

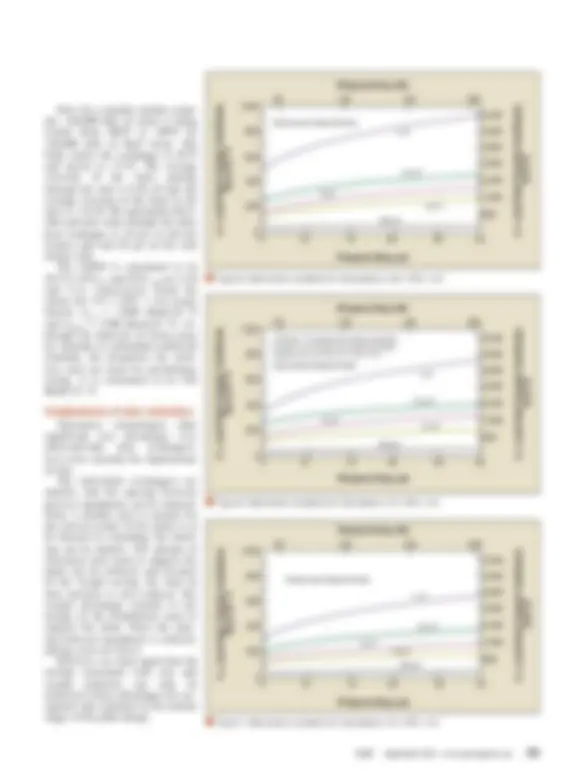
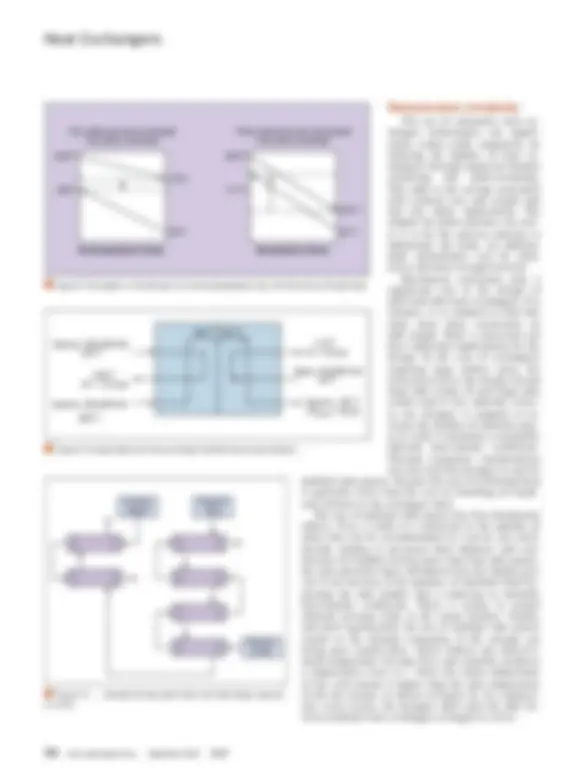
Estude fácil! Tem muito documento disponível na Docsity
Ganhe pontos ajudando outros esrudantes ou compre um plano Premium
Prepare-se para as provas
Estude fácil! Tem muito documento disponível na Docsity
Prepare-se para as provas com trabalhos de outros alunos como você, aqui na Docsity
Os melhores documentos à venda: Trabalhos de alunos formados
Prepare-se com as videoaulas e exercícios resolvidos criados a partir da grade da sua Universidade
Responda perguntas de provas passadas e avalie sua preparação.
Ganhe pontos para baixar
Ganhe pontos ajudando outros esrudantes ou compre um plano Premium
Comunidade
Peça ajuda à comunidade e tire suas dúvidas relacionadas ao estudo
Descubra as melhores universidades em seu país de acordo com os usuários da Docsity
Guias grátis
Baixe gratuitamente nossos guias de estudo, métodos para diminuir a ansiedade, dicas de TCC preparadas pelos professores da Docsity
Design Plate and Frame Heat Exchangers by Haslego
Tipologia: Notas de aula
1 / 6
Esta página não é visível na pré-visualização
Não perca as partes importantes!
