
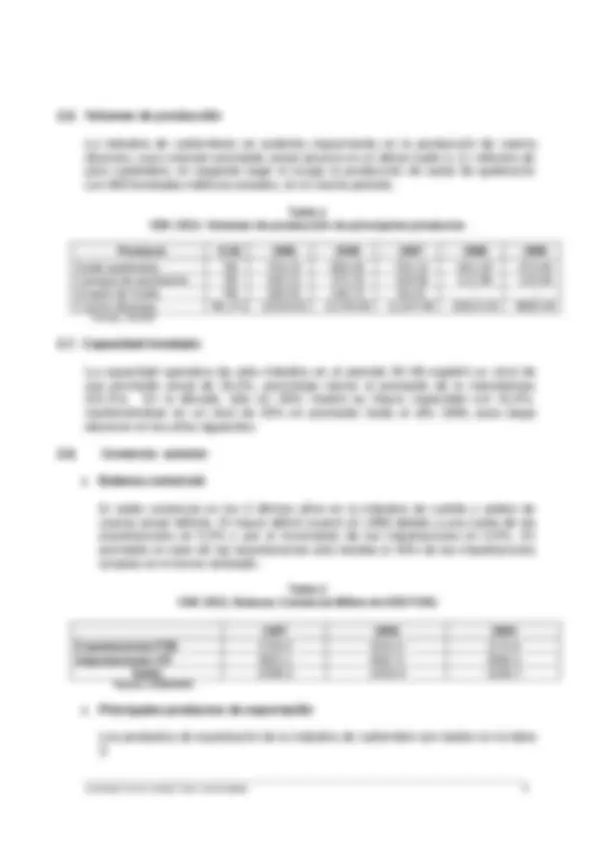
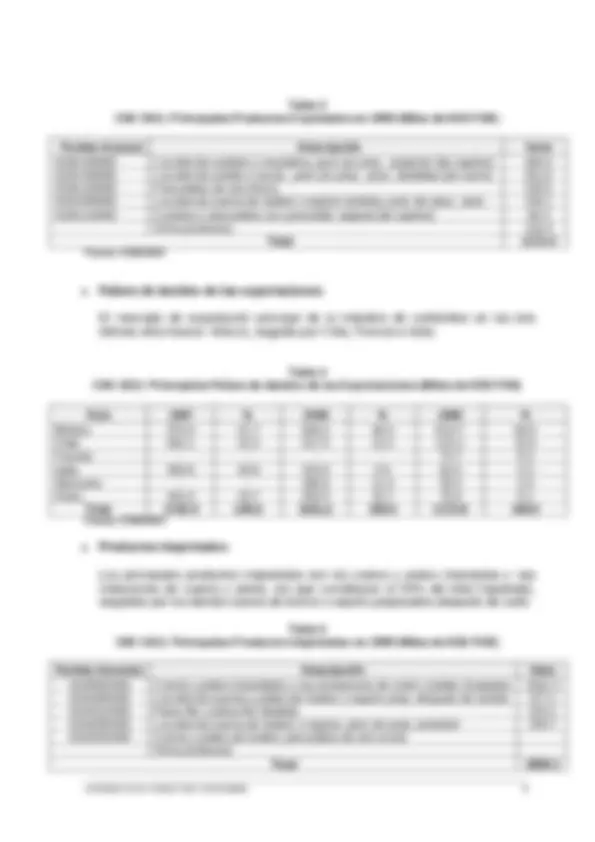
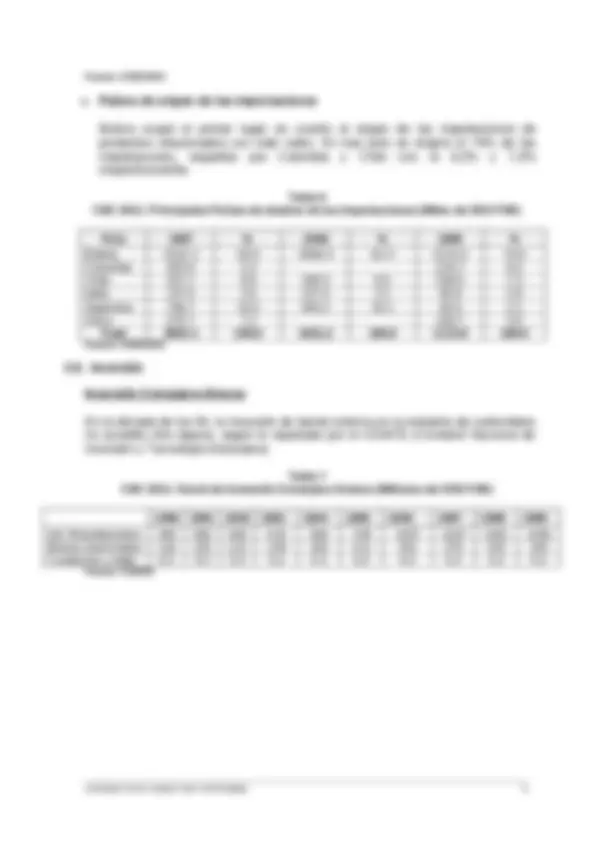

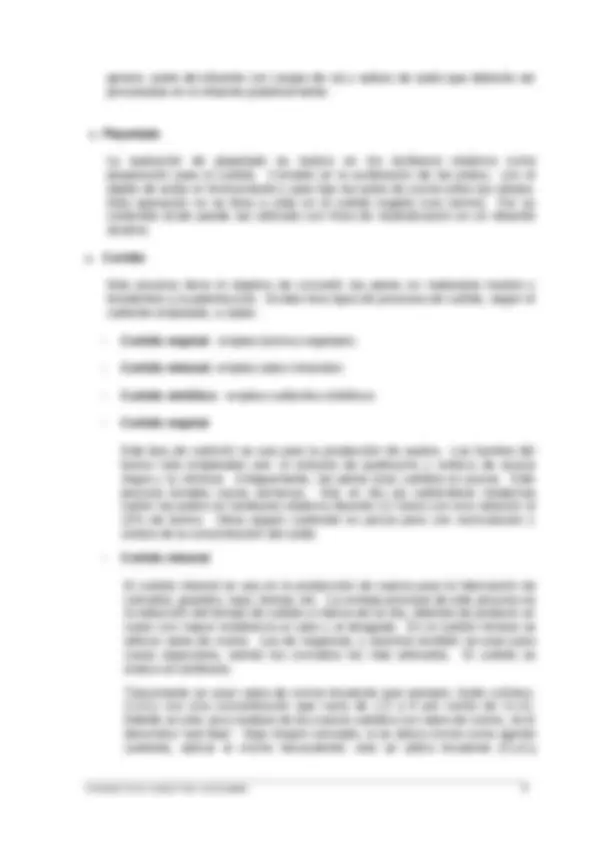
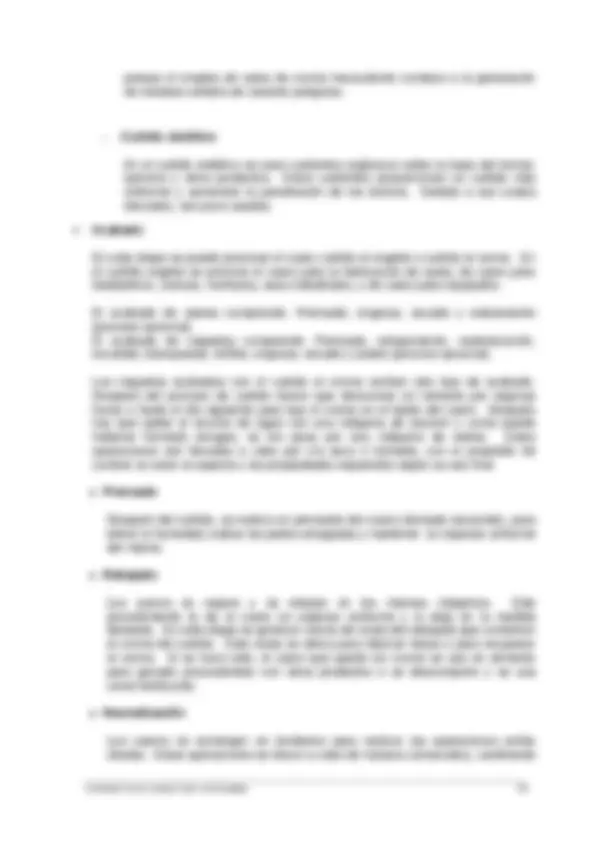
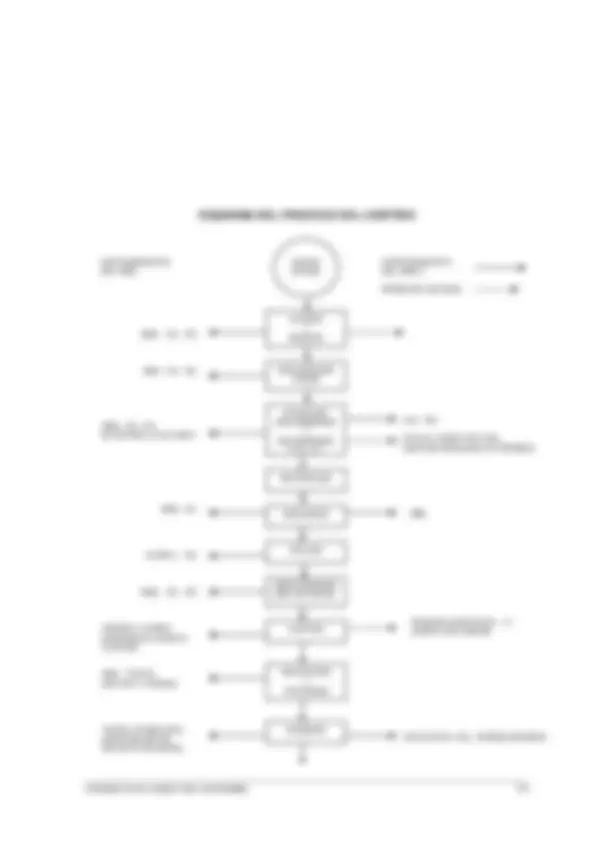
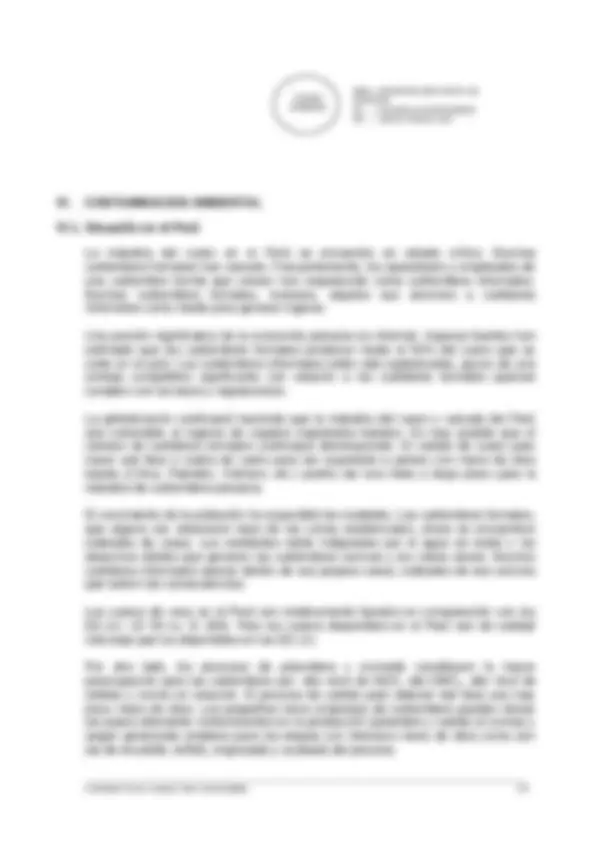
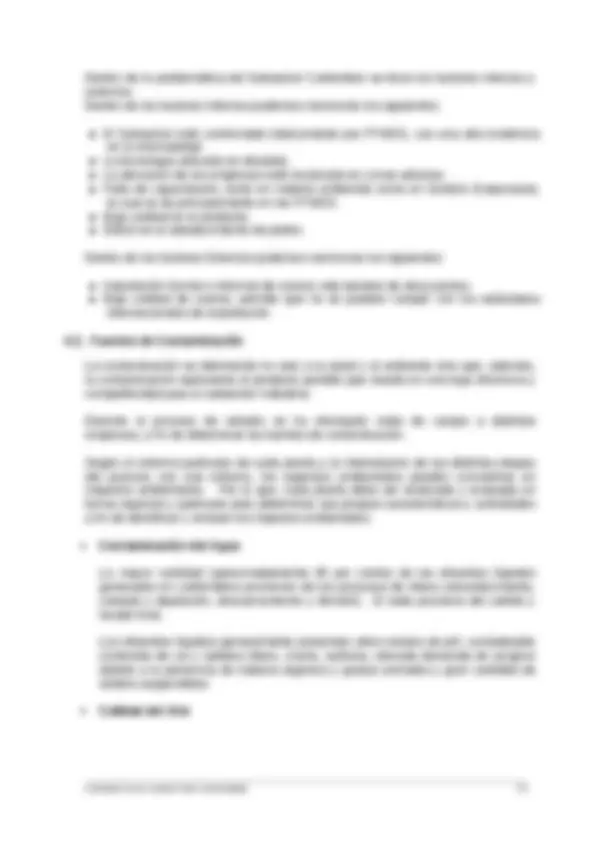
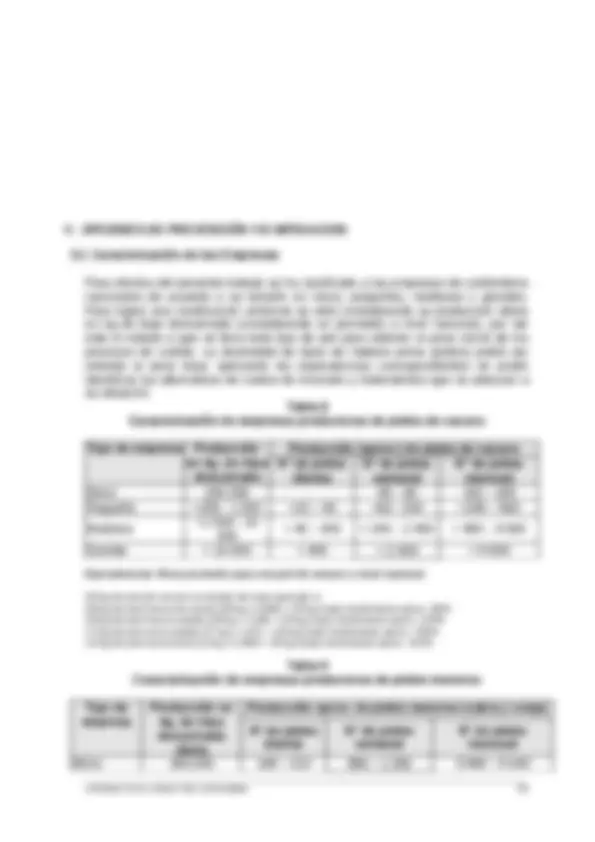
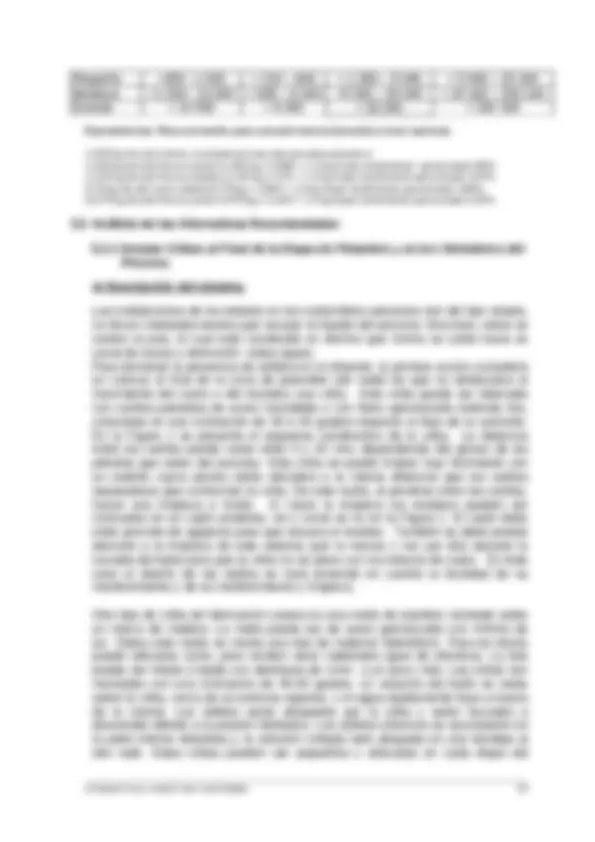
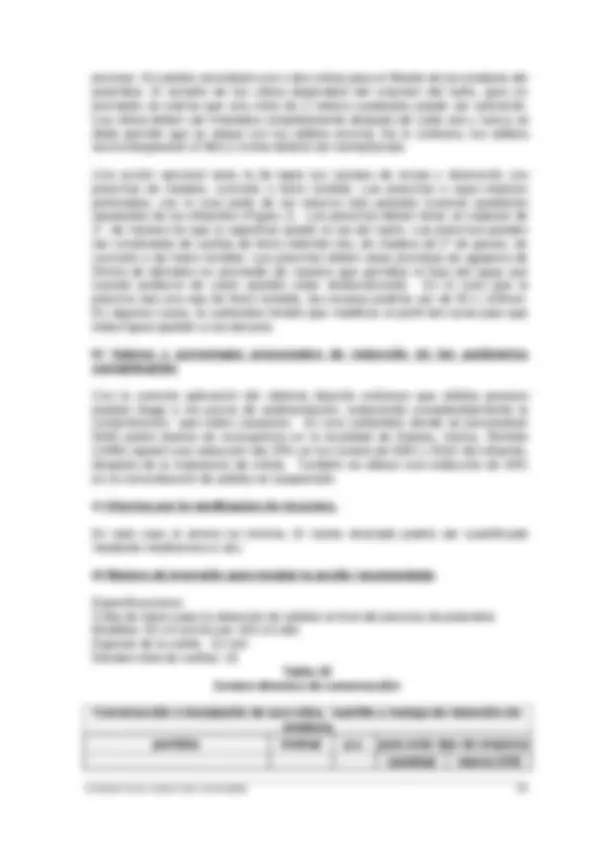
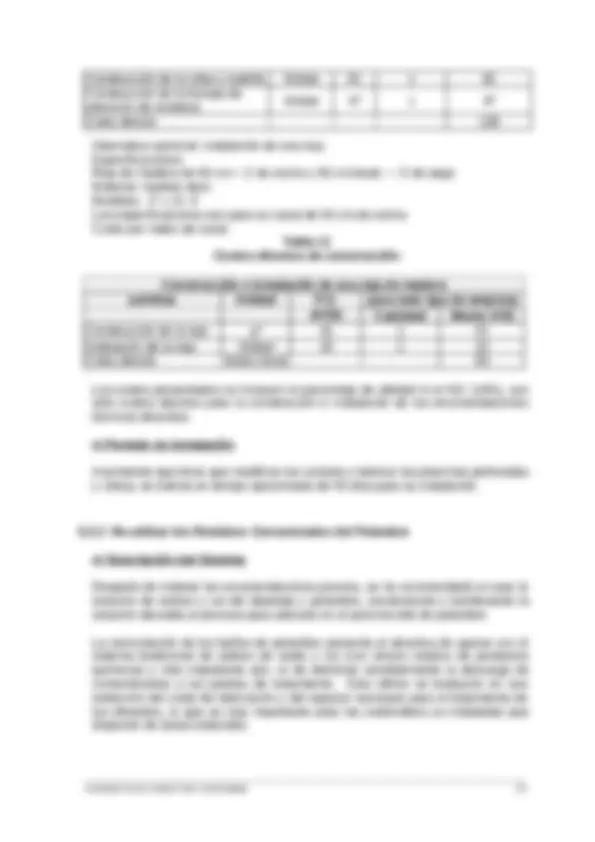
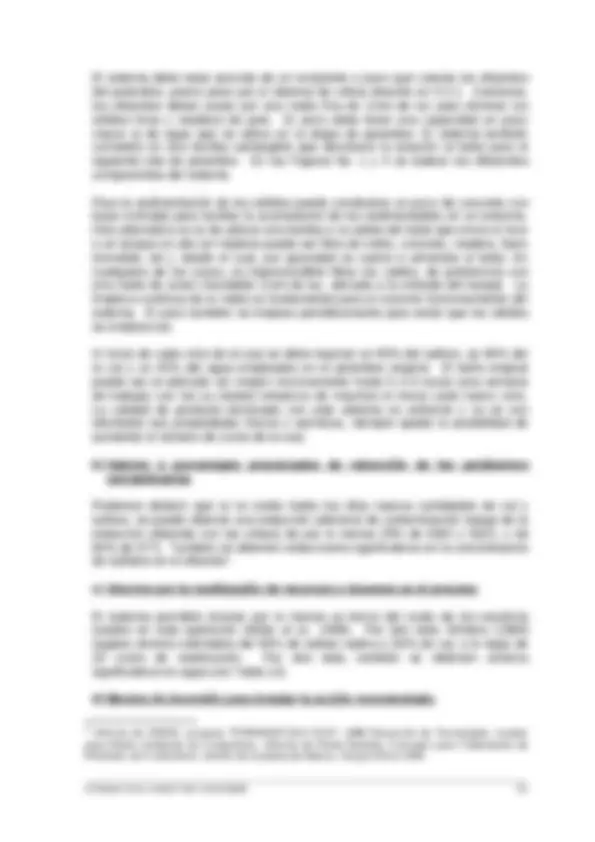
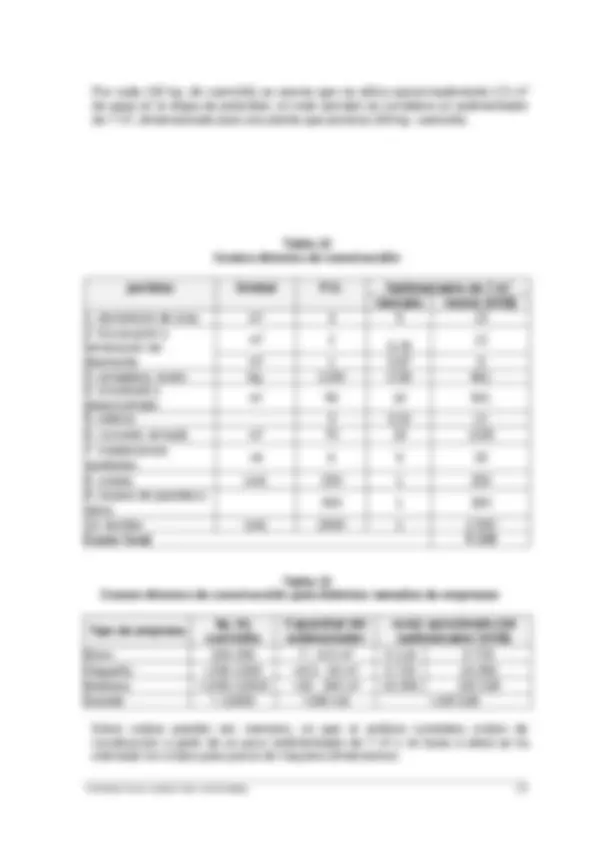
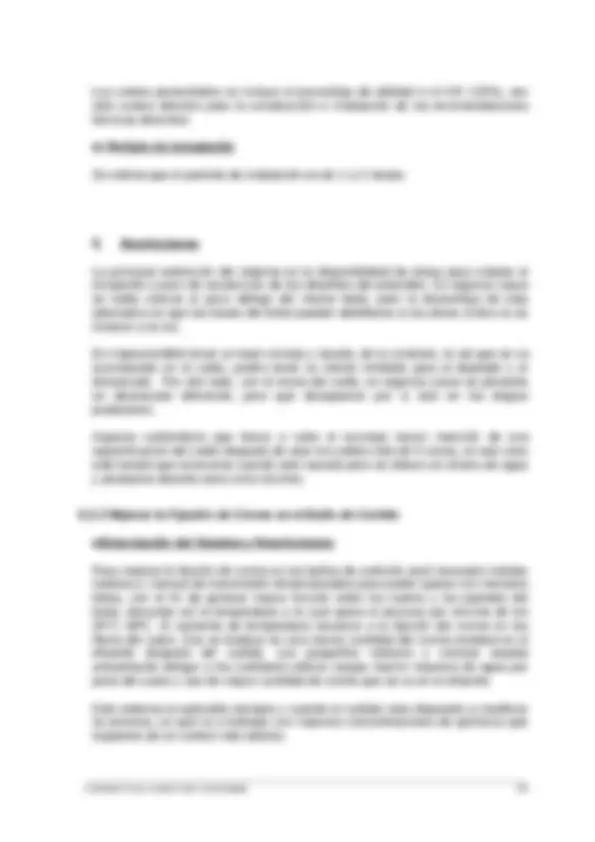
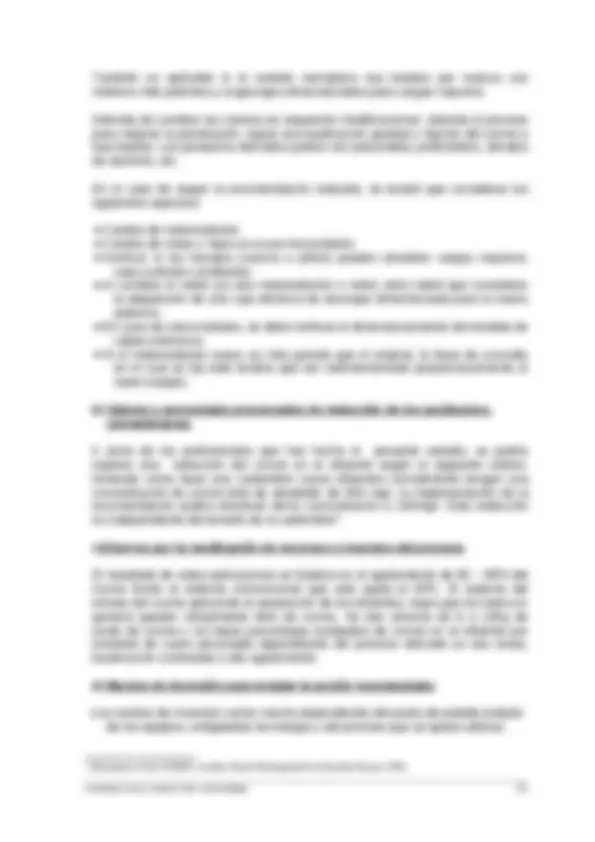
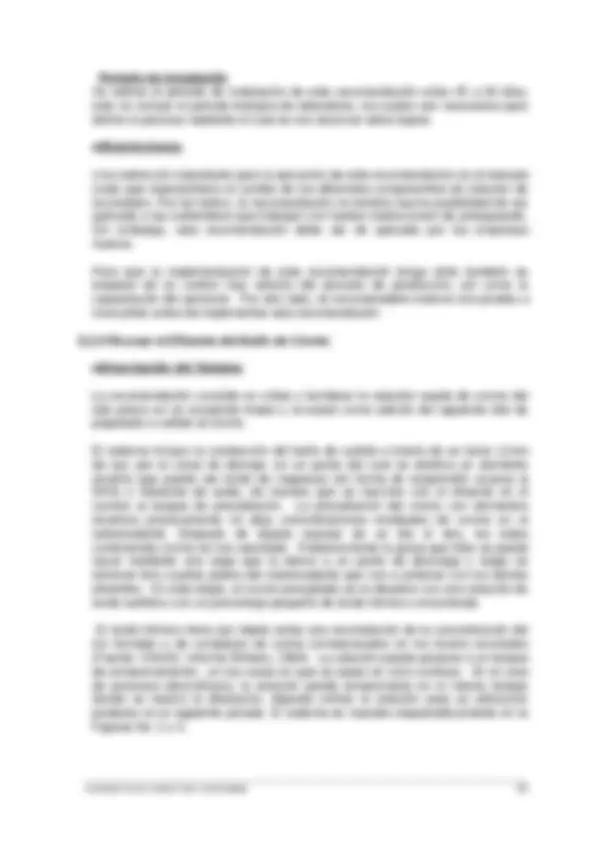
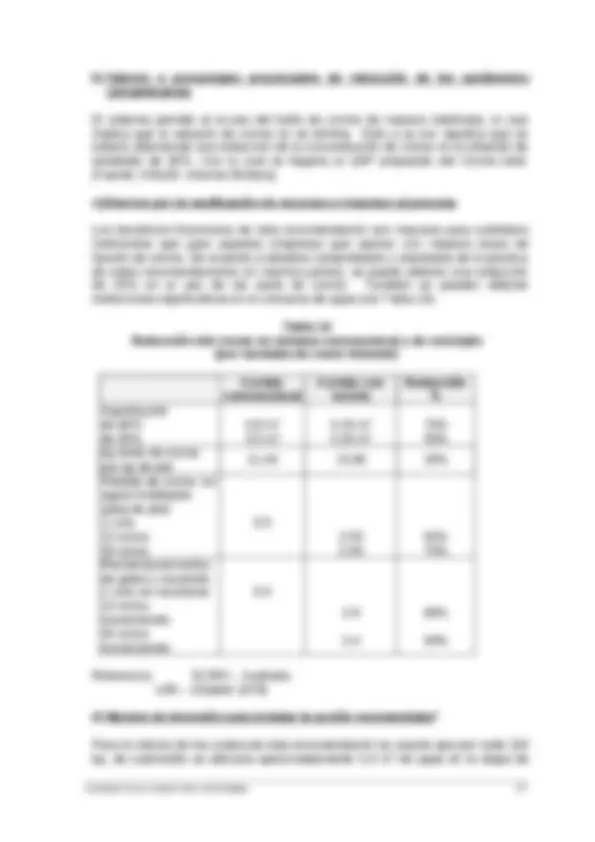
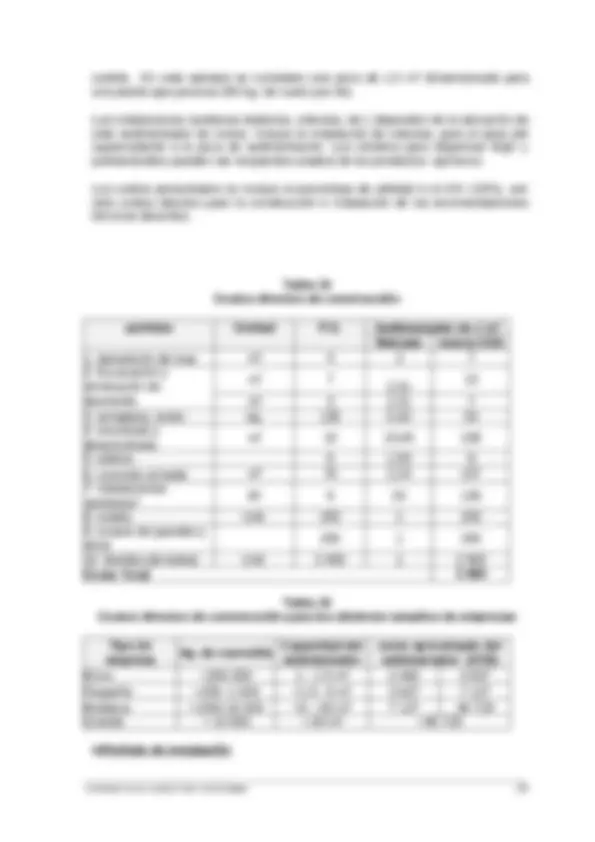
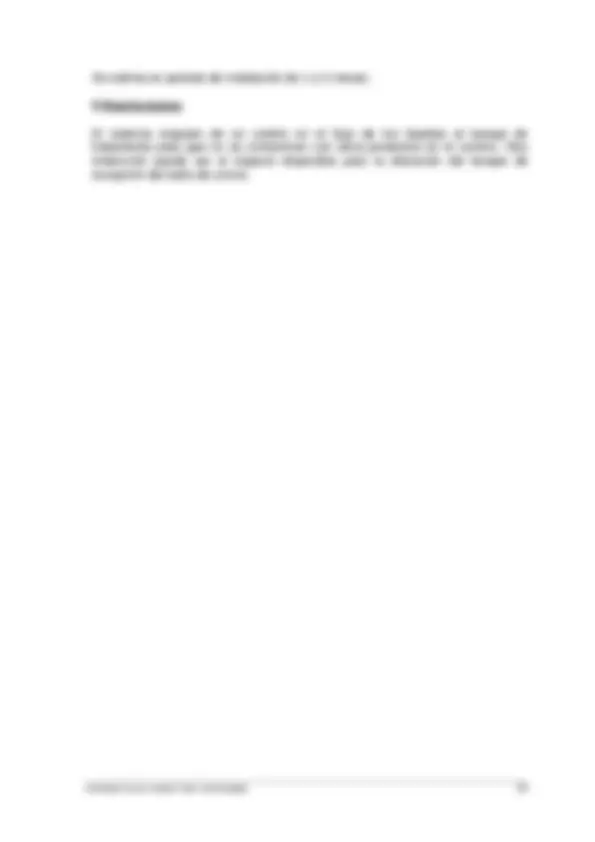
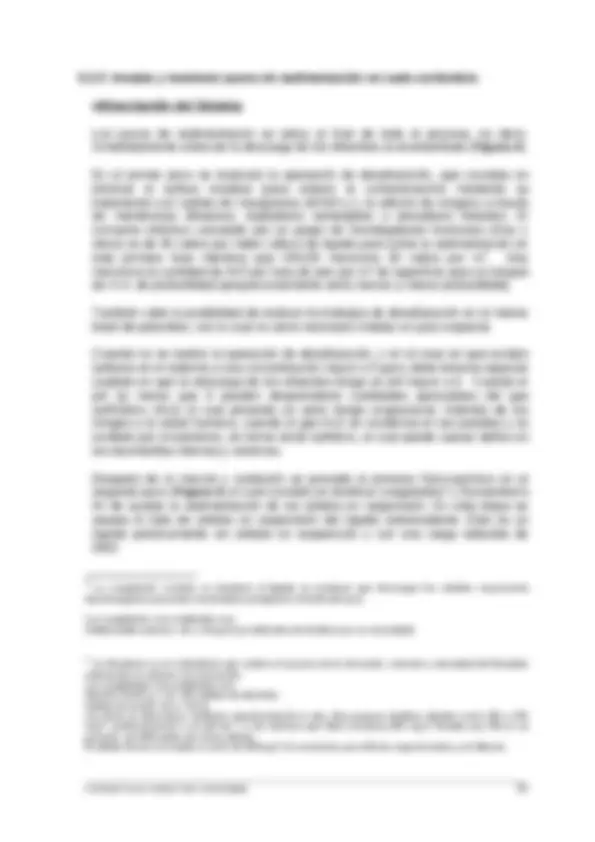
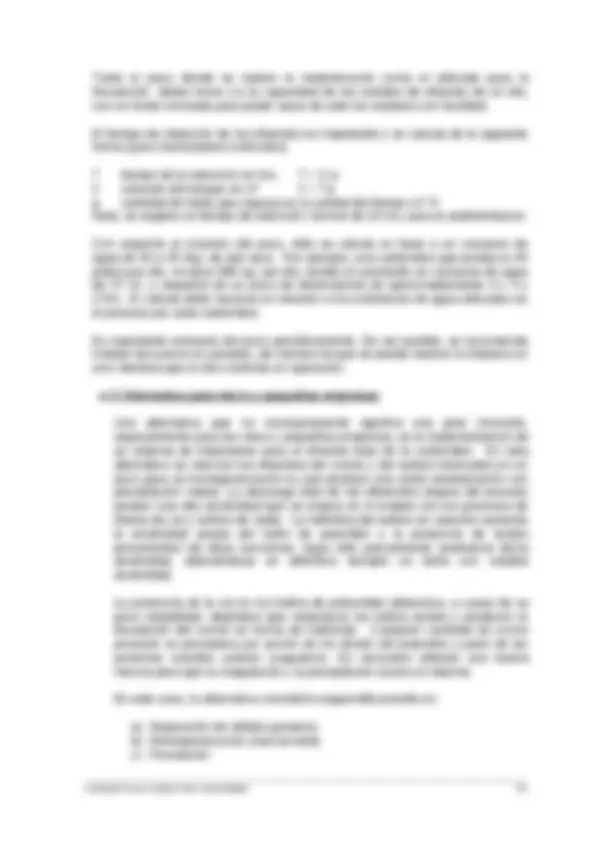
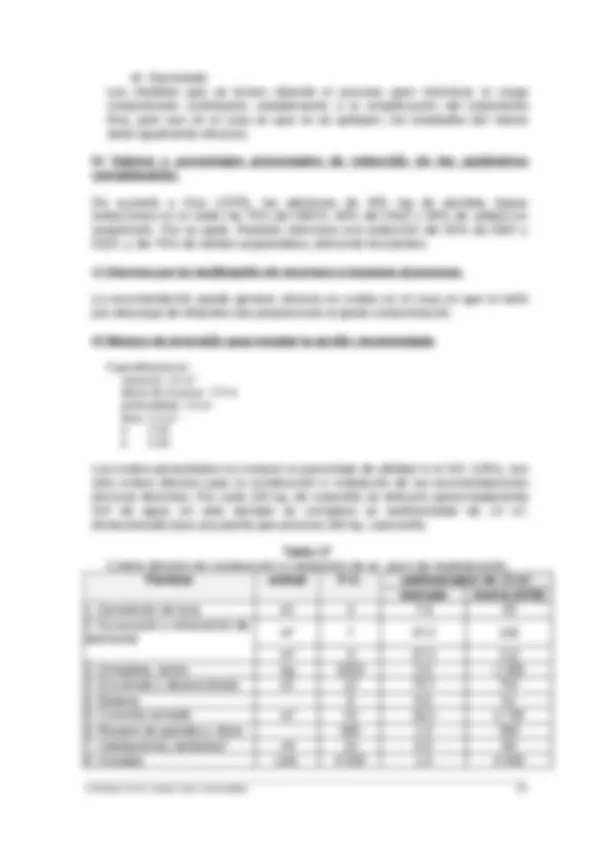
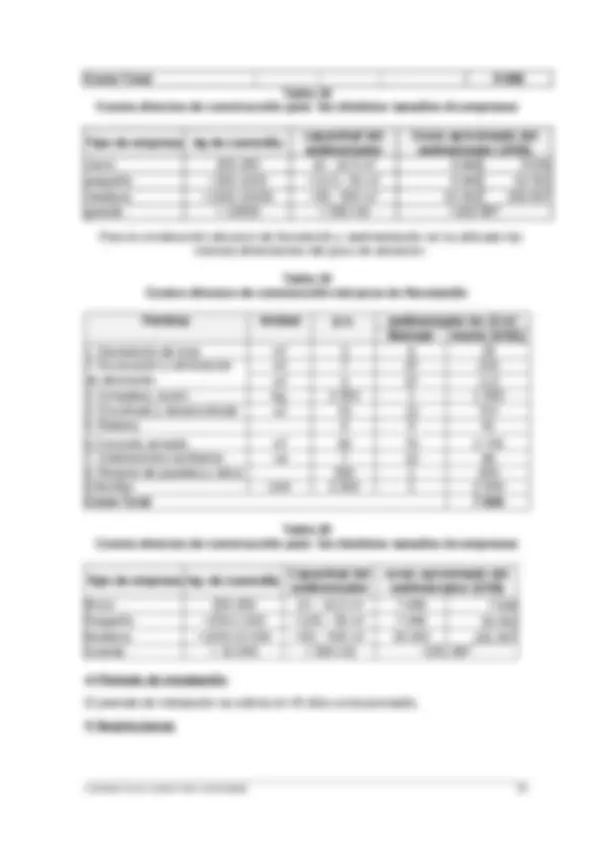
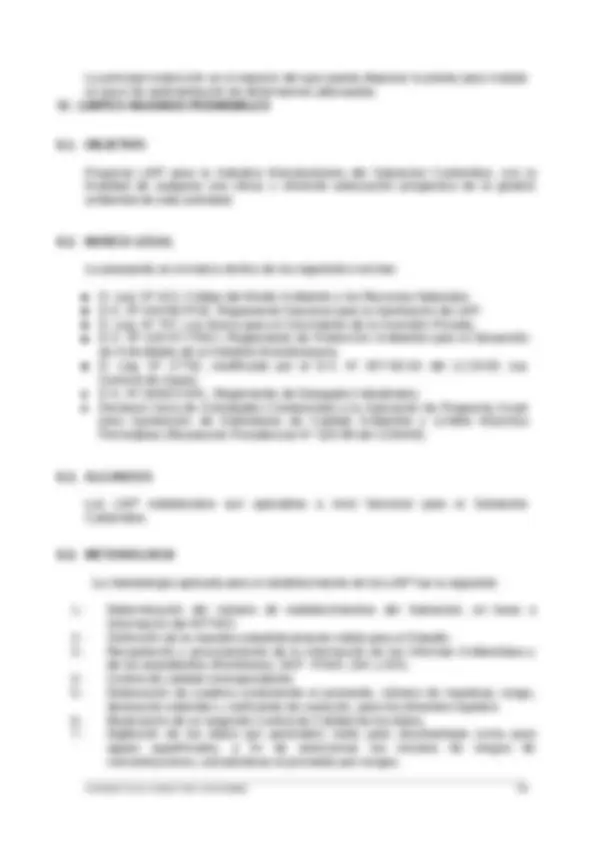
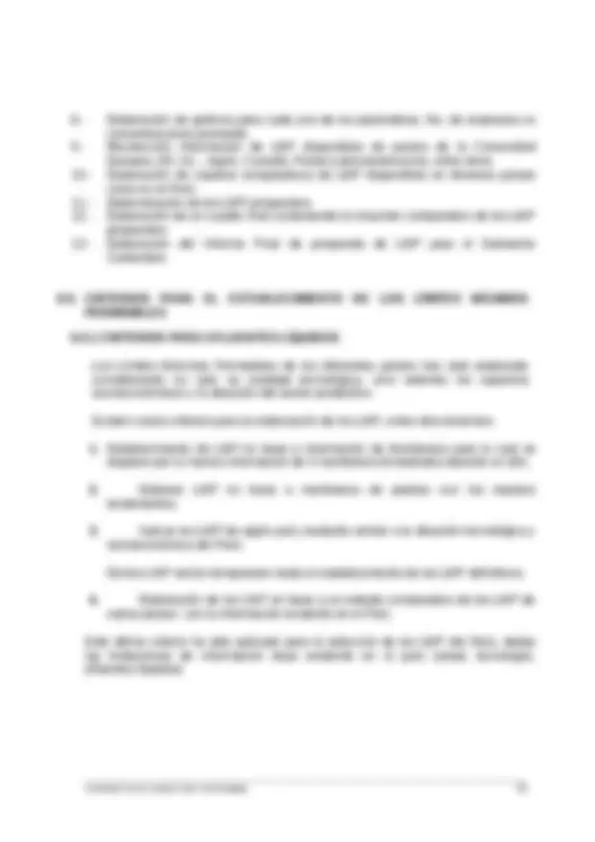
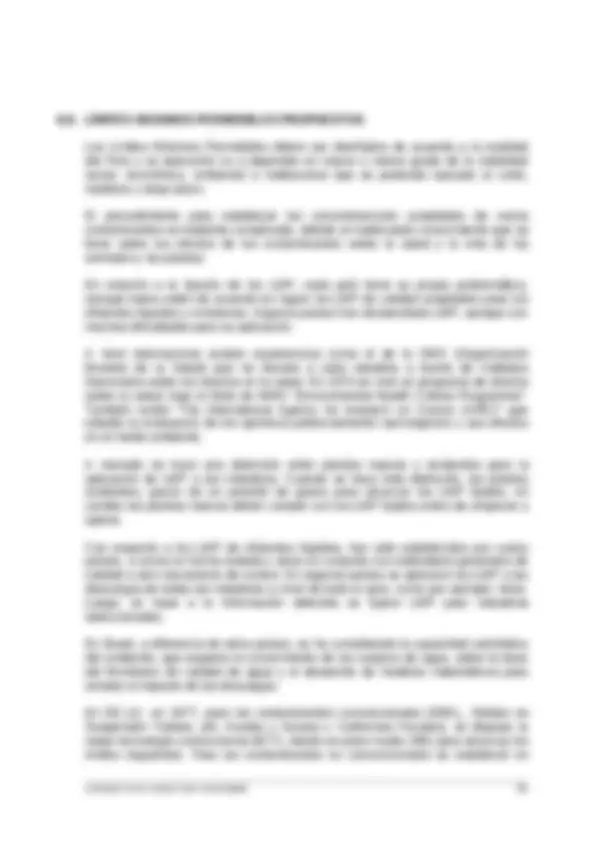
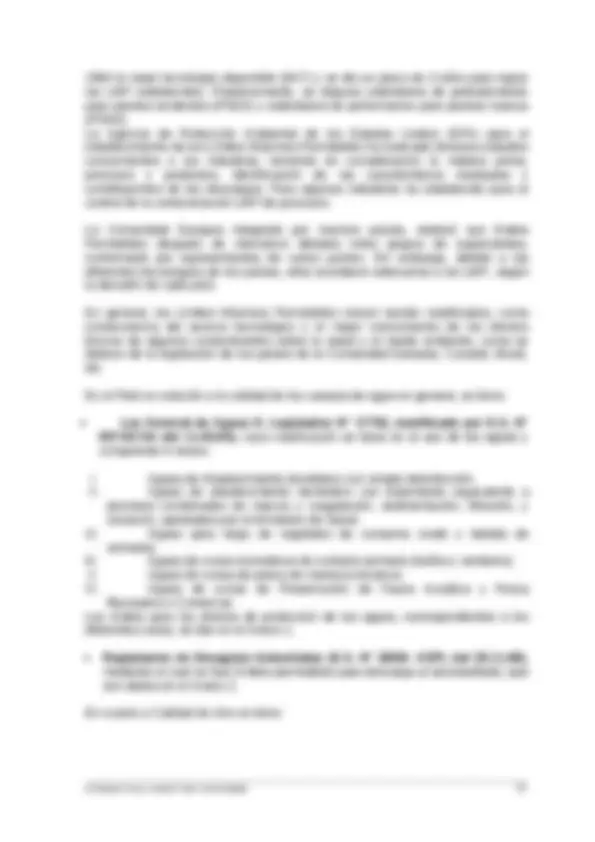
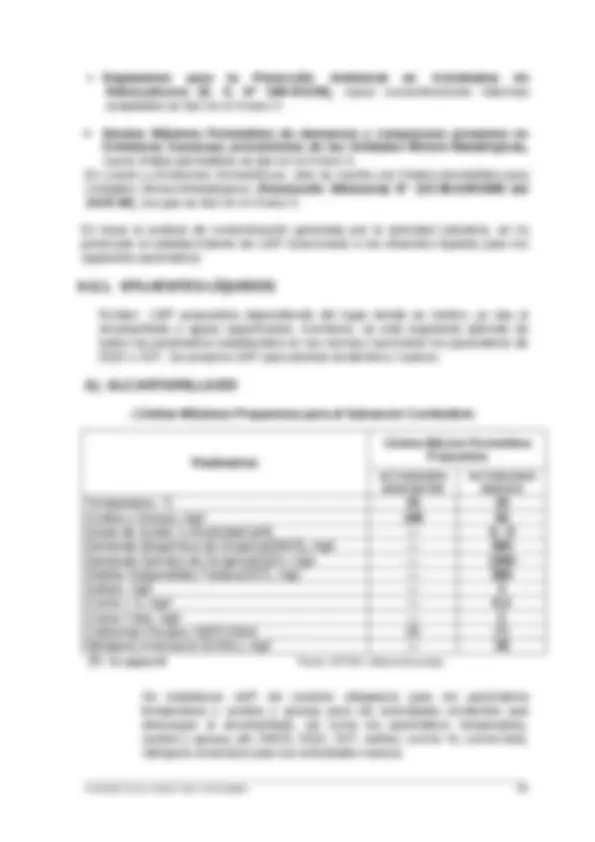
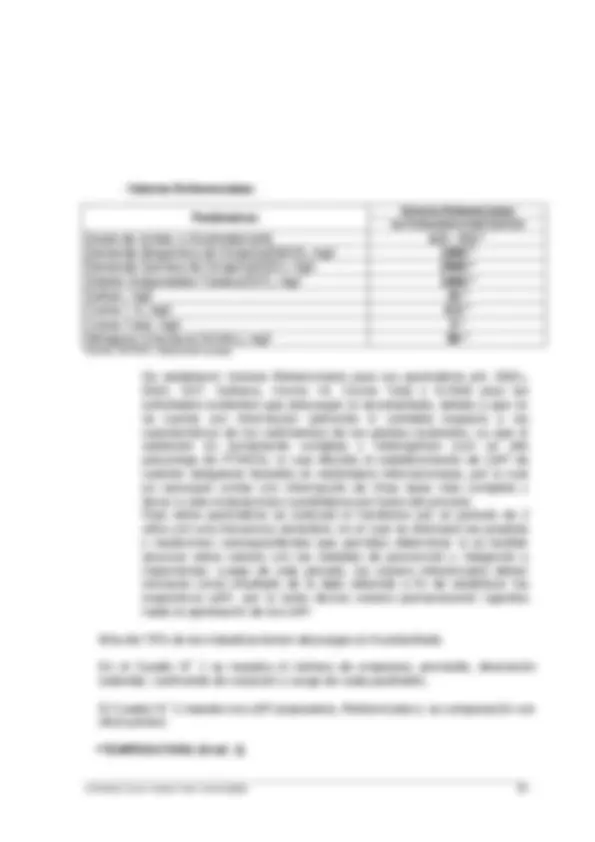
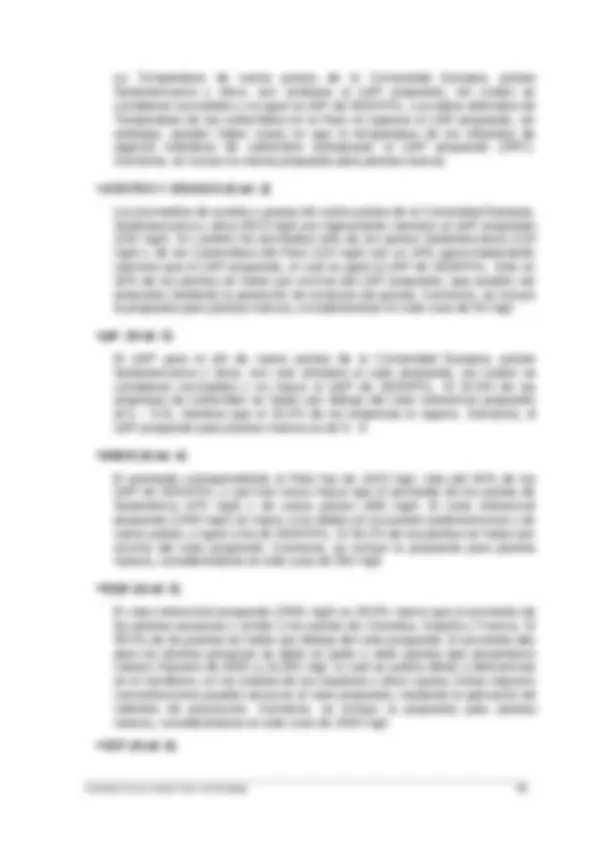
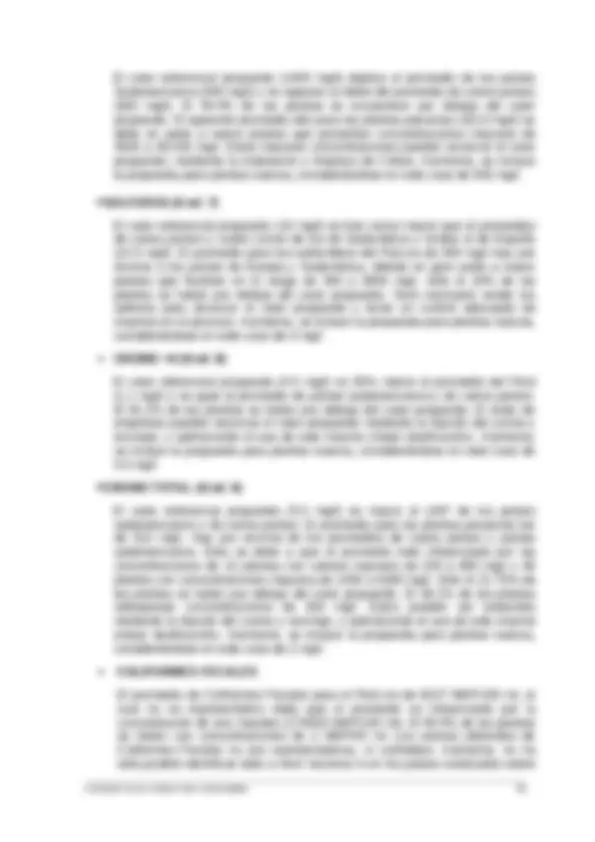
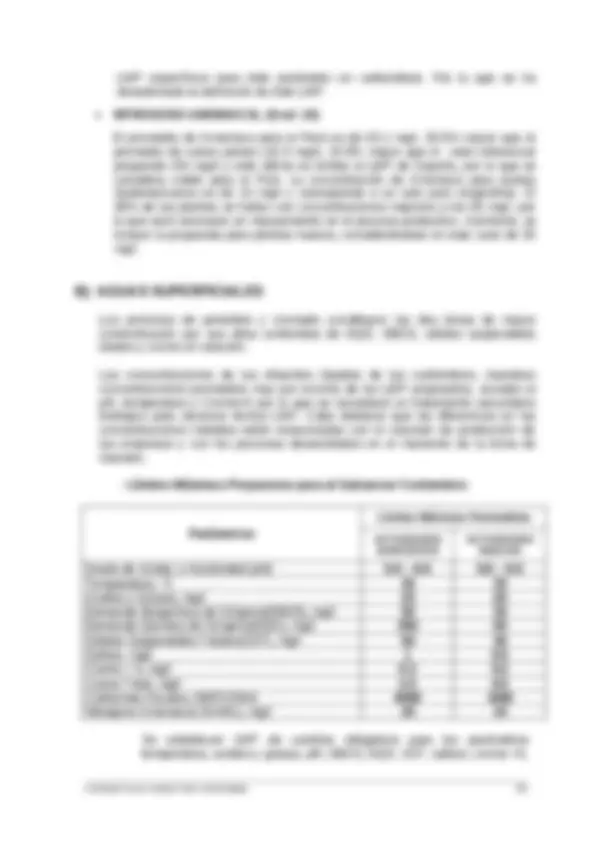
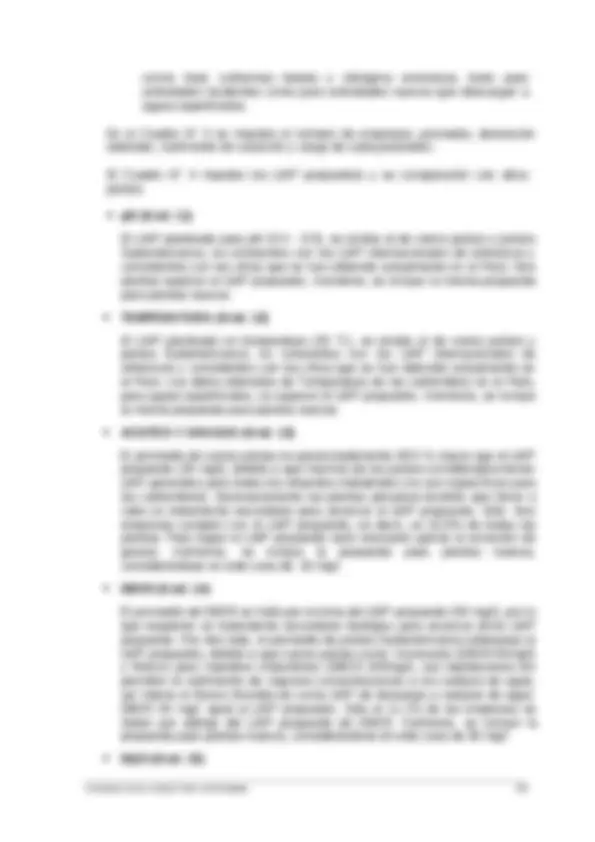
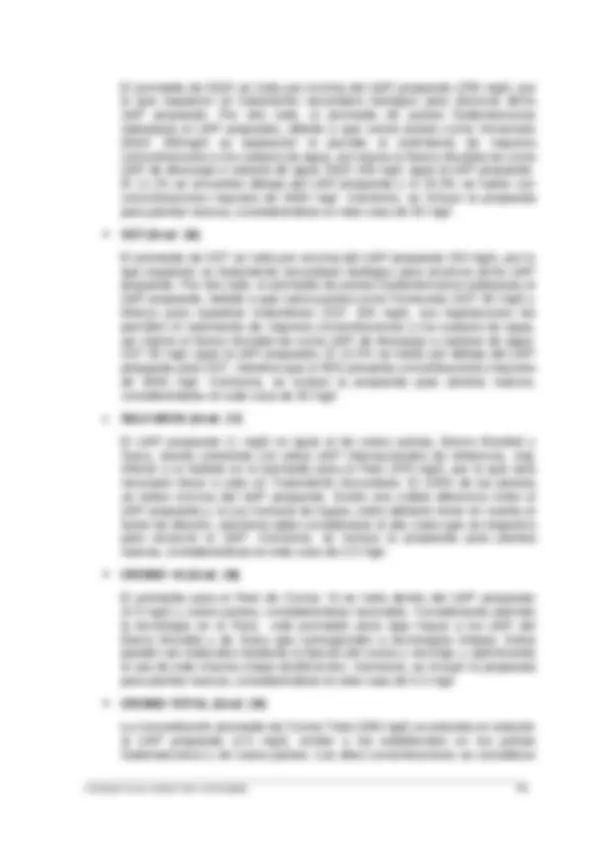
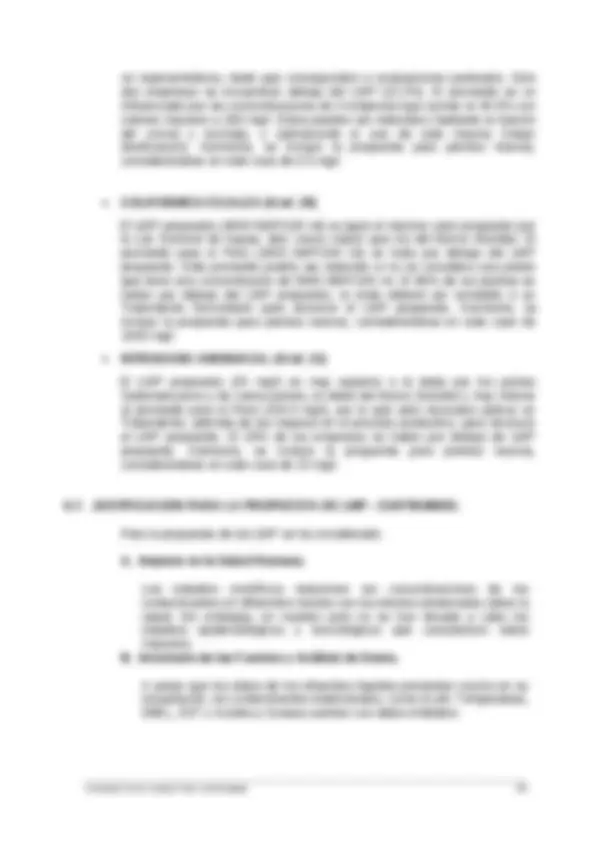
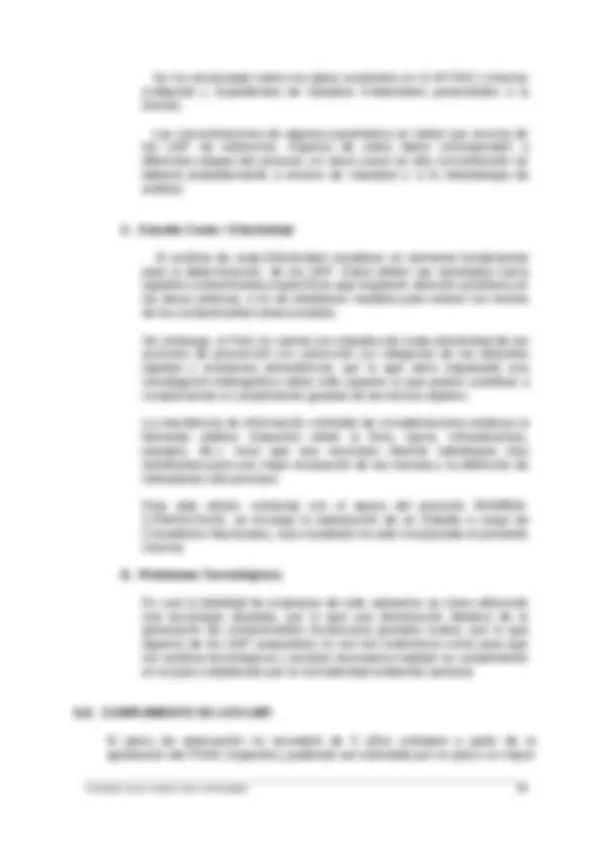
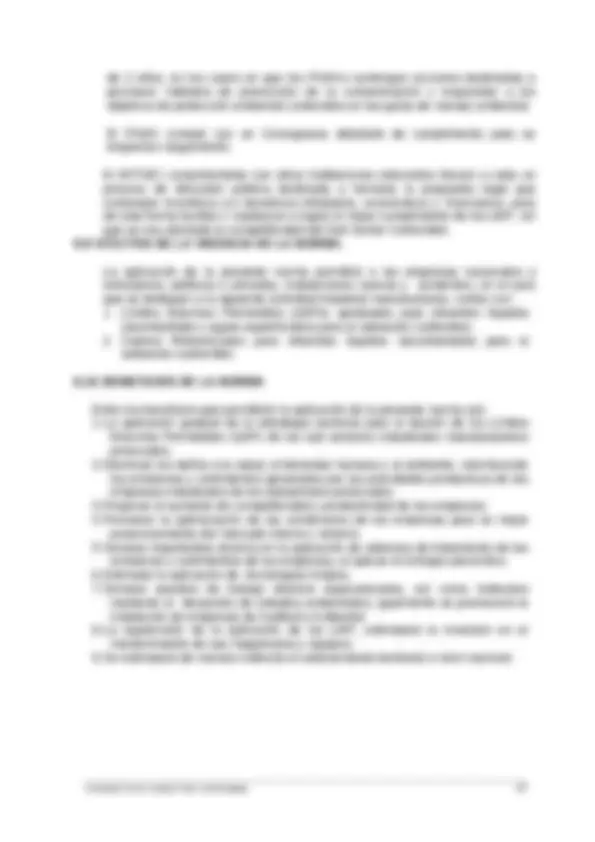
Prepara tus exámenes y mejora tus resultados gracias a la gran cantidad de recursos disponibles en Docsity
Gana puntos ayudando a otros estudiantes o consíguelos activando un Plan Premium
