
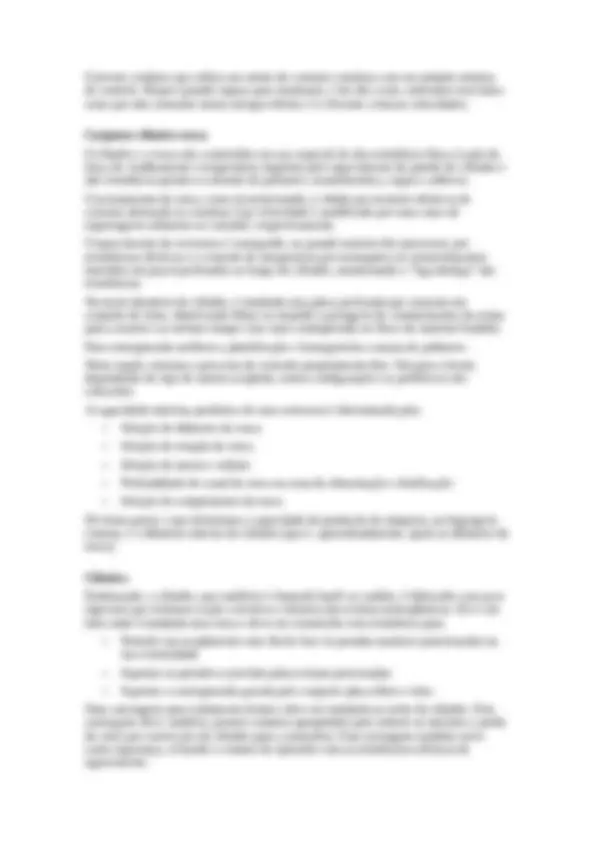
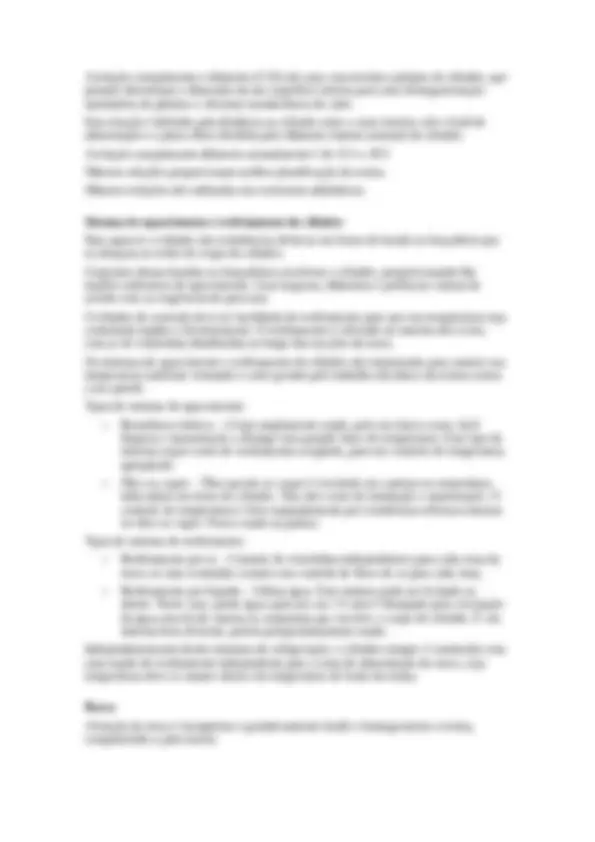
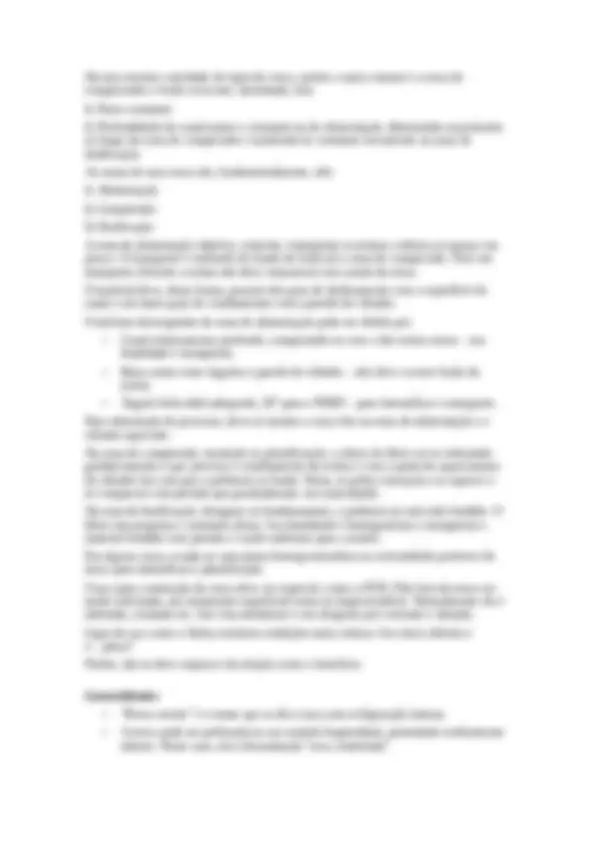
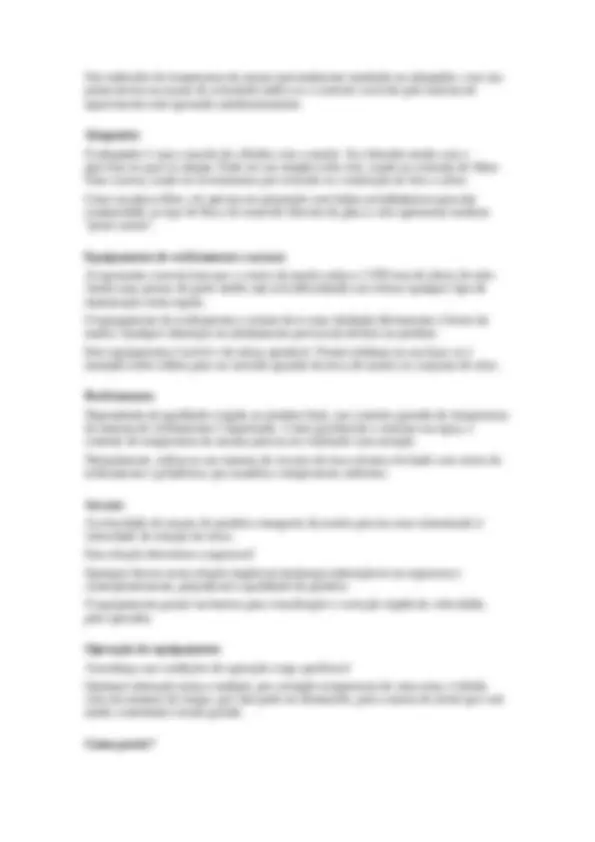
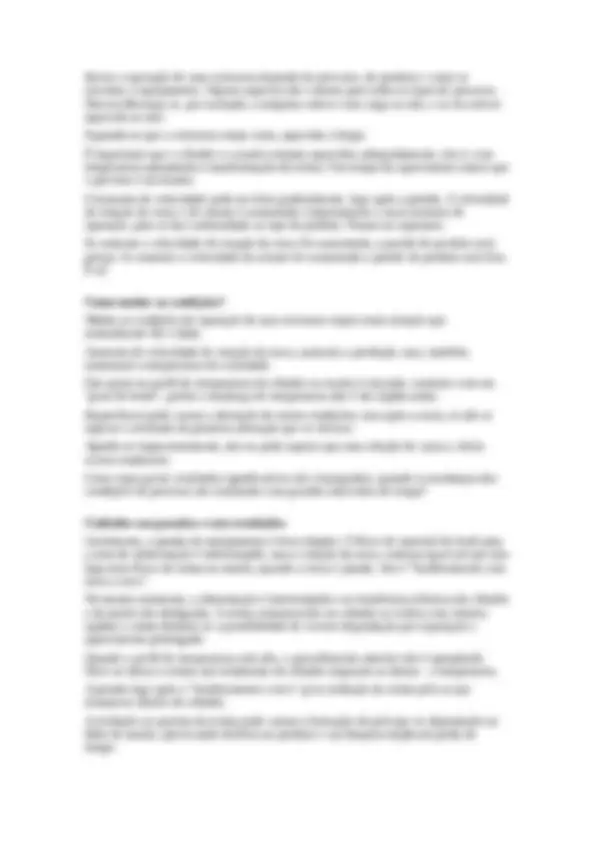
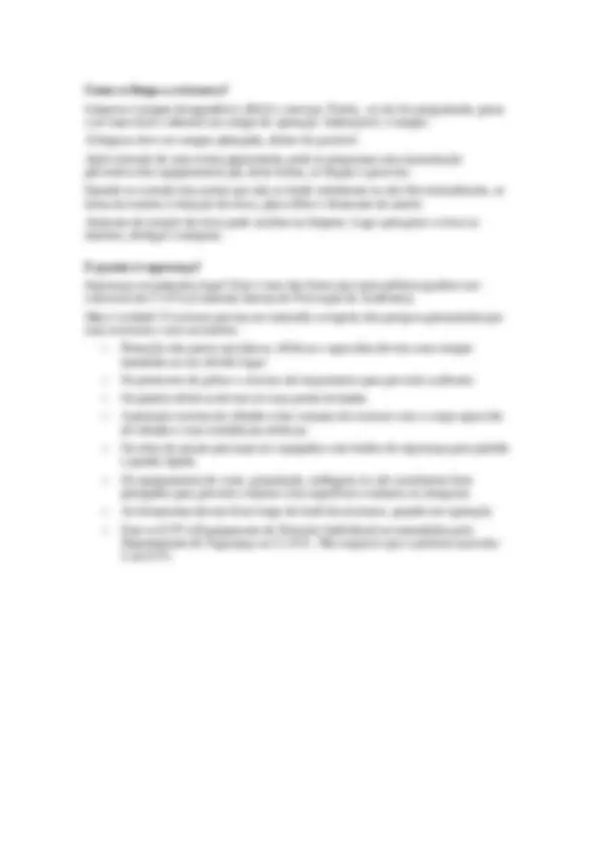
Estude fácil! Tem muito documento disponível na Docsity
Ganhe pontos ajudando outros esrudantes ou compre um plano Premium
Prepare-se para as provas
Estude fácil! Tem muito documento disponível na Docsity
Prepare-se para as provas com trabalhos de outros alunos como você, aqui na Docsity
Os melhores documentos à venda: Trabalhos de alunos formados
Prepare-se com as videoaulas e exercícios resolvidos criados a partir da grade da sua Universidade
Responda perguntas de provas passadas e avalie sua preparação.