32 www.cepmagazine.org September 2002 CEP
onsidering available heat exchanger technolo- gies at the outset of process design (at the process synthesis stage) is not general prac- tice. In fact, procedures established in some companies preclude it. For instance, some purchasing de- partments’ “nightmare” is having to deal with a single sup- plier — instead they want a general specification that can be sent to all equipment vendors, in the mistaken belief that they are then operating on a “level playing field.” This omission is both unfortunate and costly. It results in unnecessary cap- ital expenditure and in reduced energy efficiency. It also hinders the develop- ment of energy saving technology. Pinch analysis is the key tool used by engineers to develop flowsheets of ener- gy-intensive processes, where heat ex- changer selection is particularly impor- tant. Yet, this tool is hindering the adop- tion of a more-progressive approach be- cause of the way it is restricted to tradi- tional heat exchangers. Numerous articles have been pub- lished regarding the advantages of com- pact heat exchangers. Briefly, their higher heat-transfer coefficients, com- pact size, cost effectiveness, and unique ability to handle fouling fluids make them a good choice for many services. A plate-and-frame heat exchanger (Figure 1) consists of pressed, corrugat-
ed metal plates fitted between a thick, carbon-steel frame. Each plate flow channel is sealed with a gasket, a weld or an alternating combination of the two. It is not uncommon for plate-and-frame heat exchangers to have overall heat- transfer coefficients that are three to four times those found in shell-and-tube heat exchangers. This three-part series outlines the lost opportunities and the importance of proper heat exchanger selection. This arti- cle discusses some general aspects of plate-and-frame heat
COMPACT HEAT EXCHANGERS — PART 1:
Christopher Haslego, Alfa Laval Graham Polley, www.pinchtechnology.com
Figure 1. Cutaway drawing of a plate-and-frame heat exchanger.
CEP September 2002 www.cepmagazine.org 33
exchangers, outlines a procedure for accurately estimating the required area, and shows how these units can be used to simplify processes. Part 2 (which will appear next month) covers integrating plate-and-frame exchangers (and other compact technologies) into pinch analysis for new plants, while Part 3 (which also will appear next month) deals with the application of plate-and-frame exchangers and pinch technology to retrofits.
Engineers often fail to realize the differences between heat transfer technologies when preparing a specification to be sent to vendors of different types of heat exchangers. Consider the following example. A process stream needs to be cooled with cooling water before being sent to storage. The stream requires C276, an expensive high-nickel alloy, to guard against corrosion; this metallurgy makes the stream a candidate for the tubeside of a shell-and-tube heat exchanger. The cooling water is avail- able at 80°F and must be returned at a temperature no high- er than 115°F. The process engineer realizes that with the water flow being placed on the shellside, larger flowrates will enhance the heat-transfer coefficient. The basis for the heat exchanger quotation was specified as shown in the table. According to the engineer’s calculations, these basic parameters should result in a good shell-and-tube design that uses a minimum amount of C276 material. A typical plate-and-frame exchanger designed to meet the specification would have about 650 ft^2 of area, compared to about 420 ft^2 for a shell-and-tube exchanger. A plate-and- frame unit designed to the above specification is limited by the allowable pressure drop on the cooling water. If the cool- ing water flow is reduced to 655 gal/min and the outlet water temperature allowed to rise to 115°F, the plate-and-frame heat exchanger would contain about 185 ft^2 of area. The unit is smaller and less expensive, and it uses less water. The load being transferred to the cooling tower is the same. With shell-and-tube heat exchangers, increasing water flow will minimize heat-transfer area. However, with com- pact technologies, the effect is exactly the opposite. The larger water flow actually drives up the cost of the unit. Rather than supplying a rigid specification to all heat exchanger manufacturers, the engineer should have ex- plained the goal for the process stream. This could have been in the form of the following statement: “The process stream is to be cooled with cooling water. Up to 2, gal/min of water is available at 80°F. The maximum return
temperature is 115°F.” This simple statement could result in vastly different configurations compared with the de- signs that would result from the original specification.
