
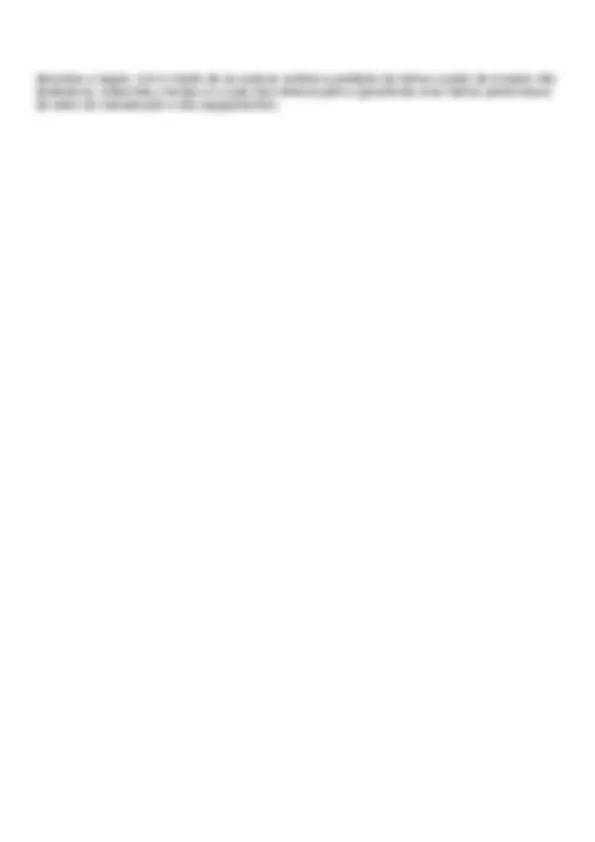

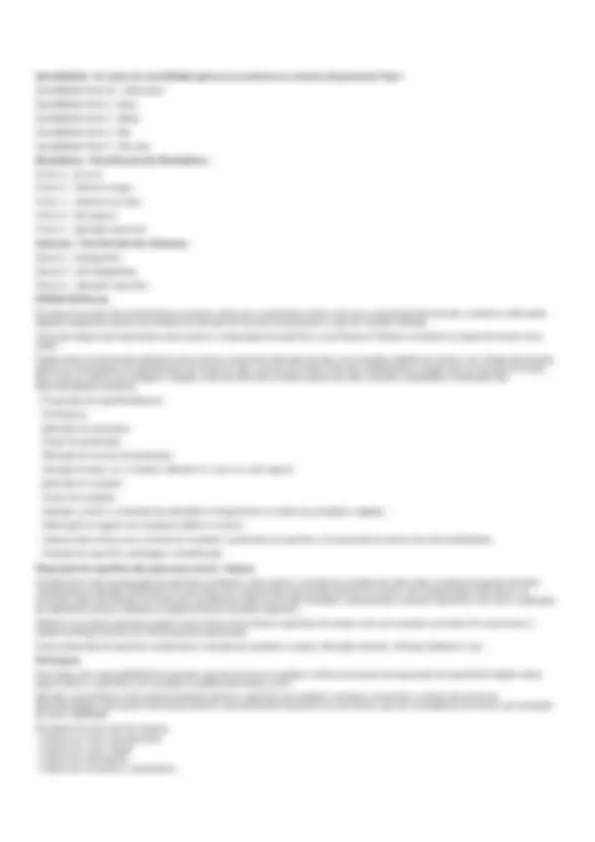
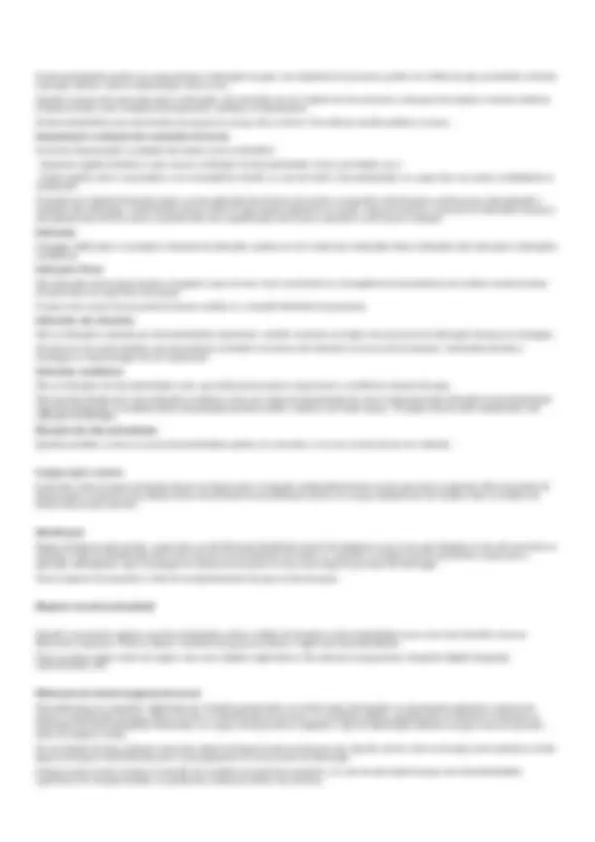
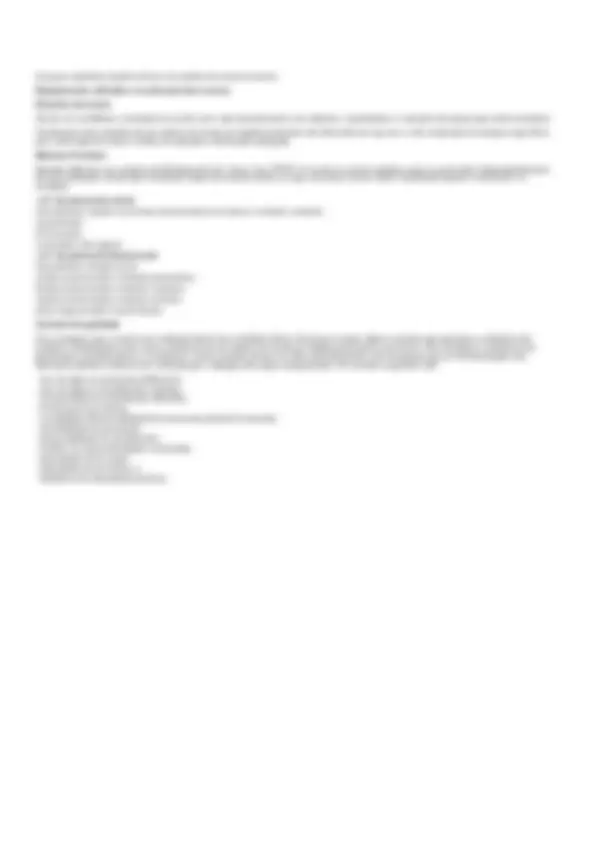
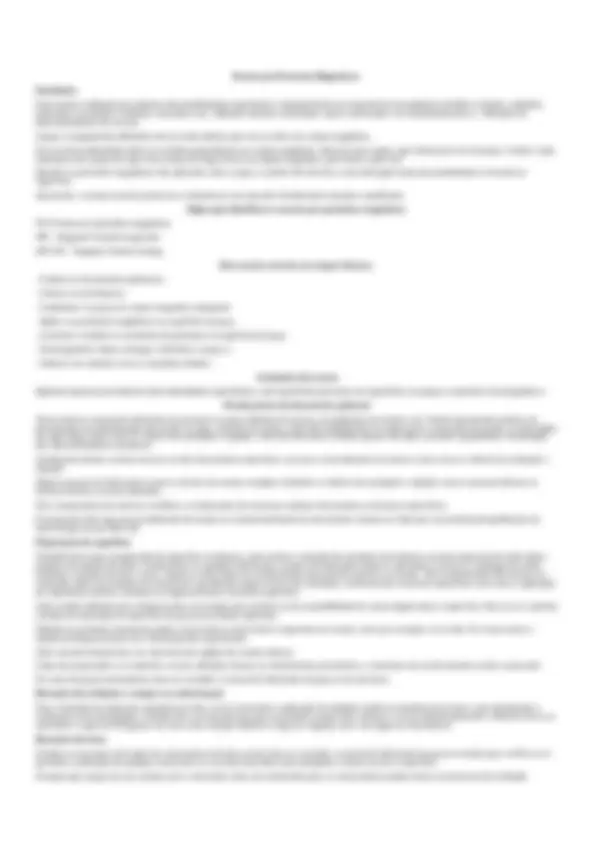
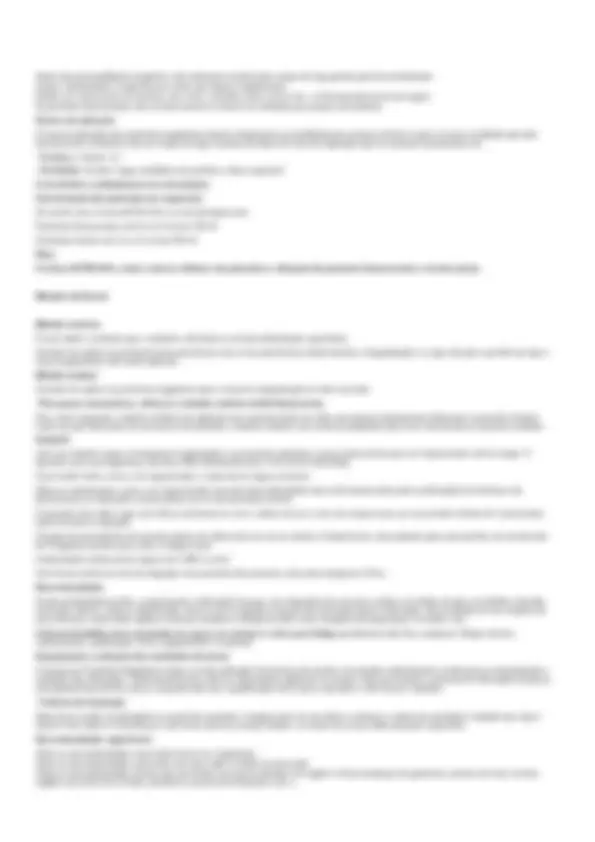
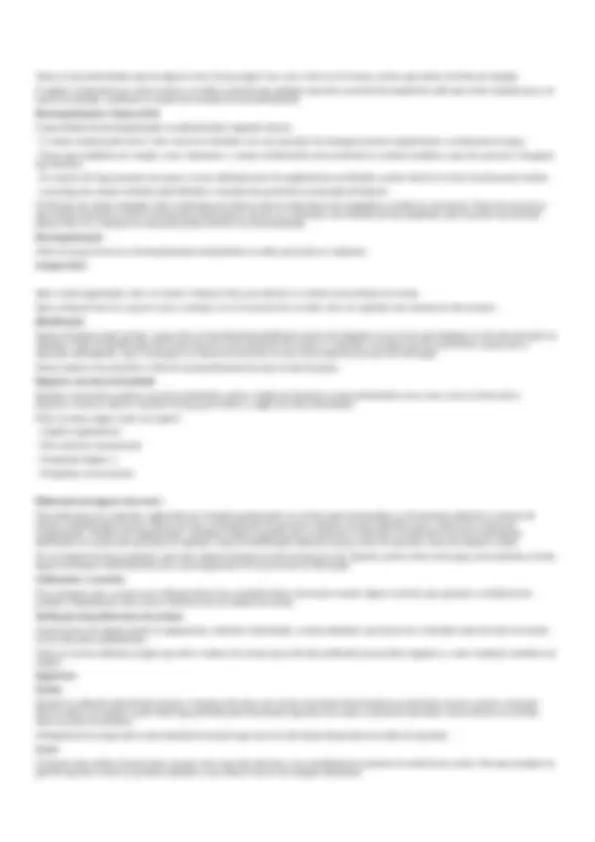
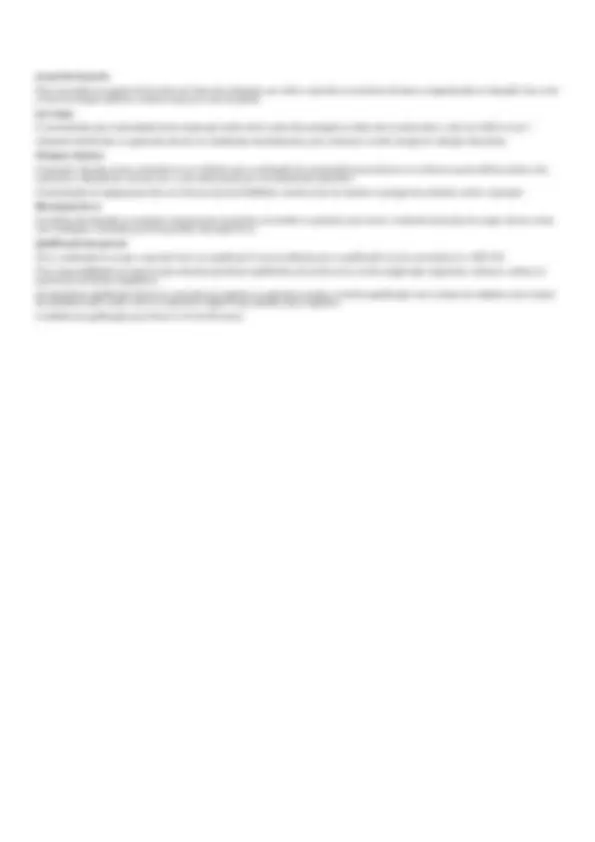
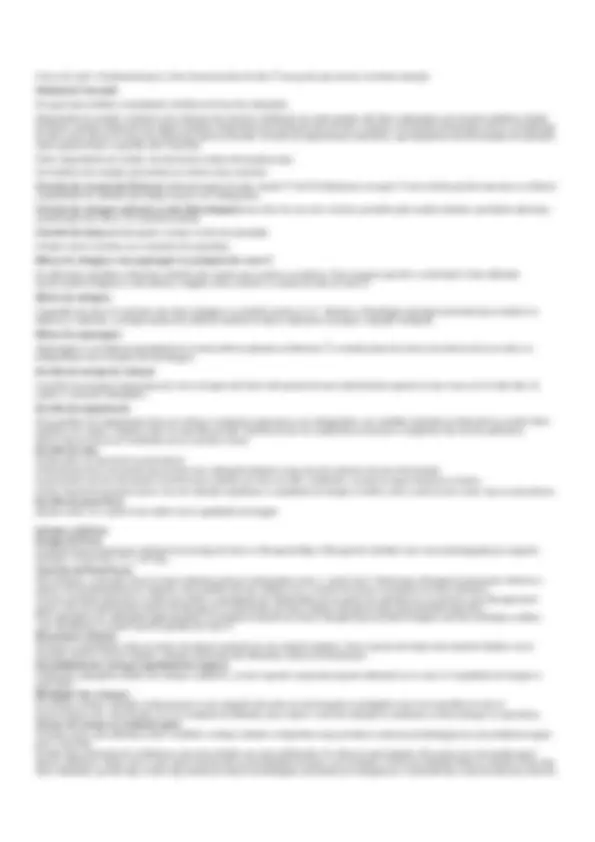
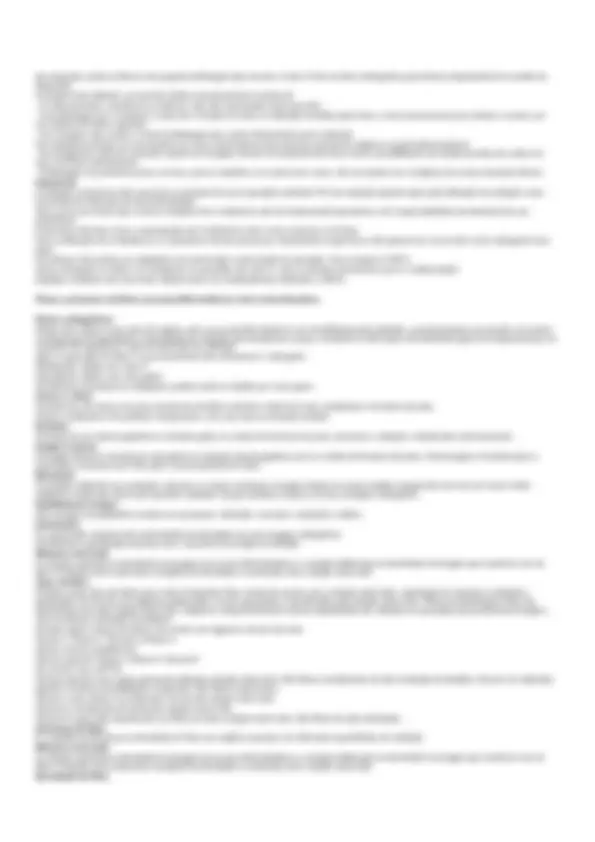
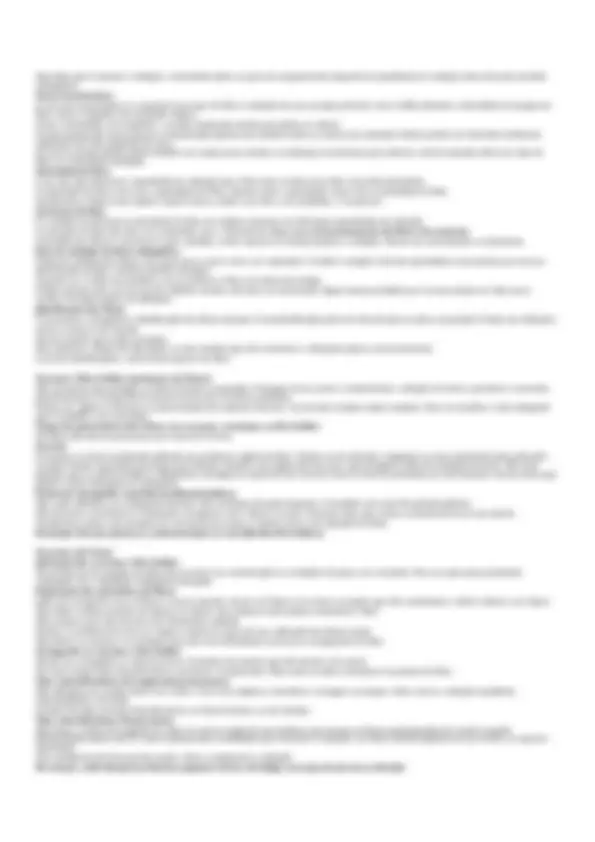
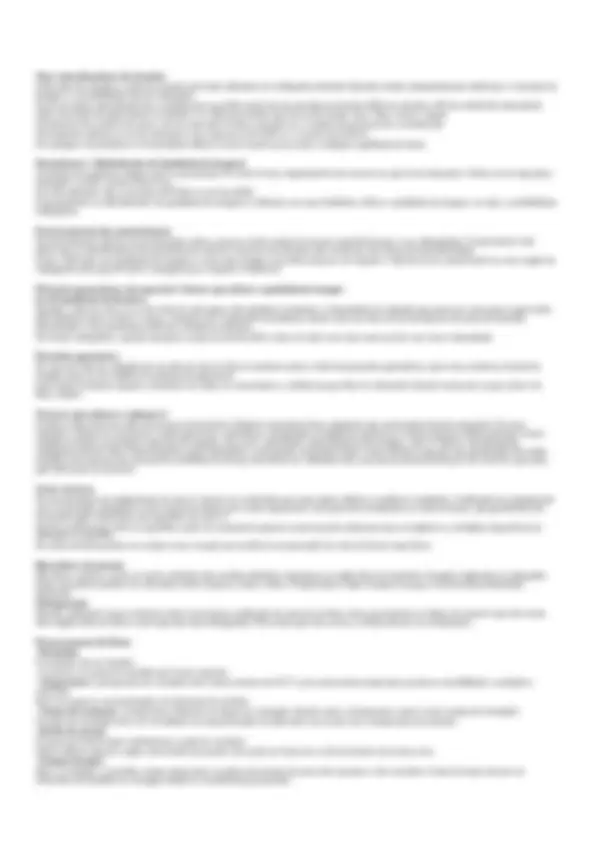
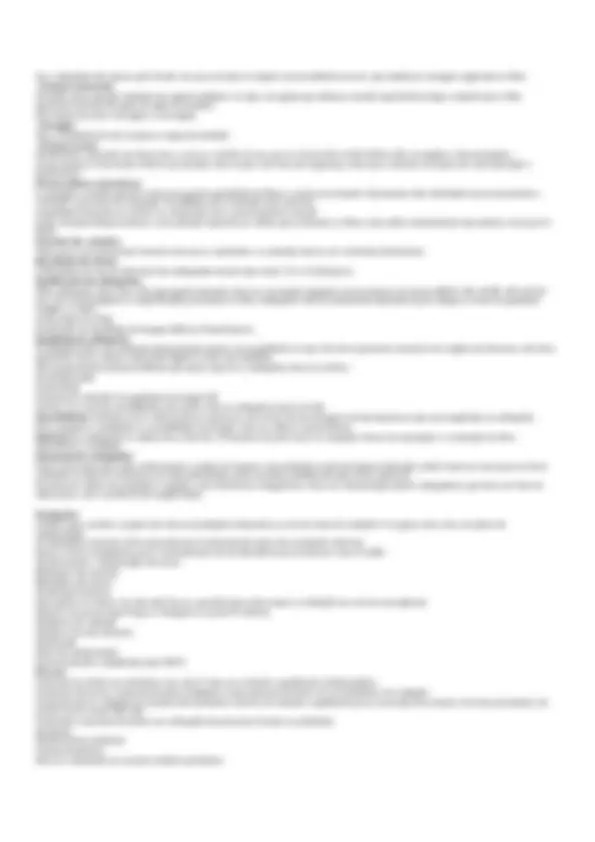
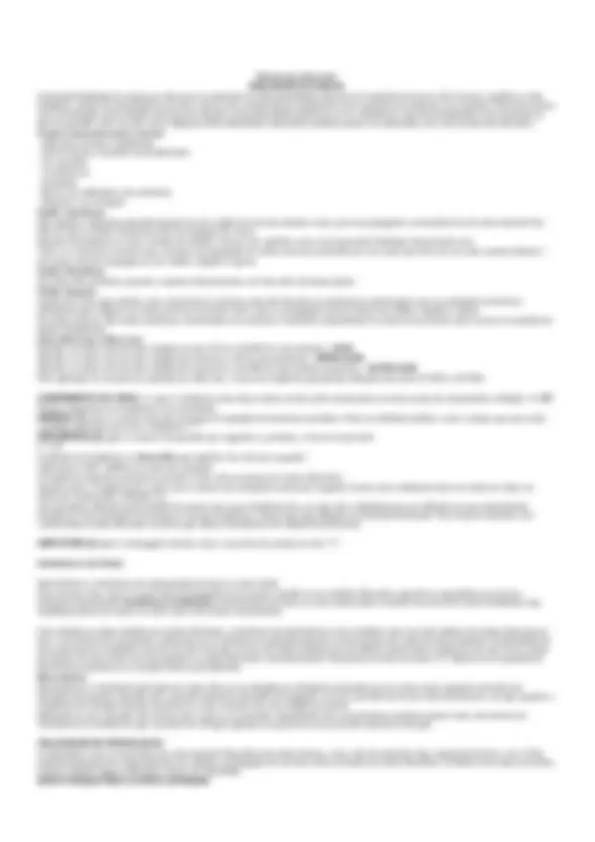
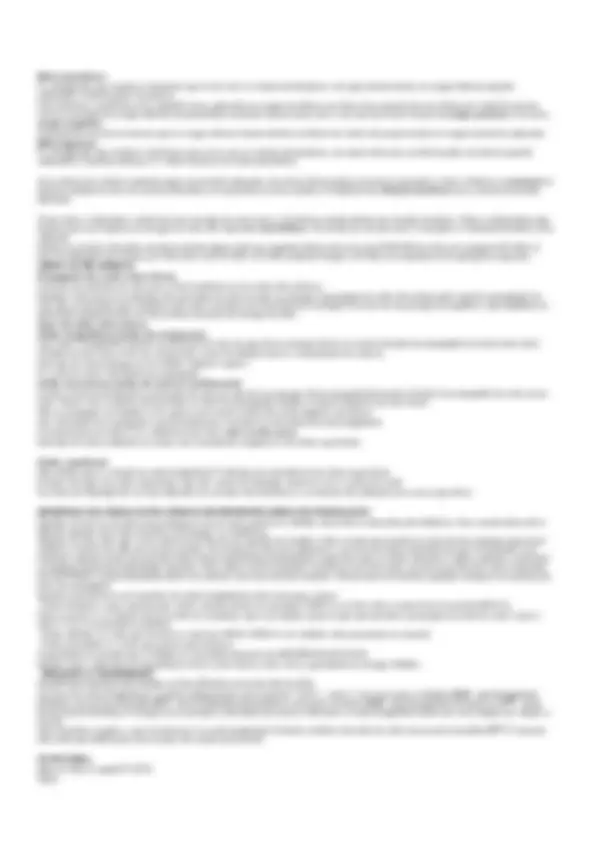
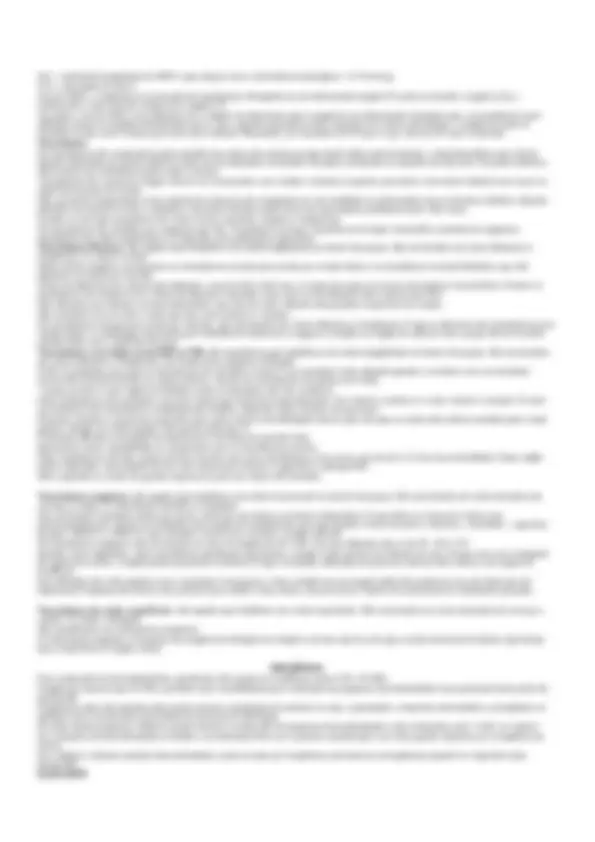
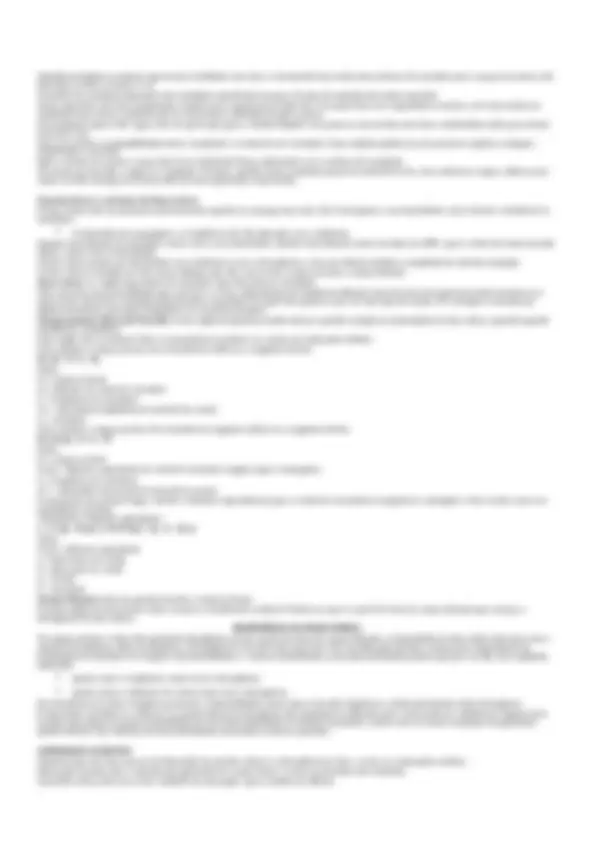
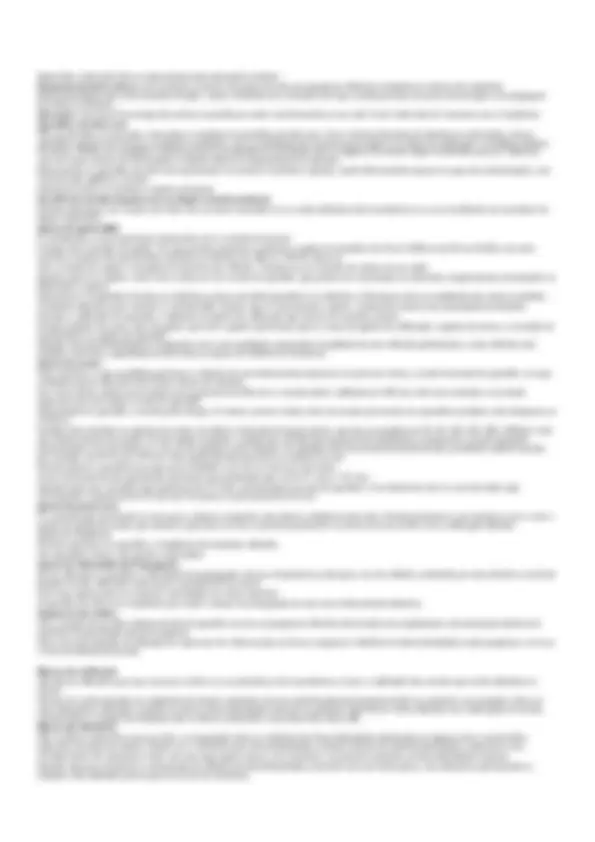
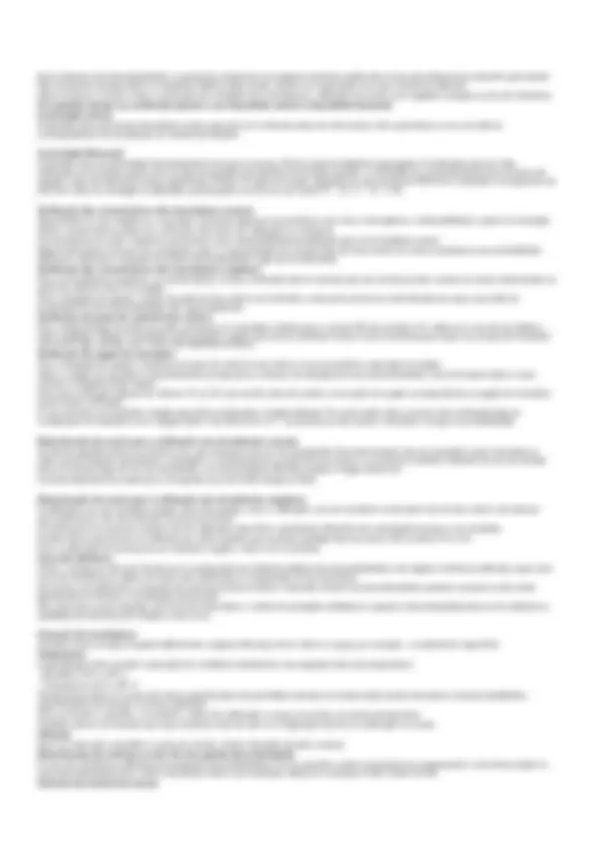
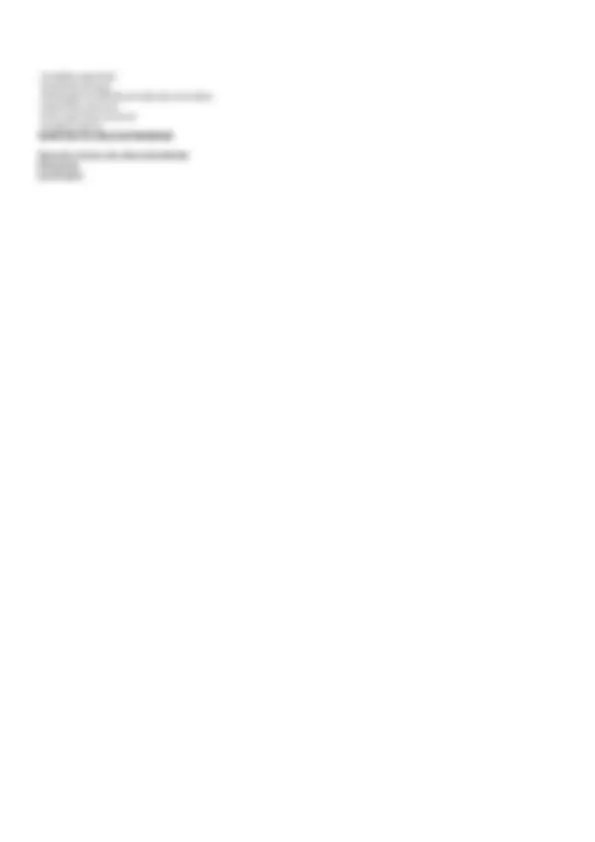
Estude fácil! Tem muito documento disponível na Docsity
Ganhe pontos ajudando outros esrudantes ou compre um plano Premium
Prepare-se para as provas
Estude fácil! Tem muito documento disponível na Docsity
Prepare-se para as provas com trabalhos de outros alunos como você, aqui na Docsity
Os melhores documentos à venda: Trabalhos de alunos formados
Prepare-se com as videoaulas e exercícios resolvidos criados a partir da grade da sua Universidade
