

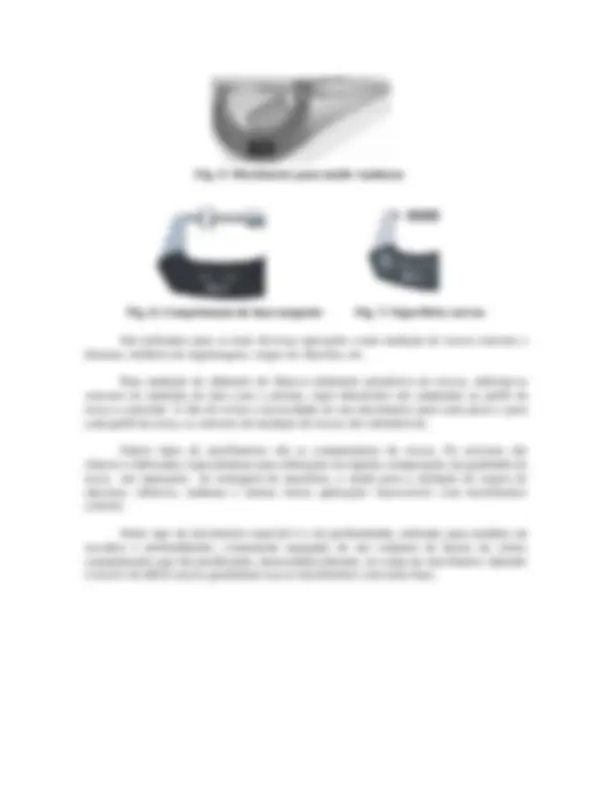
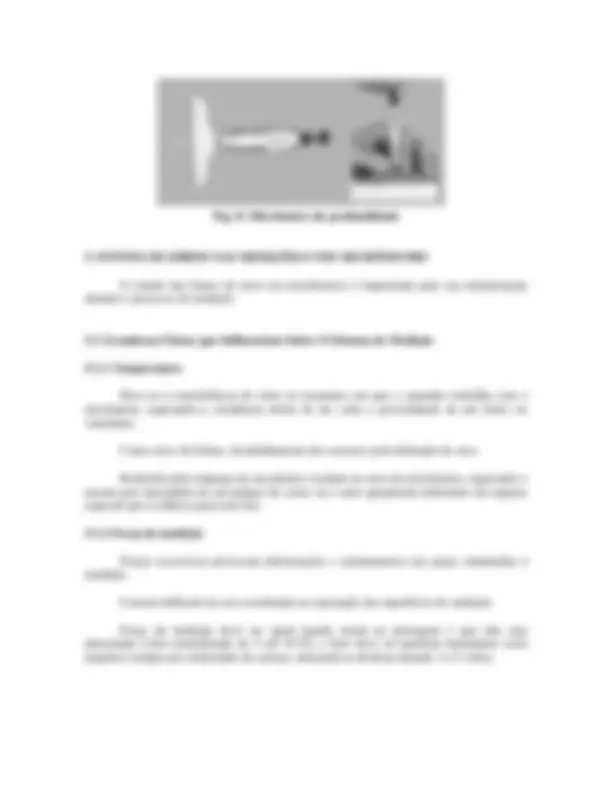
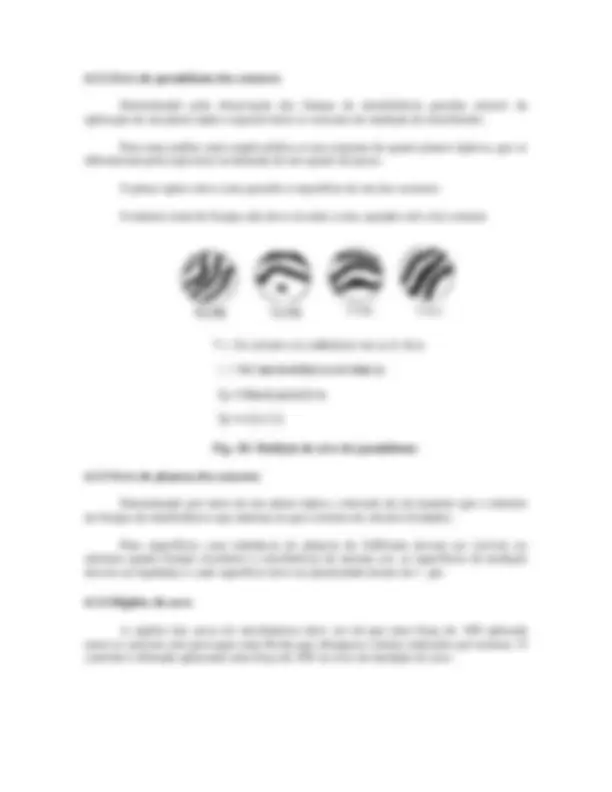
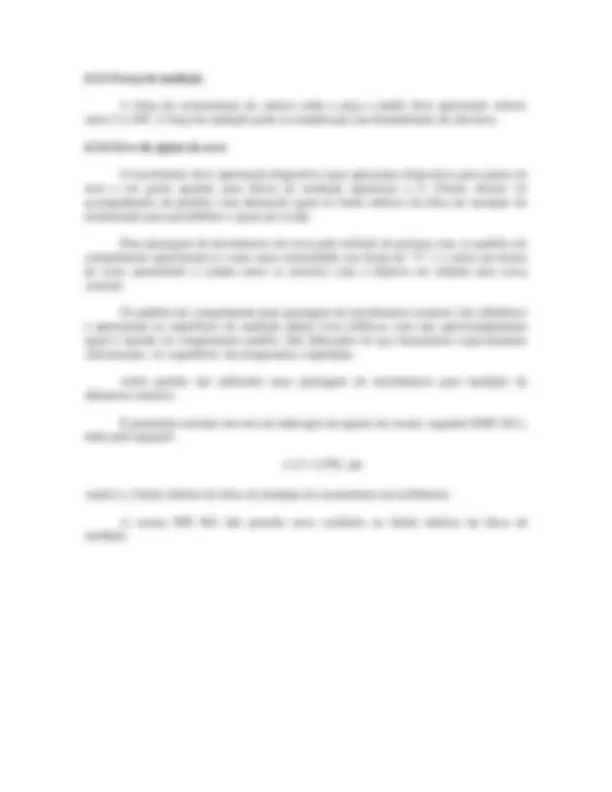
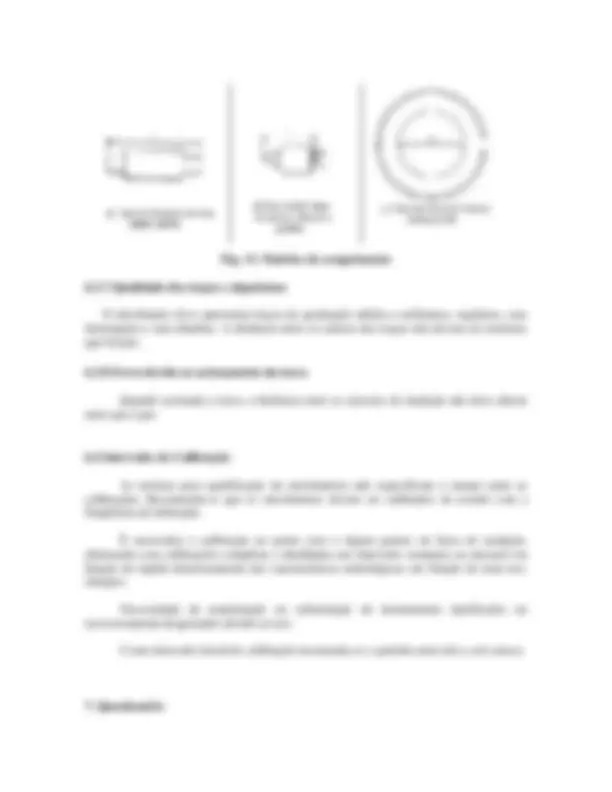
Estude fácil! Tem muito documento disponível na Docsity
Ganhe pontos ajudando outros esrudantes ou compre um plano Premium
Prepare-se para as provas
Estude fácil! Tem muito documento disponível na Docsity
Prepare-se para as provas com trabalhos de outros alunos como você, aqui na Docsity
Os melhores documentos à venda: Trabalhos de alunos formados
Prepare-se com as videoaulas e exercícios resolvidos criados a partir da grade da sua Universidade
Responda perguntas de provas passadas e avalie sua preparação.
