
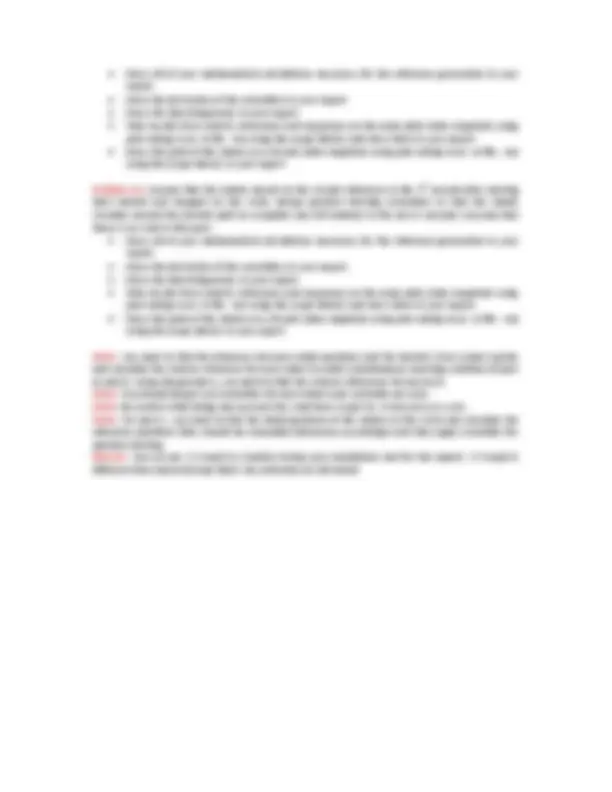
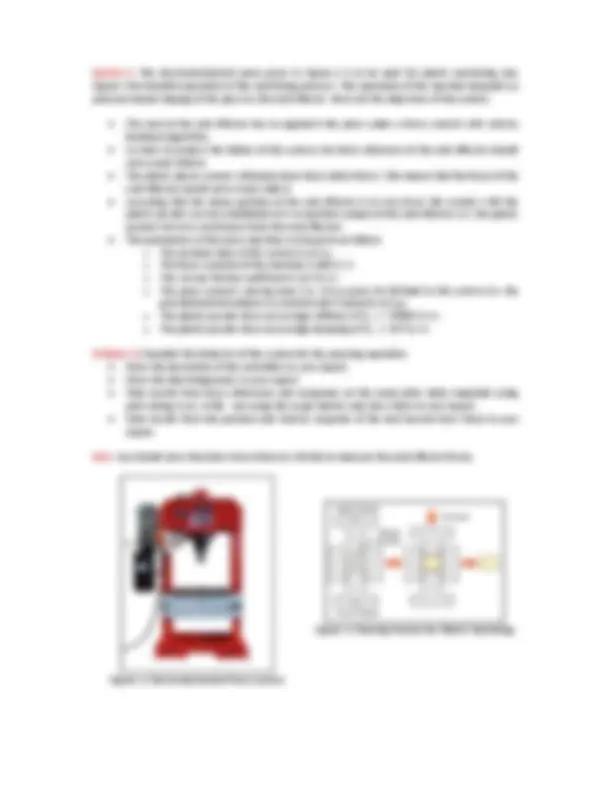
Study with the several resources on Docsity
Earn points by helping other students or get them with a premium plan
Prepare for your exams
Study with the several resources on Docsity
Earn points to download
Earn points by helping other students or get them with a premium plan
Community
Ask the community for help and clear up your study doubts
Discover the best universities in your country according to Docsity users
Free resources
Download our free guides on studying techniques, anxiety management strategies, and thesis advice from Docsity tutors
This exam is very hard for me but may be easy for you. I will be very happy if you help. Thanks
Typology: Exams
1 / 4
This page cannot be seen from the preview
Don't miss anything!
Note-1: named "NameSurname_ID_MECA333_TermProject" (like "ErayBaran_18221_MECA333_TermProject.zip). Note-2: effort. The material should include simulation files (.mdl files compatible with Matlab 2018a version or .m files coded either in Matlab or Octave), codes written for simulation files (.m) and necessary solution text (scanned hand written solution with a readable hand writing is also accepted) as your report. The codes (i.e. Parameters.m, Simulation_Problem1a.m) should include detailed comments and/or the simulation file (i.e. Simulation_Problem1a.mdl or Simulation_Problem2b.slx) should be designed "neatly" (i.e. the signal cables should be designed in a tidy and easy-to-understand way). The scanned text or the written report should be as detailed as possible containing all of the calculations. (^) The submitted zip folder should include all of the necessary material showing explicitly your You should upload your solution to BฤฐLGฤฐ-Learn System with "only one" zipped folderMECA-333: MOTION CONTROL SYSTEMS^ May 25, 2020, 14:00 AM^ Exam Duration: 24 hours^ Take Home Project Note-3: BILGI-Learn system will be accepted and the system will be closed at 14:00 on May 26, Tuesday. IMPORTANT NOTICE: plagiarism softwares. Any kind of cheating, verified by anyone of these softwares will result in a direct disciplinary action considering the results of plagiarism checking software as "proof of cheating". Late submissions or submissions via e-mail will not be accepted. Only the submissions to The sumbitted files will be checked through 3 different code comparison and Problem Problem Problem Problem Problem# Problem Grade Weights - --1a1b-1c 2 (^) Points (^20202040)
System-2: Figure-3 for detailed operation of the machining process). The operation of the machine depends on pressure based shaping of the piece by the end effector. Here are the objectives of the system: x x x x x The tool at the end effector has to approach the piece under a force control with velocity feedback algorithm.In order to protect the failure of the system, the force reference of the end effector should not exceed 1500 N.The plastic pieces cannot withstand more than 1200 N force. This means that the force of the end effector should not exceed 1200 N.Assuming that the home position of the end effector is at zero level, the contact with the plastic powder can be established at 8 cm position output of the end effector (i.e. the plastic powder sits at 8 cm distance from the end effector).The parameters of the press machine can be given as follows The electromechanical press given in Figure-2 is to be used for plastic machining (see o o o o The nominal mass of the system is 16The force constant of the machine is 200The viscous friction coefficient is 10The press system's moving mass (i.e. 16 gravitational disturbance is constant and is equal to 16 ๐๐ ๐๐/๐ ๐๐๐/) gives its full load to the system (i.e. the๐ด ๐๐) Problem-2) Hint: x x x x (^) You should use a Reaction Force Observer (RFOB) to measure the end effector forces.Show the derivation of the controllers in your report.Show the block diagram(s) in your report.Take results from force references and responses on the same plots (take snapshots using plot coding in an .m file - not using the scope blocks) and show them in your report.Take results from the position and velocity response of the tool tip and show them in your report.^ o^ oSimulate the behavior of the system for the pressing operation.^ The plastic powder have an average stiffness ofThe plastic powder have an average damping of^ ๐พ^ ๐ทเฏเฏ^ = 70000= 20^ ๐๐ /^ ๐๐/.๐. Figure-2: Electromechanical Press System^ Figure-3: Pressing Process for Plastic Machining