
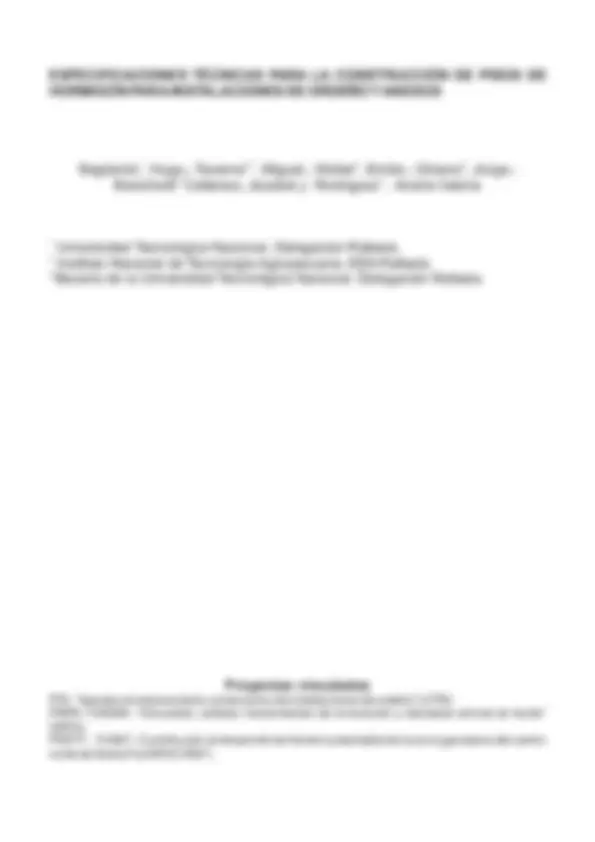
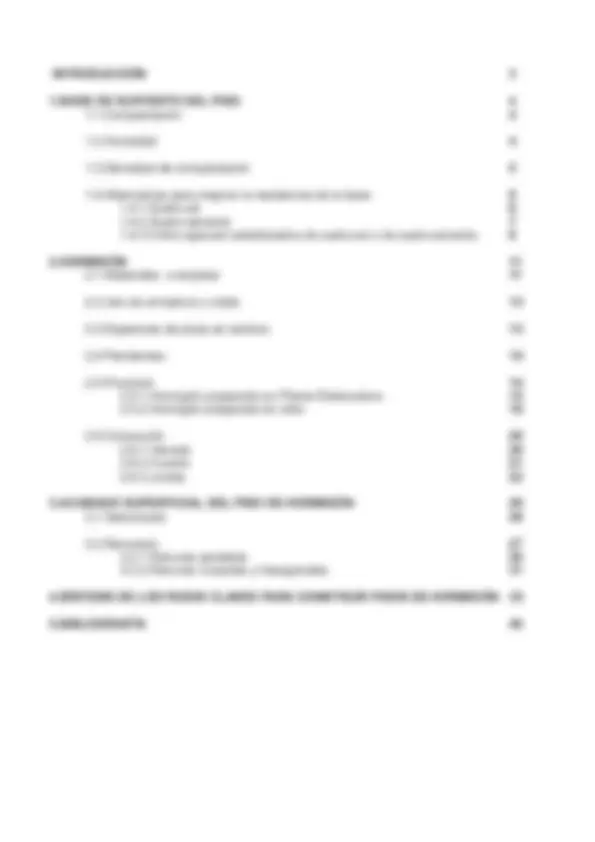
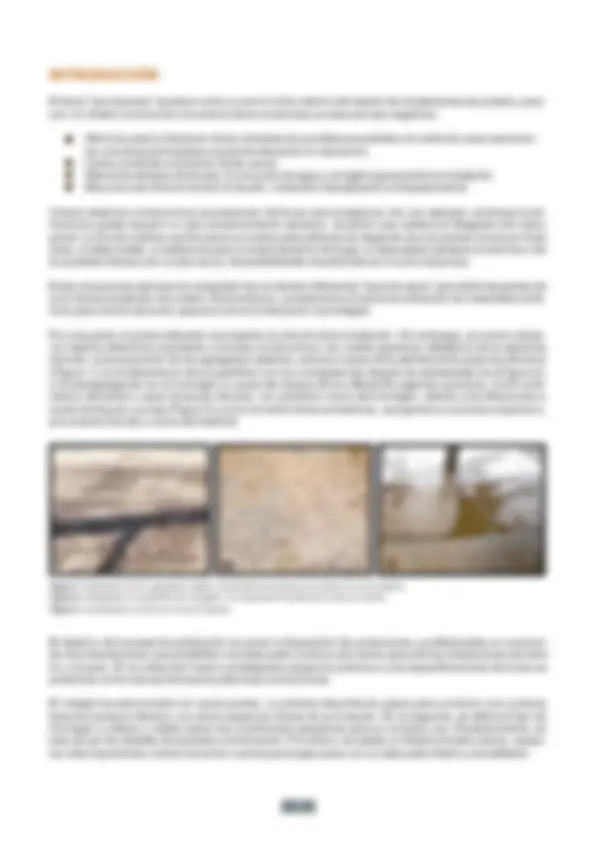
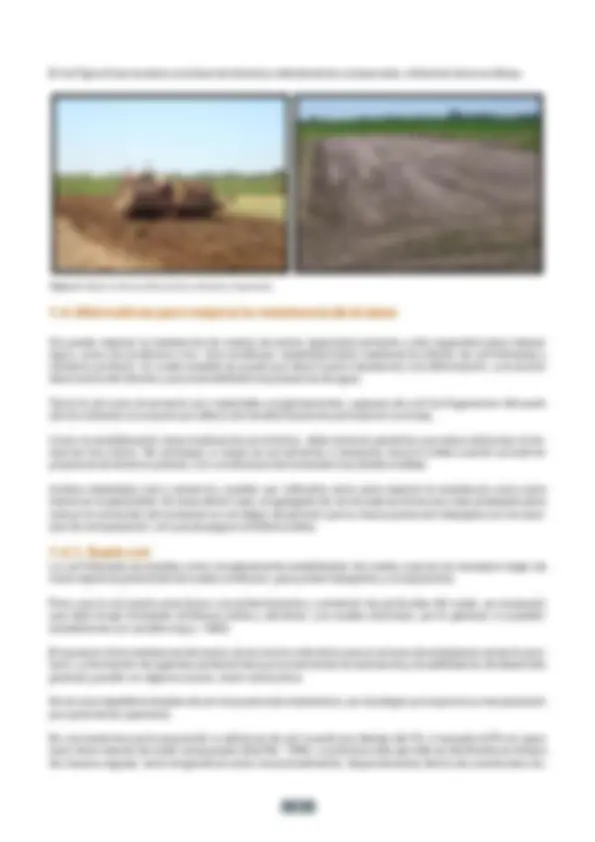
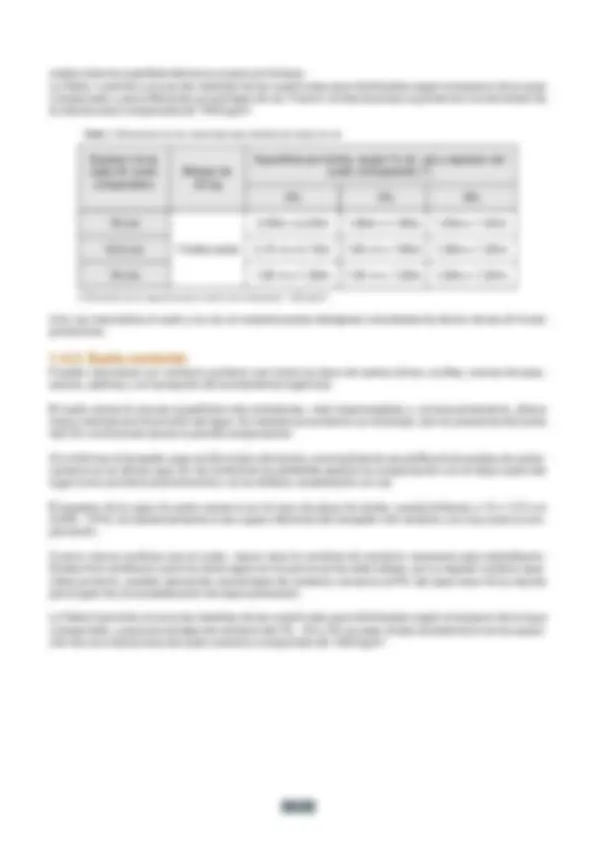
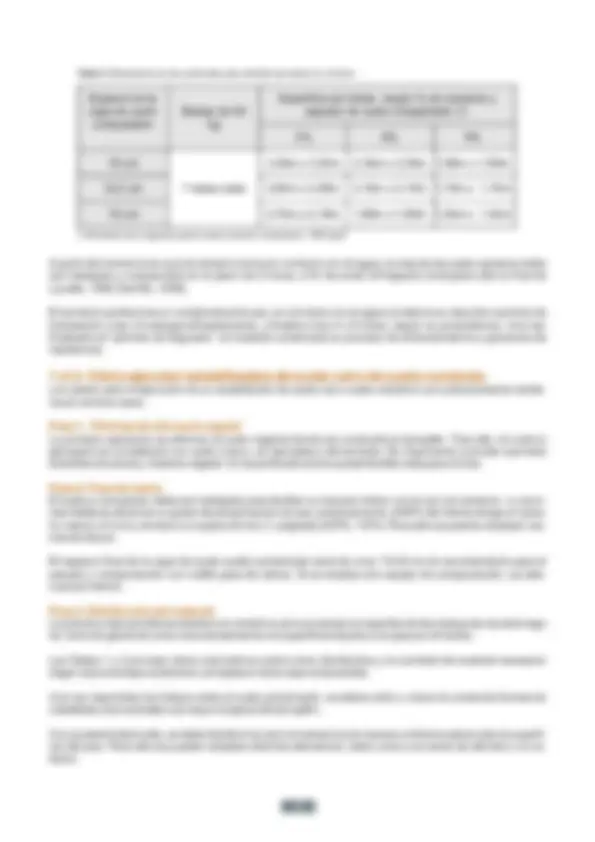
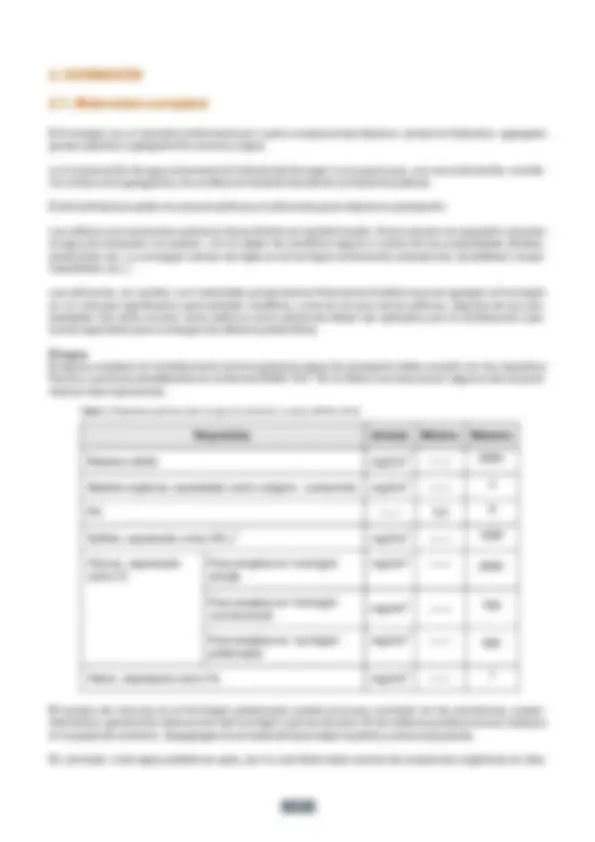
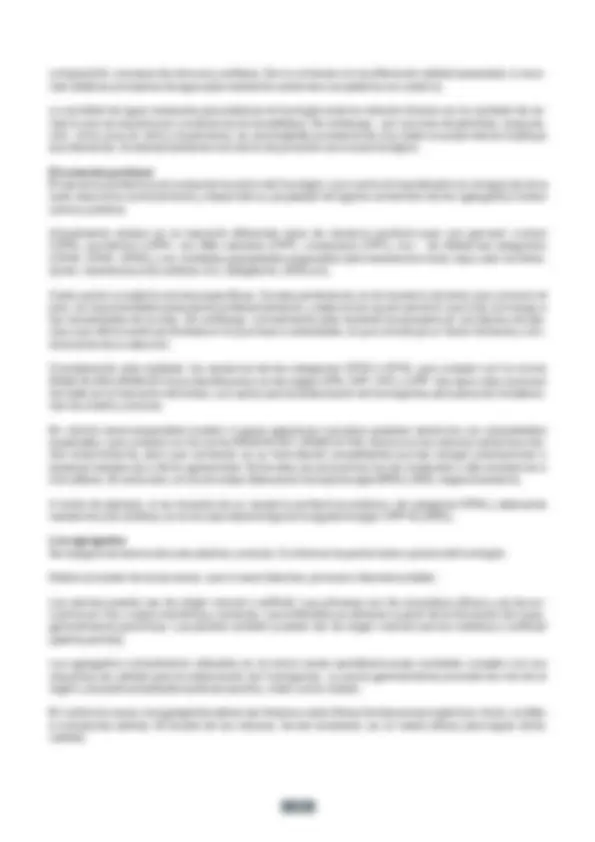
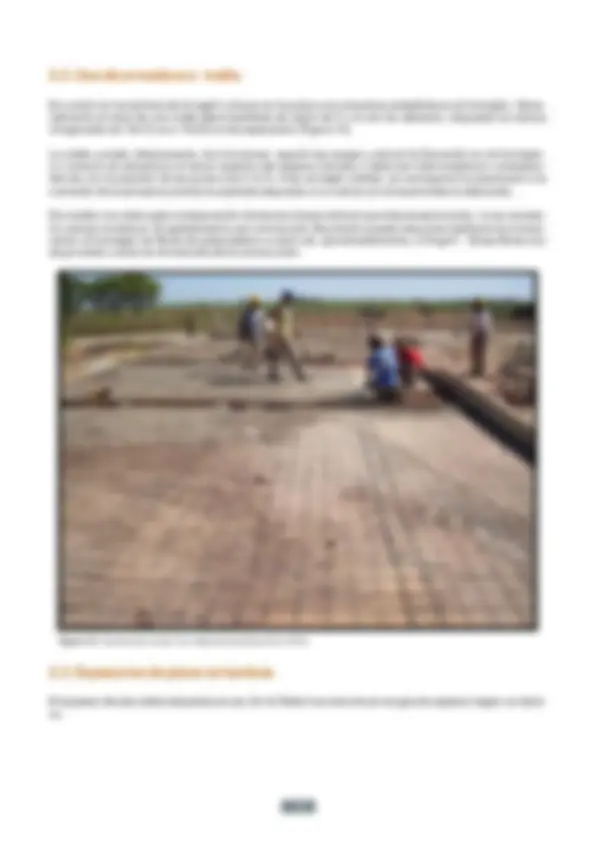
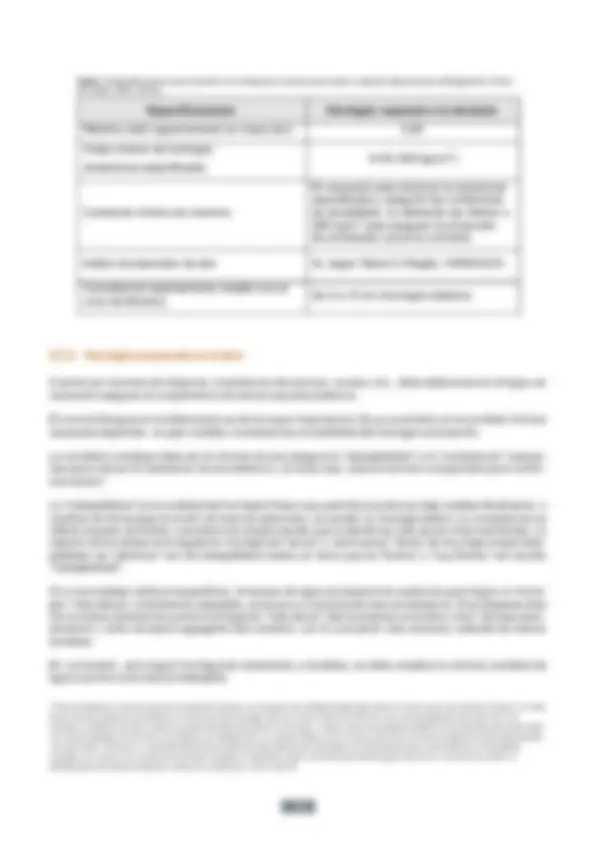
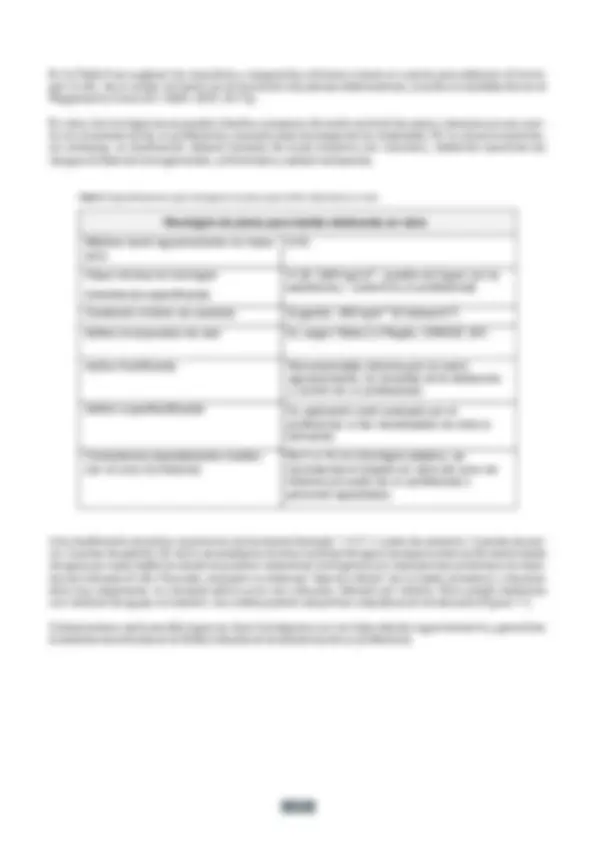
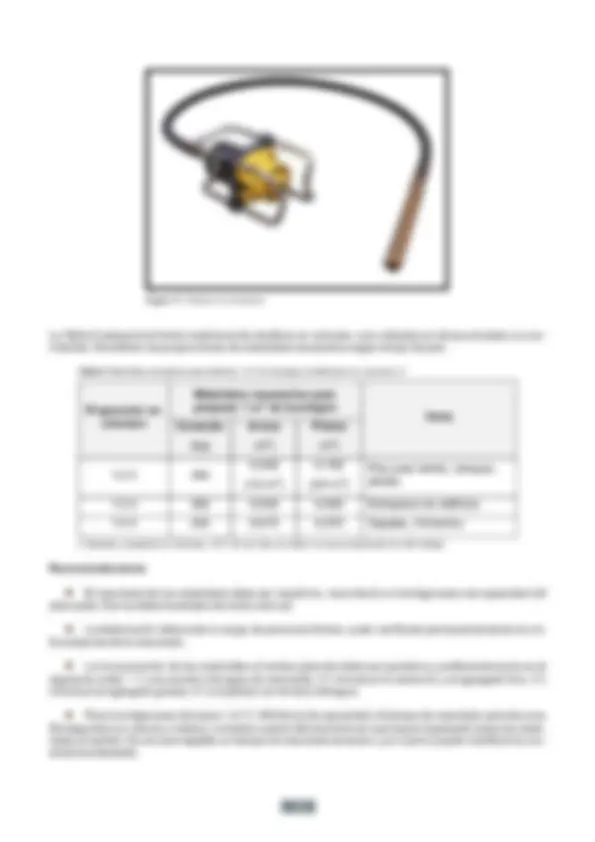
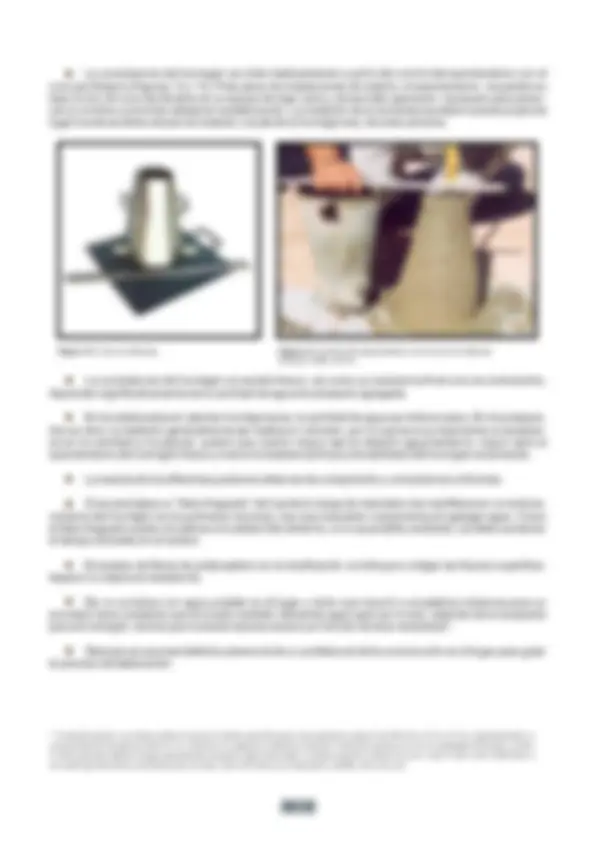
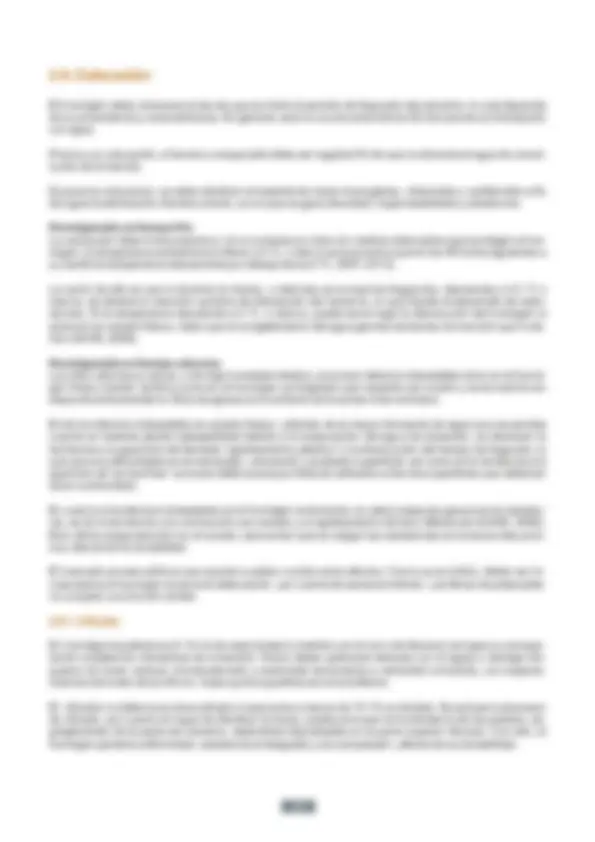
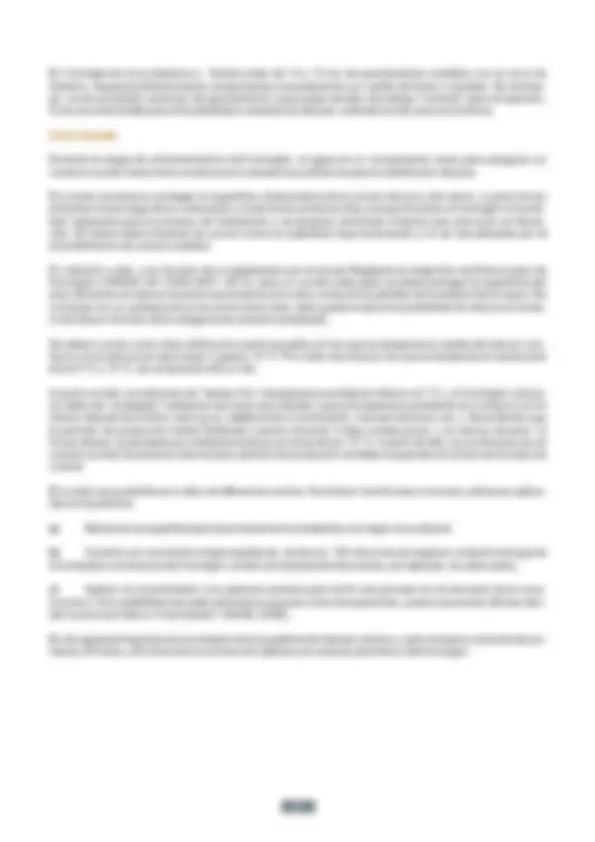
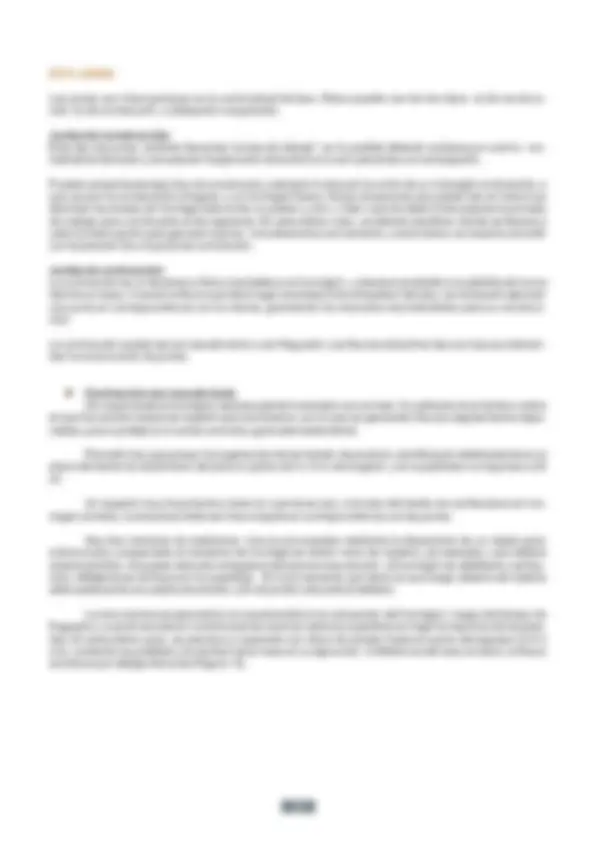
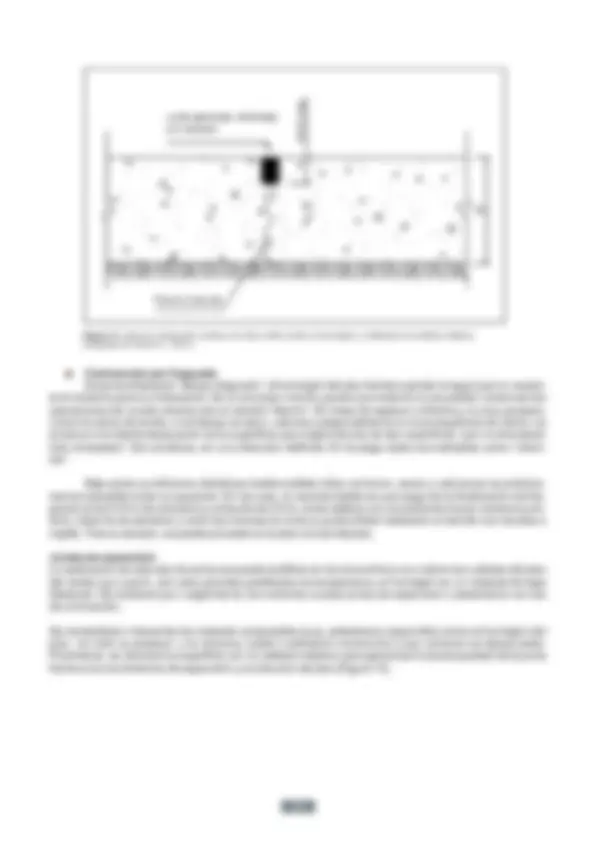
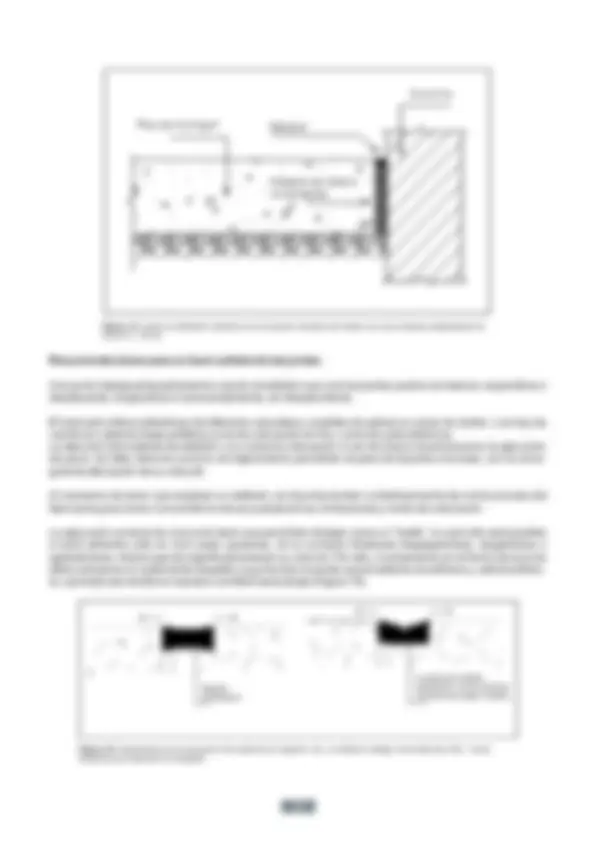
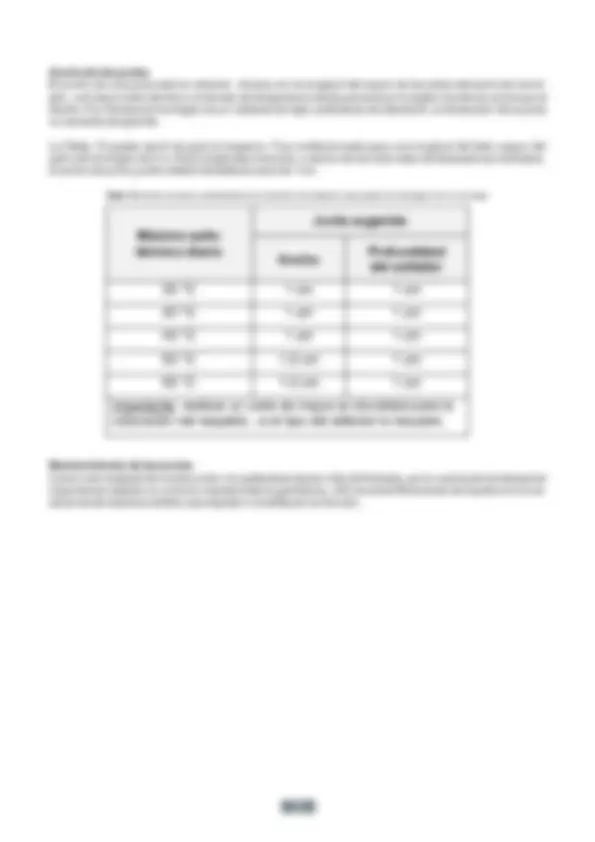
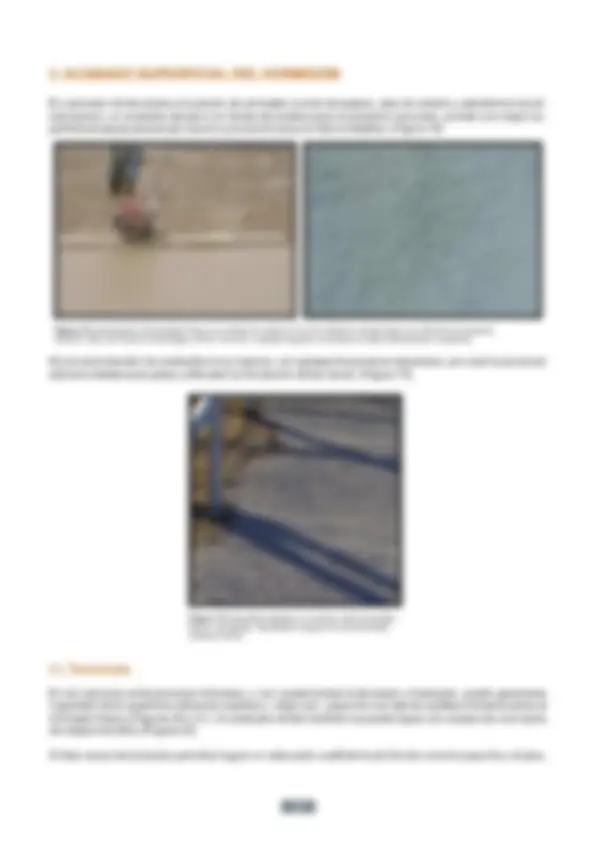
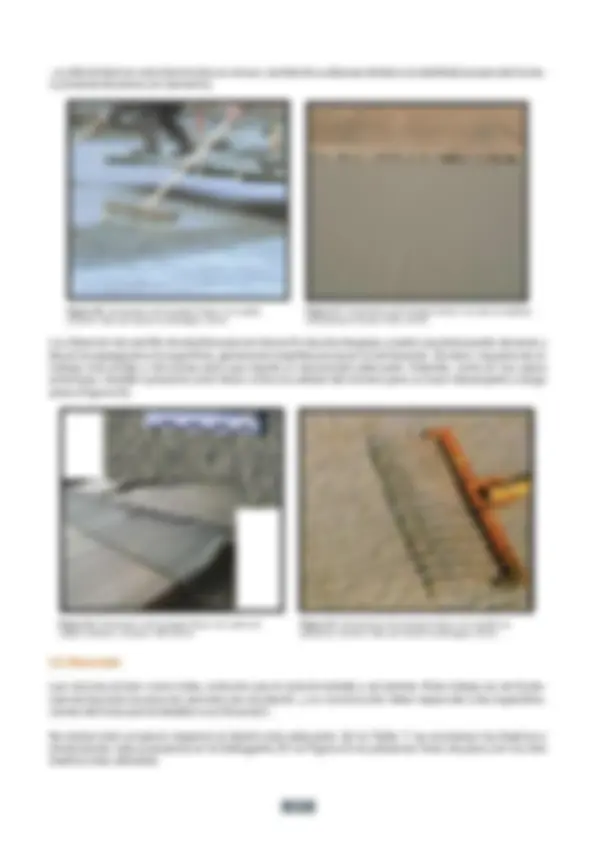
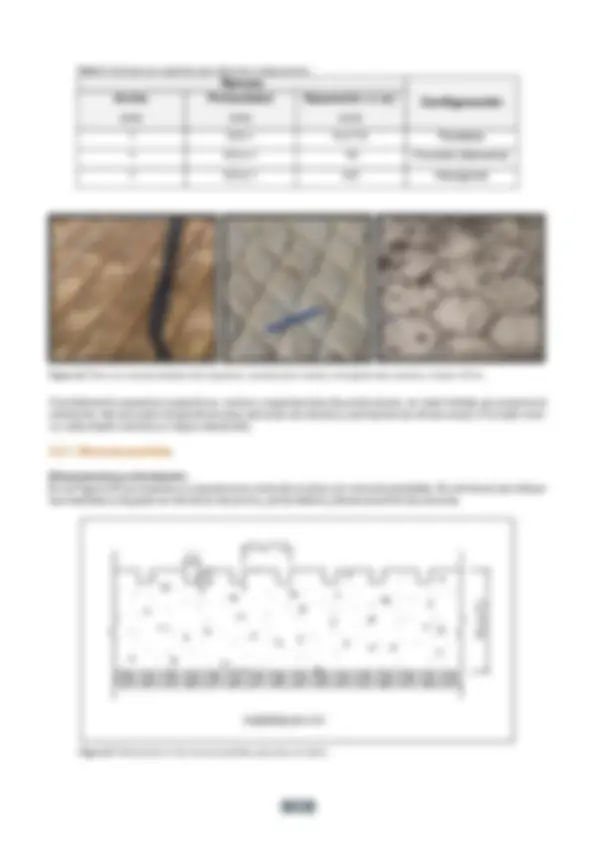
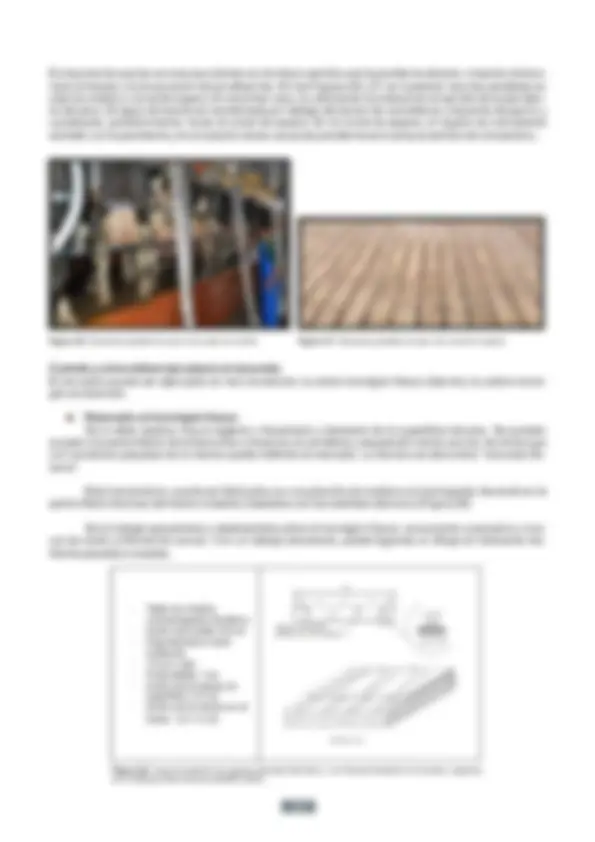
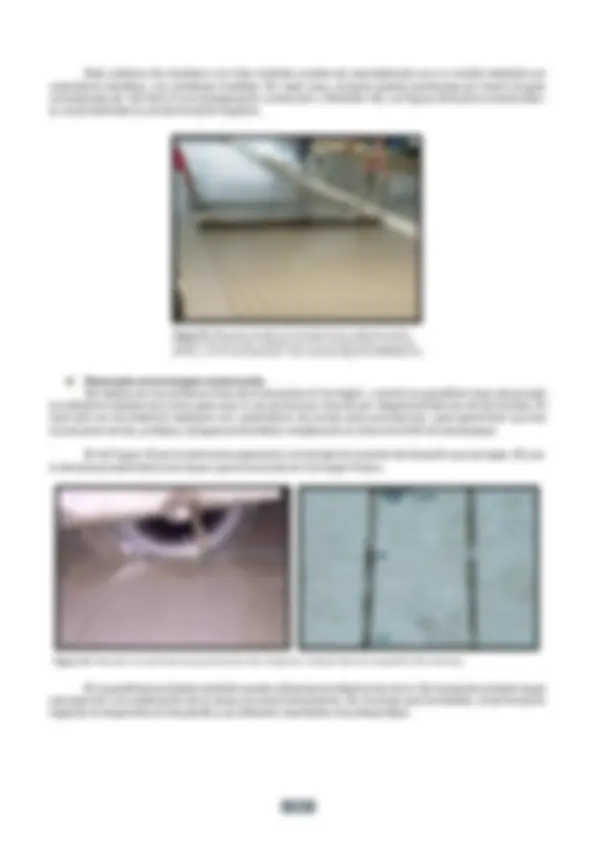
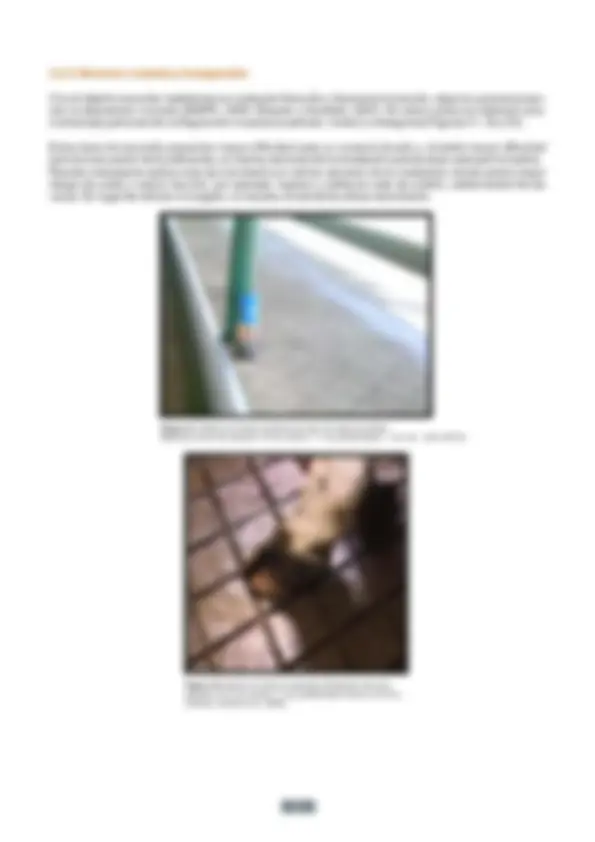
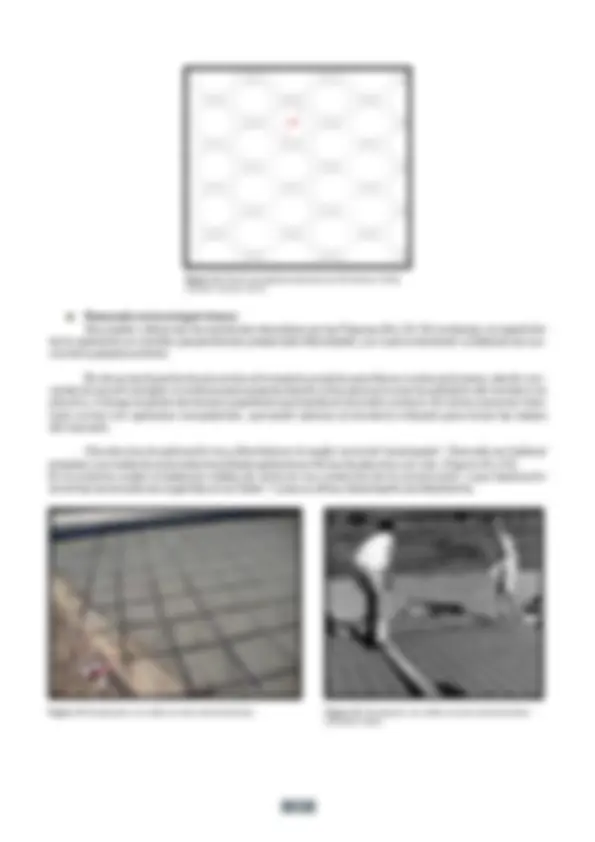
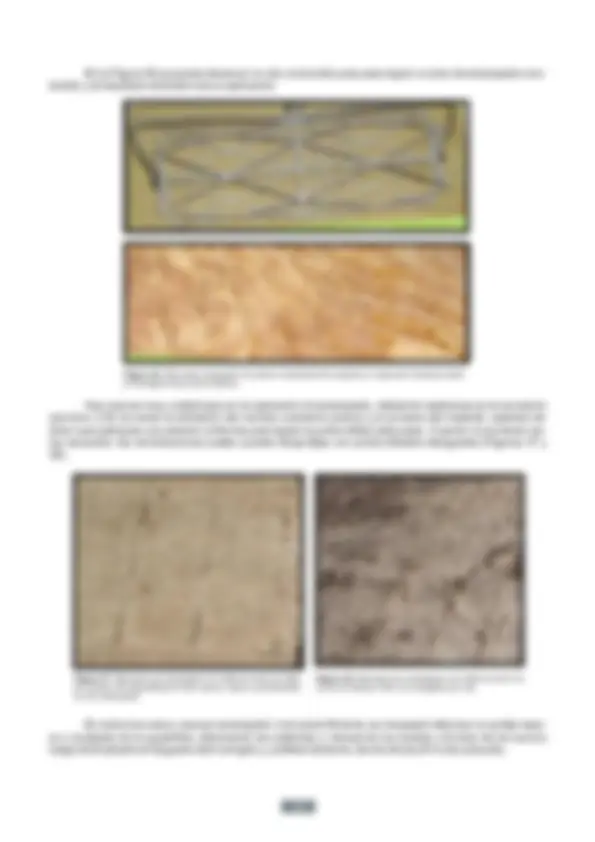
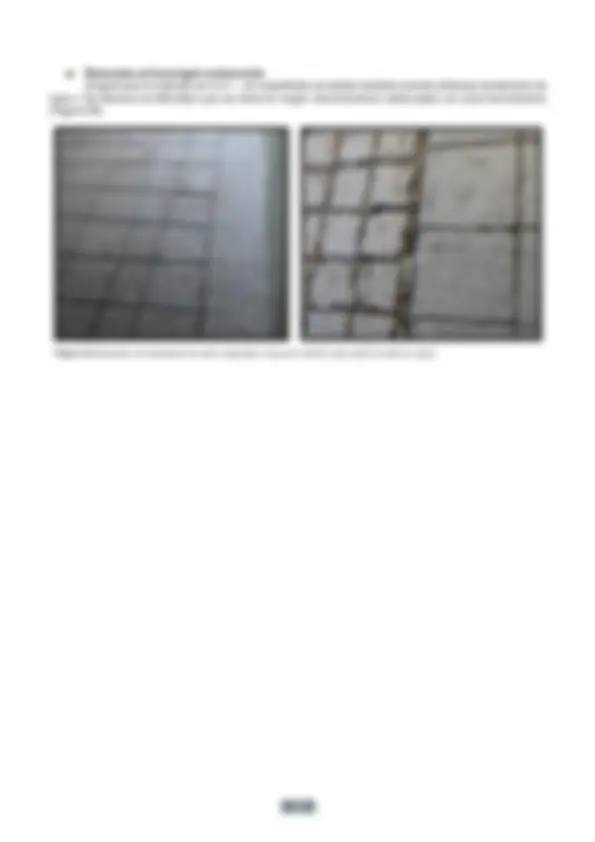
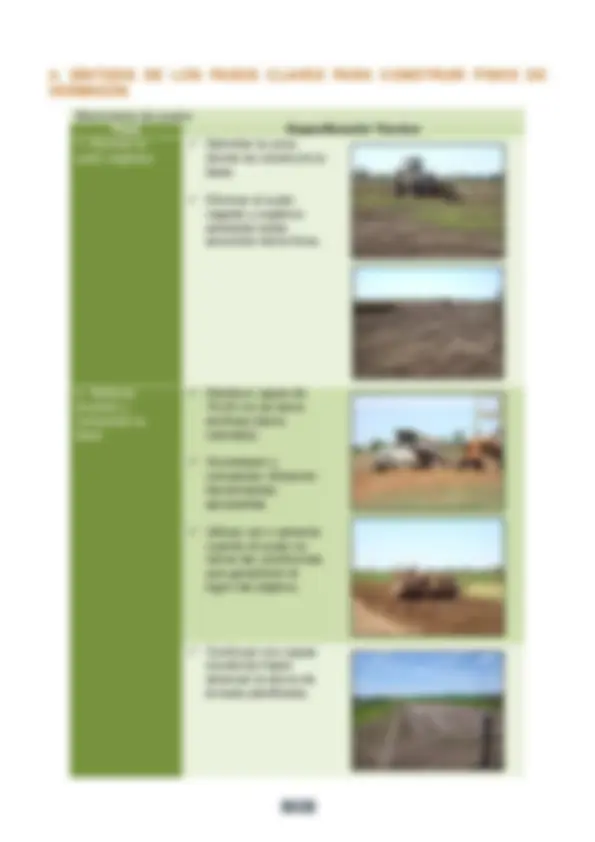
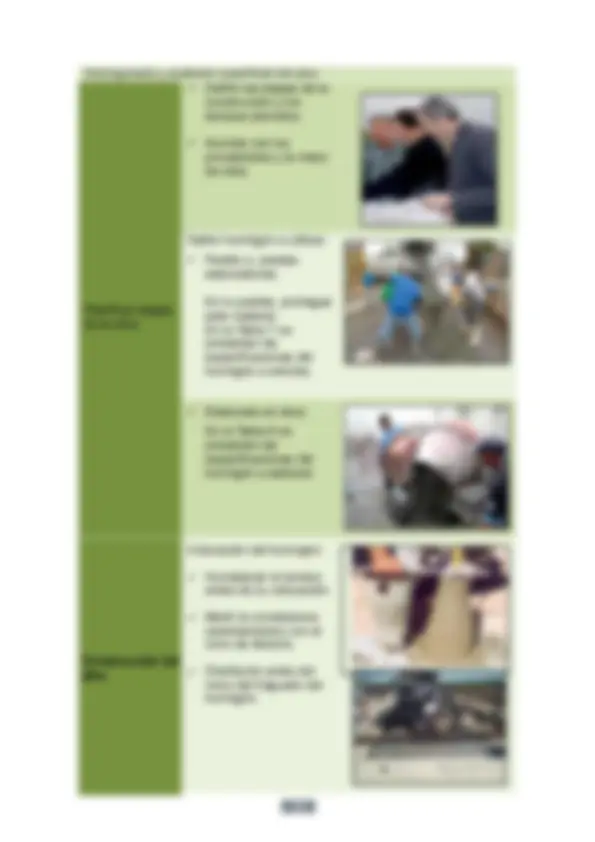
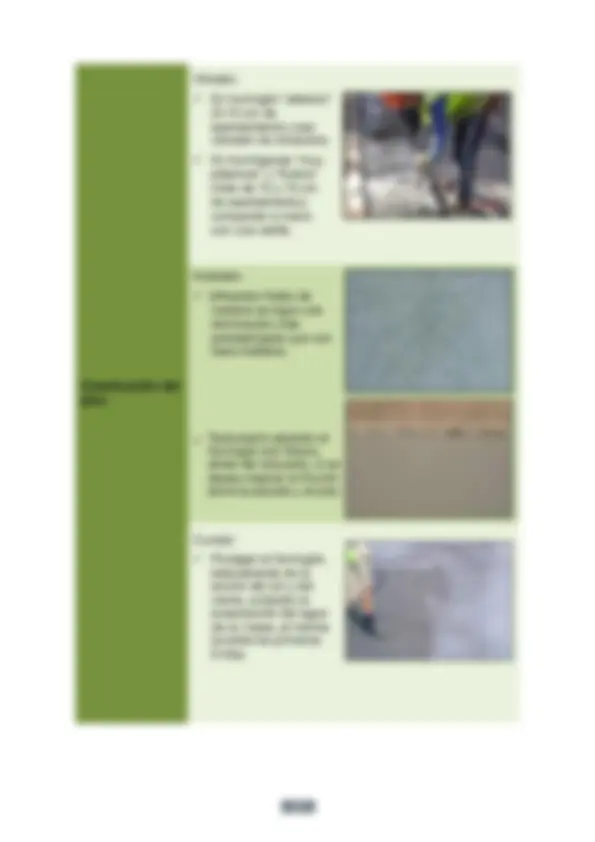
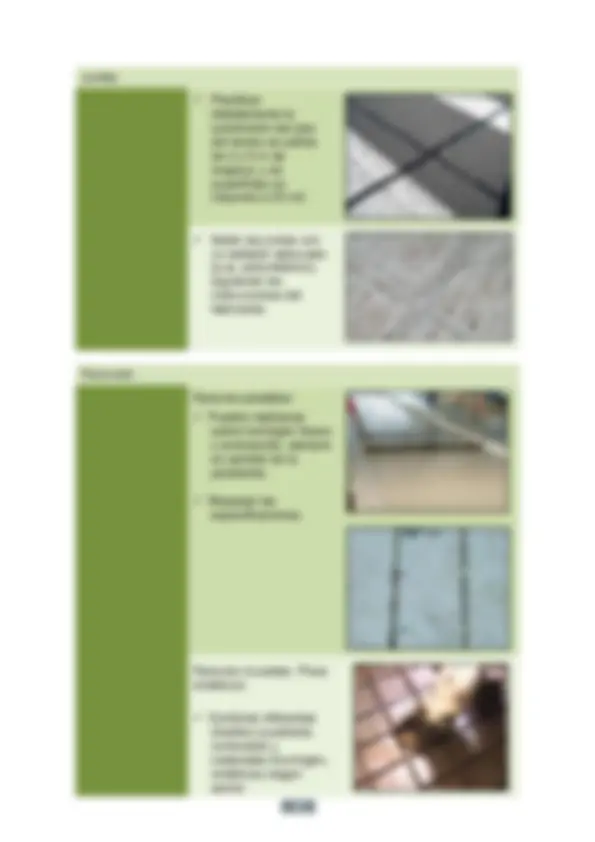
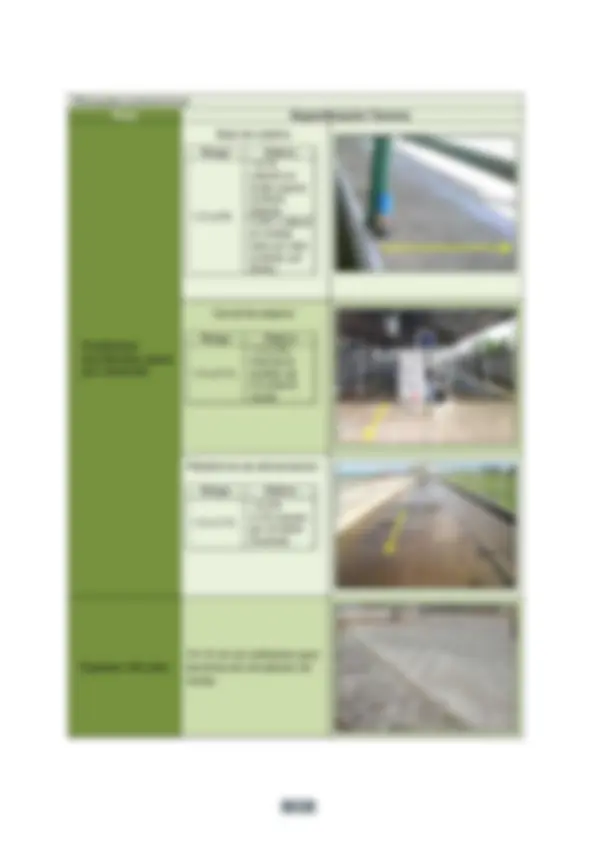
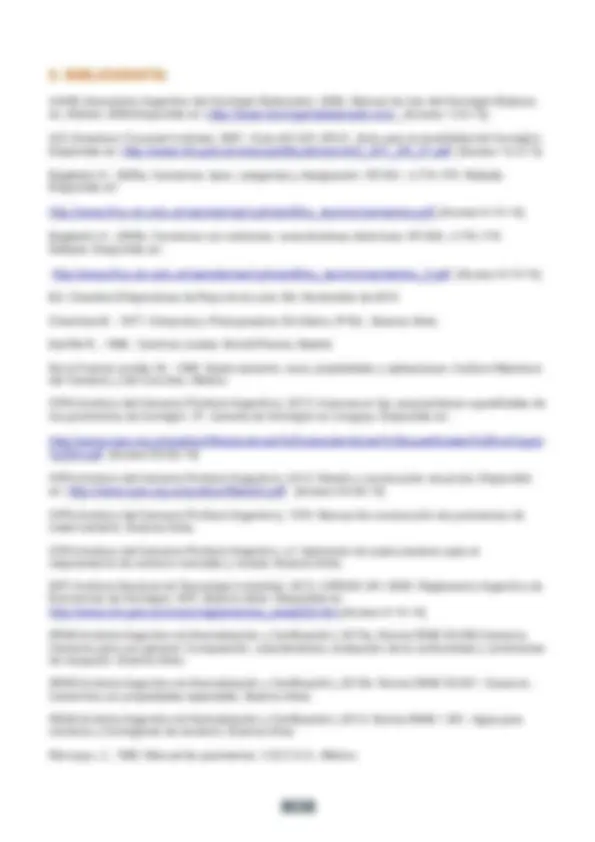
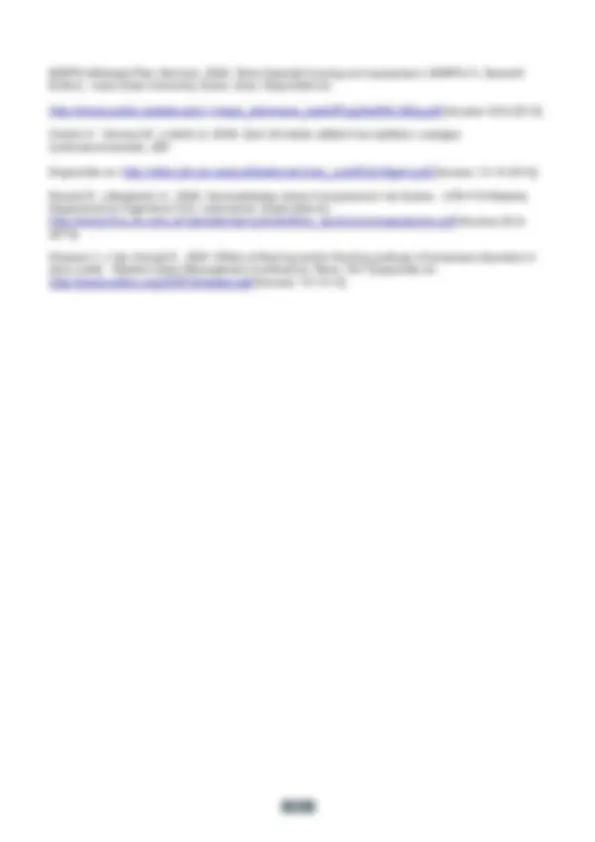
