
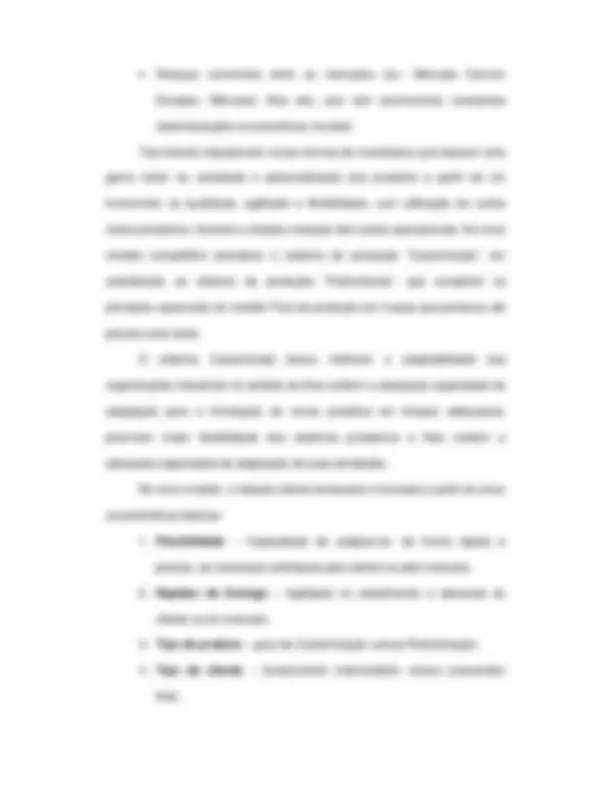
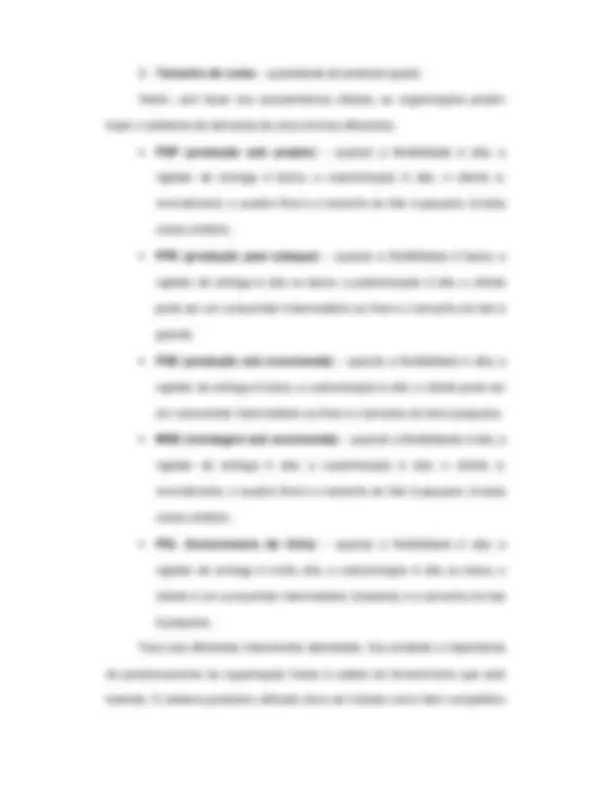
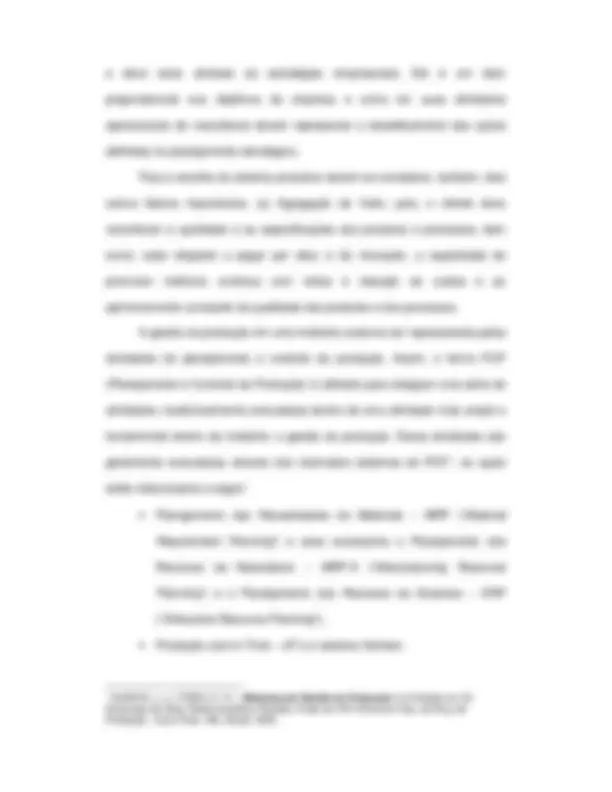
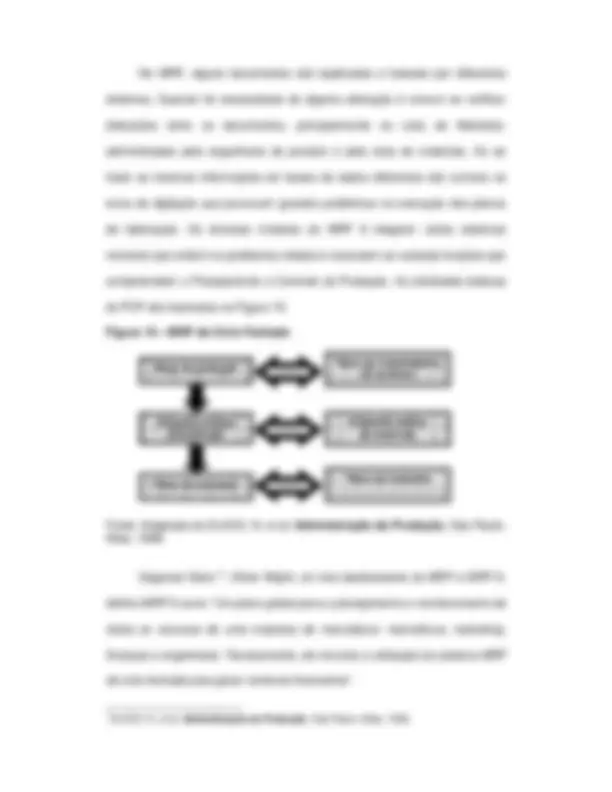
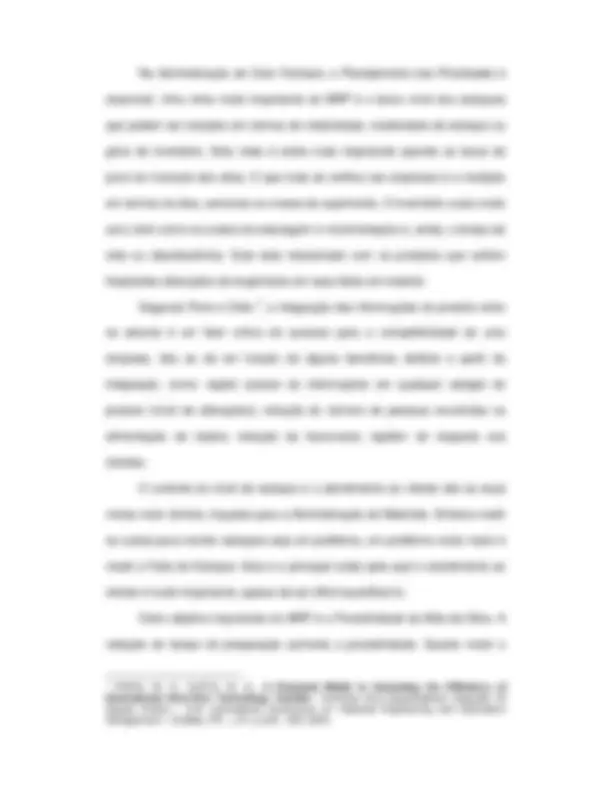
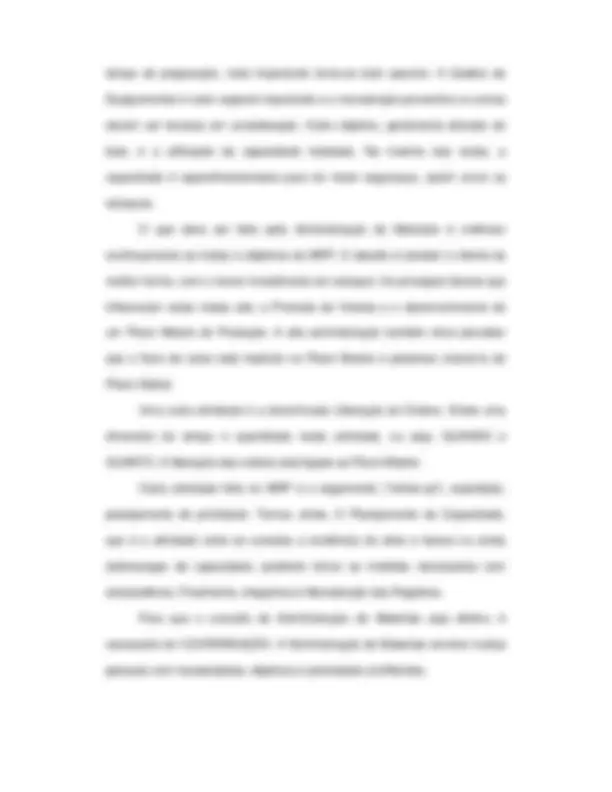
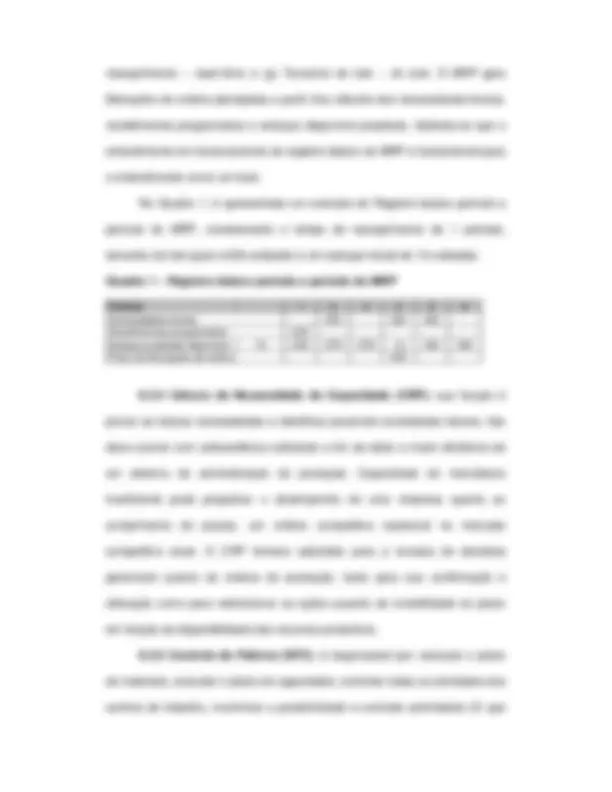
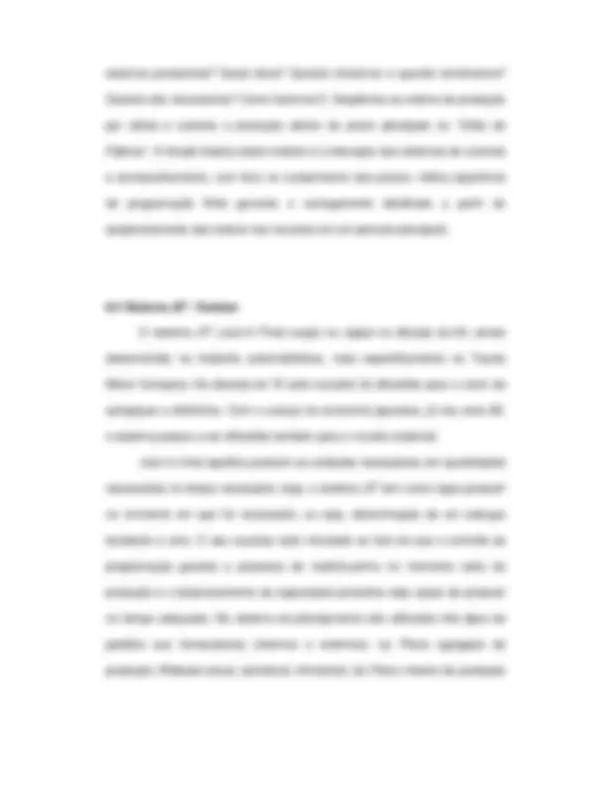
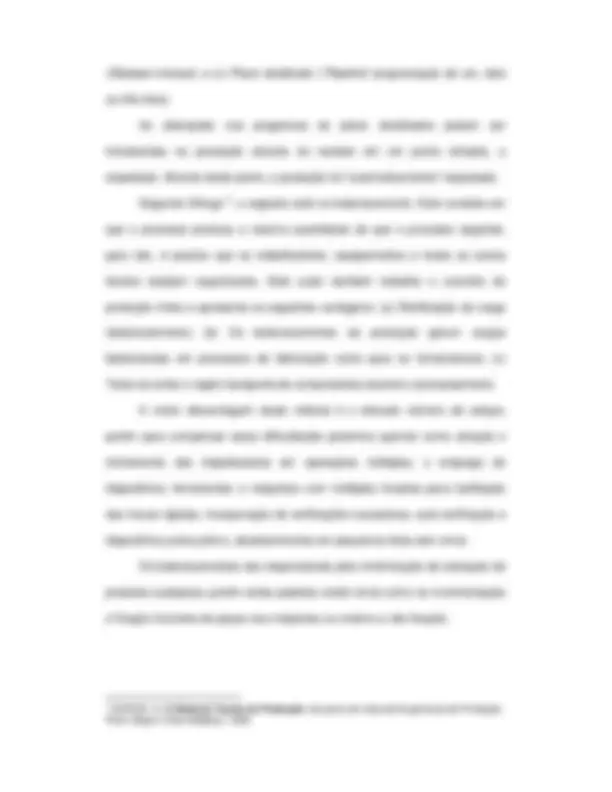
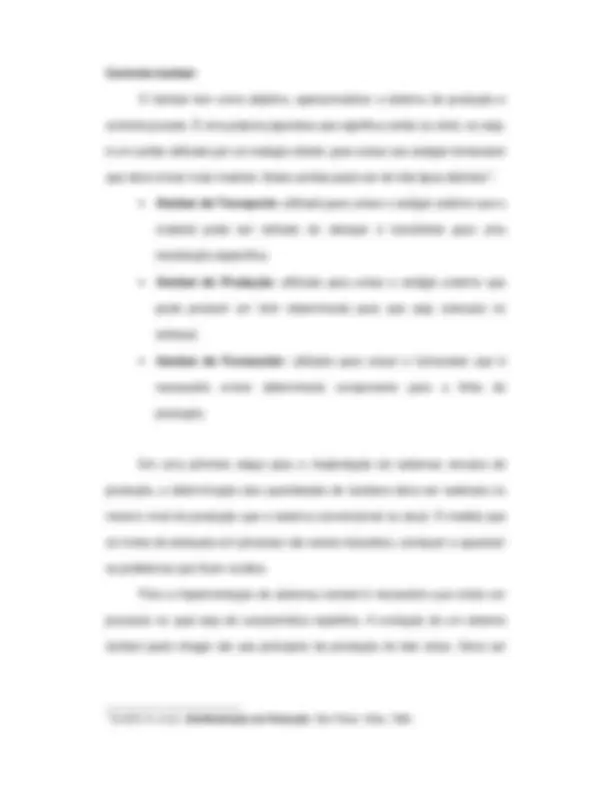
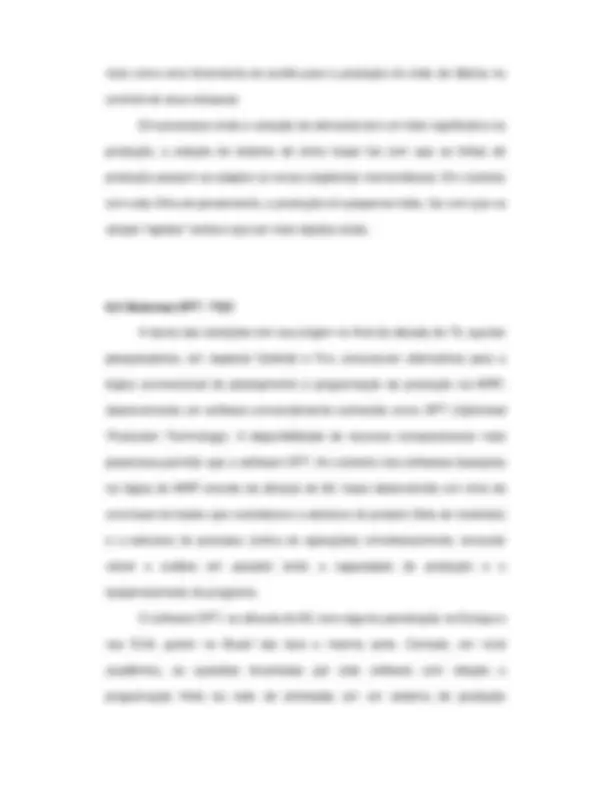
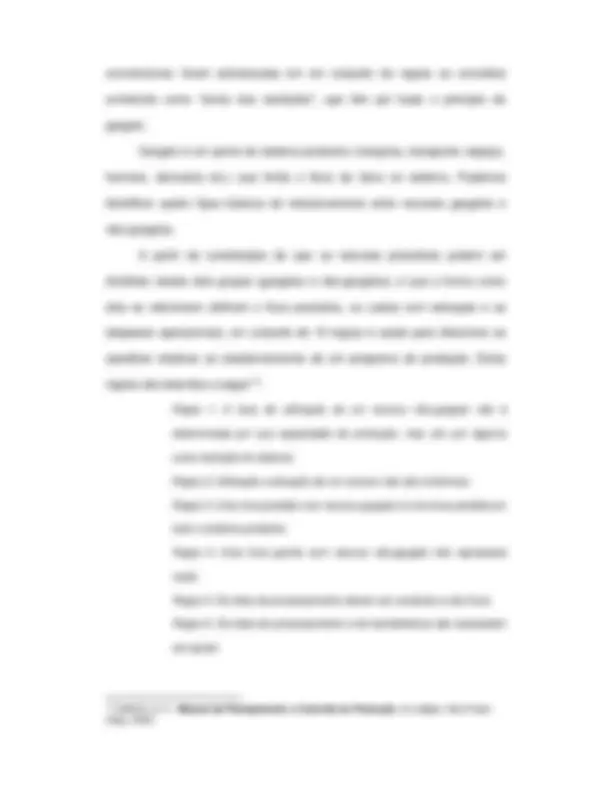
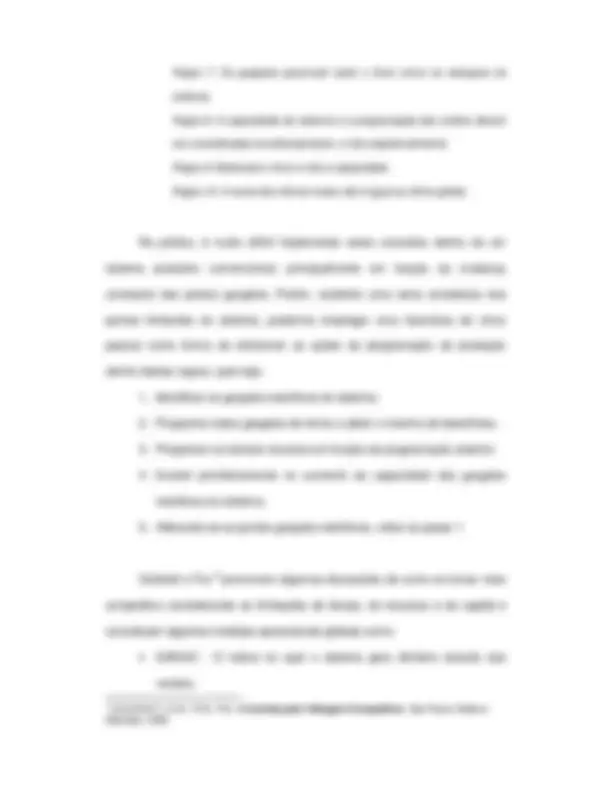
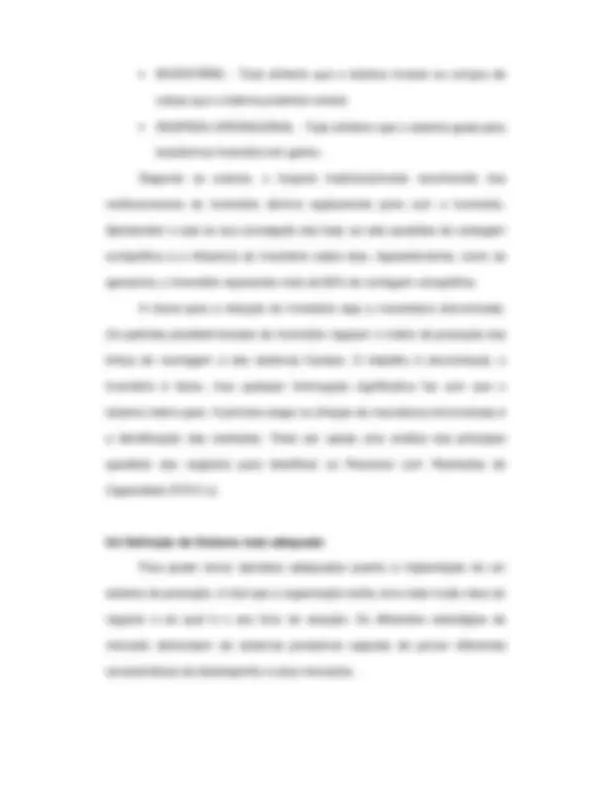
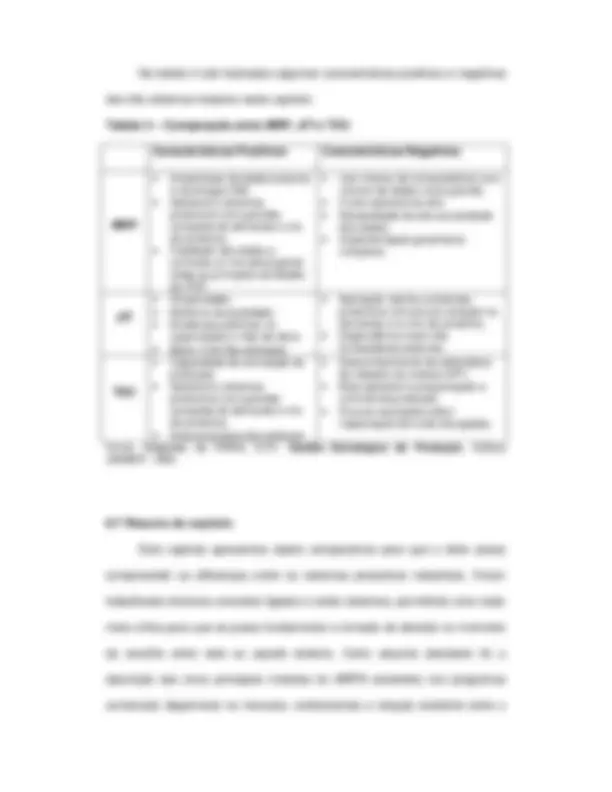
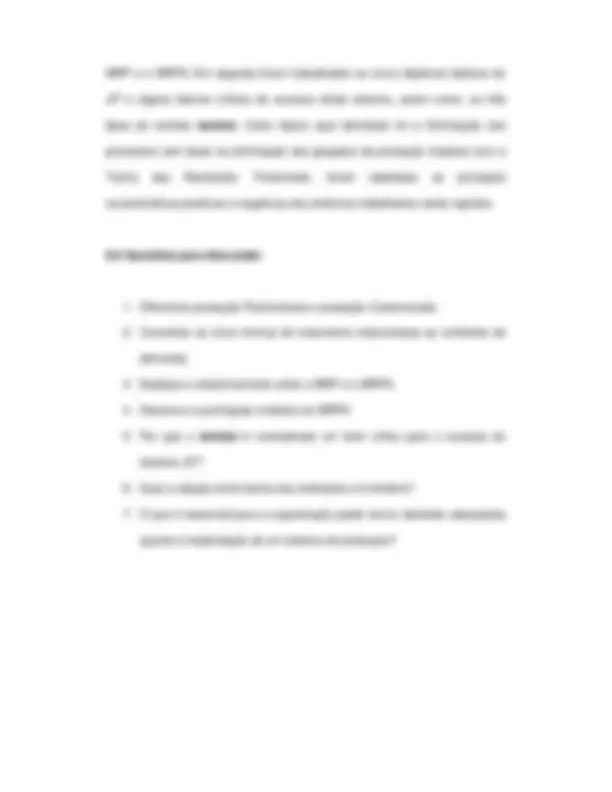
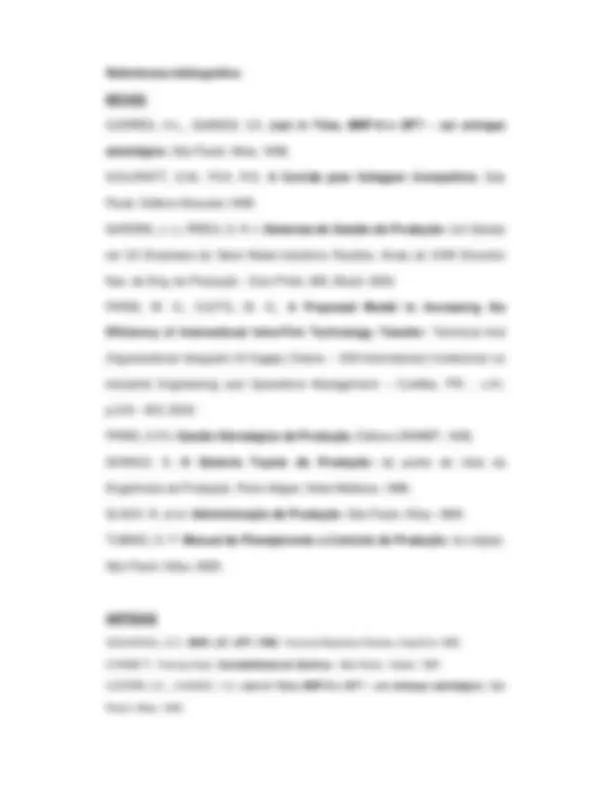
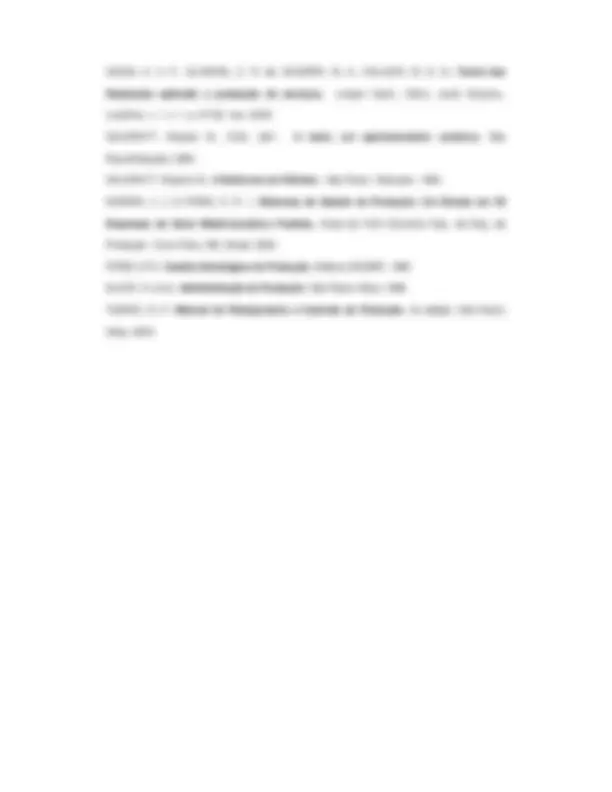
