
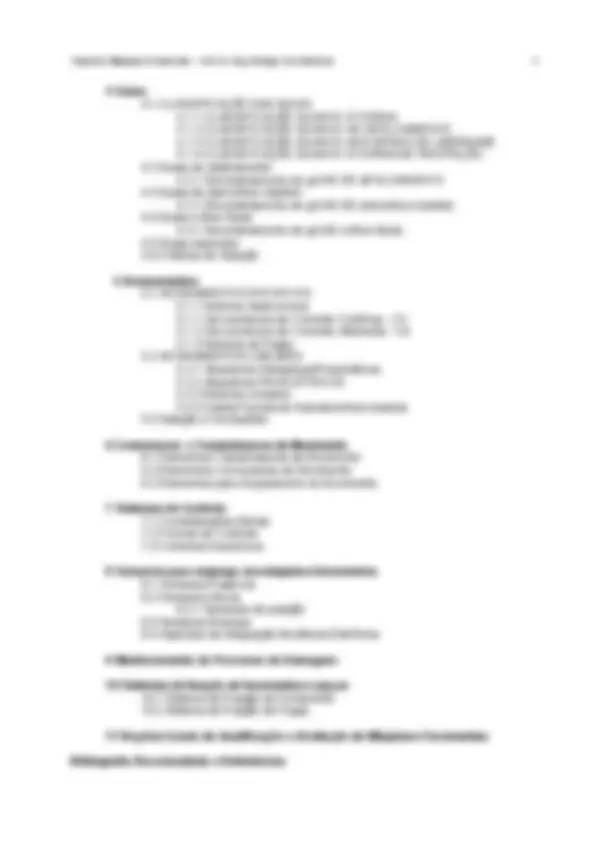
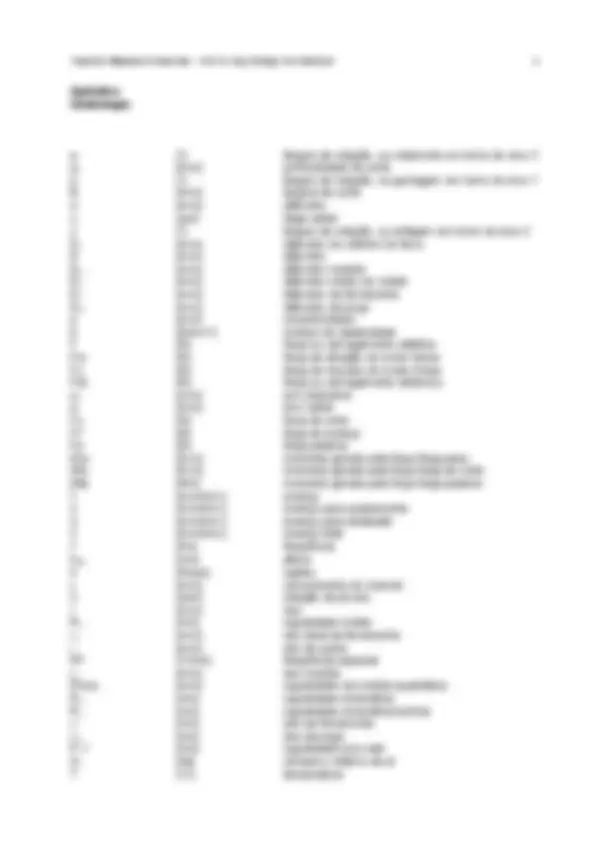
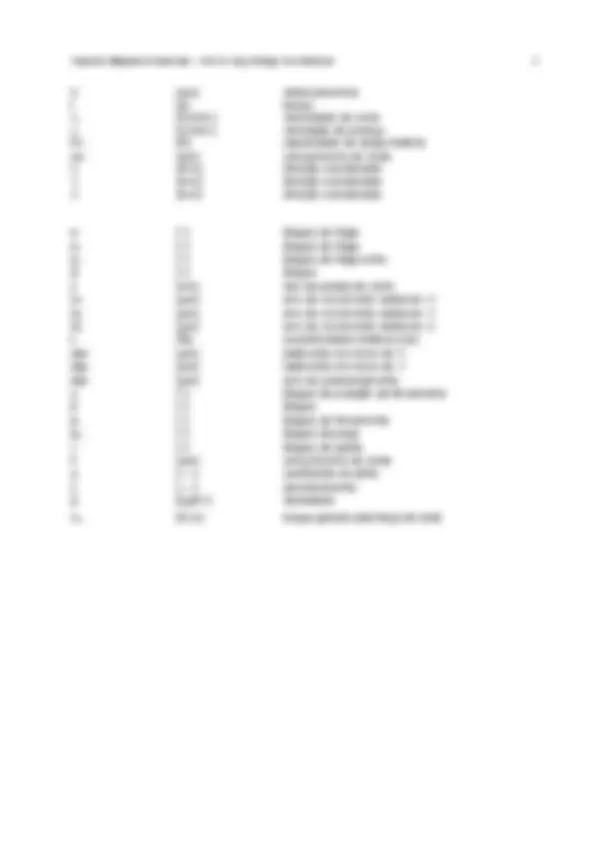
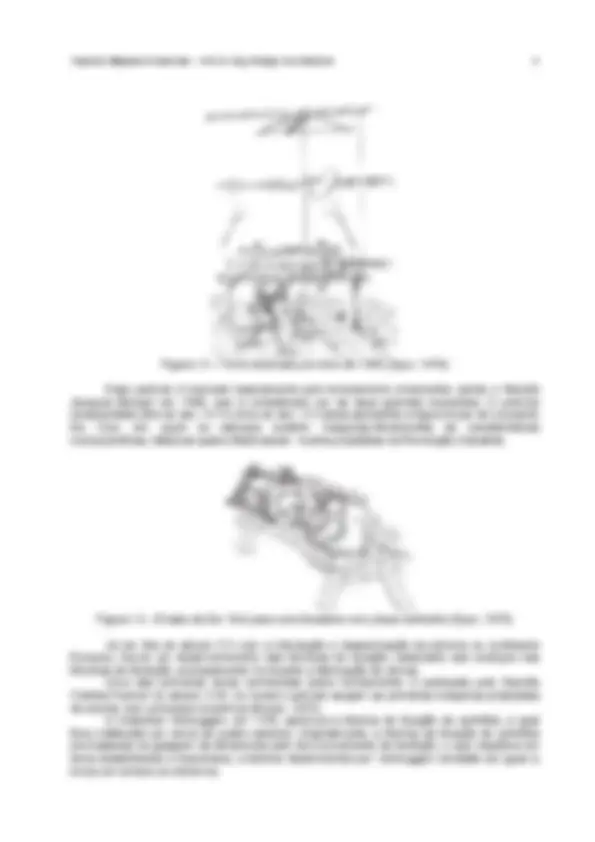
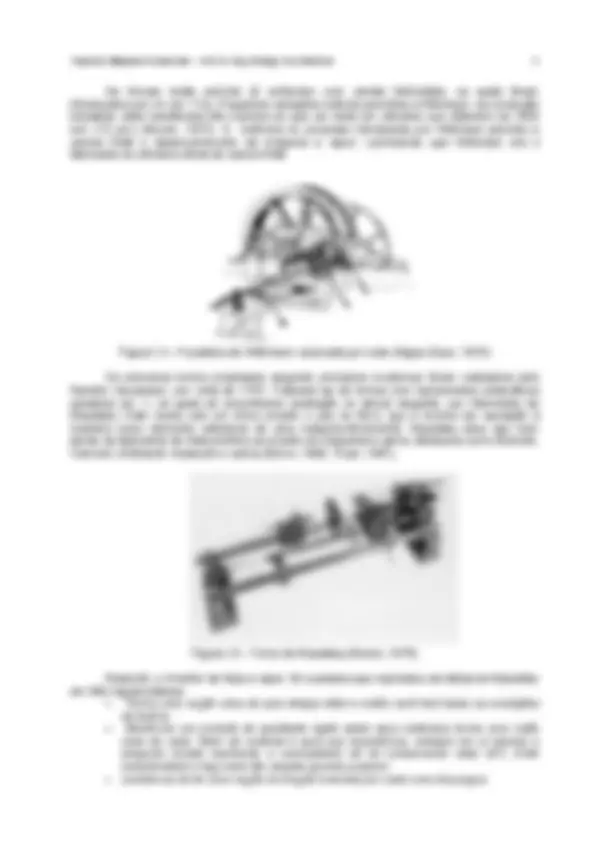
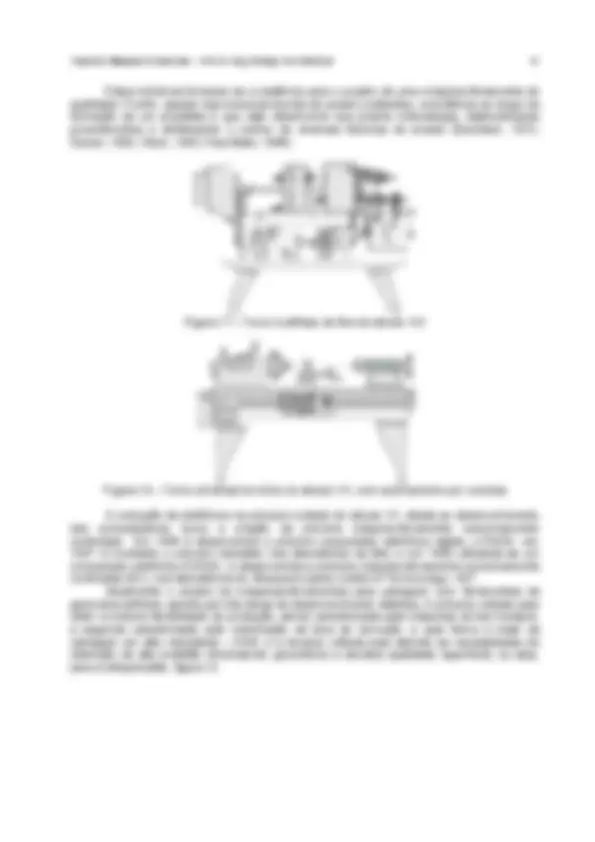
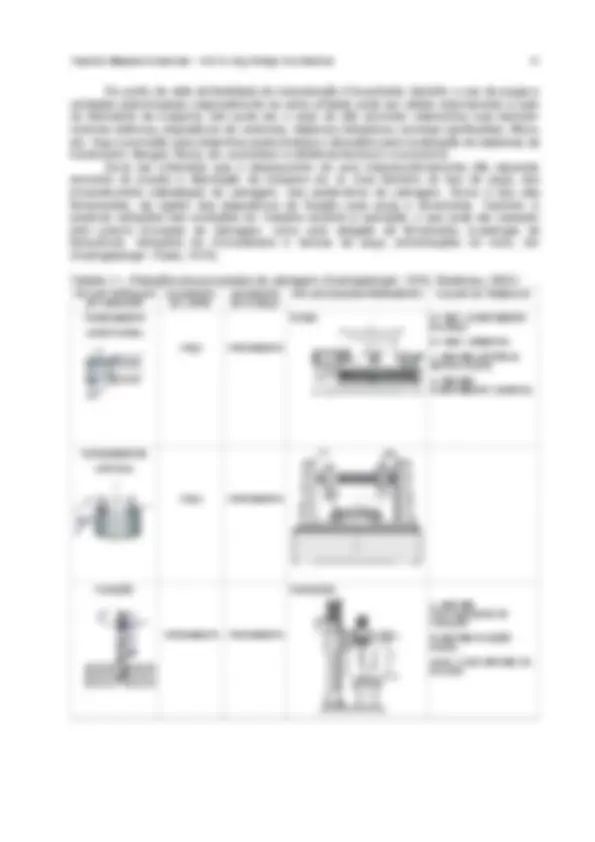
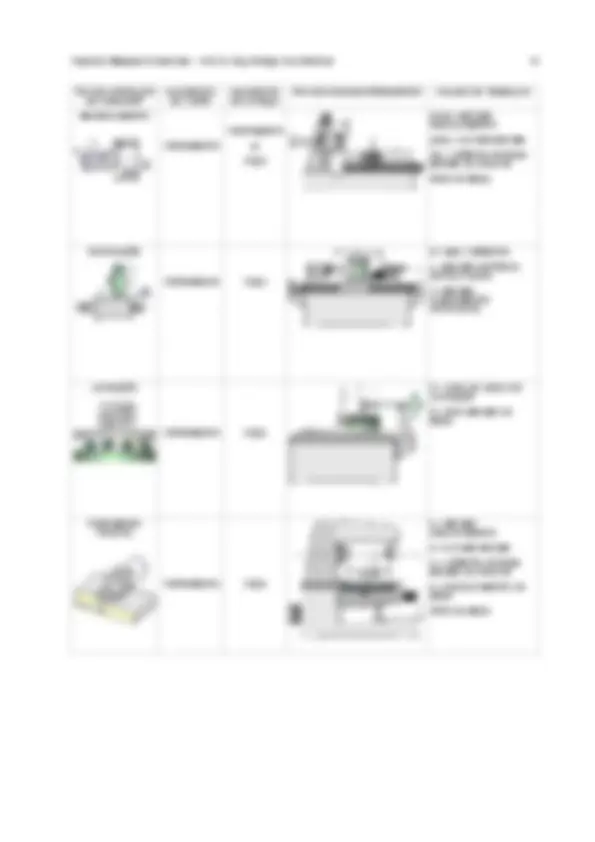
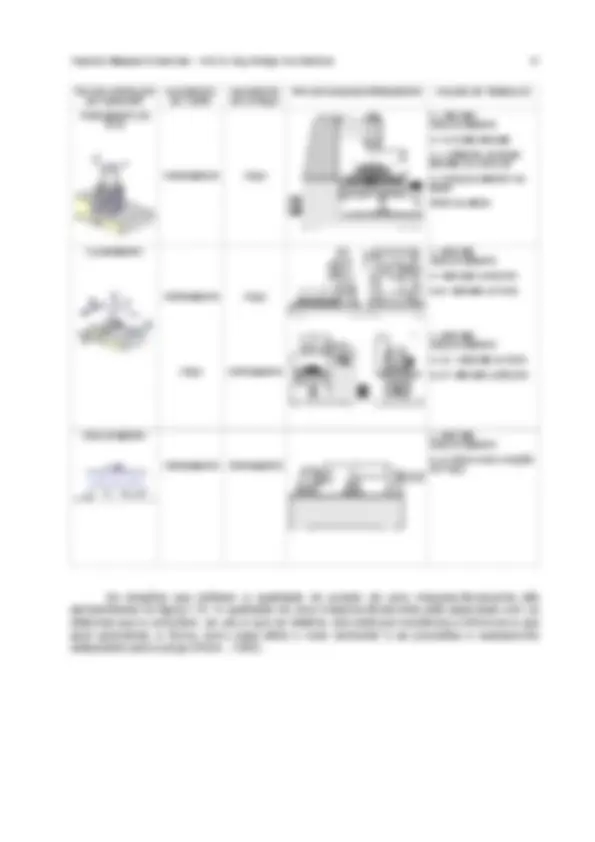
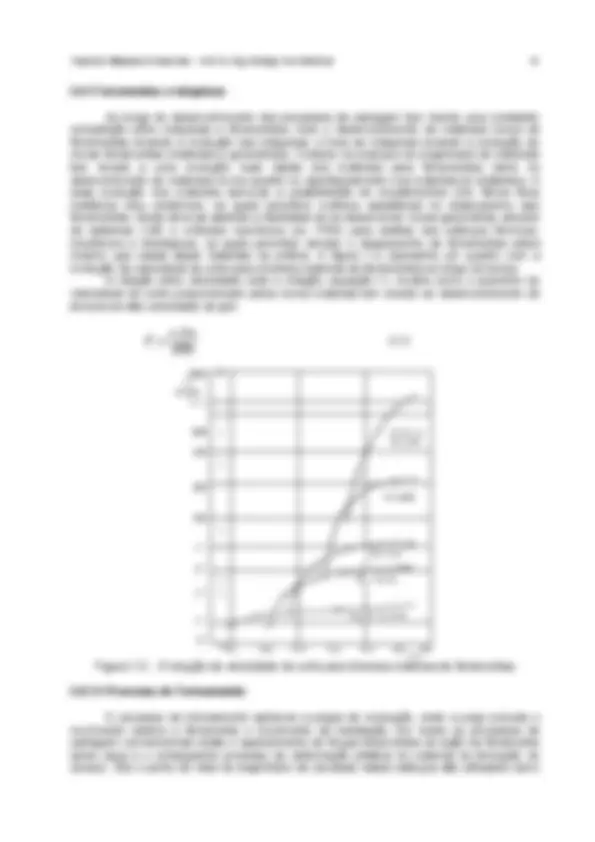
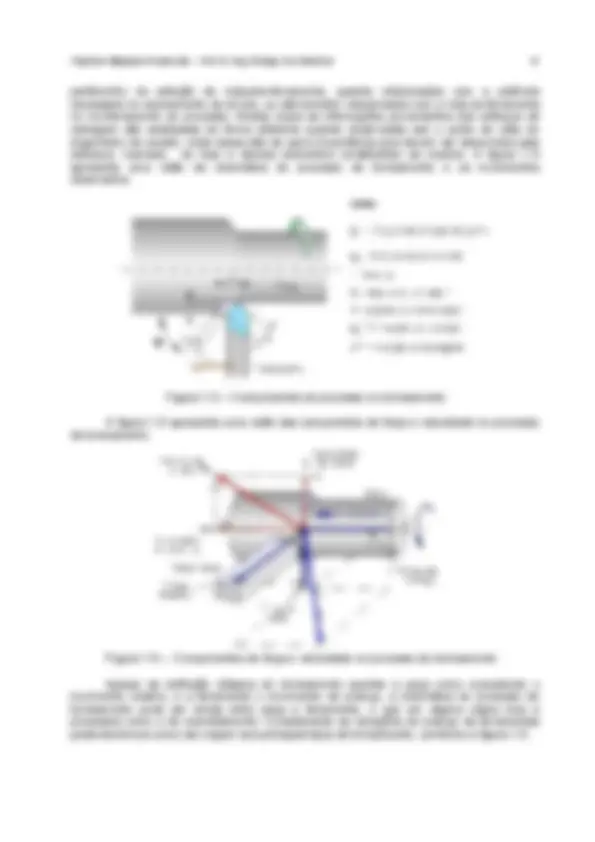
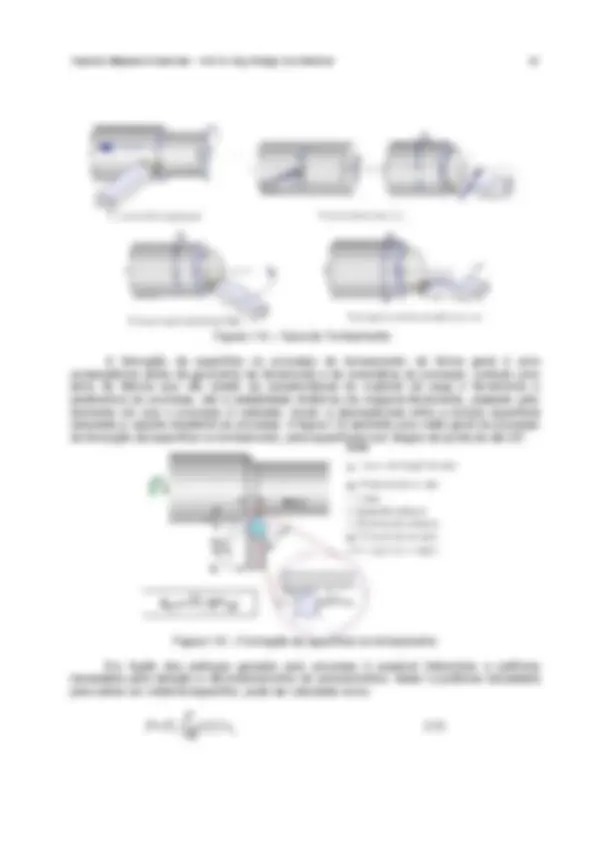
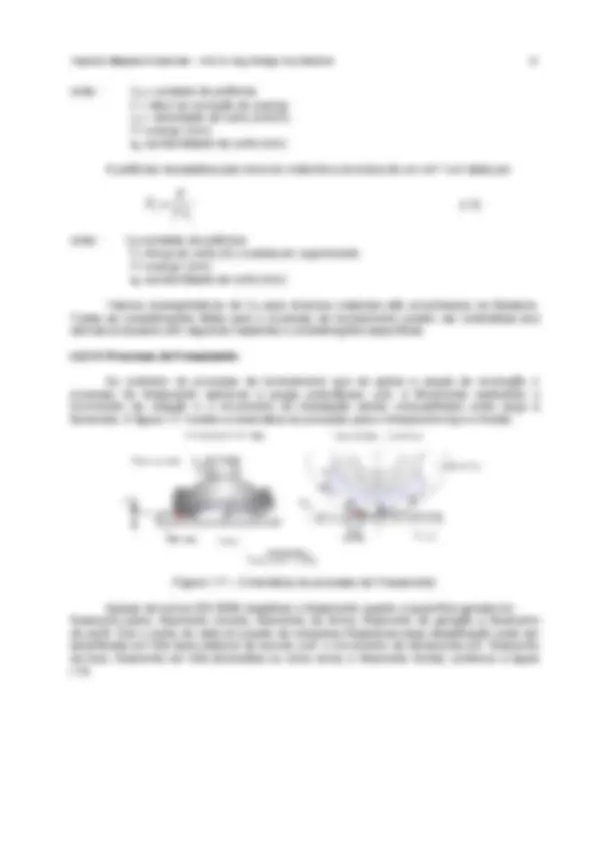
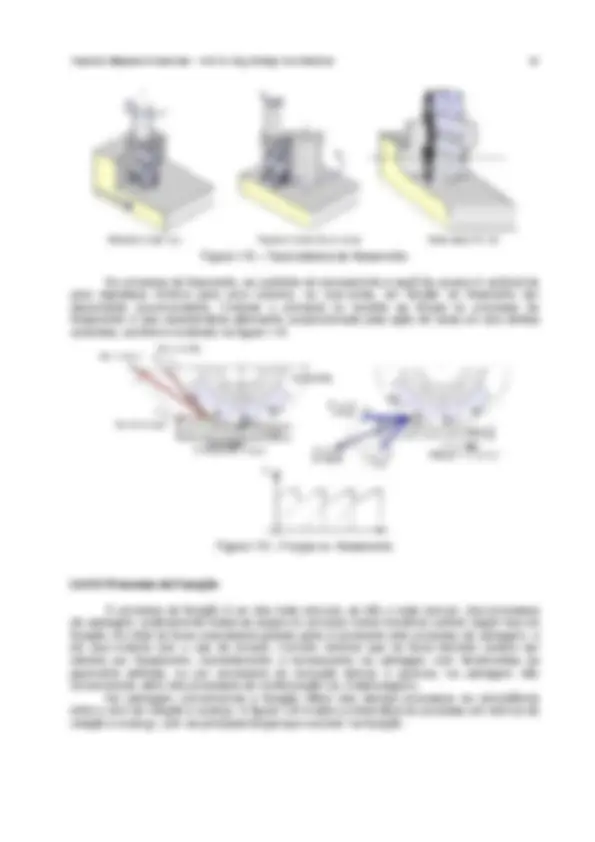
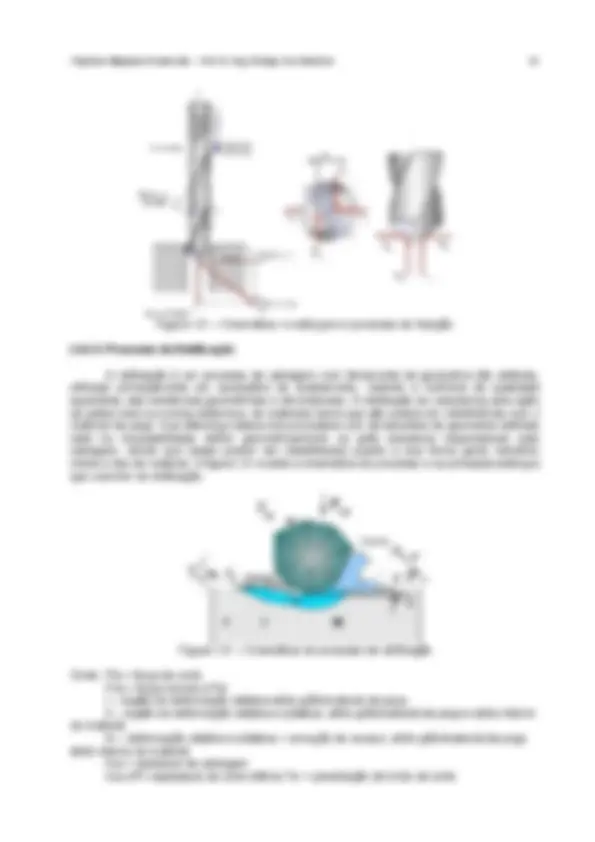