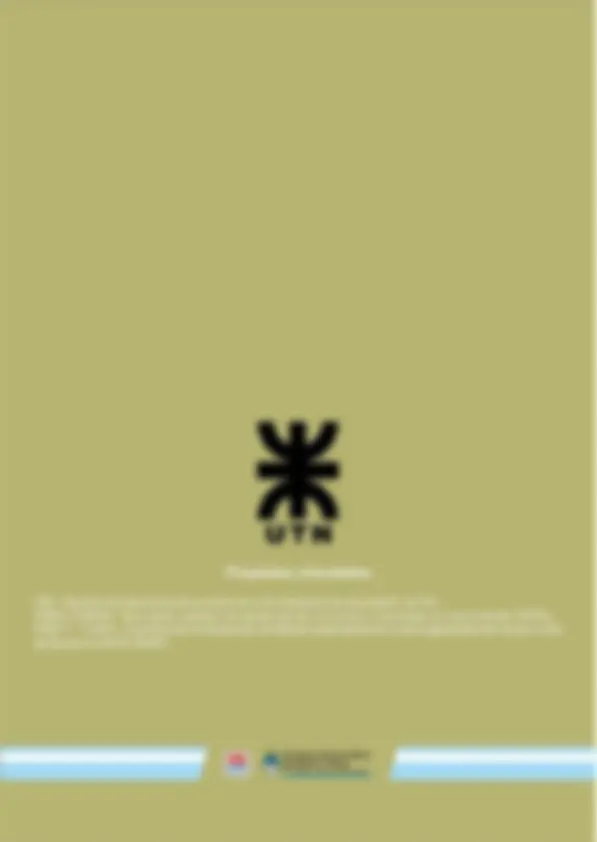
Prepara tus exámenes y mejora tus resultados gracias a la gran cantidad de recursos disponibles en Docsity
Gana puntos ayudando a otros estudiantes o consíguelos activando un Plan Premium
Prepara tus exámenes
Prepara tus exámenes y mejora tus resultados gracias a la gran cantidad de recursos disponibles en Docsity
Prepara tus exámenes con los documentos que comparten otros estudiantes como tú en Docsity
Los mejores documentos en venta realizados por estudiantes que han terminado sus estudios
Estudia con lecciones y exámenes resueltos basados en los programas académicos de las mejores universidades
Responde a preguntas de exámenes reales y pon a prueba tu preparación
Consigue puntos base para descargar
Gana puntos ayudando a otros estudiantes o consíguelos activando un Plan Premium
Comunidad
Pide ayuda a la comunidad y resuelve tus dudas de estudio
Descubre las mejores universidades de tu país según los usuarios de Docsity
Ebooks gratuitos
Descarga nuestras guías gratuitas sobre técnicas de estudio, métodos para controlar la ansiedad y consejos para la tesis preparadas por los tutores de Docsity
Tipos, características y generalidades de los concretos
Tipo: Apuntes
1 / 44
Esta página no es visible en la vista previa
¡No te pierdas las partes importantes!
Especificaciones técnicas para la construcción de pisos de hormigón para instalaciones de ordeño y anexos / Hugo Begliardo ... [et.al.]. - 1a ed. – Rafaela, Santa Fe : Ediciones INTA, 2015. E-Book.