Prepara tus exámenes
Prepara tus exámenes y mejora tus resultados gracias a la gran cantidad de recursos disponibles en Docsity
Prepara tus exámenes con los documentos que comparten otros estudiantes como tú en Docsity
Los mejores documentos en venta realizados por estudiantes que han terminado sus estudios
Estudia con lecciones y exámenes resueltos basados en los programas académicos de las mejores universidades
Responde a preguntas de exámenes reales y pon a prueba tu preparación
Consigue puntos base para descargar
Gana puntos ayudando a otros estudiantes o consíguelos activando un Plan Premium
Comunidad
Pide ayuda a la comunidad y resuelve tus dudas de estudio
Descubre las mejores universidades de tu país según los usuarios de Docsity
Ebooks gratuitos
Descarga nuestras guías gratuitas sobre técnicas de estudio, métodos para controlar la ansiedad y consejos para la tesis preparadas por los tutores de Docsity
Este documento analiza la industria de curtiembres en el perú, enfocándose en la contaminación generada, los productos importados y las mejoras propuestas en el proceso productivo. Se incluyen datos sobre la producción anual de cueros diversos y suela de quebracho, así como la importación de cueros y pieles charoladas y sus imitaciones. Además, se proponen soluciones para disminuir la presencia de sólidos en el efluente y mejorar la fijación de cromo en el baño de curtido.
Tipo: Resúmenes
1 / 47
Esta página no es visible en la vista previa
¡No te pierdas las partes importantes!
