
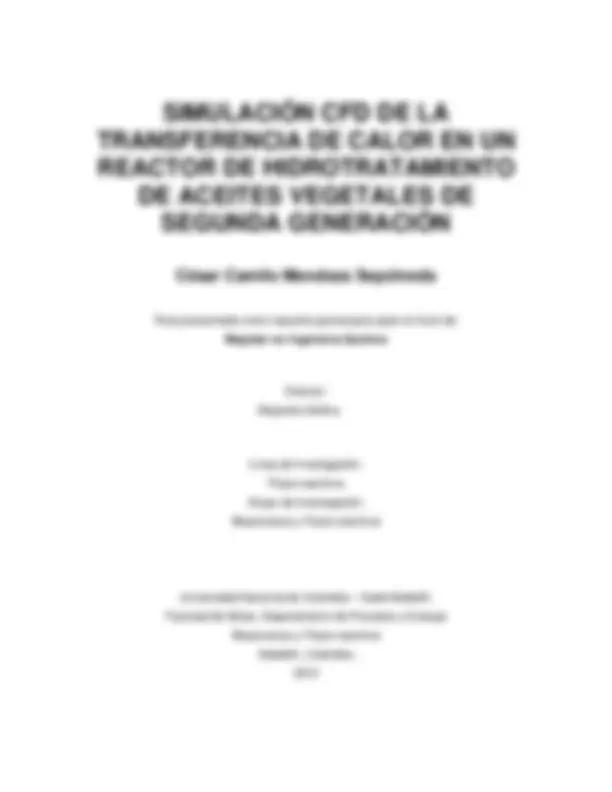
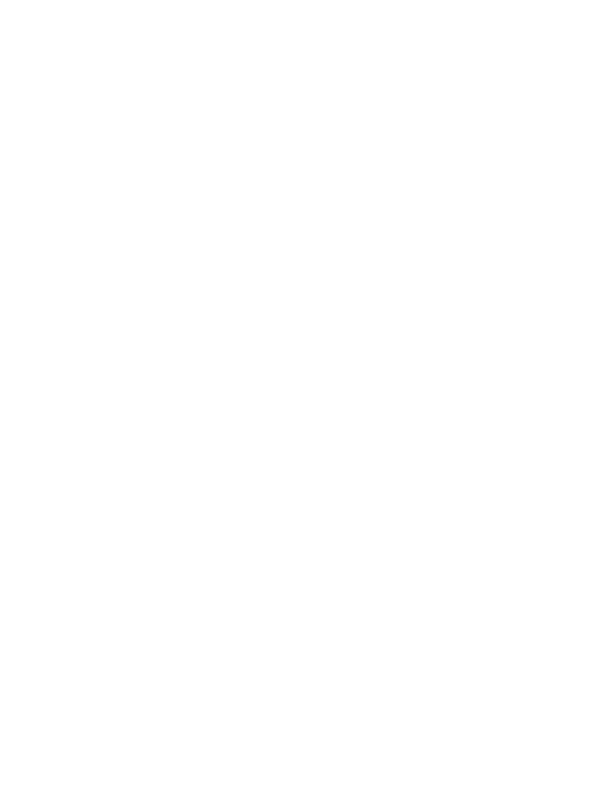
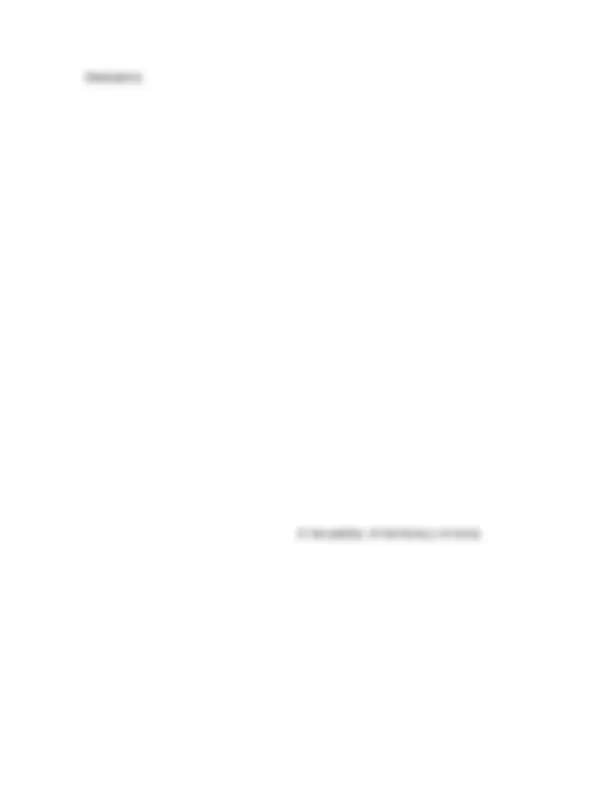
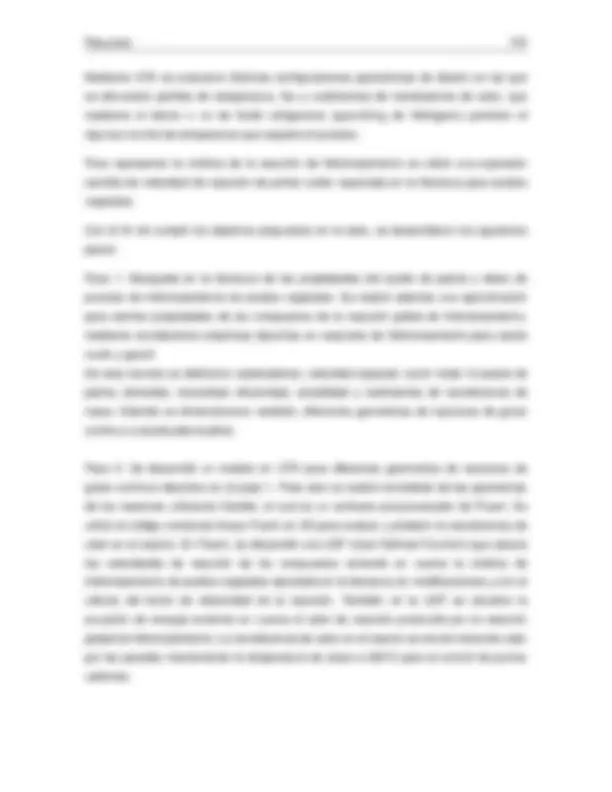
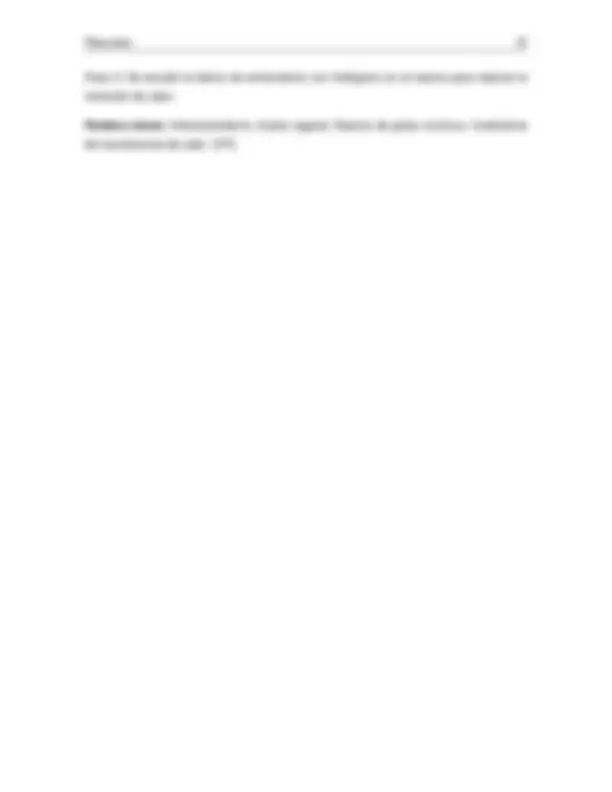
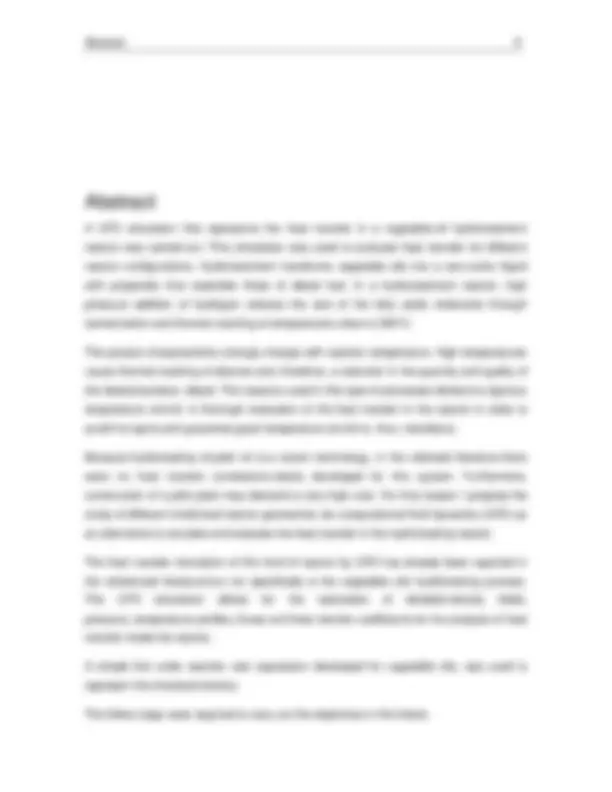
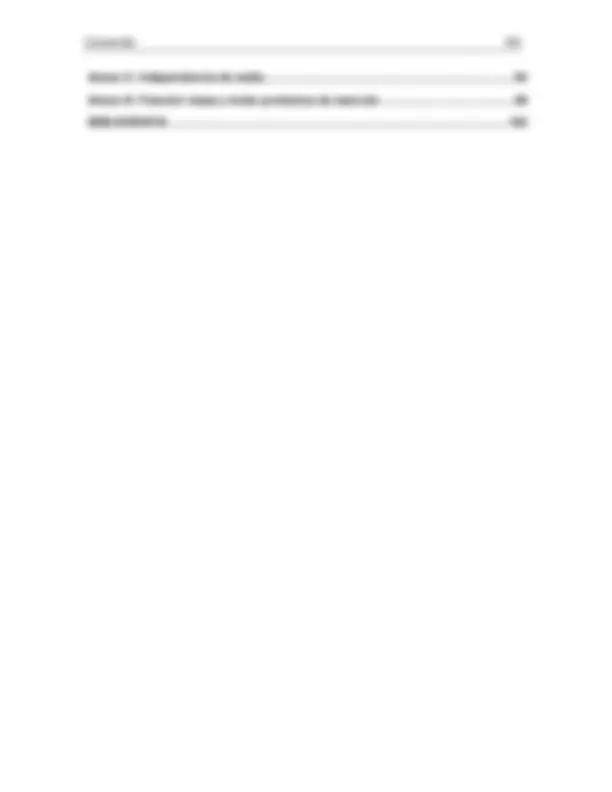
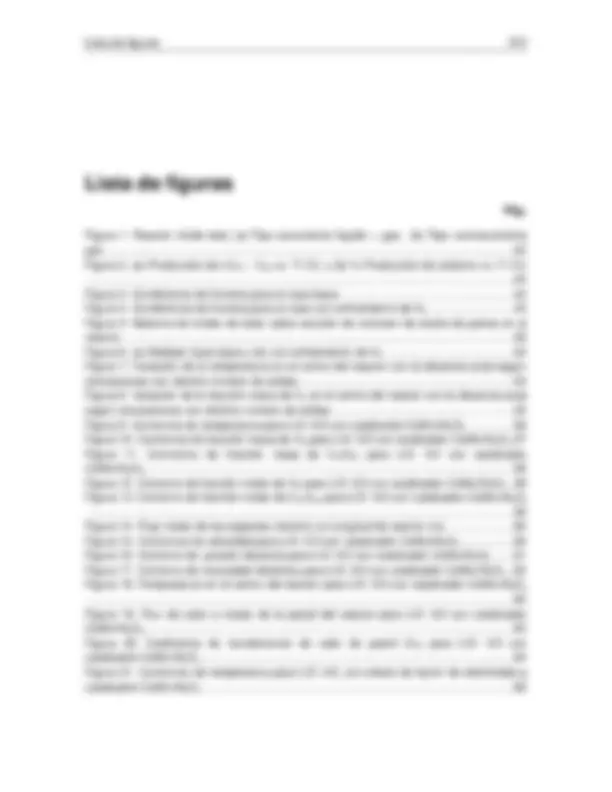
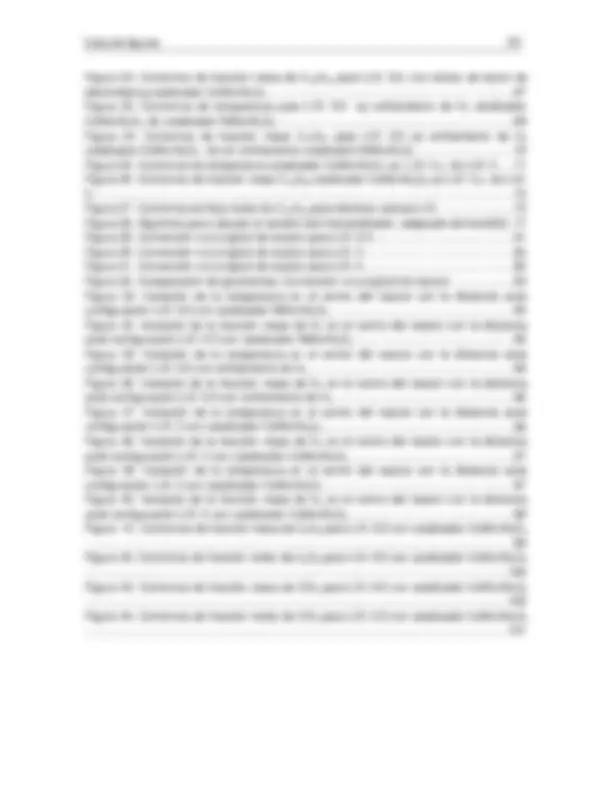
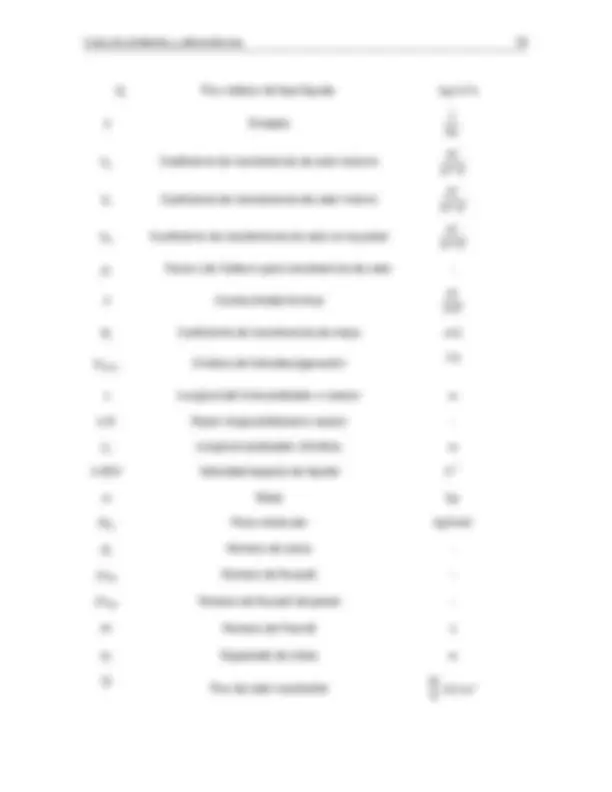
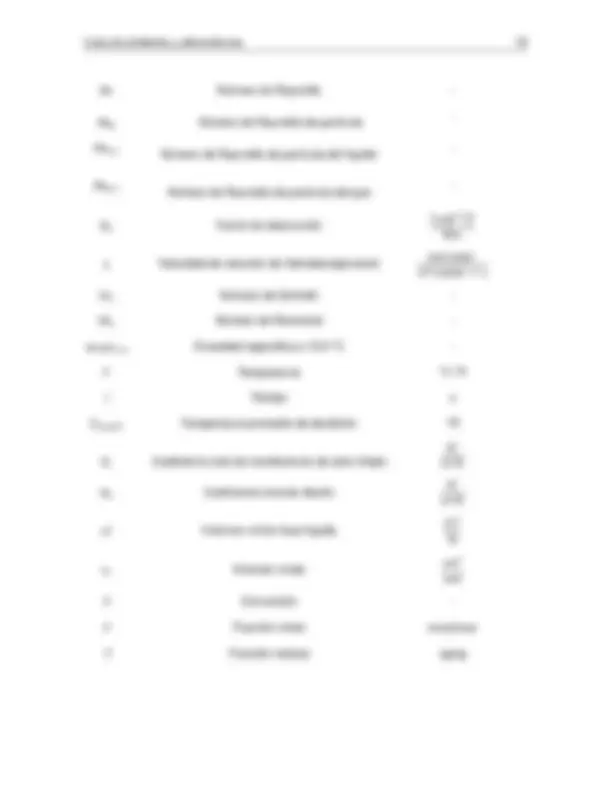
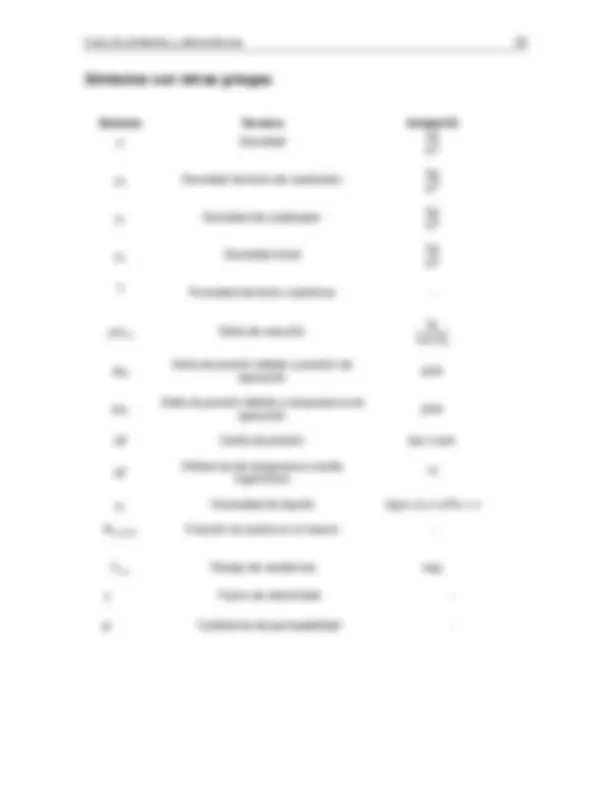
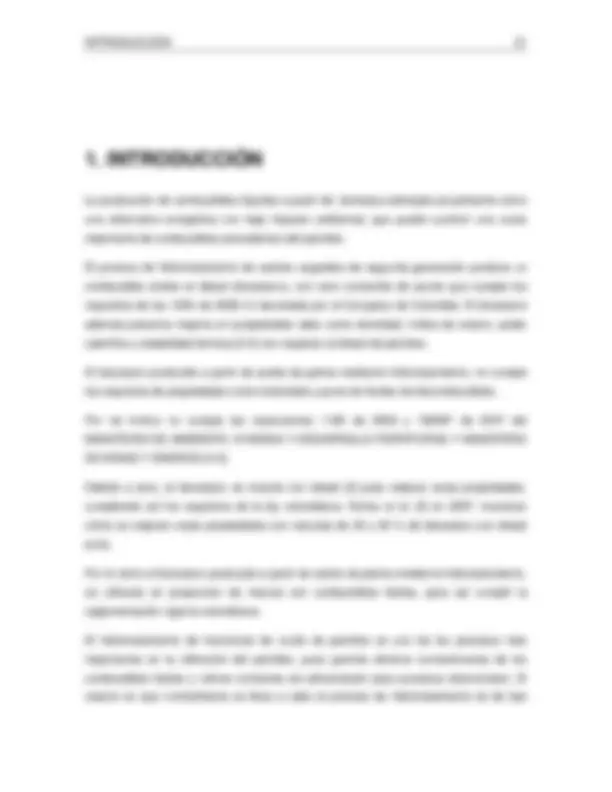
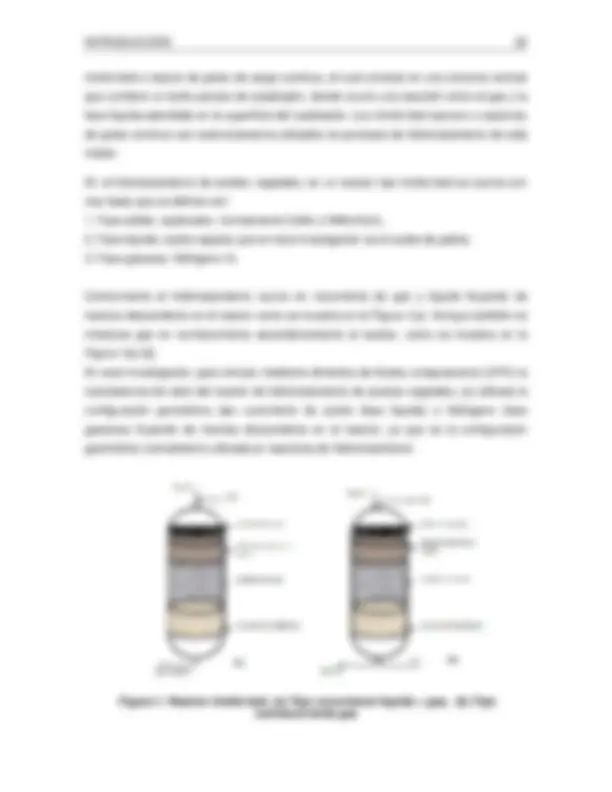
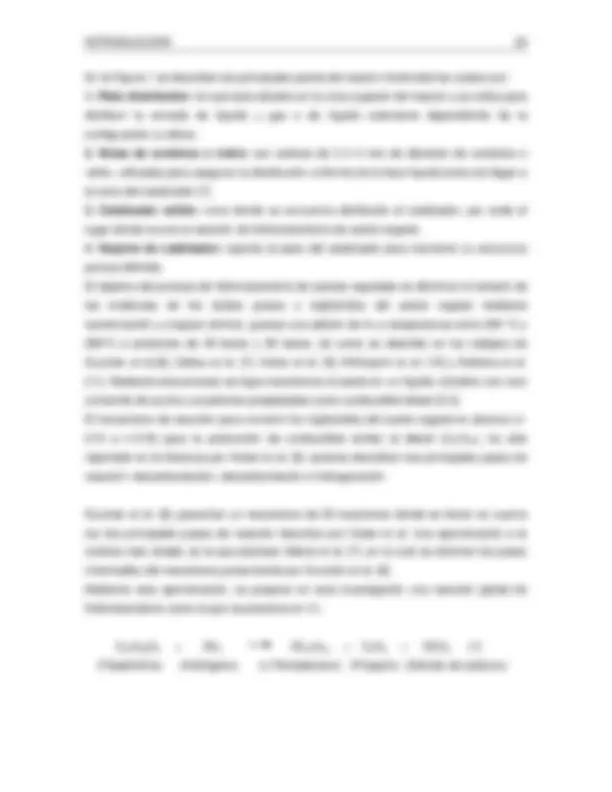
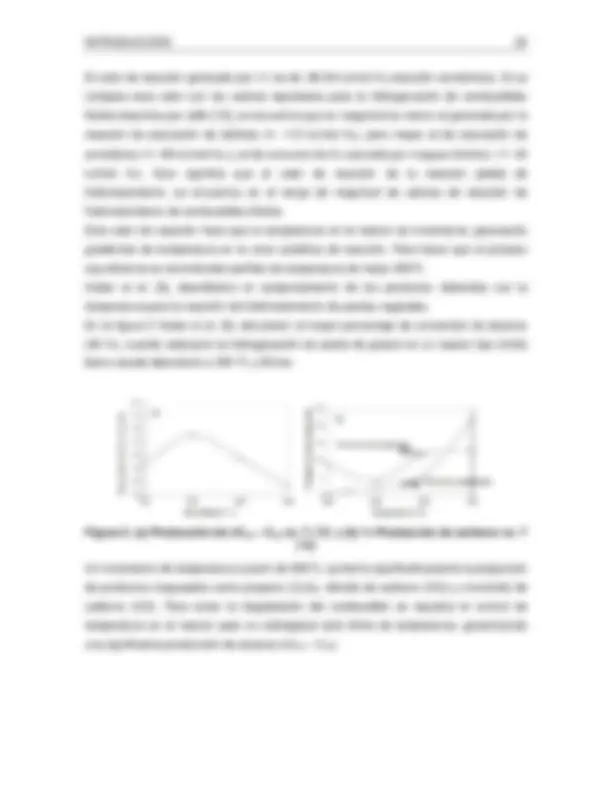
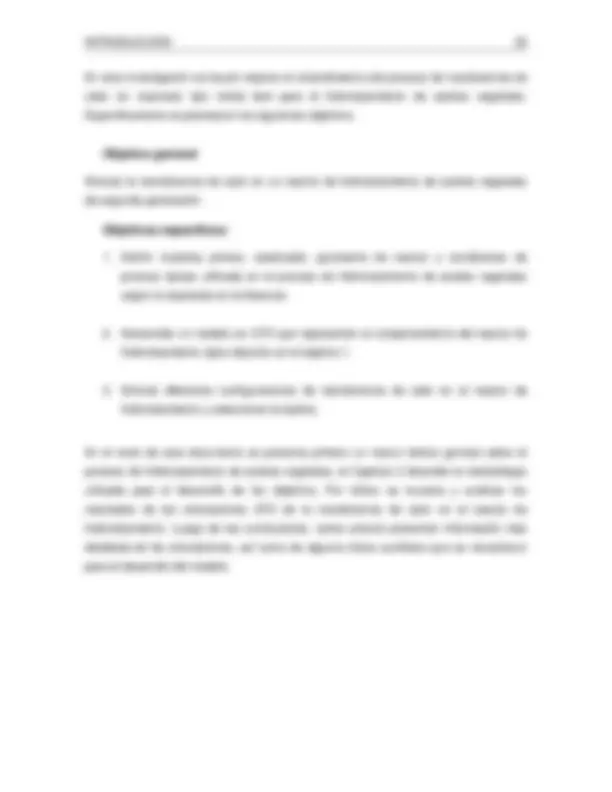