Fecha de catalogación: 13/04/
El tema “tipo de pisos” aparece como un punto crítico dentro del diseño de instalaciones de ordeño y ane- xos. Un diseño constructivo incorrecto tiene numerosas consecuencias negativas:
Afecta la salud y bienestar de los animales (los problemas podales y la caída de vacas represen- tan una de las principales causas de descarte no voluntario). Limita una fluida circulación de las vacas. Afecta los tiempos de lavado, el consumo de agua y la higiene general de la instalación. Eleva el costo de la inversión si resulta necesario reemplazarlo anticipadamente.
Ciertos objetivos constructivos se presentan de forma casi antagónica. Así, por ejemplo, optimizar la ad- herencia puede requerir un piso excesivamente abrasivo, situación que acelera el desgaste del casco podal. La fricción óptima que favorece una adecuada adherencia depende de si el animal circula en línea recta, si debe doblar, si acelera el paso (comportamiento de fuga), si desacelera (detiene la marcha) o de la suciedad del piso (en un piso sucio, las posibilidades de patinada son mucho mayores).
Estas situaciones plantean la necesidad de considerar diferentes “tipos de pisos” para distintas partes de una misma instalación de ordeño. Este enfoque, considerando inclusive la utilización de materiales sinté- ticos para ciertos sectores, aparece como la orientación a privilegiar.