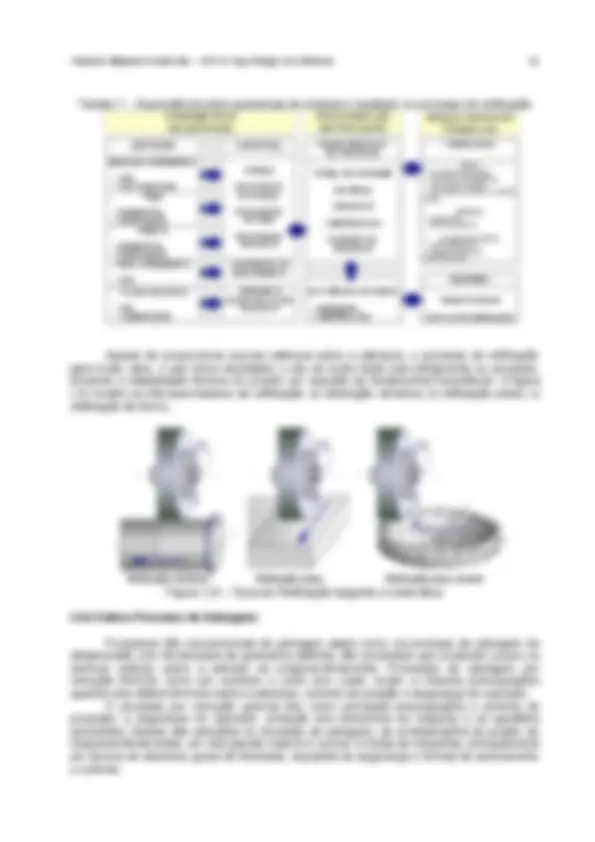
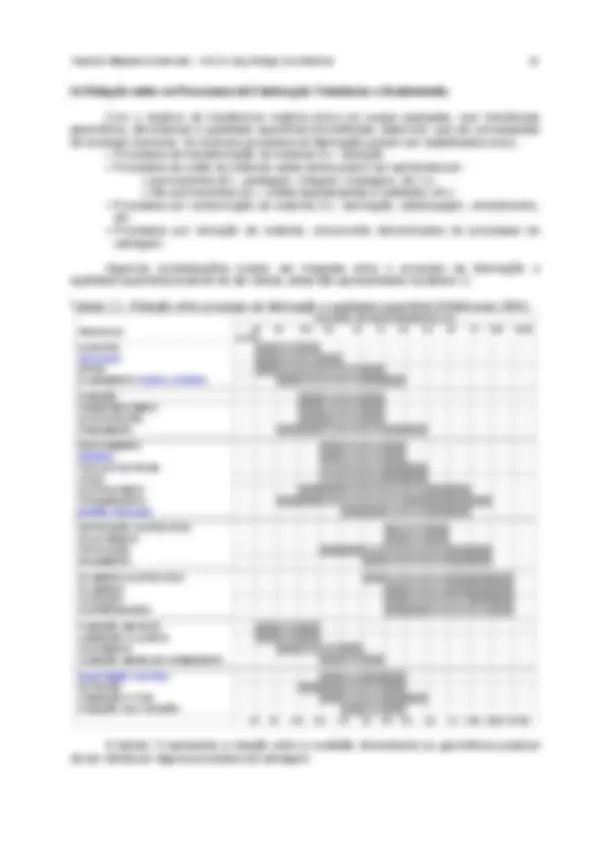
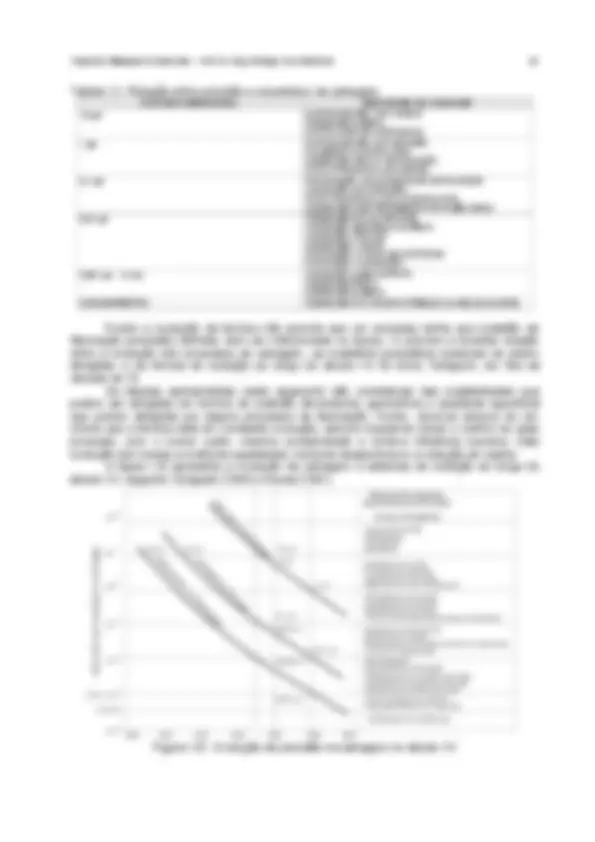
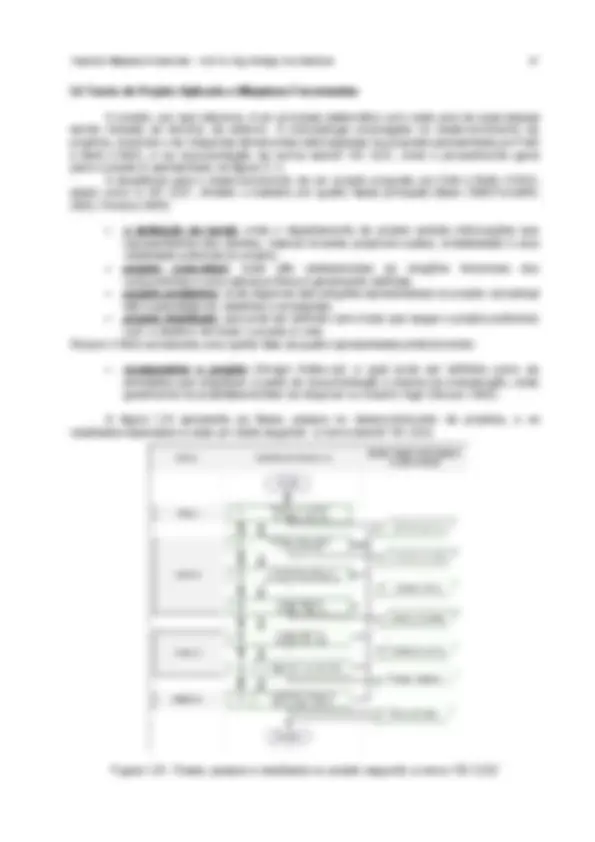
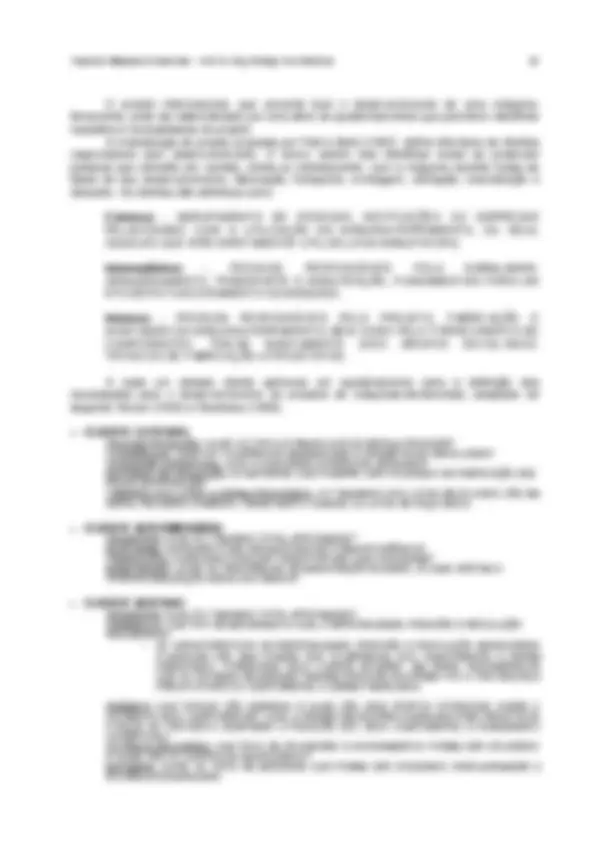
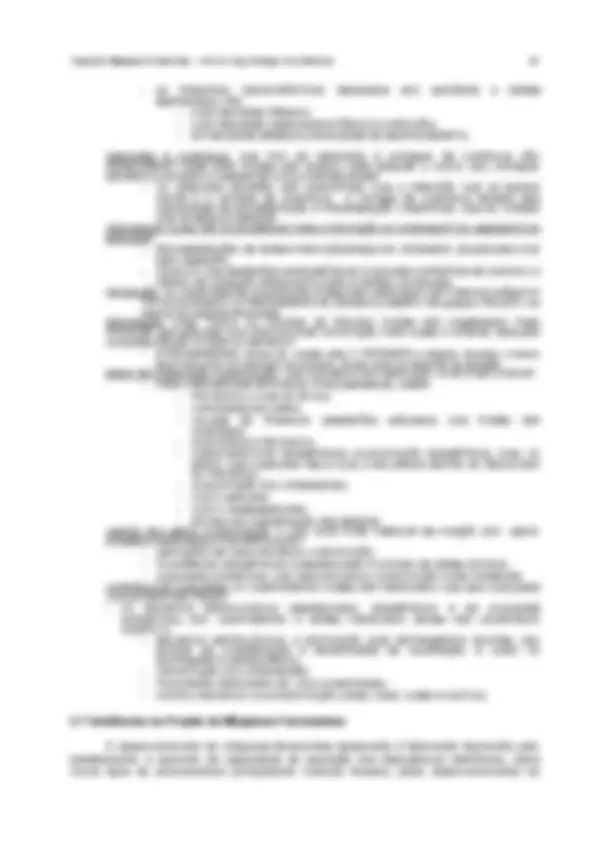
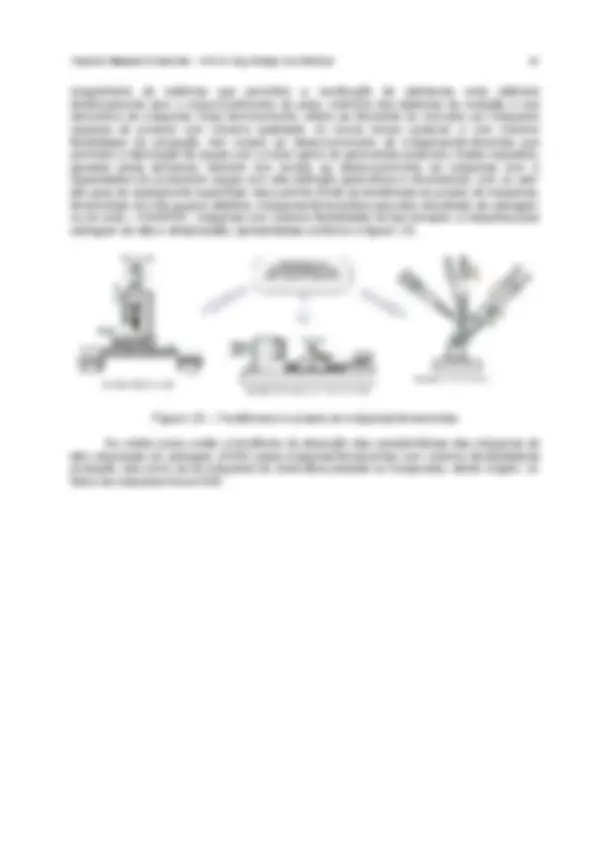
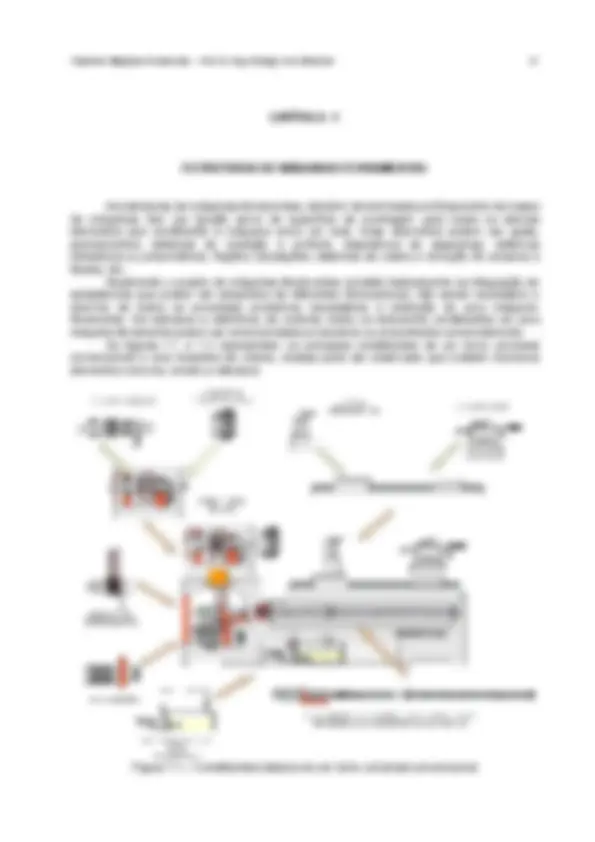
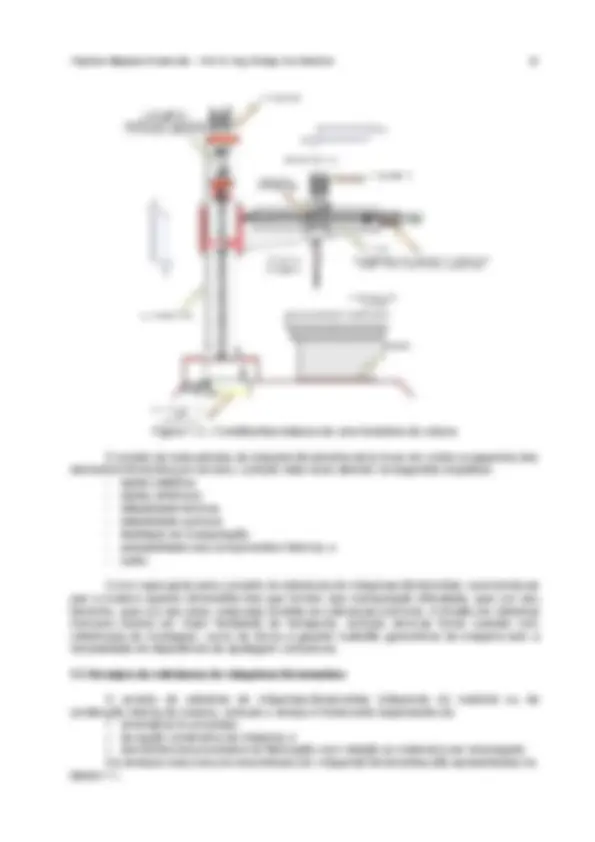
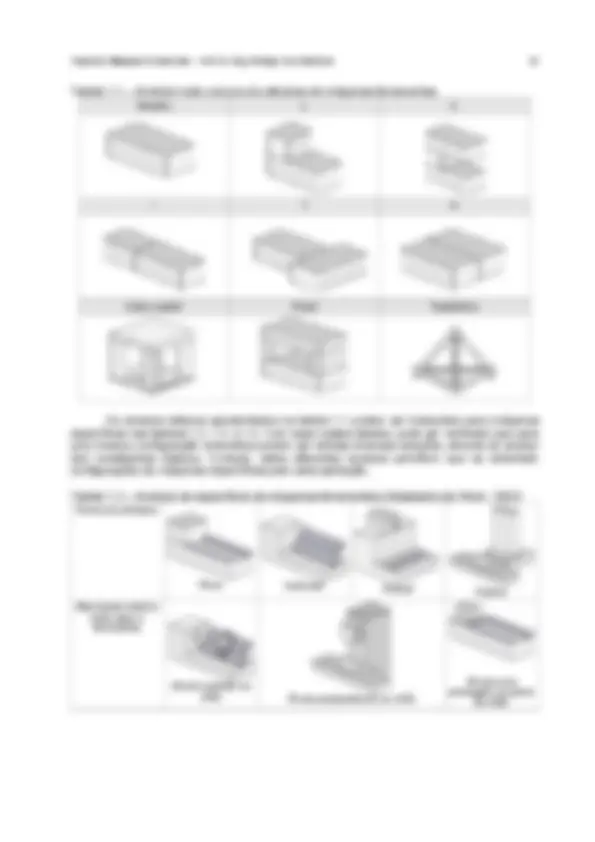
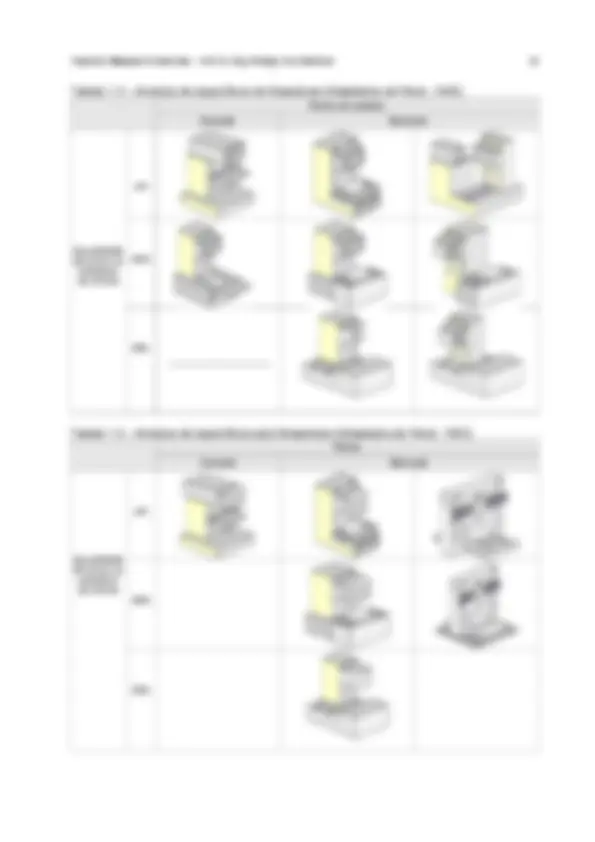
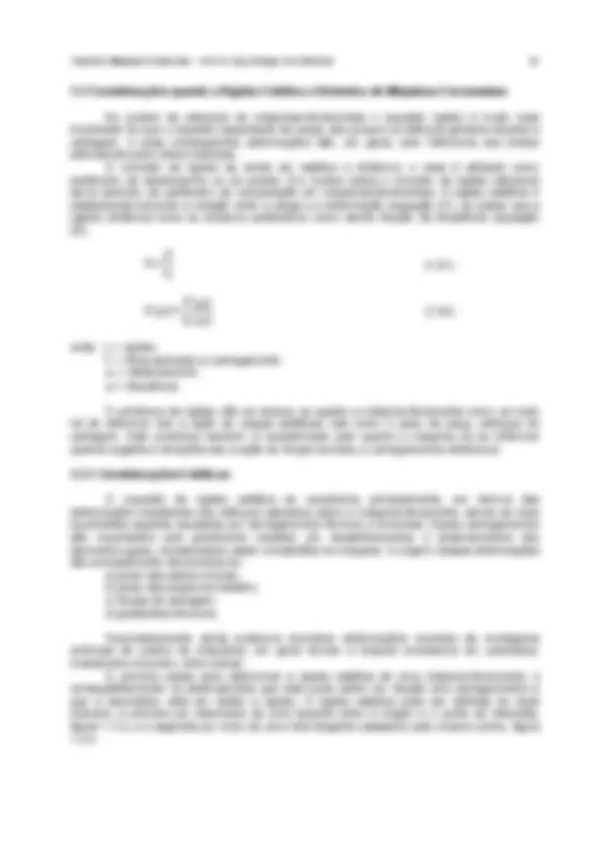
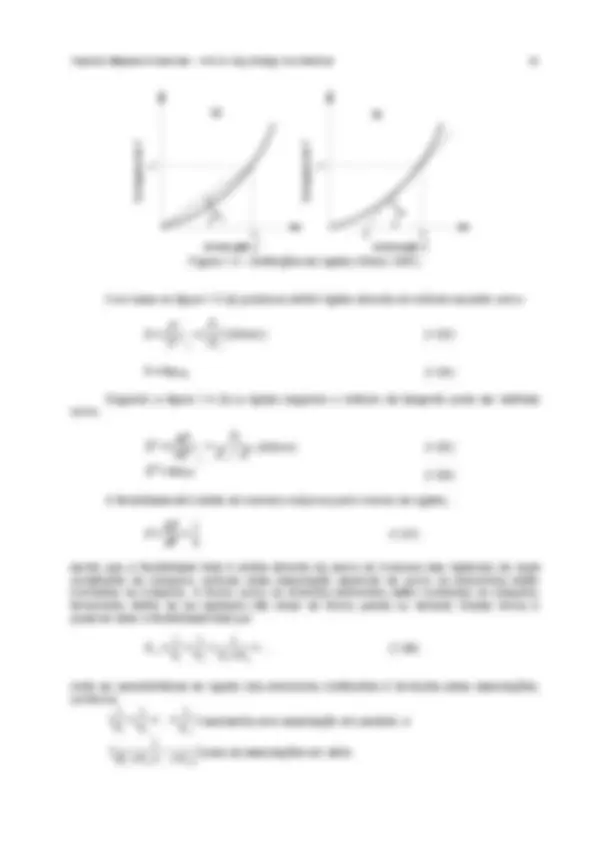
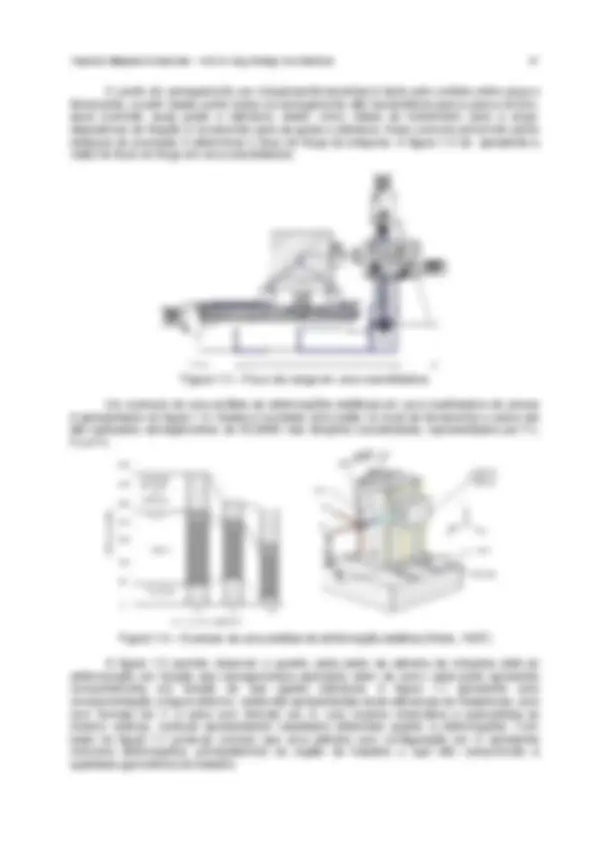
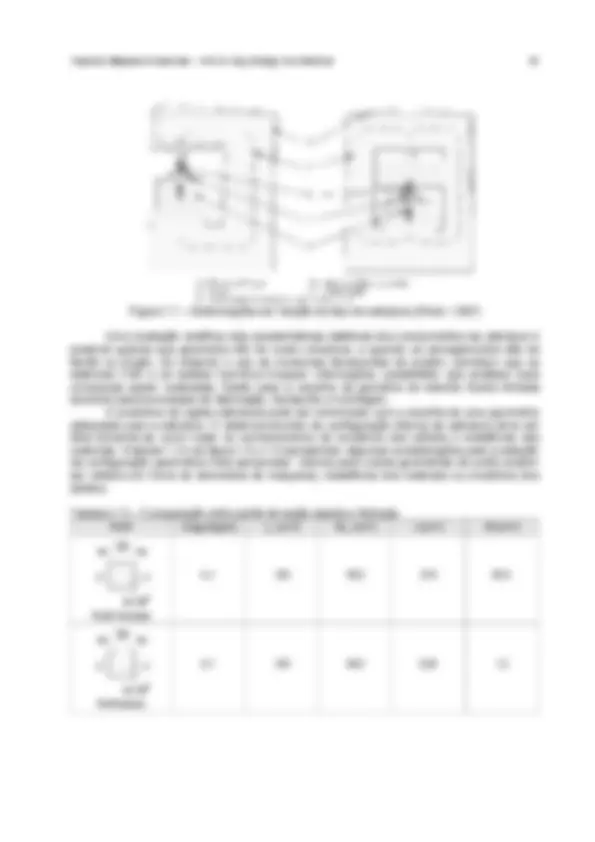
