
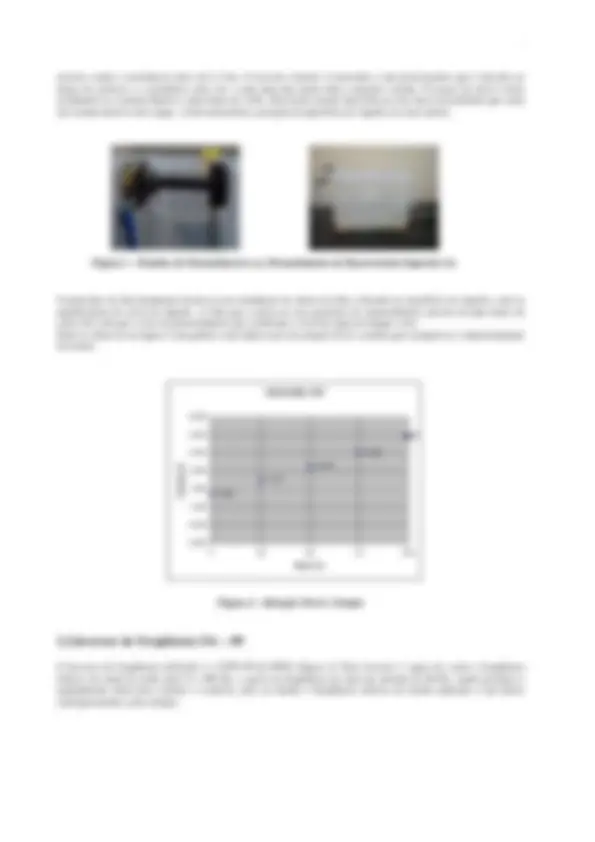
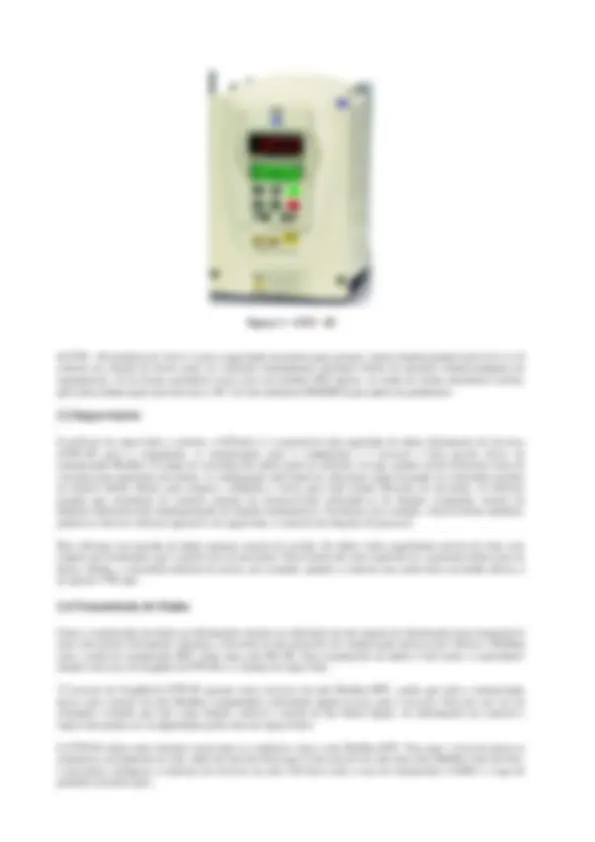
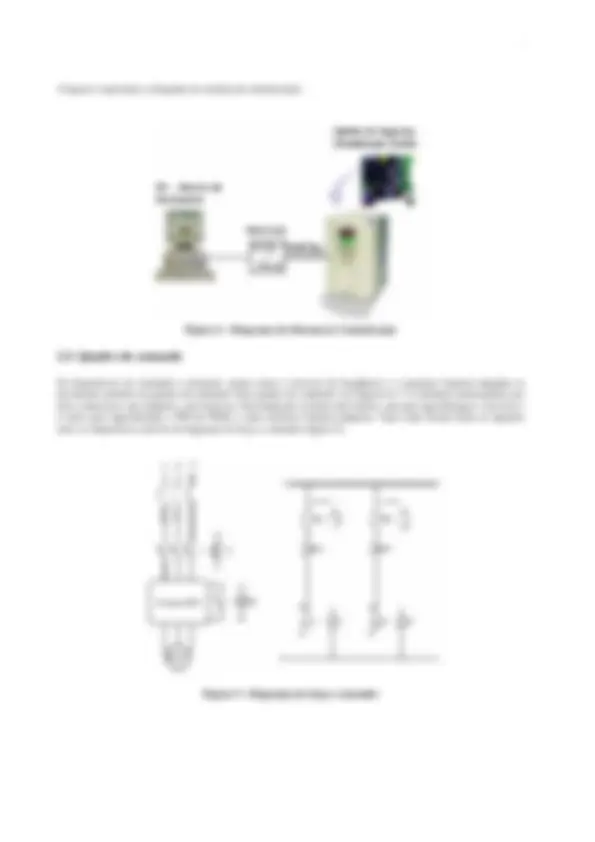
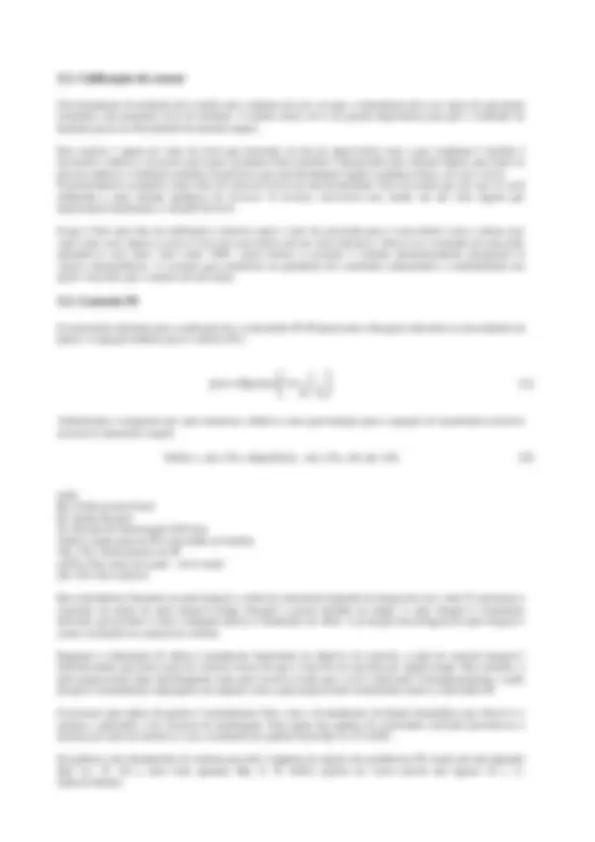
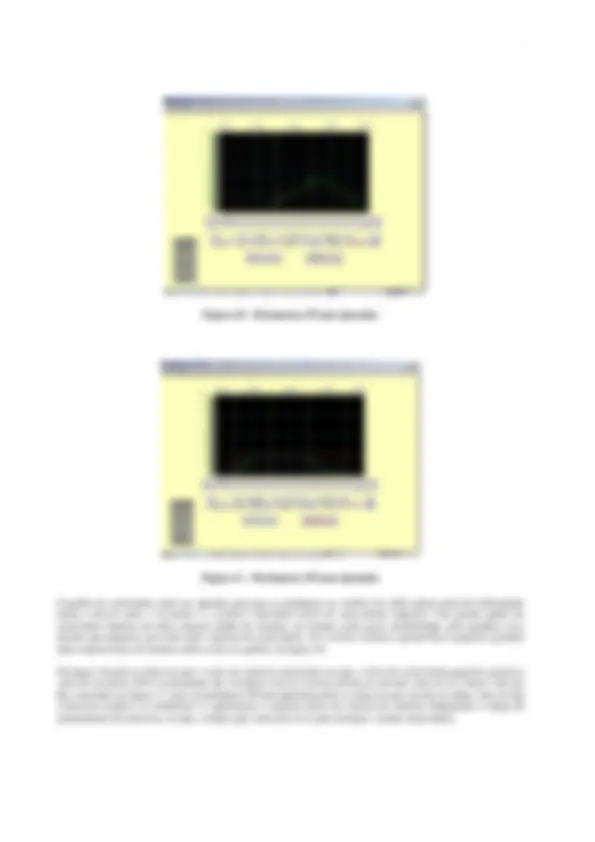
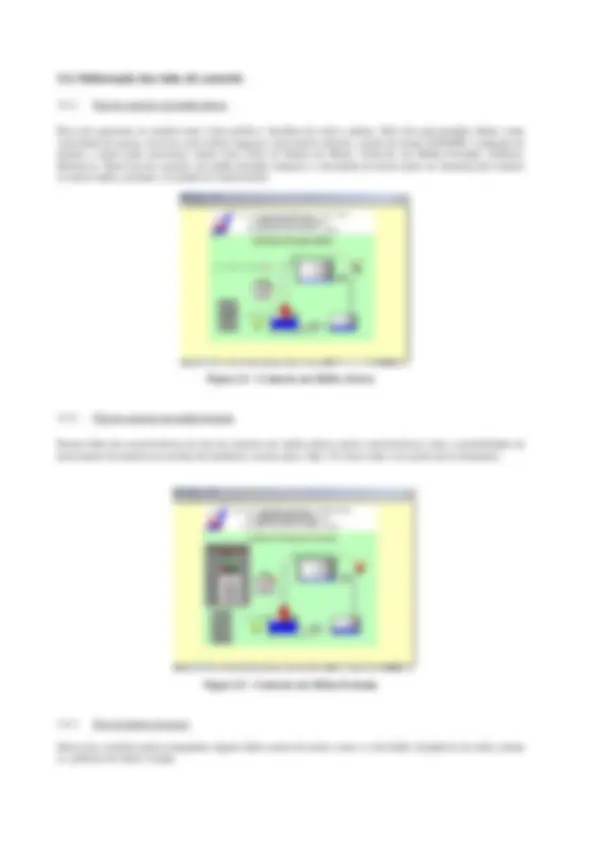
Estude fácil! Tem muito documento disponível na Docsity
Ganhe pontos ajudando outros esrudantes ou compre um plano Premium
Prepare-se para as provas
Estude fácil! Tem muito documento disponível na Docsity
Prepare-se para as provas com trabalhos de outros alunos como você, aqui na Docsity
Os melhores documentos à venda: Trabalhos de alunos formados
Prepare-se com as videoaulas e exercícios resolvidos criados a partir da grade da sua Universidade
Responda perguntas de provas passadas e avalie sua preparação.
Ganhe pontos para baixar
Ganhe pontos ajudando outros esrudantes ou compre um plano Premium
Comunidade
Peça ajuda à comunidade e tire suas dúvidas relacionadas ao estudo
Descubra as melhores universidades em seu país de acordo com os usuários da Docsity
Guias grátis
Baixe gratuitamente nossos guias de estudo, métodos para diminuir a ansiedade, dicas de TCC preparadas pelos professores da Docsity
- - - - - - -
Tipologia: Notas de estudo
1 / 12
Esta página não é visível na pré-visualização
Não perca as partes importantes!
I Congresso de Pesquisa e Inovação da Rede Norte Nordeste de Educação Tecnológica Natal-RN - 2006.
