
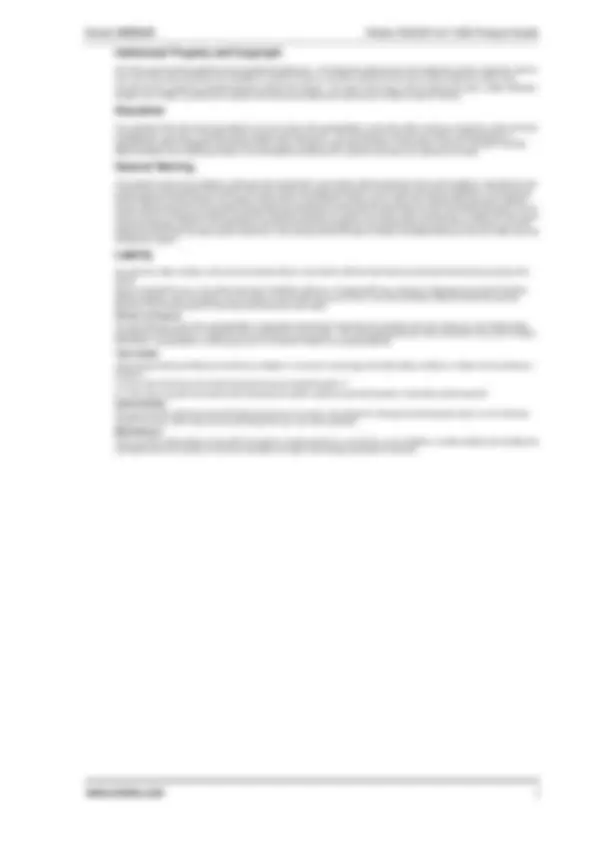
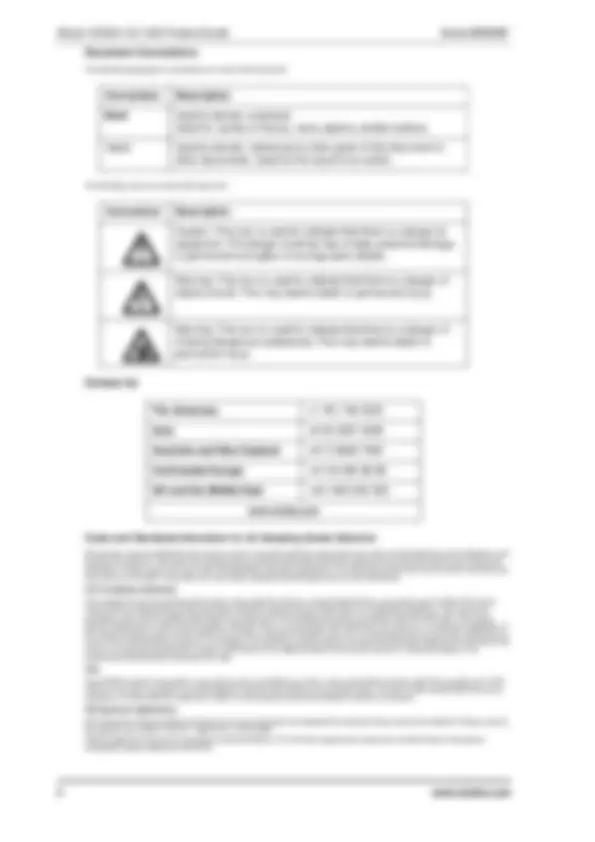
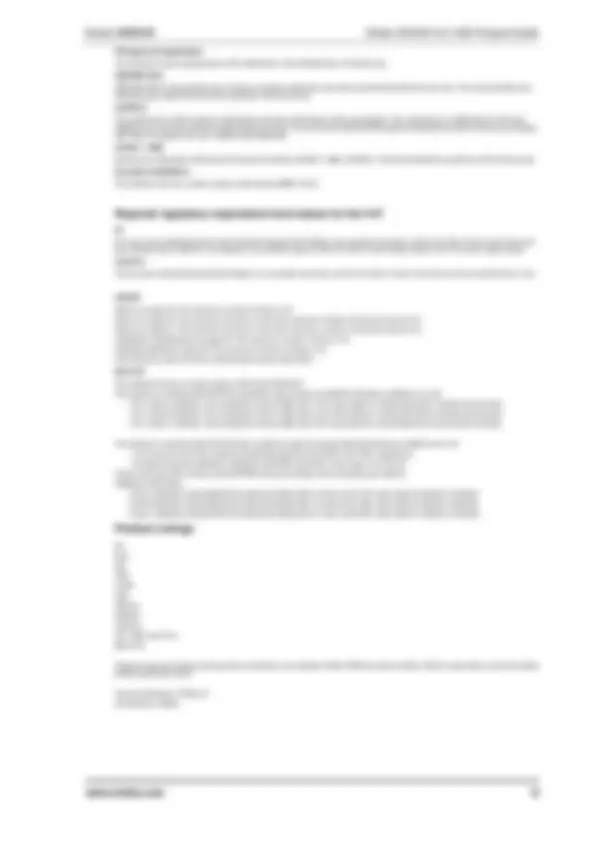
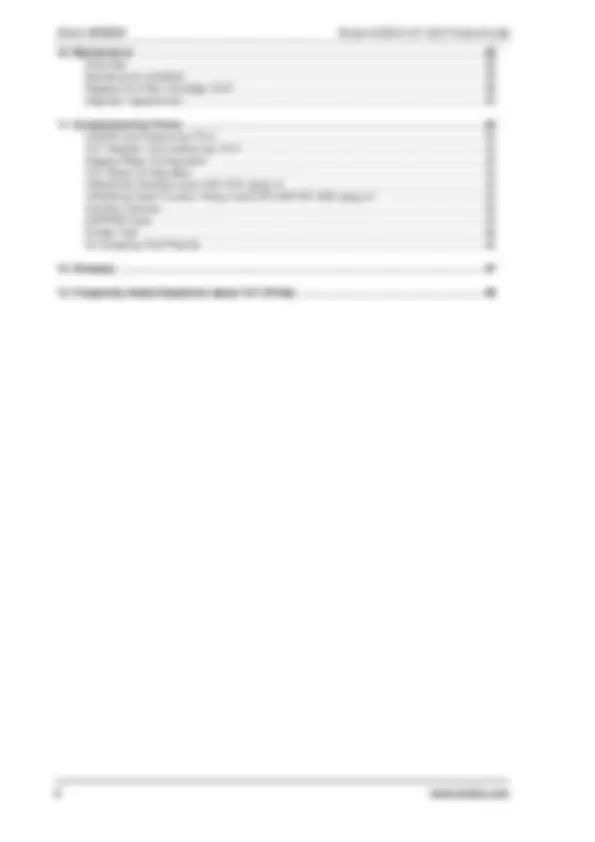
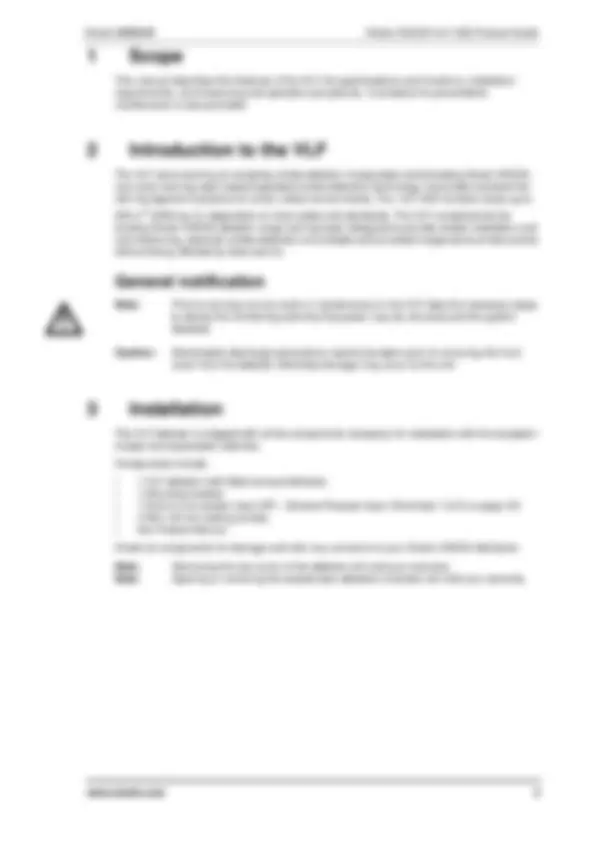
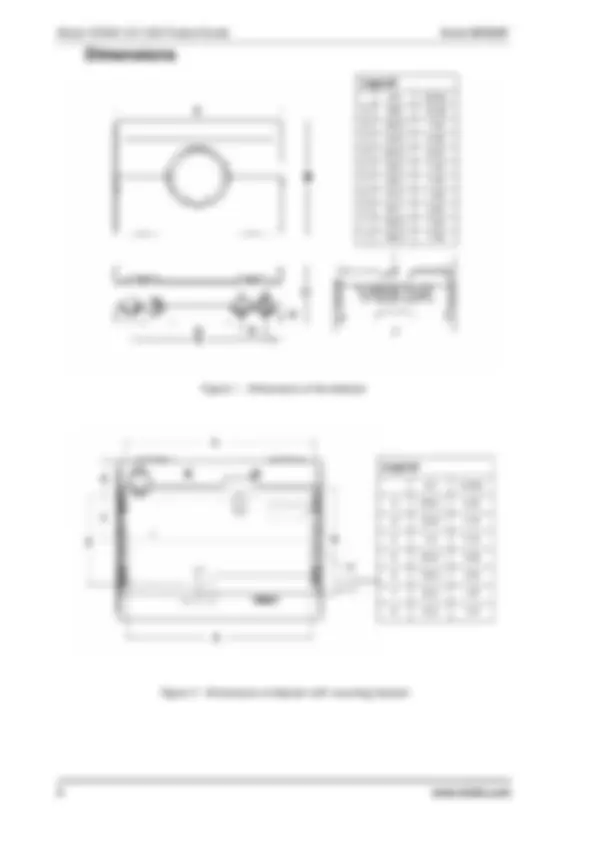
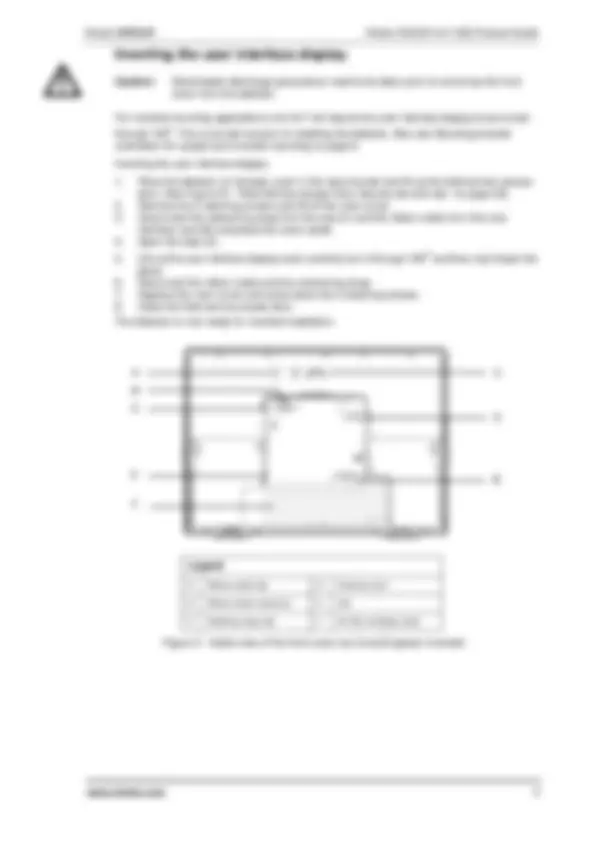
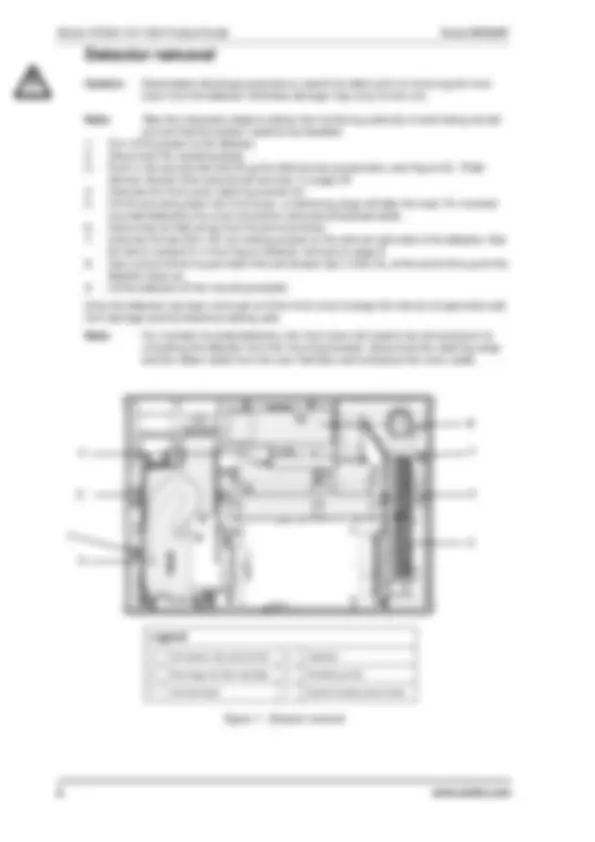
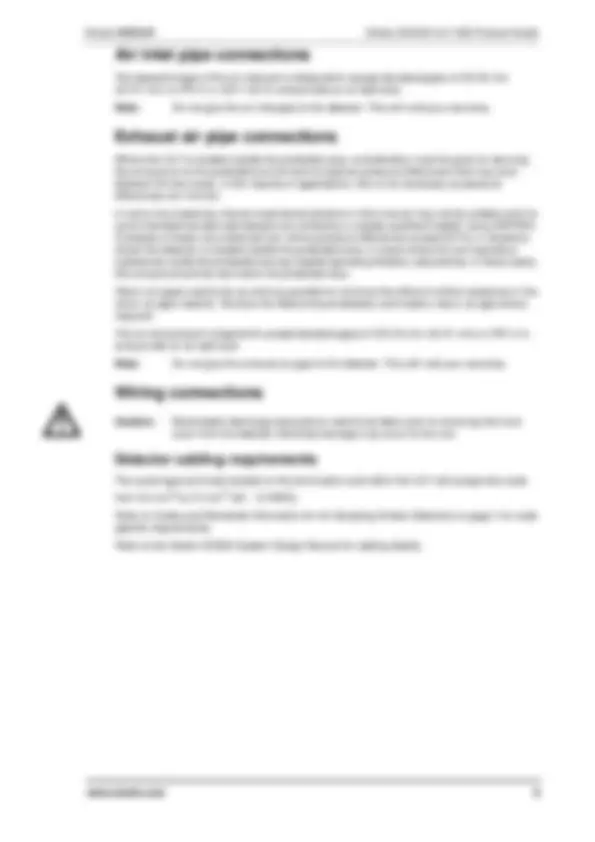
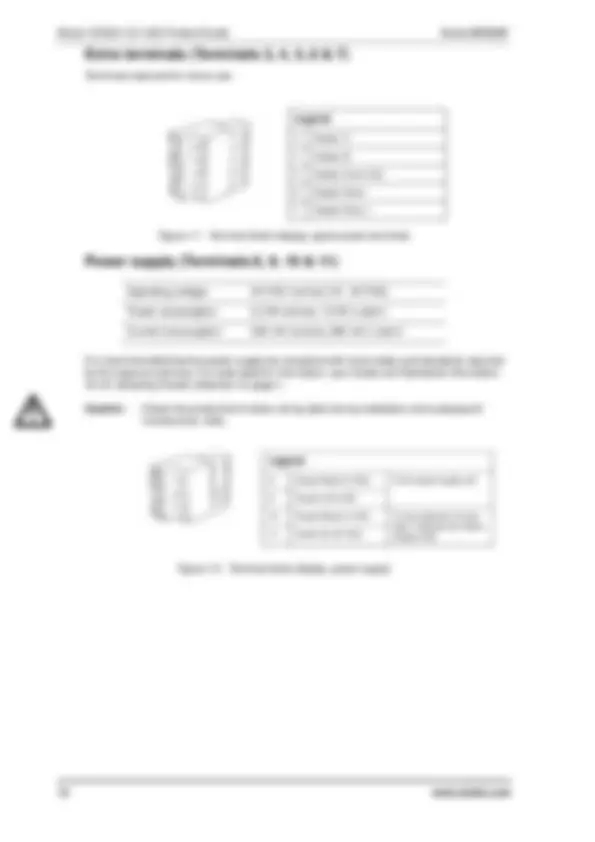
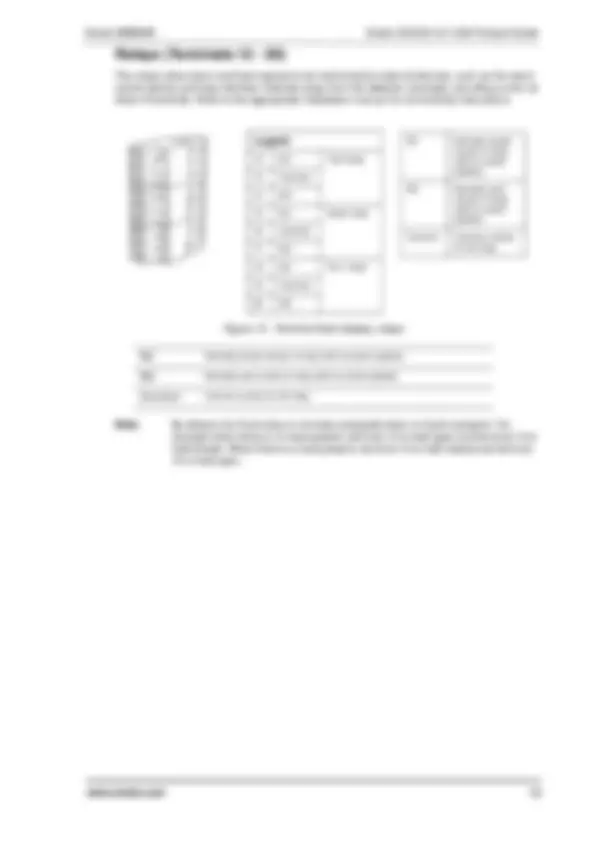
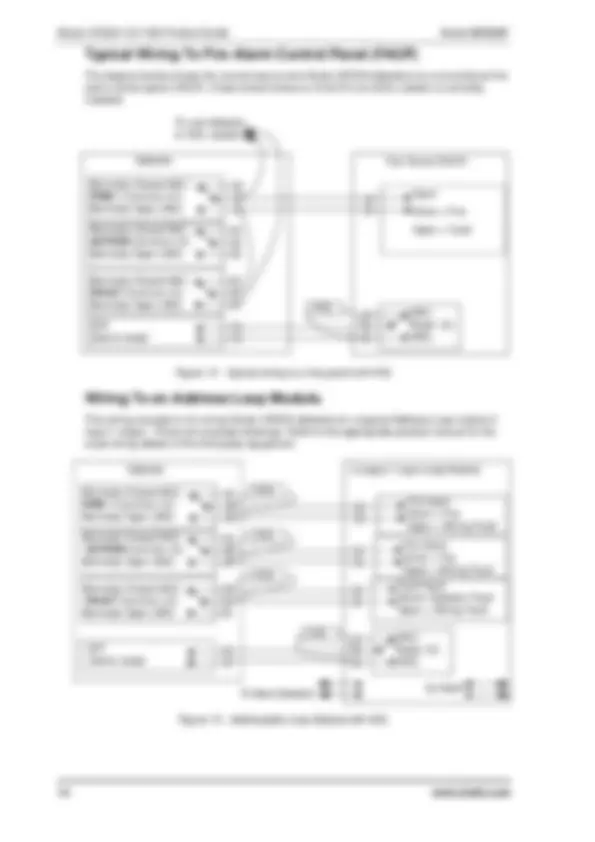
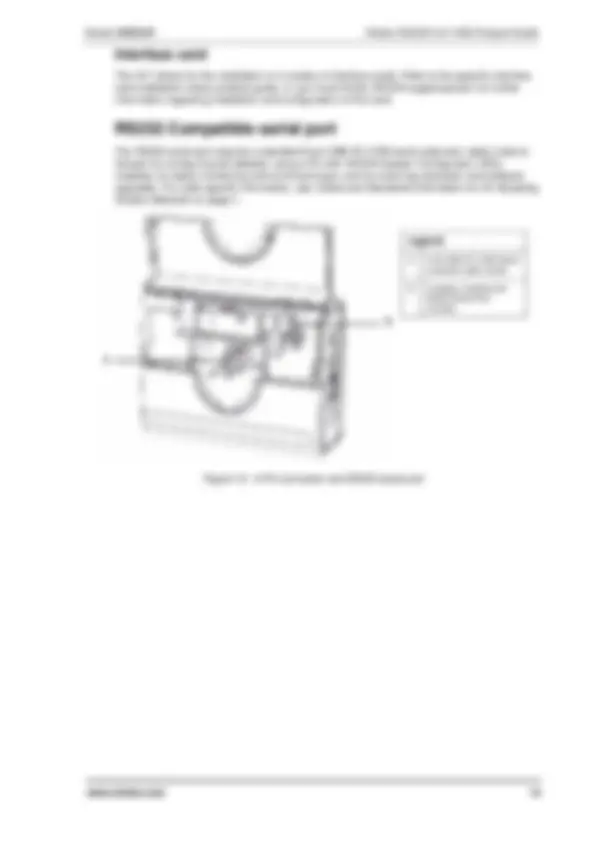
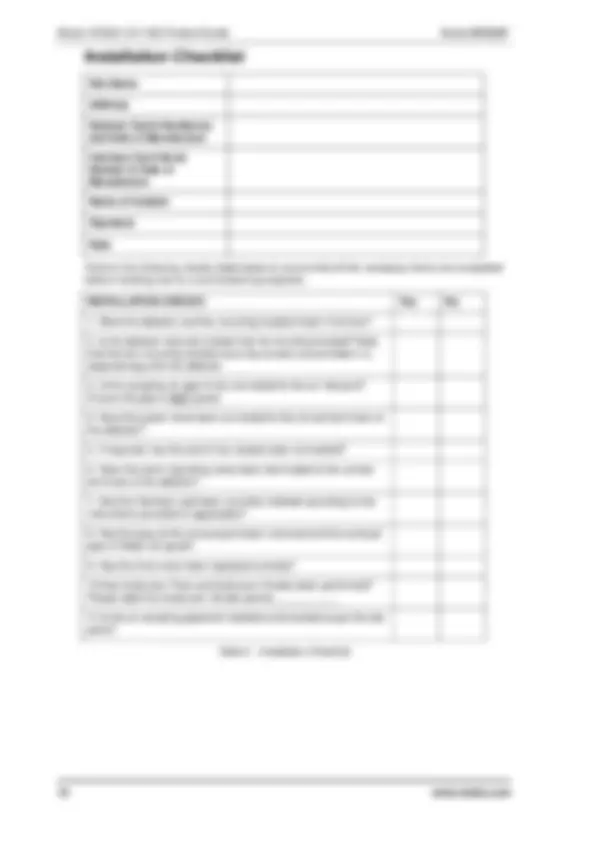