When it comes to compact heat-transfer technology, engineers often find themselves at the mercy of the equipment manufacturers. For example, limited litera- ture correlations are available to help in the preliminary design of plate-and-frame heat exchangers. This article introduces a series of charts (Figures 2–7) that can be used for performing preliminary sizing of plate- and-frame exchangers. Examples will help clarify their use. The following important points should be noted regard- ing the charts and their use:
U h
x
hot k^ hcold
= + + ( )
cold LMTD = cold out ,^^ −^ cold in ,^ ( ) 3
hot LMTD = hot in ,^^ −^ hot out ,^ ( ) 2
hot in cold out hot out cold in
hot in cold out hot out cold in
( )
, , , ,
, , , ,
ln
Table. Basis for heat exchanger quotation.
Tubeside Shellside Flowrate, gal/min 500 1, Temperature In, ° F 280 80 Temperature Out, ° F 150 92 Allowable Pressure Drop, psi 15 15
Now let’s consider another exam- ple. 150,000 lb/h of water is being cooled from 200°F to 100°F by 150,000 lb/h of NaCl brine. The brine enters the exchanger at 50°F and leaves at 171°F. The average viscosity of the water passing through the unit is 0.46 cP and the average viscosity of the brine in the unit is 1.10 cP. The maximum-allow- able pressure drop through the plate heat exchanger is 10 psi on the hot (water) side and 20 psi on the cold (brine) side. The LMTD is calculated to be 38.5°F. NTU (^) hot and NTU (^) cold are 2. and 3.14, respectively. From the charts for 2.0 < NTU < 4.0 (water based), h (^) hot ≈ 2,000 Btu/h-ft 2 -°F and h (^) cold ≈ 2,500 Btu/h-ft 2 -°F. Al- though the material of choice may be titanium or palladium-stabilized titanium, the properties for stain- less steel are used for preliminary sizing. U is calculated to be 918 Btu/h-ft 2 -°F.
Alternative technologies offer significant size advantages over shell-and-tube heat exchangers. Let’s now consider the implications of this. The individual exchangers are smaller, and the spacing between process equipment can be reduced. Thus, a smaller plot is needed for the process plant. If the plant is to be housed in a building, the build- ing can be smaller. The amount of structural steel used to support the plant can be reduced, and because of the weight saving, the load on that structure is also reduced. The weight advantage extends to the design of the foundations used to support the plant. Since the spac- ing between equipment is reduced, piping costs are lower. However, we stress again that the savings associated with size and weight reduction can only be achieved if these advantages are rec- ognized and exploited at the earliest stages of the plant design.
CEP September 2002 www.cepmagazine.org 35
Figure 5. Heat-transfer correlations for hydrocarbons, 0.25 < NTU < 2.0.
Pressure Drop, psi
h = Local Heat-Transfer Coefficient,
Btu/h-ft
2 -
5 10 15 20 25 30
1,
800
600
400
200
0
5, 4, 3, 3,
2,
1,
800
100
1 cP
2.5 cP
5 cP 10 cP 100 cP
50 150 200
h = Local Heat-Transfer Coefficient,
W/m
2 -K
Pressure Drop, kPa
Hydrocarbon-Based Fluids
Figure 6. Heat-transfer correlations for hydrocarbons, 2.0 < NTU < 4.0.
Pressure Drop, psi
h = Local Heat-Transfer Coefficient,
Btu/h-ft
2 -
5 10 15 20 25 30
1,
800
600
400
200
0
100 Correction: For liquids with average viscosities less than 2.0 cP, reduce the local heat-transfer coefficient by 15% from 3.5 < NTU < 4.0.