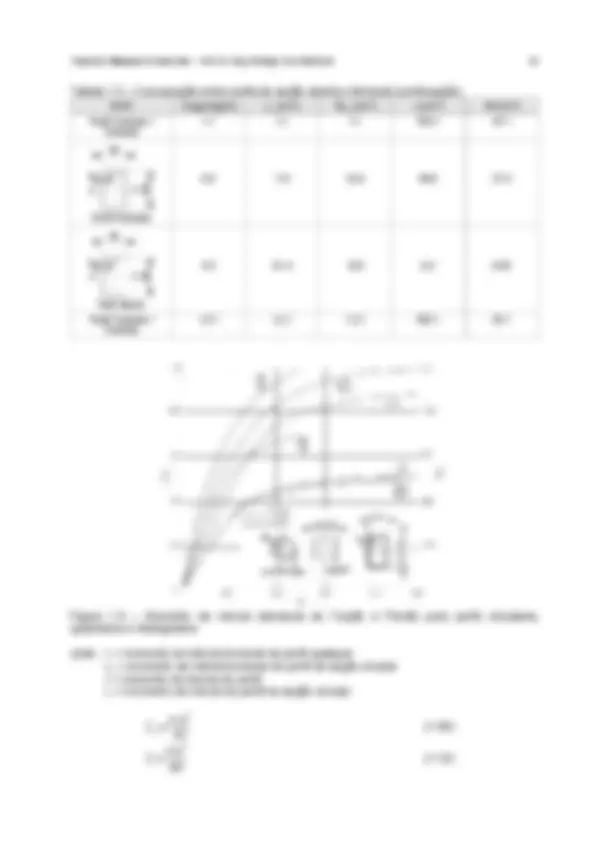
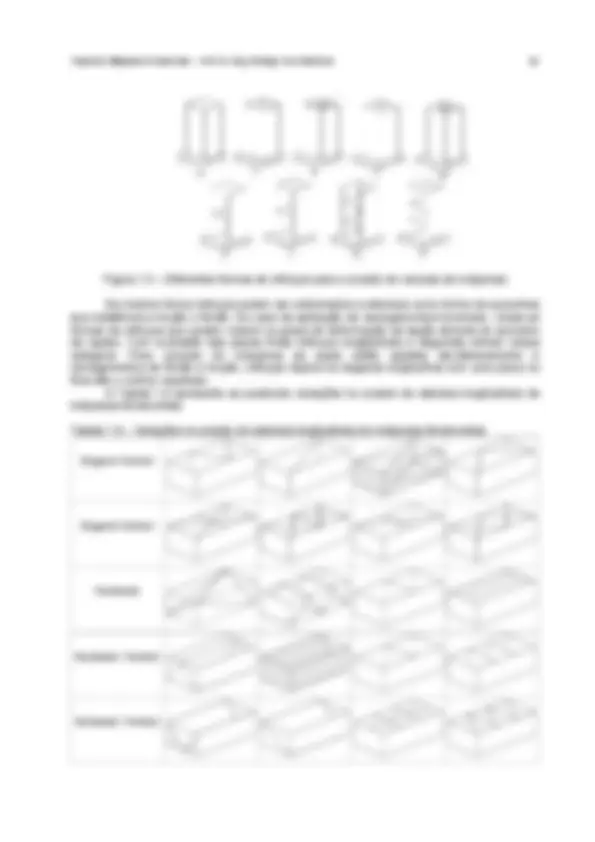
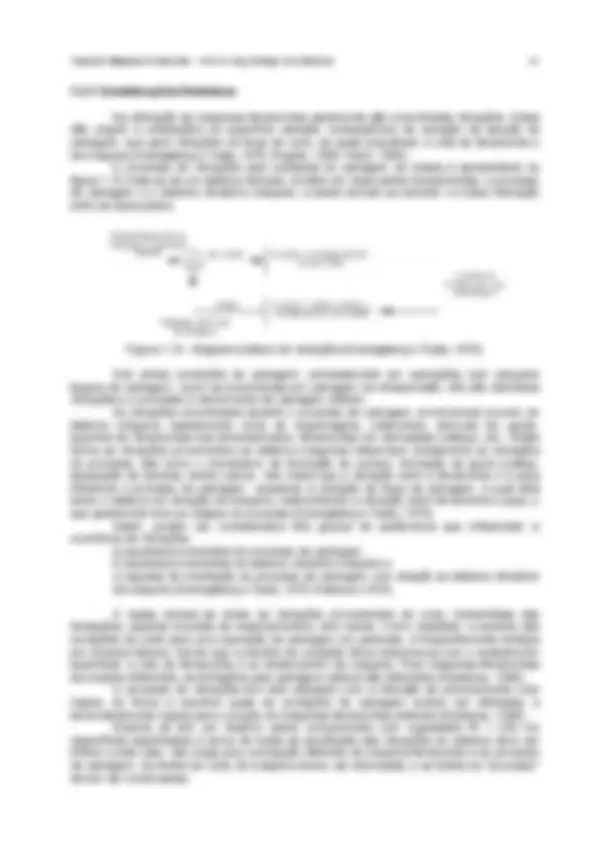
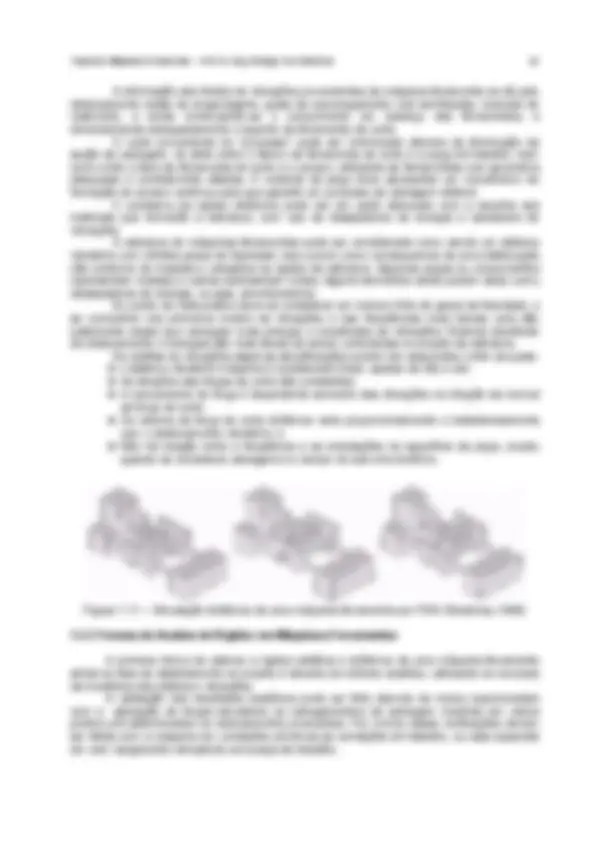
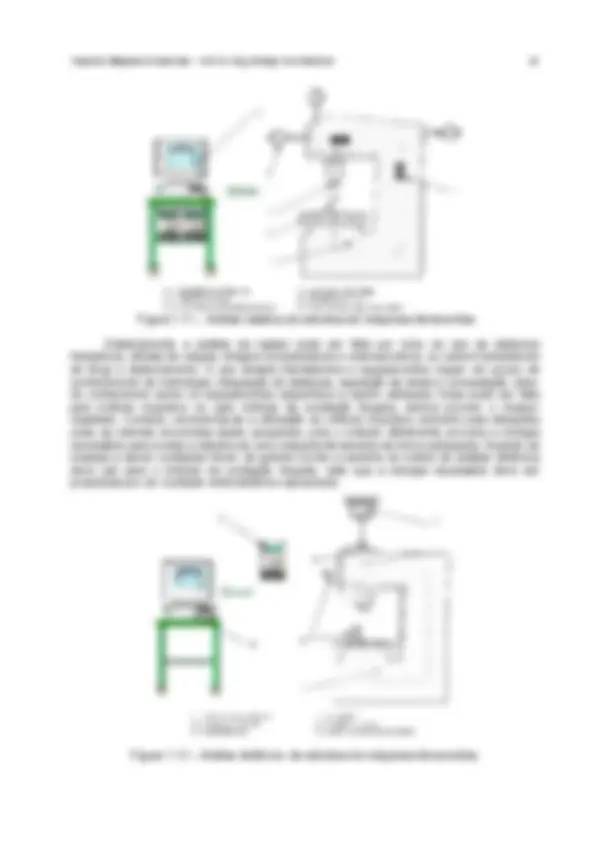
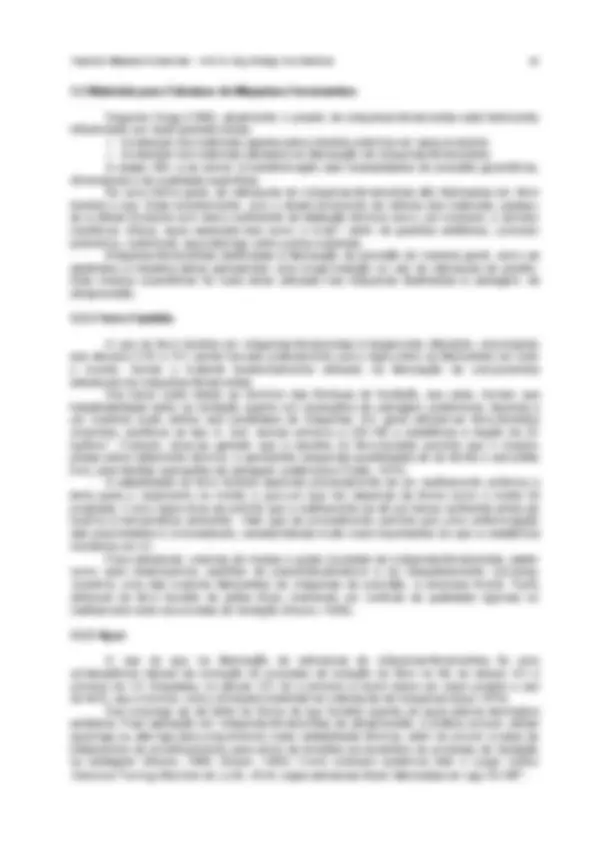
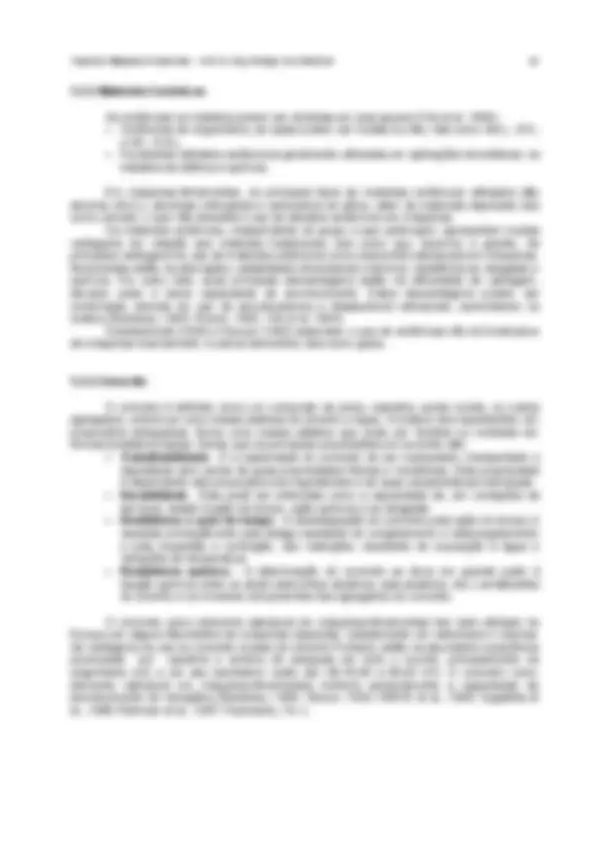
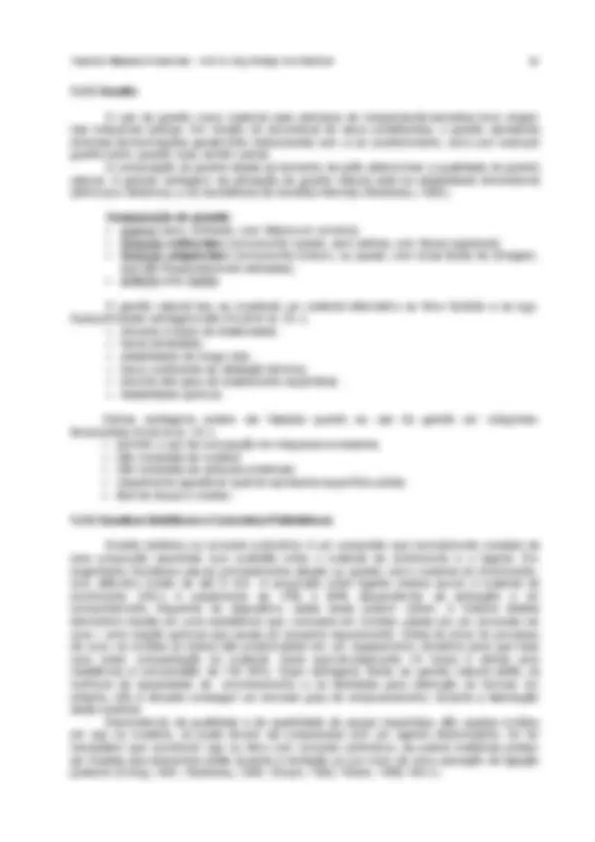
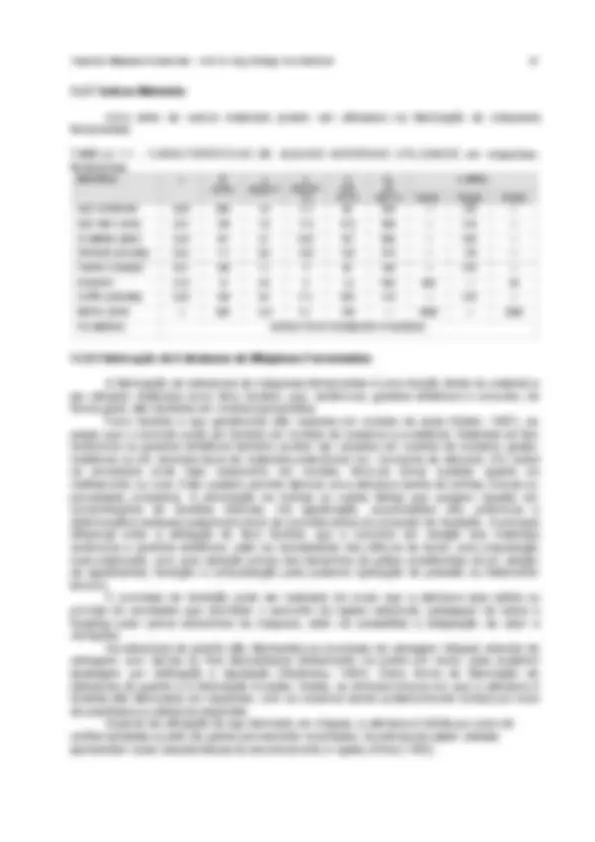
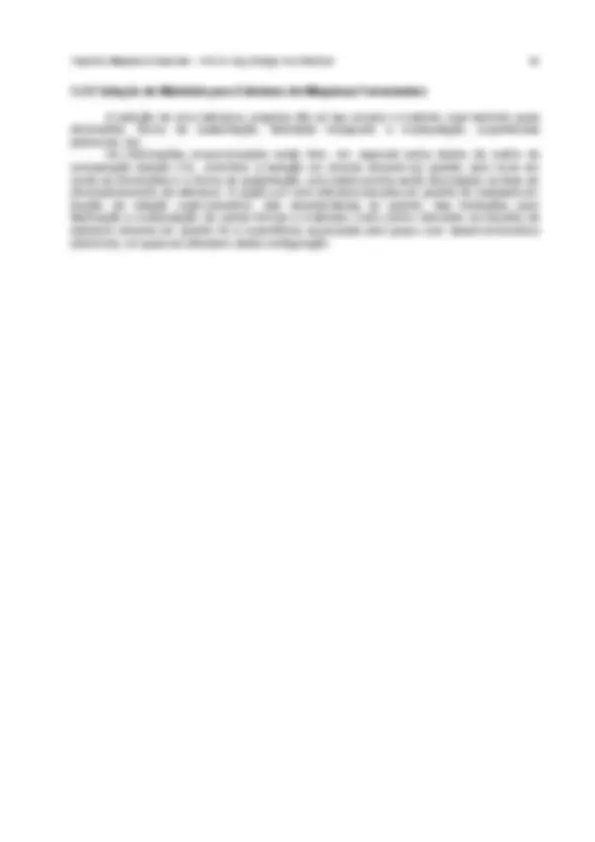
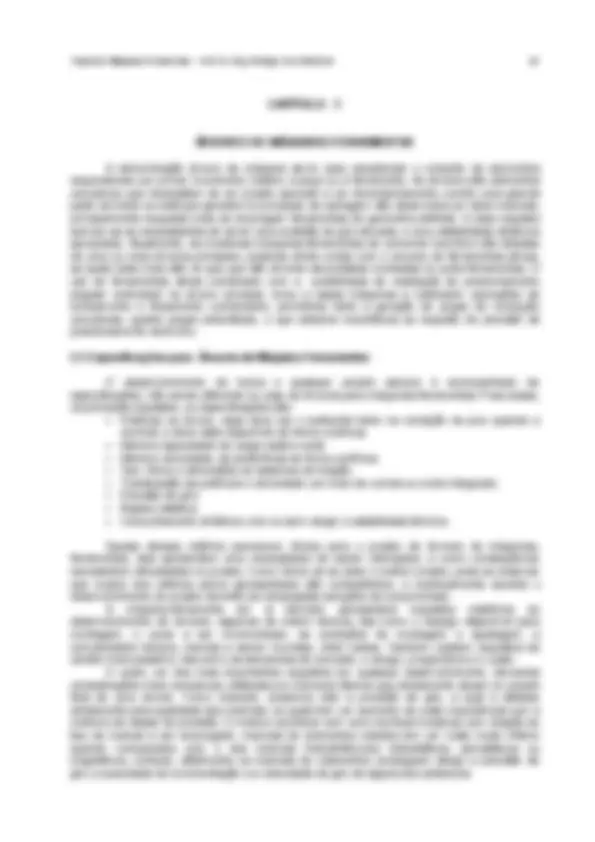
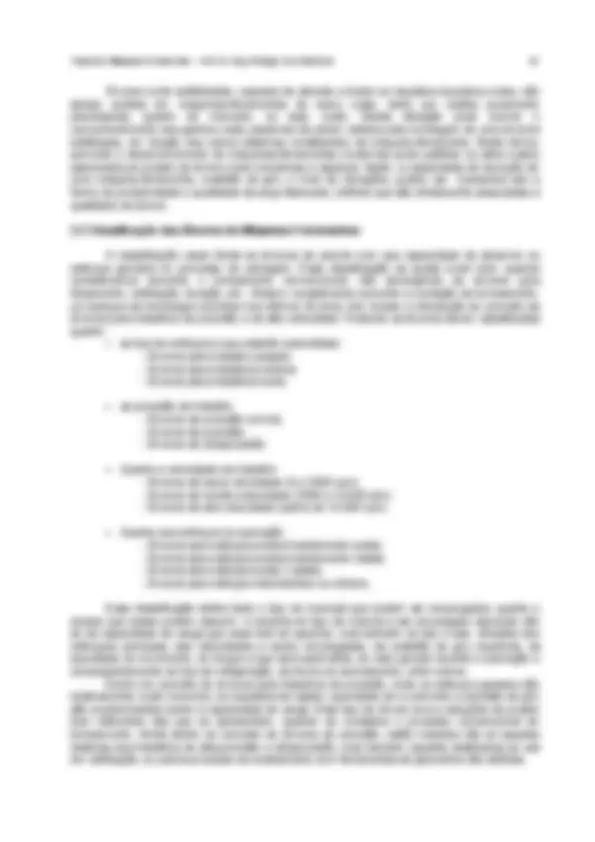
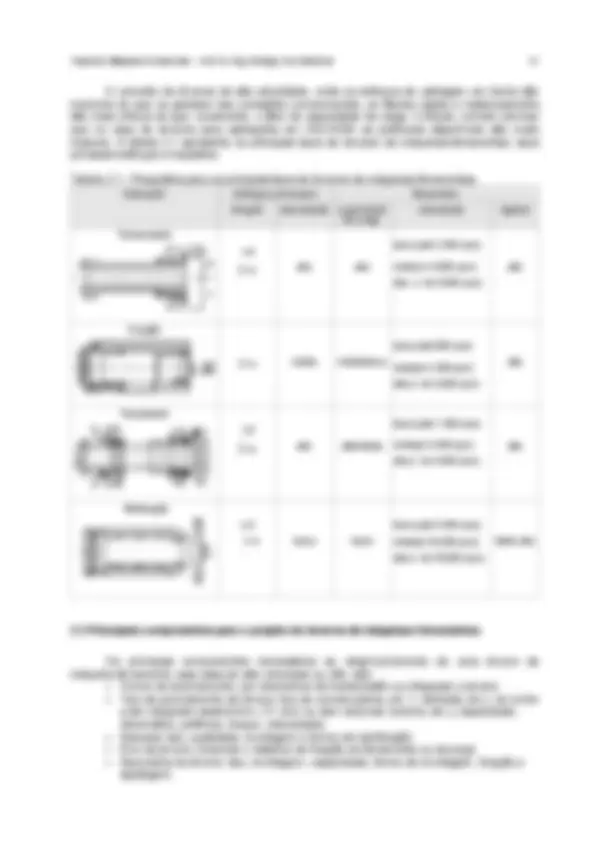
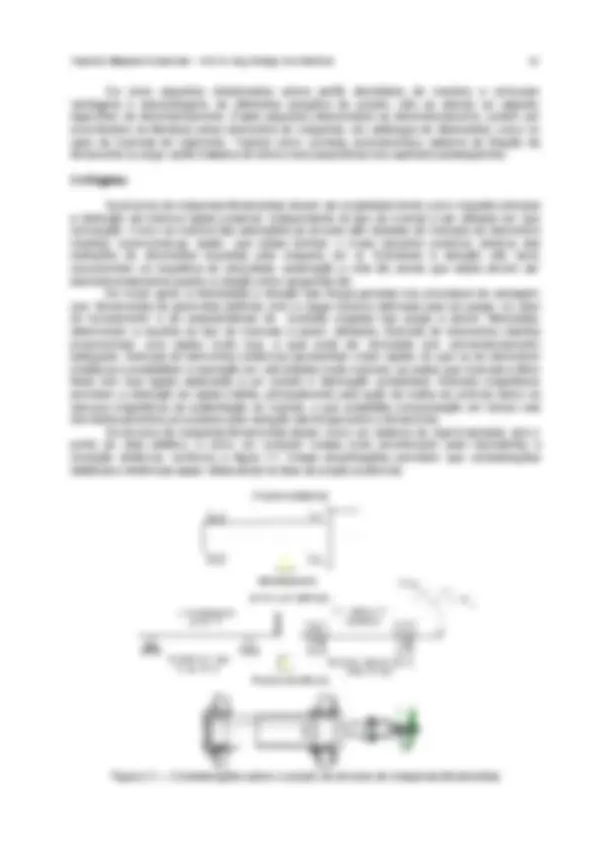
