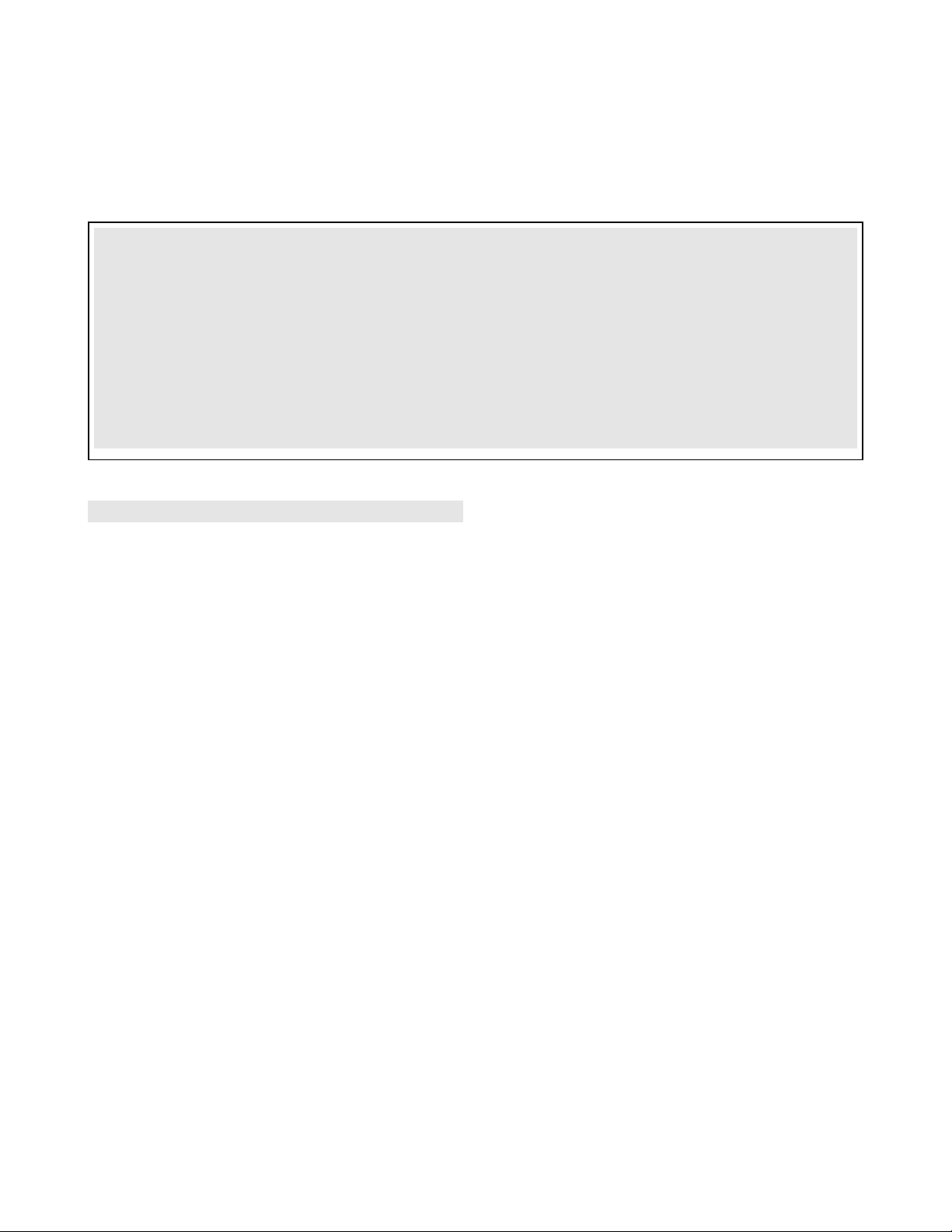
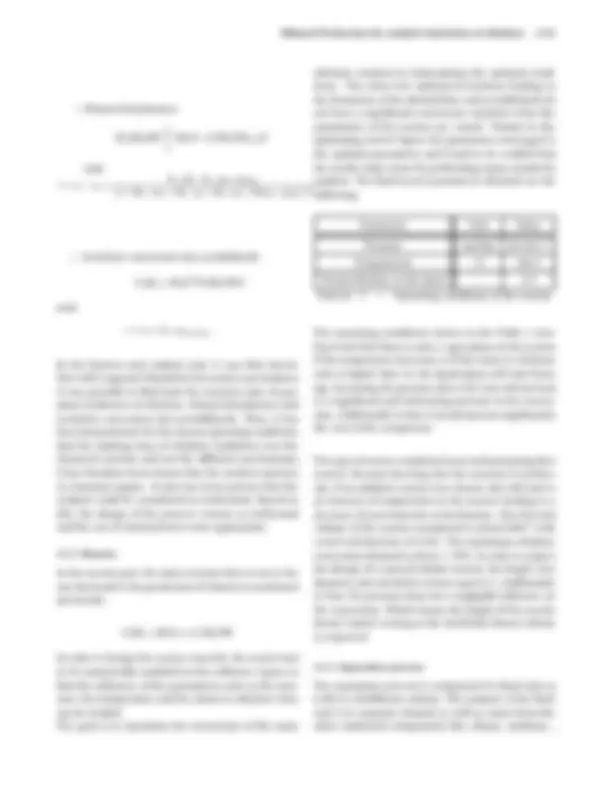
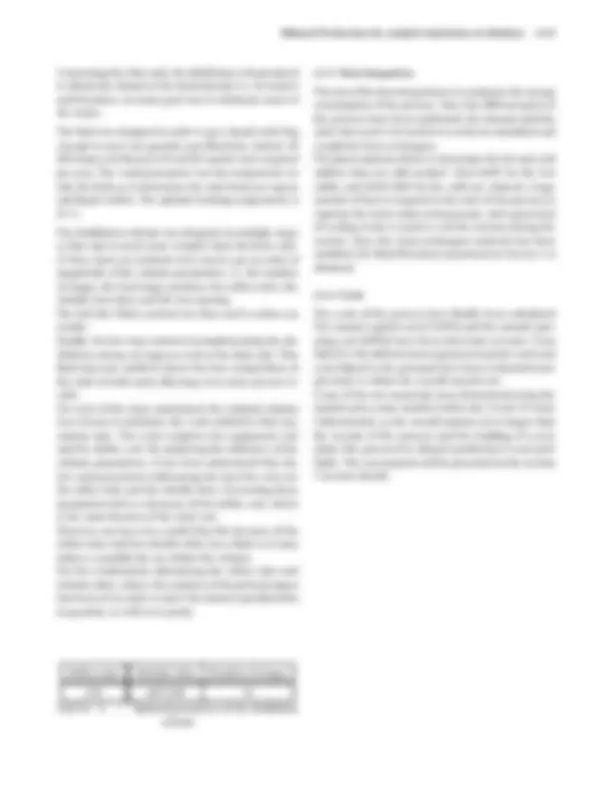
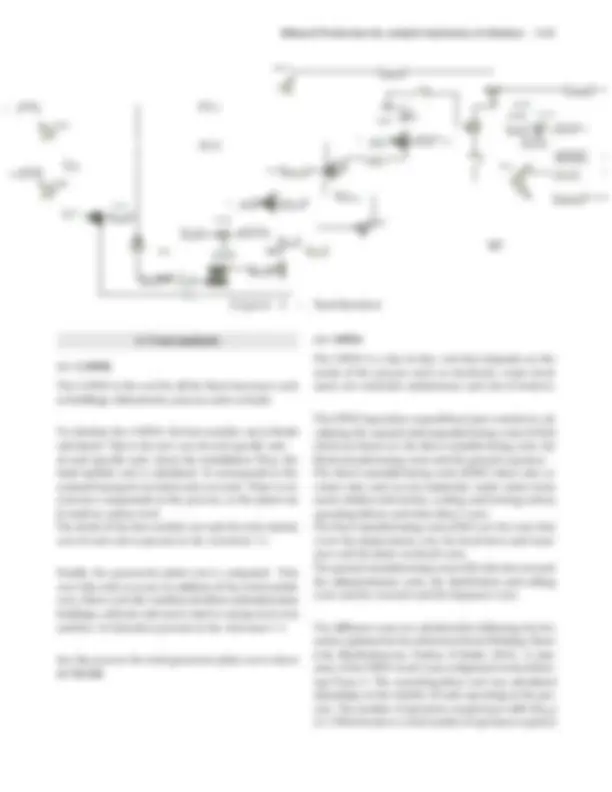
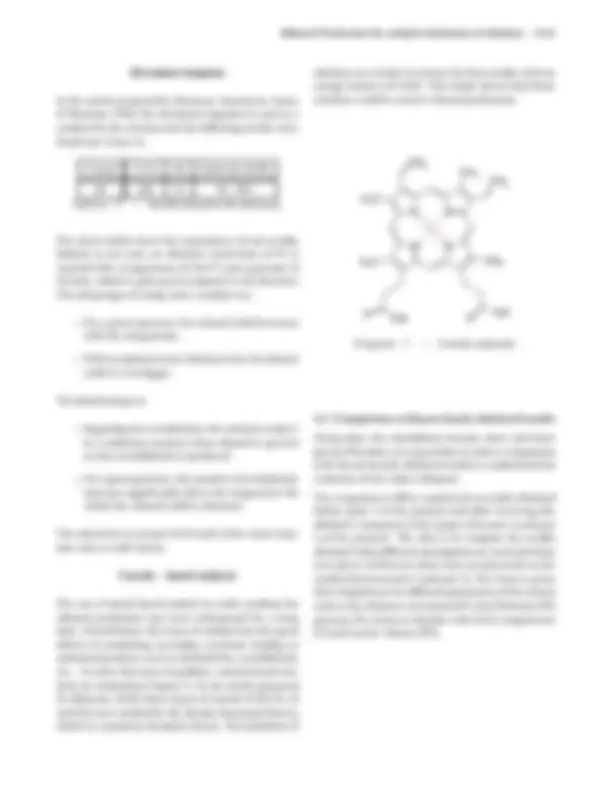
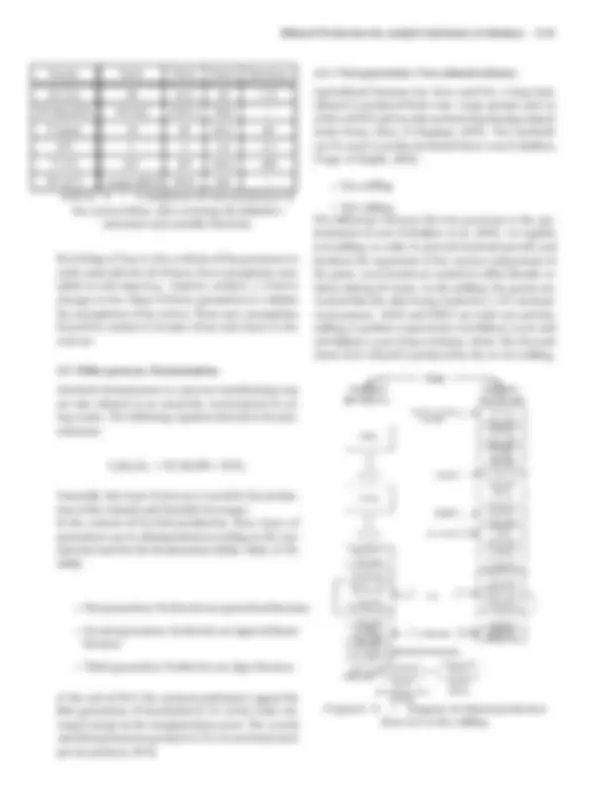
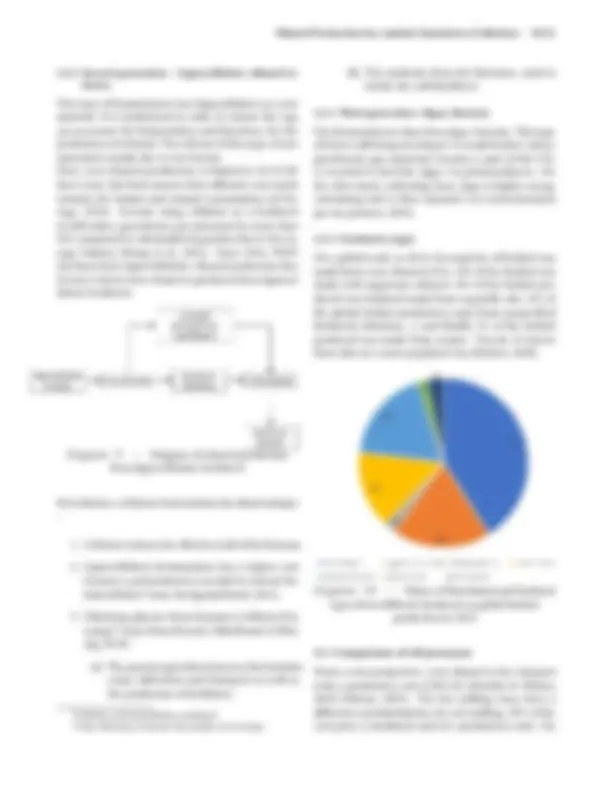
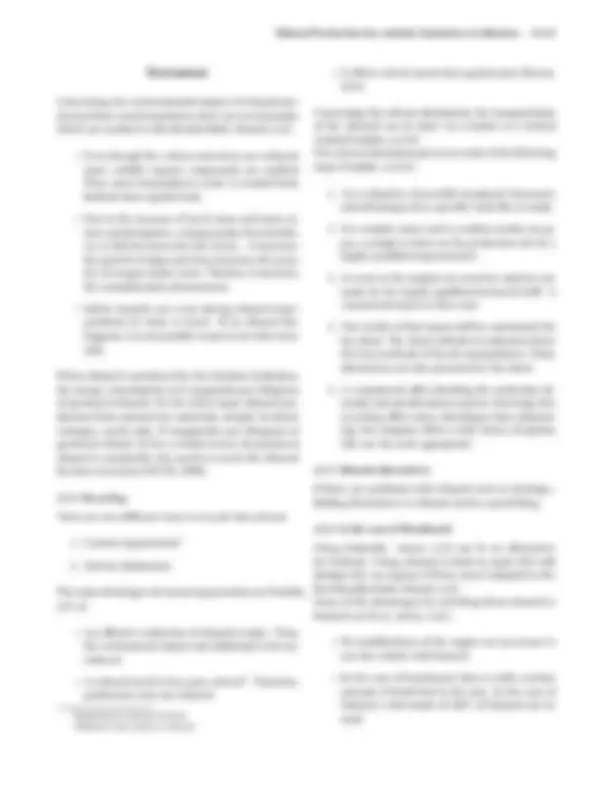
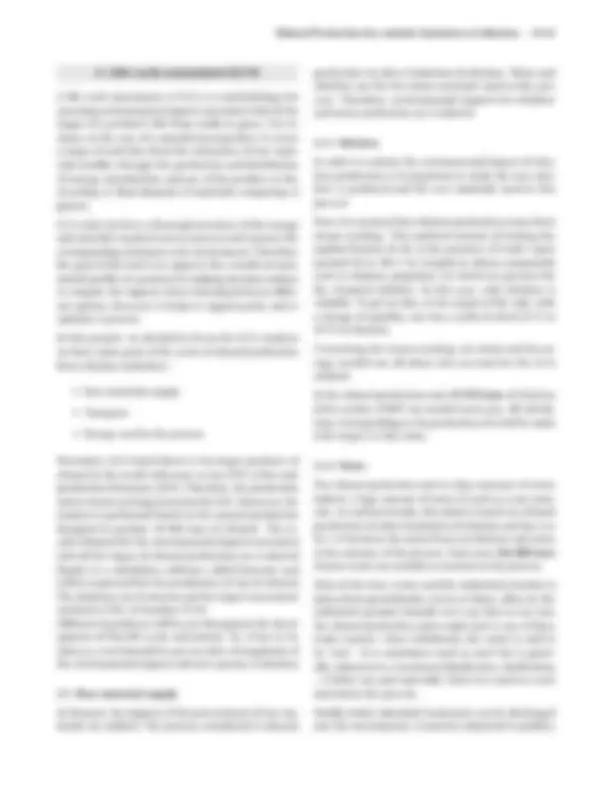
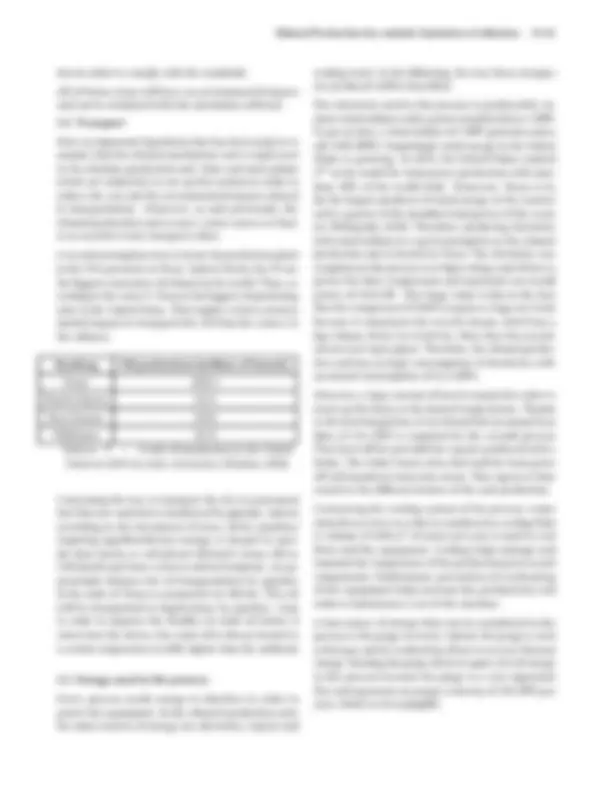
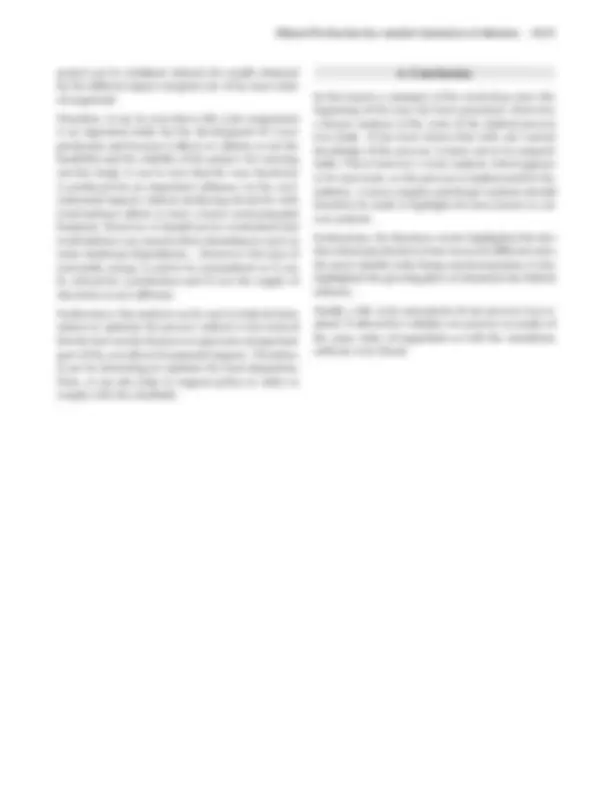
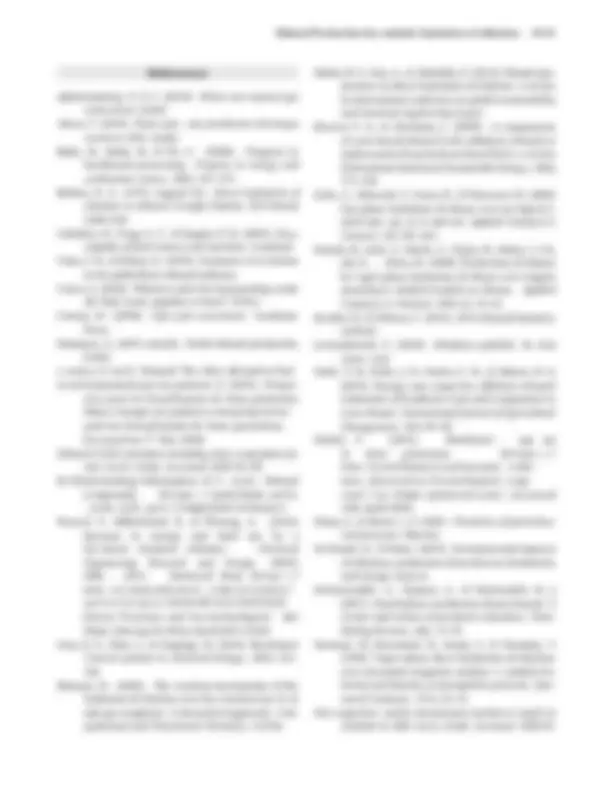
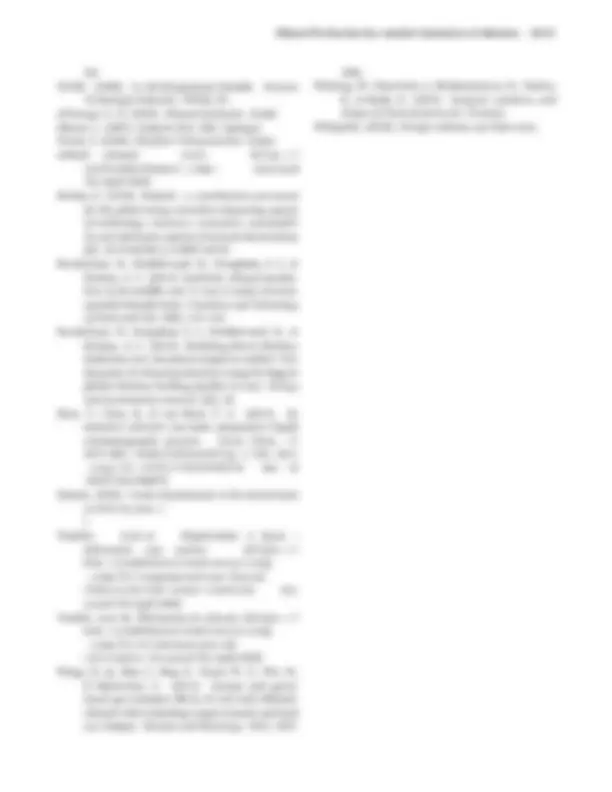
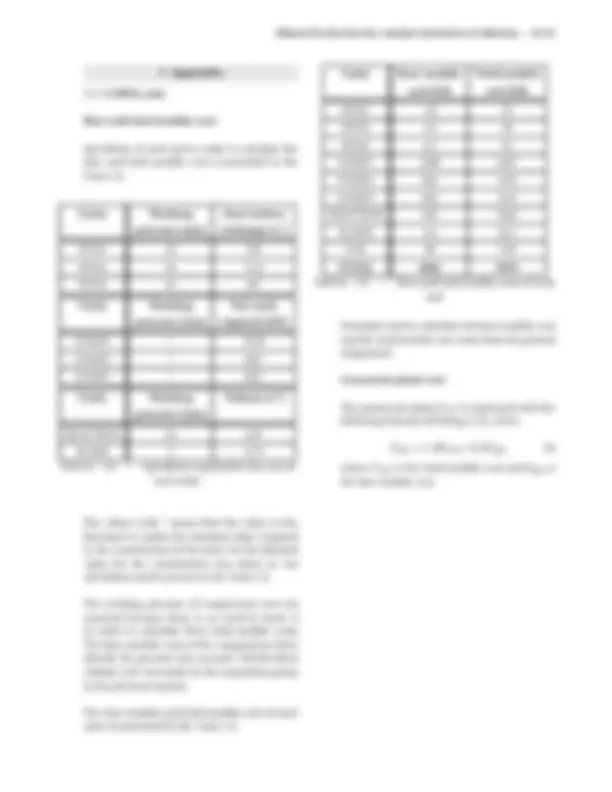
Prepara tus exámenes y mejora tus resultados gracias a la gran cantidad de recursos disponibles en Docsity
Gana puntos ayudando a otros estudiantes o consíguelos activando un Plan Premium
Prepara tus exámenes
Prepara tus exámenes y mejora tus resultados gracias a la gran cantidad de recursos disponibles en Docsity
Prepara tus exámenes con los documentos que comparten otros estudiantes como tú en Docsity
Los mejores documentos en venta realizados por estudiantes que han terminado sus estudios
Estudia con lecciones y exámenes resueltos basados en los programas académicos de las mejores universidades
Responde a preguntas de exámenes reales y pon a prueba tu preparación
Consigue puntos base para descargar
Gana puntos ayudando a otros estudiantes o consíguelos activando un Plan Premium
Comunidad
Pide ayuda a la comunidad y resuelve tus dudas de estudio
Descubre las mejores universidades de tu país según los usuarios de Docsity
Ebooks gratuitos
Descarga nuestras guías gratuitas sobre técnicas de estudio, métodos para controlar la ansiedad y consejos para la tesis preparadas por los tutores de Docsity
Analisis he identificacion de la produccion de etanol
Tipo: Apuntes
1 / 21
Esta página no es visible en la vista previa
¡No te pierdas las partes importantes!
Integrated Project 2019 - 2020
Abstract This paper discusses all the aspects of the process of ethylene hydration to produce ethanol. A short summary gives all the information known and found about the studied process. Afterwards, the necessary cost to implement this process is presented and analyzed. A literature review shows a glimpse of the other kinds of processes used in the industry to produce ethanol, detailing the catalysts used as well as the different raw materials. An overview of the ethanol properties is also displayed in this paper. Finally, the Life Cycle Analysis (LCA) gives the environmental aspect of the ethylene hydration process, underlying sections of the process to improve such as the heat integration. Keywords Ethanol - Process - Ethylene - Hydration - LCA - Market - Feedstock
1 Introduction 2
2 Summary of our process : catalytic hydration of ethylene 2
2.1 Our process........................... 2 Thermodynamics • Kinetics and catalysts • Reactor • Separation process • Heat integration • Costs
3 Cost analysis 5
3.1 CAPEX.............................. 5
3.2 OPEX............................... 5
3.3 Cash flows........................... 6
4 Literature Review 7
4.1 Catalytic Hydration of Ethylene: Other Processes 7 Catalysts
4.2 Comparison with previously obtained results.. 8
4.3 Other process: Fermentation.............. 9 First generation: Corn ethanol industry • Second generation : Lignocellulosic ethanol industry • Third generation: Algae, Bacteria • Feedstock origin
4.4 Comparison of all processes.............. 10
4.5 Ethanol overview...................... 11 Market • Raw materials uses • Toxicity and Environment • Recycling • Ethanol alternatives • In the case of Bioethanol 5 Life-cycle assessment (LCA) 14 5.1 Raw material supply................... 14 Ethylene • Water 5.2 Transport........................... 15 5.3 Energy used in the process............... 15 5.4 Environmental impacts................. 16 Conclusion 6 Conclusion 18 References 19
7 Appendix 21 7.1 CAPEX costs......................... 21
This project was devoted to the study of ethanol pro- duction by catalytic hydration of ethylene. A process for the ethanol synthesis has been developed and the operating conditions optimized in order to reduce pro- duction costs. Before the extended literature review, a summary of the work done will be presented.
The purpose of this extended literature review is to compare our process with those found in the literature. Firstly, the cost of our process will be analyzed. Sec- ondly, our process is compared to similar production processes of synthetic ethanol using oil-based products as raw materials. Afterwards, different ways of producing ethanol will be discussed and compared to our process. To end this literature review, a broader society overview including market, toxicity,... will be made. Lastly, the LCA of the process will be discussed to ac- knowledge the impacts of the considered process.
This process is mainly used to produce ethanol as a solvent. Considering the entire ethanol production, this type of process represents only 7% of the production (Roozbehani, Mirdrikvand, Moqadam, & Roshan, 2013; Mohsenzadeh, Zamani, & Taherzadeh, 2017). Indeed, producing ethanol via this process is more ex- pensive than using techniques such as fermentation. This is due to the price of ethylene, which fluctuates enormously according to the geographical area. Three large companies produce synthetic ethanol: Sasol in South Africa, SADAF in Saudi Arabia and Equistar in the USA. (Roozbehani et al., 2013).
2.1 Our process
The process displayed in the Figure 8 was the subject of an in-depth study this year. The following equilibrium describes the main reaction:
C 2 H 4 + H 2 O C 2 H 5 OH
Because of the equilibrium, the operating conditions play an important role in conversion. Part of the work done this year was useful to determine the optimal con- ditions for a maximized conversion, taking into account
the imposed constraints. However, ones must be careful about the fact that other components are present in the process due to impurities in the ethylene feed.
Figure 1 – Our process flowsheet
2.1.1 Thermodynamics The thermodynamics part was devoted to determine the properties of all the components of our process. To reach this goal, the properties for the pure compo- nents at different temperatures and pressures have to be determined. Then, the properties of ideal and real mixtures can be found. The real mixture properties will depend on the choice of the thermodynamic model. These data will be used in the other sections for the design of all unit operations. In this way, concerning the pure components, the Peng-Robinson model was chosen to describe them. For the mixtures, the model that fits the better the experimental data of binary mix- tures was chosen. For this case, the NRTL-RK is the most accurate model.
2.1.2 Kinetics and catalysts Three main reactions are occurring within the studied process:
C 2 H 4 + H 2 O
r 1 r 2
with
r = r 1 − r 2 = k 1 · pE · pW − k 2 · KA · pA { 1 + KE · pE + KW · pW + KA · pA + KDEE · pDEE }^2
Concerning the other unit, the distillation column aimed to obtain the ethanol at the desired purity i.e. 82 molar% and therefore, its main goal was to eliminate most of the water.
The flash was designed in order to get a liquid outlet big enough to meet our quantity specifications. Indeed, 30 000 tonnes of ethanol at 82 molar% purity were required per year. The varied parameter was the temperature in- side the flash as it determines the ratio between vapour and liquid outlets. The optimal working temperature is 85 °C.
The distillation column was designed in multiple steps, as this unit is much more complex than the latter unit. At first, short-cut methods were used to get an order of magnitude of the column parameters, i.e. the number of stages, the feed stage position, the reflux ratio, the reboiler heat duty and the tray spacing. The McCabe-Thiele method was then used to refine our results. Finally, the last step consisted in implementing the dis- tillation column on Aspen as well as the flash unit. This final step was useful to know the true composition at the inlet of both units allowing even more precise re- sults. For each of the steps mentioned, the optimal column was chosen to minimise the costs related to that sep- aration unit. The costs comprise the equipment cost and the utility cost. By analysing the influence of the column parameters, it has been understood that the two main parameters influencing the most the costs are the reflux ratio and the reboiler duty. Decreasing these parameters led to a decrease of the utility cost, which is the main fraction of the total cost. However, one has to be careful that this decrease of the reflux ratio and the reboiler duty has a limit as it may induce a possible dry up within the column. For the combination minimising the reflux ratio and reboiler duty values, the number of theoretical stages has been set in order to meet the desired specifications in quantity as well as in purity.
Reflux ratio Reboiler duty Number of stages 2.93 6075 kW 31
Table 2 – Optimal parameters of the distillation column
2.1.5 Heat integration The aim of the heat integration is to minimise the energy consumption of the process. Once the different parts of the process have been optimised, the streams and the units that need to be heated or cooled are identified and coupled in heat exchangers. The pinch analysis allows to determine the hot and cold utilities that are still needed: 13612.4kW for the hot utility and 18529.3kW for the cold one. Indeed, a huge amount of heat is required at the start of the process to vaporise the water under such pressure, and a great deal of cooling water is used to cool the stream exiting the reactor. Once the heat exchangers network has been included, the final flowsheet presented on Figure 2 is obtained.
2.1.6 Costs The costs of the process have finally been calculated. The annual capital cost (CAPEX) and the annual oper- ating cost (OPEX) have been taken into account. Costs linked to the infrastructures (grassroots plant costs) and costs linked to the personal have been evaluated more precisely to obtain the overall annual cost. Costs of the raw materials were determined using the market price some months before the Covid-19 crisis. Unfortunately, as the overall annual cost is larger than the income of the process and the building of a new plant, this process for ethanol production is not prof- itable. The cost analysis will be presented in the section 3 in more details.
Figure 2 – Final flowsheet
The CAPEX is the cost for all the fixed structures such as buildings, laboratories, process units or lands.
To calculate the CAPEX, the bare module cost is firstly calculated. This is the raw cost of each specific unit. of each specific unit, where the installation Then, the total module cost is calculated. It corresponds to the costand transport are taken into account. There is no corrosive compounds in the process, so the plant can be built in carbon steel. The detail of the bare module cost and the total module cost of each unit is present in the Appendix 7.1.
Finally, the grassroots plant cost is computed. This cost takes into account, in addition of the total module cost, others costs like auxiliary facilities (administration buildings, cafeteria and more), land or unexpected costs and fees. Its formula is present in the Appendix 7.1.
For this process the total grassroots plant cost is about 12 781 k$.
The OPEX is a day-to-day cost that depends on the needs of the process such as electricity, water treat- ment, raw materials, maintenance and cost of workers.
The OPEX (operation expenditure) part consists in cal- culating the annual total manufacturing costs (COM) which are based on: the direct manufacturing costs, the fixed manufacturing costs and the general expenses. The direct manufacturing costs (DMC) takes into ac- count costs such as raw materials, waste water treat- ment, utilities (electricity, cooling and heating water), operating labour and other direct costs. The fixed manufacturing costs (FMC) are the costs that cover the depreciation cost, the local taxes and insur- ance and the plant overhead costs. The general manufacturing costs (GE) take into account the administration costs, the distribution and selling costs and the research and development costs.
The different costs are calculated by following the for- mulas explained in the referenced book ( Whiting, Shaei- witz, Bhattacharyya, Turton, & Bailie, 2013). A sum- mary of the OPEX result costs is displayed in the follow- ing Table 3. The operating labor cost was calculated depending on the number of units operating in the pro- cess. The number of operators required per shift (NW P) is 3. Which leads to a total number of operators required
4.1 Catalytic Hydration of Ethylene: Other Pro- cesses In order to determine whether the results obtained make sense or not, a comparison between the latter and the results found in the literature will be made. Different catalysts will be mentioned and compared with the one chosen for this project, i.e. zirconium tungstate.
4.1.1 Catalysts Phosphoric Acid
Phosphoric acid supported by inert materials^1 has been used as catalyst in the hydration of ethylene for years and is still the most widely used catalyst in the industry thanks to its high selectivity (98.5%) The phosphorus content of the latter catalyst is between 50 and 80 % in weight of the total mass of the catalyst. The reaction is an electrophilic addition reaction where a π bond is broken, involving the formation of two covalent bonds. The reaction mechanisms involved in this catalytic re- action are the following.
Figure 4
Figure 5
(^1) Materials such as porous silica or alumina-silica.
Figure 6
As described by ( Hidzir, Som, & Abdullah, 2014) and ( Matar & Hatch, 2001), the hydration of ethylene is done in a fixed bed reactor with phosphoric (V) acid coated onto a solid silicon dioxide as a catalyst. The following operating conditions were described:
P (atm) T (°C) Steam to ethylene ratio (S/E) 70 - 80 250 - 300 0. Table 4 – Operating conditions
These operating conditions lead to a conversion of 4% to 5% of the ethylene into ethanol. Therefore, the remain- ing ethylene is recycled into the process. Nevertheless, the high concentration of phosphoric acid has conse- quence such as corrosion of the reactor ( Isobe, Yabuuchi, Iwasa, & Takezawa, 2000). For this reason, Isobe et al. ( Isobe et al., 2000) have studied the influence of phospho- ric impregnated metal phosphate on the conversion of ethylene to ethanol. The reaction takes place in a pack bed reactor at a temperature of 473K and at a pressure of 1 atm. The following results have been obtained:
Catalysts Rate of EtOH formation (μmol/min/g · cat) Ge 0. Zr 0. Ti 0. Sn 0. H3PO4/SiO2 0.
It can be seen that the Sn-based catalyst is the most efficient compared to the classical H 3 PO 4 /SiO 2 cata- lyst. However, and this is one of the reasons why an other catalyst was chosen in our process (Zirconium Tungstate), phosphorous compounds are responsible for environmental pollution (Katada et al., 2008).
Zirconium tungstate
In the article proposed by ( Momose, Kusumoto, Izumi, & Mizutani, 1982), the zirconium tungstate is used as a catalyst for the reaction and the following results were found (see Table 5).
P (atm) T (°C) S/E Selecivity EtOH 68 280 2.1 94 - 99% Table 5 – Results found in the literature
The above tables show the consistency of our results. Indeed, in our case, an ethylene conversion of 9% is reached with a temperature of 246.5°C and a pressure of 60.2atm, which is quite good compared to the literature. The advantages of using such a catalyst are :
The disadvantage is:
The selectivity is around 94-99 mol% if the water/ethy- lene ratio is well chosen.
Corrole − based catalysts
The use of metal-based catalyst in acidic medium for ethanol production has been widespread for a long time. Nevertheless, this type of catalyst has the great defect of conducting secondary reactions leading to undesired products such as diethylether, acetaldehyde, etc... To solve this type of problem, corrole-based cata- lysts are studied (see Figure 7). In the article proposed by ( Hassani, 2020), three types of corrole M (M=B, Al and Ga) were studied by the density functional theory, which is a quantum chemistry theory. The hydration of
ethylene on corrole Ga shows the best results with an energy barrier of 0.93eV. This study shows that these catalysts could be used in ethanol production.
Figure 7 – Corrole molecule
4.2 Comparison with previously obtained results Along time, the calculations became more and more precise.Therefore, it is a good idea to make a comparison with the previously obtained results to understand the evolution of the values obtained. The comparison will be conducted on results obtained before (part 1 of the project) and after receiving the definitive statement of the project (for part 2 and part 4 of the project). The idea is to compare the results obtained when different assumptions are used and when new pieces of data are taken into account (such as the catalyst between part 2 and part 4). The Table 6 gives that comparison over different parameters of the system such as the ethylene conversion (EC), feed flowrate (FF), pressure (P), steam to ethylene ratio (S/E), temperature (T) and reactor volume (RV).
4.3.2 Second generation : Lignocellulosic ethanol in- dustry
This type of fermentation uses lignocellulose as a raw material. It is hydrolysed in order to release the sug- ars necessary for fermentation and therefore, for the production of ethanol. The advent of this type of raw material is mainly due to two factors. First, corn ethanol production is limited to 56,78 bil- lion L/year, this limit ensures that sufficient corn starch remains for human and animal consumption ( of En- ergy, 2019). Second, using cellulose as a feedstock would reduce greenhouse gas emissions by more than 85% compared to reformulated gasoline due to the en- ergy balance ( Wang et al., 2011). Since 2014, POET has launched a lignocellulosic ethanol production line. Figure 9 shows how ethanol is produced from lignocel- lulosic feedstock:
Figure 9 – Diagram of ethanol production from lignocellulosic feedstock
Nevertheless, cellulosic fermentation has disadvantages :
(a) The general agricultural process that includes crops cultivation and transport as well as the production of fertilizers; (^2) Cellulose and hemicellulose combined. (^3) Value allowing to measure the quality of an energy.
(b) The methods, from the literature, used to isolate the carbohydrates.
4.3.3 Third generation: Algae, Bacteria The fermentation is done from algae, bacteria. This type of fuel is still being developed. It would further reduce greenhouse gas emissions because a part of the CO 2 is recycled to feed the algae via photosynthesis. On the other hand, cultivating these algae is highly energy consuming and is thus expensive ( et environnement par sia partners, 2015).
4.3.4 Feedstock origin On a global scale, in 2014, the majority of biofuel was made from corn ethanol (41%), 19% of the biofuel was made with sugarcane ethanol, 18% of the biofuel pro- duced was biodiesel made from vegetable oils, 15% of the global biofuel production came from unspecified feedstock (ethylene,...), and finally, 2% of the biofuel produced was made from wastes. Figure 10 shows these data in a more graphical way (Richter, 2018).
Figure 10 – Shares of bioethanol and biodiesel types from different feedstock in global biofuel production in 2014
4.4 Comparison of all processes From a cost perspective, corn ethanol is the cheapest with a production cost of $0.15/L ( Koehler & Wilson,
the other hand, the costs distribution for dry-milling is 50/50. Second-generation fuels are more expensive with a production cost of $0.5/L ( Mark, Detre, Darby, & Salassi, 2014). Pre-processing accounts for 30-40% of the cost, which is why the costs are higher.
The price of raw materials has an impact on the pro- duction costs. Indeed, the price of corn or cotton does not vary in the same way as the ethylene price, which is linked to the oil court and therefore varies more strongly. Moreover, the geographical location impacts a lot the ethylene price as can be seen in Table 7 below (Lewandowski, 2019):
USA Europe Ethylene Price per ton ($) 350 1000 Table 7 – Ethylene price
In addition, access to raw materials such as corn, cotton, wood is easier than for ethylene, produced either from oil or from shale gas. It should be noted that some reaction by-products can be valued. Indeed, concerning the corn fermentation, in addition to ethanol production, oil can be recovered and used as food. The ethanol production by direct catalytic hydration of ethylene allows the production of diethylether (DEE) in small quantities but still valuable.
The above mentioned processes also have different yields. Concerning the first generation fuel, from 2.28kg of corn 1L of ethanol is obtained. For second generation fuels, the yield depends on the type of hydrolysis. For instance, if hydrolysis is made by a diluted acid, 1L of ethanol if obtained per 5.29kg of raw material, which is quite big compared to the first generation fuel. ( Hoover & Abraham, 2009) Table 8 summarizes the various points discussed above.
4.5 Ethanol overview 4.5.1 Market
The ethanol market is broken down as follows (Source: Mordor Intelligence) :
Figure 11 – Distribution of ethanol market
The biofuels market is the largest, followed by the bever- ages, chemical, pharmaceutical and cosmetics markets. The two largest producers of bioethanol are the USA and Brazil with, respectively, 60.780 and 29.980 billion litres produced in 2018. ADM and POET are two major bioethanol manufacturing companies in the USA. In Brazil, the Cosan company dominates the bioethanol market (Figure 12). Concerning synthetic ethanol, there are companies such as Sasol in South Africa or SADAF in Saudi Arabia.
Figure 12 – Distribution of ethanol production. Source: Statista
The biofuel market is buoyant. Indeed, it is part of an ecological reasoning, allowing to reduce greenhouse
Environment
Concerning the environmental impact of ethanol pro- duction from corn fermentation, there are several points which are needed to talk about(rethink ethanol, n.d.) :
When ethanol is produced by the ethylene hydration, the energy consumption is 62 megajoules per kilogram of produced ethanol. On the other hand, ethanol pro- duction from natural raw materials, despite its disad- vantages, needs only 19 megajoules per kilogram of produced ethanol. If, for a certain reason, the produced ethanol is unsaleable, the need to recycle the ethanol becomes necessary (OCDE, 2000).
4.5.4 Recycling
There are two different ways to recycle this solvent:
The main advantages of custom regeneration are ( Tradebe, n.d.-a):
Concerning the solvent elimination, the transportation of the ethanol can be done via a tanker or a hybrid vehicle(Tradebe, n.d.-b). The solvent elimination process is made of the following steps (Tradebe, n.d.-b) :
4.5.5 Ethanol alternatives If there are problems with ethanol such as shortage , finding alternatives to ethanol can be a good thing.
4.5.6 In the case of Bioethanol Using butanol (e. ramey, n.d.) can be an alternative for biofuels. Using ethanol in fuels to make E85 will damage the car engines if those aren’t adapted to the bioethanol(rethink ethanol, n.d.). Some of the advantages by switching from ethanol to butanol can be (e. ramey, n.d.) :
A life-cycle assessment, or LCA, is a methodology for assessing environmental impacts associated with all the stages of a product’s life from cradle to grave. For in- stance, in the case of a manufactured product, it covers a range of activities from the extraction of raw mate- rials (cradle), through the production and distribution of energy, manufacture and use of the product, to the recycling or final disposal of materials composing it (grave).
LCA study involves a thorough inventory of the energy and materials required across a process and assesses the corresponding emissions to the environment. Therefore, the goal of this tool is to improve the overall environ- mental profile of a product by helping decision makers to compare the impacts when choosing between differ- ent options. Moreover, it helps to support policy and to optimise a process. In this project, we decided to focus the LCA analysis on three main parts of the cycle of ethanol production from ethylene hydration :
Nowadays, the United States is the major producer of ethanol in the world with more or less 55% of the total production ( Demmon, 2019). Therefore, the production unit is chosen as being located in the USA. Moreover, the analysis is performed based on the annual production designed to produce 30 000 tons of ethanol. The re- sults obtained for the environmental impacts associated with all the stages of ethanol production are evaluated thanks to a simulation software called Simapro and will be expressed for the production of 1kg of ethanol. The databases are Ecoinvent and the impact assessment method is CML-IA baseline V3.05. Different hypotheses will be put throughout the devel- opment of this life-cycle assessment. So, it has to be taken as a tool intended to get an order of magnitude of the environmental impacts and not a precise evaluation.
5.1 Raw material supply In this part, the impacts of the procurement of raw ma- terials are studied. The process considered is ethanol
production via direct hydration of ethylene. Water and ethylene are the two main reactants used in this pro- cess. Therefore, environmental impacts for ethylene and water production are evaluated.
5.1.1 Ethylene In order to evaluate the environmental impact of ethy- lene production, it is important to study the way ethy- lene is produced and the raw materials used in this process. First, it is assumed that ethylene production comes from steam cracking. This method consists of heating the naphta fraction of oil, in the presence of water vapor (around 30 to 100 % by weight) to obtain compounds such as ethylene, propylene, etc which are precious for the chemical industry. In this case, only ethylene is valuable. To get an idea, at the output of the unit, with a charge of naphtha, one has a yield of about 25 % to 30 % of ethylene. Concerning the steam cracking, oil, steam and the en- ergy needed are all taken into account for the LCA analysis. In the ethanol production unit, 25 870 tons of ethylene with a purity of 86% are needed each year. All calcula- tions corresponding to the production of it will be made with respect to this value.
5.1.2 Water The ethanol production unit is a big consumer of water. Indeed, a huge amount of water is used as a raw mate- rial. As said previously, this plant is based on ethanol production via direct hydration of ethylene and has a ra- tio 1:15 between the molar fluxes of ethylene and water at the entrance of the process. Each year, 246 000 tons of pure water are needed as reactant in the process. Most of the time, water used for industrial activities is taken from groundwater, rivers or lakes, often by the industrial operator himself. Let’s say that in our case, the ethanol production unit is right next to one of these water sources. Once withdrawn, the water is said to be "raw". It is sometimes used as such but is gener- ally subjected to a treatment (disinfection, clarification, ...) before use and especially when it is used as a raw material in the process. Finally, before industrial wastewater can be discharged into the environment, it must be subjected to purifica-
5.4 Environmental impacts
The environmental impacts associated with all the stages of the ethanol production are evaluated thanks to the simulation software Simapro and will be expressed for the production of 1kg of ethanol. Nowadays, the world is in an energy transition phase towards renewable en- ergies. Therefore, it can be interesting to compare the environmental impacts of two different factories, one producing electricity with fossil fuels and another with wind turbines. It was decided to focus this analyse on five impact categories :
The impact of the process on the main pollution factors is shown in the Table 10. This makes the comparison between the use of wind turbines or fossil fuels to pro- duce electricity. All data have been calculated for the equivalent of 1 kg of ethanol produced.
Label Unit Wind turbines
Fossil fuel
Abiotic depletion (fossil fuels)
Global warming (GWP100a)
kg CO 2 eq 1.45^ 2.
Human toxi- city
kg 1,4-DB eq 0.056^ 0. Fresh water aquatic eco- toxicity
kg 1,4-DB eq 0.032^ 0.
Acidification kg SO 2 eq 0.004^ 0. Table 10 – Comparison of the environmental impacts between two same process using wind turbine or fossil fuel to produce electricity.
A first observation is that producing electricity by wind turbines has a much less impact on the environment. Furthermore, regarding the Figures 15 and 16, the rela- tive % of energy recovered from the waste stream of the process (purge) is much more important when wind tur- bines are used as the environmental impacts decrease. It should be noted that the environmental impacts linked to the construction of the wind turbines are not taken into account for the life cycle analysis of the process.
Figure 15 – Electricity produced from fossil fuels
Figure 16 – Electricity produced from wind turbines
Now, regarding the environment, it makes more sense to work by producing electricity from wind turbines. This model is thus chosen for the process.
Then, to get an idea of the real impact of the process on the environment, a comparison between our process and a typical one of ethanol production from the soft- ware Simapro has been done in the Table 11. The data of the table have all been computed for a production of 1 kg ethanol with a purity equal to 82%.
Label Unit Process with Wind turbines
Typical process from Simapro Abiotic depletion (fossil fuels)
Global warming (GWP100a)
kg CO 2 eq 1.45^ 0.
Human toxi- city
kg 1,4-DB eq 0.056^ 0. Fresh water aquatic eco- toxicity
kg 1,4-DB eq 0.032^ 0.
Acidification kg SO 2 eq 0.004^ 0. Table 11 – Comparison of the environmental between the process and a typical one from the software Simapro.
From the Table 11, one notices several relevant infor- mation about our process :
5.4.1 Conclusion To conclude this LCA, based on the comparison between the environmental impacts between our process and a typical one from the software Simapro, it can be consid- ered that the ethanol unit production developed in this
administration, U. E. I. (2019). Where our natural gas comes from. (Link) Alcen, F. (2019). États-unis : une production électrique record en 2018. (Link) Balat, M., Balat, H., & Öz, C. (2008). Progress in bioethanol processing. Progress in energy and combustion science, 34 (5), 551–573. Britton, R. A. (1972, August 22). Direct hydration of ethylene to ethanol. Google Patents. (US Patent 3,686,334) Caballero, B., Trugo, L. C., & Finglas, P. M. (2003). Ency- clopedia of food sciences and nutrition. Academic. Chan, J. H., & Reiner, D. (2018). Dynamics of evolution in the global fuel-ethanol industry. Conca, J. (2018). Which is safer for transporting crude oil: Rail, truck, pipeline or boat? Forbes. Curran, M. (2008). Life-cycle assessment. Academic Press. Demmon, A. (2019, march). World ethanol production. (Link) e. ramey, D. (n.d.). Butanol: The other alternative fuel. et environnement par sia partners, E. (2015). Perspec- tives pour les biocarburants de 3ème génération. https://energie.sia-partners.com/perspectives- pour-les-biocarburants-de-3eme-generation. (Accessed on 1 st^ May 2020) Ethanol t2 fob rotterdam including duty swap platts fu- ture. (n.d.). (Link, Accessed: 2020-04-18) for Biotechnology Information, N. C. (n.d.). Ethanol (compound). https://pubchem.ncbi .nlm.nih.gov/compound/ethanol. Frenzel, P., Hillerbrand, R., & Pfennig, A. (2014). Increase in energy and land use by a bio-based chemical industry. Chemical Engineering Research and Design, 92 (10), 2006 - 2015. Retrieved from http:// www.sciencedirect.com/science/ article/pii/S026387621300542X (Green Processes and Eco-technologies) doi: https://doi.org/10.1016/j.cherd.2013.12. Gray, K. A., Zhao, L., & Emptage, M. (2018). Bioethanol. Current opinion in chemical biology, 10 (2), 141–
Hassani, N. (2020). The reaction mechanism of the hydration of ethylene over the corrolem (m= b, al, and ga) complexes: A theoretical approach. Com- putational and Theoretical Chemistry, 112766.
Hidzir, N. S., Som, A., & Abdullah, Z. (2014). Ethanol pro- duction via direct hydration of ethylene: a review. In International conference on global sustainability and chemical engineering (icgse). Hoover, F.-A., & Abraham, J. (2009). A comparison of corn-based ethanol with cellulosic ethanol as replacements for petroleum-based fuels: a review. International Journal of Sustainable Energy, 28 (4), 171–182. Isobe, A., Yabuuchi, Y., Iwasa, N., & Takezawa, N. (2000). Gas-phase hydration of ethene over me (hpo4) 2· nh2o (me= ge, zr, ti, and sn). Applied Catalysis A: General, 194 , 395–401. Katada, N., Iseki, Y., Shichi, A., Fujita, N., Ishino, I., Os- aki, K.,... Niwa, M. (2008). Production of ethanol by vapor phase hydration of ethene over tungsta monolayer catalyst loaded on titania. Applied Catalysis A: General, 349 (1-2), 55–61. Koehler, N., & Wilson, C. (2019). 2019 ethanokl industry outlook. Lewandowski, S. (2019). Ethylene–golobal. In Asia chem. conf. Mark, T. B., Detre, J. D., Darby, P. M., & Salassi, M. E. (2014). Energy cane usage for cellulosic ethanol: estimation of feedstock costs and comparison to corn ethanol. International Journal of Agricultural Management, 3 (2), 89–98. Martel, F. (2011). Bioéthanol : cap sur la 2ème génération. https:// www.bioethanolcarburant.com/ nos_dossiers/bioethanol-cap -sur-la-2eme-generation/. (Accessed 12th April 2020) Matar, S., & Hatch, L. F. (2001). Chemistry of petrochem- ical processes. Elsevier. M.Ghanta, B., D.Fahey. (2013). Environmental impacts of ethylene production from diverse feedstocks and energy sources. Mohsenzadeh, A., Zamani, A., & Taherzadeh, M. J. (2017). Bioethylene production from ethanol: A review and techno-economical evaluation. Chem- BioEng Reviews, 4 (2), 75–91. Momose, H., Kusumoto, K., Izumi, Y., & Mizutani, Y. (1982). Vapor-phase direct hydration of ethylene over zirconium tungstate catalyst: I. catalytic be- havior and kinetics at atmospheric pressure. Jour- nal of Catalysis, 77 (1), 23–31. New capacities, weaker downstream markets to weigh on ethylene in 2020. (n.d.). (Link, Accessed: 2020-04-
OCDE. (2000). Le développement durable. Sciences Technologie Industrie, 1999 (2), 99. of Energy, U. D. (2019). Ethanol feedstocks. (Link) Olsson, L. (2007). Biofuels (Vol. 108). Springer. Perrin, S. (2020). Ethylène-l’elémentarium. (Link) rethink ethanol. (n.d.). http:// rethinkethanol.com/. (Accessed 7th April 2020) Richter, E. (2018). Biofuels - a contribution assessment for the global energy transition integrating aspects of technology, resources, economics, sustainabil- ity and alternative options (Doctoral dissertation). doi: 10.13140/RG.2.2.29087. Roozbehani, B., Mirdrikvand, M., Moqadam, S. I., & Roshan, A. C. (2013). Synthetic ethanol produc- tion in the middle east: A way to make environ- mentally friendly fuels. Chemistry and Technology of Fuels and Oils, 49 (2), 115–124. Roozbehani, B., Moqadam, S. I., Mirdrikvand, M., & Roshan, A. C. (2012). Modeling direct ethylene hydration over zirconium tungsten catalyst: Fun- damental of ethanol production using the biggest global ethylene feeding pipeline in iran. Energy and environment research, 2 (2), 28. Shen, Y., Chen, B., & van Beek, T. A. (2015). Al- ternative solvents can make preparative liquid chromatography greener. Green Chem., 17 , 4073-4081. Retrieved from http://dx.doi .org/10.1039/C5GC00887E doi: 10 .1039/C5GC00887E Statista. (2020). Crude oil production in the united states in 2019, by state. ( ) Tradebe. (n.d. -a). Régénération à façon – fabrication sous contrat. https:// www.tradebesolventrecycling .com/fr/regeneration-facon -fabrication-sous-contrat. (Ac- cessed 7th April 2020) Tradebe. (n.d.-b). Élimination de solvants. https:// www.tradebesolventrecycling .com/fr/elimination-de -solvants. (Accessed 7th April 2020) Wang, M. Q., Han, J., Haq, Z., Tyner, W. E., Wu, M., & Elgowainy, A. (2011). Energy and green- house gas emission effects of corn and cellulosic ethanol with technology improvements and land use changes. Biomass and Bioenergy, 35 (5), 1885–
Whiting, W., Shaeiwitz, J., Bhattacharyya, D., Turton, R., & Bailie, R. (2013). Analysis, synthesis, and design of chemical processes. Pearson. Wikipedia. (2020). Énergie éolienne aux États-unis.