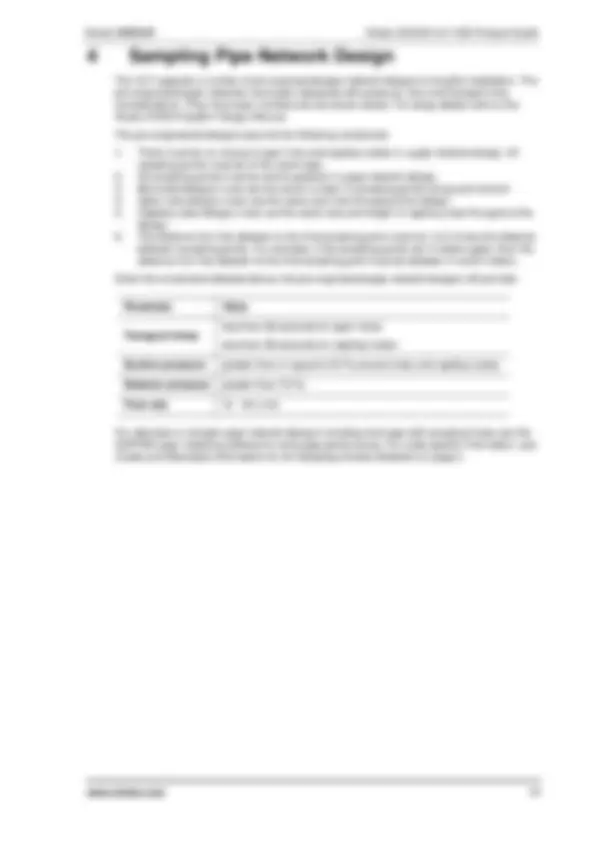
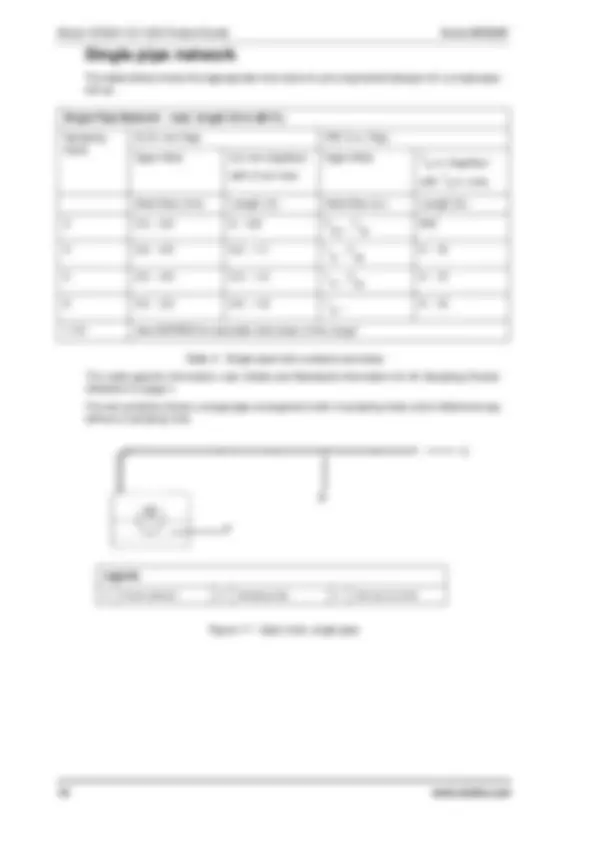
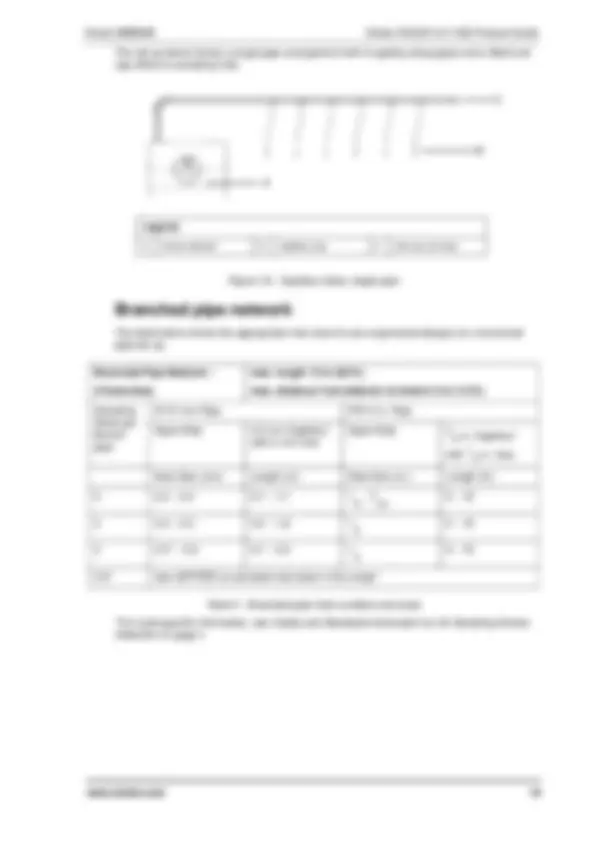
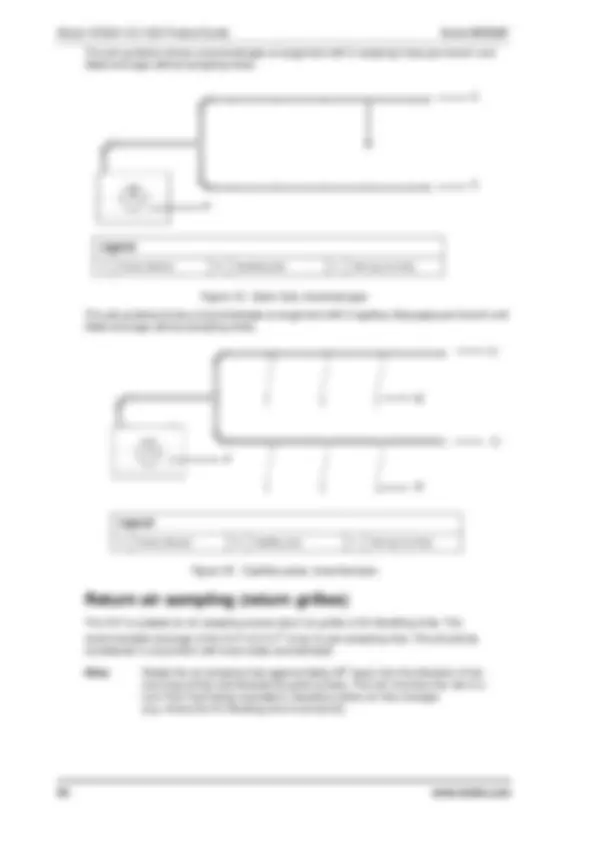
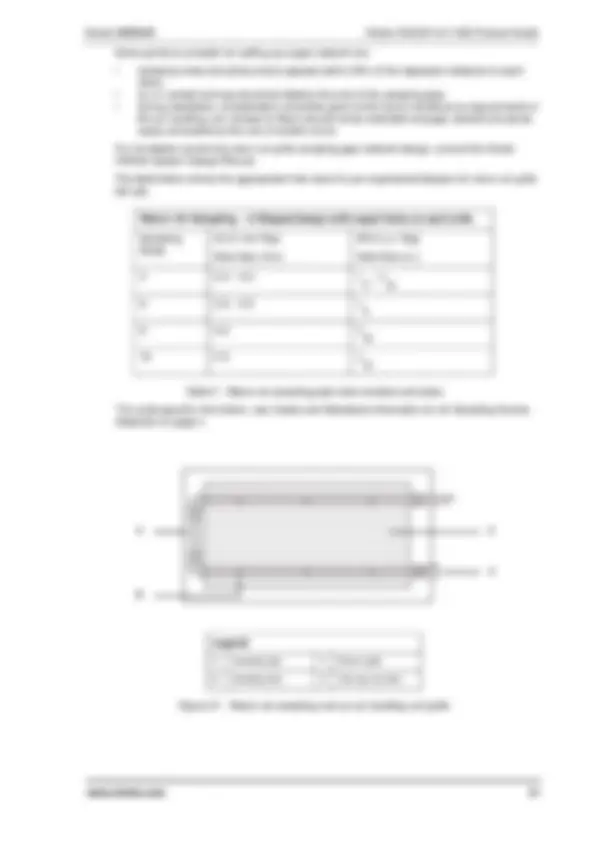

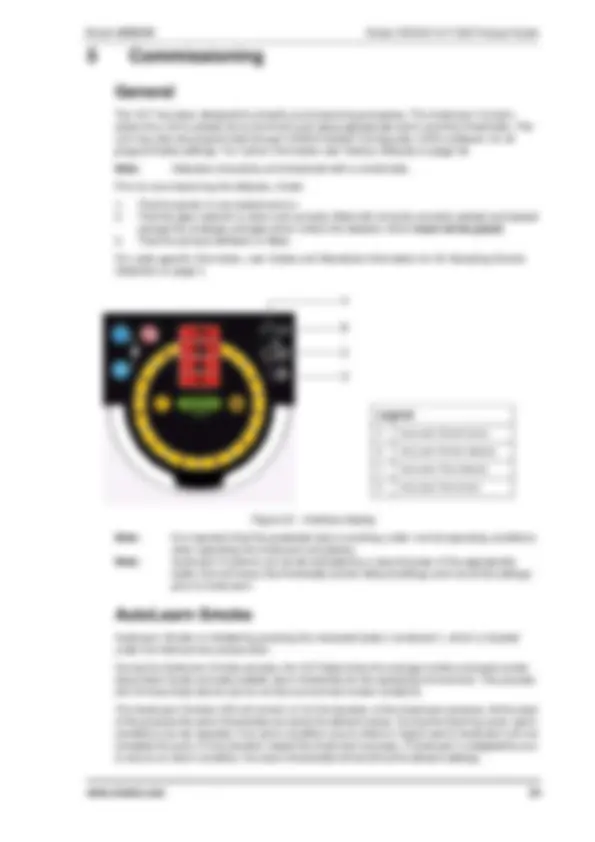
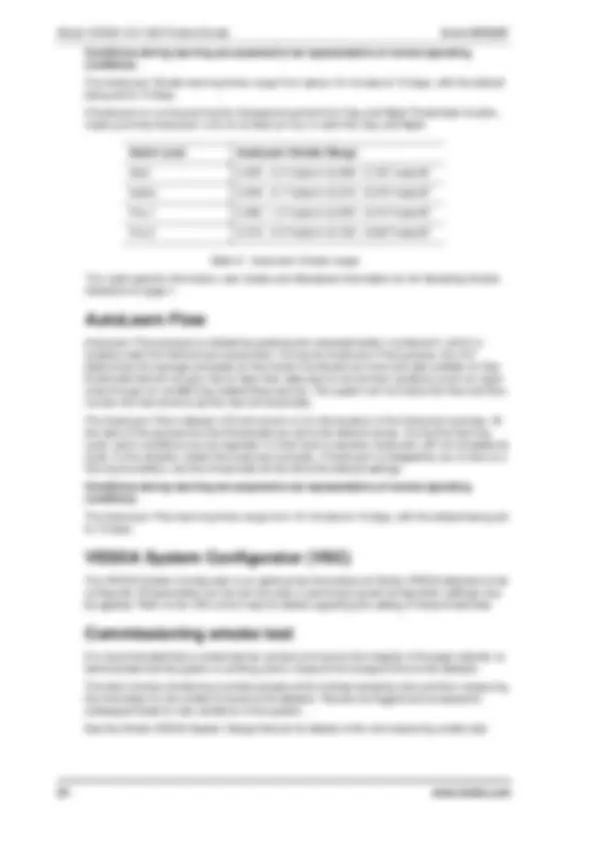
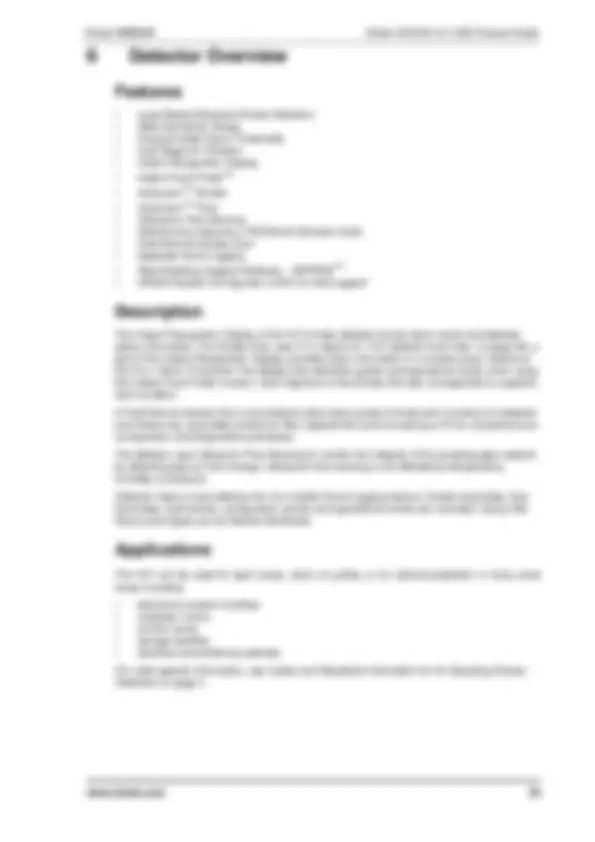
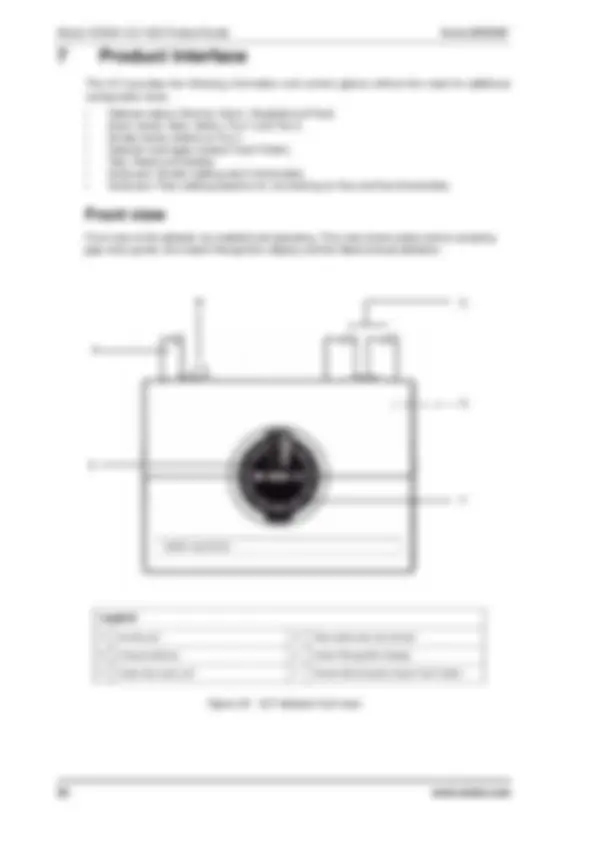
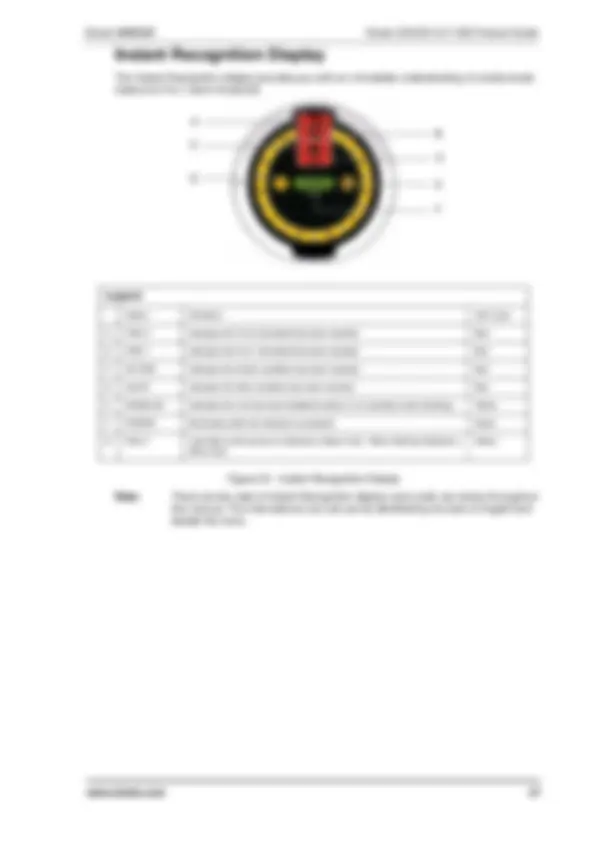
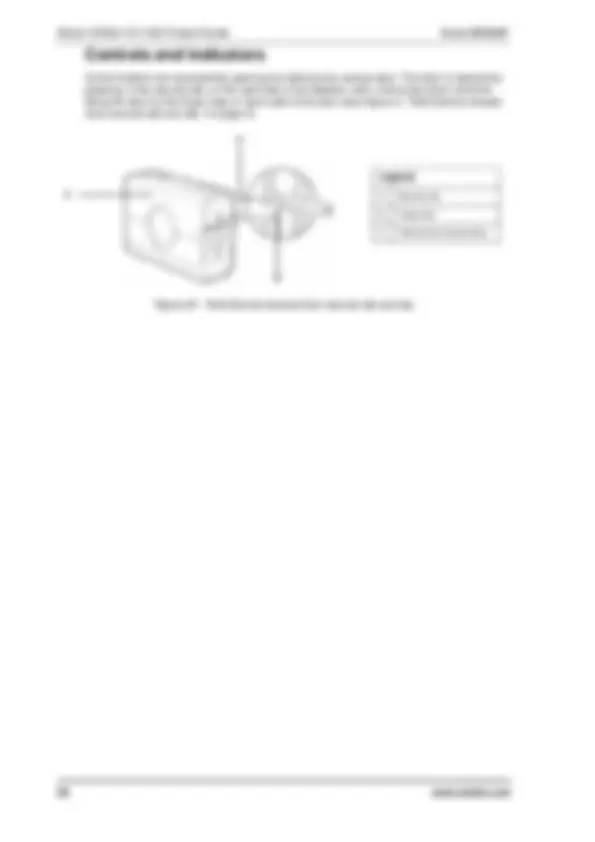
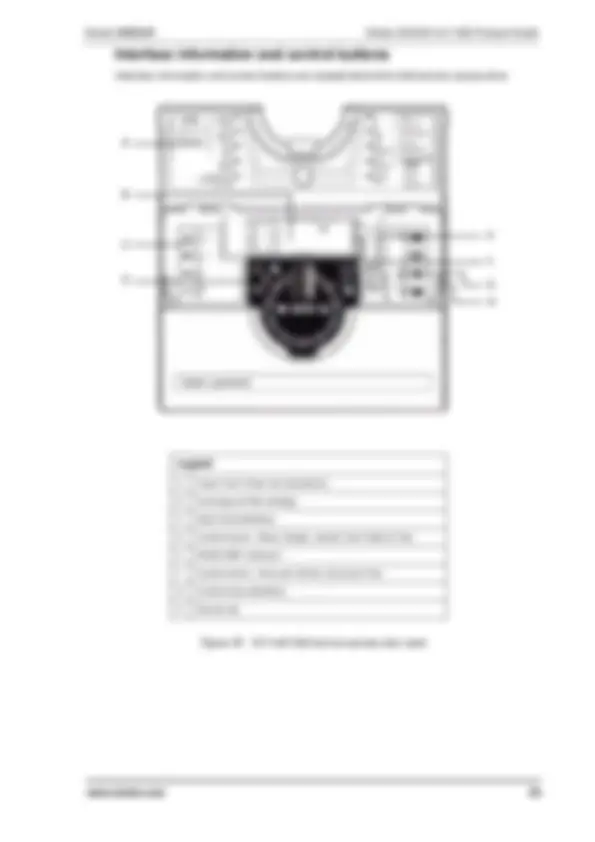
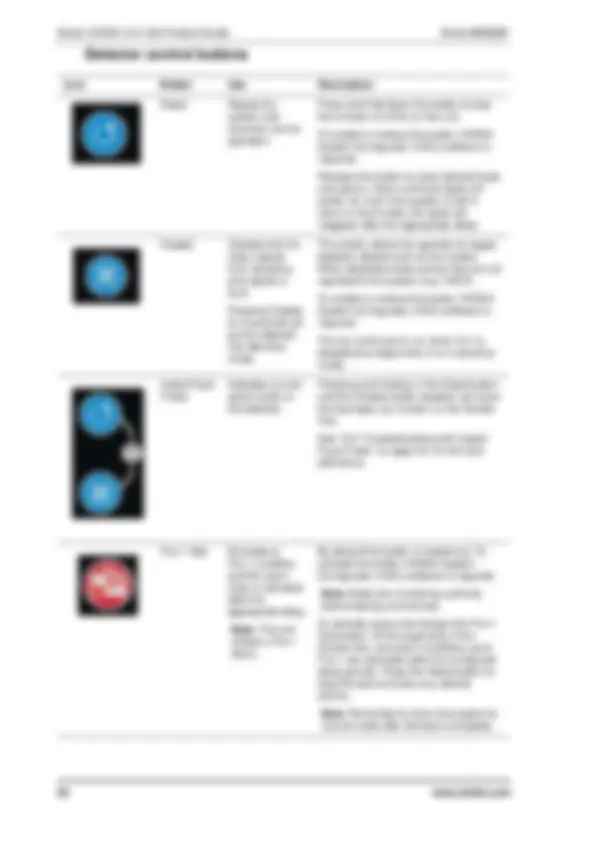
