
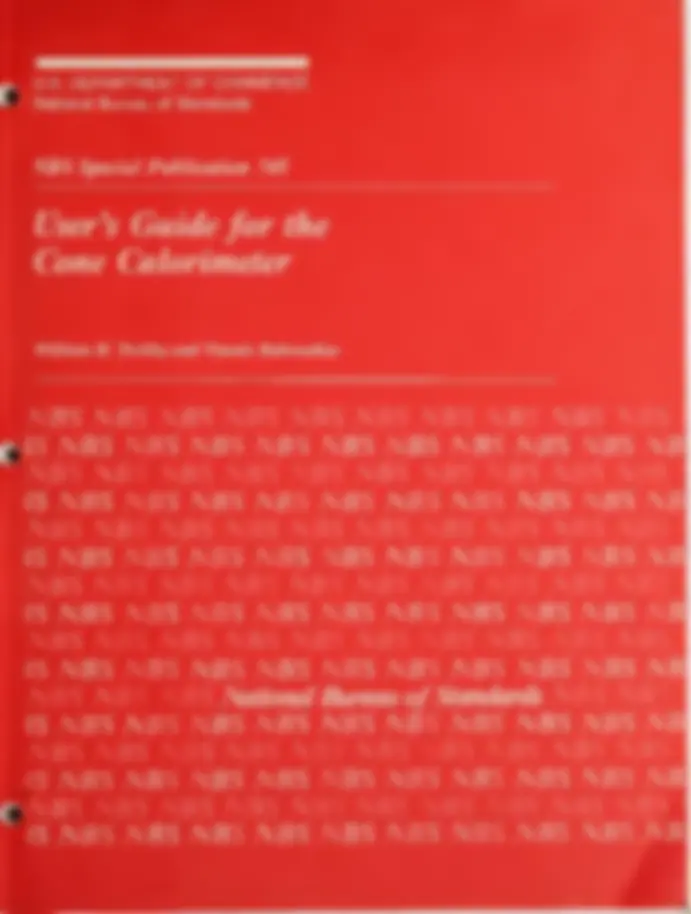
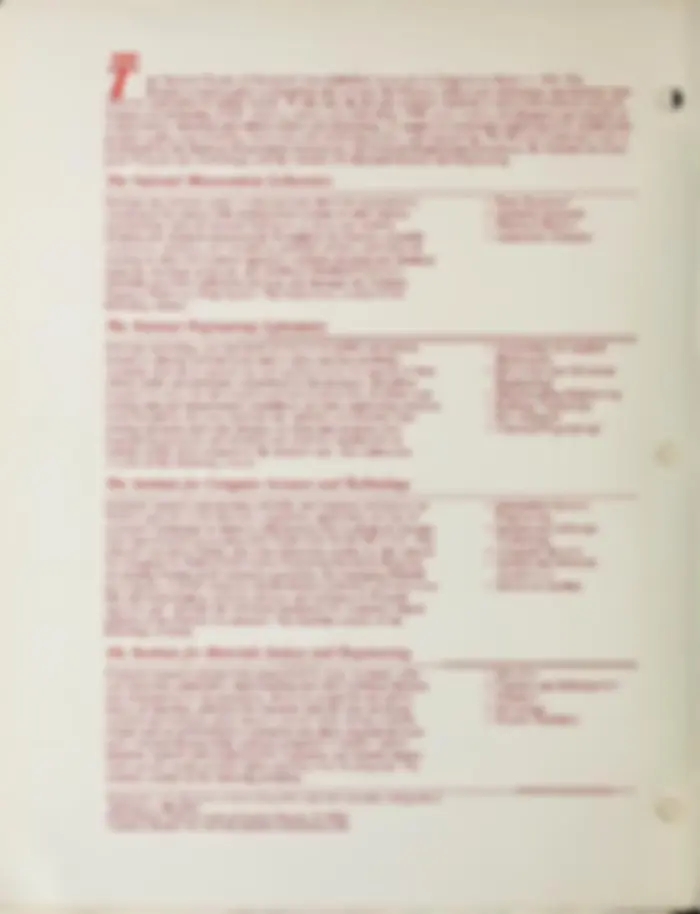
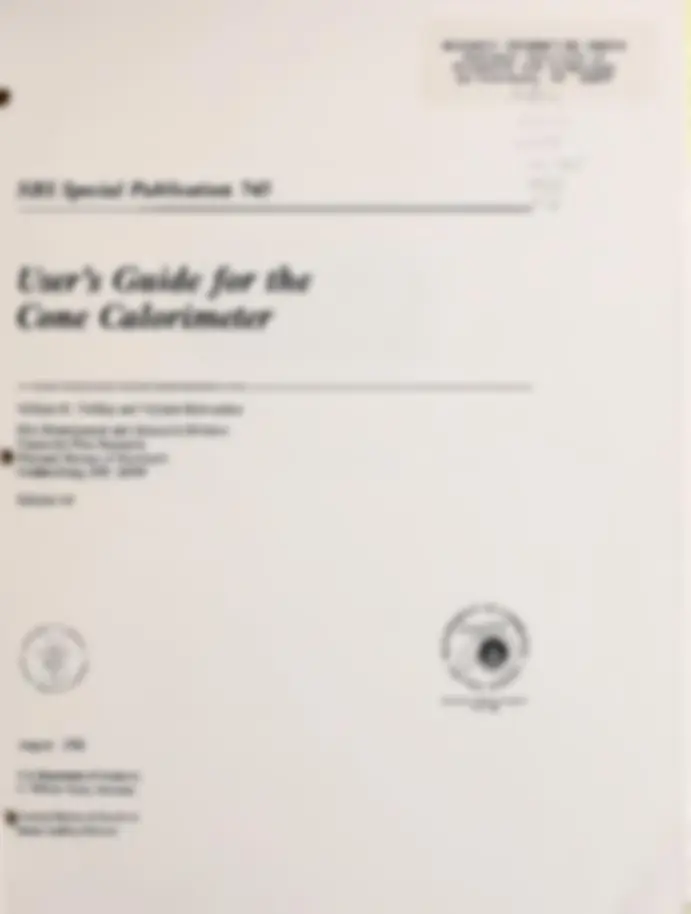
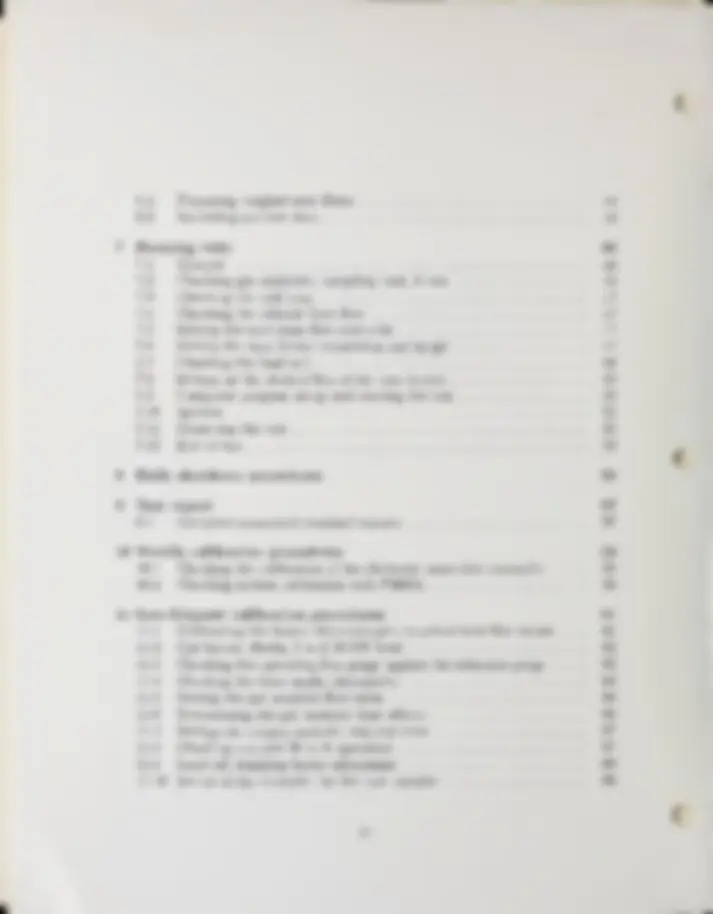
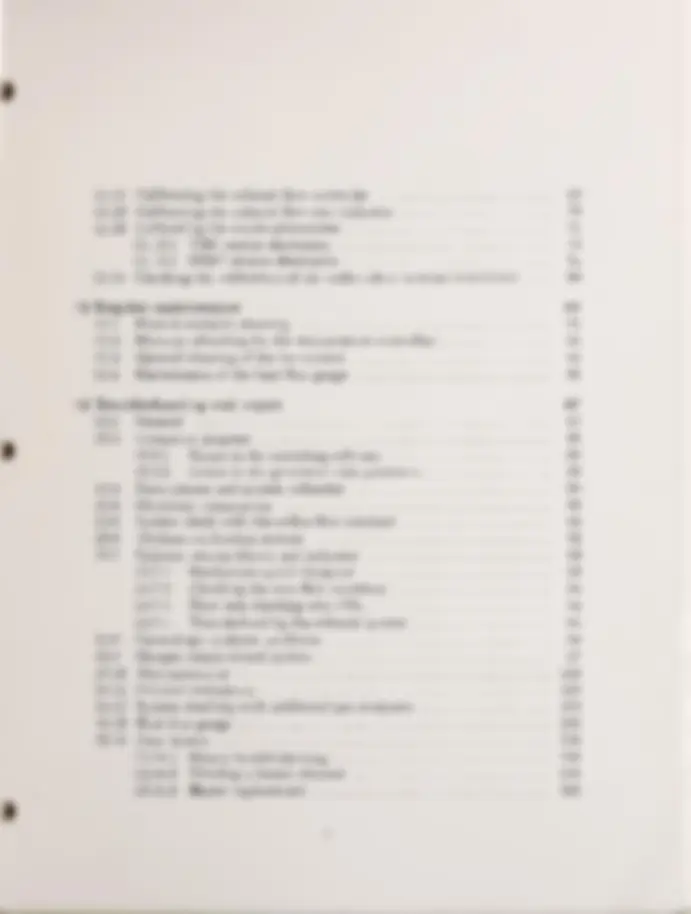
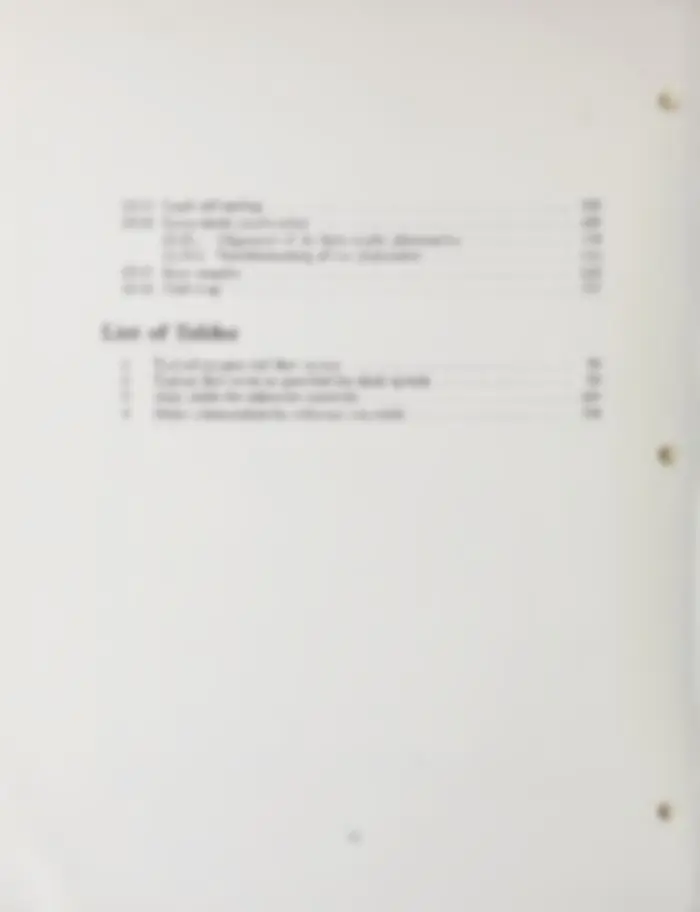
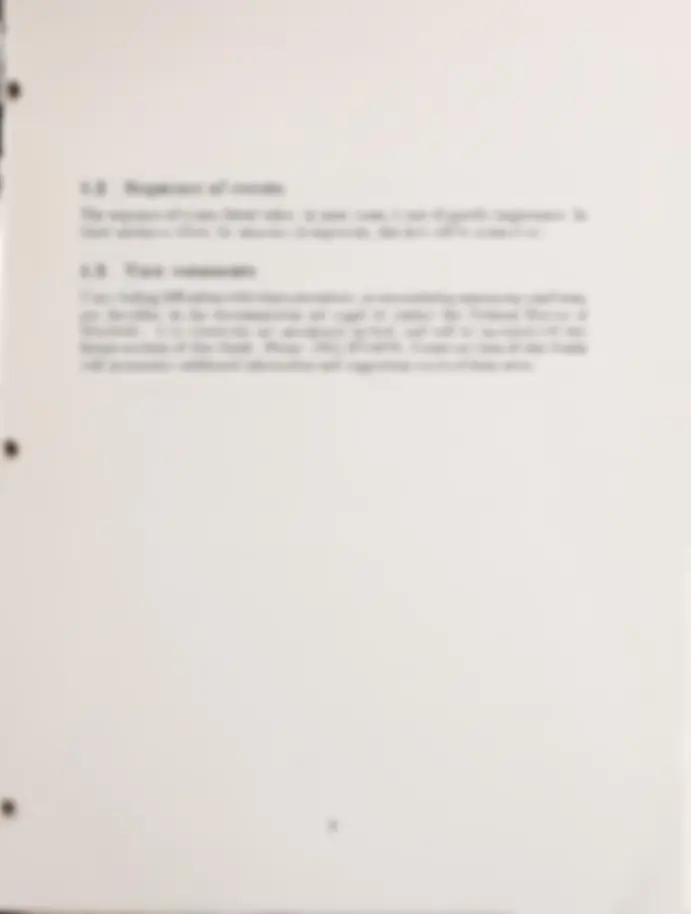
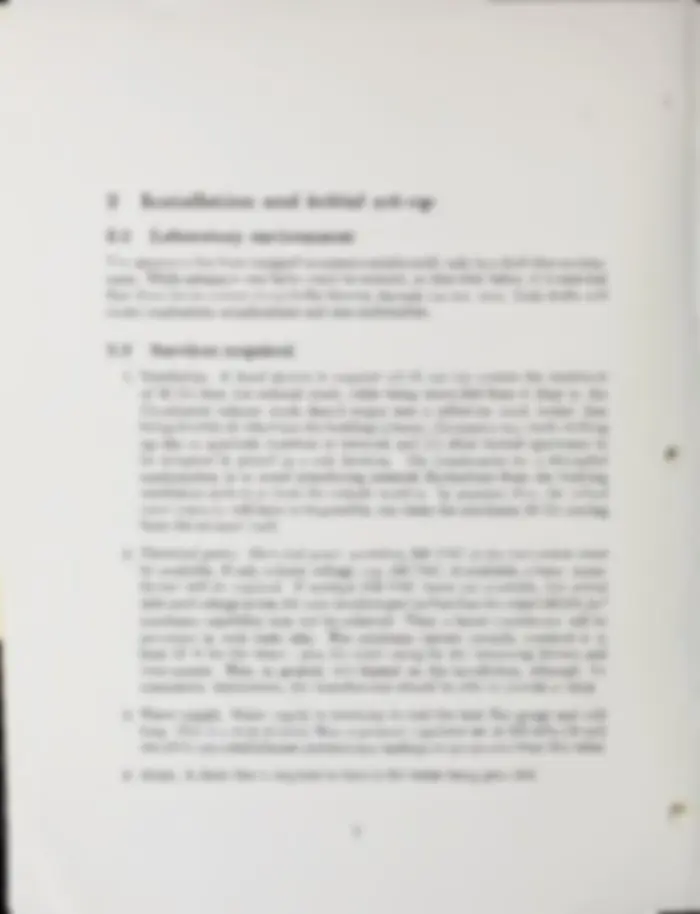
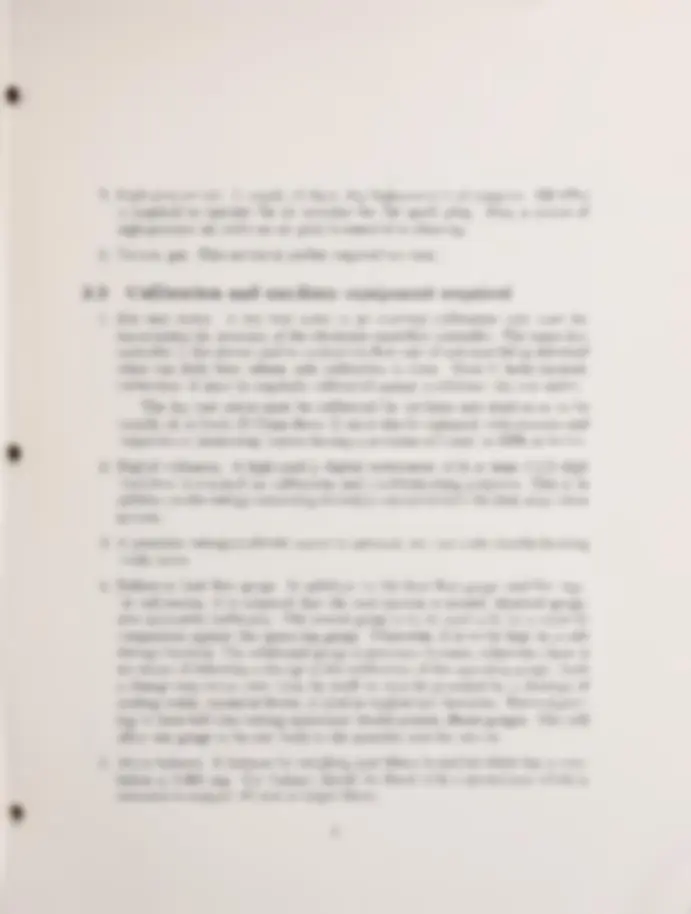
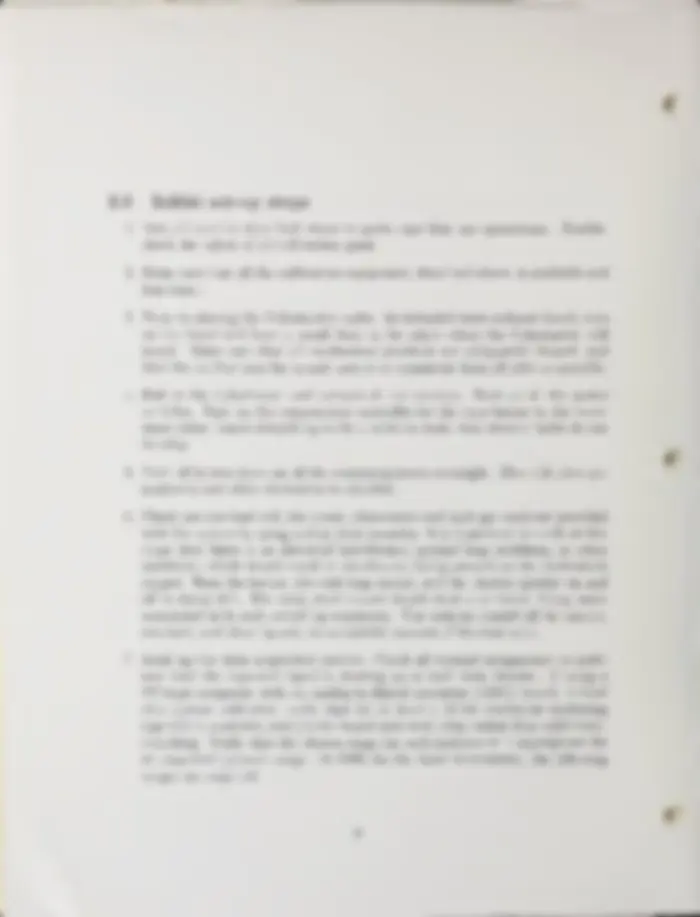