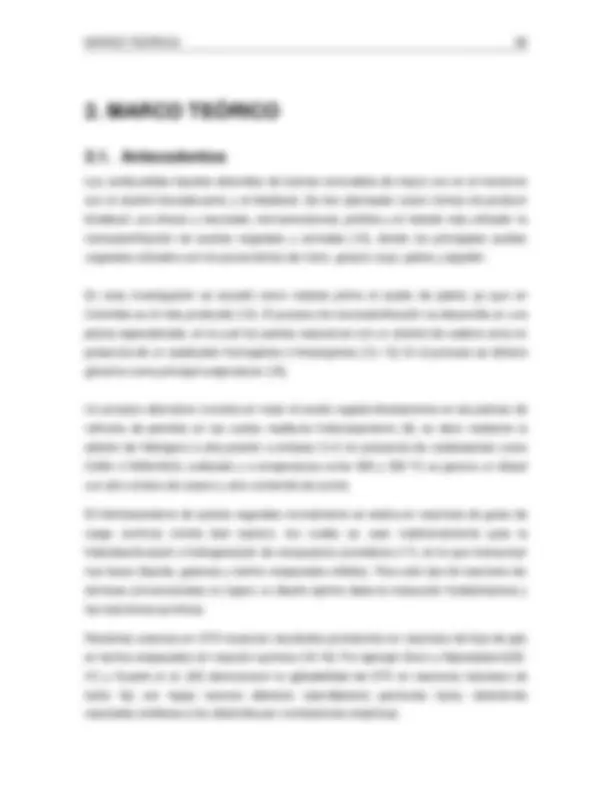
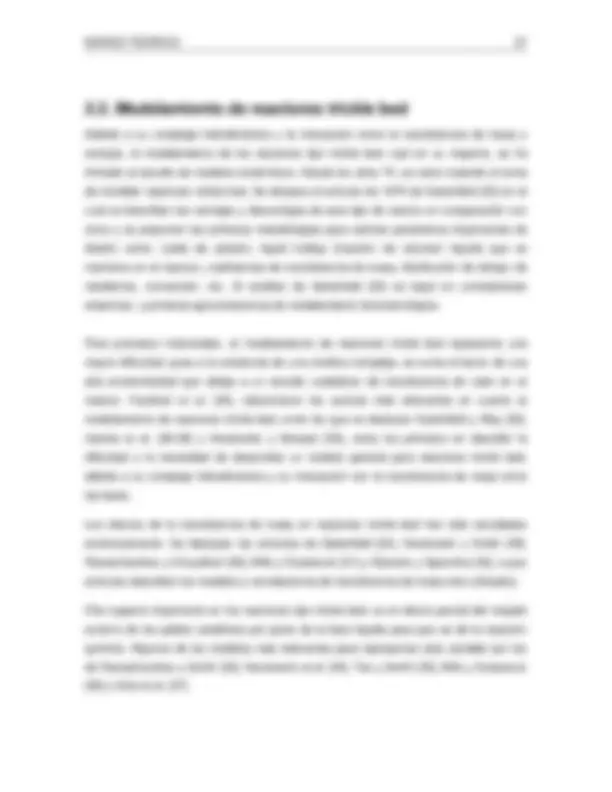
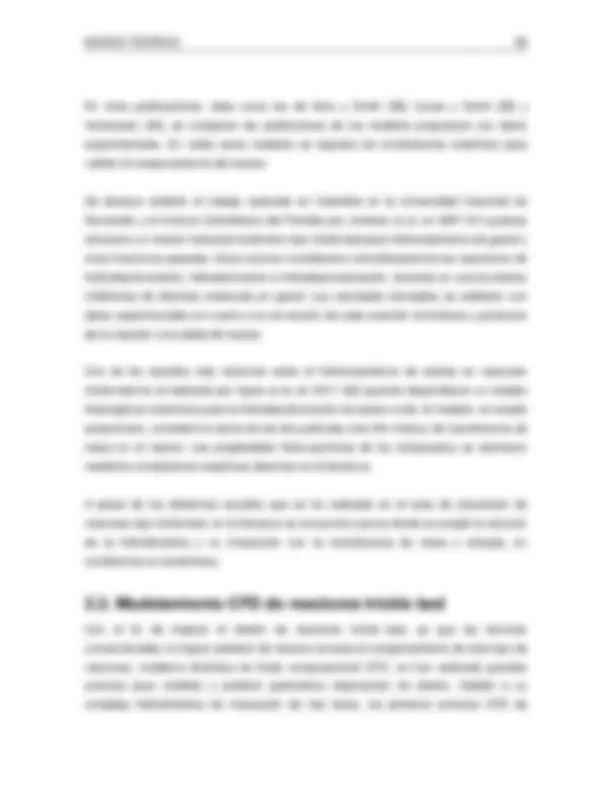
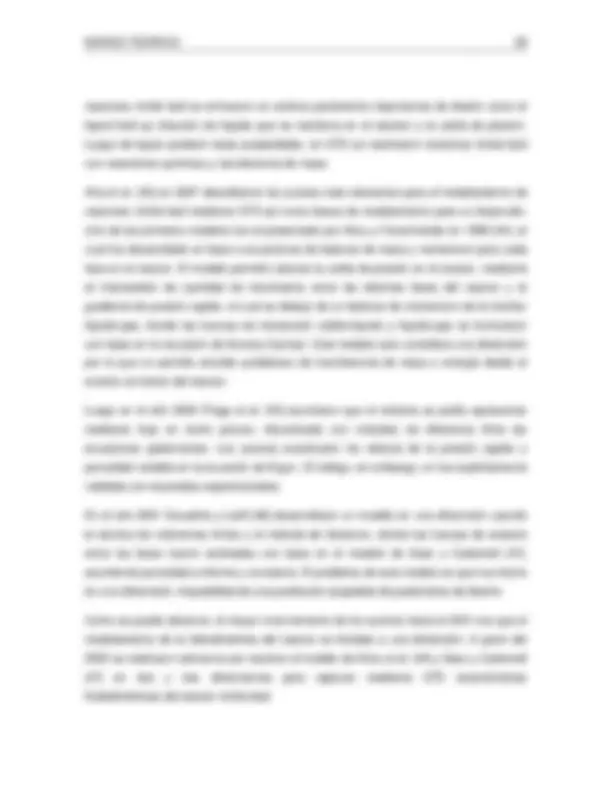
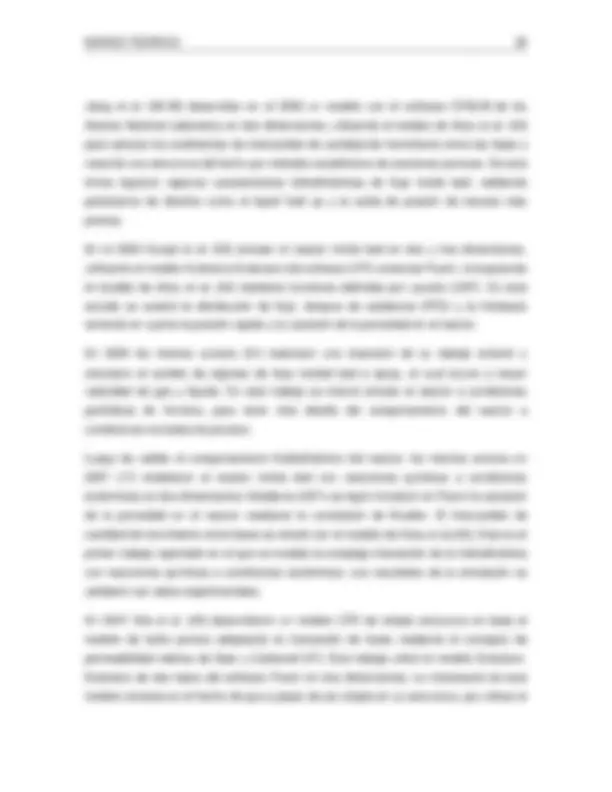
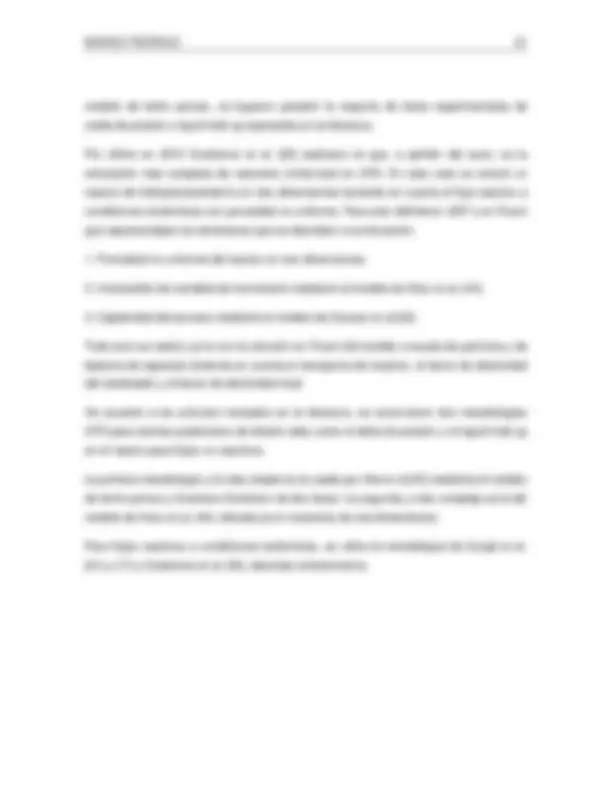
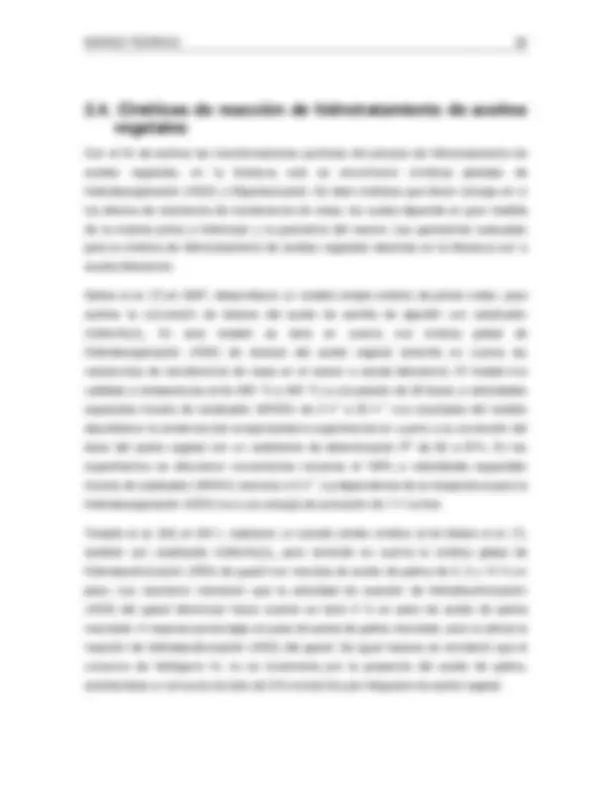
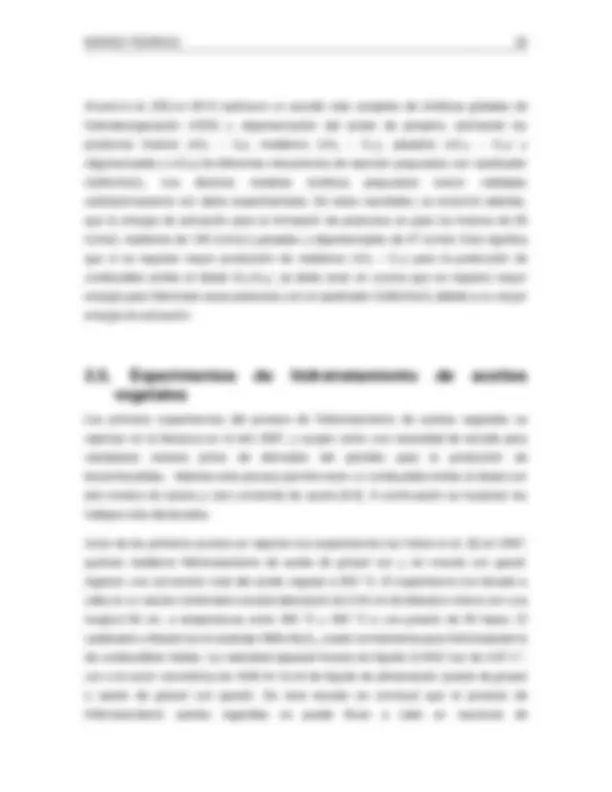
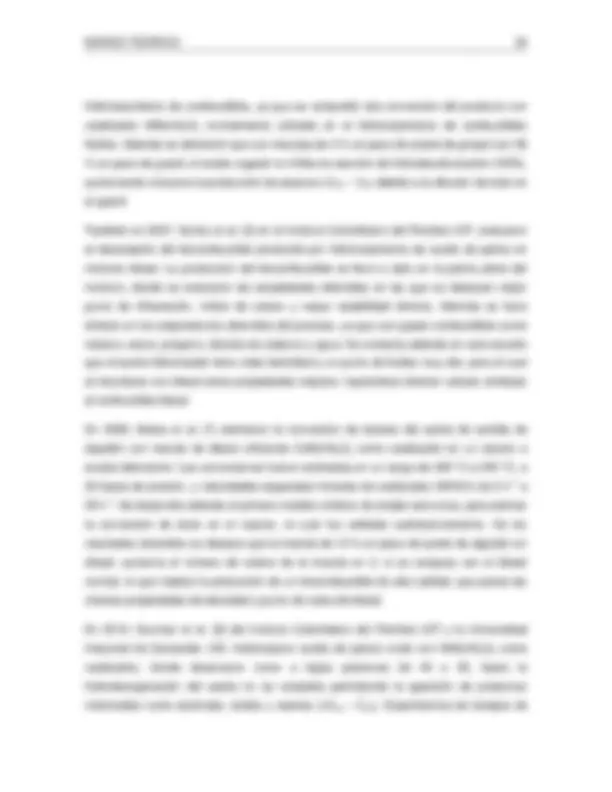
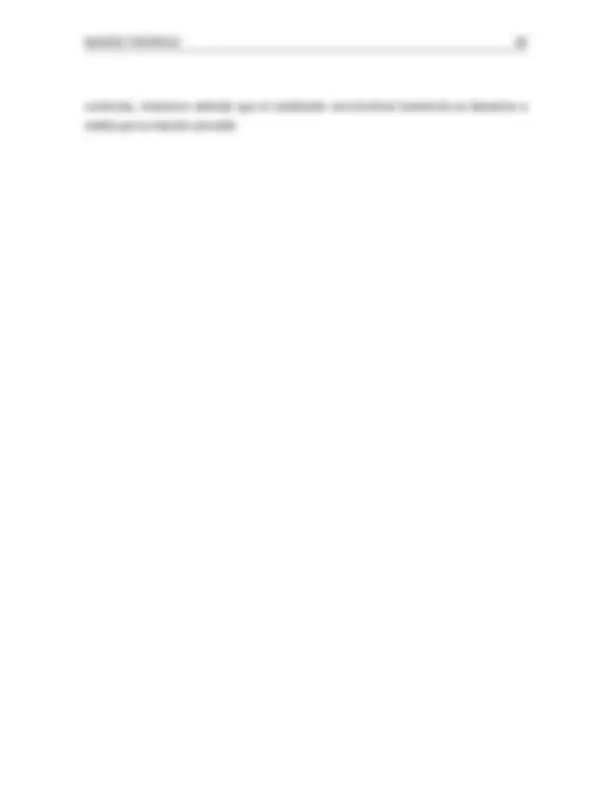
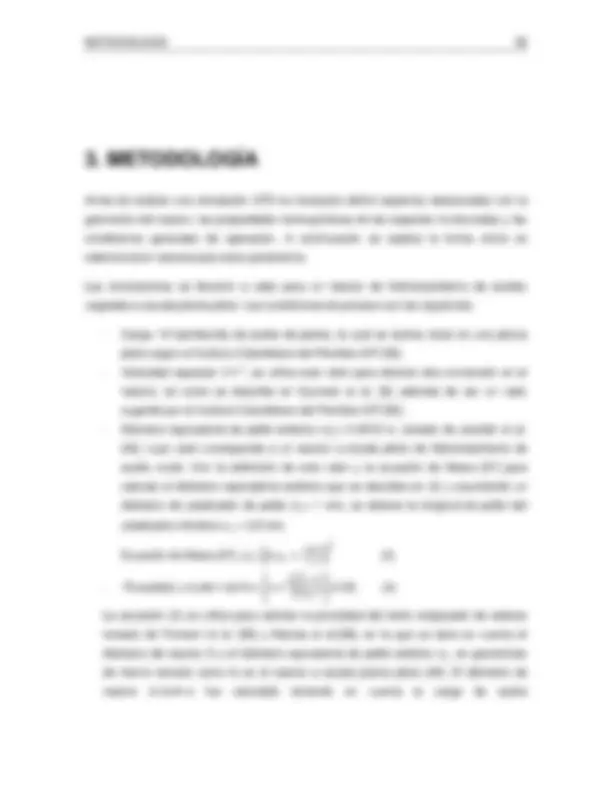
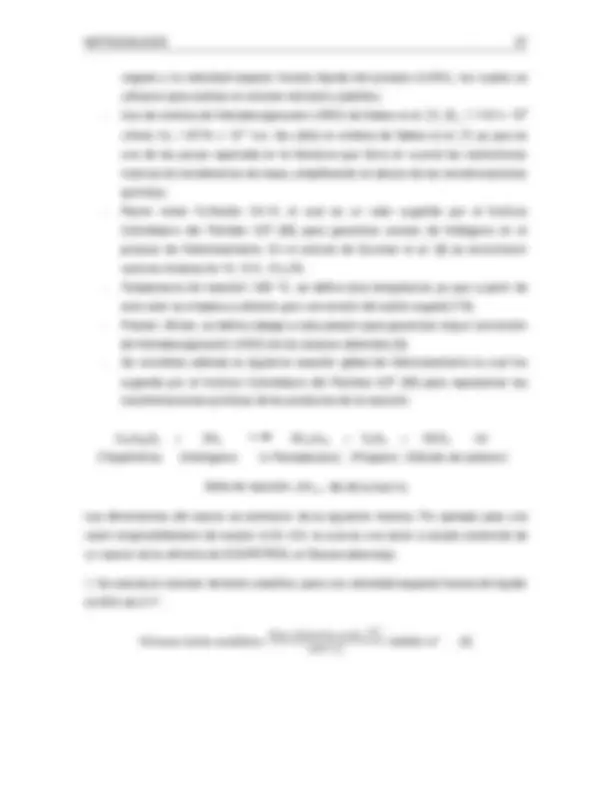
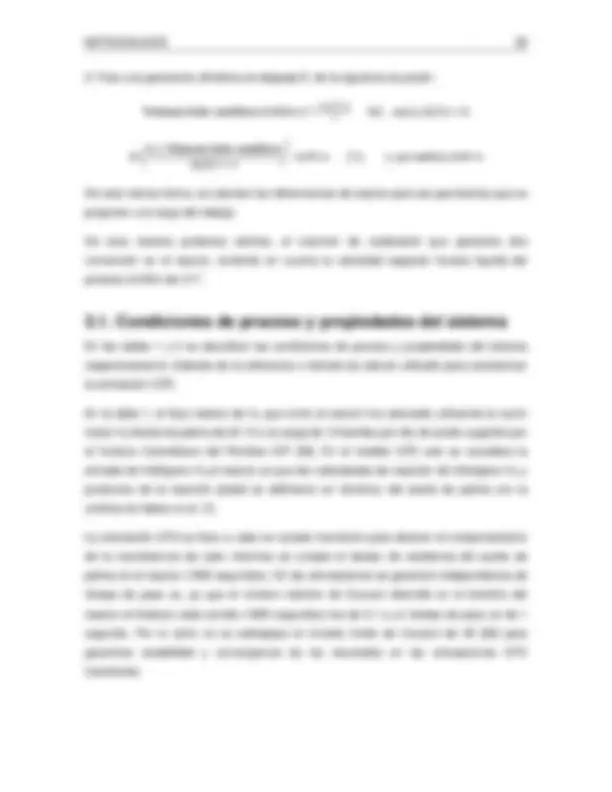
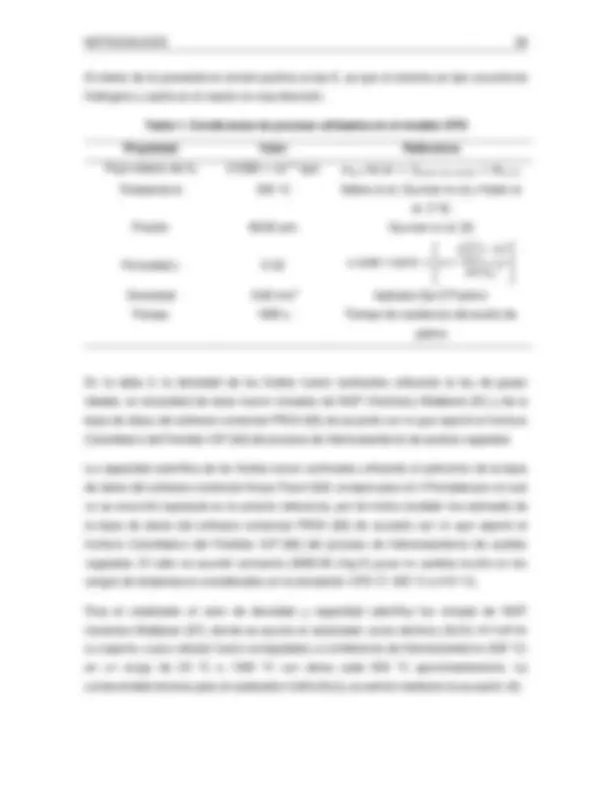
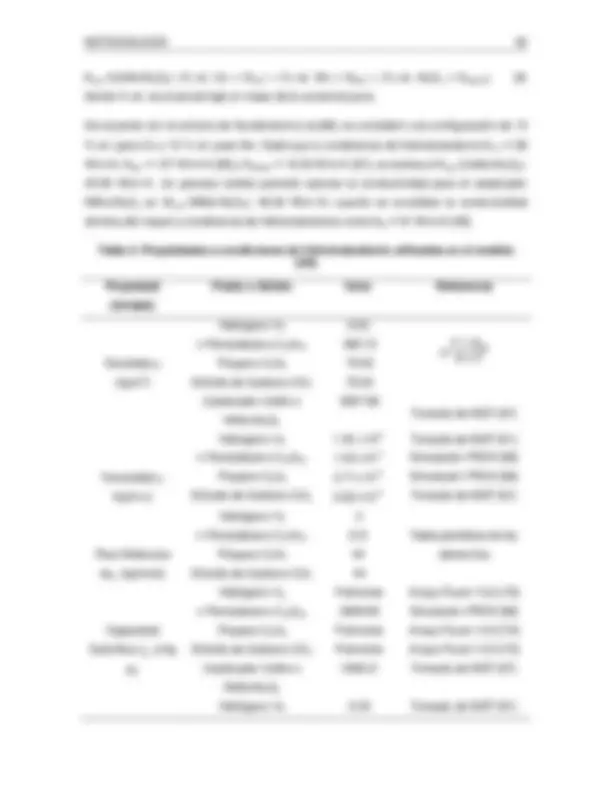
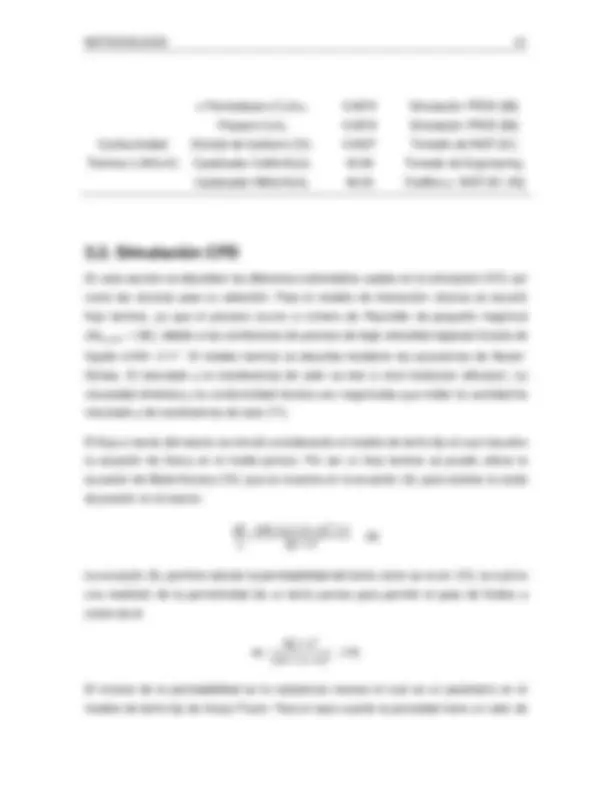
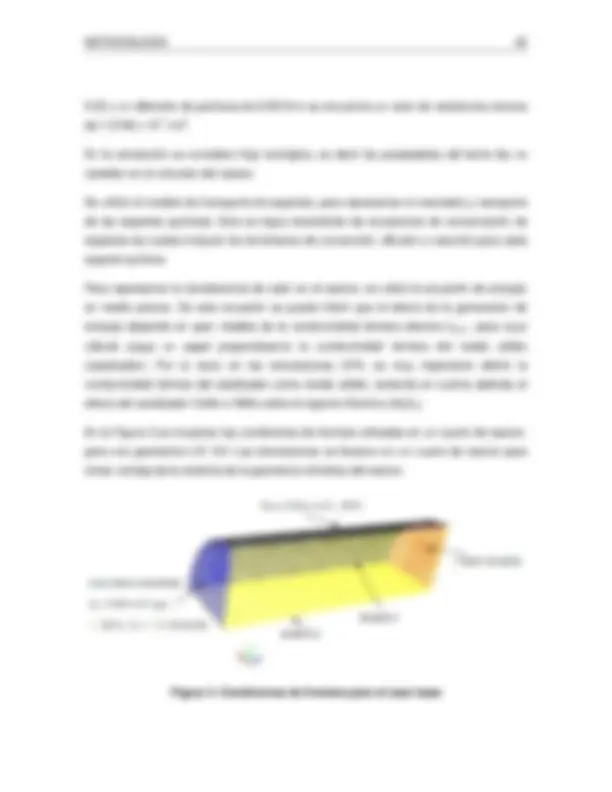
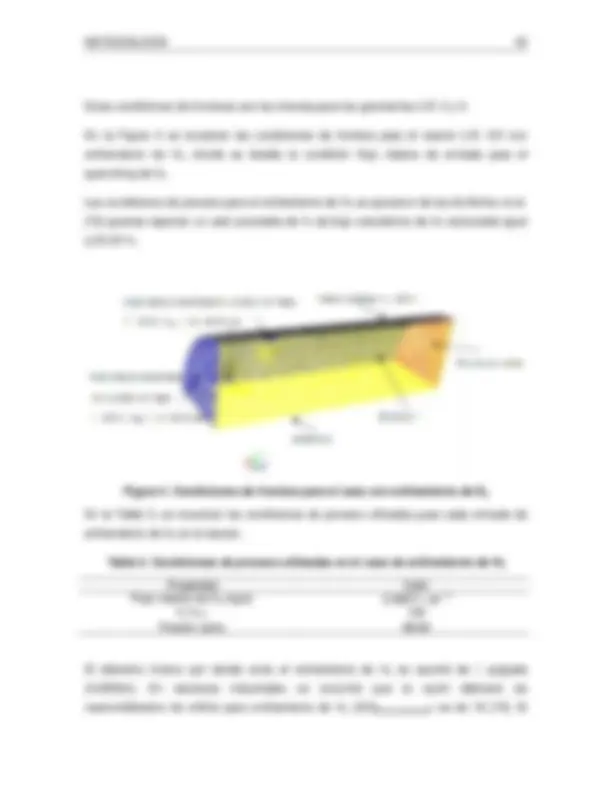
