
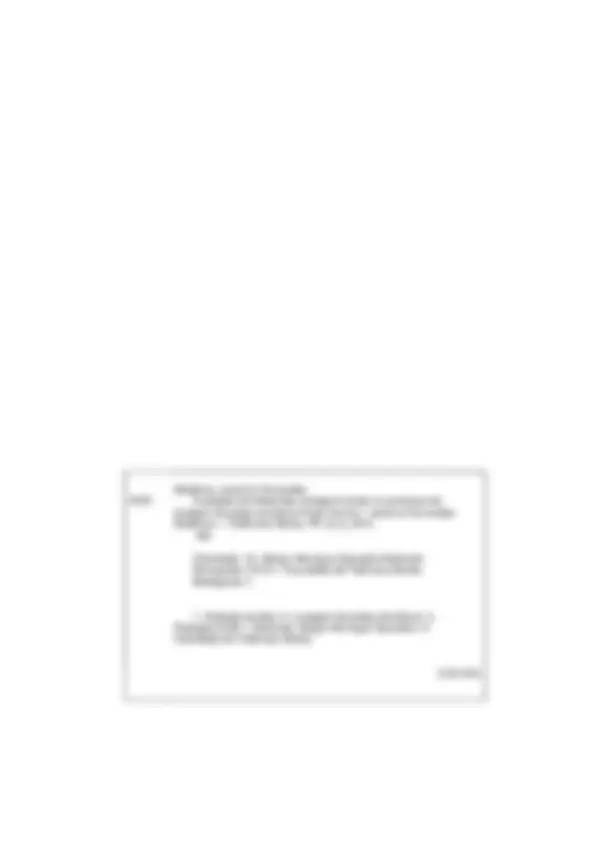
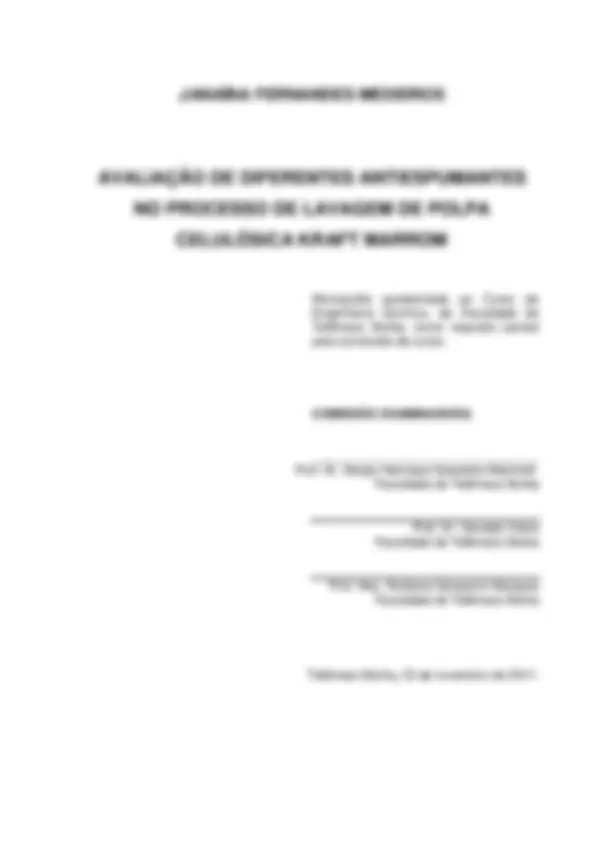
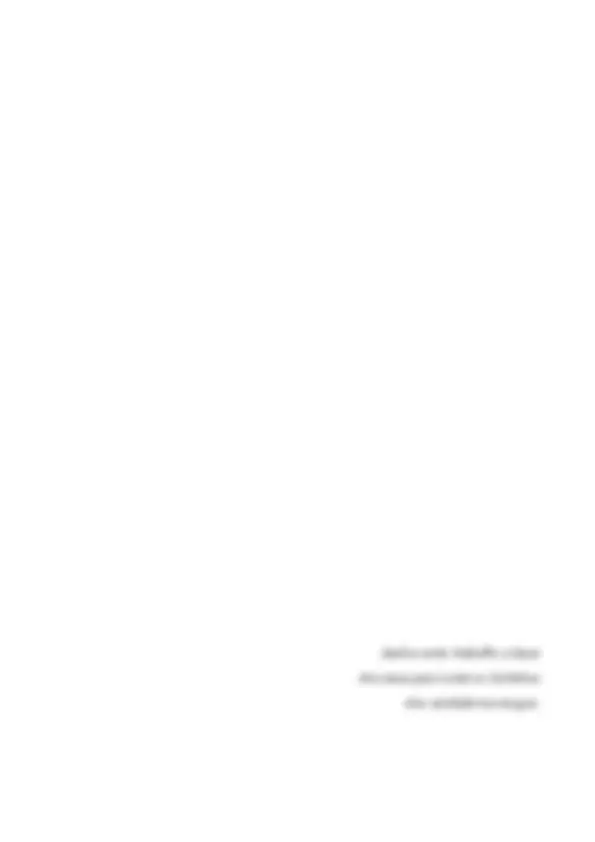
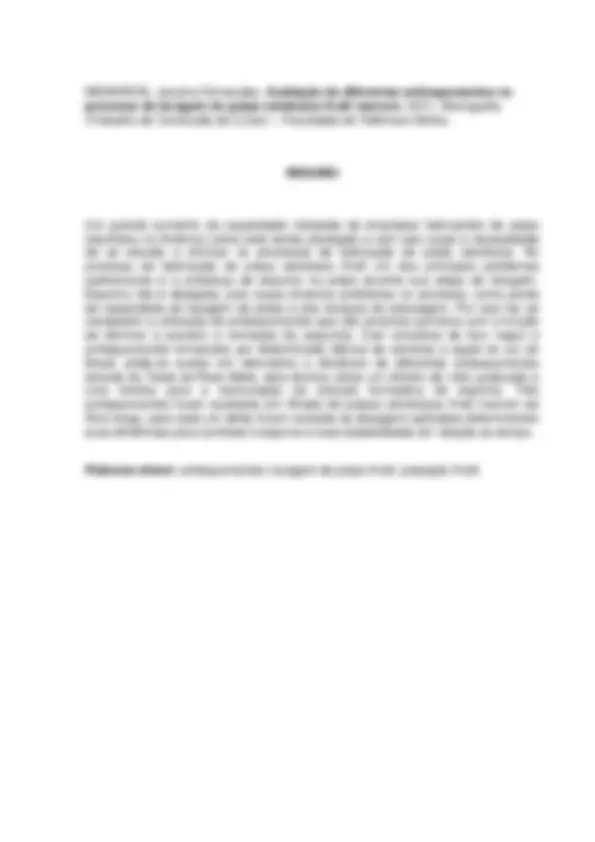
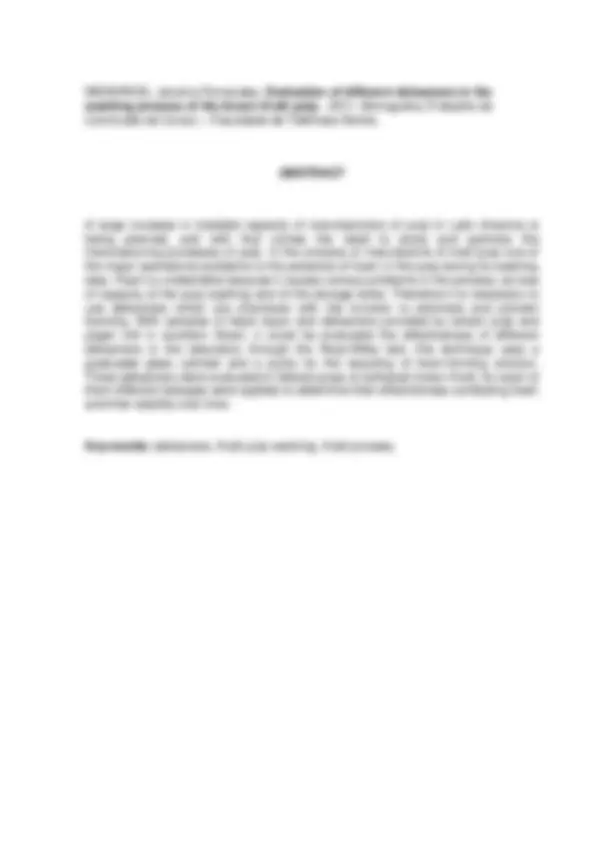
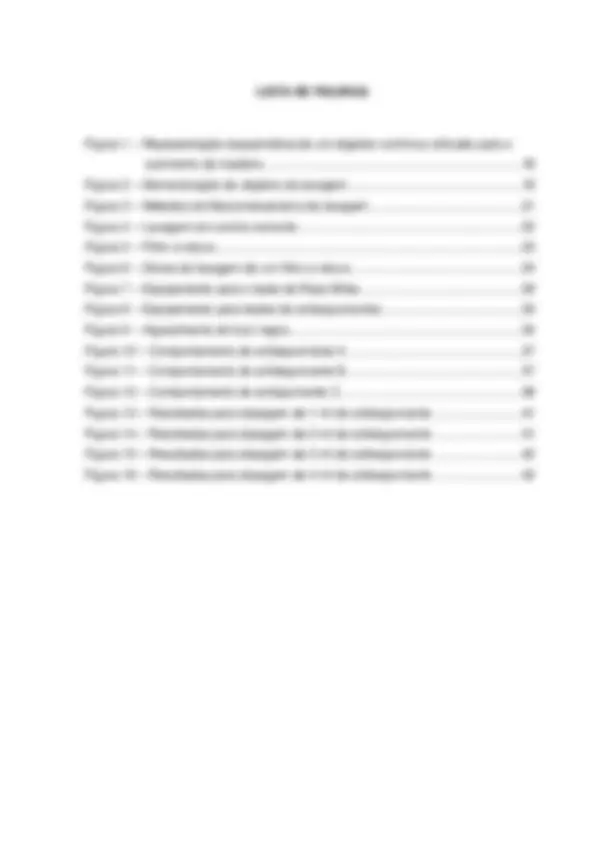
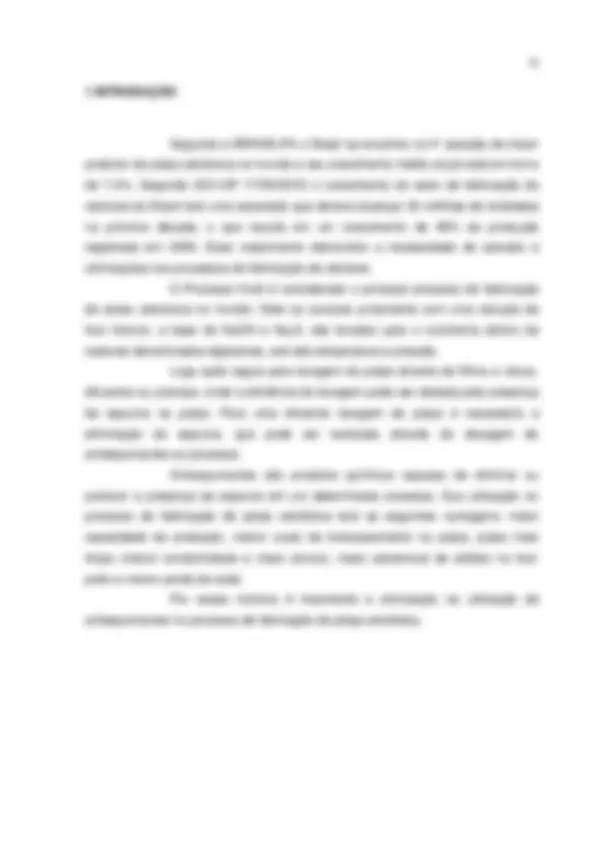
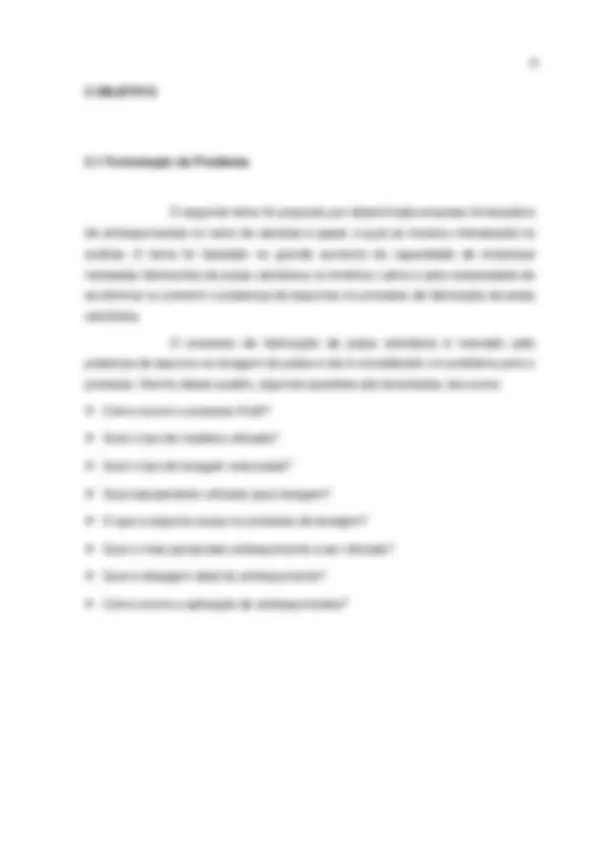
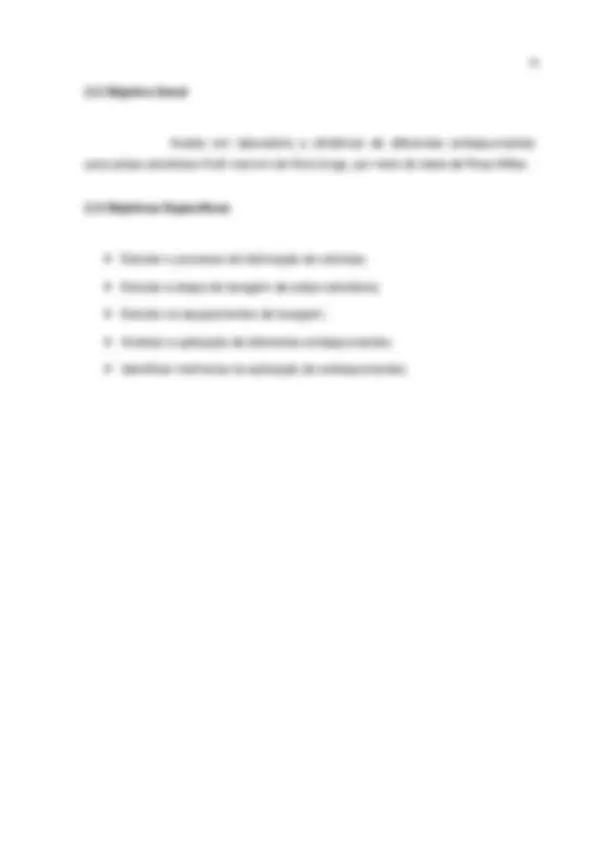
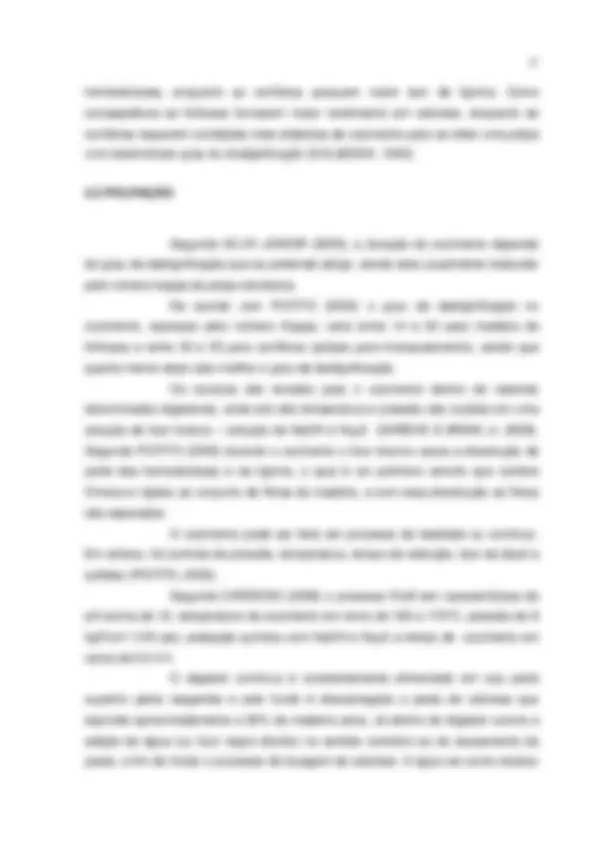
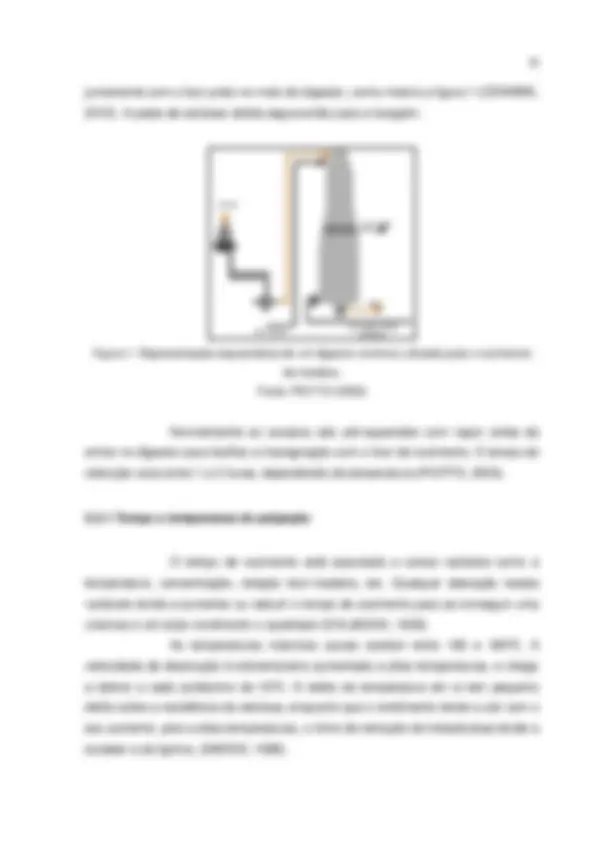
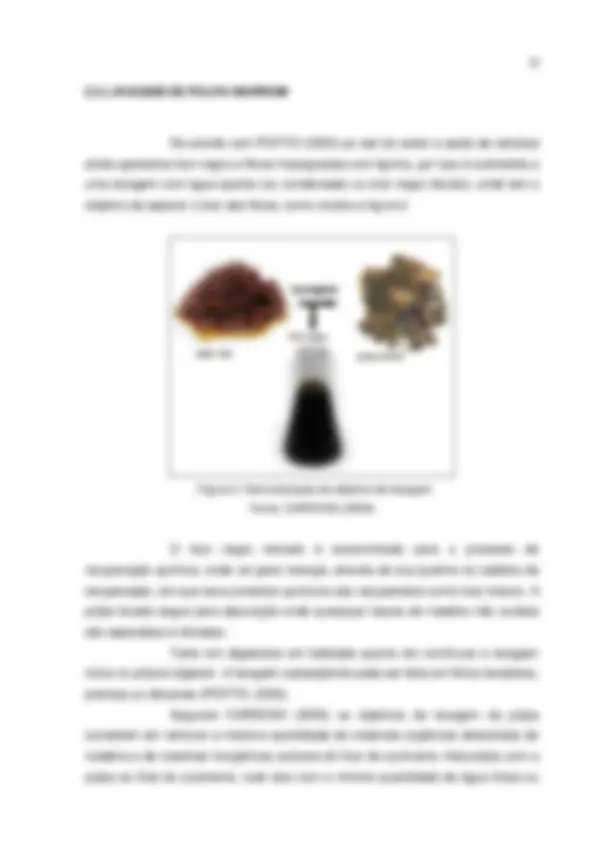
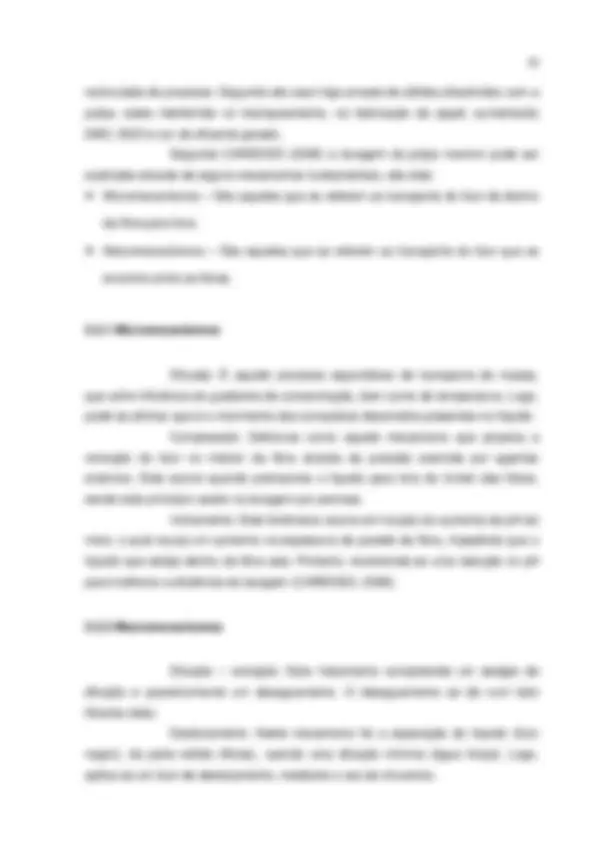
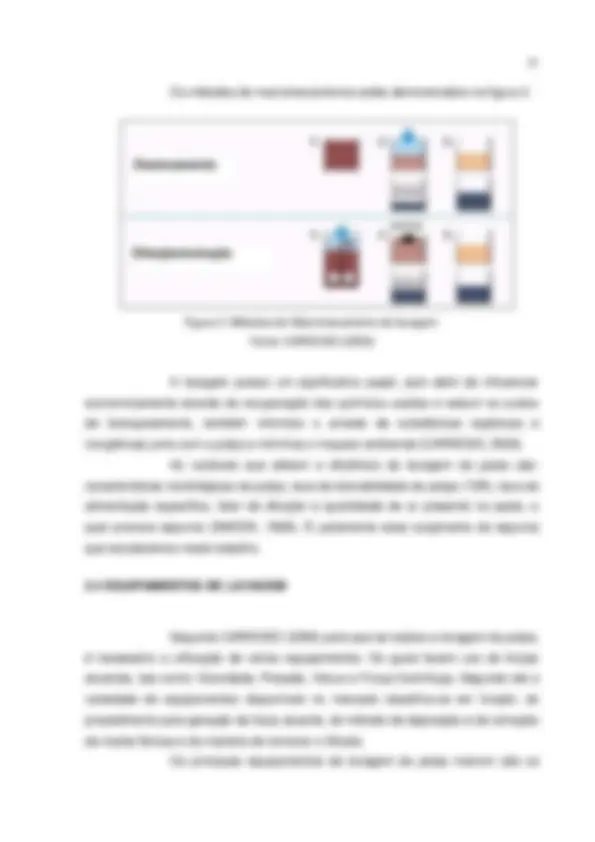
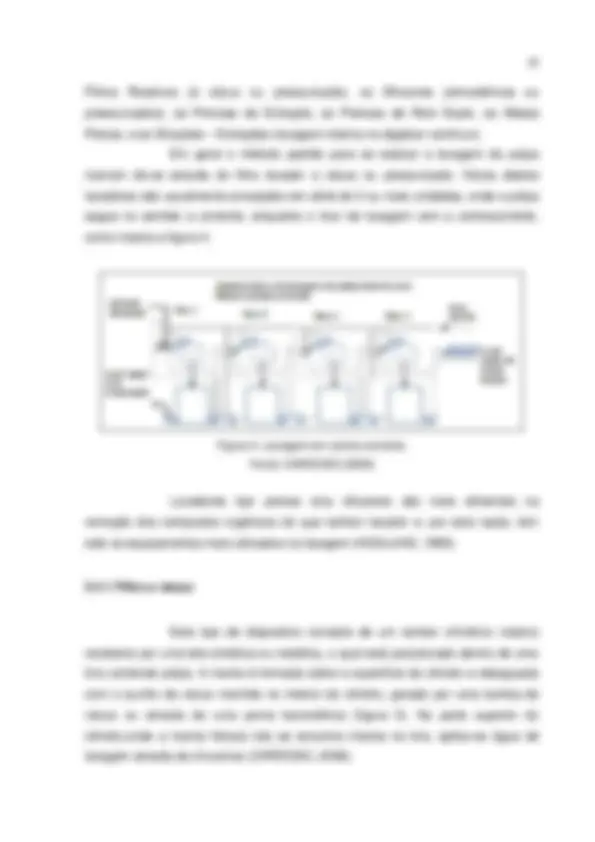
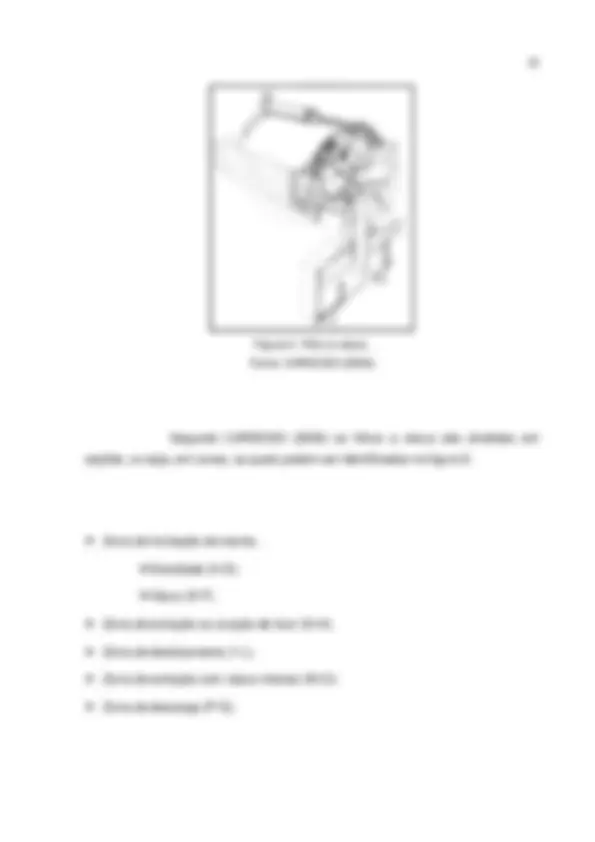
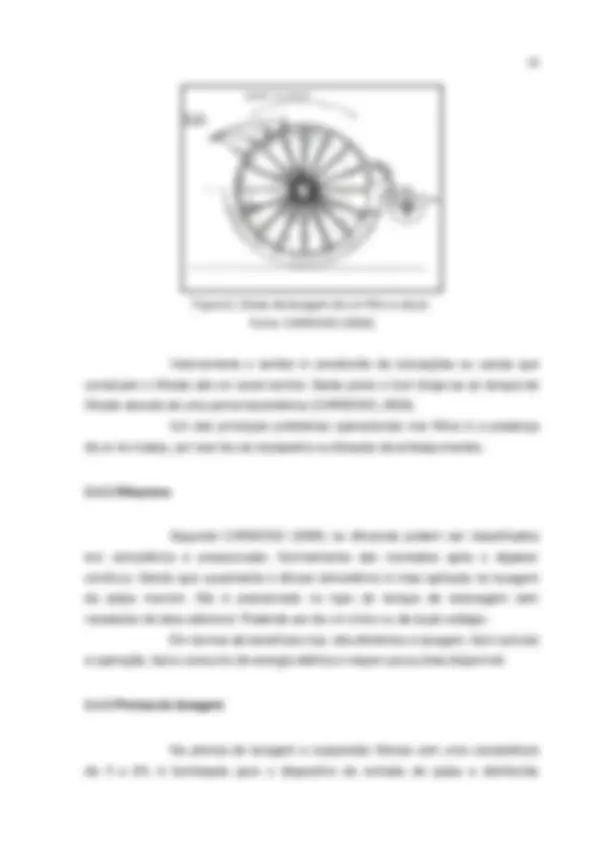