Ganhe pontos para baixar
Ganhe pontos ajudando outros esrudantes ou compre um plano Premium
Comunidade
Peça ajuda à comunidade e tire suas dúvidas relacionadas ao estudo
Descubra as melhores universidades em seu país de acordo com os usuários da Docsity
Guias grátis
Baixe gratuitamente nossos guias de estudo, métodos para diminuir a ansiedade, dicas de TCC preparadas pelos professores da Docsity
Metrologia micrômetros
Tipologia: Notas de estudo
1 / 11
Esta página não é visível na pré-visualização
Não perca as partes importantes!
Os micrômetros são instrumentos de medição de comprimentos vastamente utilizados na área metrológica.
Estes instrumentos foram os primeiros a atenderem o princípio de Ernest Abbé, que diz que o mensurando deve estar posicionado no eixo da escala do instrumento de medição.
O micrômetro mede por meio de duas superfícies de medição, sendo que uma delas se movimenta por meio de um fuso roscado. Esta superfície é a face frontal do fuso, ou parafuso micrométrico.
Um fuso roscado possui, da mesma forma que uma escala, uma divisão contínua e uniforme, representada pelos filetes da rosca. A tomada de medida é efetuada girando o fuso na porca correspondente, obtendo-se entre estes elementos um movimento relativo de um passo para cada volta completa. Frações de passo podem ser obtidas, subdividindo-se uma volta completa em tantas partes quantas se queira.
Os erros do movimento de avanço de um fuso de medição que corresponde aos erros de divisão de uma escala dependem principalmente dos erros do passo da rosca, que geram erros progressivos e periódicos, e das características geométricas e de posicionamento das superfícies de medição e do tambor de leitura.
O ajuste do ponto zero do micrômetro deve ser efetuado para minimizar seus erros. O valor Eo, correspondente à “linha zero” deve ser indicado para que esta possa ser traçada. A linha zero distribui os erros globais em torno de si.
Fig. 1: Ajuste do ponto zero
A norma ISO 3611 especifica que para um micrômetro de 0 – 25 mm, Eo pode apresentar valor igual a ±2 μm.
Pode ocorrer também o erro devido ao “curso morto”, que se origina pela folga entre rosca e porca. Para que não ocorra, o movimento final do fuso deve ser no mesmo sentido.
O principal mecanismo de um micrômetro é o fuso roscado. Seu passo é de 0,5 mm geralmente, ou seja, o deslocamento longitudinal para uma volta completa é de 0,5 mm. Os materiais empregados para sua fabricação são aço liga ou aço inoxidável. Eles são retificados e temperados
O tambor divide uma rotação em 50 partes, ou seja, uma divisão do tambor corresponde a 0,01 mm.
O tubo graduado possui as escalas de milímetro e de meio milímetro, e ainda pode ter uma escala auxiliar chamada nônio, que geralmente tem 10 divisões.
A resolução comumente adotada em micrômetros quando o mesmo não possui nônio é igual a 1/5 da divisão de escala, ou seja, 2 μm, caso contrário é dada pelo próprio nônio e vale 1 μm. Nos micrômetros digitais a resolução é equivalente ao incremento digital, que em geral é 1 μm.
A trava impede o deslocamento do fuso, possibilitando a fixação de uma medida qualquer.
A catraca é um limitador de torque que possibilita uma força de medição constante.
O isolamento térmico evita erros devido à dilatação térmica do arco.
Os sensores de medição são placas de metal duro que resistem ao desgaste que estão sujeitos por estarem em contato com a peça a ser medida.
No eliminador de folga, graças ao ajuste cônico sobre o guia do fuso, com o aperto da porca consegue-se eliminar o curso morto, permitindo ainda deslizamento suave ao girar o fuso.
