
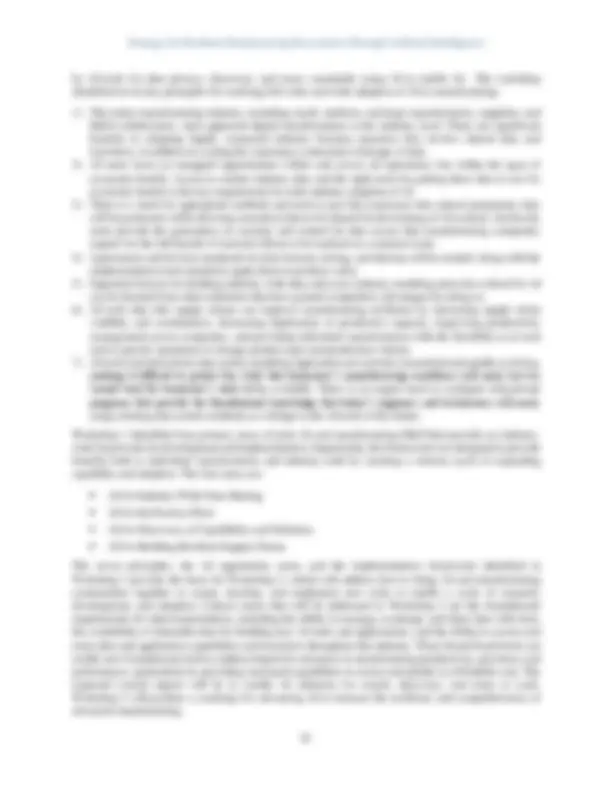
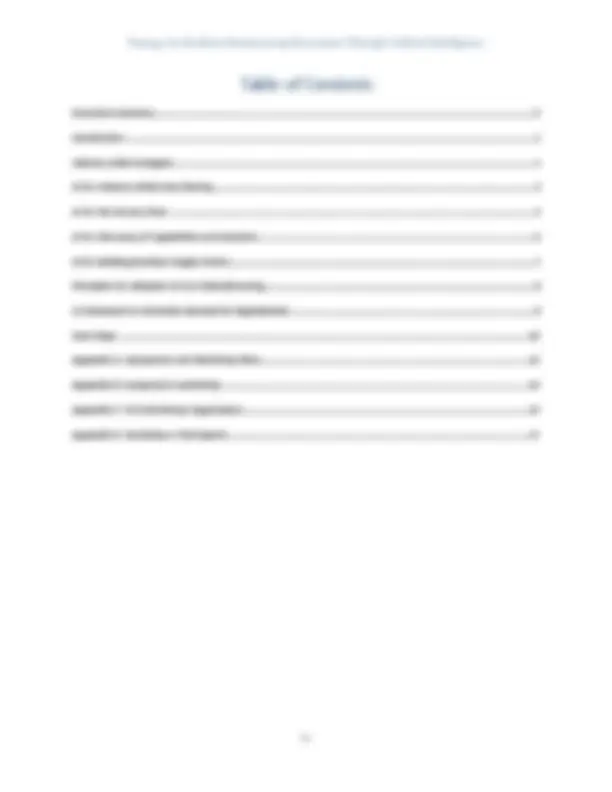
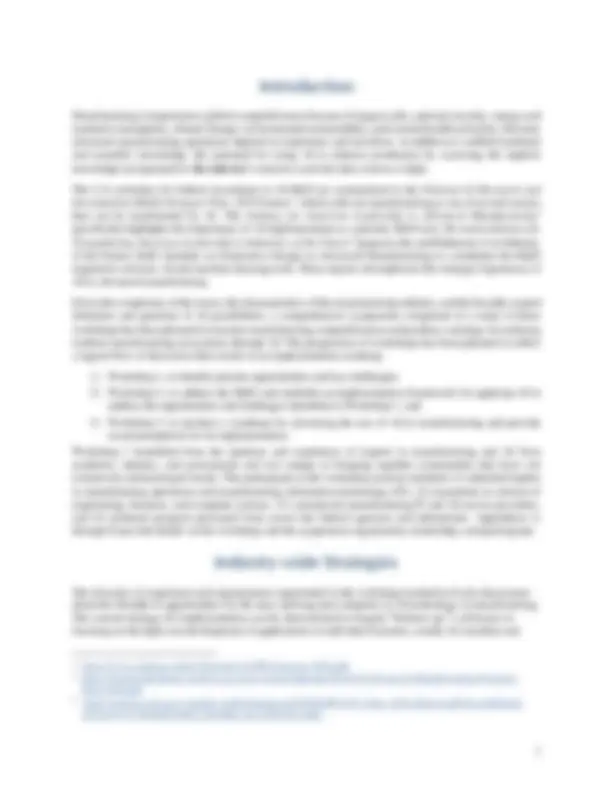
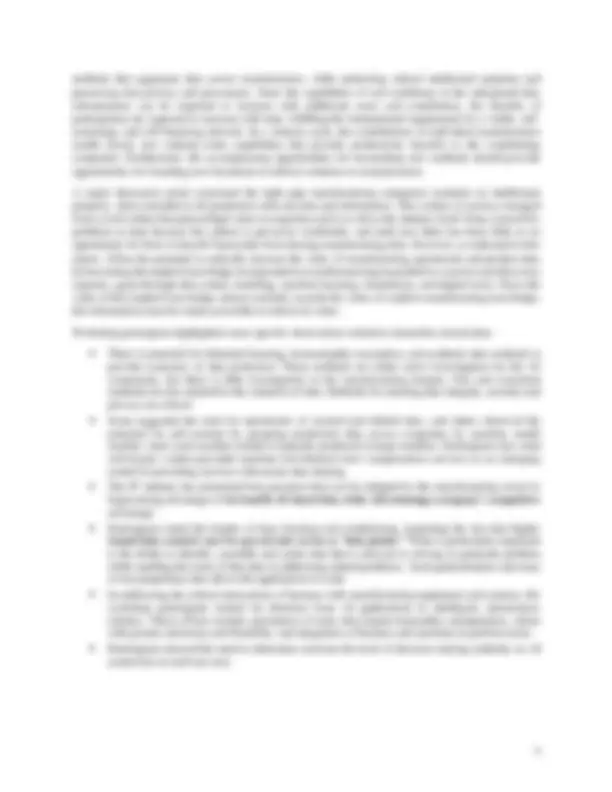
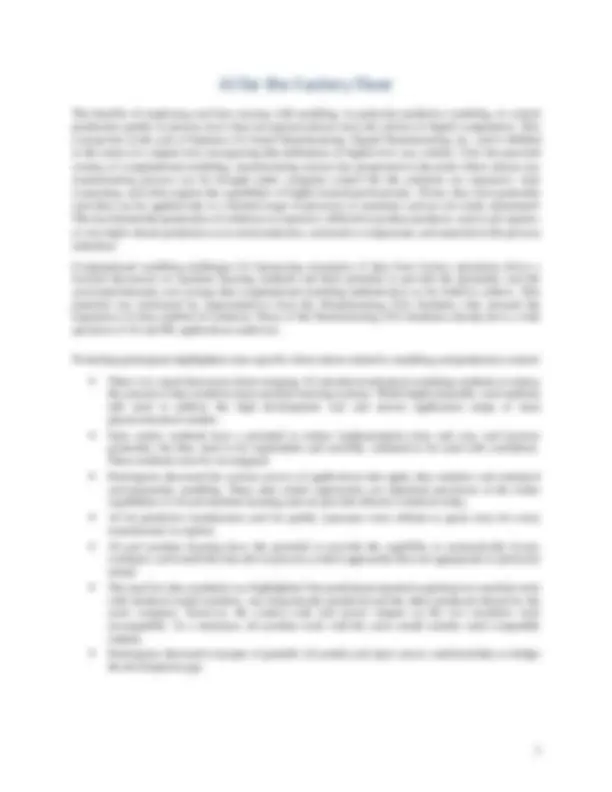
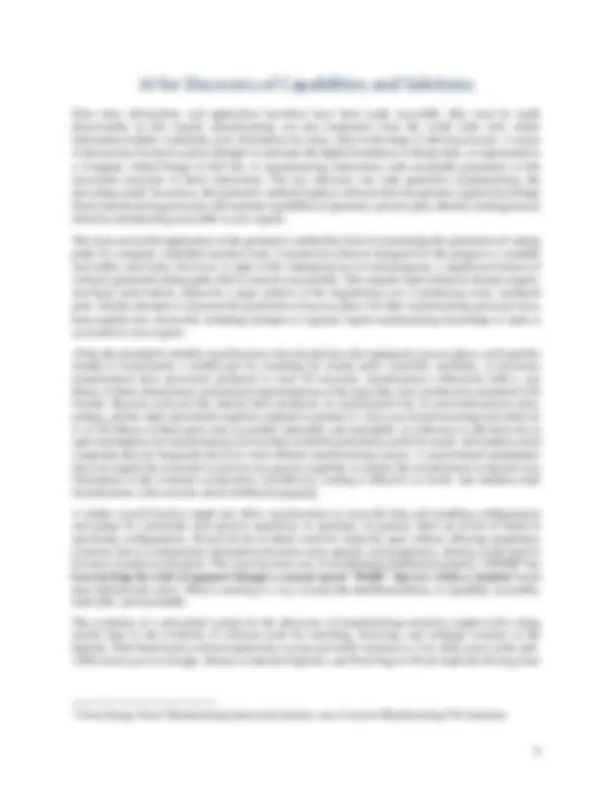
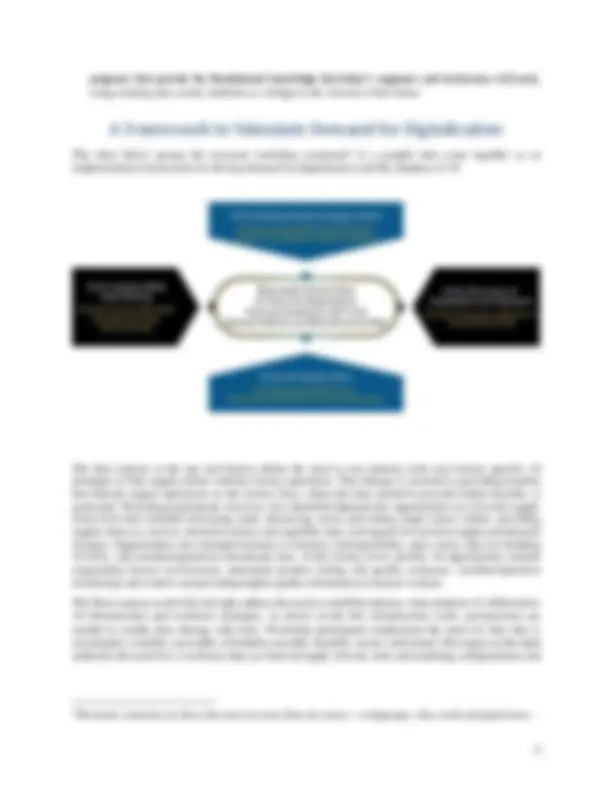
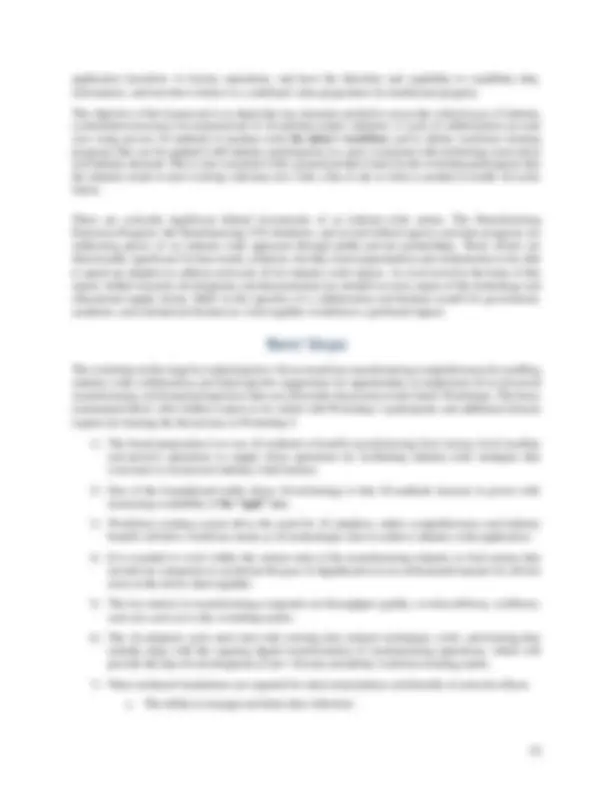
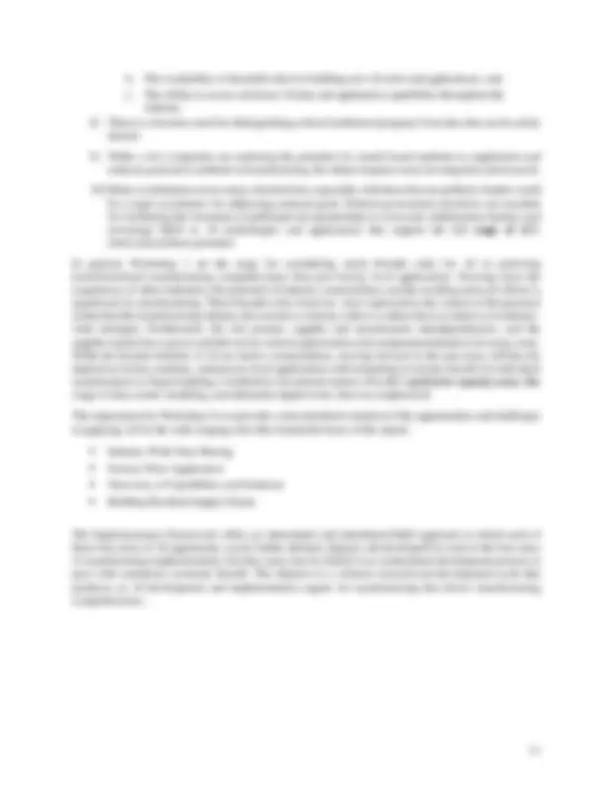
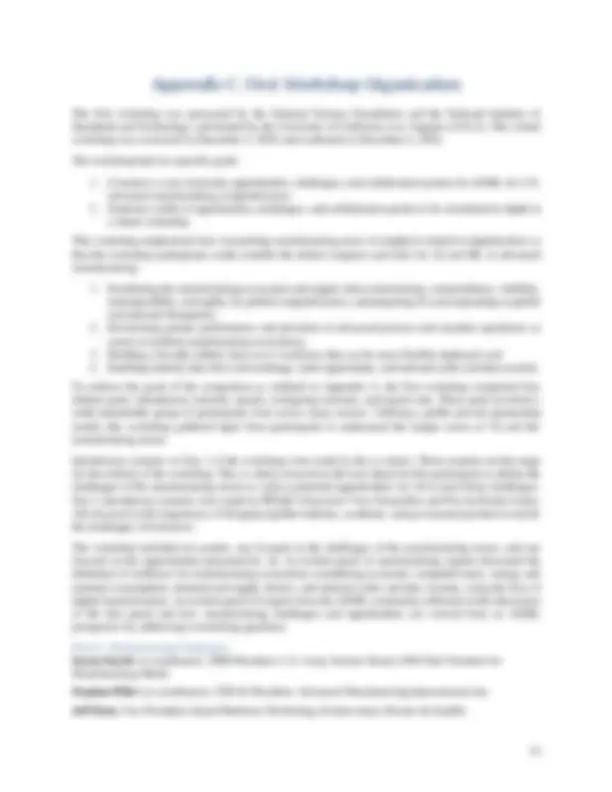
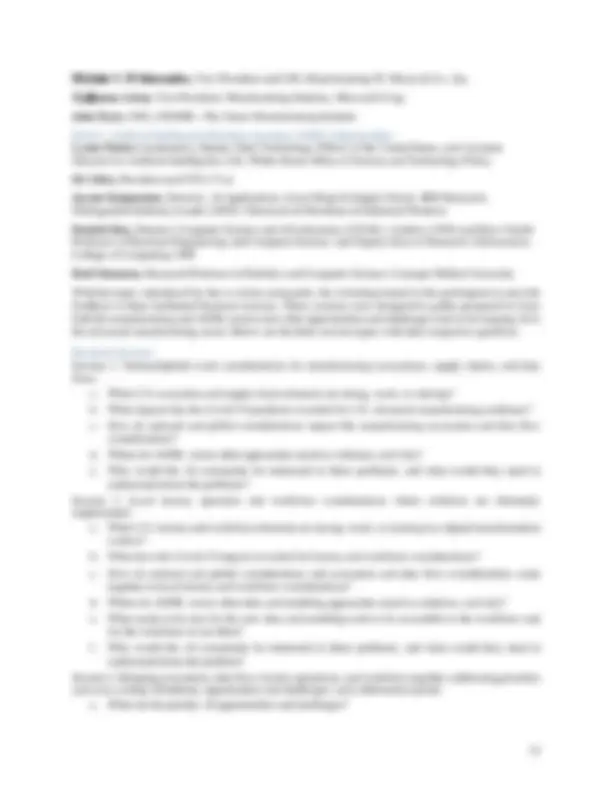
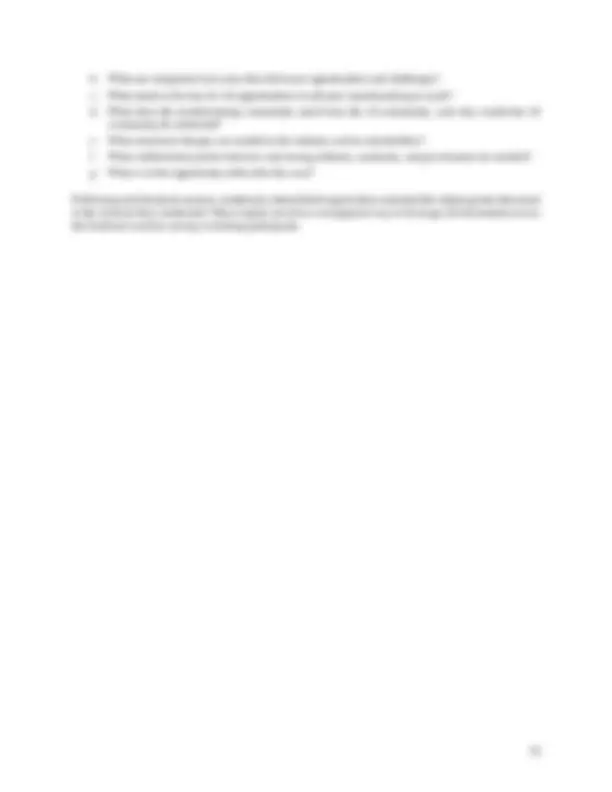
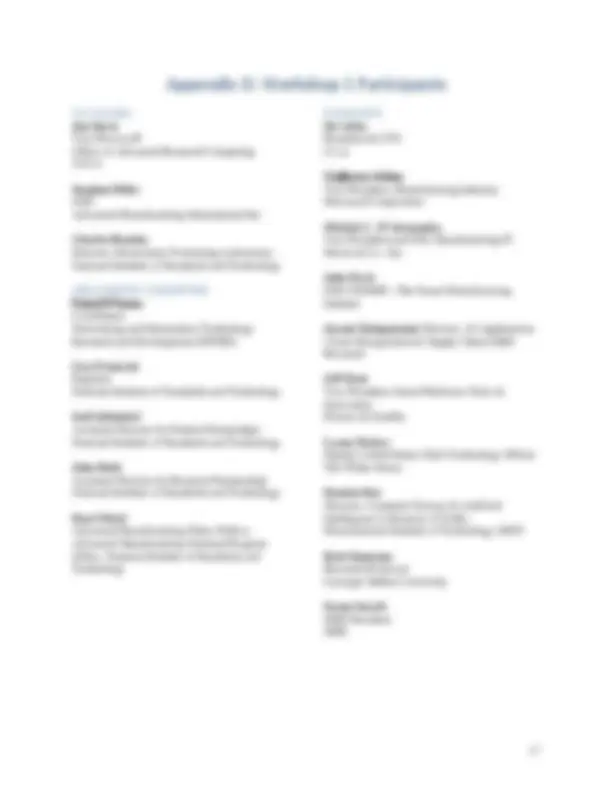
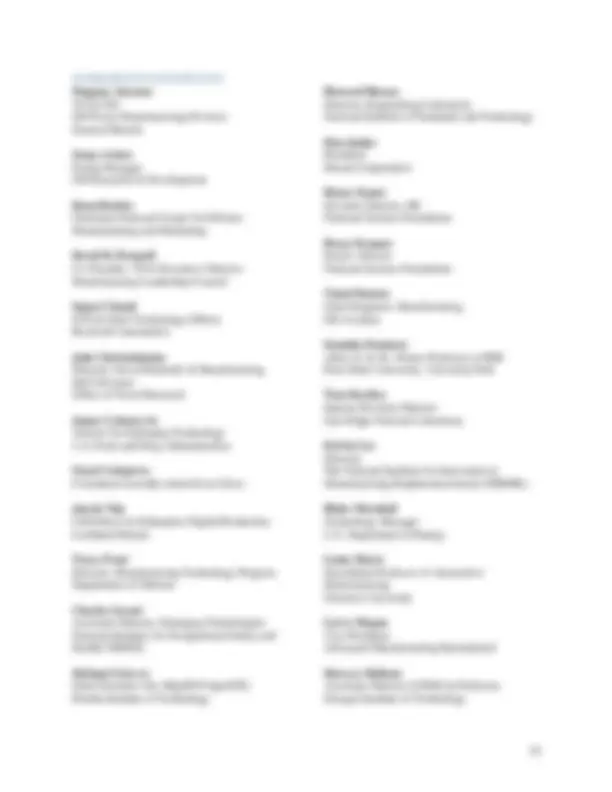
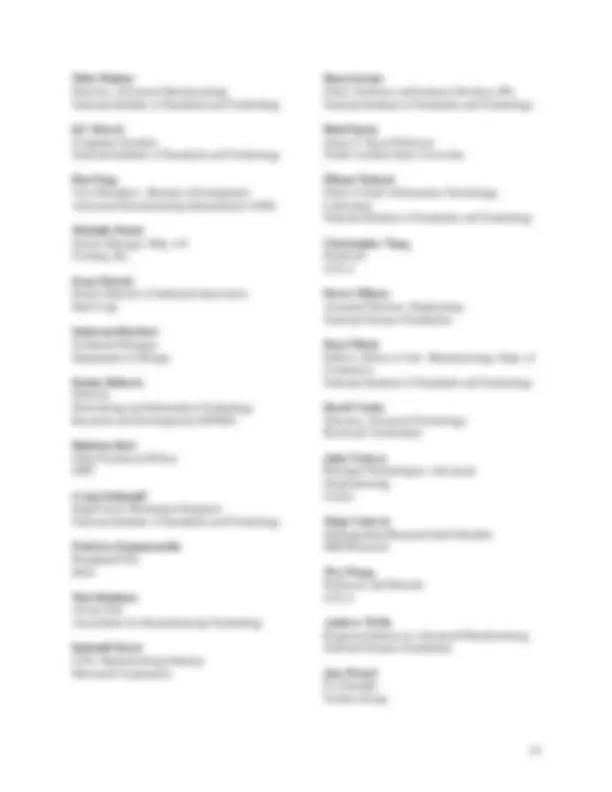
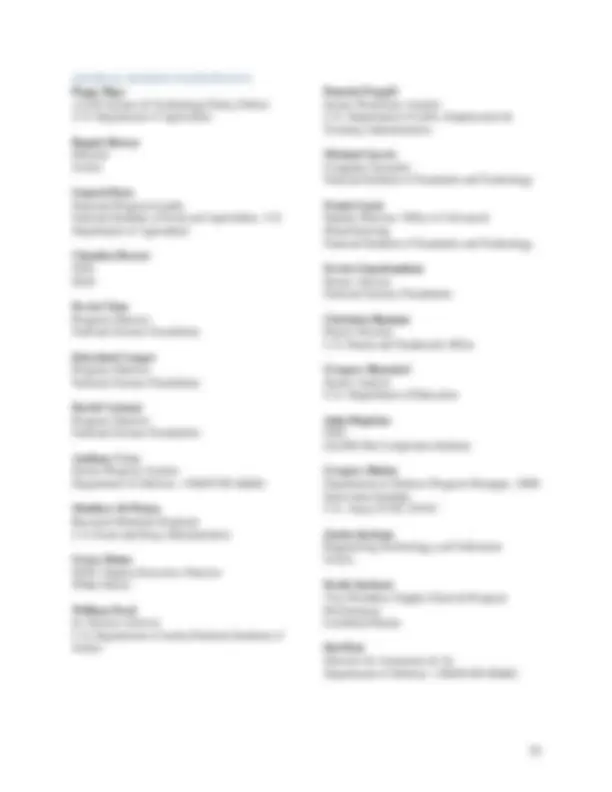
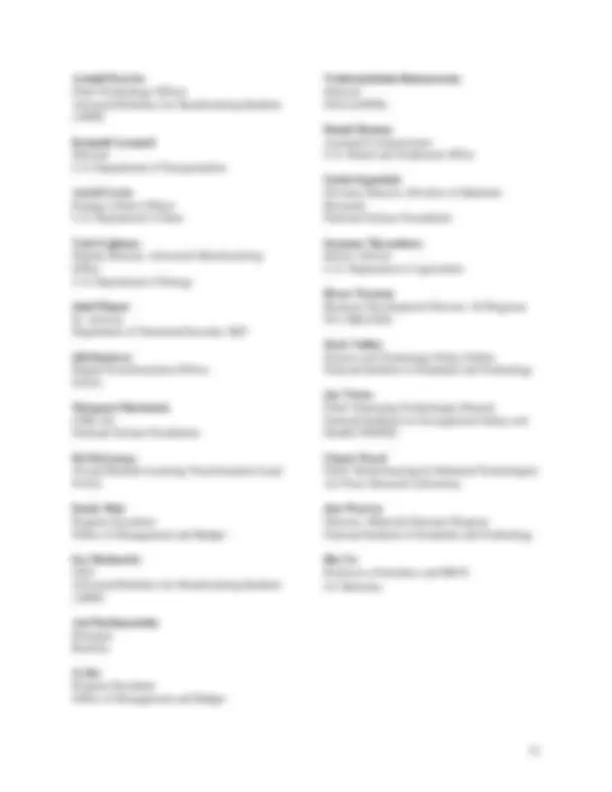
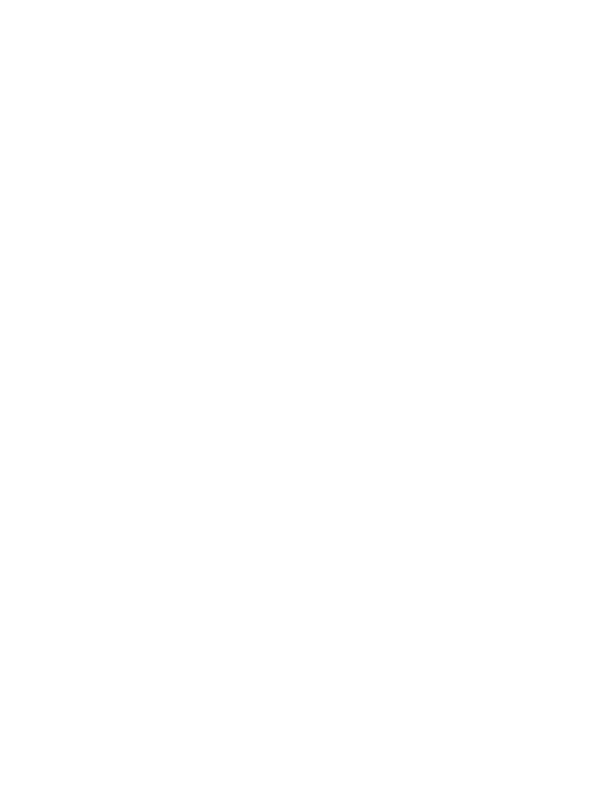
Study with the several resources on Docsity
Earn points by helping other students or get them with a premium plan
Prepare for your exams
Study with the several resources on Docsity
Earn points to download
Earn points by helping other students or get them with a premium plan
Community
Ask the community for help and clear up your study doubts
Discover the best universities in your country according to Docsity users
Free resources
