
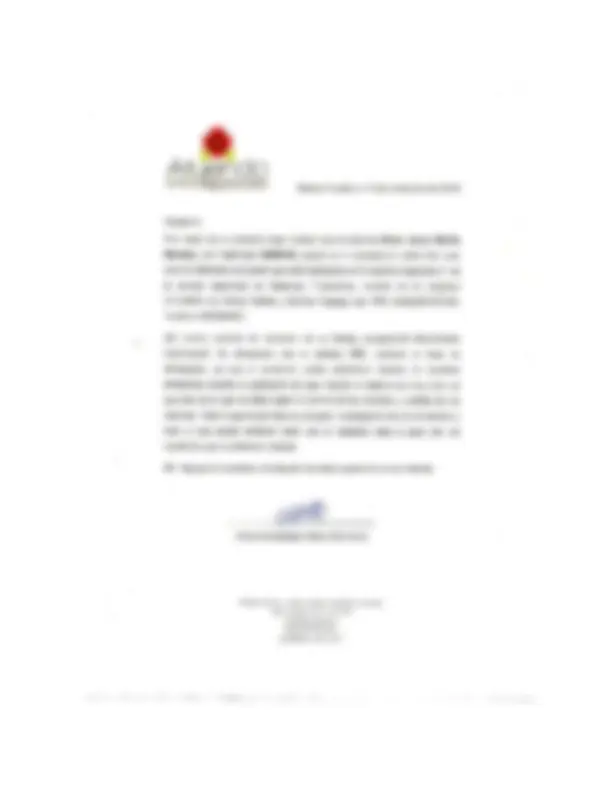
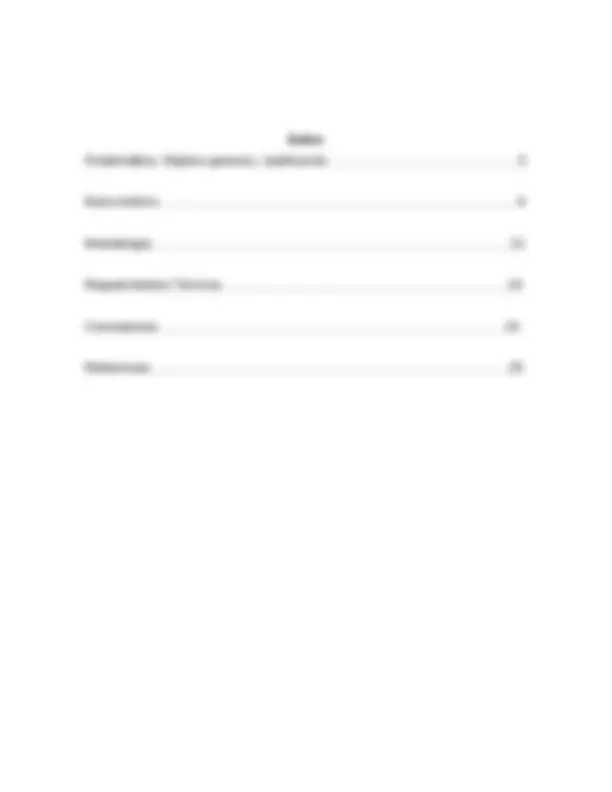
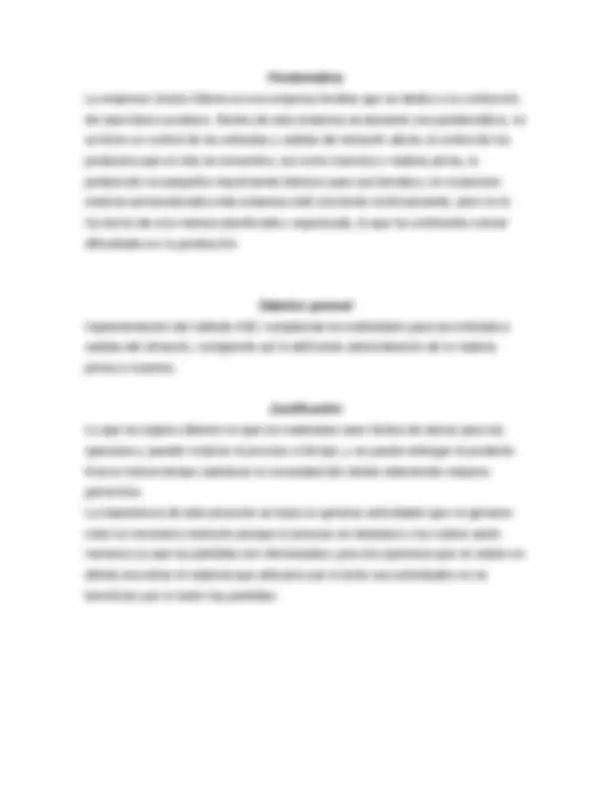
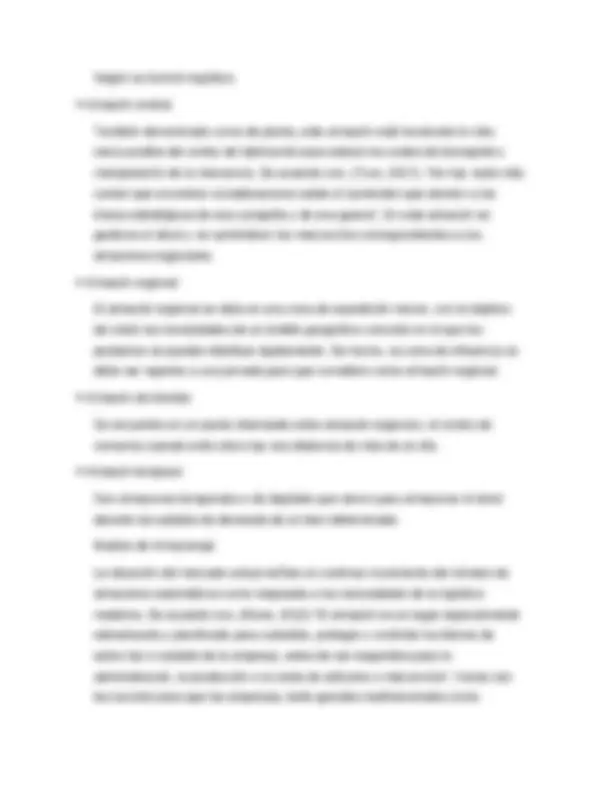
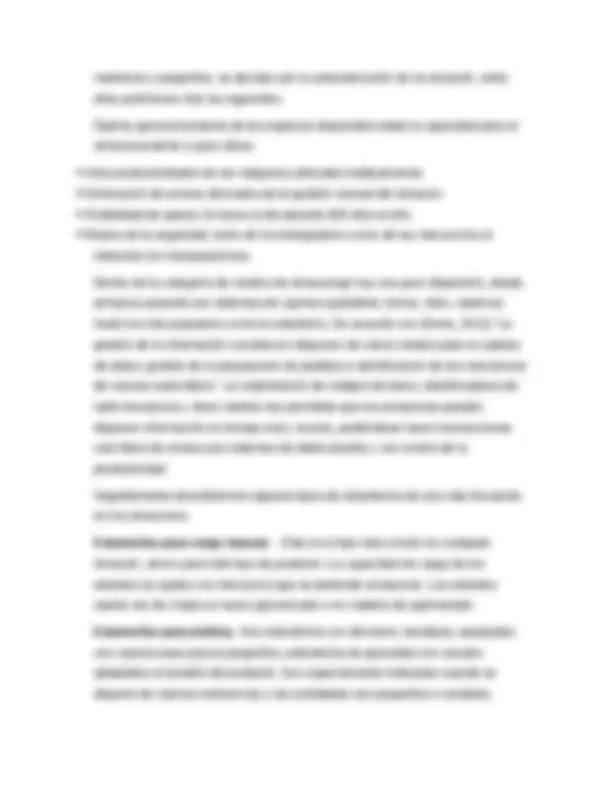
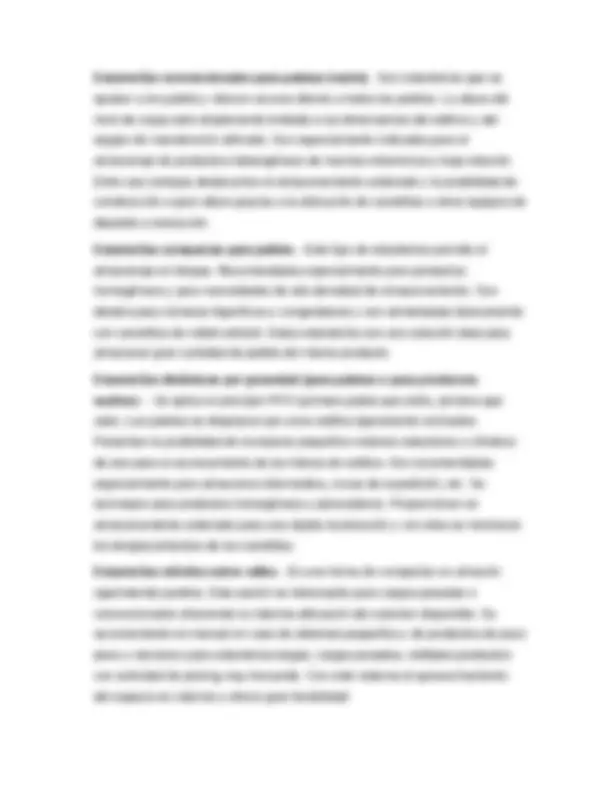
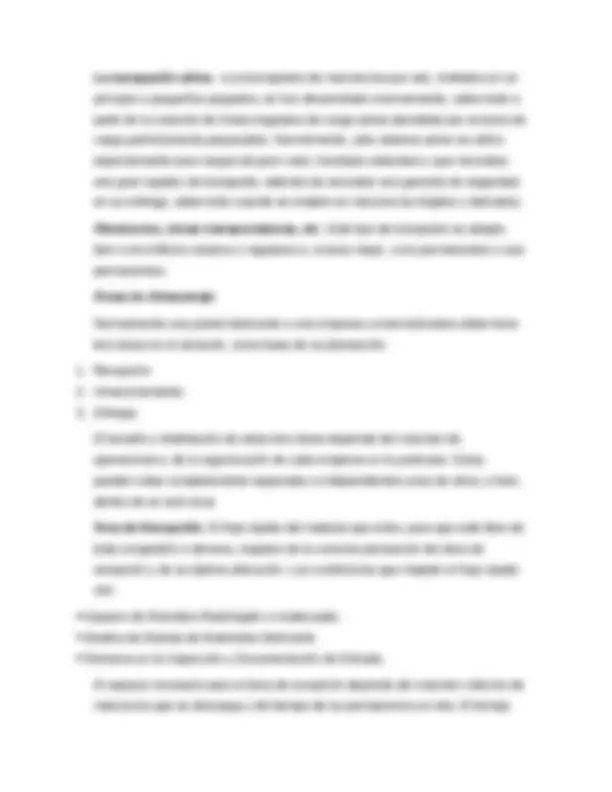
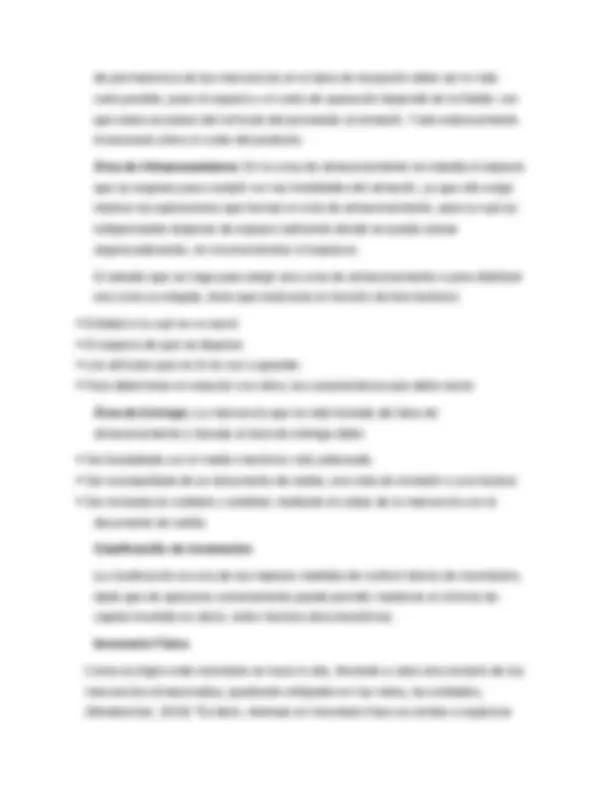
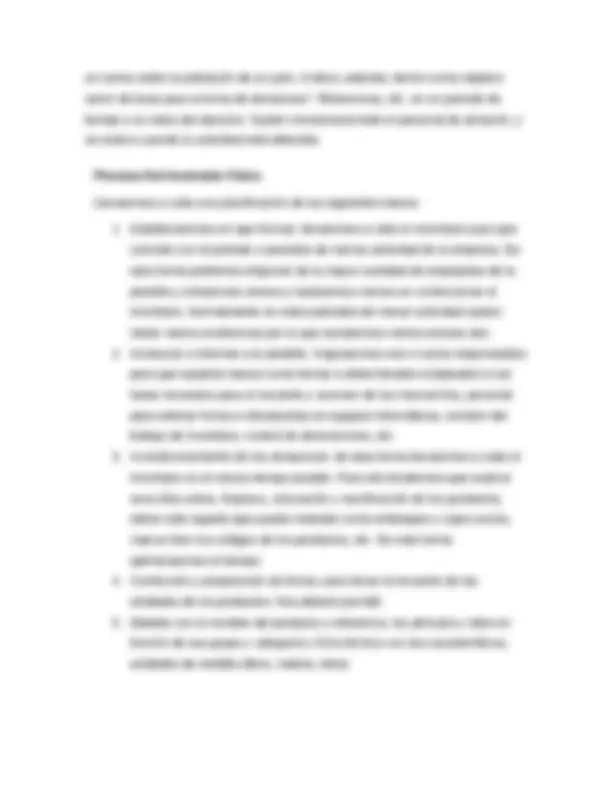
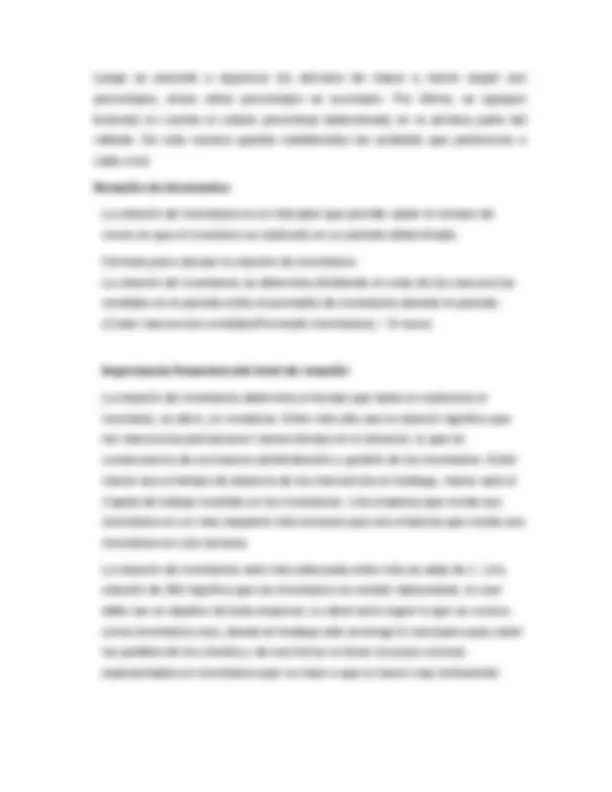
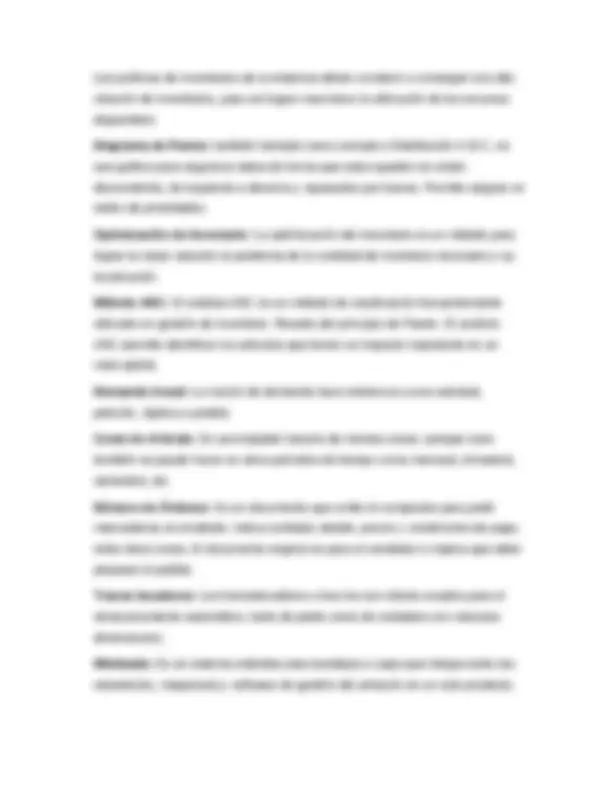
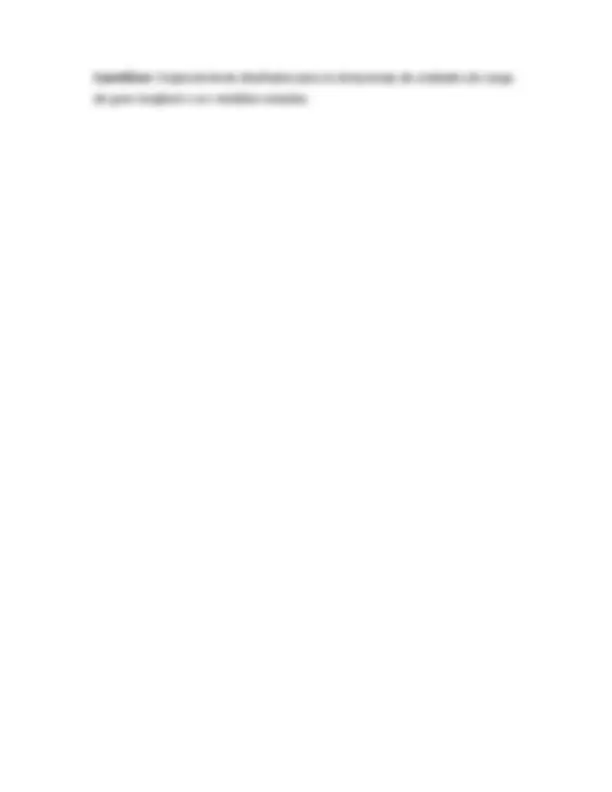