Estude fácil! Tem muito documento disponível na Docsity
Ganhe pontos ajudando outros esrudantes ou compre um plano Premium
Prepare-se para as provas
Estude fácil! Tem muito documento disponível na Docsity
Prepare-se para as provas com trabalhos de outros alunos como você, aqui na Docsity
Os melhores documentos à venda: Trabalhos de alunos formados
Prepare-se com as videoaulas e exercícios resolvidos criados a partir da grade da sua Universidade
Responda perguntas de provas passadas e avalie sua preparação.
Ganhe pontos para baixar
Ganhe pontos ajudando outros esrudantes ou compre um plano Premium
Comunidade
Peça ajuda à comunidade e tire suas dúvidas relacionadas ao estudo
Descubra as melhores universidades em seu país de acordo com os usuários da Docsity
Guias grátis
Baixe gratuitamente nossos guias de estudo, métodos para diminuir a ansiedade, dicas de TCC preparadas pelos professores da Docsity
Este capítulo objetiva apresentar alguns Sistemas Produtivos Industriais: Planejamento das Necessidades de Materiais (MRP); Planejamento dos Recursos de Manufatura (MRPII); Produção Just-in-Time (JIT) e o Sistema Kanban; Tecnologia da Produção Otimizada (OPT) e a Teoria das Restrições (TOC).
Tipologia: Notas de aula
1 / 26
Esta página não é visível na pré-visualização
Não perca as partes importantes!
Capítulo 8 – Sistemas Produtivos Industriais Este capítulo objetiva apresentar alguns Sistemas Produtivos Industriais: Planejamento das Necessidades de Materiais (MRP); Planejamento dos