Download our free guides on studying techniques, anxiety management strategies, and thesis advice from Docsity tutors
Artificial Intelligence (AI) refers to a rich spectrum of data and knowledge driven technologies that have collectively taken on a “silver bullet” status in ...
Typology: Exercises
1 / 26
This page cannot be seen from the preview
Don't miss anything!
Strategy for Resilient Manufacturing Ecosystems Through Artificial Intelligence i
Aligning Artificial Intelligence and U.S. Advanced Manufacturing Competitiveness
Symposium: Strategy for Resilient Manufacturing Ecosystems Through Artificial Intelligence
Strategy for Resilient Manufacturing Ecosystems Through Artificial Intelligence ii
Artificial Intelligence (AI) refers to a rich spectrum of data and knowledge driven technologies that have collectively taken on a “silver bullet” status in many countries, including the United States. A global competition is underway to achieve economic leadership through the development and application of AI technologies in key industries, often supported by large government investments. The U.S. priorities for federal investment in AI R&D are summarized in several reports from government agencies. These reports highlight the strategic importance of AI in advanced manufacturing, but they do not present a broad, actionable strategy for applying AI in the manufacturing industry. In building on these previous reports, the National Science Foundation (NSF) and the National Institute of Standards and Technology (NIST) have sponsored a symposium titled the “Strategy for Resilient Manufacturing Ecosystems Through Artificial Intelligence.” The symposium will define opportunities for leveraging AI in the U.S. advanced manufacturing sector and has been organized into a series of three workshops. The first workshop (Workshop 1), “Aligning Artificial Intelligence and U.S. Advanced Manufacturing Competitiveness,” was held on December 2 and 4, 2020. This workshop was unique in bringing together experts in advanced manufacturing, AI, IT, and computer science from industry, universities, federal agencies, and national laboratories. Workshop participants were enthusiastic about both the near term and long term benefits of applying AI to manufacturing. These included far better use of industry data and scaled use of domain knowlege throughout the industry, noting that AI is not a replacement for domain knowledge. They identified priority opportunities, challenges, and collaboration points