
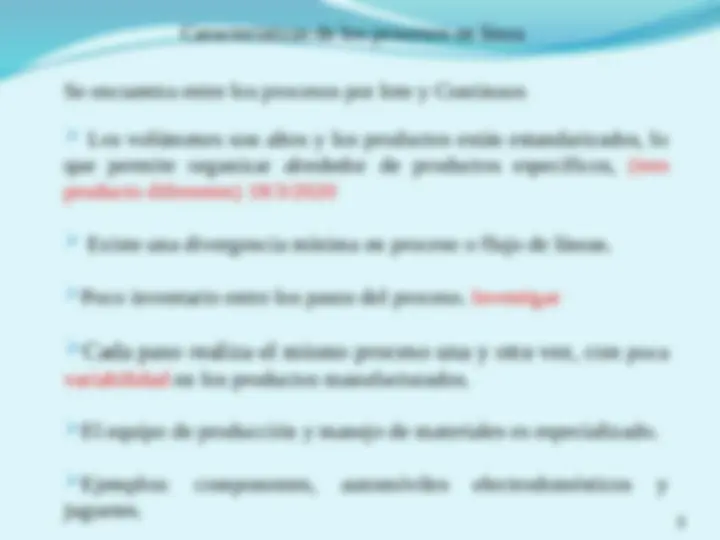
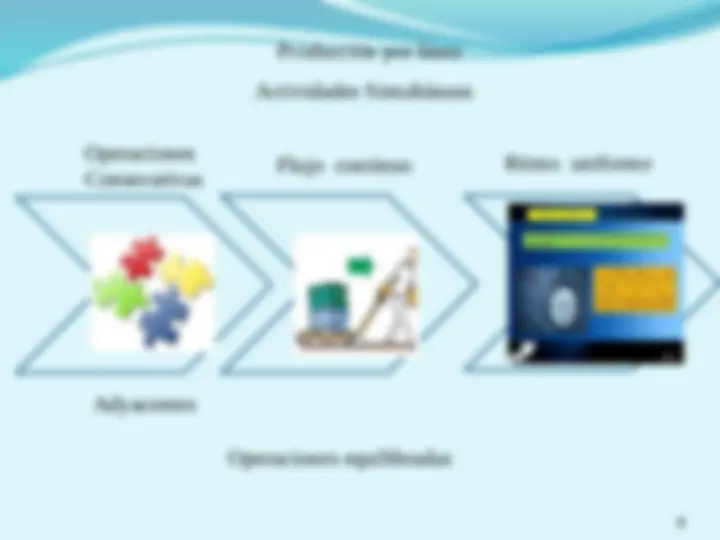
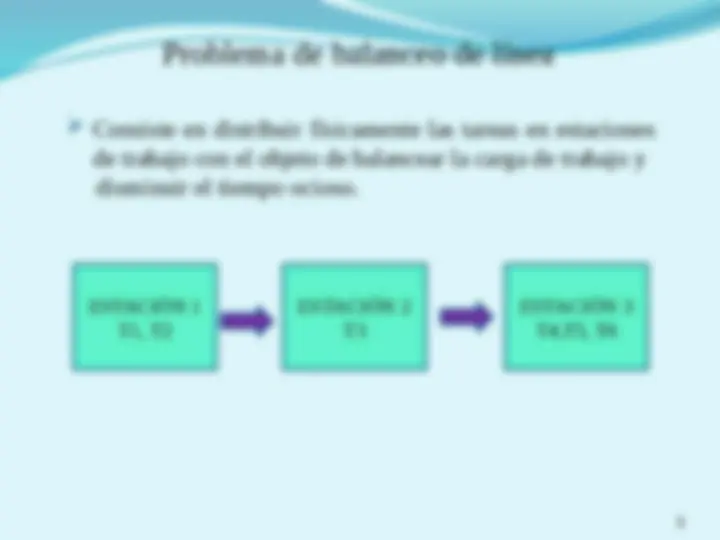
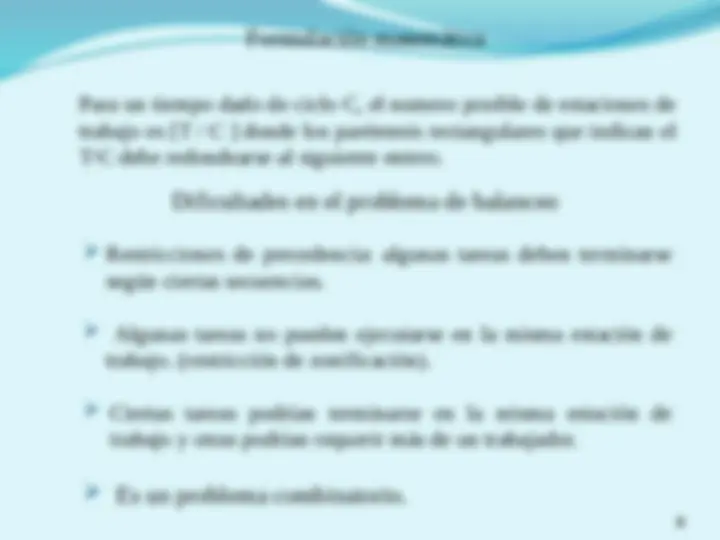
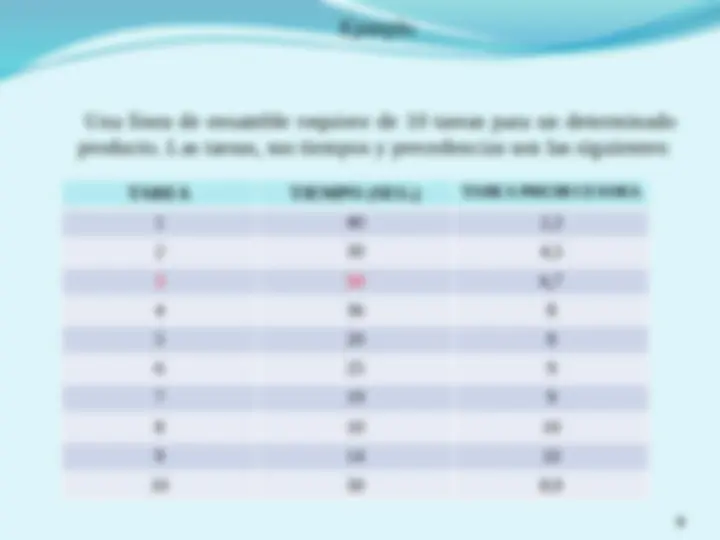
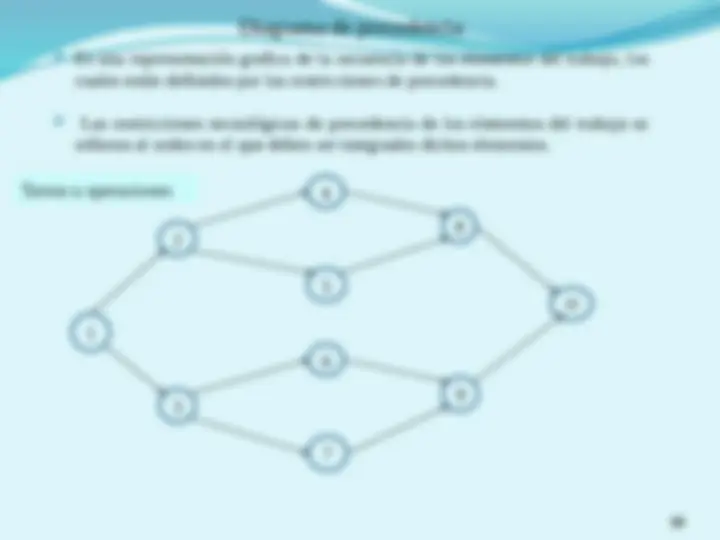
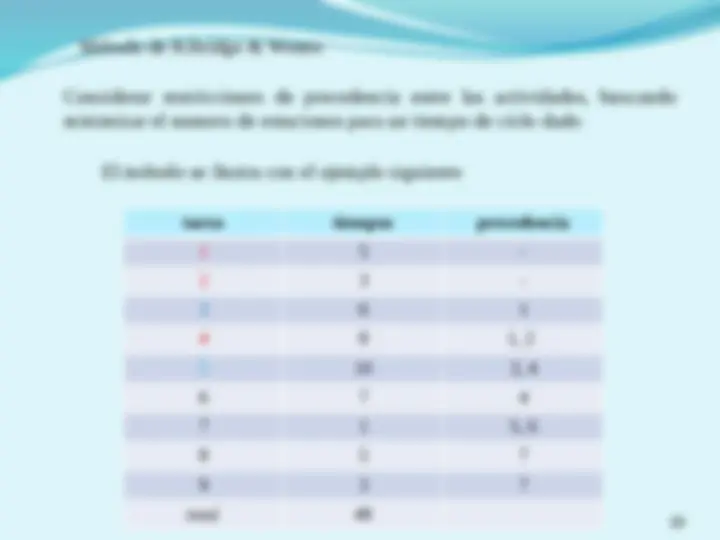
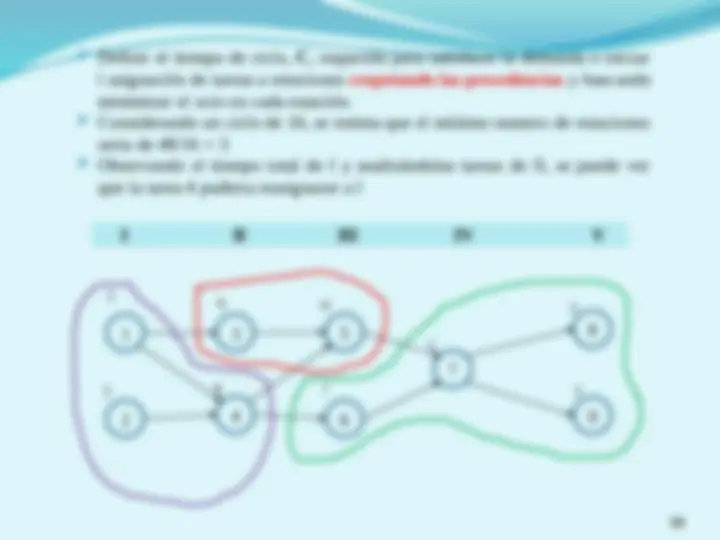
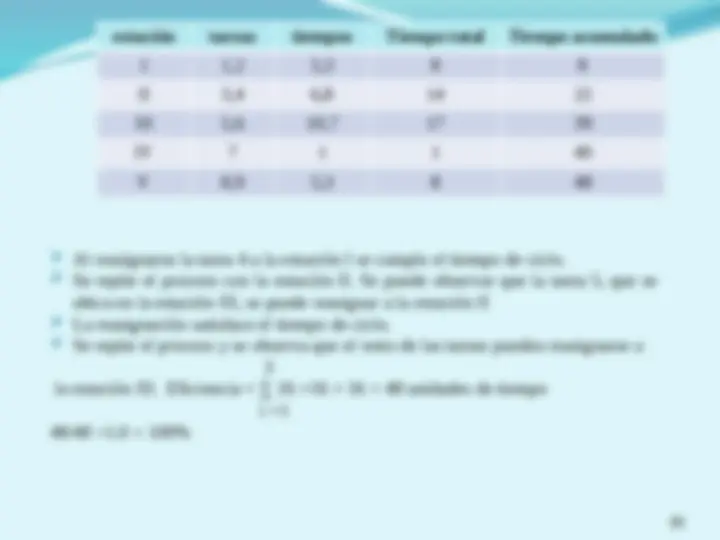