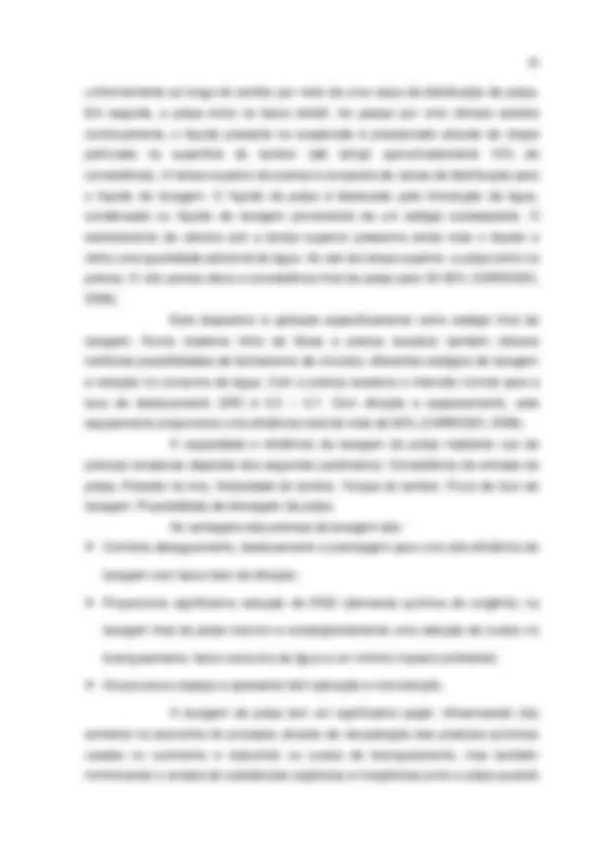
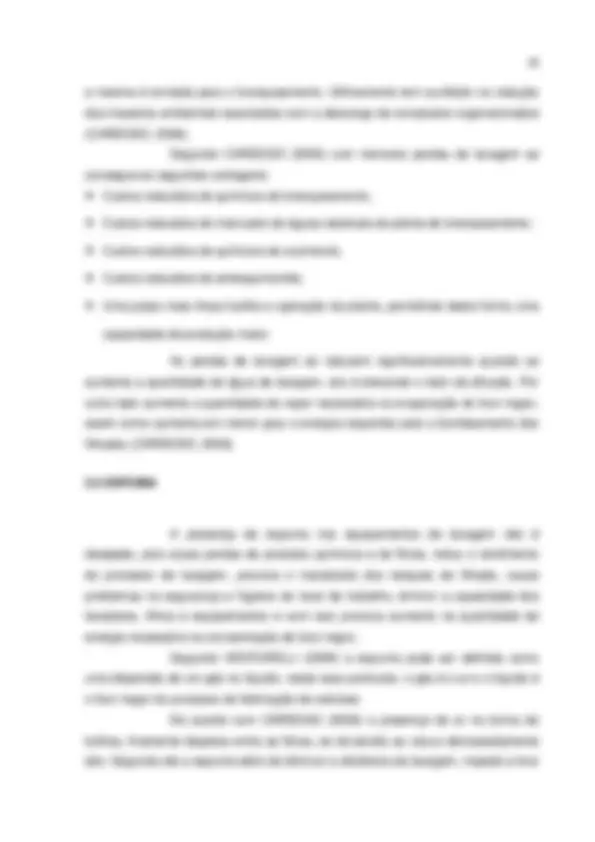
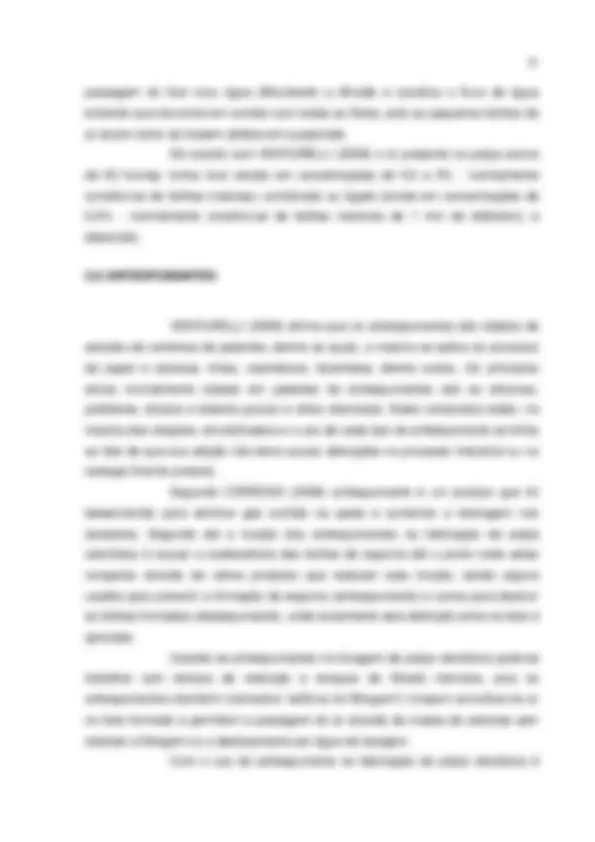
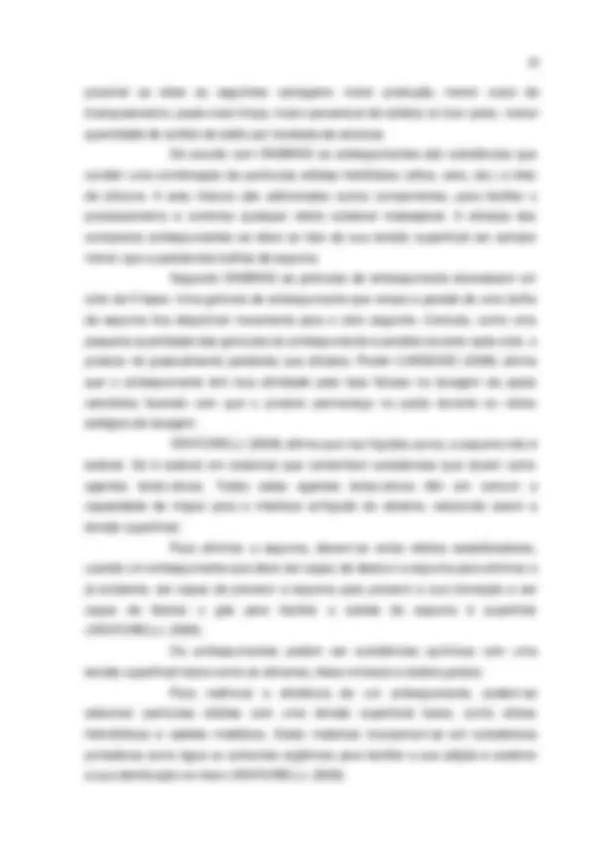
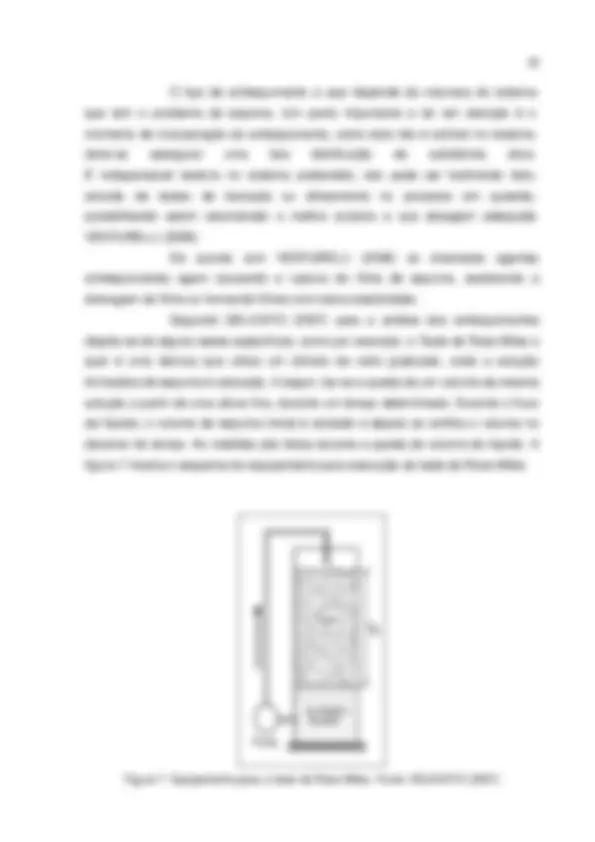
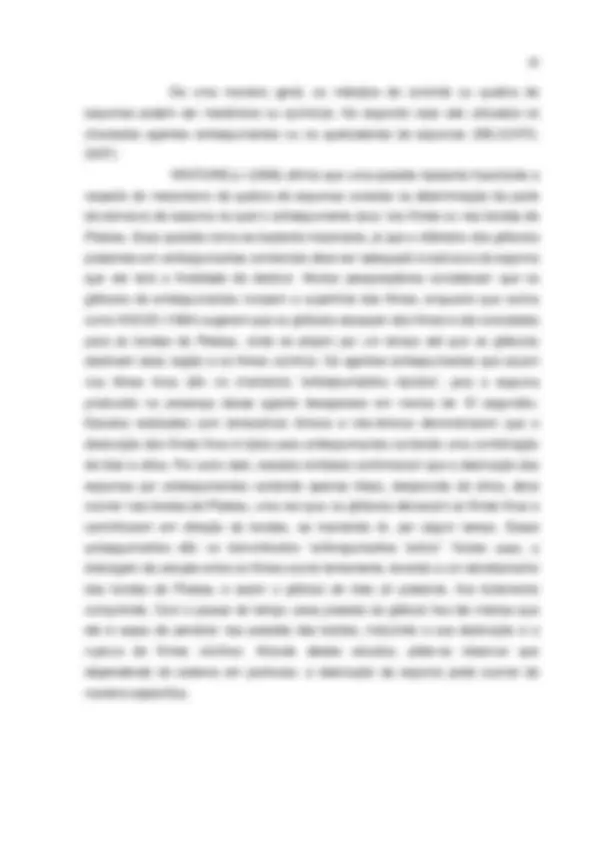
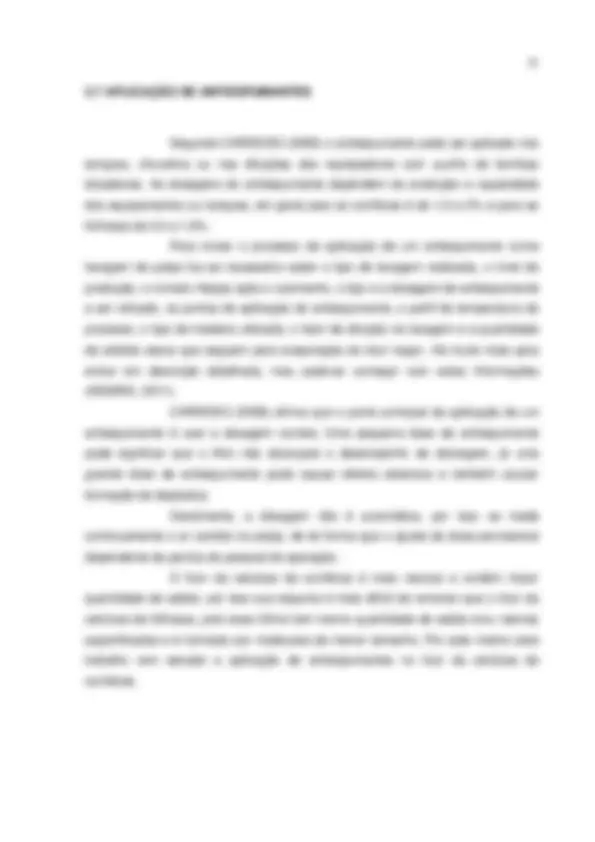
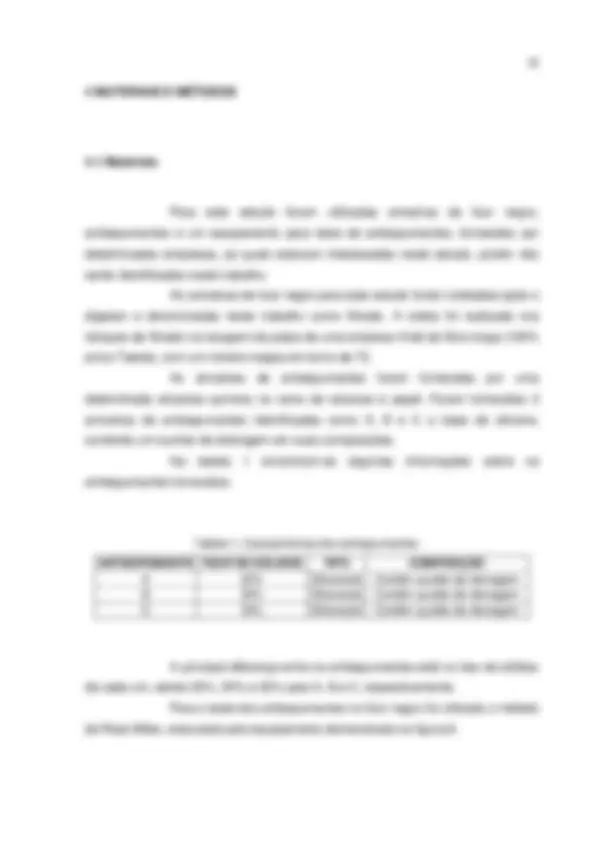
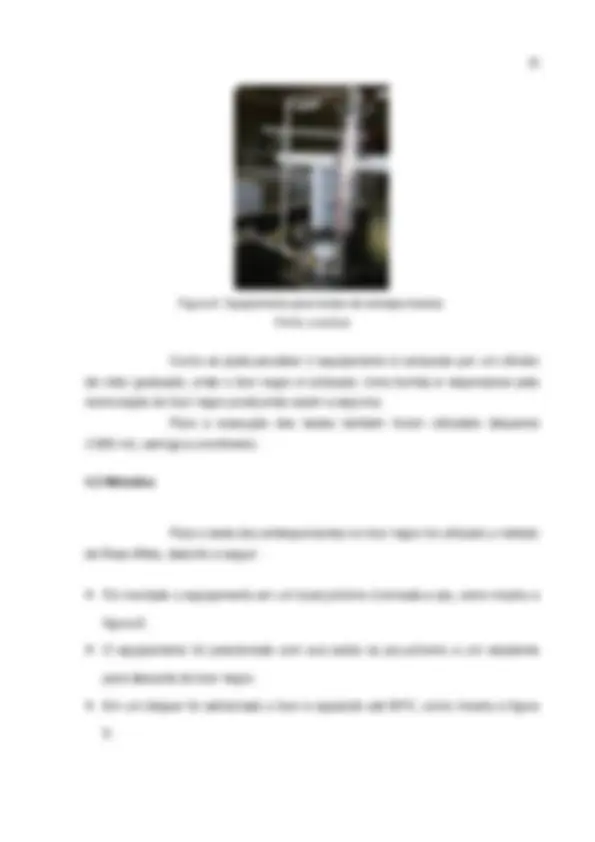
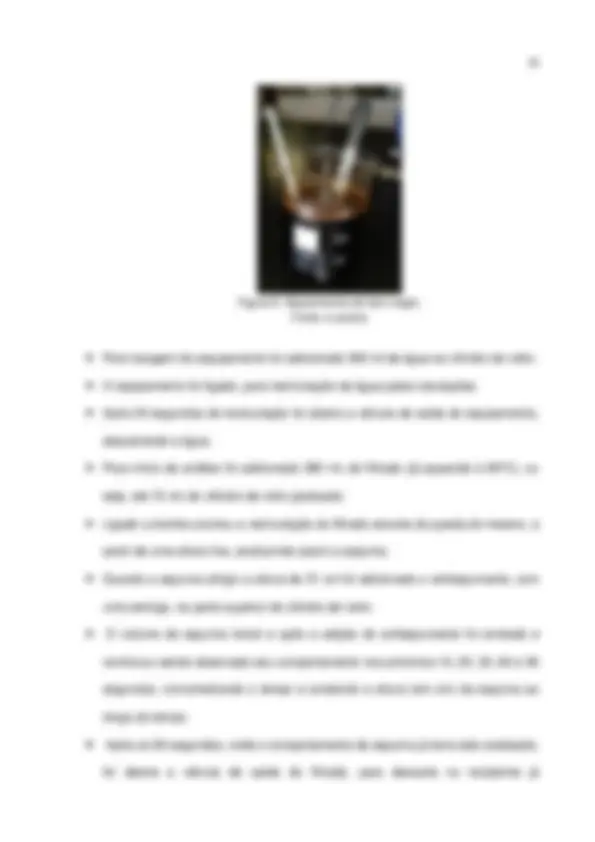
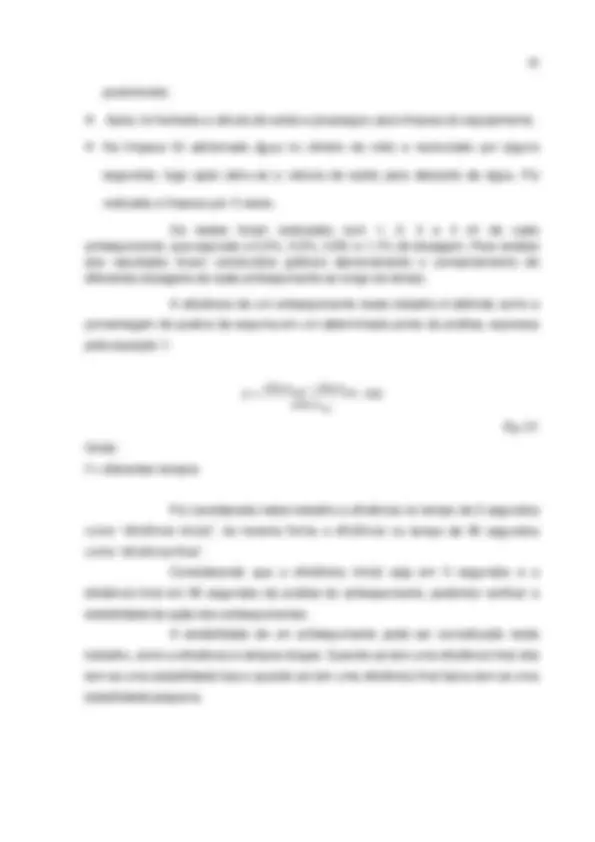
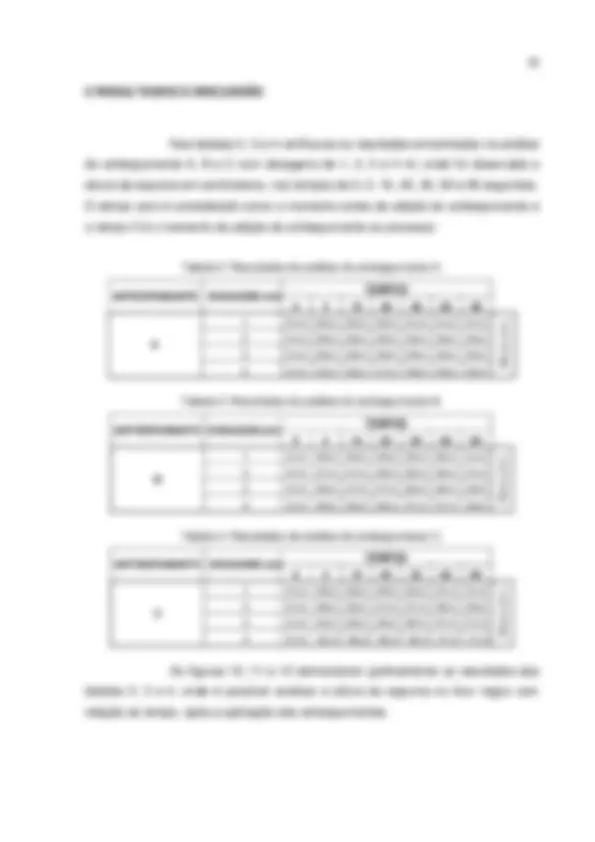
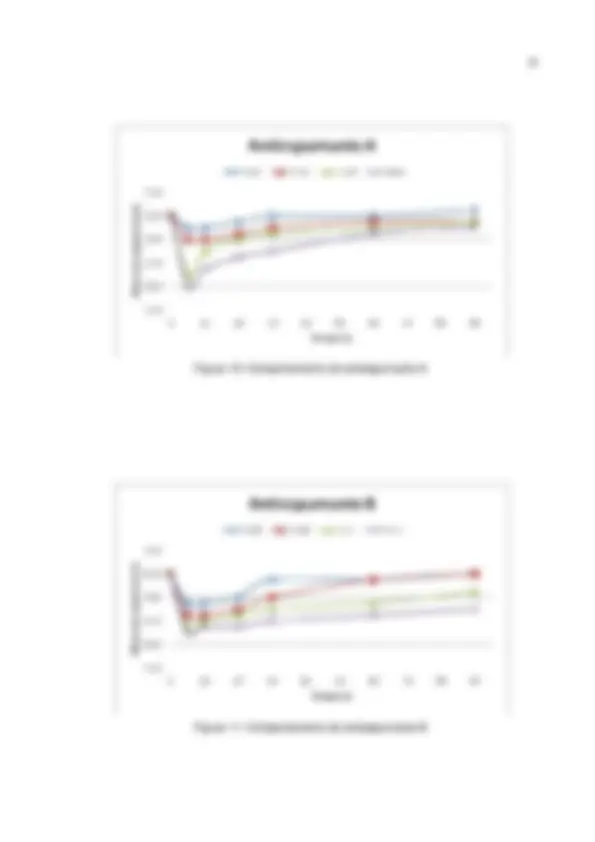
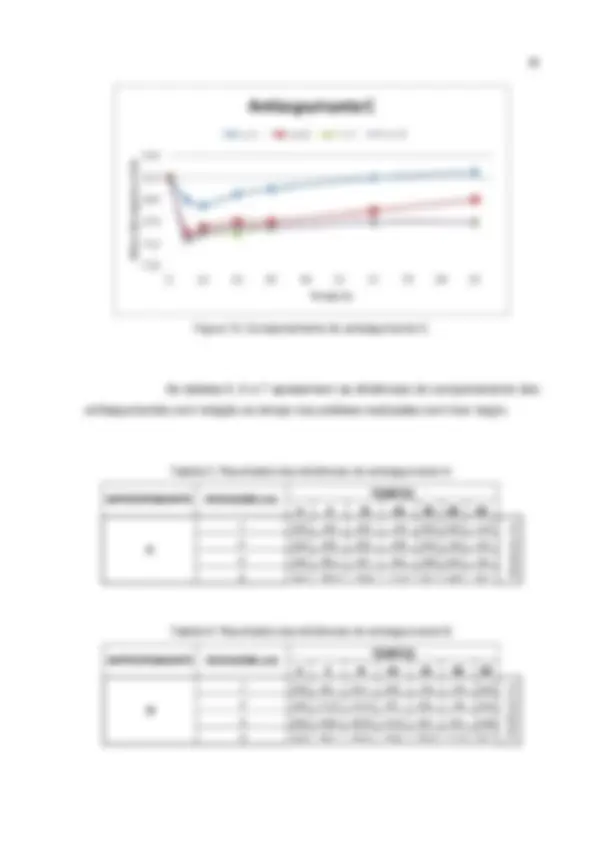
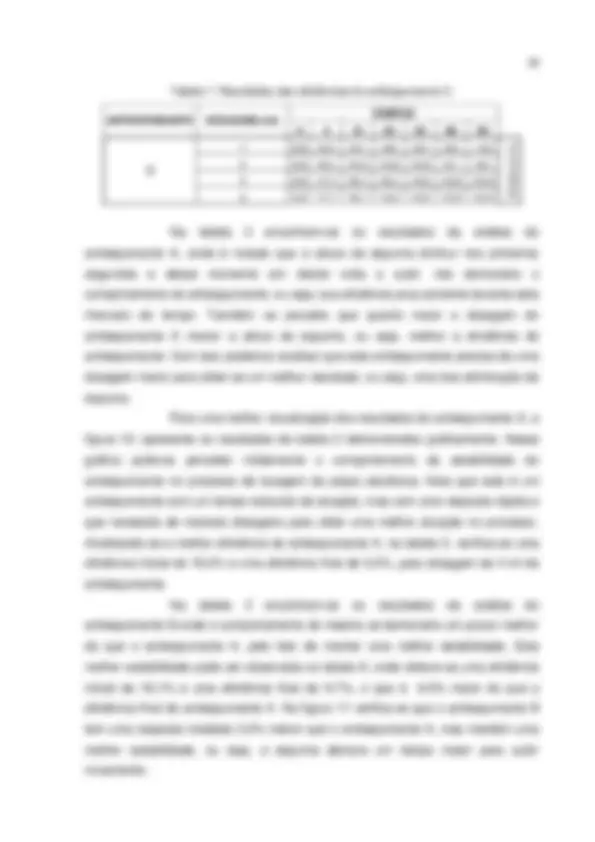
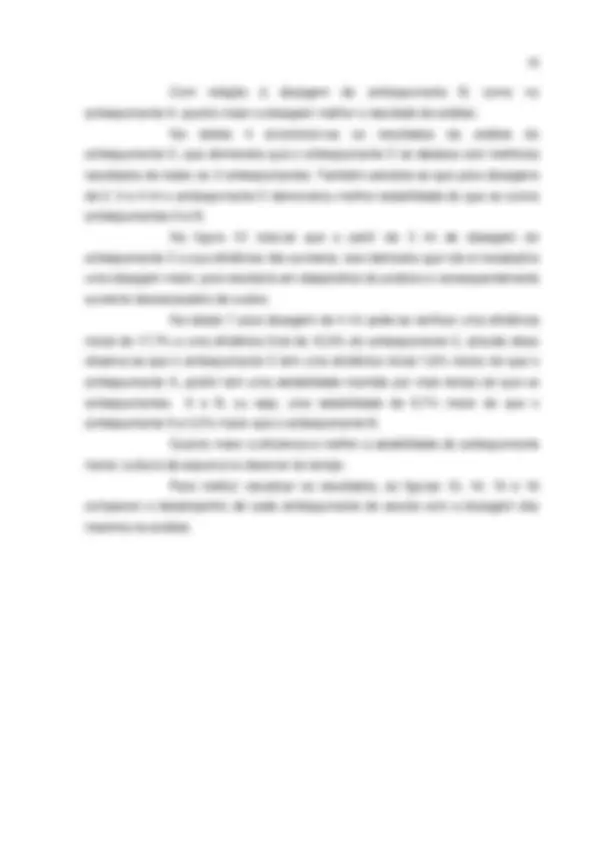
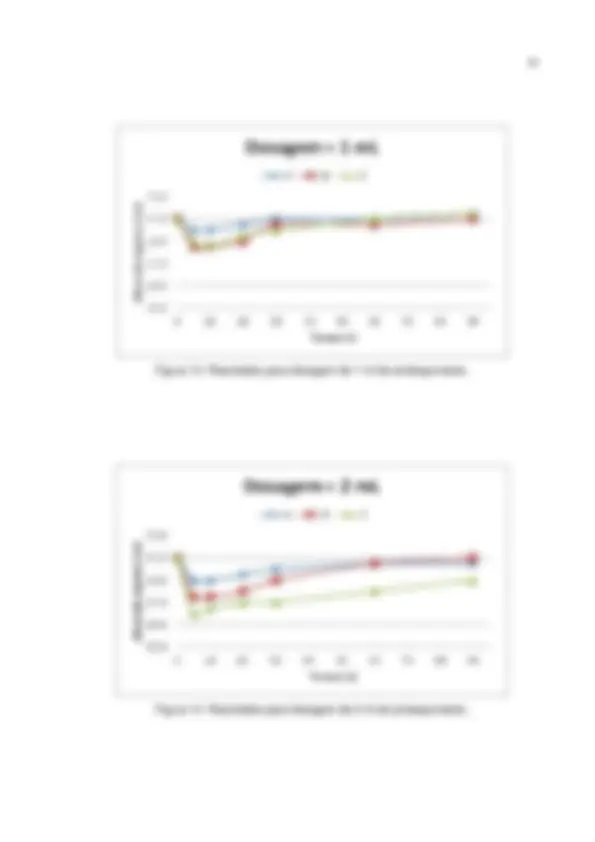