Recursos de Manufatura (MRPII); Produção Just-in-Time (JIT) e o Sistema Kanban; Tecnologia da Produção Otimizada (OPT) e a Teoria das Restrições (TOC). A abordagem inicial está focada em alguns conceitos preliminares que envolvem aspectos estratégicos na utilização destes sistemas, bem como, um pequeno apanhado do ambiente de demanda. Tal enfoque permite uma inserção do leitor aos temas que envolvem o sistema produtivo industrial. Ao final do capítulo é apresentada uma tabela comparativa entre os SPIs trabalhados evidenciando suas principais vantagens e desvantagens.
8.1 Conceitos iniciais Mudanças na economia mundial e no cenário da produção de bens industriais vêm transformando o mercado e a forma de administrá-lo. Uma das áreas que vem promovendo grandes modificações na gestão empresarial é a Administração da Produção. Vários fatores têm destacado esta área, dos quais se podem citar alguns:
e deve estar atrelado às estratégias empresariais. Ele é um fator preponderante aos objetivos da empresa e como tal, suas atividades operacionais de manufatura devem representar o desdobramento das ações definidas no planejamento estratégico. Para a escolha do sistema produtivo devem-se considerar, também, dois outros fatores importantes: (a) Agregação de Valor, pois, o cliente deve reconhecer a qualidade e as especificações dos produtos e processos, bem como, estar disposto a pagar por elas; e (b) Inovação, a capacidade de promover melhoria contínua com vistas à redução de custos e ao aprimoramento constante da qualidade dos produtos e dos processos. A gestão da produção em uma indústria costuma ser representada pelas atividades de planejamento e controle da produção. Assim, o termo PCP (Planejamento e Controle da Produção) é utilizado para designar uma série de atividades, tradicionalmente executadas dentro de uma atividade mais ampla e fundamental dentro da indústria: a gestão da produção. Essas atividades são geralmente executadas através dos chamados sistemas de PCP^1 , os quais estão relacionados a seguir:
(^1) NARDINI, J. J.; PIRES, S. R. I. Sistemas de Gestão da Produção: Um Estudo em 20 Empresas do Setor Metal-mecânico Paulista. Anais do XXIII Encontro Nac. de Eng. deProdução - Ouro Preto, MG, Brasil, 2003.
