
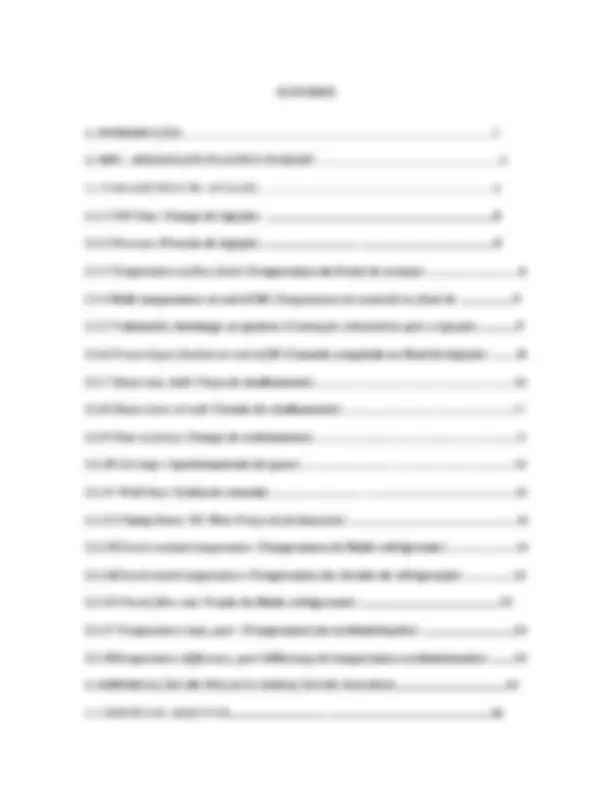
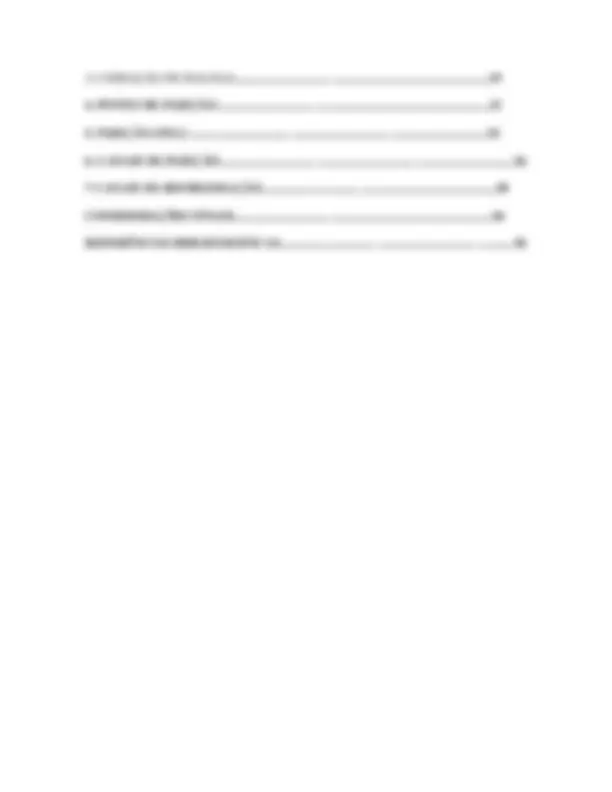
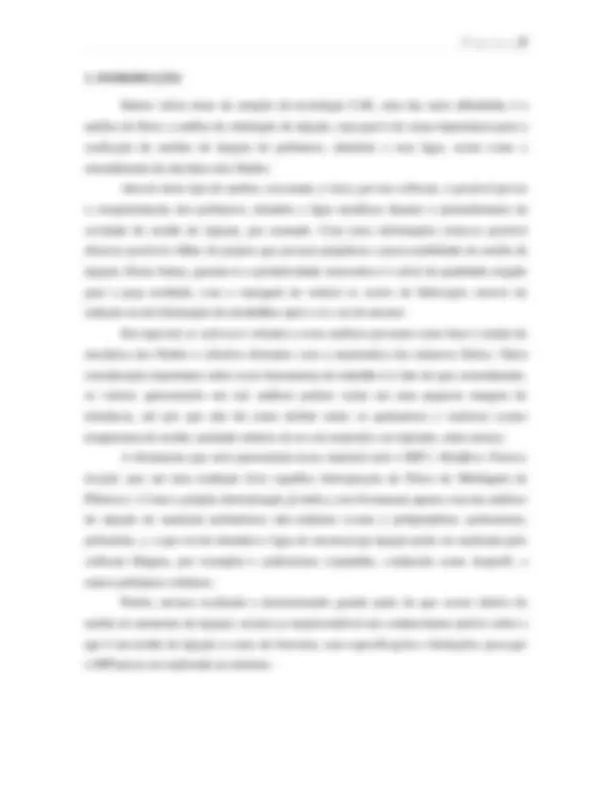
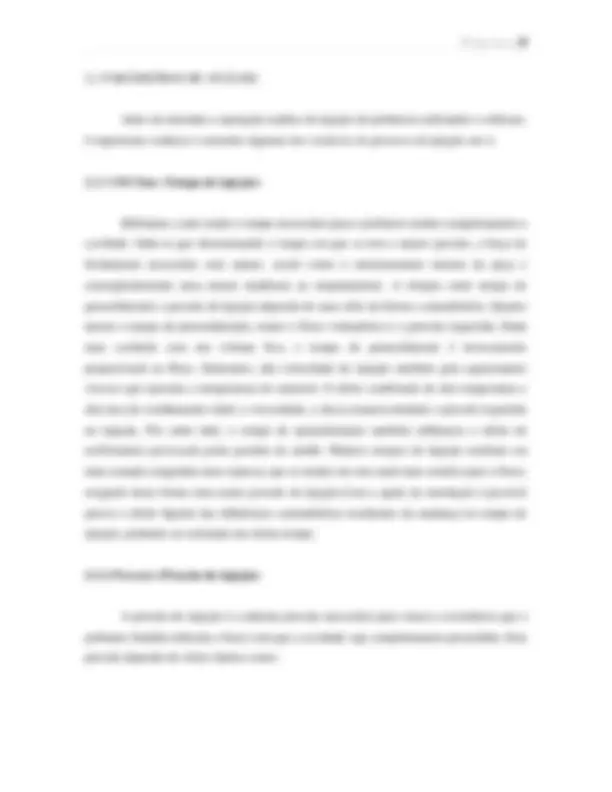
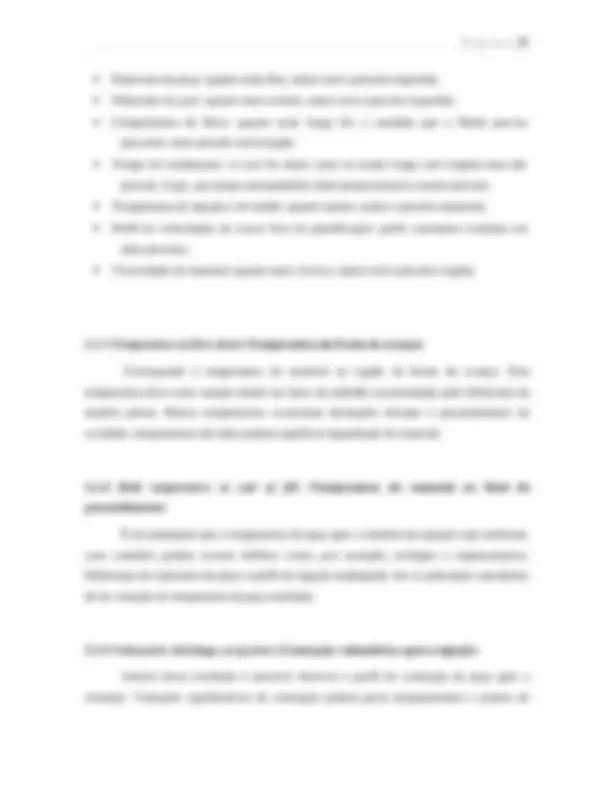
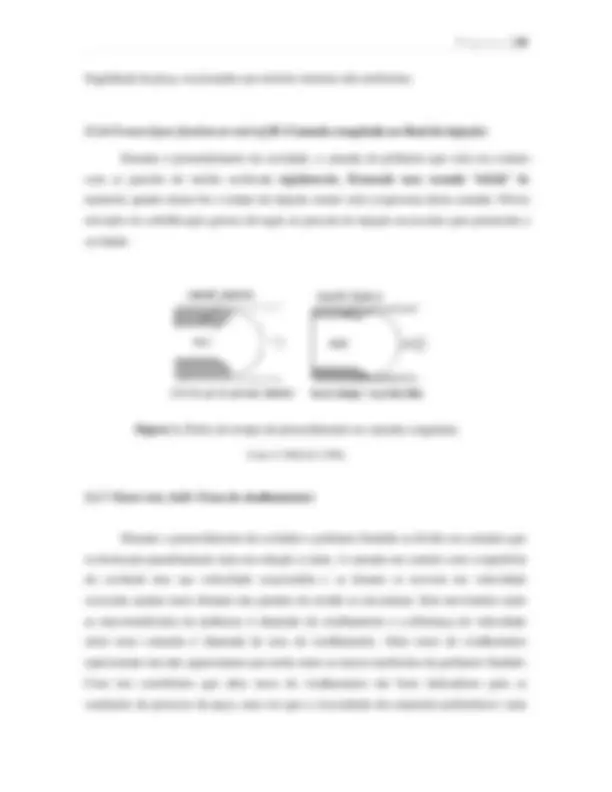
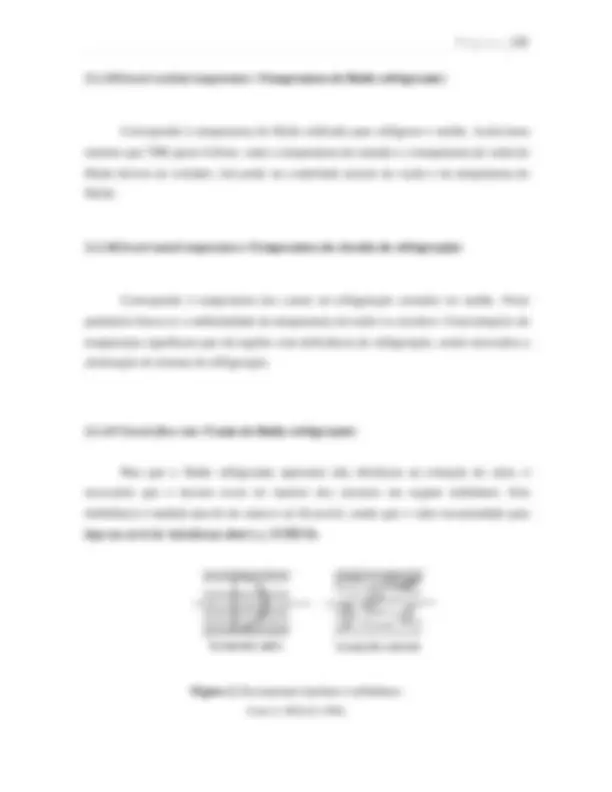