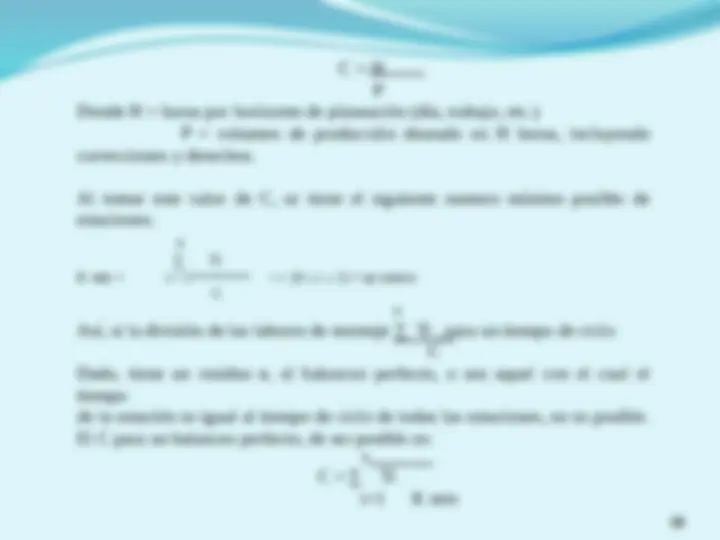
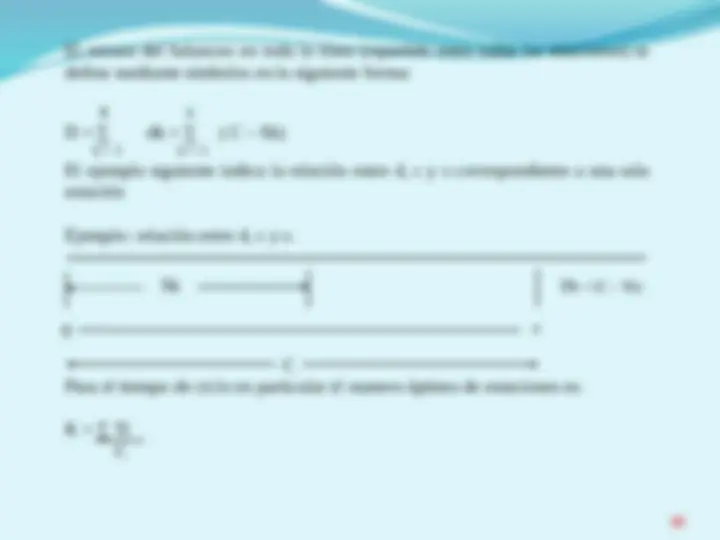
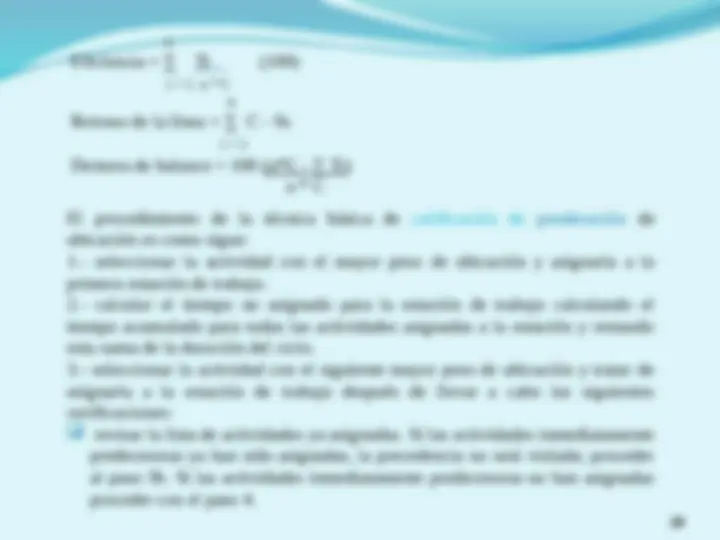
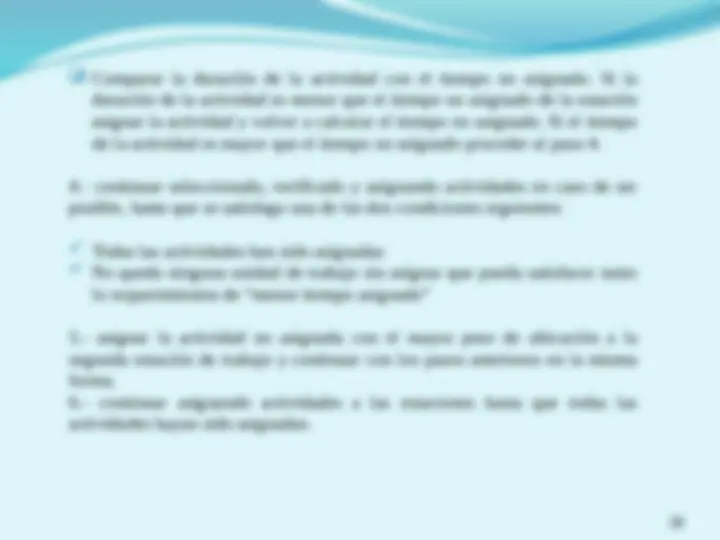
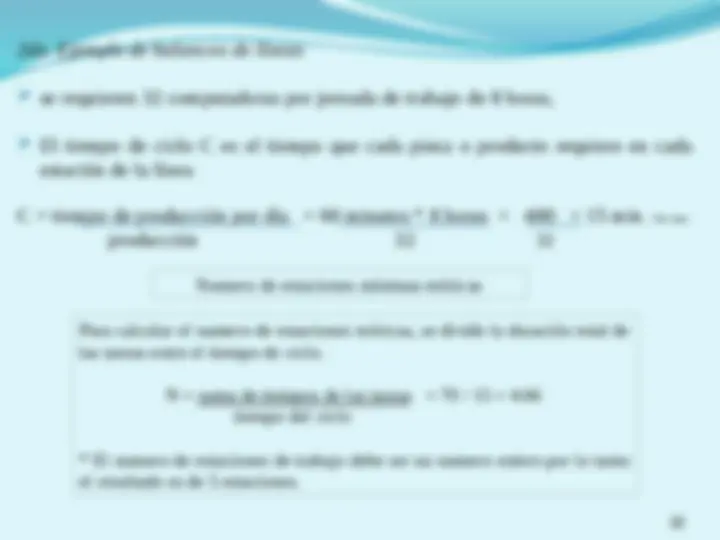
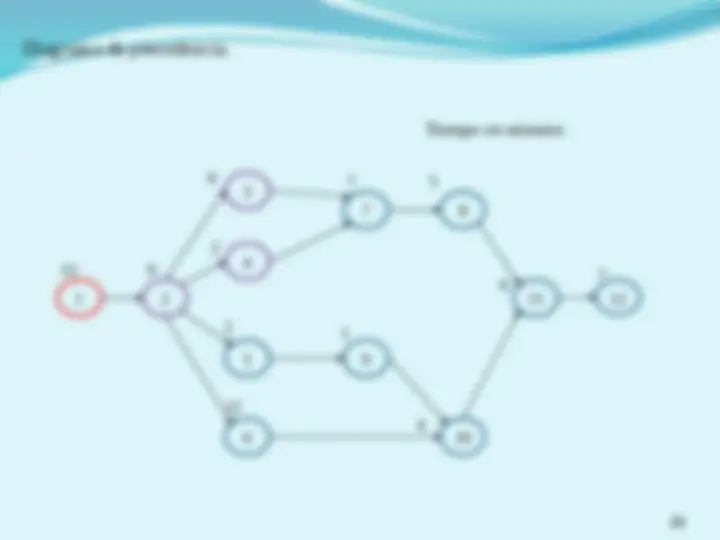
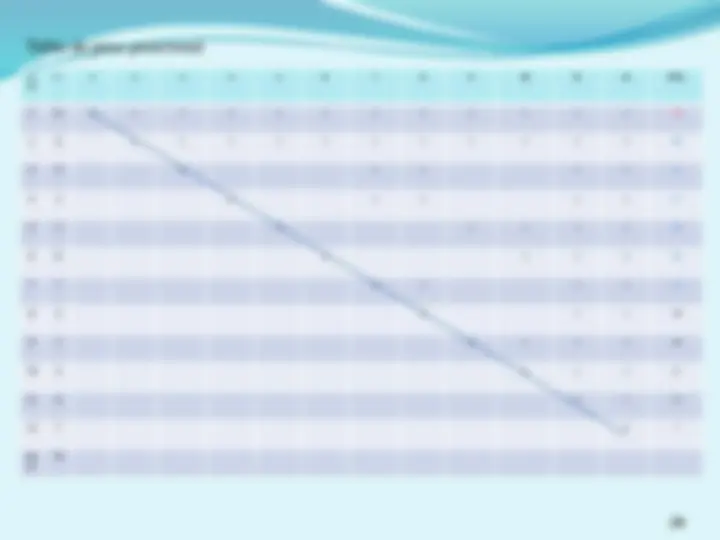
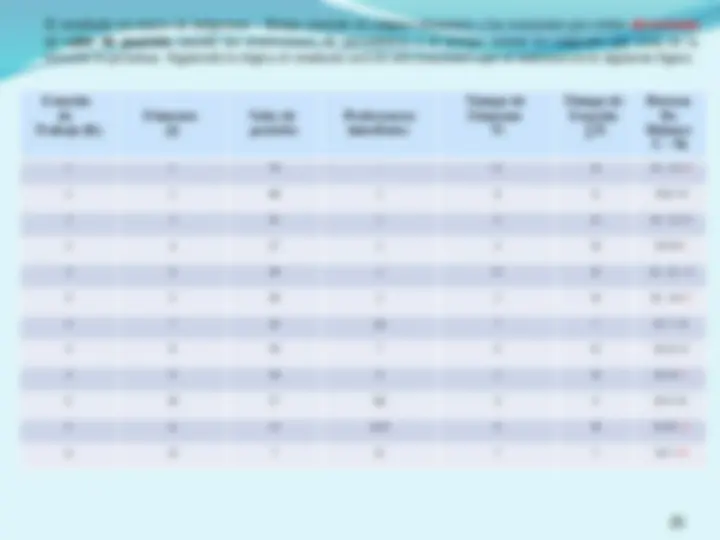
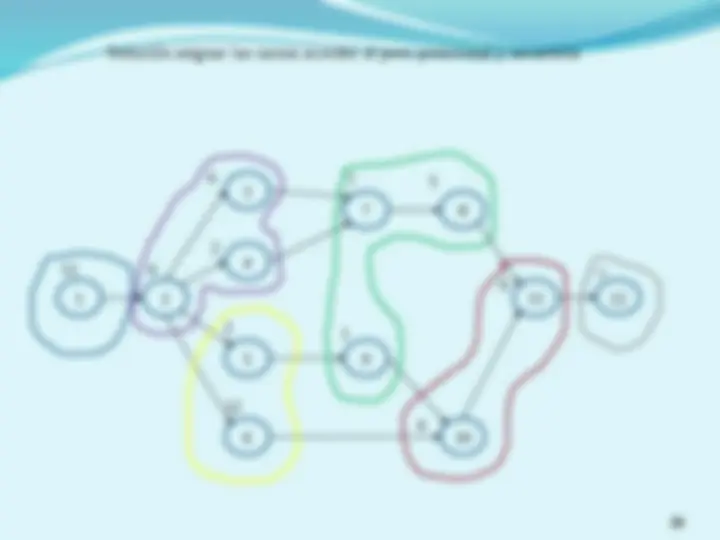
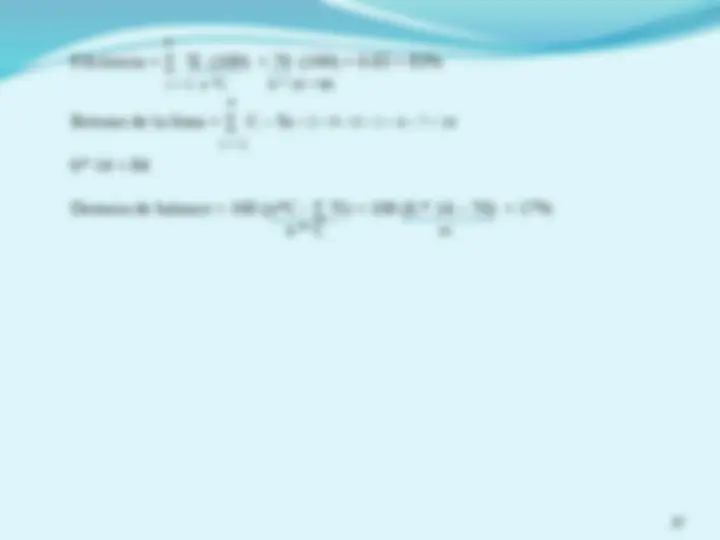