Departamento Acadêmico de Tecnologia Industrial – CEFET-RN Av. Salgado Filho, 1159 Morro Branco CEP 59.000-000 Natal-RN E-mail: anchieta@cefetrn.br
Departamento Acadêmico de Tecnologia Industrial – CEFET-RN Av. Salgado Filho, 1159 Morro Branco CEP 59.000-000 Natal-RN E-mail: jonathan@cefetrn.br
Departamento Acadêmico de Tecnologia Industrial – CEFET-RN Av. Salgado Filho, 1159 Morro Branco CEP 59.000-000 Natal-RN E-mail: prisamp@yahoo.com.br
A determinação do nível e o seu controle são pontos bastantes comuns observados em processos industriais como nas indústrias químicas, petróleo, papel, alimentos, têxtil, tratamento de água e no tratamento de efluentes, pois envolvem o controle operacional ou controle de custo.
O nível de líquido é, em geral, expresso como uma medida de comprimento em relação a uma referência (base de um tanque, por exemplo).
No processo de abastecimento de água, por exemplo, os reservatórios têm como principais funções operar como reguladores da distribuição, atendendo à variação horária do consumo, assegurando uma reserva d'água para combate a incêndio, mantendo uma reserva para atender as condições de emergência (acidentes ou reparos nas instalações), atender à demanda no caso de interrupções de energia elétrica (blecaute) e a manutenção de pressões na rede distribuidora. Geralmente os reservatórios demandam controle de nível a fim de mantê-lo cheios de forma a não extravasarem. Os sistemas mais comuns são os de bóia ligados a sinaleiros ou a controles elétrico-eletrônicos de comando das bombas que os abastecem. Sistemas de aquisição de dados poderão ser utilizados com a finalidade de obter as informações necessárias para o bom funcionamento do sistema.
Nos cursos técnicos e tecnológicos oferecidos pelo CEFET-RN na área da indústria, como os cursos de Tecnologia em Materiais, Tecnologia em Automação Industrial, curso técnico em Petróleo e técnico de Mecânica, grande parte da disciplina de instrumentação é dada de forma teórica. Observou-se, portanto uma grande necessidade de uma ferramenta didática para a prática e simulação de plantas de processos industriais, bem como a implementação e ajuste de controladores.
Diante disso foi criada uma bancada didática para preencher essa lacuna que é apresentado na tentativa de melhorar em aspectos didáticos cursos de controle e controle de processos.
O modelo didático é formado por um conjunto de três reservatórios montados um sobre o outro, o reservatório intermediário é utilizado na função de reter o fluido para simulação de esvaziamento do reservatório inferior. O controle é aplicado para regular, segundo um valor de referência o nível do reservatório superior, as informações utilizadas na realimentação do sistema são obtidas por um sistema analógico resistores acoplados a um sistema de bóia.
Todo o sistema é operado e intertravado pelo aplicativo supervisório. Nesse aplicativo são mostrados ao usuário os valores de todas as variáveis do sistema, bem como dados da bomba, alarmes, gráficos de tendência, além de todos os parâmetros do controlador didático.
O sistema realiza as operações matemáticas do controlador no aplicativo de supervisão enviando em seguida esse resultado para o inversor que por sua vez irá informar a bomba a velocidade necessária que ela deve atingir para que o nível desejado seja alcançado.
Durante o desenvolvimento da bancada, foram utilizados equipamentos, componentes e softwares, os quais são descritos abaixo.
Na construção do sensor de nível (figura 1) foram utilizados 3 elementos. Um potenciômetro, uma haste de cobre e uma bóia de isopor.
Um dos critérios analisados para a escolha do potenciômetro foi a linearidade. Um potenciômetro linear é aquele que produz variação linear da resistência, proporcional ao deslocamento ou posição. O elemento de resistência é alimentado por uma voltagem DC ou AC e a voltagem de saída é idealmente uma função linear do deslocamento.
Os potenciômetros dos reservatórios superior e inferior estão ligados às entradas analógicas AI1 e AI2 do inversor, respectivamente. Este potenciômetro é um resistor variável com três contatos. Dois contatos conectam aos fins do
Figura 3 – CFW - 09
O CFW – 09 (potência de 18,6 cv) tem a capacidade necessária para acionar o motor bomba (potência de 0,22 cv). O controle da rotação do motor pode ser realizado manualmente mediante botões da interface homem-máquina do equipamento, ou de forma automática local, pelo seu módulo PID interno, ou ainda de forma automática remota, pela intercomunicação entre Inversor e PC via rede industrial MODBUS para ajuste de parâmetros.