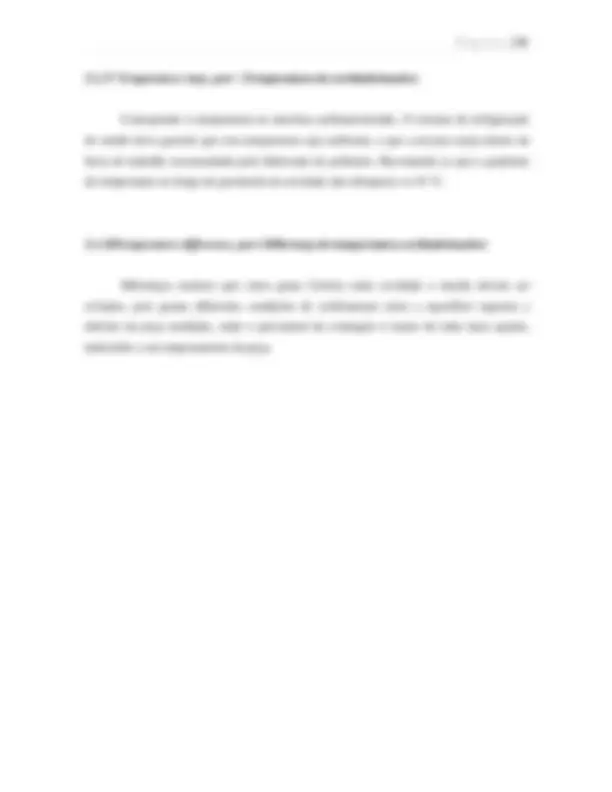
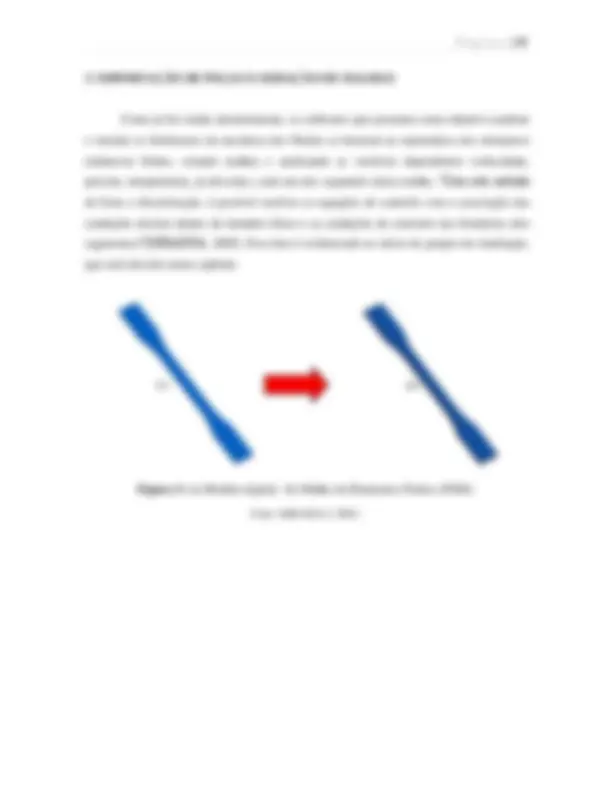
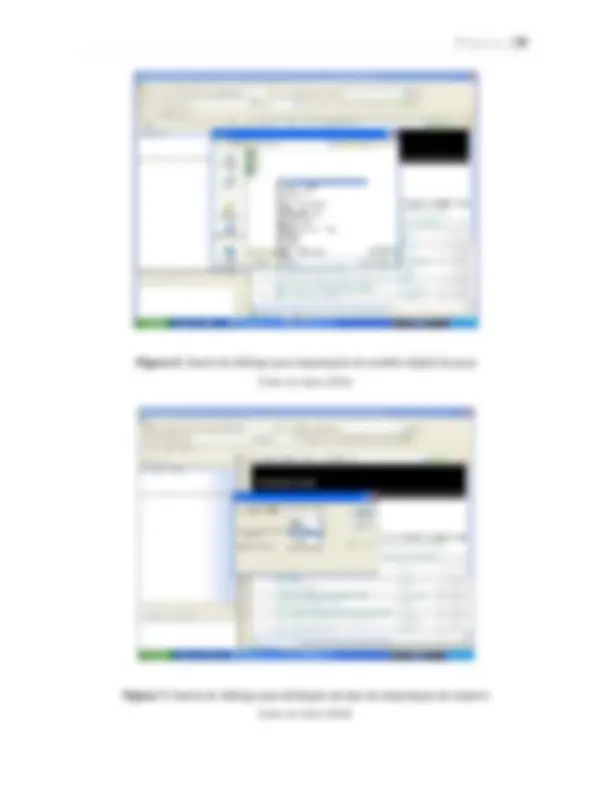
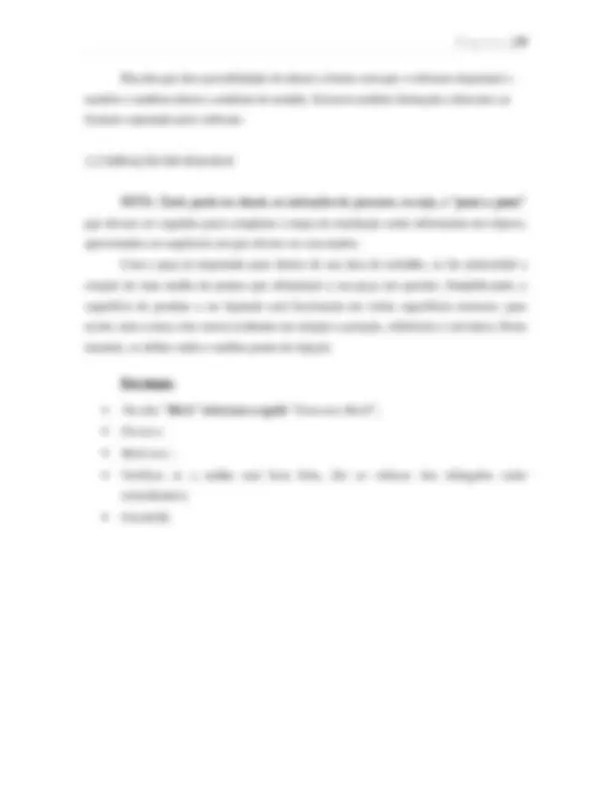
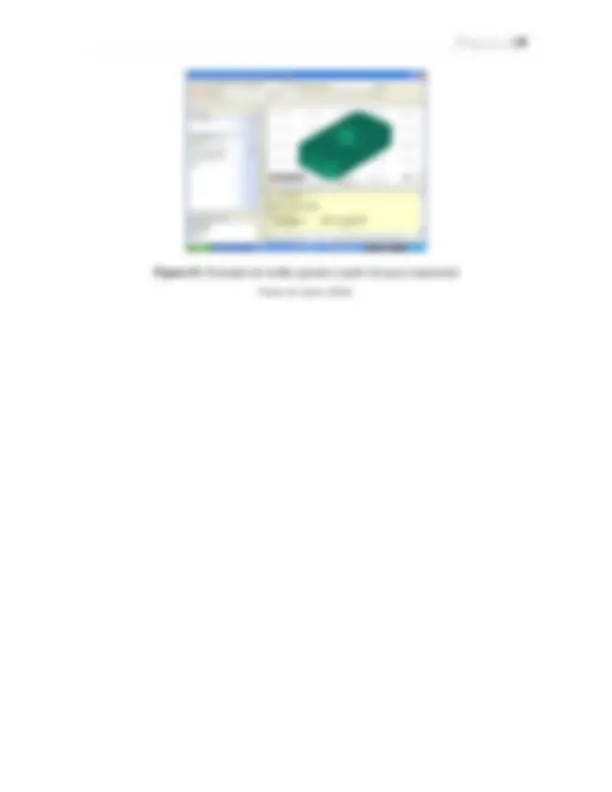
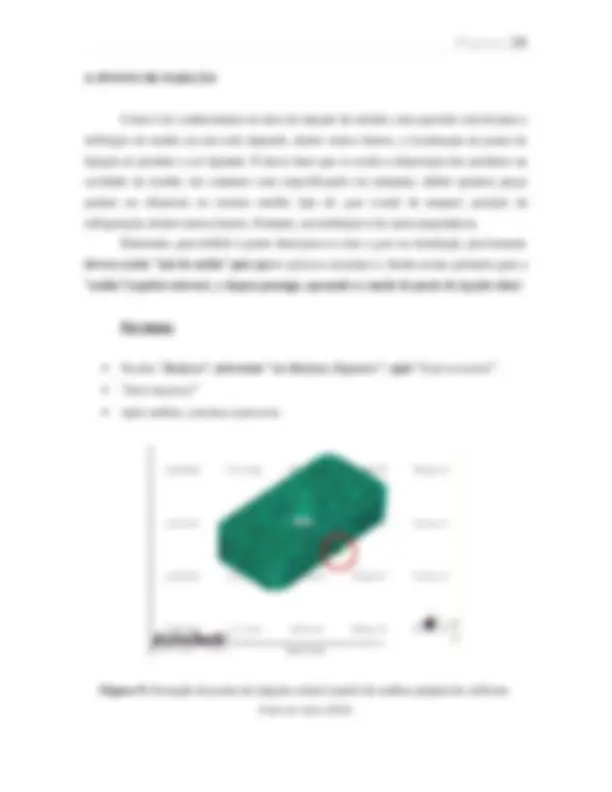