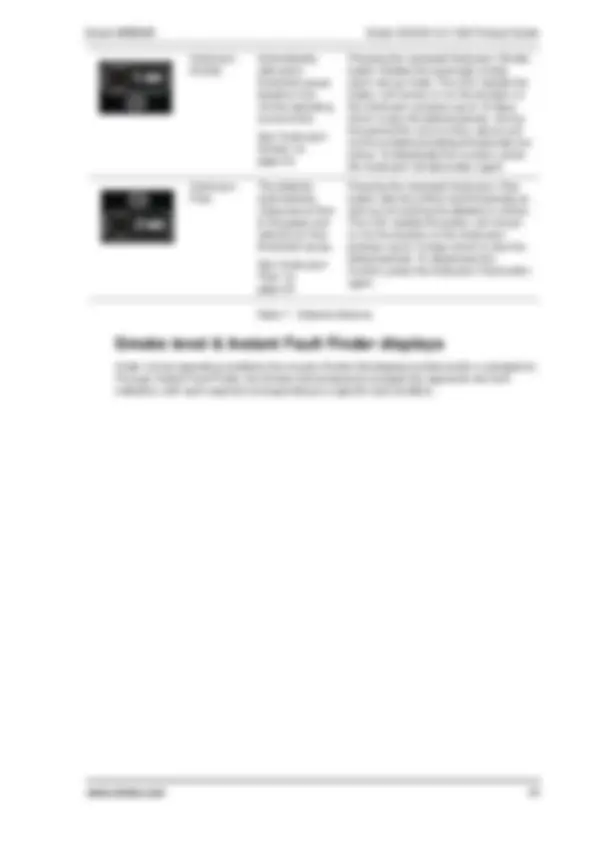
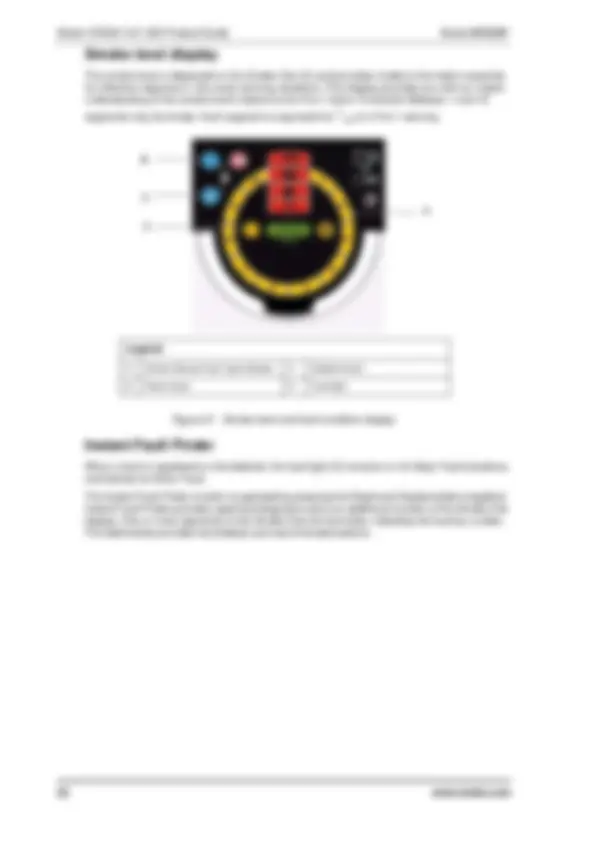
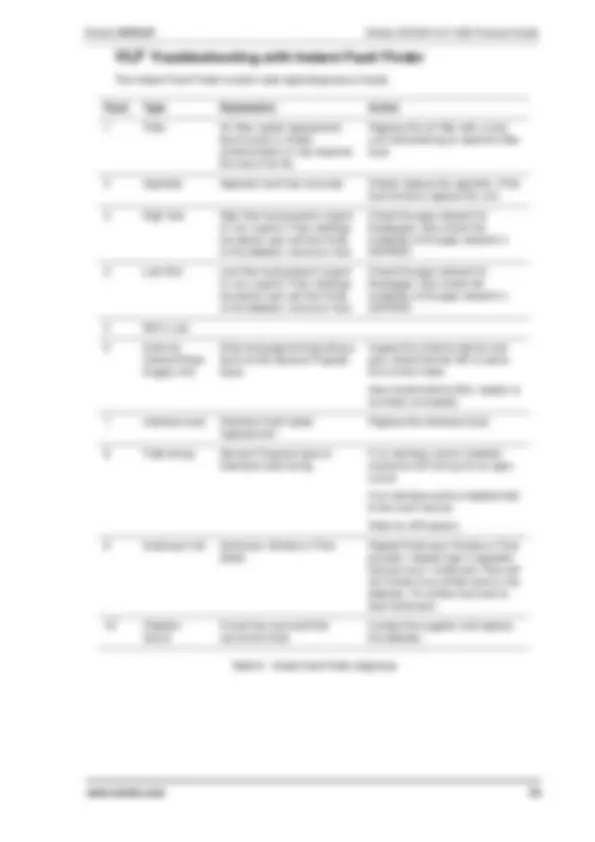
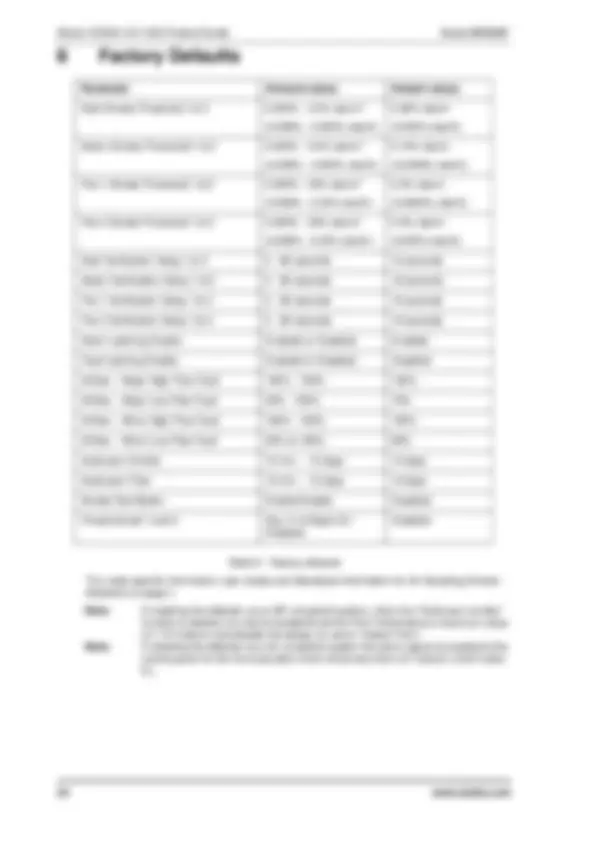
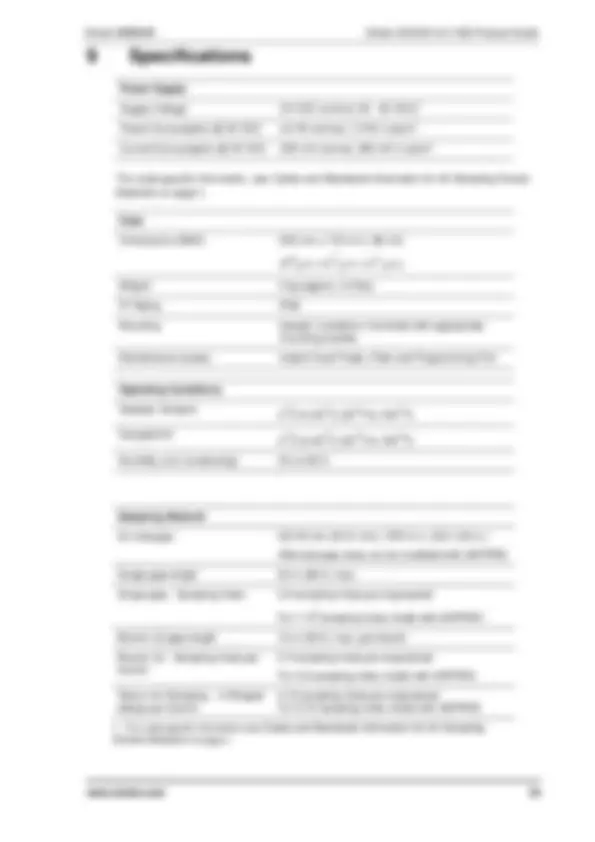
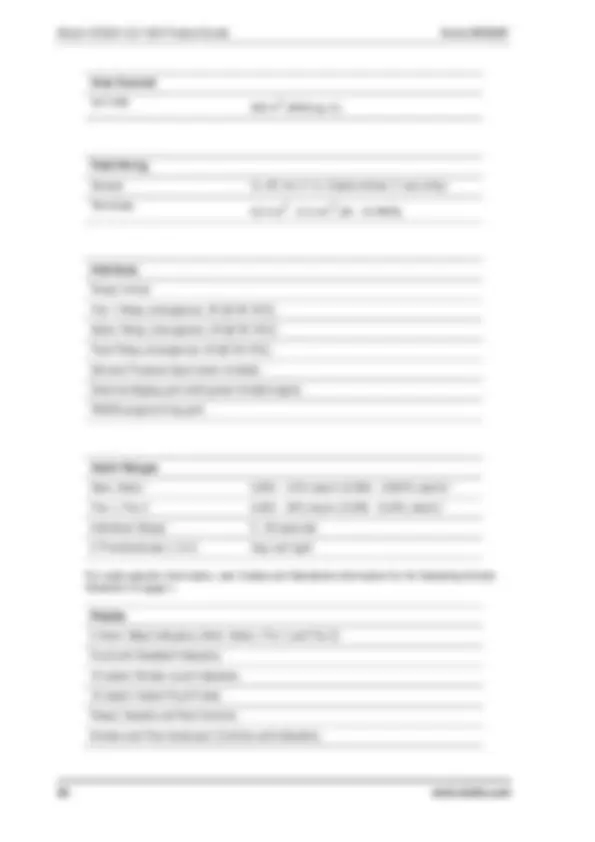
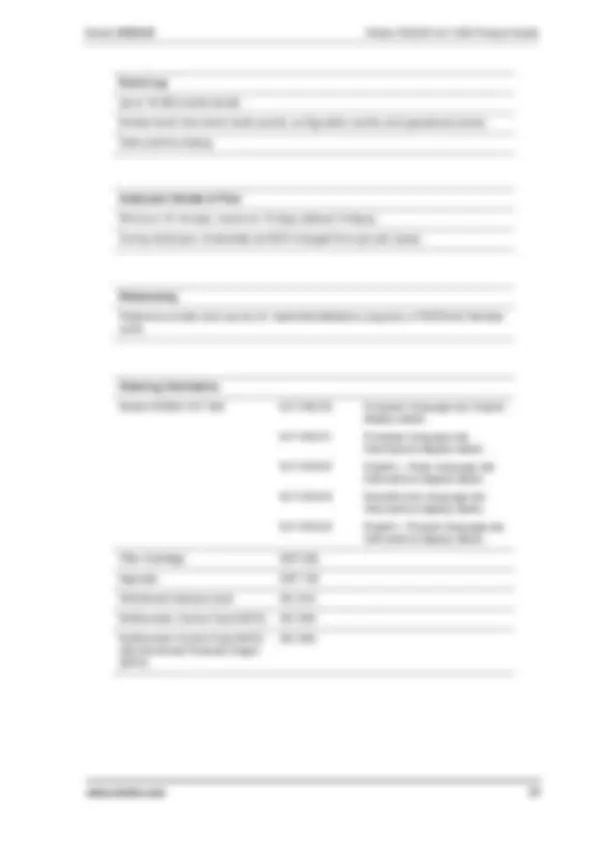
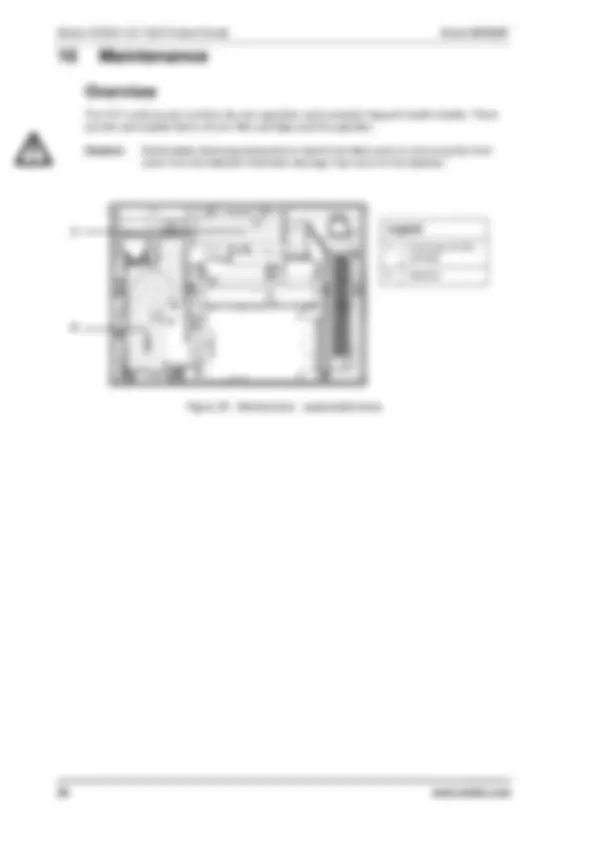
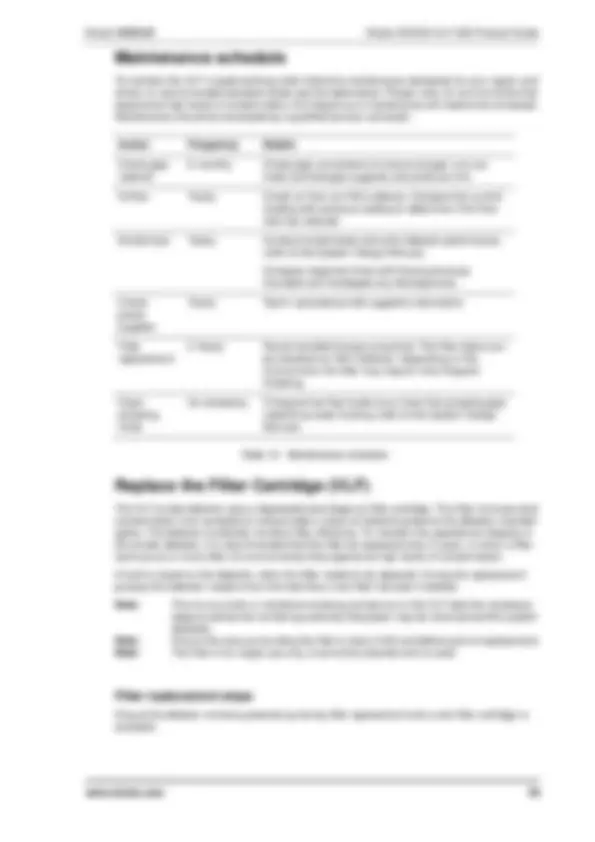
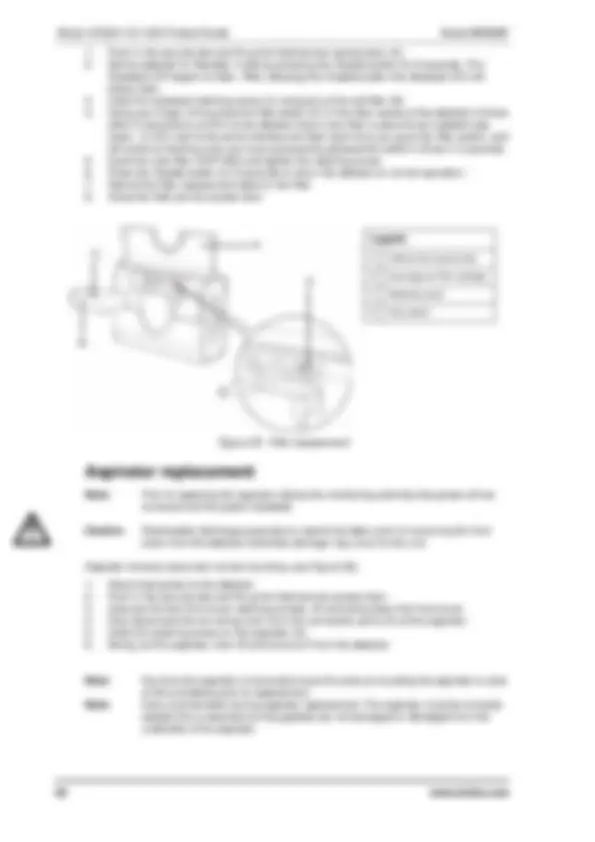
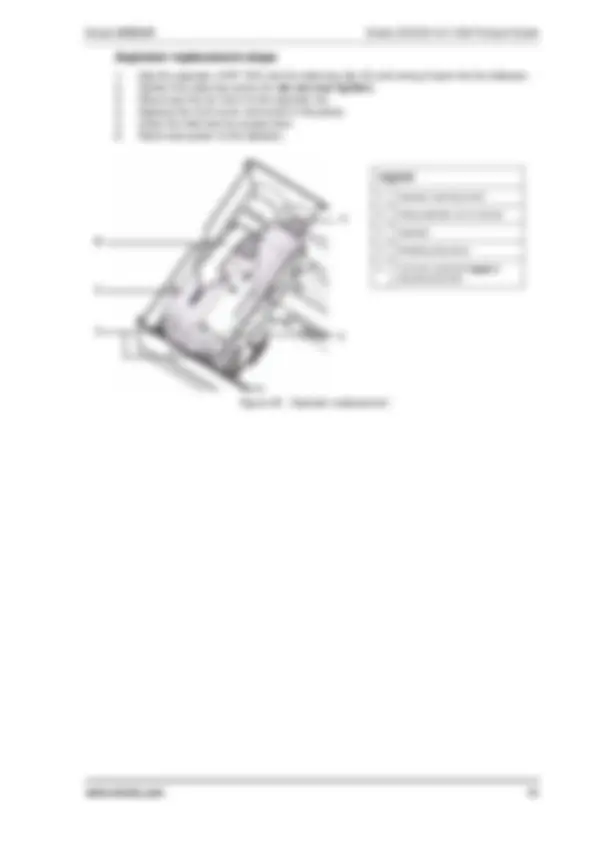
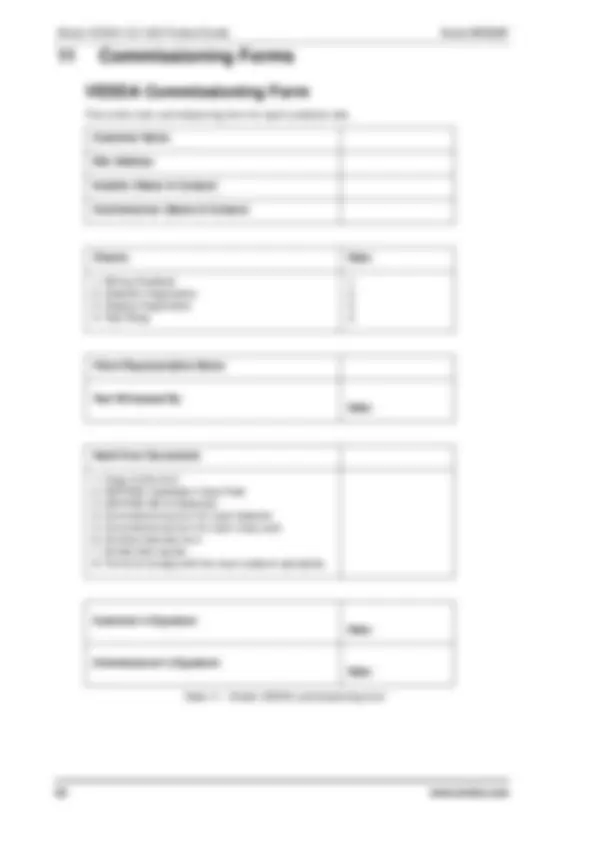
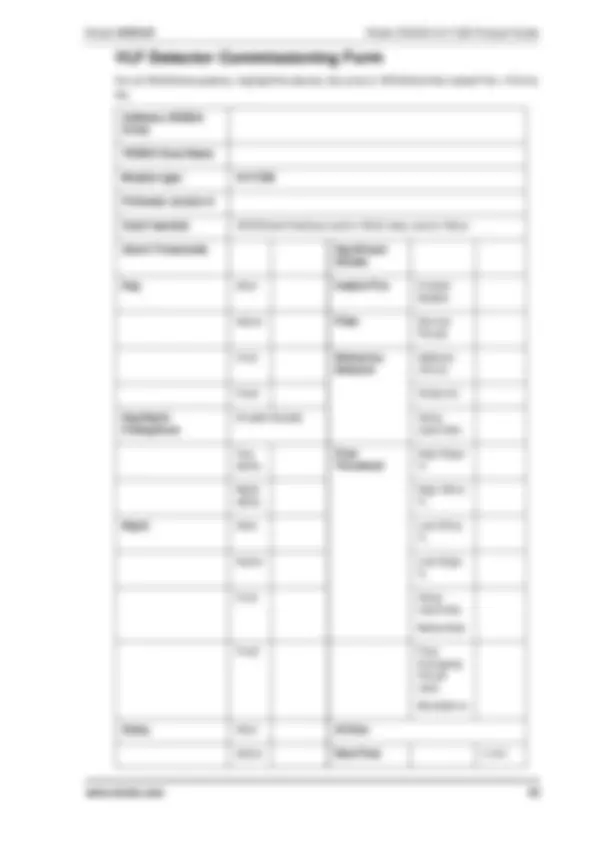

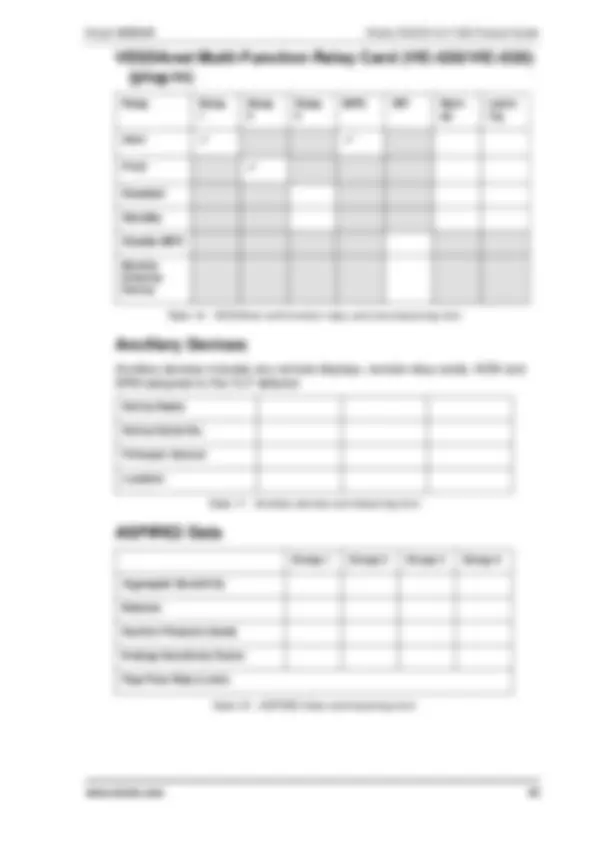
