
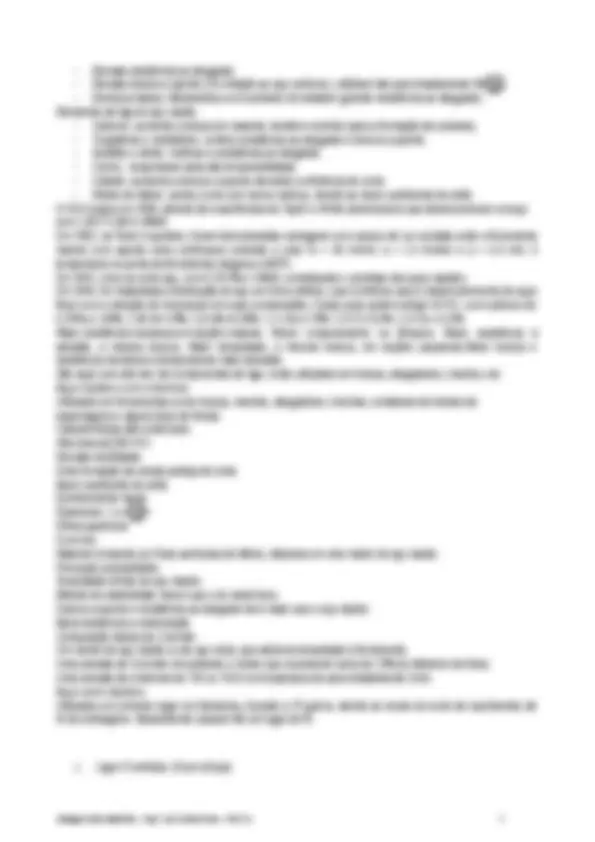
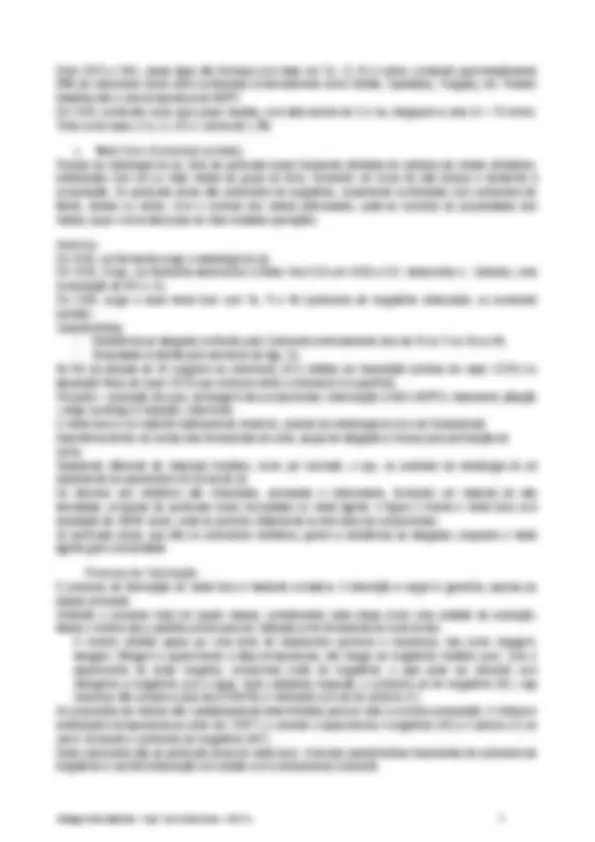
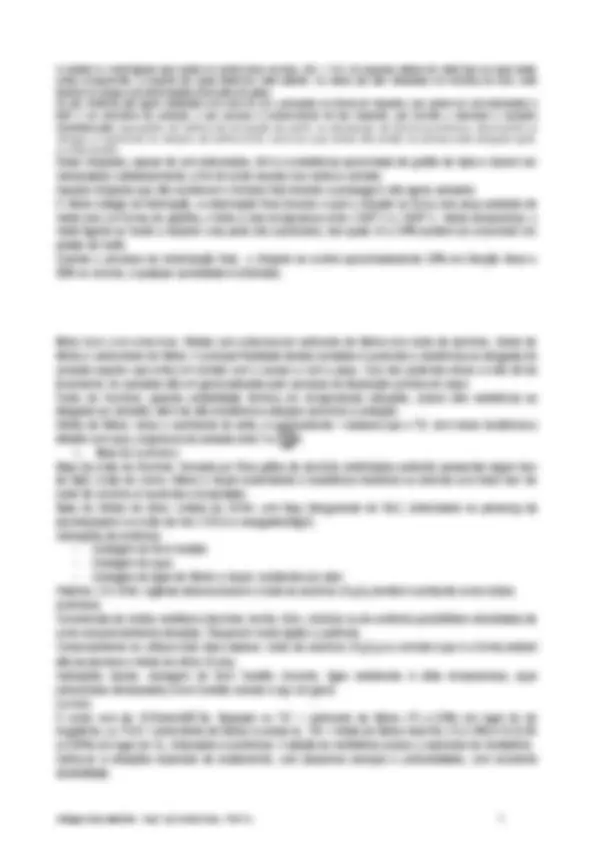
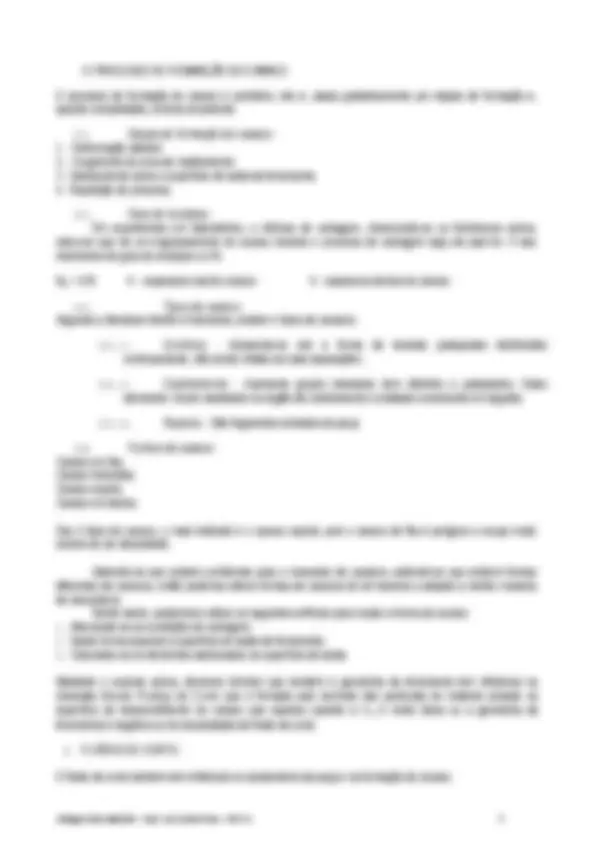
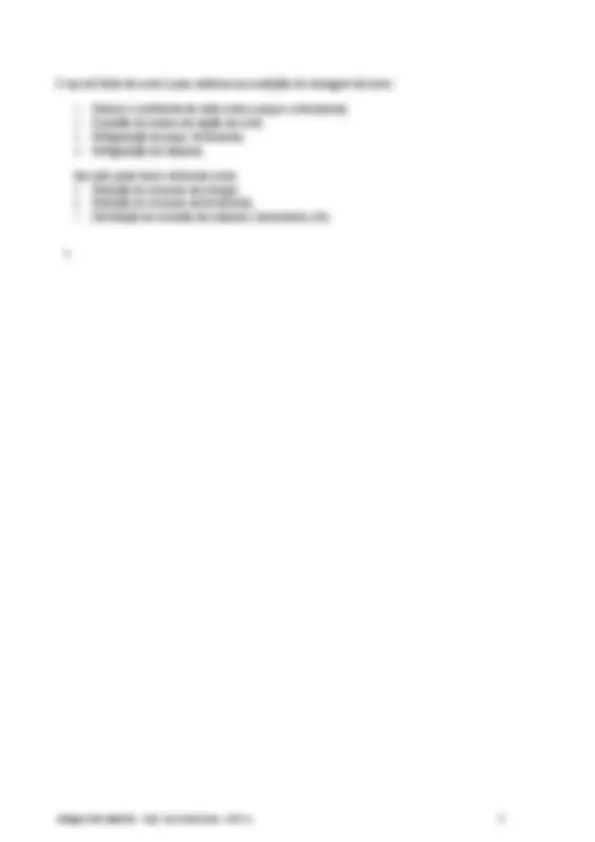
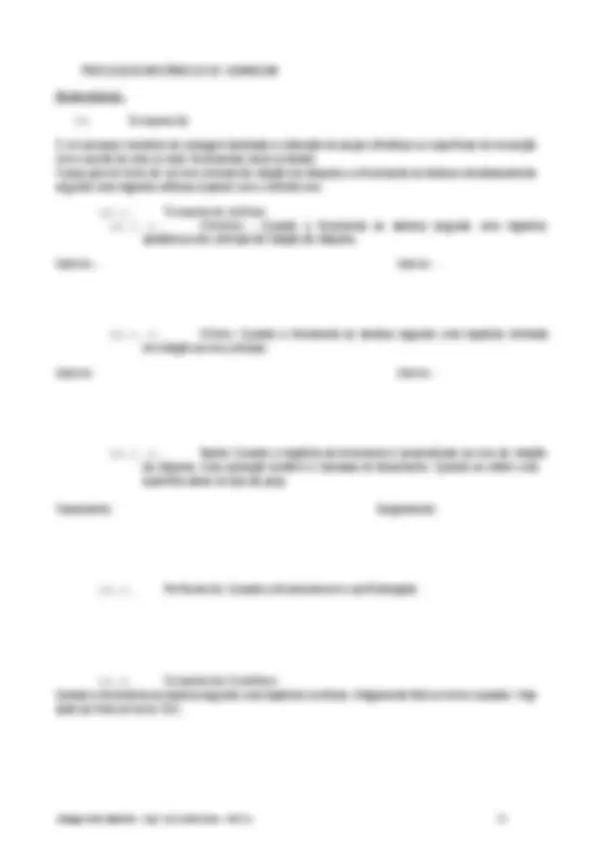
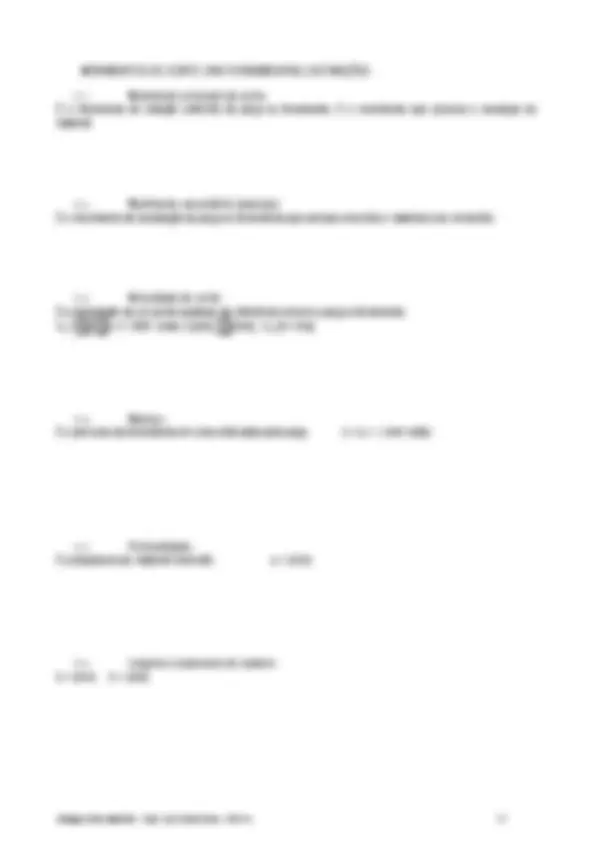
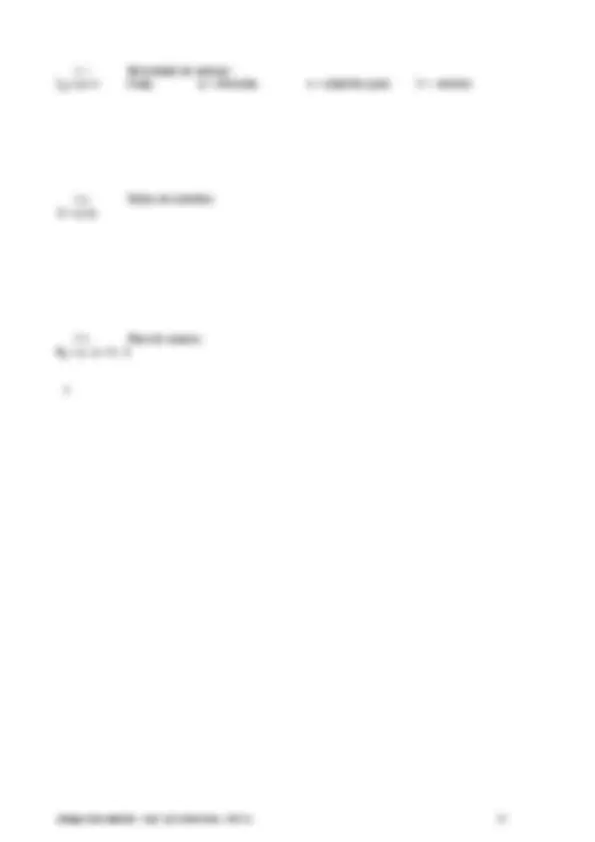
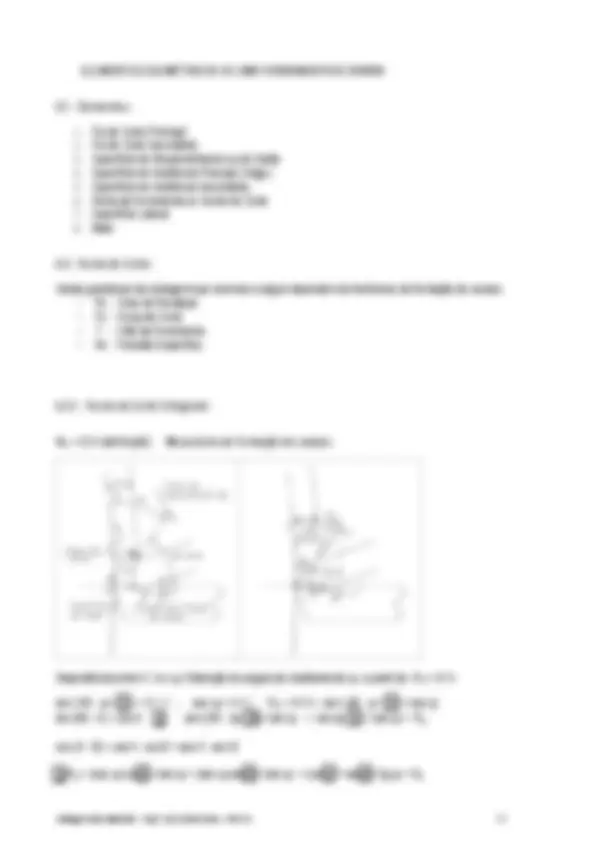
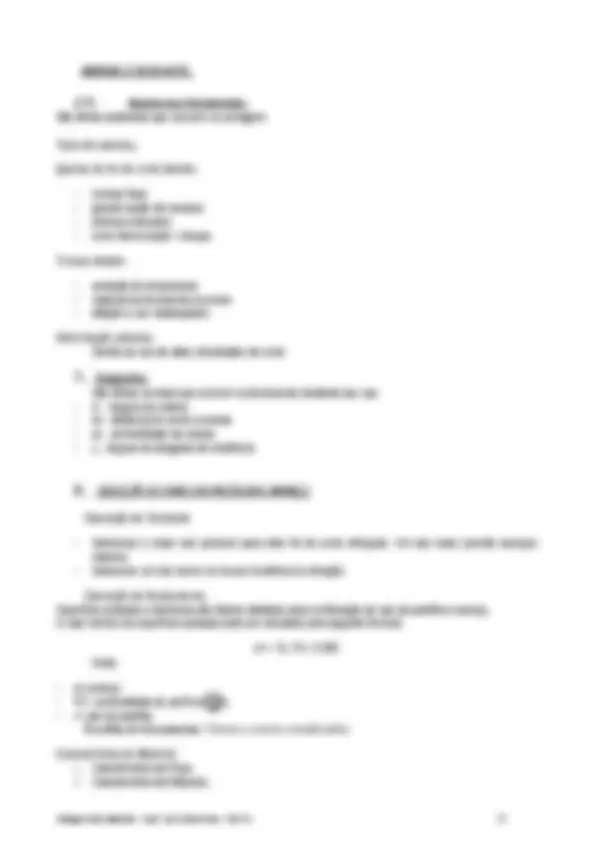

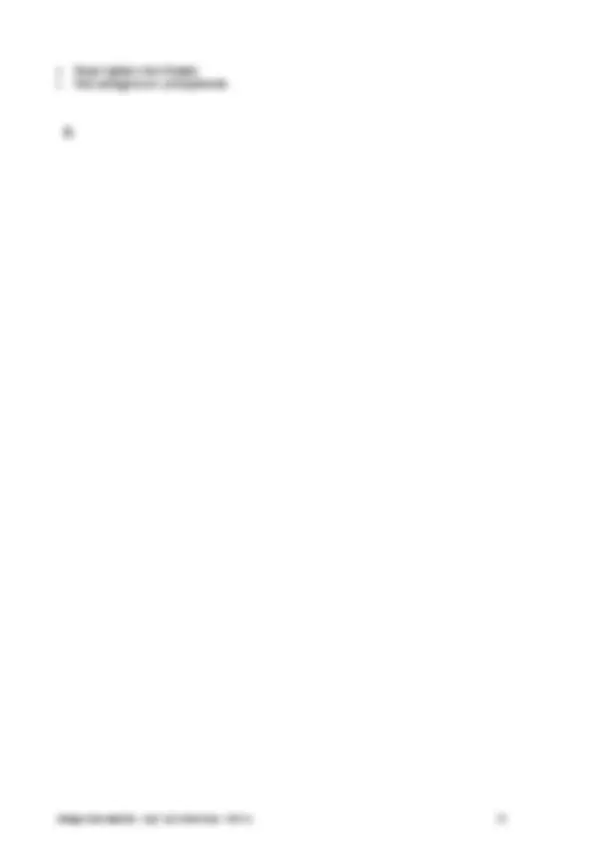
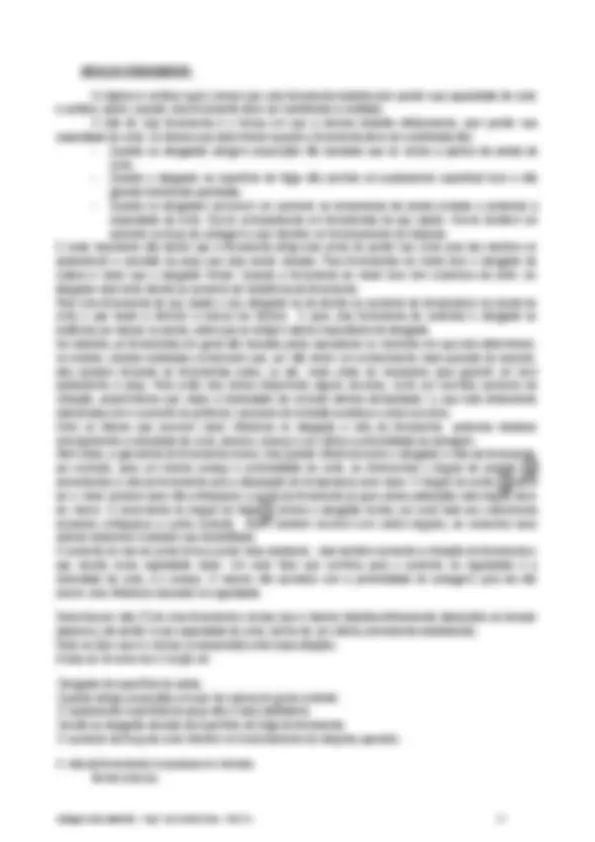
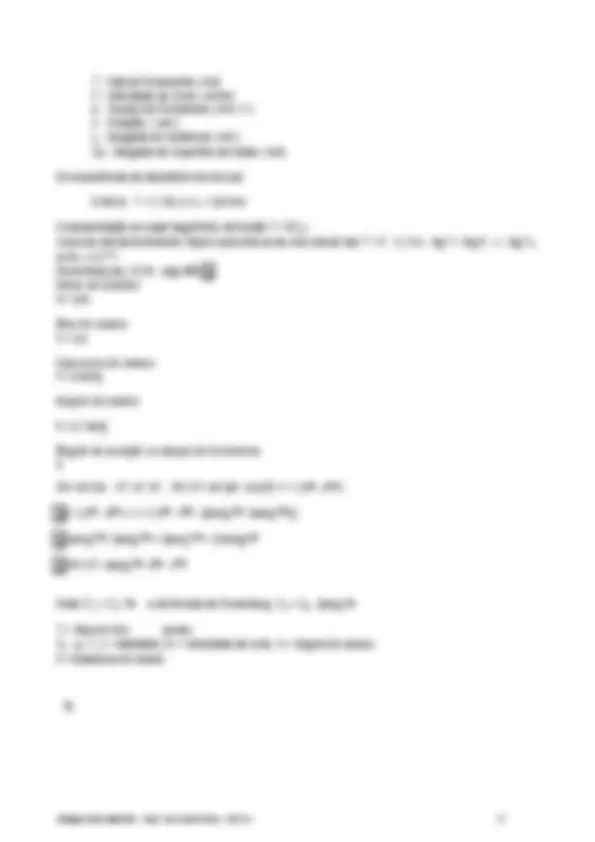
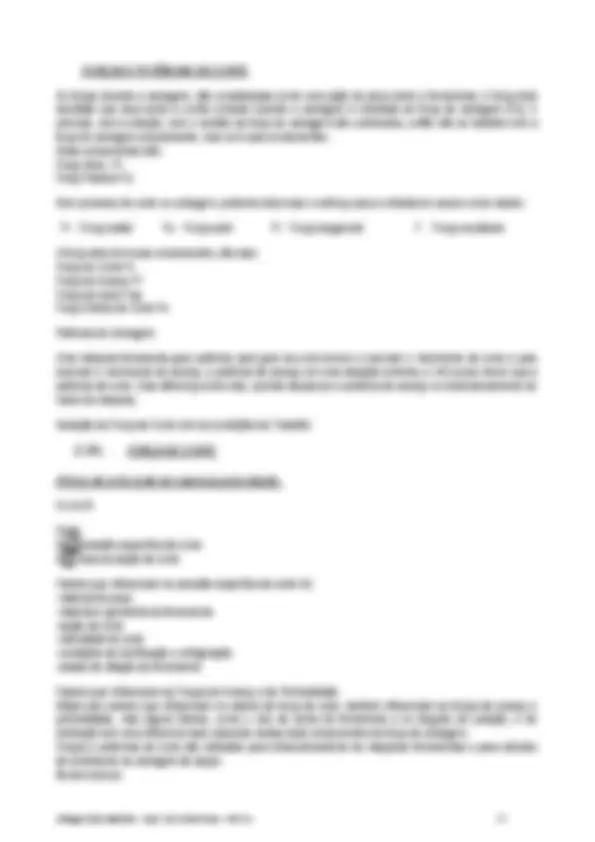
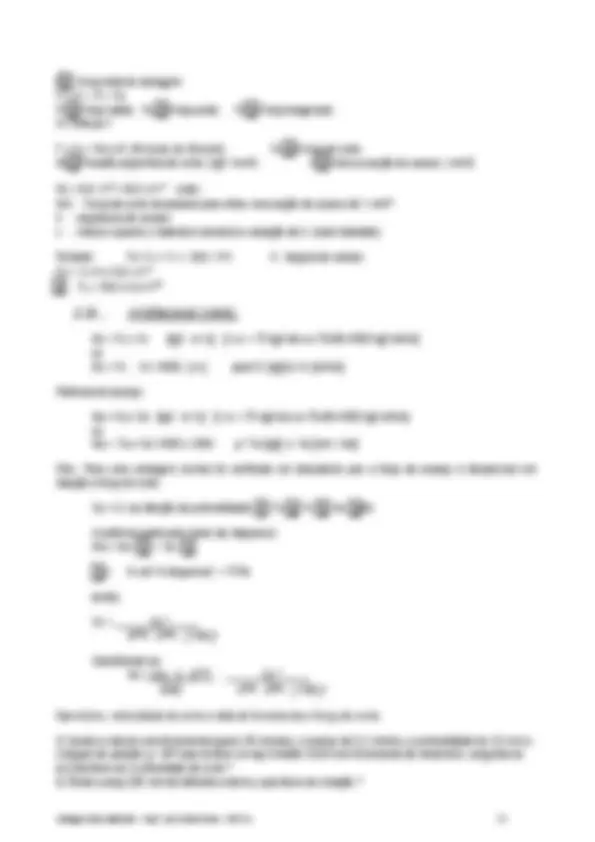
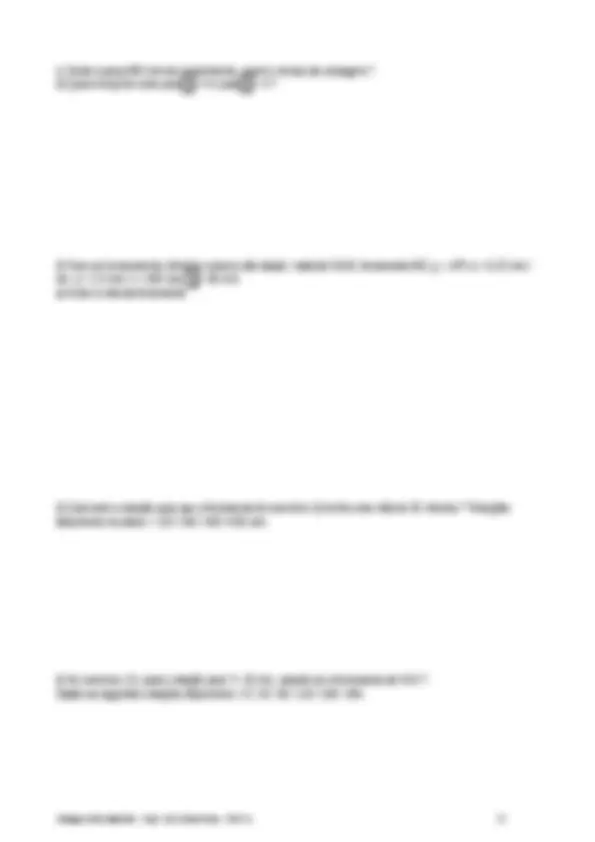
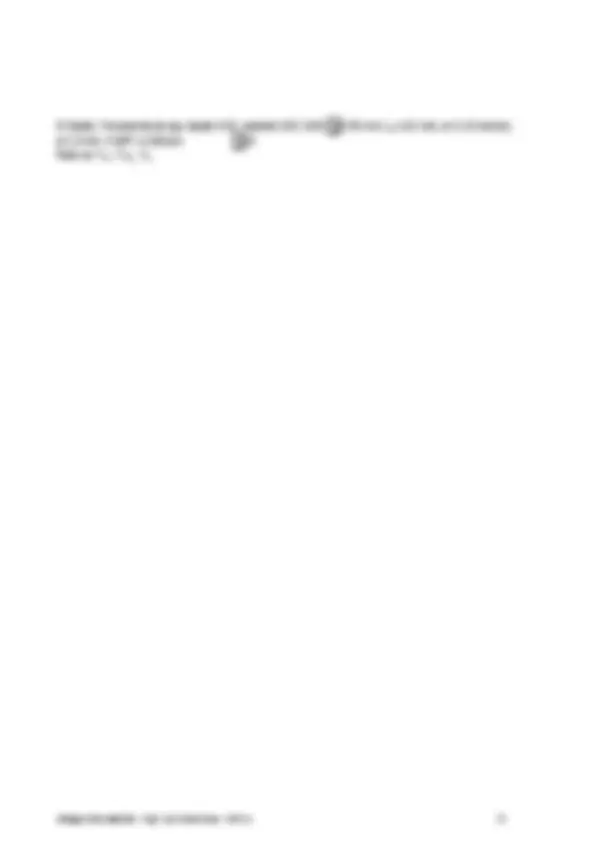
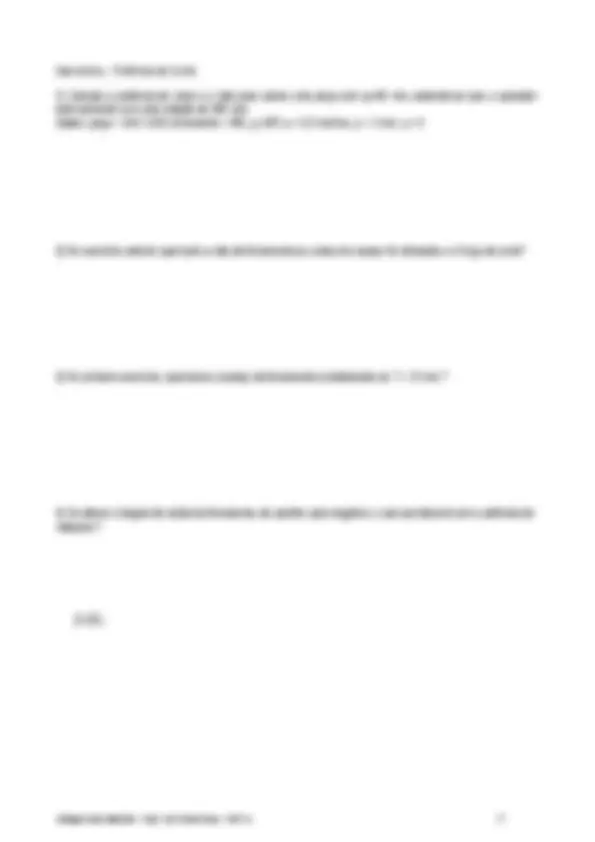
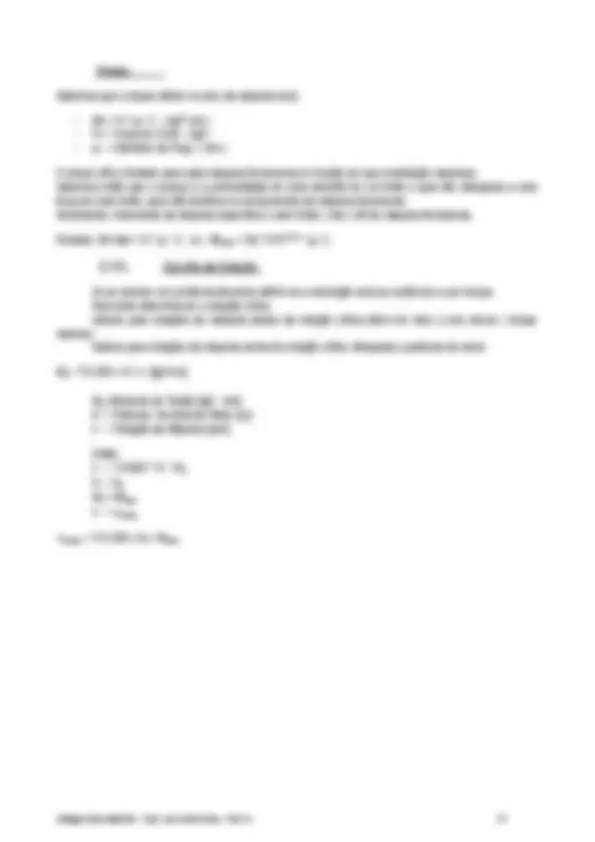
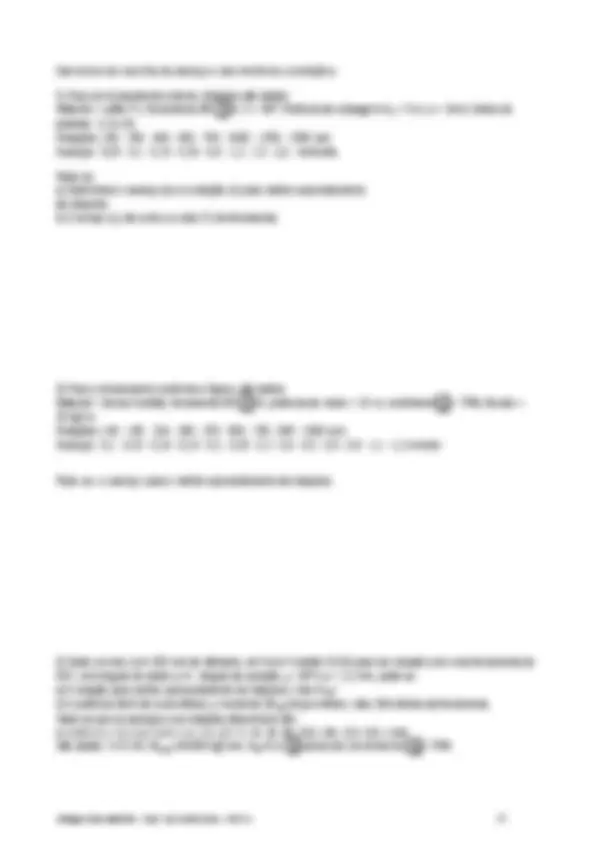
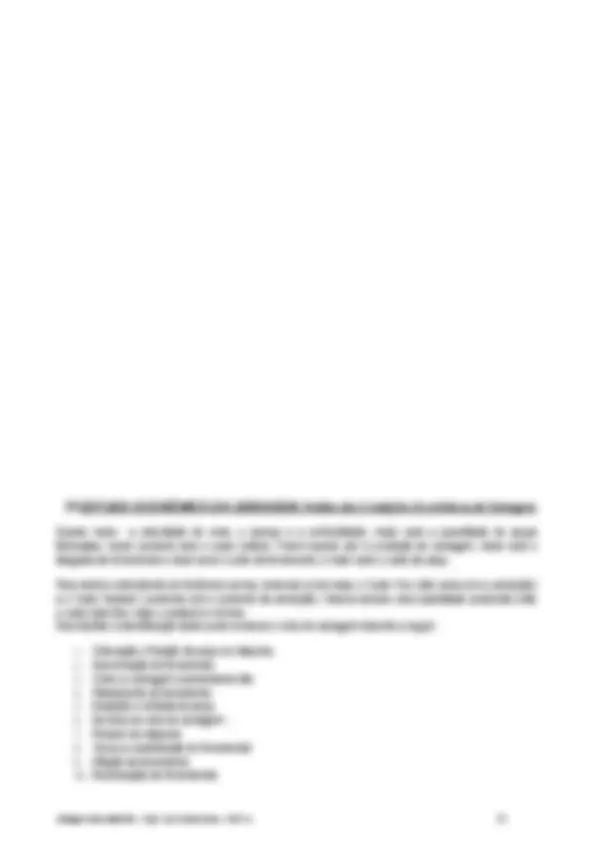
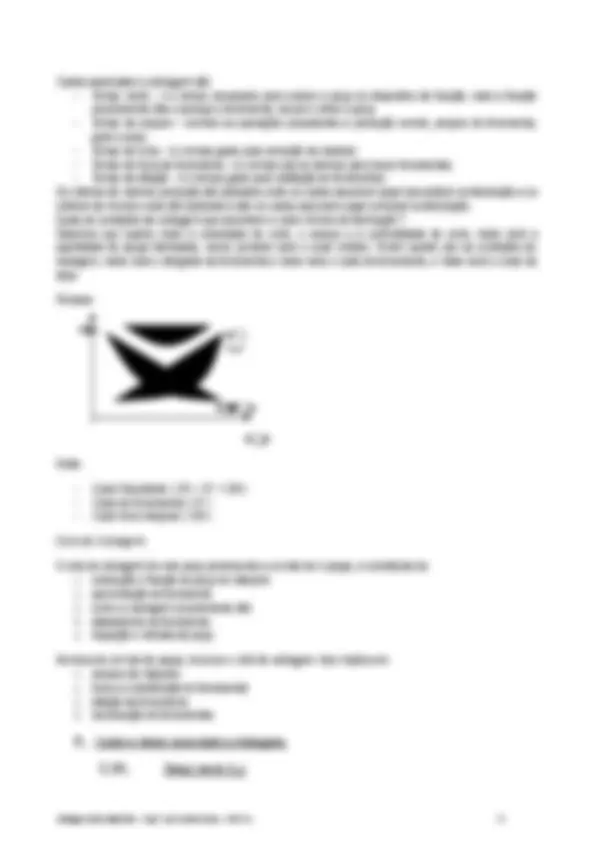
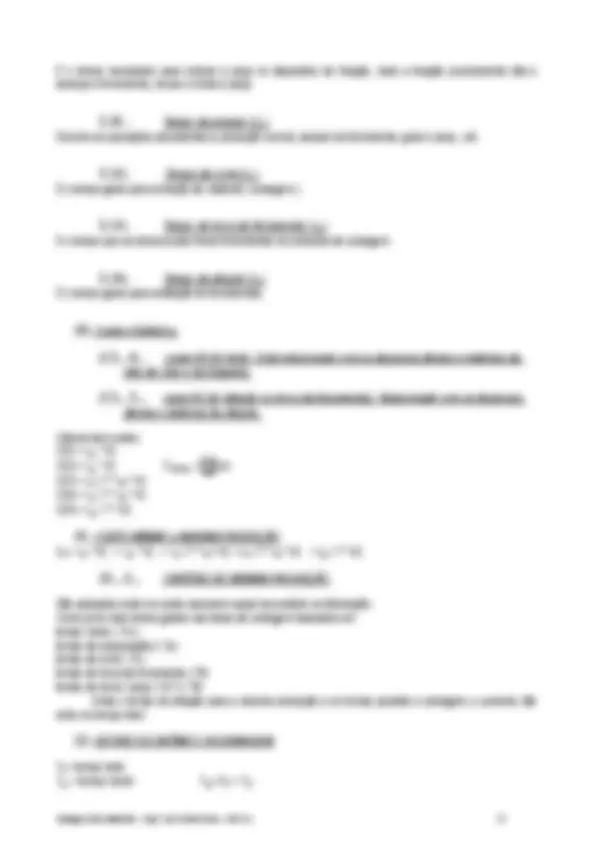
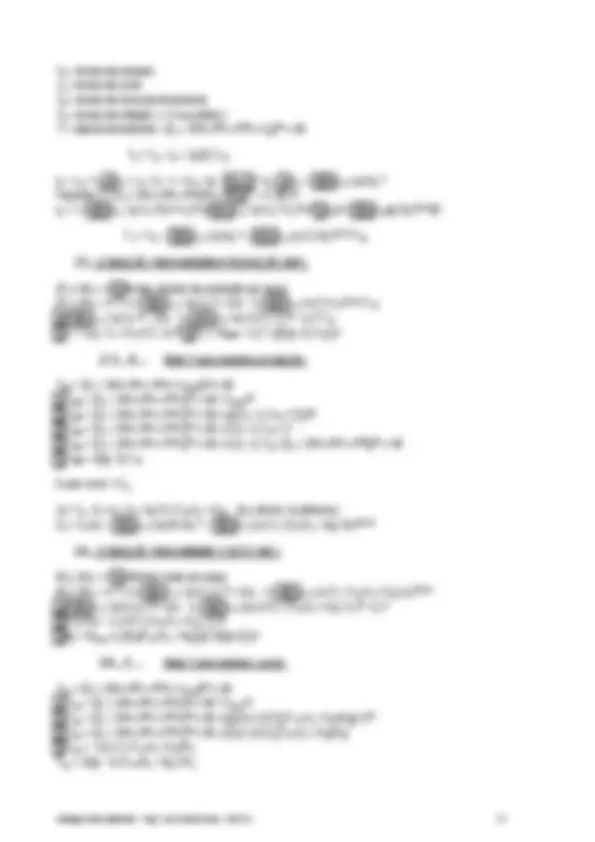
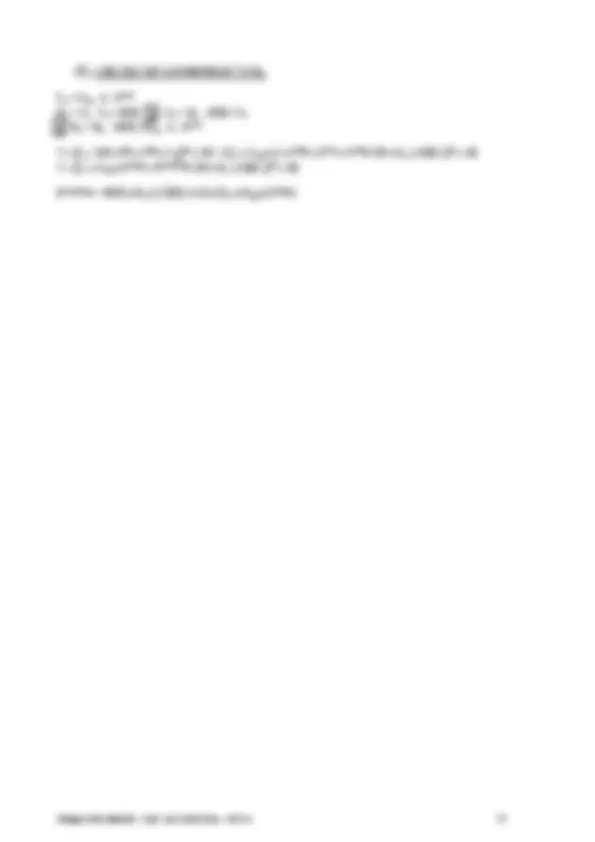
