
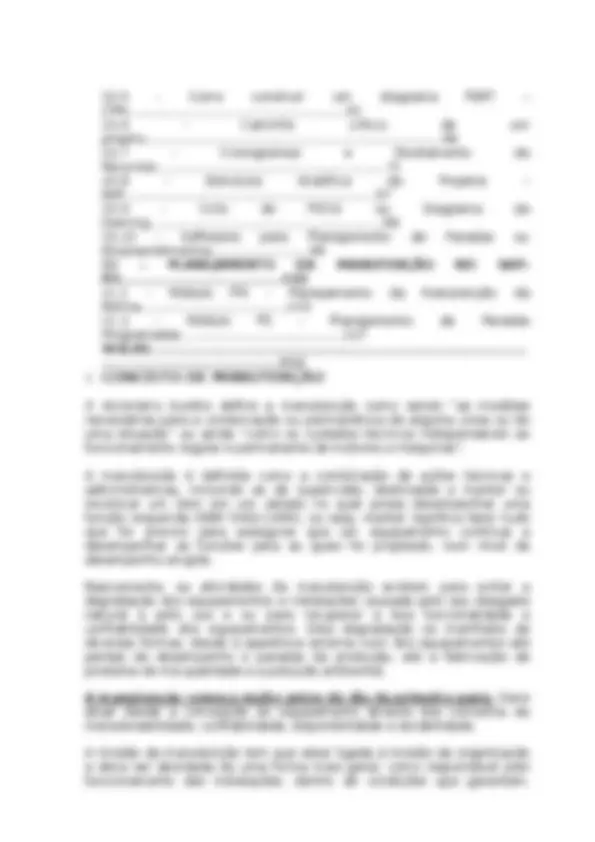
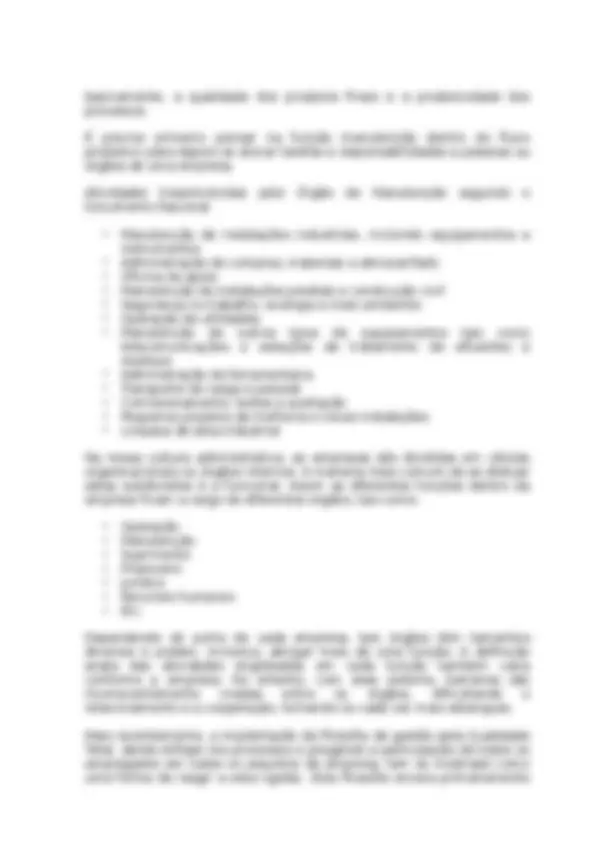
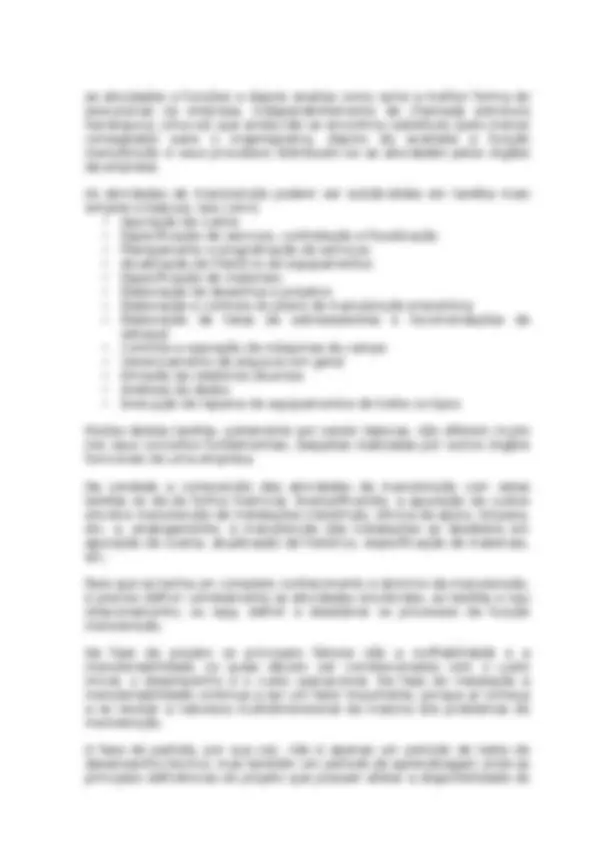
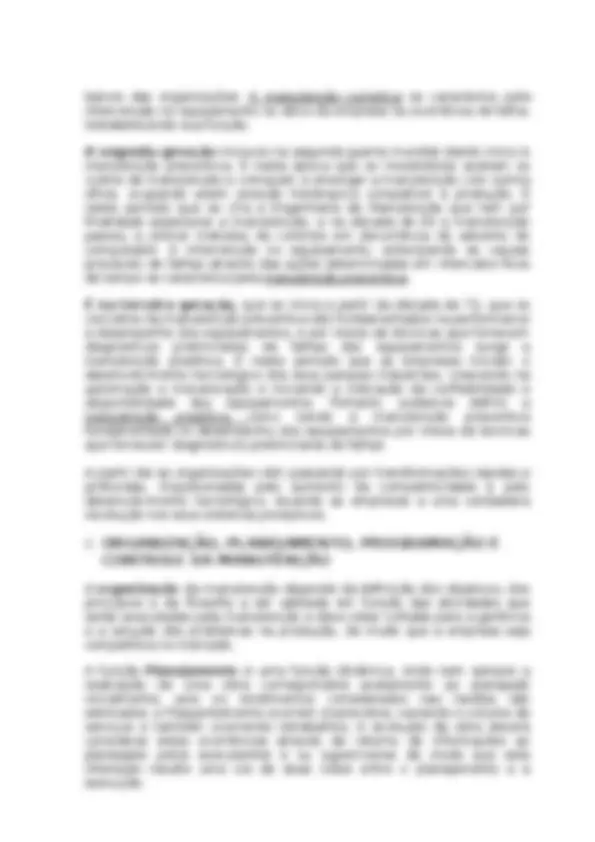
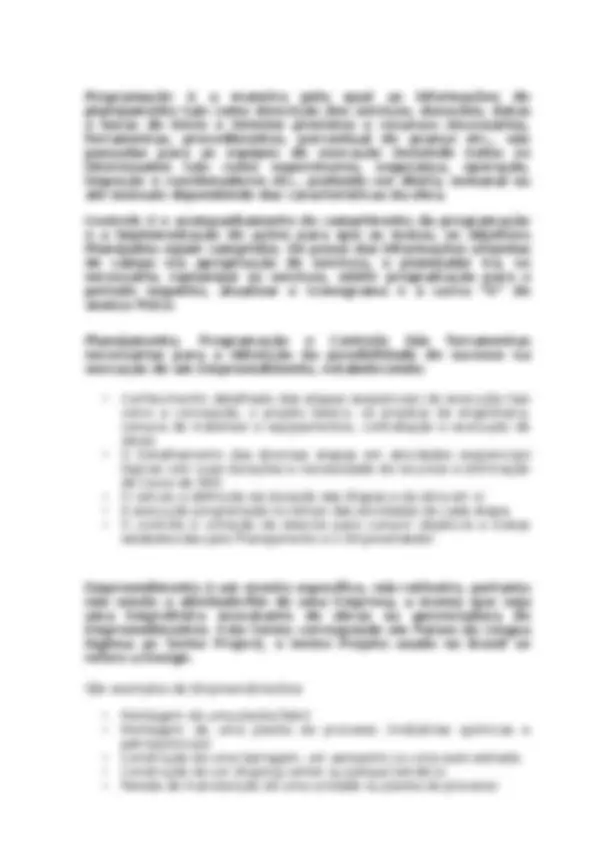
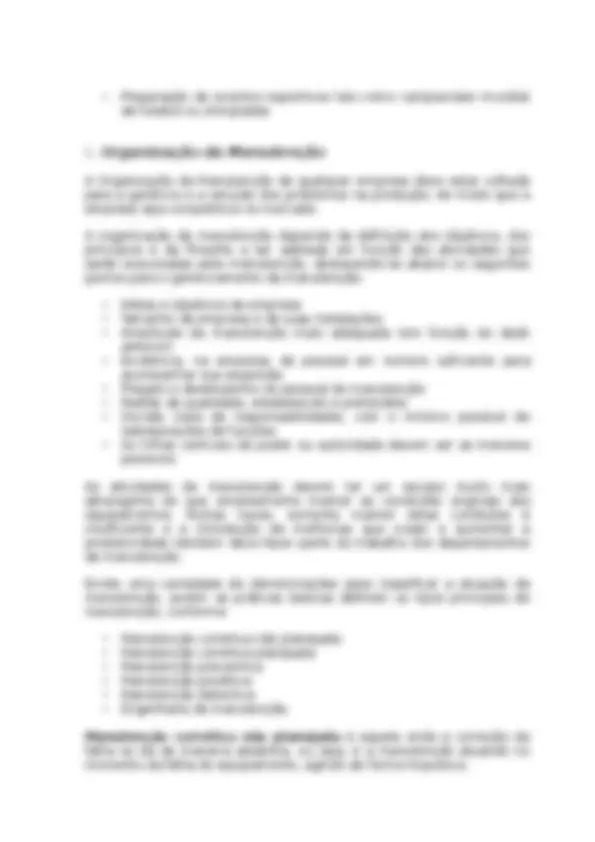
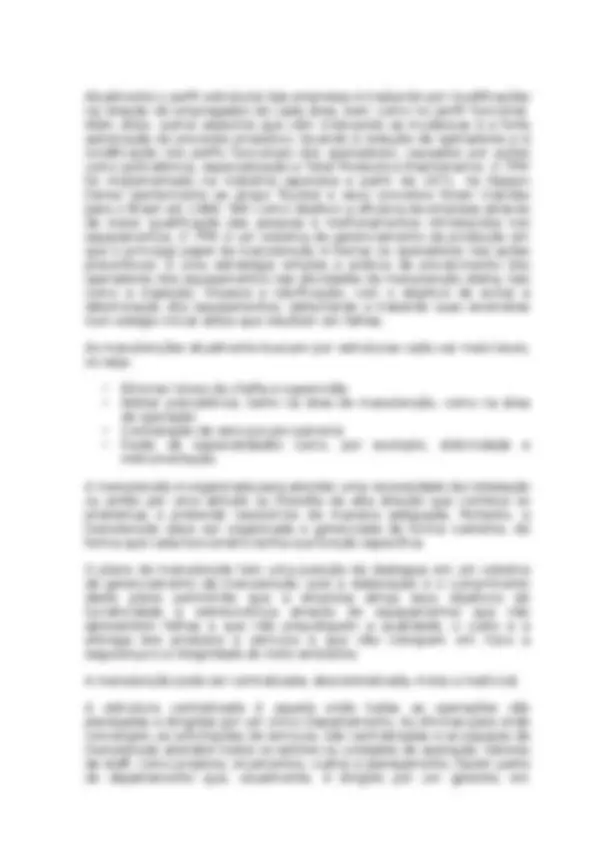
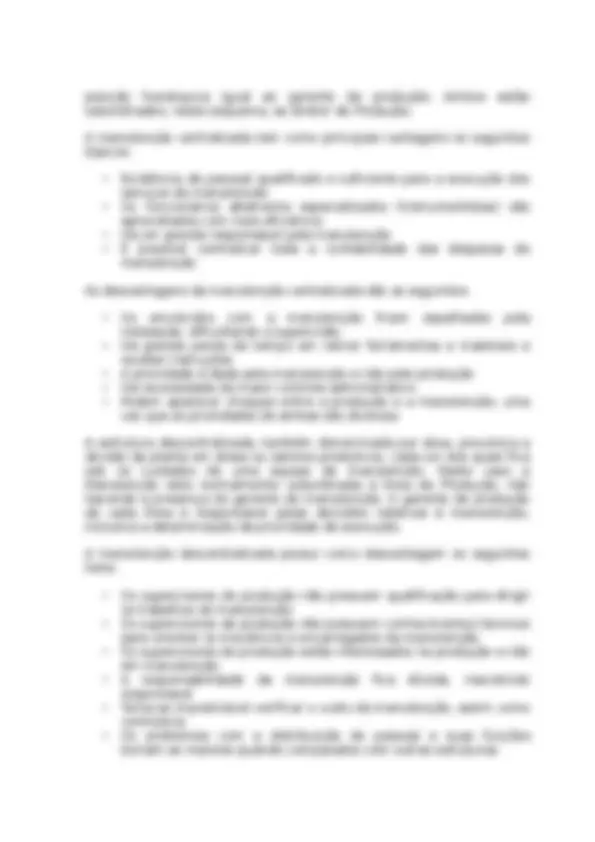
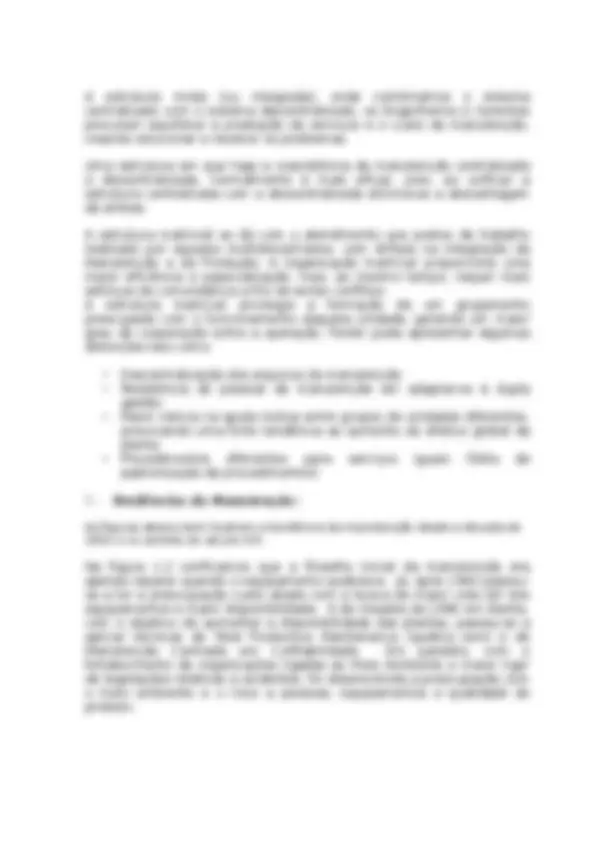
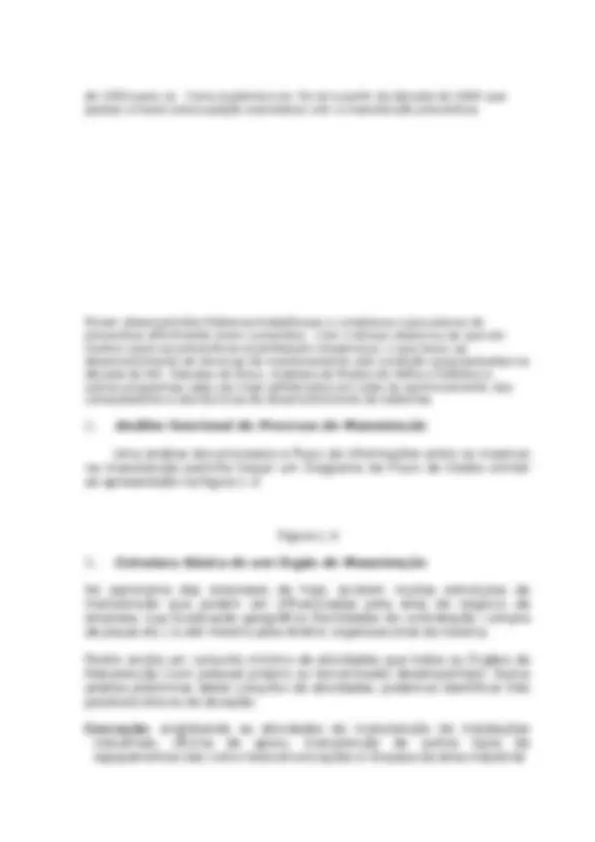
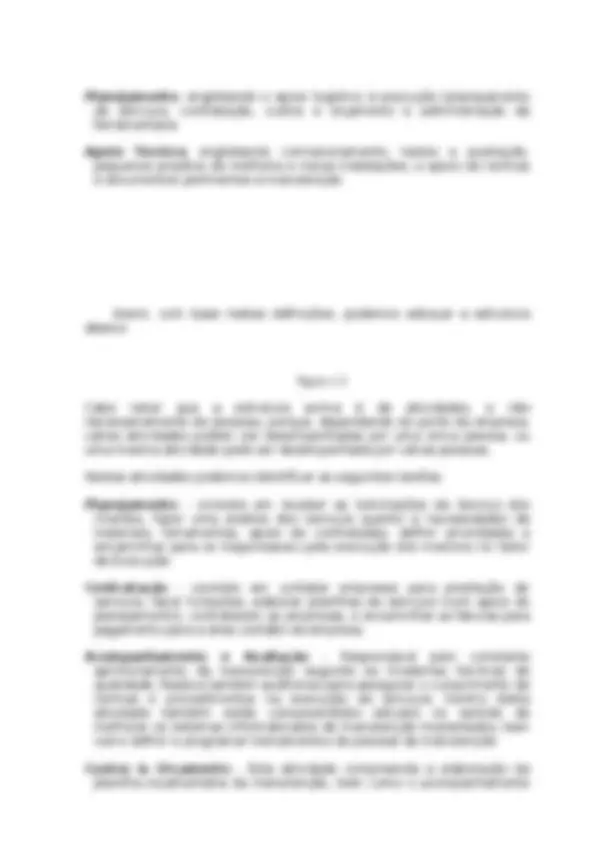
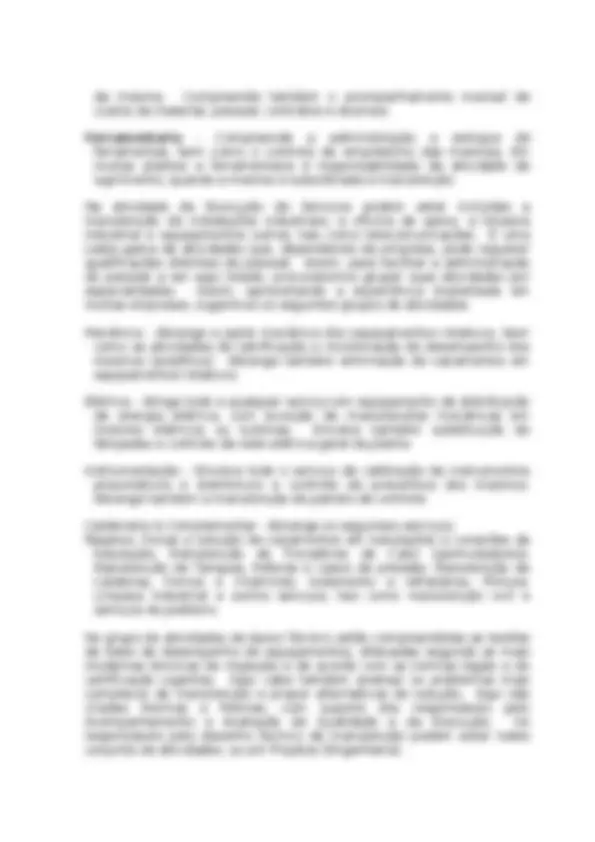
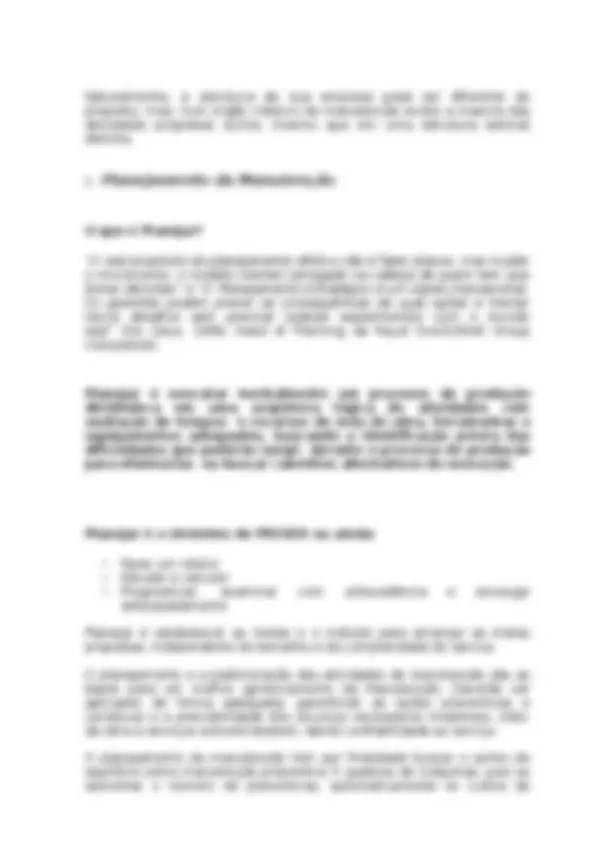
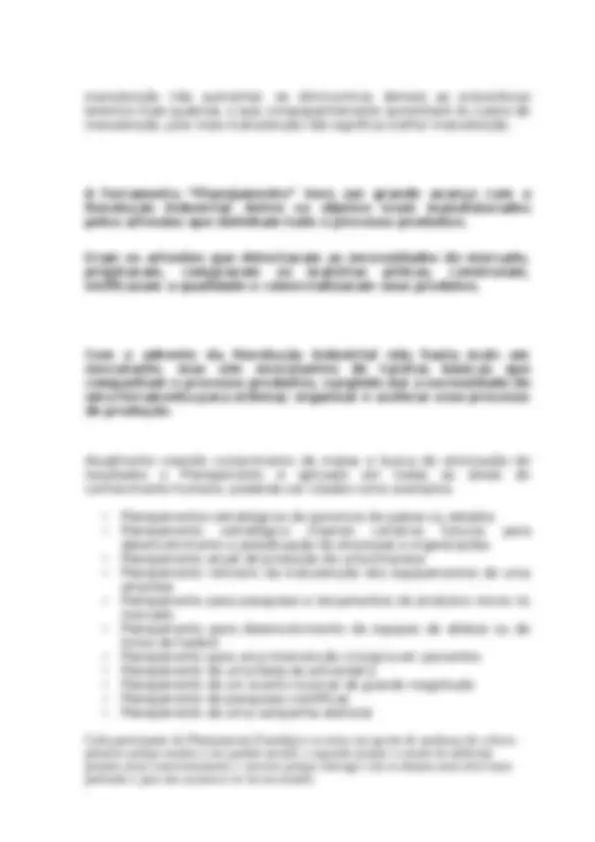
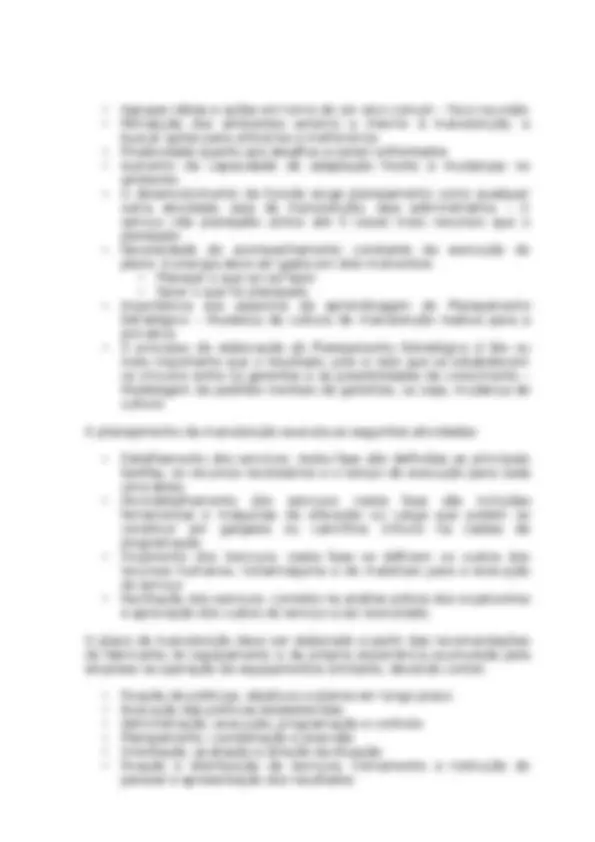
