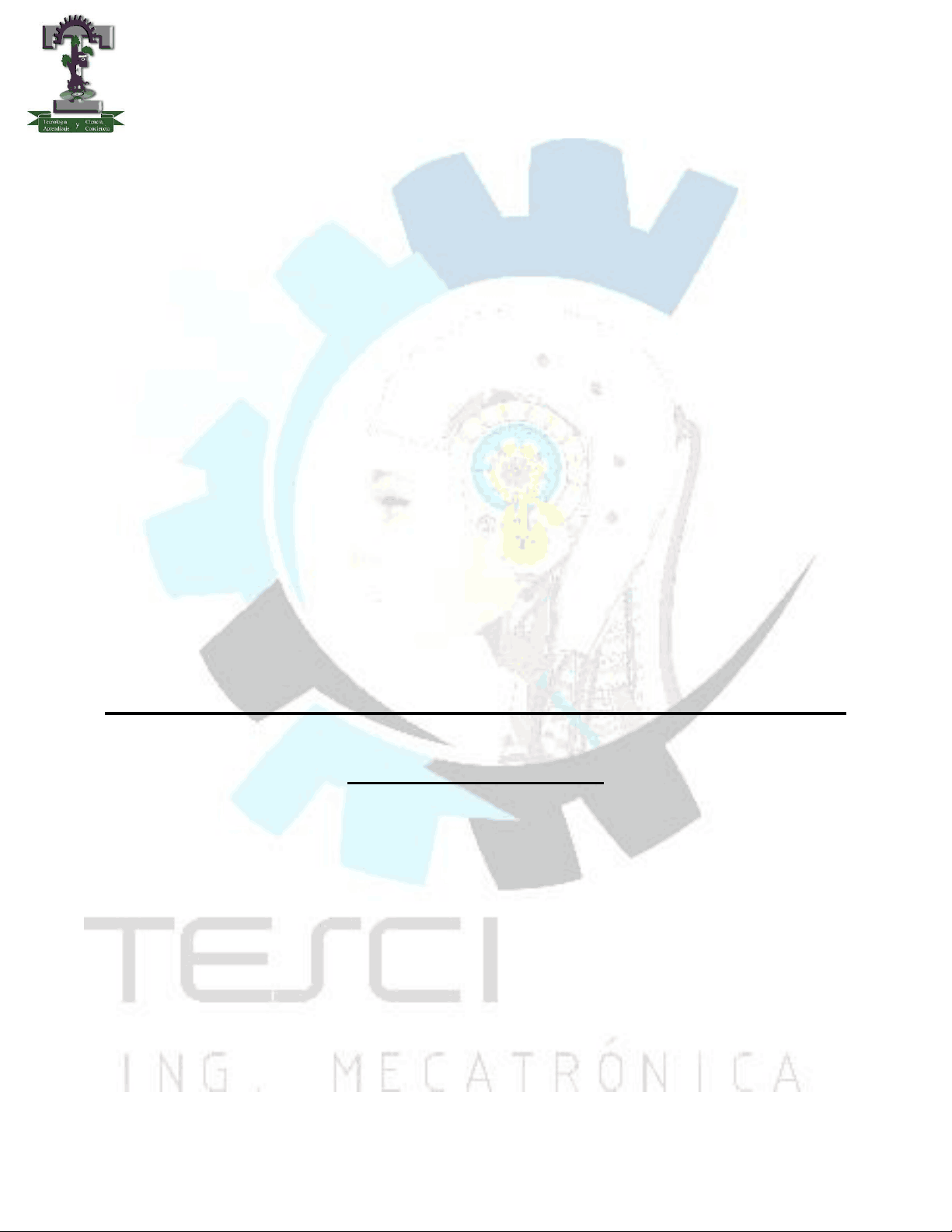
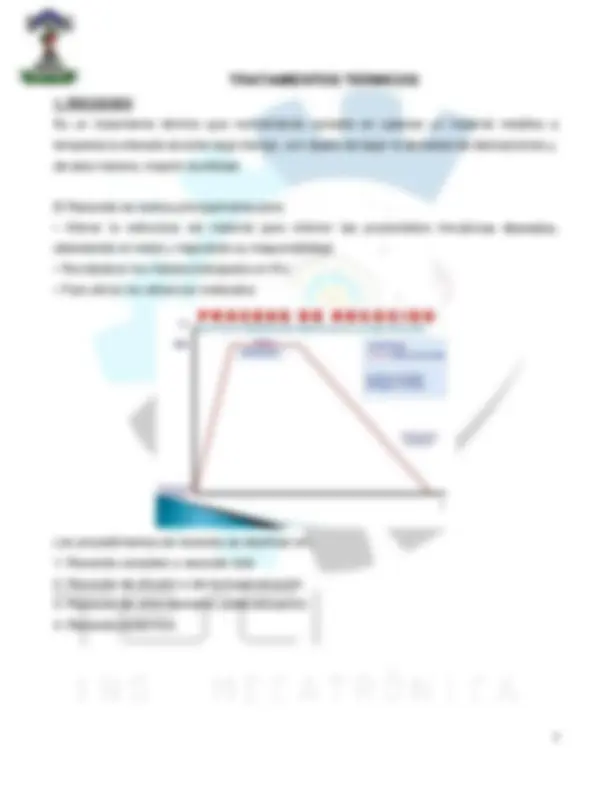
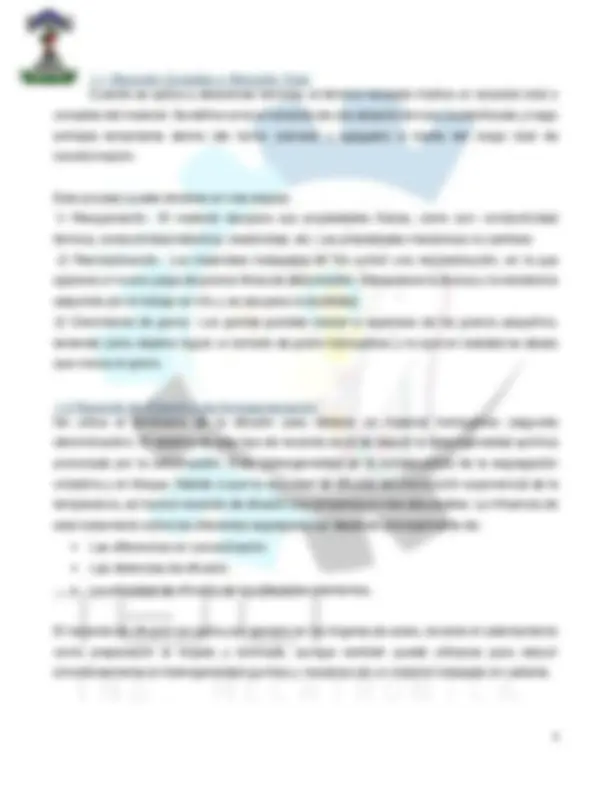
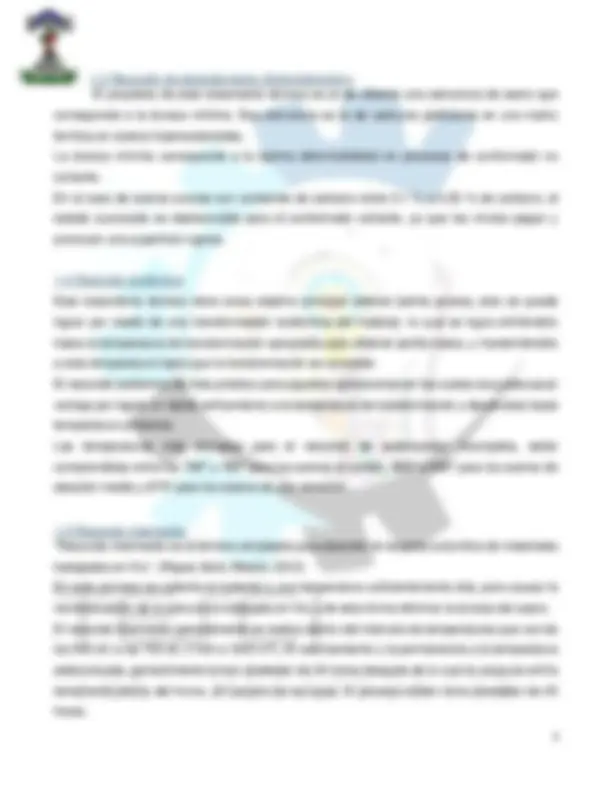

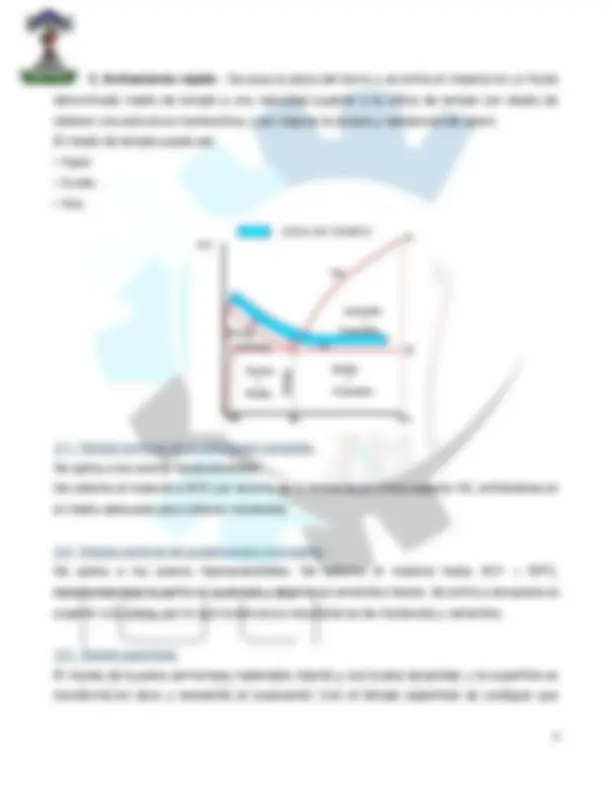
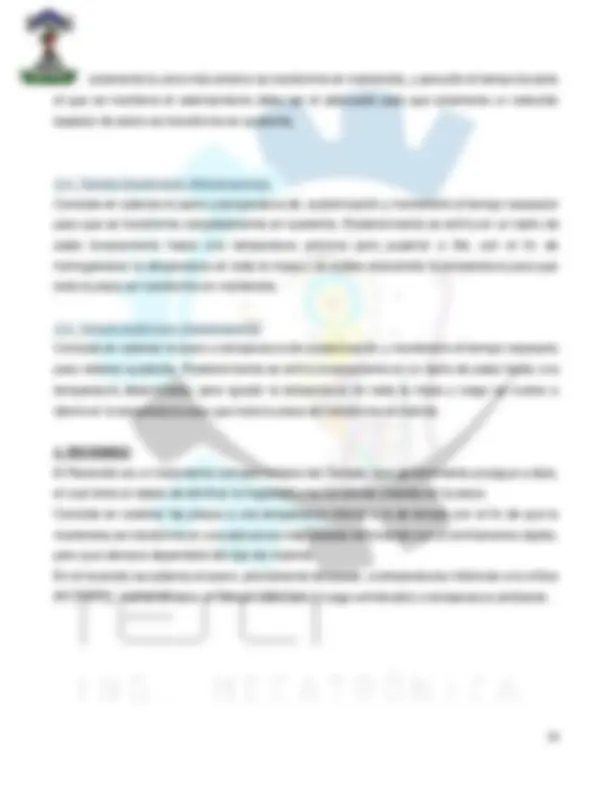
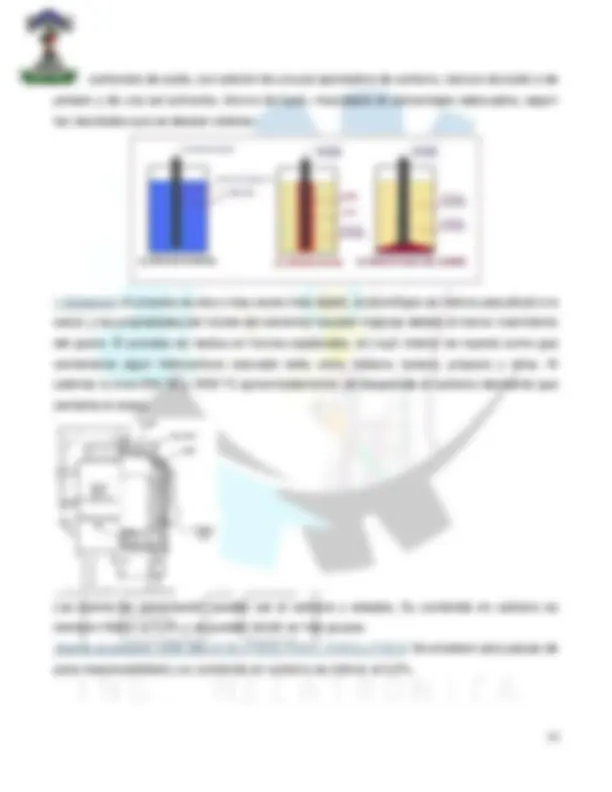
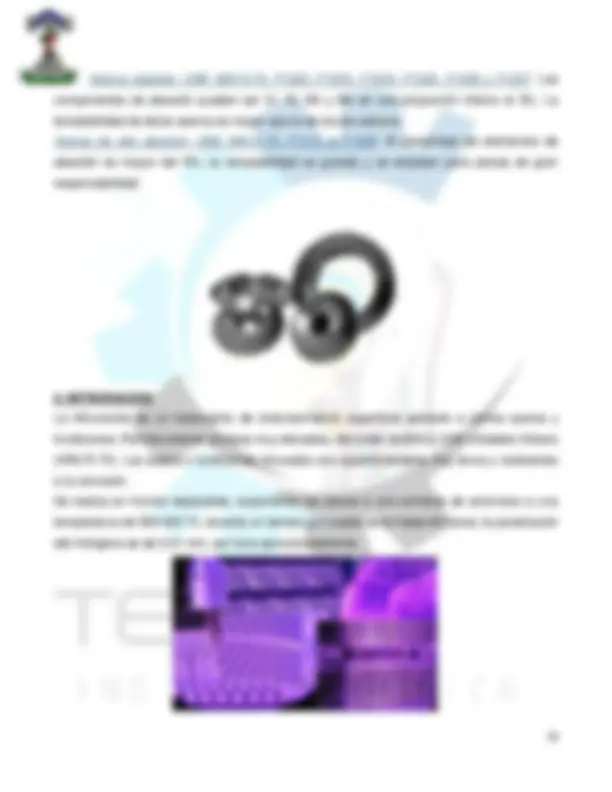
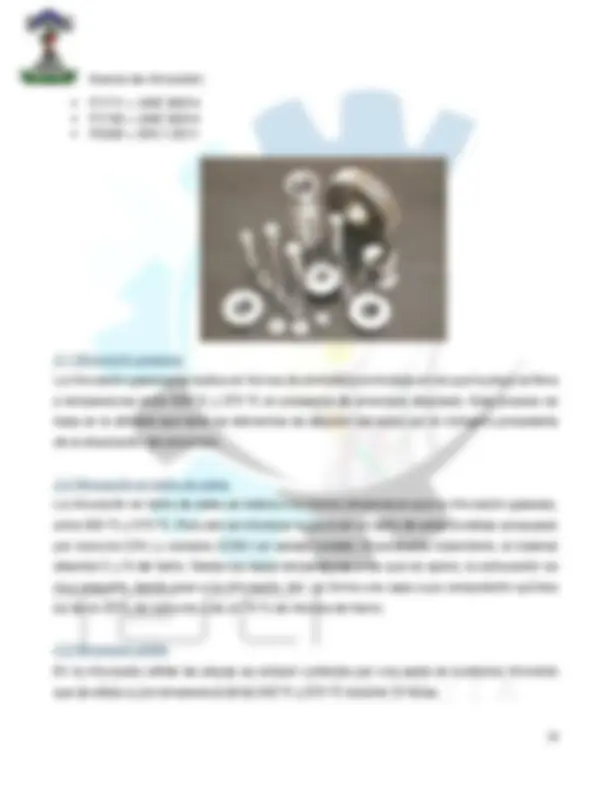
Prepara tus exámenes y mejora tus resultados gracias a la gran cantidad de recursos disponibles en Docsity
Gana puntos ayudando a otros estudiantes o consíguelos activando un Plan Premium
Prepara tus exámenes
Prepara tus exámenes y mejora tus resultados gracias a la gran cantidad de recursos disponibles en Docsity
Prepara tus exámenes con los documentos que comparten otros estudiantes como tú en Docsity
Los mejores documentos en venta realizados por estudiantes que han terminado sus estudios
Estudia con lecciones y exámenes resueltos basados en los programas académicos de las mejores universidades
Responde a preguntas de exámenes reales y pon a prueba tu preparación
Consigue puntos base para descargar
Gana puntos ayudando a otros estudiantes o consíguelos activando un Plan Premium
