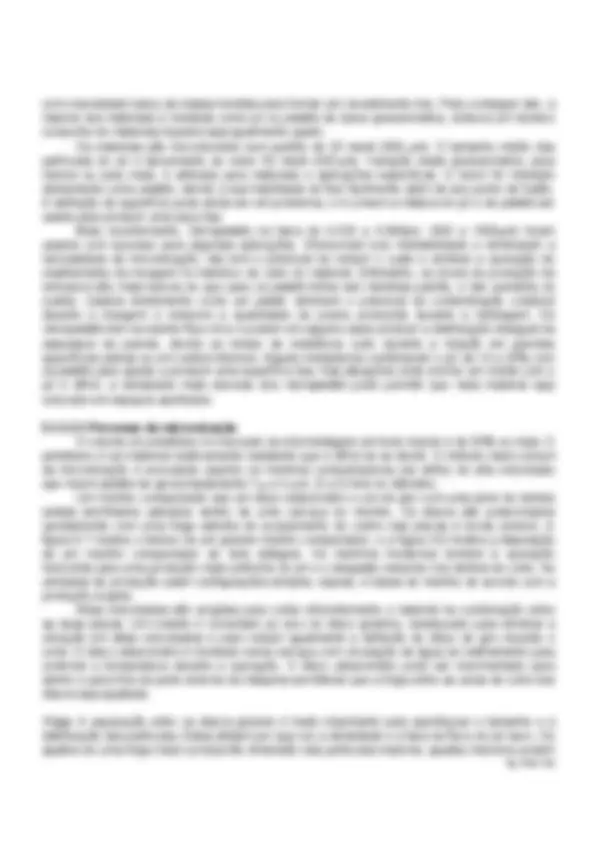
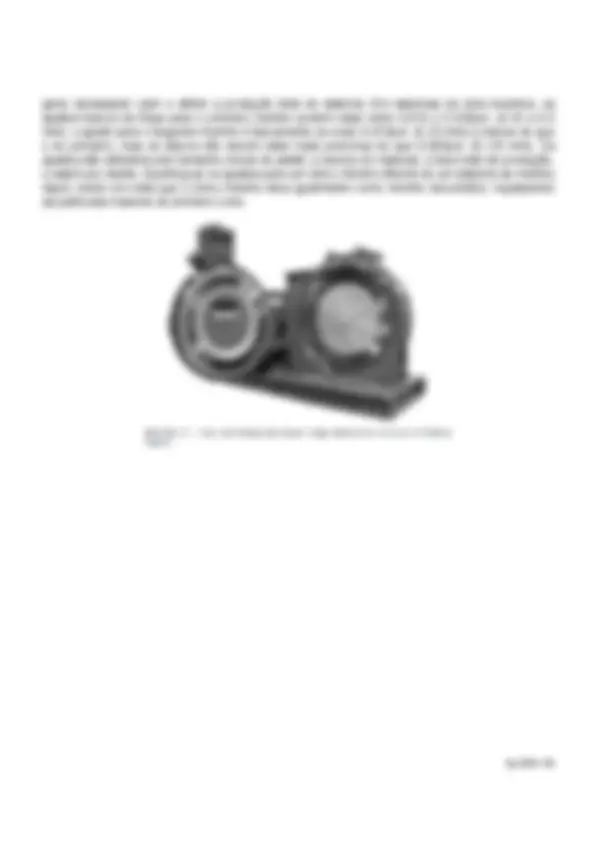
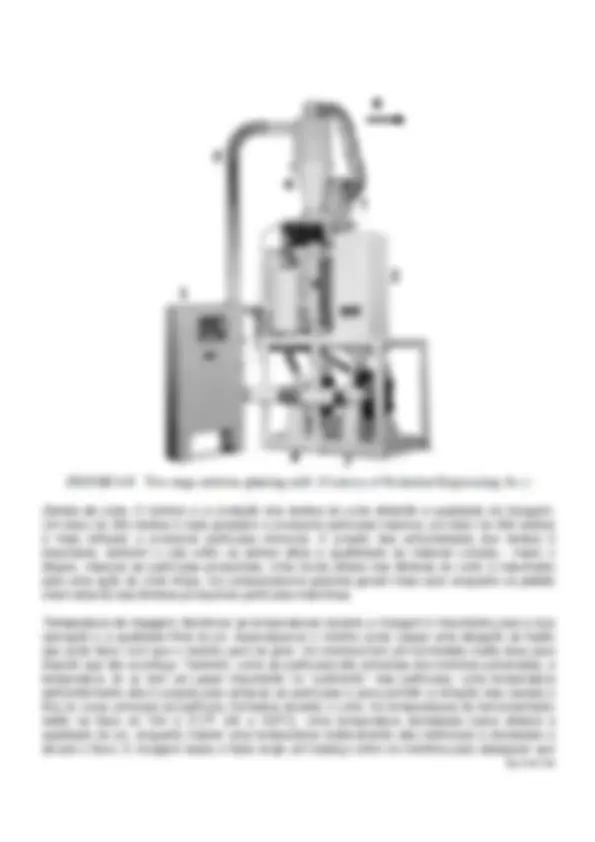
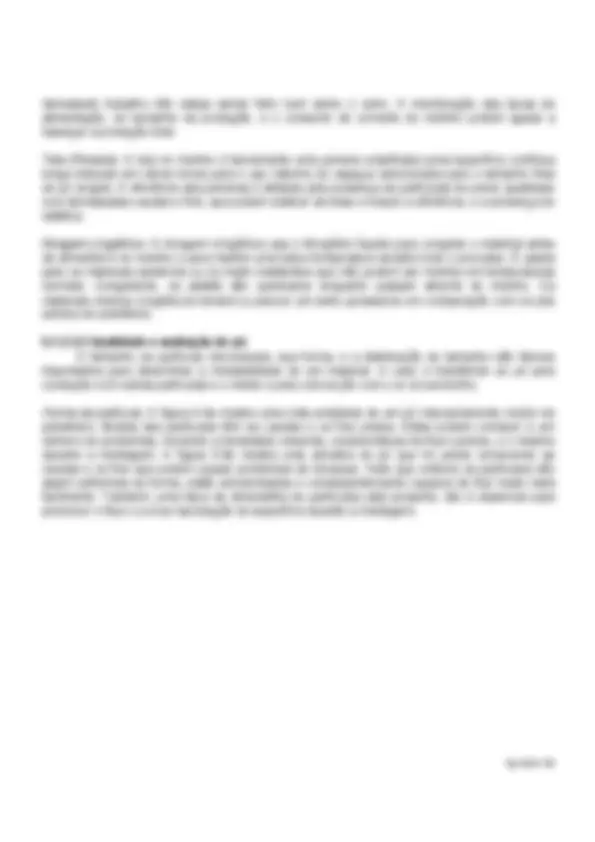
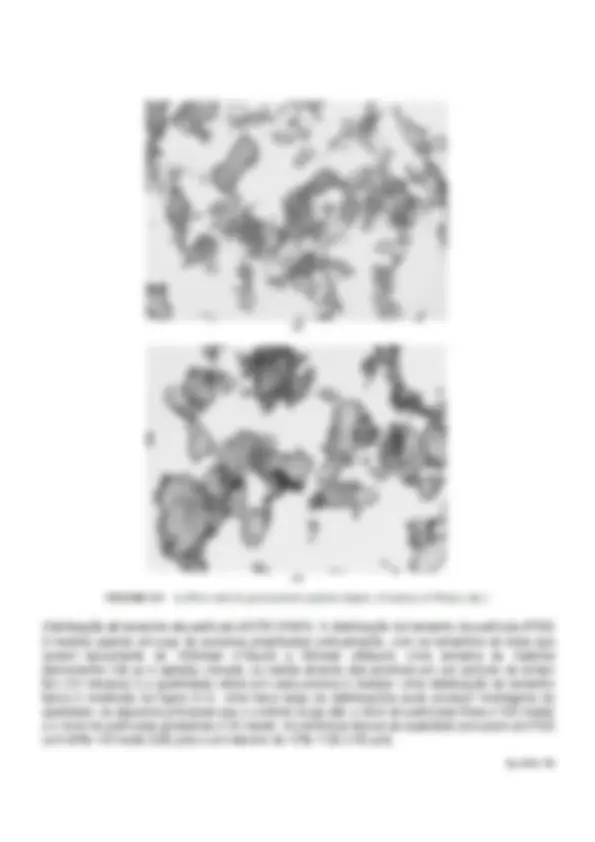
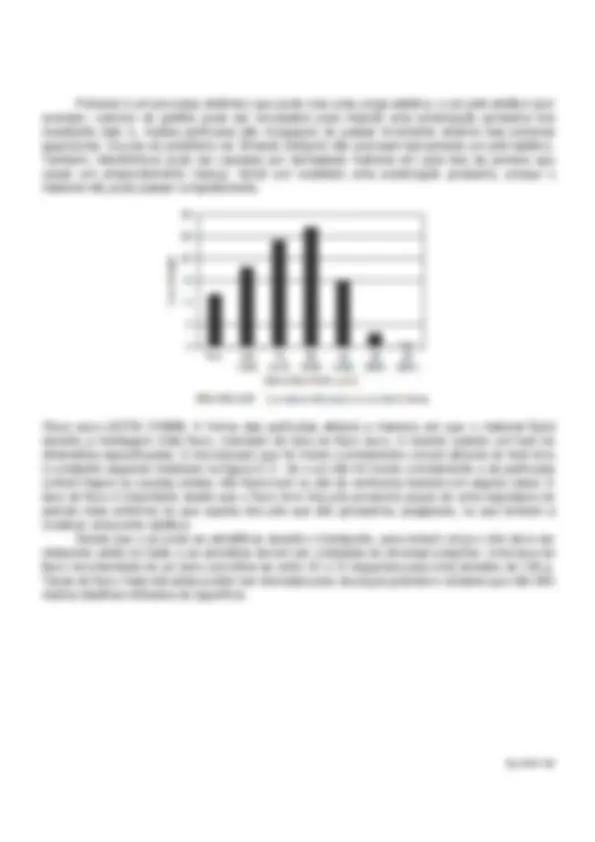
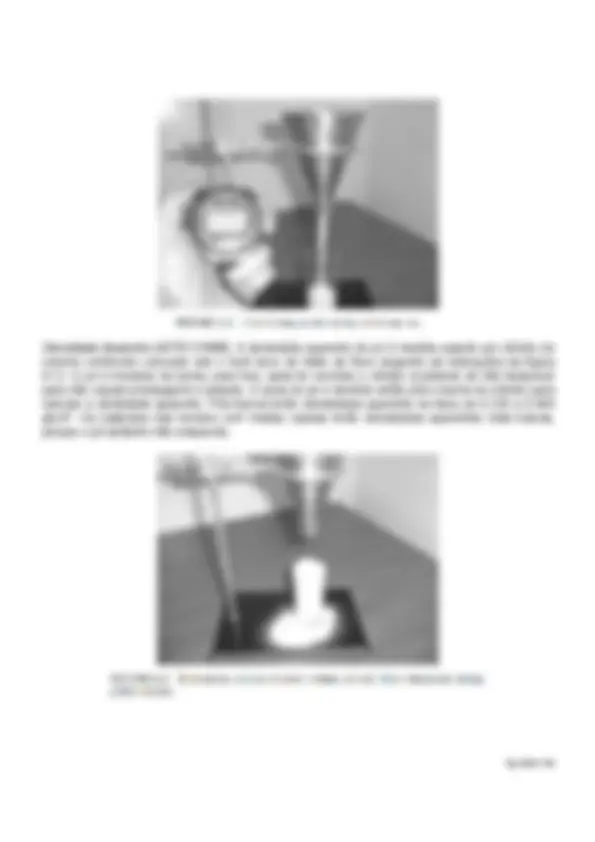
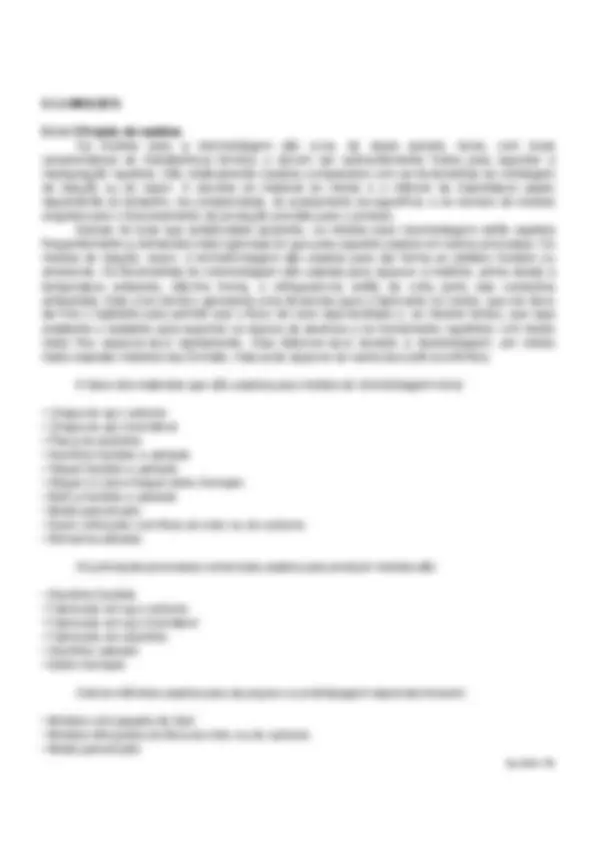
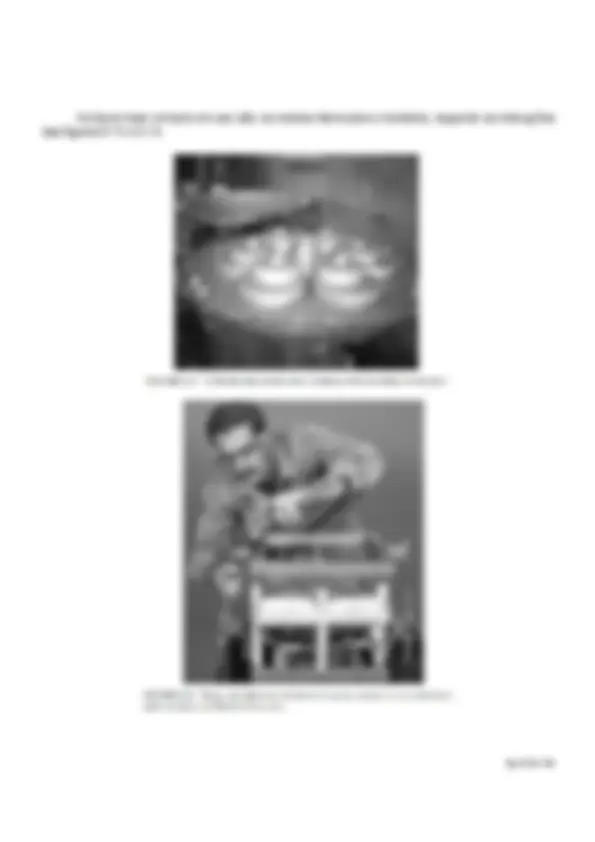
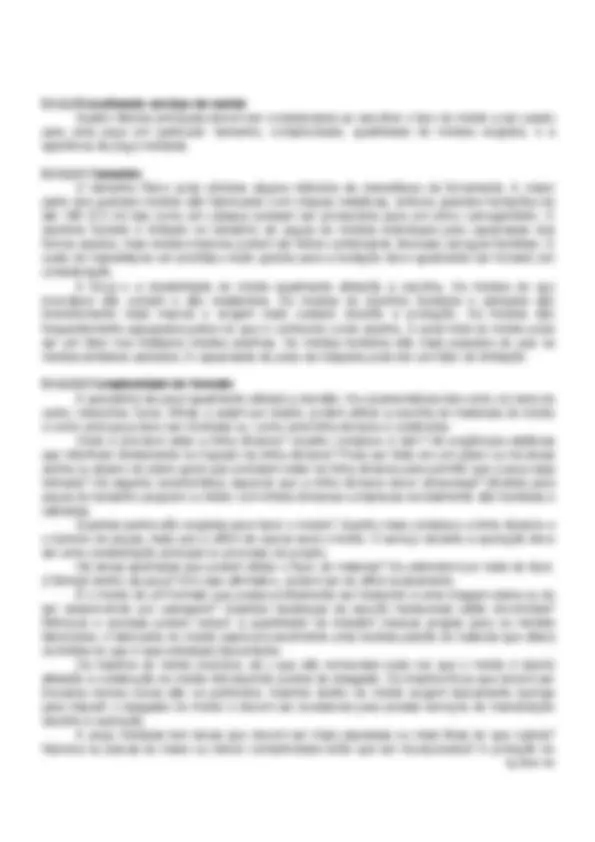
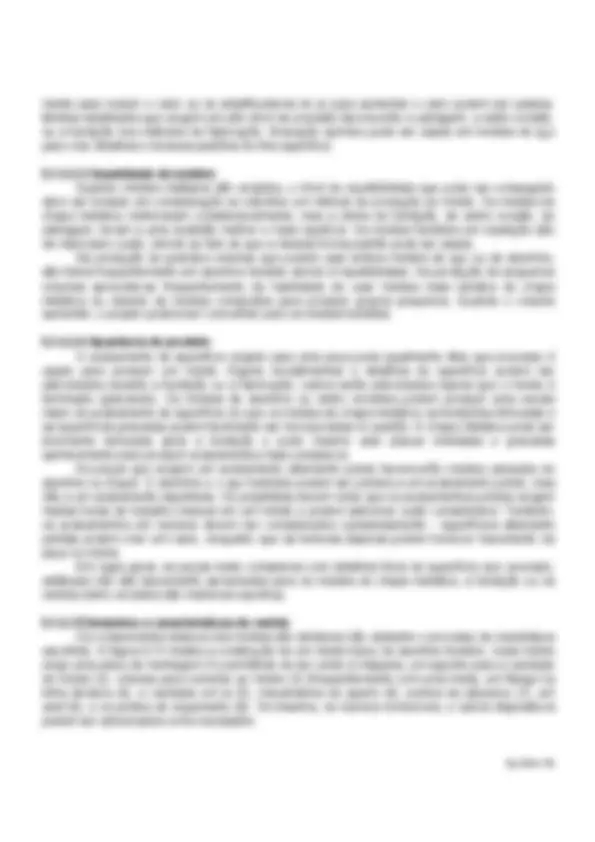

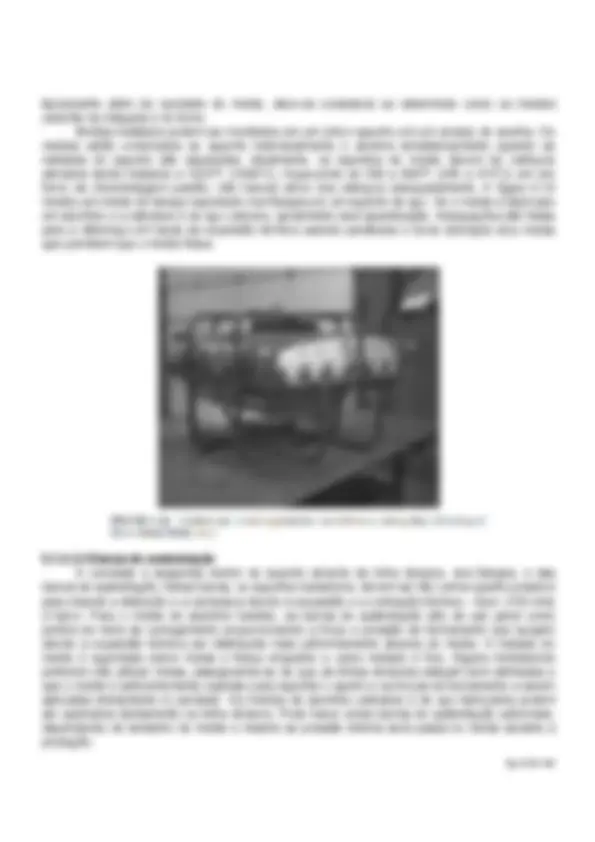
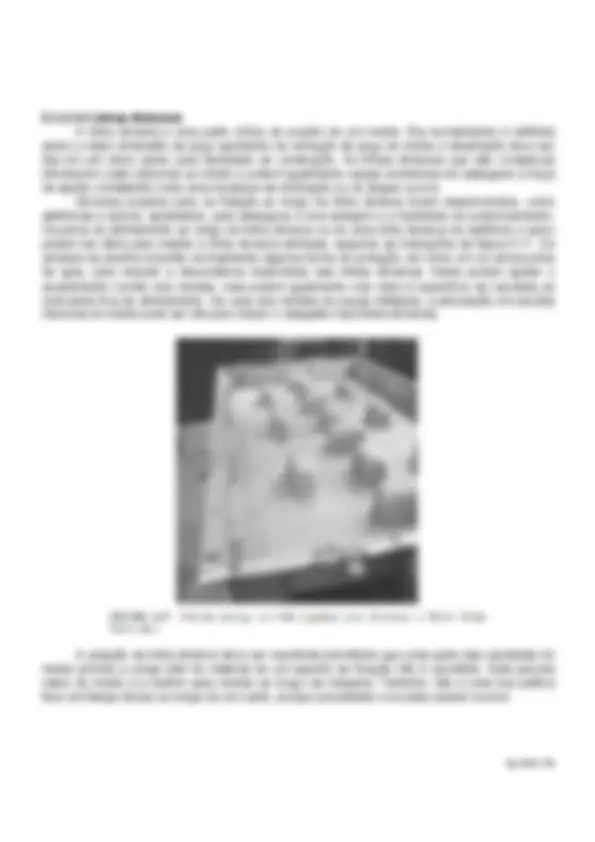
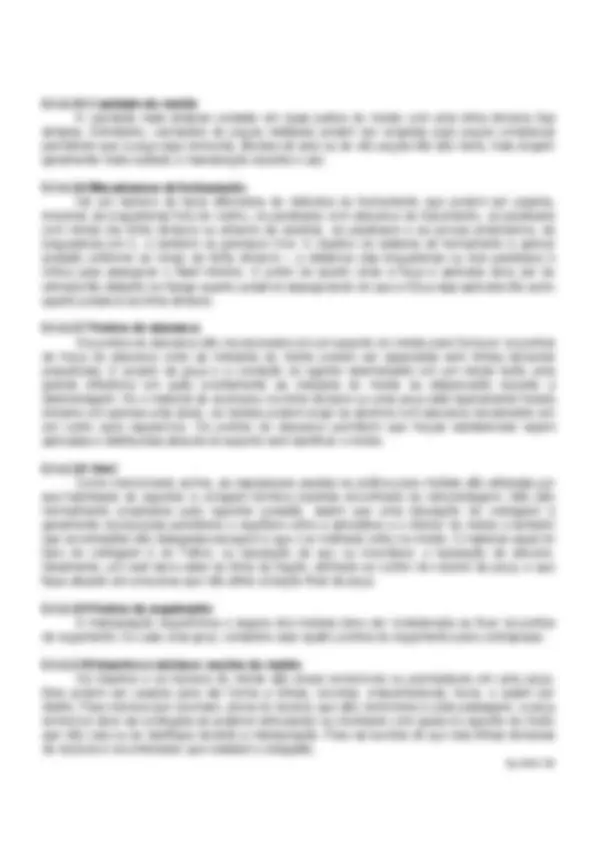
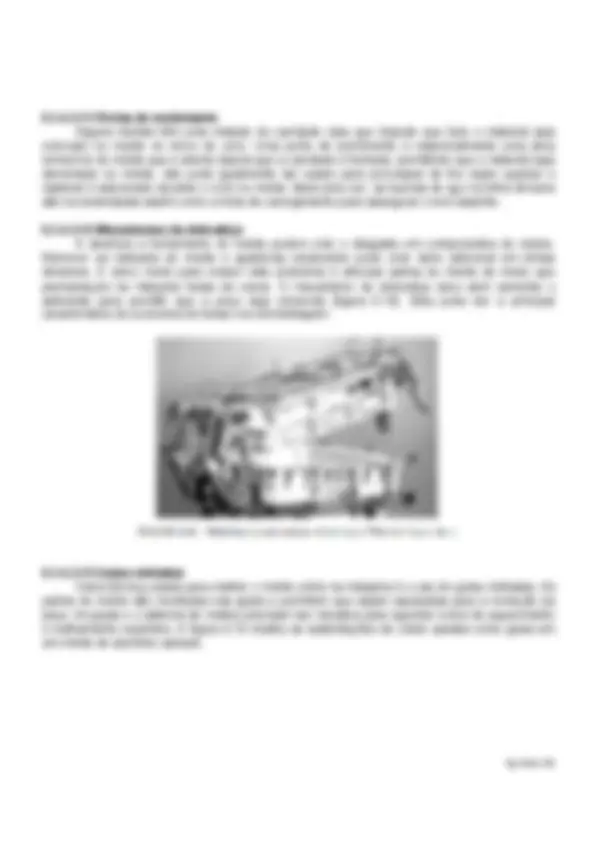
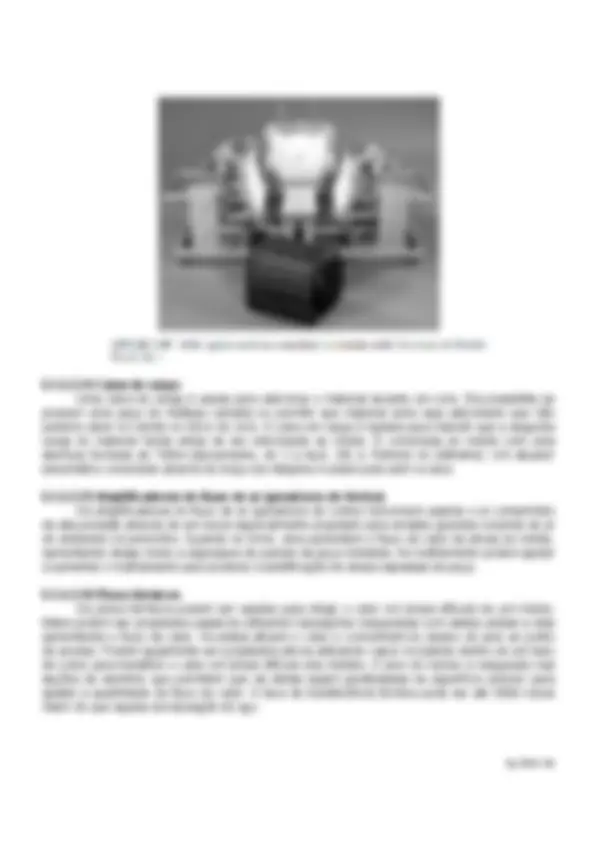
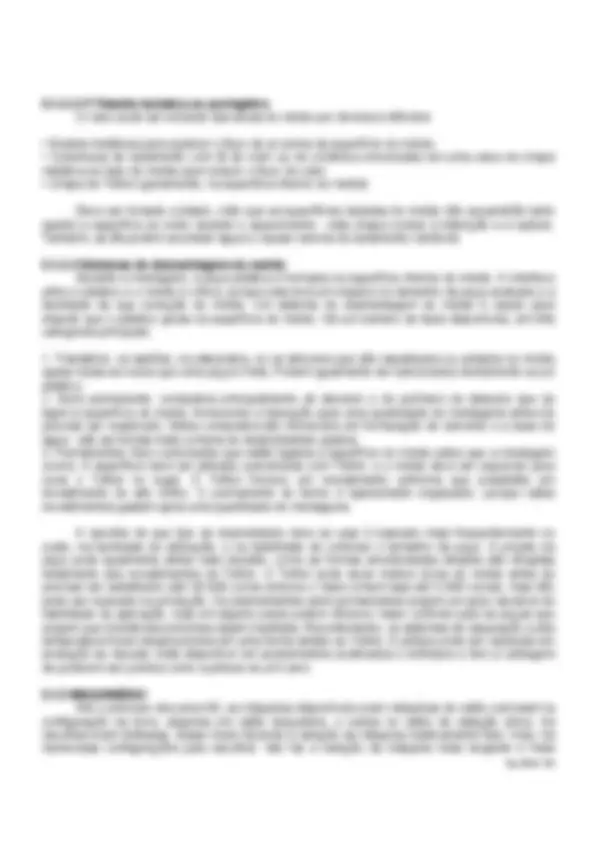
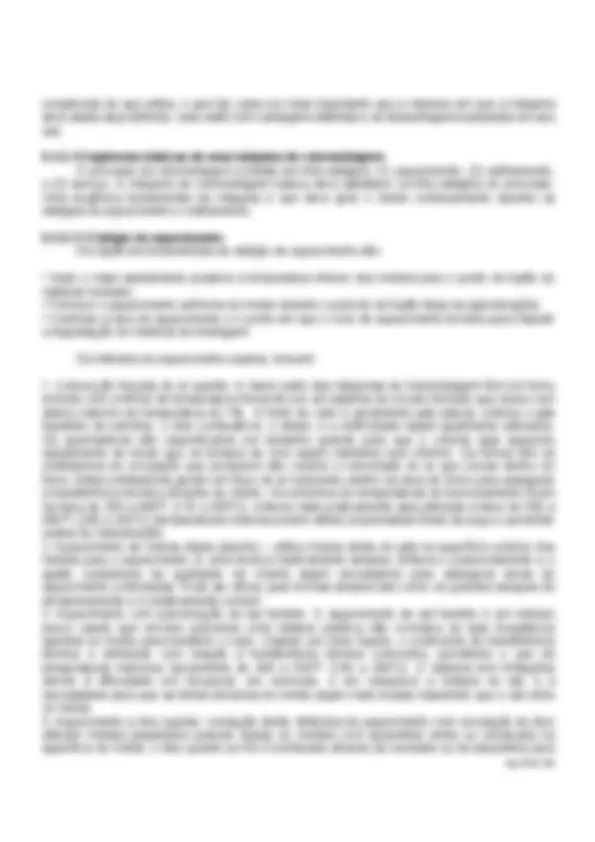
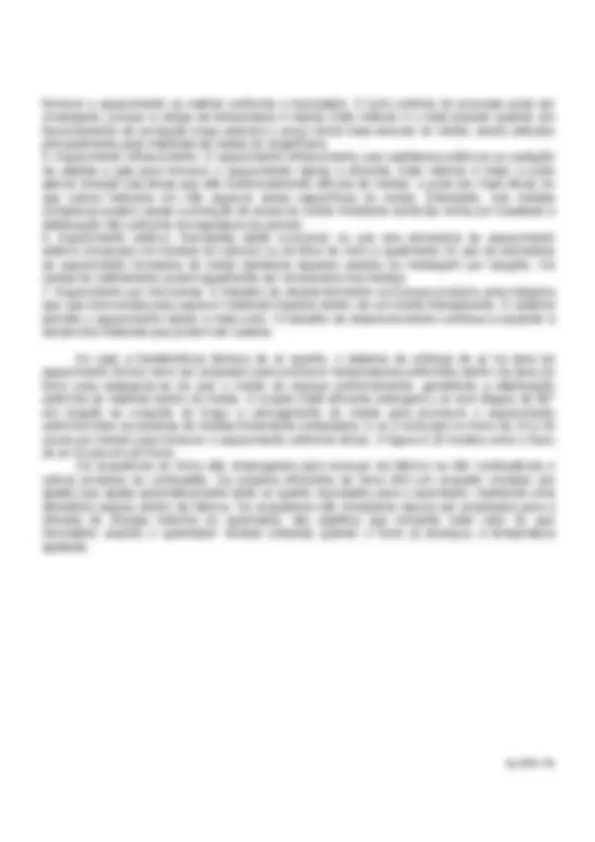
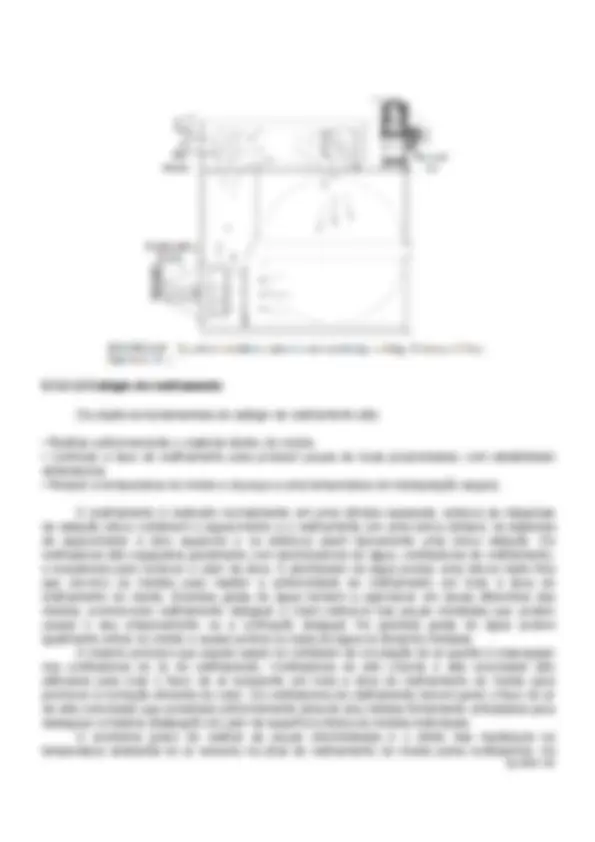
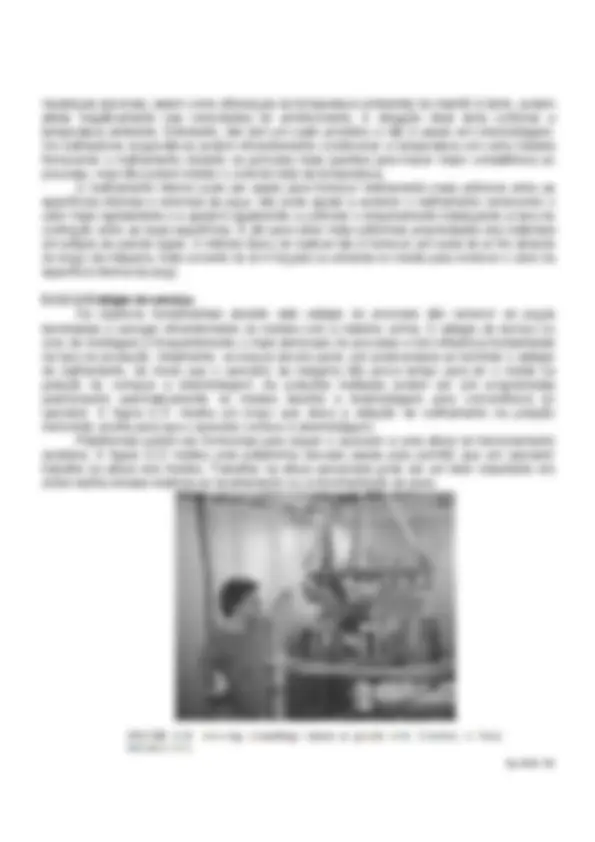
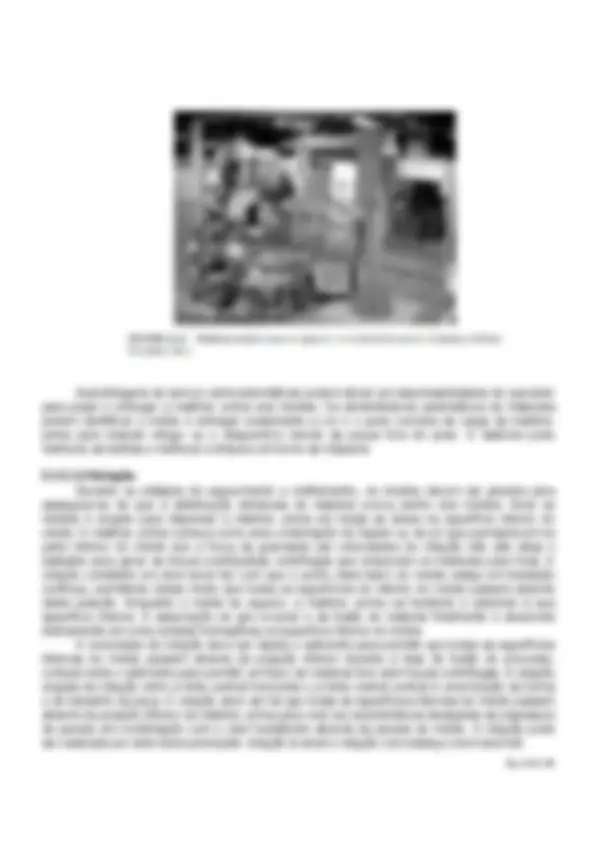
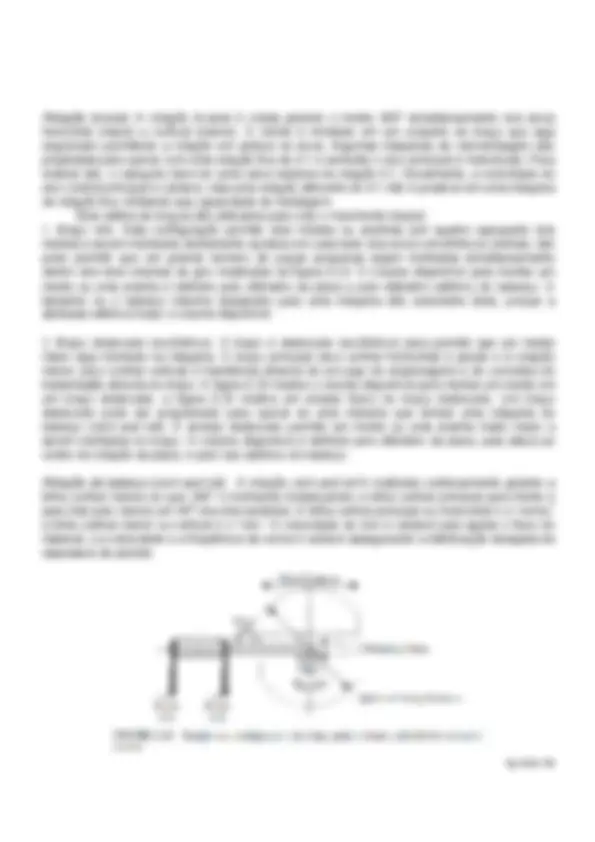
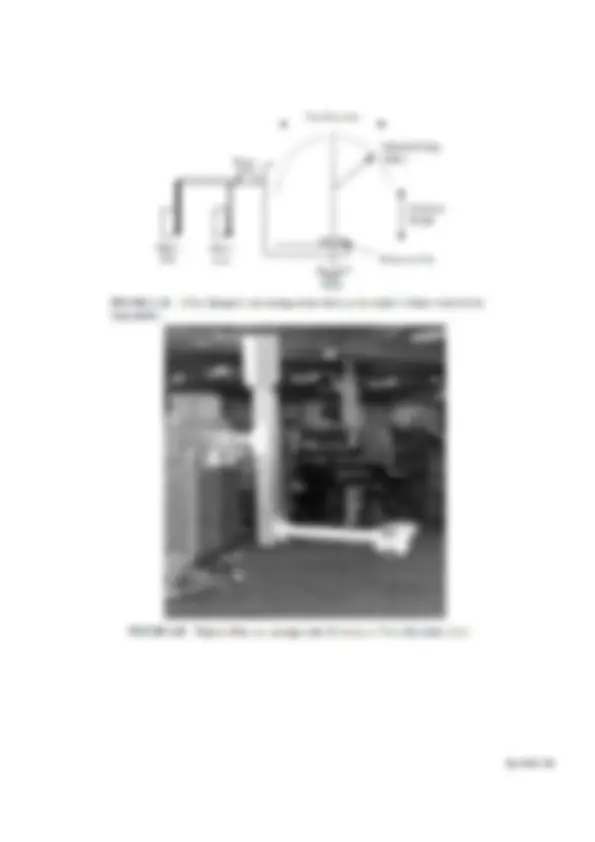
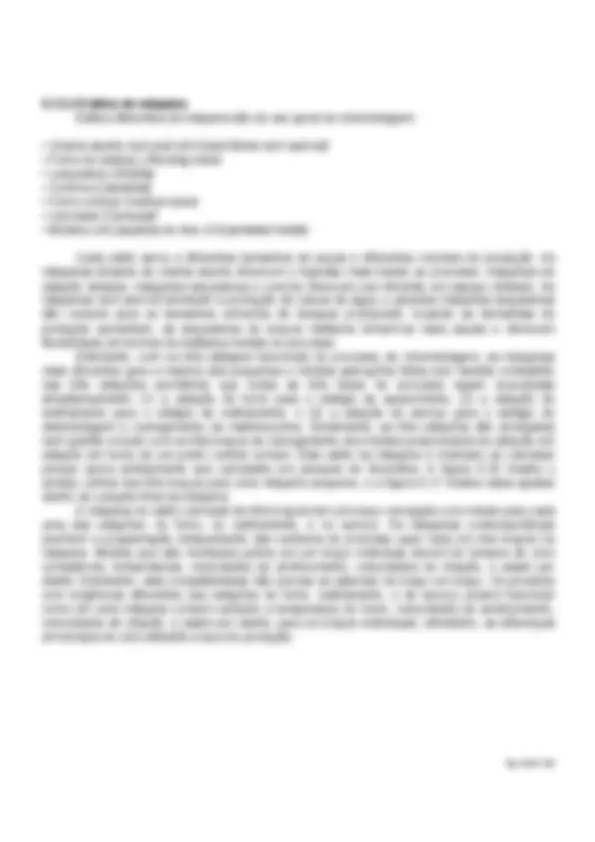
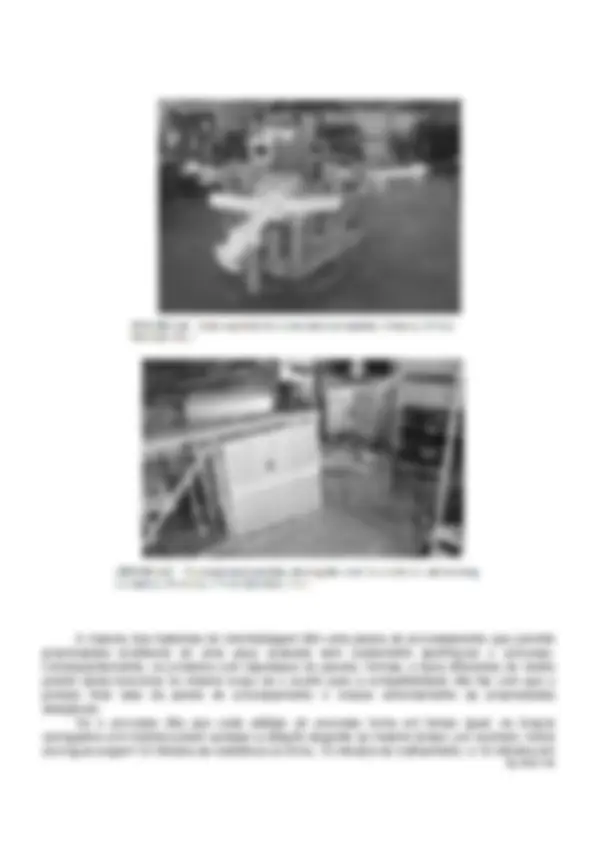
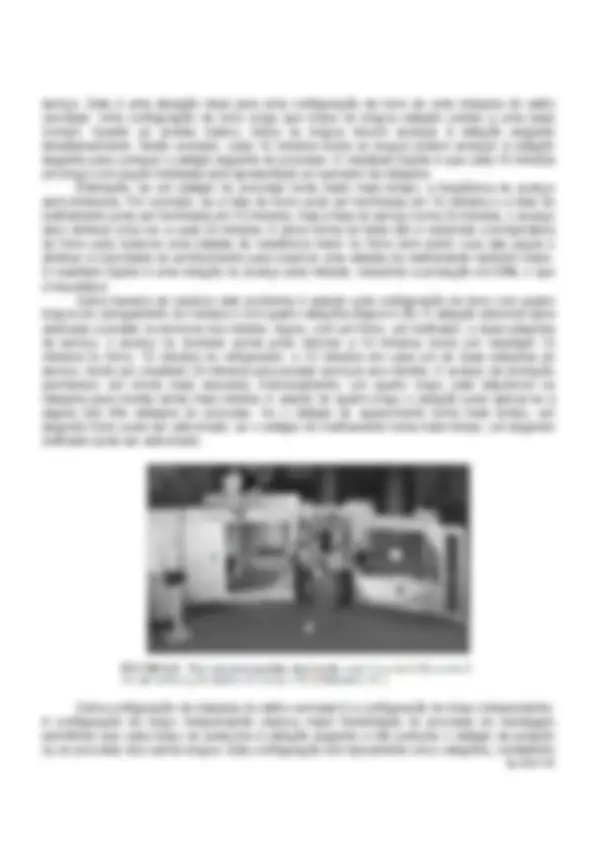
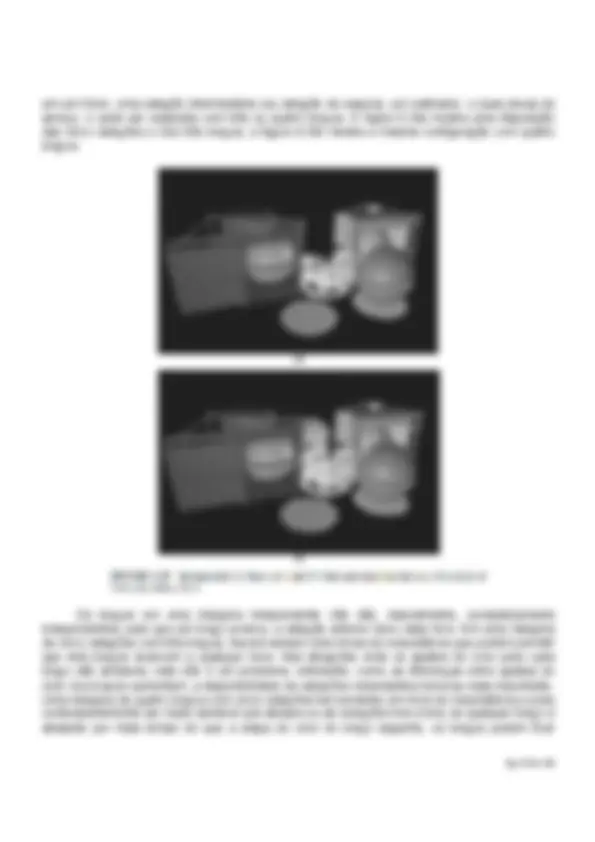
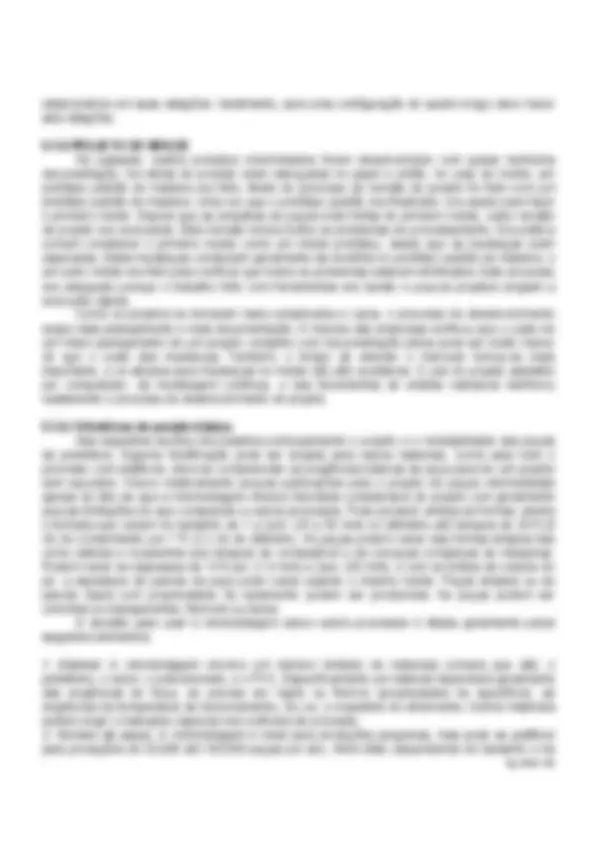
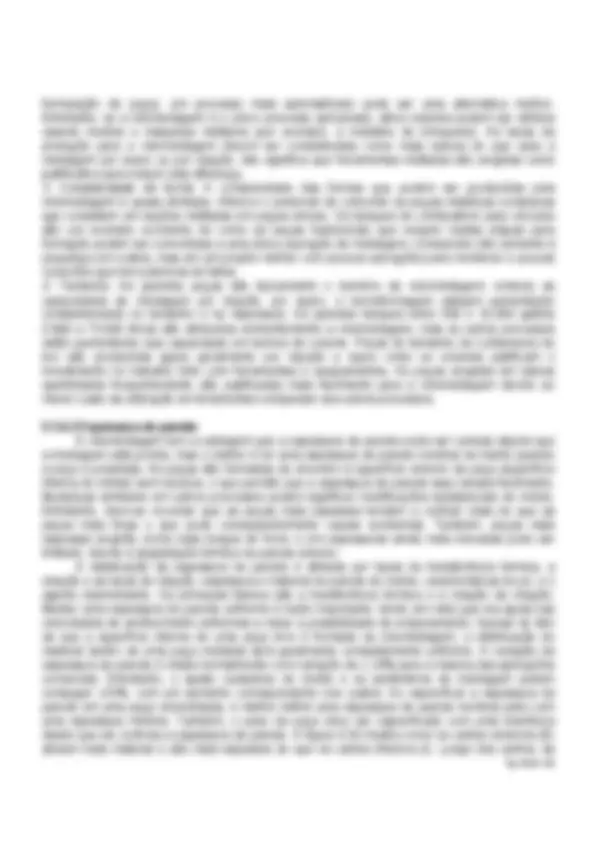
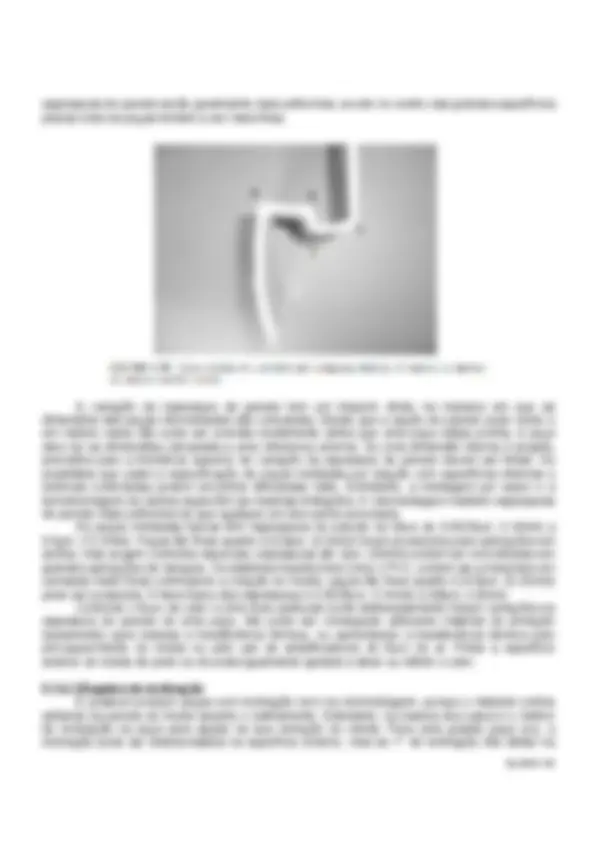
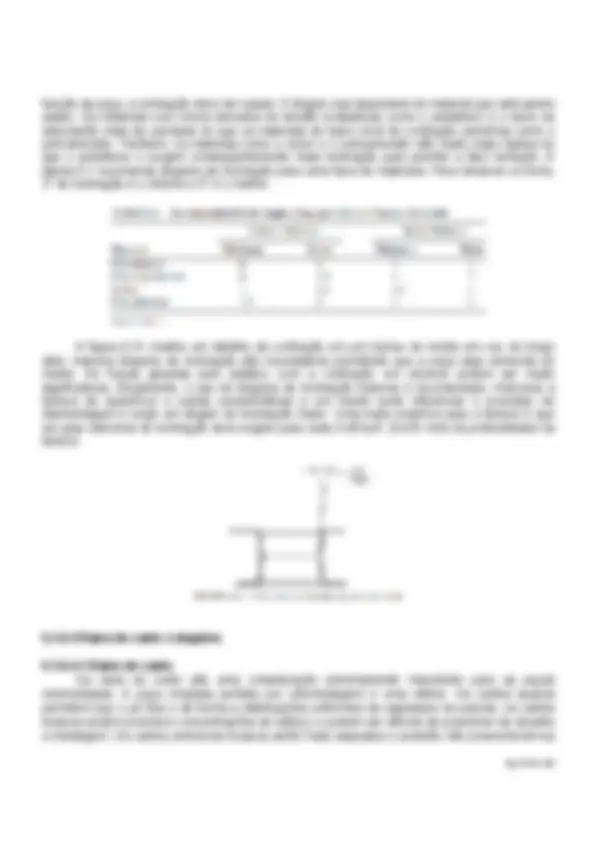
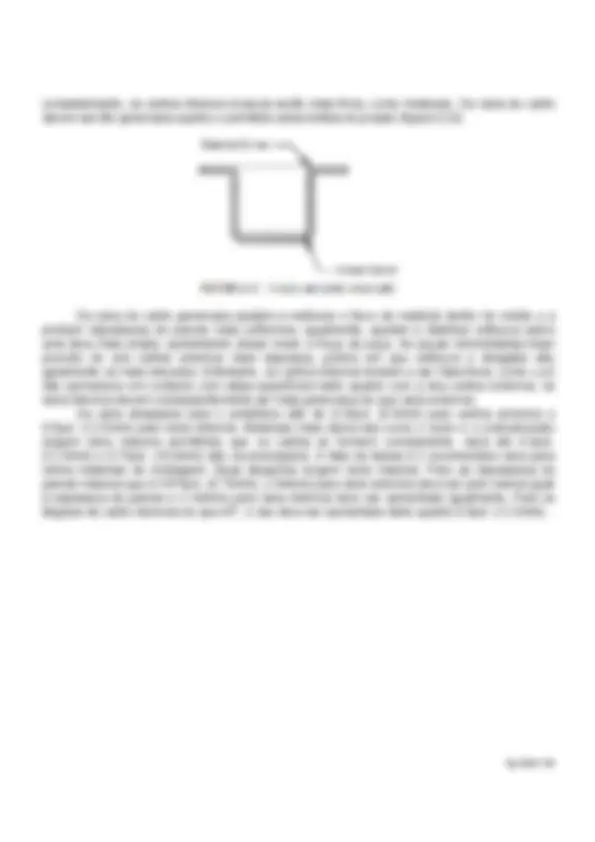