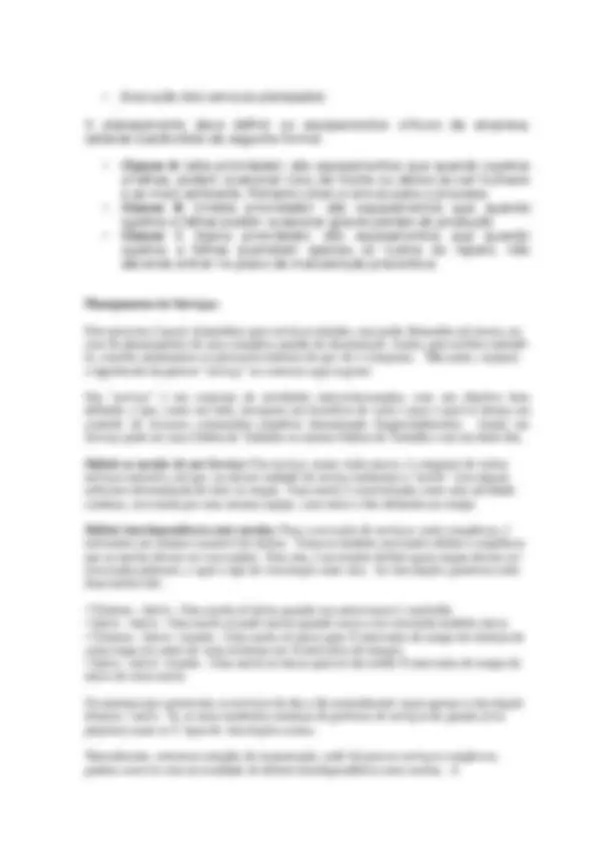
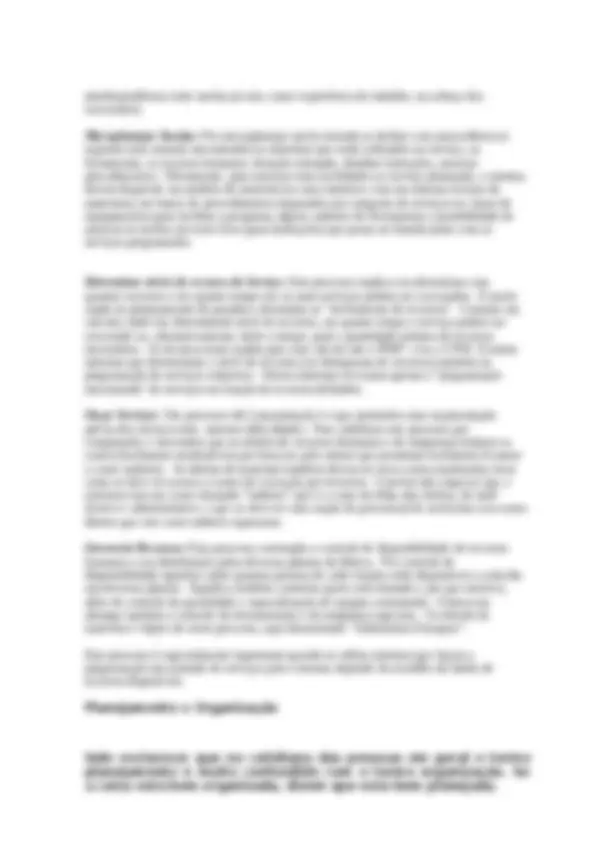
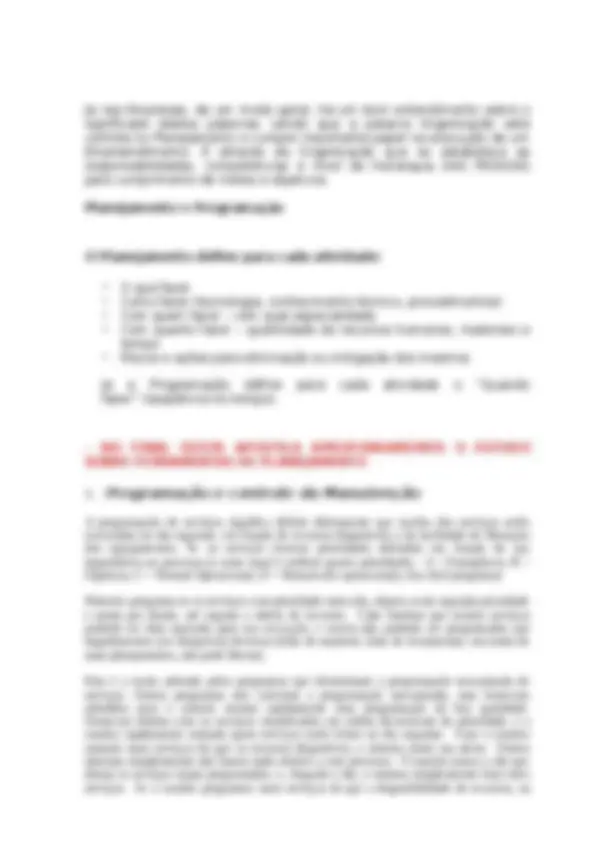
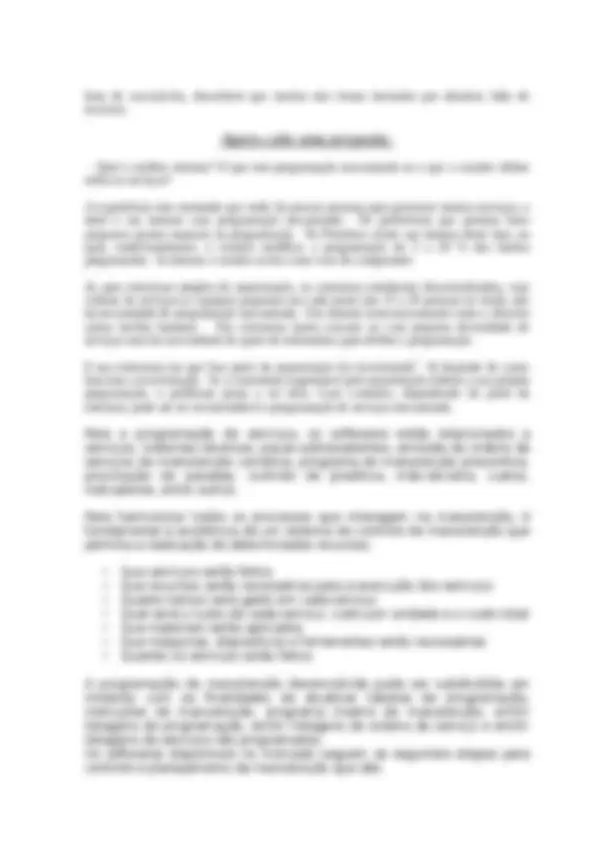
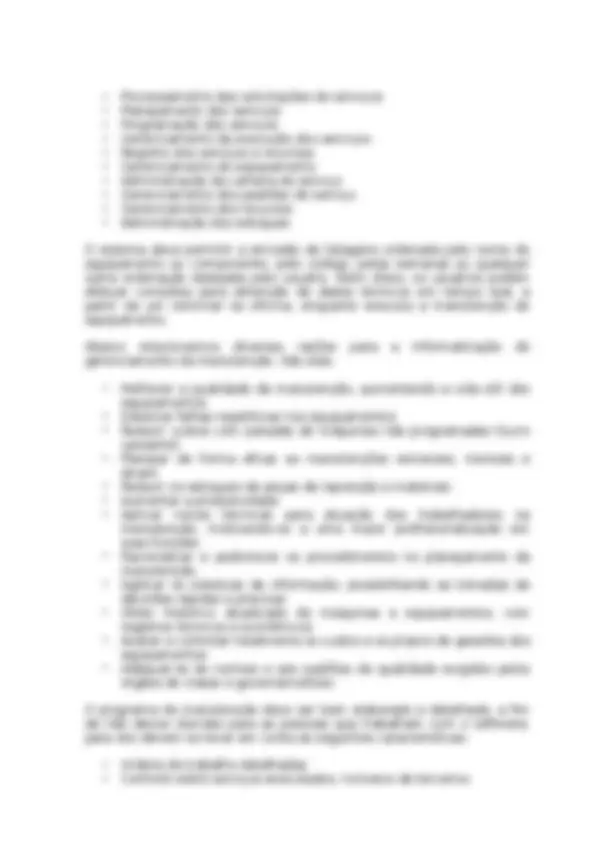
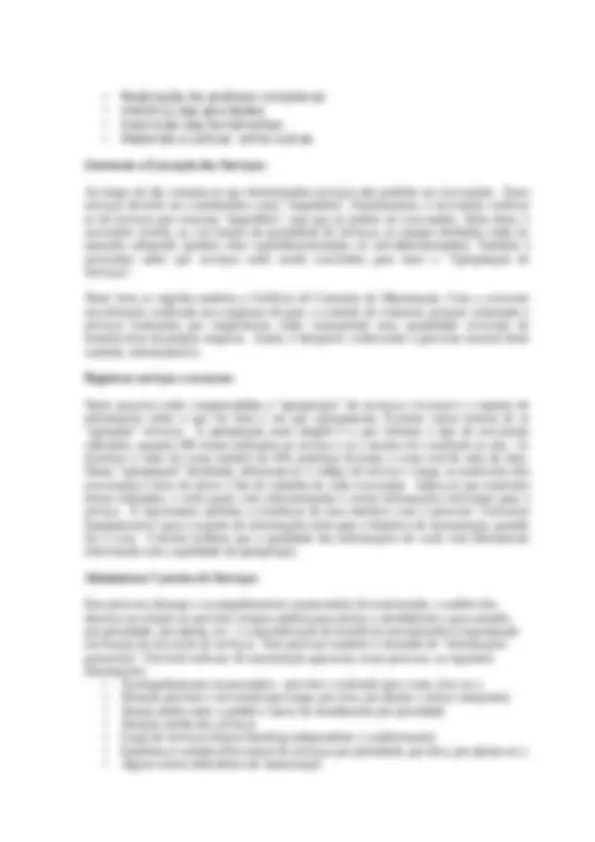
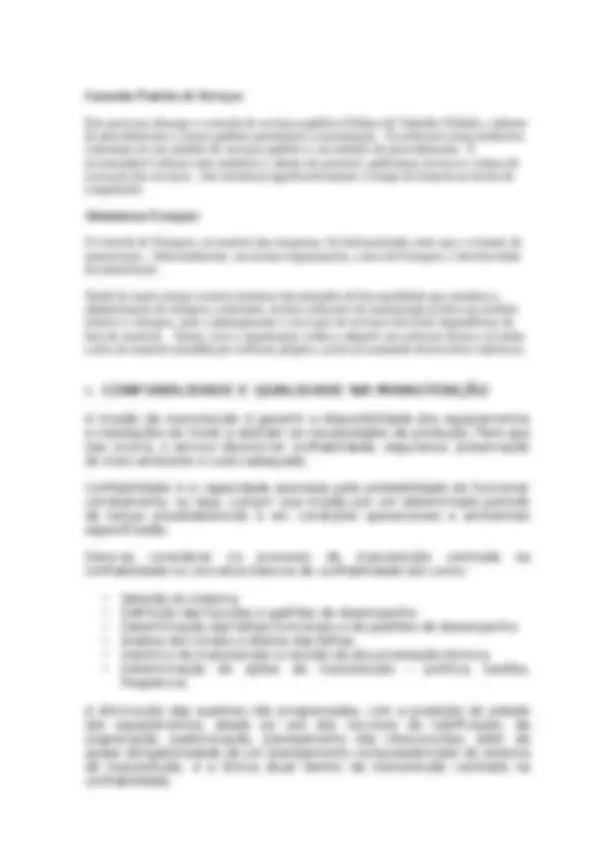
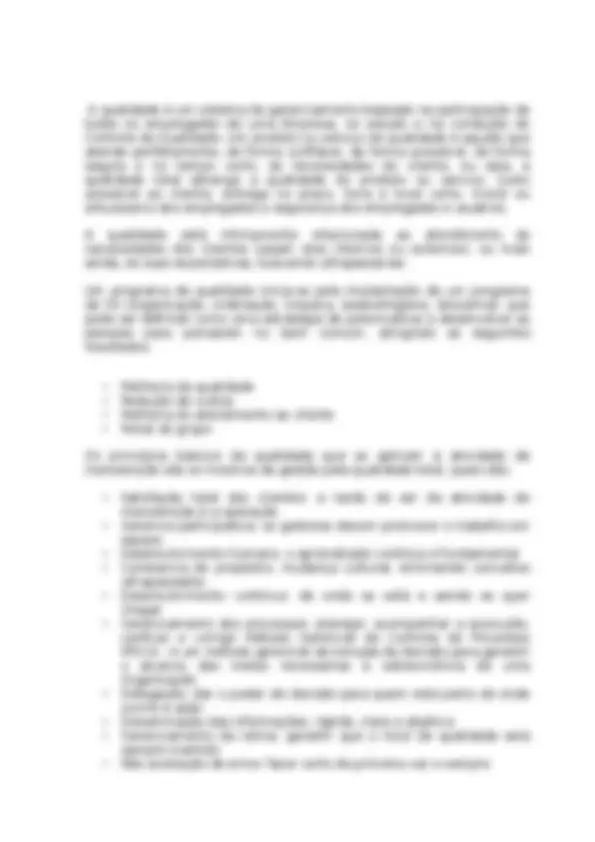
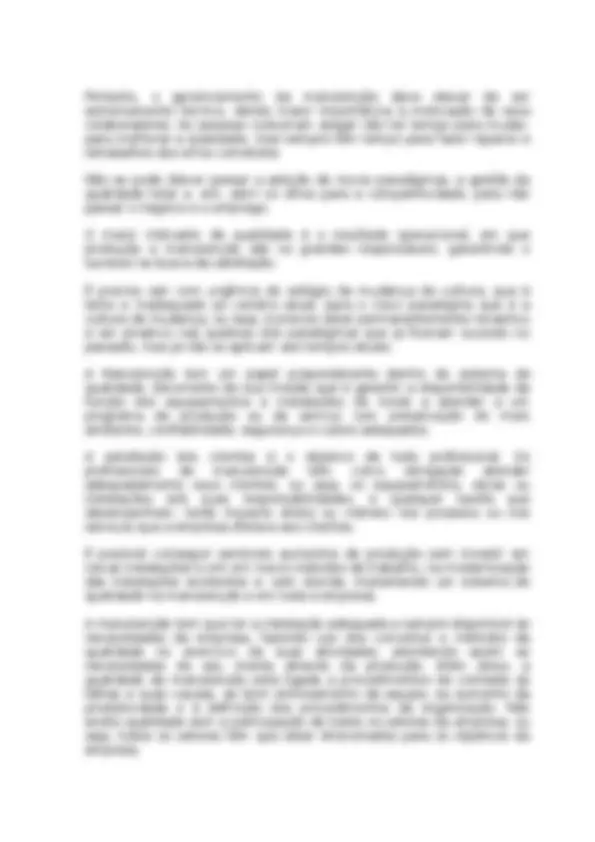
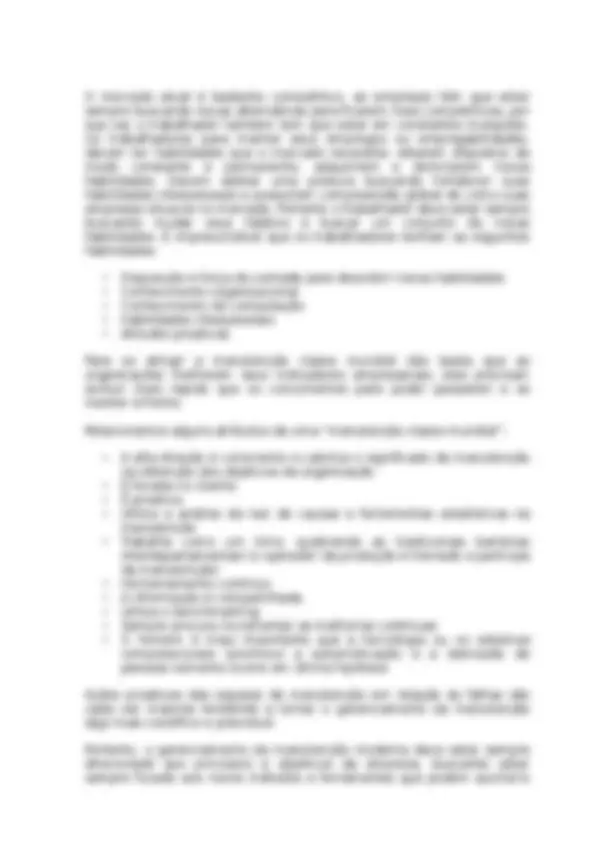
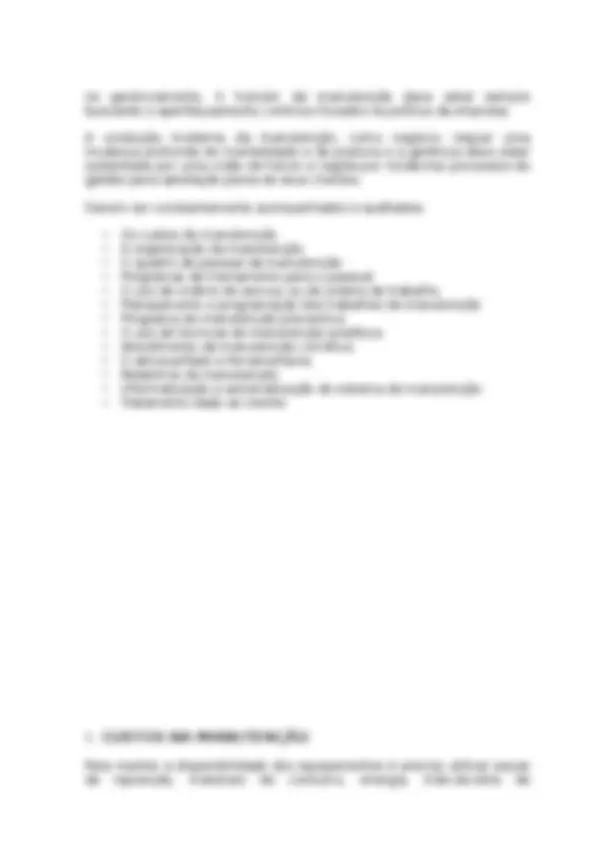
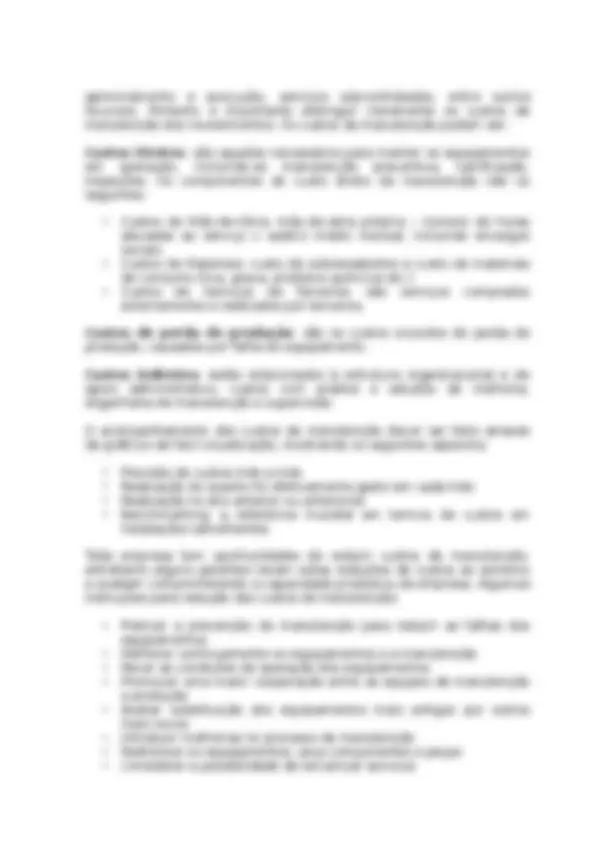
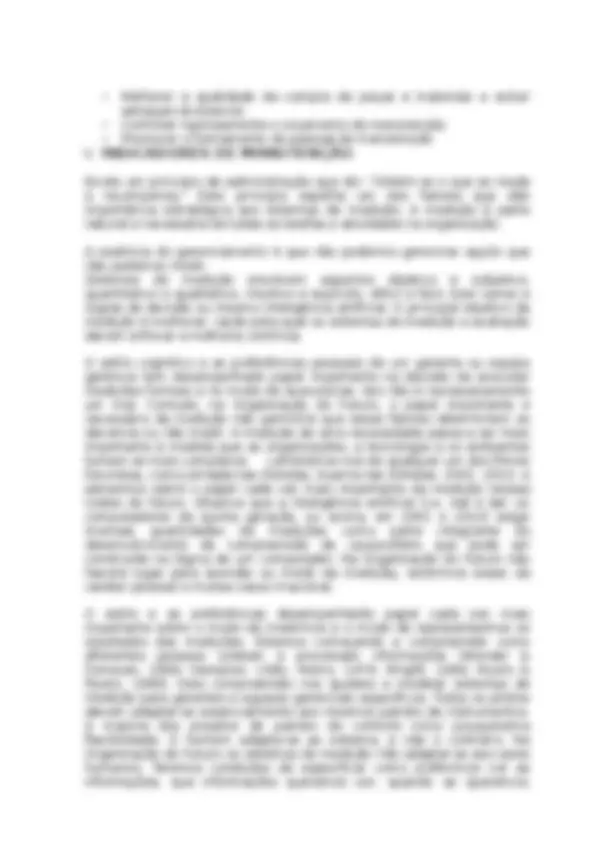
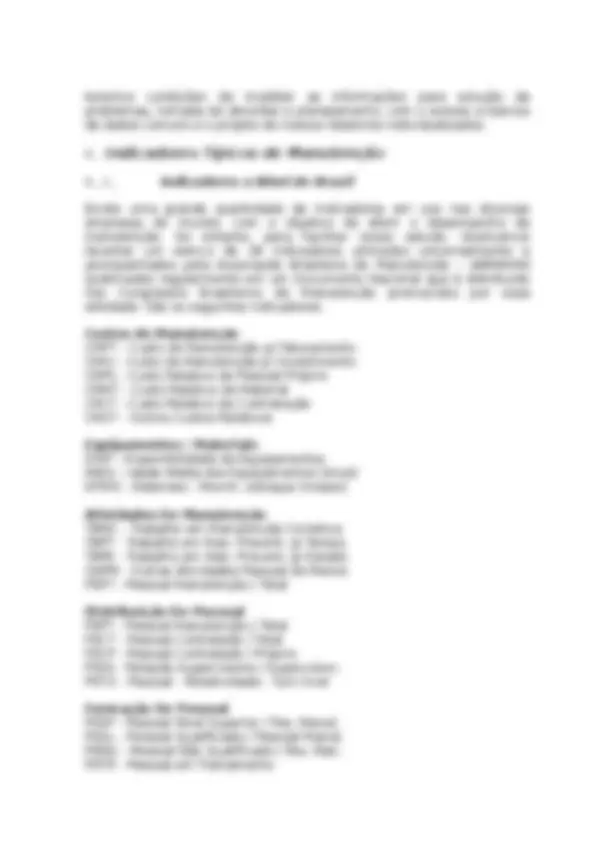