Responda perguntas de provas passadas e avalie sua preparação.
Ganhe pontos para baixar
Ganhe pontos ajudando outros esrudantes ou compre um plano Premium
Comunidade
Peça ajuda à comunidade e tire suas dúvidas relacionadas ao estudo
Descubra as melhores universidades em seu país de acordo com os usuários da Docsity
Guias grátis
Baixe gratuitamente nossos guias de estudo, métodos para diminuir a ansiedade, dicas de TCC preparadas pelos professores da Docsity
- - - - - - -
Tipologia: Notas de estudo
1 / 29
Esta página não é visível na pré-visualização
Não perca as partes importantes!
Objetivo
O objetivo do Ensaios por Líquido Penetrante é assegurar a confiabilidade do produto, por meio de:
a) Obtenção de uma imagem visual, que revela a descontinuidade na superfície da peça (mancha);
b) Revelação da natureza da descontinuidade sem danificar a peça;
c) Separação das peças aceitáveis das não aceitáveis segundo o critério estipulado.
Aplicações Industriais e finalidade
Devido às características básicas do Ensaio por Líquido Penetrante, eles podem ser aplicados em grande variedade de produtos metálicos e não metálicos, ferrosos e não ferrosos, sejam forjados, fundidos, cerâmicos de alta densidade e etc., desde que não sejam porosos, com resultados