Ganhe pontos para baixar
Ganhe pontos ajudando outros esrudantes ou compre um plano Premium
Comunidade
Peça ajuda à comunidade e tire suas dúvidas relacionadas ao estudo
Descubra as melhores universidades em seu país de acordo com os usuários da Docsity
Guias grátis
Baixe gratuitamente nossos guias de estudo, métodos para diminuir a ansiedade, dicas de TCC preparadas pelos professores da Docsity
Moldes plasticos
Tipologia: Notas de estudo
1 / 10
Esta página não é visível na pré-visualização
Não perca as partes importantes!
Moldagem por Extrusão
Extrusão: A matéria-prima amolecida é expulsa através de uma matriz instalada no equipamento denominada extrusora, produzindo um produto que conserva a sua forma ao longo de sua extensão. Os produtos flexíveis, como embalagens, sacolas, sacos e bobinas também conhecidos como filme, após o processo de extrusão, podem ser gravados sendo modelados o produto final com soldas e cortes. Os produtos rígidos ou semi-rígidos, como tubos, perfis, mangueiras e chapas, tem o mesmo processo, havendo mudança da matéria-prima e matriz.
Extrusão é um processo de transformação de termoplásticos. O processo utiliza um equipamento denominado extrusora que é constituído de um cilindro aquecido dentro do qual uma rosca. Este conjunto plastificada a resina.
A extrusora é alimentada com resina através de um funil alimentador situado na seção traseira. A resina é transportada ao longo do cilindro pelo movimento de rotação da rosca.