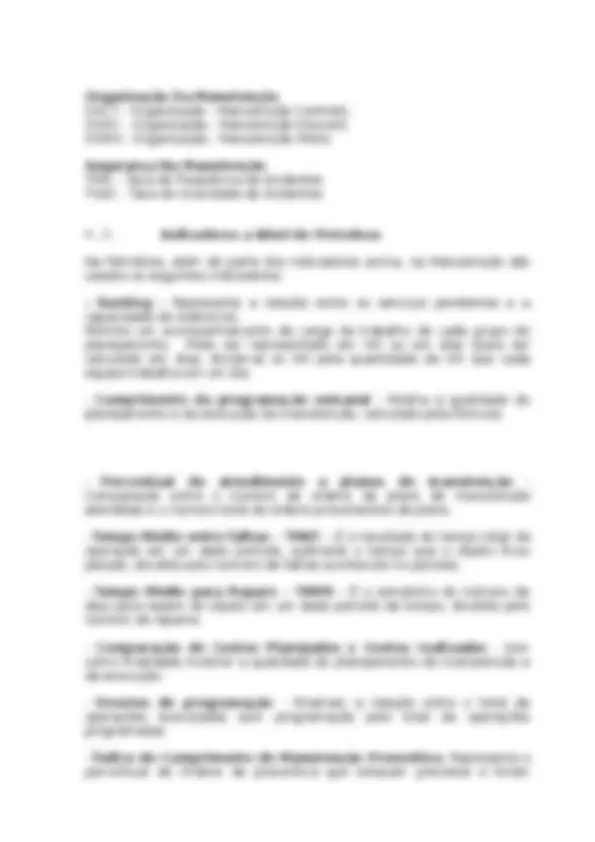
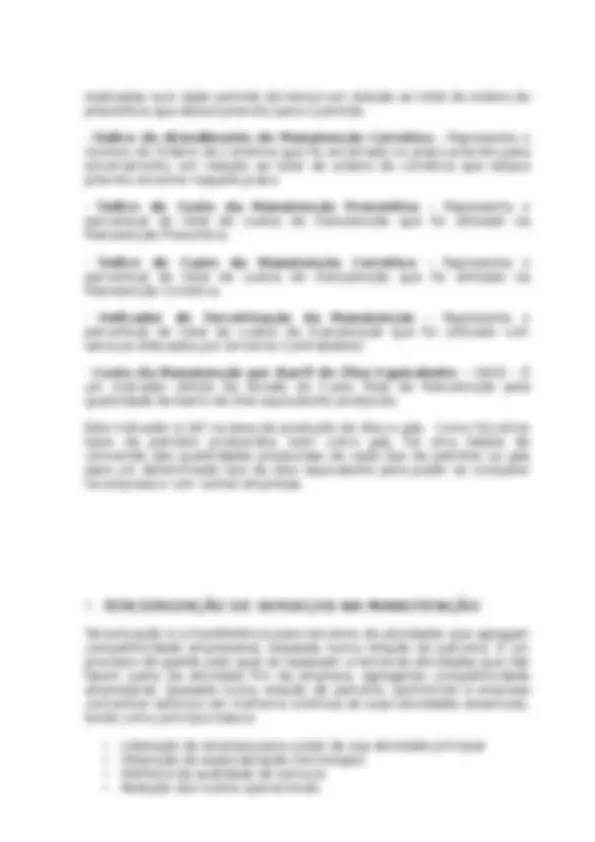
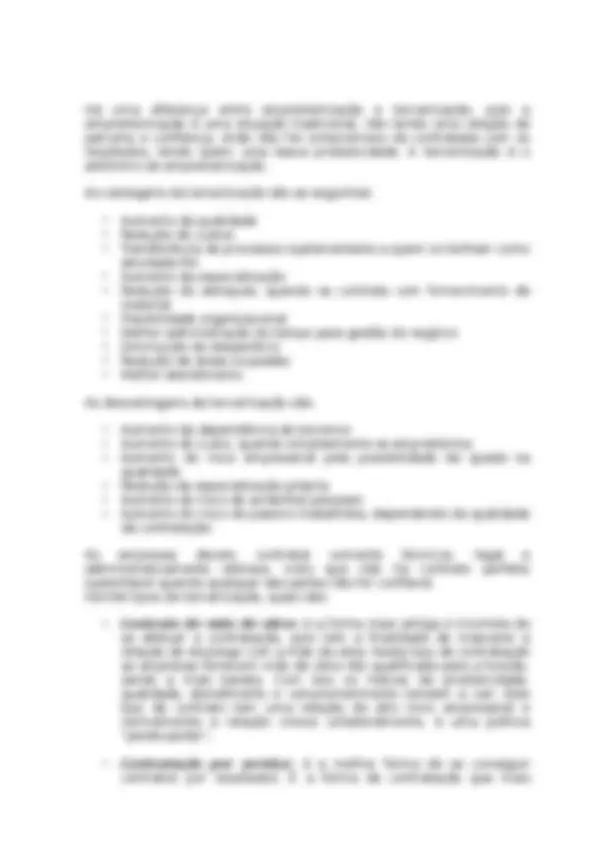
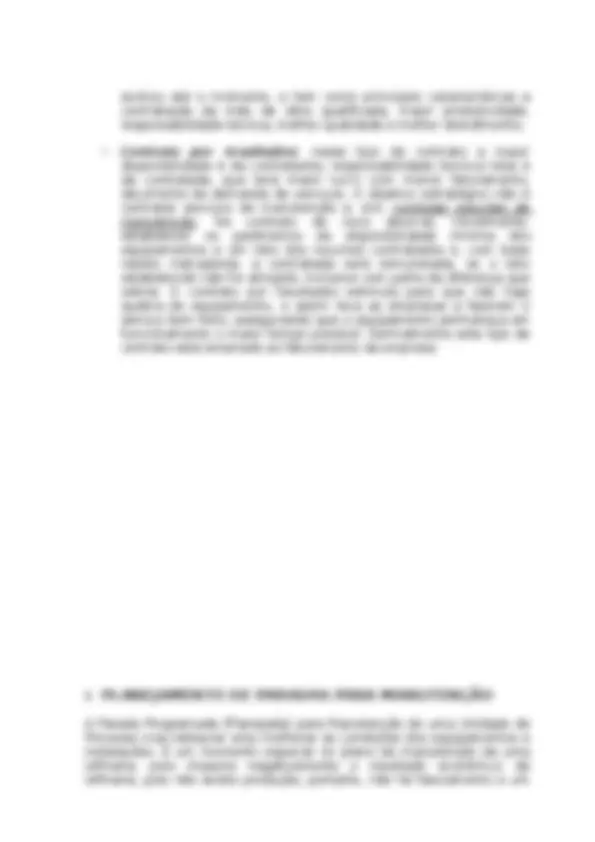
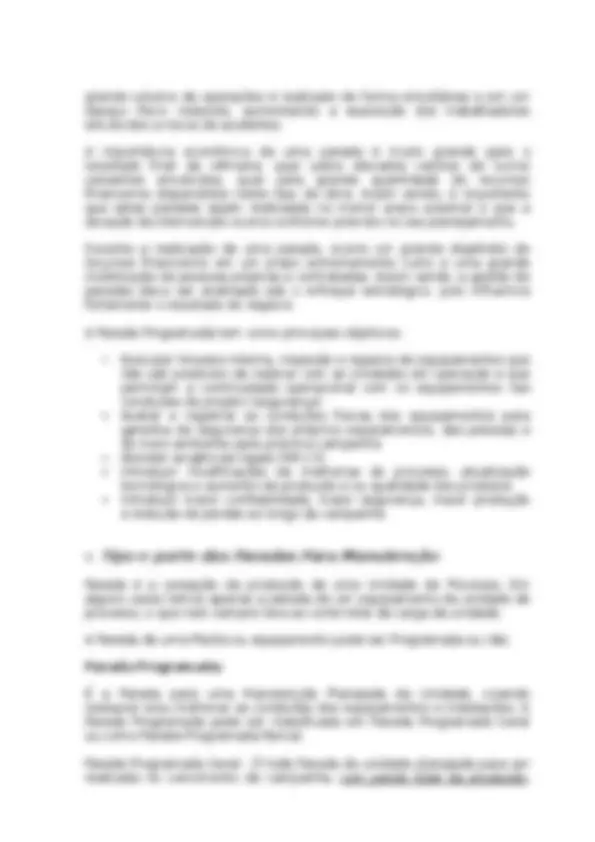
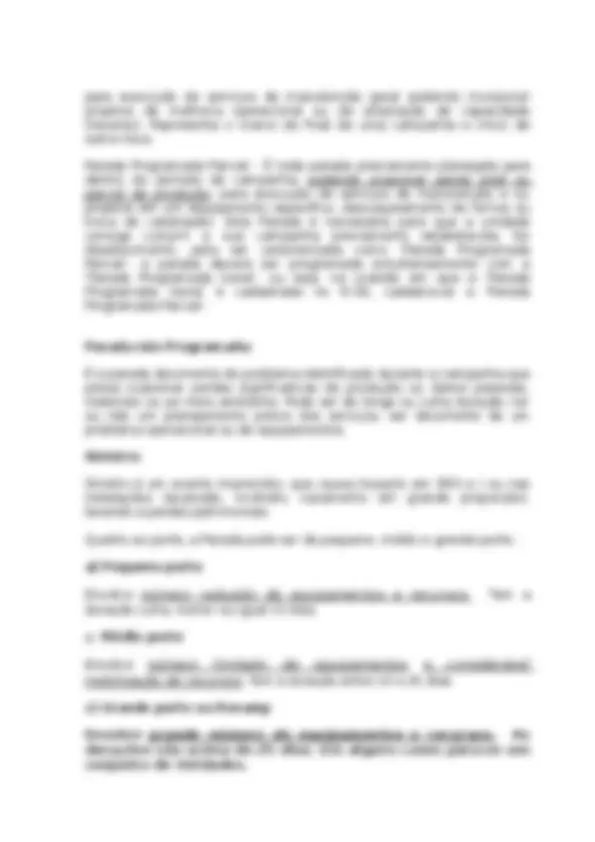
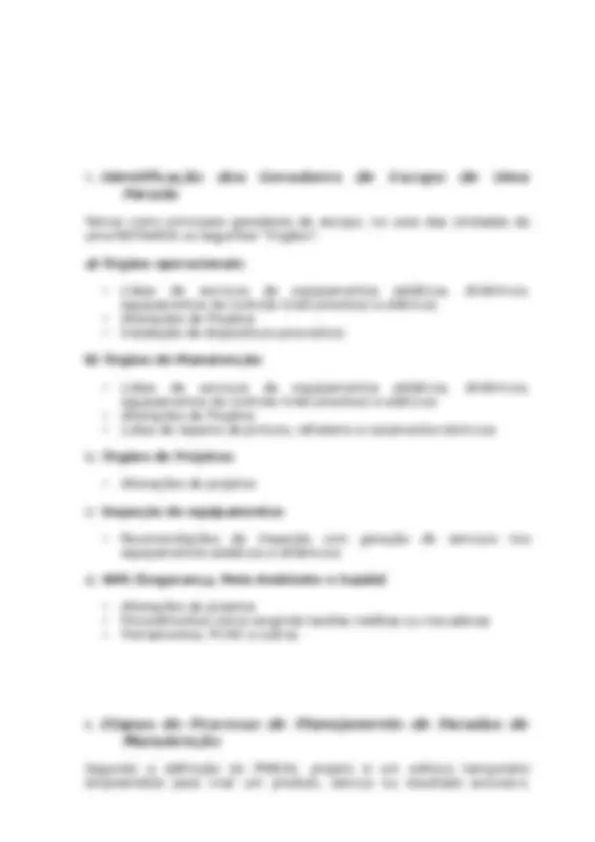
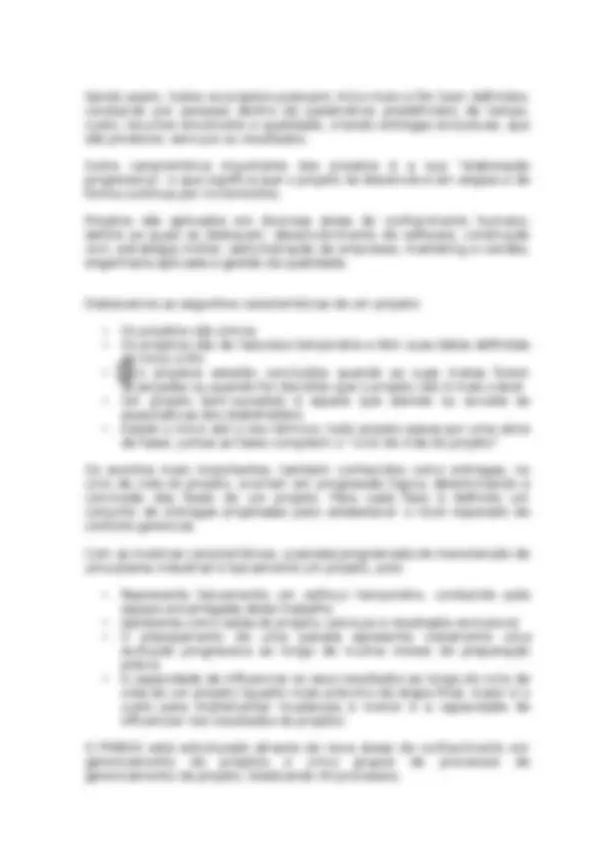
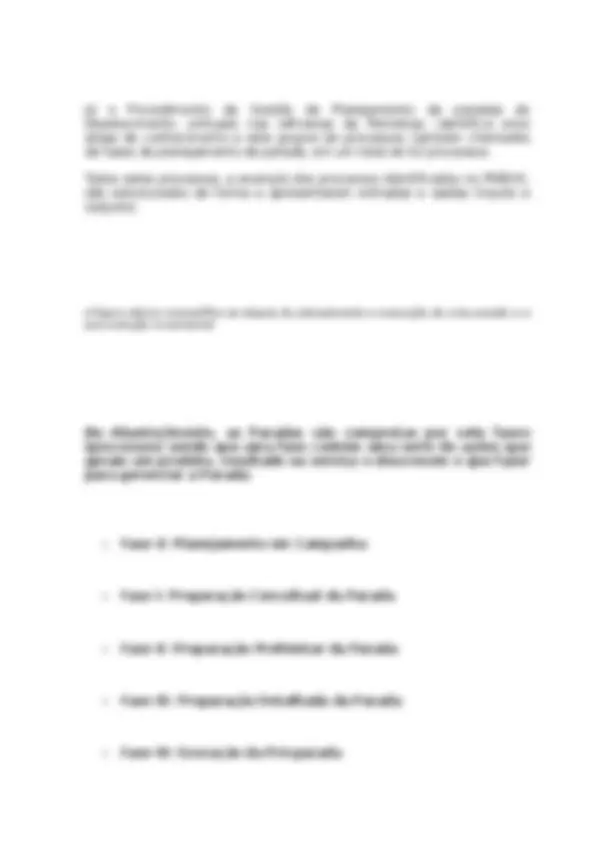
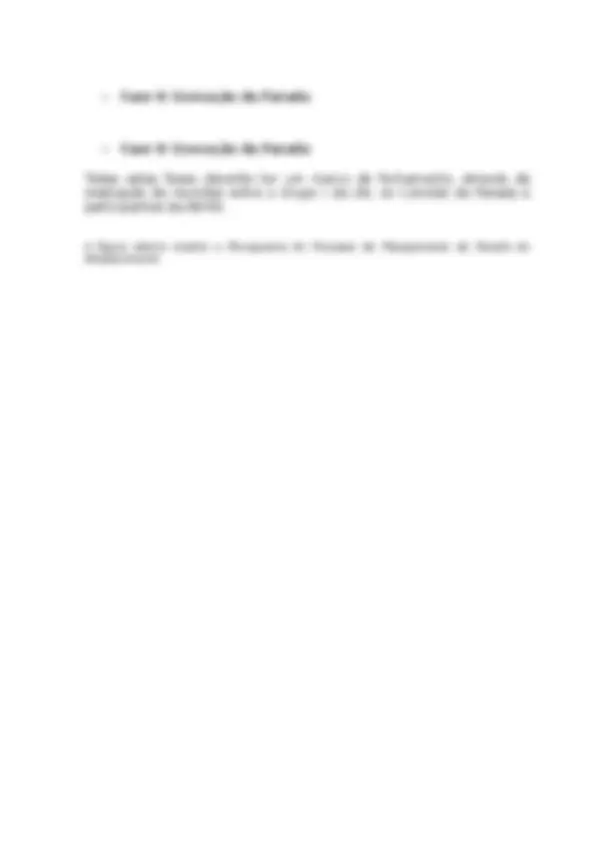
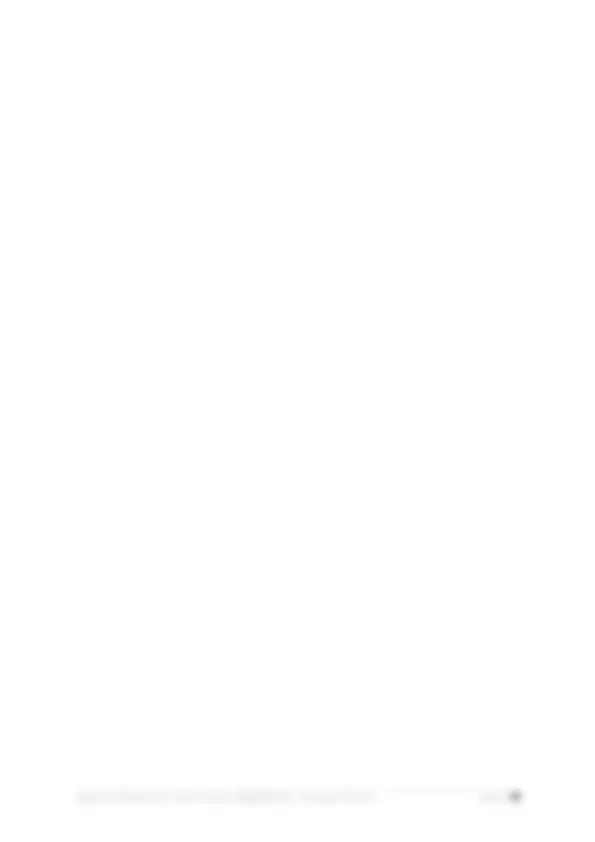
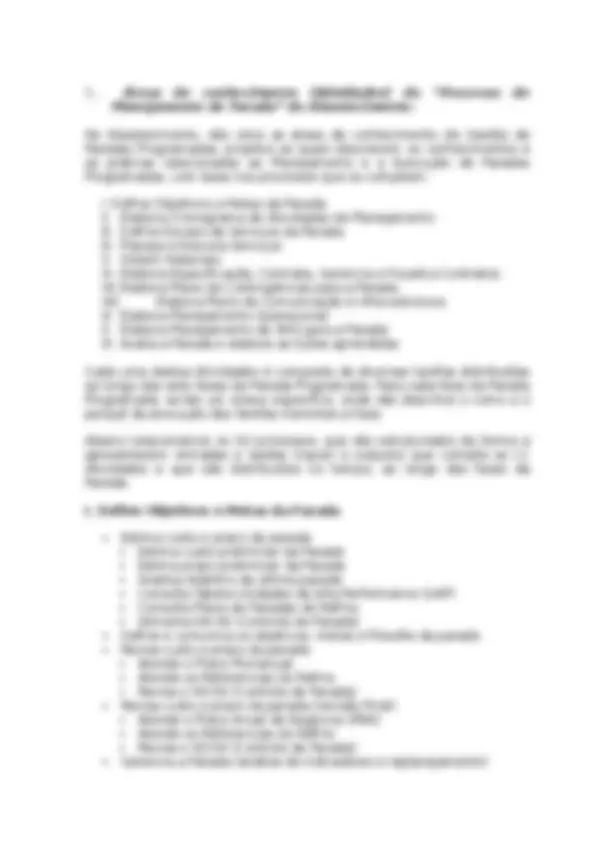
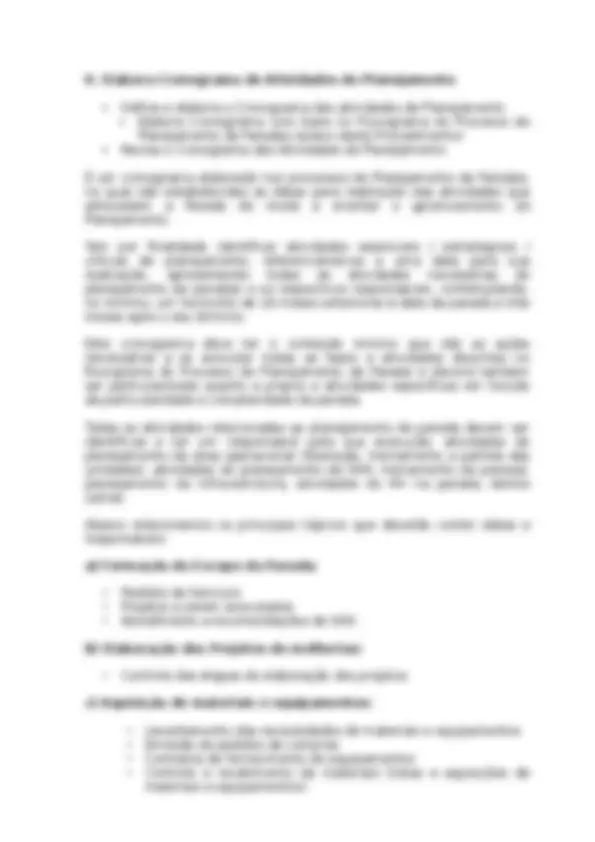
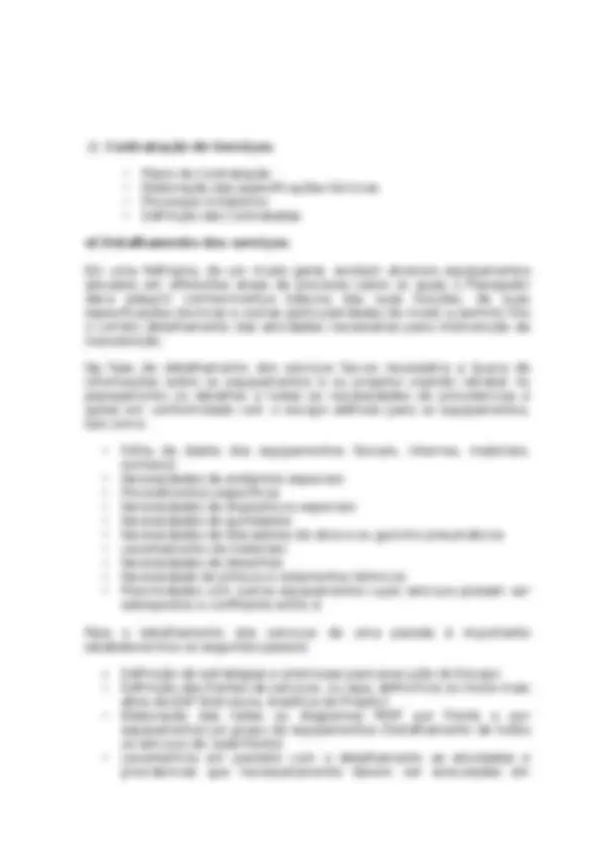
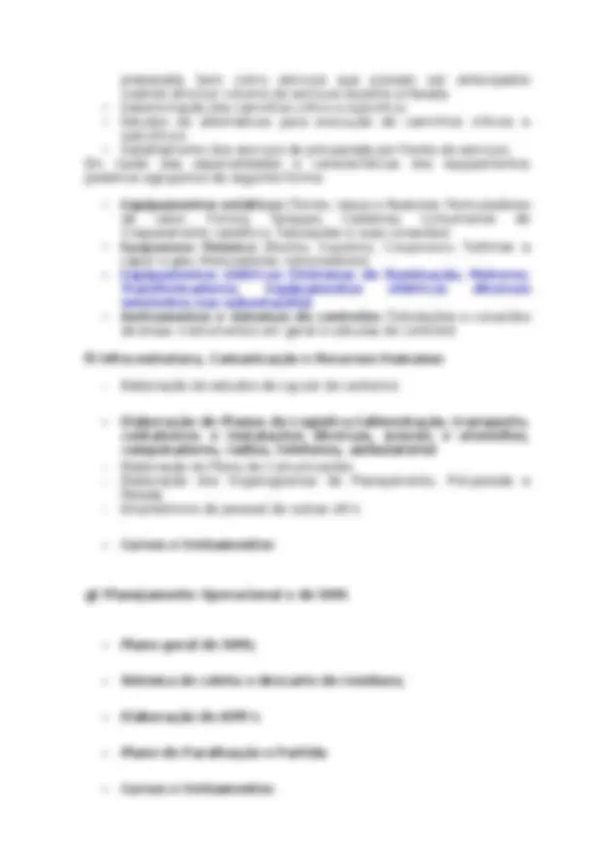