técnicos e economicamente satisfatórios na revelação de descontinuidades superficiais, por menores que sejam. Pode ser aplicado durante o processo de fabricação, ao final deste ou durante a manutenção, aqui para detectar as o surgimento das descontinuidades em serviço.
Considerando que alguns materiais podem ser afetados pelos produtos utilizados no ensaio, devem ser realizados testes para assegurar que o material a ser ensaiado não seja danificado.
Liquido penetrante - Apresentação
O ensaio por líquido penetrante baseia-se na ação da capilaridade.
Vantagens e limitações
Vantagens:
Limitações:
- As peças devem estar completamente limpas e a entrada das possíveis descontinuidades desobstruídas;
Os produtos utilizados podem causar irritação na pele se manuseados sem luvas;
A luz negra deve ser usada mantendo-se os cuidados com os olhos e pele.
Aplicação
Quando um líquido penetrante é aplicado numa peça, deve-se aguardar o tempo suficiente para ocorrer a penetração nas descontinuidades superficiais Como elas são normalmente pequenas e estreitas, o fenômeno da capilaridade propicia a penetração.
Indicação da Descontinuidade
Terminada a penetração, o excesso de líquido penetrante deve ser escoado e o residual que ainda permanecer sobre a superfície deve ser removido,
Visibilidade da Indicação
O sucesso deste ensaio depende da visibilidade da indicação. Por isso o penetrante contém agente químico corante (de cor usualmente vermelha) para ser analisado sob luz branca, ou agente químico fluorescente (de cor usualmente amarelo-esverdeada) para ser analisado sob luz negra (ultravioleta), este muito mais sensível que o visível.
Classificação dos penetrantes, processos e materiais (de acordo com a ASTM 1417)
Tipo - Classificação dos Penetrantes
Tipo I – fluorescente
Tipo II - visível
Método - Classificação dos Métodos
Método A – Lavável com água
Método B – Pós emulsificável, Lipofílico
Método C – Removível com solvente
Método D – Pós emulsificável, Hidrofílico
Sensibilidade : Os níveis de sensibilidade aplicam-se somente aos sistemas de penetrante Tipo I
Sensibilidade Nível 1/2 - Muito baixa
Sensibilidade Nível 1 - Baixa
Sensibilidade Nível 2 - Média
Sensibilidade Nível 3 - Alta
Sensibilidade Nível 4 - Ultra alta
Reveladores - Classificação dos Reveladores :
Forma a – pó seco
Forma b – solúvel em água
Forma c – suspenso em água
Forma d – não-aquoso
Forma e – aplicação específica
Solventes - Classificação dos Solventes :
Classe 1 – halogenados
Classe 2 – não halogenados
Classe 3 – aplicação específica.
