
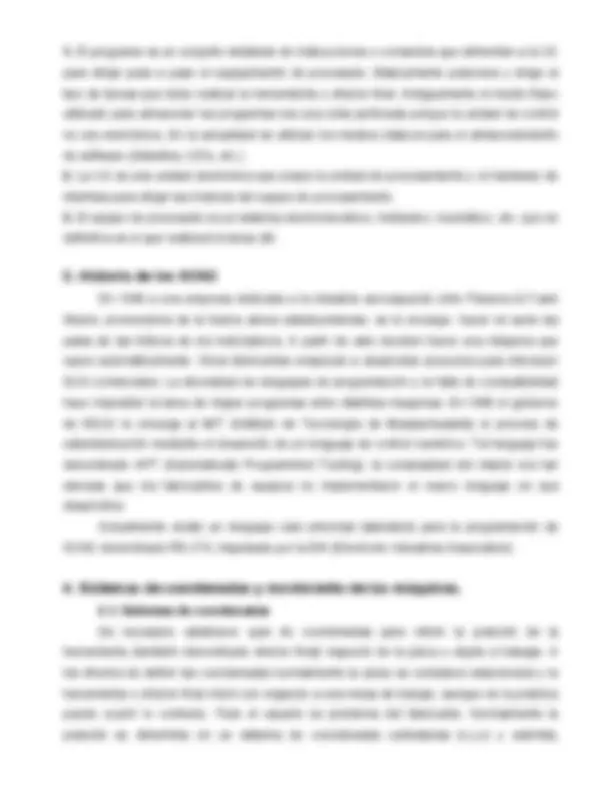
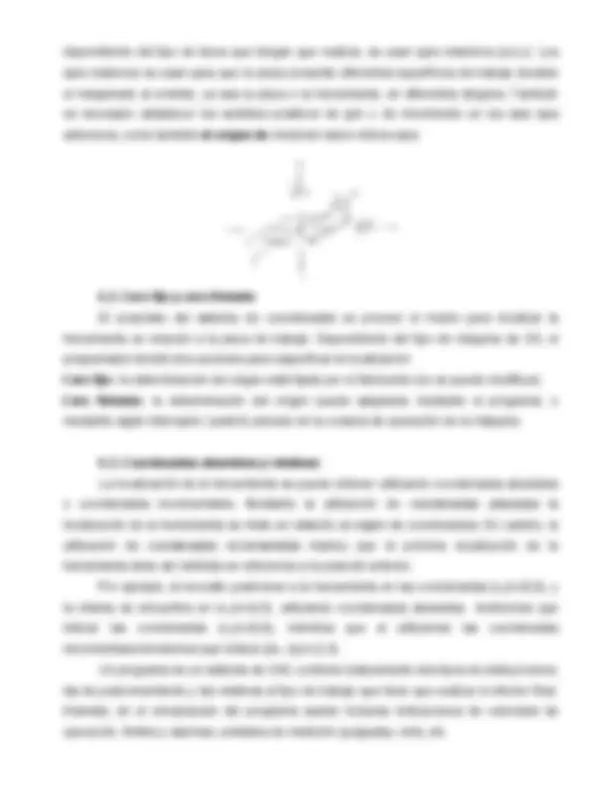
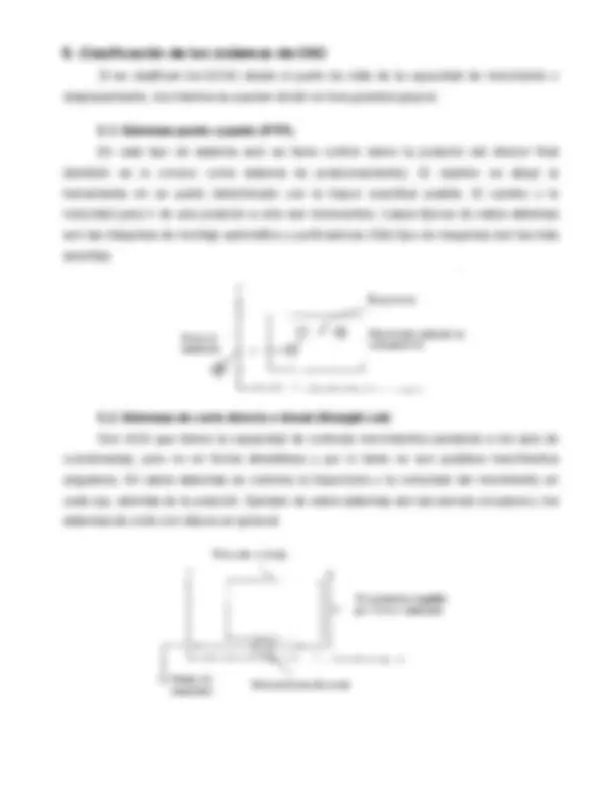
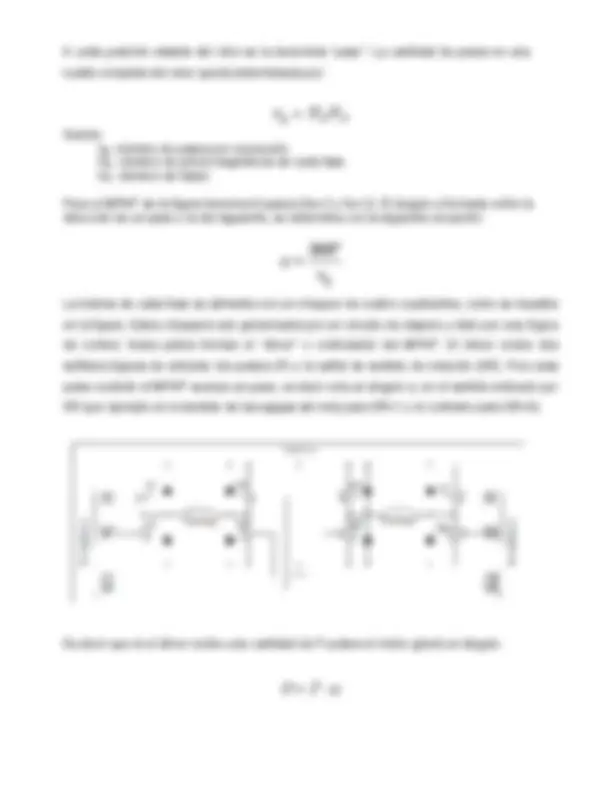
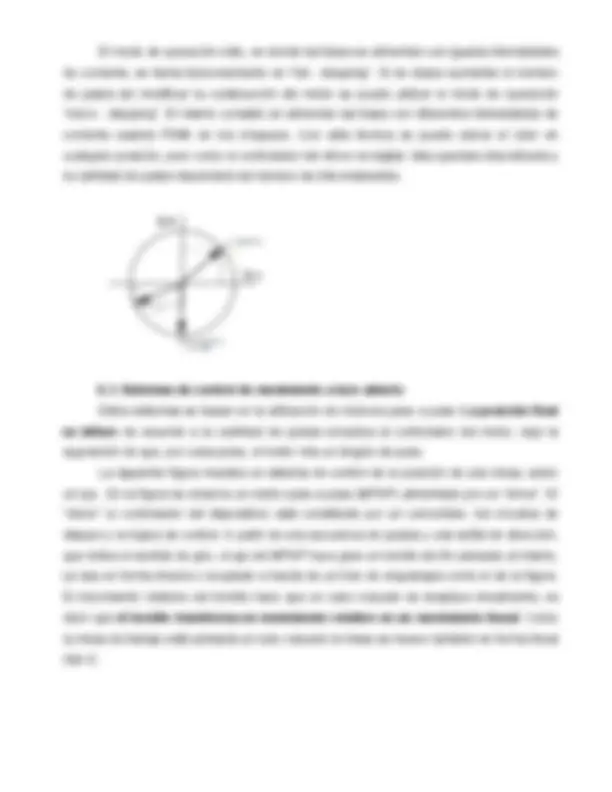
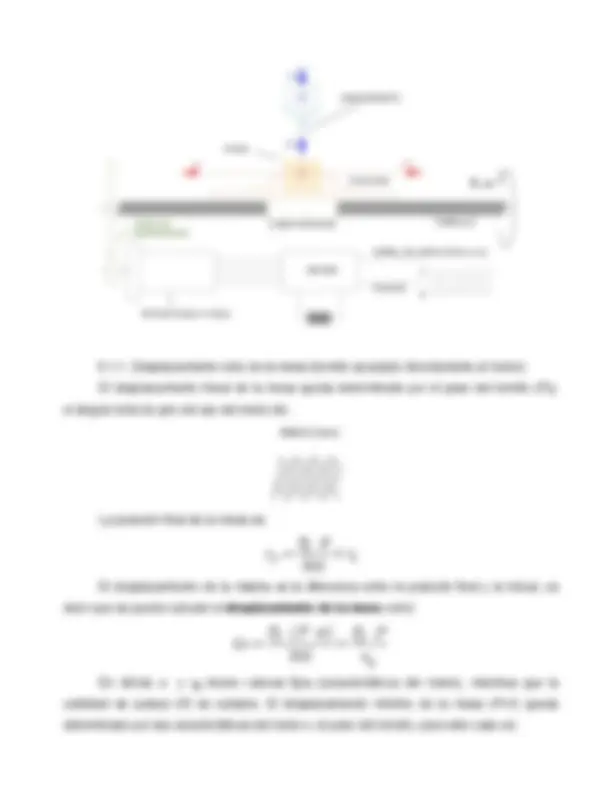
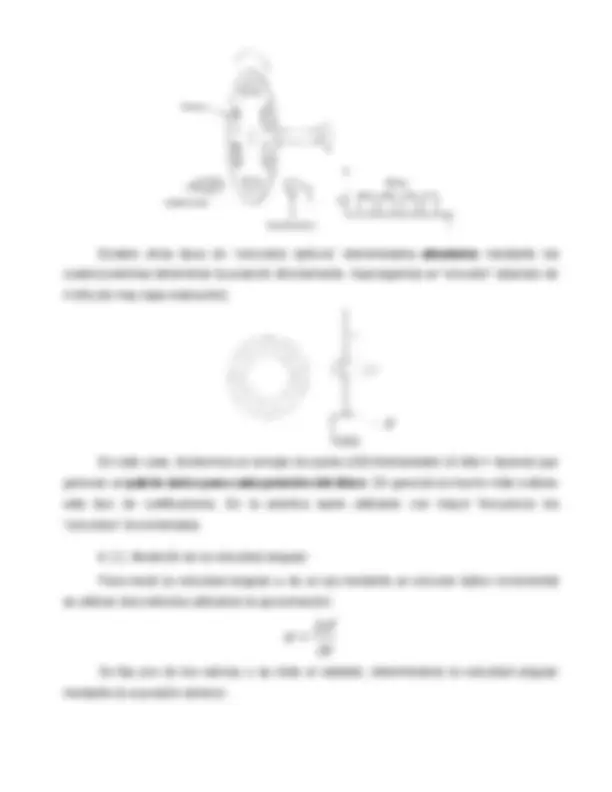
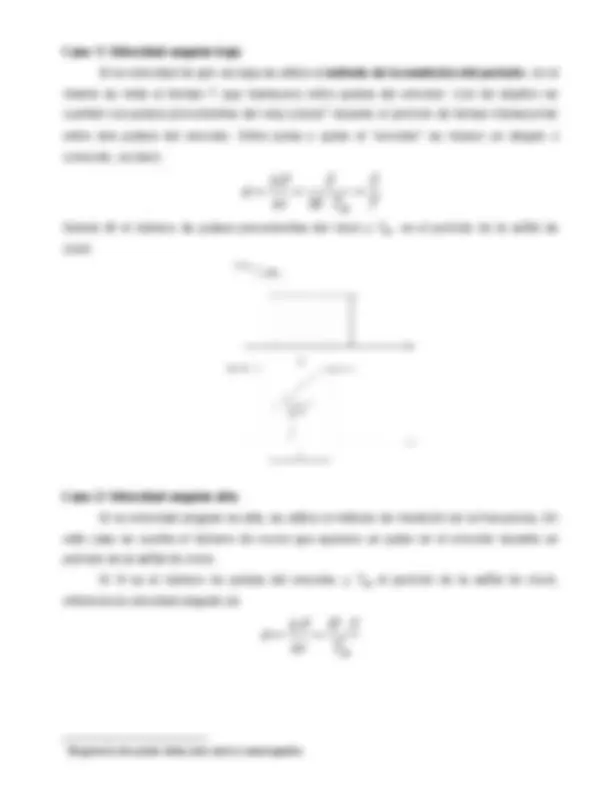
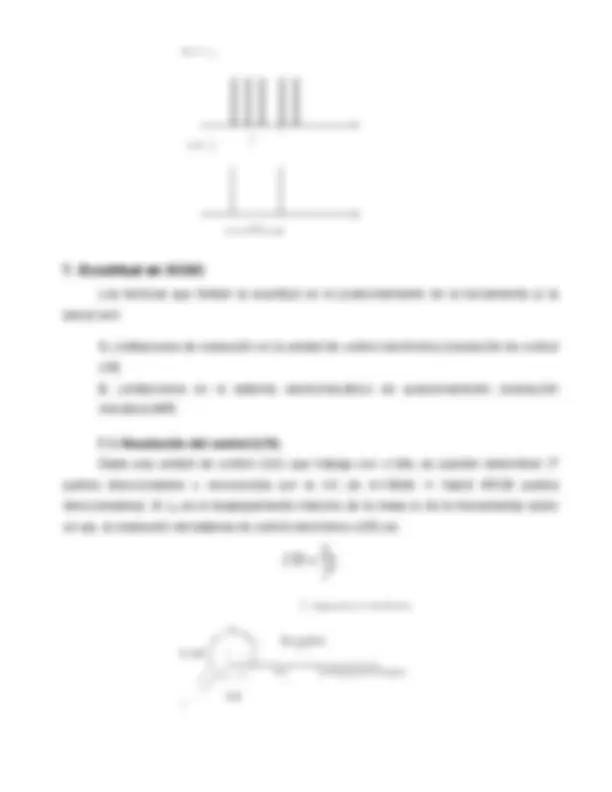