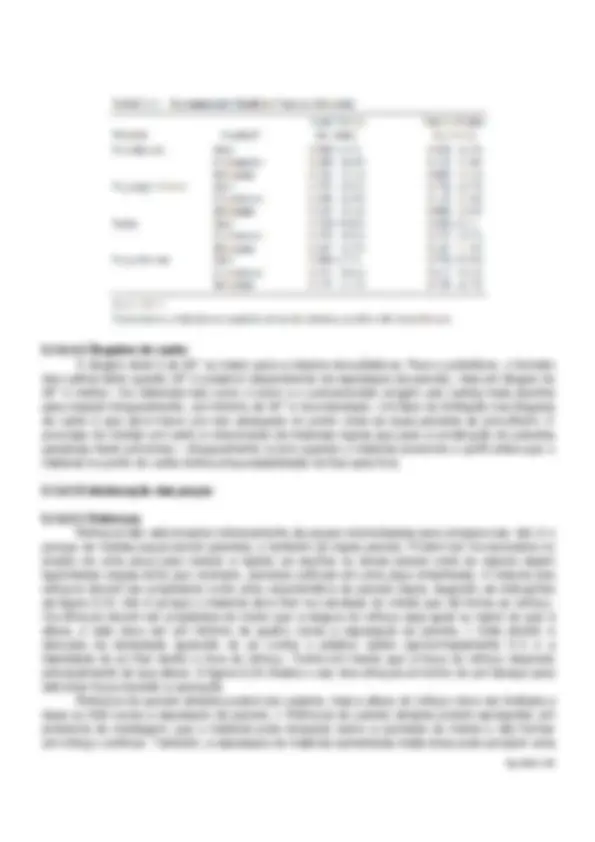
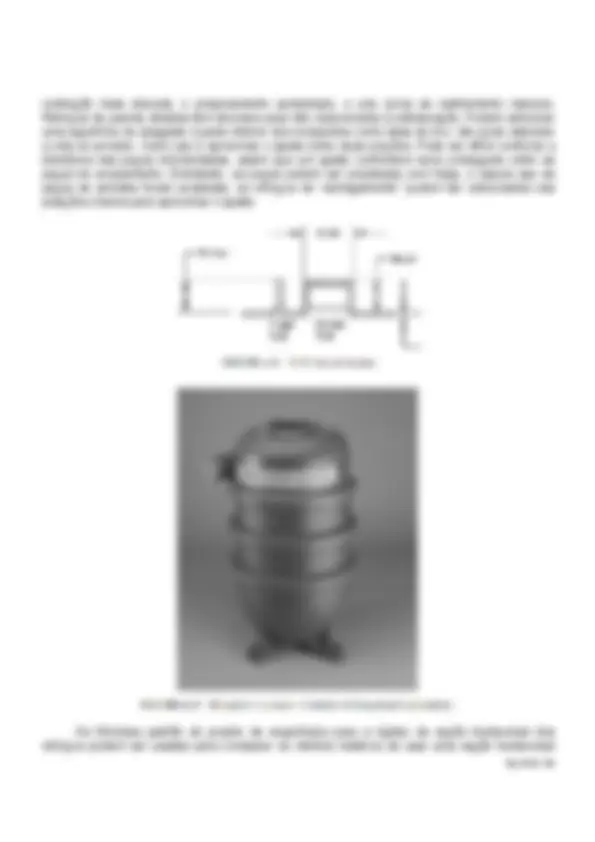
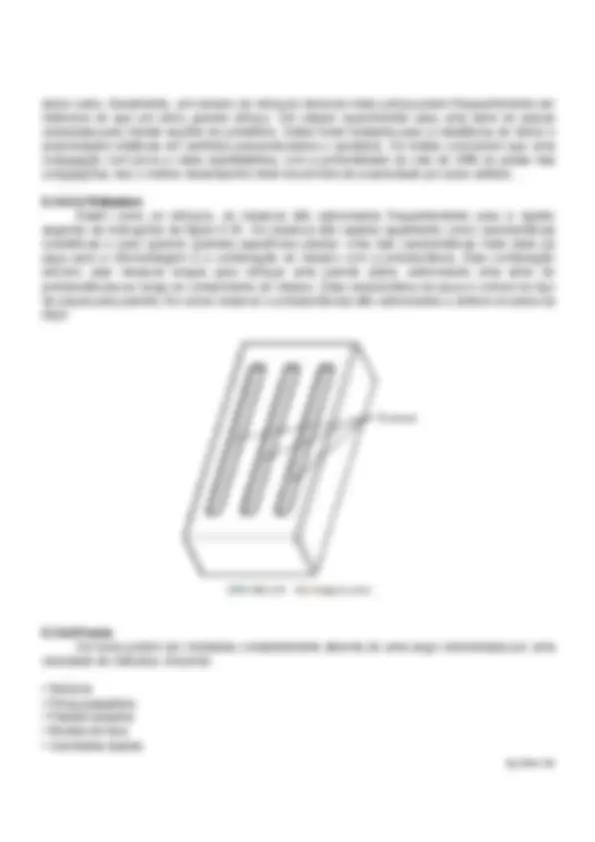
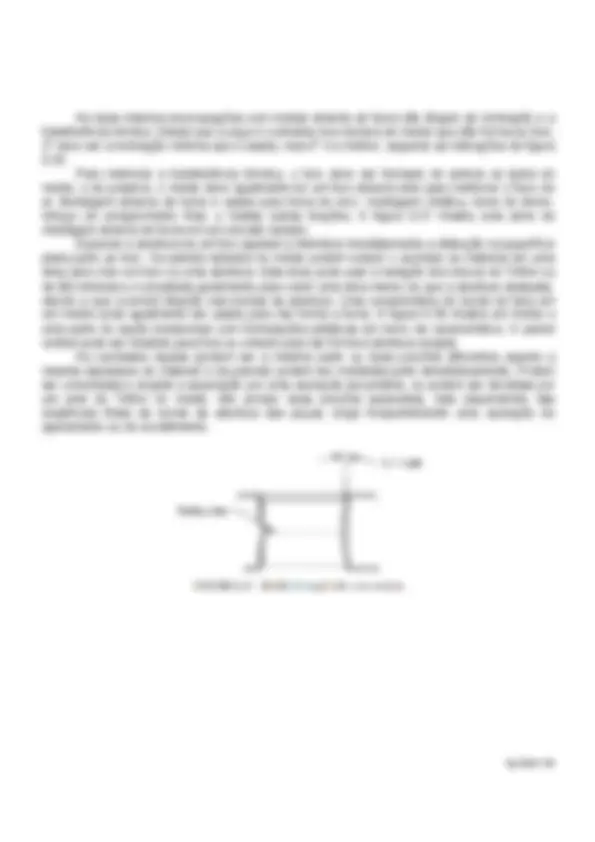
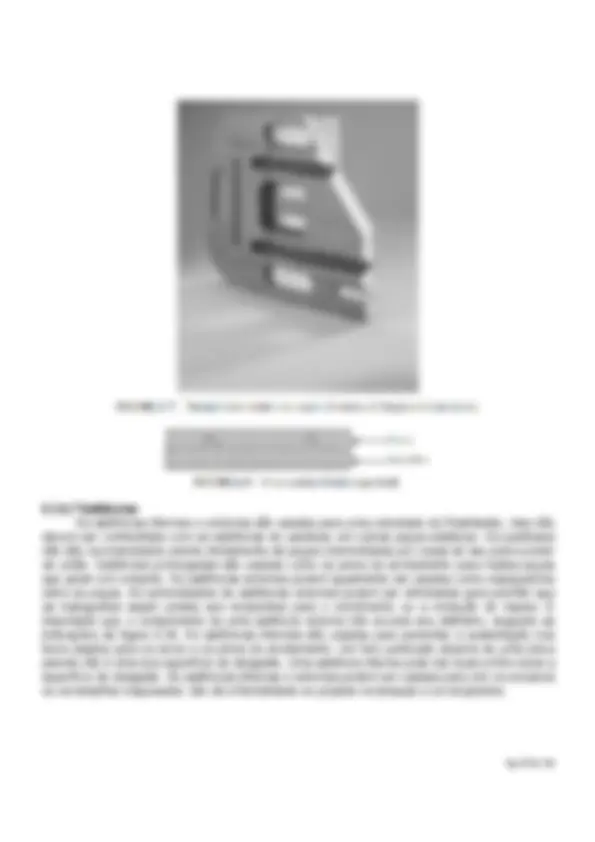
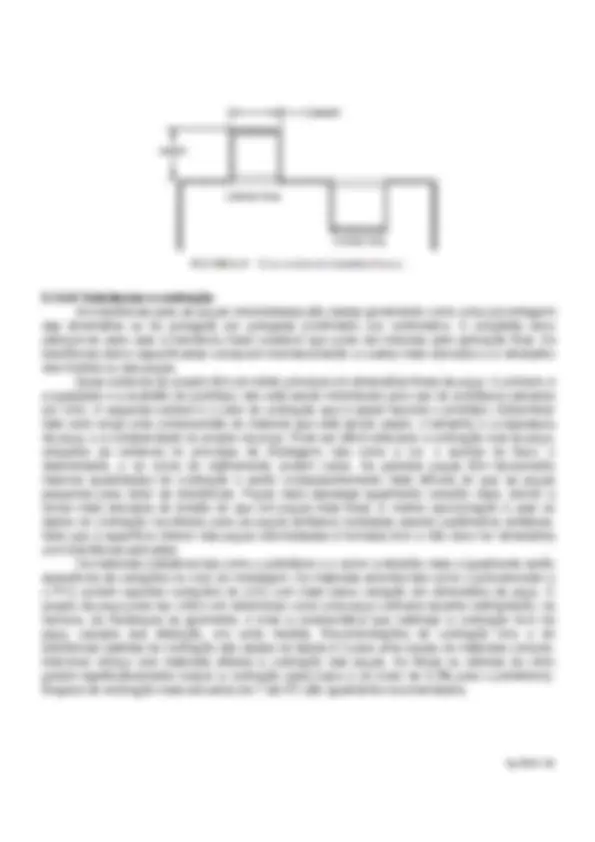
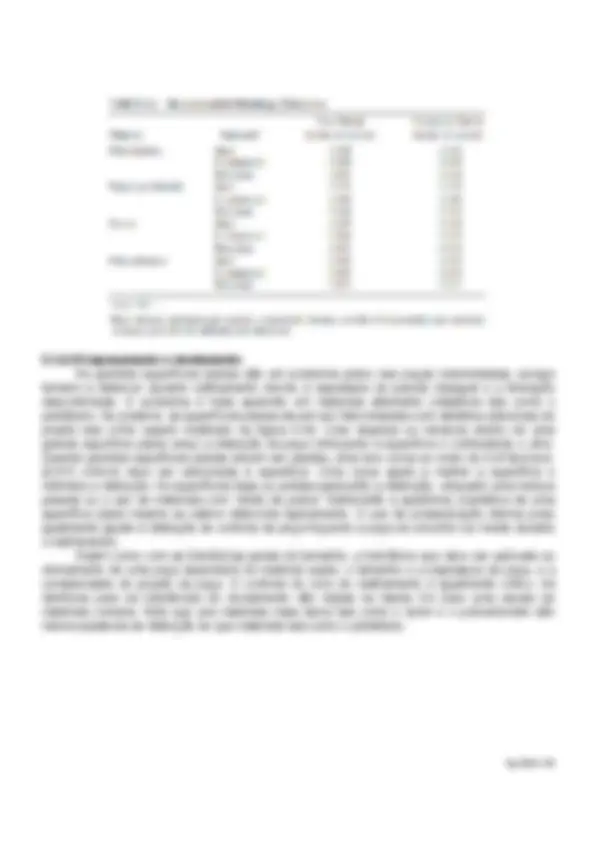
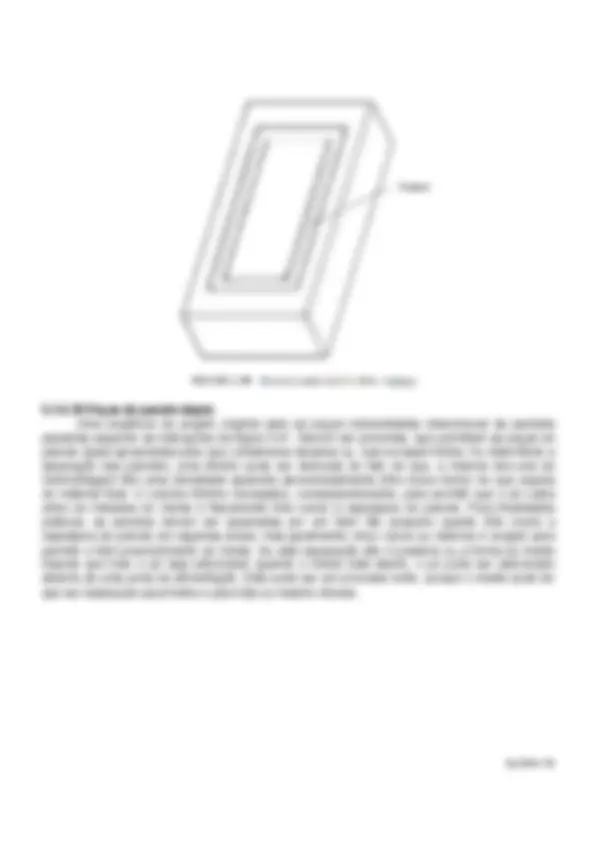
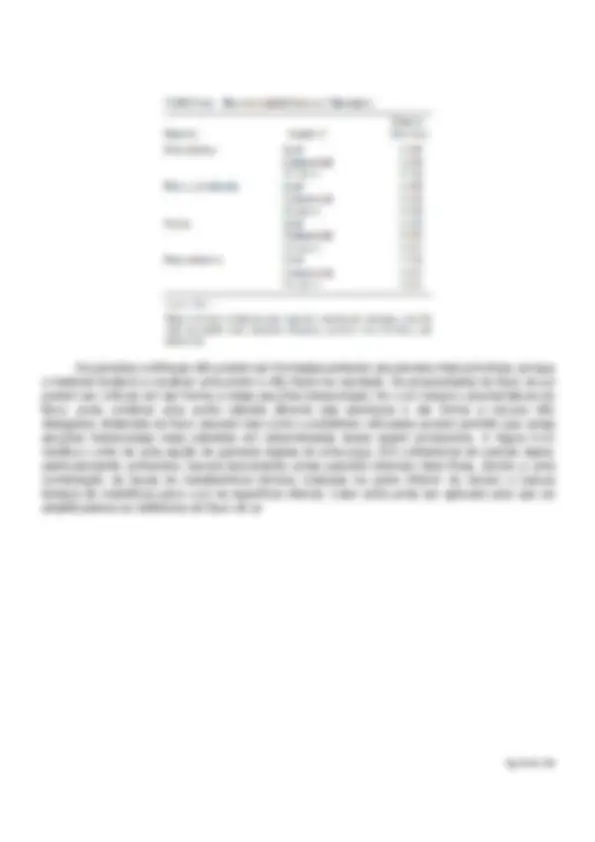
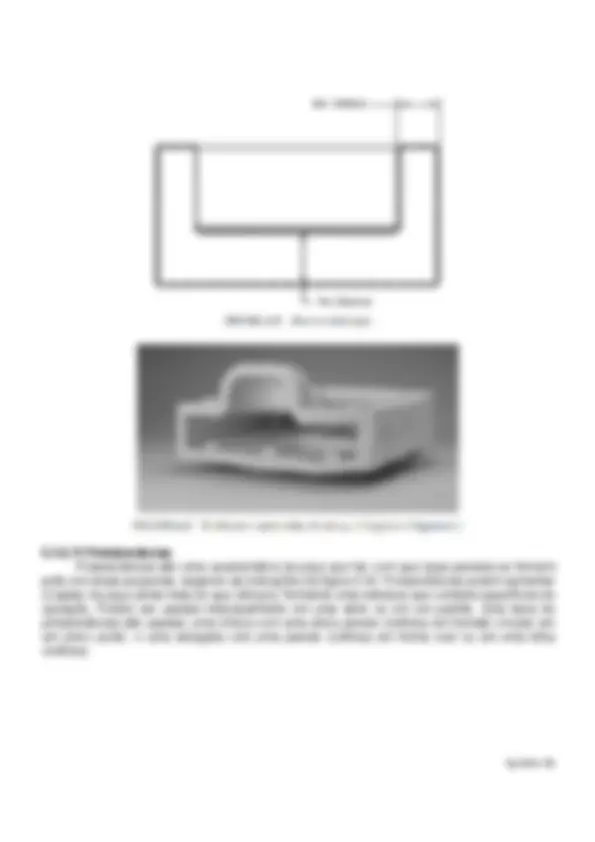
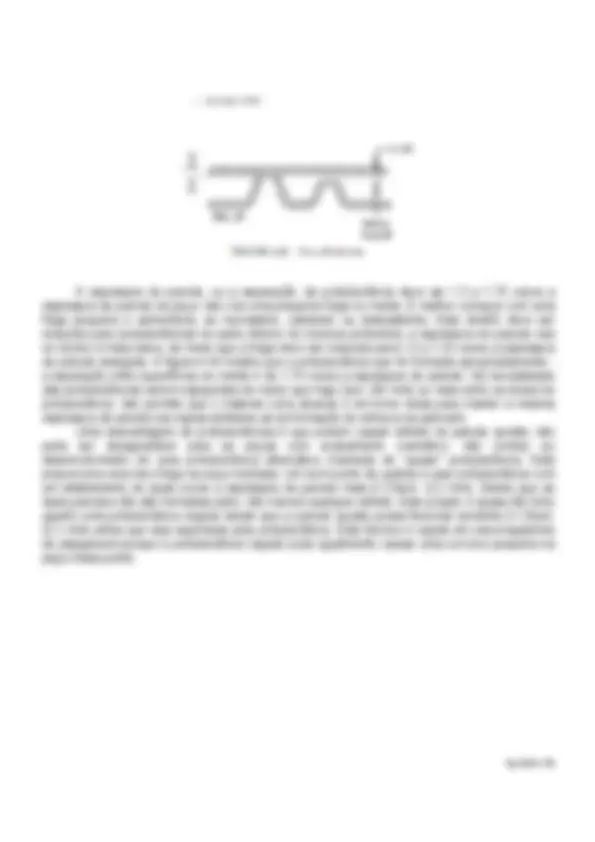

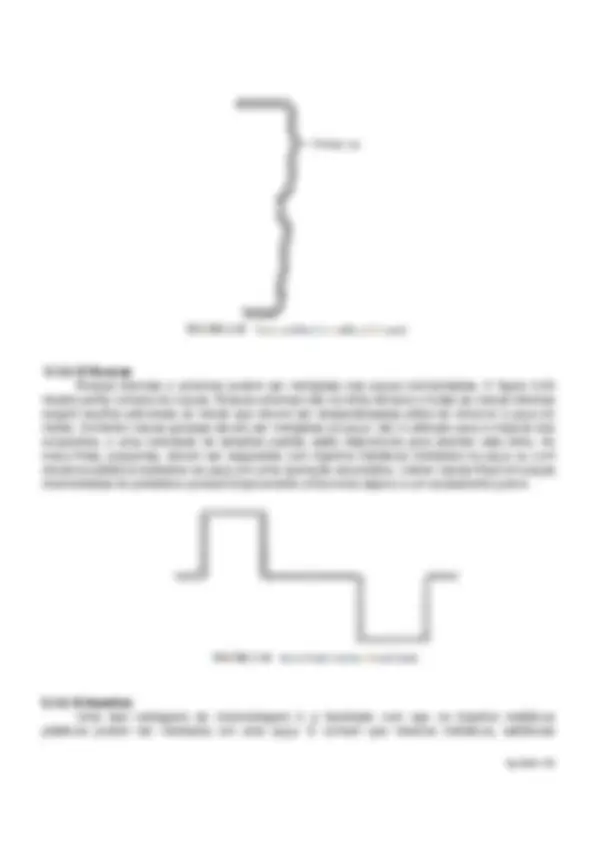
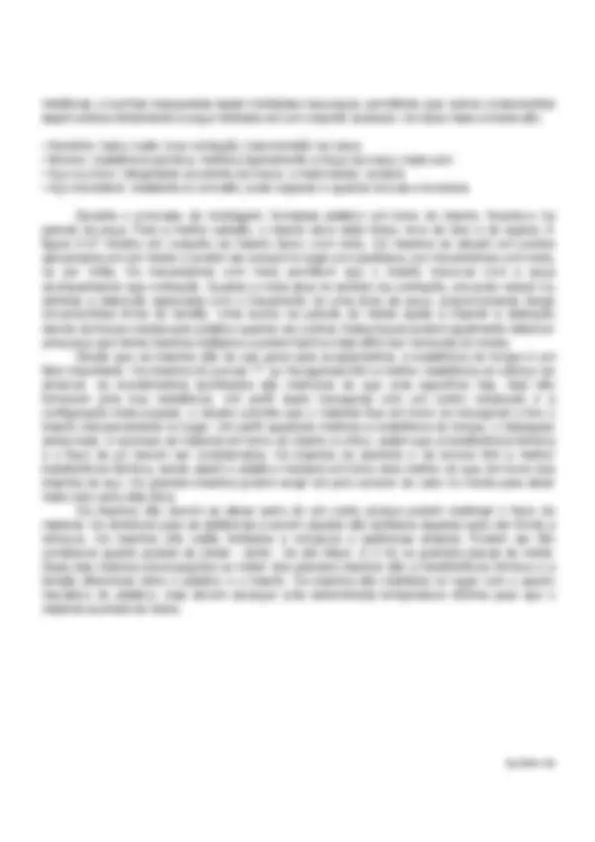
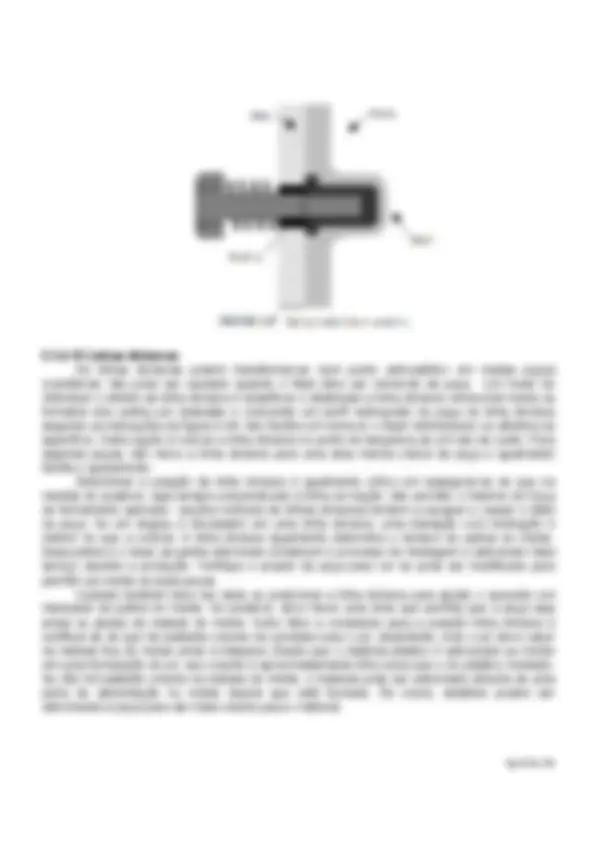
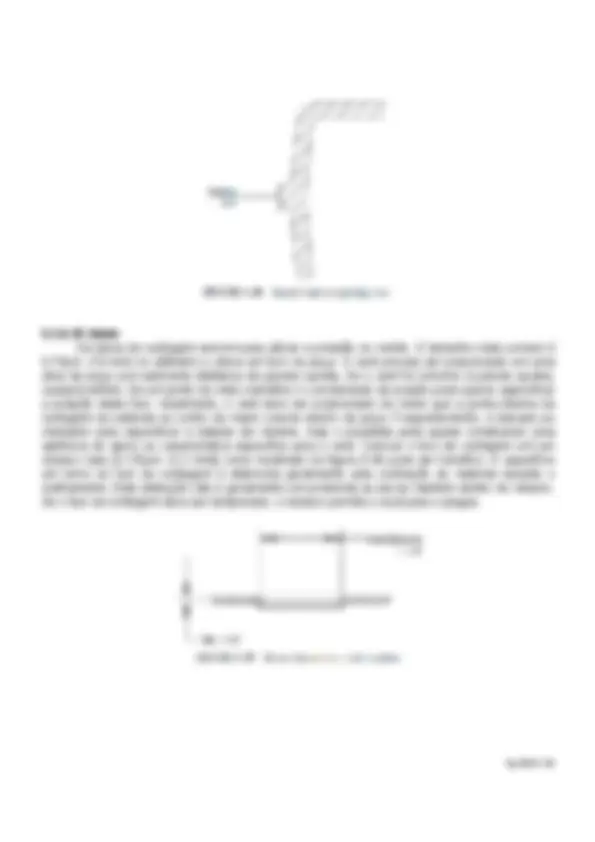
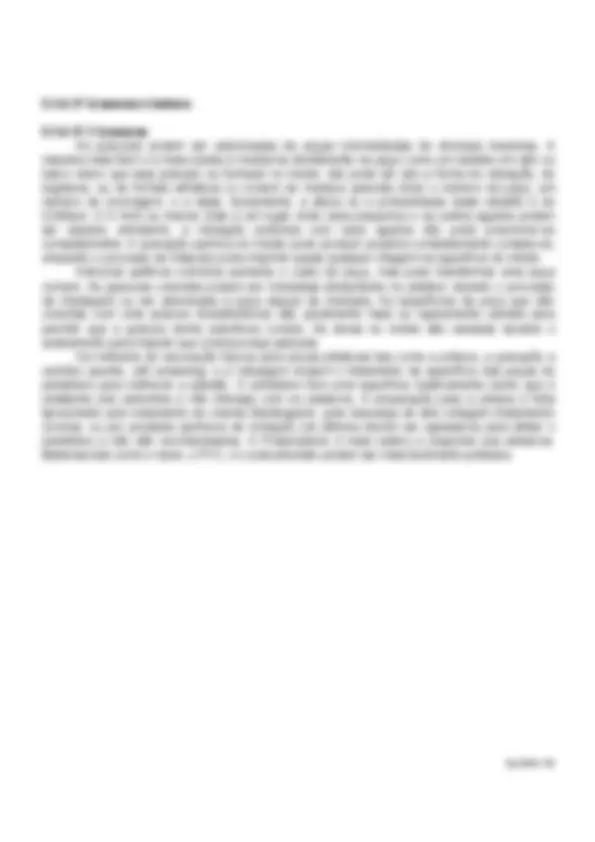
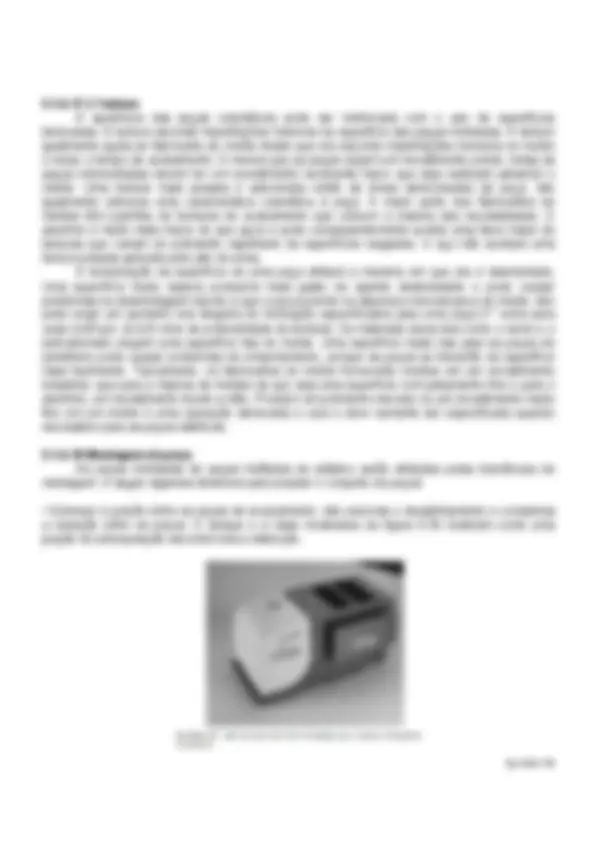
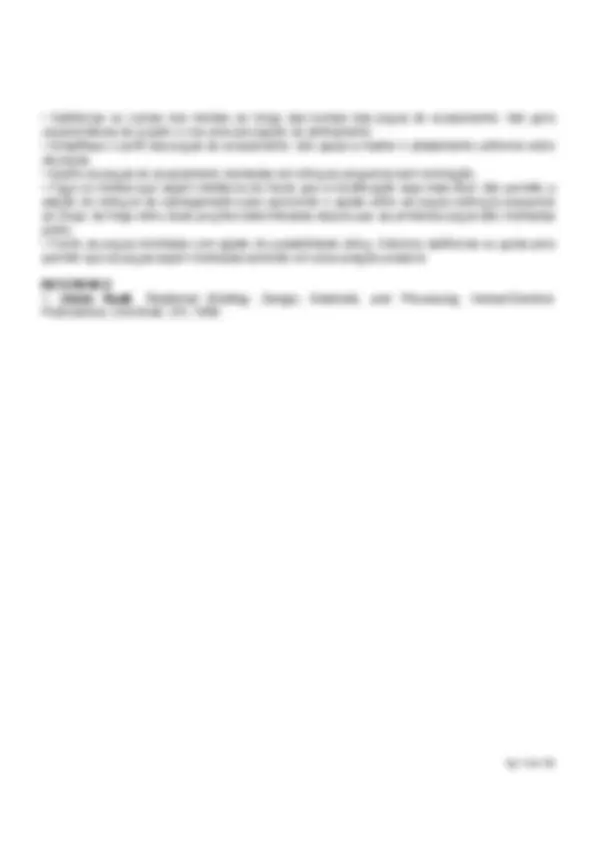
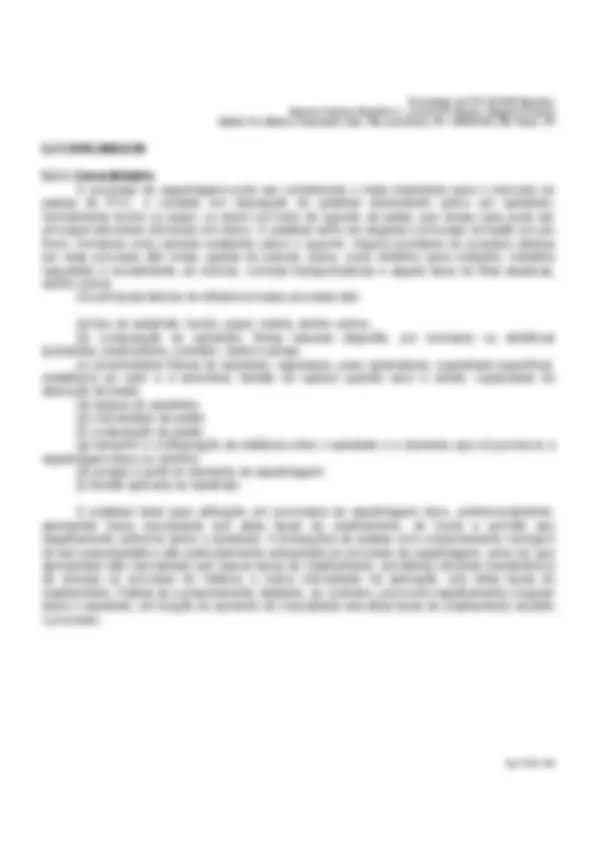
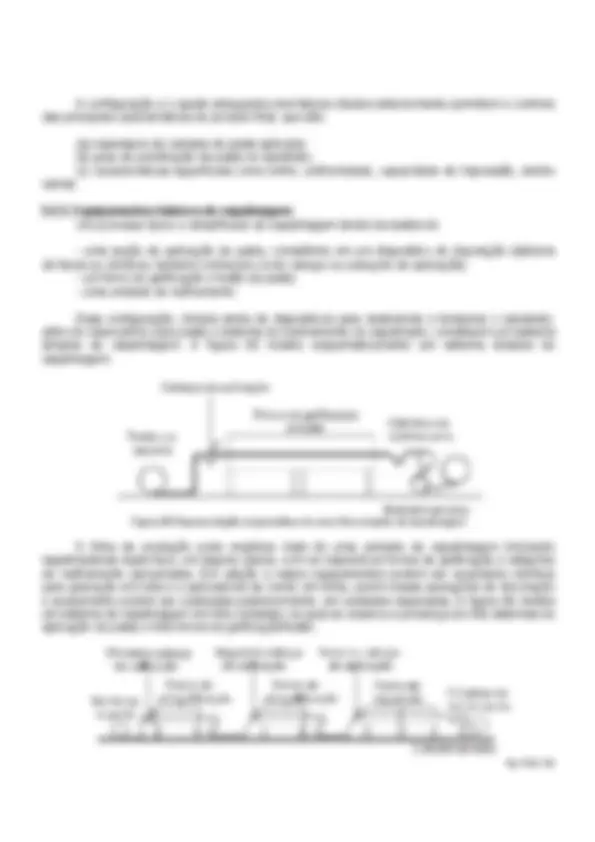
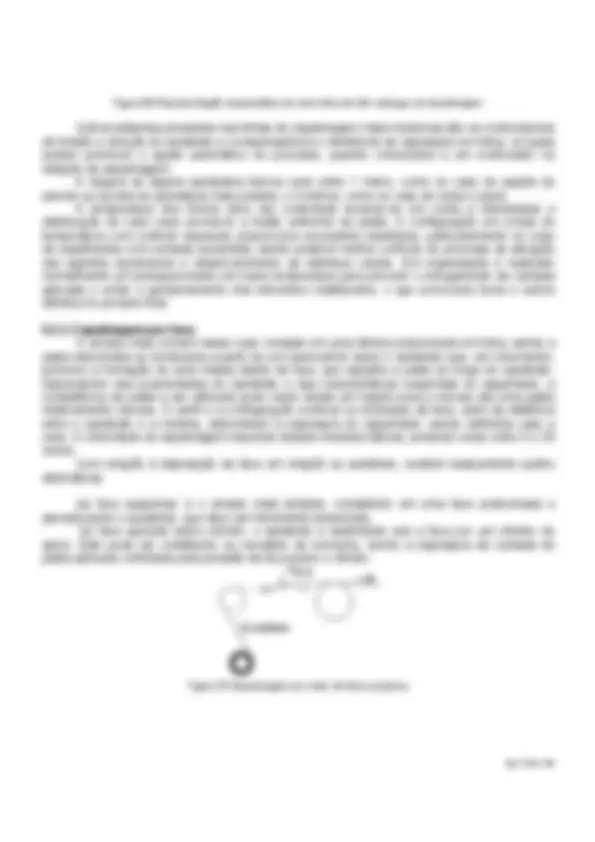
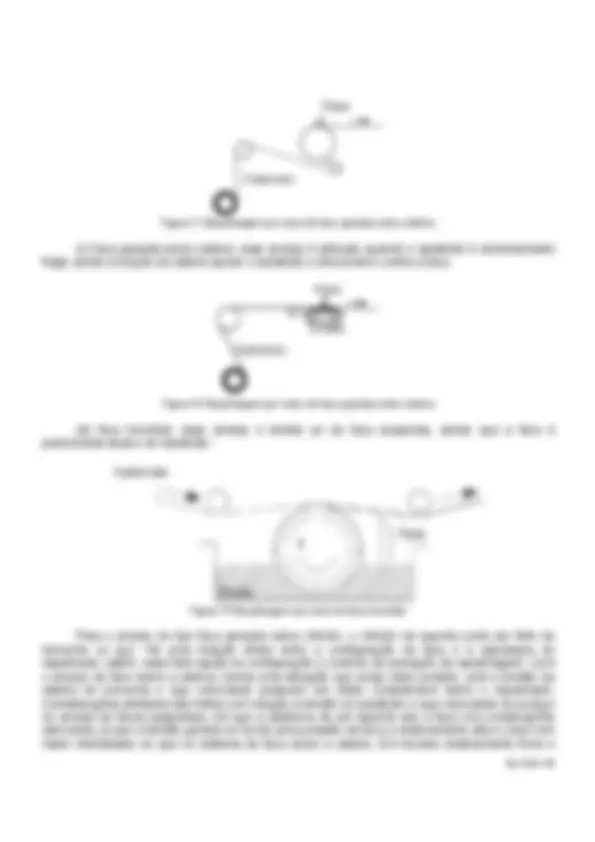
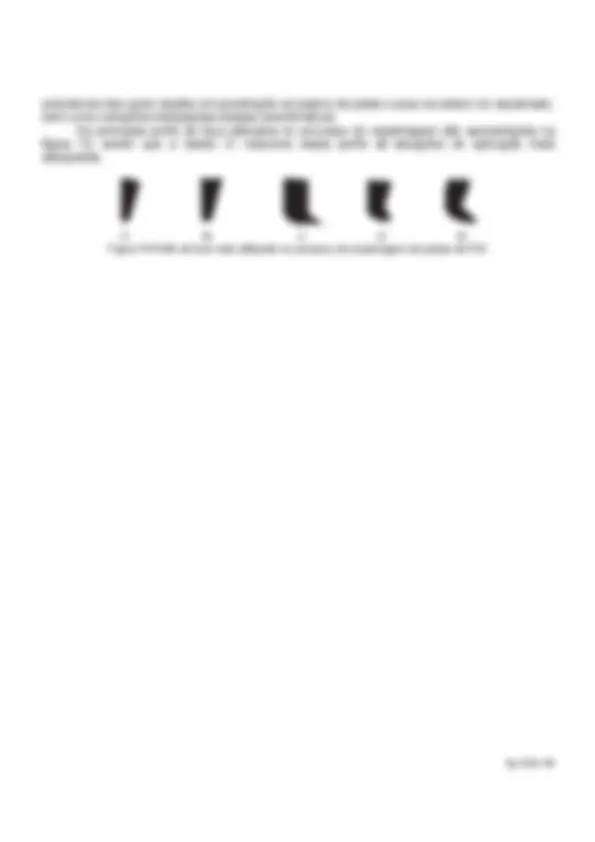
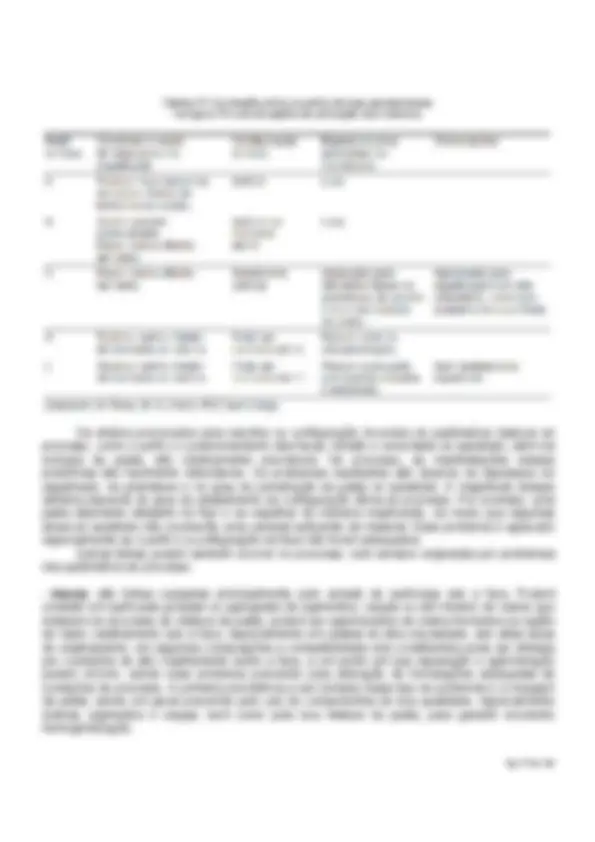
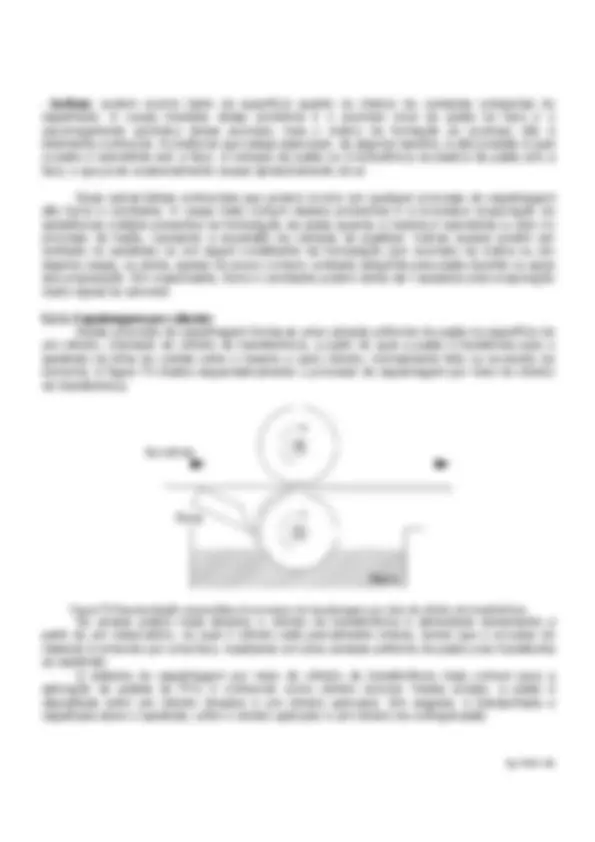
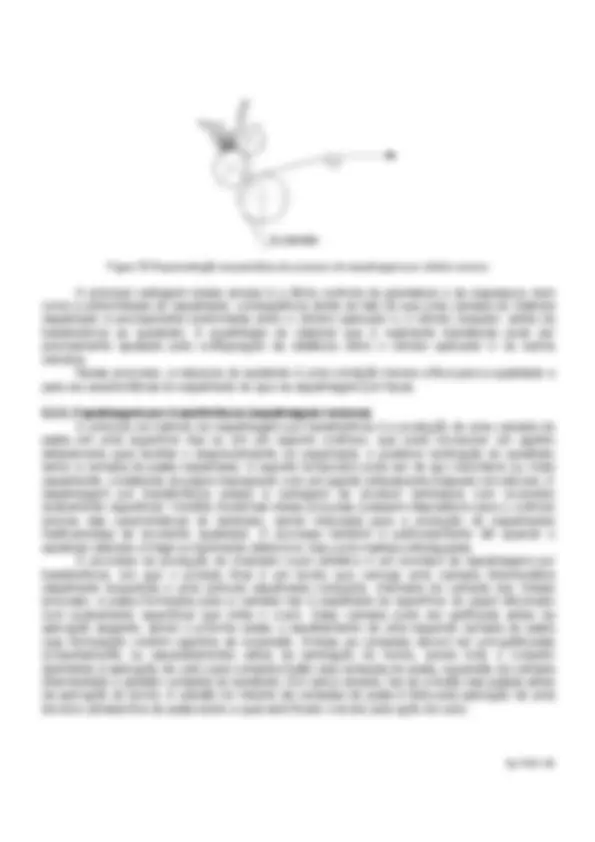
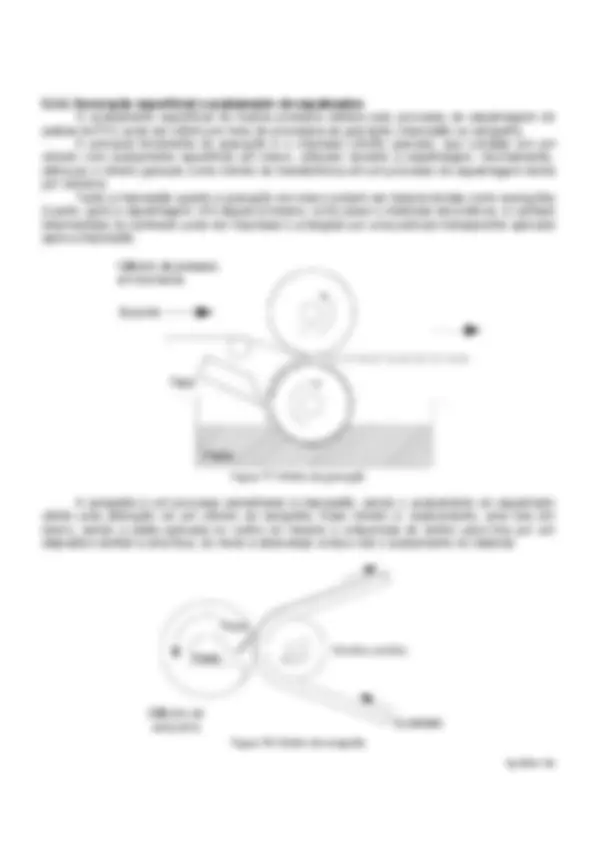
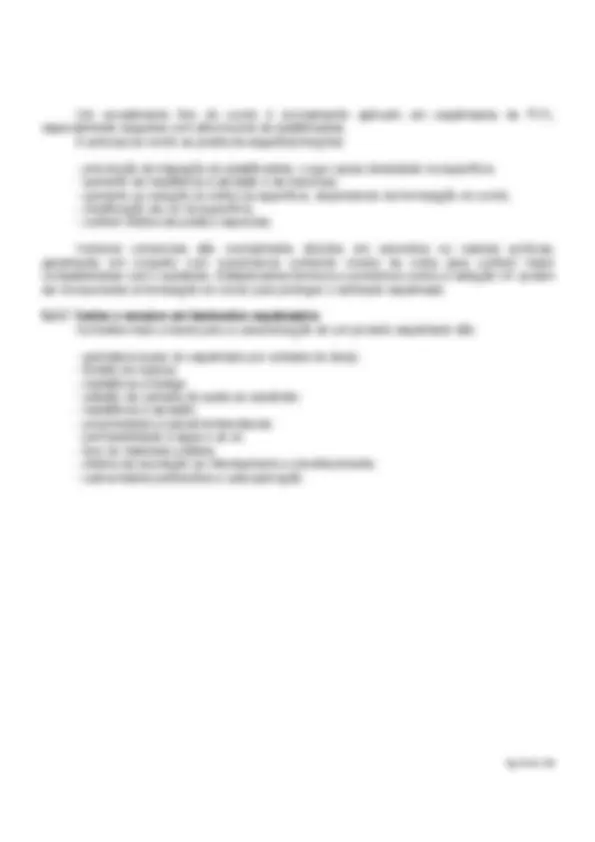
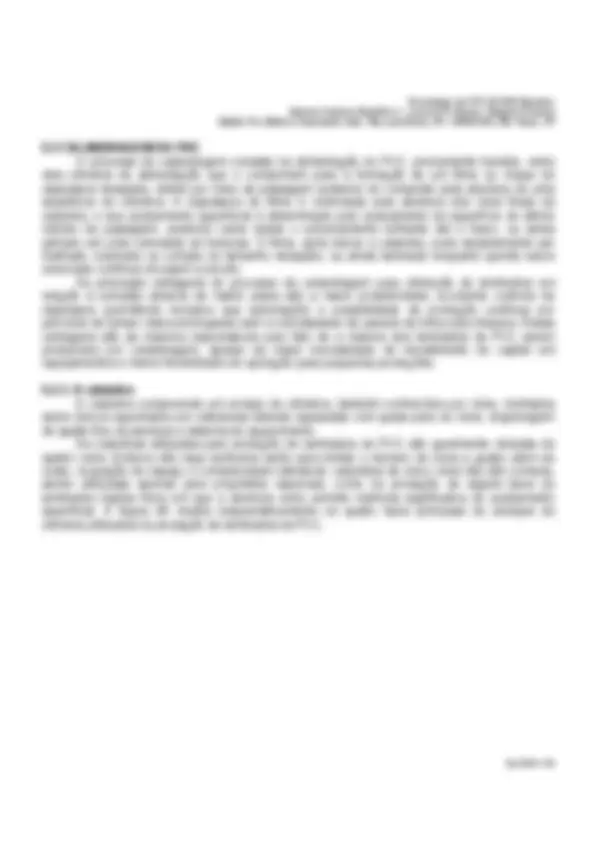
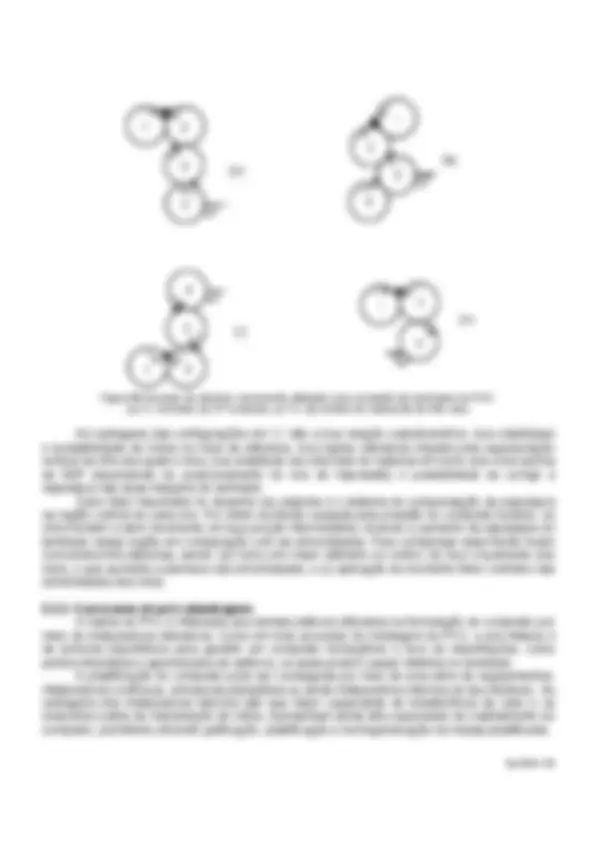
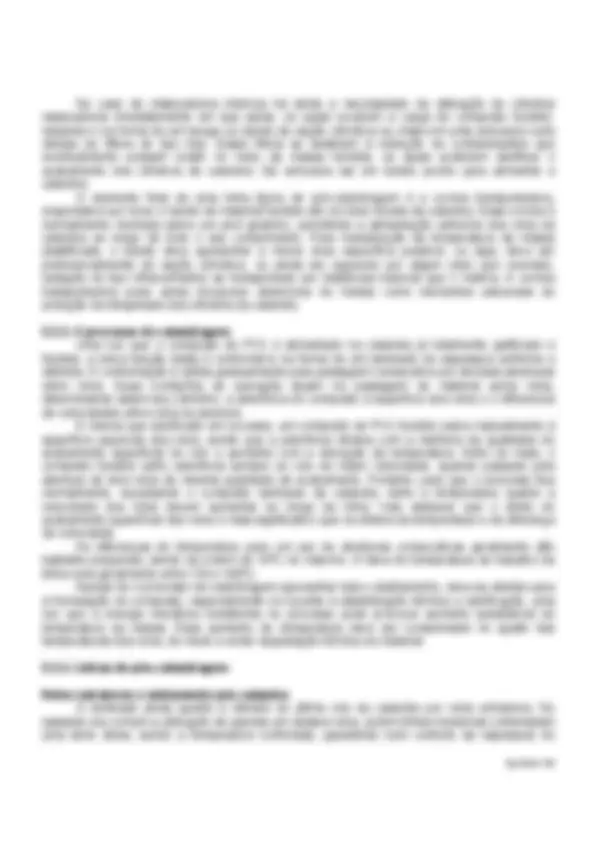
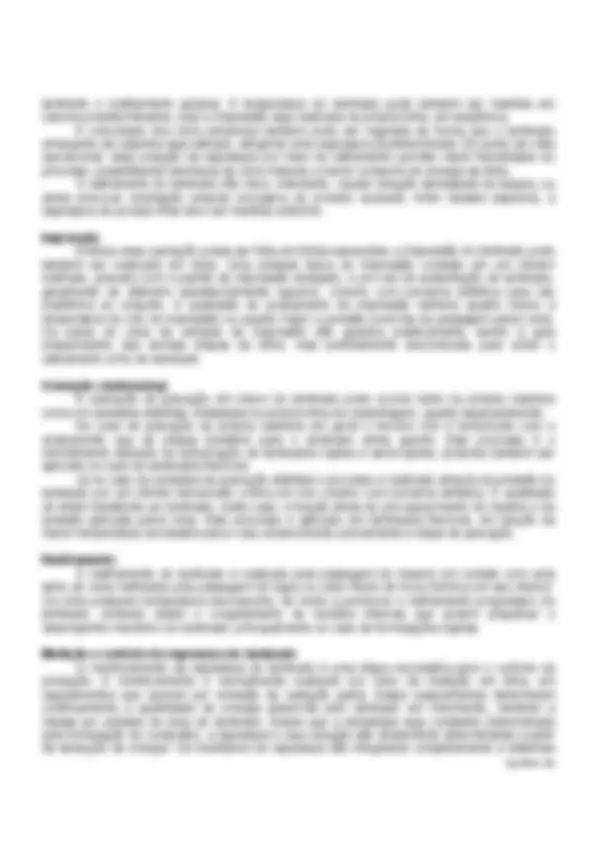
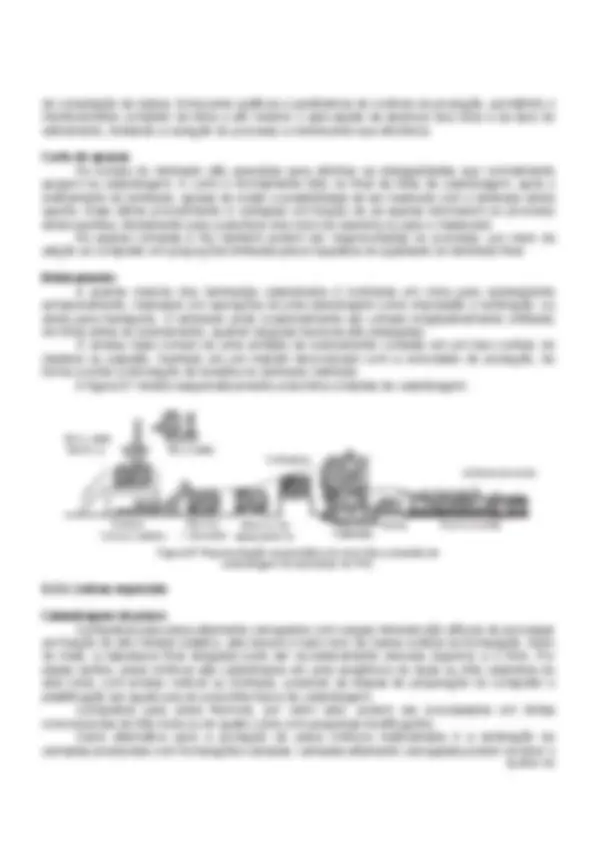