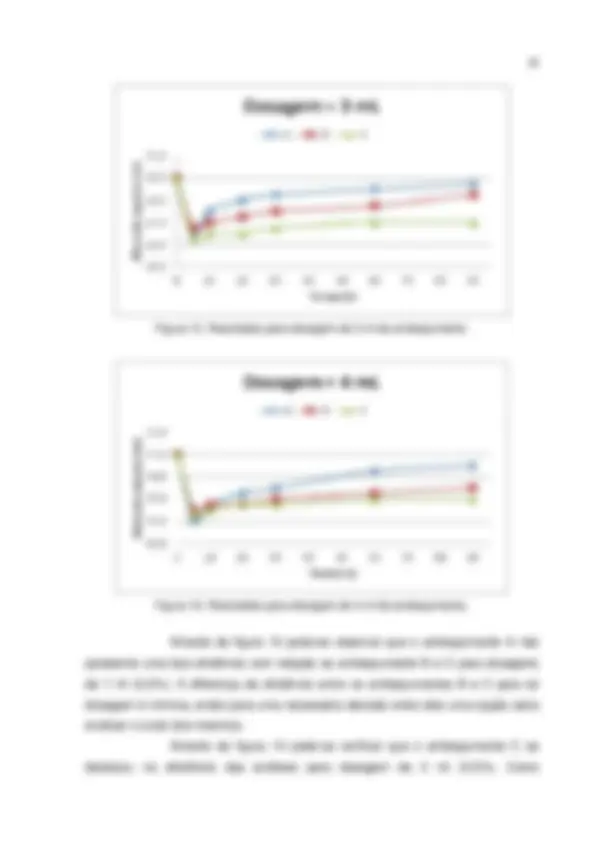
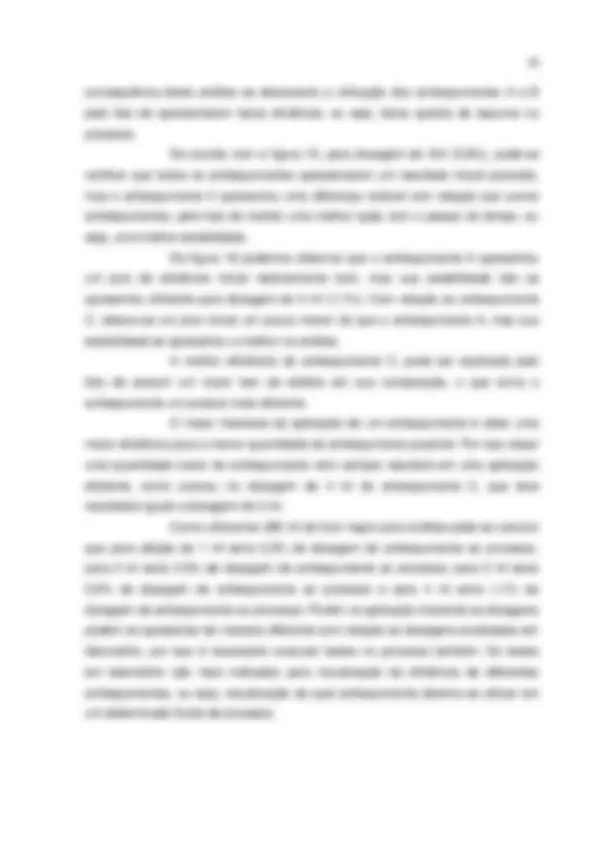
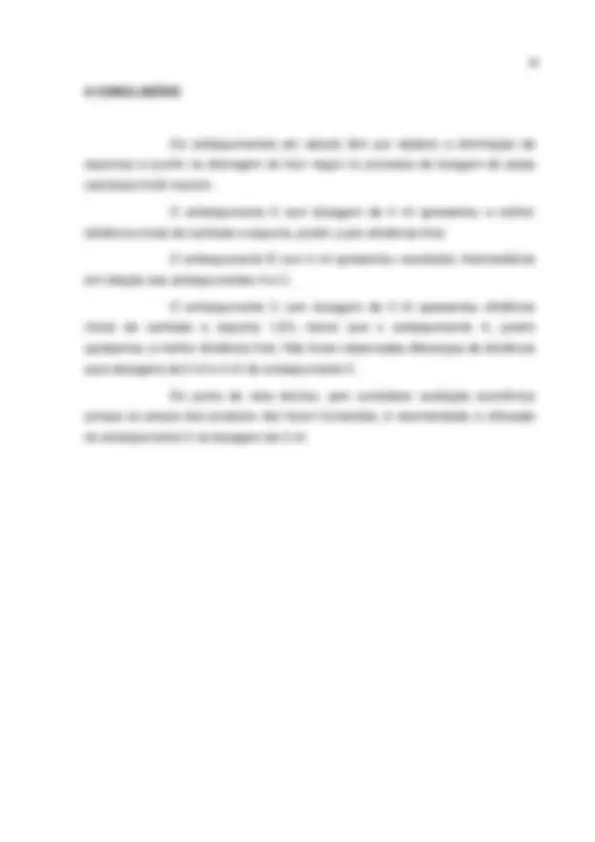
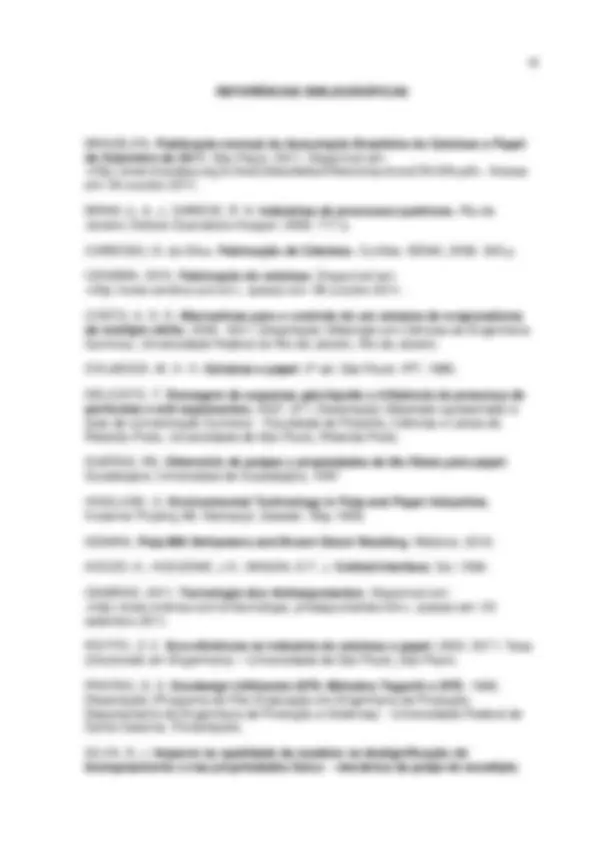
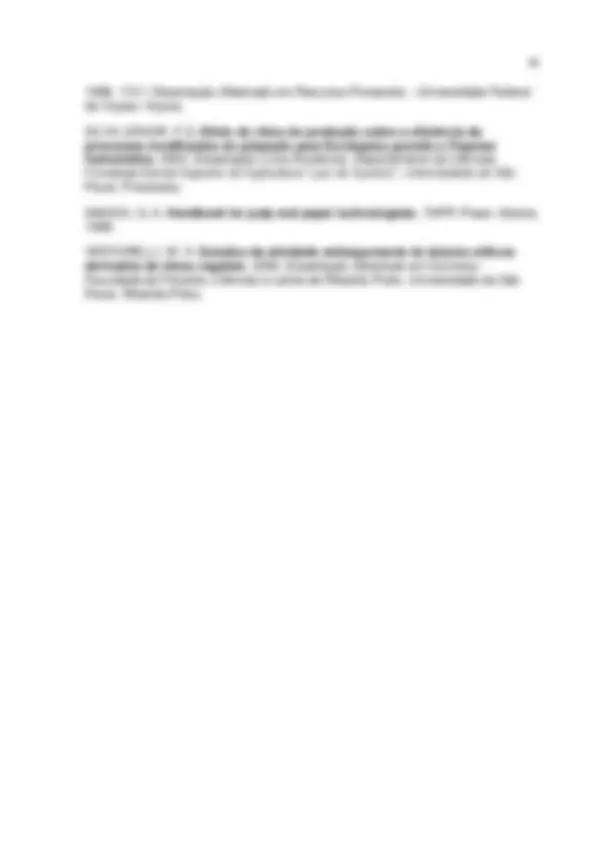
Estude fácil! Tem muito documento disponível na Docsity
Ganhe pontos ajudando outros esrudantes ou compre um plano Premium
Prepare-se para as provas
Estude fácil! Tem muito documento disponível na Docsity
Prepare-se para as provas com trabalhos de outros alunos como você, aqui na Docsity
Os melhores documentos à venda: Trabalhos de alunos formados
Prepare-se com as videoaulas e exercícios resolvidos criados a partir da grade da sua Universidade
Responda perguntas de provas passadas e avalie sua preparação.