Para medidas grandes, a bigorna, e às vezes também o mecanismo micrométrico são construídos de modo ajustável, permitindo faixas de medição maiores do que 25 mm, por exemplo, de 300 a 350 mm. Nestes casos deve-se ajustar a bigorna e o mecanismo micrométrico de 25 em 25 mm, com auxílio de blocos padrão ou hastes padrão calibradas.
O arco é feito de aço forjado ou ferro fundido especial e deve ser livre de tensões e envelhecido artificialmente.
Fig. 5: Micrômetro para medir ranhuras
Fig. 6: Comprimento de base tangente Fig. 7: Superfícies curvas
São utilizados para as mais diversas operações como medição de roscas externas e internas, módulos de engrenagens, rasgos de chavetas, etc.
Para medição do diâmetro de flancos (diâmetro primitivo) de roscas, utilizam-se sensores de medição do tipo cone e prisma, cujas dimensões são adaptadas ao perfil da rosca a controlar. A fim de evitar a necessidade de um micrômetro para cada passo e para cada perfil da rosca, os sensores de medição de roscas são substituíveis.
Outros tipos de micrômetros são os comparadores de roscas. Os sensores são cônicos e fabricados especialmente para utilização em rápidas comparações da qualidade da rosca em operações de usinagem de parafusos, e ainda para a medição de rasgos de chavetas, rebaixos, ranhuras e muitas outras aplicações inacessíveis com micrômetros comuns.
Outro tipo de micrômetro especial é o de profundidade, utilizado para medidas de ressaltos e profundidades, comumente equipado de um conjunto de hastes de vários comprimentos que são parafusadas, intercambiavelmente, no corpo do micrômetro. Quando o local é de difícil acesso geralmente usa-se micrômetros com meia base.
Fig. 8: Micrômetro de profundidade
O estudo das fontes de erros em micrômetros é importante para sua minimização durante o processo de medição.
5.1 Grandezas Físicas que Influenciam Sobre O Sistema de Medição
5.1.1 Temperatura
Deve-se à transferência de calor no momento em que o operador trabalha com o micrômetro segurando-o, incidência direta de luz solar e proximidade de um forno ou ventilador.
Causa erros de leitura, desalinhamento dos sensores pela dilatação do arco.
Reduzido pelo emprego de um plástico isolante no arco do micrômetro, segurando o mesmo por intermédio de um pedaço de couro ou o mais apropriado utilizando um suporte especial que se fabrica para este fim.
5.1.2 Força de medição
Forças excessivas provocam deformações e achatamentos nas peças submetidas à medição.
Causam deflexão do arco resultando na separação das superfícies de medição.
Força de medição deve ser igual àquela usada na ajustagem e que não seja demasiada (valor normalizado de 5 até 10 N), o fuso deve ser apertado lentamente (sem impulso) sempre por intermédio da catraca, deixando-se deslizar durante 3 a 5 voltas.
dos resultados. As normas especificam que os comprimentos dos blocos utilizados sejam os seguintes: 2,5 - 5,1 - 7,7 -10,3 -12,9 - 15,0 - 17,6 - 20,2 - 22,08 e 25,0 mm. O ponto zero ou o limite inferior da faixa de medição também é um ponto de calibração.
O erro máximo (por norma) para qualquer ponto da faixa de medição do micrômetro é determinado por:
onde L é o limite inferior da faixa de operação.
Fig. 9: Erro máximo de micrômetros
As normas definem que o micrômetro deve atender a dois requisitos simultâneos considerando-se o processo de calibração de um instrumento com faixa de medição 0-25 mm:
que este erro pode assumir sinal positivo ou negativo (ISO 3611). A diferença entre a tendência máxima e mínima determinada na calibração não pode
Diferença entre as duas normas: ISO permite uma tendência residual de zero e a DIN exige que o instrumento seja ajustado obrigatoriamente de modo a obter erro igual a “zero” no ponto zero ou limite inferior da faixa de medição.
6.3.1.2 Repetitividade
É um erro aleatório com confiabilidade de 95%, ocorre em medições repetidas realizadas em condições variáveis.