El MITINCI luego de la aprobación del “Reglamento de Protección Ambiental para el Desarrollo de Actividades de la Industria Manufacturera”, D.S. N° 019-97-ITINCI del 01.10.1997, dada la complejidad y diversidad de subsectores industriales bajo su ámbito de competencia, decidió trabajar en cuatro subsectores priorizados: Cerveza, Cemento, Curtiembre y Papel. A partir de ese momento, se ha venido desarrollando una ardua labor, en cada uno de los mencionados subsectores, destinados a definir las propuestas de Límites Máximos Permisibles, así como la estrategia a ser utilizada para su adecuación. Al inicio de nuestra gestión se contó con el asesoramiento especializado brindado por expertos proporcionados por el proyecto SENREM (convenio CONAM/USAID), el cual involucró reuniones técnicas de coordinación y visitas de campo a una muestra de empresas del subsector que permitieron conocer el proceso productivo y determinar las opciones de prevención de la contaminación que pudieran ser aplicadas. Como producto de este trabajo se elaboró el respectivo informe técnico que incluyó el diagnóstico del subsector y las recomendaciones respectivas con propuestas de Límites Máximos Permisibles para algunos parámetros, para el caso de efluentes líquidos y emisiones atmosféricas Posteriormente, y dado que no se contaba con un sustento completo de las propuestas referidas a los Límites Máximos Permisibles, se decidió contratar a una empresa consultora nacional, la misma que realizó una evaluación de la propuesta del Proyecto SENREM (convenio CONAM/USAID), elaboró “Guías de Buenas Prácticas” y también estructuró una nueva propuesta de LMP para el caso de efluentes líquidos y calidad de aire. Luego, mediante Resolución Ministerial N° 054-2000-ITINCI/DM de fecha 08.05.00, el MITINCI requirió la presentación del Informe Ambiental a todas las empresas pertenecientes a los subsectores