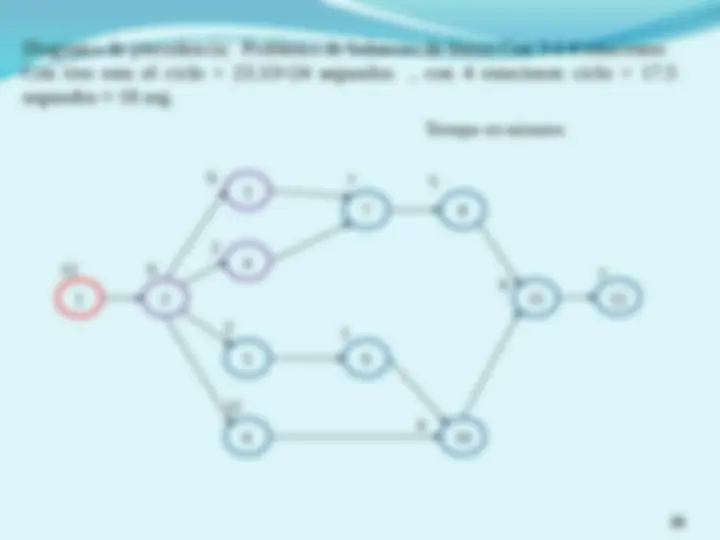
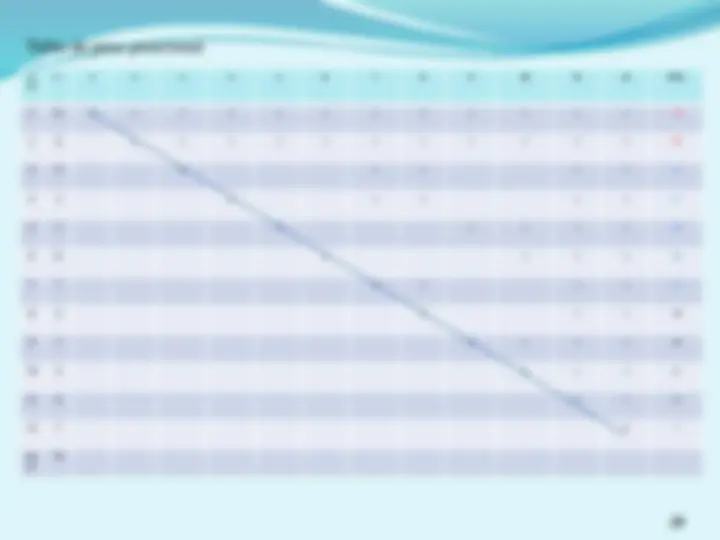
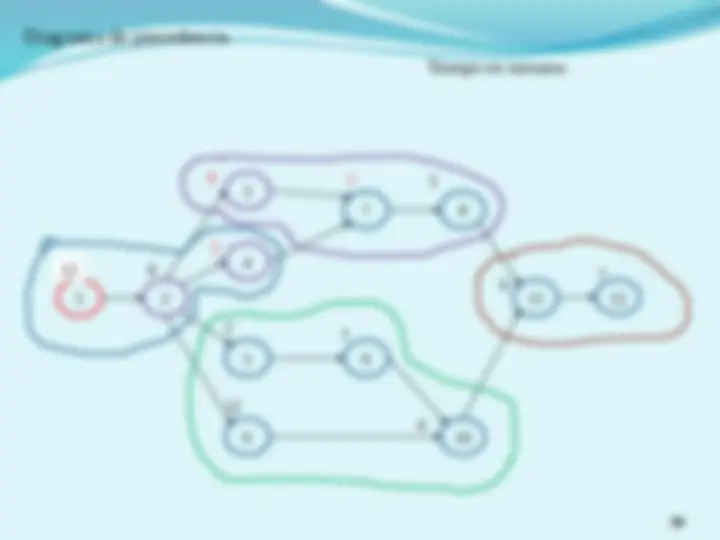
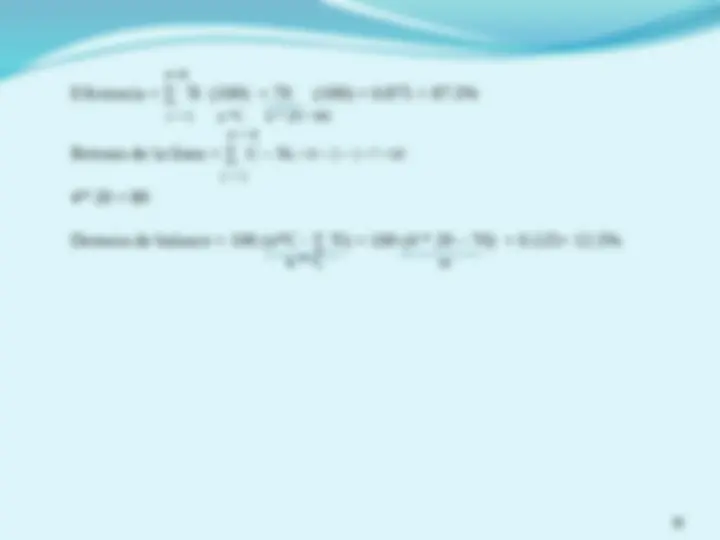
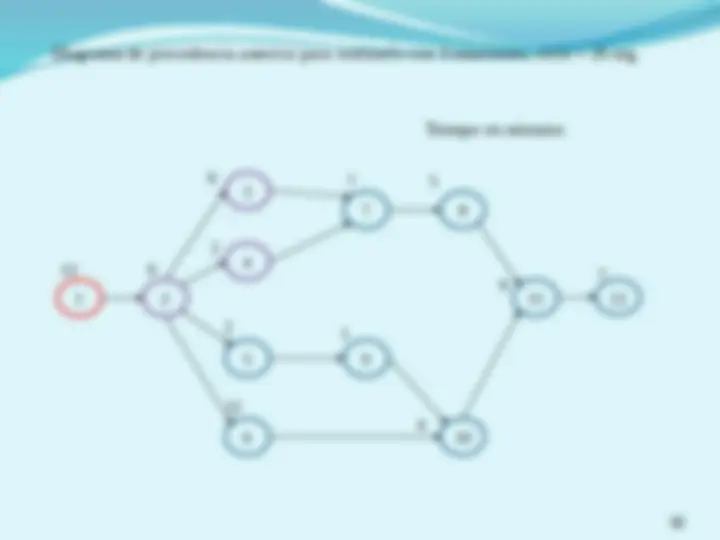
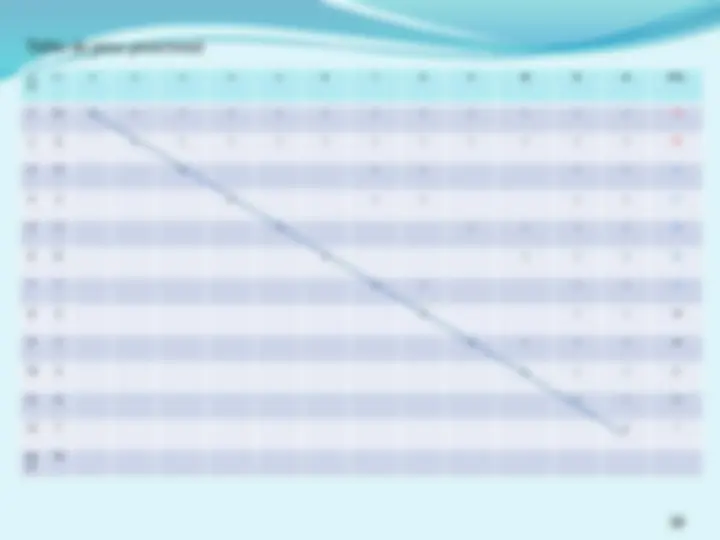
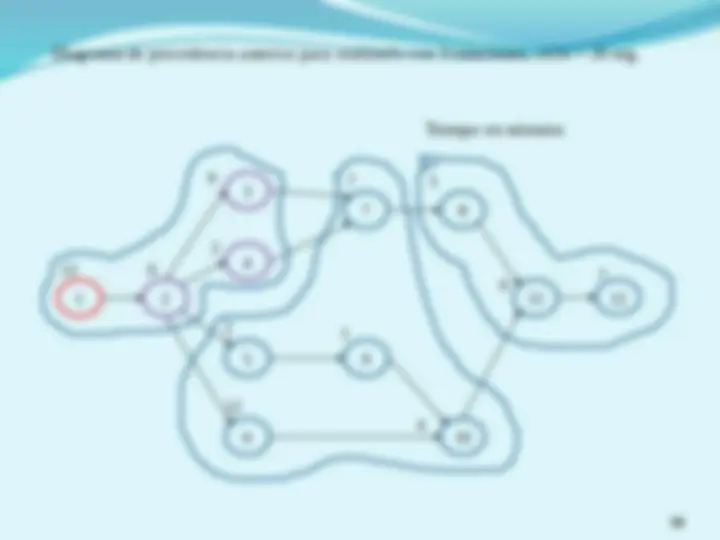
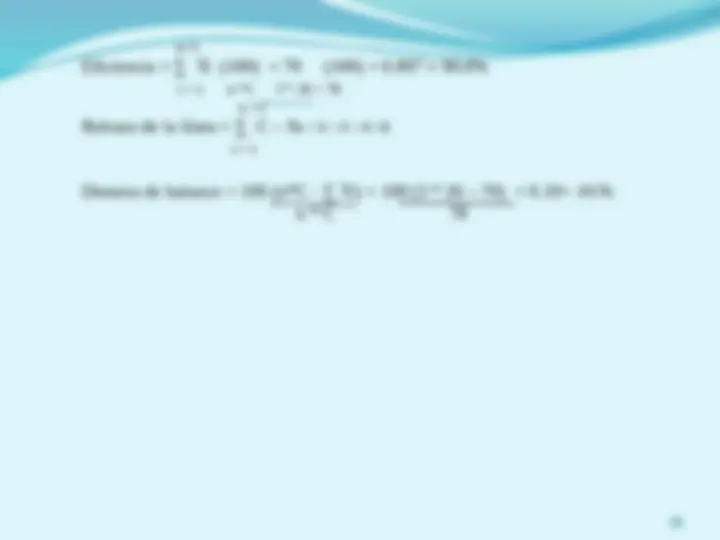
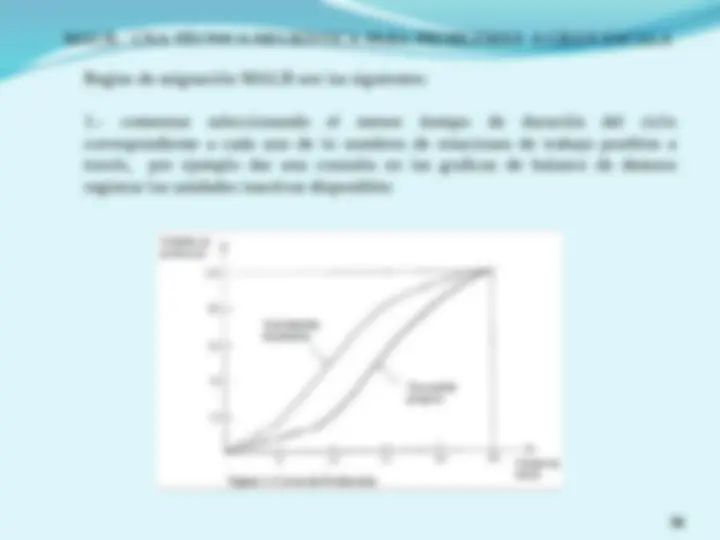