Por otra parte, los pisos deberían acompañar la vida útil de la instalación. Sin embargo, es común obser- var rápidos deterioros asociados a errores constructivos, los cuales aparecen reflejados de la siguiente manera: a) la exposición de los agregados (piedras, arena) a causa de la pérdida de la pasta de cemento (Figura 1); b) el alisamiento de la superficie con los consiguientes riesgos de resbalamientos (Figura 2); c) la desagregación en el hormigón a causa del ataque de los diferentes agentes químicos; d) el hundi- miento del terreno, base de apoyo del piso, con posterior rotura del hormigón, debido a las filtraciones a través de fisuras y juntas (Figura 3) y e) la corrosión de las armaduras, que genera un proceso expansivo, provocando fisuras y rotura del material.
El objetivo de la presente publicación es poner a disposición de productores y profesionales un conjunto de recomendaciones que posibiliten una adecuada construcción de los pisos de las instalaciones de orde- ño y anexos. En la redacción fueron privilegiados aspectos prácticos y las especificaciones técnicas se presentan como manual de buenas prácticas constructivas.
El trabajo fue estructurado en cuatro partes. La primera describe los pasos para construir una correcta base de sustento del piso, uno de los aspectos claves de su duración. En la segunda, se define el tipo de hormigón a utilizar y cuáles serían las condiciones operativas