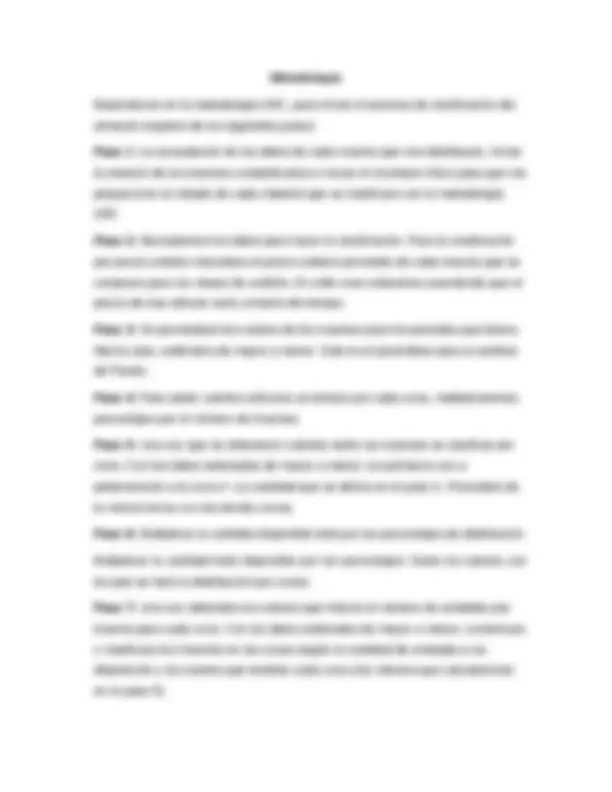
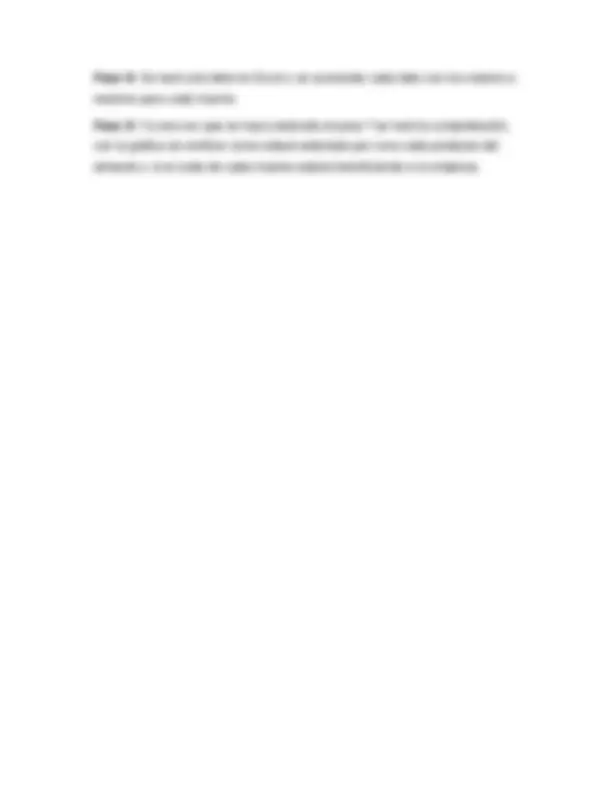
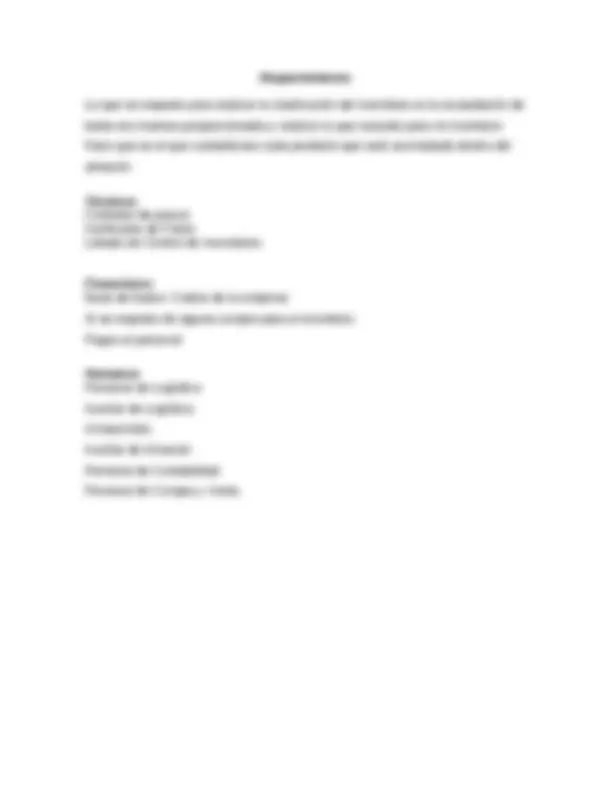
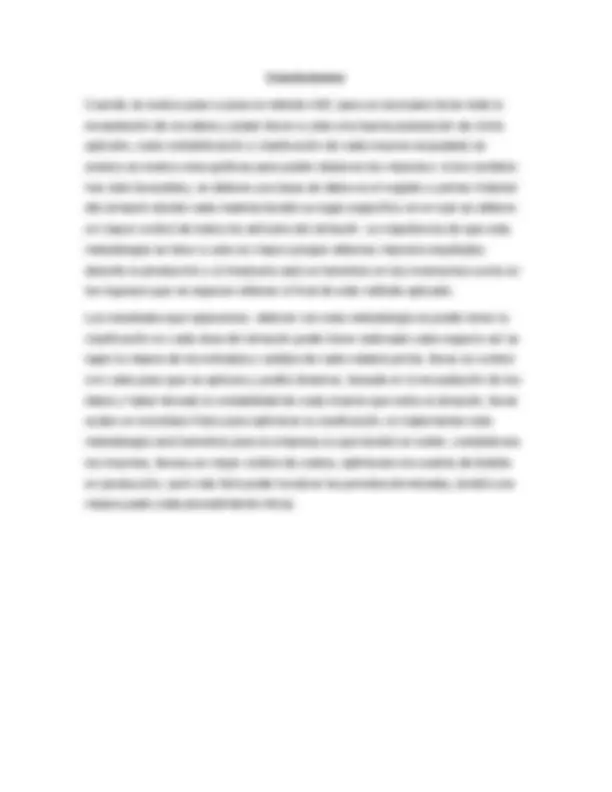
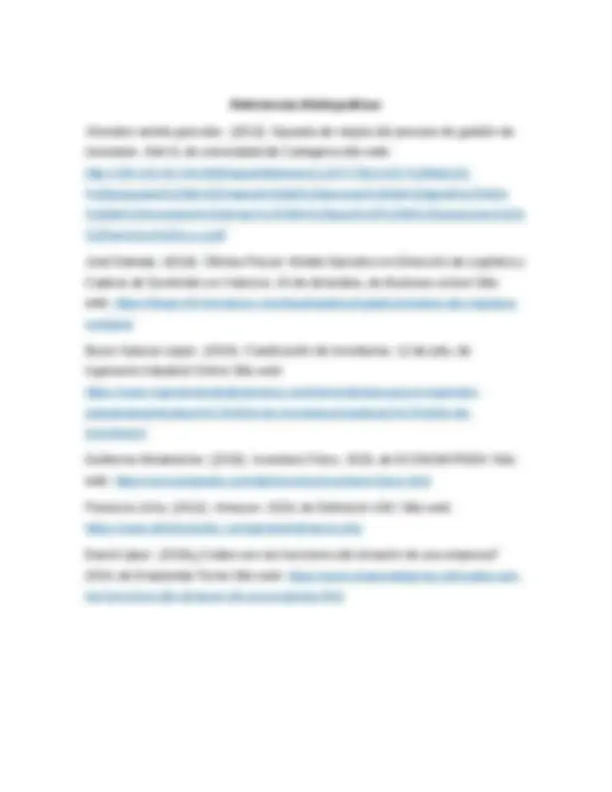
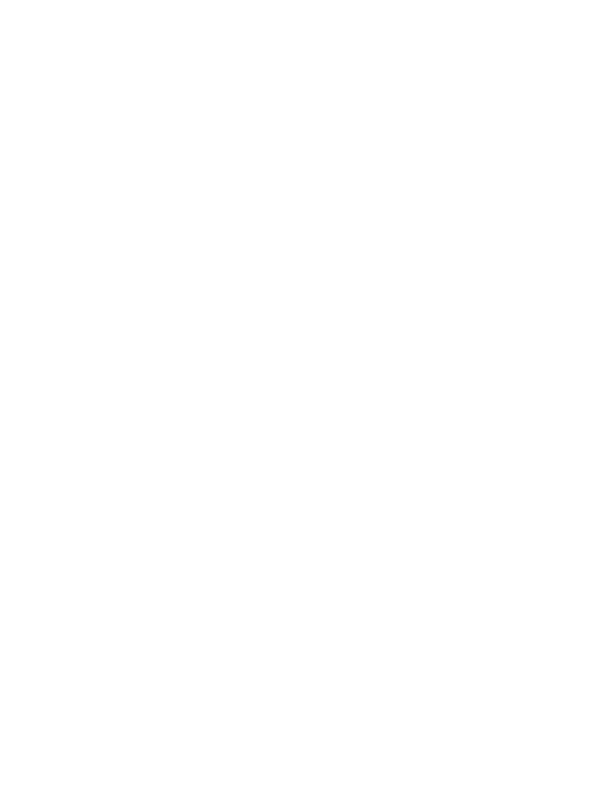
Prepara tus exámenes y mejora tus resultados gracias a la gran cantidad de recursos disponibles en Docsity
Gana puntos ayudando a otros estudiantes o consíguelos activando un Plan Premium
Prepara tus exámenes