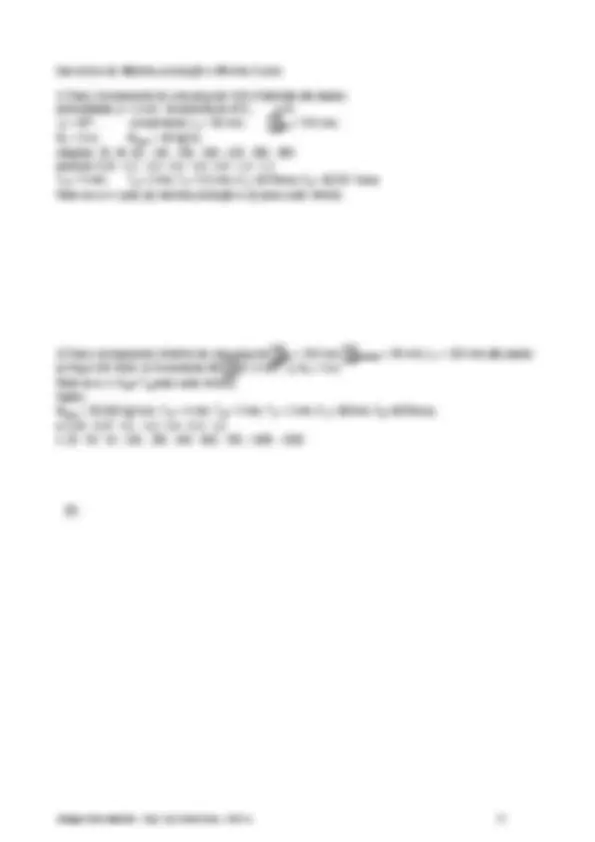
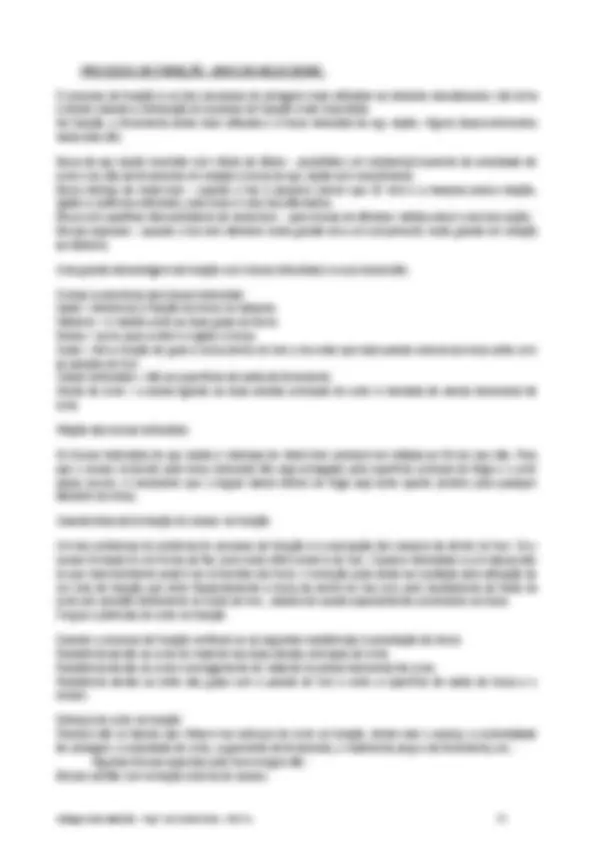
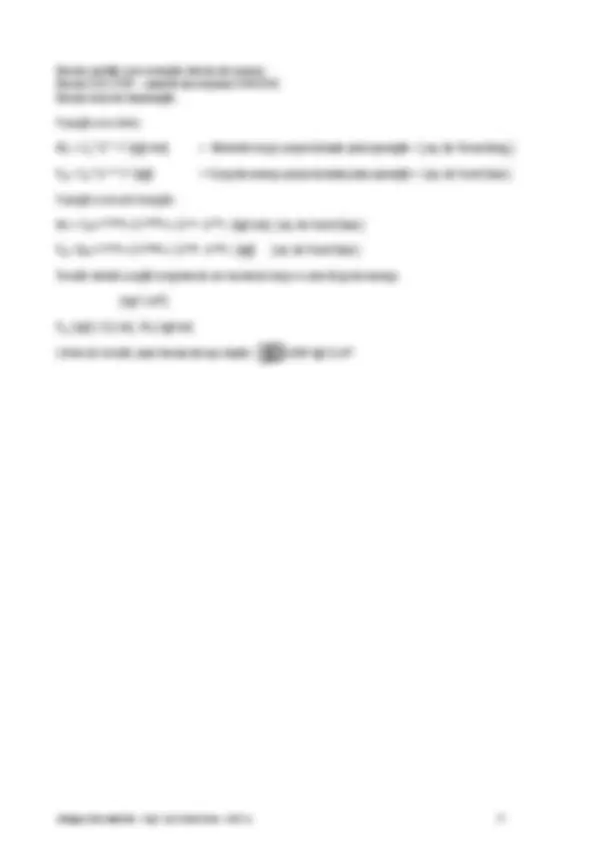
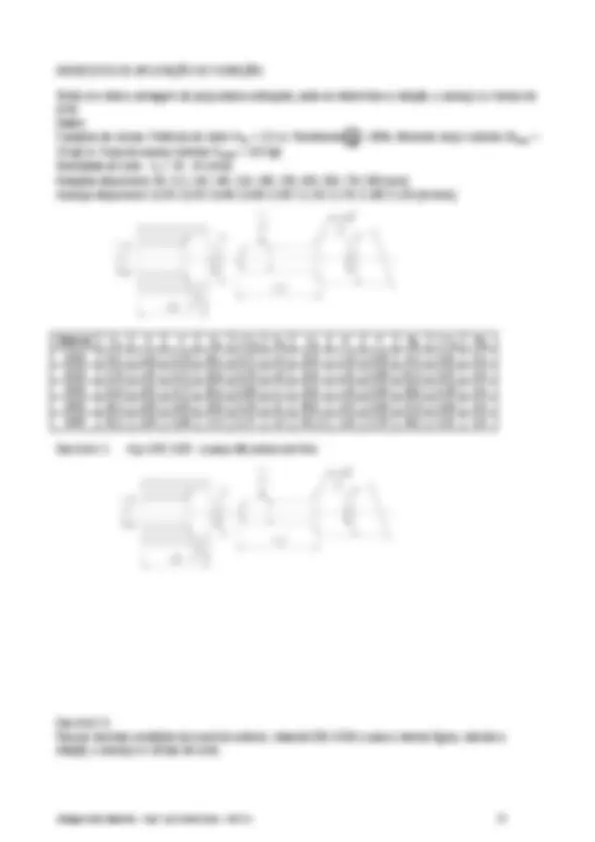
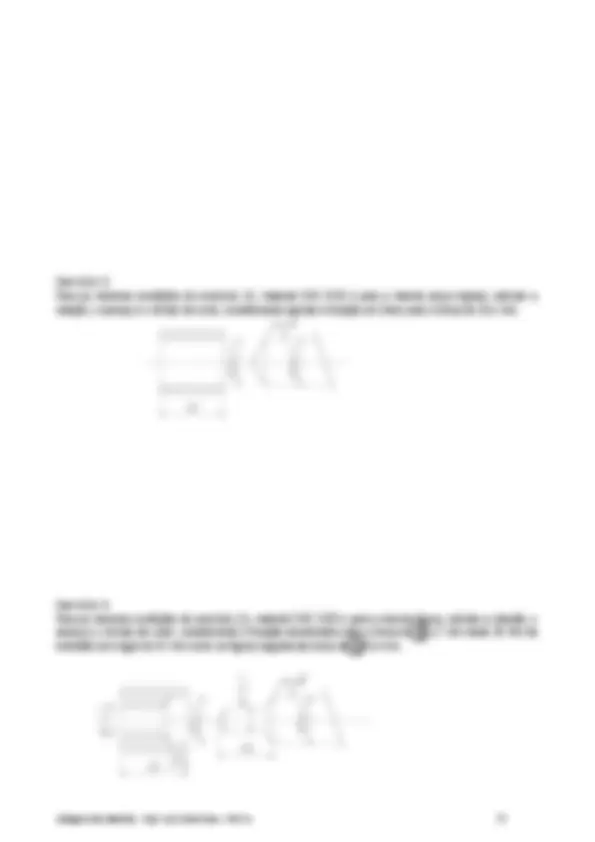
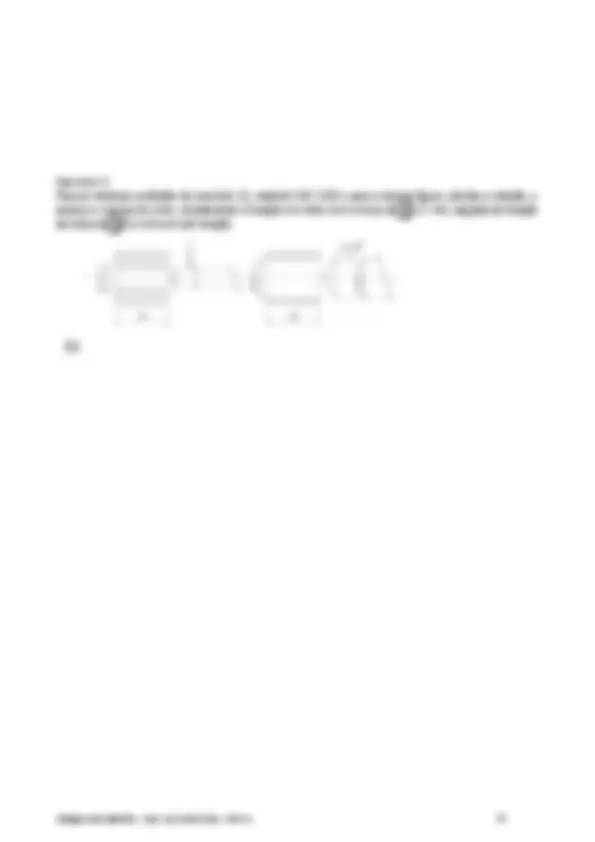
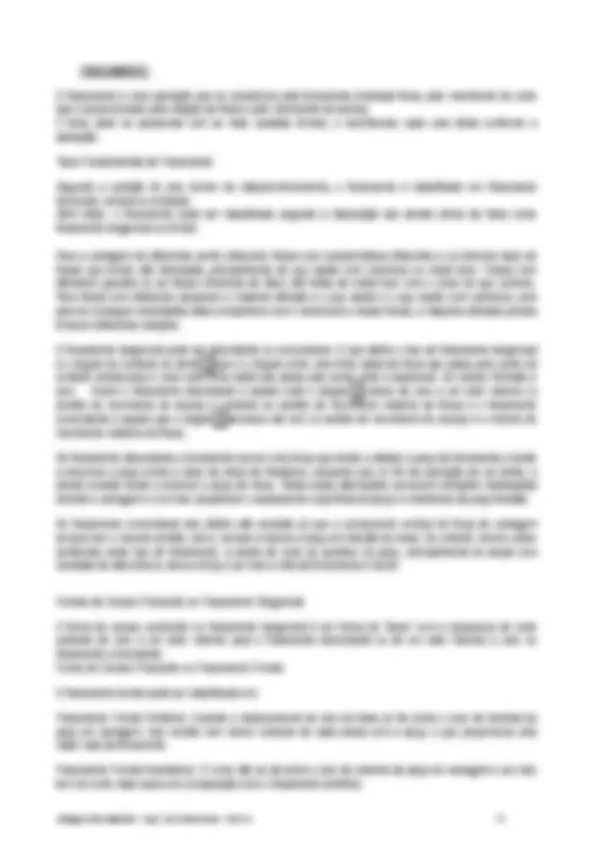
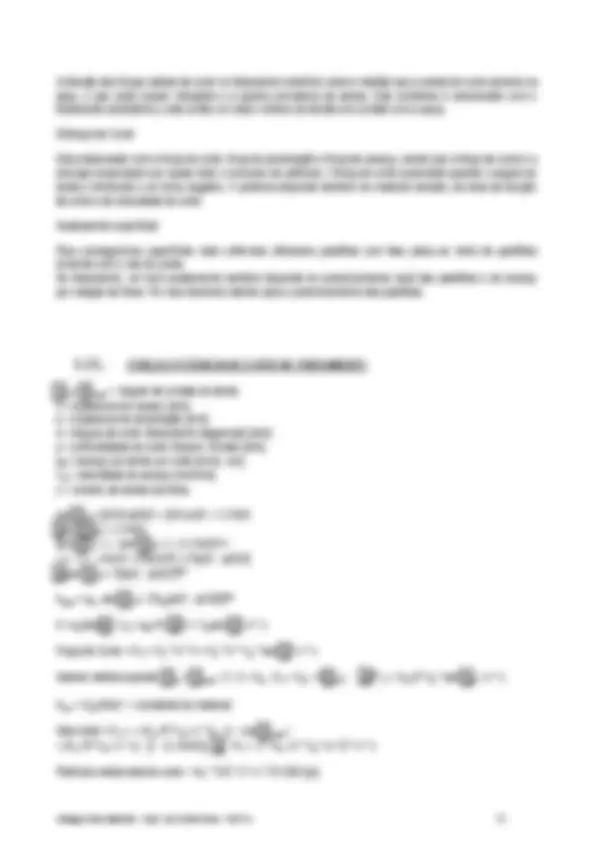
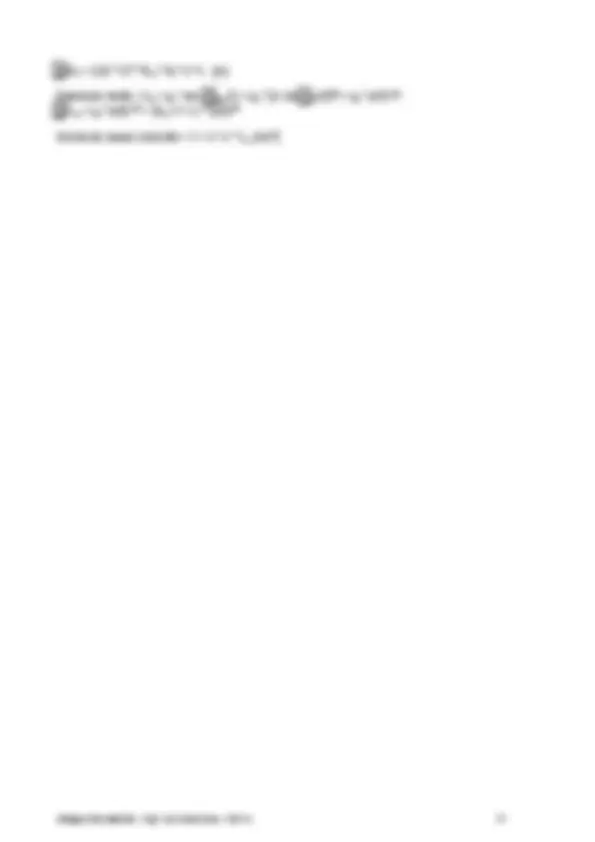
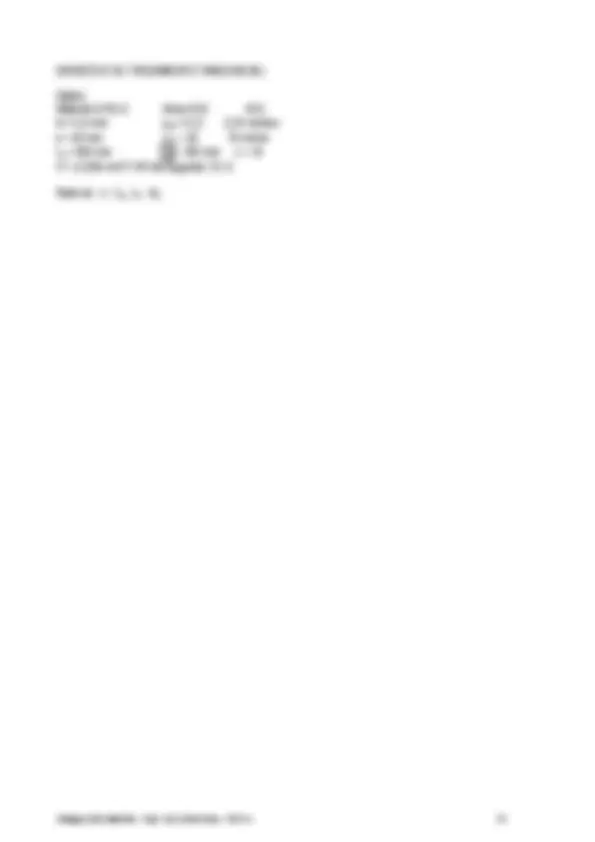
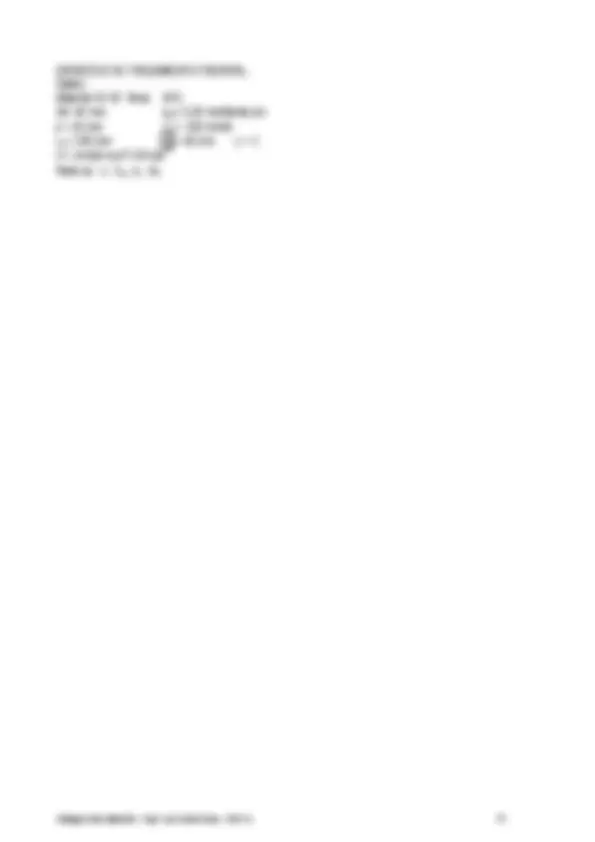
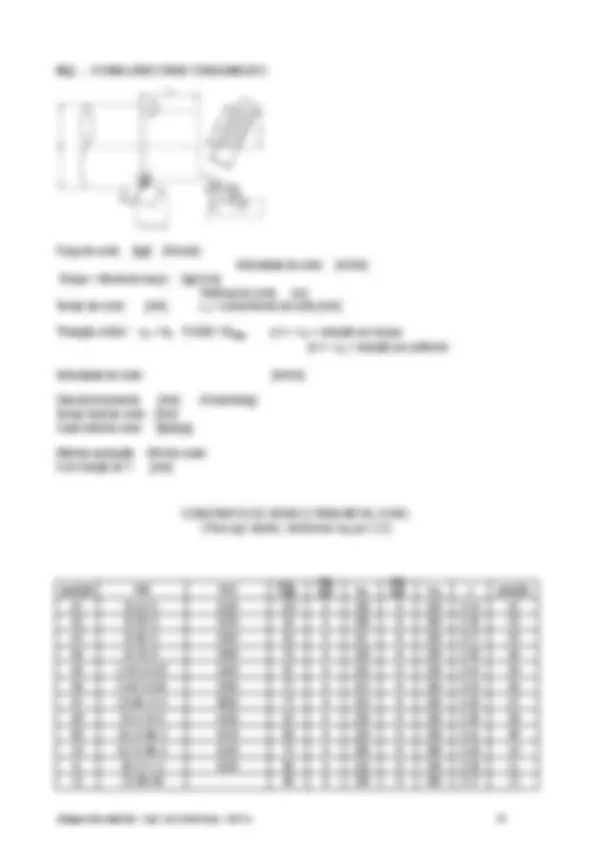
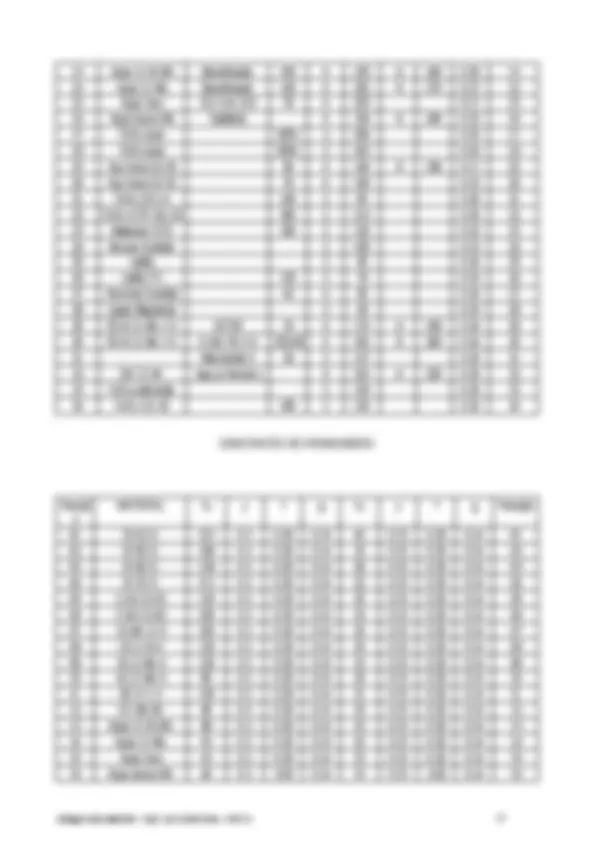
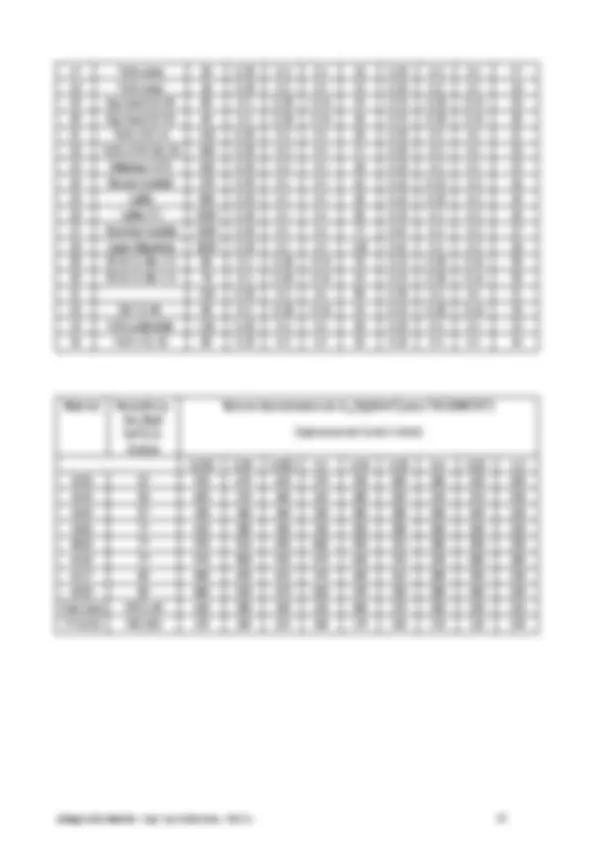
Estude fácil! Tem muito documento disponível na Docsity
Ganhe pontos ajudando outros esrudantes ou compre um plano Premium
Prepare-se para as provas
Estude fácil! Tem muito documento disponível na Docsity
Prepare-se para as provas com trabalhos de outros alunos como você, aqui na Docsity
Os melhores documentos à venda: Trabalhos de alunos formados
Prepare-se com as videoaulas e exercícios resolvidos criados a partir da grade da sua Universidade