para su correcto uso. Posteriormente, se mencionan los detalles de acabado y terminación. Por último, se realiza un listado sintético de los aspec- tos más importantes a tener a tener en cuenta para lograr pisos con un adecuado diseño y durabilidad.
Figura 1. Exposición de los agregados debido a la pérdida de la pasta de cemento en corral espera. Figura 2. Alisamiento de superficie por desgaste, con exposición de piedras en sala de ordeño. Figura 3. Hundimiento de piso en corral de espera.
En la práctica, la determinación del porcentaje de humedad óptimo y el valor de densidad máxima posible de alcanzar, se realiza mediante un ensayo de laboratorio vial denominado “Proctor Estándar” (Rosetti y Begliardo, 2005). Cuanto mayor sea la energía de compactación del equipo, menor será la humedad requerida. Para los suelos limo-arcillosos del centro-oeste santafesino y este cordobés, los valores de humedad óptima empleando rodillos pata de cabra suelen estar en el entorno del 20 al 24 %, alcanzándo- se valores de densidad seca que van de 1,45 a 1,55 g/cm³ (1.450-1.550 kg/m³).
En obra se procurará lograr y mantener la humedad del suelo surgida de dicho ensayo, humedeciéndolo o aireándolo con cualquier implemento de cultivo (p.ej., un arado) hasta conseguirla. El exceso de hume- dad se puede reducir mediante el espolvoreo y mezcla con cal hasta permitir el tránsito del rodillo pata de cabra, o el paso del vibro-apisonador.