Prepara tus exámenes y mejora tus resultados gracias a la gran cantidad de recursos disponibles en Docsity
Prepara tus exámenes con los documentos que comparten otros estudiantes como tú en Docsity
Los mejores documentos en venta realizados por estudiantes que han terminado sus estudios
Estudia con lecciones y exámenes resueltos basados en los programas académicos de las mejores universidades
Responde a preguntas de exámenes reales y pon a prueba tu preparación
Consigue puntos base para descargar
Gana puntos ayudando a otros estudiantes o consíguelos activando un Plan Premium
Comunidad
Pide ayuda a la comunidad y resuelve tus dudas de estudio
Descubre las mejores universidades de tu país según los usuarios de Docsity
Ebooks gratuitos
Descarga nuestras guías gratuitas sobre técnicas de estudio, métodos para controlar la ansiedad y consejos para la tesis preparadas por los tutores de Docsity
Un resumen ejecutivo de un proyecto que se centra en la implementación de la metodología abc (análisis por tipos de artículos) en una empresa que presenta problemas de control de inventarios, especialmente en lo que respecta a las entradas y salidas del almacén. El texto explica los pasos necesarios para la recogida y clasificación de datos, así como el objetivo de mejorar el control de la materia prima y los insumos mediante la optimización del inventario. Además, se discuten los conceptos básicos del almacenaje y la clasificación de inventarios.