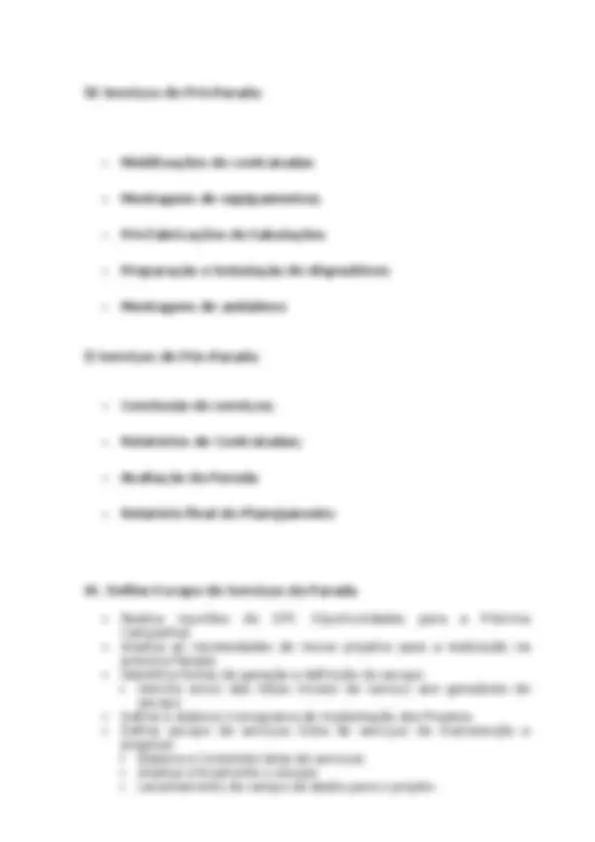
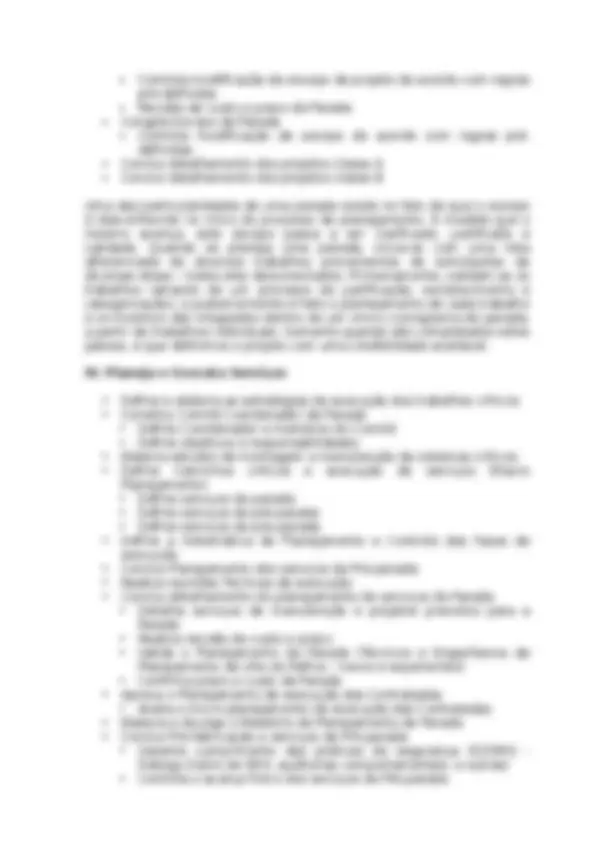
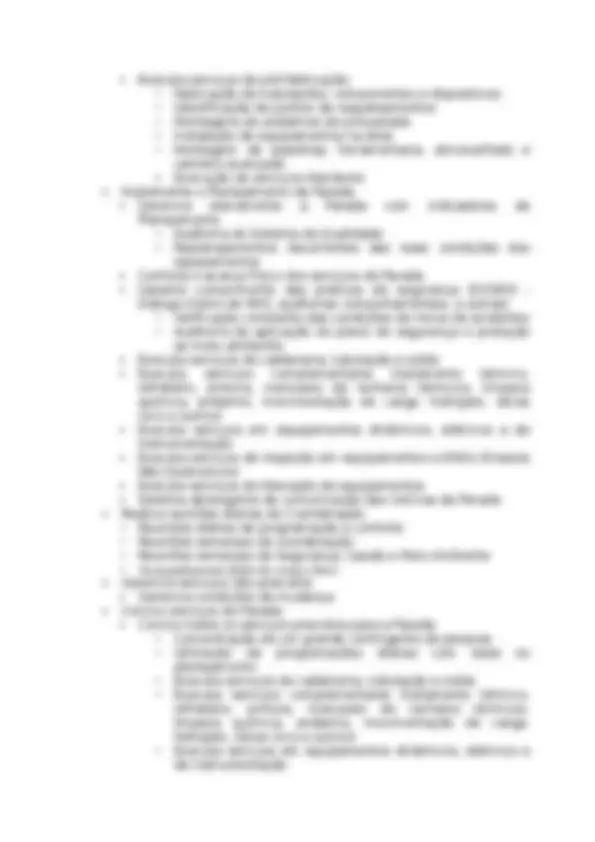
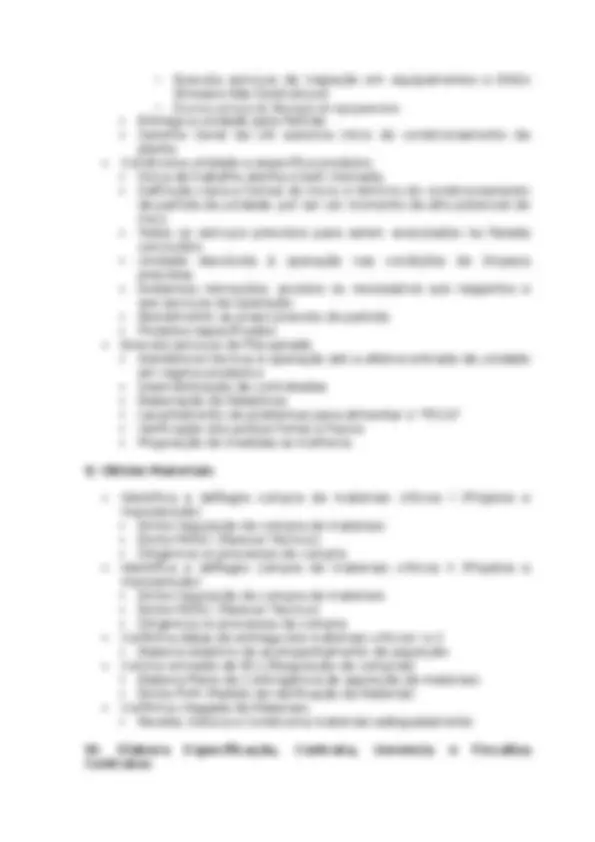
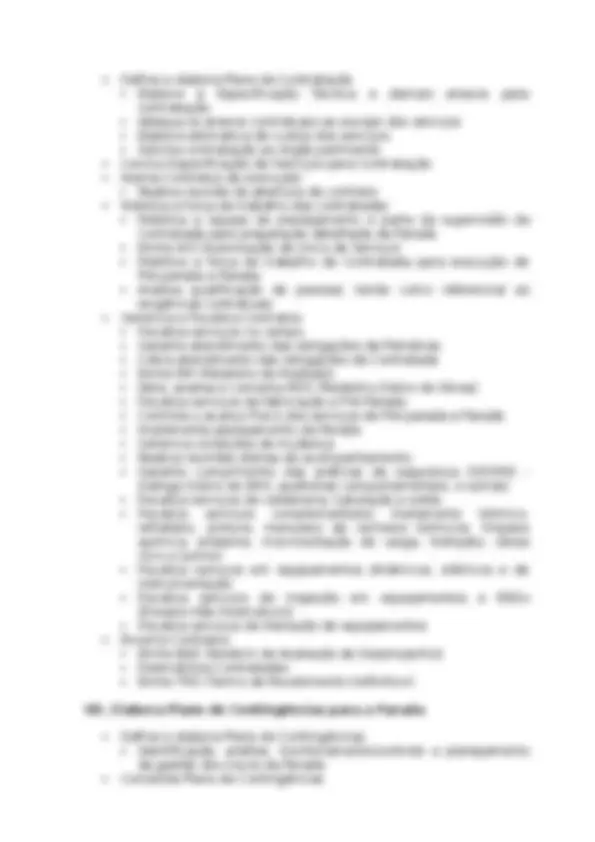
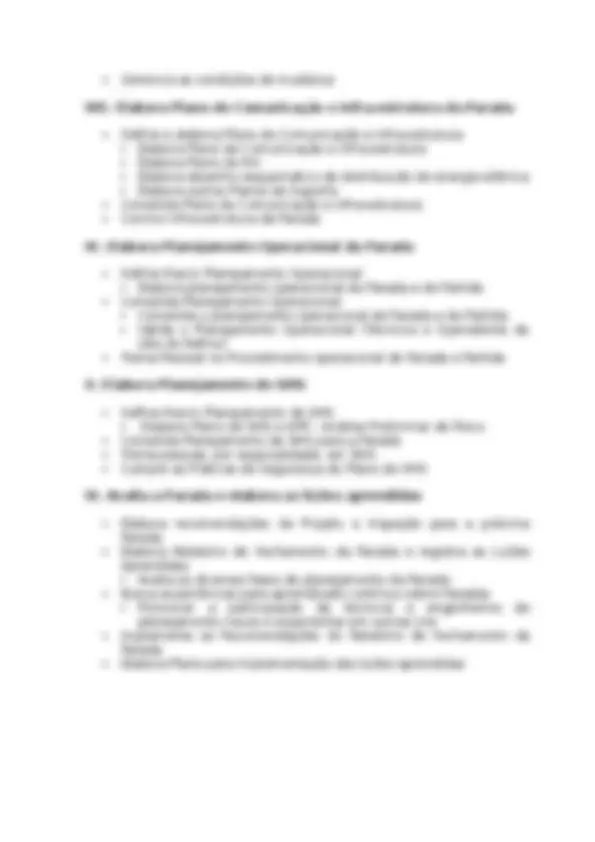
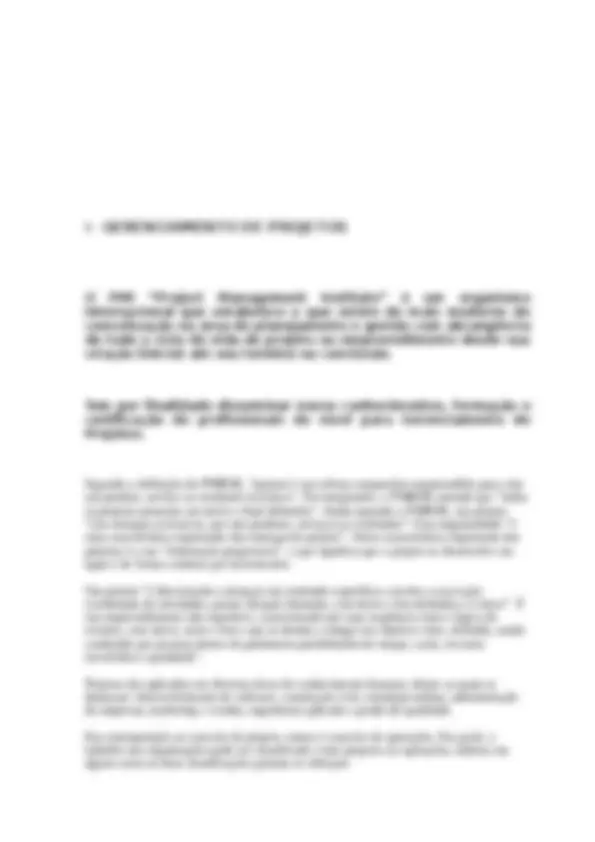
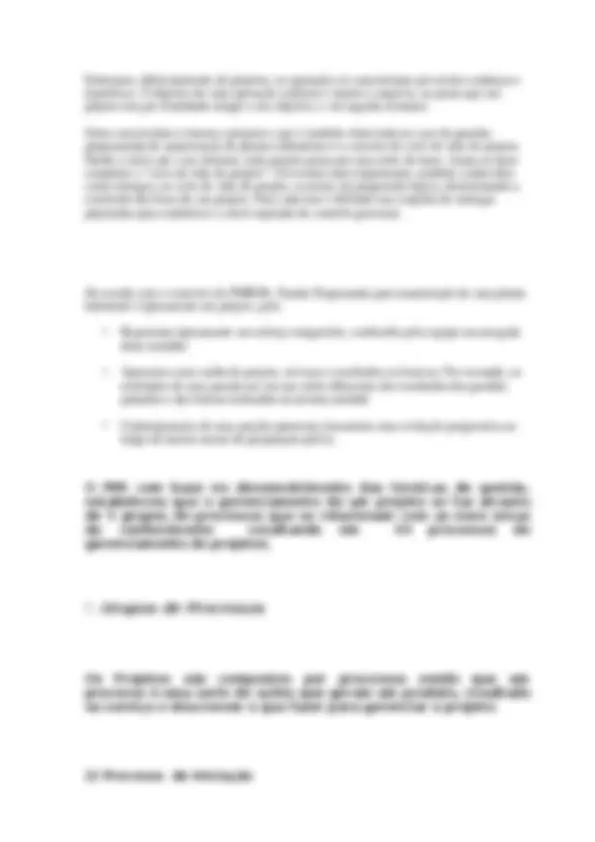
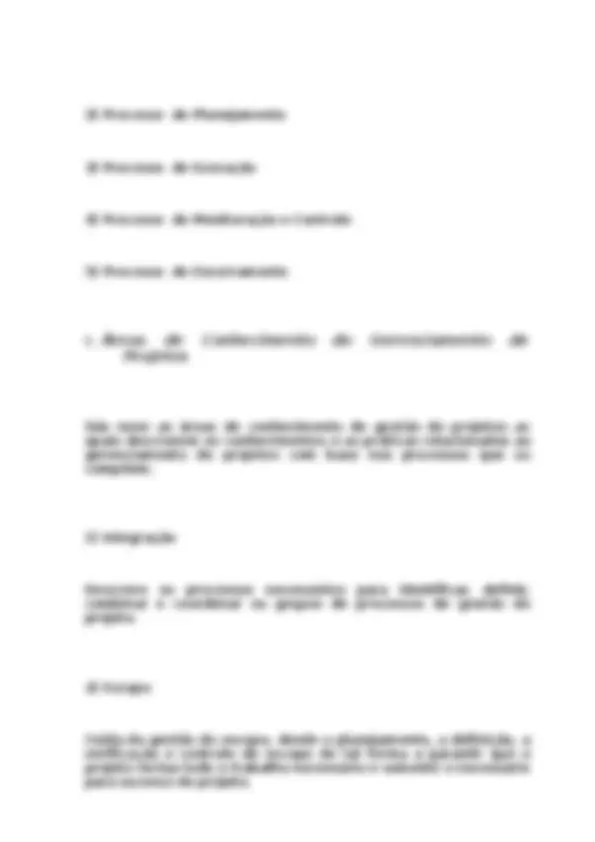
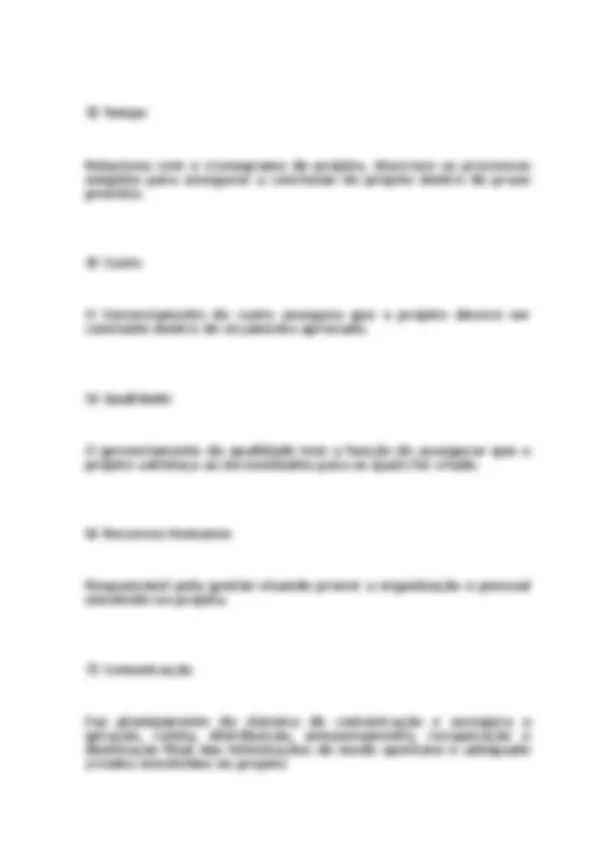
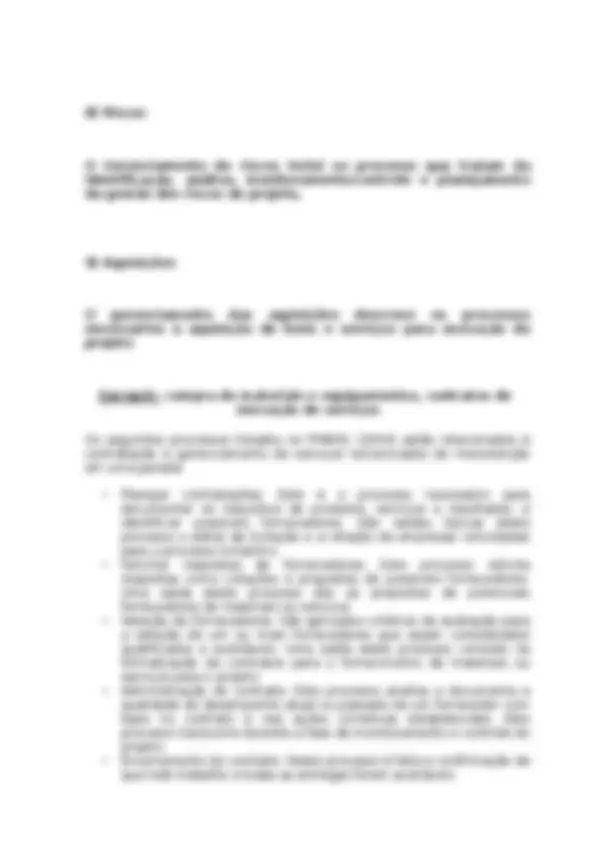
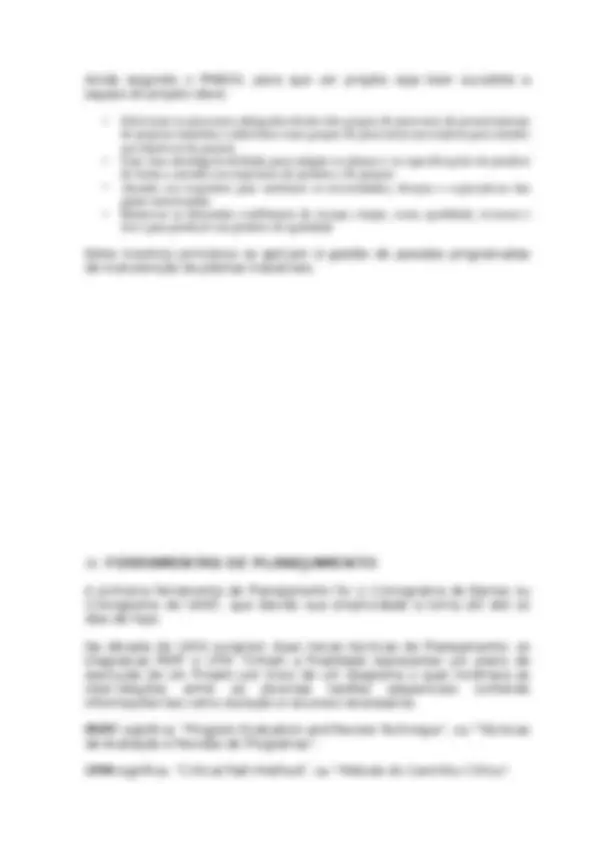
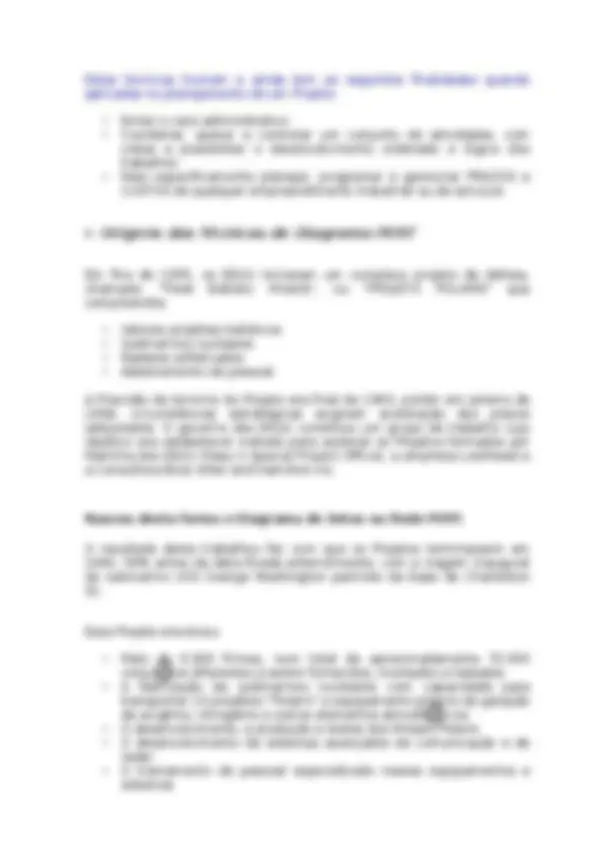
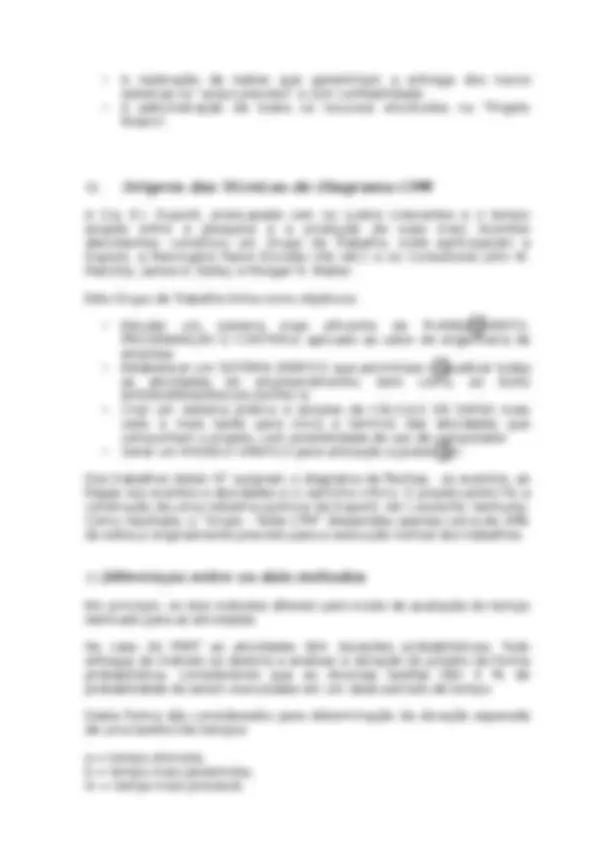
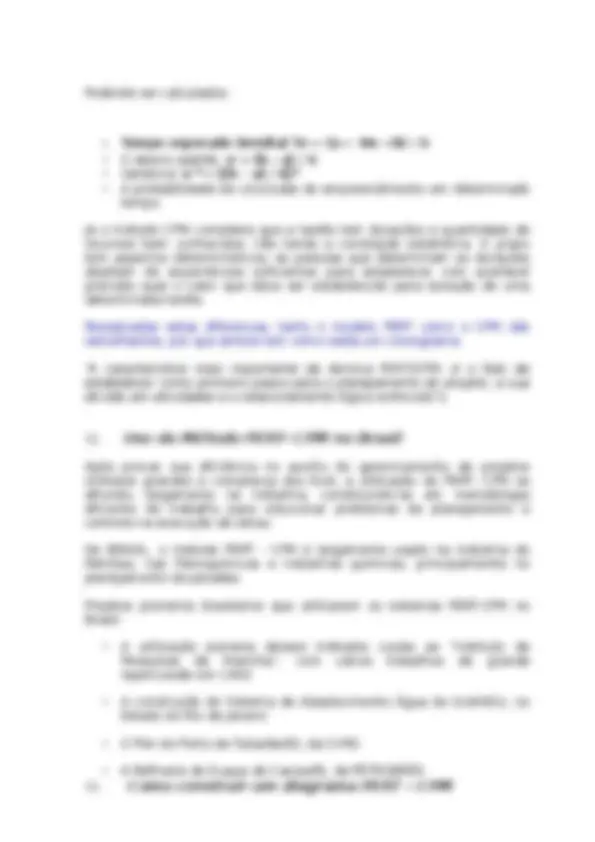