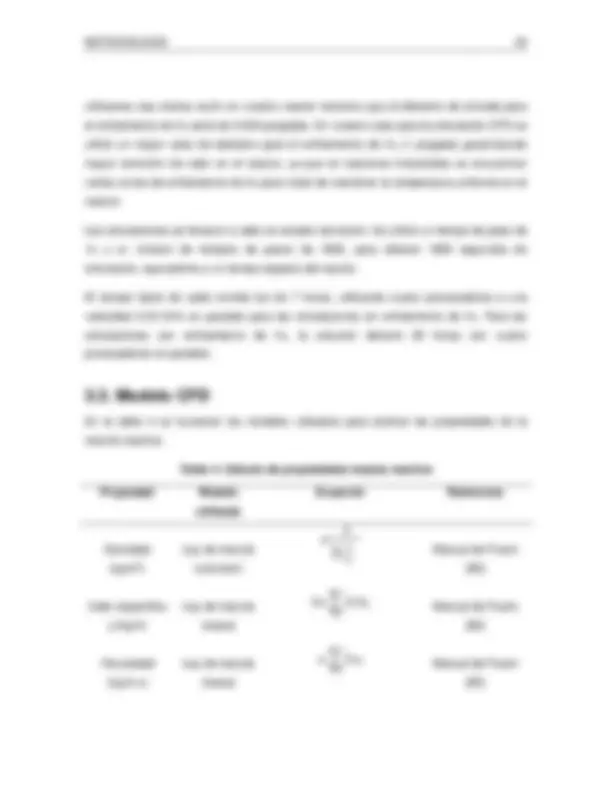
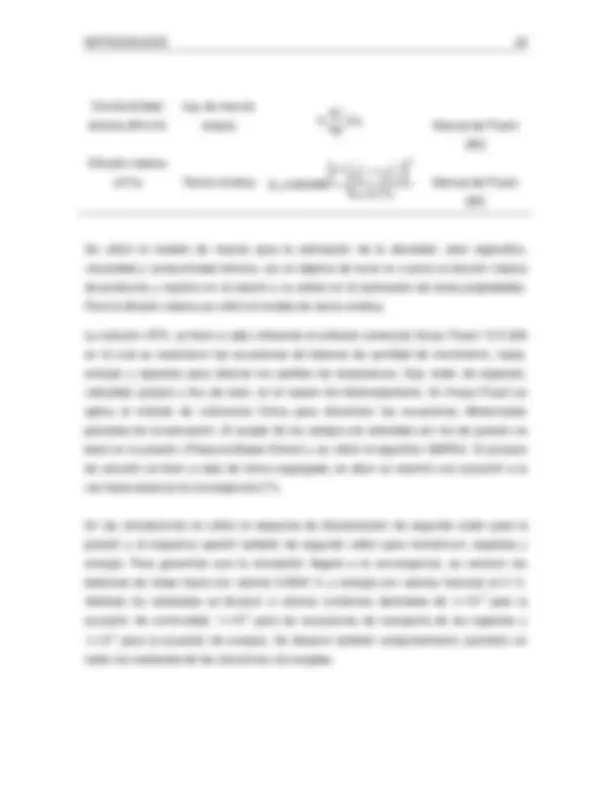
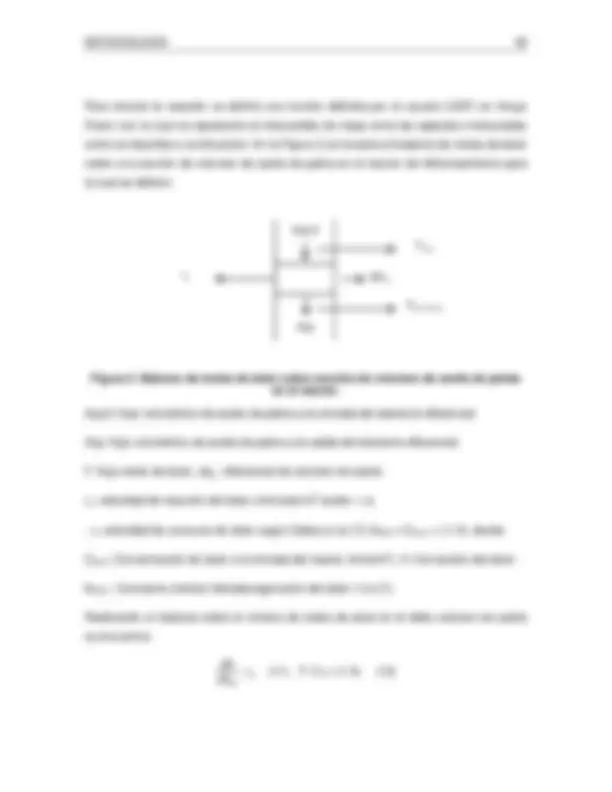
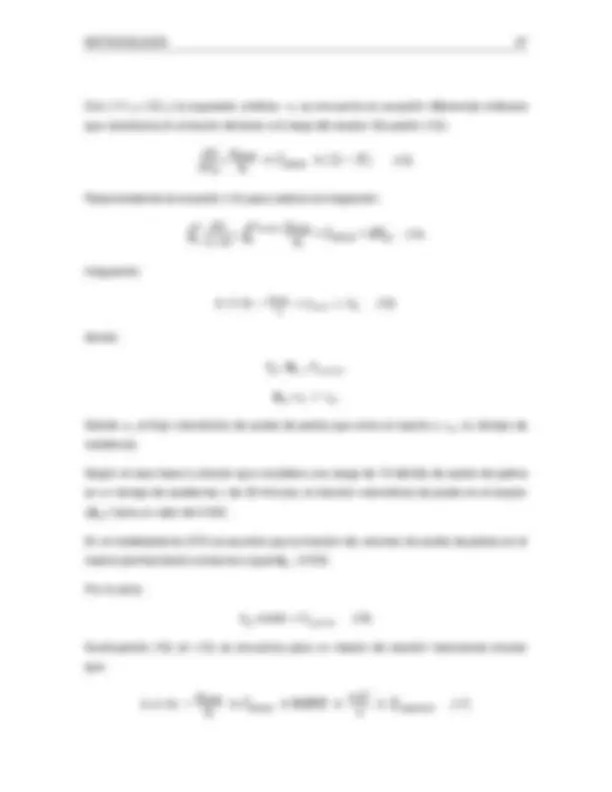
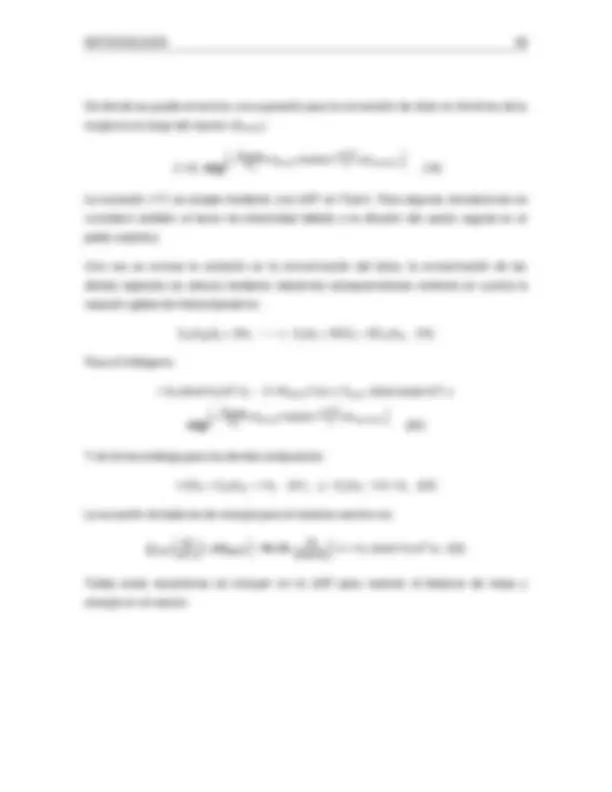
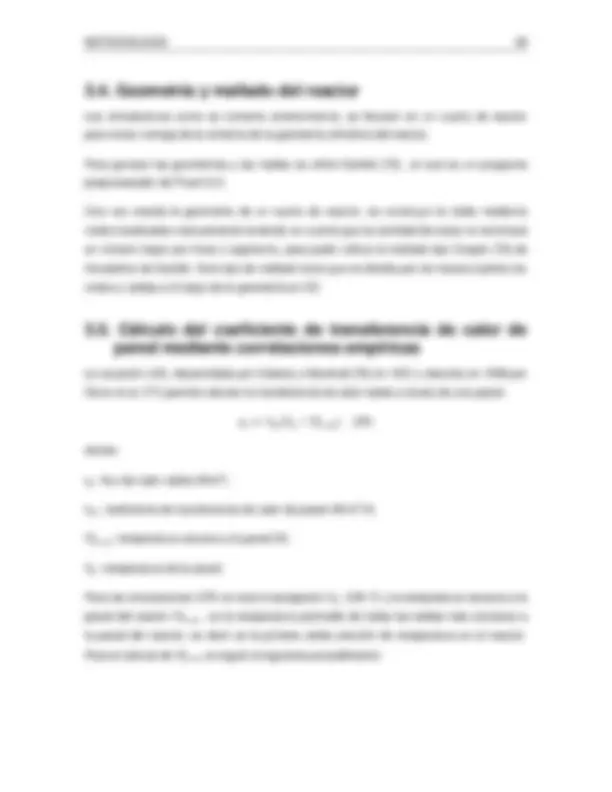
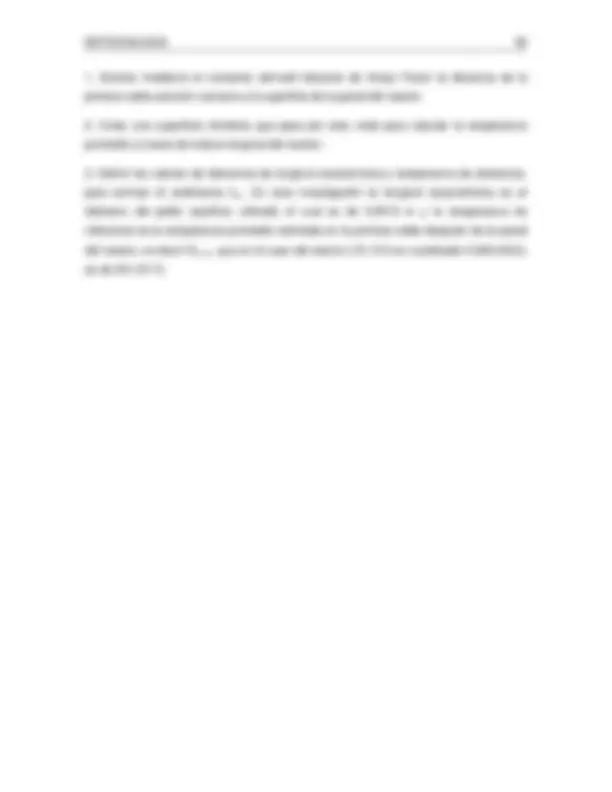
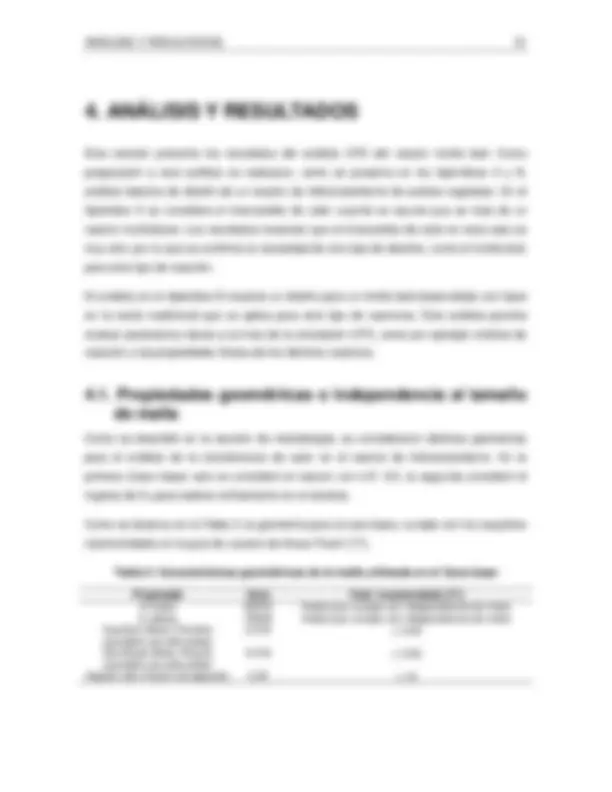
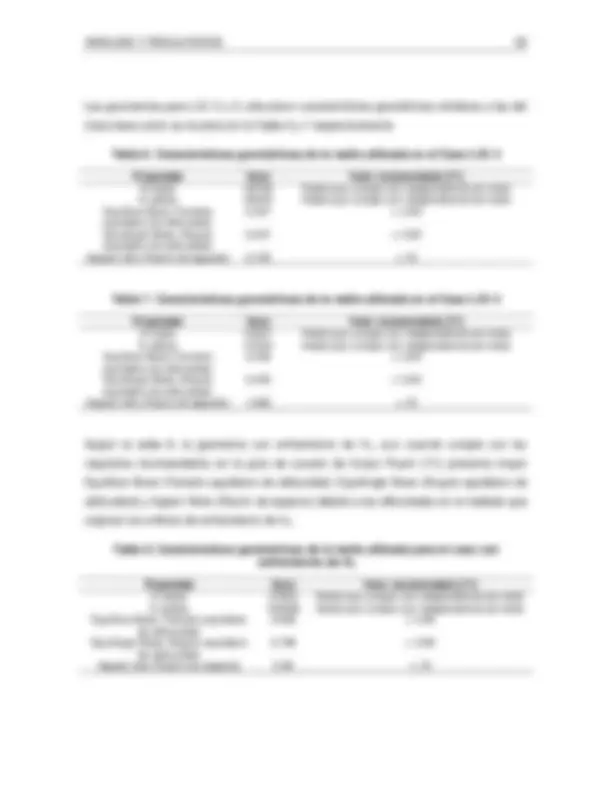
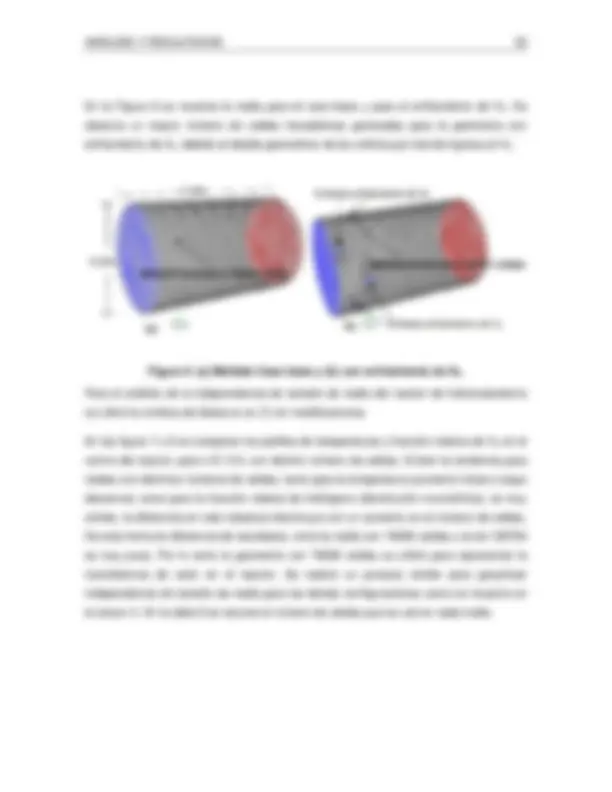
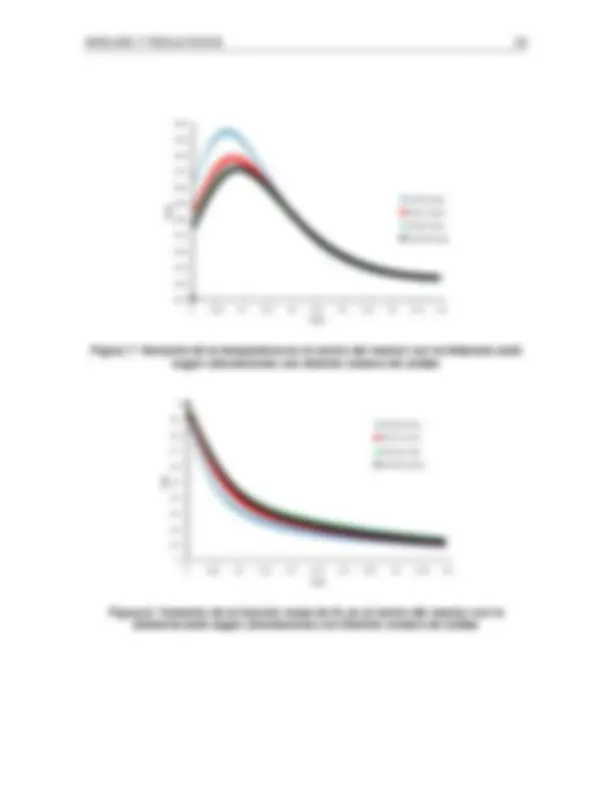
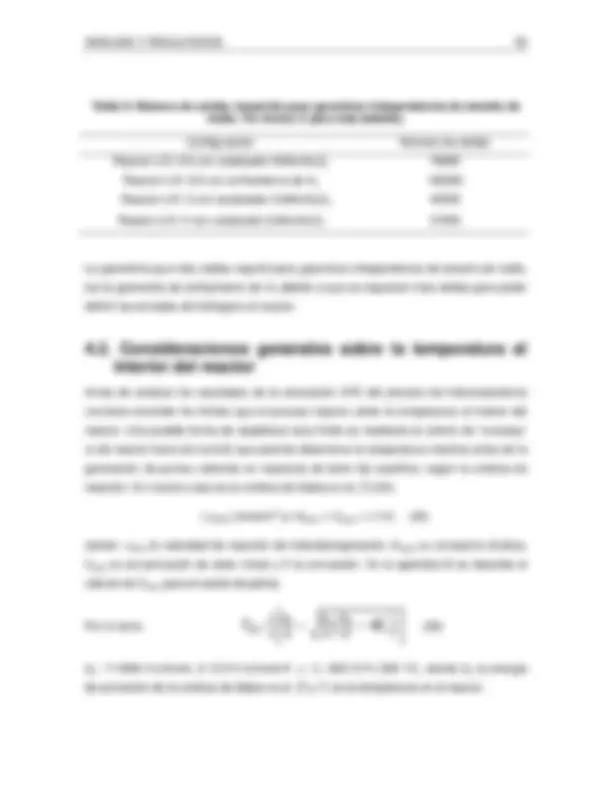

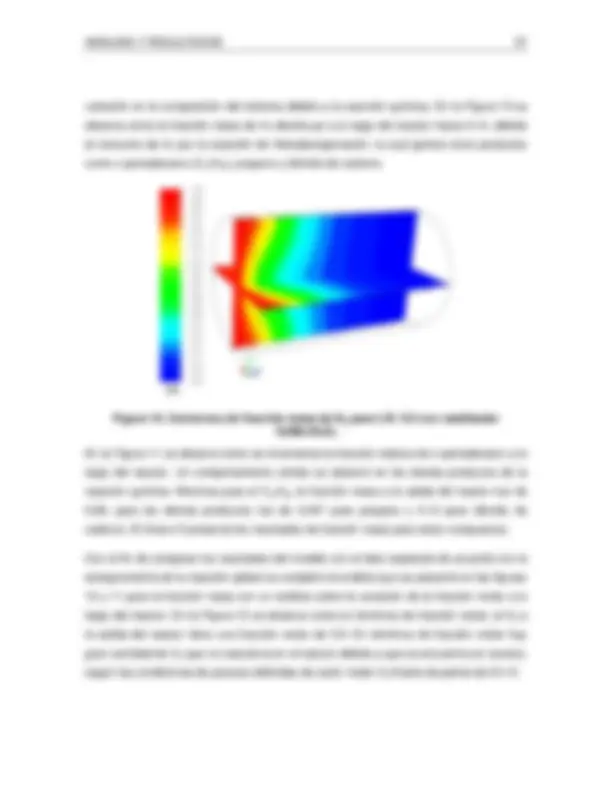
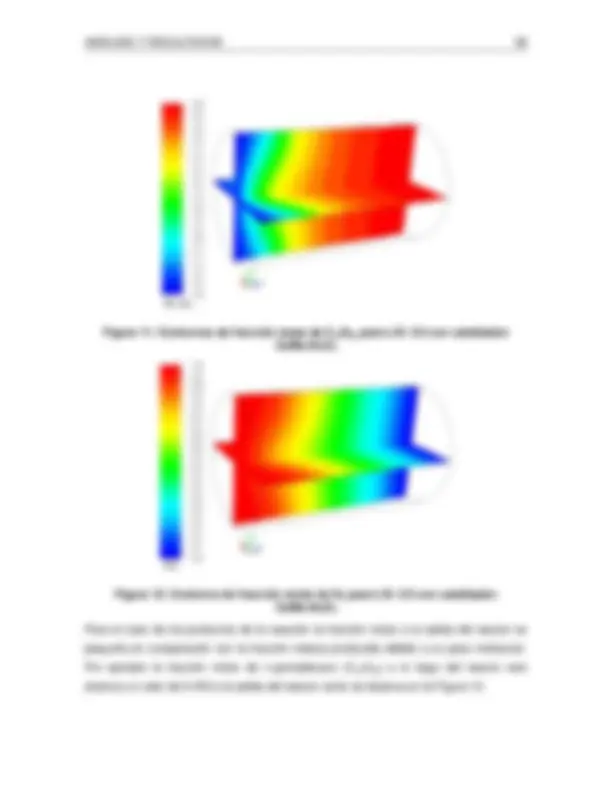
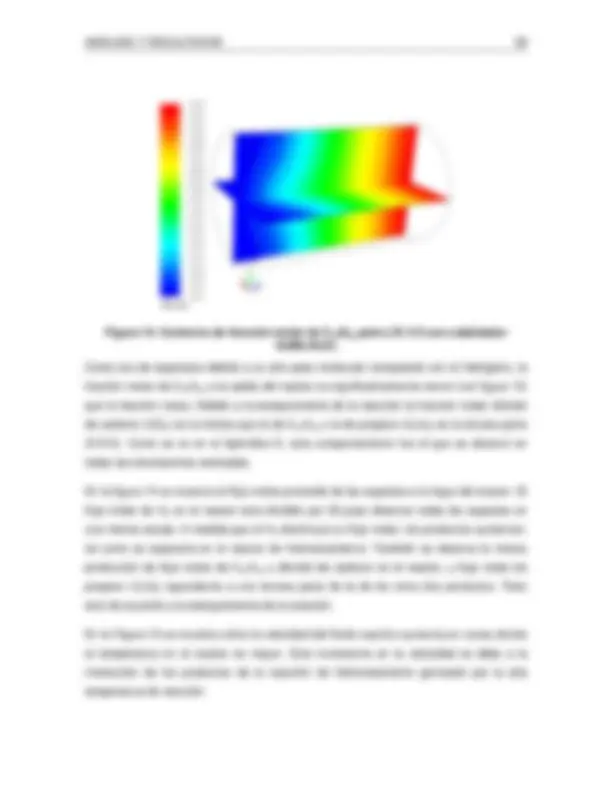
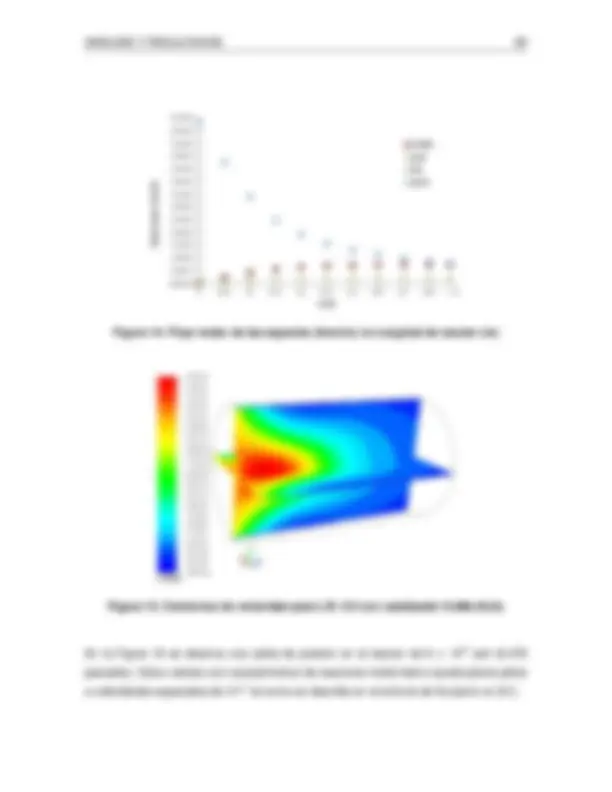
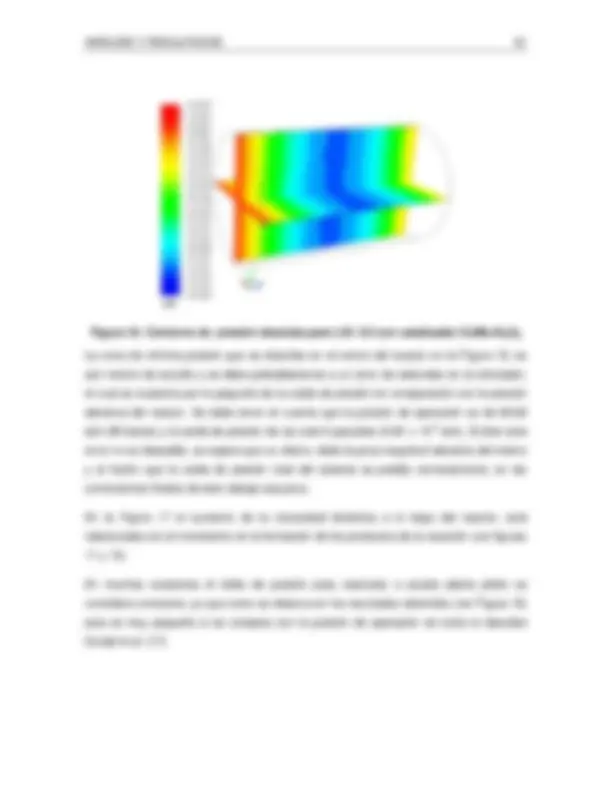