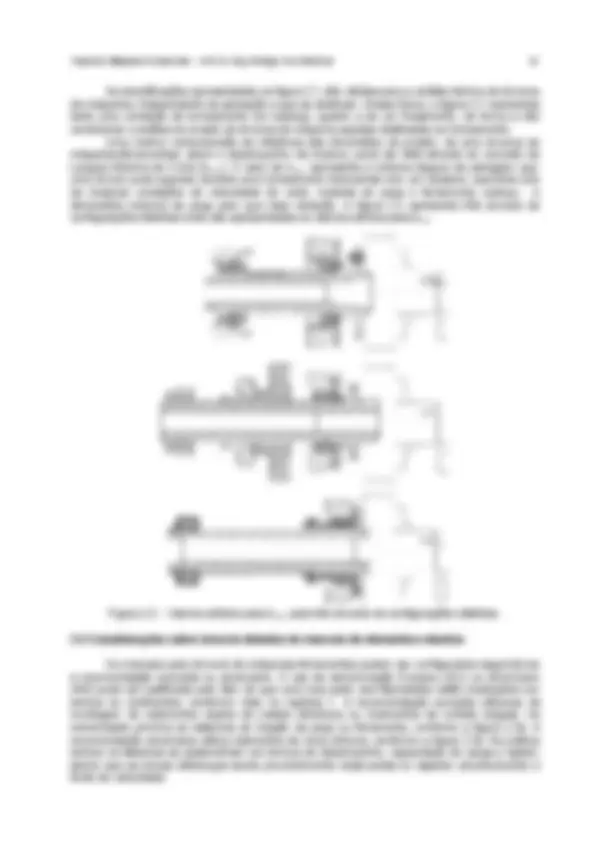

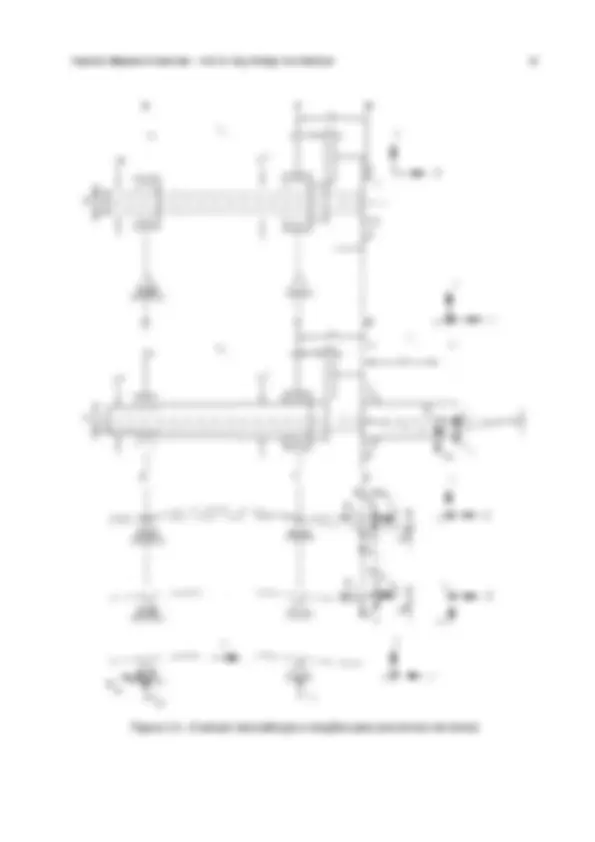
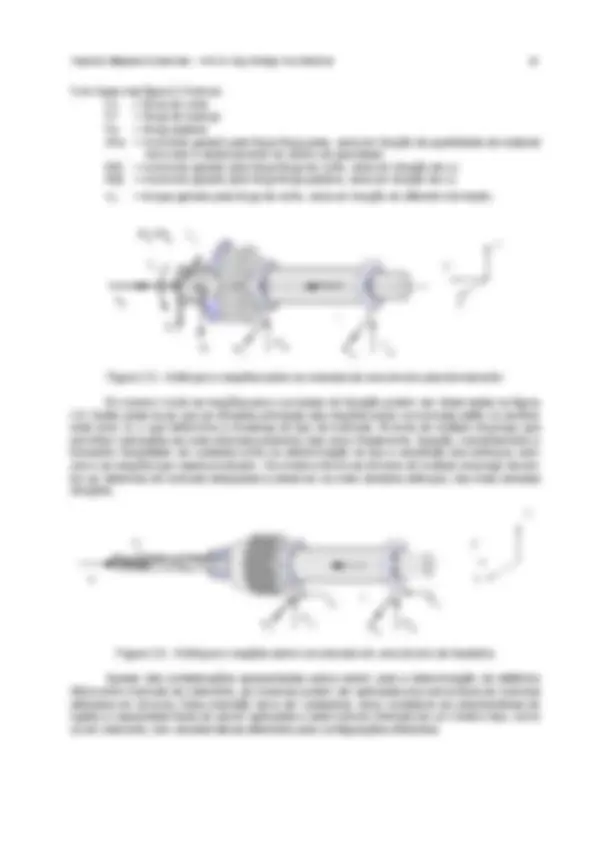
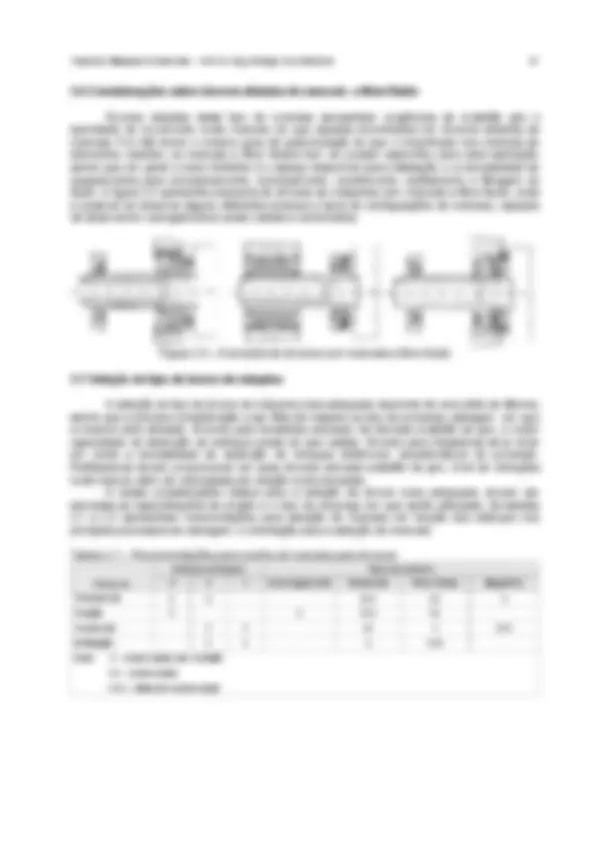
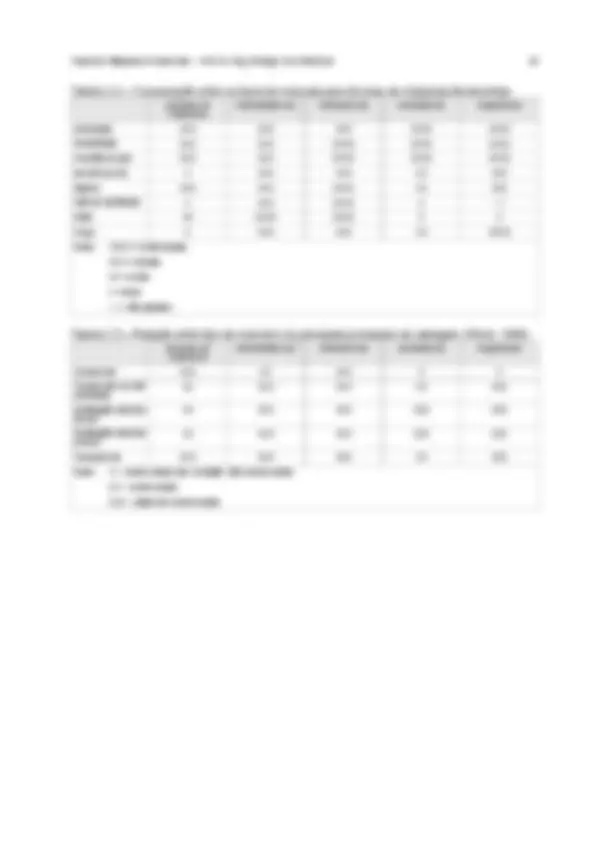
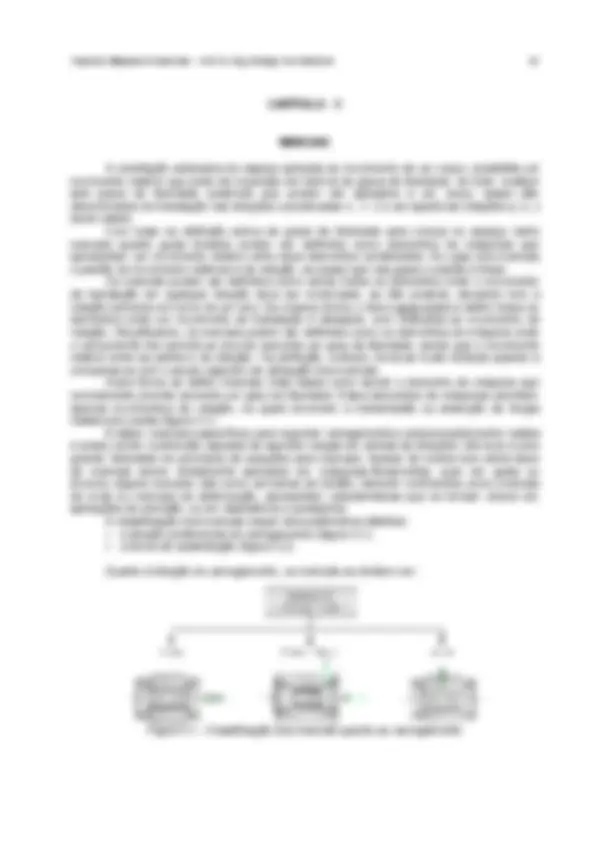
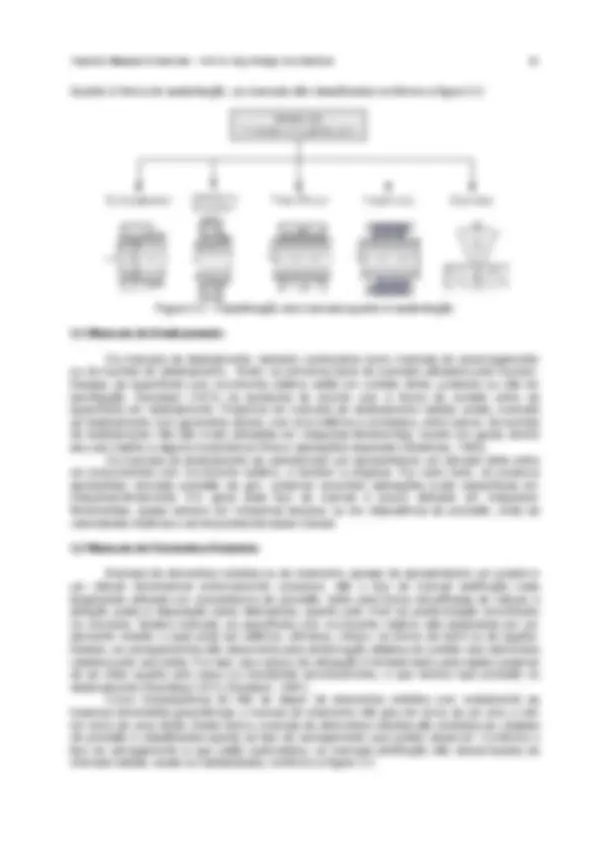
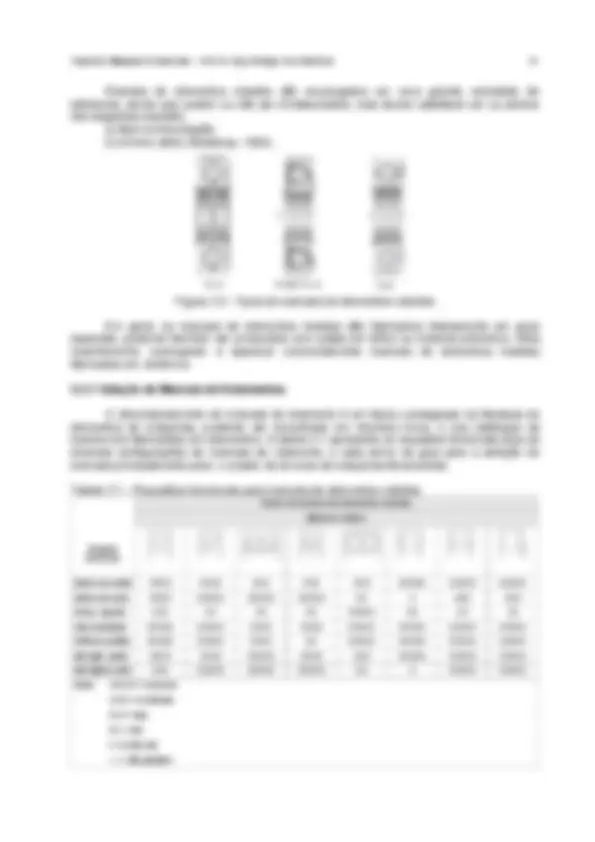
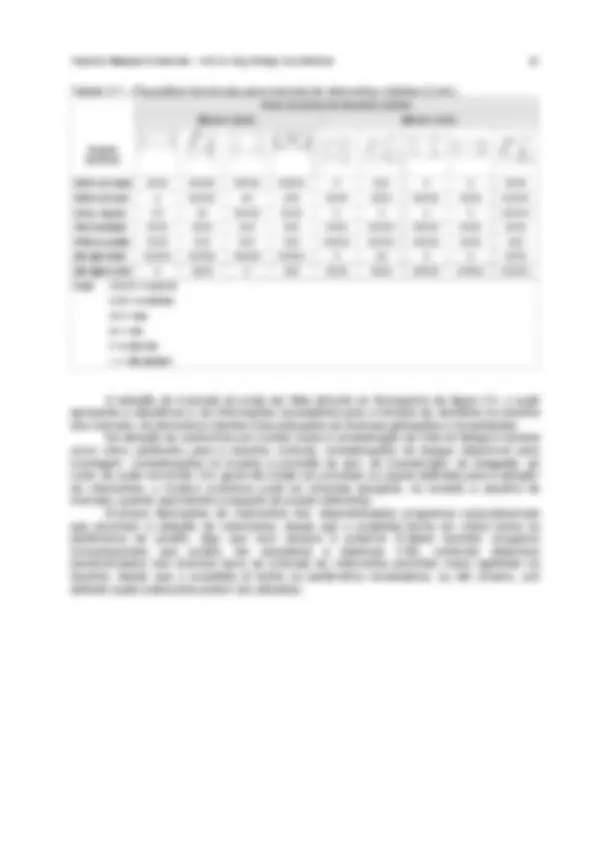
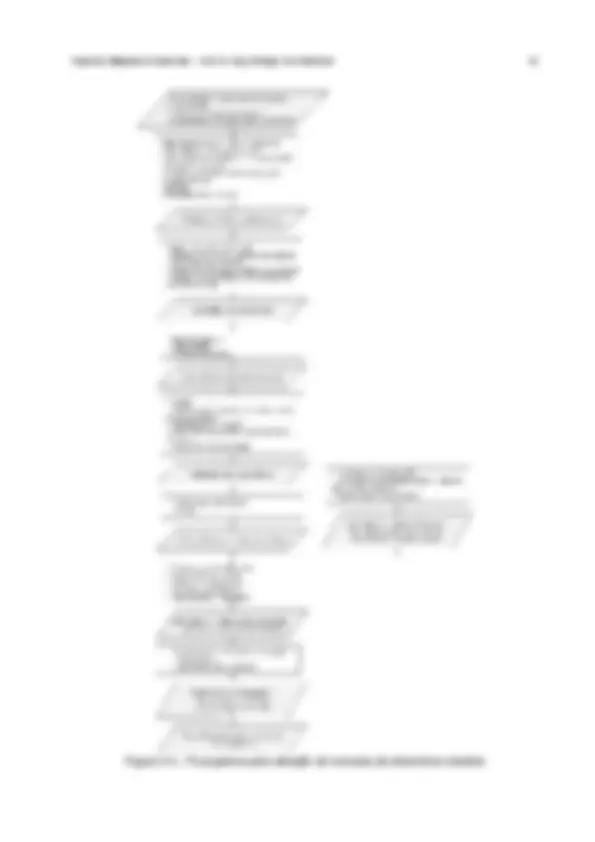
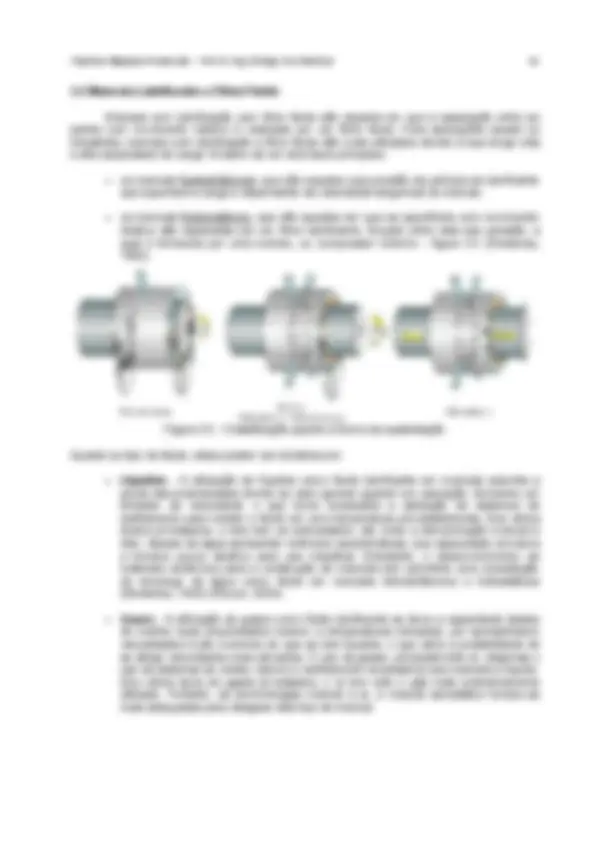
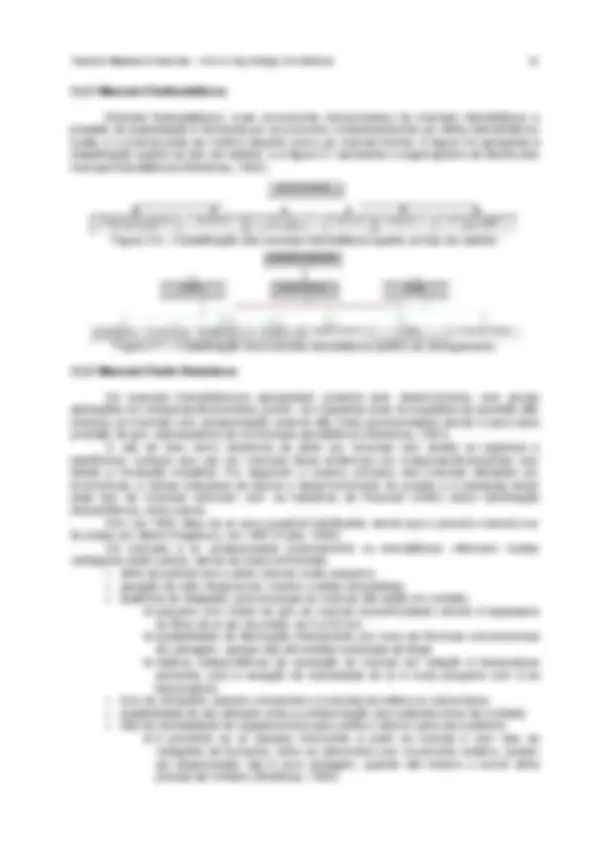
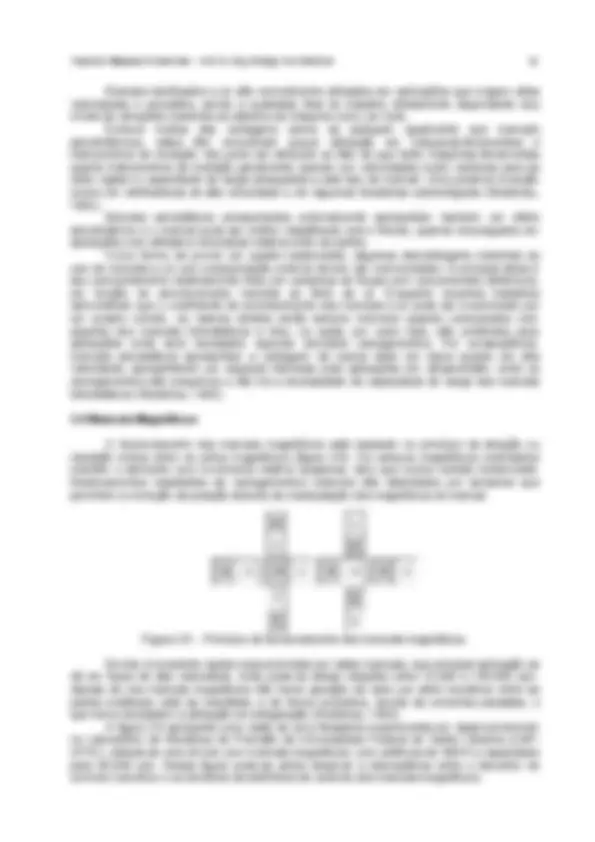
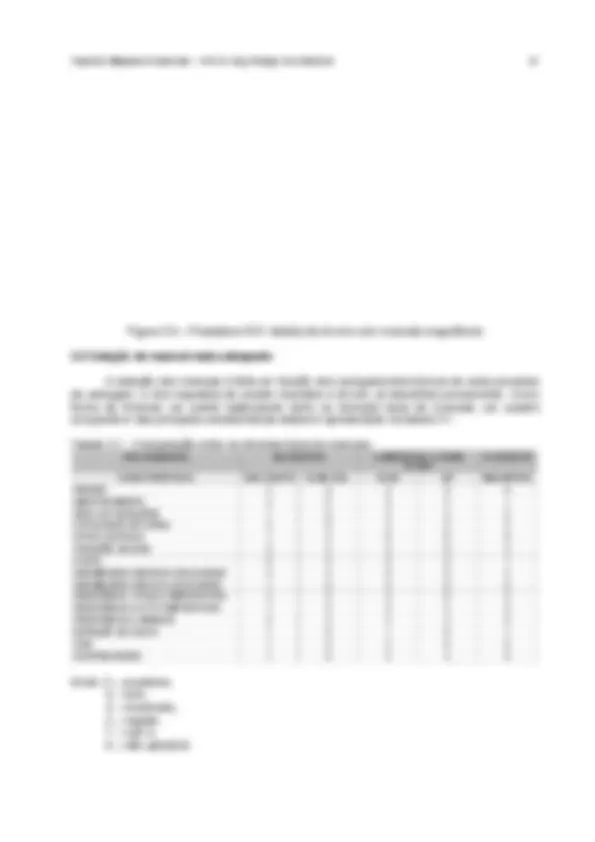
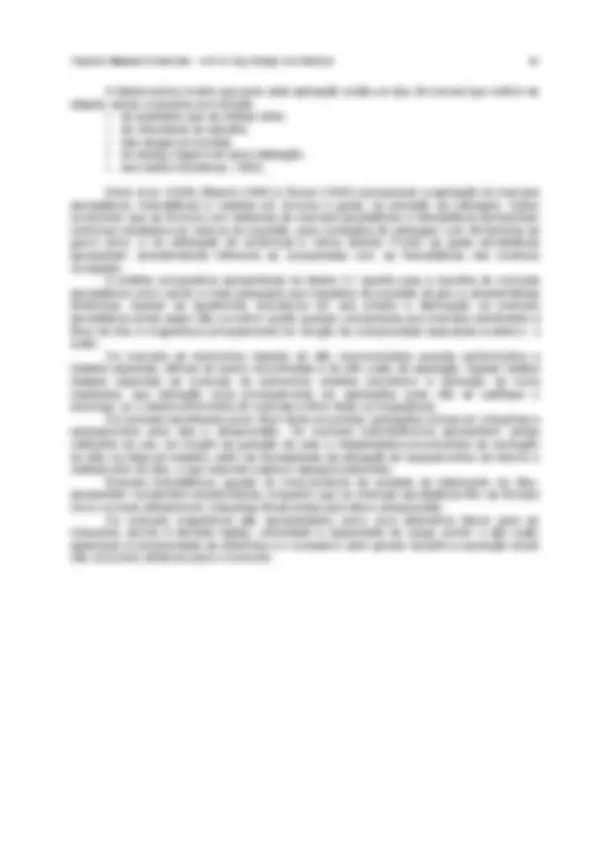