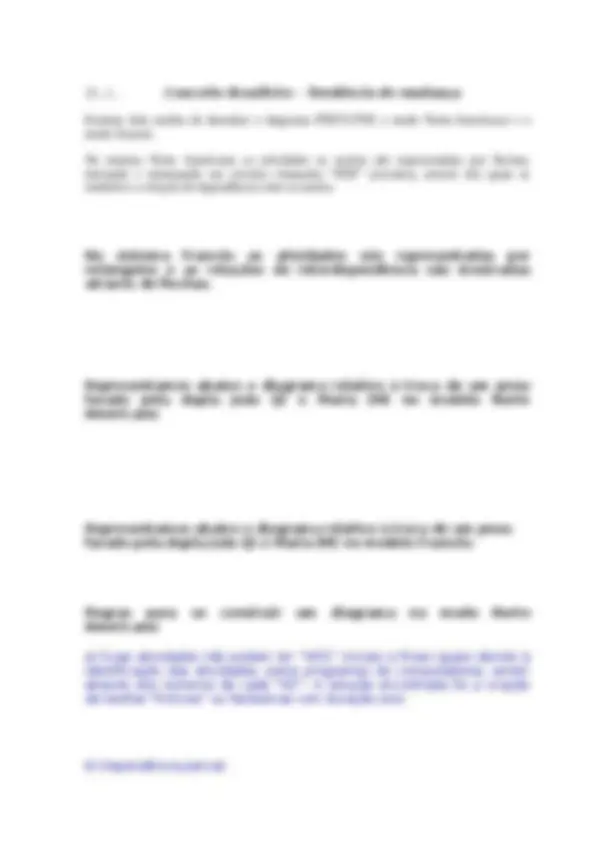
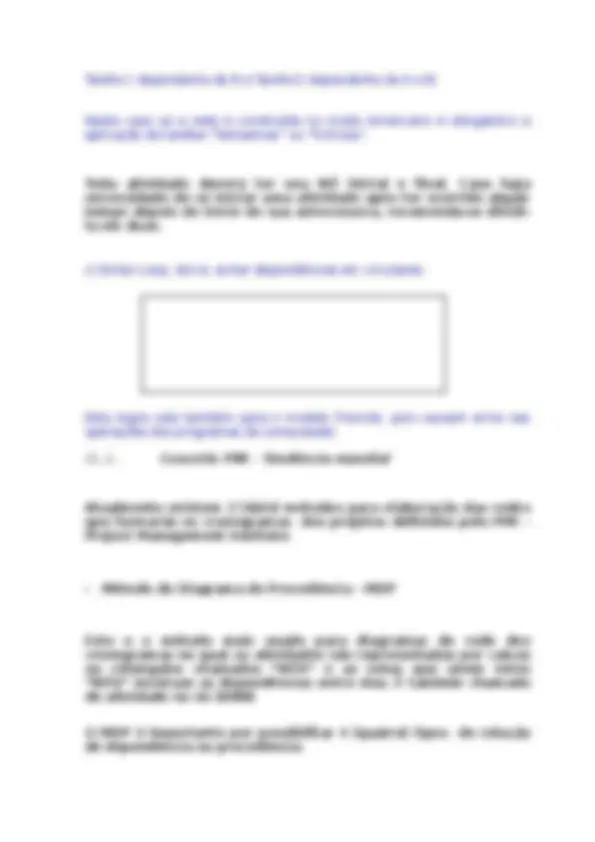
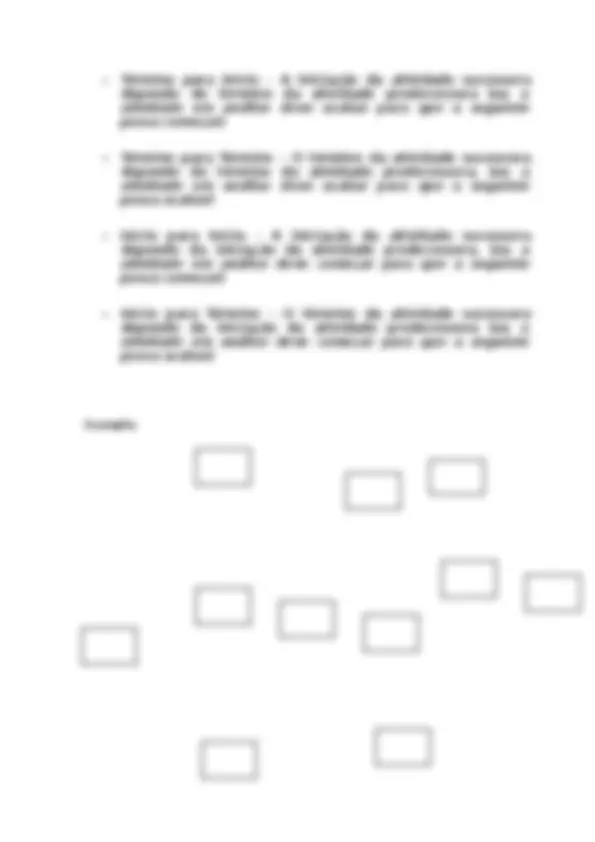
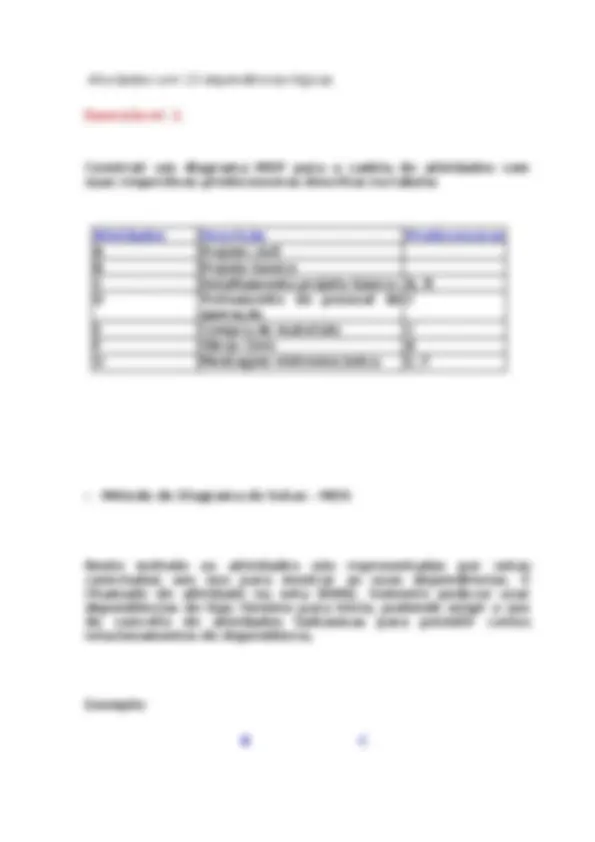
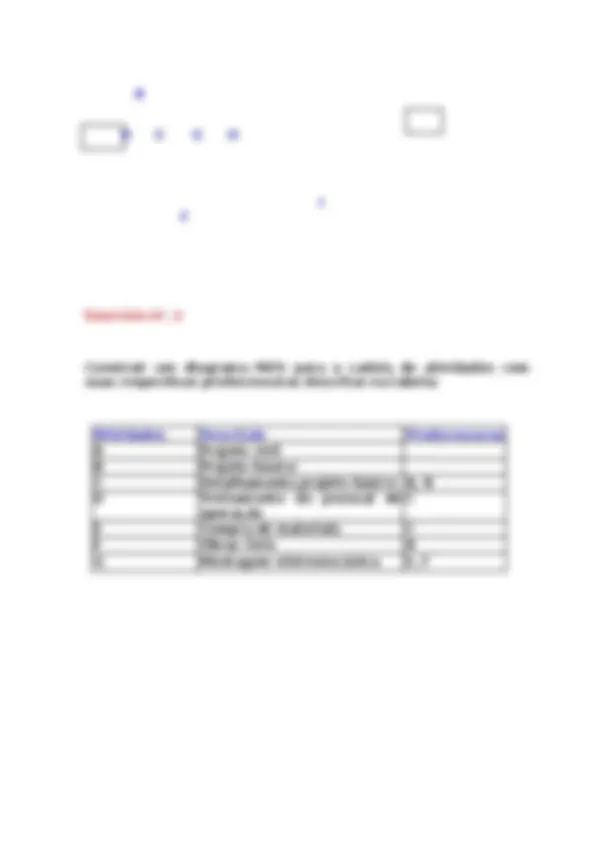
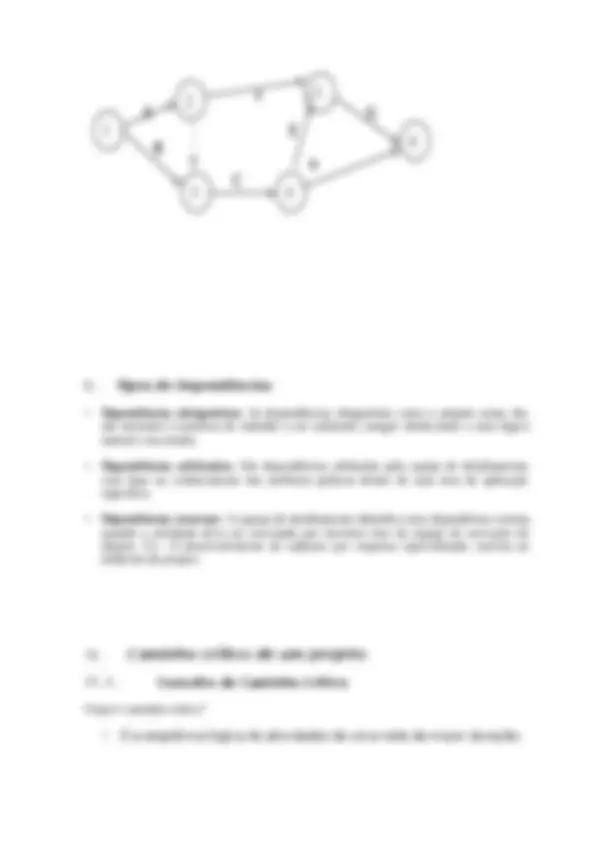
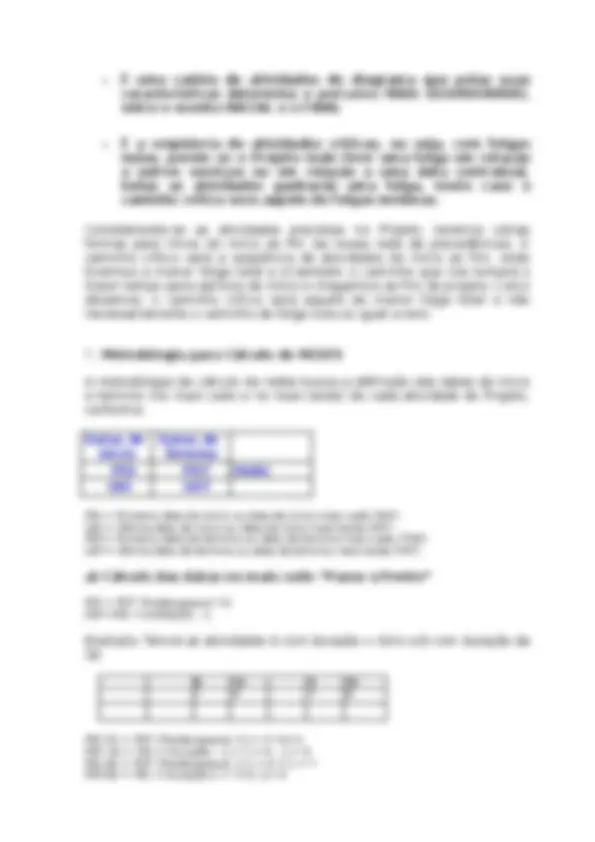
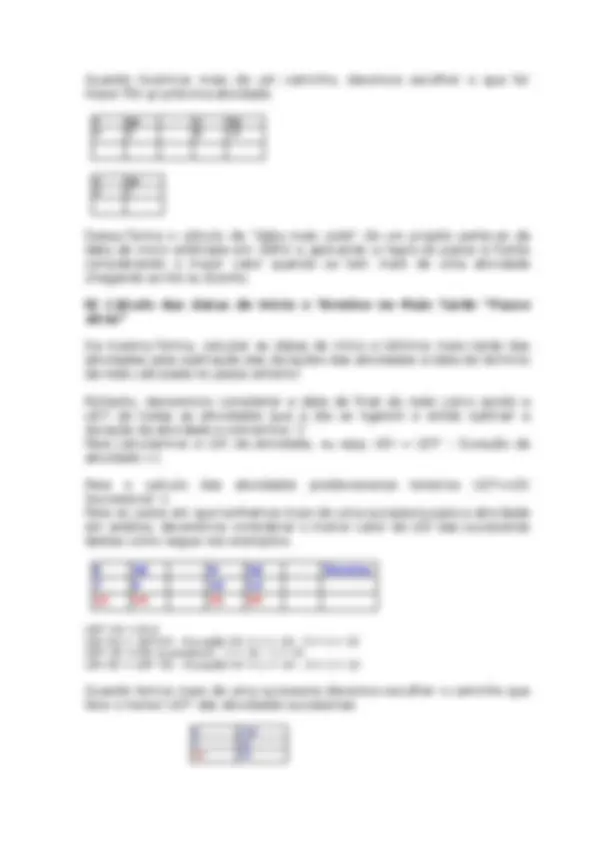
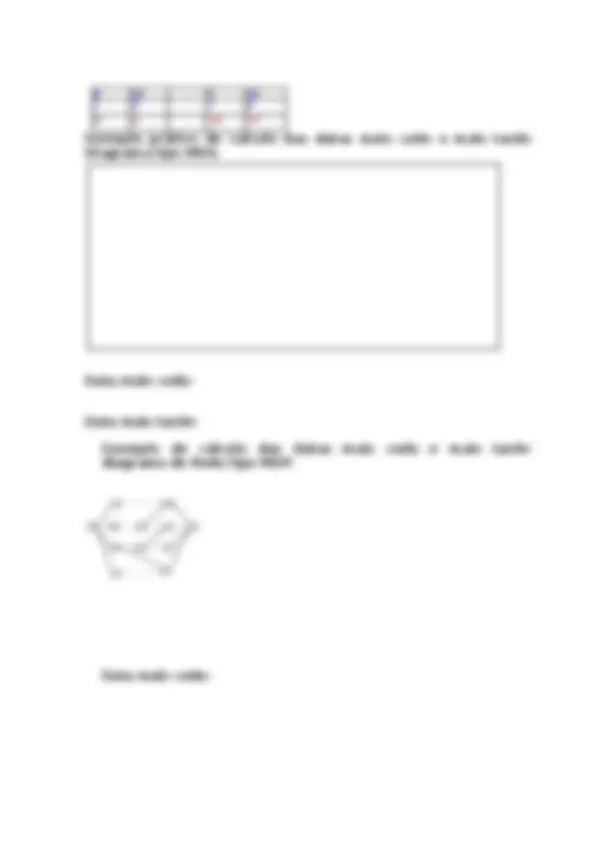
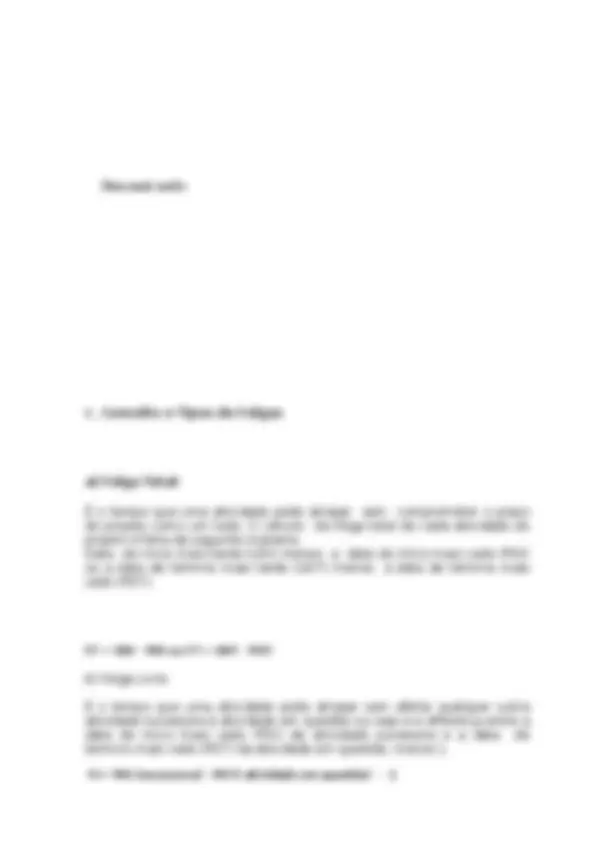

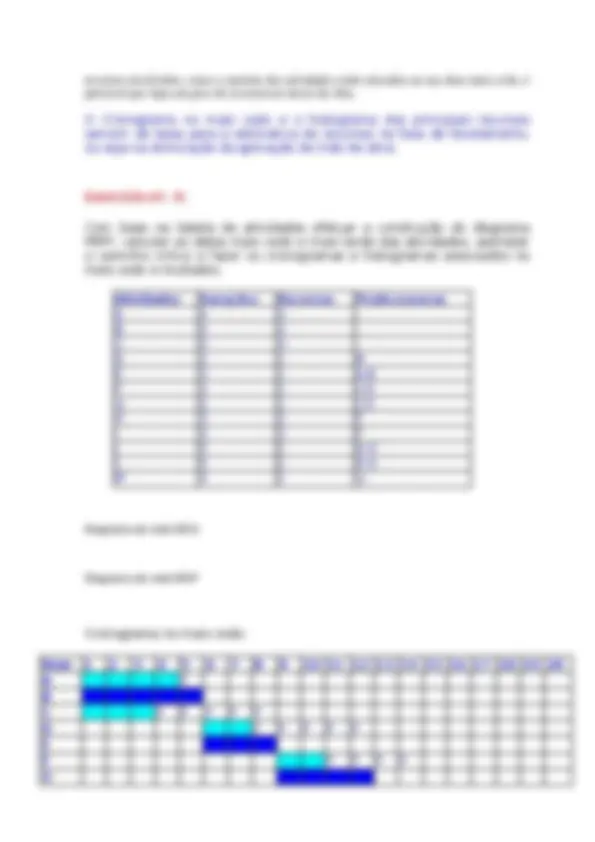
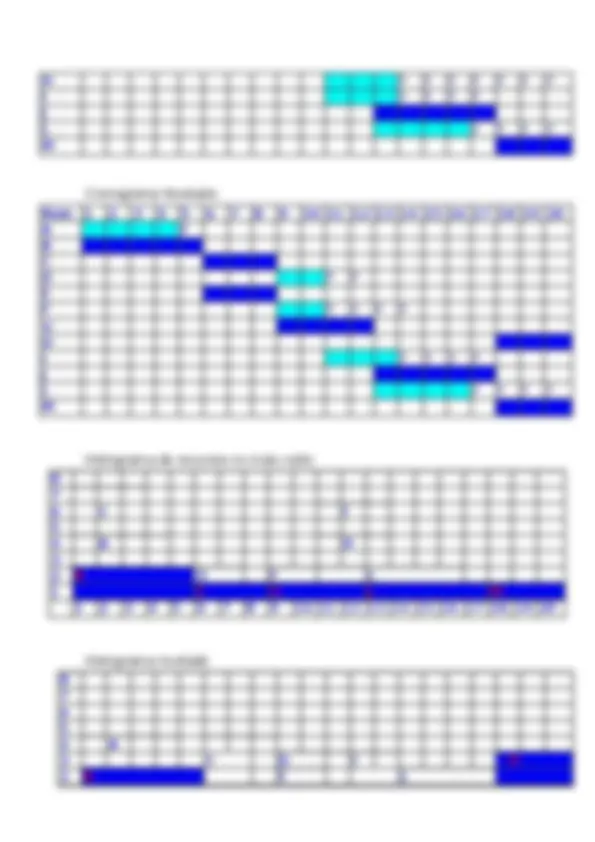
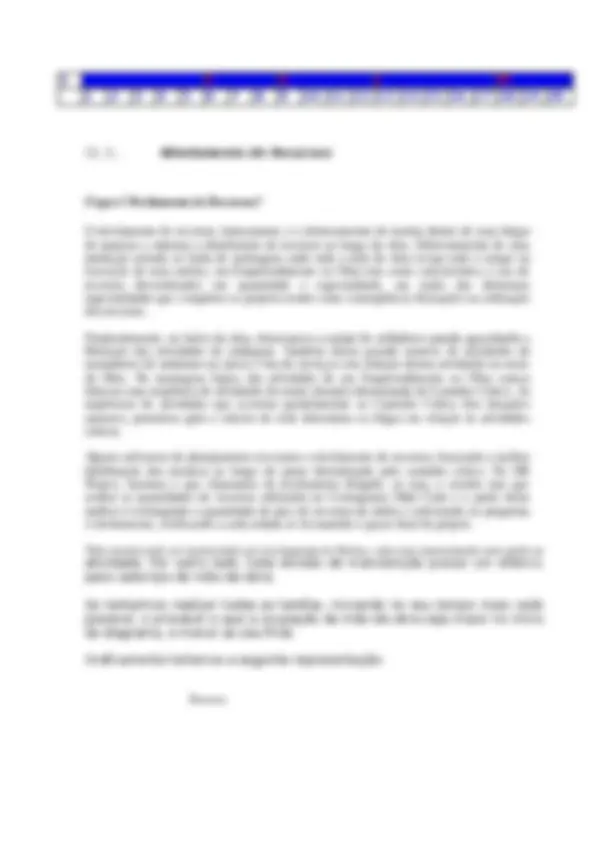
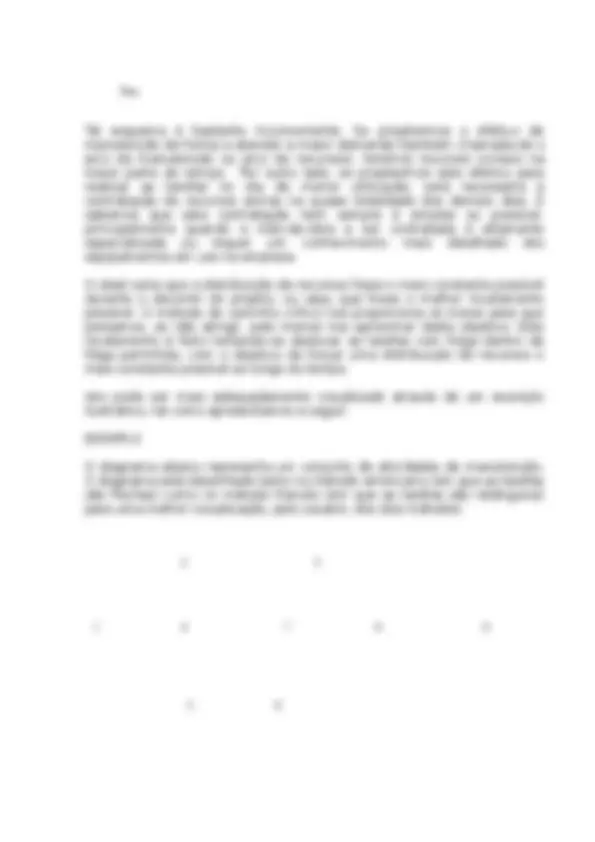