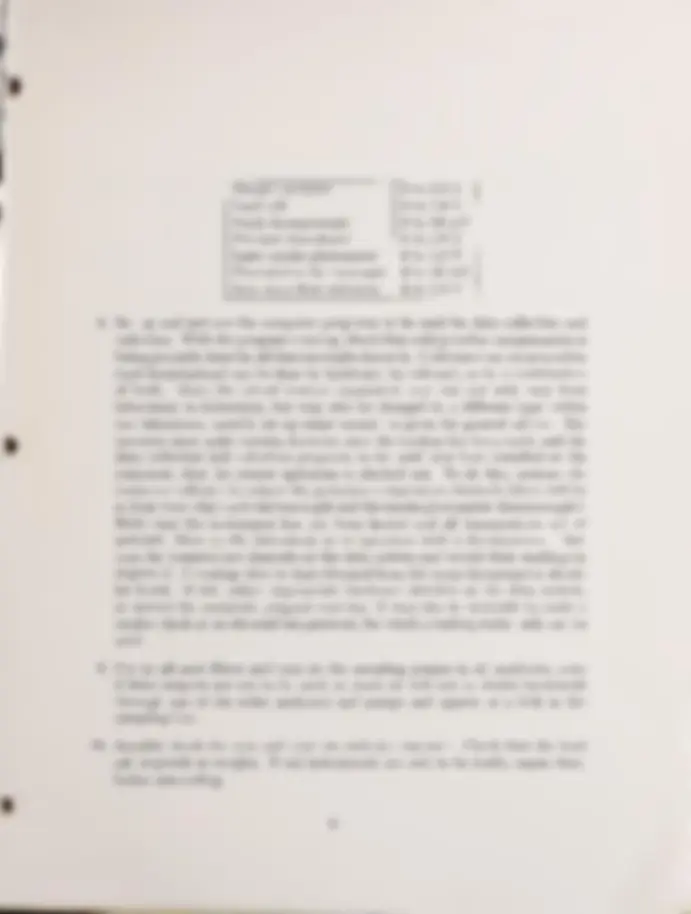
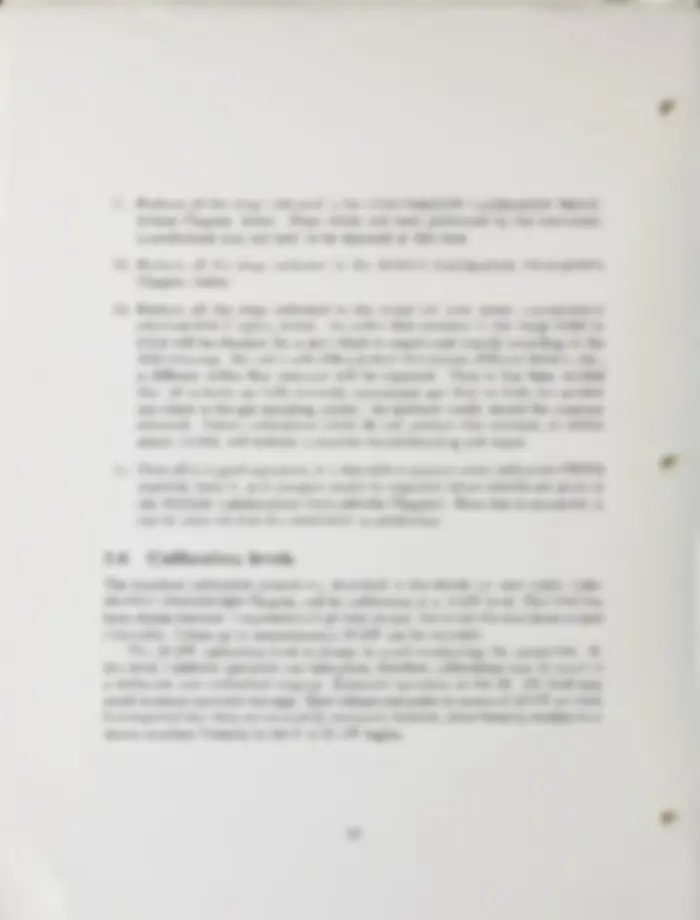
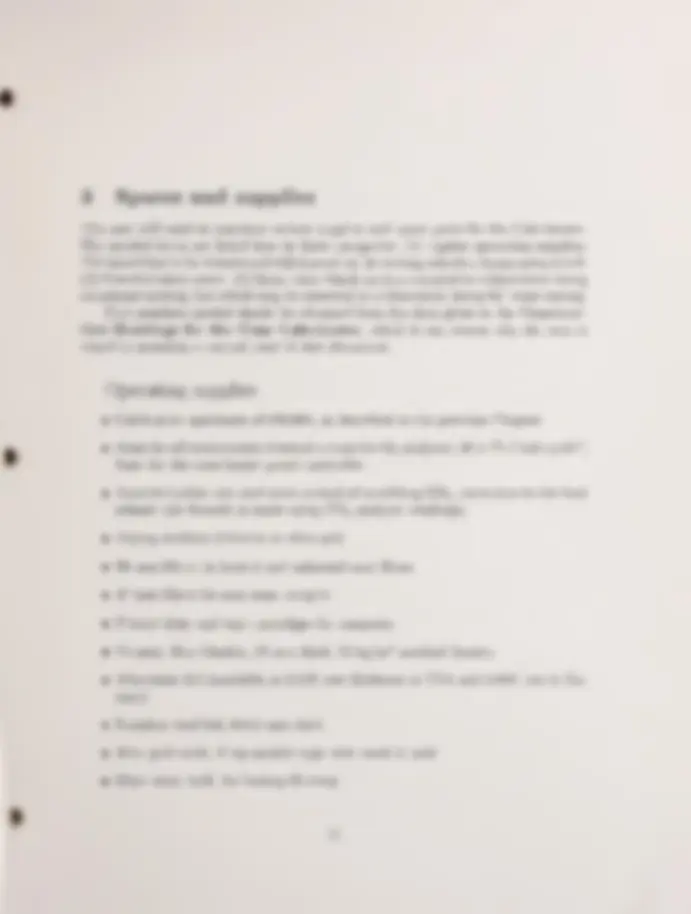
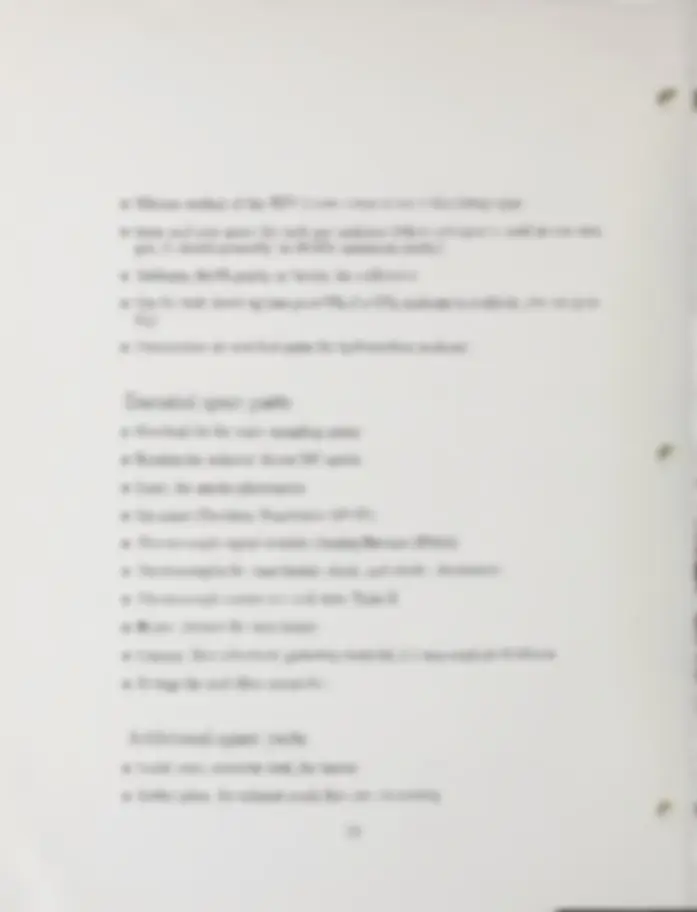
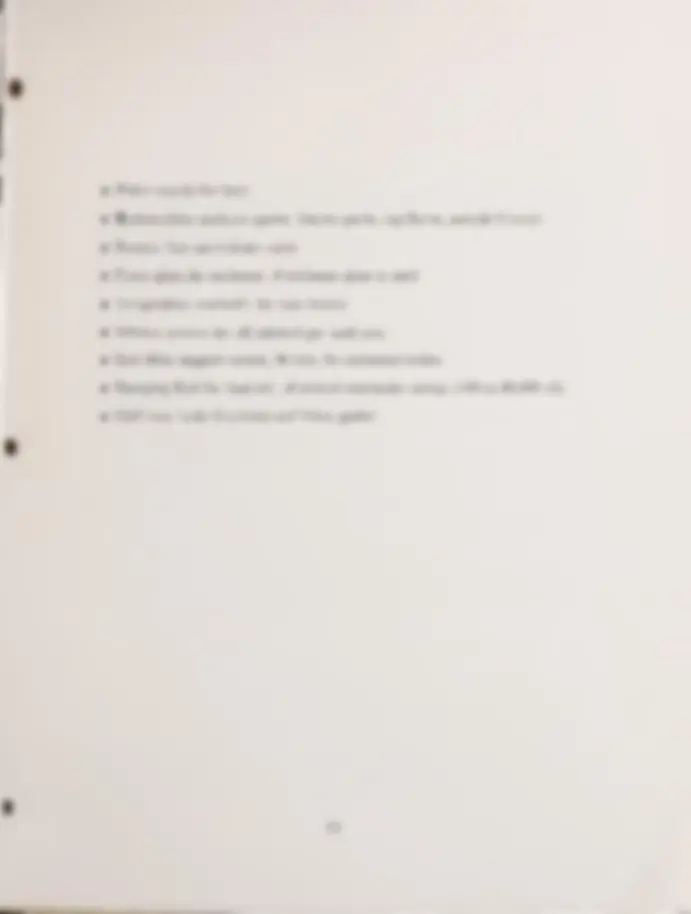
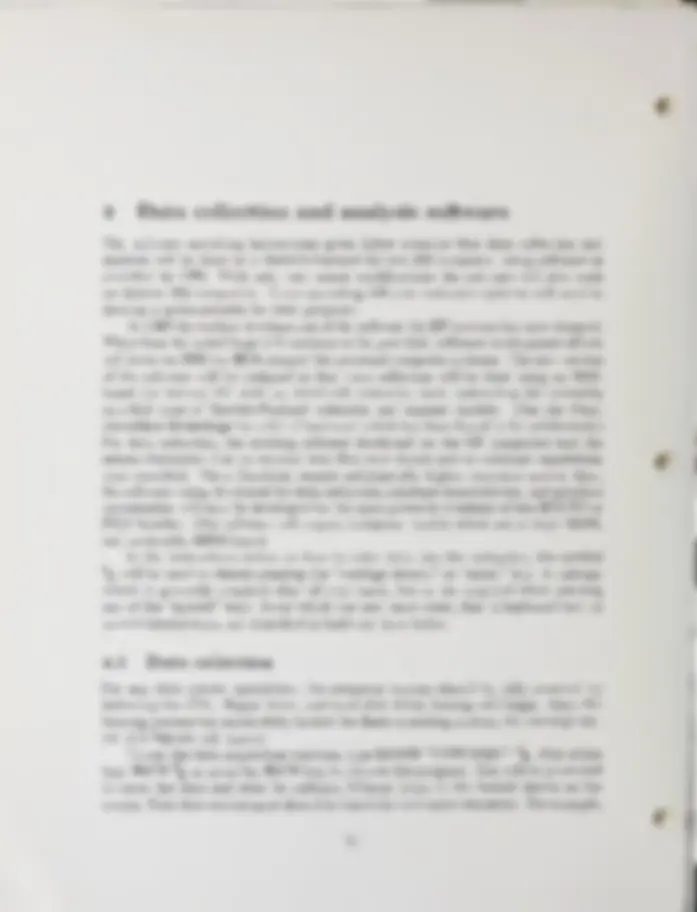
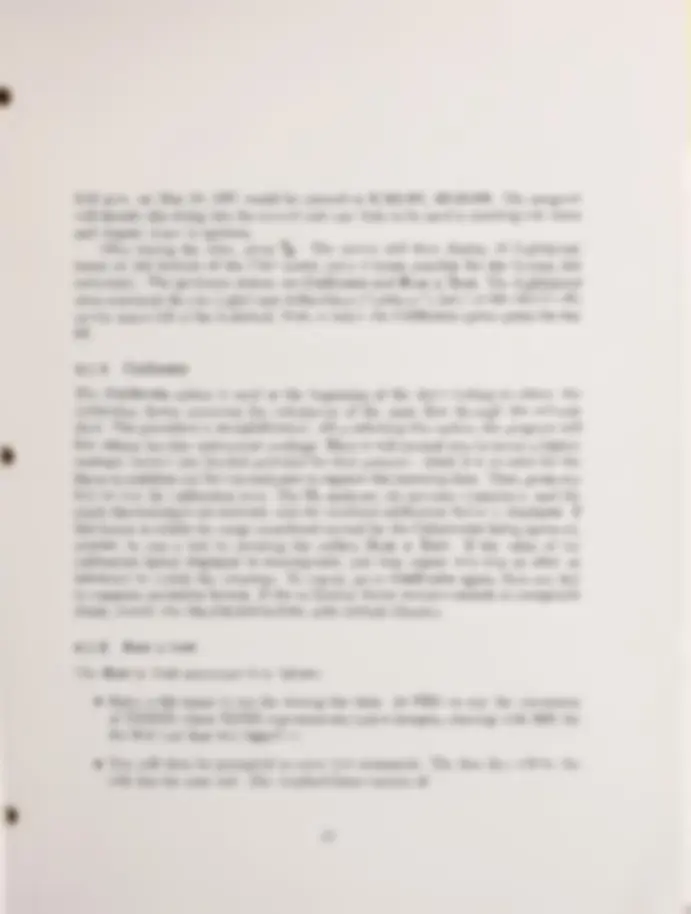
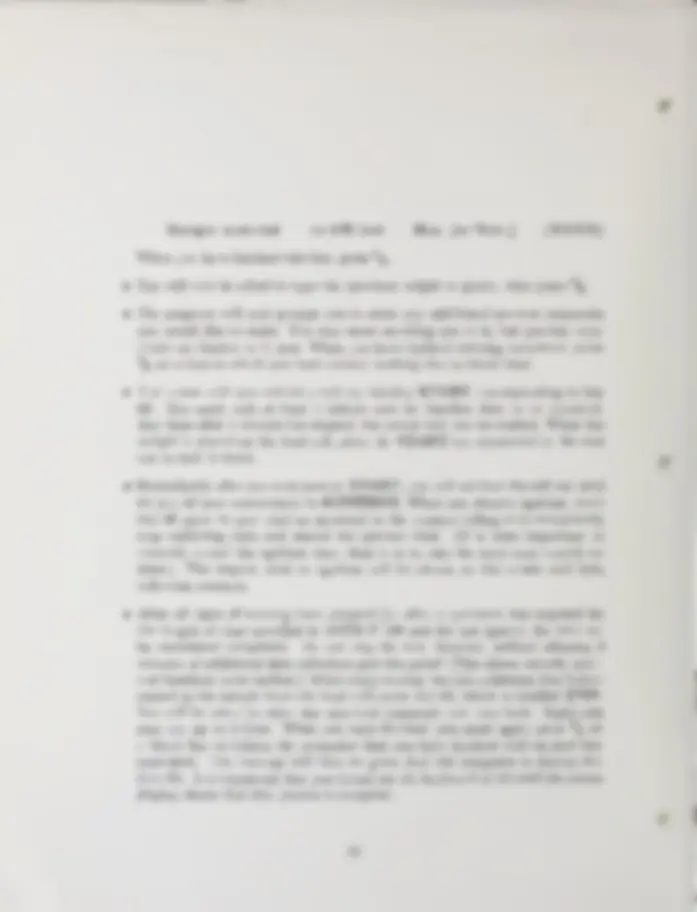
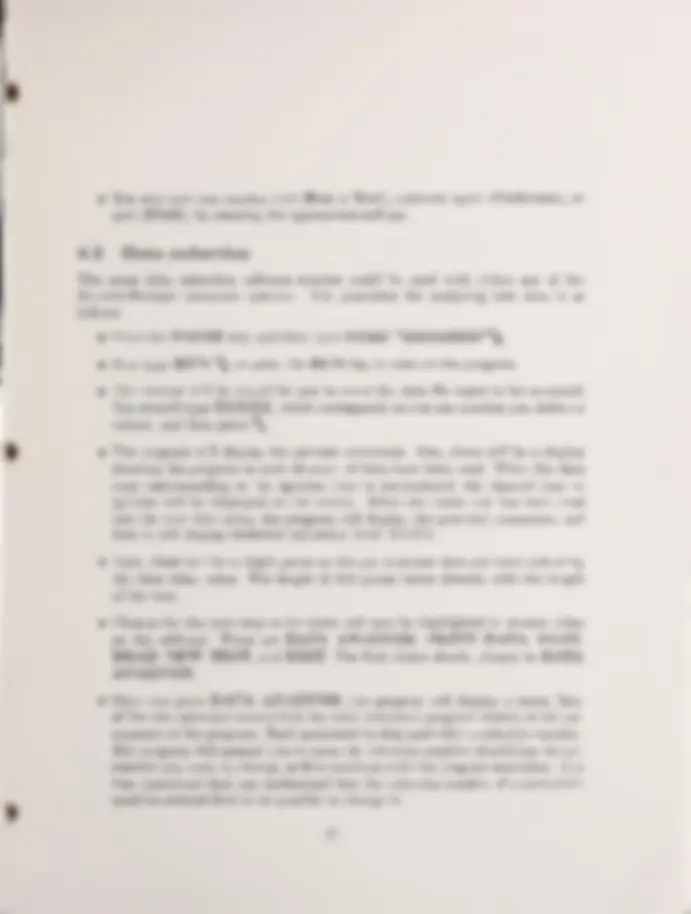
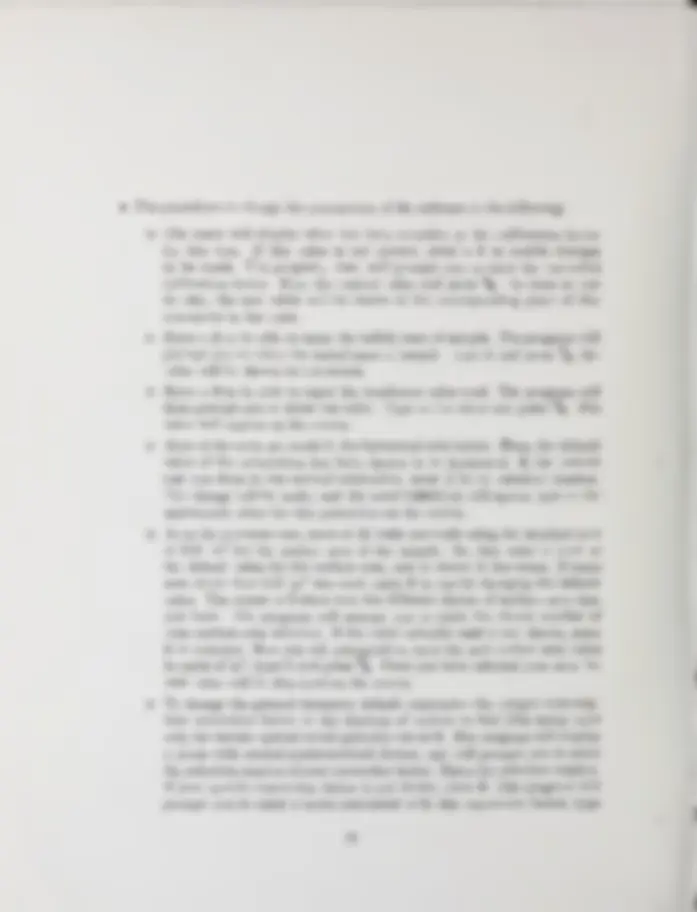