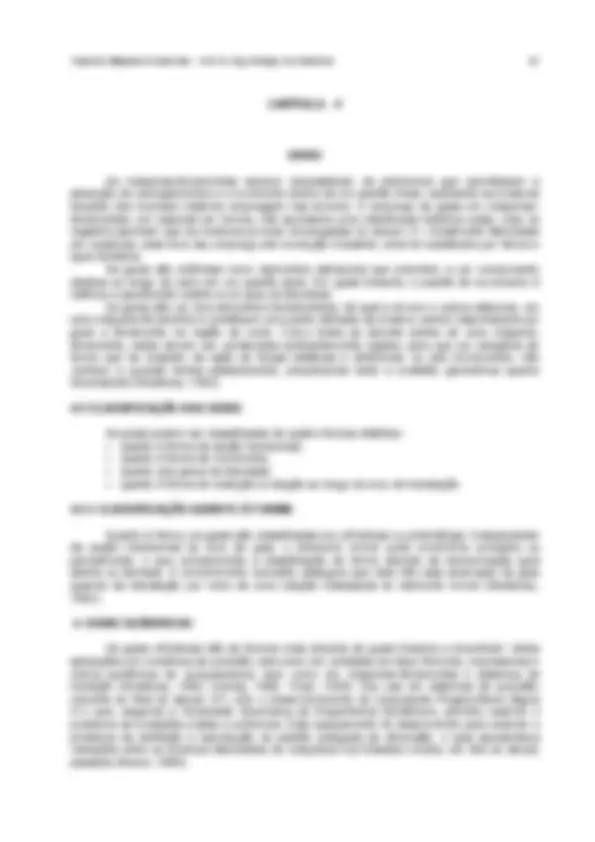
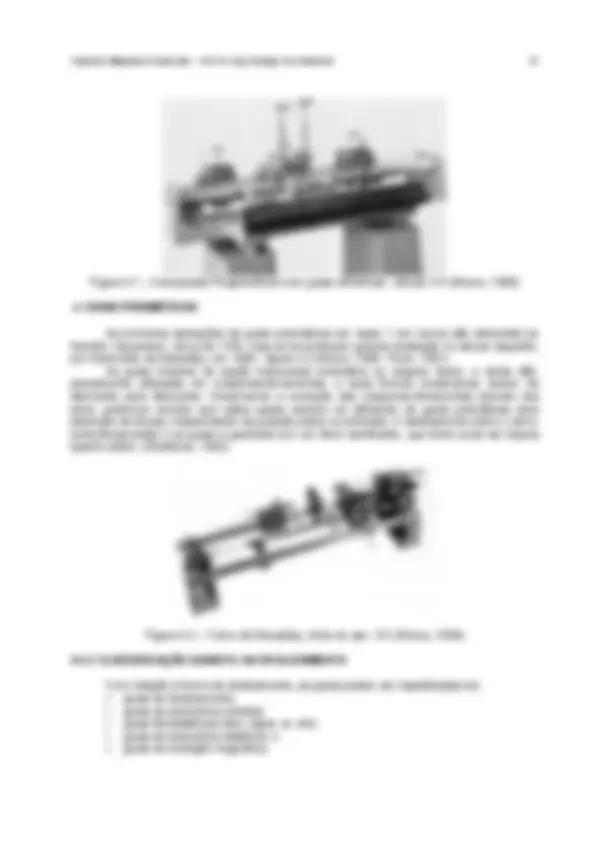
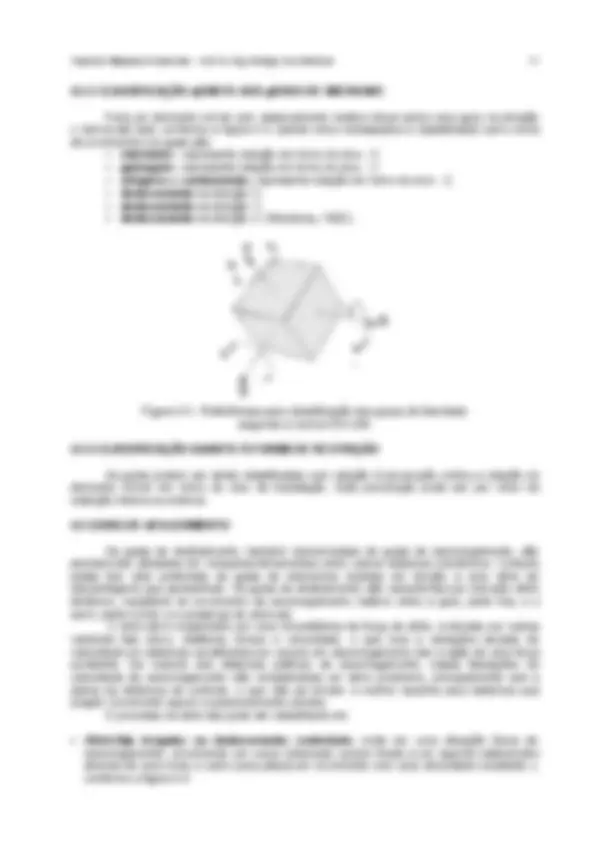
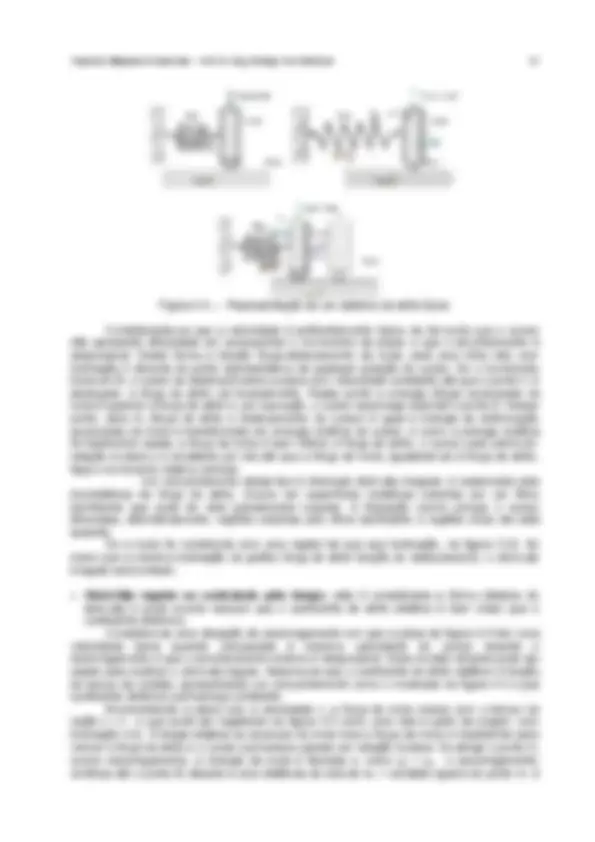
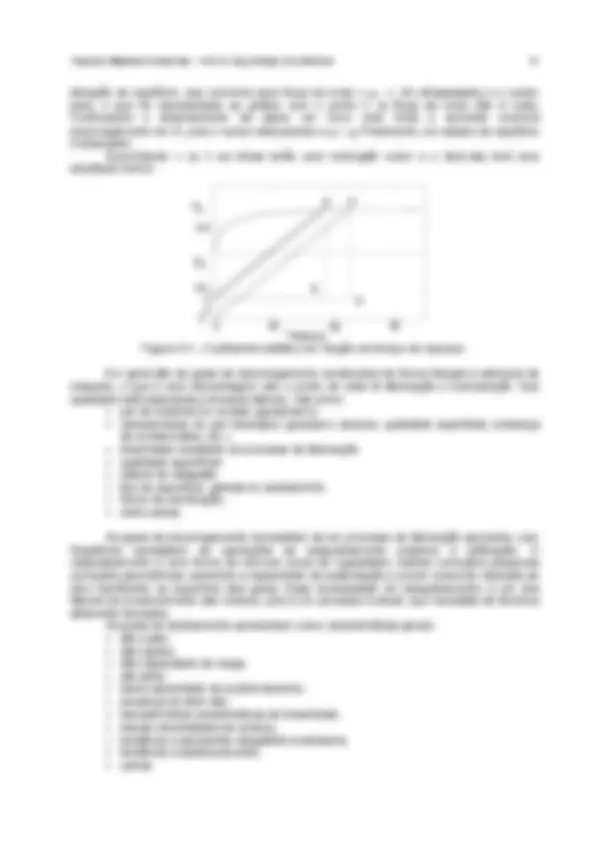
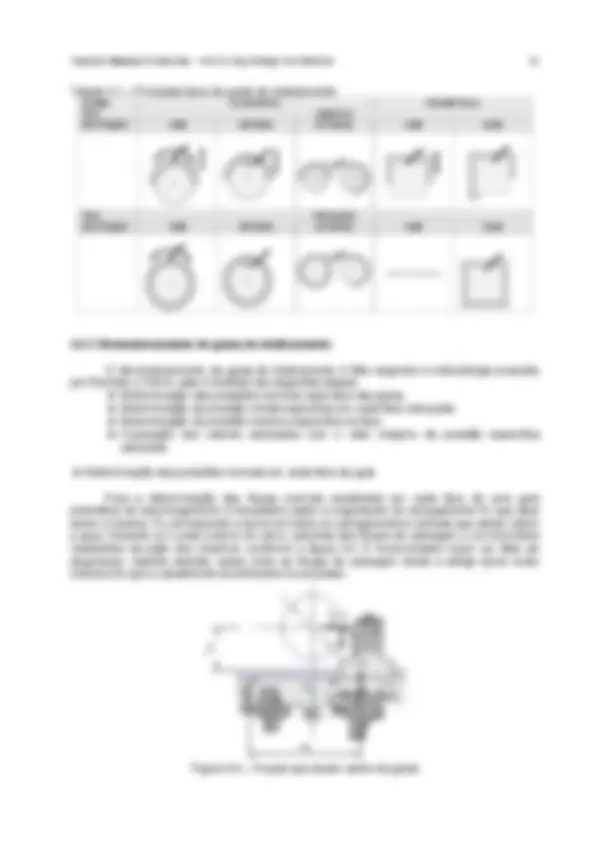
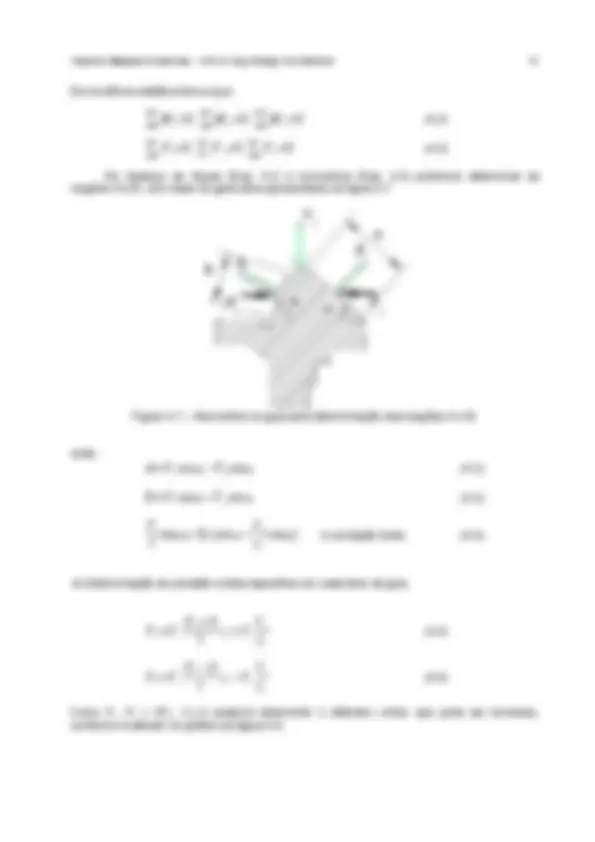
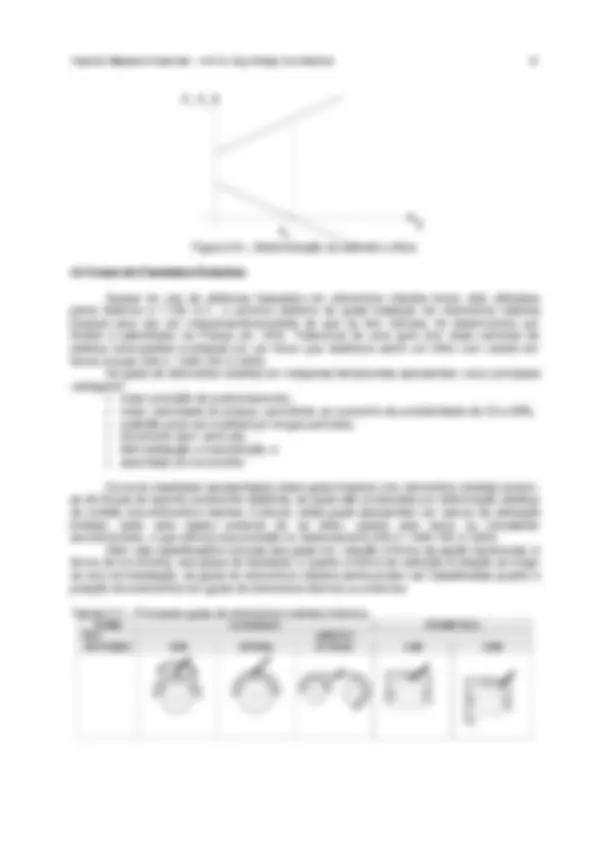
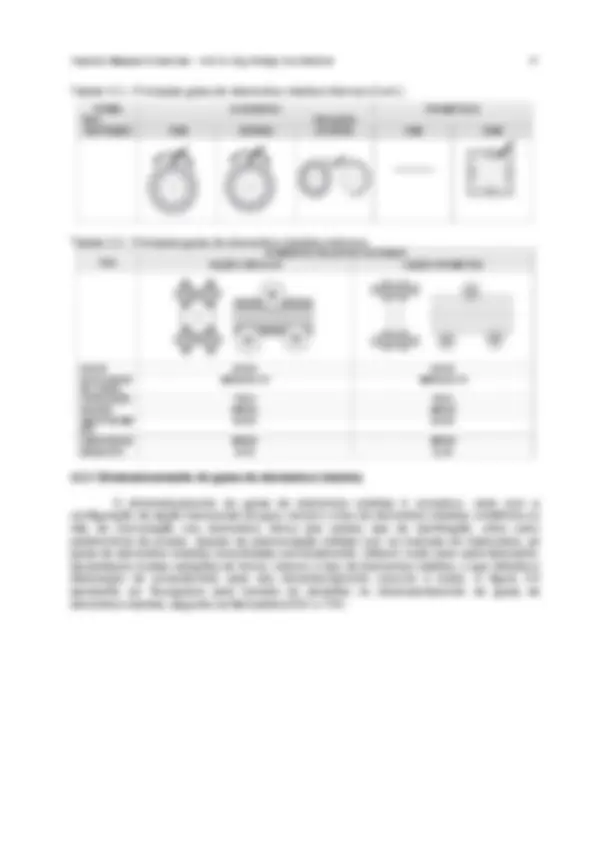
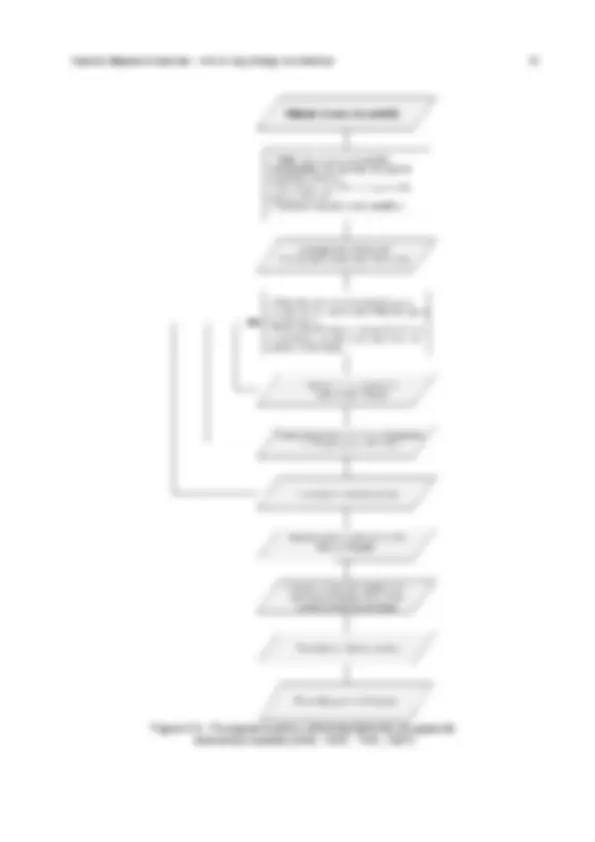
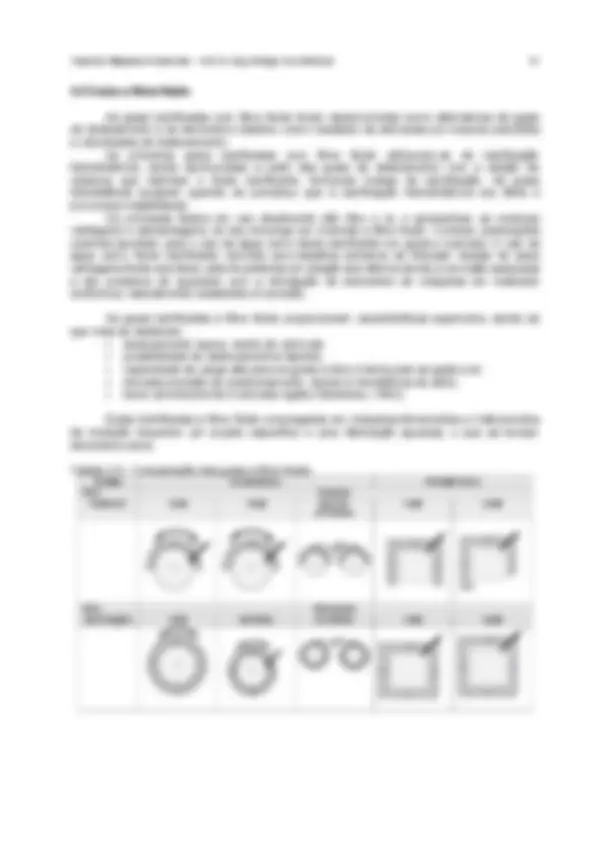
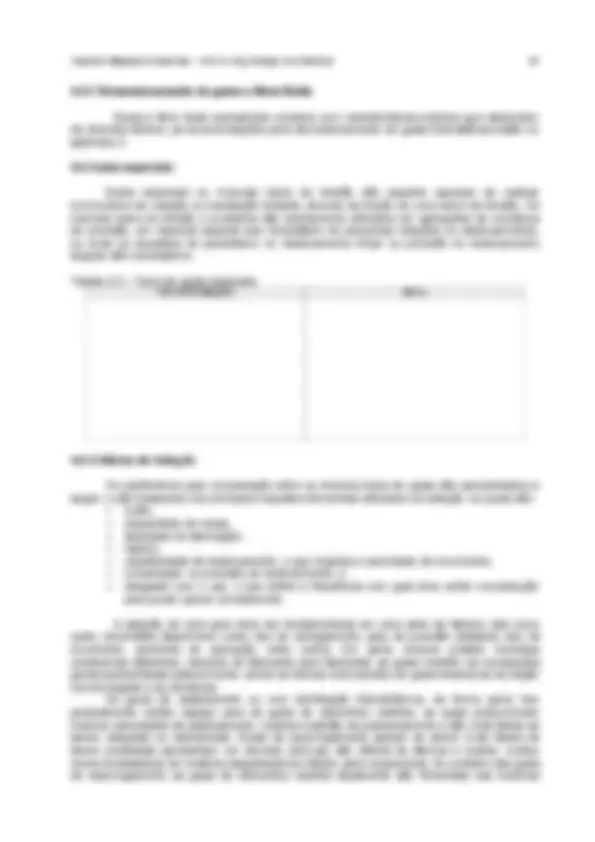
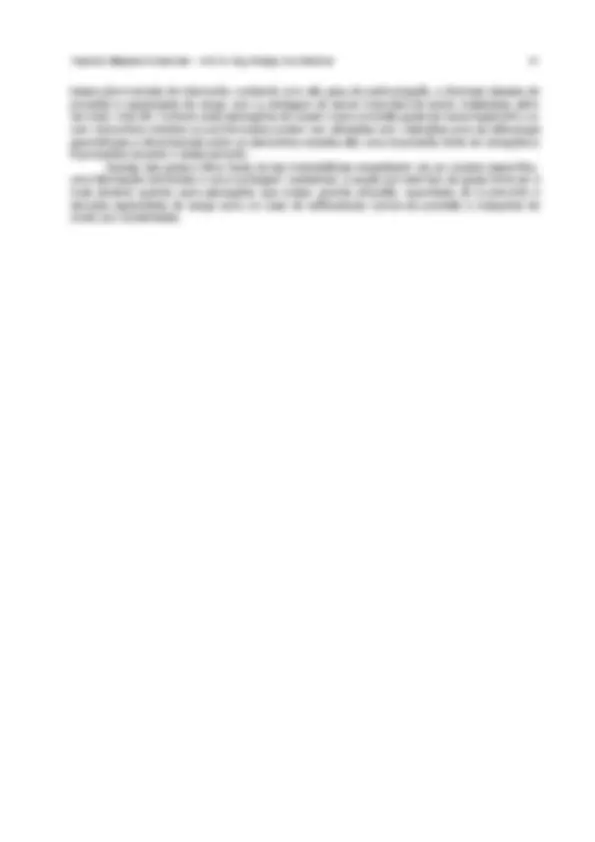
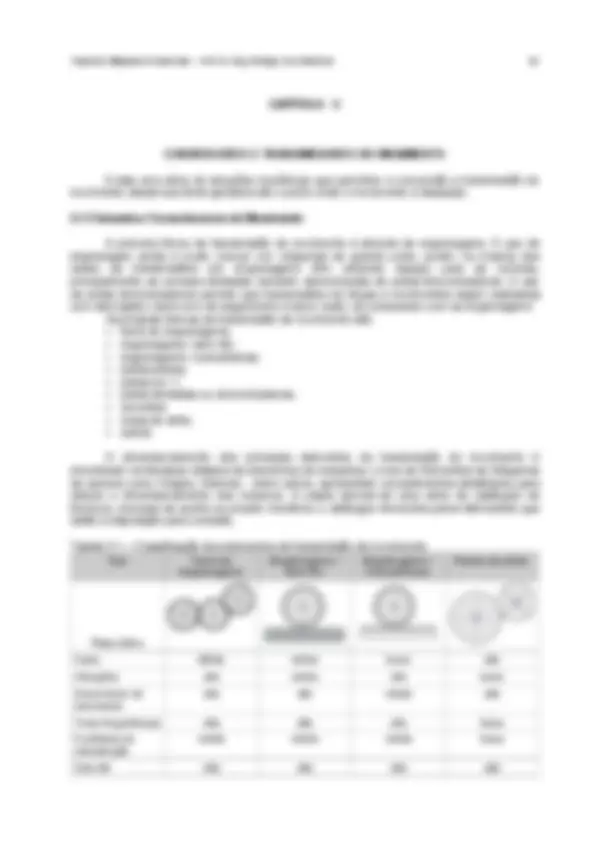
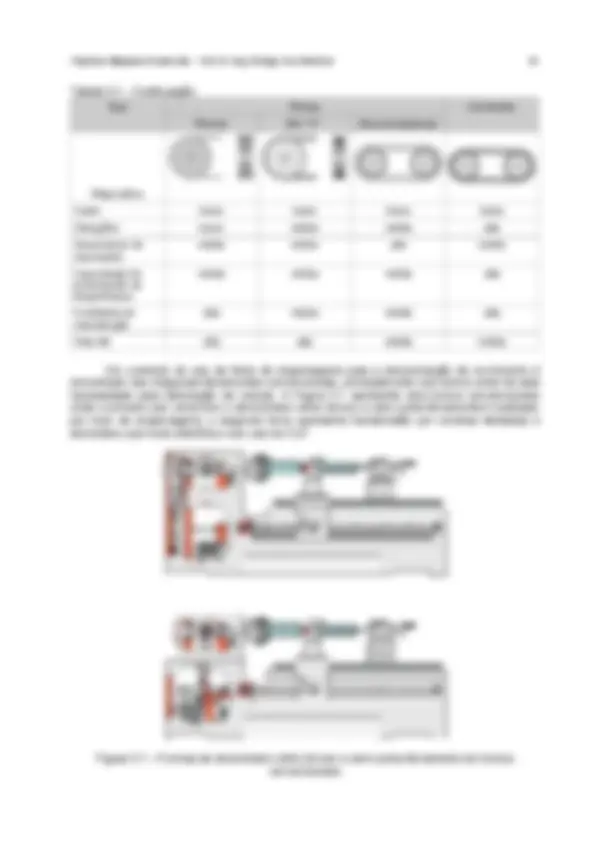