En el caso de no disponer de los señalados valores de laboratorio, se deberá recurrir a una medida prácti- ca que consiste en tomar un puñado de suelo con la mano y presionarlo. La humedad próxima a la ideal para compactar es aquella que permite moldearlo fácilmente en forma de terrón, dejando la impronta de los dedos marcados en la muestra, sin exudación o aparición de brillo sobre la misma (Figura 6). De par- tirse el terrón en dos porciones, el suelo no debe desmenuzarse (Figura 7).
Se recomienda alcanzar en obra al menos el 90% de la densidad máxima seca obtenida en el ensayo “Proctor”. Los controles y evaluación deben ser realizados por personal especializado de laboratorios.
Cuando no fuese posible realizar la evaluación antes mencionada, un modo práctico de proceder es com- pactar hasta el “rechazo” (rebote) del equipo vial o de compactación.
Es importante señalar que esta alternativa práctica, al igual que la indicada para el control de humedad de compactación, sólo se deberá implementar por razones de fuerza mayor o cuando no fuese posible contar con controles de laboratorios especializados.
Figura 6. Suelo con contenido de humedad cercano al óptimo para compactar (muestra de laboratorio).
Figura 7. Suelo con contenido de humedad cercano al óptimo: el terrón partido no debe desmenuzarse (muestra de laboratorio).
En la Figura 8 se muestra una base terminada y debidamente compactada, utilizando tierra arcillosa.