ETAPAS DO Ensaio
As etapas do ensaio são praticamente as mesmas, tanto para o penetrante visível, como para o penetrante fluorescente, variando ou alternando algumas seqüências devido aos métodos de remoção do excesso do penetrante e o tipo de revelador utilizado.
Umas das etapas mais importantes neste ensaio é a preparação da superfície e a pré-limpeza. Podemos considerar as etapas do ensaio como sendo:
Estudo prévio do documento aplicável: norma técnica, manual do fabricante da peça a ser ensaiada, boletins de serviço e etc. Nestes documentos podem ser encontradas as especificações do ensaio ou seja, a técnica de ensaio, onde são estabelecidas as regras para a execução do ensaio, bem como os critérios de aceitação e rejeição, onde são descritos os limites quanto aos tipos, tamanho, quantidade e localização das descontinuidades aceitáveis.
- Preparação da superfície/limpeza:
Preparação da superfície das peças para ensaio - limpeza
Consideremos aqui a preparação da superfície ou limpeza, como sendo a remoção de camadas de óxido, tintas, produtos de queima de óleos, combustíveis ou qualquer lubrificante ou outros tipos de contaminantes que possam interferir no ensaio. Tais contaminantes não devem ser removidos pelos executantes do ensaio pois, geralmente exige-se para tais remoções, conhecimento e técnicas específicas, tais como a aplicação de substâncias ácidas e alcalinas ou algum processo mecânico específico.
Métodos ou produtos impróprios podem causar danos irreversíveis à superfície em ensaio, como por exemplo a corrosão. Por esse motivo, o método de limpeza deverá ser criteriosamente especificado.
Como preparação da superfície consideramos: remoção de oxidação e carepas, Remoção de tintas, Etching / Deslustre e etc..
Pré-limpeza
Esta etapa é de responsabilidade do operador, que deverá remover qualquer resíduo proveniente da preparação da superfície.O objetivo desta etapa é deixar a superfície a ser ensaiada, completamente limpa e seca.
Atenção: na pré-limpeza, não estamos limpando apenas a superfície mas também a entrada e se possível. o interior das possíveis descontinuidades, pois quanto mais limpas estivem, mais penetrante irá penetrar em seu interior, que por conseqüência, provocará uma indicação de maior visibilidade
Principais Processos de Pré-Limpeza
Enxaguando a Camada Emulsificada.
Quando a difusão do emulsificador alcançar o resultado desejado (final do tempo de emulsificação), o processo é seguido pelo enxágüe com água, que interrompe o processo de difusão. Este enxágüe deve retirar apenas o penetrante emulsificado da superfície da peça e não do interior das descontinuidades.
Seguindo-se as orientações sobre a pressão da água e sua temperatura, dificilmente irá se retirar o penetrante não emulsificado do interior das descontinuidades.
Inspeção Visual da Remoção
Nesta etapa, acompanha-se a remoção do excesso do penetrante para que ao final da operação, a peça esteja completamente livre de acúmulos indesejáveis de penetrante na superfície. Desejamos apenas manter na peça, o penetrante que encontra-se no interior das descontinuidades.
Quando é utilizado um penetrante do TIPO I, a remoção deve ser feita sob luz negra, para um maior controle no enxágüe.
Se o penetrante for do TIPO II, o simples fato de não se constatar traços vermelhos na peça ou no pano utilizado, assegura uma completa remoção.
Secagem
Esta é uma etapa necessária antes de aplicar o revelador seco e o não aquoso. No caso de utilizar o revelador em solução ou suspensão em água, apenas retira-se o excesso de água aplica-se o revelador e só então a peça é levada à estufa para a secagem do revelador.
Normalmente são usadas estufas com controles que permitem regulagem de temperatura, entre 0 e 100o^ C e a temperatura máxima permitida é de 71 oC.
Reveladores
Como regra geral, o tempo de revelação não deverá ser menor que a metade do tempo de penetração.
É importante salientar que para a aplicação dos reveladores secos e não aquosos, a peça deverá esta completamente limpa e seca.
Métodos de aplicação: os reveladores podem ser aplicados por: Spray; Spray eletrostático;
Imersão;
Ventilação;
Polvilhamento
Sopro;
Mergulho e etc.
Podem ser aplicados por processos manuais ou automáticos. Isso dependerá das necessidades.
Para linhas de produção seriada, existem sistemas automáticos não apenas para a aplicação do revelador, mas para toda a seqüência do ensaio, desde a pré-limpeza até a limpeza final.
Tipos de Reveladores
Forma a - pó seco
Forma b - solúvel em água
Forma c - suspenso em água
Forma d - não-aquoso
Forma e aplicação específica
Luz negra
Intensidade: A lâmpada deve estar acesa pelo menos 5 (cinco) minutos antes do início do ensaio ou até atingir a intensidade requerida de 1. micro watts/cm^2.
Local da inspeção
A inspeção deve ser feita em local apropriado, com iluminação apropriada e limpo, para evitar que a peça venha a ser contaminada com resíduos que possam interferir não ensaio.
Quando utilizando o penetrante Tipo I (fluorescente): necessita-se de uma fonte de luz ultravioleta (luz negra), com uma intensidade luminosa mínima de 1.000 micro watts/cm 2 , na
Deve ser controlada a intensidade de luz branca deve ser controla.
A luz negra deve ser posicionada de tal maneira que não incida diretamente nos olhos do operador.
Quando utilizando o penetrante Tipo II (visível): deve se inspecionar a peça em local limpo e que tenha uma iluminação mínima de 1.000 lux.
Inpeção
Fazer incidir sobre a área a ser inspecionada, o foco de luz negra ou branca.
Observar atentamente a área a ser inspecionada; havendo descontinuidades elas serão denunciadas pela manifestação do fenômeno da fluorescência ou indicações vermelhas no caso do penetrante visível.
Descontinuidades
As descontinuidades podem ser surgir durante a fabricação da peça, isso dependerá do processo, podem ser: bolhas de gás, porosidade, inclusão, contração, dobras, costura, delaminação, trincas e etc..
Quando as peças são aprovadas após a fabricação, são montadas em um conjunto de uma aeronave, esta peça esta sujeita a esforços estáticos e dinâmicos bem como variações de temperatura, umidade e contaminantes.
As descontinuidades mais encontradas nas peças em serviço são as trincas. Corrosão por tensão também é comum.
Interpretação e avaliação dos resultados do ensaio
Os termos Interpretação e avaliação são muitas vezes confundidos:
O ensaios por Líquido Penetrante exige a correta aplicação das técnicas de ensaio e um grande conhecimento e prática para a interpretação e avaliação das indicações, conhecimento prévios sobre os documentos aplicáveis ao ensaio, o tipo de material, o processo de fabricação da peça e uma grande dose de bom senso, somando tudo isso à qualificação nível I para o operador e nível II para o inspetor.
Indicações
A imagem obtida após a revelação é chamada de indicação e podem ser de 3 naturezas: indicações falsas, indicações não relevantes e indicações verdadeiras.
Indicações Falsas
São indicações observadas durante a inspeção e que ocorrem, mais comumente em conseqüência da permanência de resíduos remanescentes do penetrante nas superfícies das peças.
A causa mais comum da permanência desses resíduos é a remoção deficiente do penetrante.
Indicações não relevantes
São as indicações causadas por descontinuidades superficiais, contudo, inerentes ao projeto e/ou processos de fabricação da peça ou montagem.
Devemos ter em mente também, que não podemos considerar normal ou não relevante as marcas de ferramentas introduzidas durante a montagem ou desmontagem de um componente.
Indicações verdadeiras
São as indicações de descontinuidades reais, que efetivamente podem comprometer a resistência estrutural da peça.
Não havendo dúvidas de é uma indicação verdadeira, inicia-se a etapa de interpretação da causa responsável pela indicação da descontinuidade superficial detectada. O resultado dessa interpretação permitirá avaliar o destino a ser dado à peça. O inspetor deverá estar familiarizado com cada tipo de indicação.
Remoção das descontinuidades
Quando permitido, a trinca ou outras descontinuidades podem ser removidas, e um novo ensaio deverá ser realizado.
Limpeza após o ensaio
A princípio, todas as peças ensaiadas devem ser limpas após a inspeção, independentemente se esta aprovada ou rejeitada. Não necessitam de limpeza após o ensaio se esta atitude estiver mencionada em procedimento escrito e se a peça rejeitada tiver um destino onde os resíduos do ensaio não possam interferir.
Identificação
Depois da limpeza após ensaio, a peça deve ser devidamente identificada através de etiquetas ou por cores que indiquem se ela está aprovada ou rejeitada. O tipo de identificação deve estar descrito no procedimento de ensaio e o operador ou inspetor deverá encaminhar a peça para a operação subseqüente, seja a montagem no sistema da aeronave ou uma outra etapa do processo de fabricação.
Nunca esquecer de preencher a ficha de acompanhamento da peça ou lote de peças.
Registrar uma descontinuidade
Quando é necessário registrar uma descontinuidade, adotar o hábito de desenhar as descontinuidades uma a uma num desenho, torna-se demorado e impreciso. Pode-se utilizar o desenho da peça para indicar a região das descontinuidades.