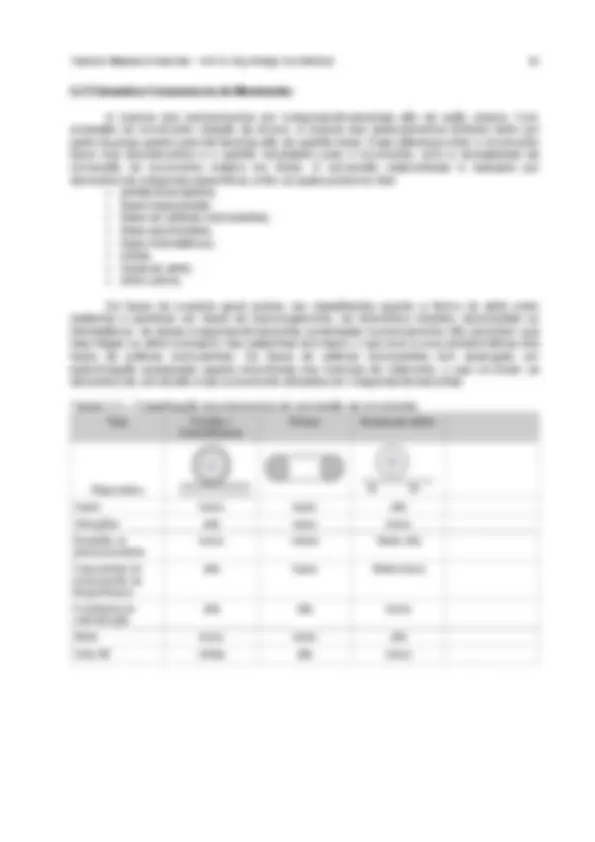
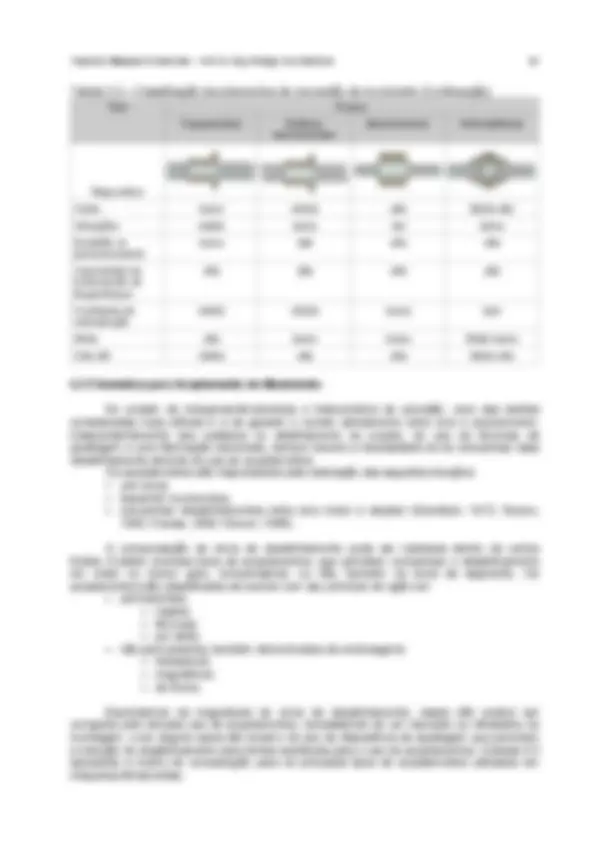
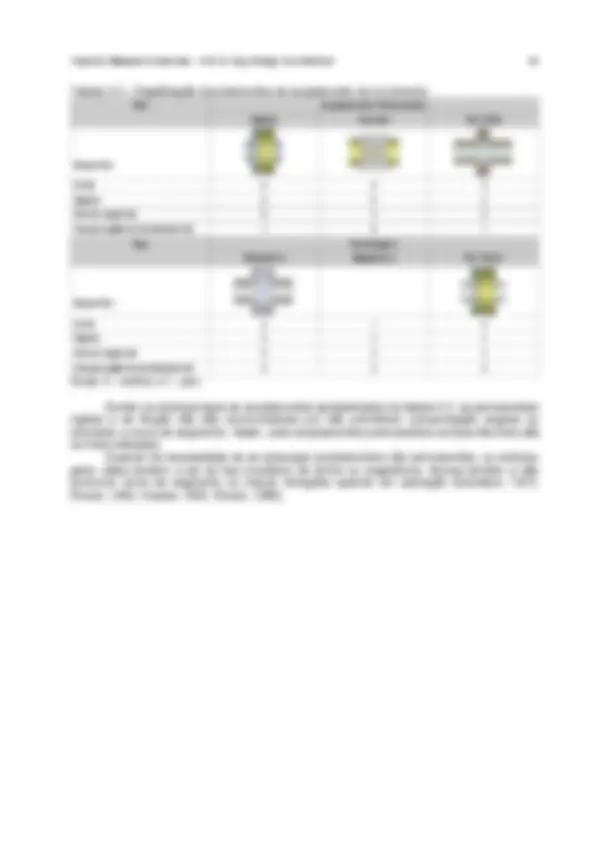
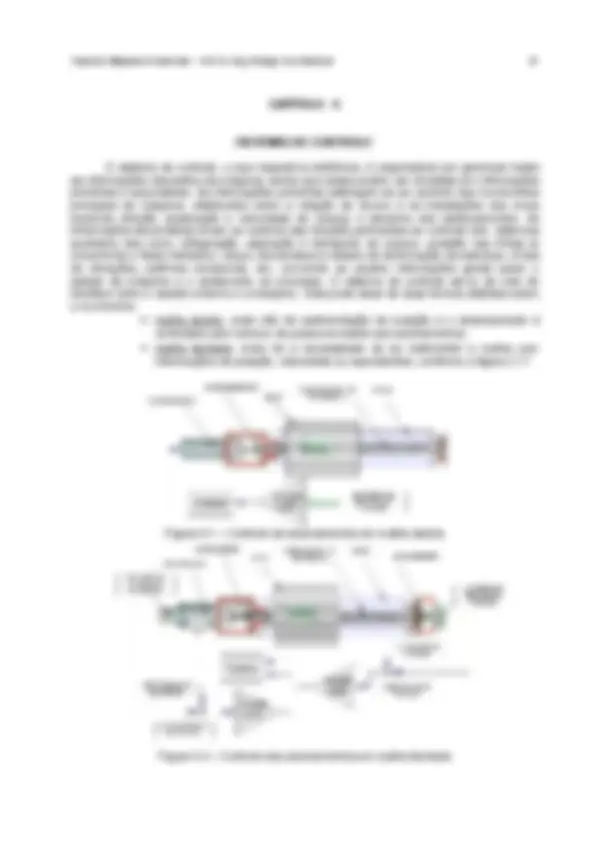
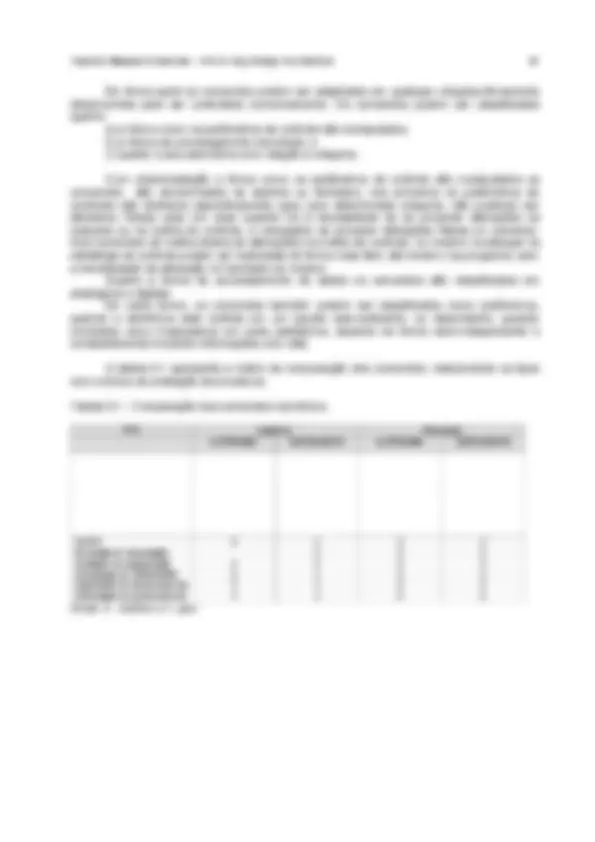
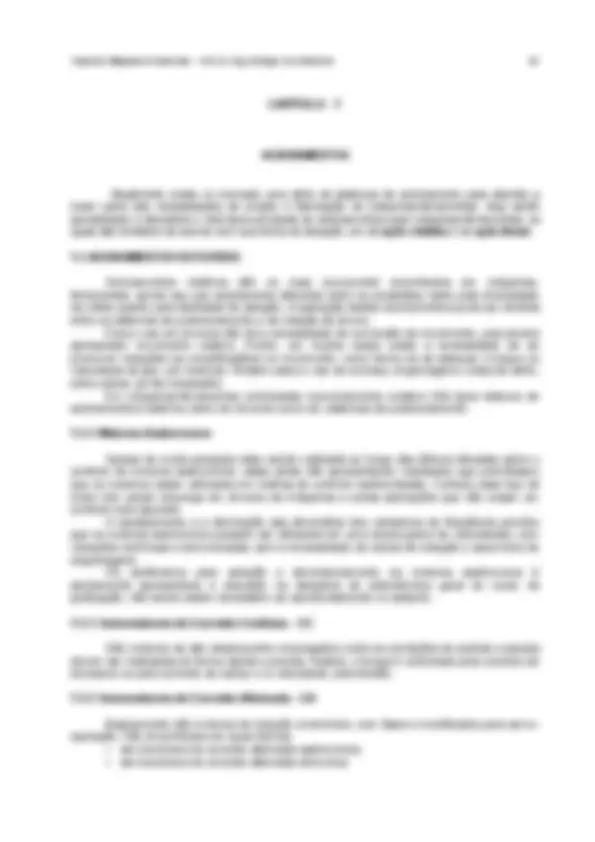
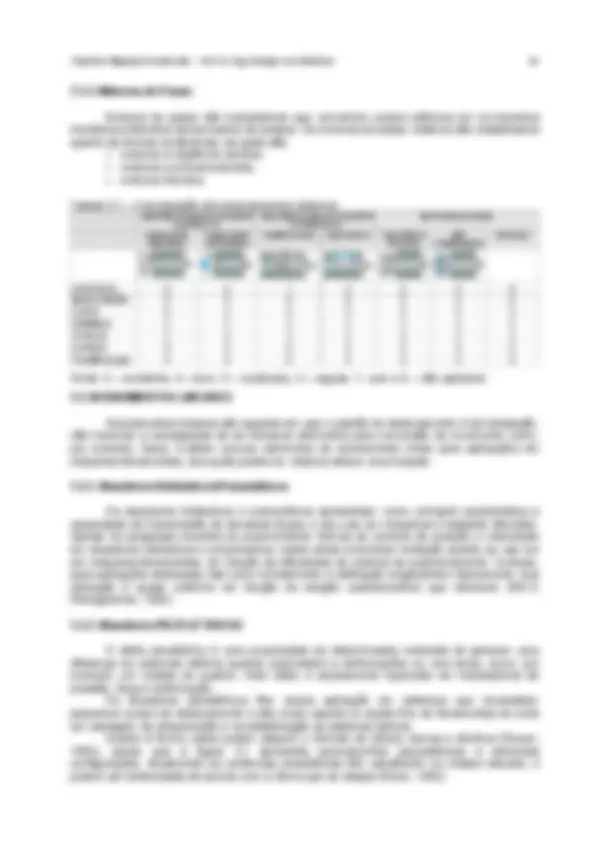
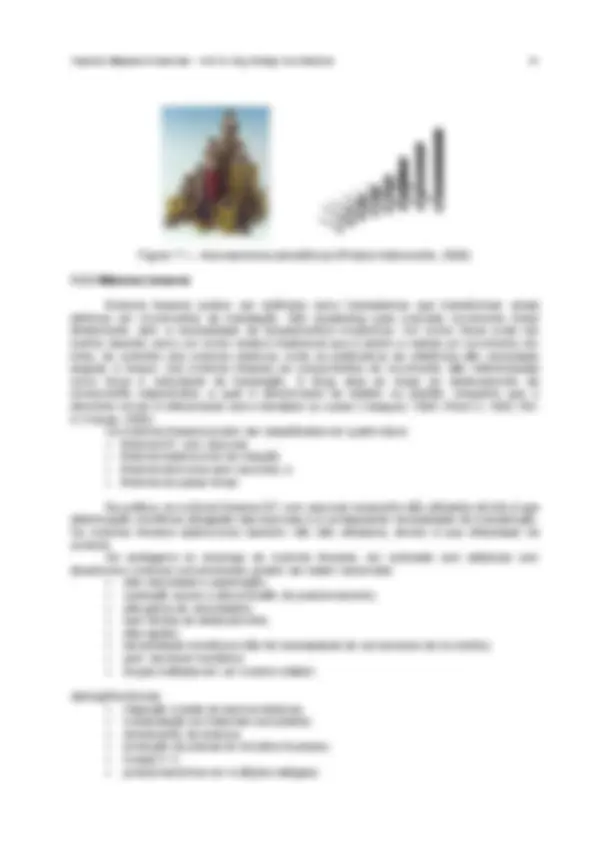
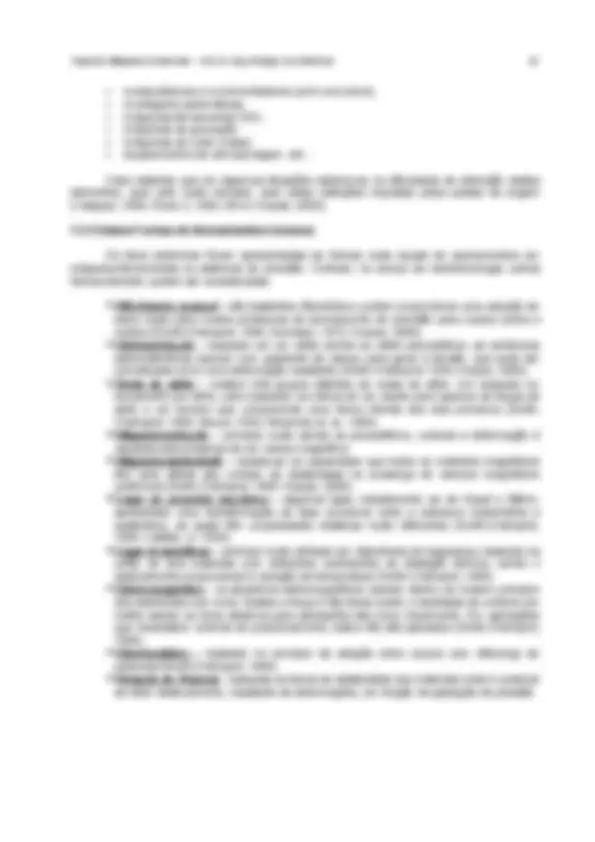
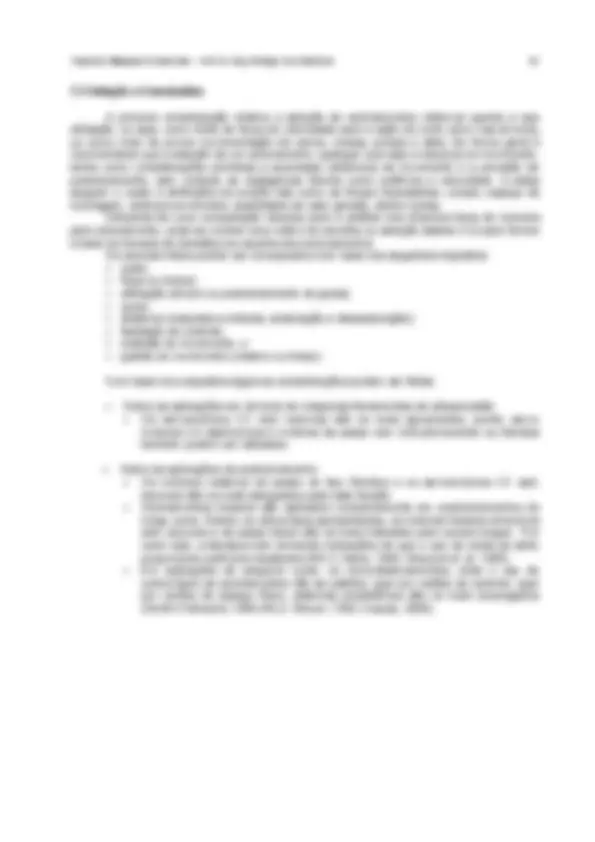
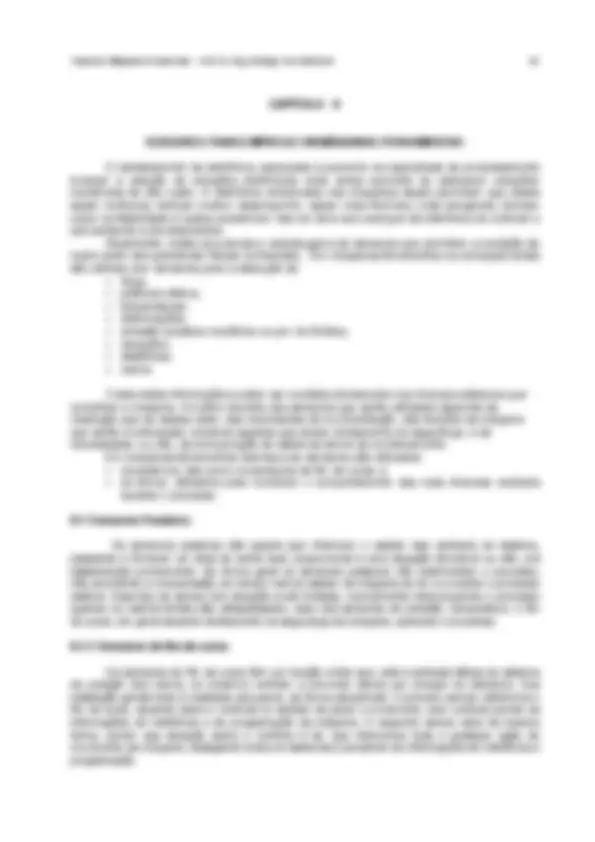
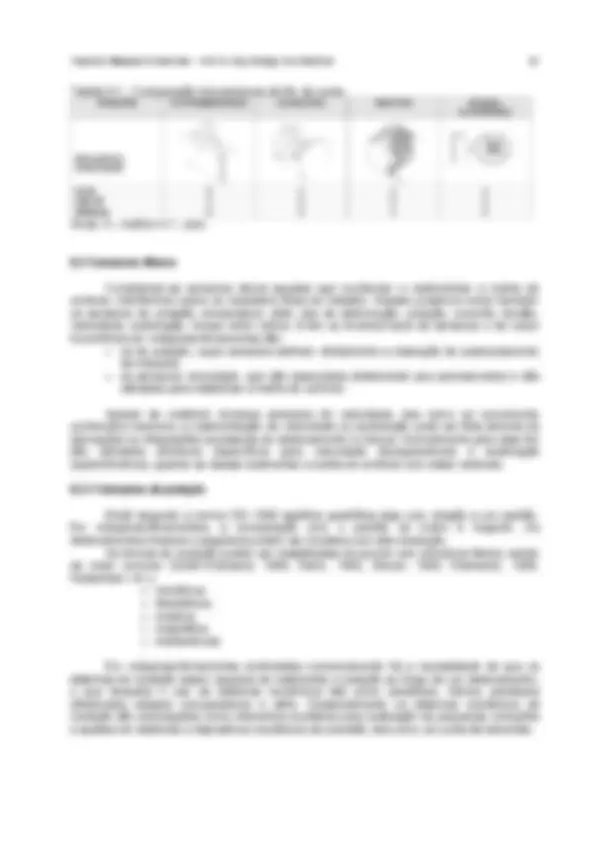
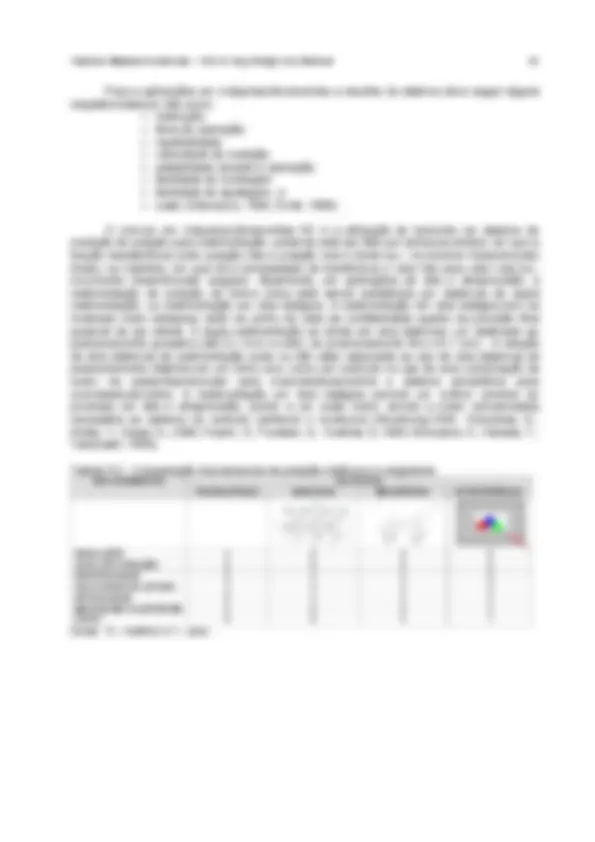
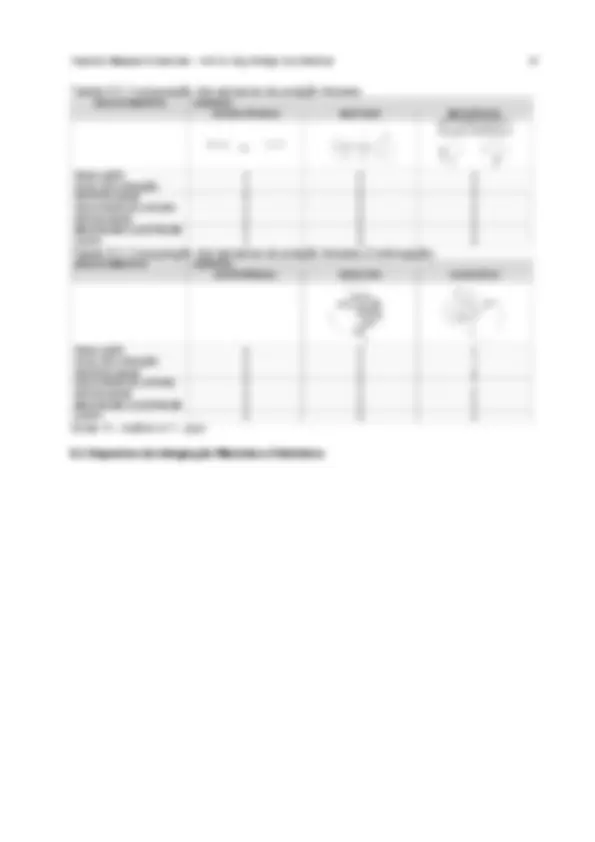
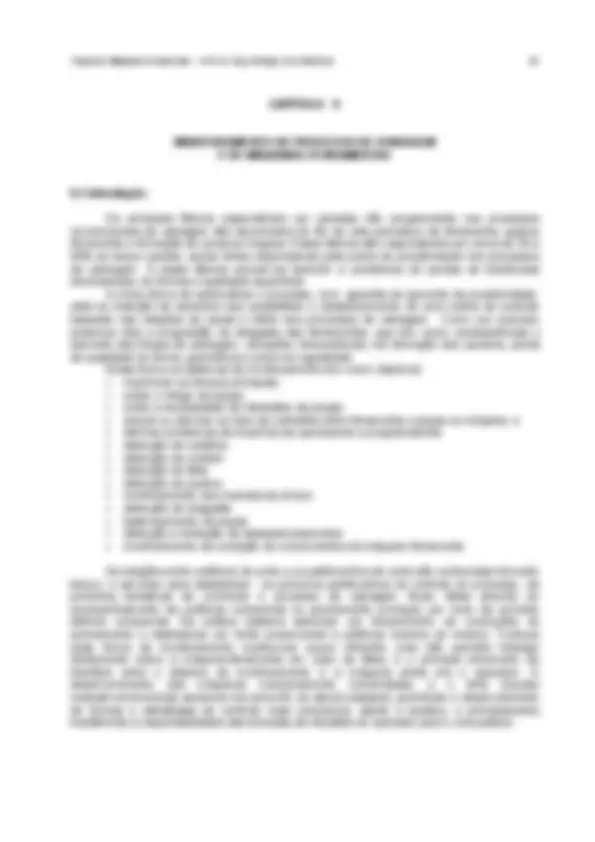