50 150 200 5, 4, 3, 3,
2,
1,
800
1 cP
2.5 cP
5 cP 10 cP
100 cP h = Local Heat-Transfer Coefficient,
W/m
2 -K
Pressure Drop, kPa
Hydrocarbon-Based Fluids
Figure 7. Heat-transfer correlations for hydrocarbons, 4.0 < NTU < 5.0.
Pressure Drop, psi
h = Local Heat-Transfer Coefficient,
Btu/h-ft
2 -
5 10 15 20 25 30
1,
800
600
400
200
0
5, 4, 3, 3,
2,
1,
800
100
1 cP
2.5 cP
5 cP 10 cP 100 cP
50 150 200
h = Local Heat-Transfer Coefficient,
W/m
2 -K
Pressure Drop, kPa
Hydrocarbon-Based Fluids
The use of alternative heat ex- changer technologies can signifi- cantly reduce plant complexity by reducing the number of heat ex- changers through improved thermal contacting and multi-streaming. This adds to the savings associated with reduced size and weight and also has safety implications. The simpler the plant structure, the easi- er it is for the process operator to understand the plant. In addition, plant maintenance will be safer, easier and more straight-forward. Mechanical constraints play a significant role in the design of shell-and-tube heat exchangers. For instance, it is common to find that some users place restrictions on tube length. Such a restriction can have important implications for the design. In the case of exchangers requiring large surface areas, the restriction drives the design toward large tube counts. If such large tube counts lead to low tubeside veloci- ty, the designer is tempted to in- crease the number of tubeside pass- es in order to maintain a reasonable tubeside heat-transfer coefficient. Thermal expansion considerations can also lead the designer to opt for multiple tube passes, because the cost of a floating head is generally lower than the cost of installing an expan- sion bellows in the exchanger shell. The use of multiple tube passes has four detrimental effects. First, it leads to a reduction in the number of tubes that can be accommodated in a given size shell, thereby leading to increased shell diameter and cost. Second, for bundles having more than four tube passes, the pass-partition lanes introduced into the bundle give rise to an increase in the quantity of shellside fluid by- passing the tube bundle and a reduction in shellside heat-transfer coefficient. Third, it results in wasted tubeside pressure drop in the return headers. Finally, and most significantly, the use of multiple tube passes results in the thermal contacting of the streams not being pure counter-flow, which reduces the effective- mean-temperature driving force and possibly produces a temperature cross ( i.e., where the outlet temperature of the cold stream is higher than the inlet temperature of the hot stream, as shown in Figure 8). If a tempera- ture cross occurs, the designer must split the duty be- tween multiple heat exchangers arranged in series.
Figure 8. The situation on the left does not involve a temperature cross, while the one on the right does.
(^200) ˚ F
(^168) ˚ F
(^175) ˚ F
One shell-and-tube exchanger One plate exchanger
(^60) ˚ F
No Temperature Cross
(^200) ˚ F
(^171) ˚ F
Three shell-and-tube exchangers One plate exchanger
(^50) ˚ F
(^100) ˚ F
Temperature Cross
36 www.cepmagazine.org September 2002 CEP
Figure 9. A single plate-and-frame exchanger handles three process streams …
(^160) ˚F Styrene, 290,285 lb/h (^130) ˚F
(^248) ˚F ∆ P = 14.6 psi
Styrene, 290,285 lb/h (^285) ˚F
Styrene, 100˚F ∆ Ptotal = 30 psi
(^112) ˚F ∆ P = 9.5 psi
Water, 248,655 lb/h (^80) ˚F
(^160) ˚F
Figure 10. … whereas the equivalent shell-and-tube design requires six units.
Styrene (Hot)
Styrene (Cold)
Cooling Water