6.3.2 Erro de paralelismo dos sensores
Determinado pela observação das franjas de interferência geradas através da aplicação de um plano óptico especial entre os sensores de medição do micrômetro
Para uma análise mais ampla utiliza-se um conjunto de quatro planos ópticos, que se diferenciam pela espessura escalonada de um quarto de passo.
O plano óptico deve estar paralelo à superfície de um dos sensores.
O número total de franjas não deve exceder a oito, quando sob a luz comum.
Fig. 10: Medição de erro de paralelismo
6.3.3 Erro de planeza dos sensores
Determinado por meio de um plano óptico, colocado de tal maneira que o número de franjas de interferência seja mínima ou que existam em círculos fechados.
Para superfícies com tolerância de planeza de 0,001mm devem ser visíveis no máximo quatro franjas circulares e concêntricas da mesma cor, as superfícies de medição
6.3.4 Rigidez do arco
A rigidez dos arcos de micrômetros deve ser tal que uma força de 10N aplicada entre os sensores não provoque uma flexão que ultrapasse valores indicados por normas. O controle é efetuado aplicando uma força de 10N no eixo de medição do arco.
Fig. 11: Padrões de comprimento
6.3.7 Qualidade dos traços e algarismos
O micrômetro deve apresentar traços de graduação nítidos e uniformes, regulares, sem interrupção e sem rebarbas. A distância entre os centros dos traços não devem ser menores
6.3.8 Erros devido ao acionamento da trava
Quando acionada a trava, a distância entre os sensores de medição não deve alterar
6.4 Intervalos de Calibração
As normas para qualificação de micrômetros não especificam o tempo entre as calibrações. Recomenda-se que os micrômetros devem ser calibrados de acordo com a freqüência de utilização.
É necessária a calibração no ponto zero e alguns pontos da faixa de medição, alternando com calibrações completas e detalhadas em intervalos semanais ou mensais em função do rápido deterioramento das características metrológicas em função do mau uso, choques.
Necessidade de manutenção ou substituição de instrumentos danificados ou excessivamente desgastados devido ao uso.
Como intervalo inicial de calibração recomenda-se o período entre três a seis meses.
7. Questionário
7.1 Qual a relação entre o passo da rosca do parafuso micrométrico e o valor de divisão de escala do micrômetro?
Um giro completo do fuso corresponde a um deslocamento longitudinal de um passo, que é lido na escala do tubo graduado. Se o passo for de 0,5 mm, cada giro corresponde a 0,5 mm e como o tambor é dividido em 50 partes o valor de escala é de (0,5 /
7.2 Qual a vantagem em se utilizar micrômetros digitais em relação aos mecânicos?
Permitem a realização de medições com menor incerteza de medição devido à facilidade de leitura no instrumento, se ganha tempo, diminui-se os erros de medição associados principalmente a construção da escala e de paralaxe.
7.3 Para que podemos utilizar os micrômetros especiais?
São utilizados para as mais diversas operações como medição de roscas externas e internas, módulos de engrenagens, rasgos de chavetas, para medidas de ressaltos e profundidades, etc.
7.4 O que podemos fazer para minimizar os erros em uma medição com micrômetro?
Utilizar a catraca aliada a um movimento suave e lento para garantir uma força de medição constante resultando em uma pequena dispersão de medição, segurar o micrômetro num suporte especial para que não haja troca de calor do operador com o micrômetro evitando erro de leitura e desalinhamento dos sensores pela dilatação do arco, não empurrar o micrômetro sobre superfícies sujas ou ásperas, não abrir o micrômetro para uma certa medida, acionar a trava e forçá-lo sobre a peça evitando um desgaste rápido dos sensores.
7.5 Cite os parâmetros a serem verificados na qualificação de um micrômetro.
Erros de indicação e repetitividade, erro de paralelismo dos sensores, erro de planeza dos sensores, rigidez do arco, força de medição, erro de ajuste do zero ou do limite inferior da faixa de medição, qualidade dos traços e algarismos, erros devido ao acionamento da trava.