Comunidad
Pide ayuda a la comunidad y resuelve tus dudas de estudio
Descubre las mejores universidades de tu país según los usuarios de Docsity
Ebooks gratuitos
Descarga nuestras guías gratuitas sobre técnicas de estudio, métodos para controlar la ansiedad y consejos para la tesis preparadas por los tutores de Docsity
Apuntes sobre los diferentes tipos de tratamientos térmicos en los metales.
Tipo: Apuntes
1 / 17
Esta página no es visible en la vista previa
¡No te pierdas las partes importantes!
1.1 Recocido Completo o Recocido Total. Cuando se aplica a aleaciones ferrosas, el término recocido implica un recocido total o completo del material. Se define como el recocido de una aleación ferrosa, austenitizada y luego enfriada lentamente dentro del horno (cerrado y apagado) a través del rango total de transformación. Este proceso puede dividirse en tres etapas: 1) Recuperación .- El material recupera sus propiedades físicas, como son: conductividad térmica, conductividad eléctrica, resistividad, etc. Las propiedades mecánicas no cambian. 2) Recristalización .- Los materiales trabajados en frío sufren una recristalización, en la que aparece un nuevo juego de granos libres de deformación. Desaparece la dureza y la resistencia adquirida por el trabajo en frío y se recupera la ductilidad. 3) Crecimiento de grano .- Los granos grandes crecen a expensas de los granos pequeños, teniendo como objetivo lograr un tamaño de grano homogéneo y no que en realidad se desee que crezca el grano. 1.2 Recocido de Difusión o de Homogeneización. Se utiliza el fenómeno de la difusión para obtener un material homogéneo (segunda denominación). El objetivo de este tipo de recocido es el de reducir la heterogeneidad química provocada por la solidificación. Esta heterogeneidad es la consecuencia de la segregación cristalina y en bloque. Debido a que la velocidad de difusión es una función exponencial de la temperatura, se hará el recocido de difusión a la temperatura más alta posible. La influencia de este tratamiento sobre las diferentes segregaciones depende principalmente de:
1.3 Recocido de ablandamiento (Esferoidización). El propósito de este tratamiento térmico es el de obtener una estructura de acero que corresponda a la dureza mínima. Esa estructura es la de carburos globulares en una matriz ferrítica en aceros hipereutectoides. La dureza mínima corresponde a la óptima deformabilidad en procesos de conformado no cortante. En el caso de aceros suaves con contenido de carbono entre 0.1 % a 0.25 % de carbono, el estado suavizado es desfavorable para el conformado cortante, ya que las virutas pegan y provocan una superficie rugosa. 1.4 Recocido Isotérmico Este tratamiento térmico tiene como objetivo principal obtener perlita gruesa, esto se puede lograr por medio de una transformación isotérmica del material, lo cual se logra enfriándolo hasta la temperatura de transformación apropiada para obtener perlita basta, y manteniéndolo a esta temperatura hasta que la transformación se complete. El recocido isotérmico es más práctico para aquellas aplicaciones en las cuales se puede sacar ventaja por lograr un rápido enfriamiento a la temperatura de transformación y desde ésta hasta temperatura ambiente. Las temperaturas más elevadas para el recocido de autenizaciòn incompleta, están comprendidas entre los 760º y 780º para los aceros al carbón, 800º a 850º para los aceros de aleación media y 875º para los aceros de alta aleación. 