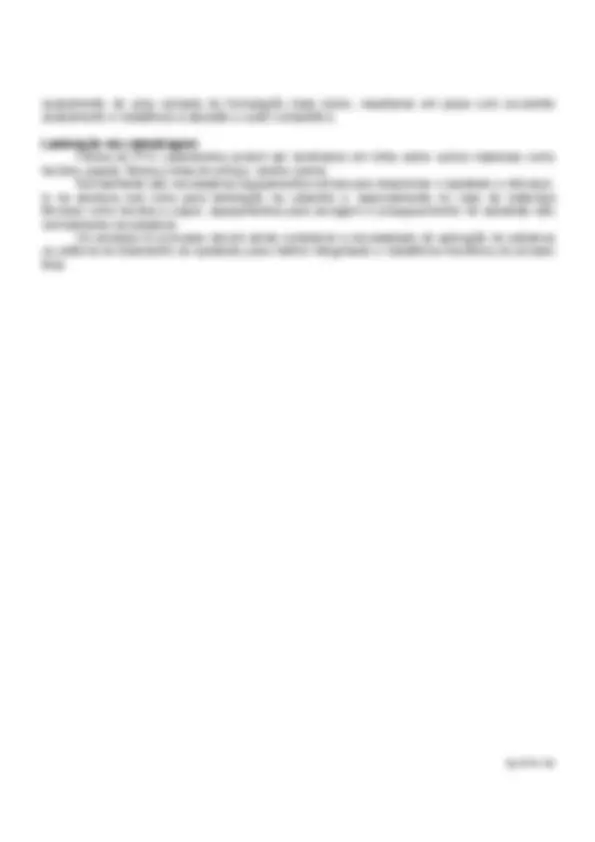
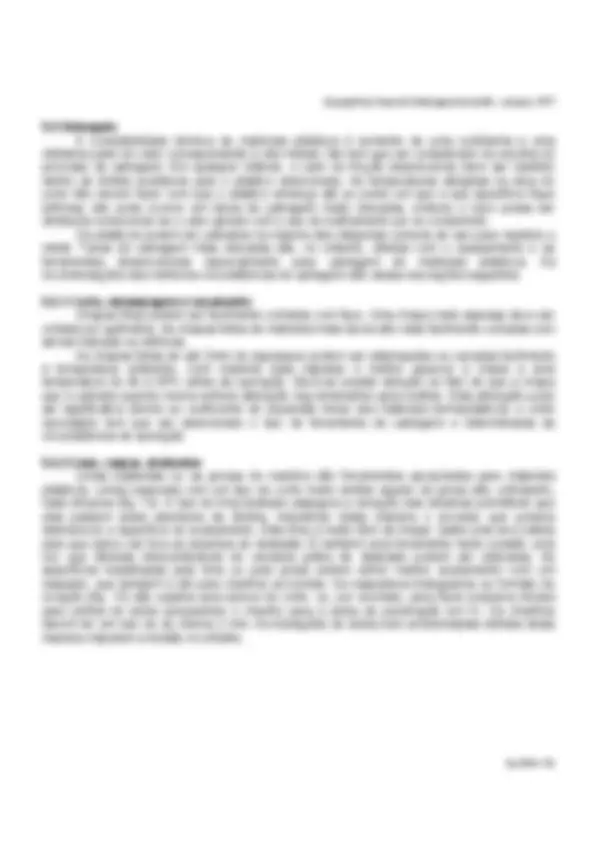
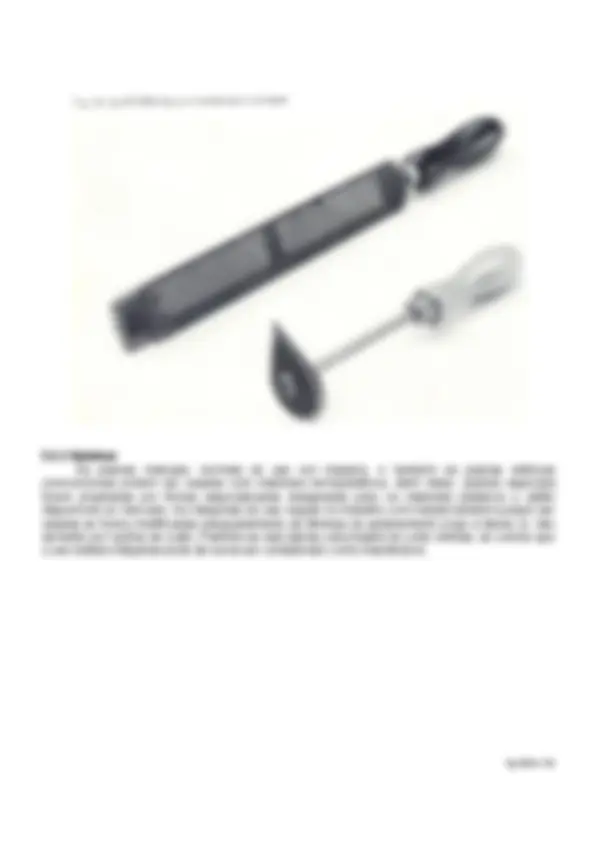
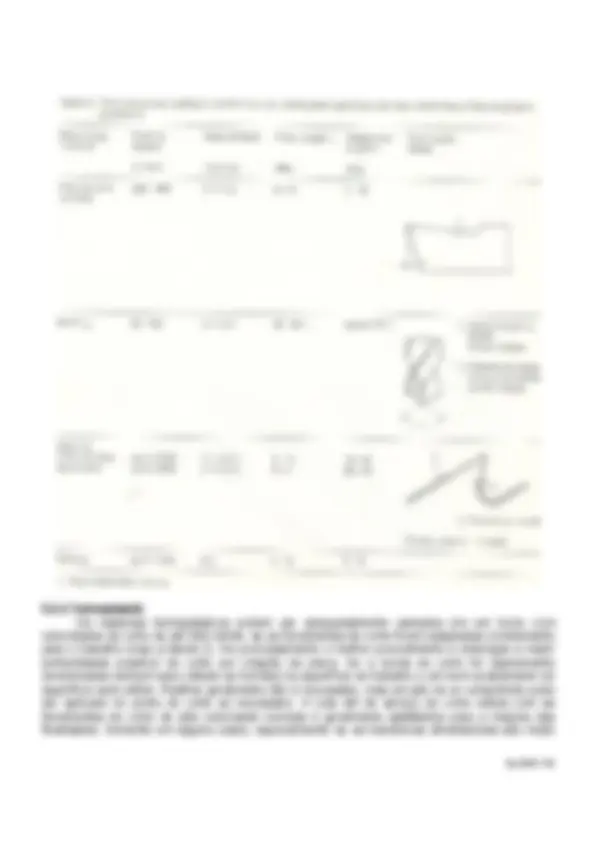
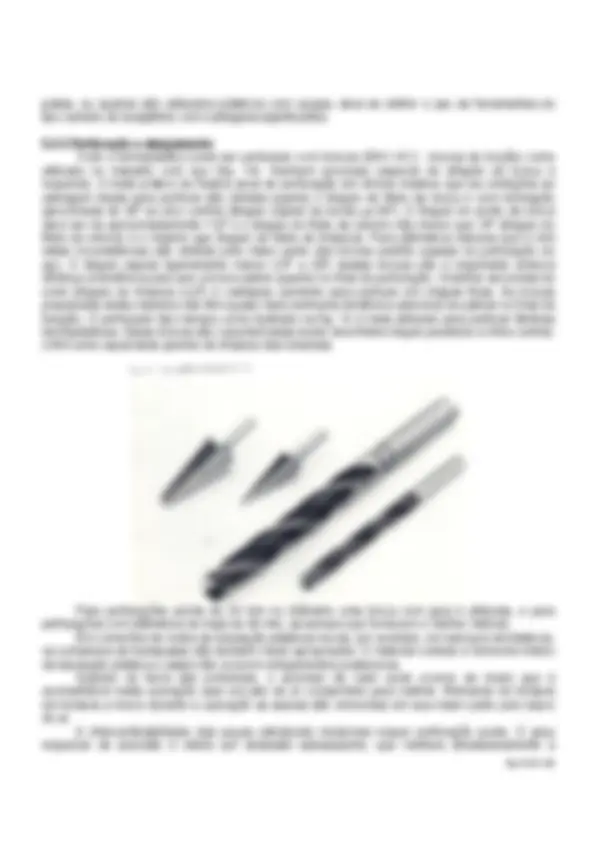
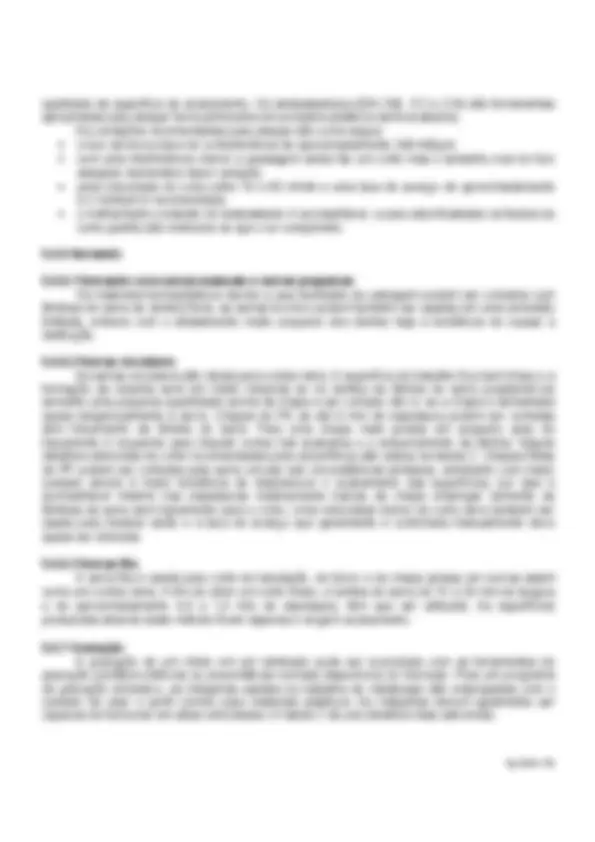
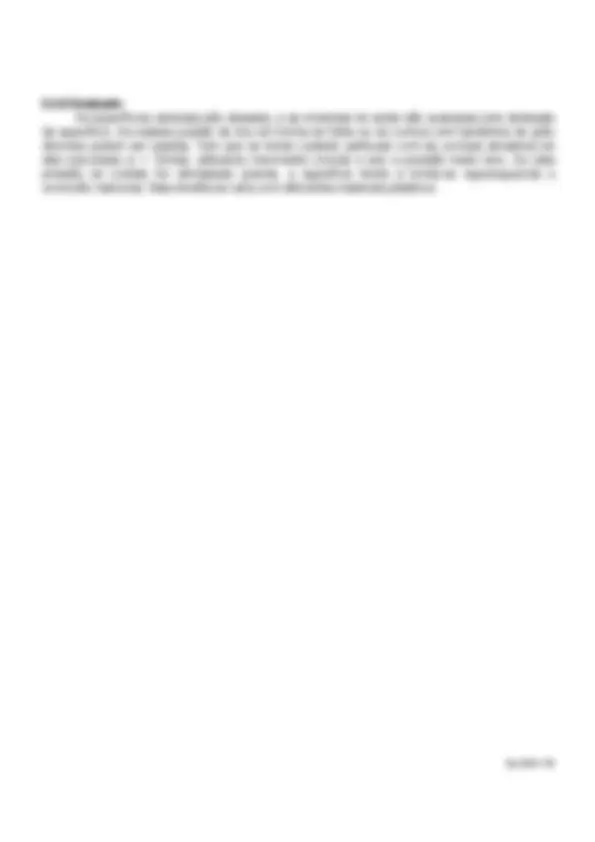
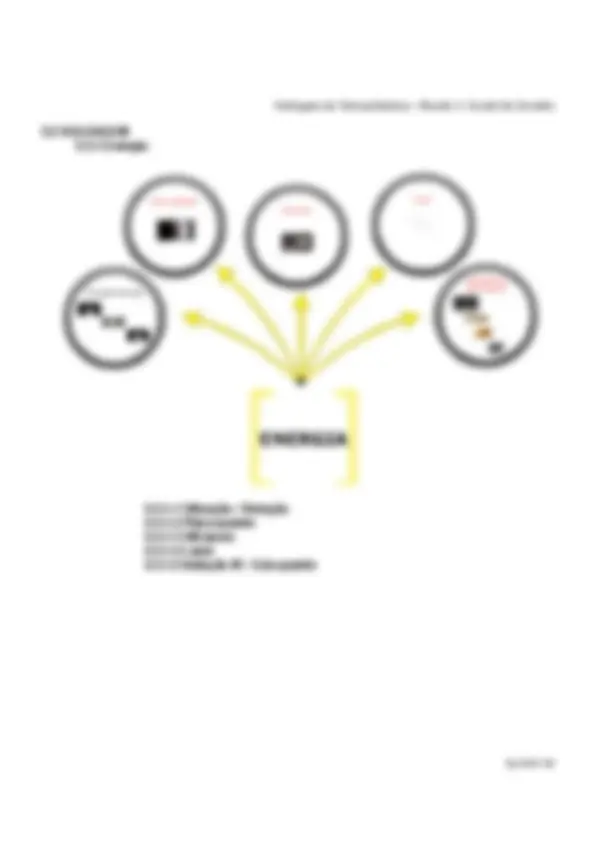
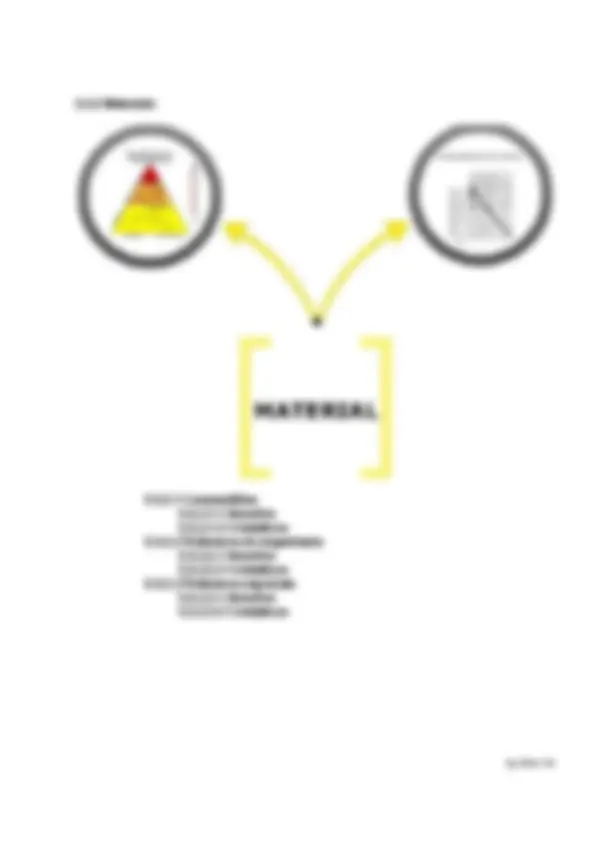
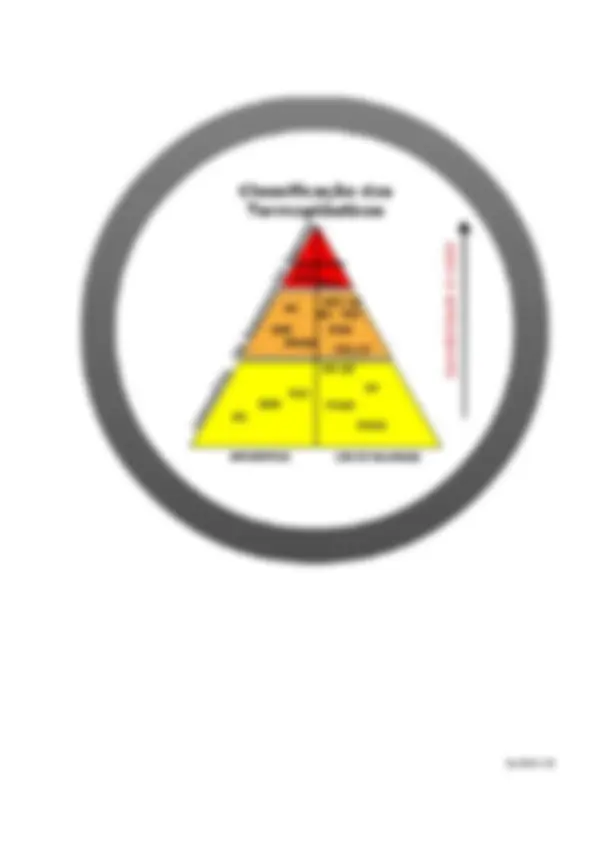
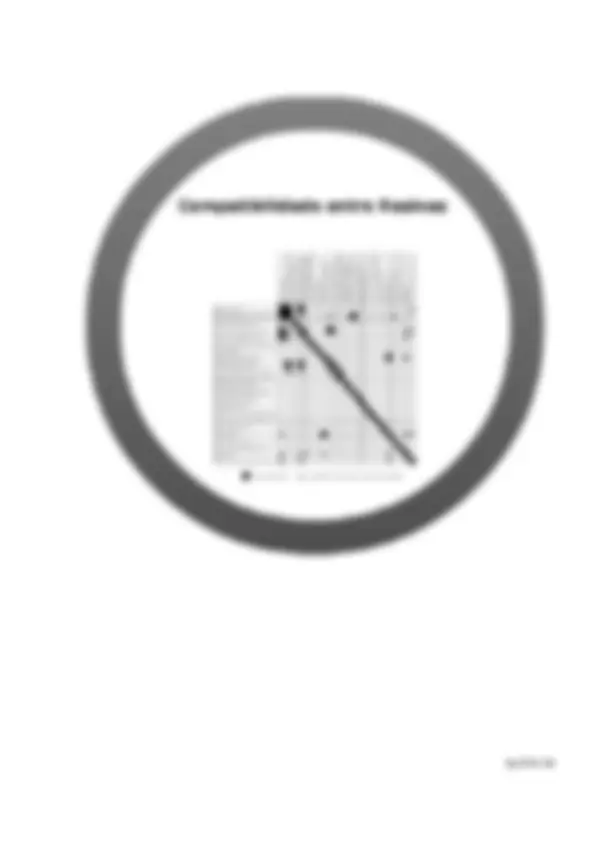
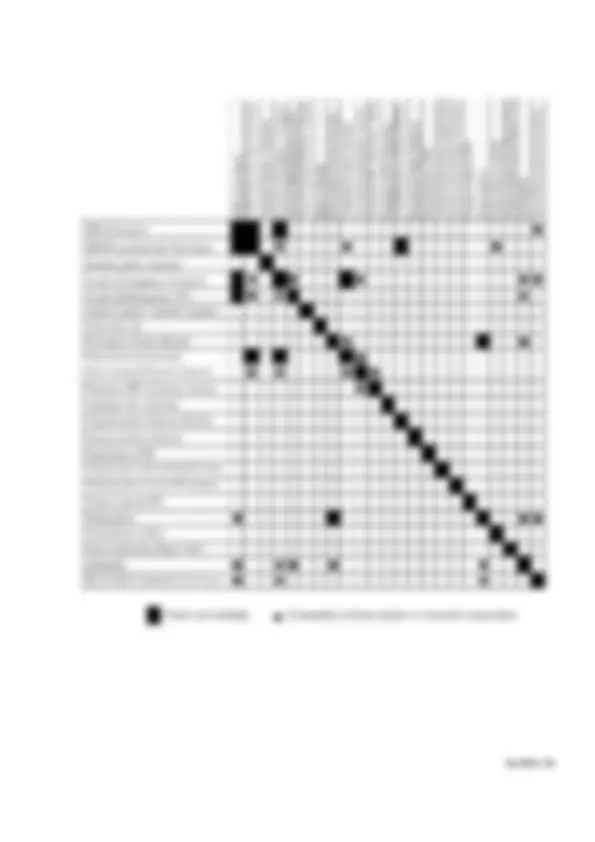
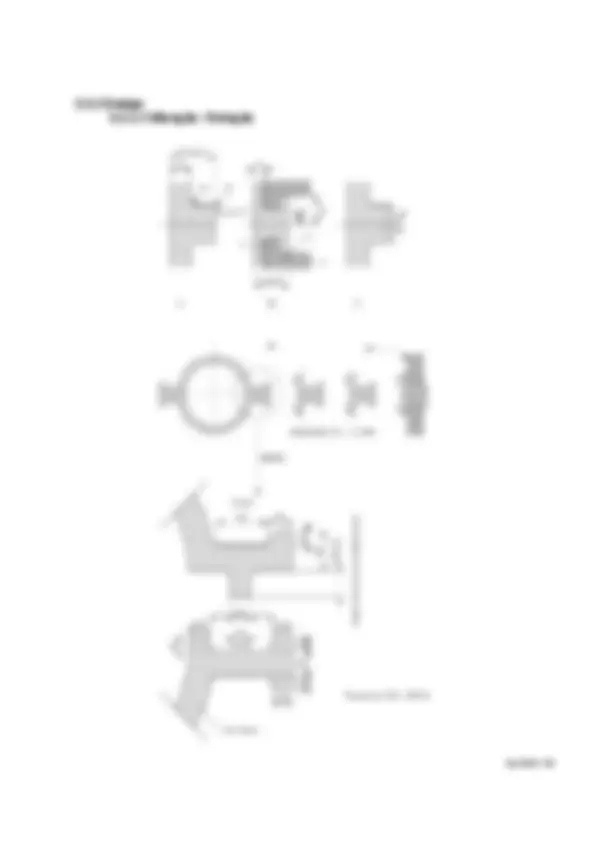
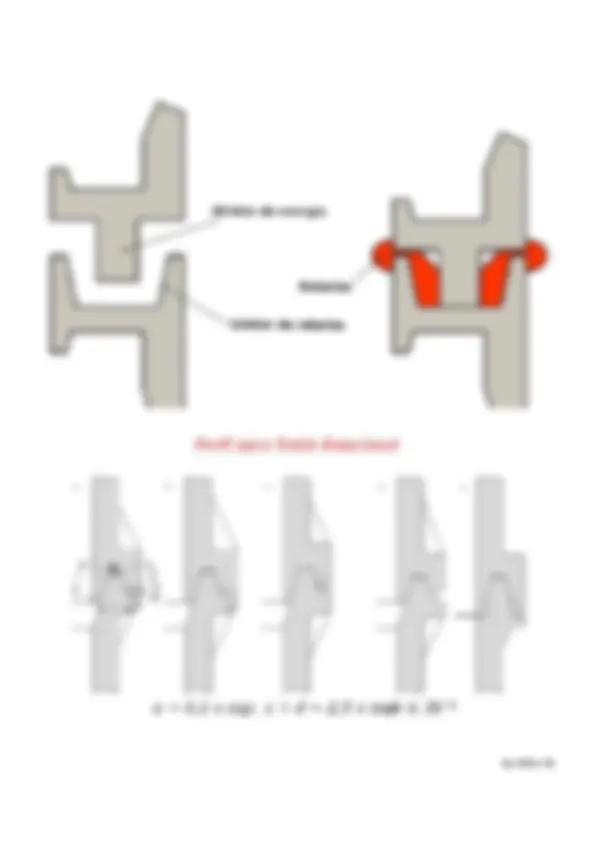
Estude fácil! Tem muito documento disponível na Docsity
Ganhe pontos ajudando outros esrudantes ou compre um plano Premium
Prepare-se para as provas
Estude fácil! Tem muito documento disponível na Docsity
Prepare-se para as provas com trabalhos de outros alunos como você, aqui na Docsity
Os melhores documentos à venda: Trabalhos de alunos formados
Prepare-se com as videoaulas e exercícios resolvidos criados a partir da grade da sua Universidade
Responda perguntas de provas passadas e avalie sua preparação.
Ganhe pontos para baixar
Ganhe pontos ajudando outros esrudantes ou compre um plano Premium
Comunidade
Peça ajuda à comunidade e tire suas dúvidas relacionadas ao estudo
Descubra as melhores universidades em seu país de acordo com os usuários da Docsity
Guias grátis