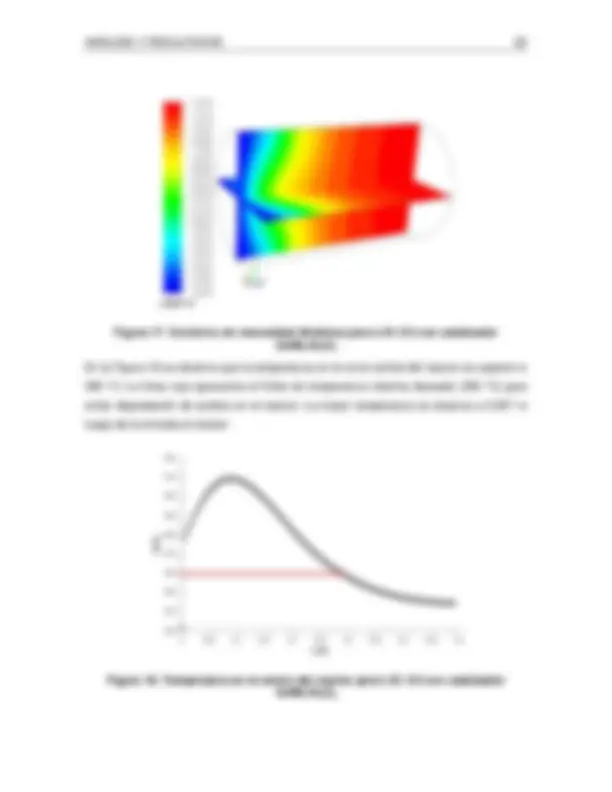
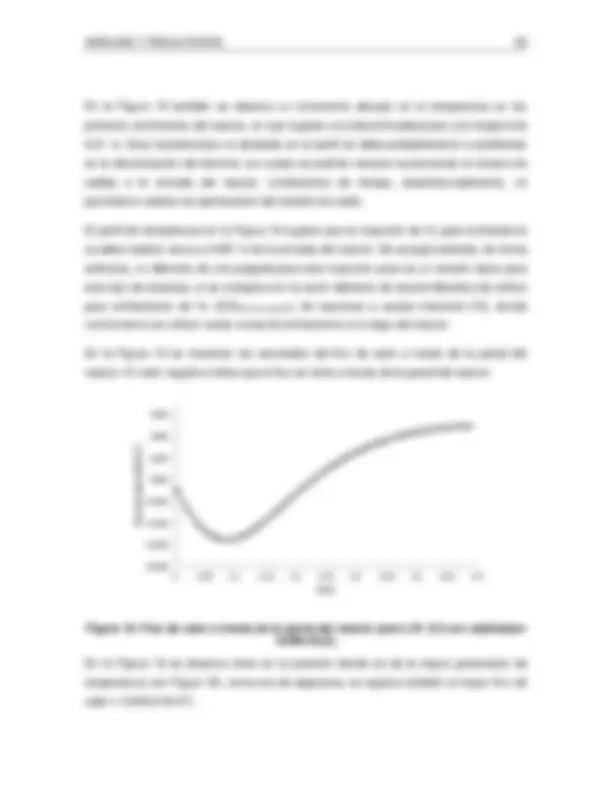
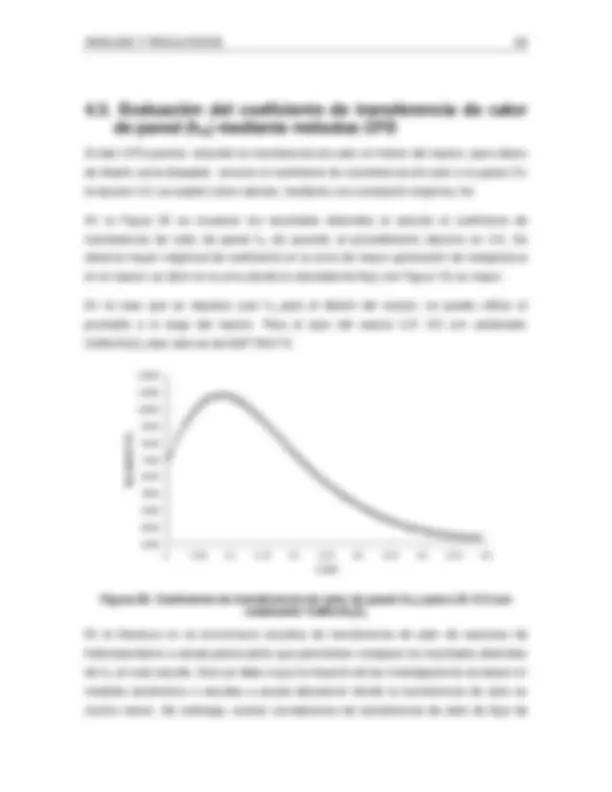
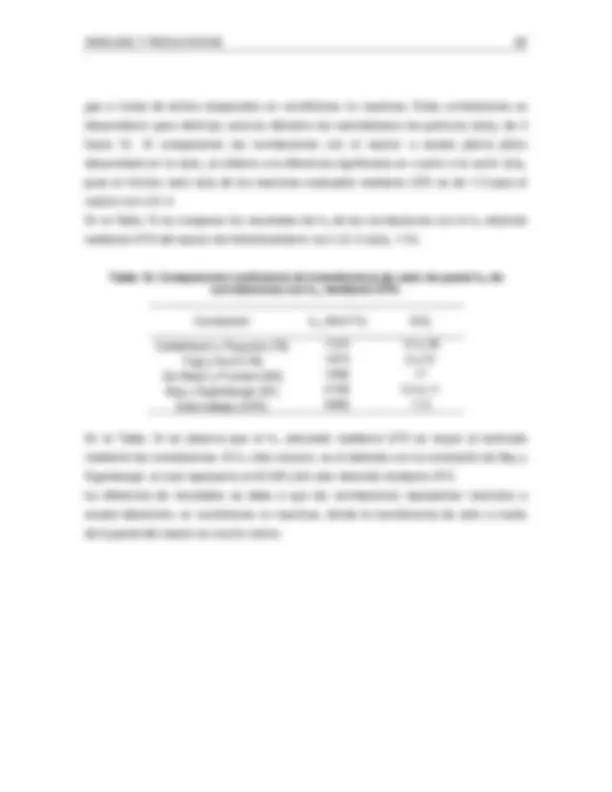
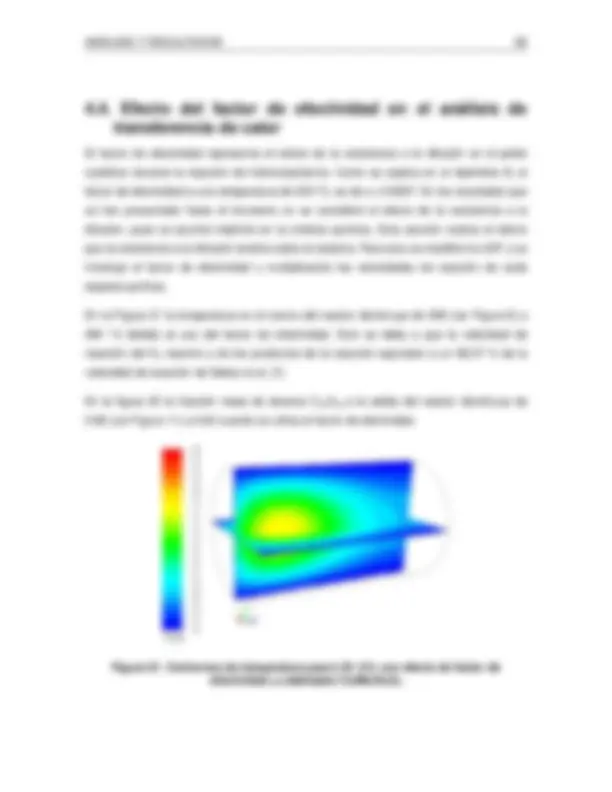
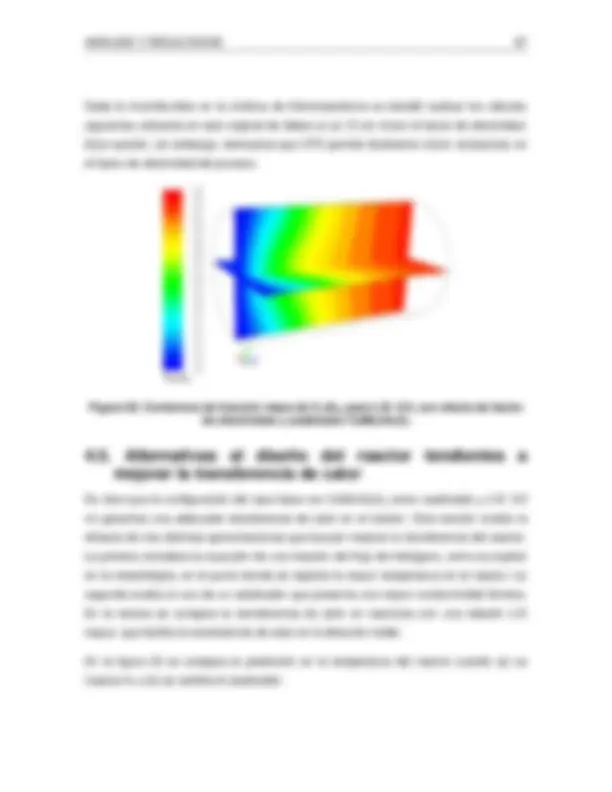
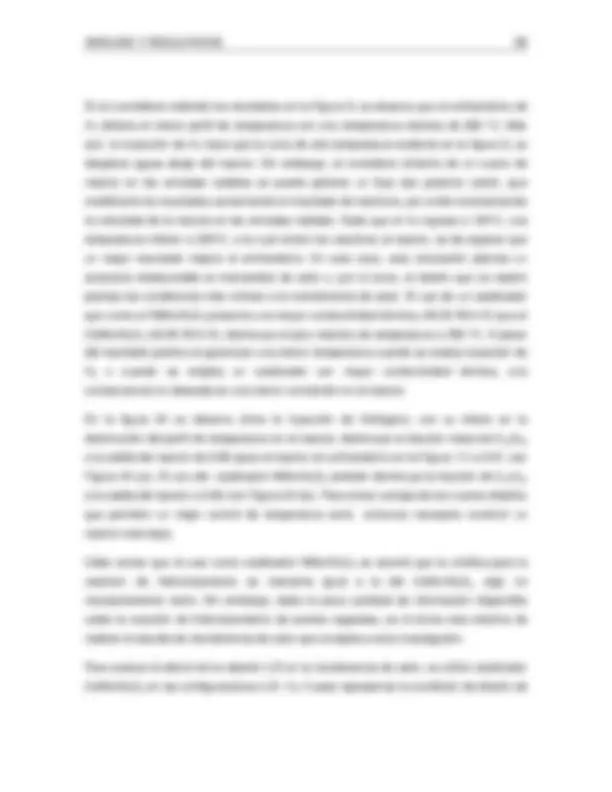
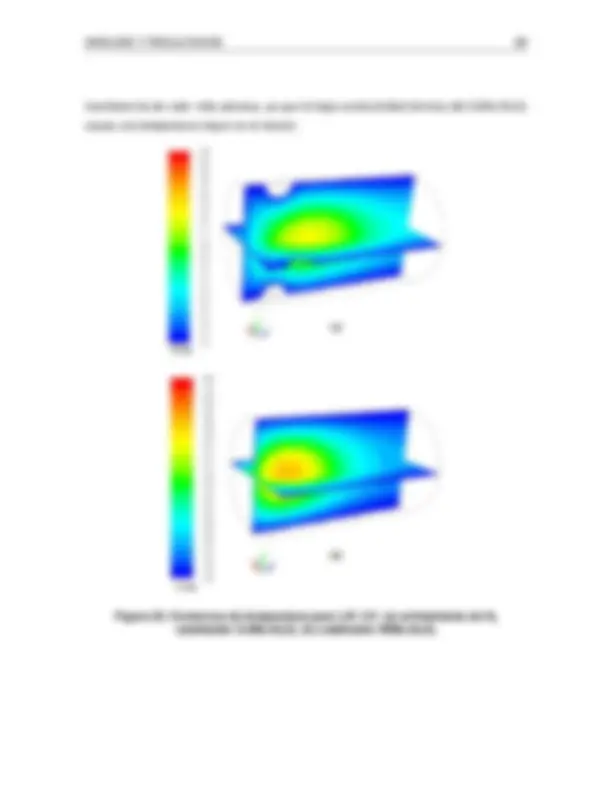
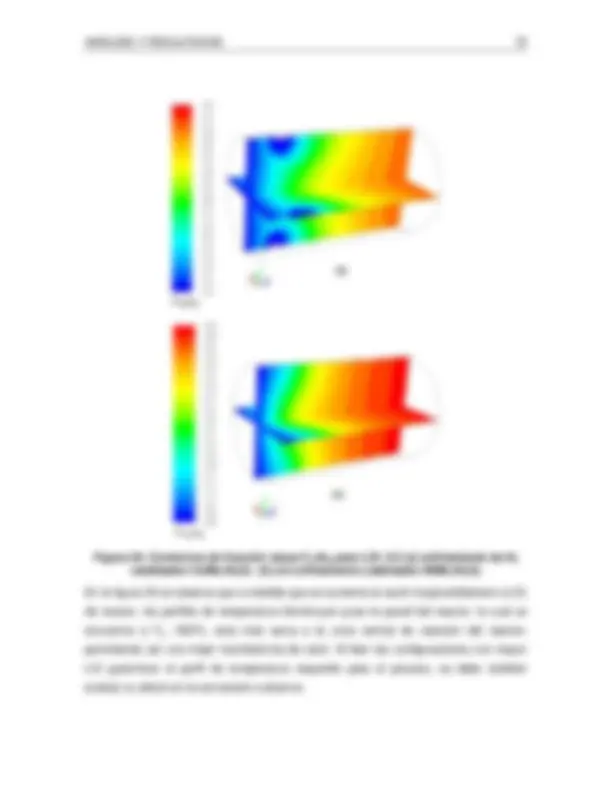
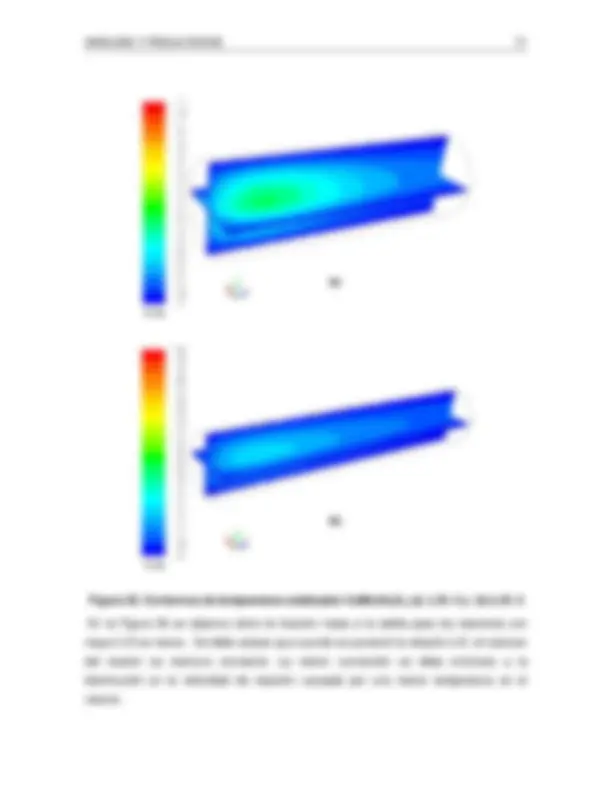
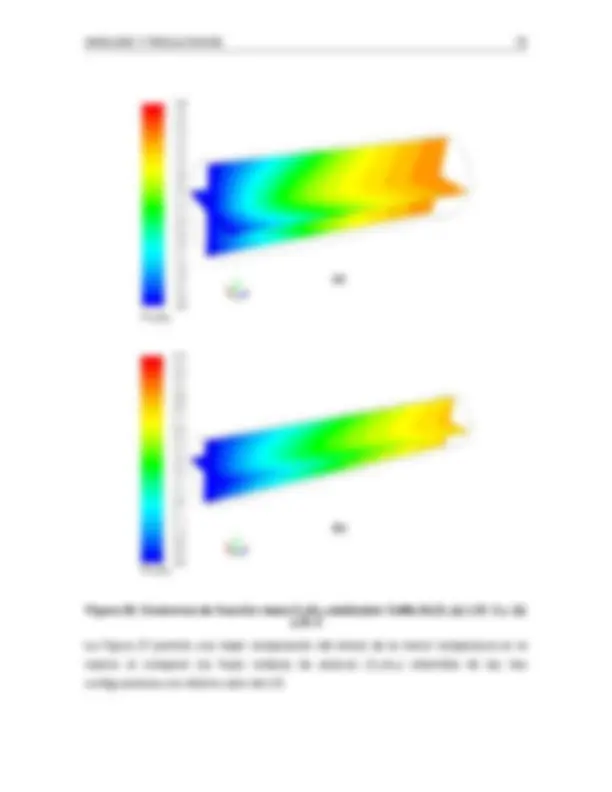
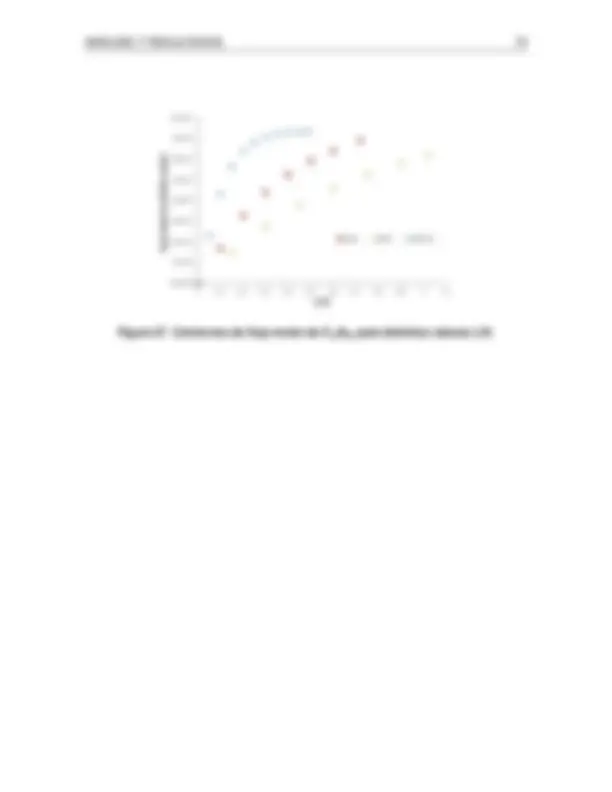
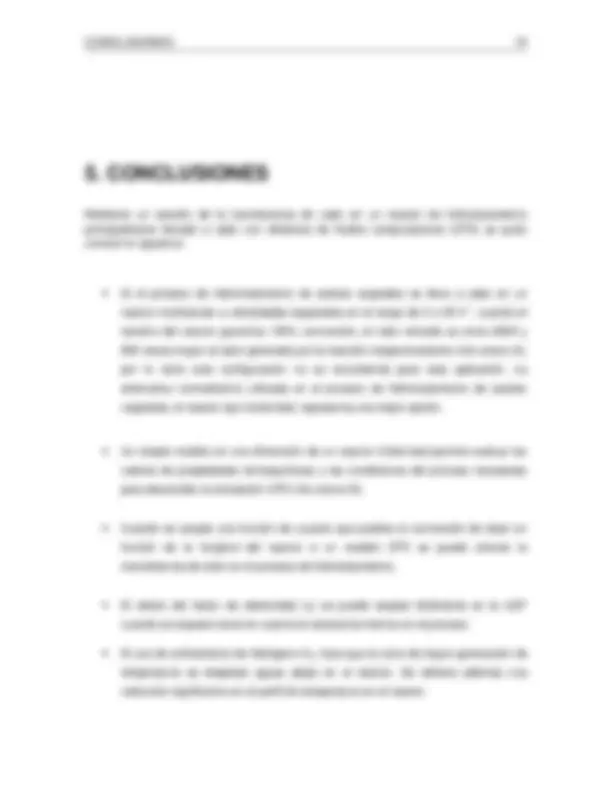
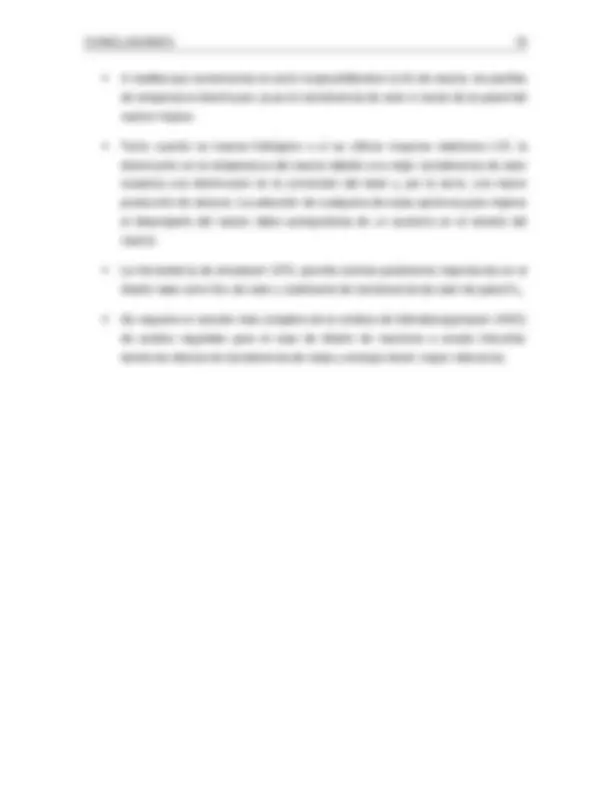
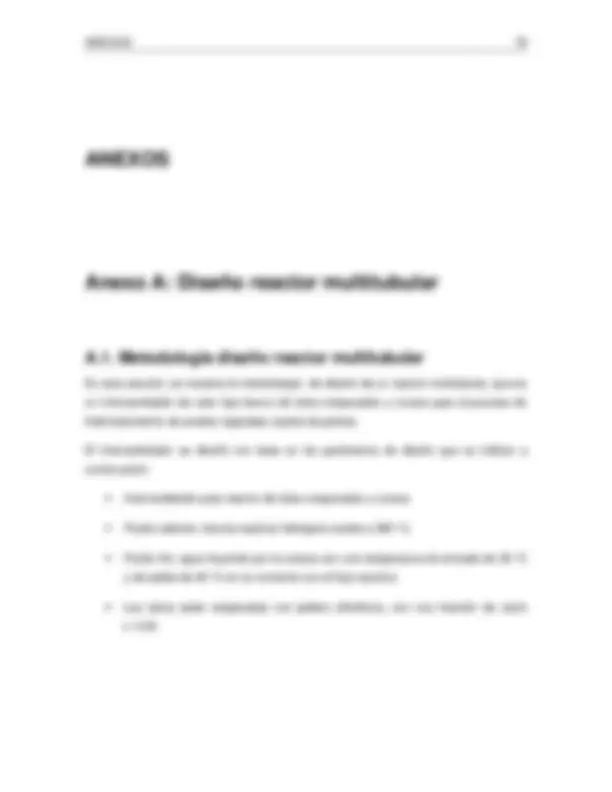
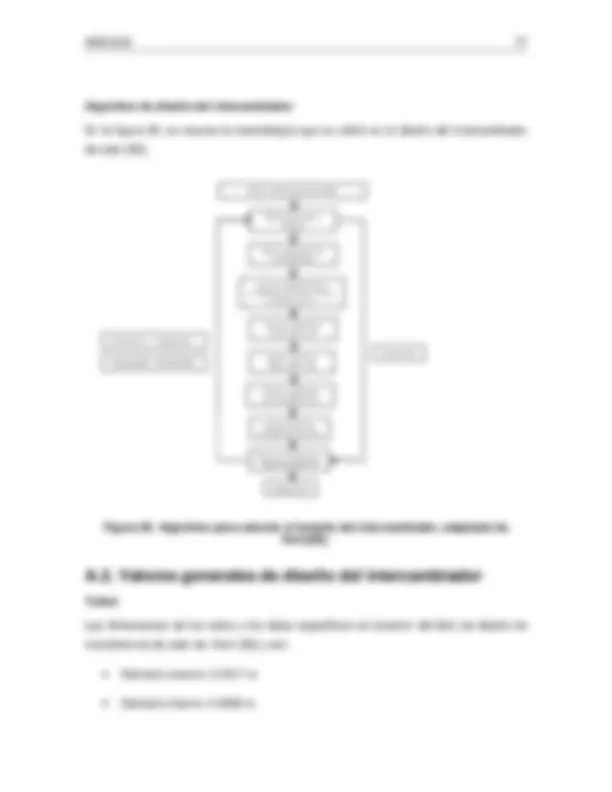
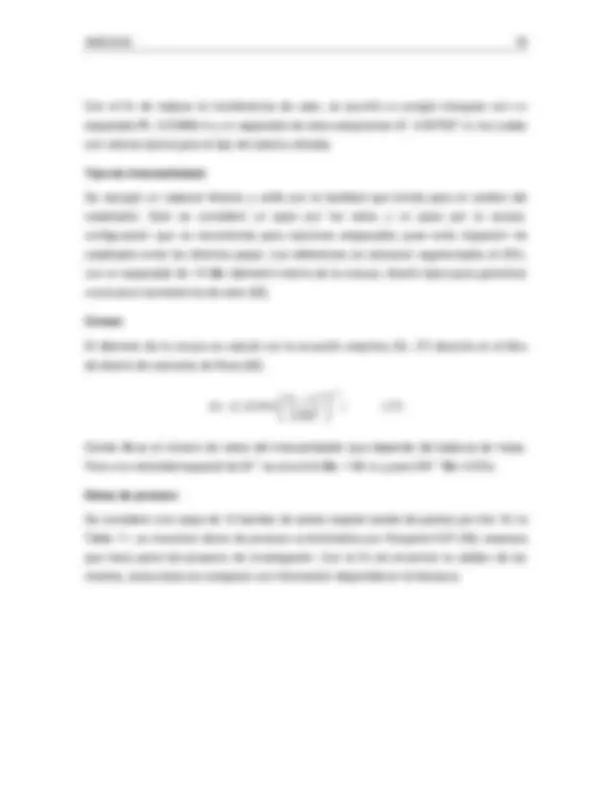
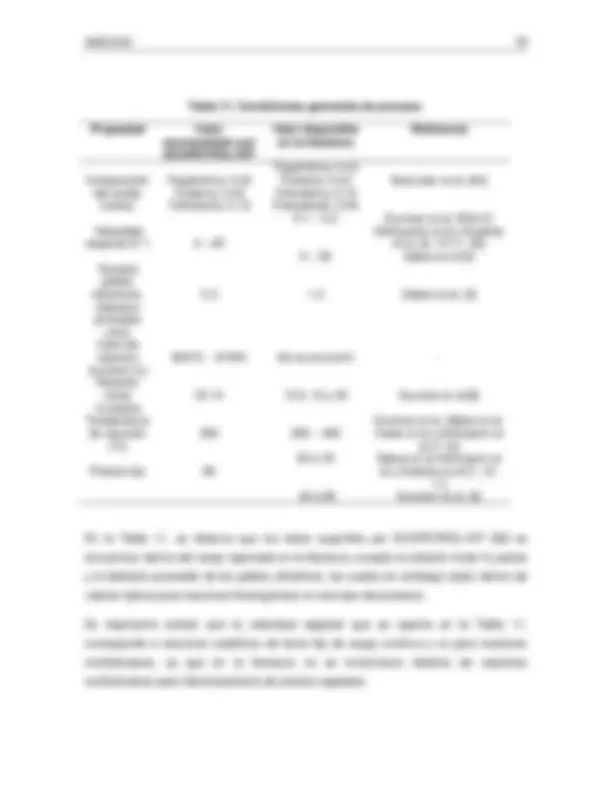