Qualquer que seja o sistema considerado, a seguinte pergunta deveria ser feita: Como o sistema está conectado em termos de Plano Mestre de Produção, Planejamento da Capacidade, Liberação dos Pedidos de Compra, Liberação das Ordens de Produção ou outros Sub-Sistemas de Controle? O MRP I – Material Requeriments Planning (Planejamento das Necessidades de Materiais) possui um modelo mais simplificado, por ser essencialmente voltado para o planejamento e controle da produção e estoques. A figura 18 mostra um modelo esquemático dos Registros de Estoque MRP. Figura 18 – Registros de Estoque MRP
Fonte: Adaptado de SLACK, N et al. Administração da Produção. São Paulo: Atlas, 1999. O Planejamento de Recursos de Manufatura (MRPII) é um sistema que reúne todas as informações referentes às diversas atividades de produção em uma única base de dados. É muito importante para o bom desempenho do planejamento da produção industrial porque ultrapassa as fronteiras do MRP, que é restrito ao cálculo das necessidades de materiais.
Planejamento dasnecessidades de materiais
Listas demateriais Registros de estoque
Programa-mestrede produção
Ordens de compra Planos de materiais Ordens de trabalho
Carteira depedidos Previsão de vendas
No MRP, alguns documentos são duplicados e tratados por diferentes sistemas. Quando há necessidade de alguma alteração é comum se verificar distorções entre os documentos, principalmente na Lista de Materiais, administradas pela engenharia de produto e pela área de materiais. Ao se tratar as mesmas informações em bases de dados diferentes são comuns os erros de digitação que provocam grandes problemas na execução dos planos de fabricação. Os diversos módulos do MRP II integram vários sistemas menores que evitam os problemas citados e executam as variadas funções que compreendem o Planejamento e Controle da Produção. As atividades básicas do PCP são ilustradas na Figura 19. Figura 19 – MRP de Ciclo Fechado
Fonte: Adaptado de SLACK, N. et al. Administração da Produção. São Paulo: Atlas, 1999.
Segundo Slack 2 , Oliver Wight, um dos idealizadores do MRP e MRP II, definiu MRP II como " Um plano global para o planejamento e monitoramento de todos os recursos de uma empresa de manufatura: manufatura, marketing, finanças e engenharia. Tecnicamente, ele envolve a utilização do sistema MRP de ciclo fechado para gerar números financeiros ”.
(^2) SLACK, N. et al. Administração da Produção. São Paulo: Atlas, 1999.
Plano de produção
Programa de produção-mestre
Plano de materiais
Plano de neces de recursossidades
Programa de produção-mestre
Plano de materiais
tempo de preparação, mais importante torna-se este assunto. A Quebra de Equipamentos é outro aspecto importante e a manutenção preventiva ou outras devem ser levadas em consideração. Outro objetivo, geralmente deixado de lado, é a utilização da capacidade instalada. Na maioria das vezes, a capacidade é superdimensionada para ter maior segurança, assim como os estoques. O que deve ser feito pela Administração de Materiais é melhorar continuamente as metas e objetivos do MRP. O desafio é atender o cliente da melhor forma, com o menor investimento em estoque. Os principais fatores que influenciam estas metas são: a Previsão de Vendas e o desenvolvimento de um Plano Mestre de Produção. A alta administração também deve perceber que o fluxo de caixa está implícito no Plano Mestre e podemos chamá-lo de Plano Global. Uma outra atividade é a denominada Liberação de Ordens. Existe uma dimensão de tempo e quantidade nesta atividade, ou seja, QUANDO e QUANTO. A liberação das ordens está ligada ao Plano Mestre. Outra atividade feita no MRP é o seguimento (“ follow-up ”), expedição, planejamento de prioridade. Temos, ainda, O Planejamento da Capacidade, que é a atividade onde se constata a existência de altos e baixos ou ainda sobrecargas de capacidade, podendo tomar as medidas necessárias com antecedência. Finalmente, chegamos à Manutenção dos Registros. Para que o conceito de Administração de Materiais seja efetivo, é necessário ter COORDENAÇÃO. A Administração de Materiais envolve muitas pessoas com necessidades, objetivos e prioridades conflitantes.
8.3 Principais módulos do MRPII Os sistemas MRPII são compostos por módulos que interligam as diferentes funções do PCP. Os pacotes computacionais disponíveis no mercado são similares quanto aos módulos principais e a lógica básica. Figura 20 – Módulos básicos do MRPII
O MRPII possui cinco módulos principais^4 :
(^4) CORRÊA, H.L., GIANESI, I.G. Just in Time, MRP-II e OPT – um enfoque estratégico. São Paulo: Atlas, 1996.