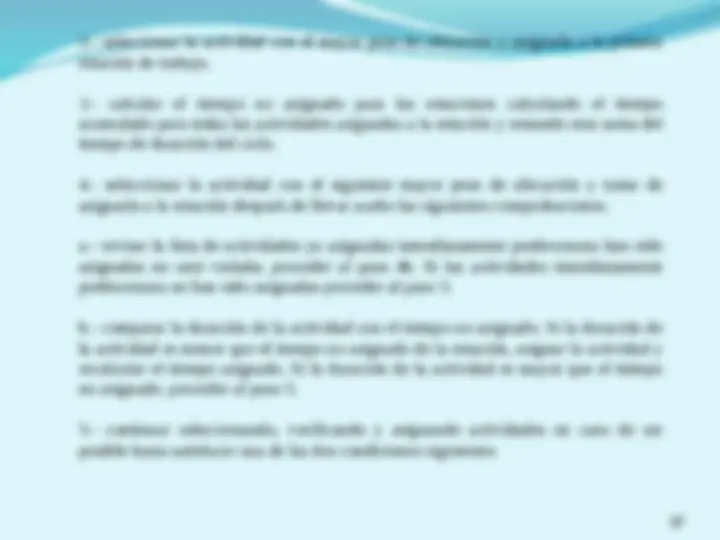
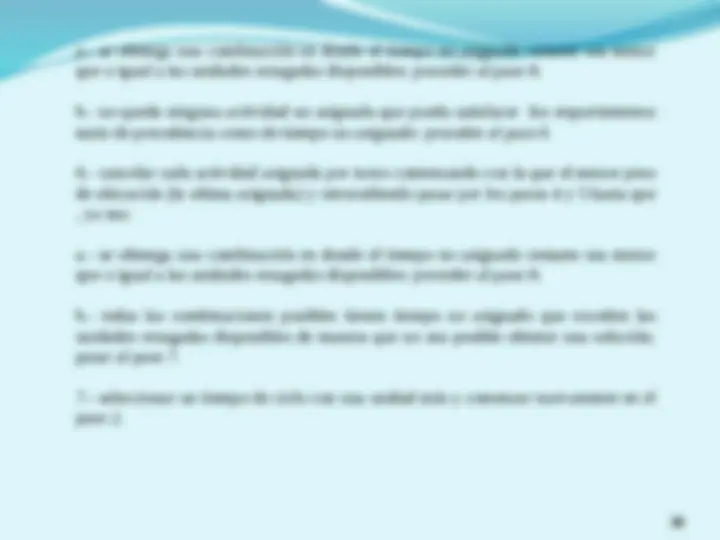
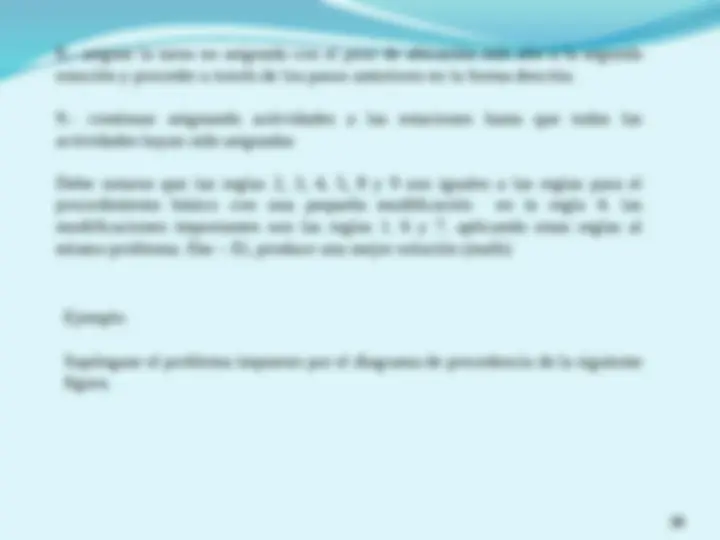
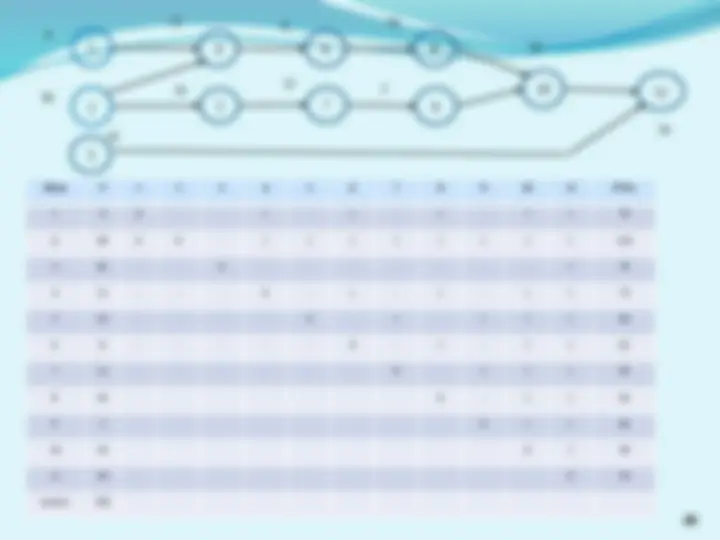
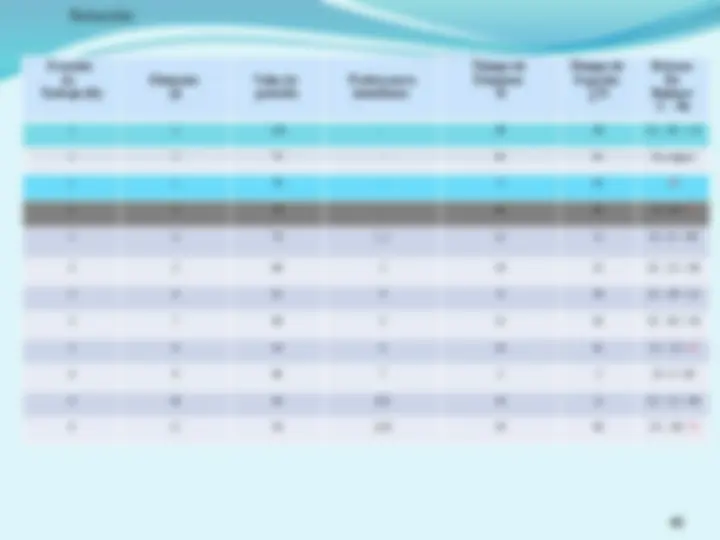
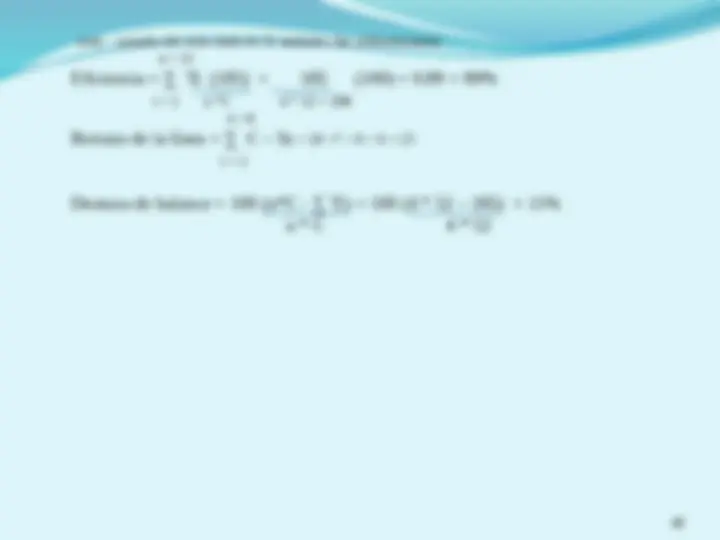
Prepara tus exámenes y mejora tus resultados gracias a la gran cantidad de recursos disponibles en Docsity
Gana puntos ayudando a otros estudiantes o consíguelos activando un Plan Premium
Prepara tus exámenes
Prepara tus exámenes y mejora tus resultados gracias a la gran cantidad de recursos disponibles en Docsity
Prepara tus exámenes con los documentos que comparten otros estudiantes como tú en Docsity
Los mejores documentos en venta realizados por estudiantes que han terminado sus estudios
Estudia con lecciones y exámenes resueltos basados en los programas académicos de las mejores universidades
Responde a preguntas de exámenes reales y pon a prueba tu preparación
Consigue puntos base para descargar
Gana puntos ayudando a otros estudiantes o consíguelos activando un Plan Premium
Comunidad
Pide ayuda a la comunidad y resuelve tus dudas de estudio
Descubre las mejores universidades de tu país según los usuarios de Docsity
Ebooks gratuitos
Descarga nuestras guías gratuitas sobre técnicas de estudio, métodos para controlar la ansiedad y consejos para la tesis preparadas por los tutores de Docsity
EL documento contiene apuntes sobre la materia estudio del trabajo
Tipo: Apuntes
1 / 42
Esta página no es visible en la vista previa
¡No te pierdas las partes importantes!