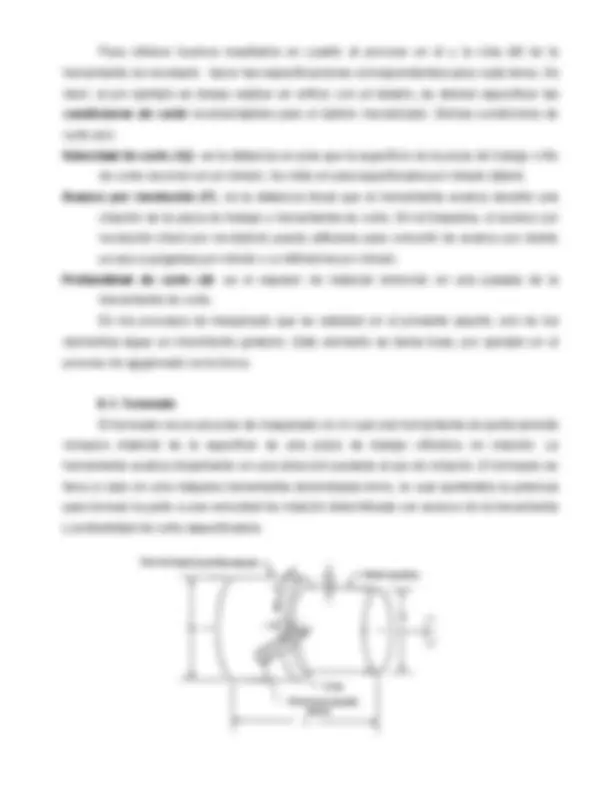
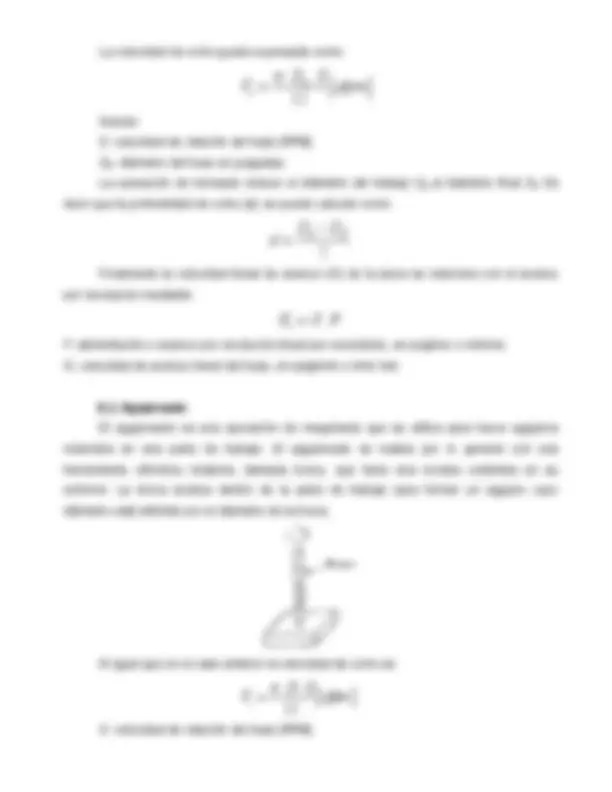
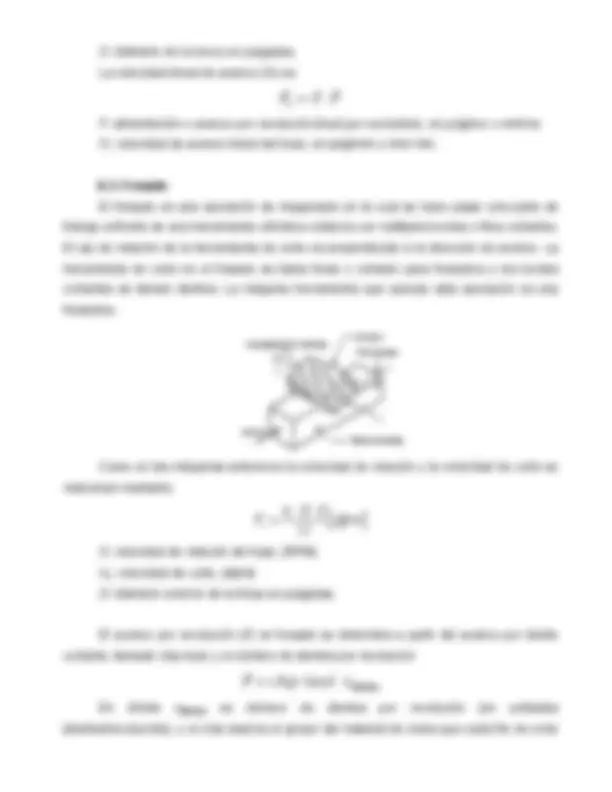
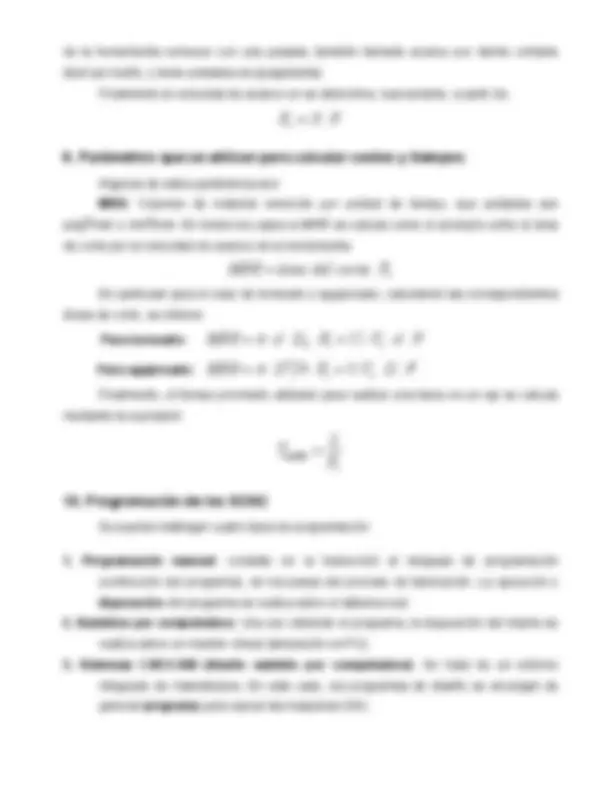
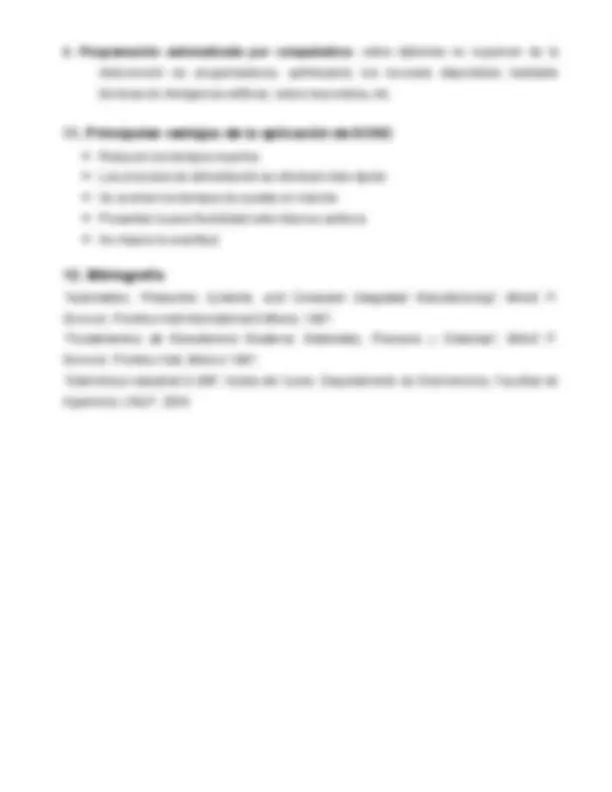
Prepara tus exámenes y mejora tus resultados gracias a la gran cantidad de recursos disponibles en Docsity
Gana puntos ayudando a otros estudiantes o consíguelos activando un Plan Premium
Prepara tus exámenes
Prepara tus exámenes y mejora tus resultados gracias a la gran cantidad de recursos disponibles en Docsity
Prepara tus exámenes con los documentos que comparten otros estudiantes como tú en Docsity
Los mejores documentos en venta realizados por estudiantes que han terminado sus estudios
Estudia con lecciones y exámenes resueltos basados en los programas académicos de las mejores universidades
Responde a preguntas de exámenes reales y pon a prueba tu preparación
Consigue puntos base para descargar
Gana puntos ayudando a otros estudiantes o consíguelos activando un Plan Premium
Comunidad
Pide ayuda a la comunidad y resuelve tus dudas de estudio
Descubre las mejores universidades de tu país según los usuarios de Docsity
Ebooks gratuitos
Descarga nuestras guías gratuitas sobre técnicas de estudio, métodos para controlar la ansiedad y consejos para la tesis preparadas por los tutores de Docsity
Es sobre las máquinas CNC y su función
Tipo: Apuntes
1 / 22
Esta página no es visible en la vista previa
¡No te pierdas las partes importantes!