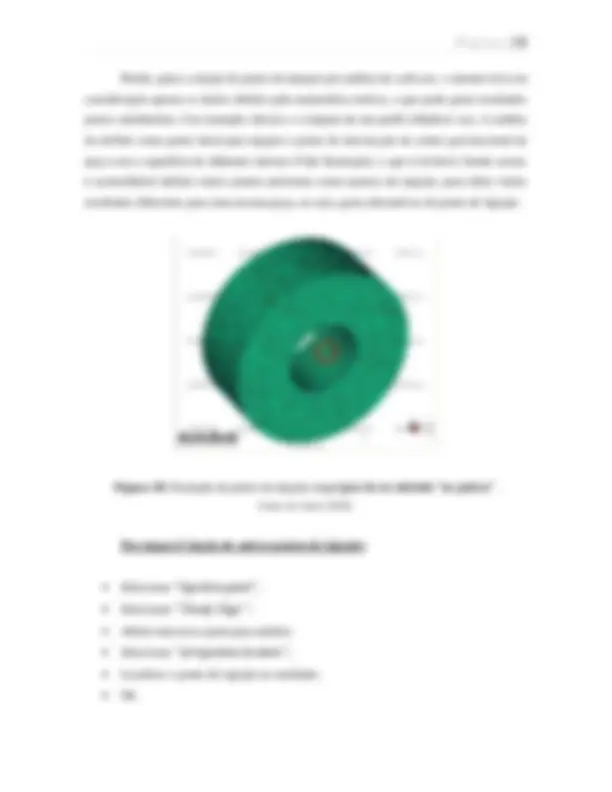
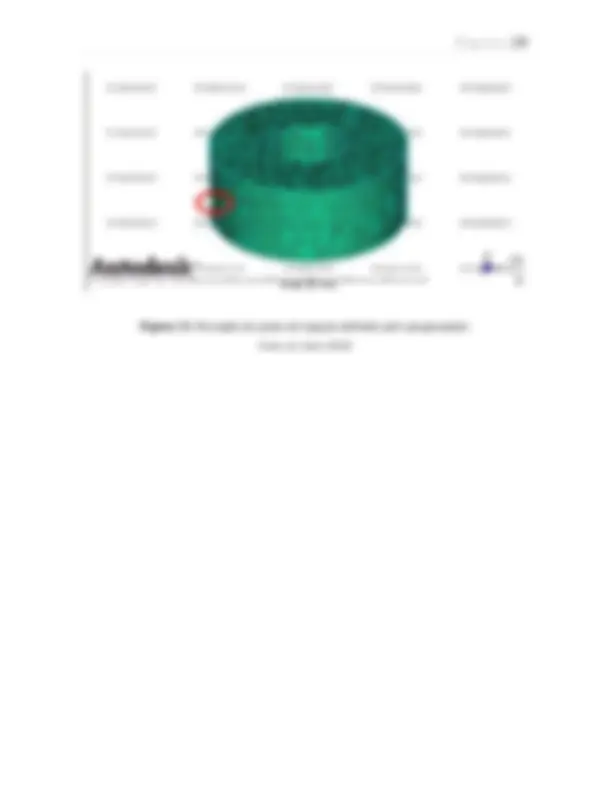
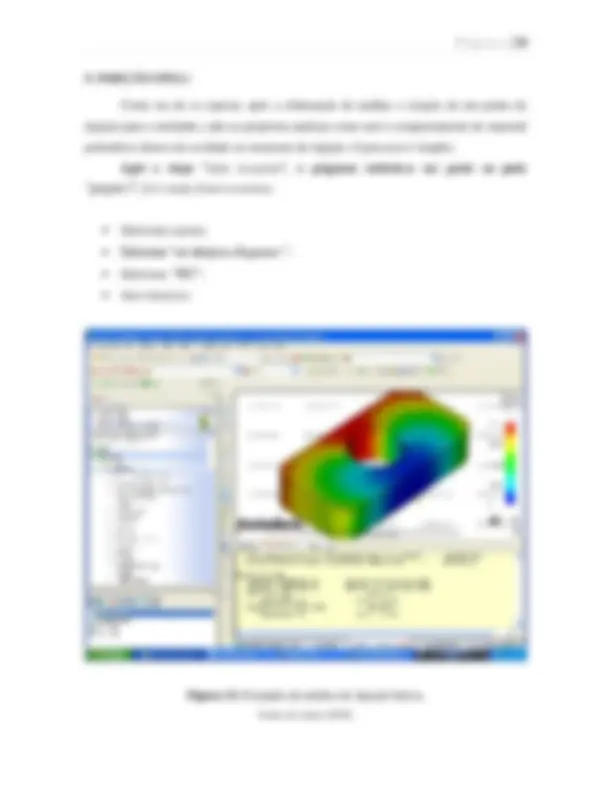
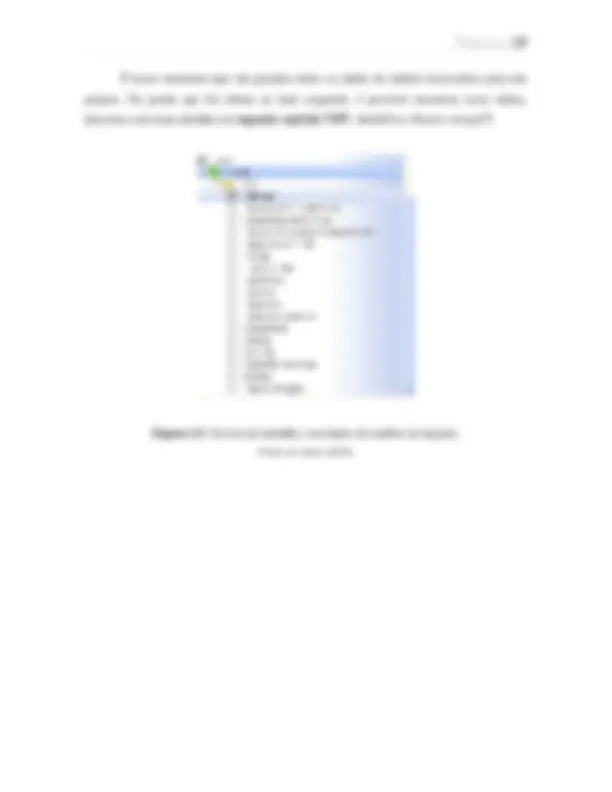
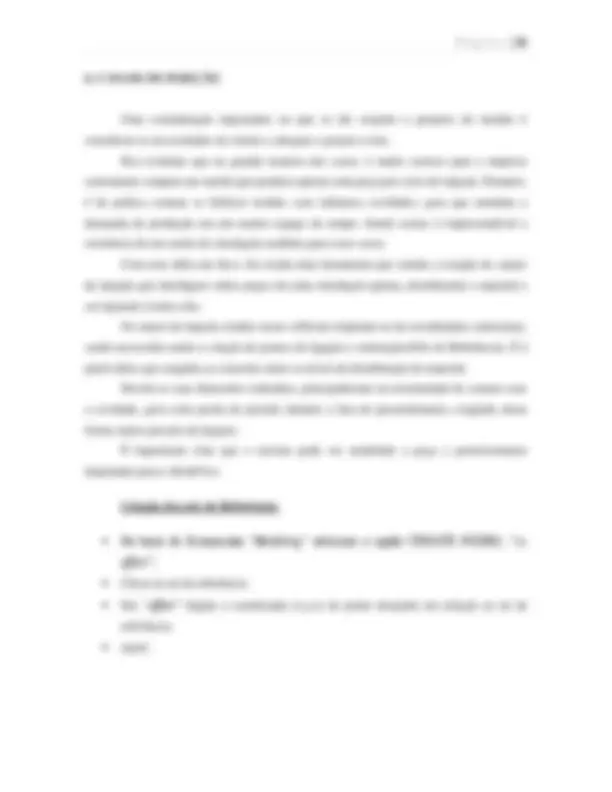
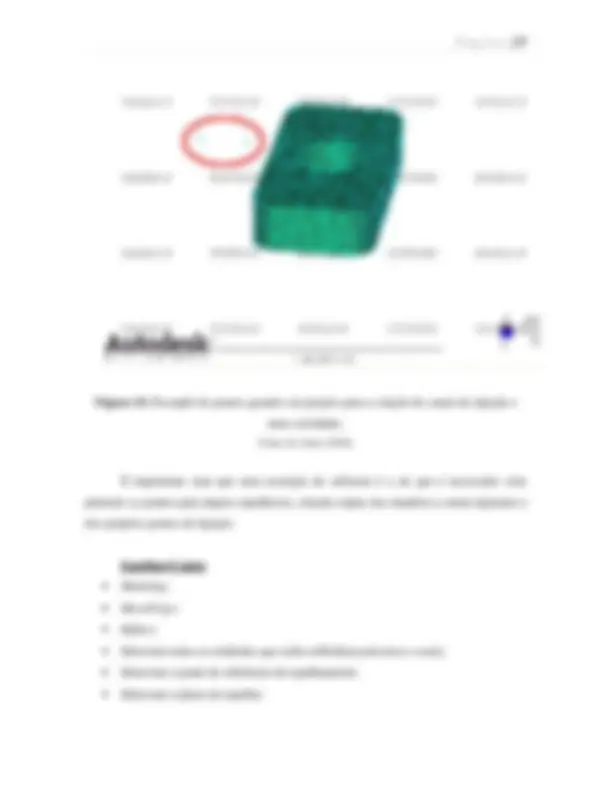
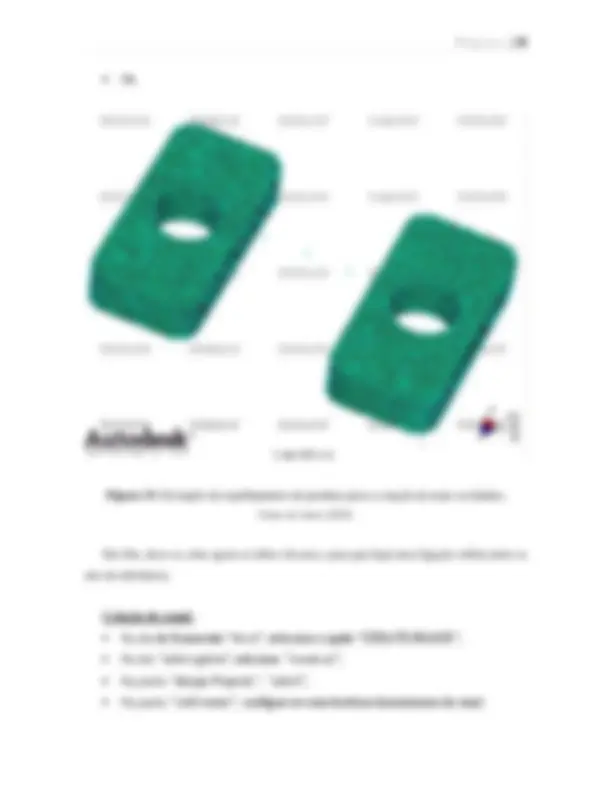