Qué aprenderás
Tipo: Ejercicios
1 / 26
Esta página no es visible en la vista previa
¡No te pierdas las partes importantes!
Resumen Ejecutivo Fecha: 26-11- Título del Proyecto: Implementación de la metodología ABC para la empresa Ursula Aldana Dentro de esta empresa se presenta una problemática, no se tiene un control de las entradas y salidas del almacén afecta al control de los productos que en ella se encuentra, así como insumos y materia prima. La implementación del método ABC cumplirá los estándares para las entradas y salidas del almacén mejorando así las deficiencias que se encuentran dentro del almacén. Para la implementación del método ABC se requieren los siguientes pasos son del 1 al 9 ahí se explica cómo inicia la recaudación de todos los datos y como se implantará durante todo el proceso de almacenaje de todo el control de entradas y salidas llevando un conteo de cada insumo y obteniendo graficas mes con mes para observar si se tiene buenos resultados. Palabras claves Almacenamiento: Se denomina almacenamiento al proceso y la consecuencia de almacenar. Esta acción se vincula a recoger, depositar, archivar o registrar algo. Método ABC: El análisis ABC es un método de clasificación utilizado en gestión de inventario. Within this company there is a problem, there is no control of the inputs and exits of the warehouse affects the control of the products that is located in it as well as inputs and raw materials. The implementation of the ABC method will meet the standards for warehouse inputs and outputs, thus improving the deficiencies that are inside the warehouse. For the implementation of the ABC method the following steps are required are from 1 to 9 there it explains how it starts the collection of all the data and how it will be implemented throughout the process of storage the entire control of inputs and outputs carrying a count of each supply or and getting graphs month by month to see if you have good results. Keywords Storage: This is called storage to the process and the consequence of storing. This action is linked to collecting, depositing, archiving or recording something. ABC Method: ABC analysis is a classification method used in inventory management. Datos del Autor: Airam Jesus Martin Morales
Problemática La empresa Ursula Aldana es una empresa familiar que se dedica a la confección de ropa típica yucateca. Dentro de esta empresa se presenta una problemática, no se tiene un control de las entradas y salidas del almacén afecta al control de los productos que en ella se encuentra, así como insumos y materia prima, la producción es pequeña mayormente fabrican para sus tiendas y en ocasiones realizan personalizados esta empresa está creciendo continuamente, pero no lo ha hecho de una manera planificada y organizada, lo que ha conllevado a tener dificultades en la producción. Objetivo general Implementación del método ABC cumpliendo los estándares para las entradas y salidas del almacén, corrigiendo así la deficiente administración de la materia prima e insumos. Justificación Lo que se espera obtener es que los materiales sean fáciles de ubicar para las operarias y puedan realizar el proceso a tiempo, y se pueda entregar el producto final al mismo tiempo satisfacer la necesidad del cliente obteniendo mejores ganancias. La importancia de este proyecto se basa en generar actividades que no generan valor es necesario realizarlo porque el proceso se retardara y los costos serán menores ya que las pérdidas son demasiadas, para los operarios que no saben en dónde encontrar el material que utilizaran por lo tanto sus actividades no se benefician por lo tanto hay perdidas.
El almacén convencional se compone de estanterías metálicas y estanterías para el depósito de paletas, para el uso de carretillas contrapesadas convencionales o de mástil retráctil. En estos almacenes la altura de la última carga no supera los 8 metros y se deben fijar pasillos adecuados para el paso de las carretillas. El sistema de almacenaje más habitual en estas infraestructuras son las estanterías para almacén, capaces de soportar diferentes pesos de carga por balda. Almacén automático En los almacenes automáticos se utilizan equipos robotizados para la manipulación de la carga, su altura sobrepasa los 10 metros y la actividad realizada por los trabajadores es mínima. Suelen ser de dos tipos: de carga paletizada a gran altura o mini-loads, para cargas más ligeras. Se utiliza un trance levador que se controla mediante un sistema informático y que se ocupa de la entrada y salida del material. Según la mercancía almacenada Materias primas Los almacenes que albergan materias directamente extraídas de la naturaleza suelen estar muy cerca del centro de producción, donde se transformarán en productos elaborados. Productos intermedios Los productos semi-elaborados se encuentran en mitad de la cadena de producción. Si la segunda fase de producción es en la misma fábrica suelen almacenarse en su interior. Aunque otros bienes como el textil se fabrican habitualmente en dos o más instalaciones, por lo que el almacenaje de bienes intermedios no siempre se hace en el interior o cerca de la fábrica. Productos terminados Son las materias acabadas y los productos elaborados que ya están disponibles para su salida y para comenzar su proceso de distribución y posterior venta.