for accelerating the implementation of AI in manufacturing, and used the span of economic value as the topmost driver – market share, productivity, energy and material consumption, national security, and climate, environmental, and ecosystem impacts. A key observation was that manufacturing has derived little benefit from the network effects that have transformed other industries, even though the potential is high for AI , machine learning, predictive modeling, and networked data centric analytics and solutions to enable such a transformation. In assessing AI in manufacturing, it was noted that current AI applications are almost exclusively for machine and operational units, i.e., component levels within individual company operations, and rarely extend to line operations, intracompany systems, or intercompany supply chains. This fact focused workshop discussions on the transformational opportunities afforded by the application of AI methods and tools to support manufacturing operations beyond the component level. The participants stressed that, with broad industry adoption, AI and machine learning systems have the potential to transform the prevailing manufacturing business model, which emphasizes the proprietary nature of data. This transformation, which is essential for the successful implementation of AI solutions, can also be enabled Artificial Intelligence (AI) in manufacturing refers to software systems that can recognize, simulate, predict, and optimize situations, operating conditions, and material properties for human and machine action. Machine Learning (generally seen as a subset of AI) refers to algorithms that use prior data to accurately identify current state and predict future state, with the goal of improving productivity, precision, and performance. Networking creates digital connections among devices, machines, equipment, databases, computer programs, and users, to provide the connectedness needed to exchange information, make decisions, and take actions. Predictive Modeling is the use of data, AI, machine learning, simulation, and digital twins to assess, predict, and anticipate process, product, and operational behaviors for control, design, optimization, health, and failure prevention and mitigation. Network Effects produce increased benefits for network users as the number of connected user nodes increases by expanding the availability of information and knowledge accessible to all.