ressuprimento – lead-time ; e (g) Tamanho do lote – lot size. O MRP gera liberações de ordens planejadas a partir dos cálculos das necessidades brutas, recebimentos programados e estoque disponível projetado. Salienta-se que o entendimento do funcionamento do registro básico do MRP é fundamental para o entendimento como um todo. No Quadro 1, é apresentado um exemplo do Registro básico período a período do MRP, considerando o tempo de ressuprimento de 1 período, tamanho do lote igual a 620 unidades e um estoque inicial de 13 unidades. Quadro 1 – Registro básico período a período do MRP Período 1 2 3 4 5 6 Necessidades brutas Recebimentos programados 620 255 364 302 Estoque projetado disponível Plano de liberações de ordens 13 633 378 378 62014 332 332
8.3.4 Cálculo de Necessidade de Capacidade (CRP): sua função é prover as futuras necessidades e identificar possíveis ociosidades futuras. Isto deve ocorrer com antecedência suficiente a fim de obter a maior eficiência de um sistema de administração da produção. Capacidade de manufatura insuficiente pode prejudicar o desempenho de uma empresa quanto ao cumprimento de prazos, um critério competitivo essencial no mercado competitivo atual. O CRP fornece subsídios para a tomada de decisões gerenciais quanto às ordens de produção, tanto para sua confirmação e alteração como para redirecionar as ações quando da inviabilidade do plano em função da disponibilidade dos recursos produtivos. 8.3.5 Controle de Fábrica (SFC): é responsável por: executar o plano de materiais, executar o plano de capacidade, controlar todas as atividades dos centros de trabalho, maximizar a produtividade e controlar prioridades (O que
estamos produzindo? Quais itens? Quando iniciamos e quando terminamos? Quando são necessários? Como fazemos?). Seqüência as ordens de produção por célula e controla a produção dentro do prazo planejado no “Chão de Fábrica”. A função básica deste módulo é a interação dos sistemas de controle e acompanhamento, com foco no cumprimento dos prazos. Utiliza algoritmos de programação finita gerando o carregamento detalhado a partir do seqüenciamento das ordens nos recursos em um período planejado.
8.4 Sistema JIT / Kanban O sistema JIT ( Just-in-Time ) surgiu no Japão na década de 60, sendo desenvolvida na indústria automobilística, mais especificamente na Toyota Motor Company. Na década de 70 este conceito foi difundido para o ramo de autopeças e eletrônica. Com o avanço da economia japonesa, já nos anos 80, o sistema passou a ser difundido também para o mundo ocidental. Just–in–time significa produzir as unidades necessárias em quantidades necessárias no tempo necessário, logo, o sistema JIT tem como regra produzir no momento em que for necessário, ou seja, determinação de um estoque tendendo a zero. O seu sucesso está vinculado ao fato de que o controle da programação garanta a presença da matéria-prima no momento certo da produção e o balanceamento da capacidade produtiva seja capaz de produzir no tempo adequado. No sistema de planejamento são utilizados três tipos de pedidos aos fornecedores (internos e externos): (a) Plano agregado de produção ( Release anual, semestral, trimestral); (b) Plano mestre de produção
De acordo com Tubino^6 , a filosofia JIT foca cinco objetivos básicos:
Um sistema JIT deve considerar alguns fatores críticos de sucesso. Abaixo estão relacionados alguns elementos básicos para o bom funcionamento do sistema:
(^6) TUBINO, D. F.. Manual de Planejamento e Controle da Produção. 2o edição. São Paulo: Atlas, 2000.
visto como uma ferramenta de auxilio para a produção do chão de fábrica no controle de seus estoques. Em processos onde a variação da demanda tem um fator significativo na produção, a adoção de sistema de único toque faz com que as linhas de produção possam se adaptar as novas exigências momentâneas. Em conexão com esta linha de pensamento, a produção em pequenos lotes, faz com que os setups "rápidos" tenham que ser mais rápidos ainda.
8.5 Sistemas OPT / TOC A teoria das restrições tem sua origem no final da década de 70, quando pesquisadores, em especial Goldratt e Fox, procuraram alternativas para a lógica convencional de planejamento e programação da produção via MRP, desenvolvendo um software comercialmente conhecido como OPT ( Optimized Production Technology ). A disponibilidade de recursos computacionais mais poderosos permitiu que o software OPT. Ao contrário dos softwares baseados na lógica do MRP oriundo da década de 60, fosse desenvolvido em cima de uma base de dados que considerava a estrutura do produto (lista de materiais) e a estrutura do processo (rotina de operações) simultaneamente, tornando viável a análise em paralelo entre a capacidade de produção e o seqüenciamento do programa. O software OPT, na década de 80, teve alguma penetração na Europa e nos EUA, porém no Brasil não teve a mesma sorte. Contudo, em nível acadêmico, as questões levantadas por este software com relação a programação finita da rede de atividades em um sistema de produção
convencional, foram estruturadas em um conjunto de regras ou conceitos conhecido como “teoria das restrições”, que têm por base o princípio de gargalo. Gargalo é um ponto do sistema produtivo (máquina, transporte, espaço, homens, demanda etc.) que limita o fluxo de itens no sistema. Podemos identificar quatro tipos básicos de relacionamento entre recursos gargalos e não-gargalos. A partir da constatação de que os recursos produtivos podem ser divididos nestes dois grupos (gargalos e não-gargalos), e que a forma como eles se relacionam definem o fluxo produtivo, os custos com estoques e as despesas operacionais, um conjunto de 10 regras é usado para direcionar as questões relativas ao seqüenciamento de um programa de produção. Estas regras são descritas a seguir 8 : Regra 1: A taxa de utilização de um recurso não-gargalo não é determinada por sua capacidade de produção, mas sim por alguma outra restrição do sistema. Regra 2: Utilização e ativação de um recurso não são sinônimas. Regra 3: Uma hora perdida num recurso gargalo é uma hora perdida em todo o sistema produtivo. Regra 4: Uma hora ganha num recurso não-gargalo não representa nada. Regra 5: Os lotes de processamento devem ser variáveis e não fixos. Regra 6: Os lotes de processamento e de transferência não necessitam ser iguais.
(^8) TUBINO, D. F.. Manual de Planejamento e Controle da Produção. 2o edição. São Paulo: Atlas, 2000.