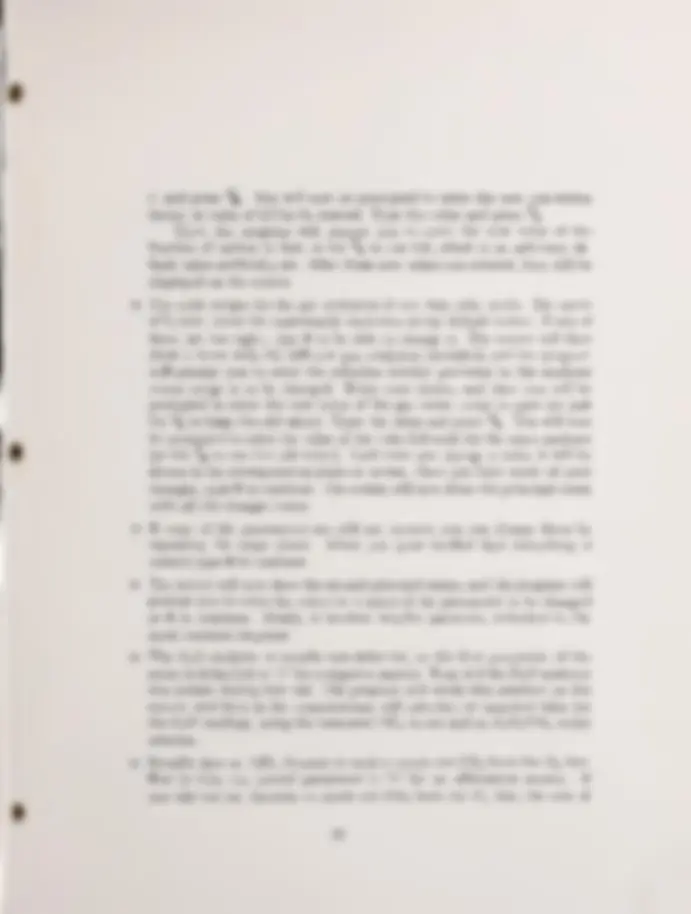
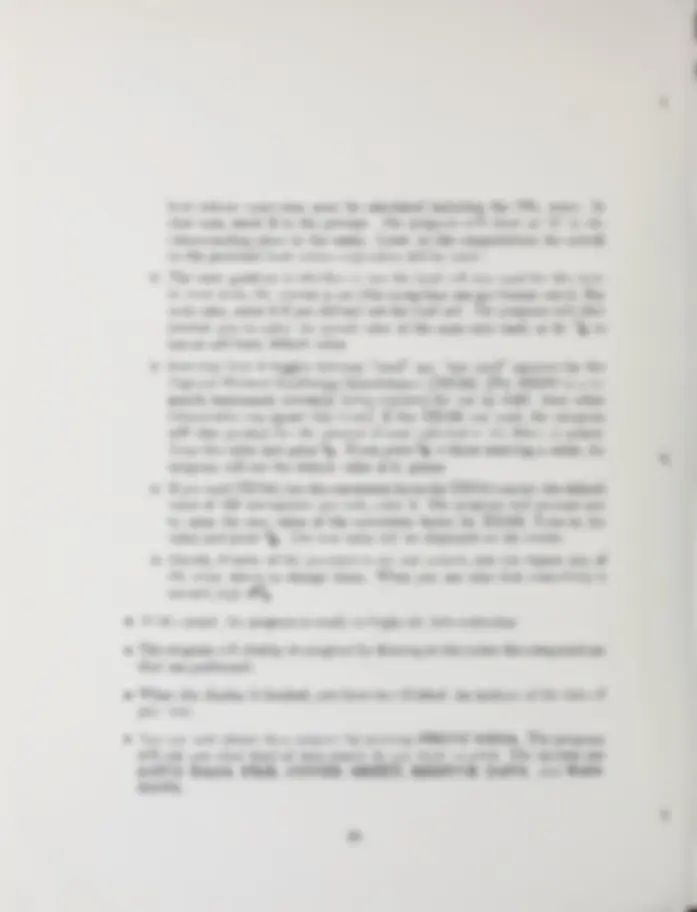
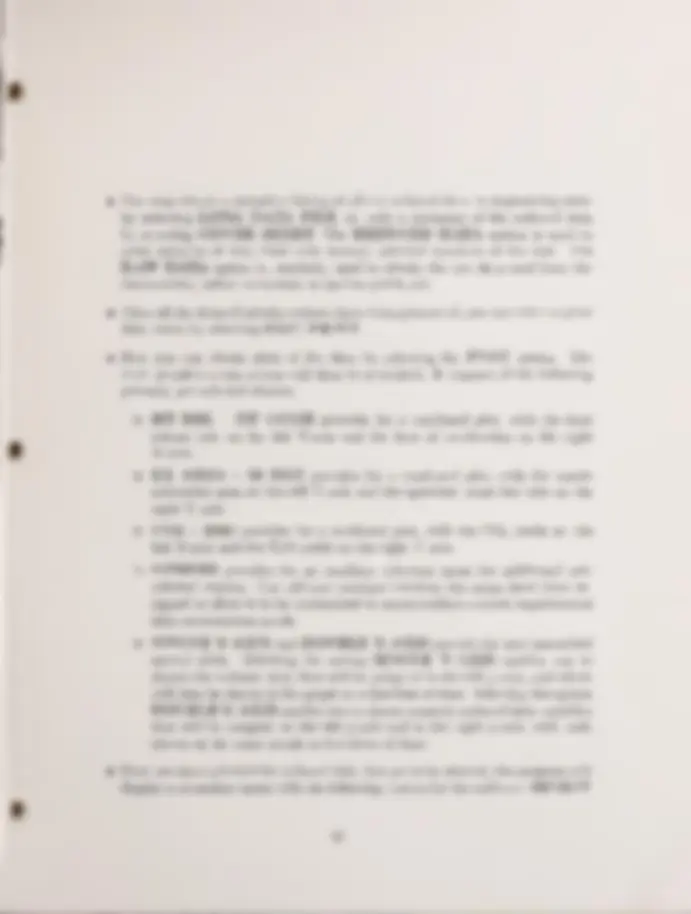
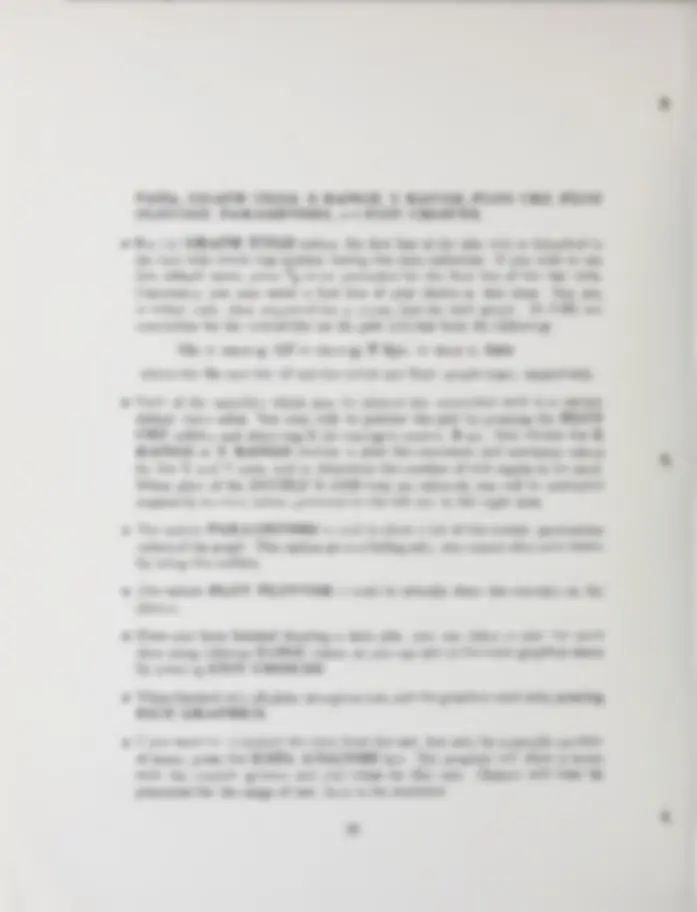
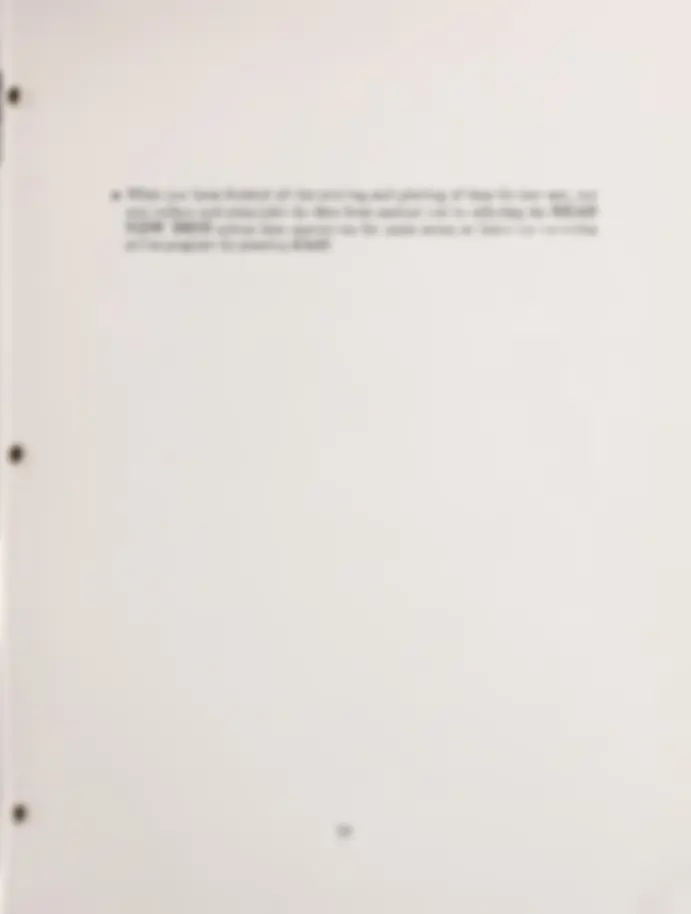
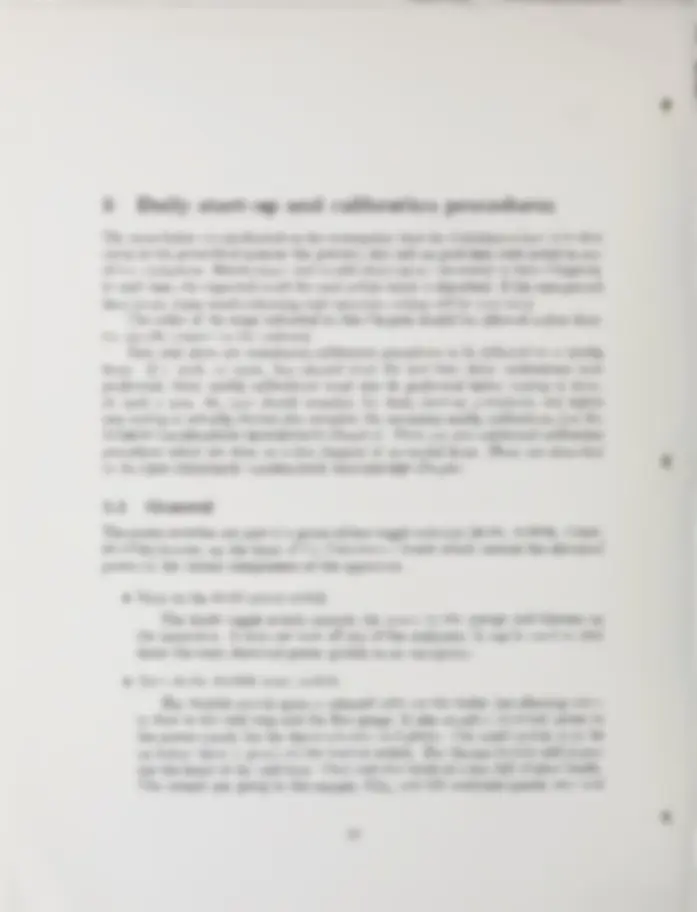
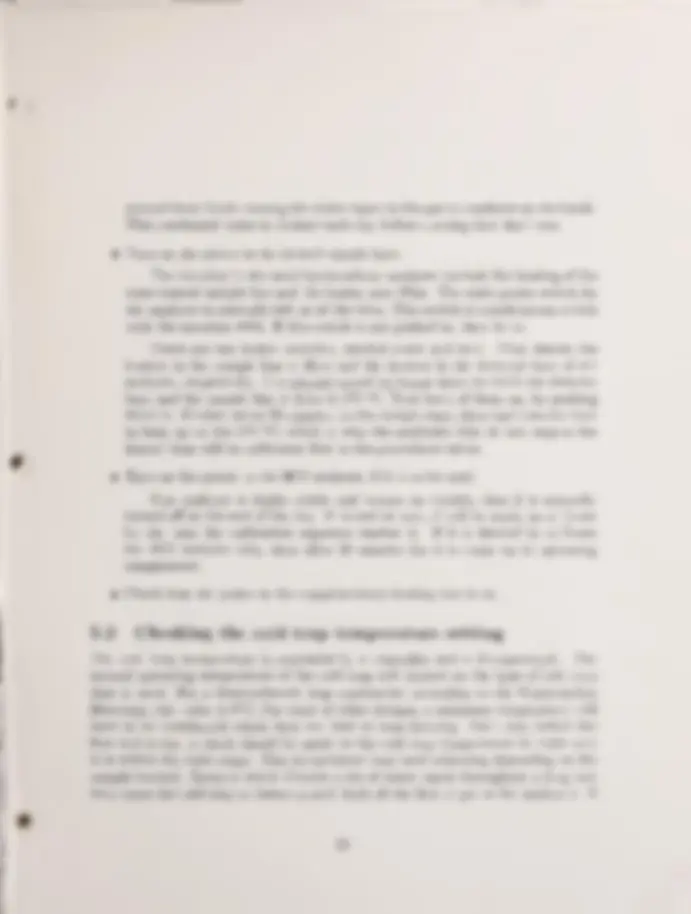
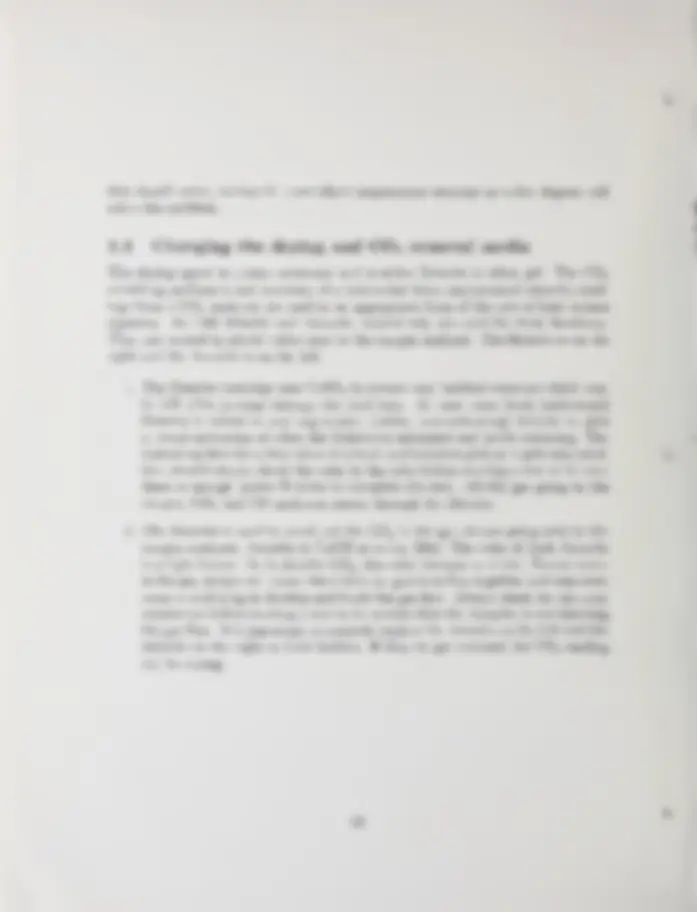
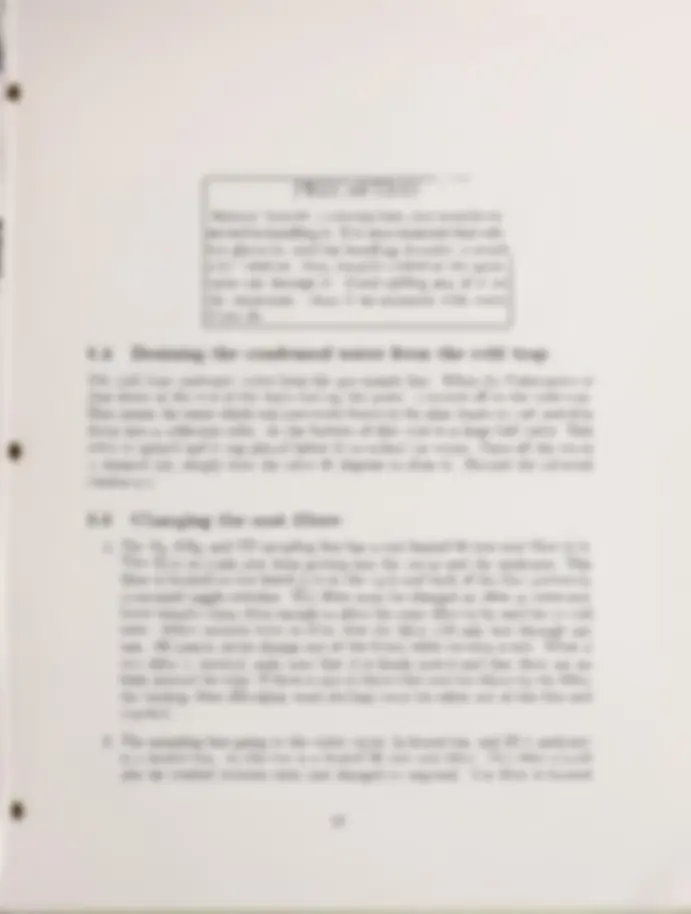
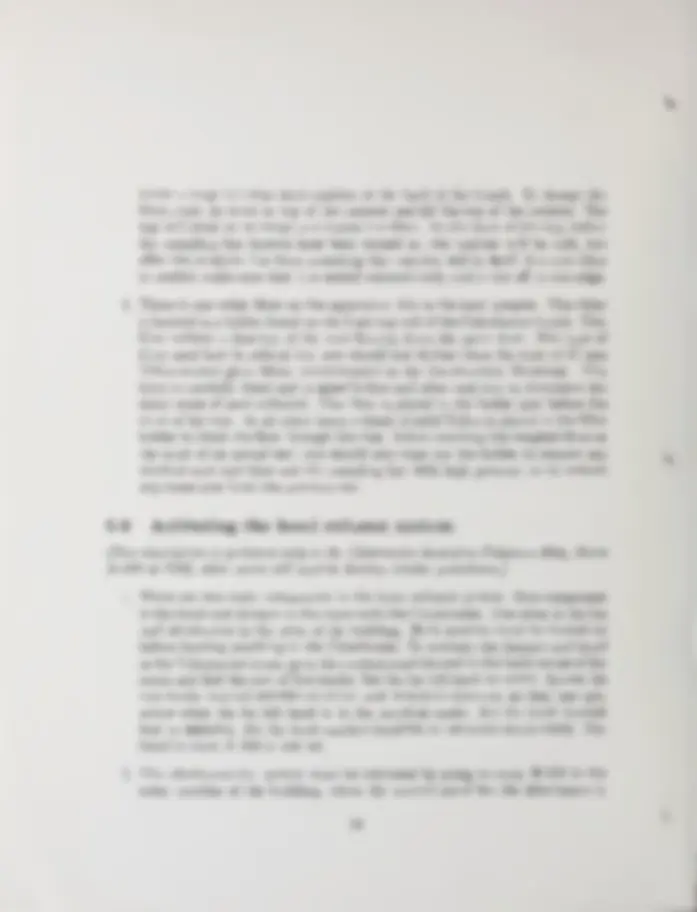