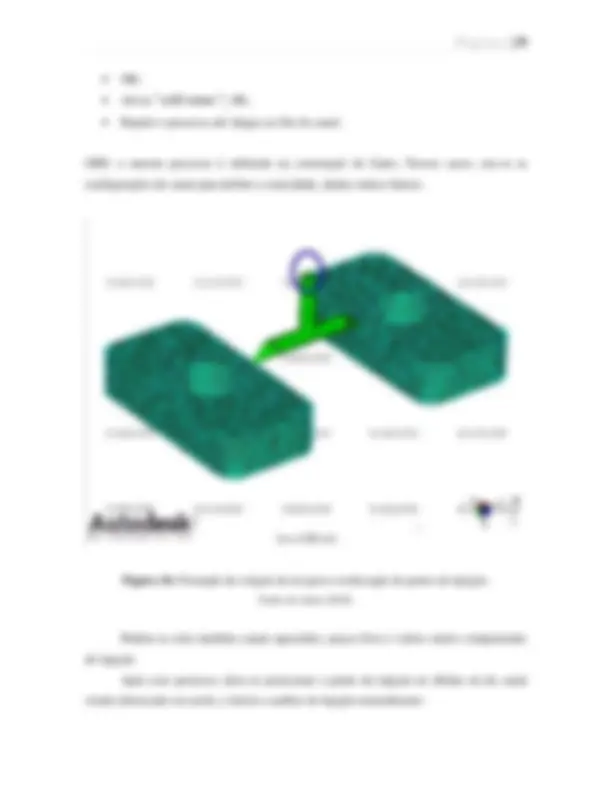
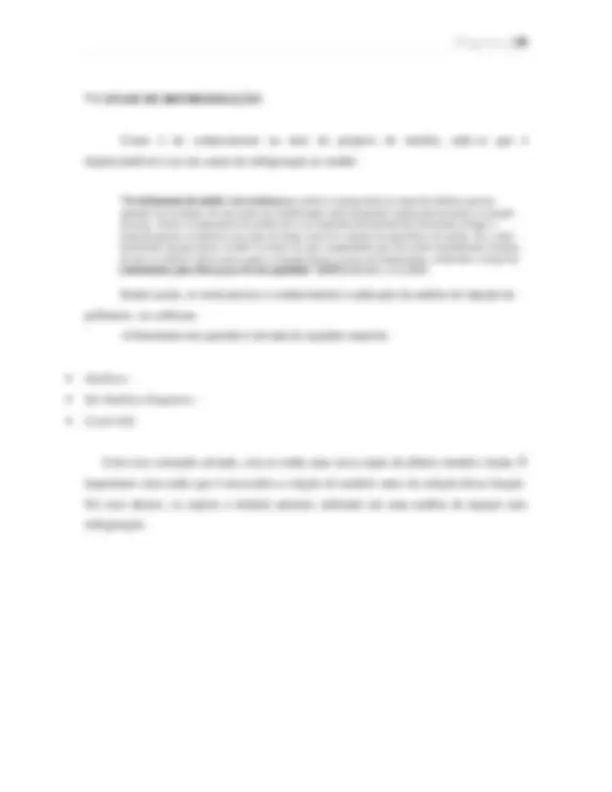
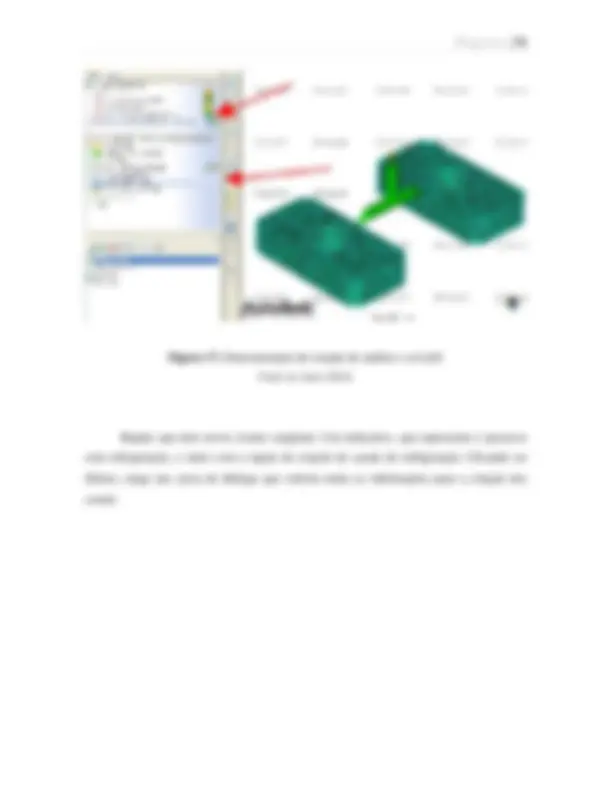
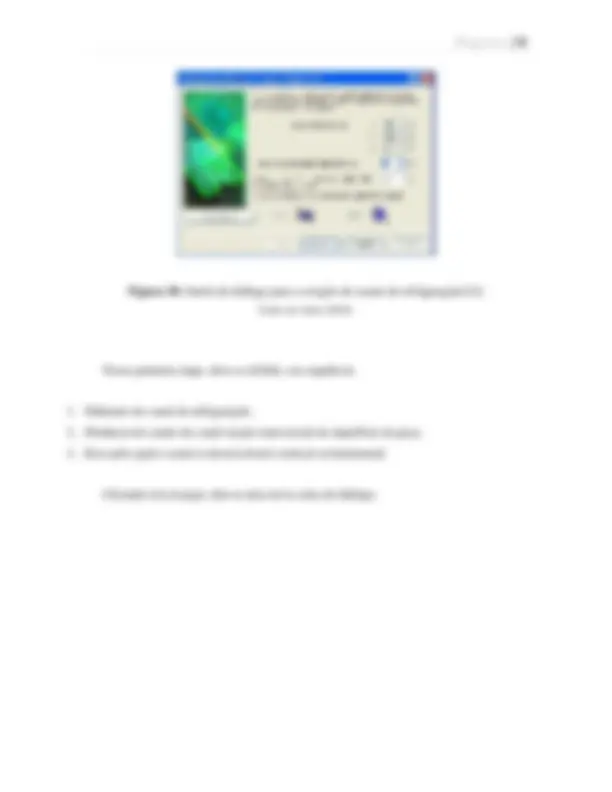
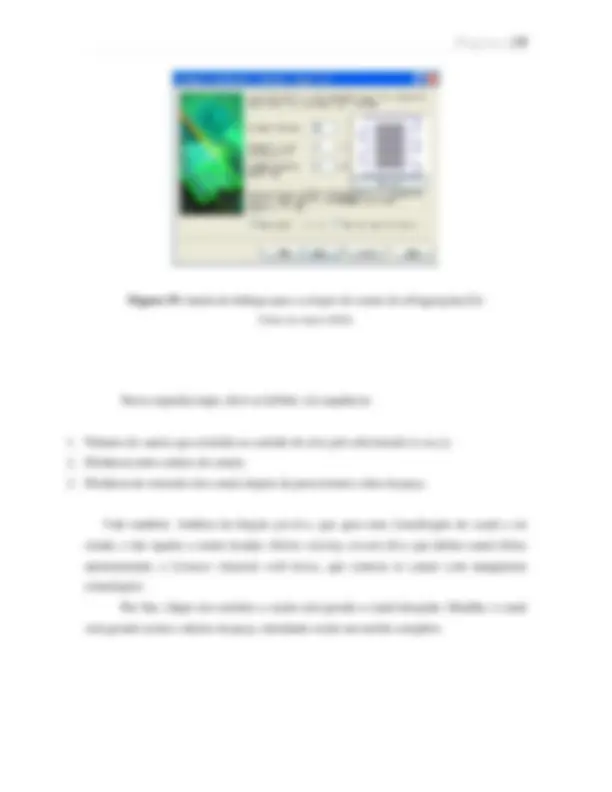
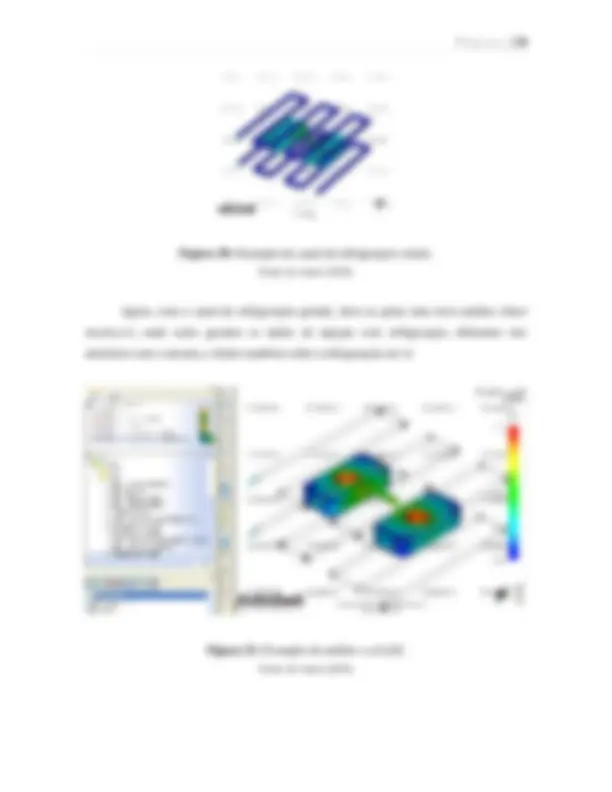
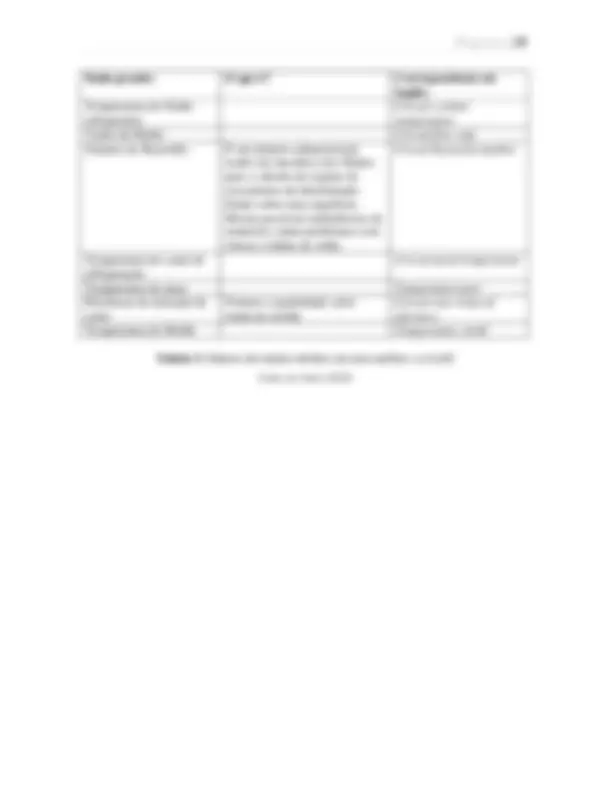