As resinas são fundidas gradativamente pelo contato com a parede aquecida do cilindro e o calor gerado cisalhamento da massa entre a rosca e o cilindro.
A rosca comprime o polímero através da matriz, que molda o fundido na sua forma final.
O diâmetro externo da rosca é igual ao diâmetro interno do cilindro com a devida folga proporcional ao diâmetro e comprimento da rosca.
Um sistema de aquecimento e resfriamento, composto, geralmente, de quatro ou mais termopares instalados no corpo do cilindro, informa a temperatura do processo.
A rosca á acionada por um conjunto motor – caixa de redução.
A resina já totalmente plastificada é forçada a passar por uma placa perfurada que sustenta um jogo de telas, cuja finalidade é filtrar os eventuais contaminantes da massa fundida e criar uma contrapressão no fluxo que se dirige à matriz.
O dimensionamento do equipamento é padronizado pelo diâmetro interno do cilindro e varia, normalmente, entre 45 a 200 mm. A capacidade de produção é dada, normalmente, por:
Este processo é comum a vários segmentos da terceira geração petroquímica, como:
Até a matriz ou cabeçote, este processo é semelhante a todos os tipos de transformação mencionados. A matriz é que dá forma, ou molda o termoplástico fundido no produto que se pretende obter.
Motor e caixa de redução
A rosca é acionada por motor elétrico, geralmente de 220, 380 ou 440 volts. A força requerida é de 1 a 2 CV do motor para cada 2,3 a 4,5 kg/h de resina.
Portanto o processo para extrudar 23 a 45 kg/h de resina requer um motor de 10 a 20 CV.
O mais comum é um conjunto de velocidade variáveis formado por um motor com potência, geralmente, 30% maior que a exigida pela extrusora na sua condição mais crítica e um variador de velocidade que pode ser eletromagnético ou mecânico.
A massa plástica extrudada depende da velocidade da rosca. Assim, aumentando-se a velocidade de rotação da rosca, a massa de plástico fundido bombeado pela extrusora é proporcional. Este mecanismo deve proporcional uma velocidade constante que é importantíssima ao processo.
Para se alterar a taxa de bombeamento deve-se ajustar a velocidade da rosca de duas maneiras:
A velocidade dos motores elétricos é normalmente de 1.750 rpm em ligações diretas com a rosca. As roscas comuns têm suas rotações de 20 a 200 rpm e por esta razão as caixas redutoras são usadas entre o motor e a rosca.
Geralmente, estas caixas redutoras requerem o mínimo de manutenção, como por exemplo, verificação periódica do nível de óleo. A redução de velocidade da rosca é efetuada através de polias e correias, unindo o motor à caixa redutora.
As unidades de conversão proporcionam reduções de velocidade na razão de 8 para 1, ajustando-as na faixa de 20 a 160 rpm.
Para que a velocidade seja mudada num processo de extrusão, é necessários conhecer-se as características físicas da resina e a potência do motor.
Acionamento
Dois são, atualmente, os tipos de acionamento mais usados no processo de extrusão:
Eletromagnético que usa um motor de corrente alternada, velocidade constante e acoplamento magnético. O controle de velocidade é mantido pelo ajuste do campo magnético no acoplamento. Este tipo de acoplamento é pequeno e de baixo custo. Sua grande desvantagem é o seu alto nível de ruído, superando, às vezes, o nível de 80 decibéis que é o máximo tolerado pelo ouvido humano.
A relação comprimento e diâmetro (C/D) são uma característica própria do cilindro, que permite determinar a dimensão da sua superfície interna para uma homogeneização satisfatória do plástico e eficiente transferência de calor.
Esta relação é definida pela distância no cilindro entre a zona traseira sob o funil de alimentação e a placa-filtro dividida pelo diâmetro interno nominal do cilindro.
A relação comprimento-diâmetro normalmente é de 15:1 a 30:
Maiores relações proporcionam melhor plastificação da resina.
Menores relações são utilizadas em extrusoras adiabáticas.
Sistema de aquecimento e resfriamento do cilindro
Para aquecer o cilindro são resistências elétricas em forma de banda ou braçadeira que se abraçam ao redor do corpo do cilindro.