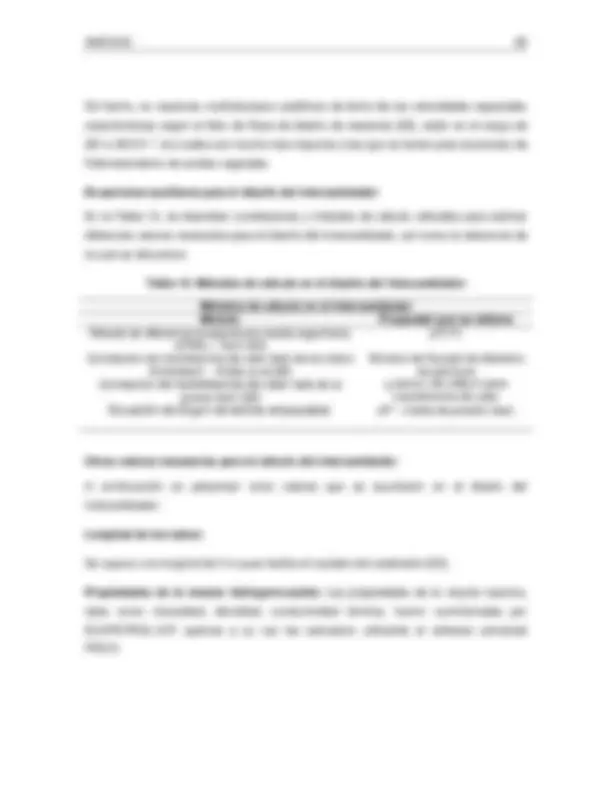
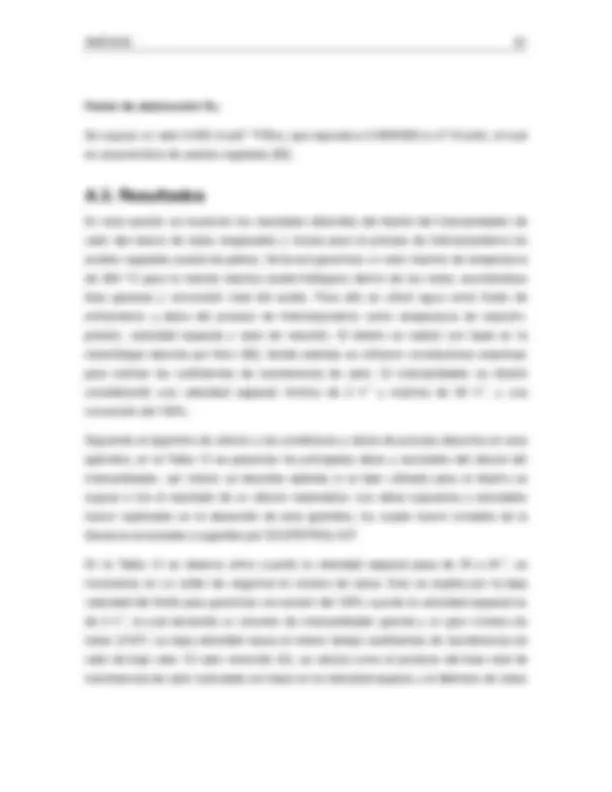
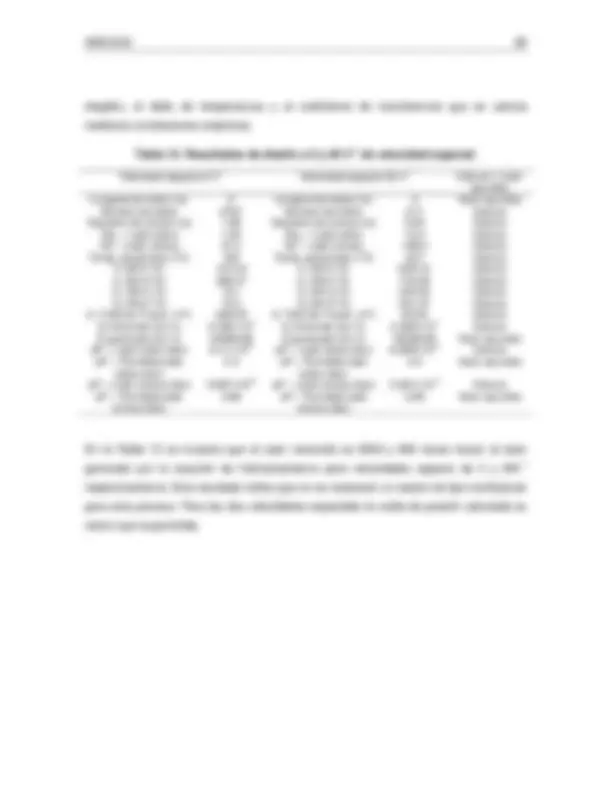
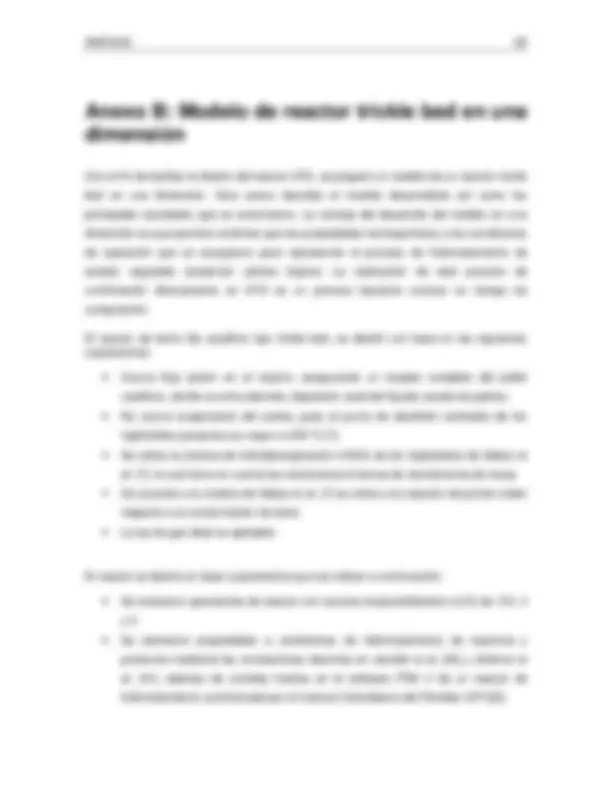
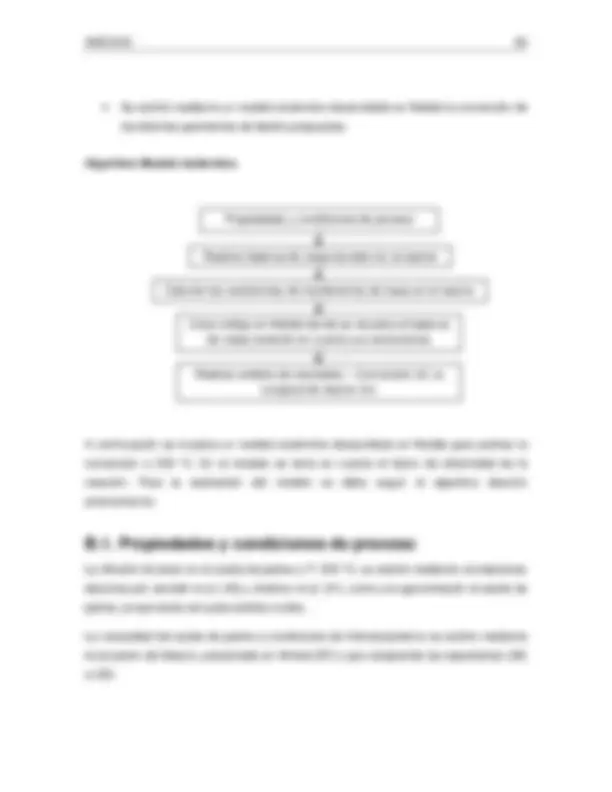
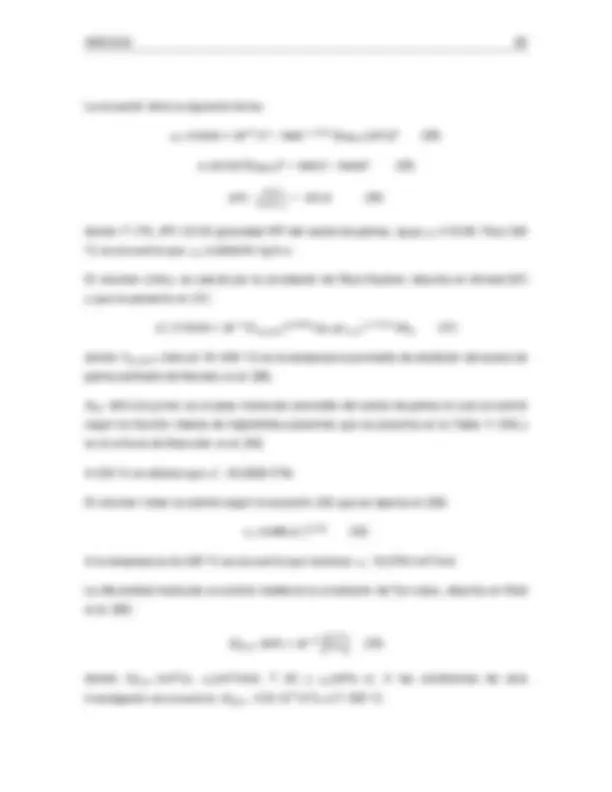
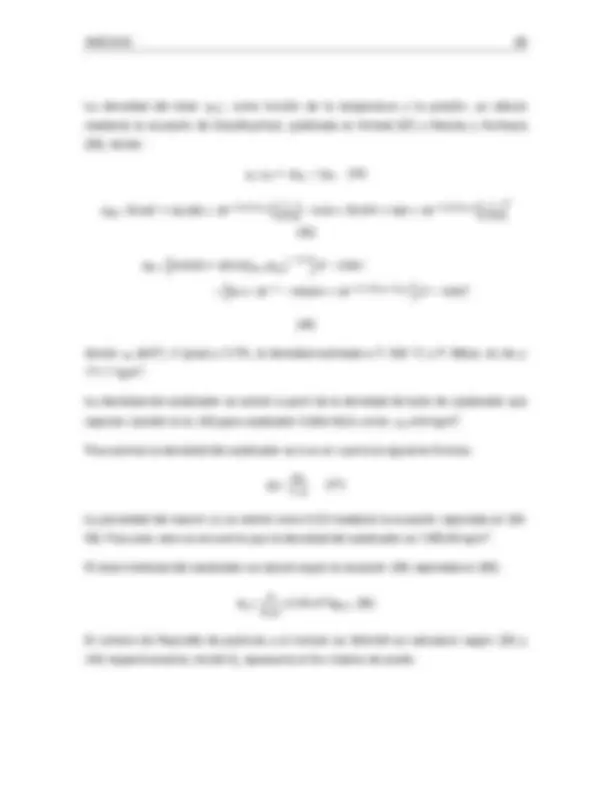
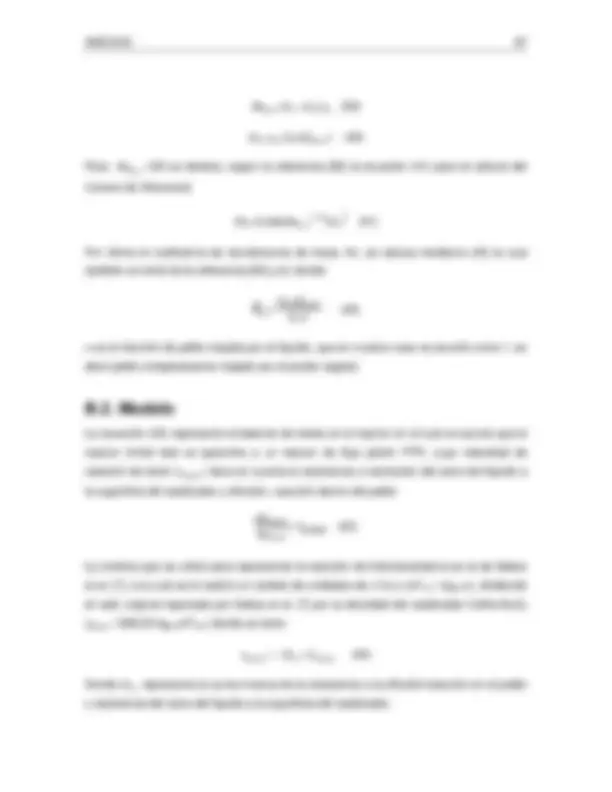
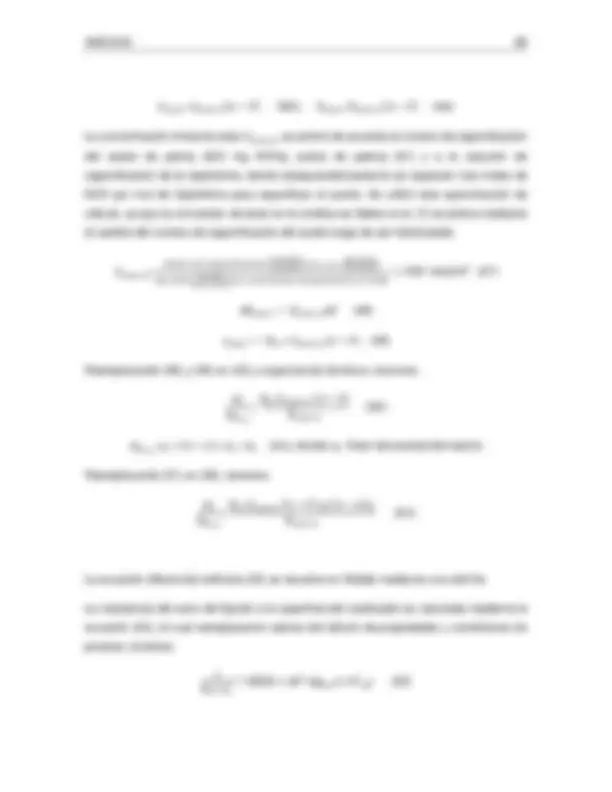
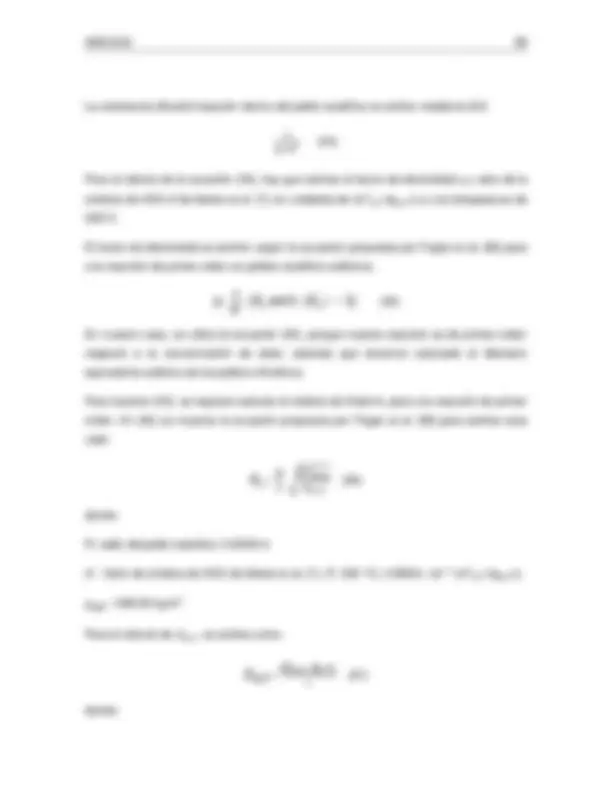
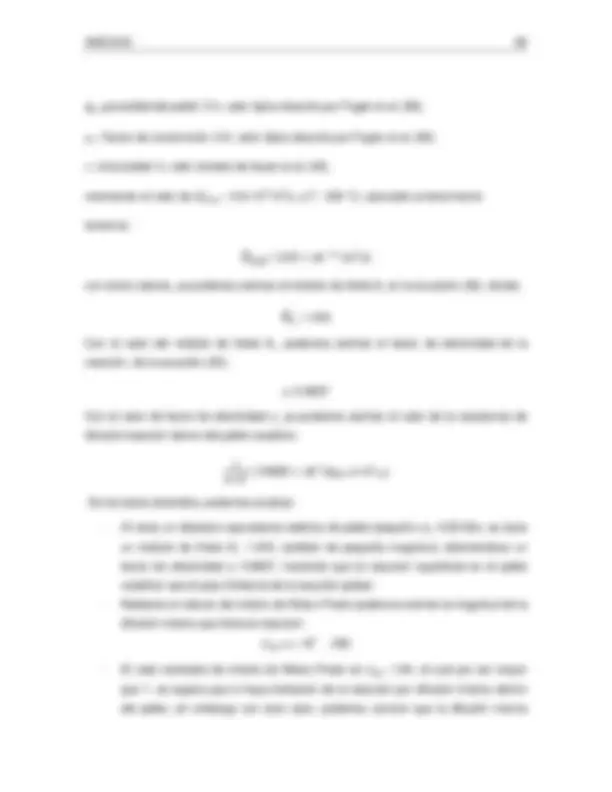
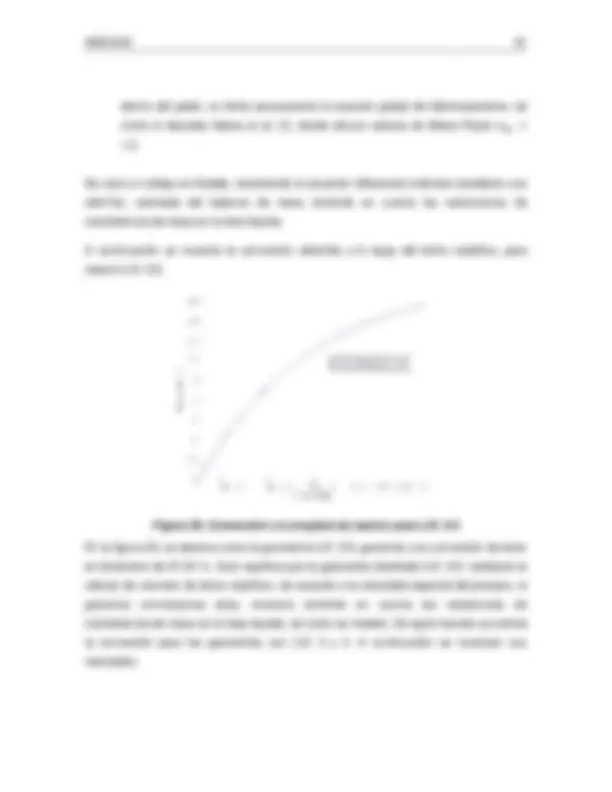
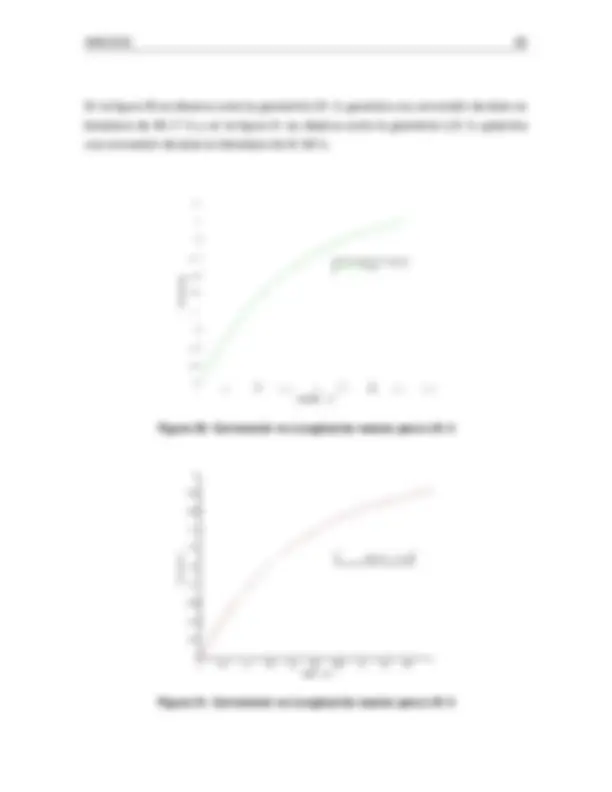
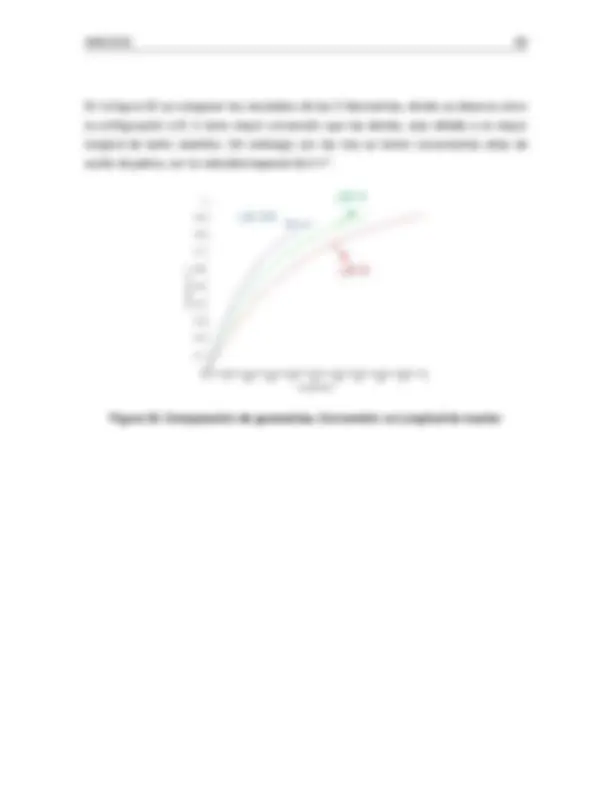
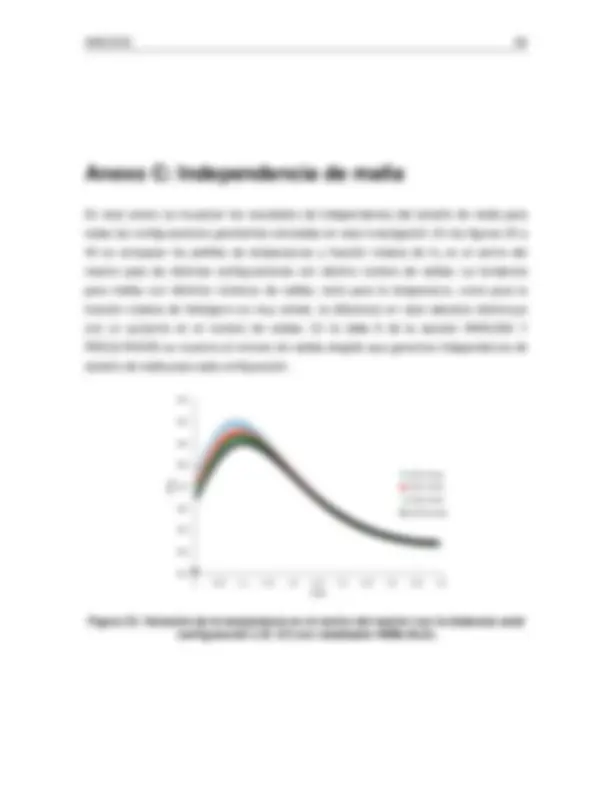
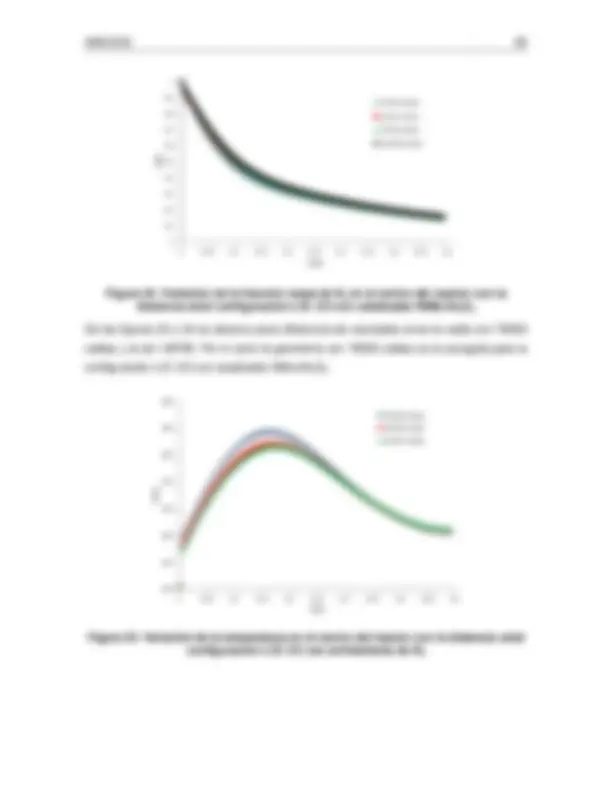
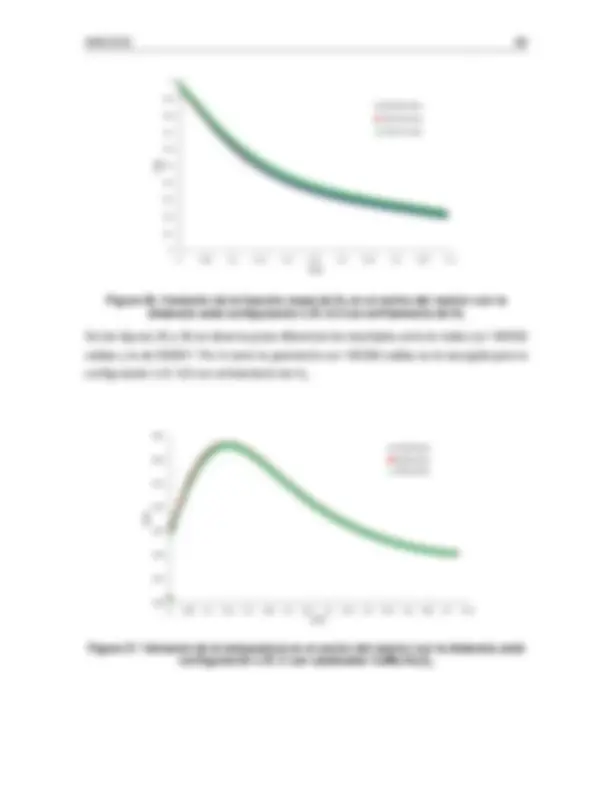