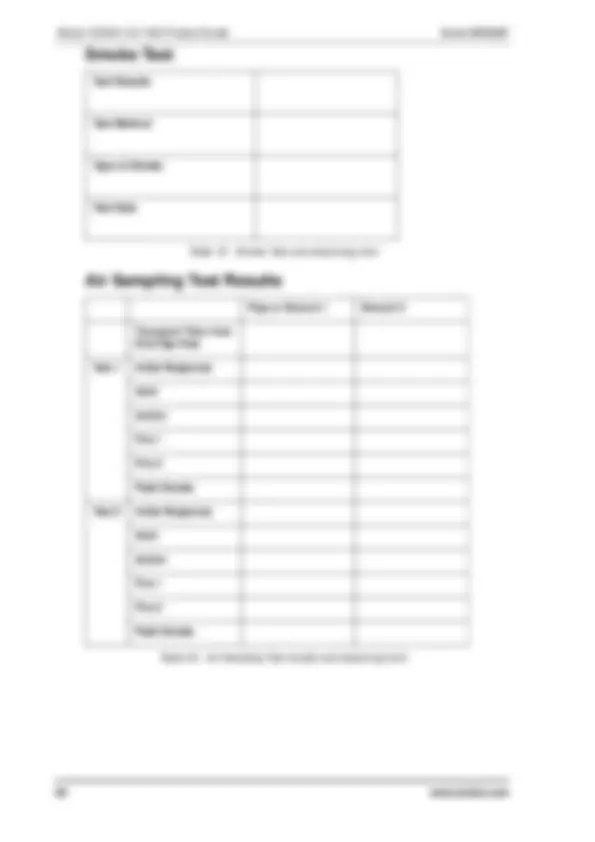
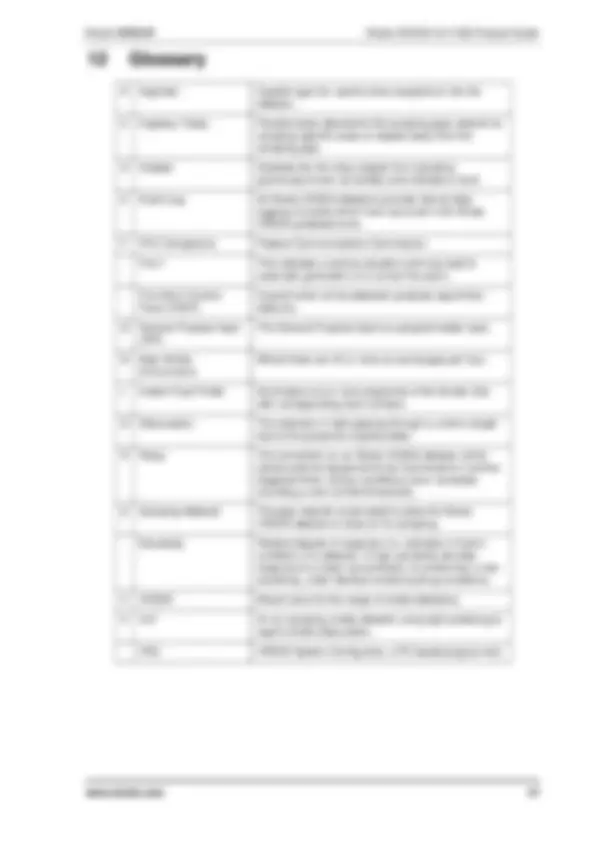
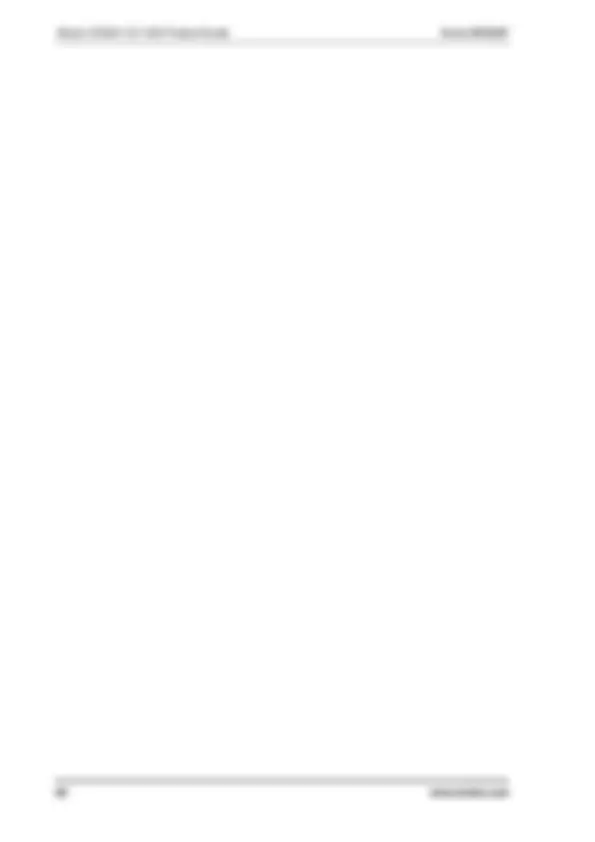
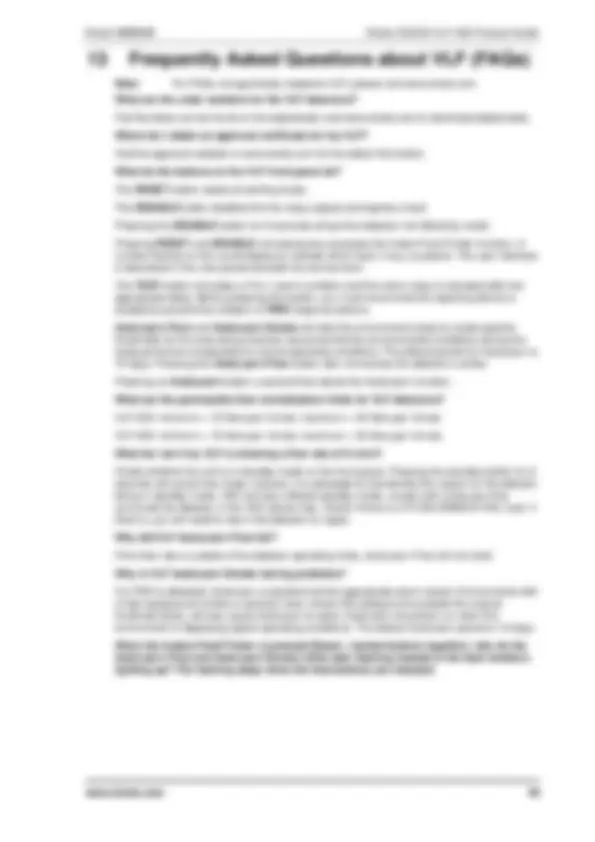
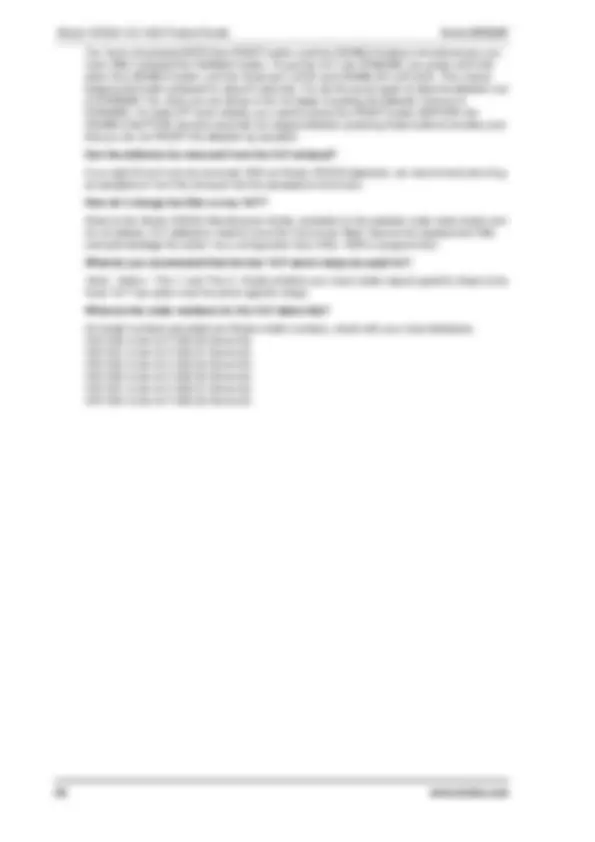
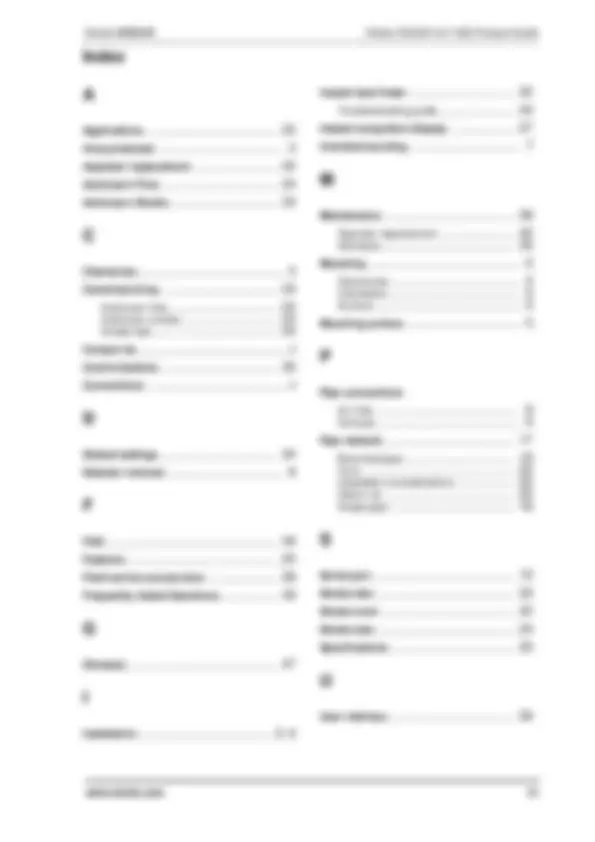
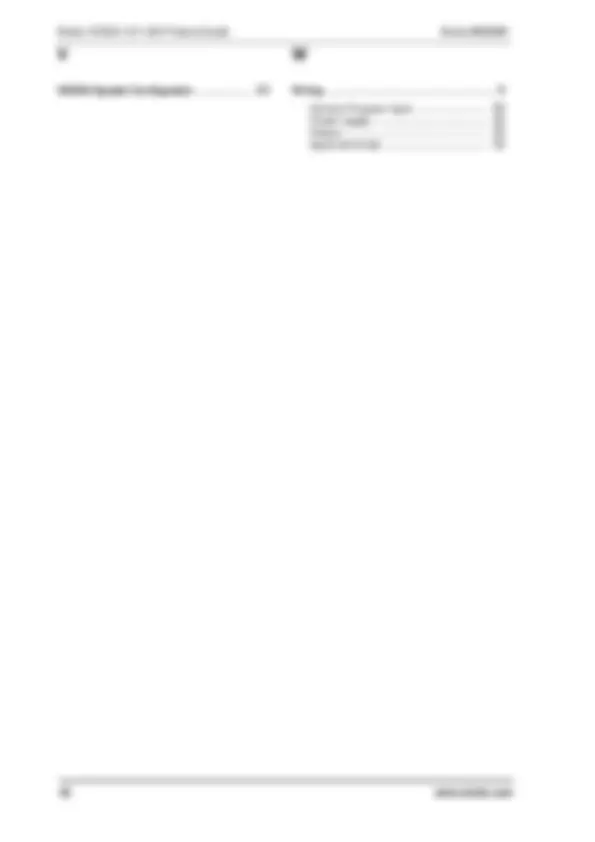
Estude fácil! Tem muito documento disponível na Docsity
Ganhe pontos ajudando outros esrudantes ou compre um plano Premium
Prepare-se para as provas
Estude fácil! Tem muito documento disponível na Docsity
Prepare-se para as provas com trabalhos de outros alunos como você, aqui na Docsity