priorizados, incluyendo la realización de monitoreos ambientales (emisiones atmosféricas, efluentes líquidos, ruido ambiental y disposición de residuos sólidos). Esta información fue revisada, depurada y procesada a fin de establecer de una manera más efectiva la línea base respectiva; no obstante, dado que subsiste el problema de limitaciones de información debido a que la misma consiste en datos puntuales e incompletos (no existe información específica de procesos), la metodología empleada ha sido la comparación del nivel promedio de emisión de contaminantes en cada subsector en el Perú (basada en el Informe Ambiental, Estudios Ambientales e información complementaria presentados al MITINCI), así como la comparación con LMP existentes en otros países, específicos a la Industria de Curtiembre. Es importante destacar, que para la elaboración del diagnóstico sectorial se contó con la información proporcionada por la Dirección Nacional de Industria de los Análisis Sectoriales correspondientes.
2.1. Principales líneas de producción Incluye la producción de cueros curtidos y adobados: curtidos vegetal, mineral y químico. Comprende también la fabricación de cueros gamuzados y apergaminados, charol y cueros metalizados, así como cueros regenerados, a saber planchas, hojas y tiras que contienen cuero o fibras de cuero. 2.2. Número de empresas por ubicación A nivel nacional a septiembre del 2000, las empresas registradas suman 438, de las cuales: el 30.1% se concentra en Lima, el 29.5% en Arequipa, el 24.2% en La Libertad, el 3.2% en Cuzco, el 2.7% en Junín y el 10.3% en el resto del país. 2.3. Tamaño de las empresas En 1999, el 89.2% corresponde a microempresas, 5.1% a pequeñas empresas, 4.0% a medianas y 1.7% a grandes empresas. 