Baixe gratuitamente nossos guias de estudo, métodos para diminuir a ansiedade, dicas de TCC preparadas pelos professores da Docsity
ROTOMOLDAGEM, ESPALMAGEM, CALANDRAGEM, USINAGEM, SOLDAGEM
Tipologia: Manuais, Projetos, Pesquisas
1 / 104
Esta página não é visível na pré-visualização
Não perca as partes importantes!
PROCESSOS ESPECIAIS DE TRANSFORMAÇÃO ROTOMOLDAGEM, ESPALMAGEM, CALANDRAGEM, USINAGEM, SOLDAGEM
Prof. Roberto Ferreira
2017
5.1 ROTOMOLDAGEM 5.1.1 INTRODUÇÃO 5.1.1.1 Mercados e aplicações da rotomoldagem Aplicações típicas 5.1.2 Processo de rotomoldagem 5.1.2.1 Quatro etapas básicas 5.1.2.2 Vantagens e limitações da rotomoldagem 5.1.2.3 Analisando o processo 5.1.3 MATERIAIS DA ROTOMOLDAGEM 5.1.3.1 Características desejáveis 5.1.3.2 Listagem dos materiais disponíveis 5.1.3.2.1 Polietileno 5.1.3.2.2 Polipropileno 5.1.3.2.3 Nylon 5.1.3.2.4 PVC (líquido) 5.1.3.2.5 PVC (pó) 5.1.3.2.6 Policarbonato 5.1.3.2.7 ABS 5.1.3.2.8 Fluorpolímero 5.1.3.2.9 Materiais Espumados 5.1.3.2.10 Materiais carregados 5.1.3.3 Preparação do Material 5.1.3.3.1 Processo de micronização 5.1.3.3.2 Qualidade e avaliação do pó 5.1.4 MOLDES 5.1.4.1 Projeto de moldes 5.1.4.2 Escolhendo um tipo de molde 5.1.4.2.1 Tamanho 5.1.4.2.2 Complexidade do formato 5.1.4.2.3 Quantidade de moldes 5.1.4.2.4 Aparência do produto 5.1.4.3 Elementos e características do molde 5.1.4.3.1 