Pode-se adotar alguns meios de registro, tais como: líquidos registradores, fitas adesivas transparentes, fotografias digitais fotografias convencionais e etc..
Elaboração do relatório (registro) do ensaio
Esta etapa deve ser cumprida, registrando em formulário padronizado, no mínimo estas informações: os documentos aplicáveis; a técnica de ensaio; a identificação do peça; número do lote; ou identificação da aeronave; os resultados obtidos, quantificando, localizando e indicando as dimensões das descontinuidades detectadas; se a peça está aprovada ou rejeitada; o tipo de identificação utilizada na peça; nome do operador, nome do inspetor e datas.
Em se tratando de peça acabada e aprovada, depois da limpeza estará pronta para uso. Quando, porém, tratar-se de peça semi-acabada ou bruta, depois da limpeza estará liberada para o prosseguimento do seu processo de fabricação.
A limpeza após ensaio consiste na remoção do revelador da superfície ensaiada e, no caso de aprovação da peça com descontinuidades superficiais, da remoção também, do penetrante residual do interior das mesmas.
Ensaio por Partículas Magnéticas
Introdução
Este ensaio é utilizado para detectar descontinuidades superficiais e subsuperficiais em materiais ferromagnéticos fundidos, forjados, soldados, laminados, extrudados, trefilados, usinados e etc.. Aplicado durante a fabricação, após a fabricação e na manutenção para a detecção de descontinuidades em serviço.
A peça é magnetizada utilizando uma corrente elétrica que cria ou induz um campo magnético.
Se uma descontinuidade estiver no sentido perpendicular ao campo magnético, desviará este campo, que saltará para fora da peça, criando o que chamamos de campo de fuga. Este campo de fuga formará um dipolo magnético, pólo Norte e pólo Sul.
Quando as partículas magnéticas são aplicadas sobre a peça, os pólos irão atraí-las e uma indicação desta descontinuidade é formada na superfície.
Importante: o ensaio somente poderá ser realizado por um operador devidamente treinado e qualificado.
Siglas que identificam o ensaio por partículas magnéticas
PM- Ensaio por partículas magnéticas
MPI - Magnetic Particles Inspection
MPT/MT - Magnetic Particle Testing
Este ensaio consiste em etapas básicas:
Limitações do ensaio
Aplicável apenas para detectar descontinuidades superficiais e sub-superficiais (próximas da superfície), em peças e materiais ferromagnéticos.
Estudo prévio do documento aplicável
Norma técnica, manual do fabricante da aeronave ou peça, boletins de serviço, procedimento de ensaio e etc. Nestes documentos podem ser encontradas as especificações do ensaio ou seja, a técnica de ensaio, onde são estabelecidas as regras para a execução do ensaio, as descrições de cada etapa, bem como os critérios de aceitação e rejeição, onde são descritos os limites quanto aos tipos, tamanho, quantidade e localização das descontinuidades aceitáveis.
Geralmente adotam-se duas normas ou dois documentos específicos, um para o procedimento do ensaio e outro com os critérios de aceitação e rejeição.
Alguns manuais de fabricantes trazem a técnica de ensaio completa, incluindo os critérios de aceitação e rejeição, outros manuais indicam as normas técnicas a serem adotadas.
Para componentes de motores e turbinas, os fabricantes de aeronaves adotam documentos ou técnicas específicas.
É necessário dizer que um procedimento de ensaio ou o desenvolvimento de uma técnica, devem ser feitos por um profissional qualificado em Nível III pela norma NAS 410.
Preparação da superfície
Consideremos aqui a preparação da superfície ou limpeza, como sendo a remoção de camadas mais densas ou mais espessas de óxido; tintas; produtos de queima de óleos, combustíveis ou qualquer lubrificante; carepas de laminação soltas ou aderentes; escória ou respingos de solda; rebarbas; camadas de tinta, cromo, níquel ou outros tipos de contaminantes que possam interferir no ensaio. Tais contaminantes não devem ser removidos pelos executantes do ensaio pois, geralmente exige-se para tais remoções, conhecimento e técnicas específicas, tais como a aplicação de substâncias ácidas e alcalinas ou algum processo mecânico específico.
Todo produto utilizado para a limpeza deve ser testado para verificar se há a possibilidade de causar algum dano à superfície. Deve-se aí, controlar o tempo de exposição da superfície da peça aos produtos aplicados.
Métodos ou produtos impróprios podem causar danos irreversíveis à superfície em ensaio, como por exemplo a corrosão. Por esse motivo, o método de limpeza deverá ser criteriosamente especificado.
Toda camada isolante deve ser removida das regiões de contato elétrico.
O tipo de preparação e os materiais a serem utilizados devem ser devidamente autorizados e constarem de um documento escrito e aprovado.
Em caso de peças aeronáuticas, deve-se consultar o manual do fabricante da peça ou da aeronave.
Remoção de oxidação e carepas ou carbonização
Para a remoção de espessas camadas de óxido, se faz necessária a aplicação de soluções ácidas ou alcalinas para fazer o que geralmente é conhecido como decapagem. Cuidado deve ser tomado para que os produtos usados não venham a corroer demasiadamente o material. Deve-se neutralizar a ação do decapante com uma outra solução inibidora e logo em seguida, lavar com água em abundância.
Remoção de tintas
Existem no mercado vários tipos de removedores de tinta, porém deve-se consultar o manual do fabricante da peça em ensaio para verificar se é permitida a utilização de qualquer removedor ou se existe uma linha mais adequada e menos nociva à superfície.
O tempo que a peça fica em contato com o removedor, deve ser monitorado pois, os removedores podem iniciar um processo de oxidação.
Limpeza da peça - pré-limpeza.
Esta etapa é de responsabilidade do operador, que deverá remover qualquer resíduo proveniente da preparação da superfície.
Deve-se remover todo material estranho, contaminantes ou sujeira (óleo, graxa, corrosão, poeira, água e etc.), pois, interferem na formação das descontinuidade , dificultando ou impedindo a mobilidade das partículas ou encobrindo um possível campo de fuga.
Após a pré-limpeza, a peça deve ficar limpa e seca.
Principais Processos de Pré-Limpeza
Proteção e Isolamento de Regiões
Quando uma peça a ser ensaiada possuir furos, pequenas aberturas, passagens para galerias ou componentes metálicos ou não que possam reter ou serem contaminados com os produtos e resíduos provenientes do ensaio, devem ter estas regiões devidamente mascaradas ou obstruídas com material não abrasivo e que possa ser removido sem exigir trabalho mecânico. O material da máscara não deverá contaminar o banho.
Campo magnético
Genericamente, define-se campo magnético como sendo "toda região próxima em torno de um condutor percorrido por uma corrente elétrica, ou em torno de um imã".
Regra da mão direita
Com o polegar da mão direita indicando o sentido da corrente os dedos envolvendo o condutor indicam o sentido das linhas de indução magnética que envolvem o condutor.
Materiais influenciáveis pelo campo magnético
Os materiais podem ser divididos em três grandes grupos, segundo a influência que venham a sofrer em função do campo magnético:
Materiais ferromagnéticos:
Em elementos como o Ferro(Fe), Cobalto(Co), Níquel(Ni), Gadolínio(Gd), e em certas ligas destes, ocorre um fenômeno denominado ferromagnetismo, que os possibilita adquirir um alto grau de alinhamento magnético de tal modo que venham ser fortemente atraídas por imãs. Nesses elementos a permeabilidade magnética é maior do que 1 (um).
Materiais paramagnéticos:
Quando colocadas num campo magnético, o alinhamento dos dipolos atômicos elementares não é perfeito, ocasionando uma fraca atração pelos imãs.
Normalmente a permeabilidade magnética relativa de tais metais é praticamente igual a 1 (um).
Materiais diamagnéticos:
São os materiais cuja permeabilidade relativa é pouco menor 1 (um).
Como exemplo, tem-se o Zinco (Zn), Mercúrio (Hg), Bismuto (Bi) e o Cobre (Cu), em que a permeabilidade relativa e pouco menor que 1 (um).
Campo magnético e descontinuidade
Existindo um campo de fuga, as linhas de fluxo atraem as partículas magnéticas para que elas funcionem como uma ponte para as linhas de fluxo do campo magnético.
No caso de um campo magnético circular criado ou induzido numa peça tubular, teremos um campo contido, sem a possibilidade da formação dos pólos magnéticos N e S.
Se interrompermos esse campo circular promovendo um corte, possibilitaremos a formação dos pólos magnéticos no campo de fuga das linhas de força.
Para melhor sensibilidade do ensaio por partículas magnéticas, a descontinuidade deve estar orientada a 90o^ em relação à direção do campo magnético.
Tipos de correntes de magnetização
Curva de histerese
Esta curva mostra a magnetização e desmagnetização de um material, indicando algumas propriedades, tais como:
Tendo alta permeabilidade magnética, são facilmente atraídas pelo campo de fuga gerado pela descontinuidade. A baixa retentividade é requerida para evitar que fiquem magnetizadas. Podem ser visíveis (com luz branca), nas cores: vermelha, preta, cinza e etc., ou fluorescentes (com luz negra). As partículas fluorescentes são as mais sensíveis e devem ser adotadas para peças aeronáuticas
Formas de aplicação
O meio de aplicação das partículas magnéticas interfere diretamente na mobilidade das mesmas devido à maior ou menor facilidade que elas encontram de se deslocar até um campo de fuga. Existem dois tipos de forma de aplicação que se resumem basicamente em:
- Via Seca : Veículo "ar" - Via Úmida: Veículos "água, destilados de petróleo e óleos especiais".