Conjuntos dessas bandas ou braçadeiras envolvem o cilindro, proporcionando-lhe regiões uniformes de aquecimento. Suas larguras, diâmetros e potências variam de acordo com as exigências do processo.
O cilindro de extrusão deve ter facilidade de resfriamento para que sua temperatura seja controlada rápida e eficientemente. O resfriamento é efetuado na maioria das vezes, com ar de ventoinhas distribuídas ao longo das secções da rosca.
Os sistemas de aquecimento e resfriamento do cilindro são importantes para manter sua temperatura uniforme retirando o calor gerado pelo trabalho mecânico da resina contra a sua parede.
Tipos de sistema de aquecimento:
Tipos de sistema de resfriamento:
Independentemente destes sistemas de refrigeração, o cilindro sempre é construído com uma região de resfriamento independente para a zona de alimentação da rosca, cuja temperatura deve se manter abaixo da temperatura de fusão da resina.
Rosca
A função da rosca é transportar e gradativamente fundir e homogeneizar a resina, comprimindo-a pela matriz.
Há uma enorme variedade de tipos de rosca, porém o mais comum é a rosca de compreensão e fusão crescente, desenhada com:
1. Passo constante 2. Profundidade do canal maior e constante na de alimentação, diminuindo suavemente ao longo da zona de compressão e mantendo-se constante novamente na zona de dosificação.
As zonas de uma rosca são, fundamentalmente, três:
1. Alimentação 2. Compressão 3. Dosificação
A zona de alimentação objetiva, somente, transportar as resinas, embora as aqueça um pouco. O transporte é realizado do fundo do funil até a zona de compressão. Para um transporte eficiente a resina não deve remanescer nos canais da rosca.
O material deve, desta forma, possuir alto grau de deslizamento com a superfície do canal e um baixo grau de cisalhamento com a parede do cilindro.
O máximo desempenho da zona de alimentação pode ser obtido por:
Para otimização do processo, deve-se manter a rosca fria na zona de alimentação e o cilindro aquecido.
Na zona de compressão, transição ou plastificação, a altura do filete vai se reduzindo gradativamente o que provoca o cisalhamento da resina e com a ajuda do aquecimento do cilindro faz com que o polímero se funda. Nesta, os grãos começam a se aquecer e se compactar com pressão que gradualmente vai aumentando.
Na zona de dosificação, dosagem ou bombeamento, o polímero já está todo fundido. O filete tem pequena e constante altura. Sua finalidade é homogeneizar e transportar o material fundido com pressão e vazão uniforme para a matriz.
Em alguns casos, acopla-se uma ponta homogeneizadora na extremidade posterior da rosca para intensificar a plastificação.
O aço para construção da rosca deve ser especial, como o 8550. Pelo fato da rosca ser muito solicitada, um tratamento superficial torna-se imprescindível. Normalmente ela é nitretada, cromada etc. Isto visa minimizar o seu desgaste por corrosão e abrasão.
Ligas de aço como o Xaloy resistem condições mais criticas. Seu único defeito é o ...preço!
Porém, não se deve esquecer da relação custo x beneficio.
Generalidades
O projeto e construção da placa requerem precisão, para serem evitados "pontos mortos", que são espaços que retêm o plástico fundido e degradam ou contaminam o processo ou o produto.
Conjunto de telas mais freqüentemente usados na extrusão do PEBD
Índice de fluidez ( g/10m ) "Mesh" 0,3 a 0,7 30-60-80- 1,0 a 2,0 30-60-100- 2,5 a 3,0 30-80-120-
"Mesh" é o número de aberturas por polegada quadrada.
Controle do processo
Toda extrusora tem uma instrumentação própria, que facilita ao máximo sua operação e manutenção. Um painel de controle mais simples possível é configurado com:
Cada zona possui um amperímetro individual que indica se o termopar, resistência elétrica ou os instrumentos estão operando normalmente.
Equipamentos de tecnologia mais avançada podem possuir, também:
"Este último encontra campo junto aos processos que contribuem para controlar e otimizar as paredes dos filmes. Assim melhora-se a relação do binômio transformador/ usuário através do trinômio custo / beneficio / desempenho.