2.4. Mercado El subsector curtiembres procesa en mayor volumen pieles de vacunos, siendo inferior el de pieles de caprinos y ovinos. El mayor volumen de lo producido se destina al mercado interno, siendo vendidos al exterior las pieles de carnero, cabra y sajino. En cuanto a pieles de vacuno, se exporta un pequeño porcentaje en etapas de procesos de semiterminado o terminado. Una proporción muy considerable se destina a la industria de calzado, la que a su vez sufre una fuerte recesión agravada por las desmedidas importaciones sobre todo de origen asiático. La Sociedad Nacional de Industria ha señalado que el Perú es deficitario en pieles de vacuno, por lo que en una situación económica normal se requeriría importar una considerable cantidad de pieles. Además, la industria nacional no puede competir con los productos importados porque el arancel que se paga por los insumos en terceros países oscila entre 0 y 5%, mientras que en el Perú se paga el 15% de arancel. 2.5. Evolución de la producción La industria de curtiembre, en la década del 90, tuvo una fuerte contracción al registrar una tasa media de crecimiento de -5.3% anual, divergiendo de la tendencia creciente observada por la agrupación de bienes intermedios (al cual pertenece), que en conjunto logró una tasa de 5.82% anual, en el mismo periodo. Con excepción de los años 92 y 95 cuando alcanzó tasas de crecimiento de 6.6% y 18,8%, en la década se mantuvo una evolución negativa, que determinaron la tendencia decreciente de esta actividad.