A via úmida é a adotada para uso aeronáutico
Concentração das partículas em suspensão
De acordo com a norma ASTM 1444, as concentrações são:
Partículas fluorescentes: de 0,1 a 0,4 ml em 100 ml
Partículas visíveis: de 1,2 a 2,4 ml em 100 ml
Nota:
A norma ASTM 1444 e outras normas militares não permitem a utilização de partículas fluorescentes e visíveis juntas.
Métodos de Ensaio
Método contínuo
É mais rápido e eficiente que o residual e não limita-se às descontinuidades superficiais.
Consiste em aplicar as partículas tanto pela técnica seca como pela técnica úmida durante a magnetização, ou seja, durante o período em que a força magnetizante está sendo aplicada.
Método residual
Consiste em aplicar as partículas magnéticas após a força de magnetização ter sido removida.
*Para peças aeronáuticas, utiliza-se o método contínuo úmido fluorescente.
Para casos especiais o método residual será aplicado mas somente tendo em mãos uma técnica devidamente elaborada e aprovada. Existem casos em que fabricantes de aeronaves recomendam o método residual, mas a técnica detalhada deverá ser encontrada no manual ou boletim.
Inspeção
Uma vez estando a peça corretamente magnetizada e as partículas aplicadas, a peça estará pronta para ser inspecionada sob luz negra. O operador, para sua segurança, não deve olhar diretamente para o foco de luz ultravioleta.
Fazer incidir sobre a área a ser inspecionada, o facho de luz negra ou branca
Observar atentamente a área a ser inspecionada; havendo descontinuidades elas serão denunciadas pela manifestação do fenômeno da fluorescência ou indicações características da cor das partículas visíveis.
O operador deve deixar que seus olhos acostumem-se com a cabine escura e com a luz negra acesa, por um período mínimo de 1 (um) minuto antes de iniciar a inspeção.
O tempo de permanência do operador dentro da cabine deve ser de no máximo 2 (duas) horas, necessitando após este período, de um intervalo de 15 (quinze) minutos para evitar a fadiga visual.
A intensidade mínima da luz negra é de 1.000 m w/cm^2
A luz branca dentro da área de inspeção com partículas fluorescentes, não pode ultrapassar 20 lux.
Descontinuidades
As descontinuidades podem surgir durante a fabricação da peça, isso dependerá do processo, podem ser: bolhas de gás, porosidade, inclusão, contração, dobras, costura, delaminação, trincas e etc.ou quando as peças são aprovadas após a fabricação, são montadas em um conjunto de uma aeronave, onde estão sujeitas a esforços estáticos e dinâmicos bem como variações de temperatura, corrosão e etc..
A descontinuidade mais encontrada nas peças em serviço é a trinca por fadiga, geralmente muito fina e pequena. Requer técnica, conhecimento, qualificação e bons equipamentos e materiais.
Interpretação e avaliação dos resultados do ensaio
O ensaio por Partículas Magnéticas exige a correta aplicação das técnicas de ensaio e um grande conhecimento e prática para a interpretação e avaliação das indicações, conhecimento prévio sobre os documentos aplicáveis ao ensaio, o tipo de material, o processo de fabricação da peça e uma grande dose de bom senso, somando tudo isso à qualificação nível I para o operador e nível II para o inspetor.
- Critérios de Aceitação:
Antes de se avaliar as indicações na superfície ensaiada, o inspetor deve ter em mãos e conhecer o critério de aceitação e rejeição que rege o ensaio. Este critério é fornecido por uma norma técnica, manual, boletim ou ordem de serviço elaborada pelo requerente.
Descontinuidades registráveis:
Todas as descontinuidades reprovadas devem ser registradas. Todas as descontinuidades aprovadas mas que estão no limite de aprovação Todas as descontinuidades mesmo que aprovadas mas que localizadas em regiões críticas (mudança de geometria, próxima de furos, bordas, regiões com início de corrosão, próximas a marcas de ferramenta e etc..)
Todas as descontinuidades que de alguma forma ofereça algum risco com o decorrer do tempo, mesmo que abaixo do limite de rejeição.
O registro é importante por vários motivos, um deles é permitir que qualquer operador e pessoal da engenharia saiba que existe naquela peça, um motivo de atenção, auxiliando no estudo de evolução de descontinuidades.
Desmagnetização e limpeza final
A necessidade de desmagnetização é explicada pelos seguintes fatores:
O indicador de campo magnético não é suficiente para indicar valores muito baixos de magnetismo residual ou remanente. Partes de aeronaves que contêm bússolas ou outros instrumentos influenciáveis, devem ser verificadas com bússolas de boa qualidade, pois somente uma bússola poderá dizer se o residual ou remanente podem interferir na instrumentação.
Desmagnetização
Todas as peças devem ser desmagnetizadas independente se estão aprovadas ou rejeitadas.
Limpeza final
Após a desmagnetização, deve-se realizar a limpeza final, para eliminar os resíduos provenientes do ensaio.
Após a limpeza final, se a peça for para o estoque ou se for passível de corrosão, deve ser aplicada uma camada de óleo protetor.
Identificação
Depois da limpeza após ensaio, a peça deve ser devidamente identificada através de etiquetas ou por cores que indiquem se ela está aprovada ou rejeitada. O tipo de identificação deve estar descrito no procedimento de ensaio e o operador ou inspetor deverá encaminhar a peça para a operação subseqüente, seja a montagem no sistema da aeronave ou uma outra etapa do processo de fabricação.
Nunca esquecer de preencher a ficha de acompanhamento da peça ou lote de peças.
Registrar uma descontinuidade
Quando é necessário registrar uma descontinuidade, adotar o hábito de desenhar as descontinuidades uma a uma, torna-se demorado e impreciso. Pode-se utilizar o desenho da peça para indicar a região das descontinuidades.
Pode-se adotar alguns meios de registro:
Elaboração do registro de ensaio
Esta etapa deve ser cumprida, registrando em formulário padronizado, no mínimo estas informações: os documentos aplicáveis; a técnica de ensaio; a identificação do peça; número do lote; ou identificação da aeronave; método e técnica utilizados, tipo e valores da corrente de magnetização, direções de magnetização, resultados obtidos, quantificando, localizando e indicando as dimensões das descontinuidades detectadas; se a peça está aprovada ou rejeitada; o tipo de identificação utilizada na peça; nome do operador, nome do inspetor e datas.
Em se tratando de peça acabada e aprovada, depois da limpeza estará pronta para uso. Quando, porém, tratar-se de peça semi-acabada ou bruta, depois da limpeza estará liberada para o prosseguimento do seu processo de fabricação.
Calibrações e controles
Para assegurar que o ensaio será realizado dentro das condições ideais, deveremos manter alguns controles que garantam a eficiência dos produtos, isoladamente, bem como a eficiência de um sistema de ensaio
Verificação da performance do sistema
A performance do sistema inclui os equipamento, materiais e iluminação, a serem utilizados, que devem ser verificados antes do início do ensaio ou em intervalos estabelecidos.
Todas as normas utilizadas exigem que todo o sistema de ensaio seja verificado (calibrado) em períodos regulares, e seus resultados mantidos em arquivo.
Segurança
Óculos
Quando for utilizado material fluorescente, o inspetor não deve usar óculos com lentes fotocromáticas ou de lentes escuras, porém o operador deverá utilizar um protetor ocular desde que permitido pelo documento específico do ensaio ( manual do fabricante, norma técnica ou contrato entre as partes envolvidas).
A lâmpada de luz negra deve estar instalada de maneira que seu foco não incida diretamente nos olhos do operador.
Luvas
O inspetor deve utilizar durante todo o ensaio, luvas que não interfiram com a facilidade de manuseio do material em ensaio. Mas que protejam da pele do operador contra os produtos utilizados e aos efeitos nocivos da radiação ultravioleta.
Para a realização deste ensaio necessita-se de uma fonte de radiação, que pode ser natural ou artificial, de um objeto (peça) e um meio de registro, no caso o filme radiográfico. Chamaremos de radiografia o resultado da exposição de um filme utilizando raios-X e gamagrafia o resultado da utilização de raios gama. Importante
Quando utilizar o ensaio radiográfico Quando a descontinuidade causar uma diferença detectável na espessura, na densidade ou na composição do material.
Efeito Compton: Quando os fótons têm uma energia de 100 keV a 1 Mev, toda energia não é requerida para desalojar um elétron orbital e acelerá-lo por indução de energia cinética. Neste caso a fotoabsorção pode ocorrer mas o fóton continua a sua trajetória, porém com sua energia reduzida, pois perdeu energia para o elétron. Por esse mecanismo de absorção, a trajetória do fóton é alterada e sua energia diminuída. Esse mecanismo de absorção é chamado de efeito Compton. Este efeito acontece com energias entre 100 keV e 1 Mev.
Produção de pares: Quando a energia da radiação excede 1,02 MeV, poderá causar a produção de pares. Neste caso, um fóton de alta energia é desintegrado pelo campo nuclear que circunda o núcleo do átomo. A energia do fóton é convertida em um par "elétron-pósitron".
Fator de contraste do material A quantidade de radiação absorvida pela peça a ser radiografada dependerá do número atômico, densidade e espessura do material. O operador não poderá mudar esses fatores mas pode mudar a energia de radiação.