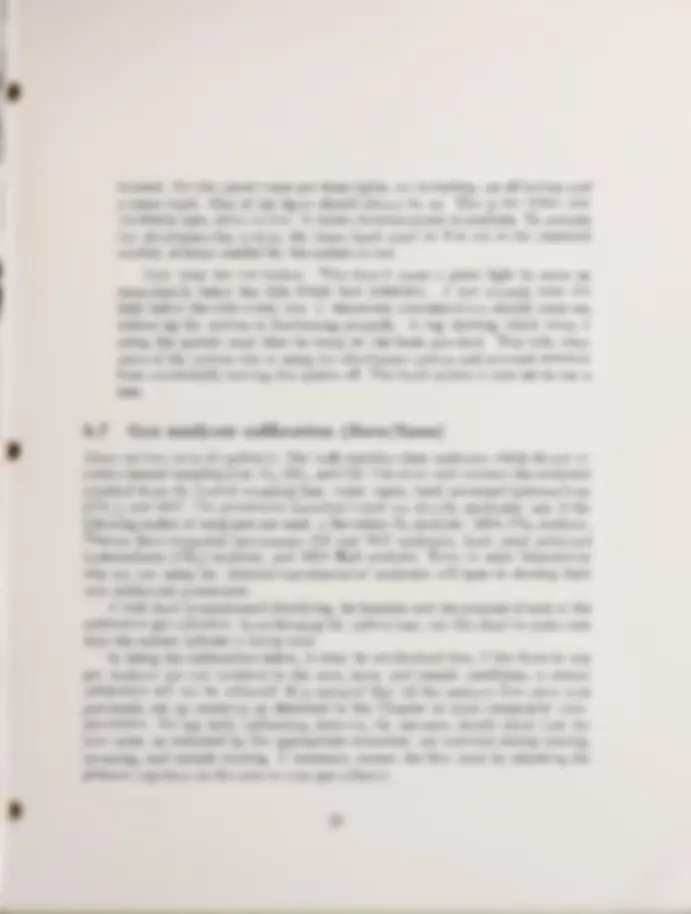
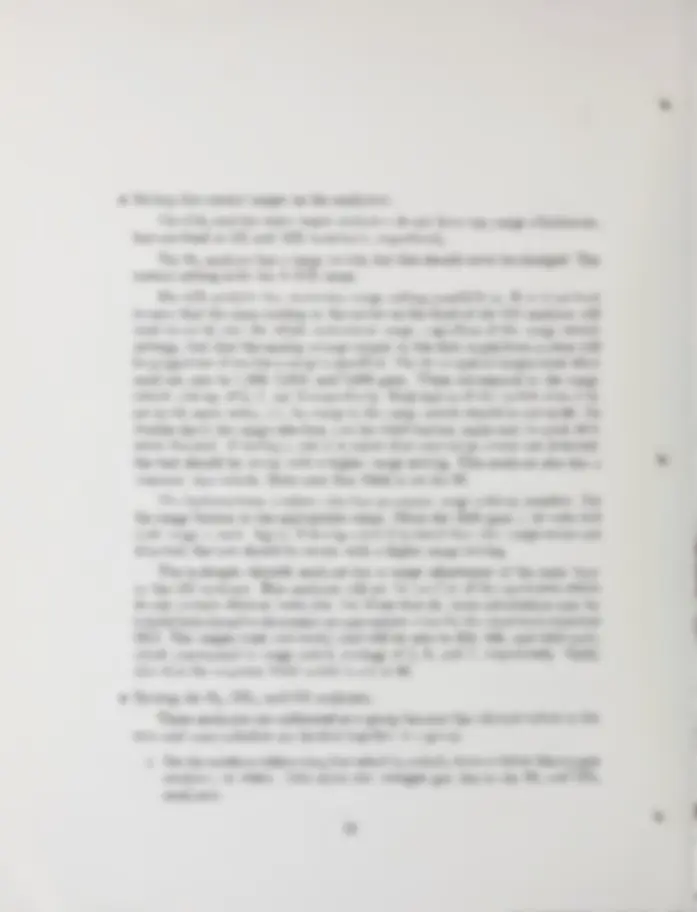
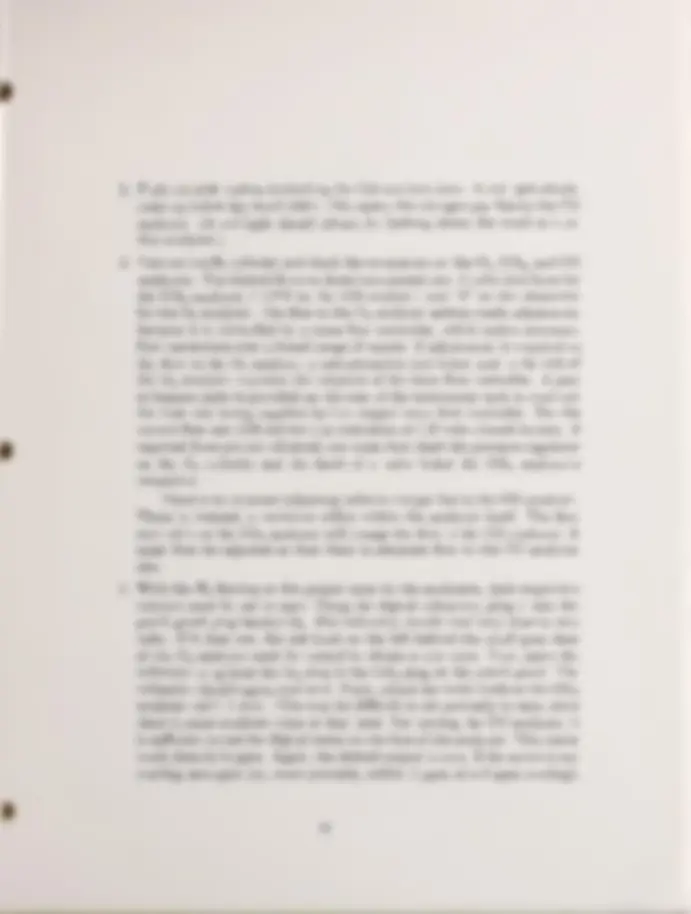
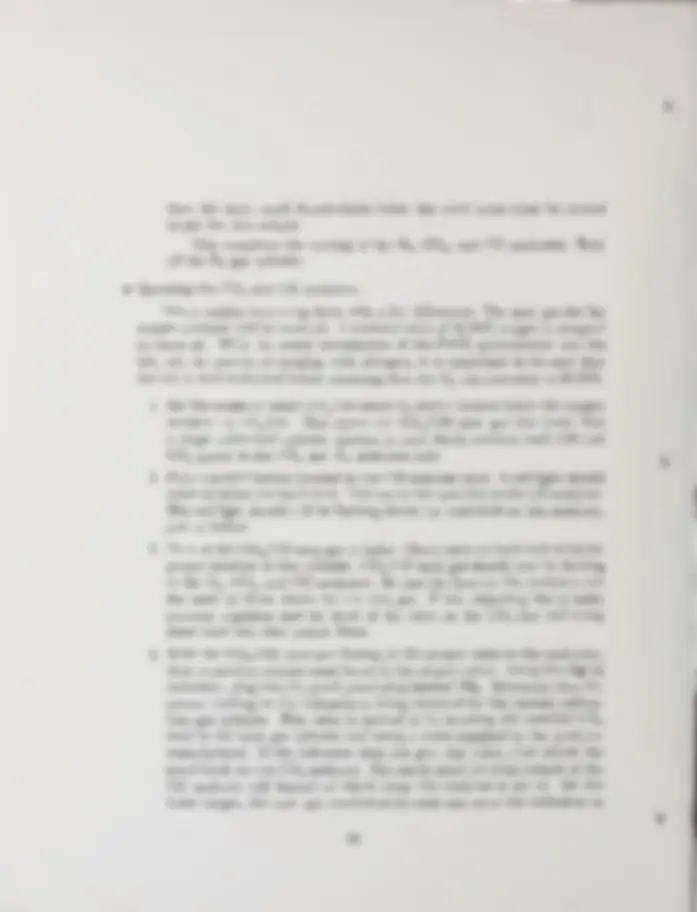
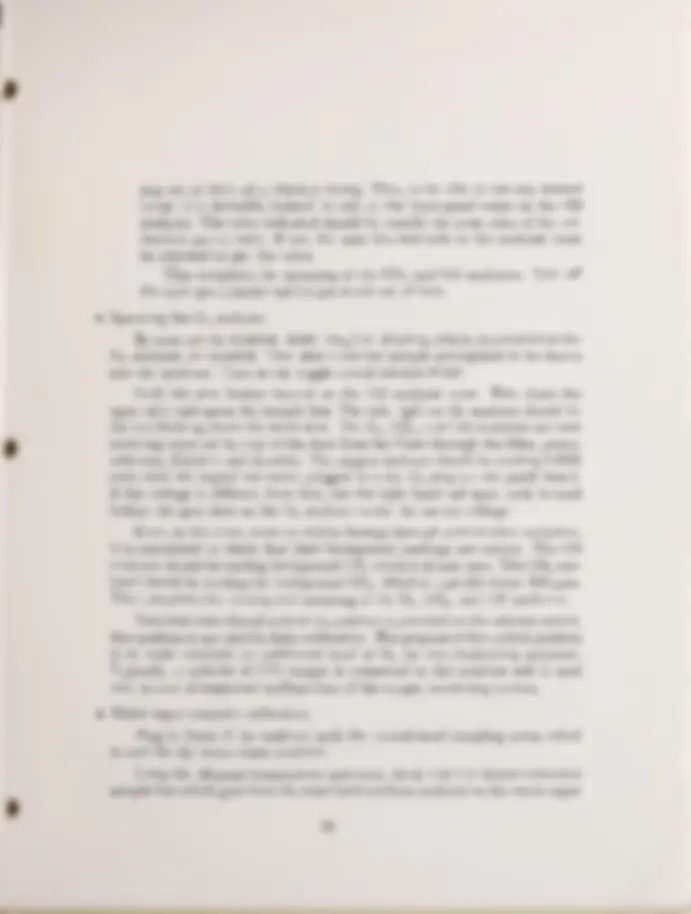
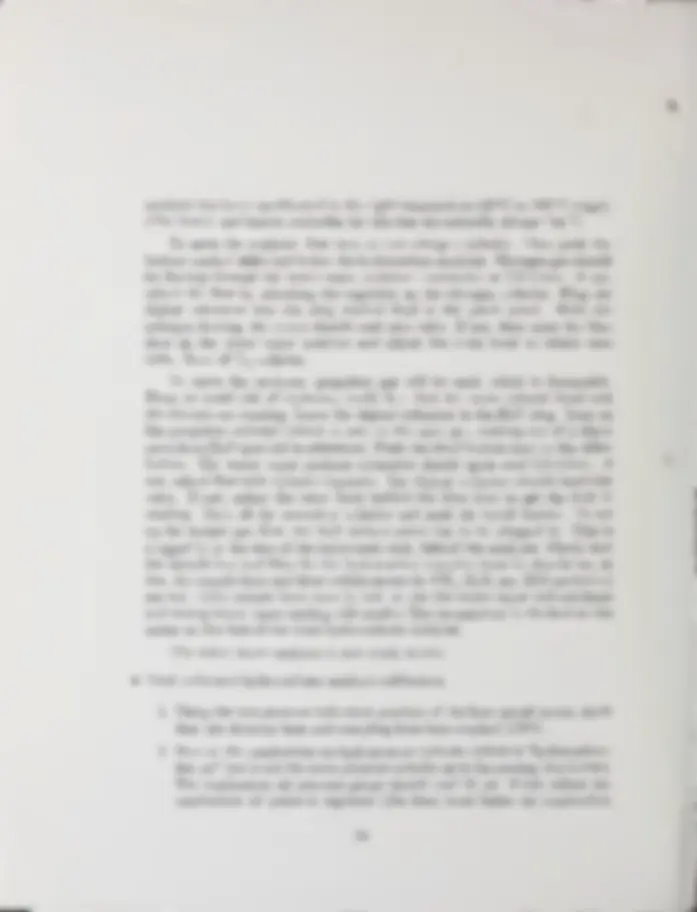
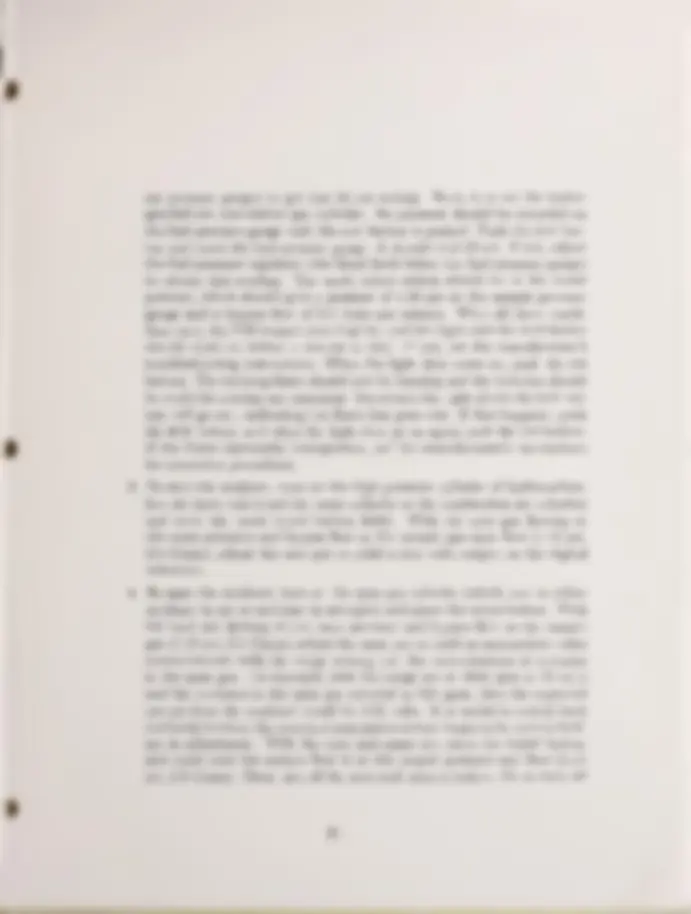
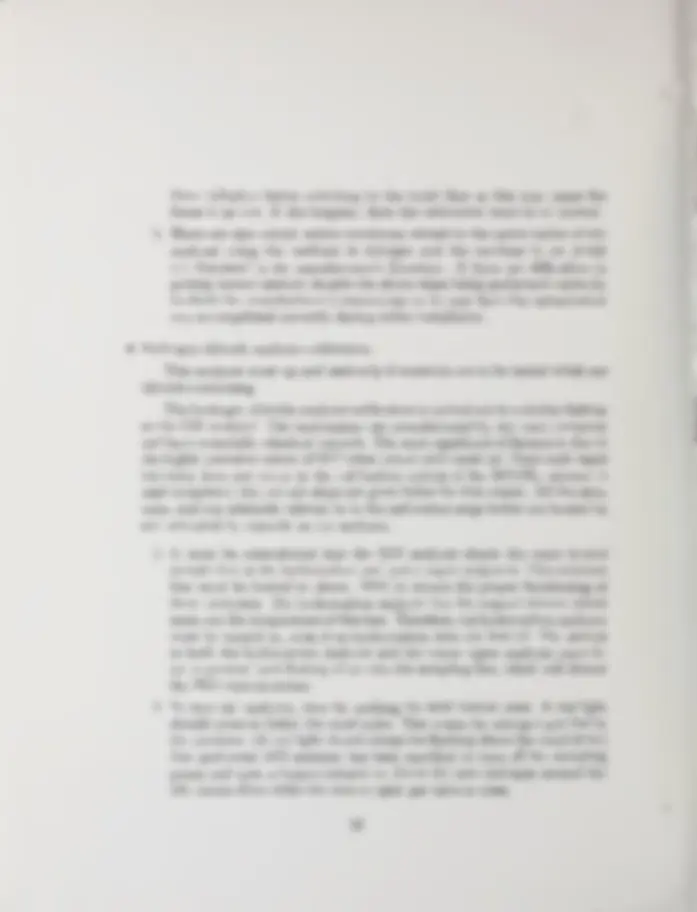
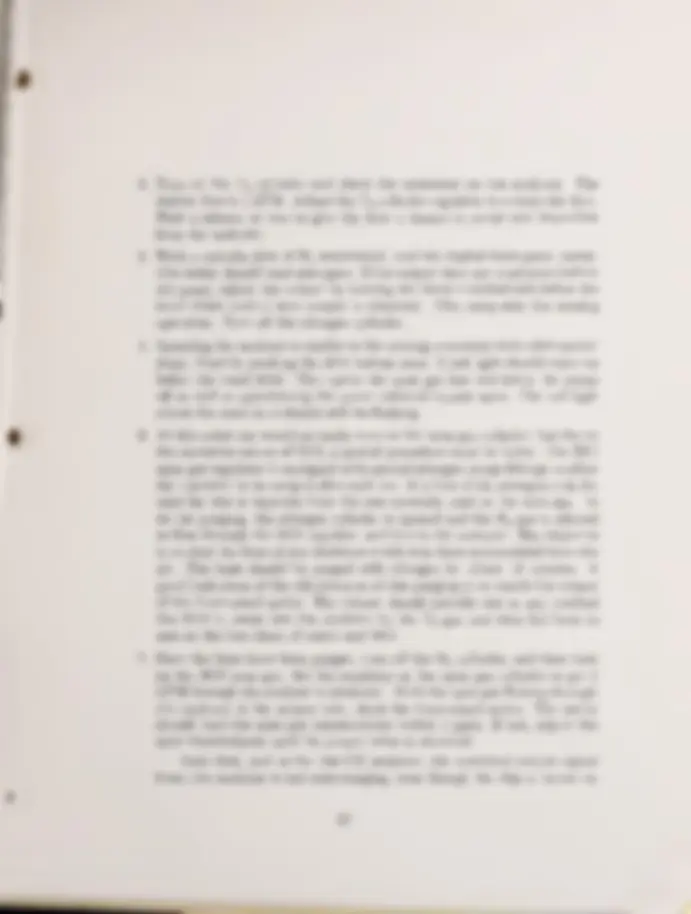