Se puede mejorar la resistencia de suelos de pobre capacidad portante y alta capacidad para retener agua, como los arcillosos o los limo-arcillosos, estabilizándolos mediante la adición de cal hidratada o cemento portland. Un suelo estable es aquél que tiene buena resistencia a la deformación, a la acción destructora del tránsito y poca sensibilidad a la presencia de agua.
Tanto la cal como el cemento son materiales conglomerantes, capaces de unir los fragmentos del suelo dando cohesión al conjunto por efecto de transformaciones químicas en su masa.
Como la estabilización tiene implicancia económica, debe tenerse presente que estas adiciones incre- mentan los costos. Sin embargo, a veces es conveniente o necesario recurrir a ellas cuando se está en presencia de terrenos pobres, con condiciones de humedad muy desfavorables.
Ambos materiales (cal o cemento), pueden ser utilizados tanto para mejorar la resistencia como para disminuir la plasticidad. En este último caso, el agregado de cal al suelo es el recurso más empleado para reducir el contenido de humedad con el objeto de permitir que su masa pueda ser trabajada con los equi- pos de compactación, sin que se pegue o adhiera a ellos.
La cal hidratada se emplea como conglomerante estabilizador de suelos cuando es necesario bajar de modo rápido la plasticidad de suelos arcillosos, para poder trabajarlos y compactarlos.
Para que la cal pueda reaccionar convenientemente y cementar las partículas del suelo, es necesario que éste tenga minerales arcillosos (sílice y alúmina). Los suelos arenosos, por lo general, no pueden estabilizarse con cal (Moncayo, 1980).
El aumento de la resistencia del suelo-cal es mucho más lento que en el caso de emplearse cemento port- land. La formación de agentes cementantes que incrementan la resistencia y durabilidad es de desarrollo gradual y puede, en algunos casos, durar varios años.
No es aconsejable el empleo de cal viva para este tratamiento, por el peligro que supone su manipulación por parte de los operarios.
Es conveniente que la proporción a adicionar de cal no esté por debajo del 3% ni exceda el 8% en peso seco de la mezcla de suelo compactado (Dal Ré, 1996). La práctica más sencilla es distribuirla en bolsas de manera regular, tanto longitudinal como transversalmente, disponiéndolas dentro de cuadrículas tra-
Figura 8. Base de tierra arcillosa (tierra colorada) compactada.
A partir del momento en que el cemento entra en contacto con el agua, la mezcla de suelo-cemento debe ser trabajada y compactada en el plazo de 2 horas, a fin de evitar el fraguado anticipado (De la Fuente Lavalle, 1995; Dal-Re, 1996).
El cemento portland es un conglomerante que, en contacto con el agua comienza su reacción química de hidratación a las 2 horasaproximadamente, y finaliza a las 4 o 6 horas, según su procedencia. Una vez finalizado el “período de fraguado”, el material comenzará su proceso de endurecimiento y ganancia de resistencia.
Los pasos para la ejecución de un estabilizado de suelo-cal o suelo-cemento son prácticamente simila- res en ambos casos.
Paso 1. Eliminación del suelo vegetal La primera operación es eliminar el suelo vegetal donde se construirá el terraplén. Tras ello, el cuenco generado se completará con suelo nuevo, en reemplazo del extraído. Es importante controlar que éste esté libre de raíces y materia vegetal. Un escarificado previo puede facilitar este paso inicial.
Paso 2. Paso de rastra El suelo a compactar debe ser trabajado para facilitar su mezcla íntima con la cal o el cemento. Lo reco- mendable es alcanzar un grado de pulverización tal que, prácticamente, el 80% del mismo tenga un tama- ño menor a 5 mm y el resto no supere 25 mm (1 pulgada) (ICPA, 1974). Para ello se pueden emplear ras- tras de discos.
El espesor final de la capa de suelo suelto pulverizado será de unos 15-20 cm (lo recomendado para el pasado y compactación con rodillo pata de cabra). Si se emplea otro equipo de compactación, se ade- cuará al mismo.
Paso 3. Distribución del material La práctica más sencilla es distribuir en el sitio la cal (o el cemento) repartiendo las bolsas de manera regu- lar, tanto longitudinal como transversalmente a la superficie del piso a ocupar por el tambo.
Las Tablas 1 y 2 proveen datos orientativos sobre cómo distribuirlos y la cantidad de material necesario según el porcentaje a adicionar y el espesor de la capa compactada.
Una vez repartidas las bolsas sobre el suelo pulverizado, se deben abrir y volcar el contenido formando caballetes transversales a la mayor longitud del terraplén.
Con posterioridad a ello, se debe distribuir la cal (o el cemento) de manera uniforme sobre toda la superfi- cie del piso. Para ello se pueden emplear distintos elementos, tales como una rastra de dientes o un ra- basto.
Tabla 2. Dimensiones de las cuadrículas para distribuir las bolsas de cemento.
Espesor de la capa de suelo compactado
Bolsas de 50 kg
Superficie por bolsa , según % de cemento y espesor de suelo compactado (*)
10 cm
1 bolsa cada
3,35m x 3,35m 2,35m x 2,35m 1,90m x 1,90m
12,5 cm 3,00m x 3,00m 2,10m x 2,10m 1,70m x 1,70m
15 cm 2,70m x 2,70m 1,90m x 1,90m 1,55m x 1,55m
(*) Densidad seca supuesta para el suelo cemento compactado: 1500 kg/m³.
El contenido de humedad del suelo para esta operación es muy importante. En el caso de mezclas de suelos de alto contenido de arcillas con cemento, lo recomendable es que la humedad esté un poco por debajo de la óptima indicada en el punto 1.2.
Paso 4. Mezclado Tras el paso anterior debe procederse de modo inmediato a la mezcla con cal (o cemento) del suelo hume- decido. Para ello se pueden emplear rastras de discos de dientes flexibles o cualquier otro implemento agrícola o instrumento que asegure una mezcla íntima y uniforme en varias pasadas.
Paso 5. Compactación de la mezcla (Foto 9). Suelo-cal Tratándose de cal, al ser la reacción química lenta, la operación de compactación puede realizar- se cómodamente durante la jornada de trabajo o dentro de las 24 horas de iniciado el mezclado del suelo con la cal y agua, como se indicó en 1.4.1. En este tipo de estabilizado, la elevada temperatura ambiente es beneficiosa para generar ga- nancia de resistencia del conjunto. En tal sentido, se recomienda interrumpir los trabajos si se está por debajo de los 10 °C, y acelerar el ritmo si se está por encima de los 30 °C. Sin embargo, nunca se debe descuidar el control permanente de la humedad de la mezcla, procurando que no esté por debajo de la óptima (Dal-Re, 1996).
Suelo-cemento La operación de compactación debe ser comenzada de inmediato y, como se mencionó en 1.4.2, finalizarse lo antes posible, procurando no excederse del tiempo indicado a partir del momento en que el cemento entra en contacto con el suelo húmedo. Como la hidratación del cemento no se produce cuando la temperatura está cercana o por debajo del punto de congelamiento, las tareas no deben realizarse si el pronóstico anticipa temperaturas inferio- res a los 4 °C (ICPA, 1974). Al iniciar la compactación, se evaluará en qué estado se encuentra la humedad de la mezcla. Tra- tándose de días secos, de alta temperatura o ventosos, puede ser conveniente regarlo previamente y trabajar con un contenido de humedad un poco mayor al sugerido como óptimo. La humedad debe ser controlada permanentemente a medida que la compactación va progresando, desde abajo hacia arriba, hasta alcanzar el espesor final de la capa. Es importante que, al menos durante los 7 días siguientes a la finalización de la compactación del suelo-cemento, la superficie sea curada para evitar la pérdida de la humedad que necesita para endure- cer y ganar resistencia (ICPA, s.f.). El procedimiento de curado puede realizarse de diferentes maneras, de las cuales se sugieren las dos siguientes en razón de su economía: a) regar la superficie 2 o 3 veces por día saturándola con agua; b) regarla a saturación y cubrirla inmediatamente con restos de silo-bolsa, sobre los que se depositarán elementos de cierto peso (ladrillos, postes en desuso, piedra, etc.), a fin de evitar su voladura.
Figura 9. Incorporación de la cal al suelo utilizando rastra de disco y posterior compactado.
El hormigón es un material conformado por cuatro componentes básicos: cemento hidráulico, agregado grueso (piedra), agregado fino (arena) y agua.
La incorporación de agua al cemento lo hidrata dando lugar a una pasta que, una vez endurecida, mantie- ne unidos a los agregados y le confiere al material resultante consistencia pétrea.
Eventualmente pueden incorporar aditivos y/o adiciones para mejorar su prestación.
Los aditivos son productos químicos de suministro en estado líquido. Se incorporan en pequeño volumen al agua de amasado o al pastón, con el objeto de modificar alguna o varias de sus propiedades (fluidez, plasticidad, etc.) y conseguir ciertas ventajas en el hormigón endurecido (resistencia, durabilidad, imper- meabilidad, etc.).
Las adiciones, en cambio, son materiales pulverulentos finamente divididos que se agregan al hormigón en un volumen significativo para también modificar, como en el caso de los aditivos, algunas de sus pro- piedades. De todos modos, tanto aditivos como adiciones deben ser aplicados por un profesional o per- sonal capacitado para conseguir los efectos pretendidos.
El agua El agua a emplear en la elaboración de los pastones (agua de amasado) debe cumplir con los requisitos físicos y químicos establecidos en la Norma IRAM 1601. En la Tabla 3 se mencionan algunos de los pará- metros más importantes.
El exceso de cloruros en el hormigón pretensado puede provocar corrosión en las armaduras, expan- diéndolas y generando destrucción del hormigón que las recubre. El de sulfatos puede provocar ataques en la pasta de cemento, desagregando el material hasta dejar la piedra y arena expuestas.
En principio, toda agua potable es apta, por lo cual debe estar exenta de sustancias orgánicas en des-
Tabla 3. Requisitos químicos para el agua de mezclado y curado (IRAM, 2012).
Requisitos Unidad Mínimo Máximo
Residuo sólido mg/dm^3 ------ 5000
Materia orgánica, expresada como oxígeno consumido mg/dm^3 ------ 3
Sulfato, expresado como SO 4 2-^ mg/dm^3 ------ 1000
Cloruro, expresado como Cl-
Para emplear en hormigón simple
mg/dm^3 ------ (^2000)
Para emplear en hormigón convencional
mg/dm^3 ------ 700
Para emplear en hormigón pretensado
mg/dm^3 ------ (^500)
Hierro, expresado como Fe mg/dm^3 ------ 1
composición, excesos de cloruros y sulfatos. De no contarse con acuíferos de calidad apropiada, lo reco- mendable es proveerse de agua apta mediante camiones o acoplados con cisterna.
La cantidad de agua necesaria para elaborar el hormigón está en relación directa con la cantidad de ce- mento que se requiere por condiciones de durabilidad. Sin embargo, por razones de pérdidas, evapora- ción, otros usos en obra o imprevistos, es aconsejable proveerse de una reserva queal menos duplique esa demanda, fundamentalmente si el centro de provisión se encuentra lejano.
El cemento portland El cemento portland es el componente activo del hormigón, por cuanto al mezclárselo con el agua de ama- sado reacciona químicamente y desarrolla su propiedad de ligante cementicio de los agregados inertes (arena y piedra).