1.5 Recocido Intermedio. “Recocido intermedio es el término empleado para describir el recocido subcrítico de materiales trabajados en frío”. (Reyes Solís Alberto, 2012) En este proceso se calienta el material a una temperatura suficientemente alta, para causar la recristalización de la estructura trabajada en frío y de esta forma eliminar la dureza del acero. El recocido intermedio generalmente se realiza dentro del intervalo de temperaturas que van de los 595 oC a los 705 oC (1100 a 1300 o F). El calentamiento y la permanencia a la temperatura seleccionada, generalmente toman alrededor de 24 horas después de lo cual la carga se enfría lentamente dentro del horno, sin sacarla de las cajas. El proceso entero toma alrededor de 40 horas.
y la segunda recristalización por la transformación de la austenita a ferrita y perlita. Cada transformación de fase provoca una recristalización y afino de grano. Sobrepasando la temperatura AC3 o AC1 en el calentamiento, los granos de ferrita y/o perlita forman pequeños granos de austenita, cuyo número depende principalmente del grado de nucleación, lo que a su vez depende de la velocidad con la que se sobrepasa la temperatura de transformación: Lo mismo es válido para la transformación de austenita a ferrita y perlita, o perlita, por eso es el enfriamiento al aire. La normalización también se puede utilizar para mejorar la maquinabilidad, modificar y refinar las estructuras dendríticas de piezas de fundición, y refinar el grano y homogeneizar la microestructura para mejorar la respuesta en las operaciones de endurecimiento. Se realiza calentando el acero a una temperatura unos 100ºC superior a la crítica y una vez austenizado se deja enfriar al aire tranquilo. La velocidad de enfriamiento es más lenta que en el temple y más rápida que en recocido. Con este tratamiento se consigue afinar y homogeneizar la estructura. Este tratamiento es típico de los aceros al carbono de construcción de 0.15% a 0.60% de carbono. A medida que aumenta el diámetro de la barra, el enfriamiento será más lento y por tanto la resistencia y el límite elástico disminuirán y el alargamiento aumentará ligeramente.