Requisitos básicos para produção de raios-x
Raios-x ..são produzidos quando alguma forma de matéria é bombardeada elétrons em alta velocidade. Para isso são necessários três requisitos básicos:
Sistema de refrigeração
Como a produção de raios-X gera altas temperaturas dentro do tubo, necessita-se de técnicas eficazes para a remoção de calor. Alguns aparelhos contam com um radiador de óleo que circular nas proximidades do ânodo, promovendo a troca de calor. Esse óleo que circula, retorna ao radiador, onde é refrigerado por água, de um outro radiador que envolve o circuito de óleo.
Outros aparelhos contam com a dissipação de calor utilizando membranas de radiador térmico, contando com a dissipação de calor pelo cobre que envolve o alvo e externamente ao tubo os dissipadores secos.
O sistema de refrigeração dependerá da capacidade e a portabilidade do aparelho.
de comandos, pode-se liberar uma pequena blindagem que envolve a fonte. Pode-se obter radiografias panorâmicas dependendo do modelo do dispositivo O modelo mais utilizado, por permitir melhor posicionamento consiste de:
Filmes, protetores de filmes (cassetes/film holders) e telas intensificadoras
Filmes radiográficos Filmes são usados como meio de registro, pois a sua emulsão depois de ser sensibilizada pela radiação e posteriormente processada, irá mostrar as diferenças de quantidade e intensidade da radiação que ultrapassou a peça, revelando as diferenças de densidade (grau de enegrecimento), as variações de espessura e grau de absorção da radiação. Após a exposição do filme e o processamento dele, obteremos a radiografia. Radiografia: obtida com raios-X Gamagrafia: obtida com raios gama Geralmente chamadas de radiografia, podem incluir as obtidas por raios gama Como é o filme Consiste de uma base com uma camada de emulsão contendo cristais de prata, usualmente o brometo de prata. A base usualmente é de poliéster transparente, com uma suave coloração azulada. Emulsão Consiste de um material gelatinoso contendo grãos ou cristais de brometo de prata, sensíveis a radiação e distribuídos uniformemente. Imagem Latente. A imagem latente é formada por interações da radiação eletromagnética com os cristais de brometo de prata.. Esta imagem é formada após a exposição e somente será vista após o processamento do filme. Revelação O produtos utilizados na revelação, reduzem os cristais contendo a imagem latente em prata metálica enegrecida mas terá um menor efeito naqueles cristais que não foram expostos radiação. A prata metálica é opaca e forma a imagem radiográfica. Qualidade da imagem Uma imagem de qualidade consiste em apresentar: definição, contraste, resolução e nitidez. Granulação É a impressão visual de não uniformidade de densidade em uma imagem radiográfica Geralmente a granulação aumenta com o aumento da energia da radiação Relação sinal-ruído A variação acidental na densidade da imagem torna mais difícil identificar a variação deliberada na densidade da imagem que resulta do uso do filme. A relação entre estas duas variações de densidade é conhecida como relação sinal-ruído Tipos de filme Existem vários tipos de filmes para raios-X industrial. Eles variam de acordo com a relação sinal-ruído, velocidade de resposta à radiação e granulação. De acordo com algumas publicações, é mais apropriada a classificação pela relação sinal-ruído. Filmes de granulação muito fina apresentam uma alta relação sinal ruído, requerem comparativamente maiores quantidades de radiação na exposição para produzirem imagens com excelentes resolução de detalhes. Existem quatro classes de filmes, de acordo com algumas normas são elas: Classe 1, Classe 2, Classe3 e Classe 4. Outras normas estabelecem: Classe especial, Classe I, Classe II, Classe III De acordo com a ASTM Classe especial: essa classe apresenta altíssima relação sinal-ruído. São filmes considerados de alta resolução de detalhes. Devem ser utilizados quando a máxima sensibilidade é requerida. São filmes muito lentos. Classe I: essa classe é considerada com de alta relação sinal-ruído Classe II: considerada de moderada relação sinal-ruído. Classe III: aqui estão classificados os filmes de baixa relação sinal-ruído. São filmes de alta velocidade. Contraste do filme É a medida da diferença na densidade do filme em regiões expostas com diferentes quantidades de radiação. Relação sinal-ruído A variação acidental na densidade da imagem torna mais difícil identificar a variação deliberada na densidade da imagem que resulta do uso do filme. A relação entre estas duas variações de densidade é conhecida como relação sinal-ruído Densidade do filme
Num filme que é exposto à radiação, a densidade óptica ou grau de enegrecimento depende da quantidade de radiação absorvida pela emulsão radiográfica. Curva Característica A curva de característica é a resposta de um tipo de filme à radiação de uma energia particular. Isso é obtido plotando a densidade da imagem do filme contra o logaritmo de exposição relativa. Como a densidade é um logaritmo , escalas log-log são usadas para plotar os valores. Escalas log-log não fazem apenas a interpretação gráfica mas também todos os valores da exposição relativa podem ser derivados facilmente, subtraindo um valor logaritmo de outro. As curvas características podem também ser usadas para calcular as mudanças necessárias para otimizar a técnica quando altera-se o tipo de filme ou a densidade desejada. Velocidade do filme E um fator que determina a quantidade de radiação que o filme deve receber para obter uma dada densidade. A velocidade do filme varia com a granulação do filme. Quanto maior a granulação, maior será a velocidade do filme. Geralmente os filmes mais rápidos custam menos, então é um fator a ser analisado, a "economia". Contraste do filme É a medida da diferença na densidade do filme em regiões expostas com diferentes quantidades de radiação. O contraste do filme não deve ser confundido com o contraste do objeto (peça). Armazenamento de filmes não expostos A emulsão dos filmes é sensível ao calor, umidade, certos vapores ou fumaça química e radiação. Devem ser armazenados corretamente. Data de validade do filme radiográfico A data de validade dos filmes vem expressa na caixa e deve ser respeitada. O melhor é adquirir somente quantidades necessárias para uso por determinado período, evitando grandes estoques. Fazendo-se o rodízio de prateleira, usa-se primeiro o filme com data mais antiga. O filme quando está com sua ata de validade vencida, não deve ser descartado, alguns testes permitidos por normas podem ser feitos para verificar se ainda podem ser utilizados. Identificação dos filmes É necessária e obrigatória a identificação dos filmes expostos. Esta identificação pode ser feita durante ou após a exposição. Podem ser utilizados: Letras e números de chumbo Fita de chumbo que aceita inscrições Fitas adesivas, chapas de impressão ou outro método que não contamine a radiografia (após o processamento) Local das identificações: canto direito superior do filme.
Cassetes / filme holders (protetores de filmes) São acessórios que protegem os filmes durante a exposição. Protegem da luz, poeira, contaminantes, radiação de fundo e permitem o manuseio, posicionamento e transporte da câmara escura até o local da exposição. Podem ser rígidos ou flexíveis e confeccionados de materiais diversos. No mercado existem muitos modelos. Deve-se escolher o mais adequado para o trabalho a ser executado. Tempo de permanência dos filmes nos cassetes, envelopes ou film holders Os filmes não devem permanecer por mais de 24 horas Cassete O cassete é o termo usualmente aplicado aos protetores rígidos de filme. Podem ser de alumínio, magnésio ou outro material de baixa absorção na parte frontal e apresenta uma base mais robusta, inclusive com algum tipo de ecran, que protegerá o filme da radiação de fundo. São mais pesados que os outros modelos e dificilmente consegue-se repará-los em caso de riscos ou marcas profundas em sua estrutura, marcas estas que podem causar indicações na radiografia. Protetores de papelão revestido (cardboard holders) São muito utilizados em radiografia industrial. São envelopes de papel espesso e revestidos com uma fina película plástica. São duráveis e econômicos e facilmente carregáveis com o filmes e ecrans. Possuem abas que evitam a entrada de luz em seu interior. Geralmente contam com proteção em sua base para evitar os efeitos nocivos da radiação de fundo. Envelopes flexíveis plásticos, emborrachados ou vinil (flexible film holders)
Cassetes sob Vácuo Aplicação dos cassetes e film holders Na escolha de um portador de filme deve-se levar em consideração as condições da peça a ser ensaiada. Deve-se optar pela praticidade conjugada com a qualidade radiográfica desejada. Preparação dos portadores de filmes Antes de carrega-los com os filmes a serem expostos, devem ser limpos com panos ou papéis que não contaminem o interior destes, com fiapos. Não utilizar nenhum produto de limpeza no interior dos protetores pois podem contaminar o filme Não assoprar para abri-los pois será introduzida umidade. Verificar a existência de furos ou rasgos e repará-los antes do uso, utilizando fita adesiva preta Não dobrar ou amassar os envelopes pois isso trará dificuldade na hora do carregamento do filme. Carregando os cassetes e film holders Devem ser carregados na câmara escura e fechados de maneira que não deixem a luz entrar Se forem usadas telas intensificadoras, posicionar corretamente o filme entre as telas e introduzir no protetor de filme. Telas intensificadoras de imagem (ecrans/screens) São utilizadas em contato direto com o filme. Têm como objetivos, intensificar a imagem e proteger o filme contra a radiação espalhada, retroespalhada e de fundo. Existem dois tipos de telas intensificadoras: as fluorescentes e as de chumbo. Telas intensificadoras fluorescentes: São feitas e cristais de tungstato de cálcio ou outros cristais de sais químicos que tornam-se fluorescentes(emitem luz visível), quando bombardeados pelos raios-X. esses materiais têm a habilidade para converter a radiação- em fótons eletromagnéticos de luz visível, no espectro ultravioleta. A luz emitida da tela fluorescente expõe o filme e suplementa a radiação. Na aviação, onde desejamos detectar pequenas trincas de fadiga, este tipo de tela não é utilizada.