Tabla 3 CIIU 1911: Principales Productos Exportados en 1999 (Miles de US$ FOB) Partida Arancel. Descripción Valor 4106190000 Los demás curtidos o recurtidos, pero sin prep.. posterior (de caprino) 458. 4105190000 Los demás curtido o recurt., pero sin prep.. post., divididas (de ovino) 251. 4106120000 Precurtidos de otra forma 149. 4104290000 Los demás cueros de bobino o equino curtidos, pero sin prep.. post. 136. 4106110000 Curtidos o precurtidos con precurtido vegetal (de caprino) 60. Otros productos 116. Total 1172. Fuente: ADUANAS Países de destino de las exportaciones El mercado de exportación principal de la industria de curtiembre en los tres últimos años fueron: México, seguido por Chile, Francia e Italia. Tabla 4 CIIU 1911: Principales Países de destino de las Exportaciones (Miles de US$ FOB) País 1997 % 1998 % 1999 % México 374.4 21.7 594.2 36.4 814.7 69. Chile 262.1 15.2 217.5 13.3 123.1 10. Francia - - - - 73.7 6. Italia 359.6 20.8 153.0 9.4 62.0 5. Alemania - - 186.6 11.4 28.4 2. Otros 341.0 19.7 255.9 15.7 70.9 6. Total 1726.9 100.0 1631.2 100.0 1172.8 100. Fuente: ADUANAS Productos importados Los principales productos importados son los cueros y pieles charolados y sus imitaciones de cueros y pieles, los que constituyen el 54% del total importado, seguidos por los demás cueros de bovino o equino preparados después de curtir. Tabla 5 CIIU 1911: Principales Productos Importados en 1999 (Miles de US$ FOB) Partida Arancela Descripción Valor 4109000000 Cueros y pieles charolados y sus imitaciones de cuero y pieles chapados 1561. 4104390000 Los demás (cueros y pieles de bobino o equino prep. después de curtido 377. 4104310000 Plena flor y plena flor dividida 233. 4104290000 Los demás cueros de bobino o equino, pero sin prep. posterior 228. 4104220000 Cueros y pieles de bobino precurtidos de otro modo Otros productos Total 2858.