Es una forma de automatización programable en la que el equipamiento de procesado es controlado por medio de números, letras o símbolos. Estos números, letras o símbolos son codificados en un formato apropiado para conformar un programa de instrucciones para desarrollar una tarea en particular. La capacidad que tienen los sistemas de control numérico (SCN) de cambiar programas los hace apropiados para volúmenes de producción bajos o medios. Estos aceptan muy bien cambios en la configuración del producto final haciéndolos ideales para la producción en lotes (batch). Entre las aplicaciones encontramos 2 grandes divisiones: Máquinas herramienta clásicas, tales como tornos, fresadoras, taladros, etc. Máquinas para el montaje de piezas (o ensambladoras), y de inspección. Ambas categorías tienen en común la tarea de posicionar una herramienta o elemento procesador con respecto al objeto para luego efectuar una tarea en particular.
Conceptualmente está constituido por tres partes:
PROGRAMA (^) UNIDAD DE CONTROL UC EQUIPAMIENTO DE PROCESADO
dependiendo del tipo de tarea que tengan que realizar, se usan ejes rotatorios (a,b,c). Los ejes rotatorios se usan para que la pieza presente diferentes superficies de trabajo durante el maquinado al orientar, ya sea la pieza o la herramienta, en diferentes ángulos. También es necesario establecer los sentidos positivos de giro y de movimiento en los seis ejes anteriores, como también el origen de medición sobre dichos ejes.
4.2. Cero fijo y cero flotante El propósito del sistema de coordenadas es proveer el medio para localizar la herramienta en relación a la pieza de trabajo. Dependiendo del tipo de máquina de CN, el programador tendrá dos opciones para especificar la localización Cero fijo: la determinación del origen está fijada por el fabricante (no se puede modificar). Cero flotante: la determinación del origen puede asignarse mediante el programa, o mediante algún interruptor (switch) ubicado en la consola de operación de la máquina.
4.3. Coordenadas absolutas y relativas La localización de la herramienta se puede obtener utilizando coordenadas absolutas o coordenadas incrementales. Mediante la utilización de coordenadas absolutas la localización de la herramienta se mide en relación al origen de coordenadas. En cambio, la utilización de coordenadas incrementales implica que la próxima localización de la herramienta debe ser definida en referencia a la posición anterior. Por ejemplo, si necesito posicionar a la herramienta en las coordenadas (x,y)=(6,8), y la misma se encuentra en (x,y)=(4,5), utilizando coordenadas absolutas tendremos que indicar las coordenadas (x,y)=(6,8), mientras que si utilizamos las coordenadas incrementales tendremos que indicar (∆x, ∆y)=(2,3). Un programa de un sistema de CNC contiene básicamente dos tipos de instrucciones: las de posicionamiento y las relativas al tipo de trabajo que tiene que realizar el efector final. Además, en el encabezado del programa suelen incluirse indicaciones de velocidad de operación, límites y alarmas, unidades de medición (pulgadas, mm), etc.
Si se clasifican los SCNC desde el punto de vista de la capacidad de movimiento o desplazamiento, los mismos se pueden dividir en tres grandes grupos:
5.1. Sistemas punto a punto (PTP). En este tipo de sistema solo se tiene control sobre la posición del efector final (también se lo conoce como sistema de posicionamiento). El objetivo es situar la herramienta en un punto determinado con la mayor exactitud posible. El camino y la velocidad para ir de una posición a otra son irrelevantes. Casos típicos de estos sistemas son las máquinas de montaje automático y perforadoras. Este tipo de maquinas son las más sencillas.
5.2. Sistemas de corte directo o lineal (Straight-cut) Son SCN que tienen la capacidad de controlar movimientos paralelos a los ejes de coordenadas, pero no en forma simultánea y por lo tanto no son posibles movimientos angulares. En estos sistemas se controla la trayectoria y la velocidad del movimiento en cada eje, además de la posición. Ejemplo de estos sistemas son las sierras circulares y los sistemas de corte con discos en general.