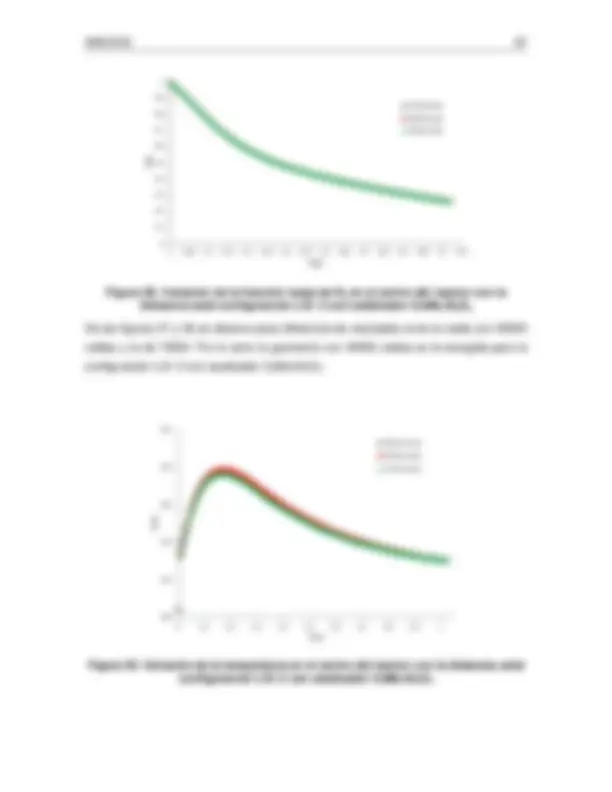
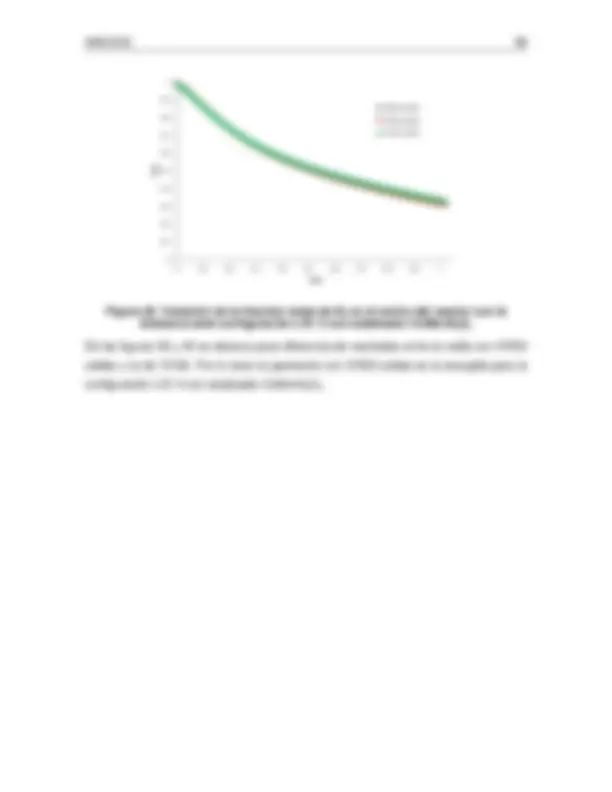
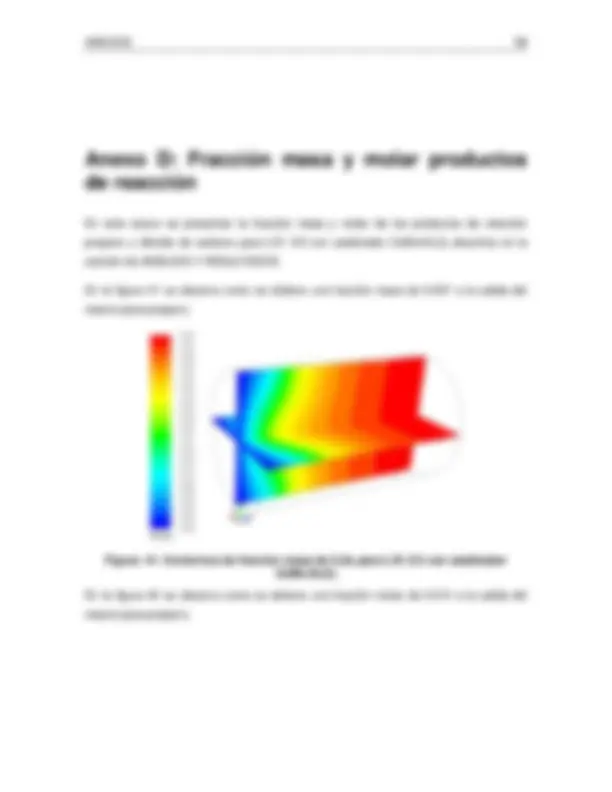
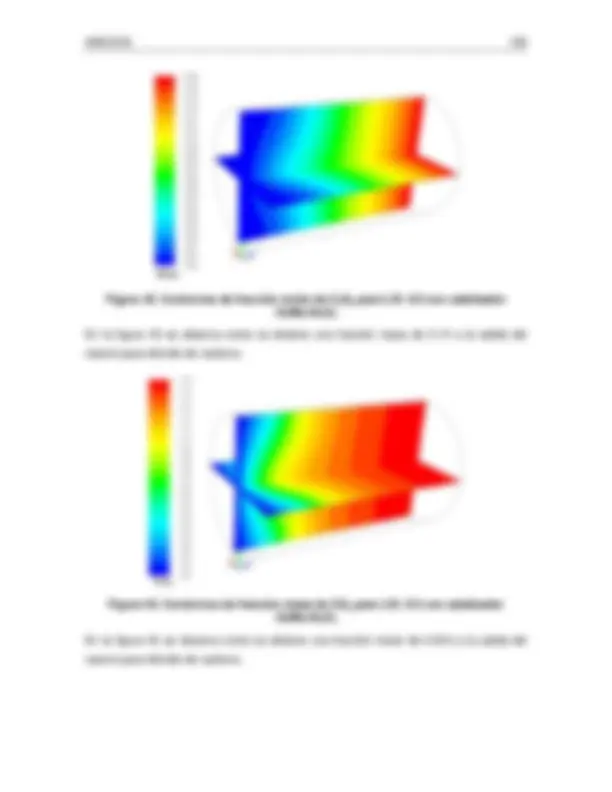
Prepara tus exámenes y mejora tus resultados gracias a la gran cantidad de recursos disponibles en Docsity
Gana puntos ayudando a otros estudiantes o consíguelos activando un Plan Premium
Prepara tus exámenes
Prepara tus exámenes y mejora tus resultados gracias a la gran cantidad de recursos disponibles en Docsity
Prepara tus exámenes con los documentos que comparten otros estudiantes como tú en Docsity
Los mejores documentos en venta realizados por estudiantes que han terminado sus estudios
Estudia con lecciones y exámenes resueltos basados en los programas académicos de las mejores universidades
Responde a preguntas de exámenes reales y pon a prueba tu preparación
Consigue puntos base para descargar
Gana puntos ayudando a otros estudiantes o consíguelos activando un Plan Premium
Comunidad
Pide ayuda a la comunidad y resuelve tus dudas de estudio
Descubre las mejores universidades de tu país según los usuarios de Docsity
Ebooks gratuitos
Descarga nuestras guías gratuitas sobre técnicas de estudio, métodos para controlar la ansiedad y consejos para la tesis preparadas por los tutores de Docsity
Material de lectura acerca de reactores
Tipo: Apuntes
1 / 105
Esta página no es visible en la vista previa
¡No te pierdas las partes importantes!