Fuente: ADUANAS Países de origen de las importaciones Bolivia ocupó el primer lugar en cuanto al origen de las importaciones de productos relacionados con este rubro. En ese país se originó el 74% de las importaciones, seguidos por Colombia y Chile con el 8,2% y 7,3% respectivamente. Tabla 6 CIIU 1911: Principales Países de destino de las Importaciones (Miles de US$ FOB) País 1997 % 1998 % 1999 % Bolivia 2122.1 55.5 2506.3 61.3 2114.2 74. Colombia 203.9 5.3 234.7 8. Chile 337.7 8.8 349.3 8.5 208.0 7. Italia 137.0 3.6 127.0 3.1 80.8 2. Argentina 746.7 19.5 655.2 16.1 60.0 2. Otros 275.7 7.2 160.7 5. Total 3823.1 100.0 1631.2 100.0 1172.8 100. Fuente: ADUANAS 2.9. Inversión Inversión Extranjera Directa En la década de los 90, la inversión de fuente externa en la industria de curtiembres no acredita cifra alguna, según lo reportado por el CONITE (Comisión Nacional de Inversión y Tecnología Extranjera). Tabla 7 CIIU 1911: Stock de Inversión Extranjera Directa (Millones de US$ FOB) 1990 1991 1992 1993 1994 1995 1996 1997 1998 1999 Ind. Manufacturera 440 456 465 516 569 709 1037 1247 1361 1435 Bienes Intermedios 116 125 121 149 183 211 251 275 310 343 Curtidurías y taller 0.2 0.2 0.2 0.2 0.2 0.2 0.2 0.2 0.2 0. Fuente: CONITE
Los cueros salados son remojados con varios baños de agua enriquecidos con humectantes, bactericidas, detergentes y desinfectantes. La operación de remojo se lleva a cabo en tambores rotativos o en tanques donde se generan los efluentes líquidos que contienen sal, sangre, tierra, heces, sebo y grasas que aumentan la DBO. La operación dura de seis a 24 horas, los efluentes se desechan de manera intermitente. Pelambre Después del remojo, las pieles pasan al proceso de pelambre. Esta operación se realiza para hinchar la epidermis, retirar el pelo del cuero, saponificar las grasas naturales y entumecer las fibras para facilitar el efecto del curtido. Se utiliza un baño con agitación periódica en una solución que contiene sulfuro de sodio (Na 2 S) y cal hidratada (Ca(OH) 2 ), durante un periodo que varía entre 17 a 20 horas. Puede reducirse el tiempo del caleado aumentando la concentración del sulfuro de sodio. Las aguas residuales de esta operación son las más concentradas de todas las generadas en el proceso de la fabricación del cuero y representan un 70% a 80% de toda la contaminación de la carga originada en los efluentes principalmente como DQO, sólidos suspendidos y sulfuros. Presentan valores elevados de pH (superiores a 11) y restos de sebo, carnaza, pelo, sulfuros y proteínas solubles. Debido a estas altas concentraciones, las aguas residuales de pelambre pueden ser re-utilizadas cuatro o cinco veces previo retiro de los sólidos mediante bombeo y un tanque de recepción en el cuál se repotencia el sulfuro para el siguiente lote. El sulfuro de sodio, en medio alcalino, no libera ácido sulfídrico. Sin embargo, en presencia de pH bajo (efluente ácido) hay fuerte desprendimiento de ácido sulfídrico con el olor característico y un gran poder de corrosión. Con un pH por debajo de 8,0 se inicia el desprendimiento de ácido sulfídrico en suficiente cantidad que causa incomodidad por su fuerte olor a huevos podridos. Es importante mantener el pH por encima de 8 para que esto no suceda. Una forma alternativa de lograr esto consiste en diluir el caldo con otros efluentes para bajar su concentración. Esta etapa del proceso, además de aportar el 70% de la carga orgánica al efluente, aporta la totalidad de los sulfuros residuales, el 45% de los residuos sólidos sin cromo, el 35% del nitrógeno total y representa el 50% del volumen del efluente. Si hay un lugar donde se debe de tratar de reducir la contaminación a su máxima expresión, es aquí. Descarne La operación de descarne involucra la remoción de los tejidos adiposos, subcutáneos, musculares y el sebo adheridos a la cara interna de la piel, para permitir una penetración más fácil de los productos curtientes. Esta operación puede llevarse a cabo con máquinas o manualmente en curtiembres de pequeño tamaño. Algunas curtiembres realizan un pre-descarne con pelo antes del caleado, tratando de reducir el consumo de los químicos
auxiliares (cal y sulfuro de sodio) y agua, y, recuperar las grasas naturales de las carnazas lo cual representa obtener todas las ventajas mencionadas en el descarnado en verde. Los efluentes líquidos resultantes del descarne presentan concentraciones altas de sólidos en suspensión (proteínas disueltas) y pH ácido y deberían de ser tamizados para incorporarse al efluente del pelambre. Los sebos y piltrafas resultantes son utilizados por los fabricantes de cola después de un lavado de la cal ya que son puro colágeno y grasas. Hay empresas de gran producción (pe. Elmo Calf, Suecia) que obtienen una ganancia marginal de la recuperación de las grasas del cuero la cual es utilizada para cosméticos finos y el colágeno lo procesan en alimentos balanceados para el ganado. Otros usan esta grasa recuperada para volverla a incluir en el cuero con los aceites, en el se lleva a una fábrica de gelatina en Holanda. En países en desarrollo, la cola es utilizada para cosméticos finos y el colágeno lo procesan en alimentos balanceados para el ganado. Otros usan esta grasa recuperada para volverla a incluir en el cuero con los aceites en el engrase. En Europa gran parte de los recortes y piltrafas del descarne y dividido en tripa se lleva a Holanda a una fábrica para la fabricación de gelatina. En países en desarrollo la cola es utilizada para la fabricación de pinturas o gelatinas de baja concentración que son vendidos a fábricas de caramelos. En Arequipa muchos fabricantes de cola han hecho de esta actividad una industria que genera ingresos adicionales y reducen la carga contaminante en la curtiembre. Dividida Se puede hacer en la ribera después del pelambre o después del curtido con el cuero en “ wet-blue”. Esta operación consiste en dividir en dos capas la piel hinchada y depilada separando la flor, que es la parte de la piel que está en contacto con la carne. Aquí, además de partir el cuero en dos capas, también se generan piltrafas además de los recortes de la parte inferior o carnaza. Si esto se da en la etapa del pelambre, el subproducto que son piltrafas y retazos pueden ser entregados a las fábricas de cola o gelatina tal como se describe en la sección del descarne. Si ya los cueros están curtidos y contienen sales de cromo, entonces se procesan con las piltrafas de la máquina rebajadora. En Italia, por ejemplo, éstas se juntan en una planta que recupera el cromo y convierte el excedente en fertilizante. Curtido El curtido comprende los siguientes pasos: Desencalado (cuando se producen vaquetas), Purga (cuando se producen vaquetas), Piquelado (No se lleve a cabo en curtido vegetal tanino). Desencalado y Purga El desencalado es la preparación de las pieles para la curtición, mediante lavados con agua limpia, tratando de reducir la alcalinidad y removiendo los residuos de cal y sulfuro de sodio. Se utilizan aguas que contienen sulfato de amonio y ácidos. Esta operación se lleva a cabo en tambores rotativos. Esto
porque el empleo de sales de cromo hexavalente conduce a la generación de residuos sólidos de carácter peligroso. Curtido sintético En el curtido sintético se usan curtientes orgánicos sobre la base del formol, quinona y otros productos. Estos curtientes proporcionan un curtido más uniforme y aumentan la penetración de los taninos. Debido a sus costos elevados, son poco usados. Acabado En esta etapa se puede procesar el cuero curtido al vegetal o curtido al cromo. En el curtido vegetal se procesa el cuero para la fabricación de suela, de cuero para talabartería, correas, monturas, usos industriales, y de cuero para repujados. El acabado de suelas comprende: Prensado, engrase, secado y estiramiento (proceso opcional). El acabado de vaquetas comprende: Prensado, rebajamiento, neutralización, recurtido, blanqueado, teñido, engrase, secado y pulido (proceso opcional). Las vaquetas acabadas con el curtido al cromo reciben otro tipo de acabado. Después del proceso de curtido tienen que descansar en húmedo por algunas horas o hasta el día siguiente para fijar el cromo en el tejido del cuero. Después hay que quitar el exceso de agua con una máquina de escurrir y como puede haberse formado arrugas, se les pasa por una máquina de estirar. Estas operaciones son llevadas a cabo por vía seca o húmeda, con el propósito de conferir al cuero el aspecto y las propiedades requeridos según su uso final. Prensado Después del curtido, se realiza un prensado del cuero (llamado escurrido), para retirar la humedad, estirar las partes arrugadas y mantener un espesor uniforme del mismo. Rebajado Los cueros se raspan y se rebajan en las mismas máquinas. Este procedimiento le da al cuero un espesor uniforme y lo deja en la medida deseada. En esta etapa se generan cerros de viruta del rebajado que contienen el cromo del curtido. Esta viruta se utiliza para fabricar falsas o para recuperar el cromo. Si se hace esto, el cuero que queda sin cromo se usa en alimento para ganado procesándolo con otros productos o se descompone y se usa como fertilizante. Neutralización Los cueros se sumergen en tambores para realizar las operaciones arriba citadas. Estas operaciones se llevan a cabo de manera consecutiva, cambiando
solamente la composición de los baños después de descartar el baño anterior. El baño de neutralización se realiza con agua, formiato de calcio, carbonato o bicarbonato de calcio. Recurtido El curtido al tanino produce un cuero más fácil de ser prensado. Por esta razón, muchas veces, el cuero curtido al cromo, denominado “wet blue”, recibe un segundo curtimiento, el cual puede ser al cromo o al tanino vegetal o sintético. Cuando este segundo curtido es realizado luego del primero, se llama “curtido combinado”, su practica sirve para reducir cromo en el efluente. Estos procesos son realizados en la producción de vaquetas, dependiendo del tipo de producto final que uno desea obtener. El proceso es prácticamente el mismo del curtido. Algunas industrias hacen solamente el acabado del cuero, utilizando como materia prima el cuero curtido al cromo o “wet blue”, adquirido de otra curtiembre. Blanqueado La operación de blanqueado sólo es realizada en algunos casos, utilizándose baño de bicarbonato de sodio y ácido sulfúrico, seguido inmediatamente por un lavado con agua corriente tratando de quitar el ácido libre cuya presencia produce manchas y vuelve quebradizo al cuero. Teñido El teñido se realiza luego de la neutralización en baño que contiene agua, colorantes (natural, artificial o sintético) y ácido fórmico. Este baño se desecha después de cada operación. Los efluentes en esta etapa del proceso son mínimos en comparación al de pelambre y no justifica acción alguna de tratamiento. Los ácidos que contienen sirven para neutralizar el efluente general. Engrase El engrase se realiza con el objeto de evitar el cuarteamiento del cuero, volviéndose suave, doblable, fuerte, flexible y resistente. Este proceso consiste en la impregnación al cuero con grasas o aceites animales. Estas sustancias se depositan en la fibras del cuero dónde son fijadas. El engrase se lleva a cabo en los mismos tambores de las operaciones anteriores. Algunas curtiembres recuperan el sebo y las grasas naturales contenidos en las carnazas de las pieles. Estos materiales pueden aprovecharse en el proceso de engrasamiento luego de una sulfonación. La piel verde contiene de 0,5 a 1,5 kilogramos de sebo.