Ganhe pontos para baixar
Ganhe pontos ajudando outros esrudantes ou compre um plano Premium
Comunidade
Peça ajuda à comunidade e tire suas dúvidas relacionadas ao estudo
Descubra as melhores universidades em seu país de acordo com os usuários da Docsity
Guias grátis
Baixe gratuitamente nossos guias de estudo, métodos para diminuir a ansiedade, dicas de TCC preparadas pelos professores da Docsity
Trabalho de conclusão de curso
Tipologia: Trabalhos
Oferta por tempo limitado
Compartilhado em 21/07/2015
4
(1)2 documentos
1 / 47
Esta página não é visível na pré-visualização
Não perca as partes importantes!
Em oferta
Monografia apresentada ao Curso de Engenharia Química, da Faculdade de Telêmaco Borba, como requisito parcial para conclusão de curso. Orientador: Prof. Dr. Sérgio Henrique Saavedra Martinelli Co-orientadora: Talita Mendes Dultra
Monografia apresentada ao Curso de Engenharia Química, da Faculdade de Telêmaco Borba, como requisito parcial para conclusão de curso.
Prof. Dr. Sérgio Henrique Saavedra Martinelli Faculdade de Telêmaco Borba
Prof. Dr. Osvaldo Vieira Faculdade de Telêmaco Borba
Prof. Msc. Rubiane Ganascim Marques Faculdade de Telêmaco Borba
Telêmaco Borba, 23 de novembro de 2011.
“É justamente a possibilidade de realizar um
sonho que torna a vida interessante.”
Paulo Coelho