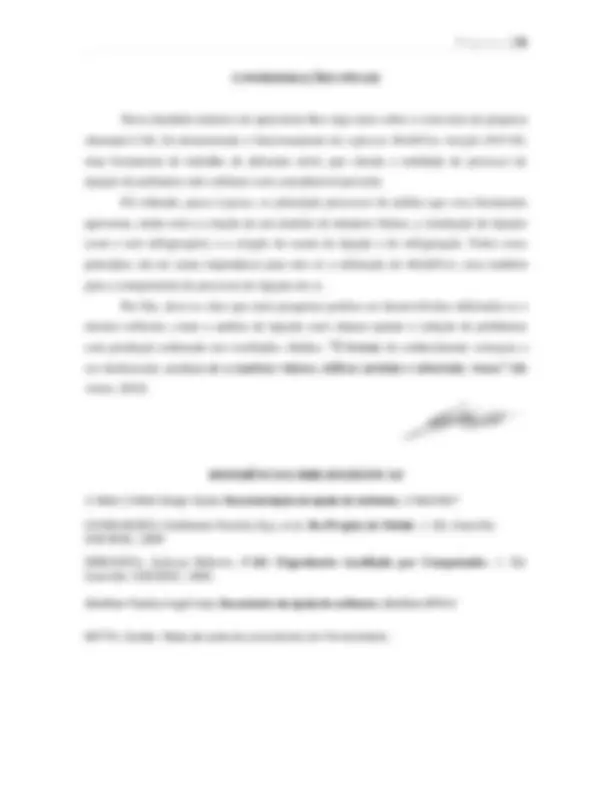
Estude fácil! Tem muito documento disponível na Docsity
Ganhe pontos ajudando outros esrudantes ou compre um plano Premium
Prepare-se para as provas
Estude fácil! Tem muito documento disponível na Docsity
Prepare-se para as provas com trabalhos de outros alunos como você, aqui na Docsity
Os melhores documentos à venda: Trabalhos de alunos formados
Prepare-se com as videoaulas e exercícios resolvidos criados a partir da grade da sua Universidade
Responda perguntas de provas passadas e avalie sua preparação.