iv
Manufacturing is important to global competitiveness because it impacts jobs, national security, energy and material consumption, climate change, environmental sustainability, and societal health and safety. Because advanced manufacturing operations depend on experience and knowhow, in addition to codified technical and scientific knowledge, the potential for using AI to enhance production by accessing the implicit knowledge incorporated in the industry’s extensive and rich data sources is high. The U.S. priorities for federal investment in AI R&D are summarized in the National AI Research and Development (R&D) Strategic Plan, 201 9 Update,^1 which calls out manufacturing as one of several sectors that can be transformed by AI. The Strategy for American Leadership in Advanced Manufacturing^2 specifically highlights the importance of AI implementation as a priority R&D area. Recommendations for Strengthening American Leadership in Industries of the Future^3 proposes the establishment of an Industry of the Future (IotF) Institute on Generative Design in Advanced Manufacturing to coordinate the R&D required to advance AI and machine learning tools. These reports all emphasize the strategic importance of AI in advanced manufacturing. Given the complexity of the issues, the characteristics of the manufacturing industry, and the broadly scoped definition and spectrum of AI possibilities, a comprehensive symposium comprised of a series of three workshops has been planned to examine manufacturing competitiveness and produce a strategy for realizing resilient manufacturing ecosystems through AI. The progression of workshops has been planned to reflect a logical flow of discussion that results in an implementation roadmap:
The diversity of experience and organizations represented in the workshop resulted in lively discussions about the breadth of opportunities for the near and long term adoption of AI technology in manufacturing. The current strategy for implementation can be characterized as largely “bottoms up,” a reference to focusing on the high cost development of applications in individual factories, mostly for machine and (^1) https://www.nitrd.gov/pubs/National-AI-RD-Strategy-2019.pdf (^2) https://trumpwhitehouse.archives.gov/wp-content/uploads/2018/10/Advanced-Manufacturing-Strategic- Plan-2018.pdf (^3) https://science.osti.gov/-/media/_/pdf/about/pcast/202006/PCAST_June_2020_Report.pdf?la=en&hash= 019A4F17C79FDEE5005C51D3D6CAC81FB31E3ABC
adoption, from factories to supply chains, will be driven by cost, with the cost of acquiring a workforce that can implement the tools an important factor. It is important to note that the benefits derived from industry-wide actions can enable vastly increased opportunities for the small and medium size businesses that constitute about 98% of all U.S. manufacturers. In this regard, it is likely that different innovations initially will provide benefits to different segments of the industry and sizes of companies. Just as the early adopters of web-based commerce were small businesses that tolerated quirky software to gain market access, new AI tools may allow small manufacturers to acquire new customers outside established supply chains and small companies to source manufacturing services domestically. The consideration of industry-wide AI strategies also stimulated significant discussion on cultural and educational barriers to AI adoption. In manufacturing, legacy practices, cultures, real and perceived risks, and a lack of transparency and trust are challenges to expanding the role of AI that are at least as great as the technical challenges. Discussions centered on the potential for homomorphic encryption, federated learning, and synthetic data methods to provide access to data needed for machine learning without revealing sensitive trade secrets or production status information. These methods are active areas of AI research that should be expanded to include manufacturing relevant applications. Business sensitive data i.e proprietary data, needs to be identified and separated from data about commonly used machines, operations, processes, and materials that can be safely and securely shared only with the intended recipient. Finally, there is a need for applications and associated industry datasets to be identified and prioritized and to make the relevant data from these available to university researchers who can more robustly research and develop new AI, machine learning, predictive, and networked modeling methods. It is instructive to draw an analogy with the annual ImageNet competition, which made several million labeled images publicly available to researchers. A competitor in the 2012 edition featured the advent of deep learning, which smashed every previous record for image identification and ushered in the age of commercial machine learning. Finally, and importantly, implementation of AI in manufacturing requires a dramatically expanded and technologically capable advanced manufacturing workforce, but AI tools are rapidly evolving, making it difficult to predict the skills that tomorrow’s manufacturing workforce will need. History has shown that it is impossible for workforce training to drive technology adoption. Rather, benefits to individual companies will drive workforce needs as companies adopting AI technologies accrue accelerating advantages. It is in this context of technology adoption that the workforce is tied to an industry-wide strategy. Just as a shortage of HTML programmers did not prove to be an impediment to the explosive growth of the Internet and web based commerce, an AI based economy is expected to grow and accelerate with the development of accessible tools and methods that enable the application of AI by non-specialists at dramatically reduced costs.