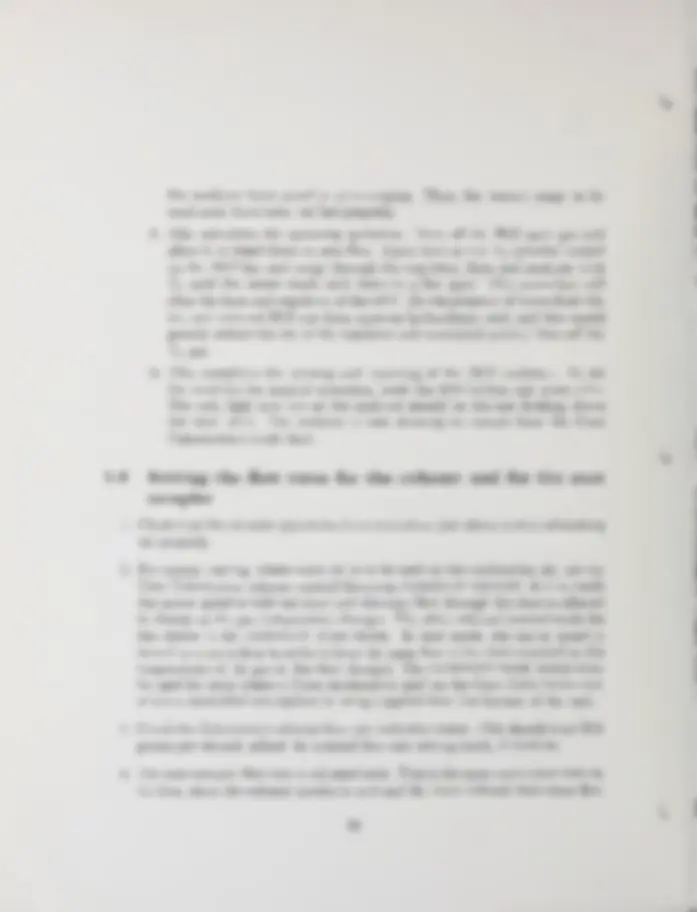
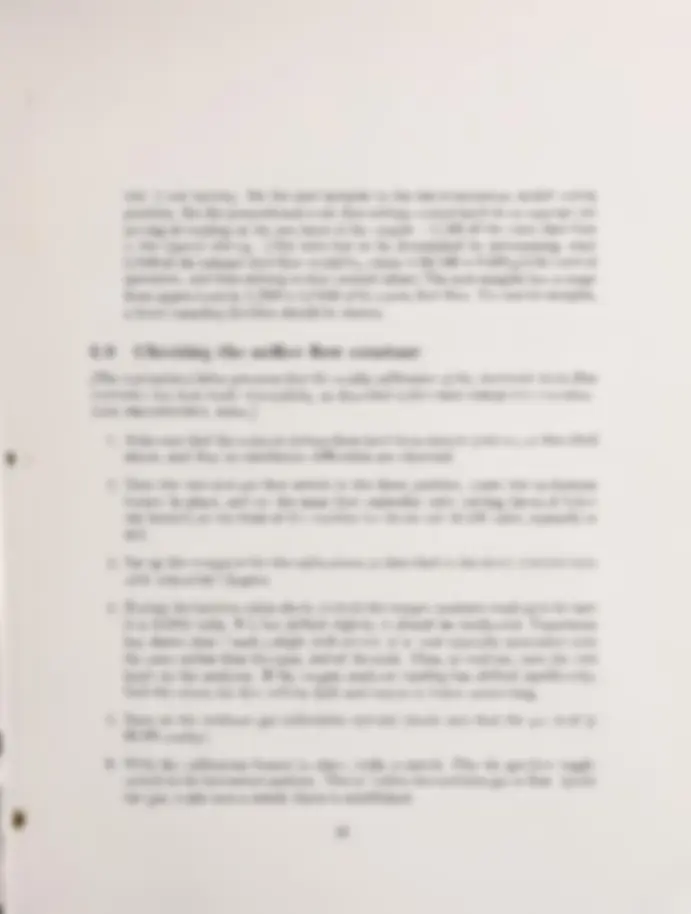
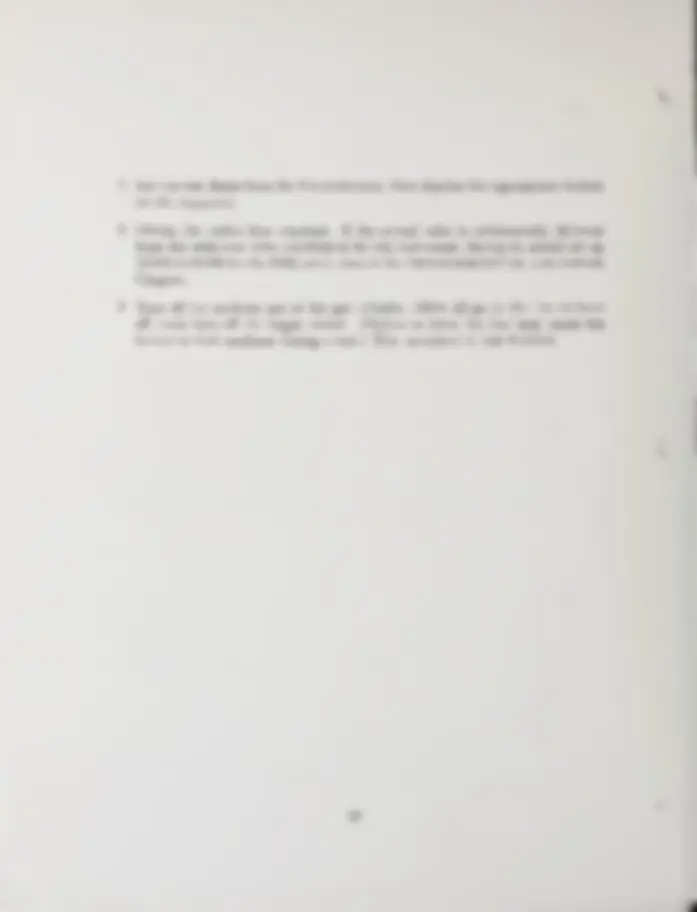
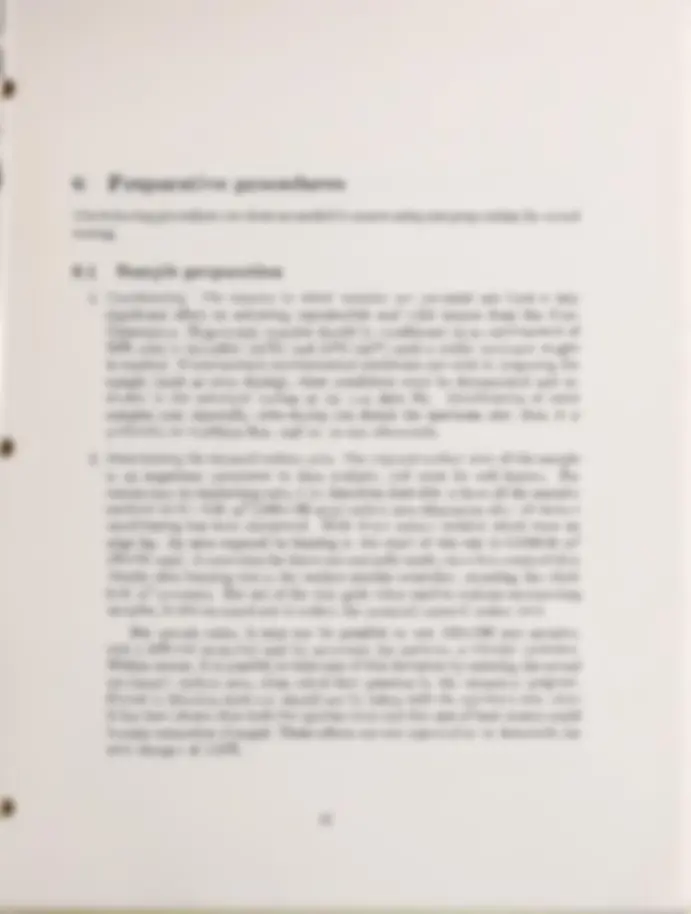
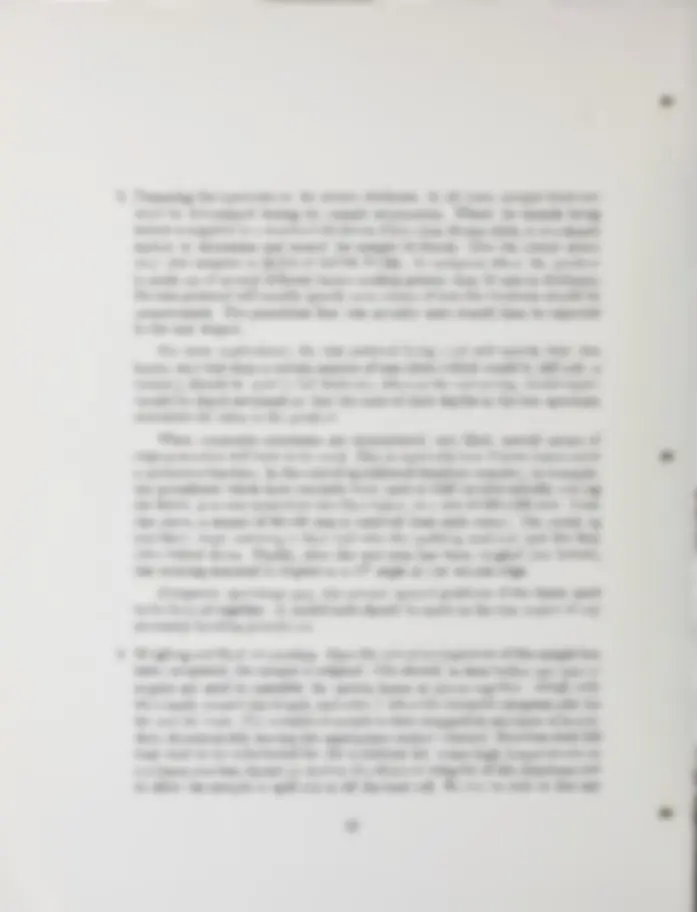
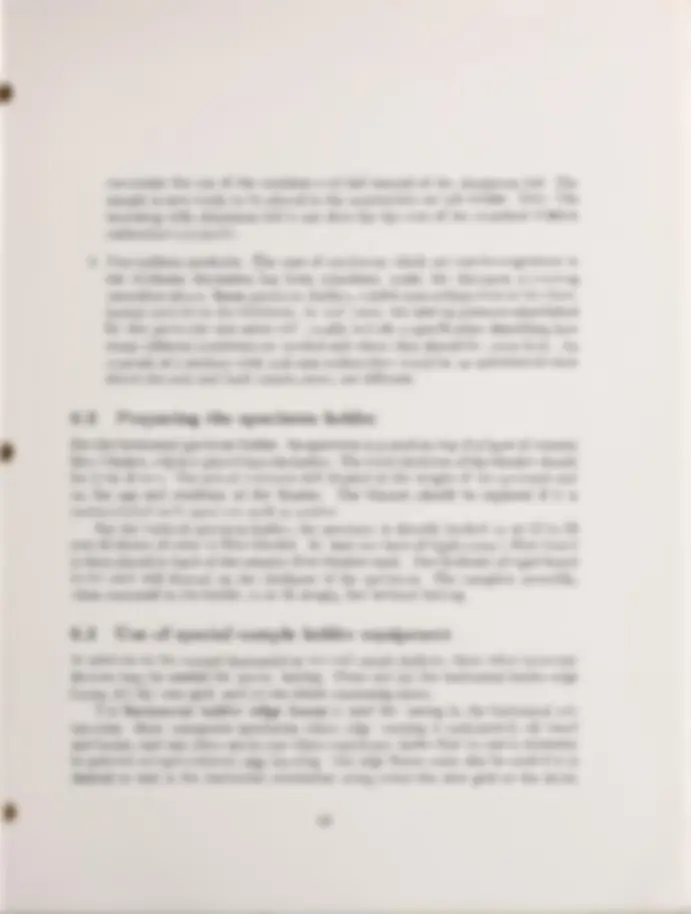
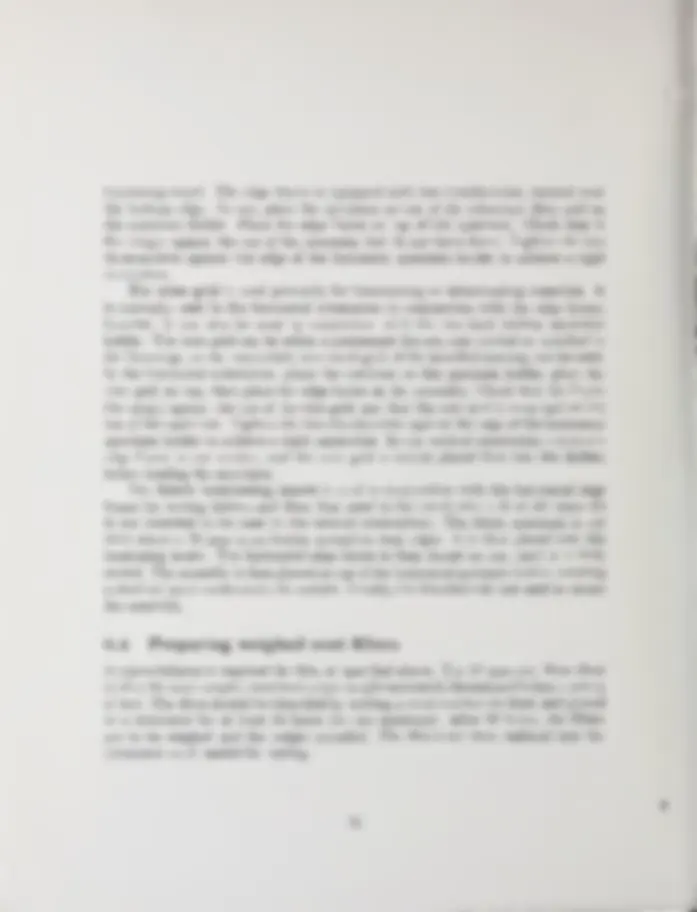
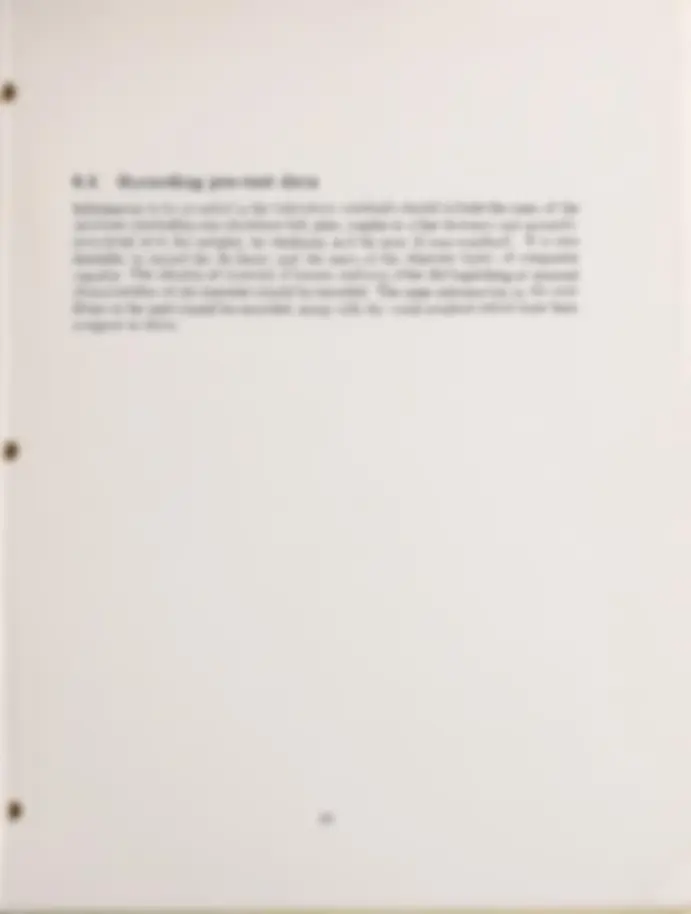
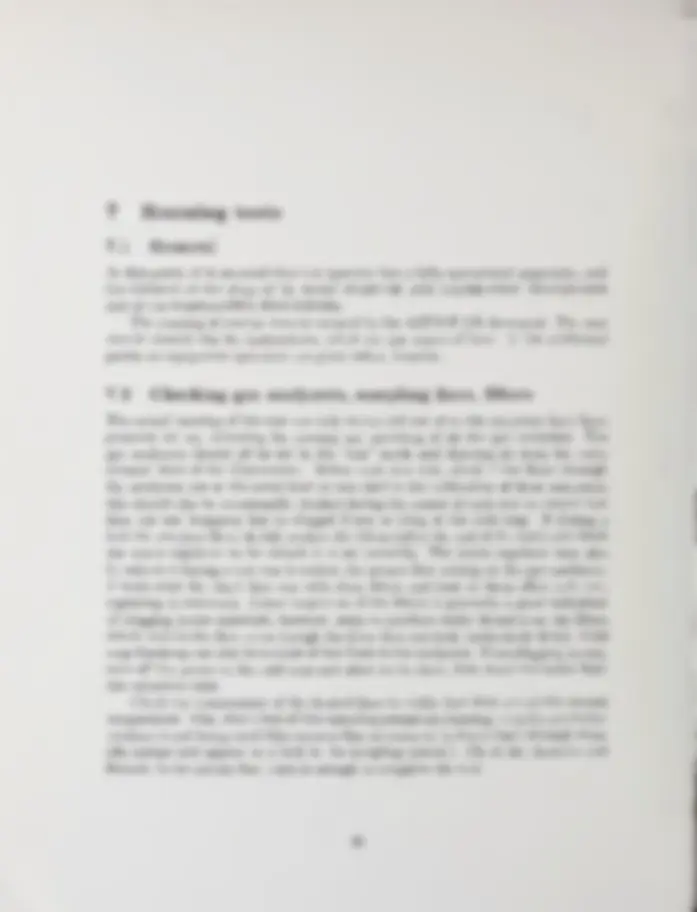
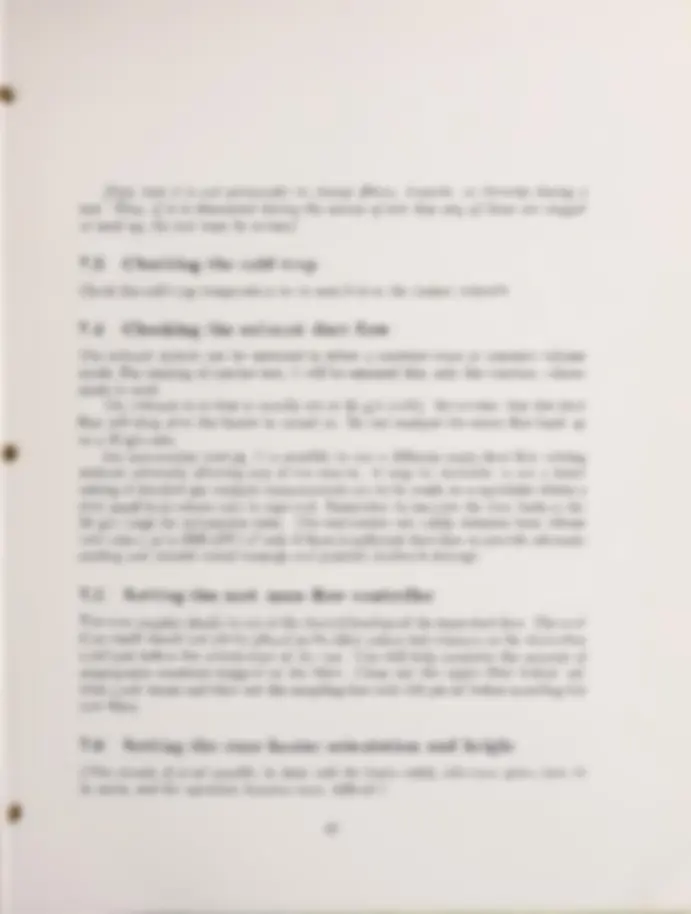