Ganhe pontos para baixar
Ganhe pontos ajudando outros esrudantes ou compre um plano Premium
Comunidade
Peça ajuda à comunidade e tire suas dúvidas relacionadas ao estudo
Descubra as melhores universidades em seu país de acordo com os usuários da Docsity
Guias grátis
Baixe gratuitamente nossos guias de estudo, métodos para diminuir a ansiedade, dicas de TCC preparadas pelos professores da Docsity
primeira edição da apostila de operação do MoldFlow 2010
Tipologia: Notas de estudo
1 / 36
Esta página não é visível na pré-visualização
Não perca as partes importantes!
Autor: Guilherme Ferreira Eça Guimarães Co-autores: Prof. Écio Prof. Ewandro José de Souza
Dentre várias áreas de atuação da tecnologia CAE, uma das mais difundidas é a análise de fluxo; a análise de simulação de injeção, cuja qual é de suma importância para a confecção de moldes de injeção de polímeros, alumínio e suas ligas, assim como o entendimento da mecânica dos fluídos. Através deste tipo de análise, executada, é claro, por um software, é possível prever o comportamento dos polímeros, alumínio e ligas metálicas durante o preenchimento da cavidade do molde de injeção, por exemplo. Com estas informações torna-se possível detectar possíveis falhas de projeto que possam prejudicar a processabilidade do molde de injeção. Desta forma, garante-se a produtividade necessária e o nível de qualidade exigido para a peça moldada, com a vantagem de reduzir os custos de fabricação, através da redução ou até eliminação de retrabalhos após o try-out do mesmo. Em especial, os softwares voltados a essas análises possuem como base o estudo da mecânica dos fluídos e cálculos efetuados com a matemática dos números finitos. Outra consideração importante sobre essas ferramentas de trabalho é o fato de que, normalmente, os valores apresentados em tais análises podem variar em uma pequena margem de tolerância, até por que não há como definir todos os parâmetros e variáveis (como temperatura do molde, umidade relativa do ar e do material a ser injetado, entre outras). A ferramenta que será apresentada nesse material será o MPI ( Moldflow Plastics Insight, que em uma tradução livre significa Introspecção do Fluxo de Moldagem de Plásticos ). Como a própria denominação já indica, esta ferramenta apenas executa análises de injeção de materiais poliméricos não-celulares (como o polipropileno, poliestireno, poliamida...), o que exclui alumínio e ligas do mesmo(cuja injeção pode ser analisada pelo software Magma, por exemplo) e poliestireno expandido, conhecido como Isopor®, e outros polímeros celulares. Porém, mesmo avaliando e demonstrando grande parte do que ocorre dentro do molde no momento da injeção, mostra-se imprescindível um conhecimento prévio sobre o que é um molde de injeção e como ele funciona, suas especificações e limitações, para que o MPI possa ser explorado ao máximo.
Este software, que já se apresenta na sua terceira versão, também permite a análise do resfriamento da peça em função do sistema de refrigeração utilizado. Alguns resultados obtidos nesse módulo de simulação são:
Tabela 2: Síntese de resultados gerados em uma análise de injeção(2/2). Fonte: do Autor, 2010.
Resultado: O que significa: Denominação no Software(inglês):
Como a denominação indica, mostra áreas de maior aquecimento e resfriamento no molde, mostrando onde se deve refrigerar mais ou não.
Delimita o aumento da temperatura do fluído refrigerante em relação ao tempo de injeção.
Circuit coolant temperature
Quantifica a vazão mínima de fluído refrigerante no sistema de refrigeração.
Circuit flow rate
Mostra quanto tempo o molde “precisa” para fazer as trocas de calor necessárias para o resfriamento da peça.
Quantifica a pressão necessária no momento de refrigeração do molde.
Antes de entender a operação/ análise de injeção de polímeros utilizando o software, é importante conhecer e entender algumas das variáveis do processo da injeção em si.
2.1.1 Fill Time (Tempo de injeção)
Definimos como sendo o tempo necessário para o polímero encher completamente a cavidade. Sabe-se que determinando o tempo em que se tem a menor pressão, a força de fechamento necessária será menor, assim como o tensionamento interno da peça e conseqüentemente uma menor tendência ao empenamento. A relação entre tempo de preenchimento e pressão de injeção depende de uma série de fatores contraditórios. Quanto menor o tempo de preenchimento, maior o fluxo volumétrico e a pressão requerida. Dada uma cavidade com um volume fixo, o tempo de preenchimento é inversamente proporcional ao fluxo. Entretanto, alta velocidade de injeção também gera aquecimento viscoso que aumenta a temperatura do material. O efeito combinado de alta temperatura e alta taxa de cisalhamento reduz a viscosidade, e dessa maneira diminui a pressão requerida na injeção. Por outro lado, o tempo de preenchimento também influencia o efeito de resfriamento provocado pelas paredes do molde. Maiores tempos de injeção resultam em uma camada congelada mais espessa, que se traduz em um canal mais restrito para o fluxo, exigindo desta forma uma maior pressão de injeção.Com a ajuda da simulação é possível prever o efeito líquido das influências contraditórias resultantes da mudança no tempo de injeção, podendo ser estimado um ótimo tempo.