The manufacturing sector generates more measured, observational, operational, modeled and experience- based data than any other sector of the economy, even surpassing the financial sector. These data offer an industry base that could be contextualized and made available to enable radical innovations by AI in business practices, process engineering, product and system design, scalability, and sustainability, going far beyond improving the efficiency of manufacturing methods at individual sites. On the other hand, few companies generate enough of the right data internally to apply AI, even for narrowly focused applications on process or machine units. This contrast of a data rich industry with data poor individual manufacturers drove the conclusion that the entire manufacturing industry can benefit from innovative AI tools and
methods that aggregate data across manufacturers, while protecting critical intellectual property and preserving data privacy and provenance. Since the capabilities of and confidence in the anticipated data infrastructure can be expected to increase with additional users and contributors, the benefits of participation are expected to increase with time, fulfilling the fundamental requirement for a viable, self- sustaining, and self-financing network. In a virtuous cycle, the contributions of individual manufacturers enable broad, new industry-wide capabilities that provide productivity benefits to the contributing companies. Furthermore, the accompanying opportunities for researching new methods should provide opportunities for founding new businesses to deliver solutions to manufacturers. A major discussion point concerned the tight grip manufacturing companies maintain on intellectual property, often extended to all production relevant data and information. This culture of secrecy emerged from a craft culture that placed high value on expertise and is as old as the industry itself. It has caused few problems to date because the culture is pervasive worldwide, and until now there has been little or no opportunity for firms to benefit financially from sharing manufacturing data. However, as indicated in this report, AI has the potential to radically increase the value of manufacturing operational and product data by harvesting the implicit knowledge incorporated in it and harnessing its predictive, reactive and discovery capacity, again through data centric modeling, machine learning, simulations, and digital twins. Since the value of this implicit knowledge almost certainly exceeds the value of explicit manufacturing knowledge, this information must be made accessible to unlock its value. Workshop participants highlighted some specific observations related to shareable, trusted data:
Once data, information, and application knowhow have been made accessible, they must be made discoverable. In this regard, manufacturing can take inspiration from the world wide web, where information holders voluntarily post information for users, often in the hope of deriving income. A series of discussions focused on prior attempts to automate the digital translation of design data, as represented in a Computer Aided Design (CAD) file, to manufacturing instructions with acceptable guarantees on the successful execution of those instructions. The key reference was with generative manufacturing, the prevailing model. In essence, the generative method employs software that incorporates explicit knowledge about manufacturing processes and machine capabilities to generate a process plan, thereby making process selection and planning accessible to non-experts. The most successful application of the generative method has been in automating the generation of cutting paths for computer controlled machine tools. Commercial software designed for this purpose is available and widely used today. However, in spite of the widespread use of such programs, a significant fraction of software generated cutting paths fails to execute successfully. This requires intervention by human experts, and those interventions represent a major portion of the engineering cost of producing many machined parts. Similar attempts to automate the generation of process plans for other manufacturing processes have been notably less successful, including attempts to organize expert manufacturing knowledge to make it accessible to non-experts. AI has the potential to identify manufacturers who already have the equipment, process plans, and expertise needed to manufacture a needed part by searching for similar parts, materials, machines, or processes manufacturers have previously produced or used. Of necessity, manufacturers collectively hold a vast library of three dimensional, geometrical representations of the parts they have produced in standard CAD formats. Because each part has already been produced, its manufacturer has an associated process plan, tooling, and the other specialized expertise required to produce it. Like case-based reasoning and retrieval, if a CAD library of these parts were accessible, indexable, and searchable, it could serve as the basis for an open marketplace for manufacturing services that would be particularly useful for small- and medium-sized companies that are frequently driven to seek offshore manufacturing sources. A search-based marketplace does not require the customer to possess any process expertise or require the manufacturer to disclose any information to the customer except price and delivery, making it attractive to small- and medium-sized manufacturers with concerns about intellectual property. A similar search function might also allow manufacturers to reuse the data and modeling configurations and setups for commonly used process operations or machines. In general, there are levels of detail in specifying configurations. Several levels of detail could be relatively open without affecting proprietary concerns, but as configuration information becomes more specific and proprietary, sharing would need to become a business transaction. The issue becomes one of recalibrating intellectual property. CESMII^4 has been tackling this kind of approach through a concept named “Profile” that acts within a standard based data infrastructure stack. What is missing is a way to make the distributed library or capability accessible, indexable, and searchable. The evolution of a networked system for the discovery of manufacturing resources might evolve along similar lines to the evolution of software tools for searching, browsing, and webpage creation on the Internet. Web-based tools evolved explosively to more powerful versions in a few short years in the mid- 1990s from Lycos to Google, Mosaic to Internet Explorer, and Front Page to Word under the driving force (^4) Clean Energy Smart Manufacturing Innovation Institute, one of sixteen Manufacturing USA Institutes
of accelerating web-based commerce. The potential exists for new software tools to promote a similar expansion of web-based commerce in manufacturing. Workshop participants highlighted some specific observations related to the discovery of manufacturing data and modeling application resources:
The supply chain disruptions created by the Covid- 19 pandemic have elevated manufacturing resilience to a national imperative by demonstrating the impossibility of managing national scale supply disruptions through company specific supply chains without vastly increased information sharing and coordination. Current efforts in applying AI methods to supply chain management are almost exclusively implemented in the proprietary supply chains of individual companies. The workshop participants associated manufacturing resilience with the ability to adjust, reconstruct, and link supply chains to provide better management of productivity at a national scale, across companies and industries. This further implies that each manufacturer has the flexibility to change product lines and/or
programs that provide the foundational knowledge that today’s engineers and technicians will need, using existing data centric methods as a bridge to the AI tools of the future.
The chart below groups the resonant workshop comments^6 in a graphic that came together as an implementation framework for driving demand for digitalization and the adoption of AI. The blue regions at the top and bottom define the need to use industry-wide and factory specific AI strategies to link supply chains with the factory operations. This linkage is essential to providing benefits that directly impact operations on the factory floor, where the data needed to provide further benefits, is generated. Workshop participants, however, also identified high priority opportunities for AI at the supply chain level that included increasing yield, decreasing waste, preventing single source failure, providing supply chain as a service, shared inventory and capability data, and signals for real time supply and demand changes. Opportunities also included business to business interoperability, open source data for building AI tools, and machine/operations benchmark data. At the factory level, priority AI opportunities include augmenting human involvement, automated product testing and quality assurance, machine/operation monitoring and control, and providing higher quality information to human workers. The black regions on the left and right address the need to establish industry-wide adoption of collaborative AI infrastructure and workforce strategies. As shown on the left, infrastructure, tools, and practices are needed to enable data sharing with trust. Workshop participants emphasized the need for data that is meaningful, available, accessible, affordable, reusable, sharable, secure, and trusted. The region on the right addresses the need for a workforce that can find and apply AI tools, data and modeling configurations and (^6) Resonant comments are those that arose in more than one source – workgroups, chat, email and panel notes
application knowhow in factory operations, and have the direction and capability to contribute data, information, and knowhow relative to a redefined value proposition for intellectual property. The objective of the framework is to depict the key elements needed to secure the critical mass of industry commitment necessary for sustained use of AI and data centric solutions. A cycle of collaboration can start now using proven AI methods to produce tools for today’s workforce and to define workforce training programs that can be updated with industry participation at a pace consistent with technology innovation and industry demand. This is also consistent with a general position taken by the workshop participants that the industry needs to start working with data now with a line of site to what is needed to enable AI in the future. There are currently significant federal investments of an industry-wide nature. The Manufacturing Extension Program, the Manufacturing USA Institutes, and several federal agency and state programs are addressing pieces of an industry-wide approach through public-private partnerships. These efforts are directionally significant for data centric solutions, but they need augmentation and orchestration to be able to speed up adoption to address and scale AI for industry-wide impact. As overviewed in the body of this report, further research, development, and demonstration are needed on every aspect of the technology and educational supply chains. R&D on the specifics of a collaboration and business model for government, academic, and commercial business to work together would have a profound impact.