Al “energizar” ó alimentar una sola de las fases el rotor trata de alinearse con el campo magnético producido por ella. Como el sentido del campo depende del sentido de circulación de la corriente en la bobina, tendremos dos posiciones posibles del rotor para cada fase:
Si se energizan dos fases simultáneamente, el campo estatórico resultante se encuentra en la dirección de la bisectriz del ángulo formado por las fases, y su sentido dependerá de los sentidos de las corrientes en las bobinas. En la figura siguiente se muestran la posición del rotor para las dos fases alimentadas con diferentes sentidos de corriente:
A cada posición estable del rotor se la denomina “paso”. La cantidad de pasos en una vuelta completa del rotor queda determinada por:
n (^) p = P F Siendo: np: número de pasos por revolución. NP: número de polos magnéticos de cada fase NF: número de fases
Para el MPAP de la figura tenemos 8 pasos (NP=2 y NF=2). El ángulo α formado entre la dirección de un paso y la del siguiente, se determina con la siguiente ecuación:
360º n p
α =
La bobina de cada fase se alimenta con un chopper de cuatro cuadrantes, como se muestra en la figura. Estos choppers son gobernados por un circuito de disparo y éste por una lógica de control; todos juntos forman el “driver” o controlador del MPAP. El driver recibe dos señales lógicas de entrada: los pulsos (P) y la señal de sentido de rotación (SR). Pos cada pulso recibido el MPAP avanza un paso, es decir rota un ángulo α, en el sentido indicado por SR (por ejemplo en el sentido de las agujas del reloj para SR=1 y el contrario para SR=0).
Es decir que si el driver recibe una cantidad de P pulsos el motor girará un ángulo:
θ = P⋅α
HERRAMIENTA
PIEZA
CUBO ROSCADO
FIJACION
TORNILLO
MOTOR PASO A PASO
DRIVER PULSOS
SEÑAL DE DIRECCION (1,0)
TREN DEENGRANAJES
-X^ +X
+Z
-Z
1 0
6.1.1. Desplazamiento neto de la mesa (tornillo acoplado directamente al motor) El desplazamiento lineal de la mesa queda determinado por el paso del tornillo (PT), el ángulo total de giro del eje del motor (θ). PASO (mm)
La posición final de la mesa es:
x (^) f = P^ T⋅^ θ +xi
El desplazamiento de la misma es la diferencia entre la posición final y la inicial, es decir que se puede calcular el desplazamiento de la mesa como:
( )
T (^) T p
⋅ ⋅ α ⋅
En dónde α y np tienen valores fijos (característicos del motor), mientras que la cantidad de pulsos (P) es variable. El desplazamiento mínimo de la mesa (P=1) queda determinado por las características del motor y el paso del tornillo, para este caso es:
min^ T^ T p
∆ = ⋅^ α =
6.1.2. Desplazamiento neto de la mesa (tornillo acoplado al motor a través de un tren de engranajes) Para disminuir el desplazamiento mínimo de la mesa se puede utilizar una caja de engranajes o poleas dentadas, donde normalmente el motor mueve el engranaje más chico.
De las relaciones entre velocidades tangenciales y angulares: 1 1 1 2 2 2
ω ω
Dónde: v 1 y v 2 : velocidad tangencial de los engranajes del eje del motor y del tornillo respectivamente, ω 1 y ω 2 : velocidad angular del eje del motor y del tornillo respectivamente, d 1 y d 2 : diámetro del disco de engranajes del motor y del tornillo respectivamente, Teniendo en cuenta además, que las velocidades tangenciales v 1 y v 2 son iguales, y
que ω = d θ dt , se puede obtener el desplazamiento de la mesa para este caso:
2 1 1
∆ = ⋅^ θ^ = ⋅θ ⋅
O bien: ( ) (^1 )
T (^) T p
⋅ ⋅ α ⋅
El desplazamiento mínimo en este caso es:
Existen otros tipos de “encoders ópticos” denominados absolutos mediante los cuales podemos determinar la posición directamente. Supongamos un “encoder” absoluto de 4 bits (de muy baja resolución).
En este caso, tendremos un arreglo de pares LED-fototransistor (4 bits 4pares) que generan un patrón único para cada posición del disco. En general es mucho más costoso este tipo de codificadores. En la práctica suele utilizarse con mayor frecuencia los “encoders” incrementales.
6.2.2. Medición de la velocidad angular Para medir la velocidad angular ω de un eje mediante un encoder óptico incremental se utilizan dos métodos utilizando la aproximación:
∆ t
ω =^ ∆^ θ
Se fija uno de los valores, y se mide el restante, determinando la velocidad angular mediante la expresión anterior.
Caso 1: Velocidad angular baja Si la velocidad de giro es baja se utiliza el método de la medición del período, en el mismo se mide el tiempo T que transcurre entre pulsos del encoder. Con tal objetivo se cuentan los pulsos provenientes del reloj (clock)^1 durante el período de tiempo transcurrido
conocido, es decir:
θ δ δ ω
Siendo M el número de pulsos provenientes del clock y Tck es el período de la señal de clock.
Caso 2: Velocidad angular alta Si la velocidad angular es alta, se utiliza el método de medición de la frecuencia. En este caso se cuenta el número de veces que aparece un pulso en el encoder durante un período de la señal de clock. Si N es el número de pulsos del encoder, y Tck el período de la señal de clock, entonces la velocidad angular es:
ck
ω = ∆^ θ^ = ⋅δ
(^1) En general estos pulsos duran entre micro y nanosegundos.