Actualmente existen en el mercado diferentes tipos de cemento portland para uso general: normal (CPN), puzolánico (CPP), con filler calcáreo (CPF), compuesto (CPC), etc.; de diferentes categorías (CP30, CP40, CP50) y con múltiples propiedades especiales (alta resistencia inicial, bajo calor de hidra- tación, resistencia a los sulfatos, etc.) (Begliardo, 2005 a,b).
Cada opción cumple funciones específicas. Consecuentemente, en el momento de tener que construir el piso, es recomendable asesorarse profesionalmente y seleccionar aquel cemento que más convenga a las necesidades de la obra. Sin embargo, normalmente este material se adquiere en corralones de pla- zas cuya oferta suele ser limitada en lo que hace a variedades, lo que constituye un factor limitante y con- dicionante de su elección.
Considerando esta realidad, los cementos de las categorías CP30 ó CP40, que cumplan con la norma IRAM 50.000 (IRAM 2010a) e identificados con las siglas CPN. CPF, CPC o CPP (los tipos más comunes de hallar en el mercado minorista), son aptos para la elaboración de hormigones para pisos de instalacio- nes de ordeño y anexos.
En ciertos casos especiales (suelos o aguas agresivos) conviene emplear cementos con propiedades especiales, que cumplan con la norma IRAM 50.001 (IRAM 2010b). Estos son los mismos cementos cita- dos anteriormente, pero que contienen en su formulación propiedades que les otorgan prestaciones o especial resistencia a dicha agresividad. Entre ellos se encuentran los de moderada o alta resistencia a los sulfatos. En este caso, en los envases debe estar inscripta la sigla MRS o ARS, respectivamente.
A modo de ejemplo, si se necesita de un cemento portland puzolánico, de categoría CP40 y altamente resistente a los sulfatos, en el envase debería figurar la siguiente sigla: CPP 40 (ARS).
Los agregados Se designa de este modo a las piedras y arenas. Conforman la parte inerte o pasiva del hormigón.
Deben proceder de rocas sanas, que no sean blandas, porosas o desmenuzables.
Las arenas pueden ser de origen natural o artificial. Las primeras son de naturaleza silícea y se las en- cuentra en ríos, costas marítimas y canteras. Las artificiales se obtienen a partir de la trituración de rocas, generalmente graníticas. Las piedras también pueden ser de origen natural (cantos rodados) o artificial (piedra partida).
Los agregados normalmente utilizados en el centro oeste santafesino-este cordobés cumplen con los requisitos de calidad para la elaboración de hormigones. La arena generalmente procede de ríos de la región y la piedra empleada suele ser partida, o bien canto rodado.
En todos los casos, los agregados deben ser limpios y estar libres de impurezas orgánicas, limos, arcillas e inclusiones salinas. El lavado de los mismos, de ser necesario, es un medio eficaz para lograr dicha calidad.
Tabla 4. Espesor del piso de hormigón según tipo de uso.
Fuente: Adaptada de Chambre D’Agricultura de Pays de la Loire. Ed. Noviembre de 2010.
En la Tabla 5 se presentan los valores de pendientes recomendadas por sector de la instalación de orde- ño y anexos. Las recomendaciones favorecen el lavado de los pisos y el rápido secado de las superficies, sin condicionar el movimiento de los animales.
Existen dos formas de proveerse del hormigón: contratando el servicio (hormigón preparado en planta elaboradora) o preparándolo en obra.
2.5.1. Hormigón preparado en planta elaboradora
Las plantas de hormigón elaborado, con certificación de calidad, utilizan protocolos de elaboración que permiten lograr la calidad solicitada. Estas firmas comerciales se ocupan de llevarlo hasta el lugar del emplazamiento mediante camiones moto-hormigoneros, también conocidos como “mixer” (mezclado- res), en tanto no se presenten problemas de accesibilidad.
Es de suma importancia el asesoramiento de un profesional de la construcción sobre las características del hormigón a solicitar, así como la presencia de éste al momento de su recepción y control en obra.
La Tabla 6 reproduce las recomendaciones de la AAHE (Asociación Argentina del Hormigón Elaborado) para solicitar este tipo de servicios, mientras que en la Tabla 7 se enumeran los datos básicos a solicitar al proveedor en función de las características especiales que requieren los pisos para instalaciones de orde- ño y anexos (resistencia a la abrasión, impermeabilidad y, en su caso, resistencia al ataque de agentes agresivos, como sulfatos y cloruros), conforme a lo establecido en el Reglamento Cirsoc 201:2005 (INTI, 2013). Para su elaboración se supuso un tambo emplazado en el centrooeste santafesino, clase de expo- sición C1 (“Elementos en contacto frecuente con agua, o zonas con humedad relativa ambiente media en invierno superior al 75%, y que tengan una probabilidad mayor que el 50% de alcanzar al menos una vez temperaturas por debajo de 5ºC).
Tabla 5. Pendientes de los pisos a utilizar según el sector de la instalación.
Sector Pendiente (valor mínimo - máximo).
Sala de ordeño
1,5 a 4 % (valor de pendiente lateral utilizado en instalaciones de ordeño lado por lado)
Corral de espera 1,5 – 5 %
Sala de leche 1,5 – 2 %
Playones de alimentación 1,5 – 3 %
Al pedir Hormigón Elaborado se está contratando un servicio que lleva implícito un producto, por lo que el pedido tiene que ser muy preciso. Se debe contar con el asesoramiento de un profesional.
Es muy importante asegurar, antes de emitir una orden de compra, que la cantidad y velocidad de despacho pueda ser verificada por el proveedor y que el hormigón pueda ser manipulado correcta- mente por el comprador. Las órdenes deben ser siempre claras y las notificaciones sobre cancelacio- nes o cambios en las mismas se deben acordar de antemano.
La descarga de un moto-hormigonero debe cumplirse dentro del tiempo establecido, debiéndose anotar claramente ese dato en el remito correspondiente al viaje del mencionado camión.
El usuario debe suministrar datos básicos de su obra al productor, los cuales se enumeran a continua- ción:
1. Tipo de estructura; total de hormigón en m³ que llevará toda la obra; tiempo estimado de ejecución. 2. Resistencia característica a compresión del hormigón en MPa o en kg/cm². 3. Tipo y cantidad mínima de cemento por metro cúbico de hormigón que pueda ser necesario por exigencias de durabilidad u otros que no sean la condición de resistencia a compresión (como relación agua/cemento). 4. Tipo y tamaño máximo de los agregados. 5. Consistencia de la mezcla fresca en centímetros en el momento de la descarga, medida en el tronco de Cono de Abrams. 6. Aditivos químicos a incorporar al hormigón. 7. Contenido de aire intencionalmente incorporado en por ciento, en las mezclas que lo especifiquen. 8. Características especiales que requiere ese hormigón (p. ej.: a la vista, resistente al desgaste, resistente al ataque por sulfatos, etc.). 9. Si será hormigón bombeado o el transporte interno se hará por medios tradicionales. 10. Capacidad de recepción del hormigón en la obra, en lo posible en m3/hora, y toda otra información pertinente que surja del cambio de ideas entre el usuario y productor.
Tabla 6. Modo de especificar el pedido de hormigones a plantas elaboradoras. (Adaptado de AAHE, 2008).
En la Tabla 8 se sugieren los requisitos y resguardos mínimos a tener en cuenta para elaborar el hormi- gón in situ , de no poder contarse con el suministro de plantas elaboradoras, acorde a lo establecido en el Reglamento Cirsoc 201:2005 (INTI, 2013)).
En obra, los hormigones se pueden diseñar y preparar de modo racional (en peso), siempre que se cuen- te con la asistencia de un profesional y equipos para el pesaje de los materiales. En no pocas ocasiones, sin embargo, la dosificación deberá hacerse de modo empírico (en volumen), debiendo asumirse los riesgos de falta de homogeneidad, uniformidad y calidad necesarias.
Una dosificación empírica usual es la comúnmente llamada “1:2:3” (1 parte de cemento: 2 partes de are- na: 3 partes de piedra). En tanto se emplee la mínima cantidad de agua necesaria (menos de medio balde de agua por cada balde de cemento) podrían obtenerse hormigones con resistencias próximas a la resis- tencia indicada (H-40). Para ello, el pastón no debe ser “blando o fluido” (al no haber armadura, o de estar ésta muy espaciada, no necesita serlo) yuna vez colocado, debería ser vibrado. Esto puede realizarse con vibrador de aguja o inmersión, los cuales pueden adquirirse o alquilarse en el mercado (Figura 11).
Ciertamenteno será sencillo lograr en obra hormigones con tan baja relación agua/cemento y garantizar la resistencia indicada en la Tabla indicada sin la asistencia de un profesional.
Tabla 8. Especificaciones para hormigones de pisos para tambo elaborados en obra.
Hormigón de pisos para tambo elaborado en obra
Máxima razón agua/cemento en masa (a/c)
Clase mínima de hormigón
(resistencia especificada)
H-30 (300 kg/cm^2 ; posible de lograr con la asistencia y control de un profesional)
Contenido mínimo de cemento Sugerido: 300 kg/m 3 (6 bolsas/m^3 )
Aditivo incorporador de aire Si, según Tabla 5.3 Reglto. CIRSOC 201.
Aditivo fluidificante Recomendable (disminuyen la razón agua/cemento; se necesita de la asistencia y control de un profesional)
Aditivo superfluidificante (^) Su aplicación será evaluada por el profesional, si las necesidades de obra lo demanda.
Consistencia (asentamiento medido con el cono de Abrams)
De 5 a 10 cm (hormigón plástico; se recomienda el empleo en obra del cono de Abrams por parte de un profesional o personal capacitado)
La Tabla 9 presenta la forma tradicional de dosificar en volumen, aún utilizada en obras privadas no con- troladas. Se definen las proporciones de materiales necesarios según el tipo de piso.
Recomendaciones
El mezclado de los materiales debe ser mecánico, recurriendo a hormigoneras de capacidad útil adecuada. Nunca debe hacérselo de modo manual.
La elaboración debe estar a cargo de personal idóneo, quien verificará permanentemente la uni- formidad de dicho mezclado.
La incorporación de los materiales al tambor girando debe ser paulatina y preferentemente en el siguiente orden: 1°) una porción del agua de mezclado; 2°) introducir el cemento y el agregado fino; 3°) introducir el agregado grueso; 4°) completar con el resto del agua.
Para hormigoneras de hasta 1 m³ (1.000 litros) de capacidad, el tiempo de mezclado será de unos 90 segundos (un minuto y medio), contados a partir del momento en que hayan ingresado todos los mate- riales al tambor. No es aconsejable un tiempo de mezclado excesivo, por cuanto puede modificar la con- sistencia deseada.
Figura 11. Vibrador de inmersión.
Tabla 9. Materiales necesarios para elaborar 1 m³ de hormigón (dosificación en volumen) (*)
Proporción en volumen
Materiales necesarios para preparar 1 m^3 de hormigón Usos Cemento
(kg)
Arena
(m^3 )
Piedra
(m^3 )
(1/2 m^3 )
(3/4 m^3 )
Piso para tambo, tanques, pilotes.
1:3:3 300 0,650 0,650 Entrepisos de edificios.
1:4:4 235 0,670 0,670 Zapatas, Cimientos
(*) Basada y adaptada de Chandías ,1977. El uso “piso de tambo” es una incorporación de este trabajo.