
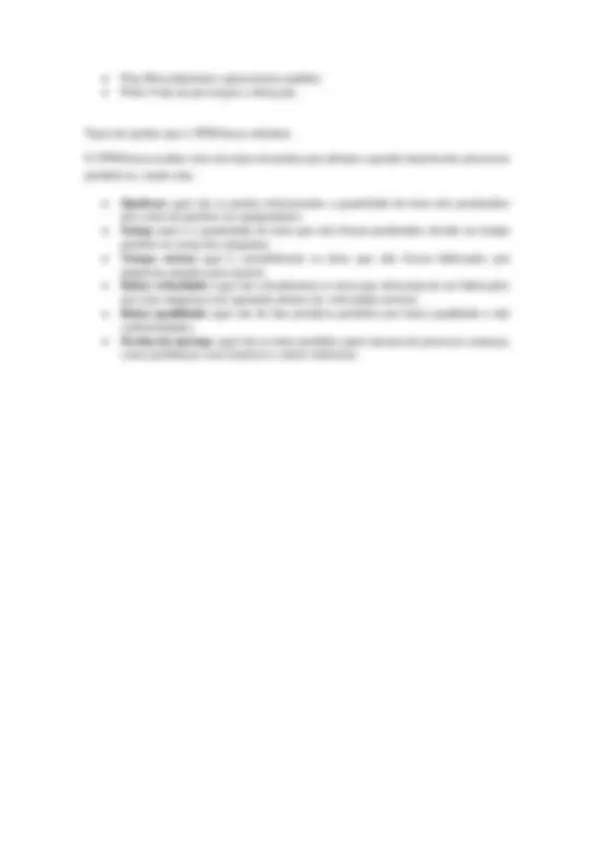
Estude fácil! Tem muito documento disponível na Docsity
Ganhe pontos ajudando outros esrudantes ou compre um plano Premium
Prepare-se para as provas
Estude fácil! Tem muito documento disponível na Docsity
Prepare-se para as provas com trabalhos de outros alunos como você, aqui na Docsity
Os melhores documentos à venda: Trabalhos de alunos formados
Prepare-se com as videoaulas e exercícios resolvidos criados a partir da grade da sua Universidade
Responda perguntas de provas passadas e avalie sua preparação.
Ganhe pontos para baixar
Ganhe pontos ajudando outros esrudantes ou compre um plano Premium
Comunidade
Peça ajuda à comunidade e tire suas dúvidas relacionadas ao estudo
Descubra as melhores universidades em seu país de acordo com os usuários da Docsity
Guias grátis
Baixe gratuitamente nossos guias de estudo, métodos para diminuir a ansiedade, dicas de TCC preparadas pelos professores da Docsity
A manutenção produtiva total (tpm) é uma estratégia gerencial japonesa criada por seiichi nakajima na década de 1970, que visa aumentar a produtividade e reduzir perdas integrando operações e manutenção. A tpm envolve todos os profissionais da empresa para produzir itens de alta qualidade e reduzir interrupções na linha de produção. Os benefícios incluem aumento da produtividade geral, redução de paradas repentinas, redução de defeitos e reclamações, redução de custos de produção e melhoria contínua. A tpm capacita operadores para realizar manutenções simples e utiliza manutenção planejada e manutenção da qualidade.
O que você vai aprender
Tipologia: Manuais, Projetos, Pesquisas
1 / 2
Esta página não é visível na pré-visualização
Não perca as partes importantes!
A TPM é uma filosofia gerencial para aumentar a produtividade de um processo produtivo ao reduzir perdas, paradas e falhas integrando os setores de manutenção e operação. A TPM foi criada na década de 1970 pelo japonês Seiichi Nakajima com o objetivo de reduzir erros através da manutenção produtiva total. A ideia é ir além da manutenção dos equipamentos e envolver todos os profissionais da empresa em prol de uma produção com produtos de qualidade superior e com uma linha produtiva com zero quebras, acidentes ou defeitos. Isso requer uma mudança comportamental na empresa, já que os funcionários precisarão abraçar a nova cultura da TPM. A ideia é aproximar os funcionários dos processos e equipamentos, para assim melhorar os resultados gerais.
A manutenção produtiva total traz diversos benefícios para a indústria que aplica seus conceitos. Para deixar mais claro, irei listar aqui alguns dos principais benefícios da filosofia, confira:
Aumento da produtividade geral da indústria Aumento da eficiência da planta Redução de paradas repentinas Redução nos defeitos Redução nas reclamações dos clientes Redução de custos de produção Aumento de sugestões de melhoria partindo de funcionários Auto-gestão da equipe ambiente de trabalho mais organizado e limpo Manutenção autonoma
A primeira característica da filosofia TPM é capacitar e empoderar os operadores para
realizarem manutenções simples no maquinário que trabalham. Dessa forma a empresa
evita problemas mais graves que poderiam gerar paradas no processo produtivo e aumenta
a produtividade geral.
Manutenção planejada
Aqui a empresa utiliza a manutenção preventiva e a manutenção preditiva para evitar
problemas nas máquinas da produção.
Essa etapa é cumprida prevenindo interrupções nas máquinas utilizando material
sobressalente e buscando inconsistências para identificar problemas no processo
produtivo.
Manutenção da qualidade
Nesta etapa a empresa busca manter os níveis de qualidade para que a empresa não acabe
gerando produtos defeituosos ou com não conformidades.
A empresa pode fazer isso utilizando ferramentas como:
Pop (Procedimentos operacionais padrão) Poka Yoke de prevenção e detecção;
Tipos de perdas que a TPM busca eliminar
O TPM busca acabar com seis tipos de perdas que afetam a grande maioria dos processos
produtivos, sendo elas:
Quebras: aqui são as perdas relacionadas a quantidade de itens não produzidos por conta de quebras no equipamento. Setup: aqui é a quantidade de itens que não foram produzidos devido ao tempo perdido no setup das máquinas. Tempo ocioso: aqui é contabilizado os itens que não foram fabricados por pequenas paradas para ajustes. Baixa velocidade: aqui são considerados os itens que deixaram de ser fabricados por uma máquina está operando abaixo da velocidade normal. Baixa qualidade: aqui são de fato produtos perdidos por baixa qualidade e não conformidades. Perdas de startup: aqui são os itens perdidos antes mesmo do processo começar, como problemas com insumos e outros materiais.