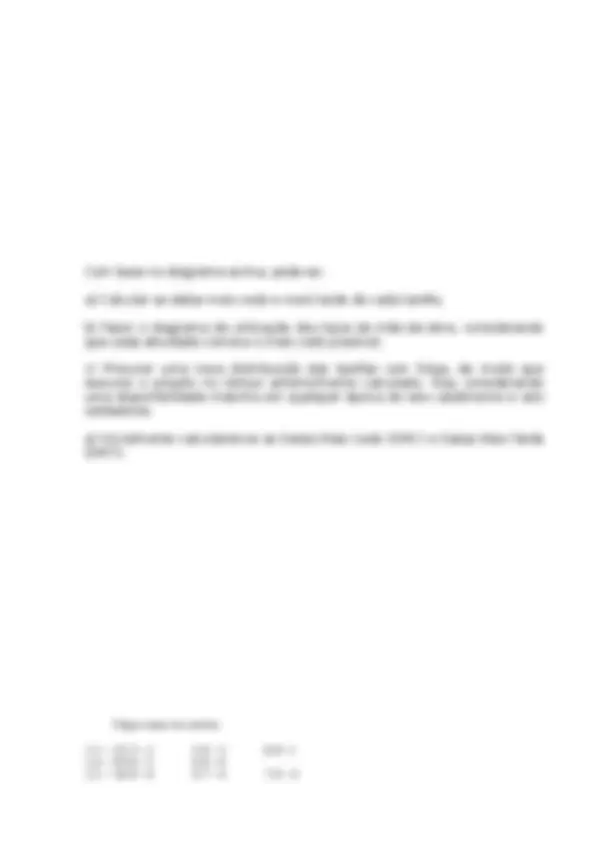
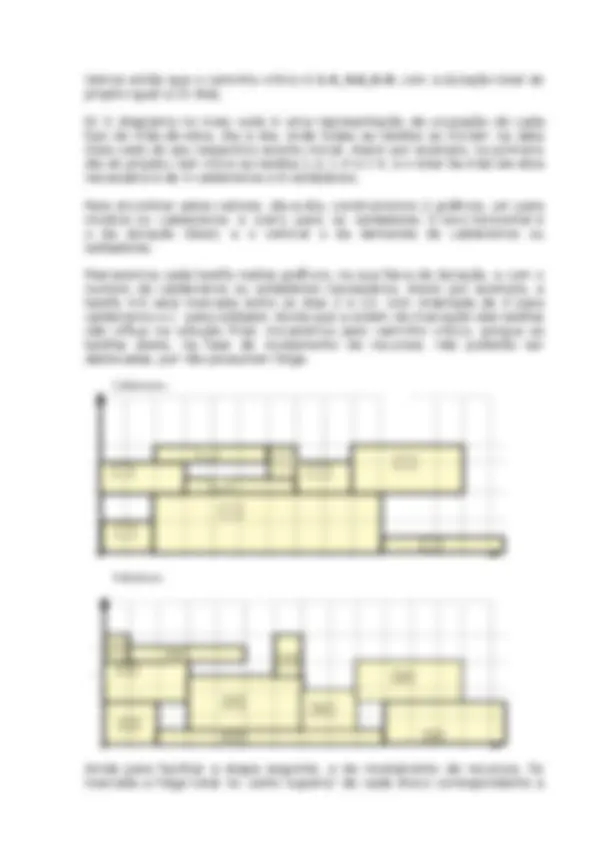
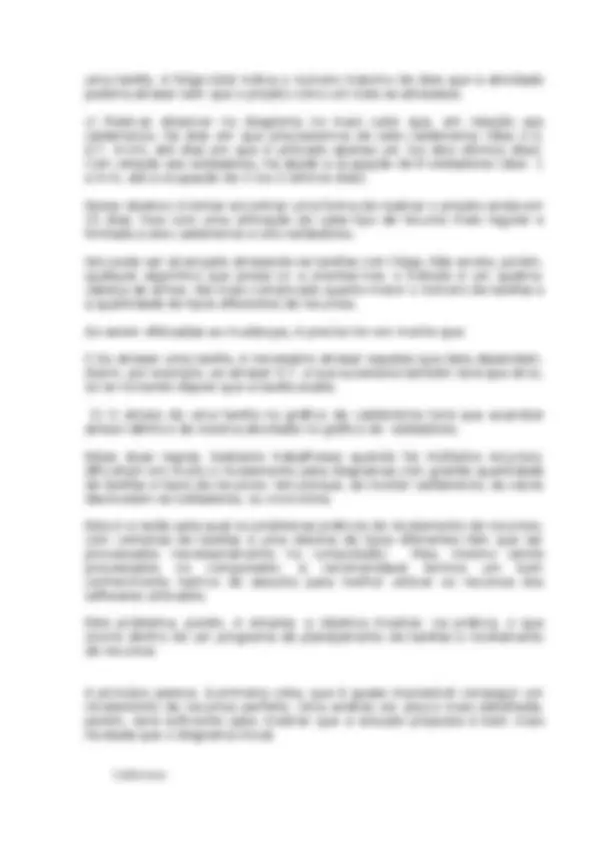
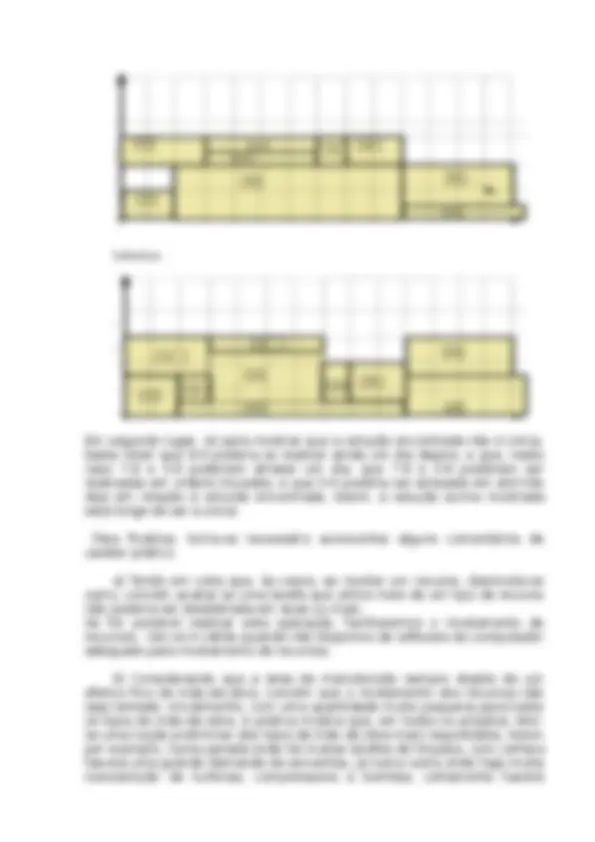
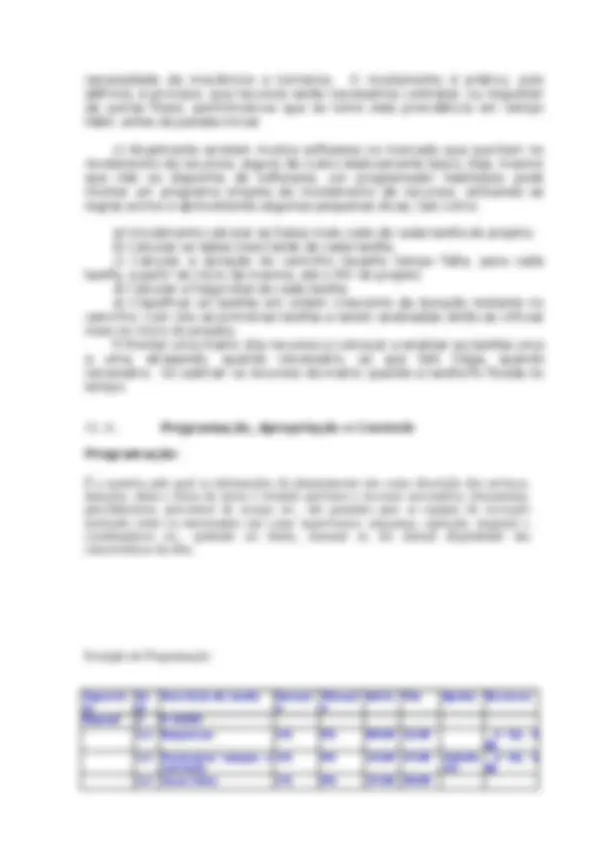
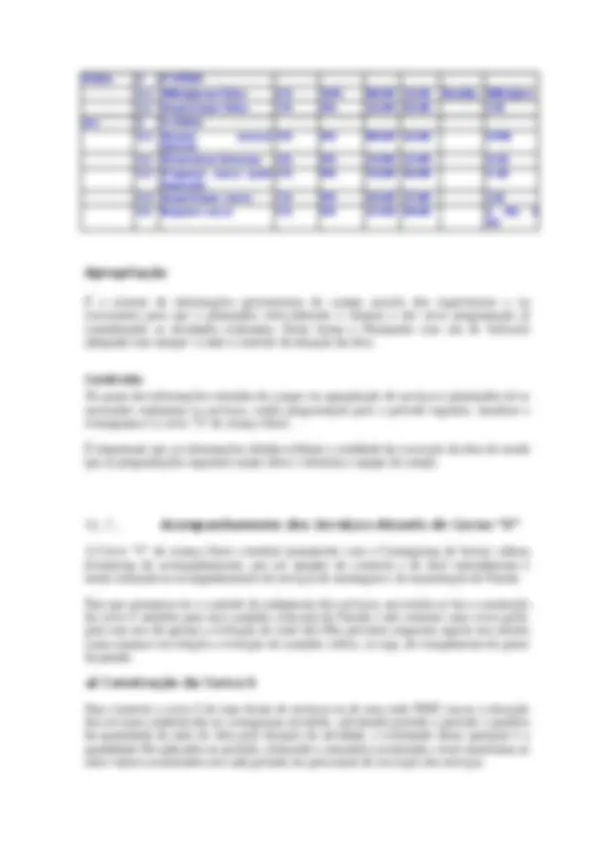
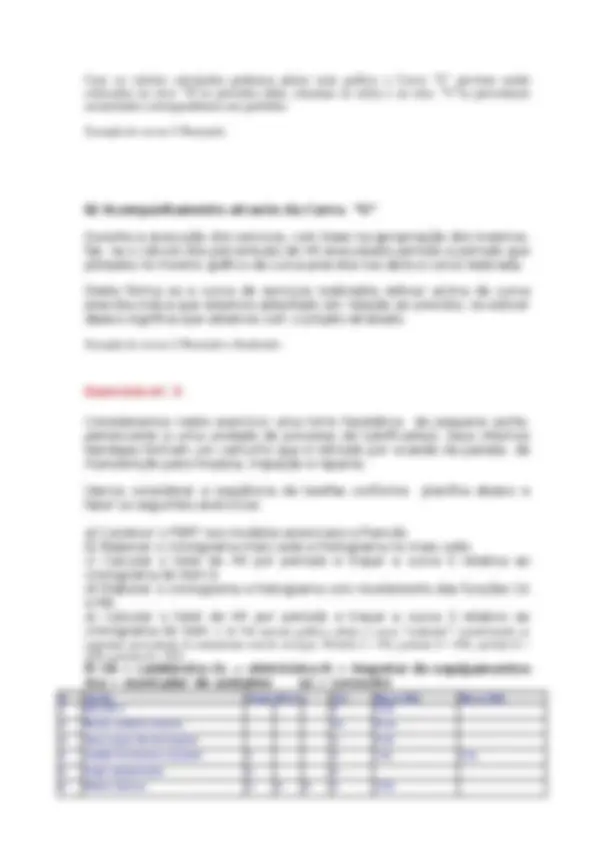
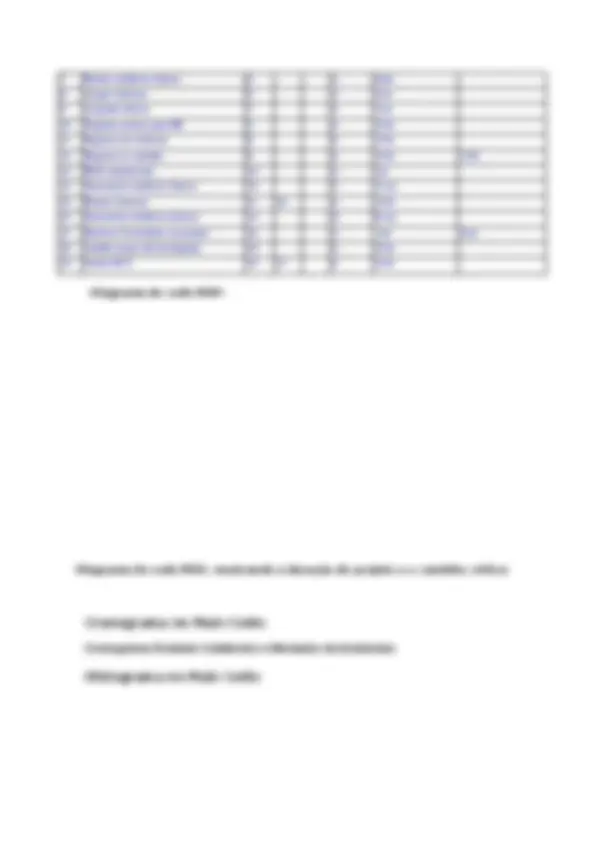
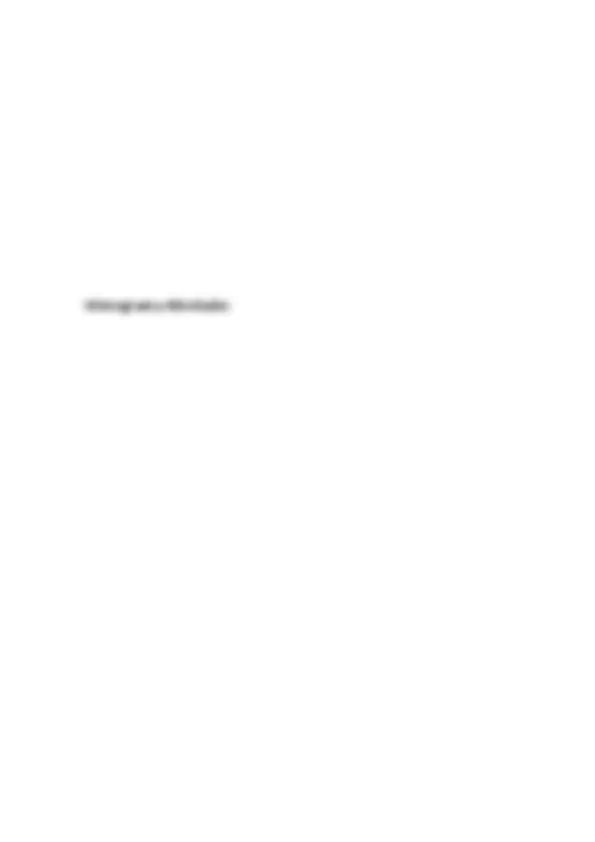
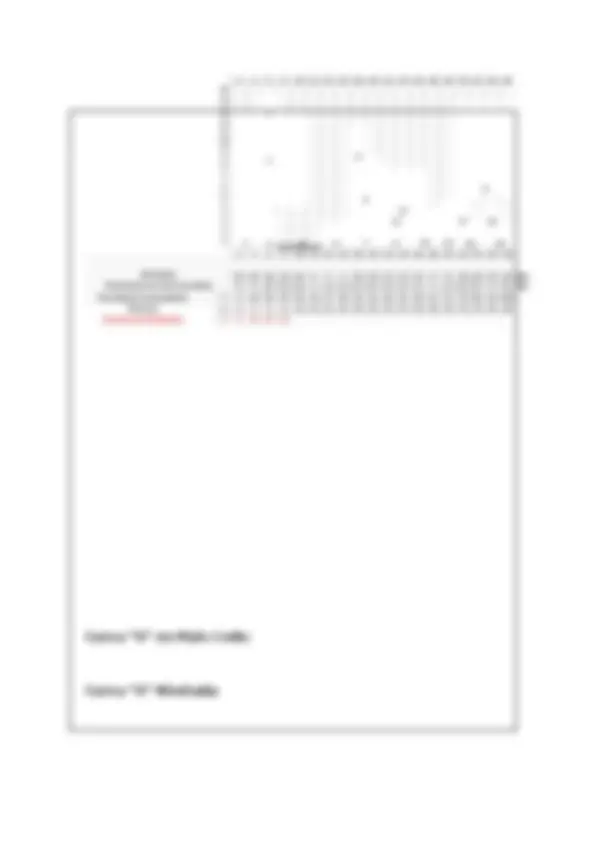
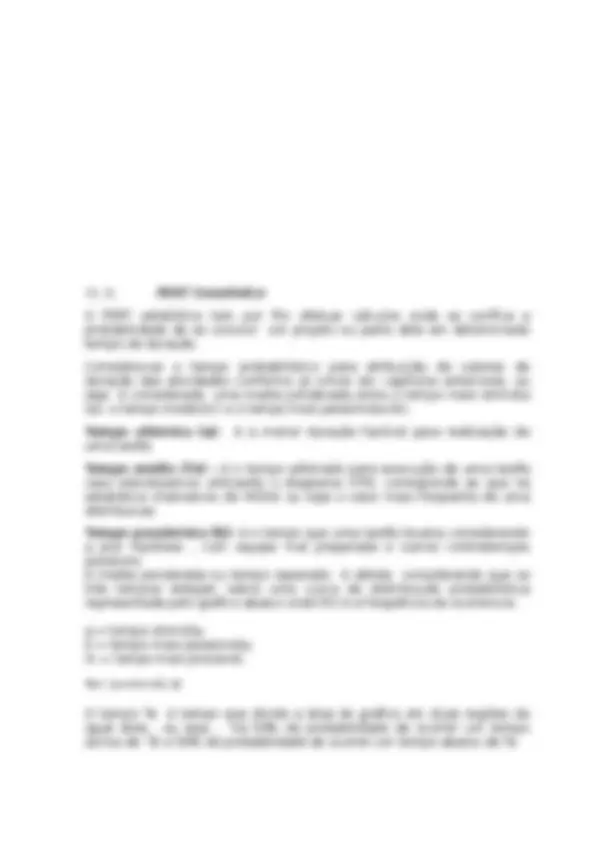
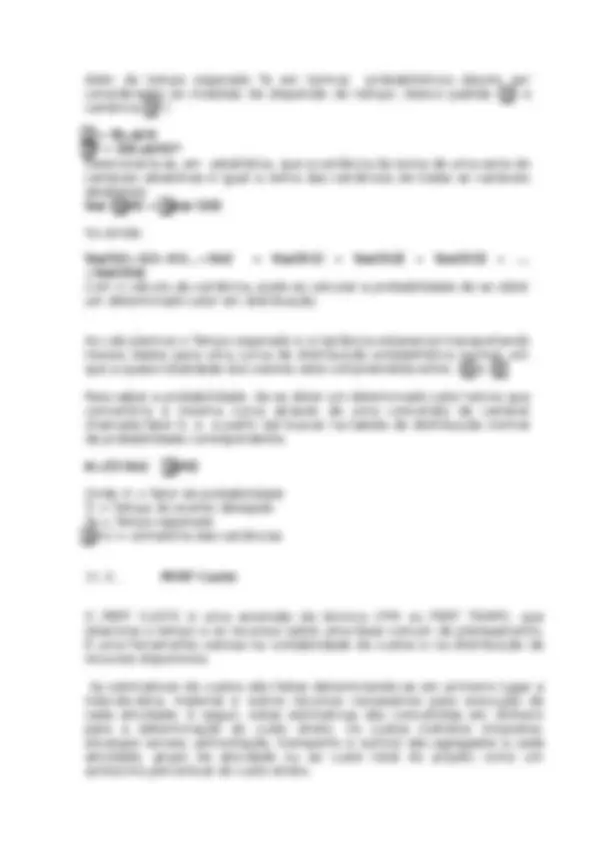
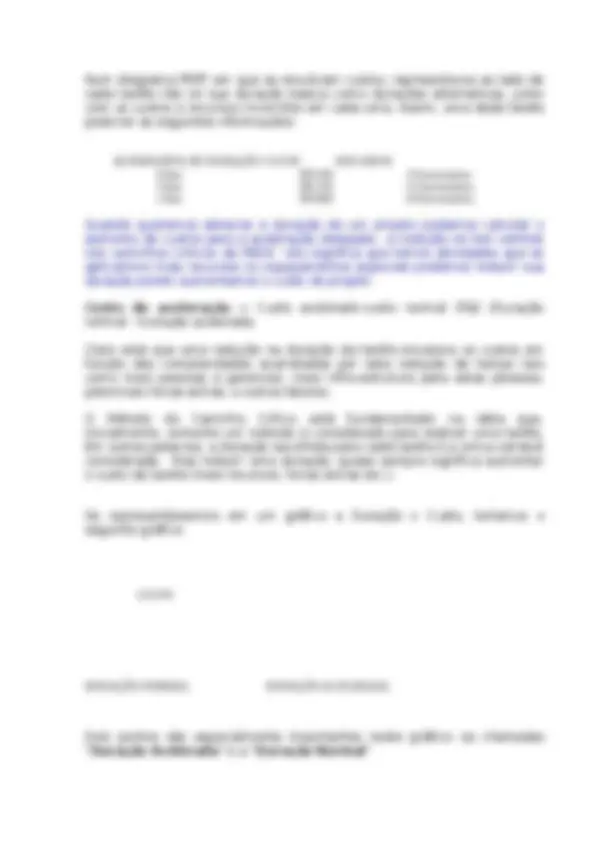

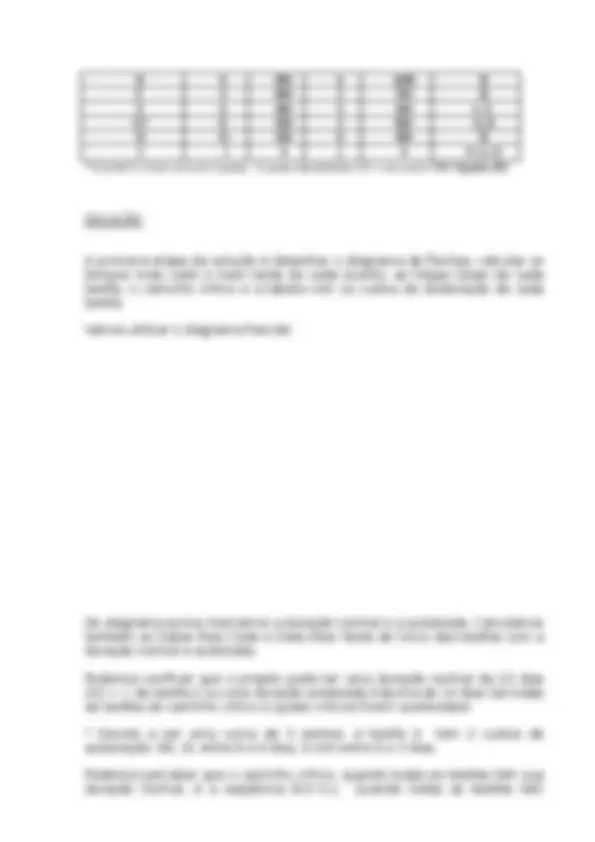
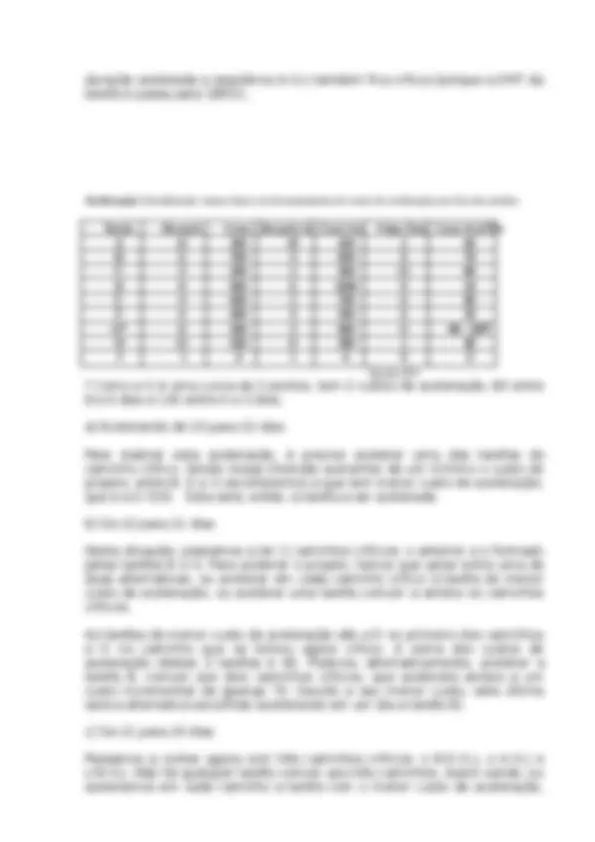