Placa de montagem 5.1.4.3.2 Suportação 5.1.4.3.3 Barras de sustentação 5.1.4.3.4 Linhas divisoras 5.1.4.3.5 Cavidade do molde 5.1.4.3.6 Mecanismos de fechamento 5.1.4.3.7 Pontos de alavanca 5.1.4.3.8 Vent
5.1.4.3.9 Pontos de erguimento 5.1.4.3.10 Insertos e núcleos: seções do molde 5.1.4.3.11 Portas de enchimento 5.1.4.3.12 Mecanismos da dobradiça 5.1.4.3.13 Guias roletadas 5.1.4.3.14 Caixa de carga 5.1.4.3.15 Amplificadores do fluxo de ar (geradores de Vortex) 5.1.4.3.16 Pinos térmicos 5.1.4.3.17 Painéis isolados ou protegidos 5.1.4.4 Sistemas de desmoldagem do molde 5.1.5 MAQUINÁRIO 5.1.5.1 Exigências básicas de uma máquina de rotomoldagem 5.1.5.1.1 Estágio de aquecimento 5.1.5.1.2 Estágio de resfriamento 5.1.5.1.3 Estágio de serviço. 5.1.5.1.4 Rotação 5.1.5.2 Estilos de máquina 5.1.6 PROJETO DE MOLDE 5.1.6.1 Diretrizes de projeto básico 5.1.6.2 Espessura de parede 5.1.6.3 Ângulos de inclinação 5,1.6.4 Raios de canto e ângulos 5.1.6.4.1 Raios de canto 5.1.6.4.2 Ângulos de canto 5.1.6.5 Estruturação das peças 5.1.6.5.1 Reforços 5.1.6.5.2 Rebaixos 5.1.6.6 Furos 5.1.6.7 Saliências 5.1.6.8 Tolerâncias e contração 5.1.6.9 Empenamento e nivelamento 5.1.6.10 Peças de parede dupla 5.1.6.11 Protuberâncias 5.1.6.12 Sobre cortes 5.1.6.13 Roscas 5.1.6.14 Insertos 5.1.6.15 Linhas divisoras 5.1.6.16 Vents 5.1.6.17 Gravuras e textura 5.1.6.17.1 Gravuras 5.1.6.17.2 Textura 5.1.6.18 Montagem da peça