El temple es un tratamiento que tiene por objeto endurecer y aumentar la resistencia del acero. Después del temple siempre debe de hacerse la operación de revenido para eliminar y suavizar las tensiones internas creadas durante el tratamiento anterior. Consiste en calentar el acero a
una temperatura suficientemente elevada como para transformarlo en austenita; seguido de un enfriamiento adecuado para transformar la austenita en martensita. Templabilidad: capacidad de penetración del temple que tienen los aceros; la templabilidad depende fundamentalmente del espesor de la pieza y de la calidad del acero (composición química). Al realizar el temple hay que tener en cuenta los siguientes factores que influyen en el mismo:
solamente la zona más exterior se transforme en martensita, y para ello el tiempo durante el que se mantiene el calentamiento debe ser el adecuado para que solamente un reducido espesor de acero se transforme en austenita. 3.4. Temple Escalonado (Martempering). Consiste en calentar el acero a temperatura de austenización y mantenerlo el tiempo necesario para que se transforme completamente en austenita. Posteriormente se enfría en un baño de sales bruscamente hasta una temperatura próxima pero superior a Ms, con el fin de homogeneizar la temperatura en toda la masa y se acaba reduciendo la temperatura para que toda la pieza se transforme en martensita. 3.5. Temple isotérmico (Austempering) Consiste en calentar el acero a temperatura de austenización y mantenerlo el tiempo necesario para obtener austenita. Posteriormente se enfría bruscamente en un baño de sales hasta una temperatura determinada, para igualar la temperatura en toda la masa y luego se vuelve a disminuir la temperatura para que toda la pieza se transforme en bainita.
4. REVENIDO El Revenido es un tratamiento complementario del Temple, que generalmente prosigue a éste, el cual tiene el objeto de eliminar la fragilidad y las tensiones creadas en la pieza. Consiste en calentar las piezas a una temperatura inferior a la de temple con el fin de que la martensita se transforme en una estructura más estable terminando con un enfriamiento rápido, pero que siempre dependerá del tipo de material. En el revenido se calienta el acero, previamente templado, a temperaturas inferiores a la crítica A1 (723ºC), manteniéndolo un tiempo adecuado y luego enfriándolo a temperatura ambiente.
Los tratamientos termoquímicos son tratamientos térmicos en los que, además de los cambios en la estructura del acero, también se producen cambios en la composición química de la capa superficial, añadiendo diferentes productos químicos hasta una profundidad determinada. Estos tratamientos requieren el uso de calentamiento y enfriamiento controlados en atmósferas especiales. Entre los objetivos más comunes de estos tratamientos está el aumentar la dureza superficial de las piezas dejando el núcleo más blando y tenaz, disminuir el rozamiento aumentando el poder lubrificante, aumentar la resistencia al desgaste, aumentar la resistencia a fatiga o aumentar la resistencia a la corrosión.
1. CEMENTACIÓN La cementación es un tratamiento termoquímico que consiste en carburar una capa superficial de una pieza de acero, rodeándola de un producto carburante y calentándola a una temperatura adecuada mediante difusión, modificando su composición, impregnando la superficie y sometiéndola a continuación a un tratamiento térmico, un temple y un revenido, quedando la pieza con buena tenacidad en el núcleo y con mucha dureza superficial. El objetivo de la cementación es que en el templado del acero proporciona dureza a la pieza, pero también fragilidad.
carbonato de sodio, con adición de una sal aportadora de carbono, cianuro de sodio o de potasio y de una sal activante, cloruro de bario, mezclados en porcentajes adecuados, según los resultados que se deseen obtener.
- Gaseosos : el proceso es dos o tres veces más rápido, la tecnología es menos perjudicial a la salud, y las propiedades del núcleo sin cementar resultan mejores debido al menor crecimiento del grano. El proceso se realiza en hornos especiales, en cuyo interior se inyecta como gas cementante algún hidrocarburo saturado tales como metano, butano, propano y otros. Al calentar a unos 900 ºC y 1000 ºC aproximadamente, se desprende el carbono elemental que cementa el acero. Los aceros de cementación pueden ser al carbono y aleados. Su contenido en carbono es siempre inferior al 0,2% y se pueden dividir en tres grupos: Aceros al carbono: UNE 36013-75; F1510, F1511, F1512 y F1513. Se emplean para piezas de poca responsabilidad y su contenido en carbono es inferior al 0,2%.