ESTUDIO DEL TRABAJO II
BALANCEO DE LÍNEA
Problema de balanceo de línea (^) Consiste en distribuir físicamente las tareas en estaciones de trabajo con el objeto de balancear la carga de trabajo y disminuir el tiempo ocioso.
n
i = 1
Formulación matemática
Dificultades en el problema de balanceo
(^) Es un problema combinatorio.
(^) Es una representación grafica de la secuencia de los elementos del trabajo, los cuales están definidos por las restricciones de precedencia. (^) Las restricciones tecnológicas de precedencia de los elementos del trabajo se refieren al orden en el que deben ser integrados dichos elementos. 1 2 3 4 5 6 7 8 9 10 Tareas u operaciones
Con diez estaciones (^) estaciones E1 E2 E3 E4 E5 E6 E7 E8 E9 E10 total 40 30 50 36 20 25 19 10 14 30 274 50 50 50 50 50 50 50 50 50 50 500 10 20 0 14 30 25 31 40 36 20 226 3 estaciones de trabajo 1 2 3 4 5 6 7 8 9 10 ESTACIÓN 1 ESTACIÓN 2 ESTACIÓN 3
tarea tiempos precedencia 1 5 - 2 3 - 3 6 1 4 8 1, 2 5 10 3, 4 6 7 4 7 1 5, 6 8 5 7 9 3 7 total 48
(^) Definir el tiempo de ciclo, C , requerido para satisfacer la demanda e iniciar l asignación de tareas a estaciones respetando las precedencias y buscando minimizar el ocio en cada estación. (^) Considerando un ciclo de 16, se estima que el mínimo numero de estaciones seria de 48/16 = 3 (^) Observando el tiempo total de I y analizándolas tareas de II, se puede ver que la tarea 4 pudiera reasignarse a I 1 2 3 4 5 6 7 8 9 I II III IV V 5 3 (^65) 8 10 7 1 3
estación tareas tiempos Tiempo total Tiempo acumulado I 1,2,4 5,3,8 16 16 II 3,5 6,10 16 32 III 6,7,8,9 7 7 39 IV 7 7,1,5,3 1 40 V 8,9 5,3 8 48 (^) La línea se balanceo optimizando la cantidad de estaciones y con un ocio de cero estación tareas tiempos Tiempo total Tiempo acumulado I 1,2,4 5,3,8 16 16 II 3,5 6,10 16 32 III 6,7,8,9 7,1,5,3 16 48
PARÁMETROS PARA MODELAR EL SISTEMA DE LÍNEA DE ENSAMBLE Para entender mejor el problema de la línea de ensamble (así como los procedimientos de balanceo con ayuda de la computadora), es necesario definir el problema por medio de símbolos. Con este propósito se presentan. C = tiempo de ciclo K = numero de estaciones de trabajo 1 ≤ k ≤ K i = numero de identificación del elemento de trabajo 1≤ i ≤ N Ti = valor de tiempo para el elemento trabajo i. Sk = cantidad de tiempo asignado a la estación k Dk = retraso (tiempo ocioso) en la estación k D = retraso del balanceo en toda la línea de ensamble El tiempo ocioso del ciclo define el ritmo con el cual salen los productos ensamblados por el extremo de la línea de ensamble. Es también el máximo durante el producto que se ensambla progresivamente esta a disposición de una estación mientras pasa frente a ella. Dado un producto que se va a ensamblar sobre una línea transportadora. El tiempo de ciclo se puede determinar de esta manera
El retraso del balanceo en toda la línea (repartido entre todas las estaciones) se define mediante símbolos en la siguiente forma: K k D = ∑ dk = ∑ ( C – Sk) k = 1 k = 1 El ejemplo siguiente indica la relación entre d, c y s correspondiente a una sola estación Ejemplo: relación entre d, c y s. Para el tiempo de ciclo en particular el numero óptimo de estaciones es: K = ∑ Ti C Sk Dk = (C – Sk) 0 c C
n Eficiencia = ∑ Ti (100) i = 1 n * C n Retraso de la línea = ∑ C - Sk i = 1 Demora de balance = 100 (n*C - ∑ Ti) n * C El procedimiento de la técnica básica de calificación de ponderación de ubicación es como sigue: 1.- seleccionar la actividad con el mayor peso de ubicación y asignarla a la primera estación de trabajo. 2.- calcular el tiempo no asignado para la estación de trabajo calculando el tiempo acumulado para todas las actividades asignadas a la estación y restando esta suma de la duración del ciclo. 3.- seleccionar la actividad con el siguiente mayor peso de ubicación y tratar de asignarla a la estación de trabajo después de llevar a cabo las siguientes verificaciones: (^) revisar la lista de actividades ya asignadas. Si las actividades inmediatamente predecesoras ya han sido asignadas, la precedencia no será violada; proceder al paso 3b. Si las actividades inmediatamente predecesoras no han asignadas proceder con el paso 4.