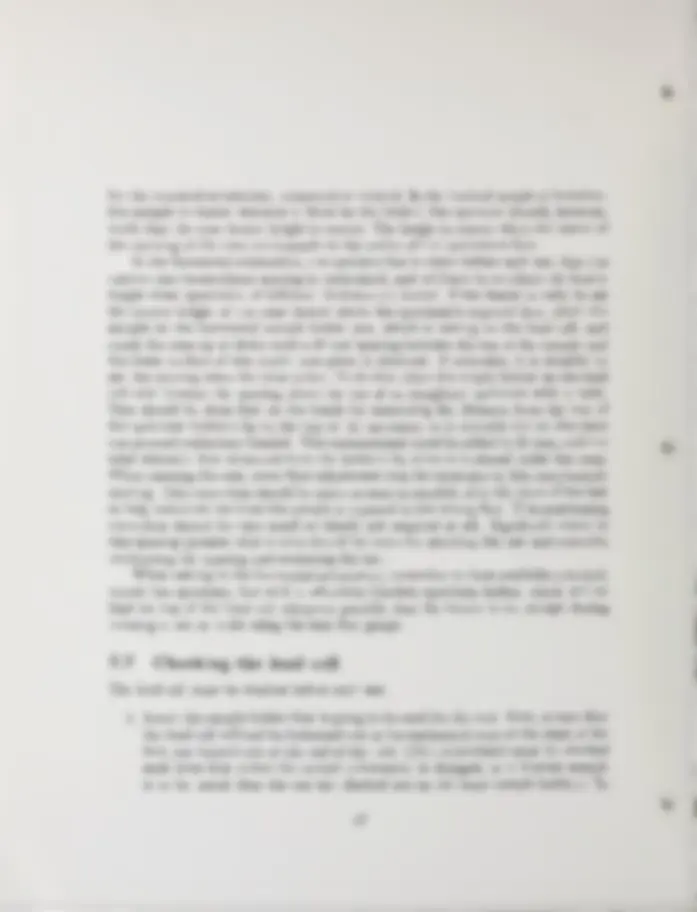
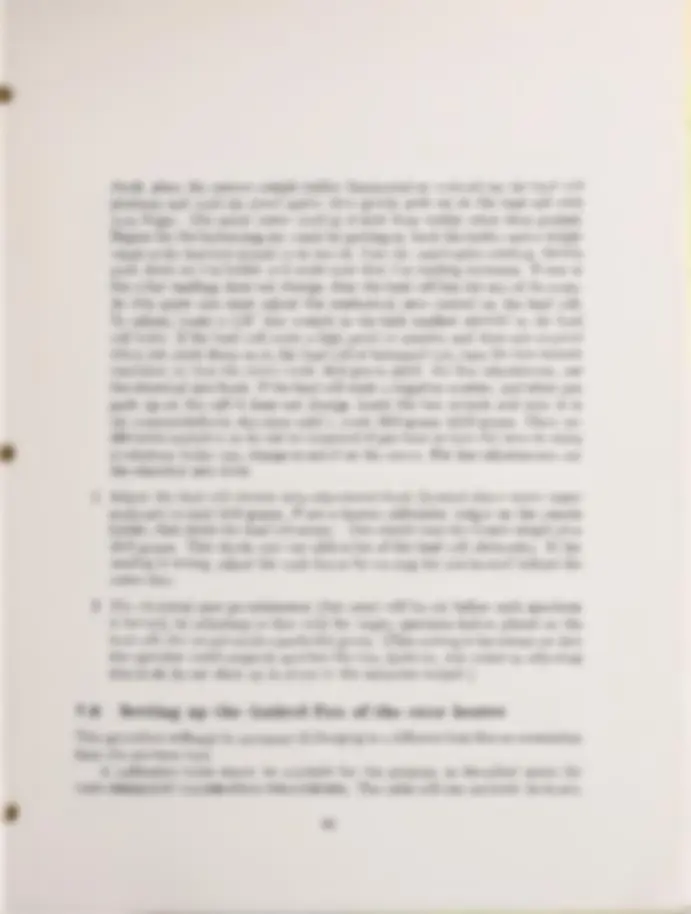
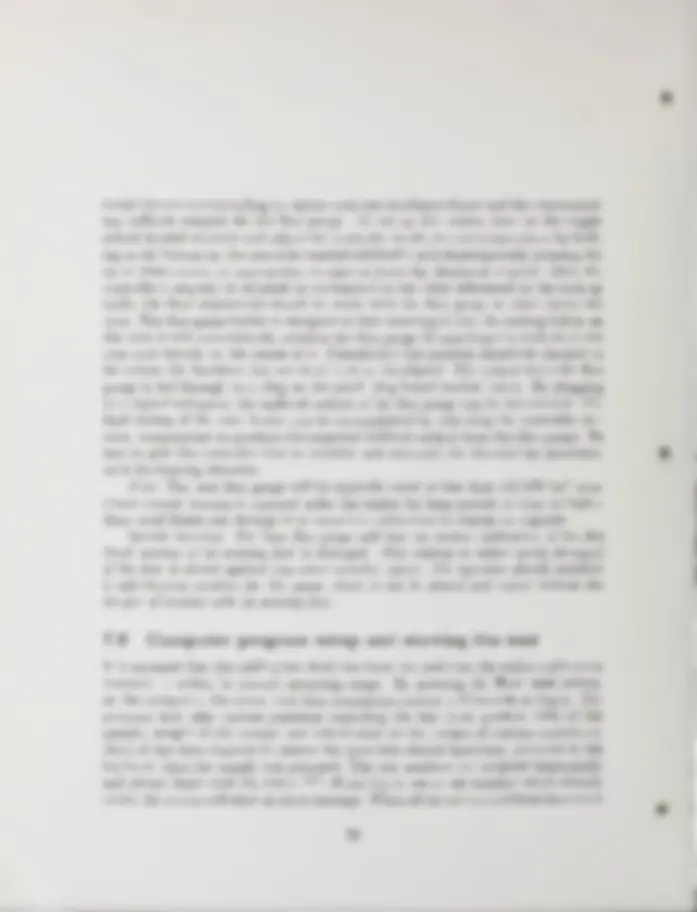
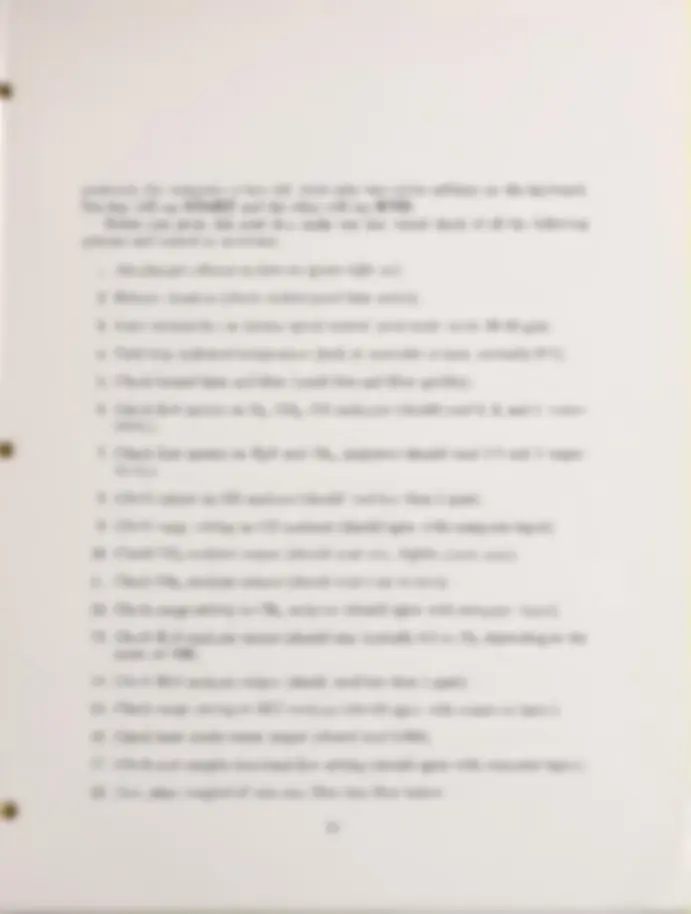
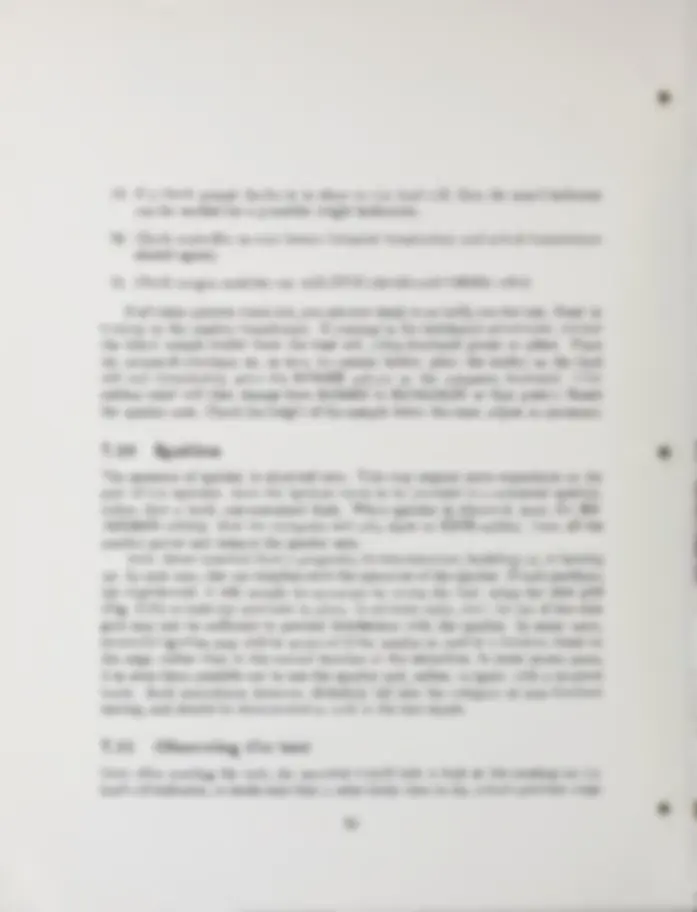
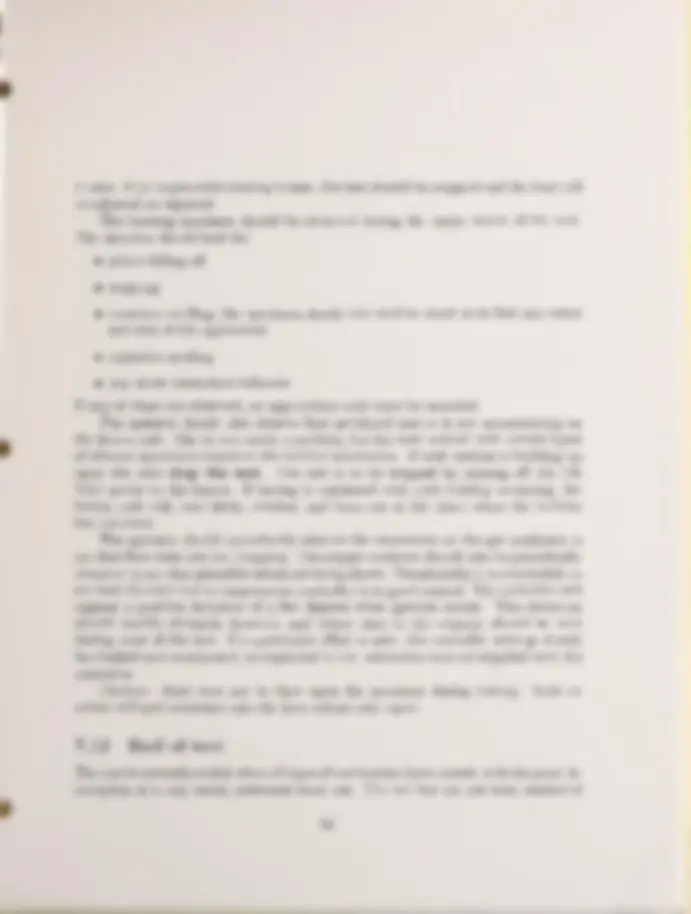
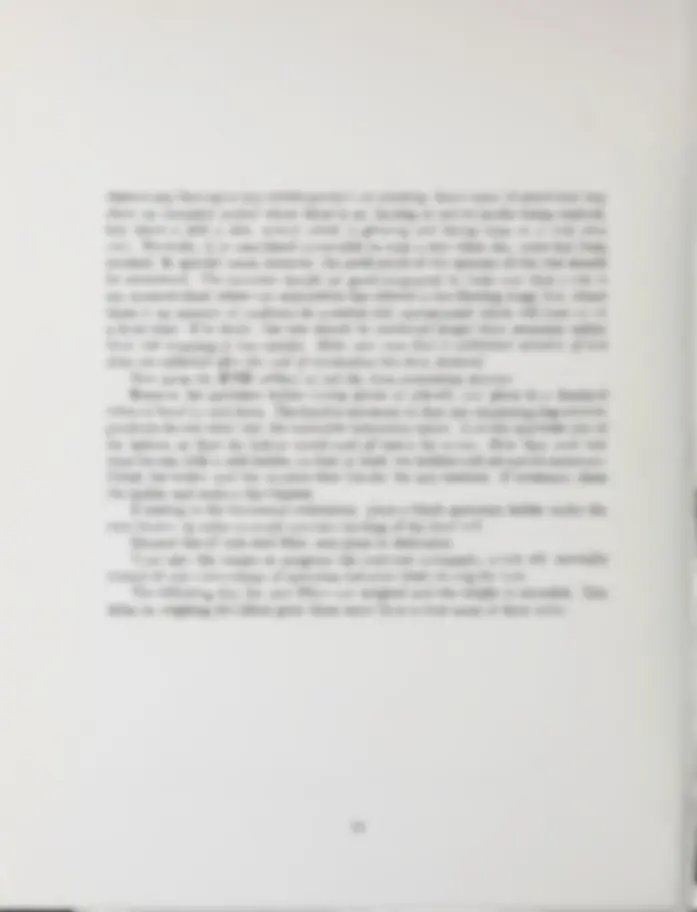
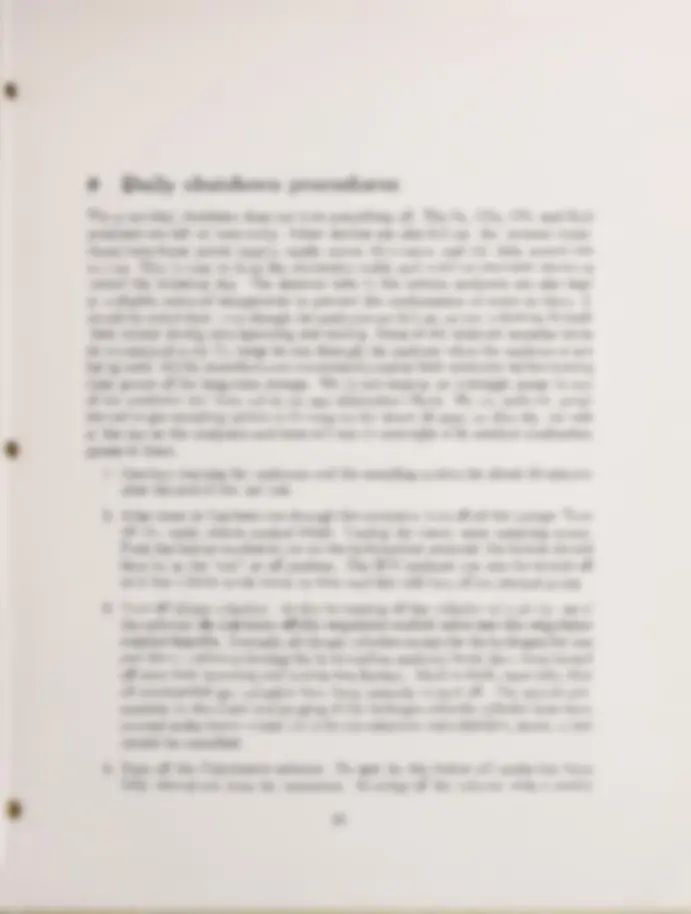
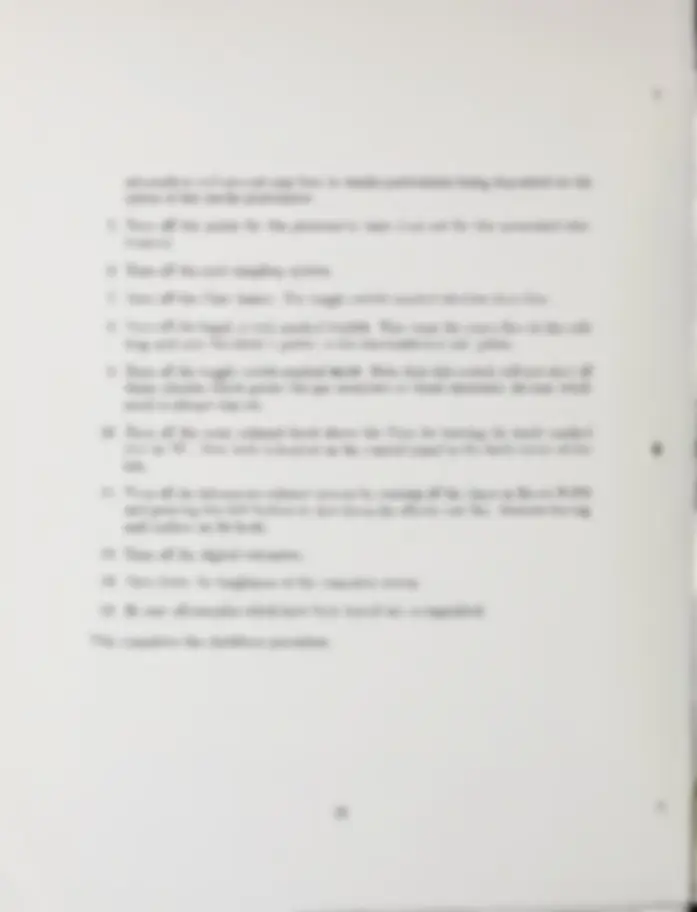
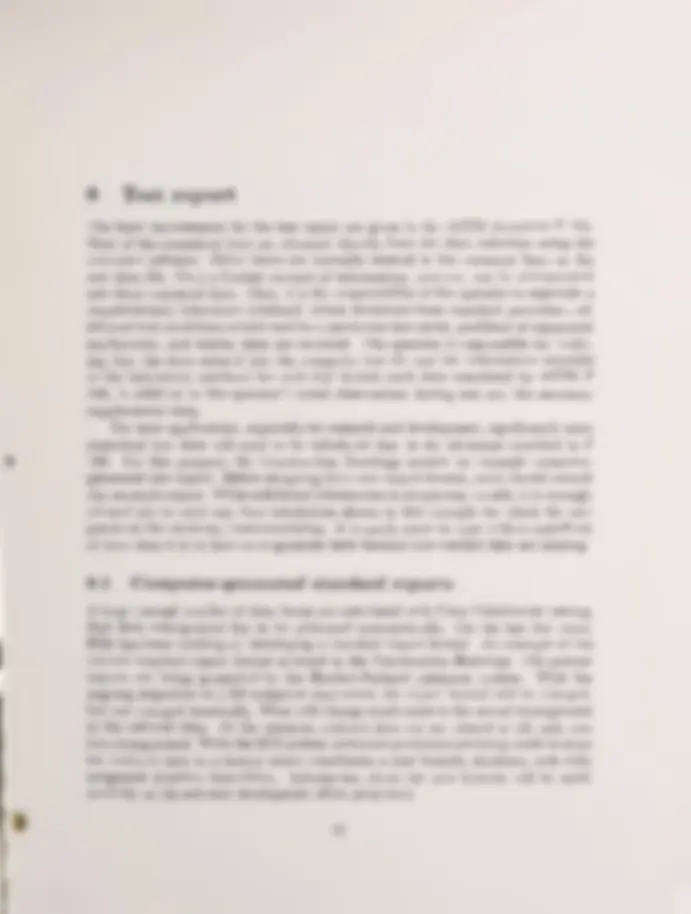