Universidad Nacional de Colombia – Sede Medellín Facultad de Minas, Departamento de Procesos y Energía Bioprocesos y flujos reactivos Medellín, Colombia 2012
Dedicatoria
A mis padres, mi hermana y mi novia.
Resumen VII
Se desarrolló un modelo CFD que permite representar la transferencia de calor en un reactor de hidrotratamiento de aceites vegetales. Este modelo permitió evaluar la transferencia de calor para distintas configuraciones del reactor. En el proceso de hidrotratamiento de aceites vegetales se transforma el aceite en un líquido con cero contenido de azufre y excelentes propiedades como combustible diesel. El proceso se basa en la adición de hidrógeno a alta presión en un reactor de lecho fijo catalítico de goteo continuo (trickle bed) para disminuir el tamaño de las moléculas de los ácidos grasos del aceite vegetal, mediante isomerización y craqueo térmico a temperaturas cercanas a 350°C.
Las características del producto cambian fuertemente con la temperatura de reacción, temperaturas elevadas causan craqueo térmico de los alcanos obtenidos, generando por tanto una reducción en la cantidad y calidad del producto. Los reactores utilizados en este tipo de proceso exigen un riguroso control en la temperatura por lo que es necesario evaluar la transferencia de calor para el control de puntos calientes.
Debido a que el hidrotratamiento de aceites vegetales es una tecnología reciente, en la literatura no se encuentran correlaciones de transferencia de calor para este proceso. La construcción de una planta piloto para estudiar el proceso puede tener un costo bastante elevado. Por tal motivo, en la presente investigación se estudió la transferencia de calor mediante la evaluación de distintas geometrías de reactores de goteo contínuo con CFD (Dinámica de Fluidos Computacional).
La simulación de la transferencia de calor en este tipo de reactores mediante CFD, ya ha sido reportada en la literatura pero no específicamente en el proceso de hidrotratamiento de aceites vegetales. La técnica de simulación CFD permite obtener detalladamente campos de velocidades, presión, perfiles de temperaturas, flux y coeficientes de transferencia de calor.
Resumen VIII
Mediante CFD se evaluaron distintas configuraciones geométricas de diseño en las que se obtuvieron perfiles de temperatura, flux y coeficientes de transferencia de calor, que mediante el efecto o no de fluido refrigerante (quenching de hidrógeno) permiten el riguroso control de temperatura que requiere el proceso.
Para representar la cinética de la reacción de hidrotratamiento se utilizó una expresión sencilla de velocidad de reacción de primer orden reportada en la literatura para aceites vegetales.
Con el fin de cumplir los objetivos propuestos en la tesis, se desarrollaron los siguientes pasos:
Paso 1: Búsqueda en la literatura de las propiedades del aceite de palma y datos de proceso de hidrotratamiento de aceites vegetales. Se realizó además una aproximación para estimar propiedades de los compuestos de la reacción global de hidrotratamiento, mediante correlaciones empíricas descritas en reactores de hidrotratamiento para aceite crudo y gasoil. De esta manera se definieron catalizadores, velocidad espacial, razón molar H 2 /aceite de palma, densidad, viscosidad, difusividad, solubilidad y coeficientes de transferencia de masa. Además se dimensionaron también, diferentes geometrías de reactores de goteo continuo a escala planta piloto.
Paso 2: Se desarrolló un modelo en CFD para diferentes geometrías de reactores de goteo continuo descritos en el paso 1. Para esto se realizó enmallado de las geometrías de los reactores utilizando Gambit, el cual es un software pre-procesador de Fluent. Se utilizó el código comercial Ansys Fluent en 3D para evaluar y predecir la transferencia de calor en el reactor. En Fluent, se desarrolló una UDF (User Defined Function) que calcula las velocidades de reacción de los compuestos teniendo en cuenta la cinética de hidrotratamiento de aceites vegetales reportada en la literatura sin modificaciones y con el cálculo del factor de efectividad de la reacción. También en la UDF se resuelve la ecuación de energía teniendo en cuenta el calor de reacción producido por la reacción global de hidrotratamiento. La transferencia de calor en el reactor se simuló retirando calor por las paredes manteniendo la temperatura de estas a 330°C para el control de puntos calientes.
Abstract X
Abstract
A CFD simulation that represents the heat transfer in a vegetable-oil hydrotreatment reactor was carried out. This simulation was used to evaluate heat transfer for different reactor configurations. Hydrotreatment transforms vegetable oils into a zero-sulfur liquid with properties that resemble those of diesel fuel. In a hydrotreatment reactor, high pressure addition of hydrogen reduces the size of the fatty acids molecules through isomerization and thermal cracking at temperatures close to 350°C.
The product characteristics strongly change with reaction temperature. High temperatures cause thermal cracking of alkanes and, therefore, a reduction in the quantity and quality of the desired product, diesel. The reactors used in this type of processes demand a rigorous temperature control. A thorough evaluation of the heat transfer in the reactor in order to avoid hot spots and guarantee good temperature control is, thus, mandatory.
Because hydrotreating of palm oil is a recent technology, in the refereed literature there were no heat transfer correlations clearly developed for this system. Furthermore, construction of a pilot plant may demand a very high cost. For that reason I propose the study of different trickle bed reactor geometries via computational fluid dynamics (CFD) as an alternative to simulate and evaluate the heat transfer in the hydrotreating reactor.
The heat transfer simulation of this kind of reactor by CFD has already been reported in the referenced literature but not specifically in the vegetable oils hydrotreating process. The CFD simulation allows for the calculation of detailed velocity fields, pressure, temperature profiles, fluxes and heat transfer coefficients for the analysis of heat transfer inside the reactor.
A simple first order reaction rate expression developed for vegetable oils, was used to represent the chemical kinetics.
The follow steps were required to carry out the objectives in this thesis:
Abstract XI
Step 1: Literature search for the palm oil properties and data for the vegetable oils hydrotreatment process. The properties of the species involved in the global hydrotreatment reaction were estimated with empirical correlations developed for the hydrotreatment of crude oil and vacuum gas oil.
This literature review defined catalysts, space velocity, H 2 /palm oil molar ratio, density, viscosity, diffusivity, solubility, mass transfer coefficient and different trickle bed reactors geometries for pilot plant scale.
Step 2: Development of a CFD model that represents hydrotreatment trickle bed reactors. The mesh was generated with Gambit and the CFD simulations were carried out with Ansys Fluent in 3D. A UDF (User Defined Function) was developed to resolve the components mol balance equations. The UDF considered well-known kinetics and effectiveness factors in the reaction rate expression. The UDF included as well source terms for energy estimating the heat of reaction produced by the hydrotreatment global reaction rate. The CFD simulation considered a constant wall temperature of 330 °C.
Step 3: The effect of hydrogen quenching to improve the heat remotion was evaluated.
Key words: Hydrotreatment, Vegetable oil, Trickle bed reactor, Heat Transfer Coefficient, CFD.
Contenido XIII
Anexo C: Independencia de malla.................................................................................. 94 Anexo D: Fracción masa y molar productos de reacción ............................................ 99 BIBLIOGRAFIA ...............................................................................................................
Lista de figuras XIV
Lista de figuras
Pág.
Figura 1. Reactor trickle bed, (a) Tipo cocorriente líquido + gas, (b) Tipo contracorriente gas ...................................................................................................................................... Figura 2. (a) Producción de nC 15 – C 18 vs. T (°C)^ y (b) % Producción de carbono vs. T (°C) ............................................................................................................................................ Figura 3. Condiciones de frontera para el caso base ......................................................... Figura 4. Condiciones de frontera para el caso con enfriamiento de H 2 ............................ Figura 5. Balance de moles de éster sobre sección de volumen de aceite de palma en el reactor................................................................................................................................. Figura 6. (a) Mallado Caso base y (b) con enfriamiento de H 2. .......................................... Figura 7. Variación de la temperatura en el centro del reactor con la distancia axial según simulaciones con distinto número de celdas ...................................................................... Figura 8. Variación de la fracción masa de H 2 en el centro del reactor con la distancia axial según simulaciones con distinto número de celdas ........................................................... Figura 9. Contornos de temperatura para L/D: 5/3 con catalizador CoMo/Al 2 O 3 ............... Figura 10. Contornos de fracción masa de H 2 para L/D: 5/3 con catalizador CoMo/Al 2 O 3. Figura 11. Contornos de fracción masa de C 15 H 32 para L/D: 5/3 con catalizador CoMo/Al 2 O 3 ......................................................................................................................... Figura 12. Contorno de fracción molar de H 2 para L/D: 5/3 con catalizador CoMo/Al 2 O 3 .. Figura 13. Contorno de fracción molar de C 15 H 32 para L/D: 5/3 con catalizador CoMo/Al 2 O 3 ............................................................................................................................................ Figura 14. Flujo molar de las especies (kmol/s) vs Longitud de reactor (m) ...................... Figura 15. Contornos de velocidad para L/D: 5/3 con catalizador CoMo/Al 2 O 3 .................. Figura 16. Contorno de presión absoluta para L/D: 5/3 con catalizador CoMo/Al 2 O 3 ....... Figura 17. Contorno de viscosidad dinámica para L/D: 5/3 con catalizador CoMo/Al 2 O 3 ... Figura 18. Temperatura en el centro del reactor para L/D: 5/3 con catalizador CoMo/Al 2 O (^3) ............................................................................................................................................ Figura 19. Flux de calor a través de la pared del reactor para L/D: 5/3 con catalizador CoMo/Al 2 O 3 ......................................................................................................................... Figura 20. Coeficiente de transferencia de calor de pared (h (^) w) para L/D: 5/3 con catalizador CoMo/Al 2 O 3 ...................................................................................................... Figura 21. Contornos de temperatura para L/D: 5/3, con efecto de factor de efectividad 𝜼 catalizador CoMo/Al 2 O 3 ......................................................................................................
Lista de tablas XVI
Lista de tablas
Pág.
Tabla 1. Condiciones de proceso utilizados en el modelo CFD ......................................... Tabla 2. Propiedades a condiciones de hidrotratamiento utilizadas en el modelo CFD ..... Tabla 3. Condiciones de proceso utilizadas en el caso de enfriamiento de H 2 .................. Tabla 4. Cálculo de propiedades mezcla reactiva .............................................................. Tabla 5. Características geométricas de la malla utilizada en el Caso base ...................... Tabla 6. Características geométricas de la malla utilizada en el Caso L/D: 3 .................... Tabla 7. Características geométricas de la malla utilizada en el Caso L/D: 5 .................... Tabla 8. Características geométricas de la malla utilizada para el caso con enfriamiento de H 2 ........................................................................................................................................ Tabla 9. Número de celdas requerido para garantizar independencia de tamaño de malla. Ver Anexo C para más detalles. ......................................................................................... Tabla 10. Comparación coeficiente de transferencia de calor de pared h (^) w de correlaciones con h (^) w mediante CFD. ........................................................................................................ Tabla 11. Condiciones generales de proceso. ................................................................... Tabla 12. Métodos de cálculo en el diseño del intercambiador .......................................... Tabla 13. Resultados de diseño a 2 y 20 h -1^ de velocidad espacial. ..................................
Lista de símbolos y abreviaturas 17
Lista de símbolos y abreviaturas
Símbolo Término Unidad SI
𝑎𝑐 Área interfacial de catalizador 𝑚
2 𝑘𝑔 𝑐𝑎𝑡 At Área transversal 𝑚^2 API Gravedad API - 𝐶𝑒𝑠𝑡,𝑜 Concentración de ester inicial kmol/ 𝑚 3 𝐶′^ Espaciado de tubos adyacentes 𝑚 𝑐𝑝 (^) Calor especifico a presión constante 𝐽 𝑘𝑔 𝐾 𝐶𝑤𝑝 Criterio de Weisz-Prater - D Diámetro de reactor 𝑚
D/DEnfriaminento,H
Razón diámetro de reactor/diámetro de orificio para enfriamiento de H 2 -
𝐷𝑒𝑠𝑡𝑒𝑟^ 𝐿^ Difusivividad ester en fase líquida 𝑚
2 𝑠
𝐷𝑒𝑓𝑓 Difusividad efectiva 𝑚
2 𝑠 𝐷𝑐 Diámetro interno de la coraza 𝑚 𝐷𝑐 Diámetro catalizador cilindro 𝑚 𝑑𝑠 Diámetro equivalente esférico^ 𝑚 d (^) t /d (^) p Razón diámetro de tubo/ diámetro de partícula - 𝑓 ̇ Flujo molar^ kmol/s
Lista de símbolos y abreviaturas 19
𝑅𝑒 Número de Reynolds -
𝑅𝑒𝑝 Número de Reynolds de partícula - 𝑅𝑒𝑝_𝐿 (^) Número de Reynolds de partícula del líquido -
𝑅𝑒𝑝_𝐺 (^) Número de Reynolds de partícula del gas -
𝑅𝑑 Factor de obstrucción ℎ^ 𝑝𝑖𝑒
𝑟𝑠 Velocidad de reacción de hidrodeoxigenación (^) 𝑚 3 𝑚𝑜𝑙 (^) 𝑎𝑐𝑒𝑖𝑡𝑒^ 𝑒𝑠𝑡𝑒𝑟 × 𝑠
𝑆𝑐𝐿 Número de Schmidt - 𝑆ℎ𝐿 Número de Sherwood - 𝑠𝑝. 𝑔𝑟 15. 6 Gravedad especifica a 15.6 °C - 𝑇 Temperatura °𝐶, °R t Tiempo s 𝑇𝑚𝑒𝐴𝐵𝑃 Temperatura promedio de ebullición °R
𝑈𝑐 Coeficiente total de transferencia de calor limpio
𝑈𝐷 Coeficiente total de diseño (^) 𝑚𝑊 (^2) 𝐾
𝑣𝑐^ 𝐿^ Volumen crítico fase líquida 𝑓𝑡
3 𝑙𝑏
𝑣𝐿 Volumen molar 𝑐𝑚
3 𝑚𝑜𝑙 𝑋 Conversión - 𝑋 Fracción molar kmol/kmol 𝑌 Fracción másica kg/kg
Lista de símbolos y abreviaturas 20
Símbolo Término Unidad SI 𝜌 Densidad (^) 𝑚𝑘𝑔 3
𝜌𝑏 Densidad de bulto de catalizador (^) 𝑚𝑘𝑔 3
𝜌𝑐 Densidad de catalizador (^) 𝑚𝑘𝑔 3
𝜌𝑜 Densidad inicial^ 𝑚𝑘𝑔 3
𝜀 (^) Porosidad de lecho catalíticos -
∆Hrxn Delta de reacción^ 𝑚𝑜𝑙𝑘𝐽 𝐻 2
∆𝜌𝑝^ Delta de presión debido a presión deoperación psia
∆𝜌𝑇^ Delta de presión debido a temperatura deoperación psia
Δ𝑃 Caída de presión bar o atm
Δ𝑇 Diferencia de temperatura medialogarítmica °F
𝜇𝐿 Viscosidad de líquido (kg/𝑚 s) o 𝑚Pa × s Φaceite Fracción de aceite en el reactor -
𝑇𝑟𝑒𝑠 Tiempo de residencia seg 𝜂 Factor de efectividad -