2.1.2 Pressure (Pressão de injeção)
A pressão de injeção é a mínima pressão necessária para vencer a resistência que o polímero fundido enfrenta e fazer com que a cavidade seja completamente preenchida. Esta pressão depende de vários fatores como:
fragilidade da peça, ocasionados por tensões internas não uniformes.
2.1.6 Frozen layer fraction at end of fill (Camada congelada no final da injeção)
Durante o preenchimento da cavidade, a camada de polímero que está em contato com as paredes do molde resfria-se rapidamente, formando uma camada “sólida” de material, quanto maior for o tempo de injeção, maior será a espessura desta camada. Níveis elevados de solidificação geram elevação na pressão de injeção necessária para preencher a cavidade.
Figura 1. Efeito do tempo de preenchimento na camada congelada. Fonte: C-MOLD (1998).
2.1. 7 Shear rate, bulk (Taxa de cisalhamento)
Durante o preenchimento da cavidade o polímero fundido se divide em camadas que se deslocam paralelamente uma em relação à outra. A camada em contato com a superfície da cavidade tem sua velocidade estacionária e as demais se movem em velocidade crescente quanto mais distante das paredes do molde se encontram. Este movimento entre as macromoléculas do polímero é chamado de cisalhamento e a diferença de velocidade entre estas camadas é chamada de taxa de cisalhamento. Altas taxas de cisalhamento representam um alto aquecimento por atrito entre as macro-moléculas do polímero fundido. Com isto concluímos que altas taxas de cisalhamento são bons indicadores para as condições de processo da peça, uma vez que a viscosidade dos materiais poliméricos varia
de acordo com a temperatura. Este aquecimento diminui a viscosidade do polímero melhorando as condições de preenchimento da cavidade. Na simulação deve-se observar se a taxa de cisalhamento está dentro do permitido pelo polímero. Caso este limite for excedido, o superaquecimento do polímero poderá causar a quebra das cadeias moleculares, degradação, descoloração e etc.
2.1.8 Shear stress at wall (Tensão de cisalhamento)
Durante o preenchimento da cavidade o polímero fundido é forçado a percorrer o espaço existente entre as duas faces do molde que definem a espessura do produto, sendo que a velocidade junto a estas faces é muito pequena e aumenta à medida que se aproxima do centro. Este preenchimento ocorre como se o material fosse dividido em camadas que deslizam uma sobre as outras. Para isto, cada “camada” exige que seja superada uma certa tensão para então deslizar sobre a outra, tensão esta conhecida como Tensão de Cisalhamento ( Shear Stress ). Então, concluímos que tensão de cisalhamento é a resistência intrínseca ao material, que precisa ser vencida para que as macromoléculas do material deslizem entre si.
2.1.9 Time to freeze (Tempo de resfriamento)
É o tempo necessário para que o polímero moldado atinja a temperatura de extração. Estas temperaturas variam conforme propriedades intrínsecas de cada tipo polímero. É o tempo mais longo do processo, normalmente representa 70% do tempo do ciclo total. A temperatura de processo do polímero e a temperatura de trabalho do molde afetam diretamente o tempo de resfriamento. Ambos podem precisar de variações para obter uma redução de tempo. Aumentando a temperatura da massa ou a temperatura do molde, o tempo de resfriamento aumenta. O projeto do molde exerce um papel importante no tempo de resfriamento e deve beneficiar ao máximo a refrigeração. O controle da temperatura do líquido refrigerante também é outro fator importante.
2.1.13 Circuit coolant temperature (Temperatura do fluido refrigerante)
Corresponde à temperatura do fluido utilizado para refrigerar o molde. Acréscimos maiores que TRE graus Celsius entre a temperatura de entrada e a temperatura de saída do fluido devem ser evitados. Isto pode ser controlado através da vazão e da temperatura do fluido.
2.1.14 Circuit metal temperature (Temperatura do circuito de refrigeração)
Corresponde à temperatura dos canais de refrigeração usinados no molde. Neste parâmetro busca-se a uniformidade de temperatura em todos os circuitos. Concentrações de temperatura significam que há regiões com deficiência de refrigeração, sendo necessária a otimização do sistema de refrigeração.
2.1.15 Circuit flow rate (Vazão do fluido refrigerante)
Para que o fluido refrigerante apresente alta eficiência na extração de calor, é necessário que o mesmo escoe no interior dos circuitos em regime turbulento. Esta turbulência é medida através do número de Reynolds , sendo que o valor recomendado para haja um nível de turbulência ideal é ≥ 10.000 Re.
Figura 2. Escoamento laminar e turbulento. Fonte: C-MOLD (1998).
2.1.17 Temperature (top), part (Temperatura da cavidade/macho)
Corresponde à temperatura na interface polímero/molde. O sistema de refrigeração do molde deve garantir que esta temperatura seja uniforme, e que a mesma esteja dentro da faixa de trabalho recomendada pelo fabricante do polímero. Recomenda-se que o gradiente de temperatura ao longo da geometria da cavidade não ultrapasse os 10 °C.
2.1.18 Temperature difference, part (Diferença de temperatura cavidade/macho)
Diferenças maiores que cinco graus Celsius entre cavidade e macho devem ser evitadas, pois geram diferentes condições de resfriamento entre a superfície superior e inferior da peça moldada, onde o percentual de contração é maior do lado mais quente, induzindo a um empenamento da peça.
Ao abrir o software, o seguinte layout será apresentado:
Figura 4: Layout de página inicial do software MoldFlow Insight 2010 R Fonte: do Autor (2010)
Á partir de então, deve-se clicar na opção “ New project ”, criando assim um arquivo onde os dados de análise da simulação serão gravados.
Figura 5: Janela de diálogo para criação de um novo projeto. Fonte: do Autor (2010)
É importante citar que o software utilizado nas aulas é educacional, e isso acarreta em algumas restrições. Uma delas é a de que a análise feita em um computador só e somente só pode ser aberta na mesma máquina. Portanto, aconselha-se que o diretório onde o projeto vai ser gravado seja mantido padronizado, pois somente serão abertos arquivos daquela pasta. E, posteriormente, deve-se criar um backup de segurança do projeto em um pen drive. Com o projeto criado, deve-se importar um modelo sólido para o programa (Import).
Perceba que há a possibilidade de alterar a forma com que o software importará o modelo e também alterar a unidade de medida. Existem também limitações referentes ao formato suportado pelo software.
3.2 GERAÇÃO DE MALHAS
NOTA: Deste ponto em diante, as instruções de processo, ou seja, o “passo a passo” que devem ser seguidos para completar a etapa da simulação serão informadas em tópicos, apresentados na sequência em que devem ser executados. Com a peça já importada para dentro de sua área de trabalho, se faz primordial a criação de uma malha de pontos que delimitará a sua peça em questão. Simplificando, a superfície do produto a ser injetado será fracionada em várias superfícies menores, para assim, uma a uma, elas serem avaliadas em relação a posição, referência e curvatura. Desta maneira, se define então o melhor ponto de injeção.
Por etapa: -Na aba “Mesh” selecione a opção “ Generate Mesh ”; Preview; Mesh now ; Verificar se a malha está bem feita, (Se os vértices dos triângulos estão coincidentes); Finish/Ok.
Figura 8: Exemplo de malha gerada á partir de peça importada Fonte: do Autor (2010)