ESQUEMA DEL PROCESO DEL CURTIDO
LAVADO Y REMOJO CUERO CRUDO DESCARNADO VERDE ENCALADO APELAMBRADO Y DESCARNADO CON CAL RECORTADO MACERADO PICLAJE DESENGRASADO (PIEL DE OVEJA) CURTIDO RECURTIDO Y TINTURADO ACABADO CONTAMINANTES DEL AIRE CONTAMINANTES DEL AIRE Y RESIDUOS SOLIDOS H 2 S, SO 2 PELOS, LODOS CON CAL, MATERIA ORGANICA PUTRESIBLE DBO, SS, SD DBO, SS, SD DBO, SS, SD ALCALINOS, SULFUROS DBO, SS ACIDEZ, SD DBO, SS, SD CROMO Y OTROS MATERIALES PARA EL CURTIDO DBO, TINTES, ACEITES Y CROMO TINTES, PIGMENTOS (ESPECIALMENTE METALES PESADOS) NH 3 TANINOS VEGETALES – O LODOS CON CROMO SOLVENTES, NH 3 , FORMALDEHIDOS
IV.1. Situación en el Perú La industria del cuero en el Perú se encuentra en estado crítico. Muchas curtiembres formales han cerrado. Frecuentemente, los operadores y empleados de una curtiembre formal que cierran han reaparecido como curtiembres informales. Muchas curtiembres formales, inclusive, alquilan sus servicios a curtidores informales como medio para generar ingreso. Una porción significativa de la economía peruana es informal. Algunas fuentes han estimado que las curtiembres formales producen hasta el 50% del cuero que se curte en el país. Las curtiembres informales están sub-capitalizadas, gozan de una ventaja competitiva significante con relación a los curtidores formales quienes cumplen con las leyes y regulaciones. La globalización continuará haciendo que la industria del cuero y calzado del Perú sea vulnerable al ingreso de zapatos importados baratos. Es muy posible que el número de curtidores formales continuará disminuyendo. El curtido de cuero para hacer wet blue o costra de cuero para ser exportado a países con mano de obra barata (China, Pakistán, Vietnam, etc.) podría ser una meta a largo plazo para la industria de curtiembres peruana. El crecimiento de la población ha expandido las ciudades. Las curtiembres formales, que alguna vez estuvieron lejos de las zonas residenciales, ahora se encuentran rodeadas de casas. Los residentes están indignados por el agua sin tratar y los desechos sólidos que generan las curtiembres vecinas y los malos olores. Muchos curtidores informales operan dentro de sus propias casas, rodeados de sus vecinos que sufren las consecuencias. Los cueros de vaca en el Perú son relativamente baratos en comparación con los EE.UU. (S/ 50 vs. S/ 200). Pero los cueros disponibles en el Perú son de calidad más baja que los disponibles en los EE.UU. Por otro lado, los procesos de pelambres y cromado constituyen la mayor preocupación para las curtiembres por: alto nivel de DQO, alto DBO 5 , alto nivel de sólidos y cromo en solución. El proceso de curtido para obtener wet blue usa muy poca mano de obra. Las pequeñas micro empresas de curtiembres pueden obviar los pasos altamente contaminantes en la producción (pelambre y curtido al cromo) y seguir generando empleos para las etapas con intensiva mano de obra como son las de recurtido, teñido, engrasado y acabado del proceso.
CUERO ACABADO DBO = DEMANDA BIOLOGICA DE OXIGENO SS = SOLIDOS SUSPENDIDOS SD = SALES DISUELTAS
La calidad del aire es afectada por la degradación de la materia orgánica (piel, sangre, pedazos de carne, etc.), proceso en el cual se generaran olores fuertes y desagradables. Asimismo, la calidad del aire dentro de la planta puede ser afectado por el escape de vapores de ácido sulfhídrico y de amoniaco durante la operación de caleado y depilación. La calidad del aire dentro de la planta también puede verse afectada debido al escape de vapores de agentes químicos utilizados en la etapa de acabado. Residuos Sólidos Los residuos sólidos típicos del proceso de curtición son los siguientes:
Rango Promedio Rango Promedio Grado de Acidez o Alcalinidad (pH) (^) 5.1 – 13.4 8.3 8.5 – 9.2 8. Temperatura, °C (^) 15 – 30 21.4 22 – 26 24. Aceites y Grasas, mg/l (^) 0.9 – 958.1 124.0 2.5 – 151 60. Demanda Bioquímica de Oxígeno(DBO 5 ), mg/l 45.6 – 4400 1422.6 15 – 5132 1961. Demanda Química de Oxígeno(DQO), mg/l (^) 1.5 – 18255 3837.1 66 – 16770 4922. Sólidos Suspendidos Totales(SST), mg/l (^) 3.5 – 38442 3213.2 37 – 6650 3007. Sulfuro, mg/l (^) 0.67 – 3606 303.5 4 – 964 378. Cromo VI, mg/l (^) 0.02 – 13.7 1.1 0.1 – 0.24 0. Cromo Total, mg/l (^) 0.05 – 6260 510.0 0.18 – 800 289. Coliformes Fecales, NMP/100ml (^) 2 – 170000 8106.5 2 – 9000 1802. Amoniaco (N-NH 4 ), mg/l (^) 1.43 – 416 63.1 0.3 - 468 164.
4.4. Impactos Ambientales Los principales impactos ambientales detectados en el subsector curtiembre se dan en los efluentes líquidos, por lo que el trabajo ambiental prioriza el establecimiento de estos, los cuales se da en el Cuadro Nº 5. 4.5. Experiencia en Otros Países En los Estados Unidos en el año 1975 existían más de 300 curtiembres, de los cuales actualmente existen menos de 90. Diez de estas producen el 50% del cuero acabado. En 1998, en los EE.UU. produjeron cerca de 34.5 millones de cueros por año e importaron 2 millones de cueros por año de Canadá. La industria Estadounidense curtió 18.5 millones de cueros y exportaron 18 millones de cueros salados, de los cuales 4.5 millones de cueros curtidos fueron exportados como “wet blue” (cueros apelambrados y curtidos al cromo). La agencia Estadounidense de Protección Ambiental (EPA) y cada uno de los estados desarrollaron e impusieron de manera estricta sus LMP para los efluentes de los residuos de las curtiembres. En el resto del mundo, los cambios también han sido dramáticos. Los cueros y los químicos de curtido son bienes que se transan en el mercado mundial. Actualmente, Alemania tiene una industria de curtiembres muy pequeña. Italia y los otros países europeos conducen operaciones limpias y eficientes. Otros países desarrollados (Estados Unidos, Canadá, Australia, Nueva Zelandia y Sudáfrica) han sido capaces de producir grandes cantidades de cuero y de wet blue para uso doméstico y exportación. En la mayoría de los casos los curtidores han construido plantas grandes y eficientes, cercanas a los mataderos. Estas plantas re-utilizan y reciclan sus efluentes de cromo. Las industrias de cuero y calzado se han mudado de Japón a Corea y de Taiwán a Indonesia. Existen evidencias de que las curtiembres también se están mudando a Vietnam y otros países del Sudeste Asiático. Corea fue una vez el centro mundial para la manufacturera de calzado deportivo y de cuero para zapatos deportivos blancos. Hoy las compañías están en bancarrota y las plantas han cerrado. A través del tiempo, la combinación de salarios más altos y nuevas regulaciones ambientales han llevado a la industria del cuero a mudarse de país en país. En la india y Turquía, las curtiembres han prosperado al localizarse en grupos donde cada empresa puede tener sus flujos de residuos separados para su óptimo reciclaje y así poder recuperar un porcentaje del valor. Asimismo, han obtenido la ventaja de poder utilizar una planta de tratamiento común. Las curtiembres más pequeñas compran wet blue de estas operaciones. Estas curtiembres pequeñas continúan realizando las etapas de acabado más intensivas en mano de obra pero menos contaminantes.
Pequeña >250 - 1 000 > 210 – 840 > 1 260 – 5 040 > 5 040 – 20 160 Mediana >1 000 - 10 000 > 840 – 8 340 >5 040 – 50 040 > 20 160 – 200 160 Grande > 10 000 > 8 340 > 50 040 > 200 160 Equivalencias: Peso promedio para una piel menos (mezcla) a nivel nacional. 1,200 kg de piel menos al estado de tripa descarnada equivale a: 1,250 kg de piel fresca camal (1,250 kg x 0,960 = 1,2 kg tripa) rendimiento aproximado 96%. 1,125 kg de piel fresca salada (1,125 kg x 0,70 = 1,2 kg tripa) rendimiento aproximado 107%. 0,75 kg de piel seca salada (0.75 kg x 1,600 = 1,2 kg tripa) rendimiento aproximado 160%. 0,575 kg de piel fresca camal 0.575 kg x 2,100 = 1,2 kg tripa) rendimiento aproximado 210%. 5.2 Análisis de las Alternativas Recomendadas 5.2.1 Instalar Cribas al Final de la Etapa de Pelambre y en los Vertederos del Proceso. a) Descripción del sistema. Las instalaciones de los botales en las curtiembres peruanas son del tipo simple, no llevan instalados ductos que recojan el líquido del proceso. Mas bien, estos se vierten al piso, el cual está construido en declive que inclina su caída hacia un canal de recojo y derivación estas aguas. Para disminuir la presencia de sólidos en el efluente, la primera acción consistiría en colocar al final de la zona de pelambre (de modo tal que no obstaculice el movimiento del cuero o del transito) una criba. Esta criba puede ser fabricada con varillas paralelas de acero inoxidable o con fierro galvanizado redondo liso, colocadas en una inclinación de 30 a 45 grados respecto al flujo de la corriente. En la Figura 1 se presenta el esquema constructivo de la criba. La distancia entre las varillas puede variar entre 5 y 20 mm, dependiendo del grosor de las piltrafas que salen del proceso. Esta criba se puede limpiar muy fácilmente con un rastrillo cuyos peines están ubicados a la misma distancia que las varillas separadoras que conforman la criba. De este modo, al penetrar entre las varillas, hacen una limpieza a fondo. Al hacer la limpieza los residuos pueden ser colocados en un cajón posterior, tal y como se ve en la Figura 1. El cajón debe estar provisto de agujeros para que escurra el residuo. También se debe prestar atención a la limpieza de este sistema (por lo menos 1 vez por día) durante la vaciada del botal para que la criba no se atore con los retazos de cuero. En todo caso el diseño de las rejillas se hará teniendo en cuenta la facilidad de su mantenimiento y de su mantenimiento y limpieza. Otro tipo de criba de fabricación casera en una malla de alambre montada sobre un marco de madera. La malla puede ser de acero galvanizado con 4-8mm de luz. Sobre esta malla se monta una tela de material hidrofóbico. Para tal efecto puede utilizarse nylon, pero existen otros materiales igual de efectivos. La tela puede ser hilada o tejida con aberturas de 1mm o un poco más. Las cribas son montadas con una inclinación de 45-60 grados. LA solución del baño se vierte sobre la criba, cerca de su extremo superior, y el agua rápidamente fluye a través de la misma. Los sólidos serán atrapados por la criba y serán forzados a descender debido a la presión hidráulica. Los sólidos entonces se acumularán en la parte inferior delantera y la solución cribada será atrapada en una bandeja al otro lado. Estas cribas pueden ser pequeñas y utilizadas en cada etapa del
proceso. El curtidor necesitará una o dos cribas para el filtrado de los residuos del pelambre. El tamaño de las cribas dependerá del volumen del baño, pero en promedio se estima que una criba de 2 metros cuadrados puede ser suficiente. Las cribas deben ser limpiadas completamente después de cada uso y nunca se debe permitir que se seque con los sólidos encima. De lo contrario, los sólidos secos bloquearán el filtro y la tela deberá ser reemplazada. Una acción opcional seria la de tapar los canales de recojo y derivación con planchas de madera, concreto o fierro fundido. Las planchas o rejas estarían perforadas, con lo cual parte de los retazos más grandes (cueros) quedarían separados de los efluentes (Figura 1). Las planchas deben tener un espesor de 2”, de manera tal que la superficie quede al ras del suelo. Las planchas pueden ser construidas de varillas de fierro redondo liso, de madera de 2” de grosor, de concreto o de hierro fundido. Las planchas deben estar provistas de agujeros de 50mm de diámetro en promedio de manera que permitan el flujo del agua aun cuando pedazos de cuero puedan estar obstaculizando. En el caso que la plancha sea una reja de fierro fundido, las ranuras podrían ser de 50 x 100mm. En algunos casos, la curtiembre tendrá que modificar el perfil del canal para que estas tapas queden a ras del piso. b) Valores y porcentajes proyectados de reducción de los parámetros contaminantes Con la correcta aplicación del sistema descrito evitamos que sólidos gruesos puedan llegar a los pozos de sedimentación, reduciendo considerablemente la contaminación que estos causarían. En una curtiembre donde se procesaban 5000 pieles diarias de ovocaprinos en la localidad de Nakuru, Kenya, Rantala (1995) reportó una reducción del 25% en los niveles de DBO y DQO del efluente, después de la instalación de cribas. También se obtuvo una reducción de 40% en la concentración de sólidos en suspensión. c) Ahorros por la reutilizacion de recursos. En este caso el ahorro es mínimo. El monto ahorrado podría ser cuantificado mediante mediciones in situ. d) Montos de inversión para instalar la acción recomendada Especificaciones Criba de hierro para la retención de sólidos al final del proceso de pelambre Medidas: 50 cm ancho por 100 cm alto Espesor de la varilla: 10 mm Número total de varillas: 22 Tabla 10 Costos directos de construcción Construcción e instalación de una criba, rastrillo y trampa de retención de residuos partidas Unidad p.u. para todo tipo de empresa cantidad monto US$