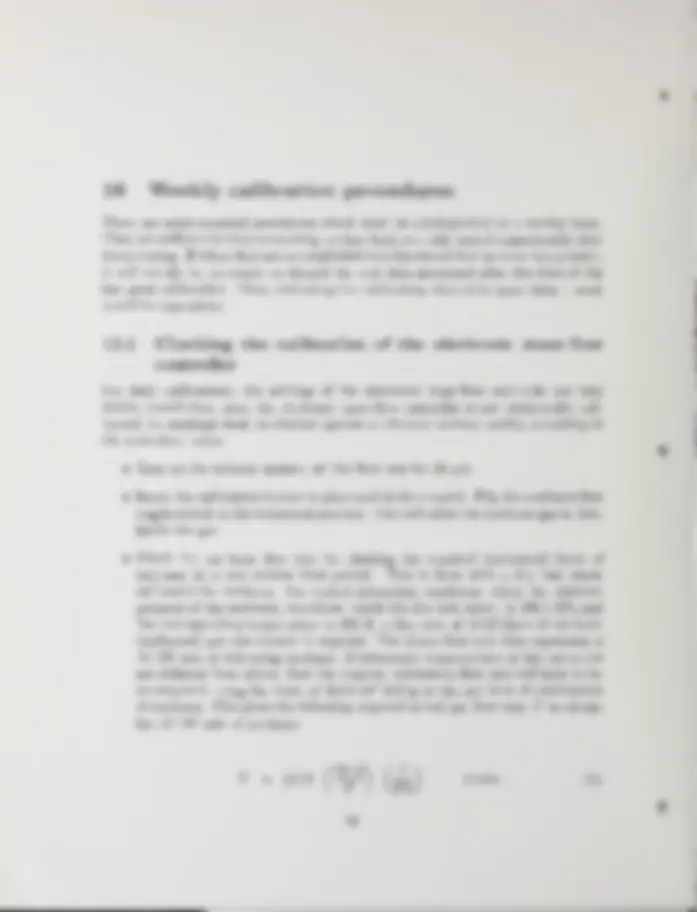
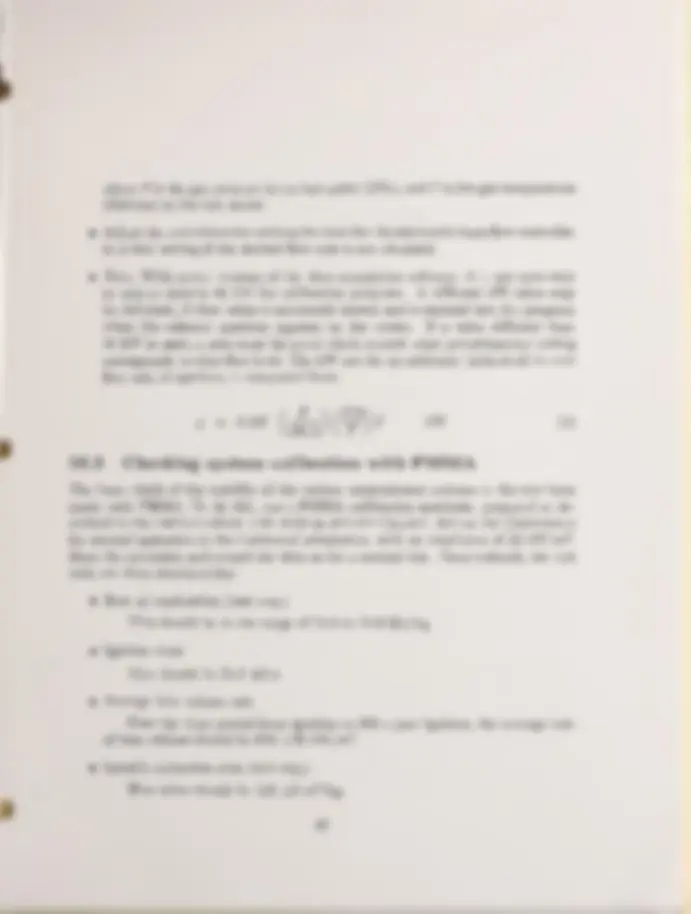
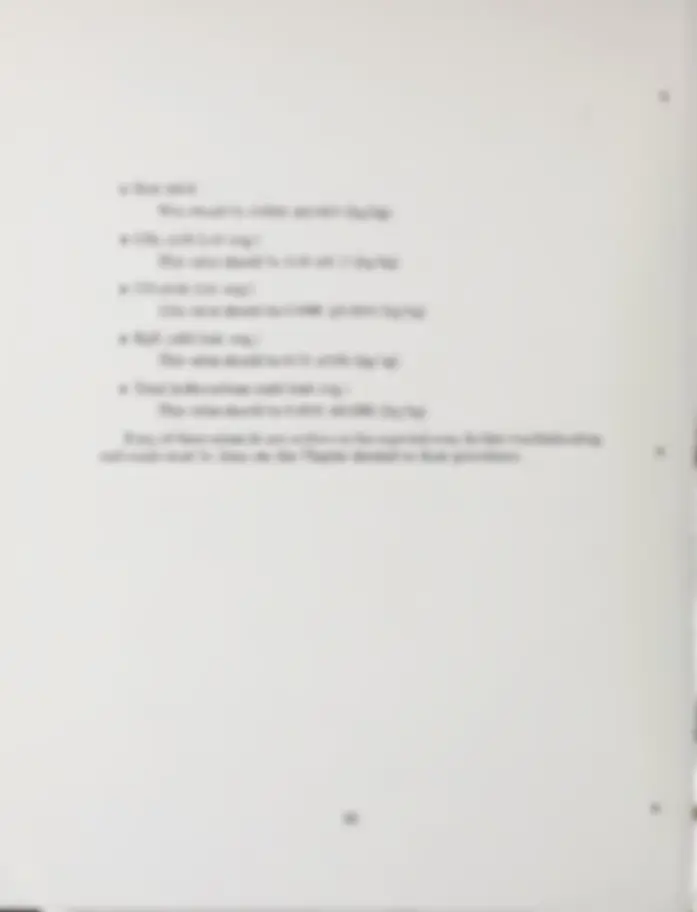
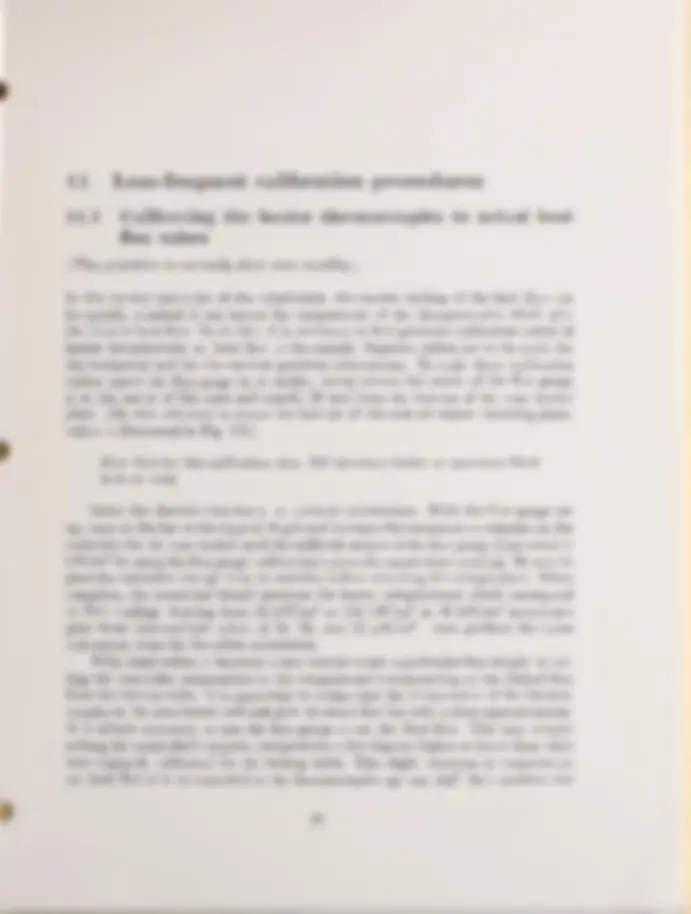
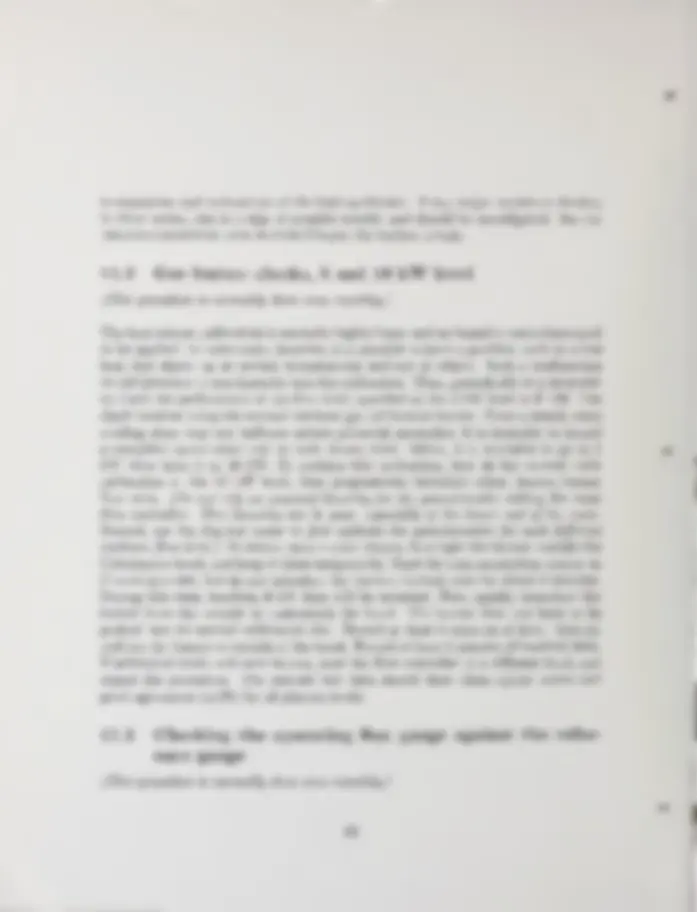
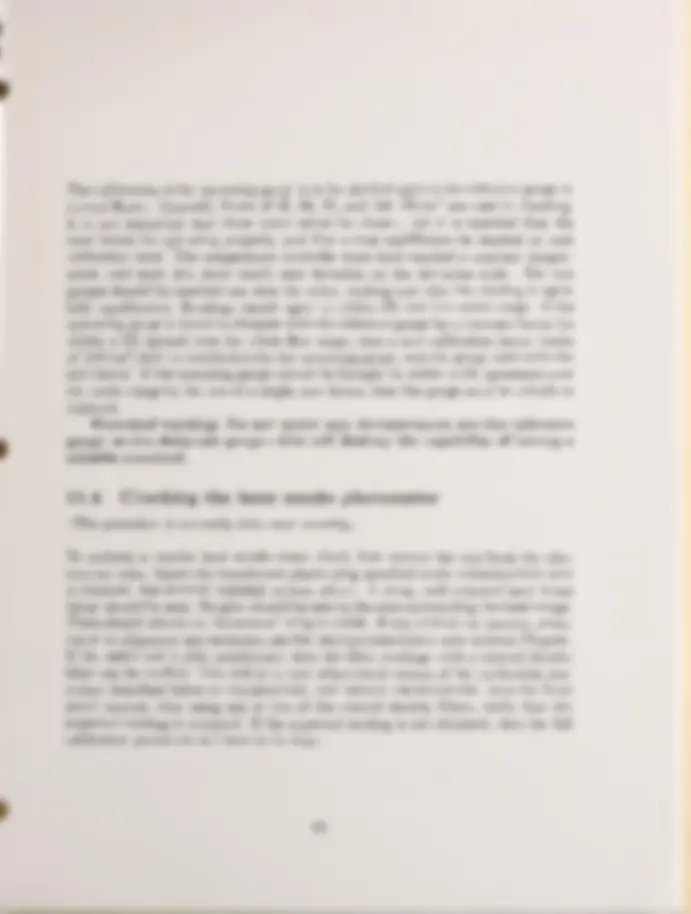
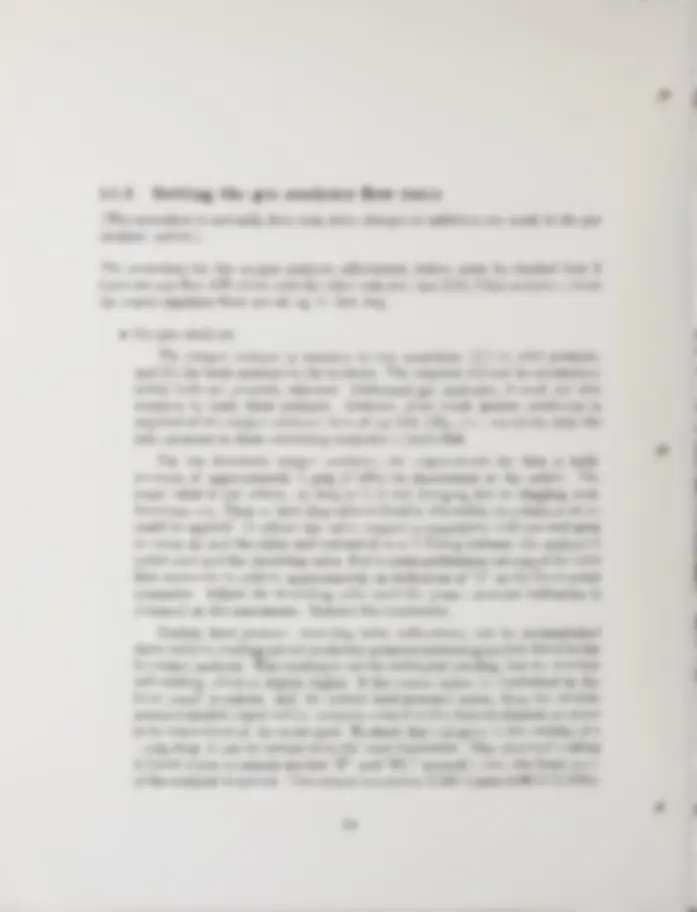
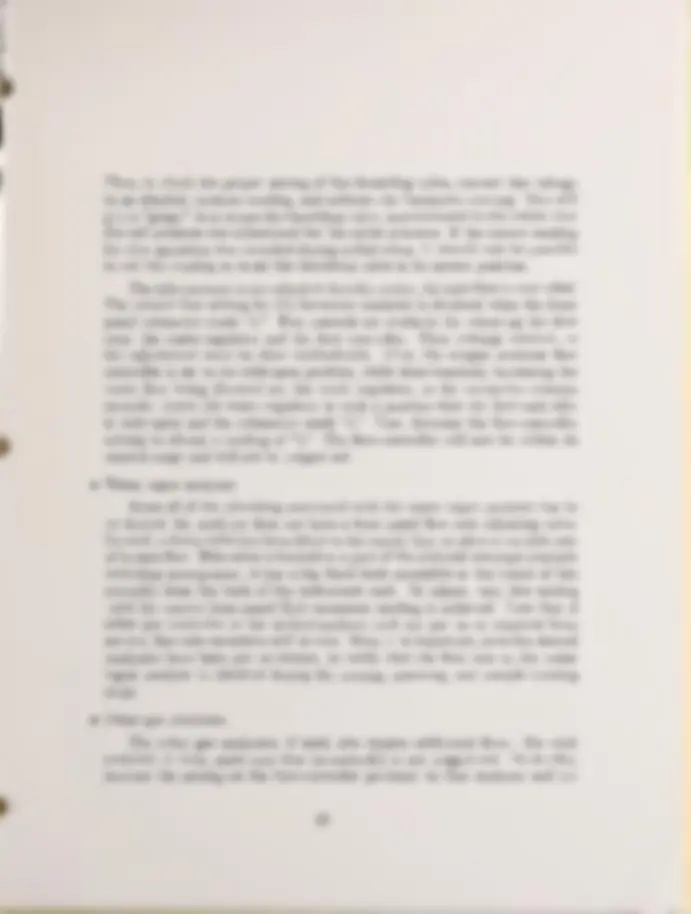
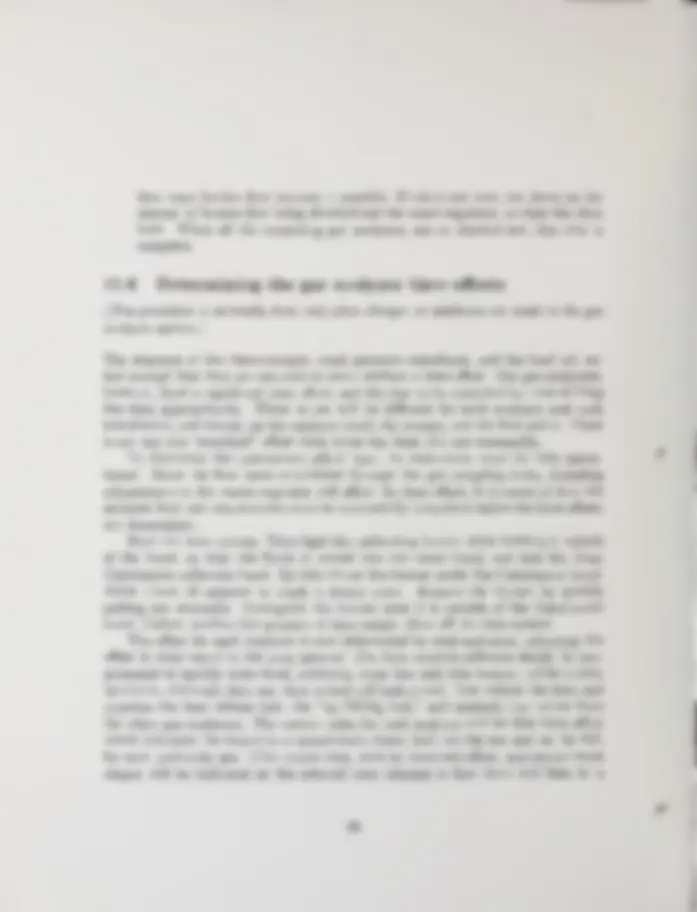
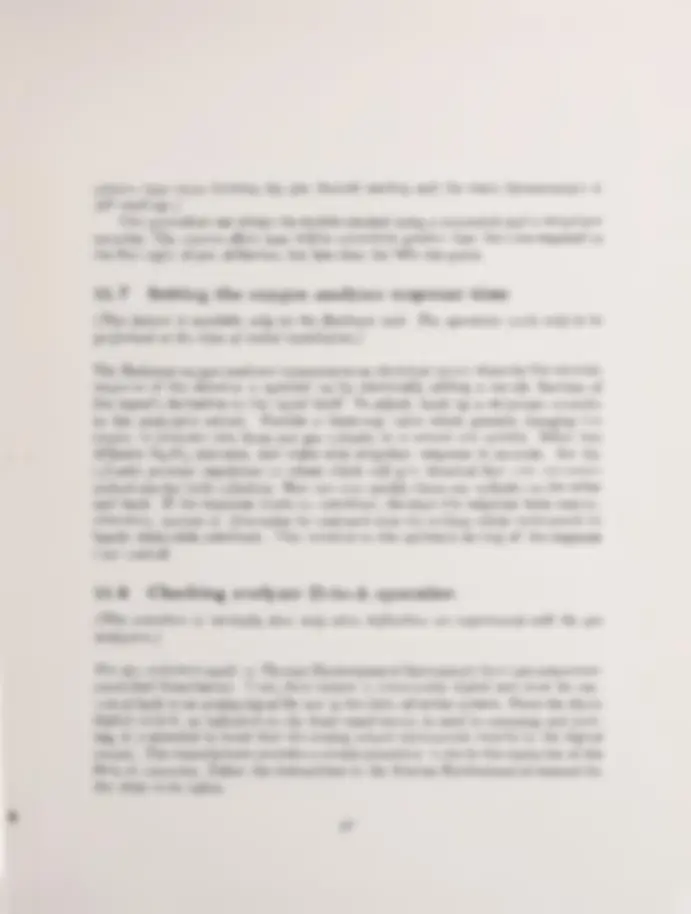