O software de supervisão e controle, o InTouch, é o responsável pela aquisição de dados diretamente do inversor (CFW-09) para o computador. A comunicação entre o computador e o inversor é feita através driver de comunicação Modbus. O tempo de varredura dos dados pode ser alterado, ou seja, podem existir diferentes taxas de varredura para aquisição dos dados. A configuração individual de cada ponto supervisionado ou controlado permite ao usuário definir limites para alarmes, condições e textos para cada estado diferente de um ponto. O software permite que estratégias de controle possam ser desenvolvidas utilizando-se de funções avançadas, através de módulos dedicados para implementação de funções matemáticas e booleanas, por exemplo. Através destes módulos, poderá ser feito no software aplicativo de supervisão, o controle das funções do processo.
Este software tem entrada de dados manual, através de teclado. Os dados serão requisitados através de telas com campos pré-formatados que o usuário deverá preencher. Estes dados são auto-explicativos e possuem limites para as faixas válidas, a velocidade máxima do motor, por exemplo, quando o controle esta sendo feito em malha aberta, é de apenas 1700 rpm.
Como a transmissão de dados ou informação consiste na utilização de um suporte de informação para transportá-lo entre dois pontos fisicamente distantes e necessita de um protocolo de comunicação optou-se por utilizar o Modbus com o modo de transmissão RTU sobre uma rede RS-485. Essa transmissão de dados é feita entre o controlador/ atuador (inversor de freqüência CFW-09) e o sistema de supervisão.
O inversor de freqüência CFW-09 operam como escravos da rede Modbus-RTU, sendo que toda a comunicação inicia com o mestre da rede Modbus (computador) solicitando algum serviço para o inversor. Este por sua vez irá comandar a bomba que tem como função, realizar a sucção de um fluido (água). As informações de controle e supervisão podem ser acompanhadas pelas telas do supervisório.
O CFW-09 utiliza uma interface serial para se cominicar com a rede Modbus RTU. Para que o inversor possa se comunicar corretamente na rede, além da conexão física que é feita através do cabo para rede Modbus com três fios, é necessário configurar o endereço do inversor na rede (30) bem como a taxa de transmissão (19200) e o tipo de paridade existente (par).
A figura 4 representa o diagrama do sistema de comunicação.
Figura 4 – Diagrama do Sistema de Comunicação
Os dispositivos de comando e proteção, assim como o inversor de freqüência e a interface homem máquina se encontram reunidos no quadro de comando. Este quadro de comando (ver figuras 6 e 7) é formado internamente por dois contactores, um disjuntor, três fusíveis). Externamente existem dois botões, um para ligar/desligar o inversor e o outro para ligar/desligar o PID da WEG, e uma interface homem máquina. Veja como foram feitas as ligações entre os dispositivos através do diagrama de força e comando (figura 5).
Figura 5 – Diagrama de força e comando
Figura 8 – Bancada Didática para Controle de Nível
Os sistemas de alarme e intertravamento são acionados nas seguintes situações:
Veja na figura 9 o fluxograma de processo da bancada.
Figura 9 – Fluxograma de Processo da Bancada
Um instrumento de medição deve medir com o mínimo de erro, ou seja, o instrumento deve ser capaz de apresentar resultados com pequenos erros de medição. A análise desse erro é de grande importância para que o resultado da medição possa ser determinado de maneira segura.
Para realizar o ajuste do valor do nível que mostrado na tela do supervisório com o que realmente é medido é necessário conhecer o processo pelo qual a grandeza física medida é interpretada pelo sistema digital, para tanto se precisa conhecer o elemento primário do processo que está diretamente ligado à grandeza física, no caso o nível. O potenciômetro acoplado a uma bóia irá converter nível em um determinado valor de tensão que por sua vez será submetido a uma entrada analógica do inversor. O inversor converterá essa tensão em um valor digital que representará linearmente a variação do nível.