MEDEIROS, Janaína Fernandes. Avaliação de diferentes antiespumantes no processo de lavagem de polpa celulósica Kraft marrom. 2011. Monografia (Trabalho de Conclusão de Curso) – Faculdade de Telêmaco Borba.
Um grande aumento da capacidade instalada de empresas fabricantes de polpa celulósica na América Latina está sendo planejado e com isso surge a necessidade de se estudar e otimizar os processos de fabricação de polpa celulósica. No processo de fabricação de polpa celulósica Kraft um dos principais problemas operacionais é a presença de espuma na polpa durante sua etapa de lavagem. Espuma não é desejada, pois causa diversos problemas no processo, como perda de capacidade de lavagem de polpa e dos tanques de estocagem. Por isso faz se necessário a utilização de antiespumantes que são produtos químicos com a função de eliminar e prevenir a formação de espumas. Com amostras de licor negro e antiespumantes fornecidos por determinada fábrica de celulose e papel do sul do Brasil, pôde-se avaliar em laboratório a eficiência de diferentes antiespumantes através do Teste de Ross-Miles, esta técnica utiliza um cilindro de vidro graduado e uma bomba para a recirculação da solução formadora de espuma. Três antiespumantes foram avaliados em filtrado de polpas celulósicas Kraft marrom de fibra longa, para cada um deles foram variadas as dosagens aplicadas determinando suas eficiências para combate à espuma e suas estabilidades em relação ao tempo.