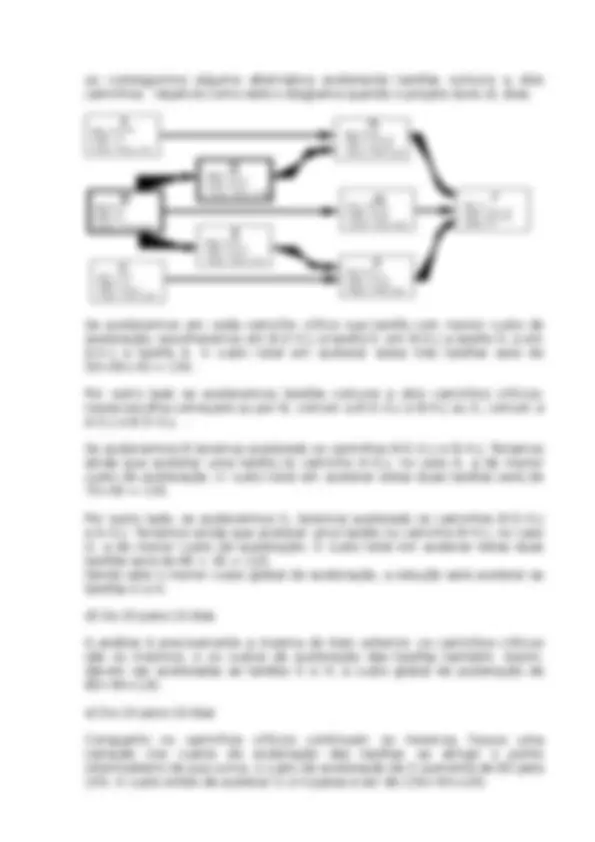
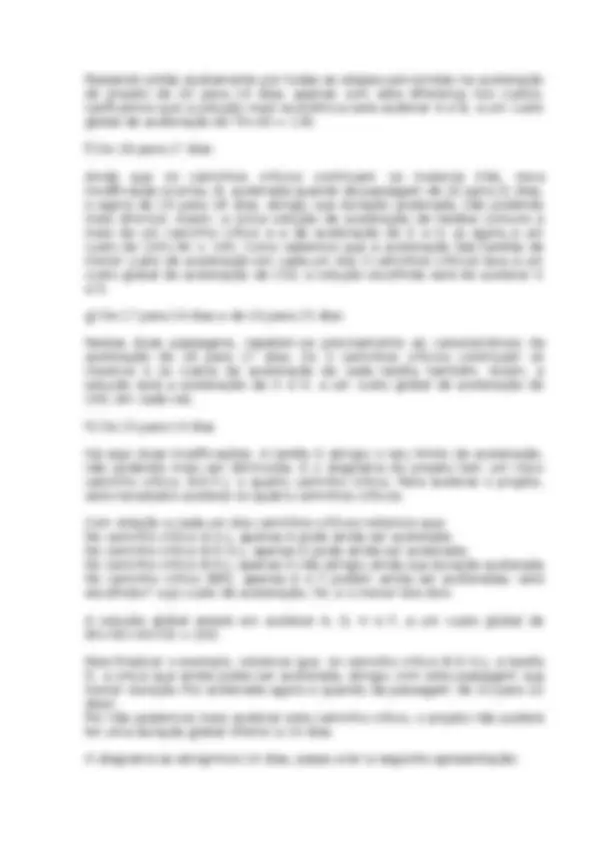
Estude fácil! Tem muito documento disponível na Docsity
Ganhe pontos ajudando outros esrudantes ou compre um plano Premium
Prepare-se para as provas
Estude fácil! Tem muito documento disponível na Docsity
Prepare-se para as provas com trabalhos de outros alunos como você, aqui na Docsity
Os melhores documentos à venda: Trabalhos de alunos formados
Prepare-se com as videoaulas e exercícios resolvidos criados a partir da grade da sua Universidade
Responda perguntas de provas passadas e avalie sua preparação.