Os melhores documentos à venda: Trabalhos de alunos formados
Prepare-se com as videoaulas e exercícios resolvidos criados a partir da grade da sua Universidade
Responda perguntas de provas passadas e avalie sua preparação.
Ganhe pontos para baixar
Ganhe pontos ajudando outros esrudantes ou compre um plano Premium
Comunidade
Peça ajuda à comunidade e tire suas dúvidas relacionadas ao estudo
Descubra as melhores universidades em seu país de acordo com os usuários da Docsity
Guias grátis
Baixe gratuitamente nossos guias de estudo, métodos para diminuir a ansiedade, dicas de TCC preparadas pelos professores da Docsity
Um manual detalhado que descreve as características, especificações, funções, requisitos de instalação, procedimentos de comissionamento e operação do detector de fumaça vlf da xtralis vesda. Ele fornece instruções passo a passo para a instalação, configuração e manutenção do dispositivo, incluindo informações sobre a conexão de cabos, ajuste de fluxo de ar, realização de testes e solução de problemas. O manual também aborda considerações importantes sobre a segurança e o desempenho do detector, como a necessidade de manter a área em torno do filtro limpa e substituir o filtro regularmente. Com detalhes técnicos abrangentes e orientações práticas, este documento é uma referência valiosa para profissionais que trabalham com sistemas de detecção de incêndio baseados no detector vlf.
Tipologia: Resumos
1 / 58
Esta página não é visível na pré-visualização
Não perca as partes importantes!
Xtralis VESDA VLF-250 Product Guide Xtralis VESDA®
ii www.xtralis.com
Document Conventions The following typographic conventions are used in this document.