The workshop set the stage by explaining how AI can transform manufacturing competitiveness by enabling industry-wide collaboration, provided specific suggestions for opportunities to implement AI in advanced manufacturing, and framed perspectives that can inform the discussions in the future Workshops. The items enumerated below offer further context to be vetted with Workshop 1 participants and additional domain experts for framing the discussions in Workshop 2:
In early 2020, the National Science and Technology Council (NSTC) Subcommittee on Advanced Manufacturing and Subcommittee on Machine Learning and Artificial Intelligence articulated cross-agency interest in the strategic and timely value of organizing a symposium on a U.S. strategy for resilient manufacturing ecosystems through AI. Co-chairs, an organizing committee, and an advisory committee (please see Appendix B) were established and engaged in a process with both subcommittees to frame, shape, focus, and plan the symposium. Considering the nature and complexity of the topic and with the aim of providing a comprehensive perspective, a three-workshop symposium was designed. The symposium brings together two communities: the advanced manufacturing community that is focused on the digitalization of manufacturing and the AI/ML community that is focused on applications, information technology, and computer science. The overall goals of the symposium are to:
Co-Chairs Jim Davis : Vice Provost IT, Office of Advanced Research Computing, UCLA, and Program Oversight, Clean Energy Smart Manufacturing Innovation Institute (CESMII) Stephan Biller : CEO & President, Advanced Manufacturing International, Inc. Charles Romine : Director of the Information Technology Laboratory, NIST Organizing Committee Said Jahanmir: Assistant Director for Federal Partnerships, Office of Advanced Manufacturing, NIST Faisal D’Souza: Networking and Information Technology Research and Development (NITRD) Program of the NSTC Lisa Fronczek: Associate Director, Advanced Manufacturing National Program Office, NIST John Roth: Assistant Director for Research Partnerships, Advanced Manufacturing National Program Office, NIST Don Ufford: Advanced Manufacturing Policy Fellow, Advanced Manufacturing National Program Office, NIST Interagency Advisory Committee Mike Molnar, Frank Gayle: Advanced Manufacturing National Program Office, NIST Sudarsan Rachuri: Advanced Manufacturing Office, DOE John Vickers: NASA Bruce Kramer: Directorate for Engineering, NSF Andy Wells: Directorate for Engineering, NSF Astrid Lewis, Aubrey Paris: Department of State Kim, Young Ah: Department of Homeland Security Chuck Geraci: NIOSH Charles Romine: NSTC, ML/AI Subcommittee Henry Kautz: Directorate for Computer and Information Science and Engineering and NITRD AI R&D Interagency Working Group (IWG) David Miller: Directorate for Computer and Information Science and Engineering and NITRD Intelligent Robotics and Autonomous Systems IWG Manufacturing USA Advisory Committee John Wilczynski : America Makes Gary Fedder : ARM Alexander Titus : ARMI/BioFabUSA John Dyck, Haresh Malkani : CESMII John Hopkins : IACMI Nigel Francis, Hadrian Rori : LIFT Chandra Brown, Federico Sciammarella : MxD Scott Miller, Janos Veres : NextFlex Kelvin Lee : NIIMBL Bill Grieco : RAPID
Michele C. D’Alessandro, Vice President and CIO, Manufacturing IT, Merck & Co., Inc. Çağlayan Arkan, Vice President, Manufacturing Industry, Microsoft Corp. John Dyck, CEO, CESMII – The Smart Manufacturing Institute Panel 2. Artificial Intelligence/Machine Learning (AI/ML) Opportunities Lynne Parker (moderator), Deputy Chief Technology Officer of the United States, and Assistant Director for Artificial Intelligence (AI), White House Office of Science and Technology Policy Ed Abbo, President and CTO, C3.ai Jayant Kalgnanam, Director, AI Applications (Asset Mngt & Supply Chain), IBM Research; Distinguished Industry Leader (2020), Chemicals & Petroleum & Industrial Products Daniela Rus, Director, Computer Science and AI Laboratory (CSAIL); Andrew (1956) and Erna Viterbi Professor of Electrical Engineering and Computer Science; and Deputy Dean of Research, Schwarzman College of Computing, MIT Reid Simmons, Research Professor in Robotics and Computer Science, Carnegie Mellon University With the topics introduced by the co-chairs and panels, the workshop turned to the participants to provide feedback in three facilitated breakout sessions. These sessions were designed to gather perspectives from both the manufacturing and AI/ML sectors into what opportunities and challenges exist in leveraging AI in the advanced manufacturing sector. Below are the three session topics with their respective questions. Breakout Sessions Session 1: National/global scale considerations for manufacturing ecosystems, supply chains, and data flows a. What U.S. ecosystem and supply chain elements are strong, weak, or missing? b. What impacts has the Covid- 19 pandemic revealed for U.S. advanced manufacturing resilience? c. How do national and global considerations impact the manufacturing ecosystem and data flow considerations? d. Where do AI/ML versus other approaches stand as solutions, and why? e. Why would the AI community be interested in these problems, and what would they need to understand about the problems? Session 2: Local factory operation and workforce considerations where solutions are ultimately implemented a. What U.S. factory and workforce elements are strong, weak, or missing in a digital transformation context? b. What have the Covid-19 impacts revealed for factory and workforce considerations? c. How do national and global considerations and ecosystem and data flow considerations come together in local factory and workforce considerations? d. Where do AI/ML versus other data and modeling approaches stand as solutions, and why? e. What needs to be true for the new data and modeling tools to be accessible to the workforce and for the workforce to use them? f. Why would the AI community be interested in these problems, and what would they need to understand about the problem? Session 3: Bringing ecosystems, data flow, factory operations, and workforce together; addressing priorities and cross-cutting AI/industry opportunities and challenges; and collaboration points a. What are the priority AI opportunities and challenges?
b. What are categorical use cases that showcase opportunities and challenges? c. What needs to be true for AI opportunities in advance manufacturing to scale? d. What does the manufacturing community need from the AI community, and why would the AI community be interested? e. What structural changes are needed in the industry and its stakeholders? f. What collaboration points between and among industry, academia, and government are needed? g. What is in the opportunity table after the scan? Following each breakout session, moderators shared brief reports that contained the salient points discussed at the sessions they moderated. These reports served as a transparent way to leverage all information across the breakout sessions among workshop participants.