
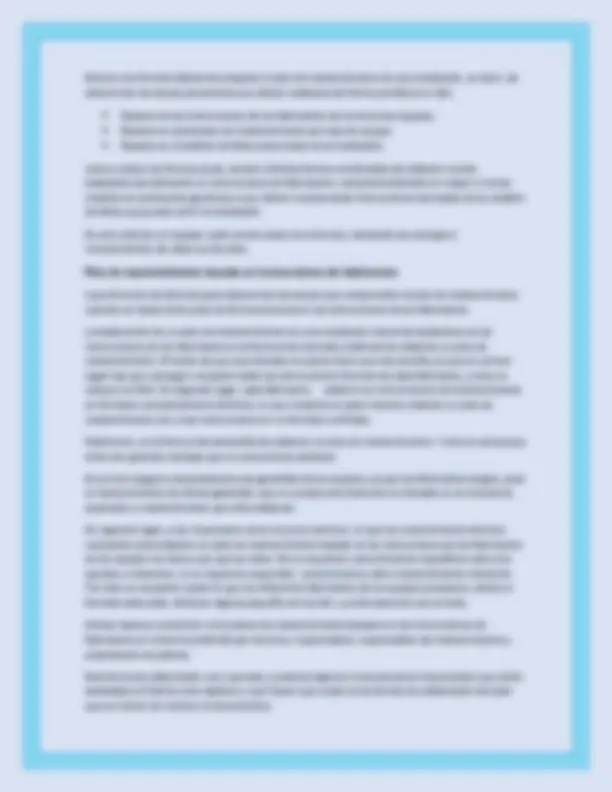
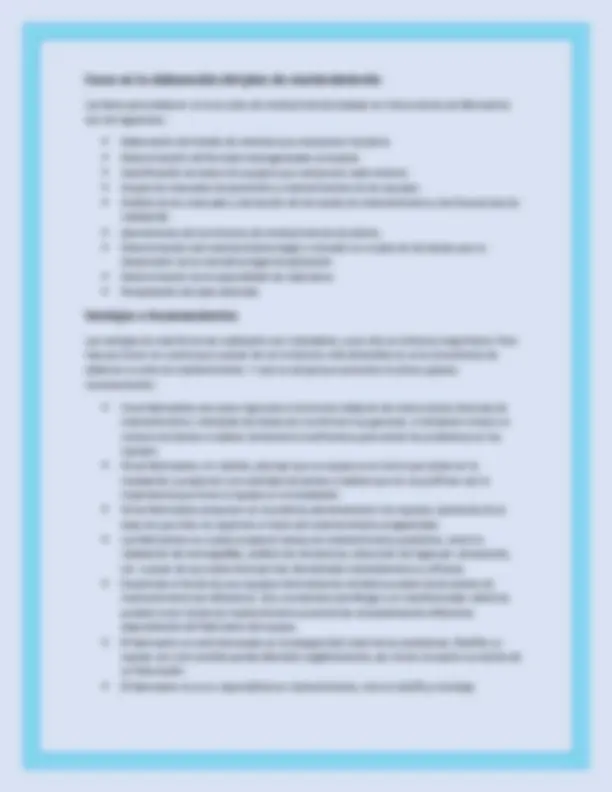
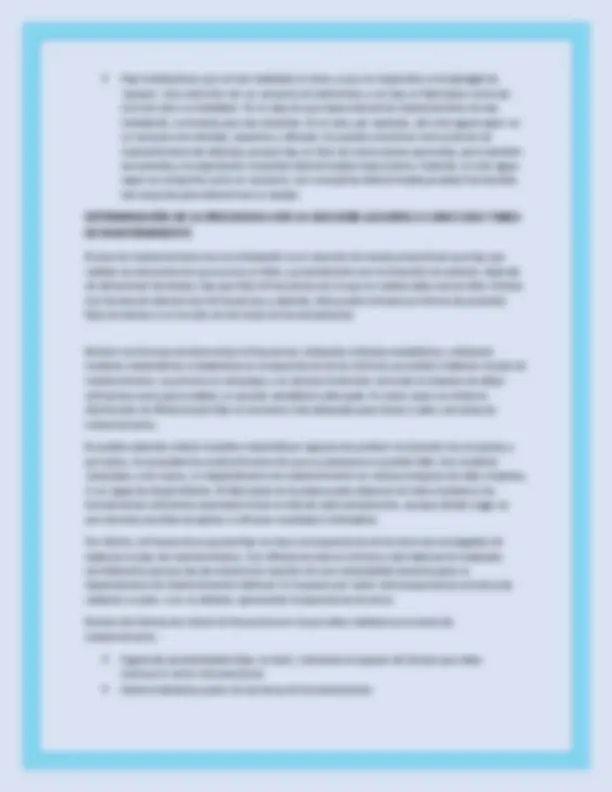
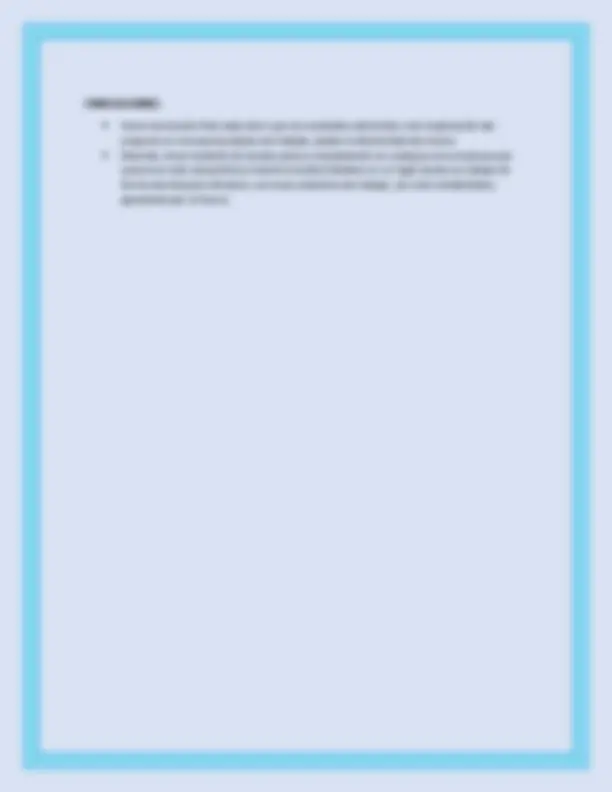
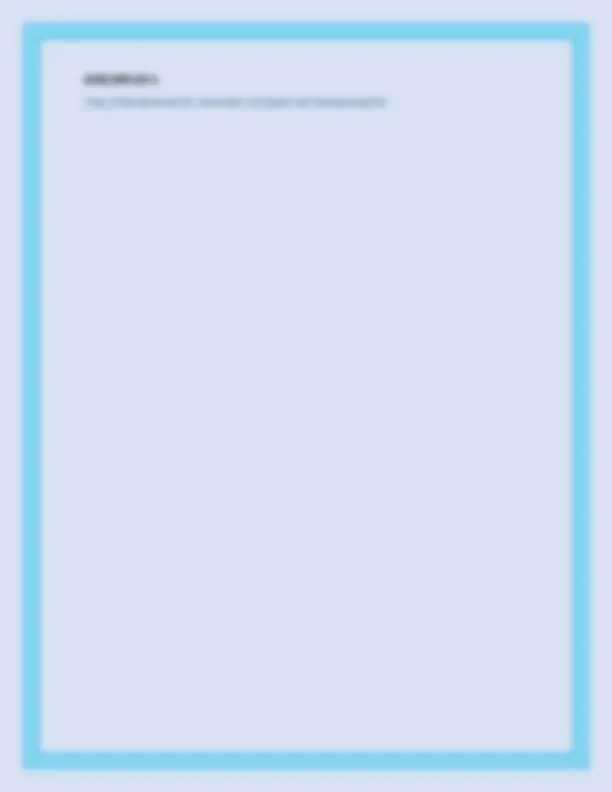
Prepara tus exámenes y mejora tus resultados gracias a la gran cantidad de recursos disponibles en Docsity
Gana puntos ayudando a otros estudiantes o consíguelos activando un Plan Premium
Prepara tus exámenes
Prepara tus exámenes y mejora tus resultados gracias a la gran cantidad de recursos disponibles en Docsity
Prepara tus exámenes con los documentos que comparten otros estudiantes como tú en Docsity
Los mejores documentos en venta realizados por estudiantes que han terminado sus estudios
Estudia con lecciones y exámenes resueltos basados en los programas académicos de las mejores universidades
Responde a preguntas de exámenes reales y pon a prueba tu preparación
Consigue puntos base para descargar
Gana puntos ayudando a otros estudiantes o consíguelos activando un Plan Premium
Comunidad
Pide ayuda a la comunidad y resuelve tus dudas de estudio
Descubre las mejores universidades de tu país según los usuarios de Docsity
Ebooks gratuitos
Descarga nuestras guías gratuitas sobre técnicas de estudio, métodos para controlar la ansiedad y consejos para la tesis preparadas por los tutores de Docsity
descripcion del proceso de mantenimiento
Tipo: Apuntes
1 / 9
Esta página no es visible en la vista previa
¡No te pierdas las partes importantes!
¨Año de la universalización de la salud”
Un plan de mantenimiento es el conjunto de tareas preventivas a realizar en una instalación con el fin de cumplir unos objetivos de disponibilidad, de fiabilidad, de coste y con el objetivo final de aumentar al máximo posible la vida útil de la instalación. Existen al menos tres formas de elaborar un plan de mantenimiento, es decir, de determinar el conjunto de tareas preventivas a llevar a cabo en la instalación: basarse en las recomendaciones de los fabricantes, basarse en protocolos genéricos o basarse en un análisis de fallos potenciales_._
Objetigo general: Conocer el proceso de formación de un proyecto de mantenimiento. Objetivo especifico: Conocer las etapas o fases del proyecto de mantenimento.
Las fases para elaborar un buen plan de mantenimiento basado en instrucciones de fabricantes son las siguientes: Elaboración del listado de sistemas que componen la planta. Determinación del formato homogenizado a emplear. Identificación de todos los equipos que componen cada sistema. Acopio de manuales de operación y mantenimiento de los equipos. Análisis de los manuales y extracción de las tareas de mantenimiento y las frecuencias de realización. Aportaciones de los técnicos de mantenimiento de planta. Determinación del mantenimiento legal e inclusión en el plan de las tareas que se desprenden de la normativa legal de aplicación. Determinación de la especialidad de cada tarea Recopilación del plan obtenido
Las ventajas de esta forma de realización son indudables, y por ello es la forma mayoritaria. Pero hay que tener en cuenta que a pesar de ser la técnica más extendida no es la única forma de elaborar un plan de mantenimiento. Y esto es así porque presenta muchos y graves inconvenientes: Unos fabricantes son poco rigurosos a la hora de elaborar las instrucciones técnicas de mantenimiento, indicando las tareas de una forma muy general, e indicando incluso un número de tareas a realizar claramente insuficientes para evitar los problemas en los equipos. Otros fabricantes, en cambio, piensan que su equipo es el único que existe en la instalación y proponen una cantidad de tareas a realizar que no se justifican con la importancia que tiene el equipo en la instalación. Otros fabricantes proponen en la práctica sobremantener los equipos, partiendo de la base de que ellos no soportan el coste del mantenimiento programado. Los fabricantes no suelen proponer tareas de mantenimiento predictivo, como la realización de termografías, análisis de vibraciones, detección de fugas por ultrasonido, etc. a pesar de que estas técnicas han demostrado sobradamente su eficacia. Sorprende el hecho de que equipos técnicamente similares puedan tener planes de mantenimiento tan diferentes. Así, una bomba centrífuga o un transformador eléctrico pueden tener tareas de mantenimiento preventivas completamente diferentes dependiendo del fabricante del equipo. El fabricante no está interesado en la desaparición total de los problemas. Diseñar un equipo con cero averías puede afectarle negativamente, por tocar una parte suculenta de su facturación. El fabricante no es un especialista en mantenimiento, sino en diseño y montaje.
Hay instalaciones que se han realizado en obra, y que no responden a la tipología de ‘equipo’, sino más bien son un conjunto de elementos, y no hay un fabricante como tal, sino tan solo un instalador. En el caso de que haya manual de mantenimiento de esa instalación, es dudoso que sea completo. Es el caso, por ejemplo, del ciclo agua-vapor: es un conjunto de tuberías, soportes y válvulas. Se pueden encontrar instrucciones de mantenimiento de válvulas, porque hay un libro de instrucciones para ellas, pero también las tuberías y la soportación necesitan determinadas inspecciones. Además, el ciclo agua- vapor se comporta como un conjunto: son necesarias determinadas pruebas funcionales del conjunto para determinar su estado.
El plan de mantenimiento de una instalación es el conjunto de tareas preventivas que hay que realizar en ésta antes de que ocurra un fallo, y precisamente con la intención de evitarlo. Además de determinar las tareas, hay que fijar la frecuencia con la que se realiza cada una de ellas. Existen tres formas de determinar la frecuencia, y además, ésta puede indicarse en forma de periodos fijos de tiempo o en función de las horas de funcionamiento. Existen tres formas de determinar la frecuencia: utilizando métodos estadísticos, utilizando modelos matemáticos o basándose en la experiencia de los técnicos que deben elaborar el plan de mantenimiento. La primera es compleja, y no siempre (más bien rara vez) se dispone de datos suficientes como para realizar un estudio estadístico adecuado. En estos casos se utiliza la distribución de Weibull para fijar el momento más adecuado para llevar a cabo una tarea de mantenimiento. Es posible además utilizar modelos matemáticos capaces de predecir la duración de una pieza, y por tanto, la necesidad de sustituirla antes de que se produzca un posible fallo. Son modelos complejos, y de nuevo, un departamento de mantenimiento no siempre dispone de tales modelos, ni es capaz de desarrollarlos. El fabricante de la pieza puede disponer de tales modelos o de herramientas suficientes para determinar la vida de cada componente, aunque desde luego no son técnicas sencillas de aplicar ni ofrecen resultados irrefutables. Por último, la frecuencia se puede fijar en base a la experiencia de los técnicos encargados de elaborar el plan de mantenimiento. Con diferencia esta es la forma más habitual de realizarlo, sencillamente porque las dos anteriores resultan de una complejidad excesiva para un departamento de mantenimiento habitual. Se requiere por tanto cierta experiencia a la hora de redactar un plan, o en su defecto, aprovechar la experiencia de otros. Existen dos formas de indicar la frecuencia con la que debe realizarse una tarea de mantenimiento: Siguiendo periodicidades fijas, es decir, indicando el espacio de tiempo que debe transcurrir entre intervenciones Determinándola a partir de las horas de funcionamiento
Anual distribuida, que se reserva para aquellas tareas de frecuencia anual que pueden realizarse en cualquier momento del año. Anual en parada, que se reserva para aquellas tareas de frecuencia anual que debe ser realizadas exclusivamente coincidiendo con la parada anual que muchas instalaciones organizan, y que supone la base del mantenimiento en muchos casos. Esta distinción facilita que las tareas anuales a realizar en parada puedan ser más fácilmente externalizables, mientras que las tareas anuales distribuidas pueden ser realizadas perfectamente por el personal habitual. La periodicidad bienal se reserva casi en exclusiva para la calibración de instrumentación y para la verificación de lazos de control. Las periodicidades trianual, cuatrienal, etc., se reservan para la realización de tareas de mantenimiento legal. Un problema habitual a la hora de fijar la frecuencia con la que realizar determinadas tareas es que algunas de ellas pueden estar referidas a horas de funcionamiento, en vez de a espacios de tiempo naturales. Algunos fabricantes de equipos prefieren referirse a horas de funcionamiento, lo cual parece muy lógico: si un equipo no se ha utilizado, no parece necesario realizar mantenimiento en él. No es fácil mezclar tareas que deben realizarse con frecuencias naturales fijas con tareas que se realizan por horas de funcionamiento, con periodos variables entre ellas. Hay muchas formas de abordar el problema, entre las que están las siguientes: Crear dos planes de mantenimiento separados: el referido a frecuencias naturales (diario, semana, mensual, etc.) y el referido a horas de funcionamiento, de forma que el mantenimiento de los equipos a los que aplica un control horario queda fuera del mantenimiento de sistemas. Es conveniente en este caso instalar horómetros para cada uno de ellos, incluso conectados con el sistema de control o con el software de mantenimiento. La instalación de horómetros y su posterior gestión no es un asunto sencillo, y tratar de llevar el control. Estimar frecuencias fijas, calculando cuando tiempo natural debe transcurrir para que se alcancen las horas de inspección recomendadas por los fabricantes. De esta manera, que es la forma recomendada por RENOVETEC, se evita esta mezcla de frecuencias determinadas por horas de funcionamiento y por periodos naturales.
Un protocolo de mantenimiento es un listado de tareas a realizar en un tipo concreto de equipo. En el protocolo de mantenimiento de un equipo tipo debe incluirse al menos la siguiente información para cada tarea incluida en el protocolo: Especialidad del trabajo. Frecuencia con la que debe realizarse. Duración estimada de la realización de la tarea. Necesidad de un permiso de trabajo especial. Si el equipo debe estar parado o en marcha para la realización de la tarea.
Como conclusión final cabe decir que los resultados obtenidos, tras la aplicación del proyecto en la empresa objeto del trabajo, avalan la efectividad del mismo. Además, sirven también de acicate para su implantación en cualquier otra empresa que quiera ser más competitiva y hacerlo transformándose en un lugar donde se trabaje de forma sencilla pero eficiente, con buen ambiente de trabajo, con más rentabilidad y apostando por el futuro.