Palavras-chave: antiespumantes; lavagem de polpa Kraft; polpação Kraft.
12
1 INTRODUÇÃO
Segundo a BRACELPA o Brasil se encontra na 4° posição de maior produtor de polpa celulosica no mundo e seu crescimento médio anual está em torno de 7,4%. Segundo (DCI-SP 17/09/2010) o crescimento do setor de fabricação de celulose do Brasil terá uma expansão que deverá alcançar 20 milhões de toneladas na próxima década, o que resulta em um crescimento de 48% da produção registrada em 2009. Esse crescimento demonstra a necessidade de estudos e otimizações nos processos de fabricação de celulose. O Processo Kraft é considerado o principal processo de fabricação de polpa celulosica no mundo. Nele os cavacos juntamente com uma solução de licor branco, a base de NaOH e Na 2 S, são levados para o cozimento dentro de reatores denominados digestores, sob alta temperatura e pressão. Logo após segue para lavagem da polpa através de filtros a vácuo, difusores ou prensas, onde a eficiência da lavagem pode ser afetada pela presença de espuma na polpa. Para uma eficiente lavagem de polpa é necessário a eliminação da espuma, que pode ser realizada através da dosagem de antiespumantes ao processo. Antiespumantes são produtos químicos capazes de eliminar ou prevenir a presença de espuma em um determinado processo. Sua utilização no processo de fabricação de polpa celulósica terá as seguintes vantagens: maior capacidade de produção, menor custo de branqueamento na polpa, polpa mais limpa (menor condutividade e maior alvura), maior percentual de sólidos no licor preto e menor perda de soda. Por esses motivos é importante a otimização na utilização de antiespumantes no processo de fabricação de polpa celulósica.
13
2 OBJETIVO
2.1 Formulação do Problema
O seguinte tema foi proposto por determinada empresa fornecedora de antiespumantes no ramo de celulose e papel, a qual se mostrou interessada na análise. O tema foi baseado no grande aumento da capacidade de empresas instaladas fabricantes de polpa celulósica na América Latina e pela necessidade de se eliminar ou prevenir a presença de espumas no processo de fabricação de polpa celulósica.
O processo de fabricação de polpa celulósica é marcado pela presença de espuma na lavagem da polpa e isto é considerado um problema para o processo. Dentro desse quadro, algumas questões são levantadas, tais como:
Como ocorre o processo Kraft?
Qual o tipo de madeira utilizada?
Qual o tipo de lavagem executada?
Qual equipamento utilizado para lavagem?
O que a espuma causa no processo de lavagem?
Qual o mais apropriado antiespumante a ser utilizado?
Qual a dosagem ideal do antiespumante?
Como ocorre a aplicação de antiespumantes?
15
Segundo CARDOSO (2006) o processo Kraft de polpação foi desenvolvido em 1879 por Carl Ferdinand Dahl e tornou-se o principal processo de produção de polpa no mundo. Desde então vários desenvolvimentos e modificações vêm sendo implementadas de forma a melhorar sua eficiência em termos de rendimento e de propriedades da polpa obtida. A palavra Kraft é de origem sueca e alemã que significa resistente. Por isso PIOTTO (2003) afirma que o processo Kraft é o mais empregado para a produção de papéis cuja resistência é o principal fator. COSTA (2000) verificou que um dos motivos para a produção de celulose pelo método Kraft ser o dominante no Brasil e no mundo seja pelo fato de gerar poucos resíduos, além de que o licor negro, principal subproduto do processo, pode ser totalmente reaproveitado, o que torna este processo ecologicamente correto. PIOTTO (2003) descreve o processo Kraft como um processo químico que visa dissolver a lignina, preservando a resistência das fibras, obtendo- se dessa maneira uma pasta forte, com rendimento entre 50 a 60%. Também afirma que cerca de 80% da polpa é produzida utilizando este processo, o qual é conhecido como processo “sulfato” devido as reposições das perdas serem feitas com Sulfato de Sódio. Segundo PRATES (1998) o processo Kraft ocorre da seguinte maneira: a madeira é alimentada ao picador , através de um transportador, onde as toras são transformadas em cavacos, os quais passam pela peneira para separar a fração aceitável dos rejeitos. Os rejeitos passam pelo repicador e voltam para a peneira. Os cavacos são levados do silo de cavacos para vasos de pressão, denominados digestores onde recebem a ação química do licor branco (solução de NaOH e Na 2 S) onde, com auxílio da pressão e temperatura do vapor, os cavacos são cozidos durante um certo tempo. SMOOK (1989) afirma que, para digestores que drenam em modo
16
batelada, após o período de cozimento, uma válvula no fundo do digestor é aberta e a pressão empurra os cavacos cozidos para um tanque (Blow Tank) onde, sob a força de alívio na descarga, os cavacos desdobram-se em fibras individualizadas, formando a pasta ou polpa. A massa do Blow Tank é bombeada para o sistema de depuração para a separação dos nós e cavacos não cozidos, os quais retornam para o digestor. A massa depurada segue então para a lavagem, onde a polpa é lavada com água e/ou licor fraco. O líquido extraído na lavagem (licor negro) é bombeado para o sistema de evaporação onde é concentrado e posteriormente queimado na caldeira de recuperação. Os produtos químicos (fundidos) obtidos na queima do licor são então conduzidos para a caustificação onde são recuperados na forma de licor branco, para re-utilização no cozimento. A celulose obtida segue para o sistema de branqueamento, para o sistema de secagem ou então para a máquina de papel. PRATES (1998) salienta que existem outros processos e diferentes seqüências para a produção de celulose, porém as operações básicas não divergem das operações mencionadas. CARDOSO (2006) afirma que as vantagens do processo Kraft estão na grande flexibilidade com relação às espécies de madeira utilizada, nos tempos de cozimentos curtos se compararmos com o processo sulfito, na capacidade de não ter tantos problemas com resina (pitch), na produção de polpa com alta resistência, na produção de valiosos subprodutos como tall-oil e terebentina e na fácil recuperação do licor utilizado. E as desvantagens estão nos altos custos de capital, na necessidade de grandes investimentos, na produção de polpas mais escuras e de ter um branqueamento mais difícil. A madeira, segundo DUEÑAS (1997), é o material lignocelulósico mais utilizado na obtenção de fibras para fabricação do papel. SILVA (1996) afirma que as matérias-primas tradicionais utilizadas como fontes de fibra para produção de polpa celulósica são oriundas de espécies de coníferas e de folhosas. PIOTTO (2003) verificou que alguns tipos de madeira como pinho, araucária, abeto etc, possuem fibras longas (3 a 5 mm) e são denominadas coníferas ou softwood (madeira macia), enquanto que as de eucalipto, álamo, carvalho, gmelina etc, possuem fibras mais curtas e finas (0,8 a 1,2 mm) e são conhecidas por folhosas ou hardwood (madeira dura). Geralmente as folhosas contêm maior porcentagem de celulose e
18
juntamente com o licor preto no meio do digestor, como mostra a figura 1 (CENIBRA, 2010). A pasta de celulose obtida segue então para a lavagem.
Figura 1. Representação esquemática de um digestor contínuo utilizado para o cozimento da madeira. Fonte: PIOTTO (2003)
Normalmente os cavacos são pré-aquecidos com vapor antes de entrar no digestor para facilitar a impregnação com o licor de cozimento. O tempo de retenção varia entre 1 a 2 horas, dependendo da temperatura (PIOTTO, 2003).
3.2.1 Tempo e temperatura de polpação
O tempo de cozimento está associado a outras variáveis como a temperatura, concentração, relação licor-madeira, etc. Qualquer alteração nestas variáveis tende a aumentar ou reduzir o tempo de cozimento para se conseguir uma celulose a um dado rendimento e qualidade (D’ALMEIDA, 1988). As temperaturas máximas usuais oscilam entre 160 e 180ºC. A velocidade de dissolução é sobremaneira aumentada a altas temperaturas, e chega a dobrar a cada acréscimo de 10ºC. O efeito da temperatura em si tem pequeno efeito sobre a resistência da celulose, enquanto que o rendimento tende a cair com o seu aumento, pois a altas temperaturas, o ritmo de remoção da holocelulose tende a exceder a da lignina, (SMOOK, 1989).
19
3.3 LAVAGEM DE POLPA MARROM
De acordo com PIOTTO (2003) ao sair do reator a pasta de celulose ainda apresenta licor negro e fibras impregnadas com lignina, por isso é submetida a uma lavagem com água quente (ou condensado ou licor negro diluído), onde tem o objetivo de separar o licor das fibras, como mostra a figura 2.
. Figura 2. Demonstração do objetivo da lavagem Fonte: CARDOSO (2006)
O licor negro retirado é encaminhado para o processo de recuperação química, onde vai gerar energia, através da sua queima na caldeira de recuperação, em que seus produtos químicos são recuperados como licor branco. A polpa lavada segue para depuração onde quaisquer lascas de madeira não cozidas são separadas e retiradas. Tanto em digestores em batelada quanto em contínuos a lavagem inicia no próprio digestor. A lavagem subseqüente pode ser feita em filtros lavadores, prensas ou difusores (PIOTTO, 2003). Segundo CARDOSO (2006) os objetivos da lavagem da polpa consistem em remover a máxima quantidade de materiais orgânicos dissolvidos da madeira e de materiais inorgânicos solúveis do licor de cozimento misturados com a polpa ao final do cozimento, tudo isso com a mínima quantidade de água limpa ou