O que é feito para fins de calibração é observar qual o valor da conversão para o reservatório vazio e adotar esse valor como zero, depois se eleva o nível do reservatório até seu valor máximo e observa-se o resultado da conversão adotando-se esse outro valor como 100%. Após realizar a correção, o sistema automaticamente interpolará os valores intermediários. A correção gera melhorias na qualidade dos resultados aumentando a confiabilidade nas ações e decisões que o usuário deverá tomar.
O controlador utilizado para a aplicação foi o controlador PI (Proporcional e Integral) suficiente às necessidades da planta. A equação didática para o controle PI é:
Substituindo o integrador por uma somatória, obtêm-se uma aproximação para a equação de transferência discreta (recursiva) mostrada a seguir:
onde: Kp: Ganho proporcional Ki: Ganho Integral Ta: Período de amostragem (0,01seg) Y(kTa): Saída atual do PI (velocidade da bomba) Y(k-1)Ta: Saída anterior do PI e(kTa): Erro atual (set-point – nível atual) e(k-1)Ta: Erro anterior
Em controladores baseados na ação integral, a saída do controlador depende da integral do erro, onde Ti representa a constante de tempo da ação integral (tempo integral) e possui unidade de tempo. A ação integral é vastamente utilizada, pois promove como vantagem prática a eliminação do offset. A principal desvantagem da ação integral é causar oscilações na resposta do sistema.
Enquanto a eliminação do offset é usualmente importante no objetivo do controle, a ação de controle integral é utilizada desde que pouca ação de controle ocorra até que o sinal de erro persista por algum tempo. Em contraste, a ação proporcional toma imediatamente uma ação corretiva assim que o erro é detectado. Conseqüentemente, a ação integral é normalmente empregada em conjunto com a ação proporcional constituindo assim o controlador PI.
O processo para ajuste de ganhos é normalmente feito, com o levantamento da função matemática que descreve o sistema e aplicando a ela, técnicas de modelagem. Para ajuste dos ganhos do controlador utilizado procedeu-se a sintonia por meio de tentativa e erro, resultando nos ganhos finais Kp: 6 e Ti: 0,001.
Os gráficos com desempenho do sistema para dois conjuntos de ajustes dos parâmetros PI, sendo um mal ajustado (Kp: 0.1, Ti: 10) e outro bem ajustado (Kp: 6, Ti: 0.001) podem ser vistos através das figuras 10 e 11, respectivamente.
3.4.1. Tela de controle em malha aberta
Esta tela apresenta ao usuário uma visão global e imediata de toda a planta. Nela são apresentados dados como velocidade do motor, nível do reservatório superior, reservatório inferior, estado do motor (ON/OFF), condição do alarme e ainda pode selecionar outras telas (Tela de Dados do Motor, Controle em Malha Fechada, Gráficos, Histórico). Nesta tela de controle em malha fechada somente a velocidade do motor pode ser alterada pelo usuário os outros dados, portanto, só podem ser monitorados.
Figura 12 – Controle em Malha Aberta
3.4.2. Tela de controle em malha fechada
Possui além das características da tela de controle em malha aberta outras características como a possibilidade de intervenção do usuário na escolha dos melhores valores para o Kp e Ti, bem como o set-point (nível desejado).
Figura 23 – Controle em Malha Fechada
3.4.3. Tela de Dados do motor
Nesta tela o usuário pode acompanhar alguns dados atuais do motor como a velocidade, freqüência de saída, tensão cc, potência de saída e torque.
Figura14– Dados do Motor
3.4.4. Tela de Gráficos
Esta tela apresenta cinco variáveis simultaneamente, na forma gráfica, com valores coletados em tempo real ("on- line").
Figura 153 – Gráficos
3.4.5. Tela de Histórico
Esta tela apresenta o histórico de três variáveis (nível do reservatório superior, set-point e velocidade da bomba) simultaneamente, na forma gráfica, com valores coletados em tempo real ("on-line").