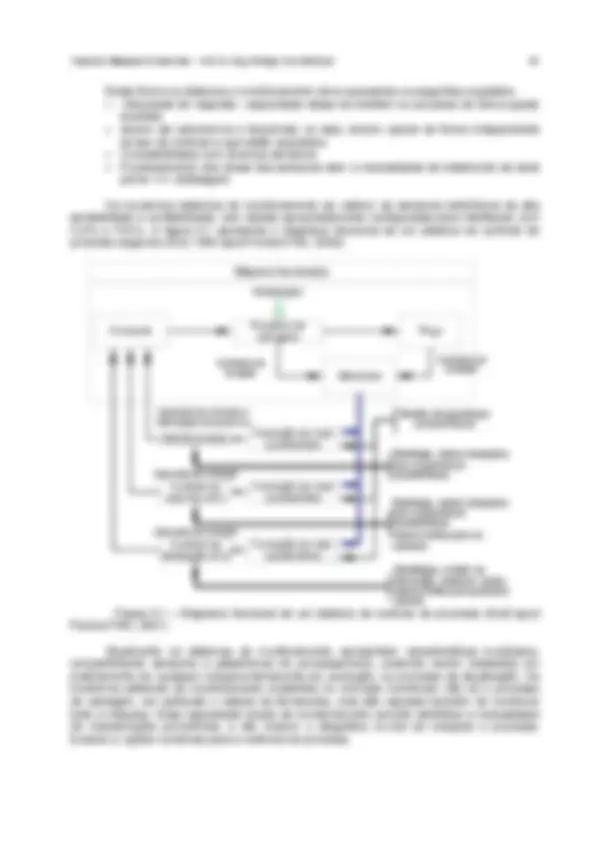
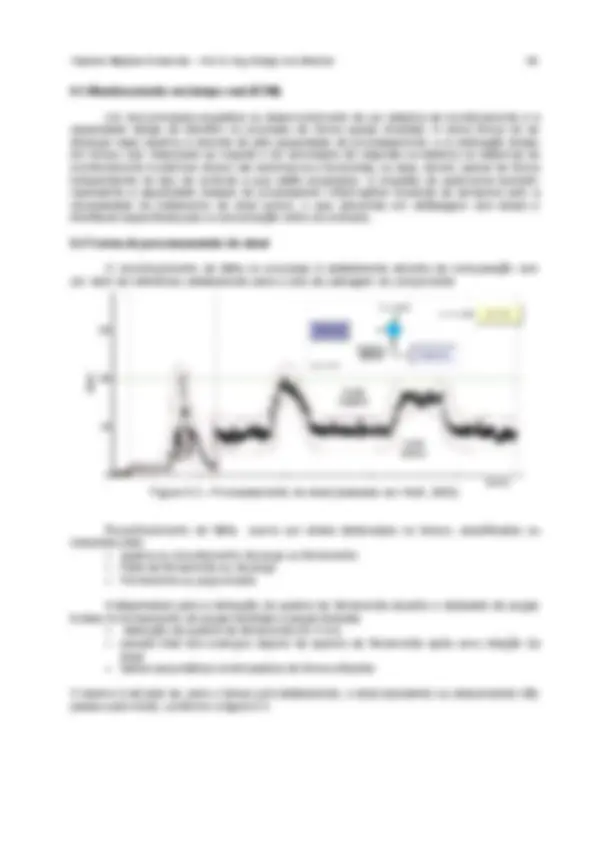
Estude fácil! Tem muito documento disponível na Docsity
Ganhe pontos ajudando outros esrudantes ou compre um plano Premium
Prepare-se para as provas
Estude fácil! Tem muito documento disponível na Docsity
Prepare-se para as provas com trabalhos de outros alunos como você, aqui na Docsity
Os melhores documentos à venda: Trabalhos de alunos formados
Prepare-se com as videoaulas e exercícios resolvidos criados a partir da grade da sua Universidade
Responda perguntas de provas passadas e avalie sua preparação.