The following icons are used in this document
Contact Us
Codes and Standards Information for Air Sampling Smoke Detection We strongly recommend that this document is read in conjunction with the appropriate local codes and standards for smoke detection and electrical connections. This document contains generic product information and some sections may not comply with all local codes and standards. In these cases, the local codes and standards must take precedence. The information below was correct at time of printing but may now be out of date, check with your local codes, standards and listings for the current restrictions. FCC Compliance Statement This equipment has been tested and found to comply with the limits for a Class B digital device, pursuant to part 15 of the FCC Rules. These limits are designed to provide reasonable protection against harmful interference in a residential installation. This equipment generates, uses and can radiate radio frequency energy and, if not installed and used in accordance with the instruction, may cause harmful interference to radio communications. However, there is no guarantee that interference will not occur in a particular installation. If this equipment does cause harmful interference to radio or television reception, the user is encouraged to try to correct the interference by one or more of the following measures; re-orientate or relocate the receiving antenna, increase the separation between the equipment and receiver, connect the equipment to a power outlet which is on a different power circuit to the receiver or consult the dealer or an experienced radio/television technician for help. FDA This VESDA product incorporates a laser device and is classified as a Class 1 laser product that complies with FDA regulations 21 CFR 1040.10. The laser is housed in a sealed detector chamber and contains no serviceable parts. The laser emits invisible light and can be hazardous if viewed with the naked eye. Under no circumstances should the detector chamber be opened. FM Hazardous Applications 3611 Hazardous Approval Warning: Exposure to some chemicals may degrade the sealing of relays used on the detector. Relays used on the detector are marked “TX2-5V”, “G6S-2-5V” or “EC2-5NU”. VESDA detectors must not be connected or disconnected to a PC while the equipment is powered in an FM Division 2 hazardous (classified) location (defined by FM 3611).
Convention Description
Bold Used to denote: emphasis Used for names of menus, menu options, toolbar buttons
Italics Used to denote: references to other parts of this document or other documents. Used for the result of an action.
Convention Description
Caution: This icon is used to indicate that there is a danger to equipment. The danger could be loss of data, physical damage, or permanent corruption of configuration details.
Warning: This icon is used to indicate that there is a danger of electric shock. This may lead to death or permanent injury.
Warning: This icon is used to indicate that there is a danger of inhaling dangerous substances. This may lead to death or permanent injury.
The Americas +1 781 740 2223
Asia +8 52 2297 2438
Australia and New Zealand +61 3 9936 7000
Continental Europe +41 55 285 99 99
UK and the Middle East +44 1442 242 330
www.xtralis.com
Xtralis VESDA®^ Xtralis VESDA VLF-250 Product Guide
www.xtralis.com iii
FM Approved Applications The product must be powered from VPS-100US-120, VPS-100US-220 or VPS-220 only. ONORM F ONORM F3014, transport times for all tubes (including capillaries) must not exceed 60 seconds from any hole. This means that the pre- designed pipe networks that include capillaries cannot be used. AS1603. The performance of this product is dependent upon the configuration of the pipe network. Any extensions or modifications to the pipe network may cause the product to stop working correctly. You must check that ASPIRE2 approves alterations before making any changes. ASPIRE2 is available from your VESDA ASD distributor. AS1851.1 2005 Maintenance Standards. Wherever this document and the AS1851.1 differ, AS1851.1 should be followed in preference to this document. European Installations The product must use a power supply conforming to EN54: Part 4.
Regional regulatory requirement and notices for the VLF UL For open area protection the fire alarm threshold (signal) that initiates an evacuation procedure via the Fire Alarm Panel must not be set less sensitive than 0.625%/ft. The detector can send this signal via the Fire Alarm Panel Output signal or the Pre-alarm output signal. ActivFire The fire alarm threshold (signal) that initiates an evacuation procedure via the Fire Alarm Panel must not be set less sensitive than 1%m.
AFNOR Table 3 on page 18: The maximum number of holes is 10. Table 4 on page 19: The minimum hole size is 3mm; the maximum number of holes per branch is 5. Table 5 on page 21: The minimum hole size is 3mm; the maximum number of holes per branch is 5. Installation considerations on page 22: The maximum number of holes is 10. Sampling Network on page 35: The maximum number of holes is 10. If 20 holes are used, the minor low flow fault must be set to 90%. EN 54- The product must use a power supply conforming to EN 54-4. The product is compliant with EN 54-20 sensitivity requirements provided the following conditions are met:
The product is compliant with EN 54-20 flow monitoring requirements provided the following conditions are met:
Regional approvals listings and regulatory compliance vary between Xtralis VESDA product models. Refer to www.xtralis.com for the latest product approvals matrix.
Document Number: 07208_ Part Number: 20295
Xtralis VESDA VLF-250 Product Guide Xtralis VESDA®
Figure 1 - Dimensions of the detector
Figure 2 - Dimensions of detector with mounting bracket
Legend mm inches A 256 10. B 182.8 7. C 134.0 5. D 204.0 8. E 36.0 1. F 25.5 1. G 27.0 1. H 92.1 3. I 182.8 7. J 180.0 7.
Legend mm inches A 236.3 9. B 120.0 4. C 4.5 0. D 230.0 9. E 100.0 3. F 50.0 1. G 40.0 1.
Xtralis VESDA®^ Xtralis VESDA VLF-250 Product Guide
The VLF can be installed upright, inverted or horizontally. Note: Ensure the smoke detector is mounted away from obstructions and below ceiling level.
Caution: An exhaust deflector must be fitted for upright mounting, unless the exhaust port is connected to a return air pipe.
Caution: Do not install this unit on its side. There is a risk of particulate and condensation collecting on critical elements of the detector chamber reducing the detectors performance.
Ensure that there is sufficient clearance to mount the detector, noting the location of air sampling pipes and cable entry points. Owing to the rigid nature of the plastic pipe, installation must provide for sufficient movement in all pipework (air inlet, air exhaust and cable pipes) to allow pipe ends to be easily fitted and removed.
Figure 3 - Mounting location
In all installation cases the mounting bracket must be fitted (upright) as shown in figure 4, “Mounting bracket orientation for upright and inverted mounting,” on page 6. Note: Ensure the mounting surface is flat. This will permit an air tight seal to be achieved between the sampling pipe and the tapered air ports on the detector.
Warning: Prior to drilling the attachment holes for the mounting bracket, ensure that all mounting surfaces (i.e. walls, cabinet sides, etc.). are clear of electrical wiring and plumbing.
Where the pipe network and cabling are already fitted, the bracket can be used to aid alignment of the detector with the pipes. The Installation procedure below explains this process.
Legend
A Min. 200 mm (8 in.) below ceiling level B Min. 500 mm (20 in.) from a wall or obstruction to allow access to the security tab C Do not install the detector on its side
Xtralis VESDA®^ Xtralis VESDA VLF-250 Product Guide
Caution: Electrostatic discharge precautions need to be taken prior to removing the front cover from the detector.
For inverted mounting applications, the VLF will require the user interface display to be turned through 180 o
. This is carried out prior to installing the detector. Also see Mounting bracket orientation for upright and inverted mounting on page 6. Inverting the user interface display:
Figure 6 - Inside view of the front cover (as it would appear inverted)
Legend
A Ribbon cable clip D Interface card B Ribbon cable connector E Clip C Retaining strap clip F Air filter cartridge cavity
Xtralis VESDA VLF-250 Product Guide Xtralis VESDA®
Caution: Electrostatic discharge precautions need to be taken prior to removing the front cover from the detector otherwise damage may occur to the unit.
Note: Take the necessary steps to advise the monitoring authority of work being carried out and that the system needs to be disabled.
Figure 7 - Detector removal
Legend A Anti-tamper clip access hole D Aspirator
B Dual stage air filter cartridge E Retaining screw C Terminal block F Bracket locking screw holes
Xtralis VESDA VLF-250 Product Guide Xtralis VESDA®
To reach the terminal block, open the field service access door, see Controls and indicators on page 28, and then unscrew the front cover retaining screws. Lift off and swing down the front cover. The terminal block is located on the right hand side of the detector.
Figure 8 - Terminal block
The General Purpose Input (GPI) is a programmable input. When the GPI function parameter is set to external, the detector shall indicate an external equipment fault condition by monitoring the line impedance. An End of Line (EOL) resistor is supplied with the product and must be assembled in parallel with the device to be monitored. The EOL resistor provides a known termination to the external equipment, this allows the VLF to detect open or short circuits. The detector monitors the EOL resistor, see Figure 8, and reports any faults when the GPI function is set to any value, except None.
Caution: These terminal blocks come assembled and should NOT be disassembled.
Figure 9 - Terminal and plug set up, GPI connections
Legend
A Terminal block, connectors 1 to 20
Legend 1 GPI pin 1 2 GPI pin 2
Xtralis VESDA®^ Xtralis VESDA VLF-250 Product Guide
The GPI function parameter can be set to the values shown in the table below to achieve several different functions:
Table 1 - GPI programming
The GP input detects a short circuit (e.g. the PSU fault relay) at or below 100 Ohms.
Figure 10 - Triggering of GPI
GPI function parameter value Result
None GPI is disabled. If GPI will not be used we recommend that you leave the EOL resistor assembled.
Reset Detector is reset on activation of the GPI (closing contact). Note: The factory-default value of the GPI function is Reset.
Disable Detector is disabled while GPI is active (contact closed) and reset on de-activation of the input (contact open).
Standby Detector is placed in standby (disabled, plus aspirator turned off) while GPI is active (contact closed) and reset on de-activation of the input (contact open).
Alarm set 1 Activation of GPI forces alarm threshold set 1 to be used. It overrides normal selection.
Alarm set 2 Activation of GPI forces alarm threshold set 2 to be used. It overrides normal selection.
External Detector indicates a fault while the GPI is active (contact closed). Typically this is used to monitor external power supply units. Note: If the contact is closed it will raise an Instant Fault Finder No.6 fault. If wire is broken to the monitoring device it will raise an Instant Fault Finder No.8 fault.
Legend
A End of Line Resistor (2.7k) B External device (1 to N) C GPI Pin 1 D GPI Pin 2
Xtralis VESDA®^ Xtralis VESDA VLF-250 Product Guide
The relays allow alarm and fault signals to be hard wired to external devices, such as fire alarm control panels and loop interface modules away from the detector (example, sounding a siren at Action threshold). Refer to the appropriate installation manual for connectivity instructions.
Figure 13 - Terminal block display, relays
Note: By default, the Fault relay is normally energized when no fault is present. For example when there is no fault present, terminal 12 is held open and terminal 14 is held closed. When there is a fault present, terminal 12 is held closed and terminal 14 is held open.
NC Normally closed contact of relay (with no power applied).
NO Normally open contact of relay (with no power applied).
Common Common contact for the relay.
Legend 12 NC Fault relay 13 Common 14 NO 15 NC Action relay 16 Common 17 NO 18 NC Fire 1 relay 19 Common 20 NO
NC Normally closed contact of relay (with no power applied). NO Normally open contact of relay (with no power applied). Common Common contact for the relay.
Xtralis VESDA VLF-250 Product Guide Xtralis VESDA®
The diagram below shows the correct way to wire Xtralis VESDA detectors to a conventional fire alarm control panel (FACP). It also shows where an End Of Line (EOL) resistor is correctly installed.
Figure 14 - Typical wiring to a fire panel with EOL
This wiring example is for wiring Xtralis VESDA detectors to a typical Address Loop module 3 input 1 output. These are example drawings. Refer to the appropriate product manual for the exact wiring details of the third party equipment.
Figure 15 - Addressable Loop Module with EOL
Normally Closed (NC) FIRE 1 Common (C) Normally Open (NO)
Normally Closed (NC) ACTION Common (C) Normally Open (NO)
Normally Closed (NC) FAULT Common (C) Normally Open (NO)
GPI (Set to reset)
Reset (C) (NO)
Input Short = Fire Open = Fault
Detector Fire Panel (FACP)
To next detector or EOL resistor
Normally Closed (NC) FIRE 1 Common (C) Normally Open (NO)
Normally Closed (NC) ACTION Common (C) Normally Open (NO)
Normally Closed (NC) FAULT Common (C) Normally Open (NO)
(Set to reset)
Reset (C) (NO)
Fire Input Short = Fire Open = Wiring Fault
Detector 3 output 1 input Loop Module
Pre Alarm Short = Fire Open = Wiring Fault Fault Input Short= Detector Fault Open = Wiring Fault
To Next Detector To FACP