Responda perguntas de provas passadas e avalie sua preparação.
Ganhe pontos para baixar
Ganhe pontos ajudando outros esrudantes ou compre um plano Premium
Comunidade
Peça ajuda à comunidade e tire suas dúvidas relacionadas ao estudo
Descubra as melhores universidades em seu país de acordo com os usuários da Docsity
Guias grátis
Baixe gratuitamente nossos guias de estudo, métodos para diminuir a ansiedade, dicas de TCC preparadas pelos professores da Docsity
Usinagem de materias
Tipologia: Notas de estudo
1 / 48
Esta página não é visível na pré-visualização
Não perca as partes importantes!
Depto Mecânica – Área 1
Máquinas Ferramentas I – O Processo de Produção com Remoção de Cavaco Eng° Luiz Carlos Rosa – Prof. Dr.
Para selecionar o material ideal para uma ferramenta de usinagem deve-se levar em consideração com relação a:
1.. Ferramentas de aço carbono: Na antiguidade foram famosos como Aços de Damasco, fabricados por fusão datam de 300 a.c. Na idade média era usado o ferro carbonetado endurecido por resfriamento em água para a fabricação de armas. No século XVIII a madeira era o material predominante e os metais eram limitados. Até o século XIX, trabalhar os metais era um serviço difícil e artesanal, até que se disponibilizou a máquina a vapor e a eletricidade, o que trouxe o desenvolvimento das máquinas operatrizes. Em 11/03/1776, entrou em operação a 1º máquina a vapor, em Bloomfield Collierge, Inglaterra. Em 1800 já operavam próximo de 100 delas, com predominância no campo da metalurgia, minas de carvão e cobre e fundições. Na América do Norte, os fabricantes de armas desenvolveram a produção em massa de componentes e por conseqüência as máquinas operatrizes. A velocidade de corte nessa época era de aproximadamente 5m/min. A temperatura da ferramenta chegava a próximo de 250ºC. Em 1868, Robert Mushet descobriu que a adição de Mn (manganês) podia tornar o aço mais duro. Acidentalmente descobriu que a presença de W (tungstênio) permitia o endurecimento do aço com