5.2 ESPALMAGEM 5.2.1. Generalidades 5.2.2. Equipamentos básicos de espalmagem 5.2.3. Espalmagem por faca 5.2.4. Espalmagem por cilindro 5.2.5. Espalmagem por transferência (espalmagem reversa)
Handbook of Plastic Processes - Charles A. Harper - Timonium, Maryland Wiley Interscience - A John Wiley & Sons, Inc., Publication Copyright © 2006 by John Wiley & Sons, Inc. Published by John Wiley & Sons, Inc., Hoboken, New Jersey Paul Nugent - Consultant, Reading, Pennsylvania
5.1 ROTOMOLDAGEM
A rotomoldagem é uma indústria relativamente nova, com suas raízes encontradas na moldagem do plastisol de policloreto de vinila (PVC) do final dos anos 50. Mesmo na atualidade, com menos de 2000 companhias no mundo inteiro, permanece um mercado pequeno, mas com excelentes perspectivas dentro do mundo dos plásticos, pois alcança quase todos os mercados concebíveis e apresenta taxa de crescimento acima da média das indústrias. Oferece muito na flexibilidade de projeto e na escala de produto, variando de recipientes simples da maioria das aplicações automotrizes, médicas, até as aeroespaciais sofisticadas. Usado regularmente para produzir peças de grande complexidade com uma escala de aplicações constantemente crescente, a rotomoldagem se presta como nenhum outro processo para artigos ocos. Peças pequenas