Aceros aleados: UNE 36013-75; F1522, F1523, F1524, F1525, F1526 y F1527. Los componentes de aleación pueden ser Cr, Ni, Mn y Mo en una proporción inferior al 3%. La templabilidad de éstos aceros es mayor que la de los de carbono. Aceros de alta aleación: UNE 26013-75; F1515 al F1589. El porcentaje de elementos de aleación es mayor del 5%; su templabilidad es grande y se emplean para piezas de gran responsabilidad
2. NITRURACION La Nitruración es un tratamiento de endurecimiento superficial aplicado a ciertos aceros y fundiciones. Permite obtener durezas muy elevadas, del orden de 800 a 1200 unidades Vickers (HRc70-72). Los aceros o fundiciones nitrurados son superficialmente muy duros y resistentes a la corrosión. Se realiza en hornos especiales, exponiendo las piezas a una corriente de amoníaco a una temperatura de 500-525 ºC, durante un tiempo que puede durar hasta 90 horas; la penetración del nitrógeno es de 0,01 mm. por hora aproximadamente.
2.4 Nitruración iónica o por plasma. Es un tipo de nitruración gaseosa dirigida a aumentar la velocidad de difusión del nitrógeno y reducir el tiempo de tratamiento. Se realiza dentro de un reactor donde se ha hecho vacío antes de introducir los gases de nitruración. Estableciéndose un circuito eléctrico en el que la pieza a nitrurar es el ánodo, por efecto del calor, el nitrógeno molecular se descompone e ioniza. Con ello se produce la difusión del nitrógeno por la superficie y la consiguiente formación de nitruros.
3. CIANURACION La cianuración se puede considerar como un tratamiento intermedio entre la cementación y la nitruración, ya que el endurecimiento se consigue por la acción combinada del carbono y el nitrógeno a una temperatura determinada. Cuando se quiere obtener una superficie dura y resistente al desgaste, se realiza a una temperatura por encima de la crítica del corazón de la pieza entre 750 ºC y 950 ºC aproximadamente, se introduce la pieza en una solución que generalmente consta de cianuro de sodio con cloruro de sodio y carbonato de sodio, el enfriamiento se hará directamente por inmersión al salir del baño de cianuro con esto se obtiene una profundidad de superficie templada uniforme de unos 0,25 mm en un tiempo de una hora. Las sales empleadas en la cinauración son calentadas a 800-900 ºC en presencia del oxígeno del aire, estas sales están compuestas de Cobalto (Co), Socio (Na), Carbono (CN) y Nitrógeno (N). El Cobalto y el Nitrógeno son los encargados de la carburación y la nitruración respectivamente. Los baños de cianuro se usan generalmente en los procesos de temple de acero para impedir la descarburación de la superficie. Sus principales ventajas son: la buena
eliminación de oxidación, la profundidad de la superficie es duradera, el contenido de carbono se reparte homogéneamente y de gran rapidez de penetración. 3.1 Cianuración a la flama El calentamiento del acero se realiza de forma local, de modo que con el enfriamiento se produzca un temple localizado en la región afectada. La profundidad de temple con este proceso varia de 1,5 a 6,5 mm este método se emplea en superficies de piezas grandes por su deformación que es mínima. Para aceros al carbono el contenido de este debe ser entre 0, % a 0,70 %. 3.2 Cianuración por inducción El calentamiento se realiza por corriente eléctrica, el calentamiento por resistencia es útil para templar secciones localizadas de algunas piezas forjadas y de fundición, pero en general su principal aplicación es para calentar partes de sección transversal uniforme. El proceso se usa para templar superficies de piezas cilíndricas, los muñones de apoyo de los cigüeñales aplicando una corriente de alta frecuencia a la sección de apoyo durante unos cuantos segundos y cuando se ha calentado el acero a la profundidad deseada, se rocía agua sobre la superficie calentada a través de orificios hechos, los bloques del inductor que rodea al apoyo.