resfriamento normal, ao ar. As velocidades de corte chegavam a 10m/min. Podiam atingir 65 RC de dureza. Continham carbono de 0,50% até 1,40% e elementos de liga: Si < 0,50%: Mn < 0,70%: S+P < 0,03%: V < 0,50%: Cr < 0,40% Hoje em dia, como ferramenta de usinagem é pouco utilizada, mas ainda são os mais usados na fabricação de ferramentas de estampagem, corte e repuxo e as fermentas manuais como chaves de boca, fenda, alicates etc.
2.. Aços rápidos - (HSS) : Material formado por alta liga de tungstênio, molibdênio, nióbio, cromo, vanádio e cobalto. Têm como principais características:
Entre 1915 e 1941, essas ligas não ferrosas com base em Co, Cr, W e outros, contendo aproximadamente 50% de carbonetos duros eram conhecidas comercialmente como Stellite, Speedaloy, Tungaloy, etc. Podiam trabalhar até a uma temperatura de 800ºC Em 1939, conhecido como aços super rápidos, com altos teores de C e Va, chegavam a uma Vc = 70 m/min. Tinha como base o Co, Cr, W e C acima de 1,5%.
4.. Metal Duro (Cemented carbide): Produto da metalurgia do pó, feito de partículas duras finamente divididas de carbetos de metais refratários, sintetizados com um ou mais metais do grupo do ferro, formando um corpo de alta dureza e resistente a compressão. As partículas duras são carbonetos de tungstênio, usualmente combinados com carbonetos de titânio, tântalo ou nióbio. Com o controle dos metais adicionados, pode-se controlar as propriedades dos metais, oque o torna ideal para as mais variadas operações.
Histórico Em 1920, na Alemanha surge a metalurgia do pó. Em 1926, Krupp, na Alemanha desenvolve a Widia. Nos EUA em 1928 a G.E. desenvolve o Carboloy, uma composição de WC e Co. Em 1930, surge o atual metal duro com Ta, Ti e Nb (carboneto de tungstênio sinterizado, ou cemented carbide). Características;
Processo de Fabricação. O processo de fabricação do metal duro é bastante complexo. A descrição a seguir é genérica, apenas as etapas principais. Dividindo o processo total em quatro etapas, considerando cada etapa como uma unidade de produção, desde o minério ate a pastilha pronta para ser utilizada como ferramenta de corte temos. O minério (shillita) passa por uma série de tratamentos químicos e mecânicos, tais como moagem, lavagem, filtragem e aquecimento a altas temperaturas, até chegar ao tungstênio metálico puro. Com o aquecimento do ácido tungstico, produzimos óxido de tungstênio, o qual pode ser reduzido com hidrogênio a tungstênio puro e água. Após cuidadosa inspeção, o puríssimo pó de tungstênio (W), cuja impureza não exceda a casa dos 0.0001%, é misturado com pó de carbono (C). As proporções da mistura são cuidadosamente determinadas para se obter a correta composição. A mistura é sintetizada à temperaturas ao redor de 1700º C, e durante o aquecimento o tungstênio (W) e o carbono (C) se unem, formando o carboneto de tungstênio (WC). Estes carbonetos são as partículas duras do metal duro. Uma das características importantes do carboneto de tungstênio é sua fácil dissolução em cobalto com a temperatura crescente.