tais como as cabeças de bonecas podem ser feitas da mesma maneira que a usada para os tanques de armazenagem enormes de 22.000 galões (80.000 litros). Peças intricadas tais como tanques de combustível e os componentes para dutos de aviões são agora comuns porque a rotomoldagem é conhecida por um grupo maior de projetistas e de coordenadores. A rotomoldagem, entretanto, ainda permanece engatinhando em termos de desenvolvimento. A simplicidade aparente do processo e os mercados de tecnologia obsoleta, geralmente utilizados, fizeram com que seja um tanto negligenciada. As tendências atuais do mercado, de consolidar componentes de produto e ciclos de vida mais curtos com volumes totais mais baixos levam a um nível de interesse aumentado. Importante, este interesse pelo mercado atraiu esforços dos principais fornecedores de materiais, que servirá como fator de desenvolvimento chave no futuro da indústria. Neste capítulo nós veremos o processo básico de rotomoldagem, os mercados a que serve, os materiais, os moldes, o maquinário utilizado e alguns princípios de projeto que podem ajudar a facilitar a moldagem. Para aqueles que procuram um tratamento maior e mais aprofundado sobre o assunto, Rotomoldagem: Um Guia Prático , do mesmo autor, é o livro mais detalhado disponível do processo, detalhes podem ser encontrados em www.paulnugent.com.