La CR disminuye con el avance de la tecnología (aumento de la cantidad de bits). Es preciso aclarar que L no es la longitud de la mesa sino que es el máximo desplazamiento posible de la misma.
7.2. Resolución mecánica (MR) La MR es el desplazamiento mínimo debido a restricciones electromecánicas (∆xmín). Para el caso de un motor un MPAP conectado directamente al tornillo guía, la resolución mecánica es:
T S
donde PT es el paso del tornillo, y nS es la cantidad de pasos por revolución del MPAP, es
decir: ns = 360º α.
La MR se puede disminuir, por ejemplo conectando el MPAP al tornillo mediante un tren de engranajes, como ya se estudió en la sección 6.1.
7.3. Determinación de la cota de error Si se desea hacer un agujero en un punto intermedio, entre puntos reconocibles por la unidad de control, la posición es redondeada al punto más cercano. Esta situación se ilustra en la figura siguiente.
Si el factor limitante es la computadora el mayor error se produce cuando se necesita realizar una operación en el punto medio de dos puntos reconocibles por la computadora. Es
conoce su valor con exactitud. De igual manera, si el factor limitante es el sistema mecánico, el máximo error queda determinado por el desplazamiento mínimo debido a limitaciones
Además de los errores determinísticos, existe otro tipo de errores que deben tenerse en cuenta, estos son los errores aleatorios o fortuitos. Los errores fortuitos se deben al sistema electromecánico, principalmente por causa de juego en los engranajes, desgaste, dilatación térmica, deformación de las piezas debido al esfuerzo. Es común asignar una distribución normal (gaussiana) para la probabilidad de ocurrencia de dichos errores, por lo tanto se puede aproximar el error aleatorio mediante:
Finalmente el máximo error del SCNC se calcula teniendo en cuenta los efectos de los errores determinísticos y los aleatorios:
3 σ
La aplicación más difundida es el proceso de maquinado, el cual es un proceso de manufactura en el que la geometría de una pieza es modificada mediante la remoción de material en exceso. Esta remoción de material en exceso es obtenida por medio del movimiento relativo entre una herramienta de corte y la pieza. Controlando este movimiento se obtiene la geometría deseada. Los tipos más comunes son: torneado, taladrado, fresado, y cepillado o devastado.
La velocidad de corte queda expresada como:
Siendo: S: velocidad de rotación del huso [RPM] Do: diámetro del huso en pulgadas. La operación de torneado reduce el diámetro del trabajo Do al diámetro final Df. Es decir que la profundidad de corte (d), se puede calcular como:
Finalmente la velocidad lineal de avance (Fr) de la pieza se relaciona con el avance por revolución mediante:
F: alimentación o avance por revolución (feed per revolution), en pulg/rev o mm/rev. Fr: velocidad de avance lineal del huso, en pulg/min o mm/ min.
8.2. Agujereado El agujereado es una operación de maquinado que se utiliza para hacer agujeros redondos en una parte de trabajo. El agujereado se realiza por lo general con una herramienta cilíndrica rotatoria, llamada broca, que tiene dos bordes cortantes en su extremo. La broca avanza dentro de la parte de trabajo para formar un agujero cuyo diámetro está definido por el diámetro de la broca.
Al igual que en el caso anterior la velocidad de corte es:
S: velocidad de rotación del huso [RPM]
D: diámetro de la broca en pulgadas. La velocidad lineal de avance (Fr) es: F r = S ⋅F F: alimentación o avance por revolución (feed per revolution), en pulg/rev o mm/rev. Fr: velocidad de avance lineal del huso, en pulg/min o mm/ min.
8.3. Fresado El fresado es una operación de maquinado en la cual se hace pasar una parte de trabajo enfrente de una herramienta cilíndrica rotatoria con múltiples bordes o filos cortantes. El eje de rotación de la herramienta de corte es perpendicular a la dirección de avance. La herramienta de corte en el fresado se llama fresa o cortador para fresadora y los bordes cortantes se llaman dientes. La máquina herramienta que ejecuta esta operación es una fresadora.
Como en las máquinas anteriores la velocidad de rotación y la velocidad de corte se relacionan mediante:
V c =^ π^ ⋅ 12 D S⋅ [ sfpm]
S: velocidad de rotación del huso, [RPM]. Vc: velocidad de corte, [sfpm] D: diámetro exterior de la fresa en pulgadas.
El avance por revolución (F) en fresado se determina a partir del avance por diente cortante, llamado chip load, y el número de dientes por revolución:
En dónde ndientes es número de dientes por revolución (en unidades [dientes/revolución]), y el chip load es el grosor del material de viruta que cada filo de corte