O SDCD – Sistema Digital de Controle Distribuído (ou Distância) consiste em um sistema computadorizado que recebe um "input" das características da matéria-prima a ser utilizada e do filme que se pretende produzir. A seguir, se estabelecem as condições ideais de processamento e, também, monitora-se o equipamento para obter o perfil ideal traçado de temperatura, regulagem de espessura, velocidade de arraste, vazão de ar refilagem do filme (acerto da largura da bobina)."
Matéria publicada no Jornal de Plásticos em setembro de 1994.
Um indicador de pressão da massa é instalada no corpo do cilindro, antes da placa-filtro e é muito útil. Ele indicará se as telas estão saturadas ou se há variação na tempetura de massa. Poderá até ser um sinalizador de problemas, desligar o motor da extrusora, quando houver aumento indevido de pressão.
Um indicador de temperatura da massa opcionalmente instalado no adaptador, com sua ponta imersa na massa do extrudado indica se o controle exercido pelo sistema de aquecimento está operando satisfatoriamente.
Adaptador
O adaptador é uma conexão do cilindro com a matriz. Seu desenho muda com o processo no qual se adapta. Pode ser um simples tubo reto, usado na extrusão de filme. Uma cruzeta, usada no revestimento por extrusão ou construção de fios e cabos.
Como na placa-filtro, ele precisa ser projetado com linhas aerodinâmicas para dar continuidade ao tipo de fluxo do material efluente da placa e não apresentar nenhum "ponto morto".
Equipamento de resfriamento e arraste
A ergonomia convenciona que o centro da matriz esteja a 1.050 mm de altura do solo. Assim uma pessoa de porte médio não terá dificuldades em efetuar qualquer tipo de manutenção nesta região.
O equipamento de resfriamento e arraste deve estar alinhado diretamente à frente da matriz. Qualquer distorção no alinhamento provocaria defeito no produto.
Este equipamento é móvel e de altura ajustável. Possui roldanas na sua base ou é montado sobre trilhos para ser movido quando da troca de matriz ou conjunto de telas.
Resfriamento
Dependendo da qualidade exigida no produto final, um controle apurado de temperatura do sistema de resfriamento é importante. Como geralmente o sistema usa água, o controle de temperatura da mesma precisa ser realizado com atenção.
Normalmente, utiliza-se um sistema de circuito de troca térmica fechado com torres de resfriamento e geladeiras, que mantêm a temperatura uniforme.
Arraste
A velocidade de arraste do produto emergente da matriz precisa estar sintonizado à velocidade de rotação da rosca.
Esta relação determina a espessura!
Qualquer desvio nesta relação implicará mudanças indesejáveis na espessura e conseqüentemente, prejudicará a qualidade do produto.
O equipamento possui tacômetro para visualização e correção rápida da velocidade, pelo operador.
Operação do equipamento
A mudança nas condições de operação exige paciência!
Qualquer alteração numa condição, por exemplo temperatura de uma zona, é obtida com um mínimo de tempo, que não pode ser diminuído, pois a massa de metal que está sendo controlada é muito grande.
Como partir?
Como se limpa a extrusora?
Limpeza é sempre desagradável, difícil e onerosa. Porém...se ela for programada, passa a ser mais fácil e diminui seu tempo de operação. Indesejável, é sempre.
A limpeza deve ser sempre planejada, dentro do possível.
Após extrusão de uma resina pigmentada, pode se programar uma manutenção preventiva dos equipamentos par, desta forma, se limpar o processo.
Quando se extruda uma resina que não se funde totalmente ou não flui normalmente, se torna necessária à remoção da rosca, placa-filtro e desmonte da matriz.
Aumento de rotação da rosca pode auxiliar na limpeza. Logo após girar a rosca ao máximo, desligar a máquina.
E quanto à segurança?
Segurança em primeiro lugar! Esta é uma das frases que mais prêmios ganhou nos concursos da C.I.P.A.(Comissão Interna de Prevenção de Acidentes).
Mas é verdade! O extrusor precisa ser instruído a respeito dos perigos apresentados por uma extrusora e seus acessórios.