Según su función logística Almacén central También denominado como de planta, este almacén está localizado lo más cerca posible del centro de fabricación para reducir los costes de transporte y manipulación de la mercancía. De acuerdo con, (Tzun, 2017), “No hay nada más común que encontrar consideraciones sobre el suministro que afecten a las líneas estratégicas de una campaña y de una guerra”, En este almacén se gestiona el stock y se suministran las mercancías correspondientes a los almacenes regionales. Almacén regional El almacén regional se sitúa en una zona de expedición menor, con el objetivo de cubrir las necesidades de un ámbito geográfico concreto en el que los productos se puedan distribuir rápidamente. De hecho, su zona de influencia no debe ser superior a una jornada para que considere como almacén regional. Almacén de tránsito Se encuentra en un punto intermedio entre almacén regional y el centro de consumo cuando entre ellos hay una distancia de más de un día. Almacén temporal Son almacenes temporales o de depósito que sirven para almacenar el stock durante las subidas de demanda de un bien determinado. Medios de Almacenaje La situación del mercado actual señala un continuo incremento del número de almacenes automáticos como respuesta a las necesidades de la logística moderna. De acuerdo con, (Mane, 2012) “El almacén es un lugar especialmente estructurado y planificado para custodiar, proteger y controlar los bienes de activo fijo o variable de la empresa, antes de ser requeridos para la administración, la producción o la venta de artículos o mercancías”. Varias son las razones para que las empresas, tanto grandes multinacionales como
Estanterías convencionales para paletas (racks). -Son estanterías que se ajustan a los pallets y ofrecen acceso directo a todas las paletas. La altura del nivel de carga está simplemente limitada a las dimensiones del edificio y del equipo de manutención utilizado. Son especialmente indicadas para el almacenaje de productos heterogéneos de muchas referencias y baja rotación. Entre sus ventajas destacamos el almacenamiento ordenado y la posibilidad de construcción a gran altura gracias a la utilización de carretillas u otros equipos de depósito o extracción. Estanterías compactas para pallets. -Este tipo de estanterías permite el almacenaje en bloque. Recomendadas especialmente para productos homogéneos y para necesidades de alta densidad de almacenamiento. Son ideales para cámaras frigoríficas y congeladores y son alimentadas básicamente con carretillas de mástil retráctil. Estas estanterías son una solución ideal para almacenar gran cantidad de pallets del mismo producto. Estanterías dinámicas por gravedad (para paletas o para productos sueltos ). - Se aplica el principio FIFO (primera paleta que entra, primera que sale). Las paletas se desplazan por unos rodillos ligeramente inclinados. Presentan la posibilidad de incorporar pequeños motores reductores o cilindros de aire para el accionamiento de las hileras de rodillos. Son recomendadas especialmente para almacenes intermedios, zonas de expedición, etc. Se aconsejan para productos homogéneos y perecederos. Proporcionan un almacenamiento ordenado para una rápida localización y con ellas se minimizan los desplazamientos de las carretillas. Estanterías móviles sobre raíles. -Es una forma de compactar un almacén suprimiendo pasillos. Esta opción es interesante para cargas pesadas o convencionales ofreciendo la máxima utilización del volumen disponible. Su accionamiento es manual en caso de sistemas pequeños y de productos de poco peso y mecánico para estanterías largas, cargas pesadas, múltiples productos con actividad de picking muy frecuente. Con este sistema el aprovechamiento del espacio es máximo y ofrece gran flexibilidad
Auto portantes para palets. -Estos sistemas ahorran la obra civil y soportan el edificio. Alcanzan grandes alturas con lo que el aprovechamiento del espacio es máximo. En estos el producto se manipula con carretillas retráctiles, trilaterales y transe levadores Estanterías para pequeños productos sueltos (sin paletizar). -Se trata de estanterías convencionales de uno o varios niveles (con contenedores o separadores modulares). En este se incluyen los sistemas automáticos para el almacenamiento de este tipo de productos, entre los que destacan los paternóster (ascensores que se desplazan de forma continua usado para el transporte de mercancías, debiendo subir y apearse en marcha), los carruseles y los miniloads (para el almacenamiento de piezas pequeñas. Estanterías de ángulo rasurado. - Son estanterías tradicionales, con o sin tornillos, para cargas ligeras. Son prácticas, de fácil montaje y adaptables a todos los sectores de actividad Estanterías tipo Cantiléver. -Son ideales para el almacenamiento de cargas largas (varillas, tubos, muebles, perfiles, maderas, paneles, carpintería metálica, etc.). Una variedad de esta estantería sería la estantería tipo Cantiléver a doble lado que permite el almacenamiento en ambas caras de la estantería Estanterías entreplantas. -Son estanterías fácilmente desmontables y adaptables, duplican el espacio del habitáculo disponible Estantería de pallets de tubos. -Son estanterías convencionales que permiten el almacenamiento de tubos mediante pallets Medios de Transporte Hay muchas formas distintas de mover físicamente un producto de un lugar a otro, pero en la mayoría de los casos las modalidades de transporte se concretan en las siguientes: Terrestre: Por carretera: furgoneta, camión, furgón o vehículo similar. Por ferrocarril: tren.