5.1.1.1 Mercados e aplicações da rotomoldagem Com a capacidade de produzir grandes peças ocas, geralmente as mais moldadas no mundo inteiro são as caixas de água. Estas são responsáveis por 70% da atividade global em rotomoldagem, concentrando-se em regiões onde a água é mais escassa. Em geral os maiores mercados em termos financeiros são encontrados na America do Norte e na Europa, e nestas regiões, não dominam as caixas de água, a rotomoldagem é utilizada numa escala de aplicações muito maior, com um grau crescente de sofisticação. As estimativas dos moldadores e o consumo de material ao redor do mundo são mostrados na figura 6.1. Afora as caixas e tanques, os pedidos ideais para a rotomoldagem são formas ocas tipicamente complexas, em quantidades relativamente baixas (até aproximadamente 10.
peças). Há exceções a isto, como brinquedos de crianças, por exemplo, mas geralmente, os benefícios de ofertas da rotomoldagem, aos clientes finais com baixo custo, está no trabalho feito com ferramentas e equipamentos, e sua capacidade de possibilitar quase todo o projeto que o
moldador puder conceber.
O processo é inerente de pressão baixa e está muito atrelado em vários aspectos aos atributos de processamento do polietileno. As escolhas de materiais fora o polietileno são limitadas em comparação com outros processos, e assim a rotomoldagem não serve sempre para as aplicações que têm maior critério de exigência de desempenho. O controle da tolerância, o acabamento da superfície, e a rigidez da peça estão entre os desafios mais comuns.
Aplicações típicas A versatilidade da rotomoldagem é demonstrada constantemente em uma larga escala de produtos e de mercados. Alguns setores típicos do mercado e as aplicações deles incluem:
do controle de poluição
material, todos ocorrem no molde sem o uso de pressão. Até recentemente, uma vez que o molde entrava no forno, nada mais se sabia além de que o pó era fundido (ou o líquido reagido) e depois então resfriado para dar forma a peça final. Nos dias de hoje, já é possível medir temperaturas
dentro do molde durante o ciclo, varrendo continuamente a superfície do molde para leituras da temperatura, ou mesmo colocando dentro uma câmera para ver a formação da peça. Durante o processo, fatores chave devem ser considerados para assegurar-se de que o processo seja eficaz e econômico: respiros são usados para assegurar-se de que a pressão dentro do molde esteja em equilíbrio com o ambiente externo; desmoldantes são usados para assegurar-se de que o material não grude ao molde; os ajustes de rotações devem ser selecionados com cuidado, porque o relacionamento entre os eixos primário e secundário afetará o modo em que o material será distribuído na peça final; somente a superfície externa da peça deve estar em contacto com o molde, e particularmente no caso de materiais semi-cristalinos, tais como o polietileno, as velocidades de resfriamento devem ser controladas para minimizar a distorção que ocorre ao se acelerar o processo.
5.1.2.2 Vantagens e limitações da rotomoldagem
As vantagens principais da rotomoldagem podem ser resumidas como segue:
5.1.2.3 Analisando o processo A figura 6.3 mostra dados das medições durante um ciclo de moldagem para o polietileno. Neste caso, dois termopares foram usados, um medindo o ambiente externo do molde e o segundo medindo a temperatura interna do molde (o volume de ar interno incluso). Examinando o perfil de temperatura externo primeiramente, no início do processo as temperaturas internas e externas são similares. Quando o molde ingressa no forno, a temperatura do ambiente sobe rapidamente. O perfil e a taxa de recuperação da temperatura do forno dependem do tamanho e do desempenho do queimador do forno e do próprio projeto do forno. A temperatura do ambiente estabelece-se em torno do ponto ajustado do forno. A variação na temperatura durante este estágio do ciclo é devido ao movimento rápido do ar no forno e à rotação do molde após a entrada do ar quente. Uma vez que o ciclo de aquecimento no forno termina, a temperatura do ambiente cai rapidamente até a temperatura do sistema de resfriamento. As temperaturas de resfriamento são ditadas por circunstâncias ambientais e todos os sistemas de resfriamento são empregados. Para resfriadores encapsulados, o calor que irradia do molde pode inicialmente fazer aumentar a temperatura circunvizinha, mas esta cai durante o tempo em que o molde esfria. Olhando o perfil de temperatura interno do ar mais detalhadamente, segundo as indicações da figura 6.4, um número de pontos de transição consistentes pode ser observado para a moldagem de polietileno. A transferência de calor através do molde e a absorção de energia pelo material afetam o perfil de temperatura do ar interno em pontos chaves no ciclo:
A - Pó começa a aderir à superfície do molde. B - Pó aderiu completamente à superfície do molde. C - Temperatura interna máxima que pode ser relacionada às propriedades da peça. D - Solidificação ou cristalização do polímero. E - Ponto de desmoldagem para a peça solidificada.
No início do processo, o material e o ar dentro do molde estão em condições ambientais ditadas pelo calor residual deixado no molde do ciclo precedente e da temperatura do material que é carregado no molde. Assim que a rotação e o aquecimento começam, a energia é transferida através do molde e da massa de ar e do material dentro do molde. O material não gruda imediatamente, mas flui como pó até que a massa do material e a superfície do molde estejam suficientemente quentes para permitir que partículas menores do material comecem a grudar na superfície. Isto ocorre no ponto A. O aquecimento continua entre os pontos A e B, o material funde ao molde em ondas sucessivas. A absorção da energia pelo processo de plastificação (quando o material é convertido de um pó a uma massa fundida contínua) causa taxa decrescente (lenta) de aumento de temperatura do ar interno, produzindo um platô. Na extremidade deste platô (o ponto B), quando todo o material adere à superfície do molde, a energia é transferida mais uma vez diretamente ao ar interno e a temperatura sobe outra vez, rapidamente. O aquecimento continua até o ponto C. Esta temperatura máxima é relacionada às propriedades finais da peça moldada; o grau final de “cura” ou de “cozimento” pode ser relacionado à temperatura interna máxima observada dentro do molde durante o ciclo. Este pico ocorrerá algum tempo depois que a peça sai do forno, dependendo da inércia térmica, da espessura de parede do molde e da peça. Os aumentos de 30 a 40°F (16 a 22ºC) nas fases iniciais de resfriamento não são raros para as peças espessas. Quando o resfriamento do molde inicia, a temperatura do interior da peça cai. A taxa de queda da temperatura do ar dentro do molde é retardada em relação à temperatura da superfície externa do molde. Esta taxa é dominada pelo método de resfriamento empregado (tipicamente, um ventilador que resfria somente durante o começo do ciclo) e pelas condições ambientais (resfriar no verão pode ser dramàticamente mais lento do que no inverno). O resfriamento continua até que o material alcance a solidificação ou cristalização. Neste tempo, a energia liberada durante a formação de uma estrutura cristalina mantém a temperatura dentro da peça, produzindo um segundo platô similar ao platô de fusão encontrado durante o estágio de aquecimento do ciclo. Isto ocorre no ponto D. Além do ponto da cristalização, o resfriamento continua usando água e/ou ar até que a peça esteja segura de manusear. Trabalho recente mostrou como as mudanças de temperatura
ser resfriado após diversos ciclos (dependendo da duração). Diversas outras opções de coleta da temperatura do molde foram desenvolvidas, incluindo sistemas infravermelhos sem contato e sistemas de equipamentos com fiação que empregam anéis coletores de alta temperatura.
5.1.3 MATERIAIS DA ROTOMOLDAGEM
5.1.3.1 Características desejáveis Há um número de propriedades desejáveis que um material deve ter a fim de ser apropriado para a rotomoldagem. Incluem o seguinte:
5.1.3.2 Listagem dos materiais disponíveis De muitos polímeros disponíveis a todos os processos com plásticos, há somente um grupo razoavelmente estreito de materiais que podem ser processados facilmente pela rotomoldagem. Este grupo está crescendo gradualmente com mais fornecedores de materiais e com mercados de ponta reconhecendo o potencial do processo. De acordo com as perspectivas do mercado, os principais materiais em uso são classificados hoje como segue: Polietilenos (PEBD, PELBD, PEAD, EVA) 95% Policloreto de Vinila 3% Nylons (nylon 6, 6.6, 11, 12) <0.5% Polipropileno <0.5% Policarbonato <0.2% Fluorpolimeros (ETFE, ECTFE, PFA, MFA, PVDF) <0.1%
Há, entretanto, uma gama de polímeros que foram moldados com sucesso nos últimos 30 anos ou estão sendo usados em quantidades pequenas para aplicações especiais. Estes incluem:
5.1.3.2.1 Polietileno Os polietilenos oferecem uma excelente combinação de facilidade de processamento, estabilidade térmica, e custo com o que continuam a dominar o mercado. O desenvolvimento de uma escala larga de materiais alternativos para a rotomoldagem foi lento por duas razões principais:
combustíveis. Os nylons são usados para os tanques de combustível de motocicletas e veículos militares.
5.1.3.2.4 PVC (líquido) O Policloreto de Vinila (PVC) está disponível em duas formulações distintas para a rotomoldagem; líquido ou seco. Os materiais líquidos sob a forma de plastisol e de organosol foram essenciais na moldagem do PVC desde sua introdução em 1947. Os pós ou os micropeletts secos de vinil foram introduzidos no princípio dos anos 80. O plastisol de vinil é a formula mais comum de PVC usado para a rotomoldagem. Os plastisois tem custo tipicamente baixo, têm uma larga escala de dureza, tem brilho e transparência elevadas, permitem a reprodução otimizada da superfície do molde, e são fáceis de colorir. Podem ser produzidos em classes aprovadas pela Agência de Medicamentos e Alimentos (FDA), possuem boa resistência química, e são de fácil processamento. Alterando-se os
ingredientes do plastisol, pode-se controlar a dureza da superfície de um produto moldado. Os plastisois da classe de rotomoldagem variam em dureza numa faixa de 30 a 70 Shore D. A dureza inerente é controlada pelas propriedades dos materiais usados e pela relação dos sólidos
(materiais) adicionados ao plastificante.
5.1.3.2.5 PVC (pó)
Os pós e os micropeletts de vinil são ofertas recentes do PVC para a rotomoldagem. Oferecem uma ampla escala de dureza, não exigem uma bomba de dispersão, são limpos, podem moldar com espessura de parede uniforme, têm uma densidade mais baixa e custo um tanto maior, mas ainda possuem uso limitado na indústria.
5.1.3.2.6 Policarbonato O policarbonato foi introduzido nos anos 50 e rotomoldado no final dos anos 70. É higroscópico, exige secagem antes da moldagem e deve ter menos de 0.02% em umidade antes de ser carregado diretamente no molde. A secagem imprópria produzirá peças que contêm matéria cinzenta, bolhas, cor amarelada, uma redução na transparência, e uma perda de resistência ao impacto. A umidade diminui o peso molecular médio do policarbonato durante a moldagem e conseqüentemente degrada as propriedades físicas. Como temperaturas maiores são exigidas para processar o policarbonato, a transferência térmica através do molde ao material pode ser um problema. Os melhores resultados são conseguidos usando moldes com jaqueta de óleo e um pó com granulometria menor que 35 mesh (500μm). Entretanto, bolhas podem ainda ocorrer nas peças, e é comum utilizar superfícies texturadas no molde para disfarçar sua presença. O uso de uma atmosfera de nitrogênio pode reduzir a cor amarelada causada pela degradação. As vantagens do policarbonato são sua rigidez mais elevada, dureza, brilho, e resistência a alta temperatura quando comparado ao polietileno [275°F (135°C) contra 122 a 158°F (50 a 70°C)]. A resistência à ação de agentes atmosféricos e a estabilidade dimensional são boas e o material é dúctil mesmo a baixas temperaturas. Classes aprovadas pela FDA e resistentes à chama estão disponíveis. É mais utilizado para aplicações tais como os bojos de luminárias e de iluminação de rua (figura 6.6). As desvantagens são o custo elevado, o difícil processamento, a necessidade de secagem e a baixa resistência química.
O acrilonitrito-butano-estireno (ABS) é um termoplástico terpolímero amorfo. Tem representado algo como um “Santo Graal” para materiais de rotomoldagem nos últimos anos, sendo visto como um material resistente ao risco, disponível a custo razoável. Foi moldado no passado comercialmente e foi assunto de diversos projetos de investigação recentes a nível universitário. Os estudos mostraram que o ABS (junto com o poliestireno e o acrílico) são sensíveis à degradação e o ABS pode se aglomerar produzindo uma estrutura porosa e estriada com baixa força elástica e elevada porosidade de superfície. O aumento do índice de borracha no ABS conduz ao aumento da dificuldade de densificação. O ABS oferece algumas vantagens potenciais, incluindo a boa resistência ao impacto, a rigidez, a resistência química, boas propriedades da adesão, possibilidade de receber pintura, e resistência a ruptura por ação de solventes. As peças moldadas podem ser pintadas usando uma combinação de primer e demãos de acabamento para aplicações tais como manequins, brinquedos, mercadorias para sanitários, componentes automotivos, equipamento de esportes, e
móveis.
5.1.3.2.8 Fluorpolímero
Os fluorpolímeros oferecem uma magnífica resistência aos produtos químicos e para aplicações de exigência de temperaturas. Exibem baixa tensão superficial (superfície repelente a umidade e não aderente a sujeira), excelente resistência química a muitos produtos agressivos, e boa resistência a temperatura. Igualmente oferecem boa resistência ao envelhecimento, porque não são afetados pelos raios ultravioletas, não se submetem à oxidação, e não absorvem água. Há duas famílias distintas de fluorpolímeros: polímeros fluorados (por exemplo, PTFE) e parcialmente fluorados (por exemplo, PVDF). Os tipos principais rotomoldados são o fluoreto de polivinilideno (PVDF), o etileno-tetrafluoretileno (ETFE), o etileno-clorotrifluoretileno (ECTFE), e o perfluoralkoxi (PFA).
com viscosidade baixa da massa fundida para formar um revestimento liso. Para conseguir isto, a maioria dos materiais é moldada como pó ou peletts de baixa granulometria, embora um número crescente de materiais líquidos seja igualmente usado.
Os materiais são micronizados num padrão de 35 mesh (500 μm). O tamanho médio das partículas do pó é tipicamente ao redor 50 mesh (597μm). Variação desta granulometria, para menos ou para mais, é utilizada para materiais e aplicações especificas. O nylon foi moldado diretamente como peletts , devido a sua habilidade de fluir facilmente além de seu ponto de fusão. A definição de superfície pode ainda ser um problema, e é comum a mistura do pó e de peletts ser usada para produzir uma peça lisa. Mais recentemente, micropeletts na faixa de 0.020 a 0.060pol. (500 a 1500μm) foram usados com sucesso para algumas aplicações. Ofereceram boa moldabilidade e eliminaram a necessidade de micronização. Isto tem o potencial de reduzir o custo e eliminar a operação de cisalhamento da moagem no histórico de calor do material. Entretanto, os níveis de produção da extrusora são mais baixos do que para os peletts feitos sob medidas padrão, e isto aumenta os custos. Usados diretamente como um pelett , eliminam o potencial de contaminação colateral durante a moagem e reduzem a quantidade de poeira produzida durante a moldagem. Os micropeletts tem excelente fluxo livre e podem em alguns casos produzir a distribuição desigual da
espessura da parede, devido ao tempo de residência curto durante a rotação em grandes superfícies planas ou em cantos internos. Alguns moldadores combinaram o pó de 10 a 20% com os peletts para ajudar a produzir uma superfície lisa. Nas situações onde encher um molde com o pó é difícil, a densidade mais elevada dos micropeletts pode permitir que mais material seja
colocado em espaços apertados.
5.1.3.3.1 Processo de micronização O volume do polietileno no mercado da rotomoldagem em todo mundo é de 95% ou mais. O polietileno é um material relativamente resistente que é difícil de se dividir. O método mais comum da micronização é executado usando os moinhos compactadores (de atrito) de alta velocidade que moem peletts de aproximadamente ¹/ 16 a ¼ pol. (5 a 6 mm) no diâmetro. Um moinho compactador usa um disco estacionário e um de giro com uma série de dentes radiais serrilhados usinados dentro de uma carcaça do moinho. Os discos são posicionados opostamente com uma folga estreita de acoplamento do centro das placas à borda exterior. A figura 6.7 mostra o interior de um grande moinho compactador, e a figura 6.8 mostra a disposição de um moinho compactador de dois estágios. Os moinhos modernos tendem à operação horizontal para uma produção mais uniforme do pó e o desgaste reduzido nos dentes de corte. As unidades de produção usam configurações simples, duplas, e triplas do moinho de acordo com a produção exigida. Altas velocidades são exigidas para cortar eficientemente o material na combinação entre as duas placas. Um volante é conectado ao eixo do disco giratório, balançeado para eliminar a vibração em altas velocidades e para reduzir igualmente a deflexão do disco de giro durante o corte. O disco estacionário é montado numa carcaça com circulação de água de resfriamento para controlar a temperatura durante a operação. O disco estacionário pode ser movimentado para dentro e para fora da parte externa da máquina permitindo que a folga entre as caras de corte dos discos seja ajustada.
Folga. A separação entre os discos girando é muito importante para aperfeiçoar o tamanho e a distribuição das partículas. Estas afetam por sua vez a densidade e a taxa de fluxo do pó seco. Os ajustes de uma folga maior produzirão dimensão das partículas maiores; ajustes menores podem
gerar demasiado calor e afetar a produção total do sistema. Em sistemas de dois moinhos, os ajustes típicos da folga para o primeiro moinho podem estar entre 0.010 e 0.020pol. (0.25 a 0. mm); o ajuste para o segundo moinho é tipicamente ao redor 0.010pol. (0.25 mm) a menos do que o do primeiro, mas os discos não devem estar mais próximos do que 0.005pol. (0.125 mm). Os ajustes são afetados pelo tamanho inicial do pelett , a dureza do material, a taxa total de produção, e assim por diante. Aperfeiçoar os ajustes para um único moinho diferirá de um sistema de moinho duplo, tendo em vista que o único moinho atua igualmente como moinho secundário, repassando as partículas maiores do primeiro corte.