O cobalto é o metal ligante mais usado em metais duros normais, (WC + CO). Em algumas classes de metal duro se usam ainda outros componentes, a respeito dos quais falaremos mais adiante. Os vários pós são misturados em moinhos de bola, onde também se chega a pré-determinadas dimensões de grãos. Os pós metálicos são agora misturados com cera em pó e prensados em forma de briquetes, que podem ser pré-sinterizados a 900º C em atmosfera de proteção, o que provoca o endurecimento tal dos briquetes, que permite o manuseio e sujeições mecânicas para operações de retífica de formação de perfis ou desbastes de forma econômica, diminuindo os refugos e reduzindo os tempos da retífica final, uma vez que ainda não estão na dureza total atingida após a sinterização. Esses briquetes, apesar de pré-sinterizados, têm a consistência aproximada de grafite de lápis e devem ser manipulados cuidadosamente, a fim de evitar avarias nos cantos e arestas. Aqueles briquetes que não receberam o formato final durante a prensagem, são agora usinados. O último estágio de fabricação, a sinterização final durante o qual o briquete se torna uma peça acabada de metal duro em forma de pastilha, é feita a uma temperatura entre 1300º C e 1600º C. Nesta temperatura, o metal ligante se funde e dissolve uma parte dos carbonetos, dos quais 10 a 50% também se encontram em estado de fusão. Durante o processo de sinterização final, o briquete se contrai aproximadamente 20% em direção linear e 50% no volume, e qualquer porosidade é eliminada.
Metal duro com cobertura : Metais com cobertura de carboneto de titânio e/ou óxido de alumínio, nitreto de titânio e carbonitreto de titânio. A principal finalidade destas camadas é aumentar a resistência ao desgaste da camada superior que entra em contato com o cavaco e com a peça. Com isto podemos elevar a vida útil da ferramenta. As camadas são em geral aplicadas pelo processo de deposição química de vapor. Óxido de Alumínio: garante estabilidade térmica em temperaturas elevadas, possui alta resistência ao desgaste por abrasão, além de alta resistência a ataques químicos e oxidação. Nitreto de titânio: reduz o coeficiente de atrito, é quimicamente + estáveis que o TiC, tem menor tendência a difusão com aços, espessura da camada entre 5 a 7F 06 D m. 5.. Material cerâmico : Base de óxido de Alumínio: formada por finos grãos de alumínio sintetizados podendo apresentar algum teor de MgO, óxido de cromo, titânio e níquel aumentando a resistência mecânica ou alumina com baixo teor de óxido de zincônio p/ aumentar a tenacidade. Base de Nitreto de sílica: cristais de Si3N4, com fase intergranular de Sio2, sinterizados na presença da alumina(sialon) ou óxido de ítrio (Y2O3) e manganês(MgO). Aplicações da cerâmica:
Material Custo relativo da ferramenta (US$)
Velocidades de corte típicas (m/min)
Custo de usinagem (US$/pol^3 ) Aço carbono 0,10 12,2 0, Aço rápido 0,50 27,5 0, Liga fundida (Stellite) 2,00 45,8 0, Metal duro 5,25 152,5 0, Material cerâmico 12,00 244,0 0,
Comparação de materiais para ferramentas de corte: Tabela VII.31, Fundamentos da Usinagem dos Metais. Valores referentes a um bit quadrado de 3/8” de seção, empregado na usinagem de SAE-4140 encruado. Adotado US$6,00/hora como custo total de mão de obra e despesas indiretas.
O processo de formação do cavaco é periódico, isto é, passa gradativamente por etapas de formação e, quando completadas, reinicia novamente.
2.1.. Etapas de formação do cavaco: 1 - Deformação plástica 2 - Surgimento da zona de cisalhamento 3 - Deslizamento sobre a superfície de saída da ferramenta. 4 - Repetição do processo
2.2.. Grau de recalque: Em experiências em laboratórios, e oficinas de usinagem, observando-se os fenômenos acima, notou-se que há um engrossamento do cavaco durante o processo de usinagem seja ela qual for. A isso chamamos de grau de recalque ou Rc.
RC = h’/h h’ - espessura real do cavaco h - espessura teórica do cavaco
2.3.. Tipos de cavaco: Segundo a literatura Alemã e Americana, existem 3 tipos de cavacos:
2.3...1... Contínuo - Apresenta-se sob a forma de lamelas justapostas distribuídas continuamente, não sendo nítidas as suas separações.
2.3...2... Cisalhamento - Apresenta grupos lamelares bem distintos e justapostos. Estes elementos foram cisalhados na região de cisalhamento e soldados novamente em seguida.
2.3...3... Ruptura - São fragmentos retirados da peça.
2.4.. Formas de cavaco: Cavaco em fita, Cavaco helicoidal, Cavaco espiral, Cavaco em lascas.
Dos 4 tipos de cavaco, o mais indicado é o cavaco espiral, pois o cavaco de fita é perigoso e ocupa muito volume ao ser descartado.
Sabendo-se que existem problemas para o manuseio de cavacos, sabendo-se que existem formas diferentes de cavacos, então podemos alterar formas de cavacos de tal maneira a adaptar a melhor maneira de manuseá-lo. Sendo assim, poderemos utilizar os seguintes artifícios para mudar a forma do cavaco:
Mediante o exposto acima, devemos lembrar que também a geometria da ferramenta tem influência na chamada Aresta Postiça de Corte que é formada pelo acúmulo das partículas do material usinado na superfície de desprendimento do cavaco que aparece quando a V (^) C é muito baixa ou a geometria da ferramenta é negativa ou há necessidade de fluido de corte.
O fluído de corte também tem influência no acabamento da peça e na formação do cavaco.
Nomenclatura:
2.5.. (^) Torneamento
É um processo mecânico de usinagem destinado a obtenção de peças cilíndricas ou superfícies de revolução com o auxílio de uma ou mais ferramentas mono-cortantes. A peça gira em torno de um eixo principal de rotação da máquina e a ferramenta se desloca simultaneamente segundo uma trajetória retilínea coplanar com o referido eixo.
2.5...1... Torneamento retilíneo 2.5...1....1.... Cilíndrico - Quando a ferramenta se desloca segundo uma trajetória paralela ao eixo principal de rotação da máquina.
Externo - Interno -
2.5...1....2.... Cônico: Quando a ferramenta se desloca segundo uma trajetória inclinada em relação ao eixo principal.
Externo Interno -
2.5...1....3.... Radial: Quando a trajetória da ferramenta é perpendicular ao eixo de rotação da máquina. Esta operação também é chamada de faceamento. Quando se obtém uma superfície plana no topo da peça.
Faceamento: Sangramento:
2.5...2... Perfilamento: Quando a ferramenta tem o perfil desejado.
2.5...3... Torneamento Curvilíneo: Quando a ferramenta se desloca segundo uma trajetória curvilínea. Antigamente feito em torno copiador. Hoje pode ser feito em torno CNC.
2.6.. Aplainamento: Para obtenção de superfícies geradas por um movimento retilíneo alternativo da peça ou ferramenta.
2.7.. Furação: Para obtenção de furo, geralmente cilíndrico numa peça com o auxílio de uma ferramenta bi ou multicortante ( broca ).
2.5...1....4.... Furação em cheio: Quando a ferramenta remove todo o material envolvido no volume do furo.
2.5...1....5.... (^) Furação com pré-furação: Quando existe um furo com diâmetro menor para ser alargado.
2.5...1....6.... Escareamento: Para a obtenção de um furo cônico em uma peça pré-furada.
2.5...1....7.... (^) Furação escalonada: Para obtenção de peças furadas com vários diâmetros diferentes.
2.8.. Fresamento: Para obtenção de uma superfície qualquer com o auxílio de ferramentas multicortantes. A ferramenta gira e a peça se desloca.
2.3...4... Fresamento cilíndrico ou tangencial: 2.3...4....1.... Concordante:
5.1.. Movimento principal de corte: É o movimento de rotação uniforme da peça ou ferramenta. É o movimento que provoca o arranque do material.
5.2.. Movimento secundário (avanço): É o movimento de translação da peça ou ferramenta que sempre encontra o material a ser removido.
5.3.. Velocidade de corte: É a velocidade de um ponto qualquer de referência comum a peça a ferramenta. V (^) C = F 07 0 x F 0C 6 x n / 1000 onde n [rpm] ; F 0C 6 [mm] ; VC [m / min]
5.4.. Avanço: É o percurso da ferramenta em uma volta dada pela peça. s = a = ( mm/ volta)
5.5.. Profundidade: É a espessura do material removido. p = (mm)
5.6.. Largura e espessura do cavaco: b = (mm) h = (mm)
5.7.. Velocidade de avanço: V (^) a = a x n Onde; a = mm/volta n = volta/min (rpm) V = mm/min
5.8.. Índice de esbeltez: G = p / a
5.9.. (^) Área do cavaco: AC = p. a = b. h
cos γ / tg φ = Rc – sen φ
F 0 D E tg^ φ^ = cos
F 0 6 7 / (R^ C^ - sen F 0 6 7 )^ (eq.1)
Exercício:
Determine o ângulo de cisalhamento φ em função do recalque para: F 0 6 7 = +10°^ F 0 6 7 = - 10°
RC tg φ φ RC tg φ φ 1 1,1917 50 ° 1 0,84 40 ° 2 0,5392 28,33° 2 0,45 24,37° 3 0,3484 19,21° 3 0,31 17,24° 4 0,2573 14,43° 4 0,24 13,28° 5 0,2040 11,53° 5 0,19 10,78°
Plotar RC = f ( φ)
6.3 - Relações Cinemáticas:
Correspondendo aos três planos acima assinalados, pode-se distinguir as três velocidades relativas:
Análise do processo de usinagem
Identificação das classes
Quando usar Ferramentas Positivas.
Quando usar Ferramentas Negativas.