Ganhe pontos para baixar
Ganhe pontos ajudando outros esrudantes ou compre um plano Premium
Comunidade
Peça ajuda à comunidade e tire suas dúvidas relacionadas ao estudo
Descubra as melhores universidades em seu país de acordo com os usuários da Docsity
Guias grátis
Baixe gratuitamente nossos guias de estudo, métodos para diminuir a ansiedade, dicas de TCC preparadas pelos professores da Docsity
Apostila de Introdução ao Projeto de Máquinas sobre Elementos de Máquinas
Tipologia: Manuais, Projetos, Pesquisas
1 / 114
Esta página não é visível na pré-visualização
Não perca as partes importantes!
Atenção: Este material está sendo elaborado para publicação sob forma de um livro junto a Editora da UFSC, não sendo permitida sua reprodução total ou parcial para a quais quer fins. O uso de seu conteúdo e das figuras contidas neste são permitidas somente com a autorização expressa do autor, ou com o uso das devidas referências.
Introdução I.1 Histórico I.2 Especificação geral do problema I.3 Importância econômica das máquinas-ferramentas I.4 Considerações sobre o processo de usinagem I.4.1 Ferramentas e máquinas I.4.2 Processo de torneamento I.4.3 Fresamento I.4.4 Furação I.4.5 Retificação I.4.6 Outros processos I.5 Relação entre os processos de Fabricação Tolerâncias e Acabamento I.6 Nocões gerais de Teoria de Projeto I.7 Tendências no projeto de máquinas-ferramentas 1 Estruturas de Máquinas-Ferramentas 1.1 Arranjos de máquinas-ferramentas 1.2 Considerações Gerais 1.2.1 Considerações estáticas 1.2.2 Considerações dinâmicas 1.2.3 Formas de análise da rigidez em máquinas-ferramentas 1.2 Materiais de máquinas-ferramentas 1.2.1 Ferro-fundido 1.2.2 Aços 1.2.3 Materiais cerâmicos 1.2.4 Concreto 1.2.5 Granito 1.2.6 Granitos sintéticos e concretos poliméricos 1.2.7 Outros Materiais 1.2.8 Fabricação de Estruturas de Máquinas-Ferramentas 1.2.9 Seleção de Materiais para Estrutura de Máquinas-Ferramentas 2 Árvores de máquinas-ferramentas 2.1 Especificações para Árvores de Máquina-Ferramentas 2.2 Classificação das Árvores de Máquinas-Ferramentas 2.3 Principais componentes para o projeto de árvores de máquinas-ferramentas 2.4 Rigidez 2.5 Configuiração dos Mancais de Elementos Rolantes 2.5.1 Determinação da distância ótima entre os rolamentos 2.6 Considerações sobr Árvores Dotadas de Mancais a Filme Fluido 2.7 Seleção do tipo de árvore 3 Mancais 3.1 Mancais de Deslizamento 3.2 Mancais de Elementos Rolantes 3.2.1 Seleção de Mancais de Rolamentos 3.3 Mancais Lubrificados a Filme Fluido 3.3.1 Mancais Fluidoestáticos 3.3.2 Mancais Fluido Dinâmicos 3.4 Mancais Magnéticos 3.5 Seleção do mancal mais adequado
Apêndice Simbologia a [o] ângulo de rotação, ou rolamento em torno do eixo X ap [mm] profundidade de corte b [o] ângulo de rotação, ou guinagem em torno do eixo Y B [mm] largura de corte d [mm] diâmetro cr [m] folga radial c [o] ângulo de rotação, ou arfagem em torno do eixo Z Dr [mm] diâmetro do restritor de fluxo D [mm] diâmetro Dm [mm] diâmetro medido Dk [mm] diâmetro médio do cristal DT [mm] diâmetro da ferramenta DW [mm] diâmetro da peça e [mm] excentricidade E [N/mm^2 ] módulo de elasticidade F [N] força ou carregamento estático Fm [N] força de atração do motor linear Fc [N] força de impulso do motor linear F(t) [N] força ou carregamento dinâmico ed [mm] erro diametral er [mm] erro radial Fc [N] forca de corte Ff [N] força de avanço Fp [N] força passiva Mw [N.m] momento gerado pela força força peso Mfc [N.m] momento gerado pela força força de corte Mfp [Nm] momento gerado pela força força passiva f [mm/min.] avanço fa [mm/min.] avanço para acabamento fd [mm/min.] avanço para desbaste ft [mm/min.] avanço total f [Hz] freqüência hAB [nm] altura K [N/m] rigidez L [mm] comprimento do mancal n [rpm] rotação da árvore r [mm] raio Ra [nm] rugosidade média rd [mm] raio ideal da ferramenta r [mm] raio de quina RF [1/mm] freqüência espacial rm [mm] raio medido Rrms [mm] rugosidade raiz média quadrática Rt,c [nm] rugosidade cinemática Rt.t [nm] rugosidade cinemática teórica rT [nm] raio da ferramenta rW [nm] raio da peça P-V [nm] rugosidade pico-vale Qr [l/s] consumo relativo de ar T [oC] temperatura
U [m] deslocamentos t [s] tempo vc [m/min.] velocidade de corte vf [m/min.] velcidade de avanço Wr [N] capacidade de carga relativa wv [m] comprimento de onda X [mm] direção coordenada Y [mm] direção coordenada Z [mm] direção coordenada [o^ ] ângulo de folga 1 [o^ ] ângulo de folga 2 [o^ ] ângulo de folga extra [o^ ] ângulo [nm] raio da aresta de corte x [m] erro de movimento radial em X y [m] erro de movimento radial em Y z [m] erro de movimento radial em Z [%] excentricidade relativa (c/e) x [m] batimento em torno de X y [m] batimento em torno de Y x [m] erro de posicionamento [o^ ] ângulo de posição da ferramenta [o^ ] ângulo T [o^ ] ângulo de ferramenta W [o^ ] ângulo da peça [o^ ] ângulo de saída [m] comprimento de onda [----] coeficiente de atrito [----] amortecimento [kg/m^3 ] densidade
I.1 Histórico As origens das máquinas-ferramentas podem ser remontadas ao período paleolítico superior, cerca de 6.000 A.C., onde nossos ancestrais desenvolveram plainas primitivas, utilizando pedaços de madeira para prover uma estrutura e pedra lascada como ferramenta, tais como a apresentada na figura I.1. Figura I.1 – Plaina neolítica (Spur,1979) Afrescos egípcios datando de 1500 A.C. mostram o trabalho com furadeiras com ferramentas rotativas acionadas a arco, elemento o qual permaneceu como principal acionamento de máquinas-ferramentas o século XVI. Figura I.2 – Furadeira de arco egípcia 1500 a.C. (Spur, 1979) A renascença (século XVI) trouxe novamente o comercio a Europa, e junto a com esse a necessidade de se produzir mais, com melhor qualidade, com menor custo e no menor tempo possível, necessidades essas que levaram a substituição dos arco pelas rodas d’água como fonte motriz nas máquinas ferramentas. Neste período as máquinas-ferramentas ainda utilizavam estruturas em madeira e suas precisões e produtividade ainda se rivalizam com a produção de hábeis artesões.
Figura I.3 – Torno acionado por arco de 1565 (Spur, 1979) Esse período é marcado basicamente pelo torneamento ornamental, sendo o francês Jacques Benson em 1569, que é considerado um de seus grandes expoentes. O período renascentista (fins do sec. XIV e início do sec. XV) ainda apresenta a figura impar de Leonardo Da Vinci, em cujos os esboços existem máquinas-ferramentas de características revolucionárias, idéias as quais influenciaram muitos projetistas na Revolução Industrial. Figura I.4 – Ensaio de Da Vinci para uma furadeira com placa centrante (Spur, 1979) Já em fins do século XVI com a introdução e disseminação da pólvora no continente Europeu, houve um desenvolvimento das técnicas de furação, associado aos avanços nas técnicas de fundição, principalmente no tocante a fabricação de armas. Uma das primeiras obras conhecidas sobre torneamento é publicada pelo francês Charles Plumier no século XVIII, no mesmo período surgem as primeiras máquinas projetadas de acordo com princípios modernos (Moore, 1975). O holandes Verbruggen, em 1755, aprimora a técnica de furação de canhões, a qual ficou inalterada por cerca de quatro séculos. Originalmente, a técnica de furação de canhões era baseada na guiagem da ferramenta pelo furo proveniente da fundição, o que resultava em furos desalinhados e imprecisos, a técnica desenvolvida por Verbruggen consistia em guiar a broca em ambos os extremos.
Estas máximas tornaram-se a essência para o projeto de uma máquina-ferramenta de qualidade. Porém, apesar das inúmeras teorias de projeto existentes, a tendência ao longo da formação de um projetista é que este desenvolva sua própria metodologia, sistematizando procedimentos e sintetizando o melhor de diversas técnicas de projeto (Davidson, 1972; Slocun, 1992; Weck, 1992; Paul-Beitz, 1996). Figura I.7 – Torno multifuso de fins do século XIX Figura I.8 – Torno universal do início do século XX, com acionamento por correias A evolução da eletrônica na primeira metade do século XX, aliada ao desenvolvimento dos computadores, levou a criação da primeira máquina-ferramenta numericamente controlada. Em 1946 é desenvolvido o primeiro computador eletrônico digital, o ENIAC, em 1947 é inventado o primeiro transistor nos laboratórios da Bell, e em 1950 utilizando-se um computador eletrônico EDSAC, é desenvolvida a primeira máquina-ferramenta numericamente controlada (NC), nos laboratórios do Massaschussets Institut of Techonology - MIT. Atualmente o projeto de máquinas-ferramentas para usinagem com ferramentas de geometria definida, aponta par três áreas de desenvolvimento distintas. A primeira voltada para obter a máxima flexibilidade de produção, sendo caracterizada pela máquinas do tipo hexapot, a segunda caracterizada pela máximação da taxa de remoção, a qual forma a base da usinagem em alta velocidade – HSM, e a terceira voltada para atender as necessidades de obtenção de alta exatidão dimensional, geométrica e elevada qualidade superficial, ou seja, para a ultraprecisão, figura I.9.
Figura I.9 – Tendências do projeto de máquinas-ferramentas Para muitos considerada como o estado-da-arte em termos de usinagem, a tecnologia de usinagem em altíssima velocidade (HSC - High Speed Cutting) está completando 70 anos. O método desenvolvido por C. Salomon foi patenteado em 27 de abril de 1931, na Alemanha, sendo a patente concedida à companhia Krupp A.G. Apesar das primeiras pesquisas sobre usinagem de alta velocidade de corte (HSC) datarem da década de trinta do século XX, essa estava baseada basicamente no conceito de alta velocidade de corte relativa entre peça e ferramenta, poderia ser somente obtida com o elevado giro da árvore máquina. A possibilidade de se obterem velocidaes de avanços elevadas transformou o conceito de usinagem em velocidade de corte – HSC – em usinagem em alta velocidade – HSM, onde as possibilidades em termos de aumento da taxas de remoção forma muito ampliados. A tecnologia de usinagem em alta velocidade só começou a despertar interesse do universo da fabricação metal mecância, especificamente da usinagem, ao longo da última década, do século passado. Essa tecnologia sofreu um grande impulso em função dos avanços nos acionamentos, nas guias de elementos rolantes e na eletrônica de controle, em especial na capacidade de processar digitalmente e em alta velocidade o elevado volume de dados transferidos entre o sistema de medição e os aciomanentos. Atualmente sistemas de posicionamento linear de alta velocidade podem operar com avanços entre 10 e 300 m/min., sendo que a tecnologia para máquinas-ferrametnas está limitada em torno de 60 m/min. I.2 Especificação geral do problema Como forma de fazer sua parte no processo produtivo, uma máquina-ferramenta deve satisfazer os seguintes requisitos: (1) – independente da habilidade do operador, as peças a serem produzidas na máquina devem ser obtidas com tolerâncias de forma e dimensional dentro de limites permitíveis, juntamente com os requisitos de qualidade superficial. (2) – como forma de ser competitiva na operação, ela deve mostrar alto desempenho técnico com eficiência econômica. Quando considerenado o projeto de uma máquina-ferramenta seus elementos podemser dividios em três grupos, os quais são: a) – a estrutura; b) – acionamentos para a ferramenta, avanços e dispositivos de movimentação; c) – a operação e os dispositivos de controles.
Do ponto de vista da facilidade de manutenção é importante, também o uso de peças e unidades padronizadas, especialmente se certa unidade pode ser obtida externanente a rede do fabricante da máquina. Isto pode ser o caso de não somente rolamentos mas também motores elétricos, dispositivos de controles, sistemas hidráulicos, bombas lubrificantes, filtros, etc. Aqui a previsão para desenhos padronizados e dimesões para localização de sistemas de travamento, flanges, freios, etc, aumentam a eficiência técnica e a economia. Deve ser entendido que o desempenho de uma máquina-ferramenta não depende somente do projeto e fabricação da máquina em sí, mas também do tipo de peça, dos procedimentos (estratégia) de usinagem, dos parâmetros de usinagem, forma e tipo das ferramentas, da rigidez dos dispositivos de fixação para peça e ferramenta. Também é possível variações nas condições de trabalho durante a operação, o que pode ser causado pelo próprio processo de usinagem, como pelo desgate da ferramenta, mudanças de tempertura, variações de microestrutra e dureza da peça, perturbações do meio, etc (Koenigsberger -Tlusty, 1970). Tabela I.1 – Relações dos processos de usinagem (Koenigsberger, 1970; Stoeterau, 2002) TIPO DE OPERAÇÃO DE USINAGEM MOVIMENTO DE CORTE MOVIMENTO DE AVANÇO TIPO DE MÁQUINA-FERRAMENTA VOLUME DE TRABALHO TORNEAMENTO LONGITUDINAL PEÇA FERRAMENTA TORNO D = MÁX. COMPRIMENTO BALANÇO D' = MAX. DIÂMETRO L = MÁXIMA DISTÂNCIA ENTRE PONTAS L'= MÁXIMO COMPRIMENTO USINÁVEL TORNEAMENTEO VERTICAL PEÇA FERRAMENTA FURAÇÃO FERRAMENTA FERRAMENTA FURADEIRA L = MÁXIMA PROFUNDIDADE DE FURAÇÃO R= MÁXIMA POSIÇÃO RADIAL (X+H) = CUSO MÁXIMO DA COLUNA
TIPO DE OPERAÇÃO DE USINAGEM MOVIMENTO DE CORTE MOVIMENTO DE AVANÇO TIPO DE MÁQUINA-FERRAMENTA VOLUME DE TRABALHO MANDRILAMENTO FERRAMENTA FERRAMENTA ou PEÇA (C+D) = MÁXIMO DESLOCAMENTO (A+B) = ALTUMA MÁXIMA Dia. = DIÂMTRO INTERNO MÁXIMO DA ÁRVORE ÁREA DE MESA RETIFICAÇÃO FERRAMENTA PEÇA D' = MAX. DIÂMETRO L = MÁXIMA DISTÂNCIA ENTRE PONTAS L'= MÁXIMO COMPRIMENTO RETIFICÁVEL LAPIDAÇÃO FERRAMENTA PEÇA R = RAIO DO DISCO DE LAPIDAÇÃO R = RAIO MÁXIMO DA MESA FRESAMENTO FRONTAL FERRAMENTA PEÇA C = MÁXIMO DESLOCAMENTO B = ALTUMA MÁXIMA H. = DIÂMTRO INTERNO MÁXIMO DA ÁRVORE A = DESLOCAMENTO DA MESA ÁREA DA MESA
Figura I.10 - Relações que envolvem a qualidade de uma máquina-ferramenta (Weck , 1992) Porém, quando o objetivo é usinar componentes com qualidade, ou seja exatidão dimensional, geométrica e com qualidade superficial, a máquina-ferramenta passa a ser um dos meios para tal fim. Mesmo indiretamenta, como no caso de peças produzidas por processos de conformação ou injeção, a qualidade resultante é uma função dos processos de usinagem utilizados na obtenção dos moldes. As relações que envolvem a precisão e qualidade de um componente usinado são apresentadas na figura I.11. Nesta figura pode-se observar as diversas parcelas que contribuem para o resultado desejado e quais suas origens. A partir desta figura também pode- se concluir que não basta apenas se concentrar no ponto máquina-ferramenta, pois mesmo a melhor das máquinas pode apresentar resultados de usinagem não satisfatórios, quando se negligencia a fixação ou controle ambiental (König, 1999; Hembrug,1989; Stoeterau, 1999). Figura I.10 - Relações que envolvem a qualidade de uma peça usinada I.3 Importância Econômica das Máquinas-Ferramentas O mercado mundial de máquinas-ferramentas é responsável pela movimentação de boa parte da economia mundial. Apesar de sucetível as variações econômicas, o comércio mundial de máquinas-ferramentas é bastante competitivo, estando os consumidores atentos as inovações tecnológicas, e principalmente aos ganhos de produtividade que estas podem promover. A American Machinist (1996) apresenta a variação do volume de recursos no mercado internacional de máquinas-ferramentas - figura I.13. Com base nesta figura, pode-se observar que os paises ricos, que detem maior tecnologia, possuem maior competitividade no setor.
Figura I.11 – Movimentação do mercado internacional de máquinas-ferramentas I.4 Considerações sobre o Processo de Usinagem A definição de usinagem segundo a norma DIN 8580, aplica-se a todos os processos onde ocorre a remoção de material sob a formade cavaco. Sendo que a usinagem pode ser classificada de acordo com o processos conforme a figura I.12. Figura I.12 – Classificação dos processos de usinagem de acordo com os processos
parâmentro de seleção de máquina-ferramenta, quando relacionados com a potência necessaria no acionamento da árvore, ou são também relacionados com a vida da ferramenta no monitoramento do processo. Muitas vezes as informações provenientes dos esforços de usinagem são analisadas de forma diferente quando observadas sob o ponto de vista do engenheiro de projeto, onde esses são de suma importância pois devem ser absorvidos pela estrutura, mancais, do fuso e demais elementos constituintes da mesma. A figura I. apresenta uma visão da cinemática do processo de torneamento e os movimentos observados. Figura I.13 – Componentes do processo no torneamento A figura I.14 apresenta uma visão das componetes de força e velocidade no processo de torneamento Figura I.14 – Componentes de força e velocidade no processo de torneamento Apesar da definição clássica do torneamento apontar a peça como executando o movimento rotativo, e a ferramenta o movimento de avanço, a cinemática do processo de torneamento pode ser divida entre peça e ferramenta, o que em alguns casos leva a processos como o de mandrilamento. Considerando as variações do avanço da ferramentas possíveis temos como dar origem aos principais tipos de torneamento, conforme a figura I.15.
Figura I.15 – Tipos de Torneamento A formação da superfície no processo de torneamento de forma geral é uma conseqüência direta da geometria da ferramenta e da cinemática do processo, contudo uma série de fatores que vão desde as características do material da peça e ferramenta e parâmetros do processo, até a estabilidade dinâmica da máquina-ferramenta, passado pelo ambiente em que o processo é realizado, levam a discrepâncias entre a textura superficial calculada a aquela resultante do processo. A figura I.16 apresnta uma visão geral do processo de formação da superfície no torneamento, para superfícies com ângulo de ponta de até 20°. Figura I.16 – Formação da superfície no torneamento Em fução dos esforços gerados pelo processo é possível determinar a potência necessária para seleção e dimensionamento de acionamentos. Assim a potência necessária para usinar um material específico, pode ser calculada como: