
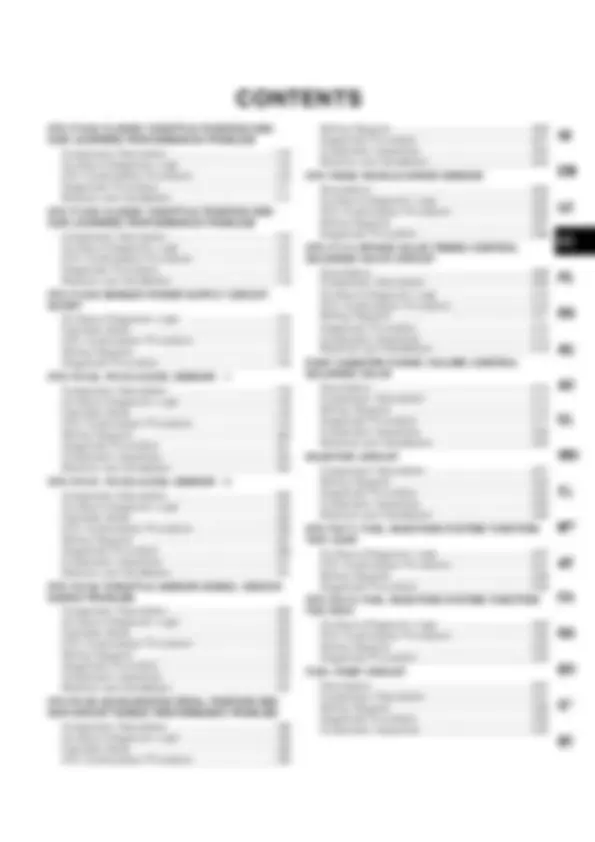
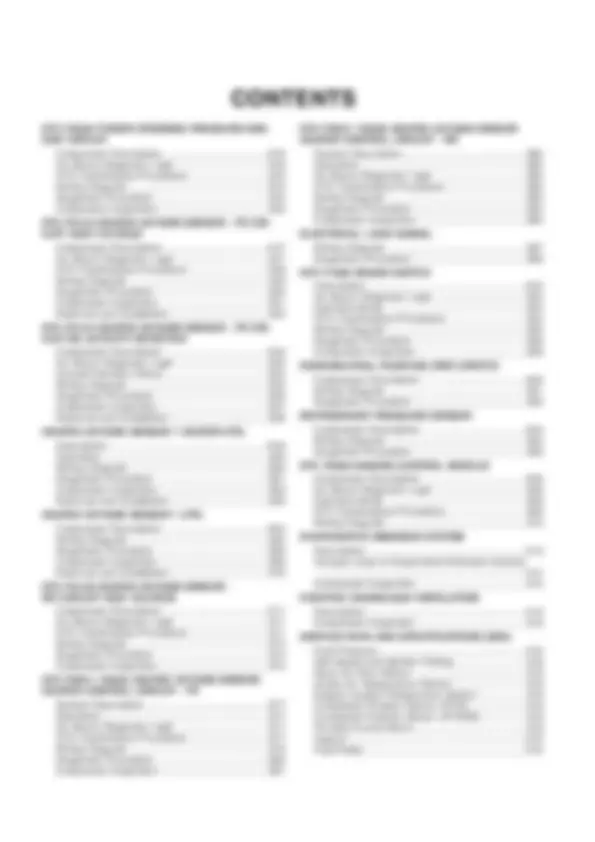
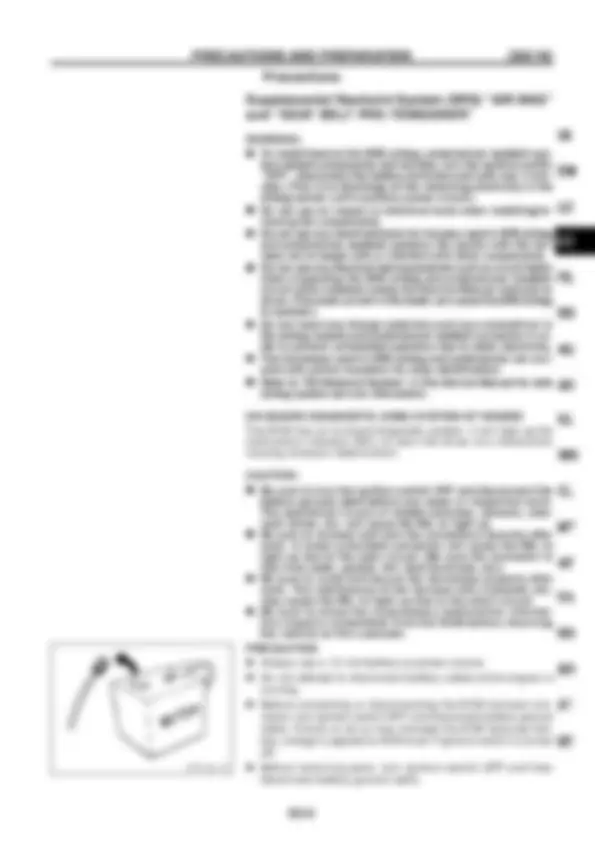
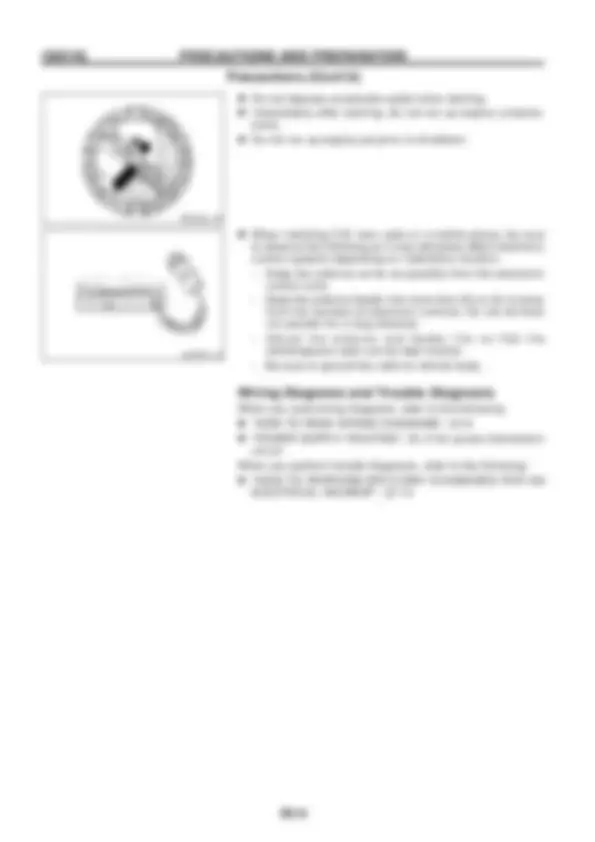
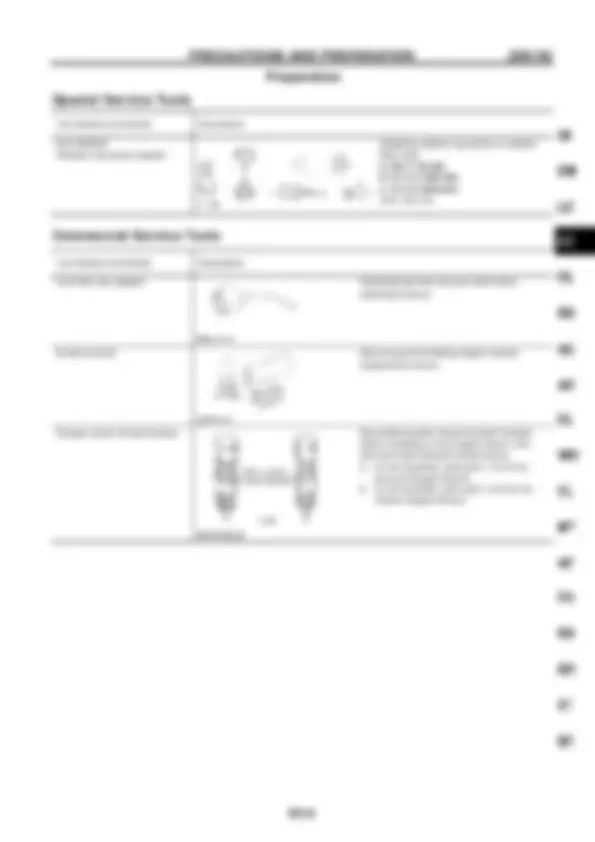
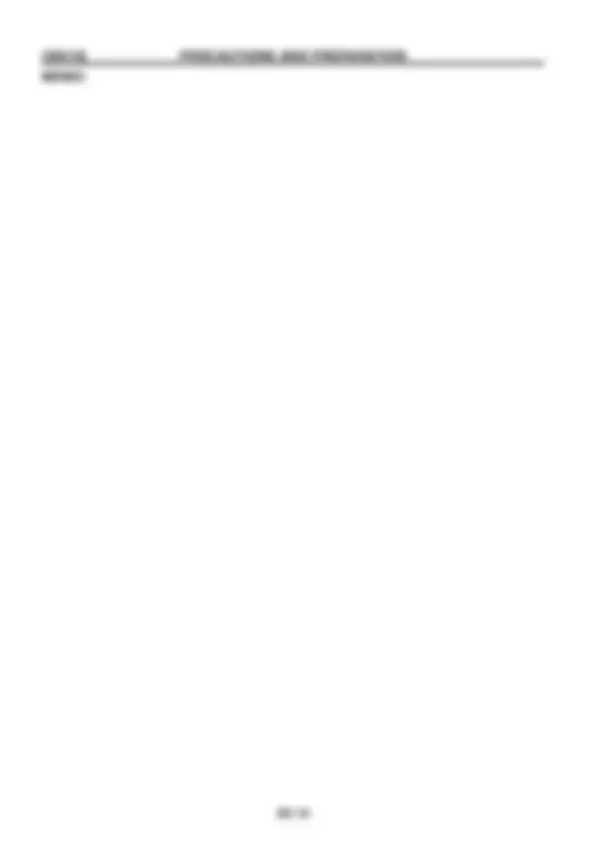
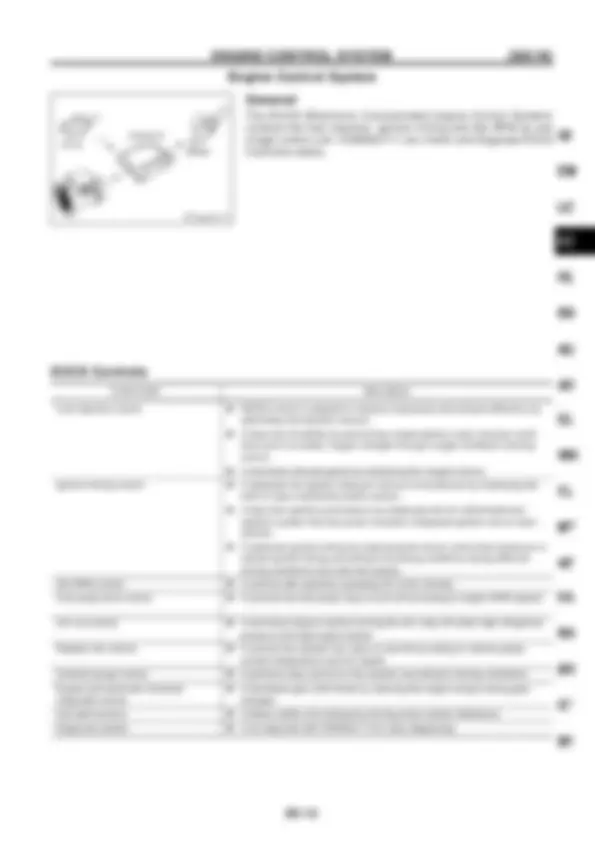
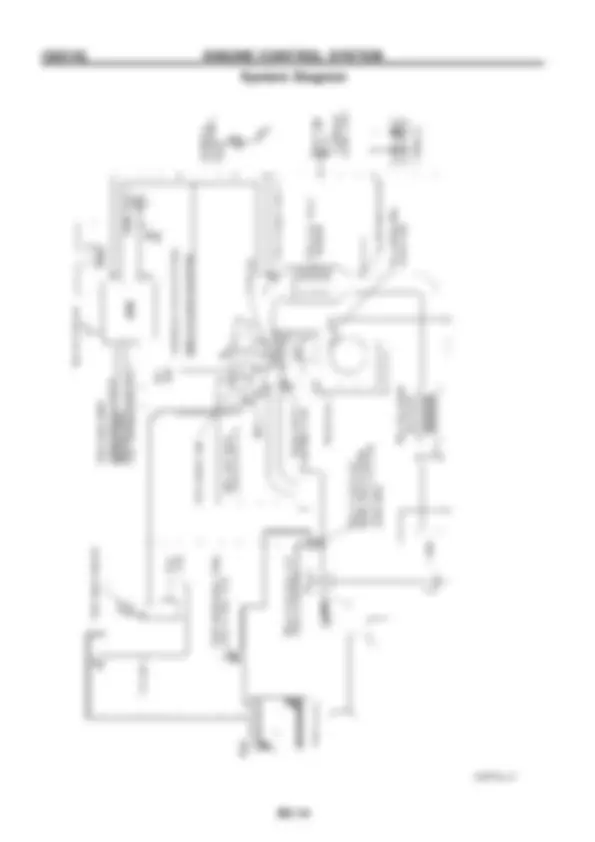
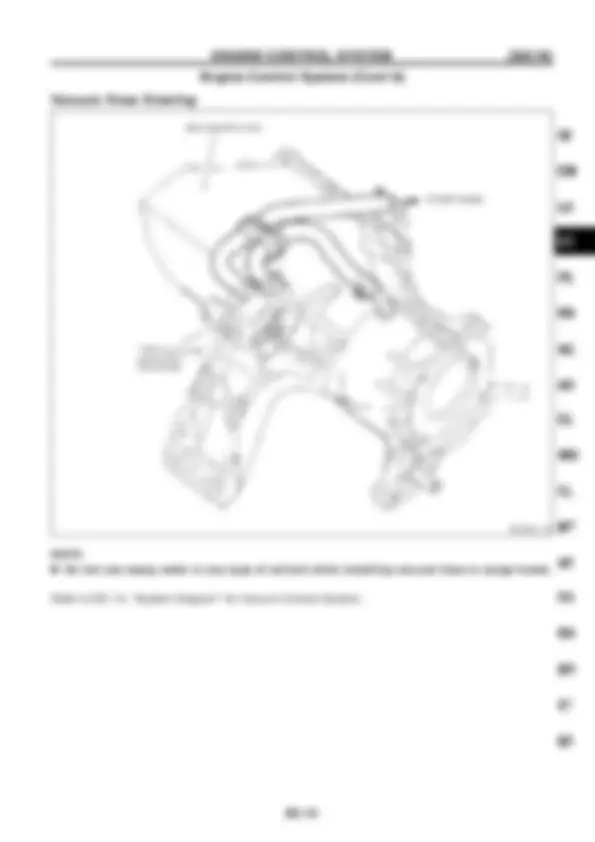
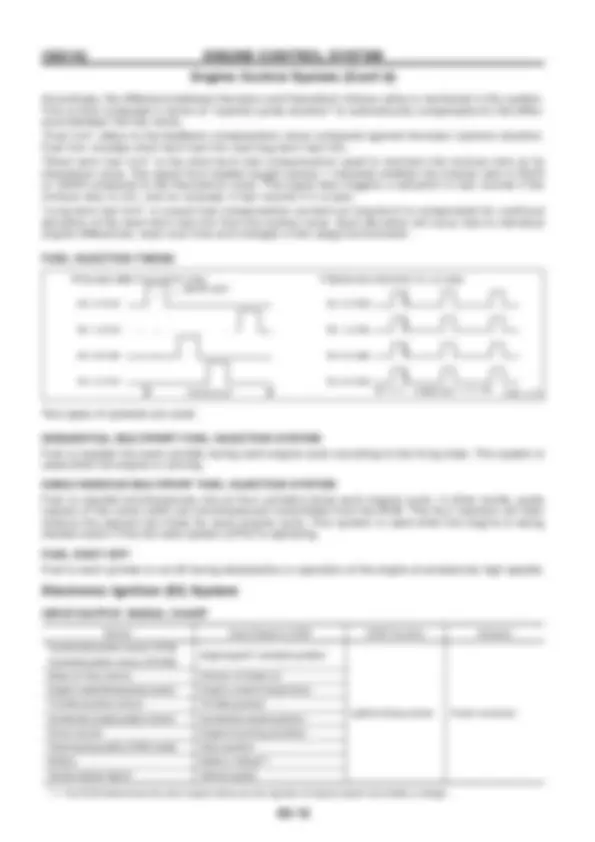
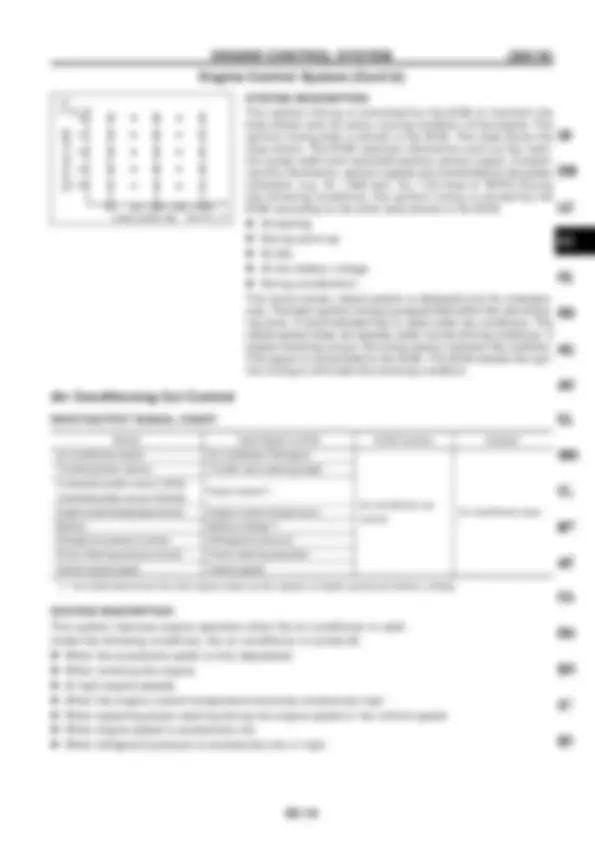
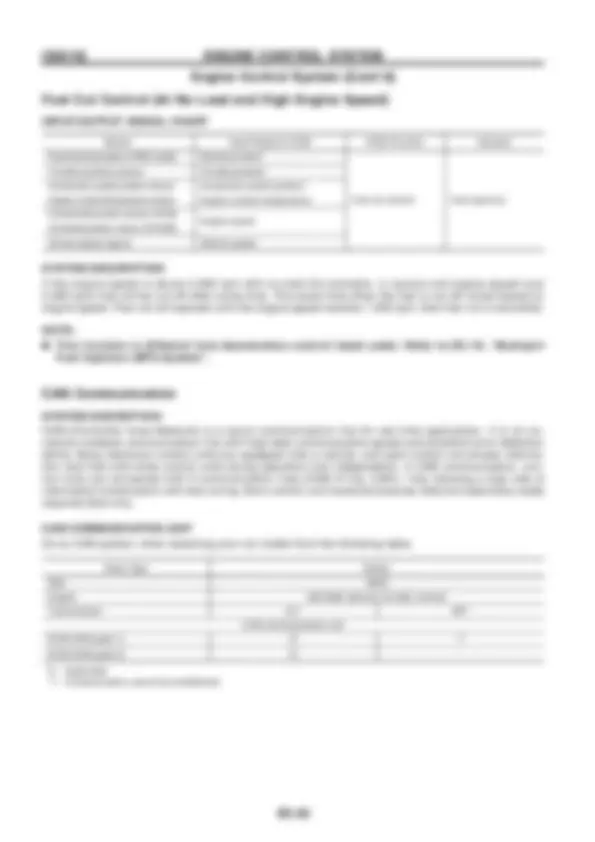
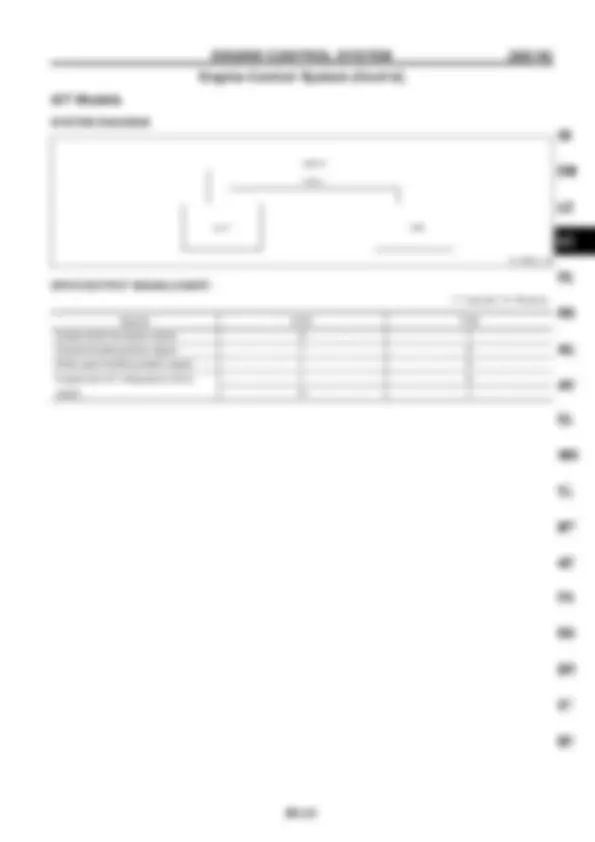
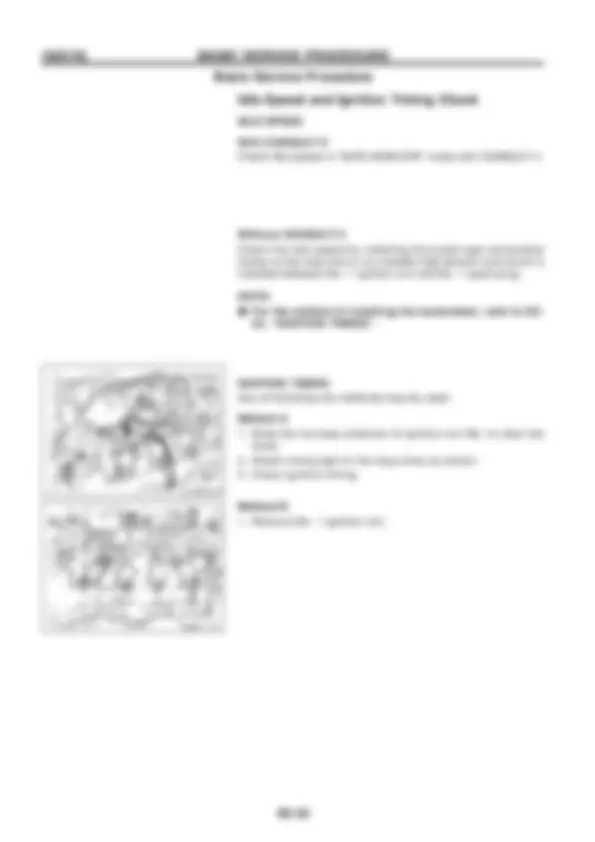
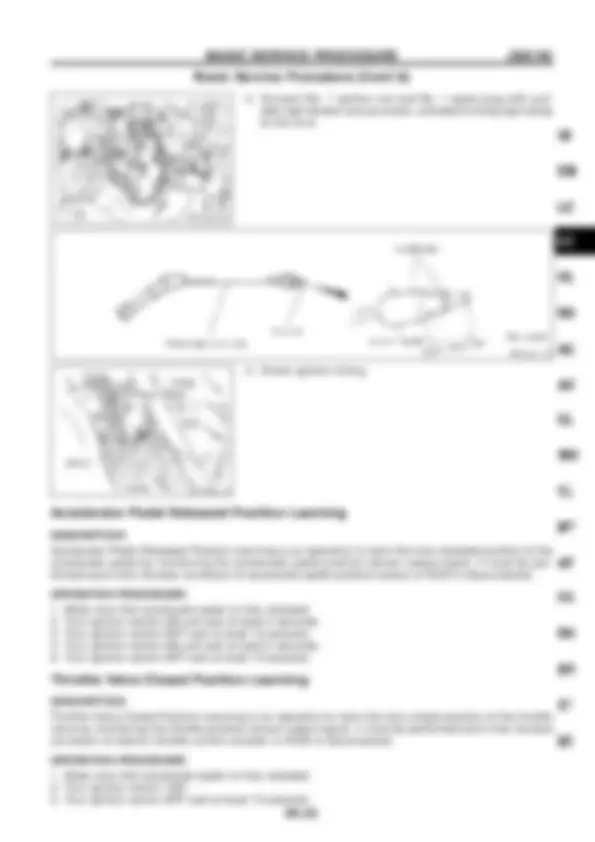
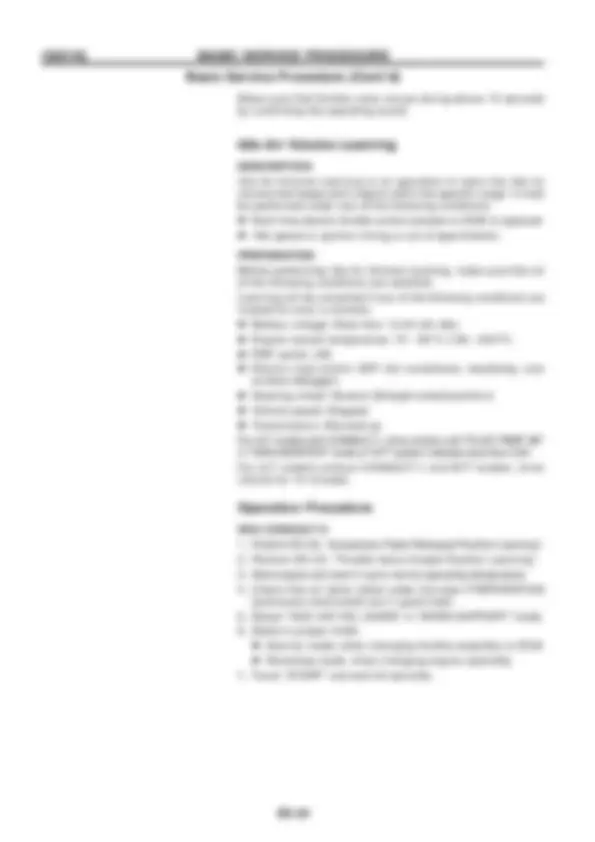
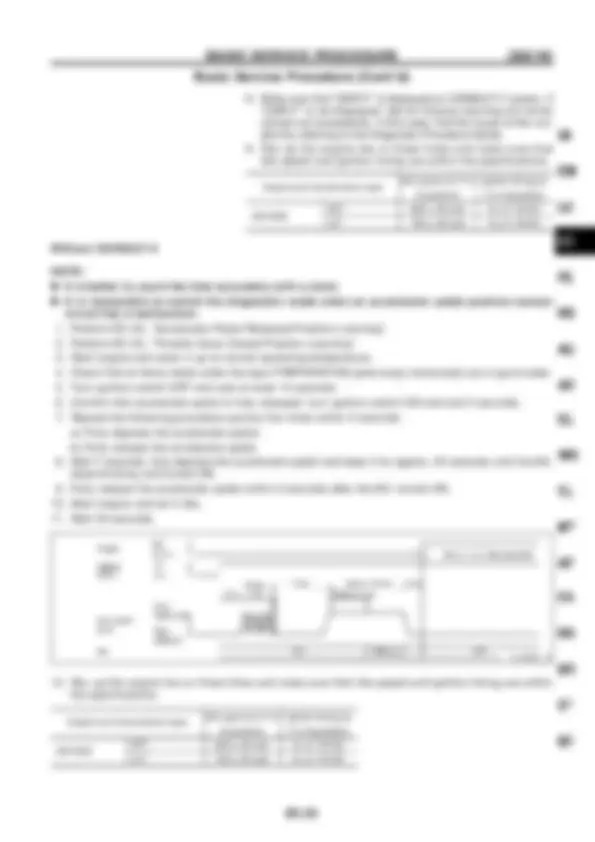
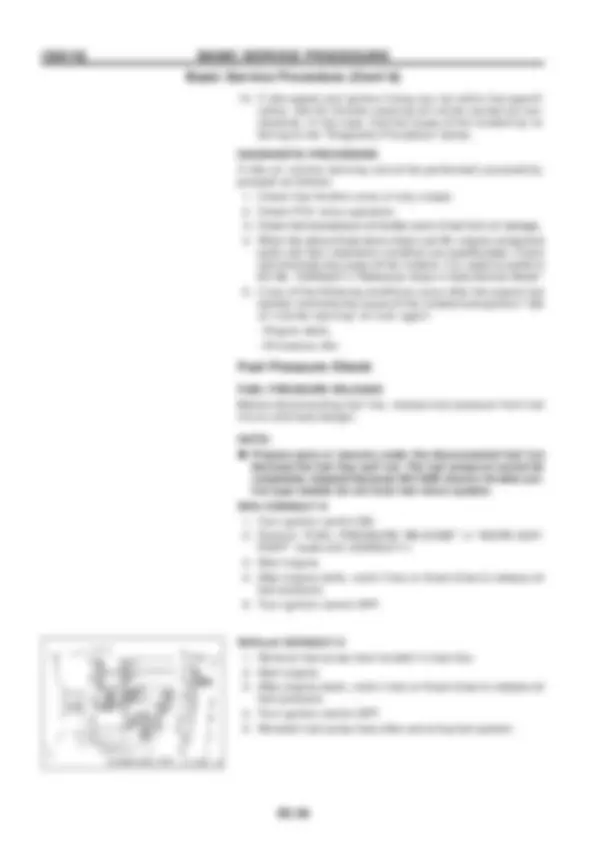
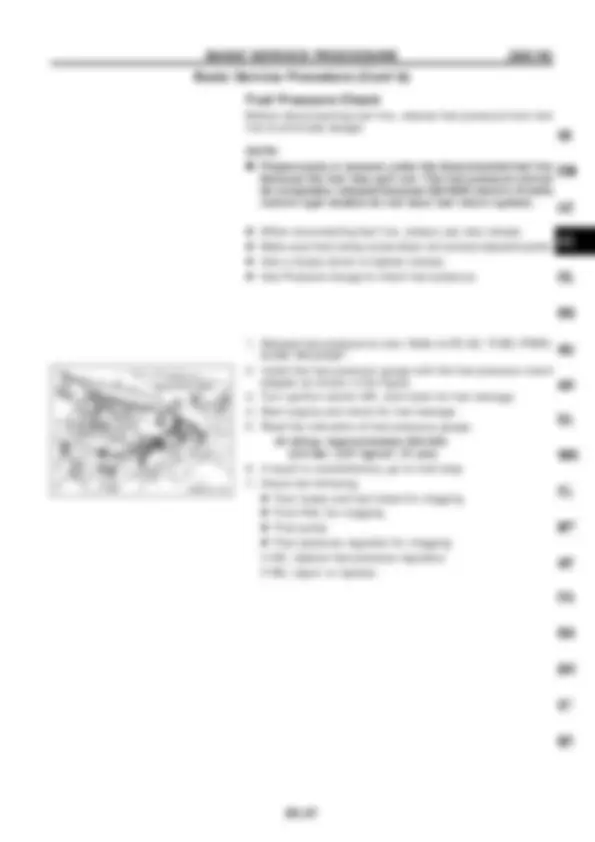
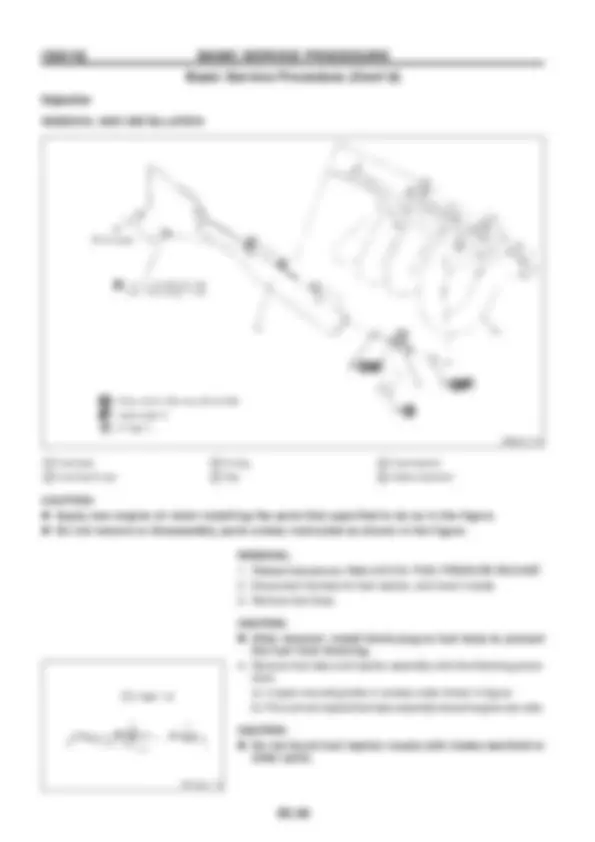
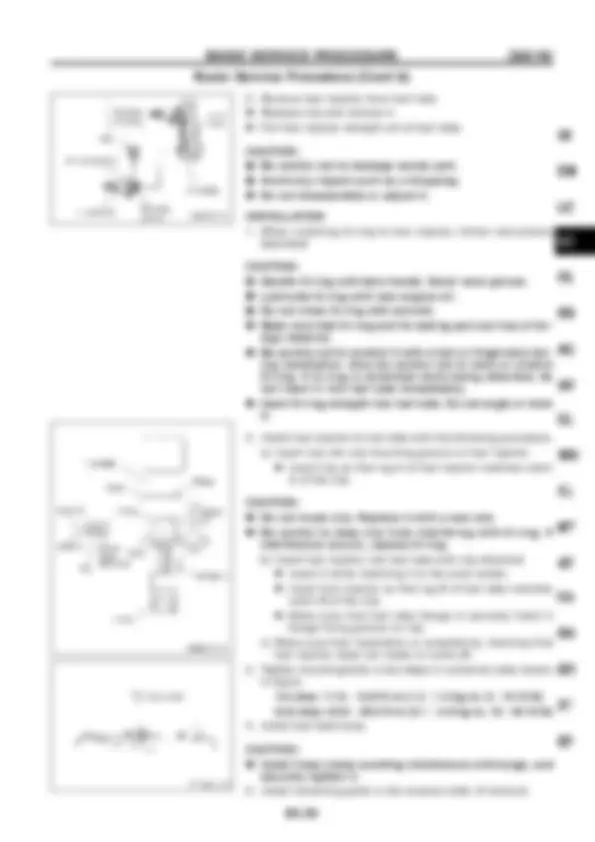
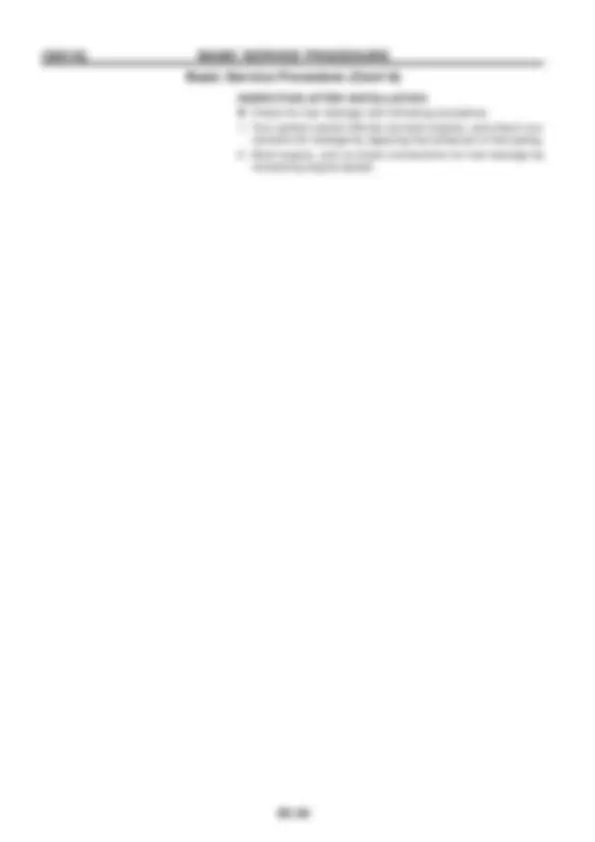
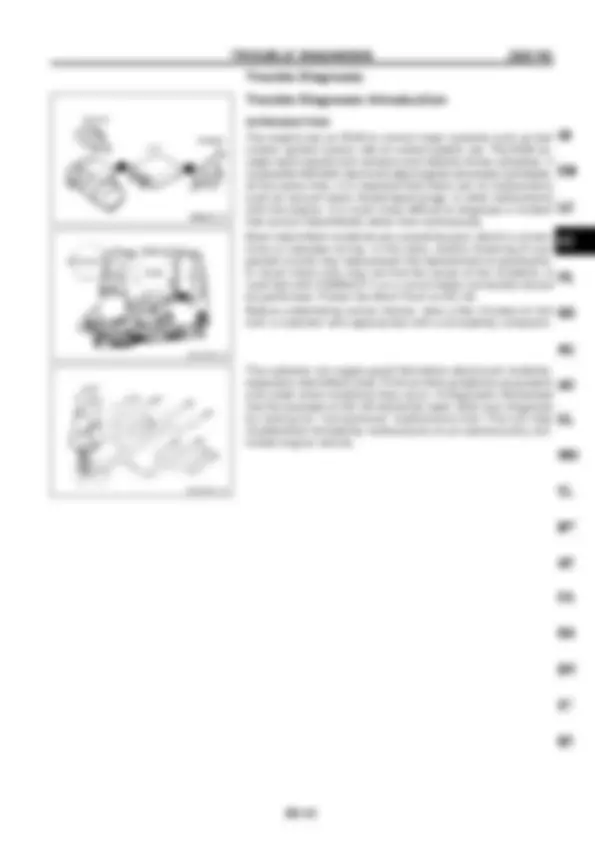
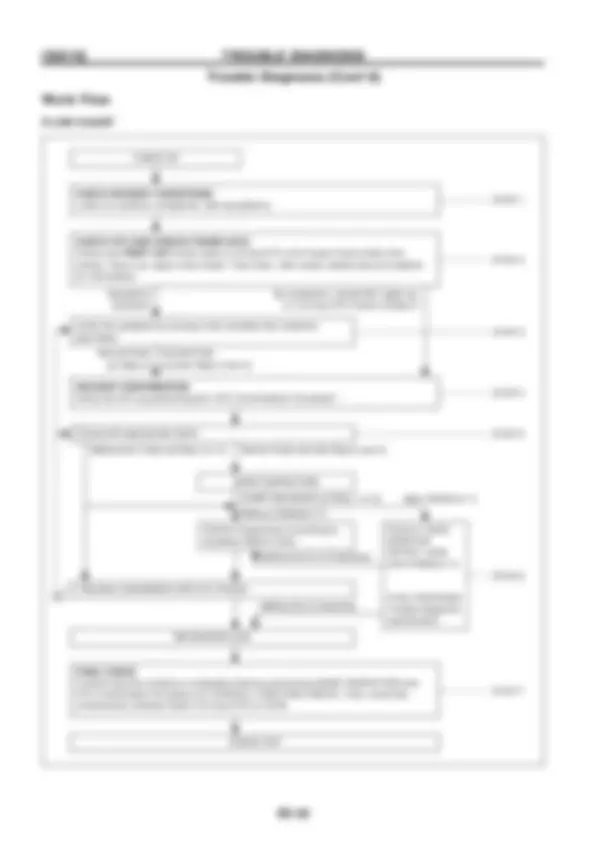
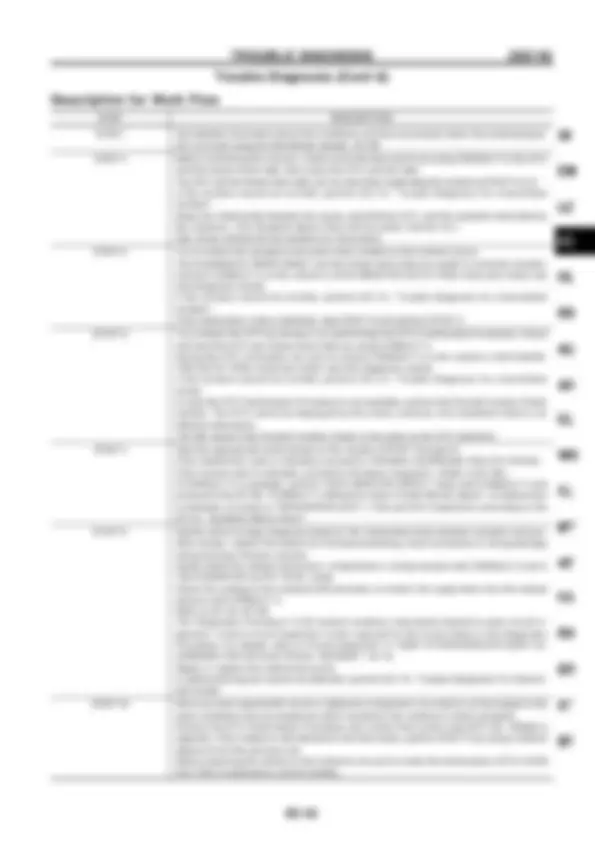
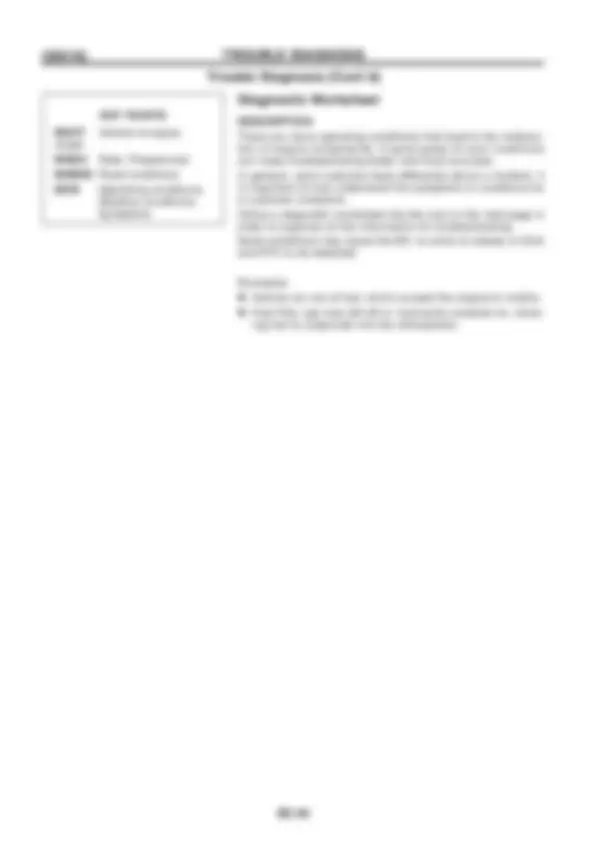
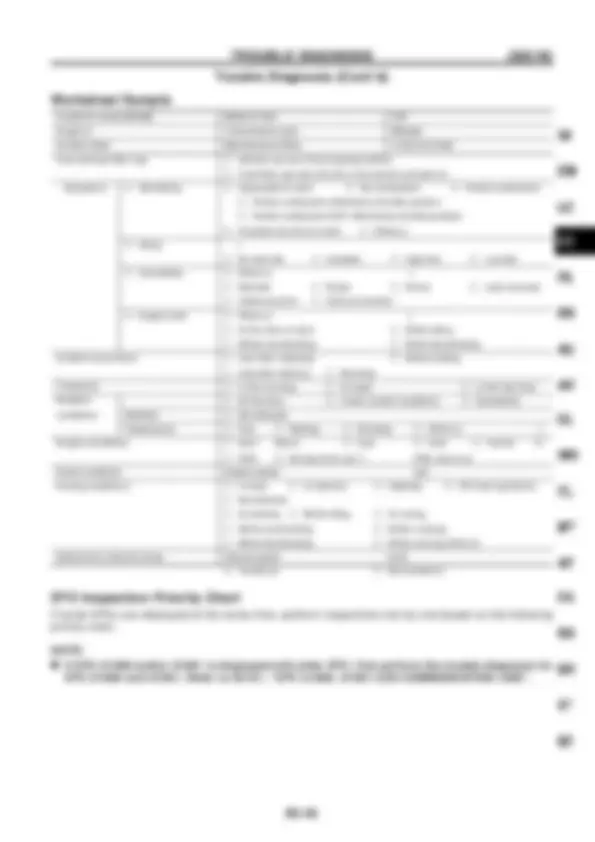
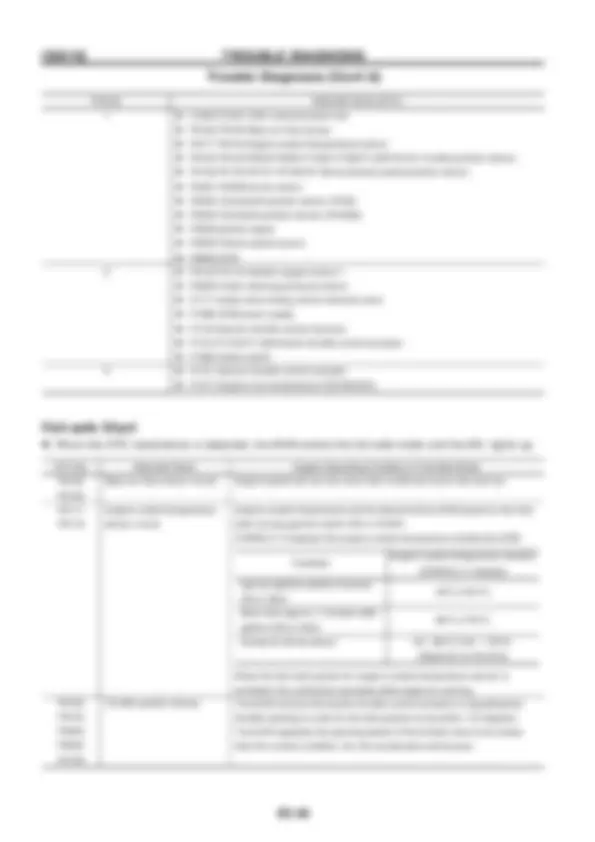
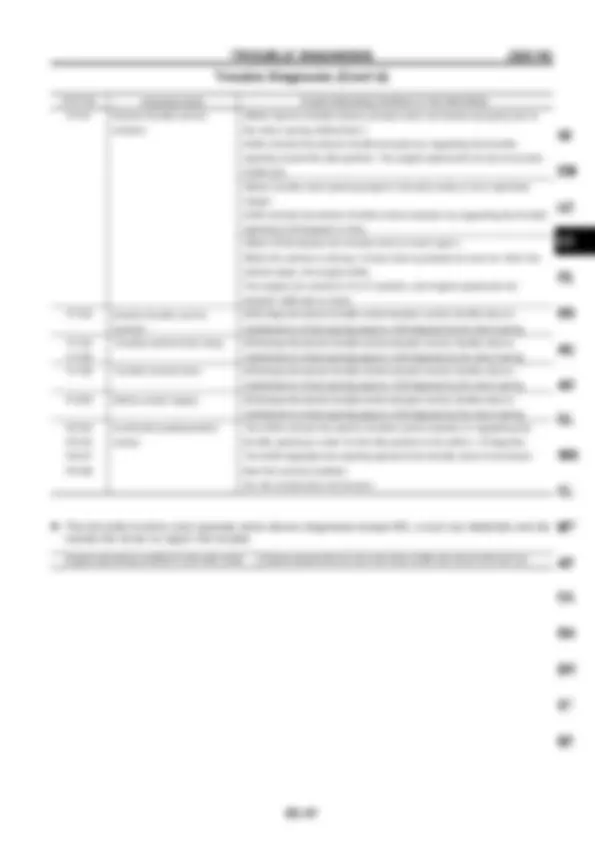
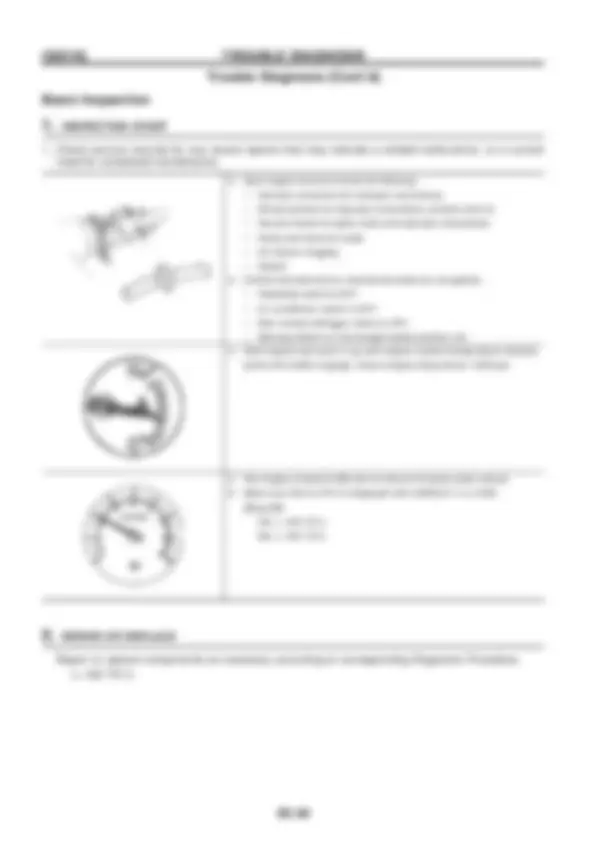
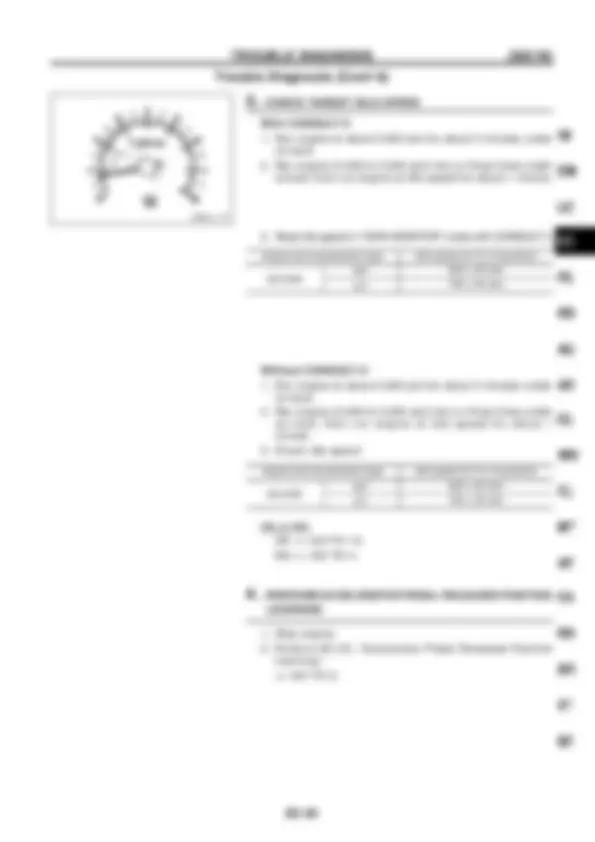
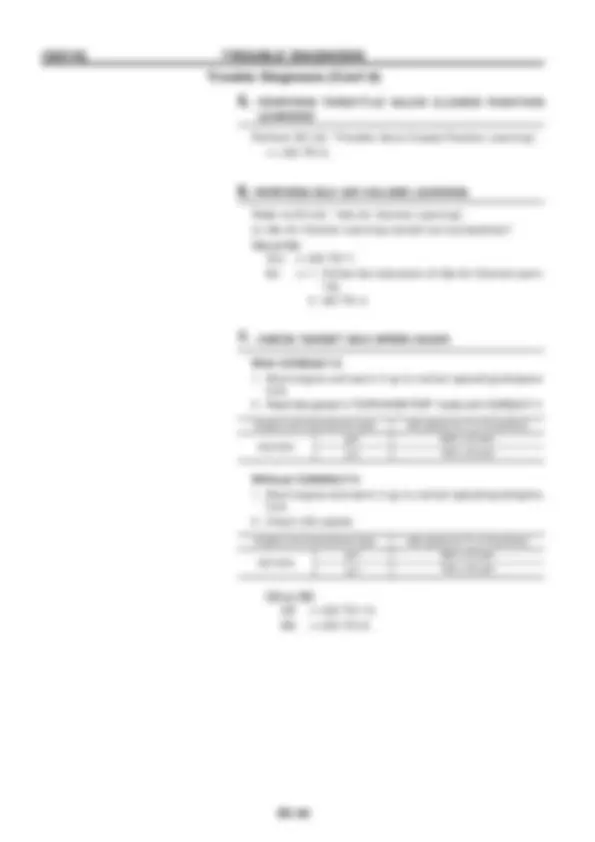
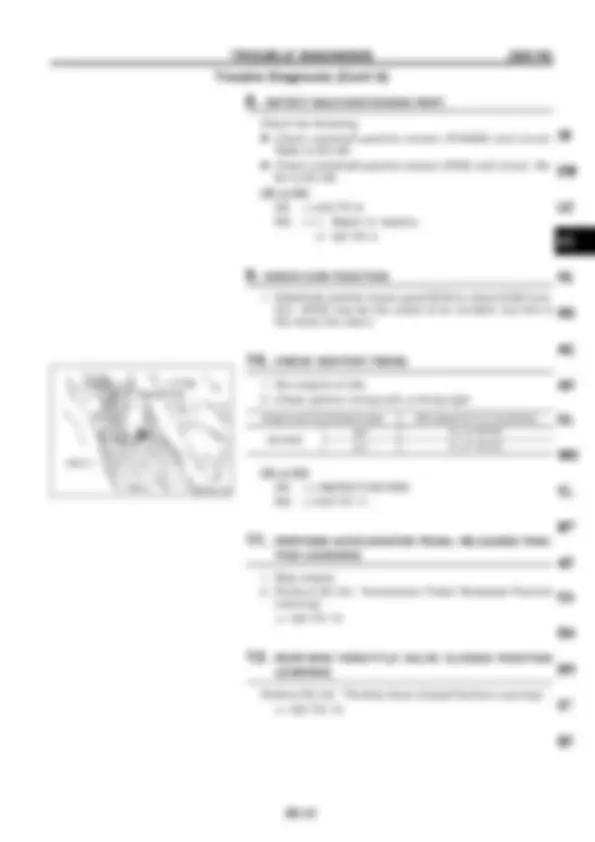
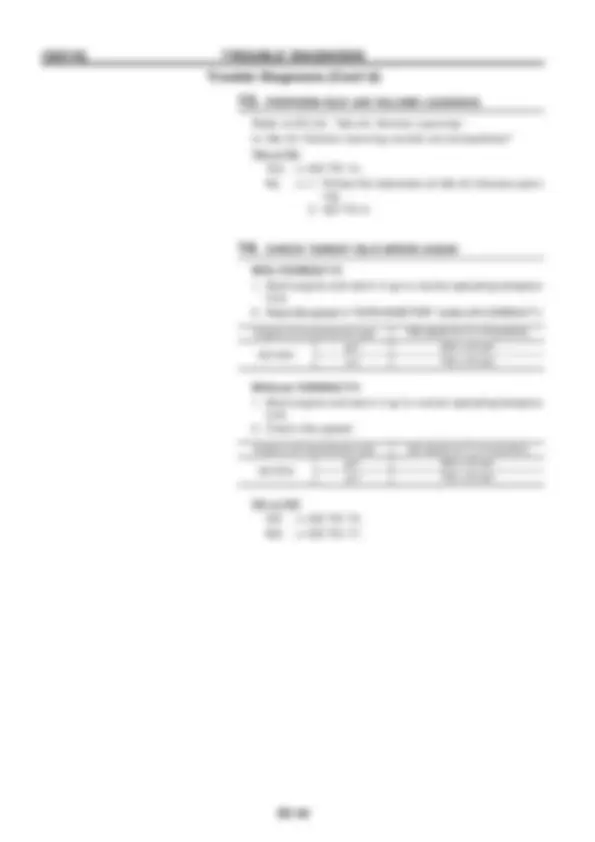
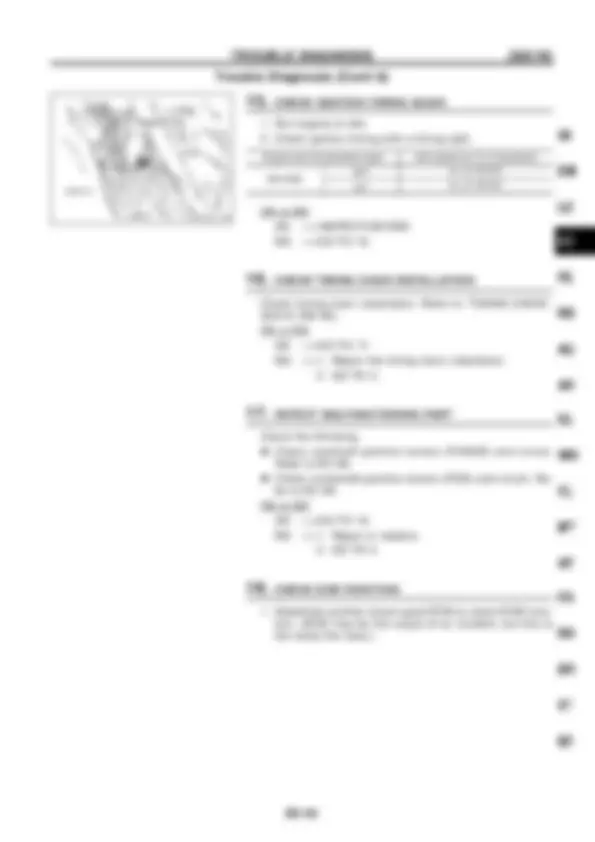
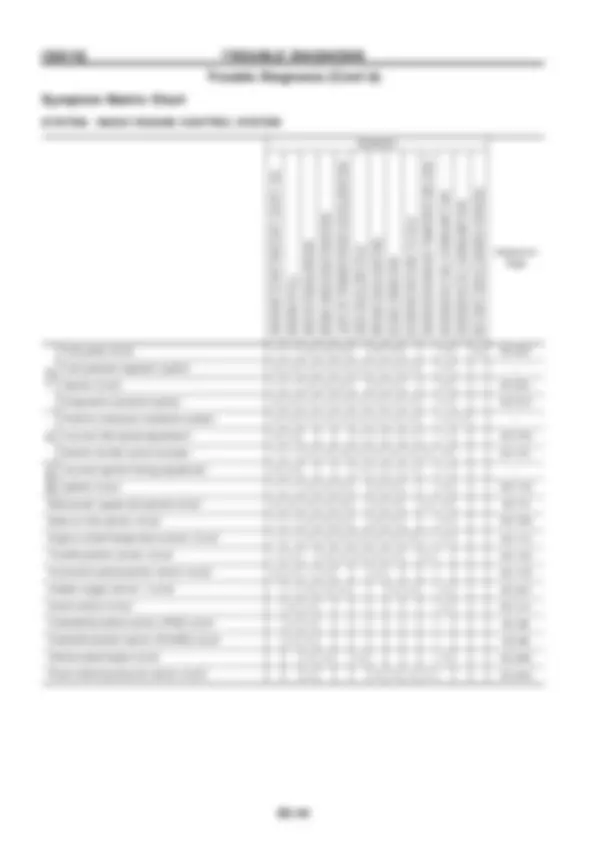
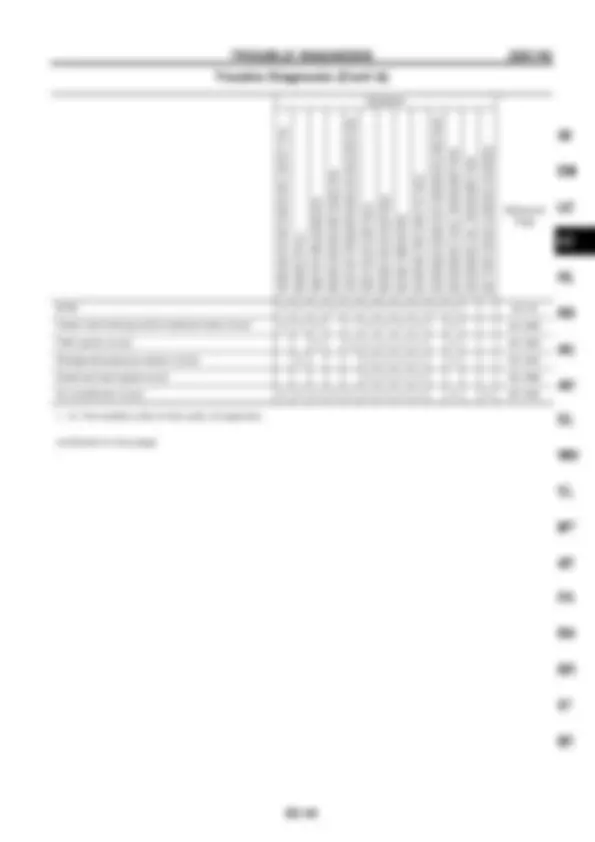
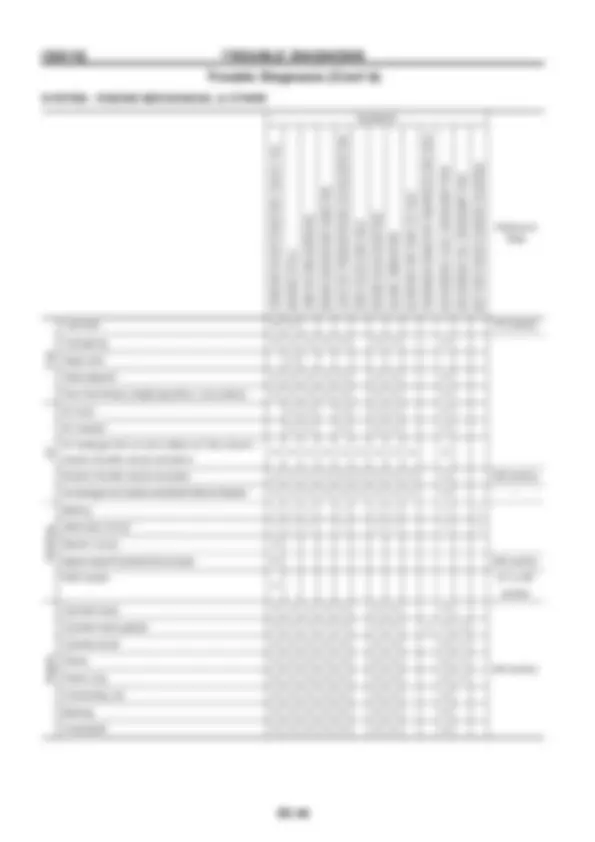
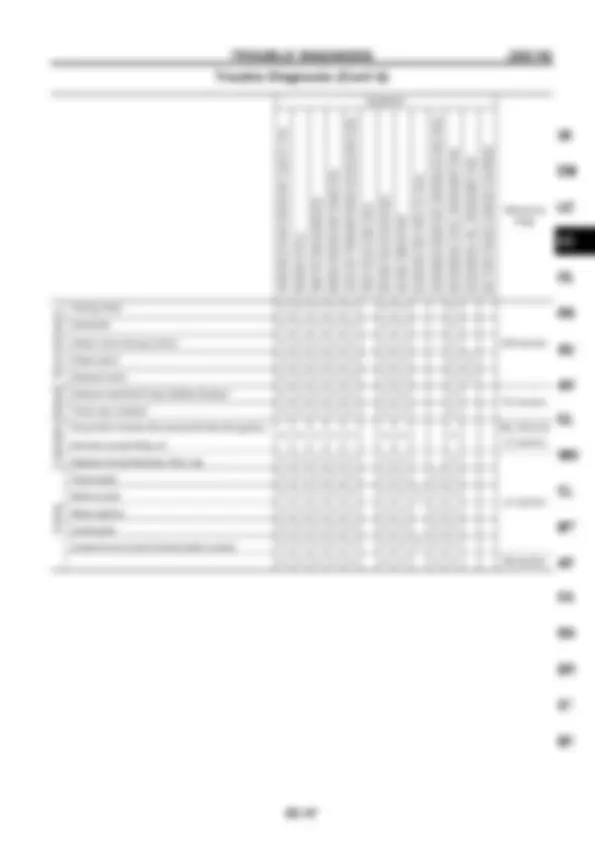
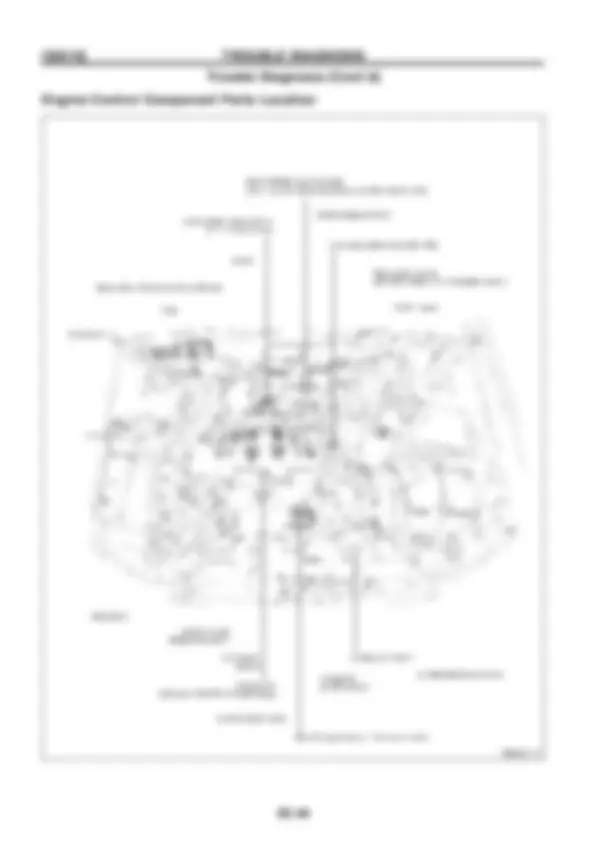
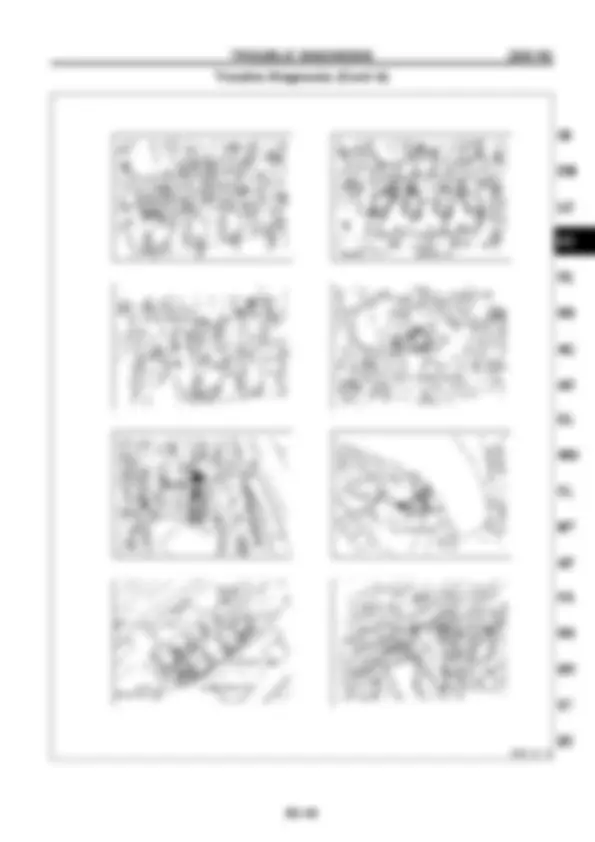
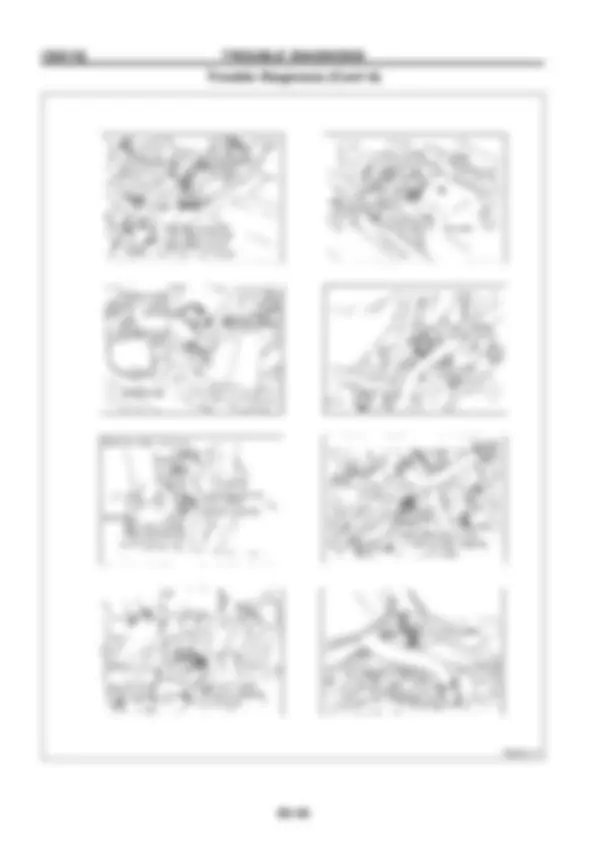
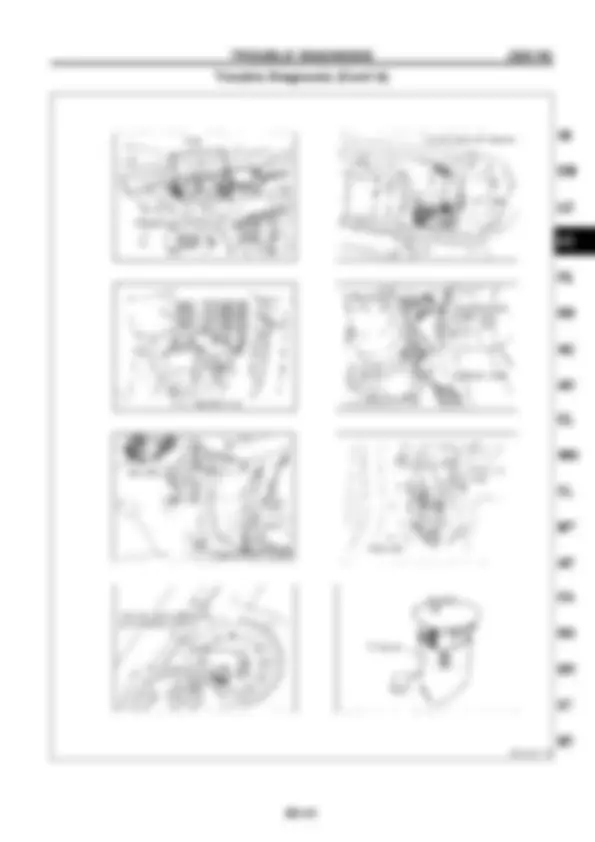
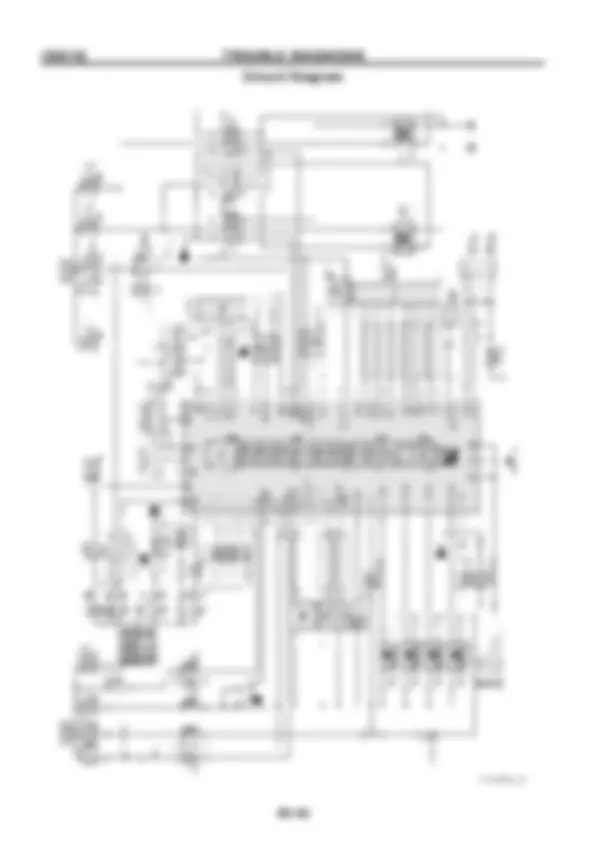
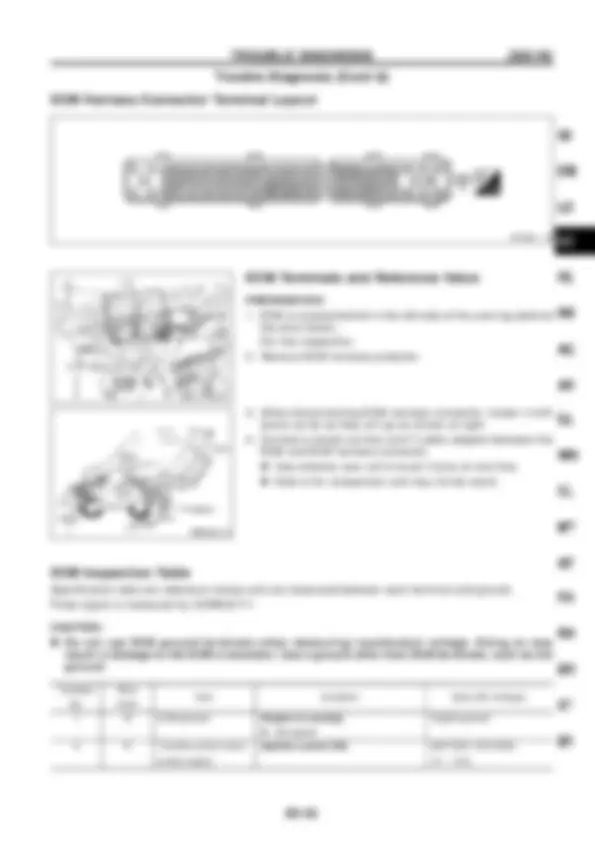
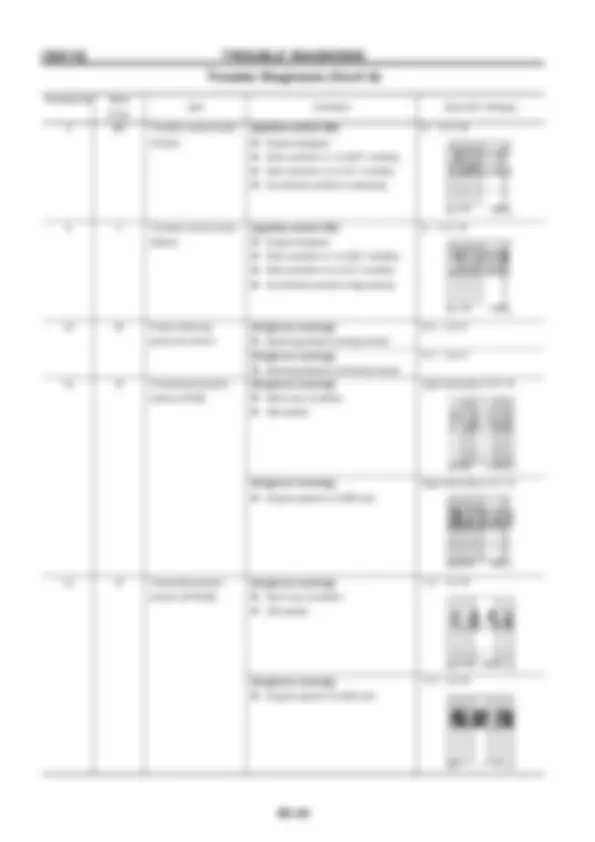
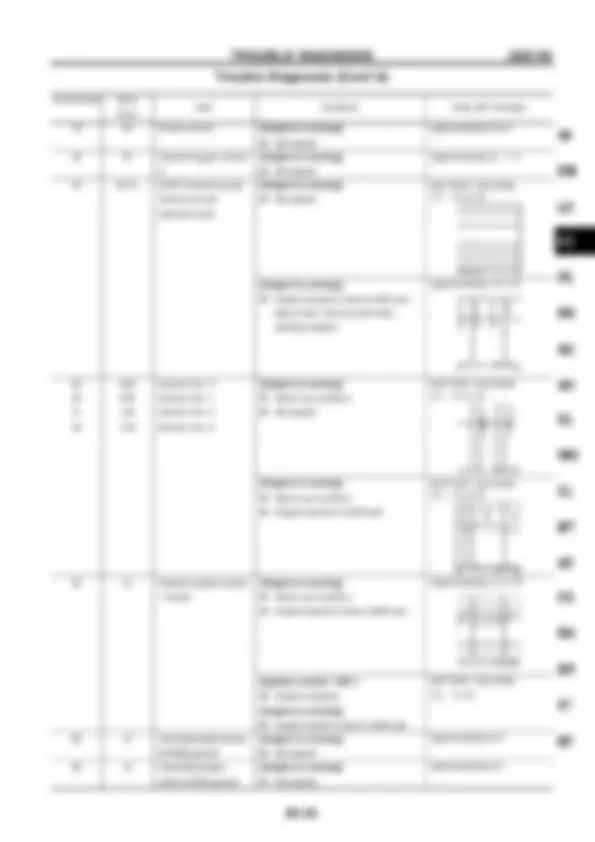
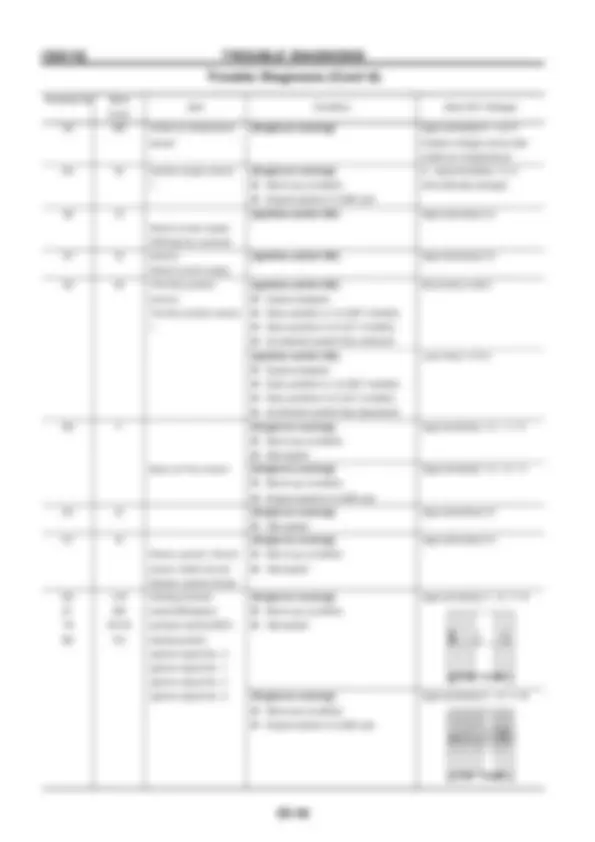
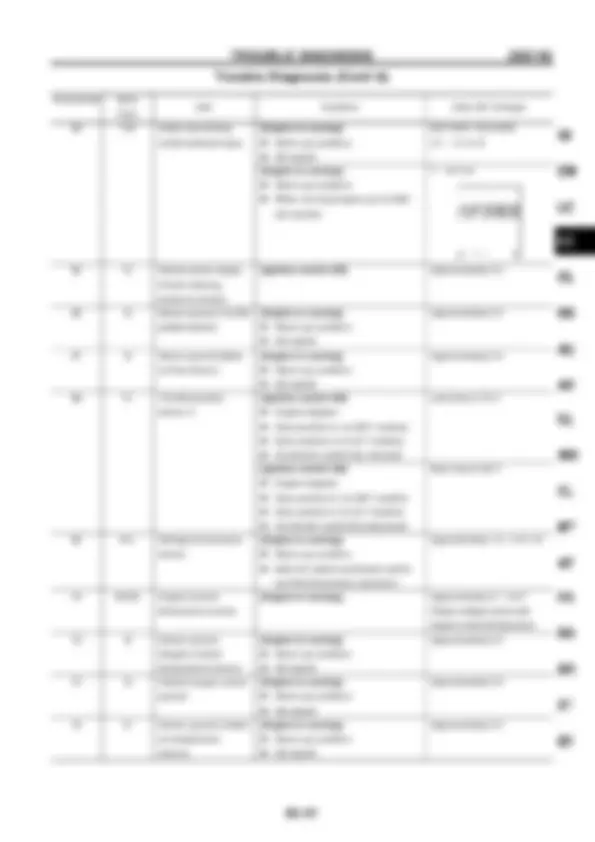
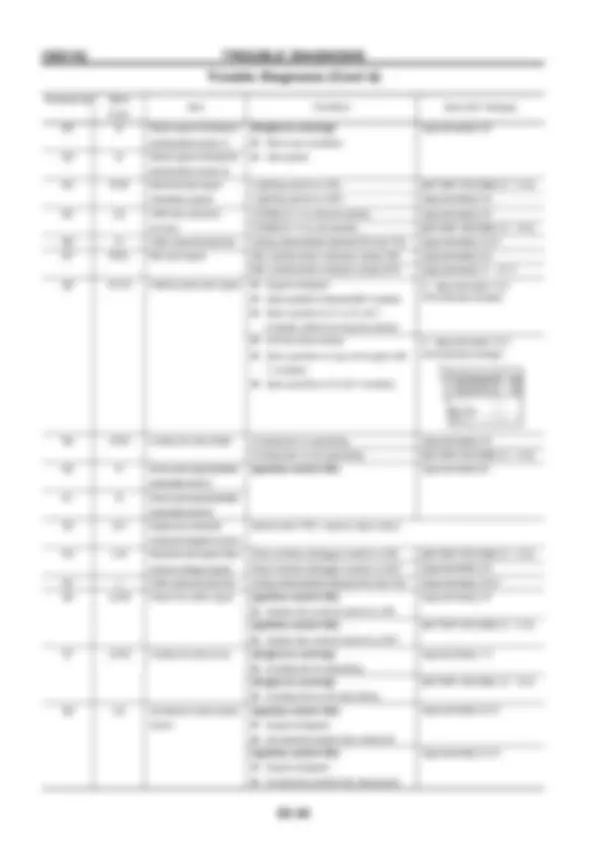
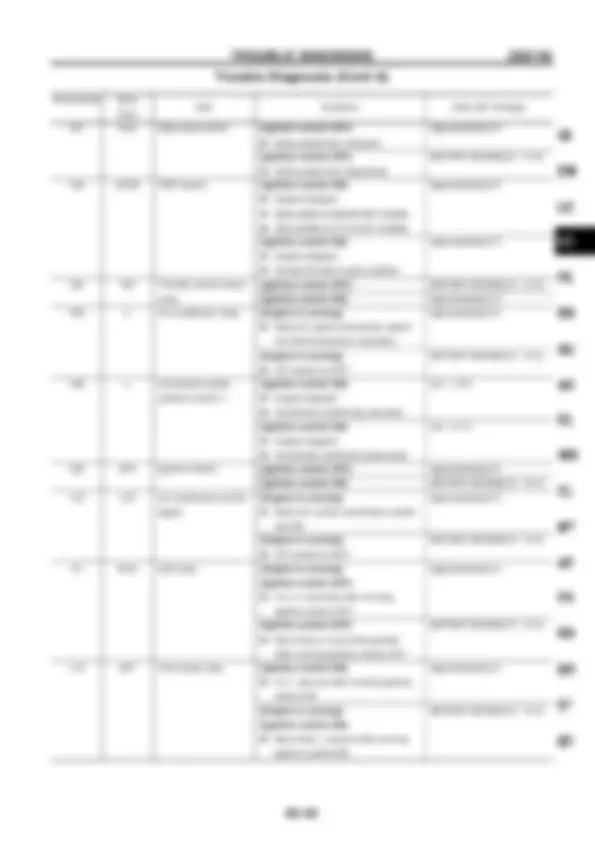
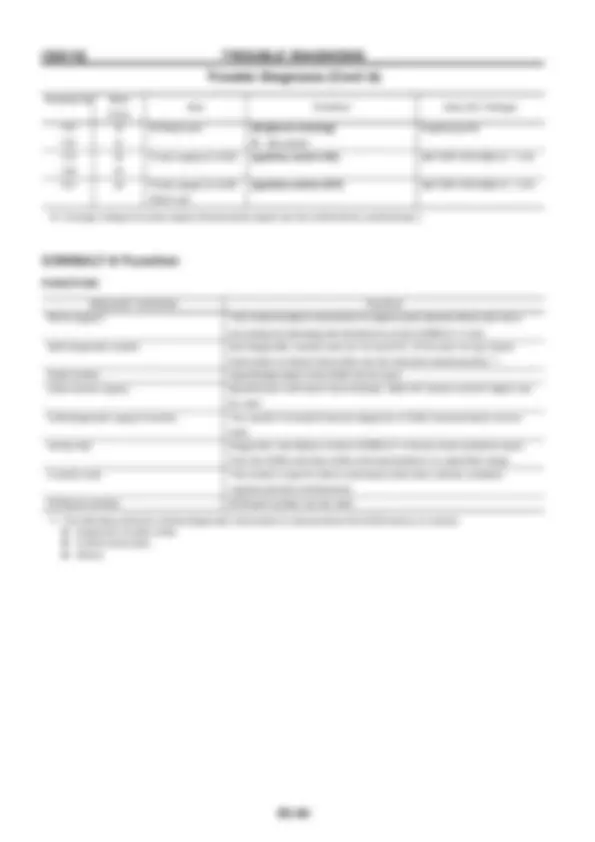
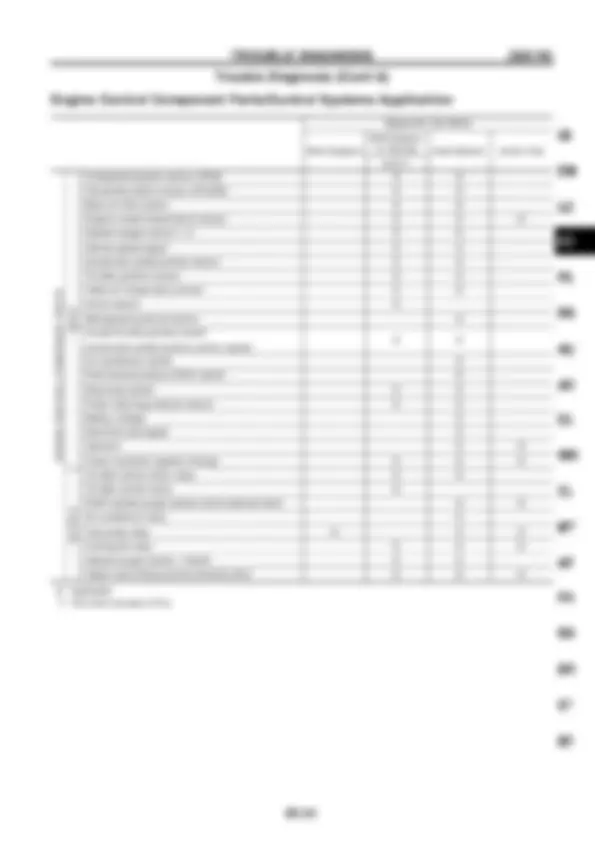
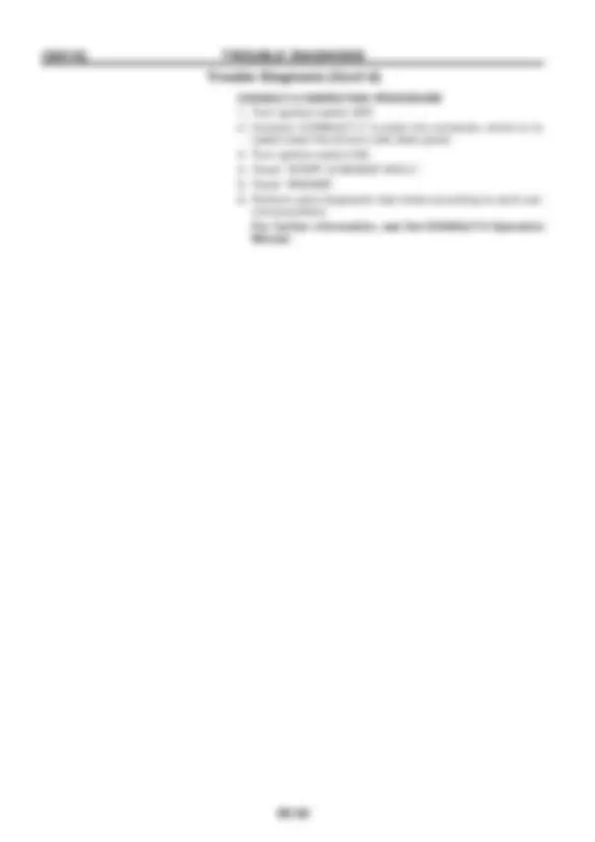
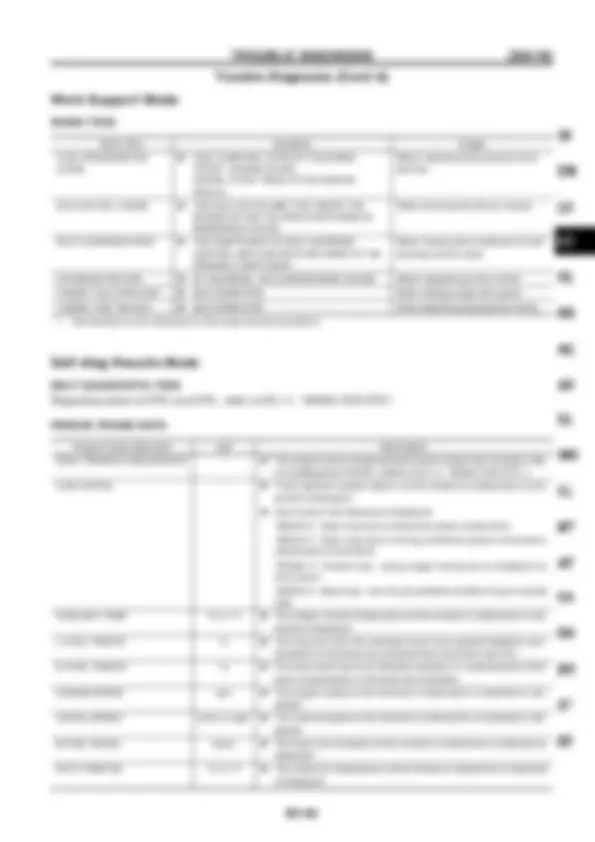
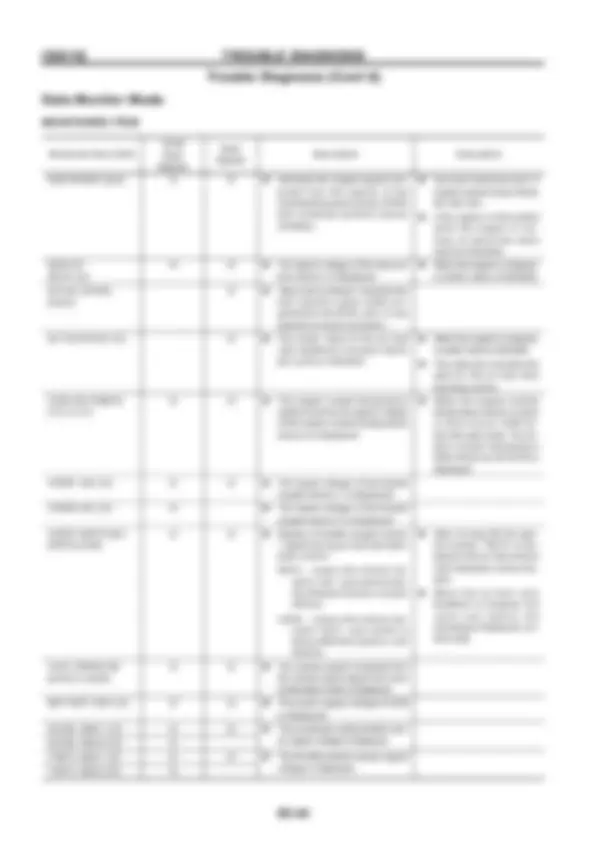
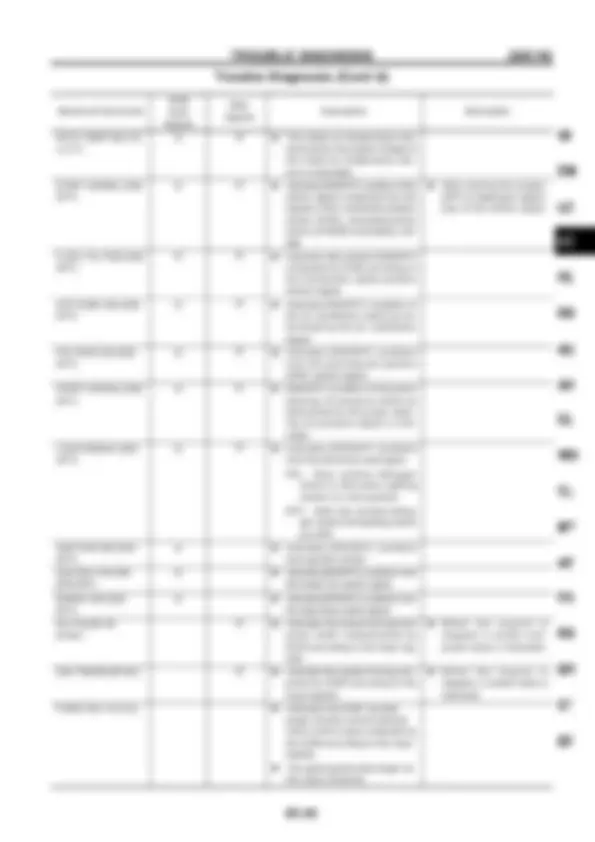
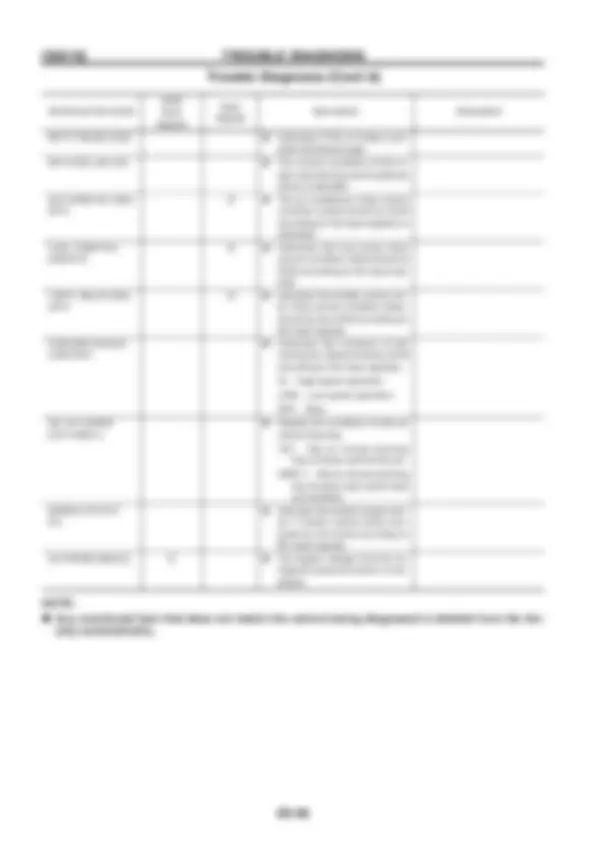
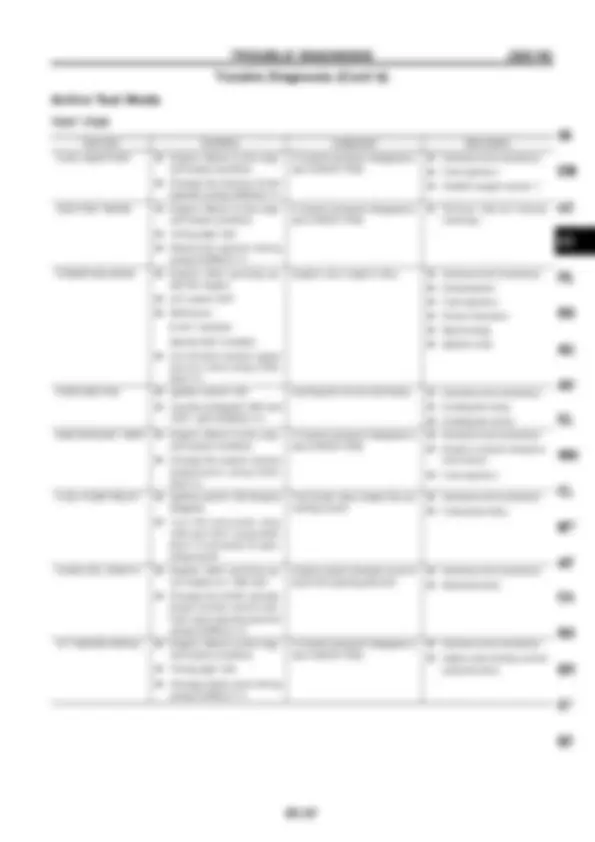
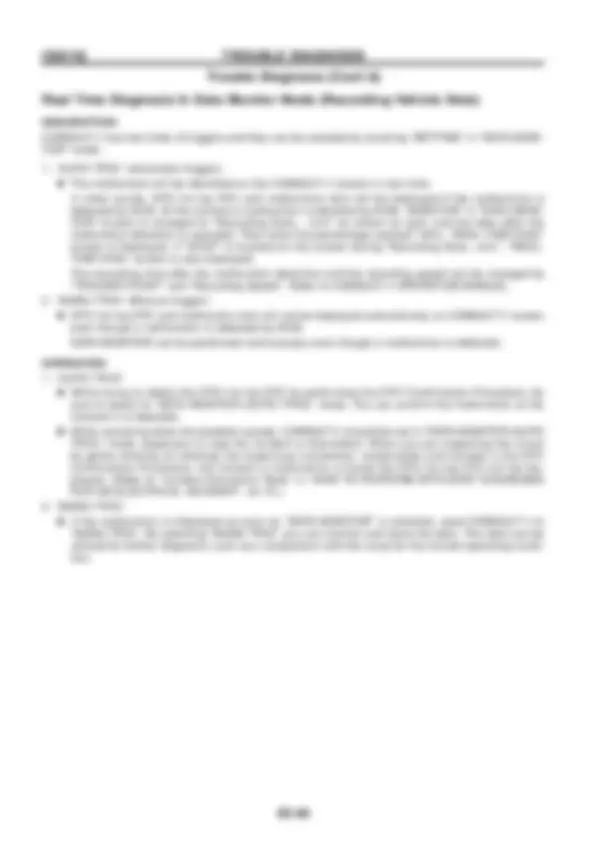
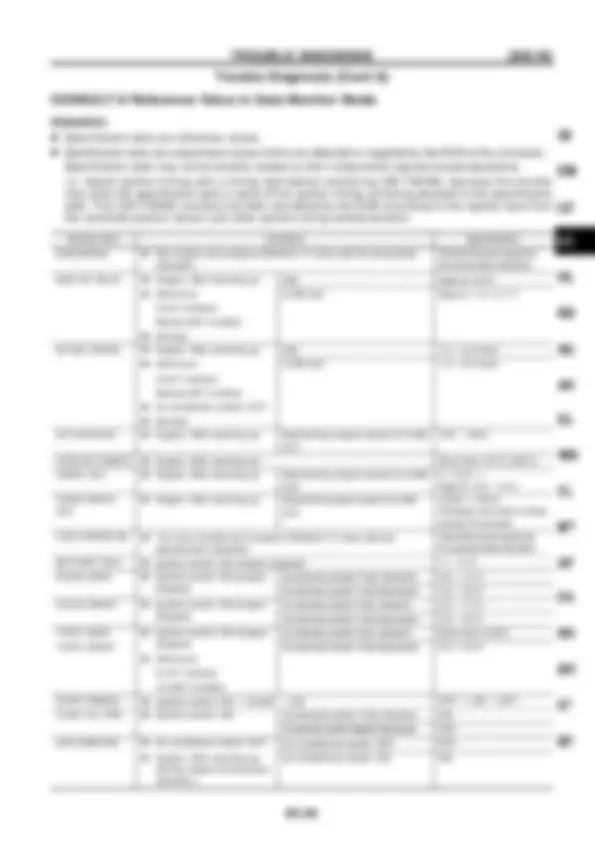
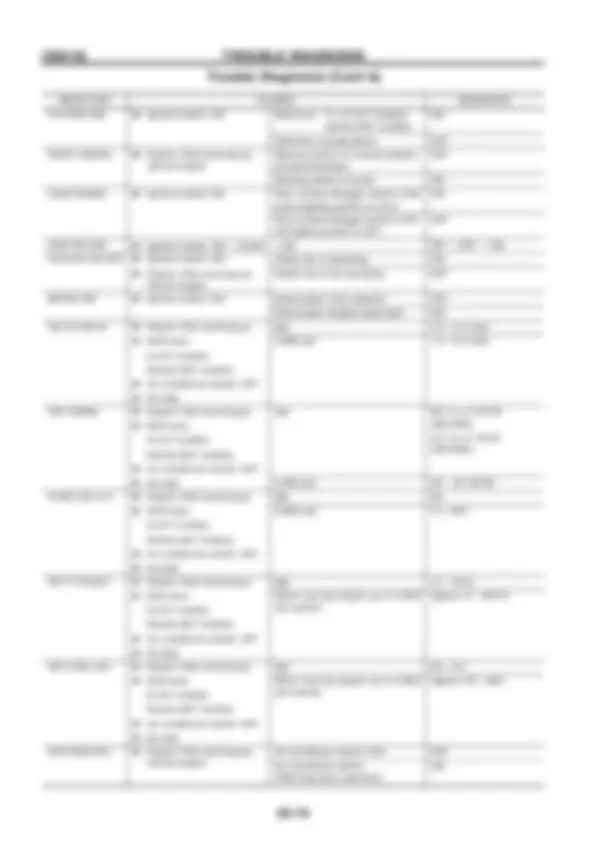
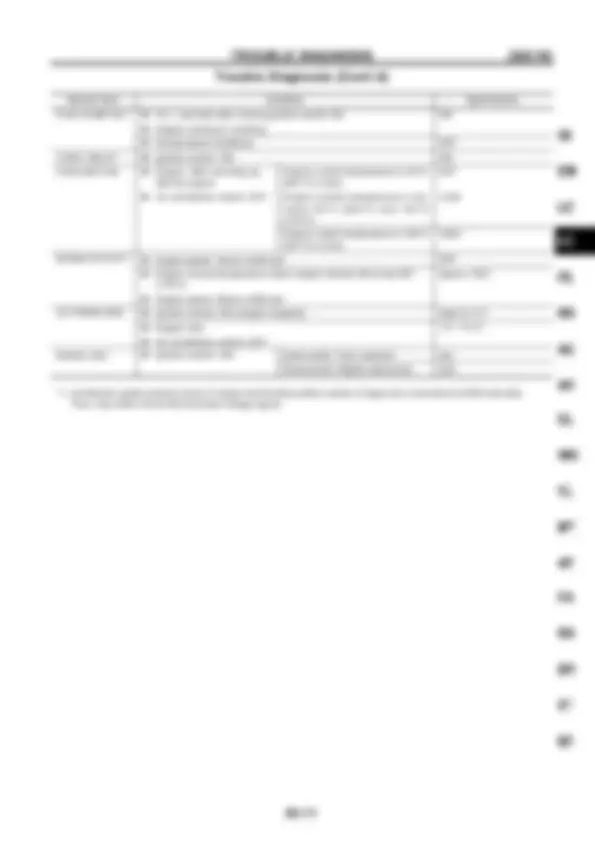
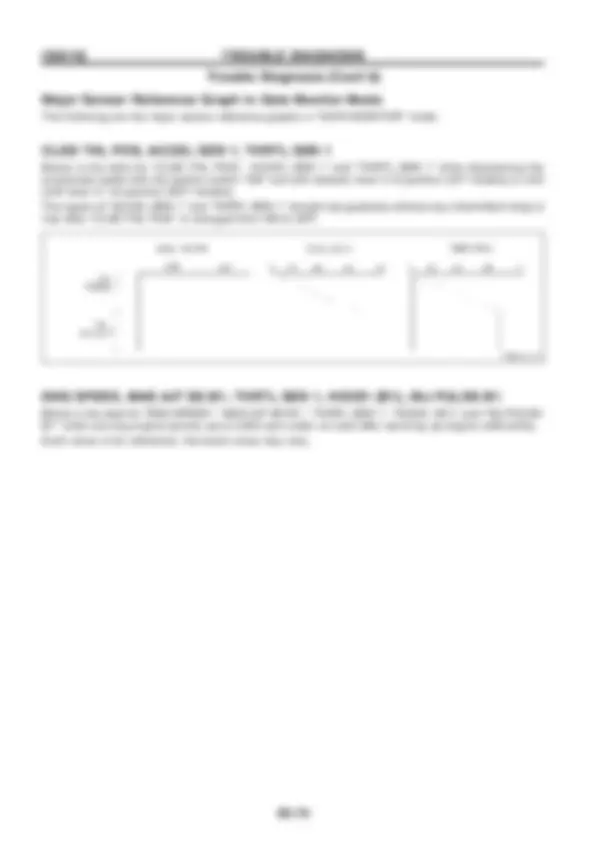
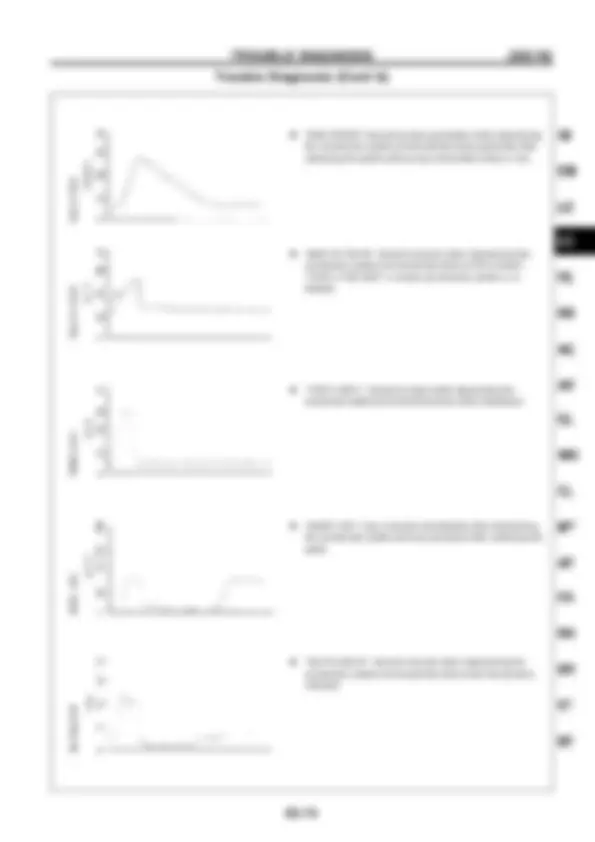
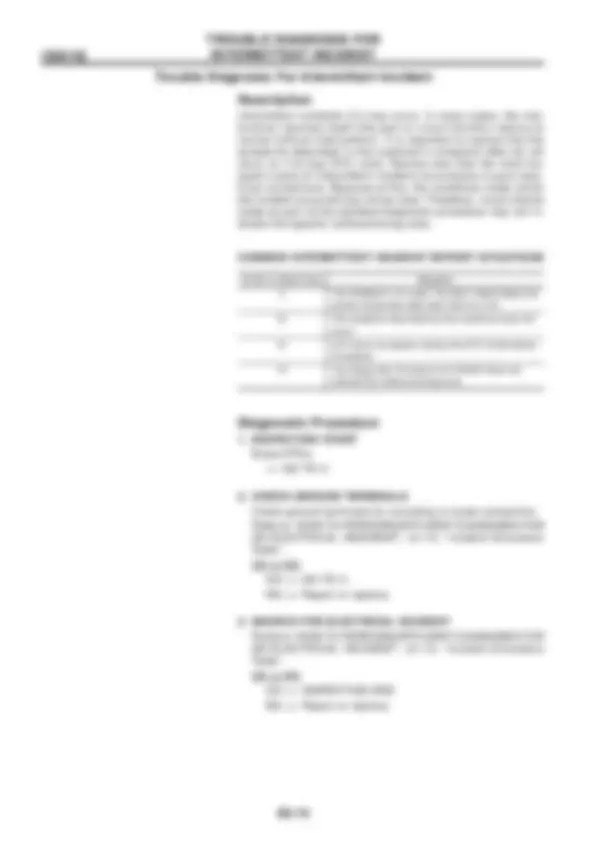
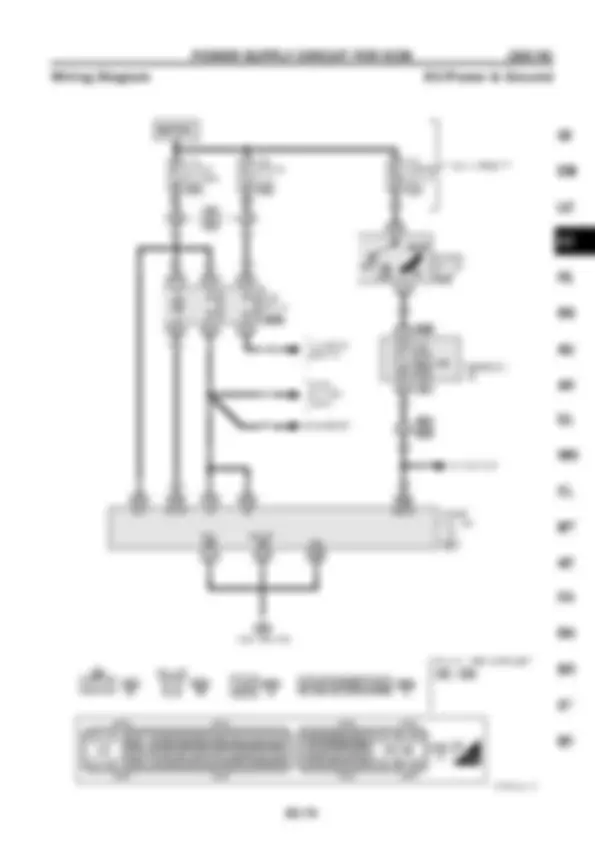
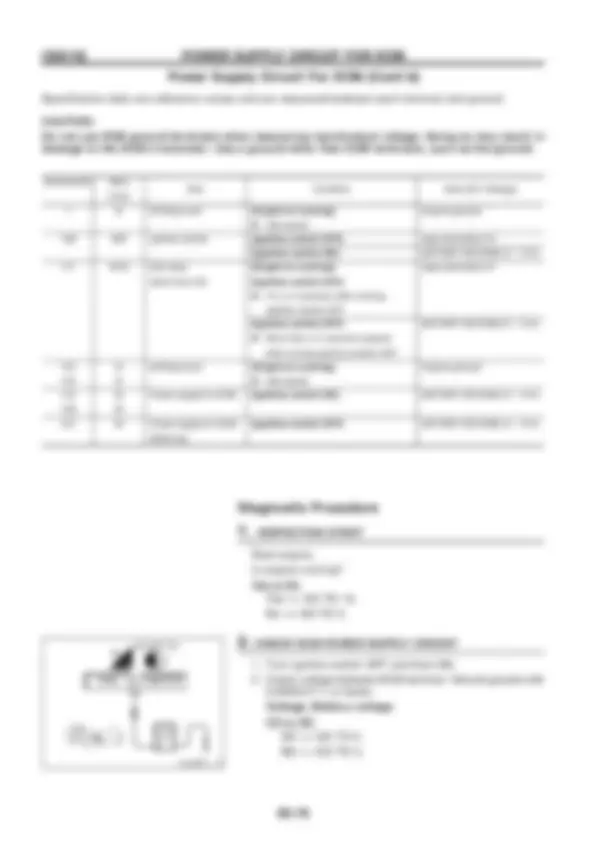
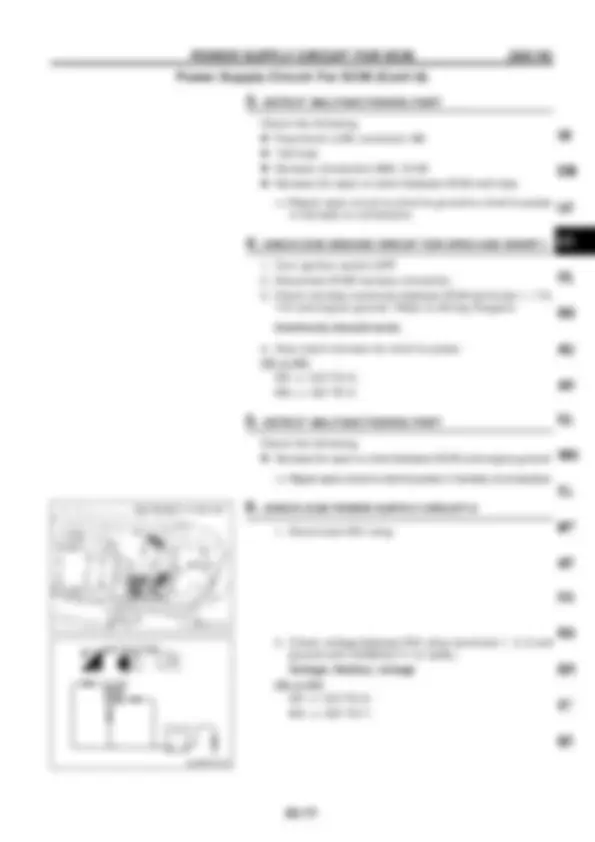
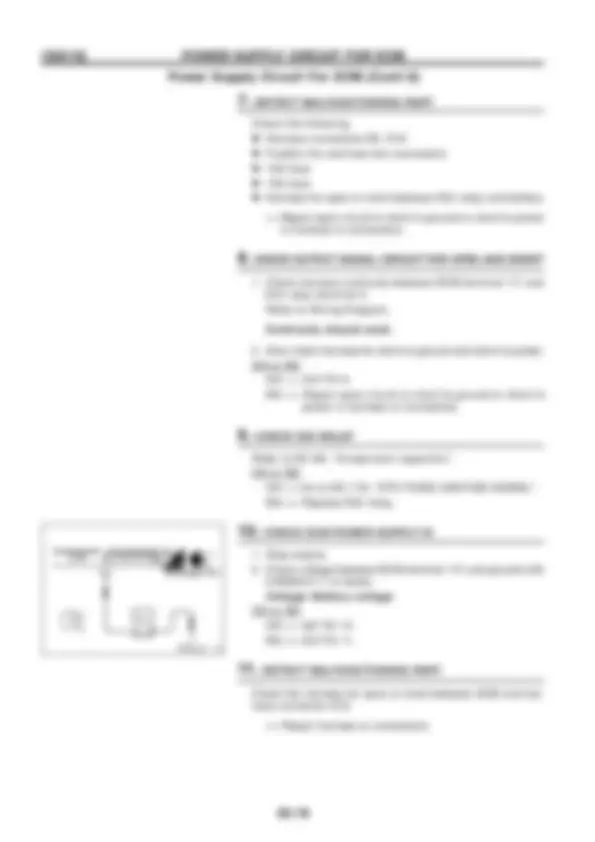
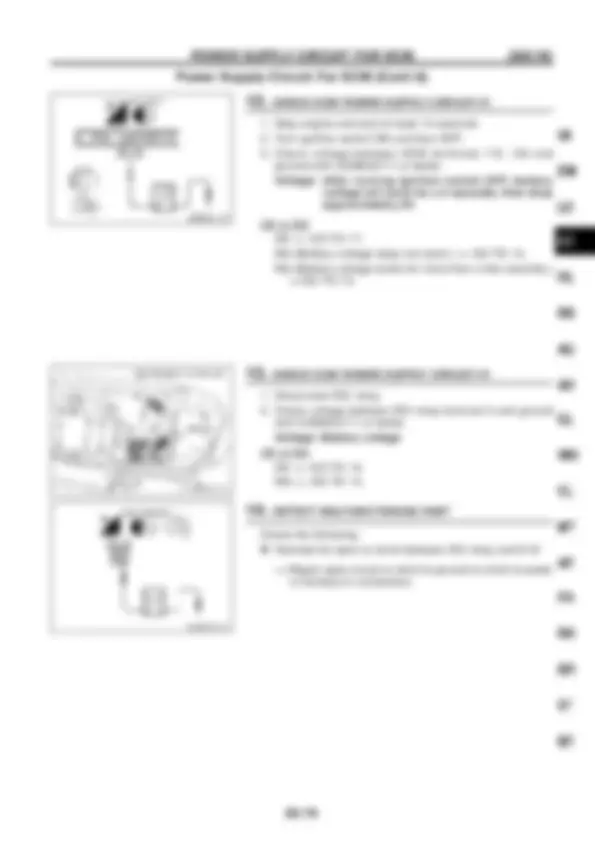
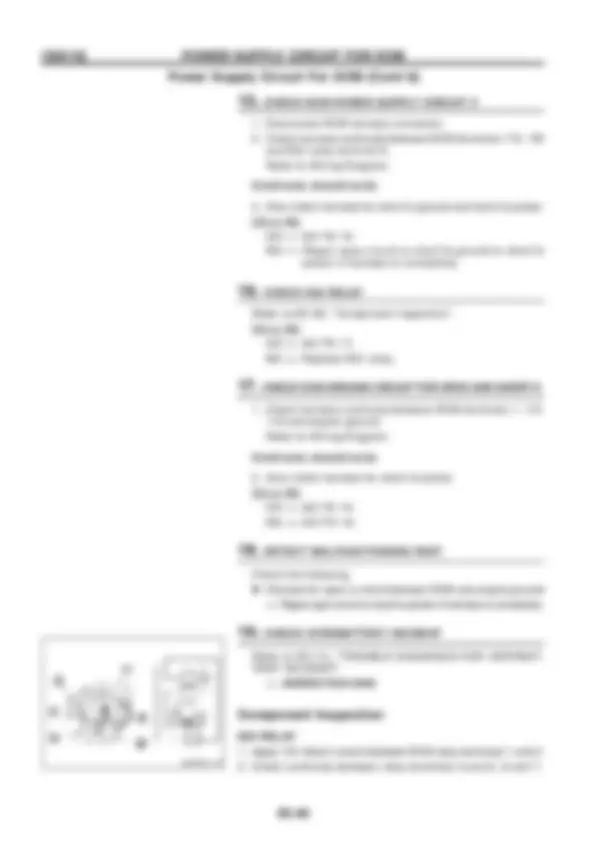
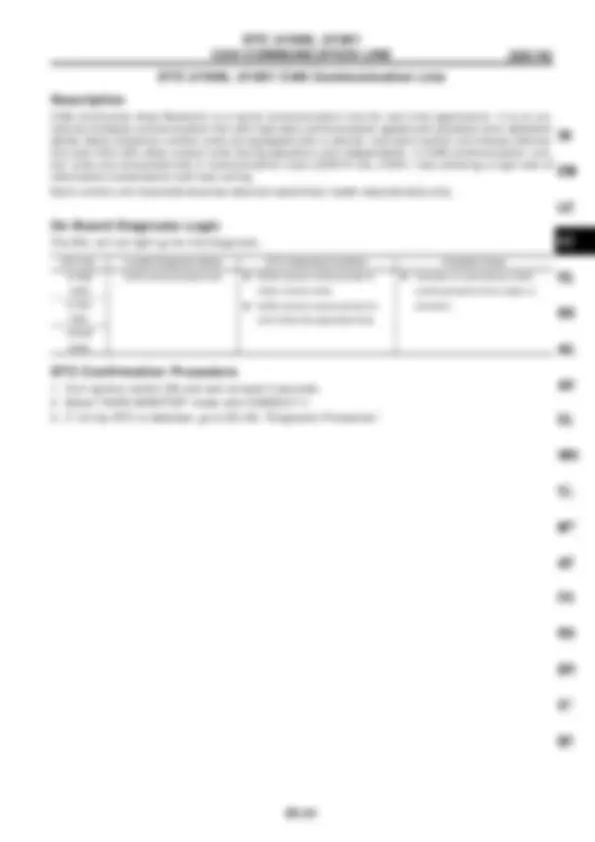
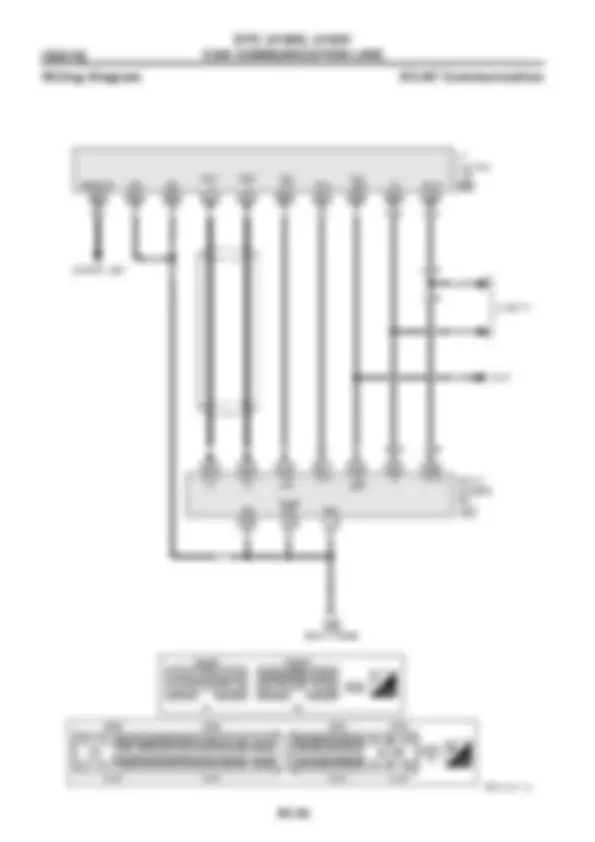
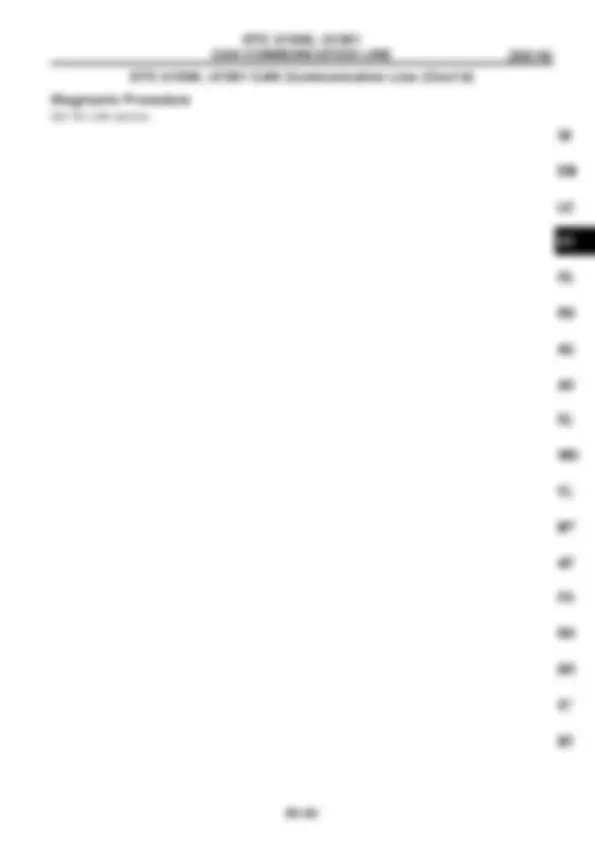
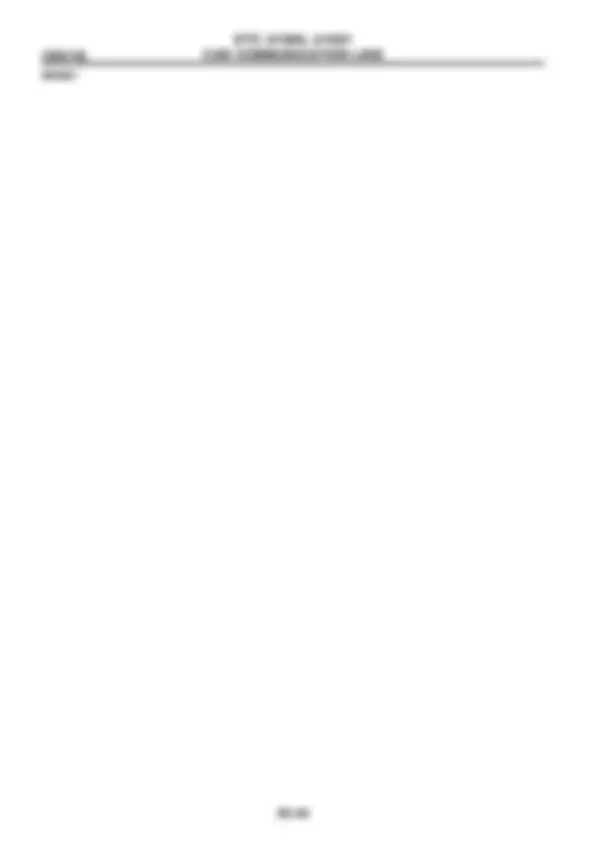
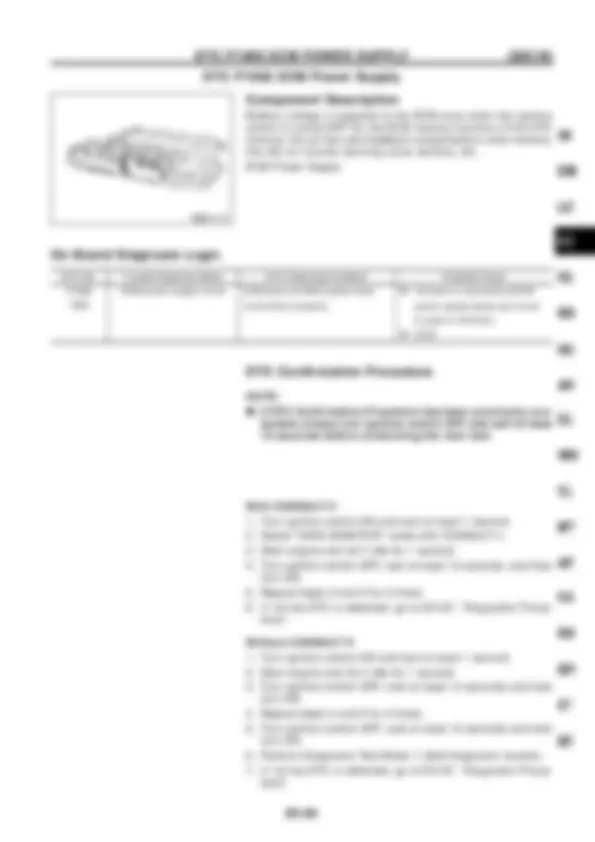
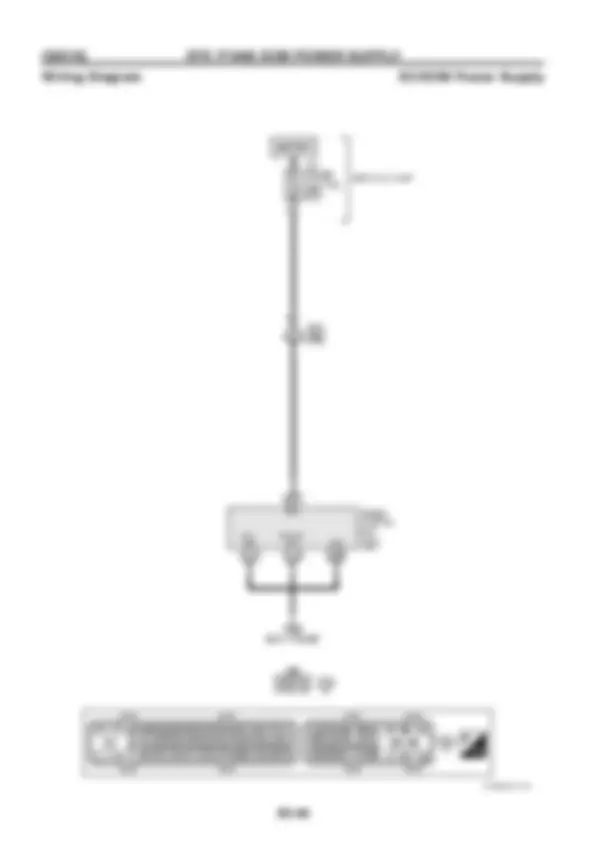
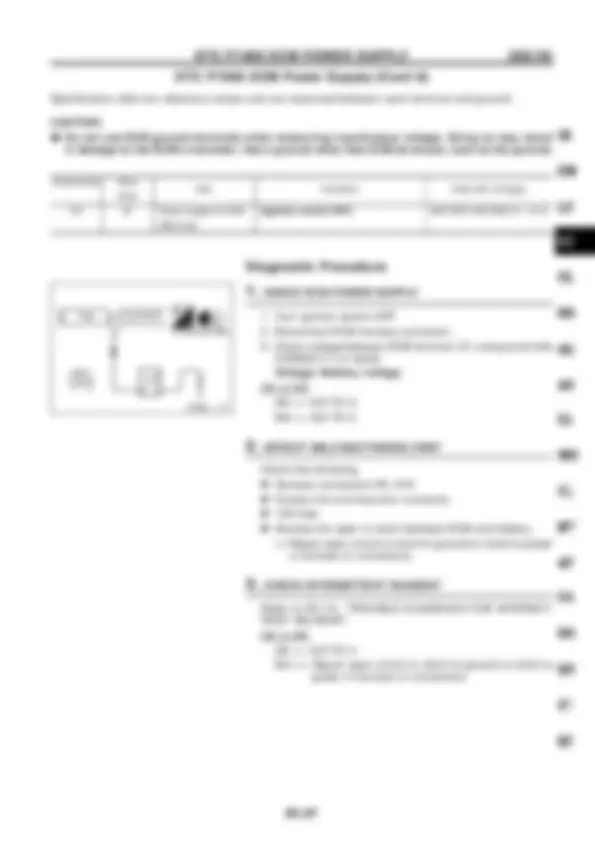
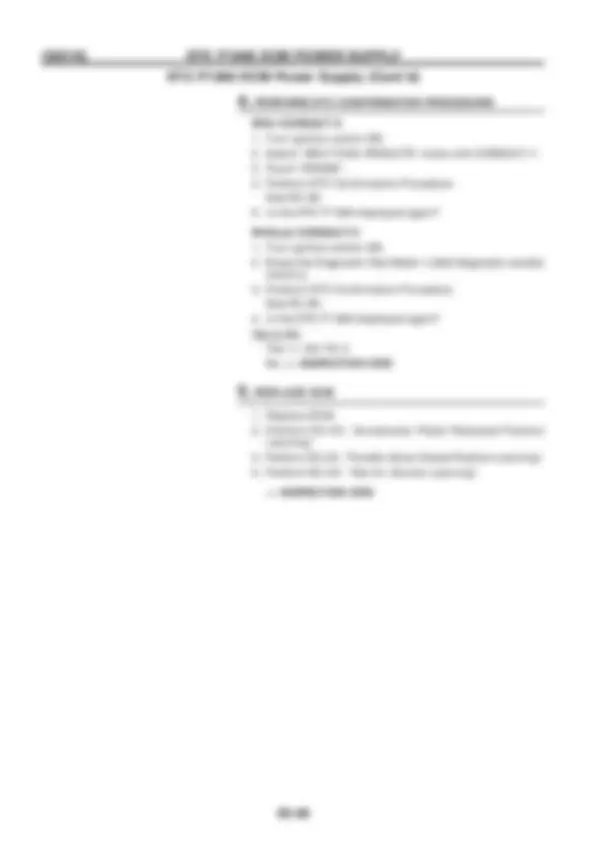
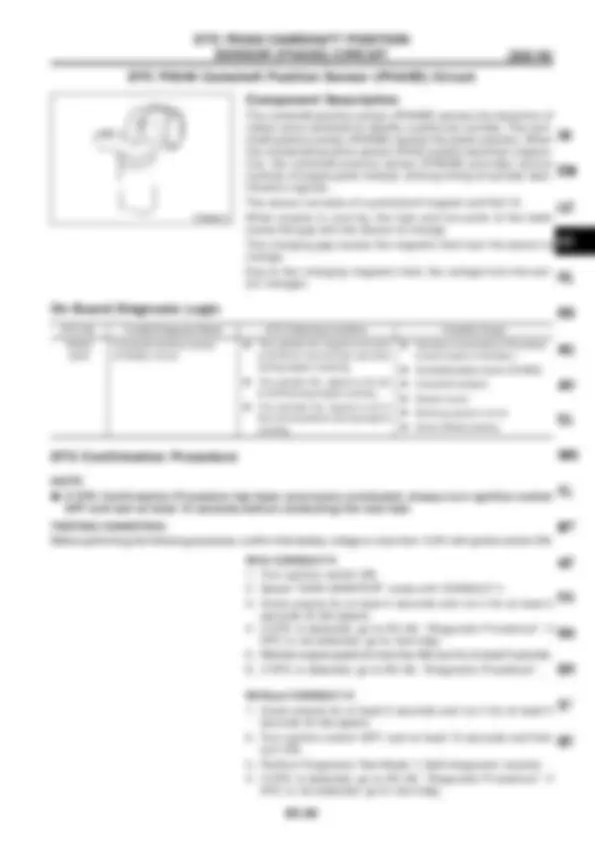
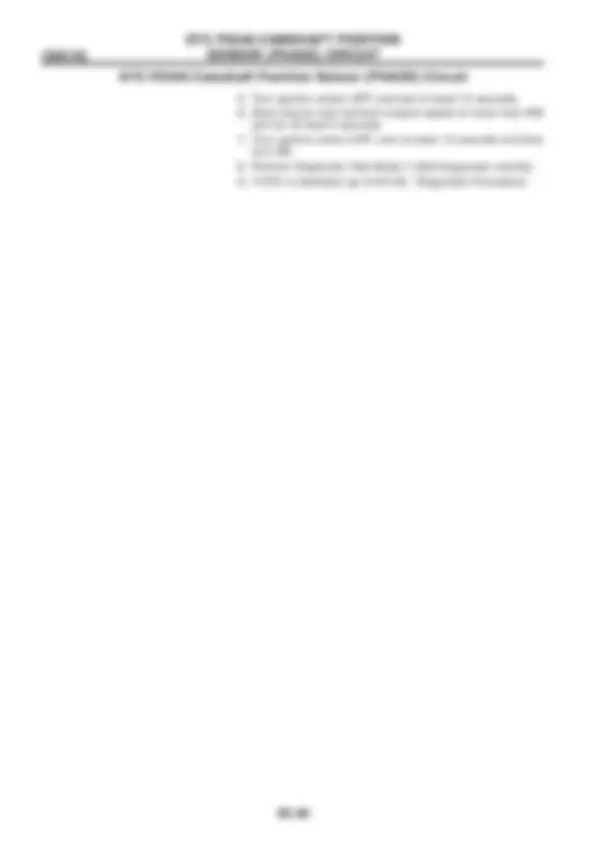
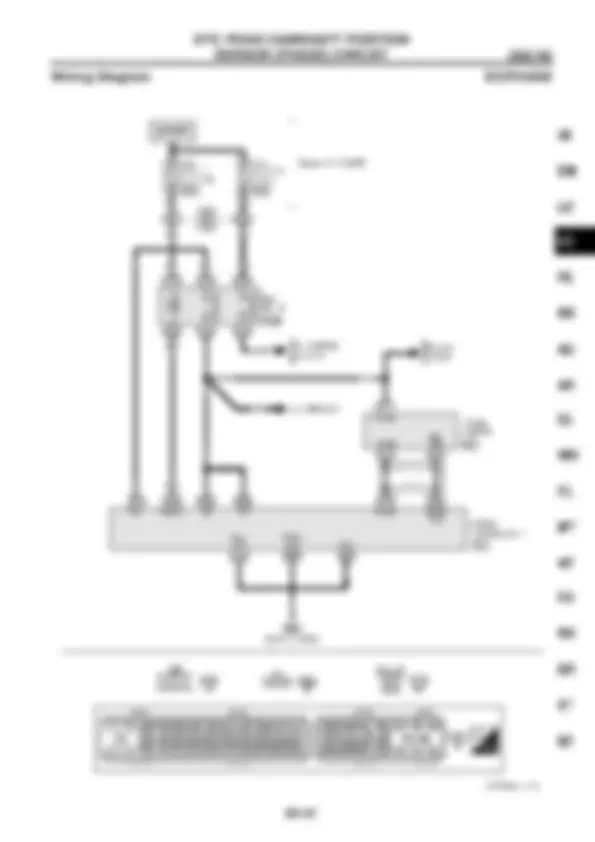
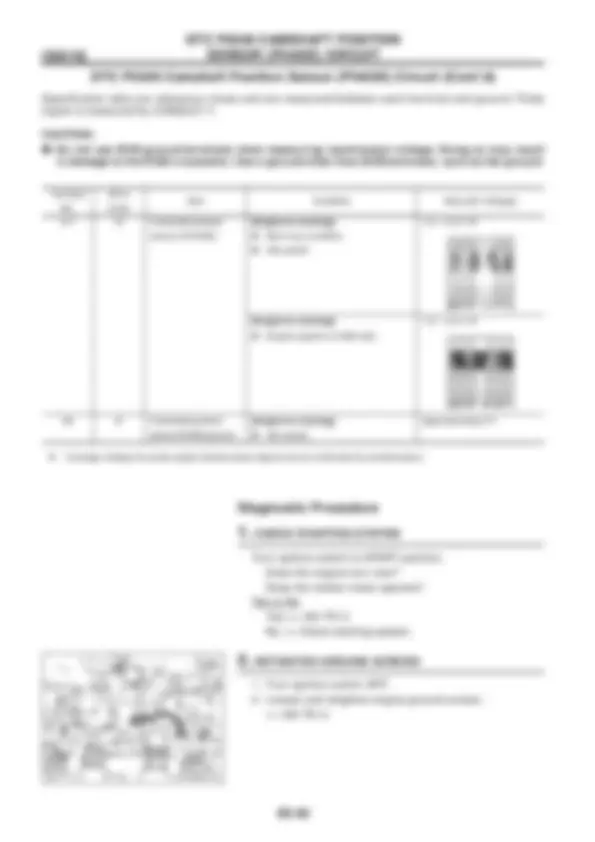
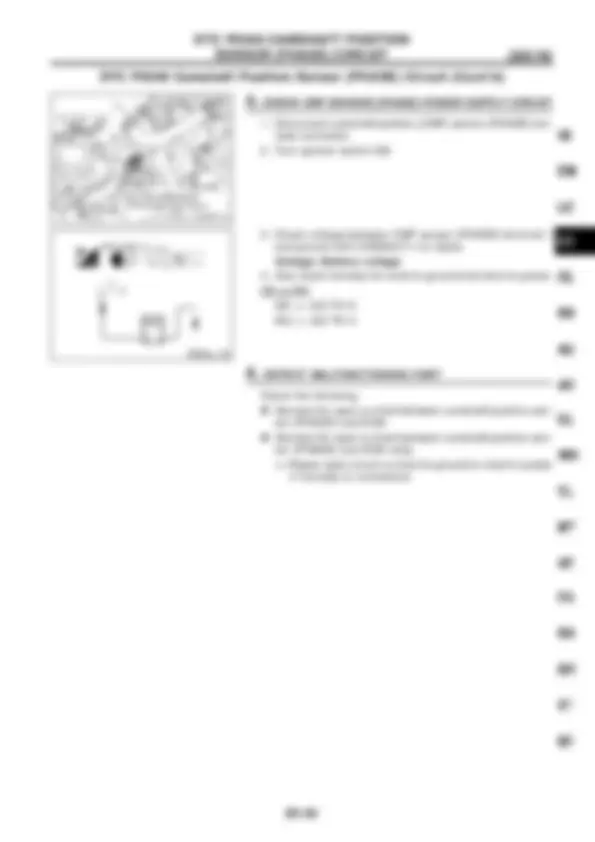
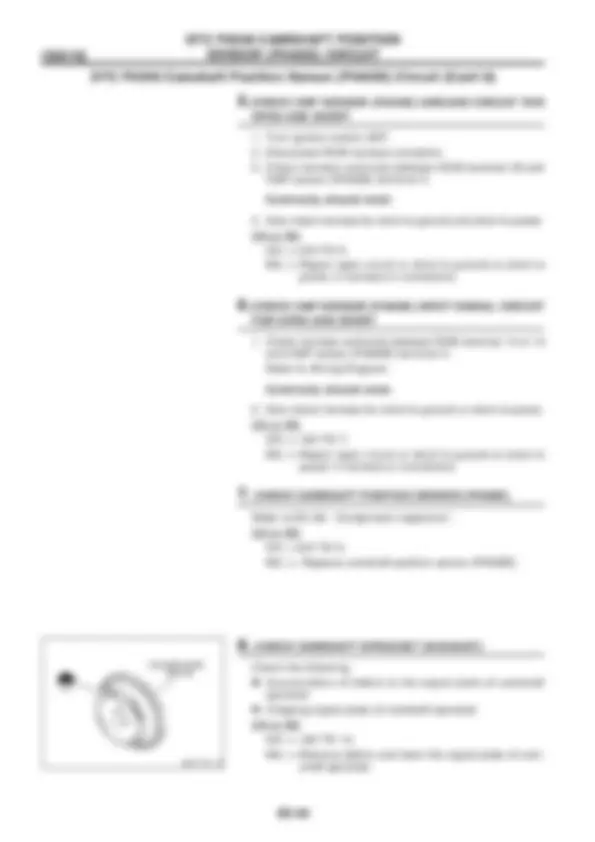
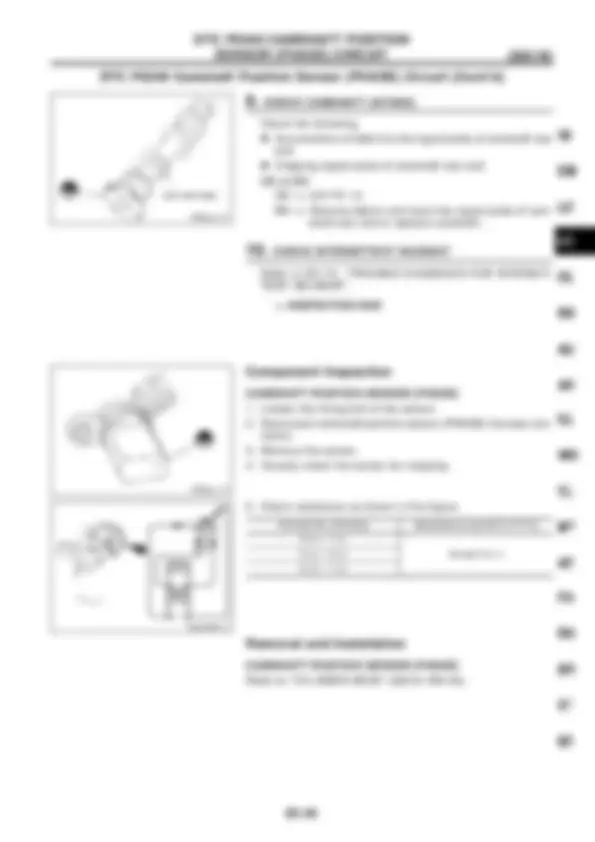
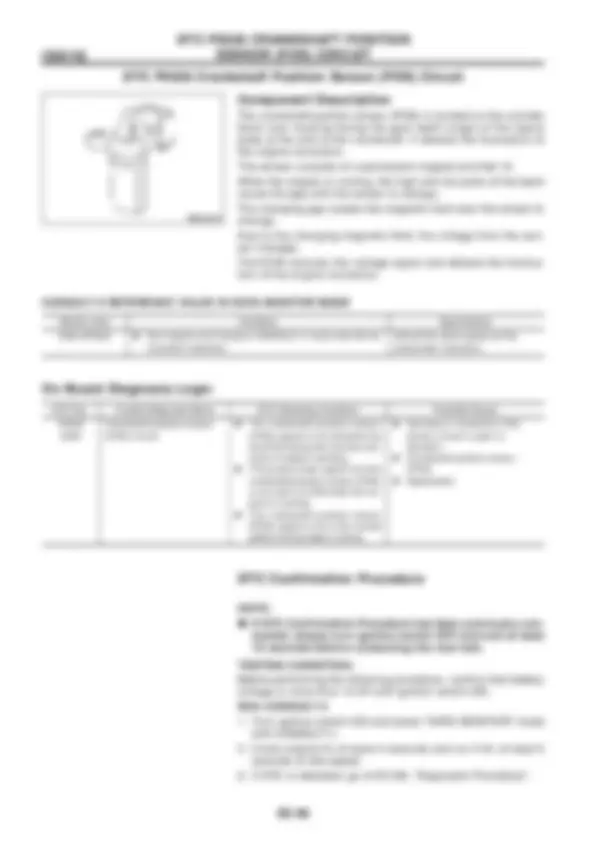
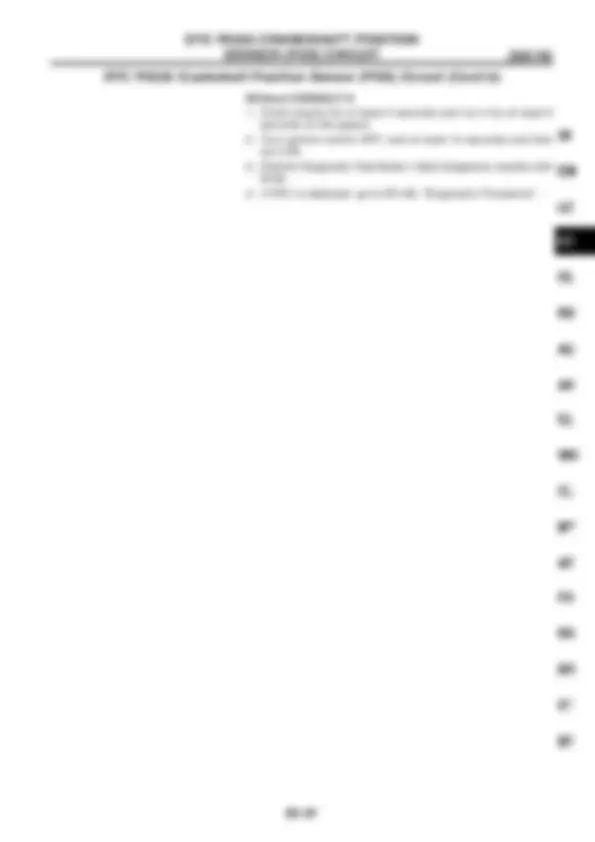
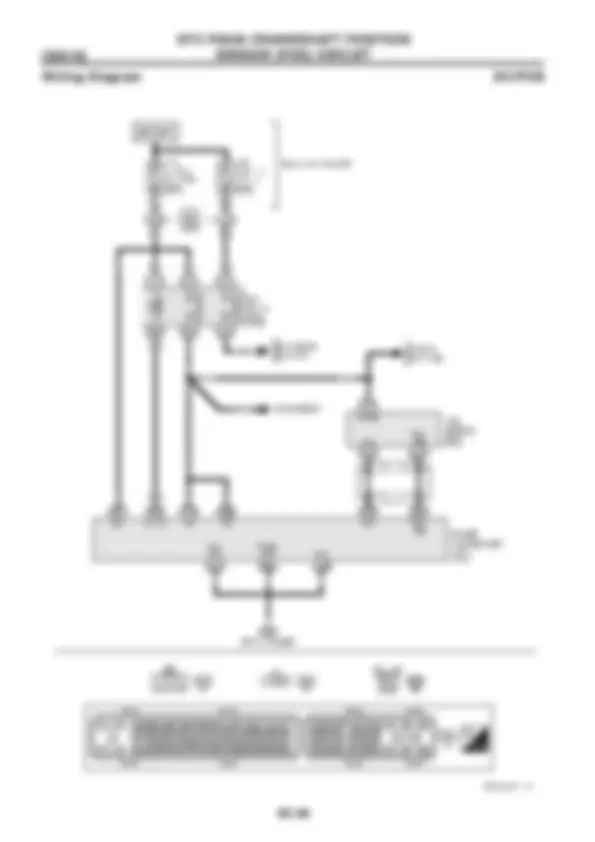
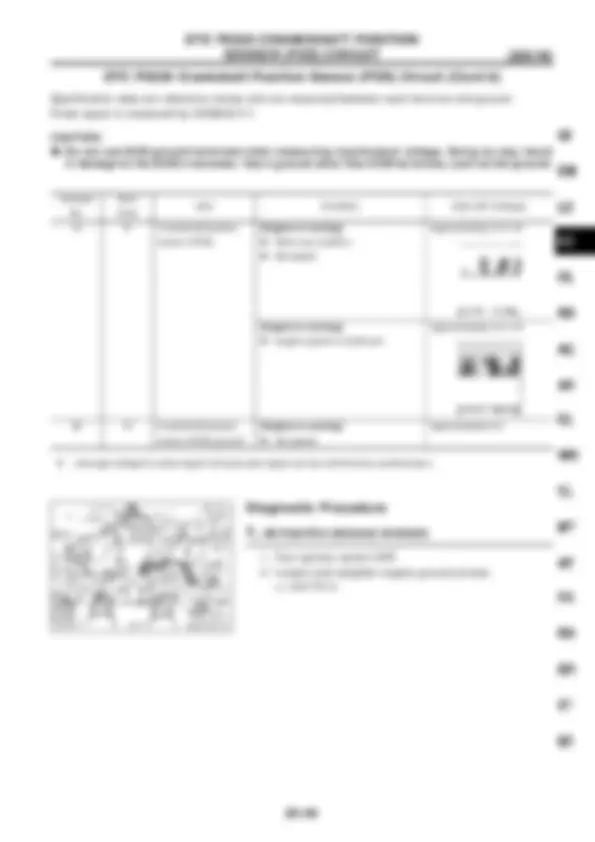
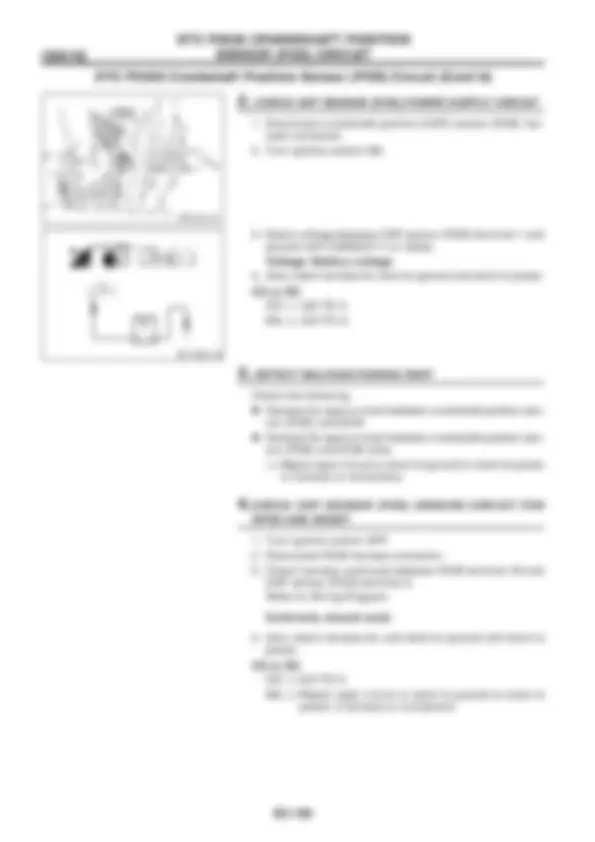
Prepara tus exámenes y mejora tus resultados gracias a la gran cantidad de recursos disponibles en Docsity
Gana puntos ayudando a otros estudiantes o consíguelos activando un Plan Premium
Prepara tus exámenes
Prepara tus exámenes y mejora tus resultados gracias a la gran cantidad de recursos disponibles en Docsity
Prepara tus exámenes con los documentos que comparten otros estudiantes como tú en Docsity
Los mejores documentos en venta realizados por estudiantes que han terminado sus estudios
Estudia con lecciones y exámenes resueltos basados en los programas académicos de las mejores universidades
Responde a preguntas de exámenes reales y pon a prueba tu preparación
Consigue puntos base para descargar
Gana puntos ayudando a otros estudiantes o consíguelos activando un Plan Premium
Comunidad
Pide ayuda a la comunidad y resuelve tus dudas de estudio
Descubre las mejores universidades de tu país según los usuarios de Docsity
Ebooks gratuitos
Descarga nuestras guías gratuitas sobre técnicas de estudio, métodos para controlar la ansiedad y consejos para la tesis preparadas por los tutores de Docsity
diagramas eléctricos de computadora
Tipo: Guías, Proyectos, Investigaciones
1 / 320
Esta página no es visible en la vista previa
¡No te pierdas las partes importantes!
DTC P0132 HEATED OXYGEN SENSOR - FR CIR- DTC P0134 HEATED OXYGEN SENSOR - FR CIR- DTC P0138 HEATED OXYGEN SENSOR - DTC P0031, P0032 HEATED OXYGEN SENSOR DTC P0037, P0038 HEATED OXYGEN SENSOR
Vacuum Lines in Evaporative Emission System
Items (CONSULT-II Screen Terms) NO DTC IS DETECTED. FURTHER TESTING MAY BE REQUIRED. CAN COMM CIRCUIT CAN COMM CIRCUIT
HO2S1 HTR (B1) HO2S1 HTR (B1) HO2S2 HTR (B1) HO2S2 HTR (B1) MAF SEN/CIRCUIT MAF SEN/CIRCUIT IAT SEN/CIRCUIT IAT SEN/CIRCUIT ECT SEN/CIRCUIT ECT SEN/CIRCUIT TP SEN 2/CIRC TP SEN 2/CIRC HO2S1 (B1) HO2S1 (B1) HO2S2 (B1) FUEL SYS-LEAN-B FUEL SYS-RICH-B TP SEN 1/CIRC TP SEN 1/CIRC KNOCK SEN/CIRC-B KNOCK SEN/CIRC-B CKP SEN/CIRCUIT CMP SEN/CIRC-B IGN SIGNAL-PRIMARY VEH SPEED SEN/CIRC PW ST P SEN/CIRC ECM
ECM BACK UP/CIRC INT/V TIM V/CIR-B ETC ACTR ETC FUNCTION/CIRC ETC MOT PWR ETC MOT PWR ETC MOT
Lighting Up X X X X X X X X X X X X O O X X X X X X X X X X X X X X X X O X X X X X X X X
Reference Page
EC- EC- EC- EC- EC- EC- EC- EC- EC- EC- EC- EC- EC- EC- EC- EC- EC- EC- EC- EC-
EC- EC- EC- EC- EC- EC- EC- EC-
EC- EC- EC- EC- EC- EC- EC-
Control Item Description
Fuel injection control
Ignition timing control
Idle RPM control Fuel pump drive control
A/C cut control
Radiator fan control
Canister purge control Engine and automatic transaxle integrated control Fail-safe function Diagnosis system
SOFIS control is adopted to enhance responses and exhaust efficiency by optimizing fuel injection amount. It improves drivability by performing compensations under extreme condi- tions such as sudden oxygen changes through oxygen feedback learning control. It minimizes exhaust gases by employing the oxygen sensor. It optimizes the ignition timing at various circumstances by employing the hole IC type crankshaft position sensor. It improves ignition performance by employing the DLI (Distributorless Ignition) system that has power transistor integrated ignition coil on each cylinder. It optimizes ignition timing by employing the knock control that advances or retards ignition timing according to knocking conditions during different driving conditions and used fuel quality. It controls idle speed by operating DC motor directly. It controls the fuel pump relay on and off according to engine RPM signals.
It minimizes engine load by turning the A/C relay off under high refrigerant pressure and high engine speed. It controls the radiator fan relay on and off according to vehicle speed, coolant temperature and A/C signal. It performs duty control on the canister according to driving conditions. It minimizes gear shift shock by reducing the engine torque during gear changes. It allows safety and emergency driving under system defectives. It corresponds with CONSULT-II for easy diagnosing.
ECM Function Fuel injection & mixture ratio control Electronic ignition system Fuel pump control On board diagnostic system Intake valve timing control Heated oxygen sensor 1 heater control EVAP canister purge flow control
Air conditioning cut control
Cooling fan control
Input (Sensor) Camshaft position sensor (PHASE) Crankshaft position sensor (POS) Mass air flow sensor Engine coolant temperature sensor Heated oxygen sensor 1 Throttle position sensor Accelerator pedal position sensor Park/neutral position (PNP) switch Intake air temperature sensor Power steering pressure sensor Ignition switch Stop lamp switch Battery voltage Knock sensor Refrigerant pressure sensor TCM (Transmission control module)* Air conditioner switch Vehicle speed signal Electrical load signal
Output (Actuator) Fuel injectors Power transistor Fuel pump relay MIL (On the instrument panel) Intake valve timing control solenoid valve Heated oxygen sensor 1 heater EVAP canister purge volume control solenoid valve Air conditioner relay
Cooling fan relays
*1: This input signal is sent to the ECM through CAN communication line.
Input Signal to ECM
Engine speed*1 and piston position
Amount of intake air Engine coolant temperature Density of oxygen in exhaust gas Throttle position Accelerator pedal position Gear position Engine knocking condition Battery voltage* Power steering operation Vehicle speed Air conditioner operation
Sensor Crankshaft position sensor (POS) Camshaft position sensor (PHASE) Mass air flow sensor Engine coolant temperature sensor Heated oxygen sensor 1 Throttle position sensor Accelerator pedal position sensor Park/neutral position (PNP) switch Knock sensor Battery Power steering pressure sensor Vehicle speed signal Air conditioner switch
ECM Function
Fuel injection & mixture ratio control
*1: The ECM determines the start signal status by the signals of engine speed and battery voltage.
Actuator
Fuel injectors
Input Signal to ECM Air conditioner ON signal Throttle valve opening angle
Engine speed*
Engine coolant temperature Battery voltage* Refrigerant pressure Power steering operation Vehicle speed
Sensor Air conditioner switch Throttle position sensor Crankshaft position sensor (POS) Camshaft position sensor (PHASE) Engine coolant temperature sensor Battery Refrigerant pressure sensor Power steering pressure sensor Vehicle speed signal
ECM Function
Air conditioner cut control
Actuator
Air conditioner relay
*1: The ECM determines the start signal status by the signals of engine speed and battery voltage.
Input Signal to ECM Neutral position Throttle position Accelerator pedal position Engine coolant temperature
Engine speed
Vehicle speed
Sensor Park/neutral position (PNP) switch Throttle position sensor Accelerator pedal position sensor Engine coolant temperature sensor Crankshaft position sensor (POS) Camshaft position sensor (PHASE) Vehicle speed signal
ECM Function
Fuel cut control
Actuator
Fuel injectors
Body Type Axle Engine Transmission
ECM (CAN gate 1) ECM (CAN gate 2)
CAN communication unit
O : Applicable *1 : Communication cannot be established.
Sedan 2WD QG16DE (Electric throttle control)