La navegación aérea. -Los transportes de mercancías por aire, limitados en un principio a pequeños paquetes, se han desarrollado enormemente, sobre todo a partir de la creación de líneas regulares de carga aérea atendidas por aviones de carga perfectamente preparados. Normalmente, este sistema aéreo se utiliza especialmente para cargas de gran valor, tonelajes reducidos y que necesitan una gran rapidez de transporte, además de necesitar una garantía de seguridad en su entrega, sobre todo cuando se emplee en mercancías frágiles y delicadas. Oleoductos, cintas transportadoras, etc .-Este tipo de transporte se adapta bien a los tráficos masivos y regulares e, incluso mejor, a los permanentes o casi permanentes. Áreas de Almacenaje Normalmente una planta fabricante o una empresa comercializadora debe tener tres áreas en el almacén, como base de su planeación:
de permanencia de las mercancías en el área de recepción debe ser lo más corta posible, pues el espacio y el costo de operación depende de la fluidez con que estas se pasan del vehículo del proveedor al almacén. Todo estancamiento innecesario eleva el costo del producto. Área de Almacenamiento: En la zona de almacenamiento se estudia el espacio que se requiere para cumplir con las finalidades del almacén, ya que ello exige realizar las operaciones que forman el ciclo de almacenamiento, para lo cual es indispensable disponer de espacio suficiente donde se pueda actuar organizadamente, sin inconvenientes ni tropiezos. El estudio que se haga para elegir una zona de almacenamiento o para distribuir una zona ya elegida, tiene que realizarse en función de tres factores: Entidad a la cual se va servir. El espacio de que se dispone. Los artículos que en él se van a guardar. Para determinar en relación con ellos, las características que debe reunir. Área de Entrega: La mercancía que ha sido tomada del área de almacenamiento y llevada al área de entrega debe: Ser trasladada con el medio mecánico más adecuado. Ser acompañada de un documento de salida, una nota de remisión o una factura. Ser revisada en calidad y cantidad, mediante el cotejo de la mercancía con el documento de salida. Clasificación de inventarios La clasificación es una de las mejores medidas de control interno de inventarios, dado que de aplicarse correctamente puede permitir mantener el mínimo de capital invertido en stock, entre muchos otros beneficios. Inventario Físico Como es lógico este inventario se hace in situ, llevando a cabo una revisión de las mercancías almacenadas, quedando reflejados en las notas, las unidades, (Westreicher, 2019) “Es decir, efectuar un inventario físico es similar a organizar
organizaciones, cada organización y sistema de inventarios tiene sus particularidades, y que quién aplique cada principio de ponderación debe estar sumamente consciente de la realidad de su empresa. La optimización del inventario es crítica para poder mantener los costes bajo control dentro de la cadena de suministro. No obstante, para poder aprovechar al máximo los esfuerzos de los gerentes, resulta eficaz concentrarse en los artículos que cuestan más al comercio. El principio de Pareto establece que el 80 % del valor de consumo total se basa solo sobre el 20 % de los artículos totales. En otras palabras, la demanda no está distribuida uniformemente entre los artículos: los que más se venden superan ampliamente a los demás. El método a desarrollar es el ABC establece que al revisar el inventario se debería se deben clasificar los artículos de la A y la C, basados en la clasificación ¿Cómo Realizar La Clasificación ABC? La clasificación ABC se realiza con base en el producto, el cual expresa su valor por unidad de tiempo (regularmente anual) de las ventas de cada ítem i , donde: D i = Demanda "anual" del ítem i (unidades/año) V i = Valor (costo) unitario del ítem i (unidades monetarias/unidad) Valor Total i = Di * v i (unidades monetarias/año) Antes de aplicar el anterior ejercicio matemático a los ítems es fundamental establecer los porcentajes que harán que determinadas unidades se clasifiquen en sus respectivas zonas (A, B o C). Luego de aplicarse las operaciones para determinar la Valorización de los artículos, se procede a calcular el porcentaje de participación de los artículos, según la valorización (suele usarse también en cantidad, "participación en cantidad"). Este ejercicio se efectúa dividiendo la Valorización dé cada ítem entre la suma total de la valorización de todos los ítems.
Las políticas de inventarios de la empresa deben conducir a conseguir una alta rotación de inventarios, para así lograr maximizar la utilización de los recursos disponibles. Diagrama de Pareto: también llamado curva cerrada o Distribución A-B-C, es una gráfica para organizar datos de forma que estos queden en orden descendente, de izquierda a derecha y separados por barras. Permite asignar un orden de prioridades. Optimización de Inventario: La optimización del inventario es un método para lograr la mejor solución al problema de la cantidad de inventario necesario y su localización. Método ABC: El análisis ABC es un método de clasificación frecuentemente utilizado en gestión de inventario. Resulta del principio de Pareto. El análisis ABC permite identificar los artículos que tienen un impacto importante en un valor global. Demanda Anual: La noción de demanda hace referencia a una solicitud, petición, súplica o pedido. Coste de Articulo: Es aconsejable hacerlo de manera anual, aunque claro también se puede hacer en otros períodos de tiempo como mensual, trimestral, semestral, etc. Número de Órdenes : Es un documento que emite el comprador para pedir mercaderías al vendedor; indica cantidad, detalle, precio y condiciones de pago, entre otras cosas. El documento original es para el vendedor e implica que debe preparar el pedido. Transe levadores: Los transelevadores o tras los son robots creados para el almacenamiento automático, tanto de palés como de unidades con menores dimensiones. Miniloads: Es un sistema estándar para bandejas o cajas que integra tanto las estanterías, maquinaria y software de gestión del almacén en un solo producto.
Cantiléver: Especialmente diseñadas para el almacenaje de unidades de carga de gran longitud o con medidas variadas.