Ganhe pontos para baixar
Ganhe pontos ajudando outros esrudantes ou compre um plano Premium
Comunidade
Peça ajuda à comunidade e tire suas dúvidas relacionadas ao estudo
Descubra as melhores universidades em seu país de acordo com os usuários da Docsity
Guias grátis
Baixe gratuitamente nossos guias de estudo, métodos para diminuir a ansiedade, dicas de TCC preparadas pelos professores da Docsity
pcp completa.
Tipologia: Notas de estudo
1 / 117
Esta página não é visível na pré-visualização
Não perca as partes importantes!
Um Mar de conhecimento
3.1 - Organização da Manutenção...................................................................................... 3.2 – Planejamento da Manutenção.................................................................................. 3.3 - Programação e controle da Manutenção.................................................................. 4 - CONFIABILIDADE E QUALIDADE NA MANUTENÇÃO............................... 5 - CUSTOS NA MANUTENÇÃO......................................................................... ....... 6 – INDICADORES DE MANUTENÇÃO................................................................... 7 - TERCEIRIZAÇÃO DE SERVIÇOS NA MANUTENÇÃO................................. 8 - PLANEJAMENTO DE PARADAS PARA MANUTENÇÃO.............................. 8.1 - Tipo e porte das Paradas Para Manutenção.............................................................. 8.2 - Identificação dos Geradores de Escopo de Uma Parada.......................................... 8.3 - Etapas do Processo de Planejamento de Paradas de Manutenção............................ 9 - GERENCIAMENTO DE PROJETOS................................................................... 9.1 - Grupos de Processos................................................................................................ 55 9.2 - Áreas de Conhecimento do Gerenciamento de Projetos.......................................... 10 - FERRAMENTAS DE PLANEJAMENTO........................................................... 10.1 - Origens das Técnicas de Diagrama PERT............................................................. 10.2 - Origens das Técnicas do Diagrama CPM.............................................................. 10.3 - Diferenças entre os dois métodos........................................................................... 10.4 - Método PERT- CPM no Brasil..............................................................................
basicamente, a qualidade dos produtos finais e a produtividade dos processos.
É preciso primeiro pensar na função manutenção dentro do fluxo produtivo para depois se alocar tarefas e responsabilidades a pessoas ou órgãos de uma empresa.
Atividades Desenvolvidas pelo Órgão de Manutenção segundo o Documento Nacional
Na nossa cultura administrativa, as empresas são divididas em células organizacionais ou órgãos internos. A maneira mais comum de se efetuar estas subdivisões é a funcional. Assim as diferentes funções dentro da empresa ficam a cargo de diferentes órgãos, tais como:
Dependendo do porte de cada empresa, tais órgãos têm tamanhos diversos e podem, inclusive, abrigar mais de uma função. A definição exata das atividades englobadas em cada função também varia conforme a empresa. No entanto, com esse sistema, barreiras são inconscientemente criadas entre os órgãos, dificultando o relacionamento e a cooperação, tornando-os cada vez mais estanques.
Mais recentemente, a implantação da filosofia de gestão pela Qualidade Total, dando ênfase nos processos e pregando a participação de todos os empregados em todos os assuntos da empresa, tem se mostrado como uma forma de reagir a esta rigidez. Esta filosofia encara primeiramente
as atividades e funções e depois analisa como seria a melhor forma de executá-las na empresa, independentemente da chamada estrutura hierárquica. Uma vez que ainda não se encontrou substituto (pelo menos consagrado) para o organograma, depois de avaliada a função manutenção e seus processos distribuem-se as atividades pelos órgãos da empresa.
As atividades de manutenção podem ser subdivididas em tarefas mais simples e básicas, tais como:
Muitas destas tarefas, justamente por serem básicas, não diferem muito nos seus conceitos fundamentais, daquelas realizadas por outros órgãos funcionais de uma empresa.
Na verdade a composição das atividades da manutenção com estas tarefas se dá de forma matricial. Exemplificando: a apuração de custos envolve manutenção de instalações industriais, oficina de apoio, limpeza, etc. e, analogamente, a manutenção das instalações se desdobra em apuração de custos, atualização de histórico, especificação de materiais, etc.
Para que se tenha um completo conhecimento e domínio da manutenção, é preciso definir corretamente as atividades envolvidas, as tarefas e seu relacionamento, ou seja, definir e desdobrar os processos da função manutenção.
Na fase de projeto os principais fatores são a confiabilidade e a manutenabilidade, os quais devem ser correlacionados com o custo inicial, o desempenho e o custo operacional. Na fase de instalação a manutenabilidade continua a ser um fator importante, porque aí começa a se revelar a natureza multidimensional da maioria dos problemas de manutenção.
A fase de partida, por sua vez, não é apenas um período de teste de desempenho técnico, mas também um período de aprendizagem onde as principais deficiências do projeto que possam afetar a disponibilidade do
A missão da manutenção é garantir a disponibilidade dos equipamentos e instalações de modo a atender as necessidades da produção e de SMS. Para que isso ocorra, o serviço deverá ter confiabilidade, segurança, preservação do meio ambiente e custo adequado.
Objetivo da Gestão da Manutenção da Rotina : “ Assegurar a disponibilidade dos equipamentos através da eficiente priorização, planejamento e execução dos serviços de manutenção e do monitoramento contínuo dos indicadores de desempenho deste processo”.
Objetivo da Gestão de Paradas: “Assegurar que o processo de planejamento da parada siga um modelo estruturado no qual os riscos de cada etapa, que envolvem recursos humanos e materiais, sejam avaliados e validados”.
Os primeiros registros de manutenção datam do século X, quando os Vikings dependiam fortemente da manutenção para manter seus navios em perfeitas condições para as batalhas.
Vemos que a história e desenvolvimento da manutenção acompanharam o desenvolvimento Industrial ao longo desses últimos 100 anos de história.
Em 1914 a manutenção era executada pelo próprio pessoal da operação tendo uma importância secundária. Com a primeira guerra mundial, Henry Ford desenvolveu e criou equipes para atender as exigências do sistema produtivo, garantindo assim o funcionamento dos equipamentos.
A manutenção evoluiu nos últimos 30 anos se dividindo em três gerações (primeira, segunda e terceira), cada uma se destacando nos seguintes aspectos:
A primeira geração corresponde ao período antes da segunda guerra mundial quando a indústria era pouco mecanizada. É neste período que surge a manutenção corretiva, e a manutenção ocupa um dos níveis mais
baixos das organizações. A manutenção corretiva se caracteriza pela intervenção no equipamento ou ativo da empresa na ocorrência de falha, restabelecendo sua função.
A segunda geração inicia-se na segunda guerra mundial dando inicio à manutenção preventiva. É nesta época que os investidores avaliam os custos de manutenção e começam a enxergar a manutenção com outros olhos, ocupando assim posição hierárquica compatível à produção. É neste período que se cria a Engenharia de Manutenção que tem por finalidade assessorar a manutenção, e na década de 60 a manutenção passou a utilizar métodos de controle em decorrência do advento do computador. A intervenção no equipamento, antecipando as causas prováveis de falhas através das ações determinadas em intervalos fixos de tempo se caracteriza pela manutenção preventiva.
É na terceira geração, que se inicia a partir da década de 70, que os conceitos da manutenção preventiva são fundamentados na performance e desempenho dos equipamentos, e por meios de técnicas que fornecem diagnósticos preliminares de falhas dos equipamentos surge a manutenção preditiva. É neste período que as empresas iniciam o desenvolvimento tecnológico dos seus parques industriais, crescendo na automação e mecanização e iniciando a indicação da confiabilidade e disponibilidade dos equipamentos. Portanto, podemos definir a manutenção preditiva como sendo a manutenção preventiva fundamentada no desempenho dos equipamentos por meios de técnicas que fornecem diagnósticos preliminares de falhas
A partir daí as organizações vêm passando por transformações rápidas e profundas, impulsionadas pelo aumento da competitividade e pelo desenvolvimento tecnológico, levando as empresas a uma verdadeira revolução nos seus sistemas produtivos.
A organização da manutenção depende da definição dos objetivos, dos princípios e da filosofia a ser adotada em função das atividades que serão executadas pela manutenção e deve estar voltada para a gerência e a solução dos problemas na produção, de modo que a empresa seja competitiva no mercado.
A função Planejamento é uma função dinâmica, onde nem sempre a realização de uma obra corresponderá exatamente ao planejado inicialmente, pois os rendimentos considerados nas tarefas são estimados, e frequentemente ocorrem imprevistos, variando o volume de serviços e também ocorrendo retrabalhos. A evolução da obra deverá considerar estas ocorrências através de retorno de informações ao planejador pelos executantes e ou supervisores de modo que esta interação resulte uma via de duas mãos entre o planejamento e a execução.
A Organização da Manutenção de qualquer empresa deve estar voltada para a gerência e a solução dos problemas na produção, de modo que a empresa seja competitiva no mercado.
A organização da manutenção depende da definição dos objetivos, dos princípios e da filosofia a ser adotada em função das atividades que serão executadas pela manutenção, destacando-se abaixo os seguintes pontos para o gerenciamento da manutenção:
As atividades de manutenção devem ter um escopo muito mais abrangente do que simplesmente manter as condições originais dos equipamentos. Muitas vezes, somente manter estas condições é insuficiente e a introdução de melhorias que visam a aumentar a produtividade também deve fazer parte do trabalho dos departamentos de manutenção.
Existe uma variedade de denominações para classificar a atuação da manutenção, porém as práticas básicas definem os tipos principais de manutenção, conforme:
Manutenção corretiva não planejada é aquela onde a correção da falha se dá de maneira aleatória, ou seja, é a manutenção atuando no momento da falha do equipamento, agindo de forma impulsiva.
Caracteriza-se pela ação, sempre após a ocorrência da falha, que é aleatória, e sua adoção leva em conta fatores técnicos e econômicos. Do ponto de vista do custo de manutenção, a manutenção corretiva é mais barata do que prevenir falhas nos equipamentos, porém pode causar grandes perdas por interrupção da produção. É comum a adoção da manutenção corretiva para algumas partes menos críticas dos equipamentos, porém é preciso dispor dos recursos necessários – peças de reposição, mão-de-obra e ferramental para agir rapidamente, ou seja, a manutenção corretiva pode ser aplicada para equipamentos que não comprometam o sistema produtivo (qualitativo ou quantitativo) ou a integridade física do funcionário.
Manutenção corretiva planejada é a correção do desempenho menor que o esperado ou da falha, por decisão gerencial, isto é, pela atuação em função do acompanhamento da manutenção preditiva ou pela decisão de operar até a quebra da máquina. A decisão da adoção da política de manutenção corretiva planejada pode advir de vários fatores, tais como: negociação de paradas de produção, aspectos ligados à segurança dos funcionários, melhores planejamentos dos serviços, garantia de ferramentais e peças sobressalentes, busca de recursos humanos com tecnologia externa. A manutenção corretiva planejada possibilita o planejamento dos recursos necessários para a operação, uma vez que a falha é esperada. Toda e qualquer manutenção corretiva por mais barata que seja não é viável para a companhia, devendo ter um planejamento para não reincidir a falha.
Manutenção preventiva é a atuação realizada de forma a reduzir ou evitar a falha ou quebra no desempenho, obedecendo a um plano previamente elaborado, baseado em intervalos definidos de tempo, ou seja, o setor de Planejamento elabora planos de manutenção baseados nos tempos dos equipamentos definidos pelos fabricantes; com isto consegue antecipar as falhas que possam vir a ocorrer nos equipamentos. Caracteriza-se pela busca sistemática e obstinada para evitar a ocorrência de falhas, procurando prevenir, mantendo um controle contínuo sobre os equipamentos, efetuando operações julgadas convenientes. A manutenção preventiva, considerada o coração das atividades de manutenção, envolvendo algumas tarefas sistemáticas tais como: as inspeções, reformas e troca de peças. O custo da manutenção preventiva é elevado, tendo em vista que peças e componentes dos equipamentos podem ser substituídos antes de atingirem seus limites de vida útil. Para adoção de uma política de manutenção preventiva devemos considerar fatores tais como: impossibilidade da adoção de manutenção preditiva, aspectos de segurança pessoal ou da instalação, equipamentos críticos de difícil liberação operacional, riscos de agressão ao meio ambiente, sistemas complexos ou de operação contínua.
Atualmente o perfil estrutural das empresas é traduzido por modificações na relação de empregados de cada área, bem como no perfil funcional. Além disto, outros aspectos que vêm motivando as mudanças é a forte automação do processo produtivo, levando à redução de operadores e à modificação nos perfis funcionais dos operadores, causados por ações como polivalência, especialização e Total Productive Maintenance. O TPM foi implementado na indústria japonesa a partir de 1971, na Nippon Denso (pertencente ao grupo Toyota) e seus conceitos foram trazidos para o Brasil em 1986. Tem como objetivo a eficácia da empresa através de maior qualificação das pessoas e melhoramentos introduzidos nos equipamentos. O TPM é um sistema de gerenciamento da produção em que o principal papel da manutenção é treinar os operadores nas ações preventivas. É uma estratégia simples e prática de envolvimento dos operadores dos equipamentos nas atividades de manutenção diária, tais como a inspeção, limpeza e lubrificação, com o objetivo de evitar a deterioração dos equipamentos, detectando e tratando suas anomalias num estágio inicial antes que resultem em falhas.
As manutenções atualmente buscam por estruturas cada vez mais leves, ou seja:
A manutenção é organizada para atender uma necessidade da instalação ou então por uma atitude ou filosofia da alta direção que conhece os problemas e pretende resolvê-los de maneira adequada. Portanto, a manutenção deve ser organizada e gerenciada de forma coerente, de forma que cada funcionário tenha sua função especifica.
O plano de manutenção tem uma posição de destaque em um sistema de gerenciamento da manutenção, pois a elaboração e o cumprimento deste plano permitirão que a empresa atinja seus objetivos de lucratividade e sobrevivência através de equipamentos que não apresentem falhas e que não prejudiquem a qualidade, o custo e a entrega dos produtos e serviços e que não coloquem em risco a segurança e a integridade do meio ambiente.
A manutenção pode ser centralizada, descentralizada, mista e matricial.
A estrutura centralizada é aquela onde todas as operações são planejadas e dirigidas por um único Departamento. As oficinas para onde convergem as solicitações de serviços, são centralizadas e as equipes de manutenção atendem todos os setores ou unidades de operação. Setores de staff, como projetos, orçamentos, custos e planejamento, fazem parte do departamento que, usualmente, é dirigido por um gerente, em
posição hierárquica igual ao gerente de produção. Ambos estão subordinados, neste esquema, ao diretor de Produção.
A manutenção centralizada tem como principais vantagens os seguintes tópicos:
As desvantagens da manutenção centralizada são as seguintes:
A estrutura descentralizada, também denominada por área, preconiza a divisão da planta em áreas ou setores produtivos, cada um dos quais fica sob os cuidados de uma equipe de manutenção. Neste caso a Manutenção está normalmente subordinada à Área de Produção, não havendo a presença do gerente de manutenção. O gerente de produção de cada Área é responsável pelas decisões relativas à manutenção, inclusive a determinação da prioridade de execução.
A manutenção descentralizada possui como desvantagem os seguintes itens:
Já, na figura 1.3, mostramos as técnicas de manutenção que têm sido aplicadas
Planejamento ; englobando o apoio logístico à execução (planejamento de serviços, contratação, custos e orçamento e administração da ferramentaria
Apoio Técnico; englobando comissionamento, testes e aceitação, pequenos projetos de melhoria e novas instalações, e apoio de normas e documentos pertinentes à manutenção
Assim, com base nestas definições, podemos esboçar a estrutura abaixo:
Figura 1.
Cabe notar que a estrutura acima é de atividades, e não necessariamente de pessoas, porque, dependendo do porte da empresa, várias atividades podem ser desempenhadas por uma única pessoa, ou uma mesma atividade pode ser desempenhada por várias pessoas.
Nestas atividades podemos identificar as seguintes tarefas:
Planejamento - consiste em receber as Solicitações de Serviço dos Clientes, fazer uma análise dos serviços quanto a necessidades de materiais, ferramentas, apoio de contratadas, definir prioridades e encaminhar para os responsáveis pela execução dos mesmos no Setor de Execução
Contratação - consiste em contatar empresas para prestação de serviços, fazer licitações, elaborar planilhas de serviços (com apoio do planejamento), contratarem as empresas, e encaminhar as faturas para pagamento para a área contábil da empresa
Acompanhamento e Avaliação - Responsável pelo constante aprimoramento da manutenção segundo as modernas técnicas de qualidade. Realiza também auditorias para assegurar o cumprimento de normas e procedimentos na execução de serviços. Dentro desta atividade também estão compreendidos estudos no sentido de melhorar os sistemas informatizados de manutenção implantados, bem como definir e programar treinamentos do pessoal de manutenção
Custos & Orçamento - Esta atividade compreende a elaboração da planilha orçamentária da manutenção, bem como o acompanhamento
da mesma. Compreende também o acompanhamento mensal de custos de material, pessoal, contratos e diversos
Ferramentaria - Compreende a administração e estoque de ferramentas, bem como o controle de empréstimo das mesmas, Em muitas plantas a ferramentaria é responsabilidade da atividade de suprimento, quando a mesma é subordinada à manutenção
Na atividade de Execução de Serviços podem estar incluídas a manutenção de instalações industriais, a oficina de apoio, a limpeza industrial e equipamentos outros, tais como telecomunicações. É uma vasta gama de atividades que, dependendo da empresa, pode requerer qualificações distintas de pessoal. Assim, para facilitar a administração do pessoal a ser aqui lotado, procuraremos grupar suas atividades por especialidades. Assim, aproveitando a experiência implantada em muitas empresas, sugerimos os seguintes grupos de atividades:
Mecânica - Abrange a parte mecânica dos equipamentos rotativos, bem como as atividades de lubrificação e monitoração de desempenho dos mesmos (preditiva). Abrange também eliminação de vazamentos em equipamentos rotativos
Elétrica - Atinge todo e qualquer serviço em equipamento de distribuição de energia elétrica, com exceção de manutenções mecânicas em motores elétricos ou turbinas. Envolve também substituição de lâmpadas e controle da rede elétrica geral da planta
Instrumentação - Envolve todo o serviço de calibração de instrumentos pneumáticos e eletrônicos e controle de preventiva dos mesmos. Abrange também a manutenção de painéis de controle
Caldeiraria & Complementar - Abrange os seguintes serviços: Reparos, trocas e solução de vazamentos em tubulações e conexões de tubulação; Manutenção de Trocadores de Calor (permutadores); Manutenção de Tanques, Esferas e vasos de pressão; Manutenção de Caldeiras, Fornos e Chaminés; Isolamento e refratários; Pintura; Limpeza Industrial e outros serviços, tais como manutenção civil e serviços de pedreiro.
No grupo de atividades de Apoio Técnico estão compreendidas as tarefas de teste de desempenho de equipamentos, efetuadas segundo as mais modernas técnicas de inspeção e de acordo com as normas legais e de certificação vigentes. Aqui cabe também analisar os problemas mais complexos de manutenção e propor alternativas de solução. Aqui são criadas Normas e Rotinas, com suporte dos responsáveis pelo Acompanhamento e Avaliação de Qualidade e da Execução. Os responsáveis pelo desenho técnico da manutenção podem estar neste conjunto de atividades, ou em Projetos (Engenharia).