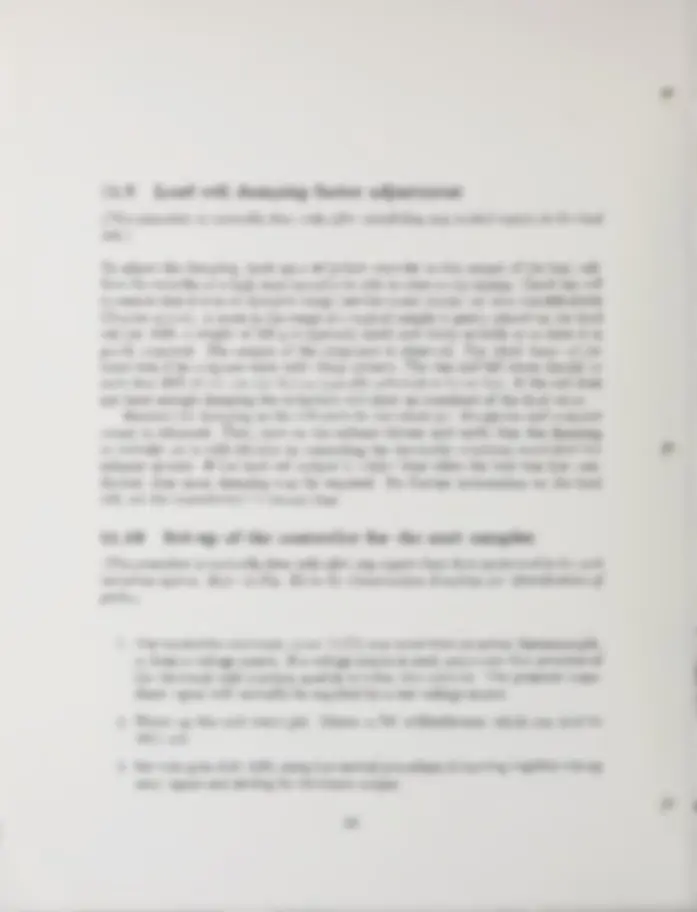
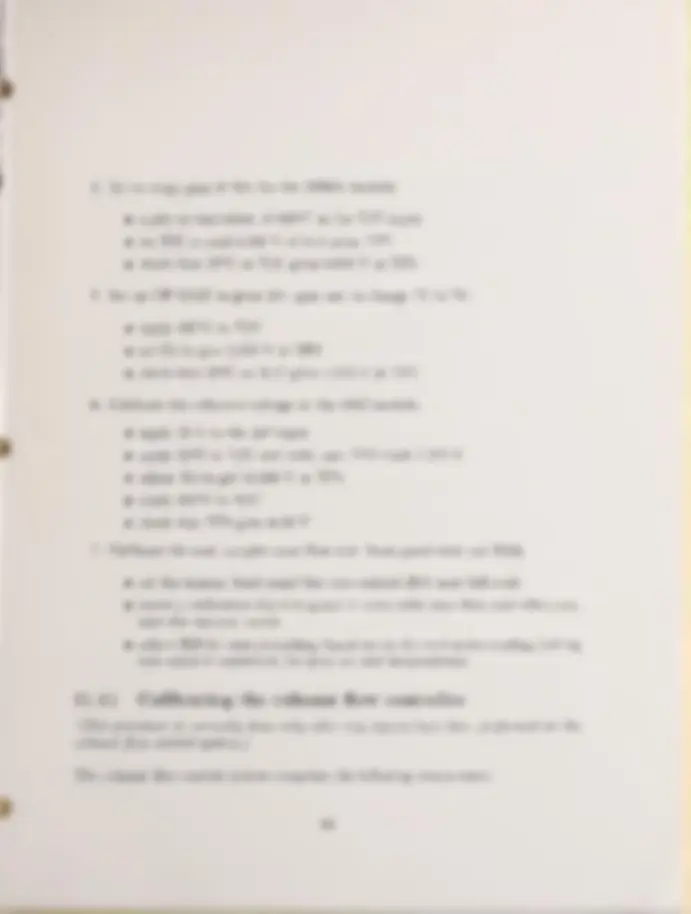
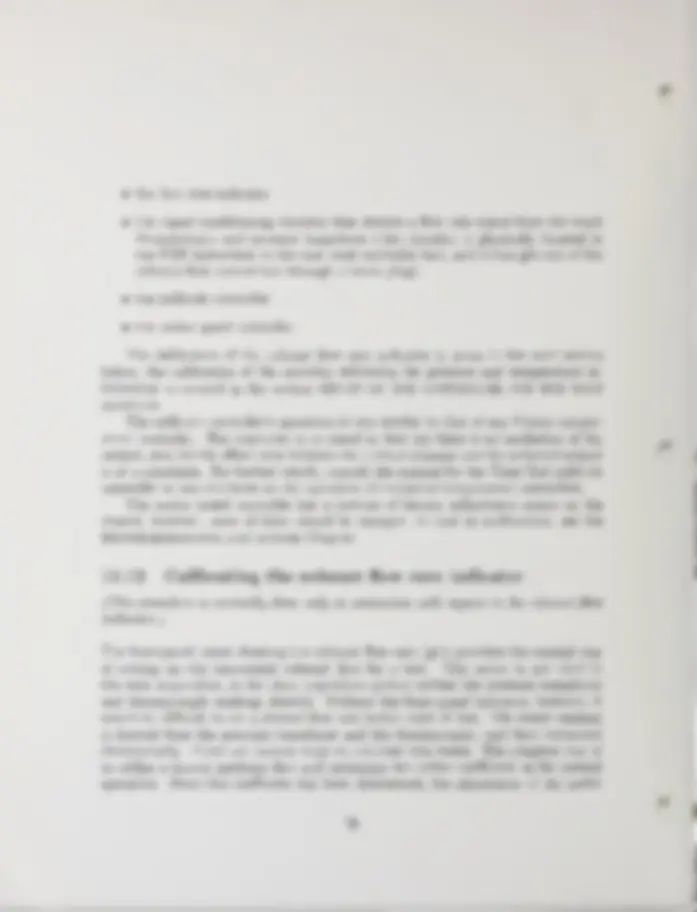
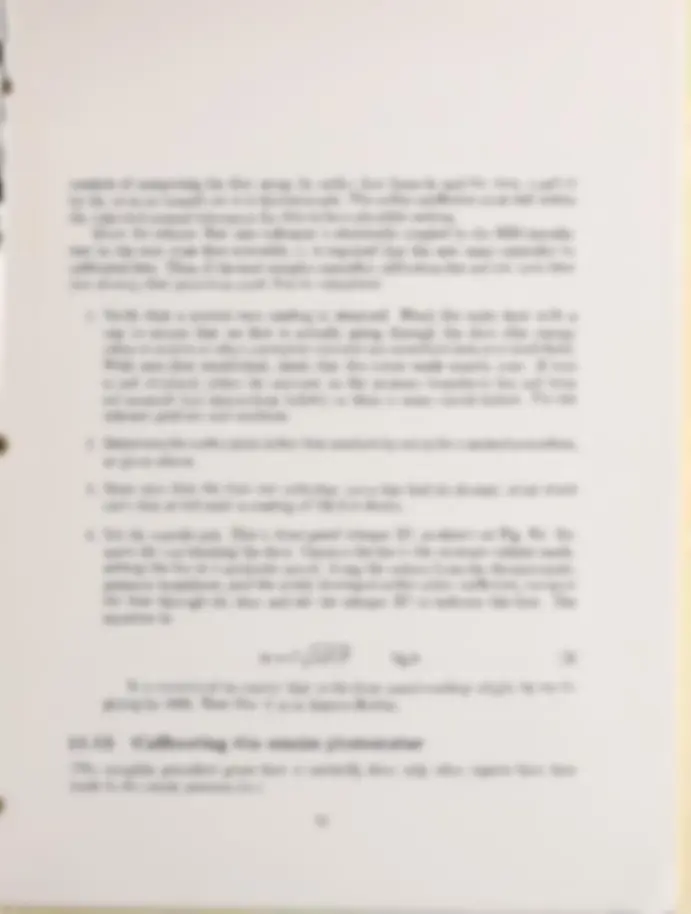
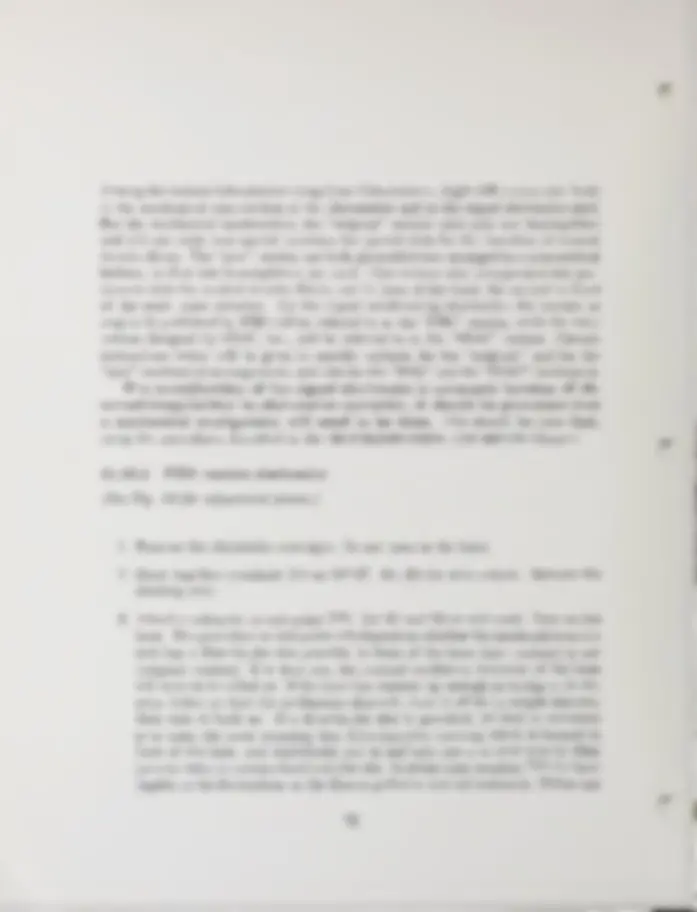
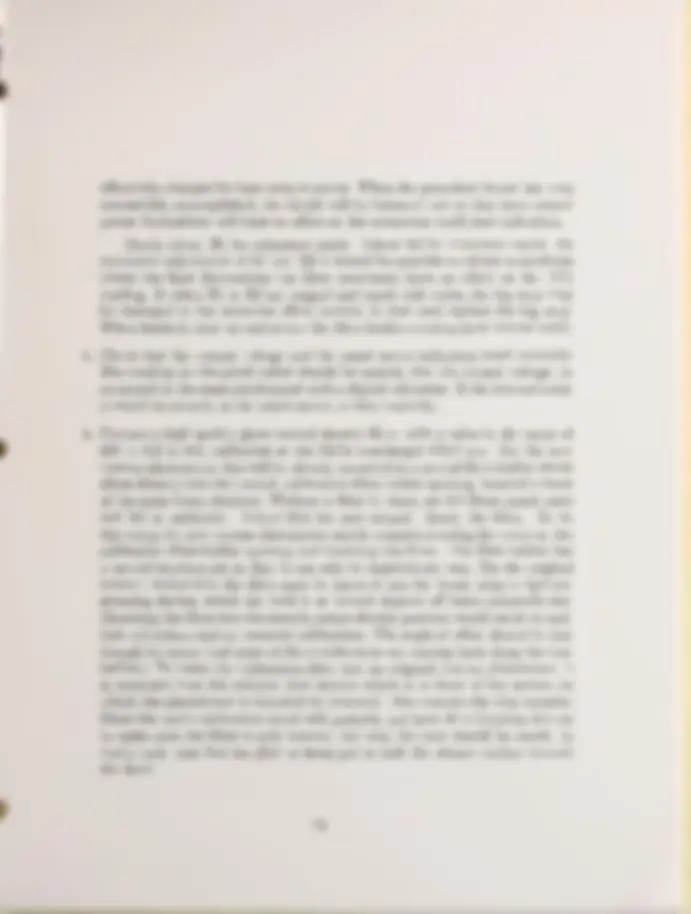
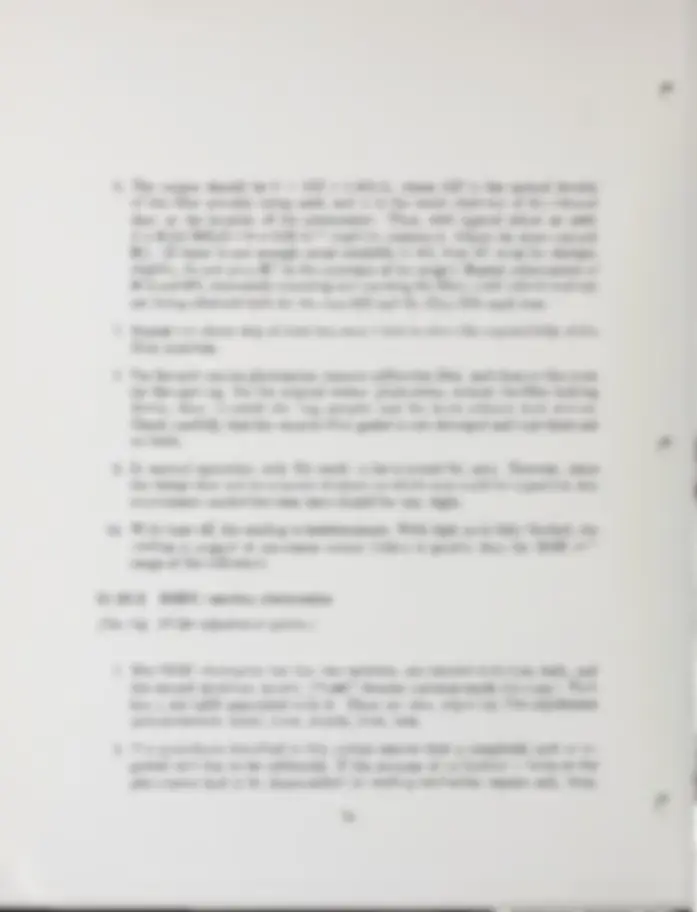
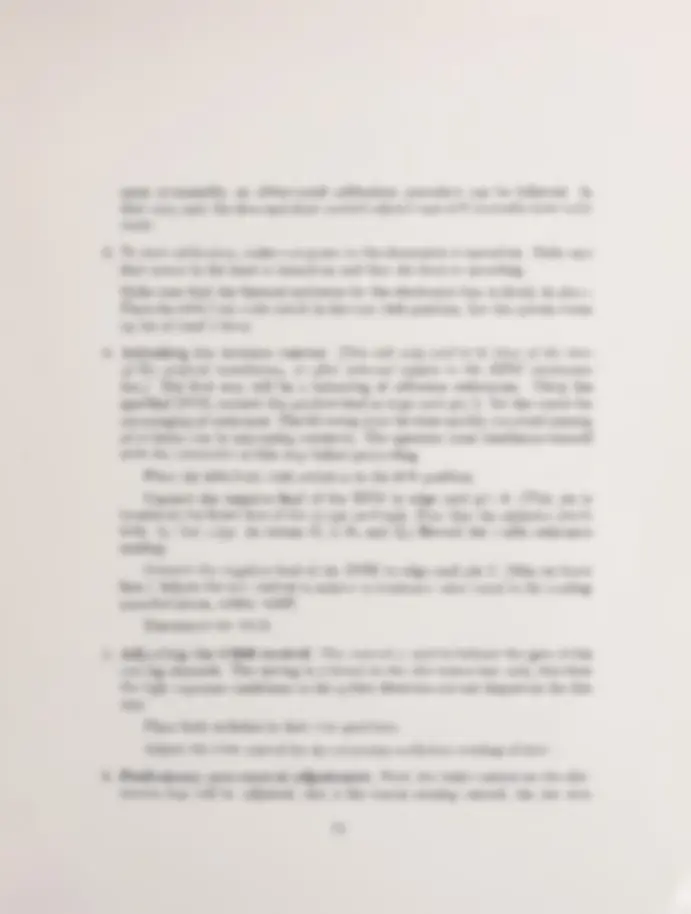
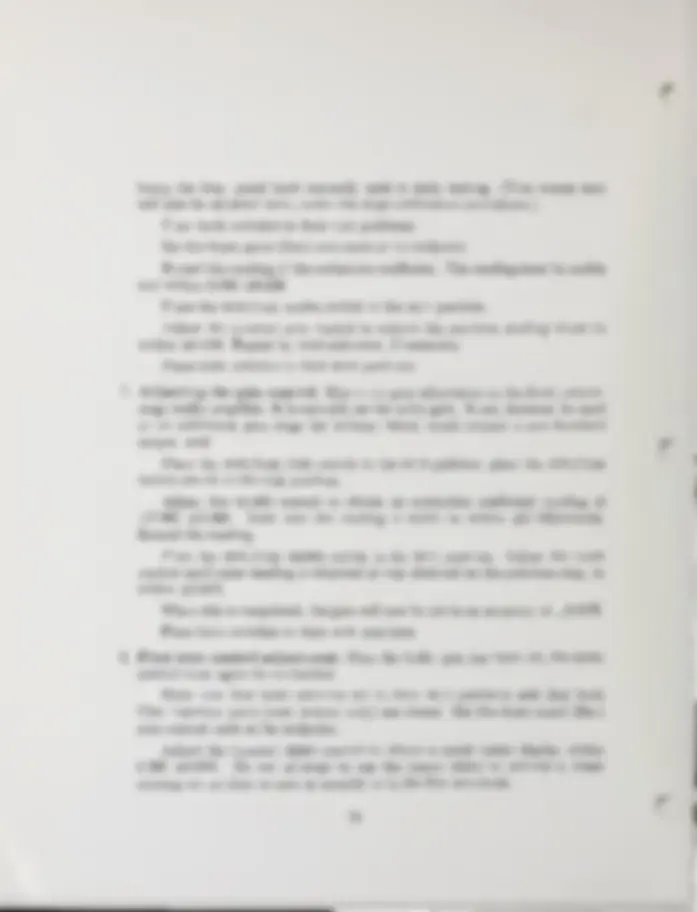
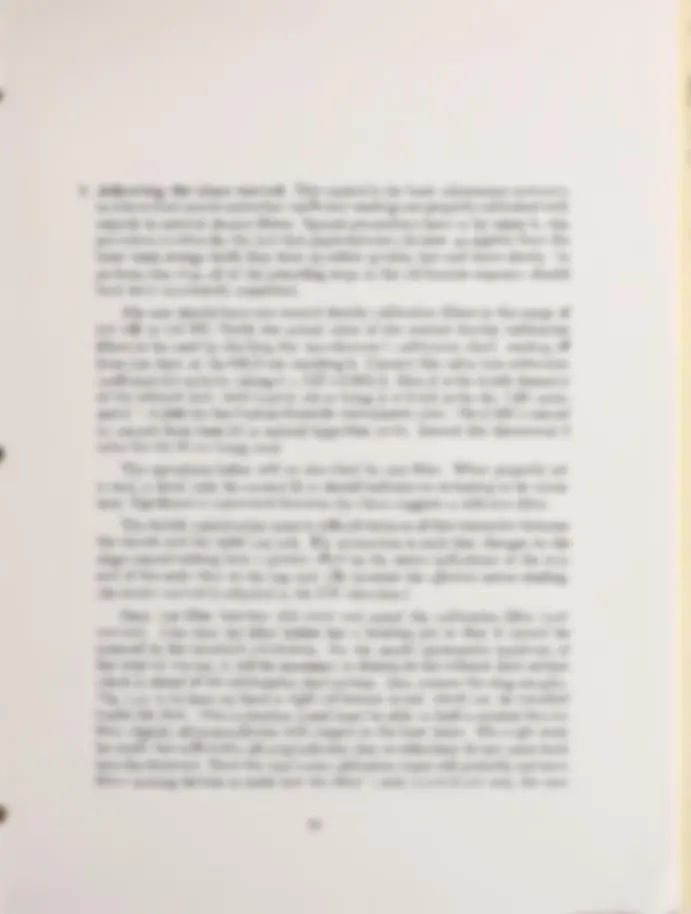
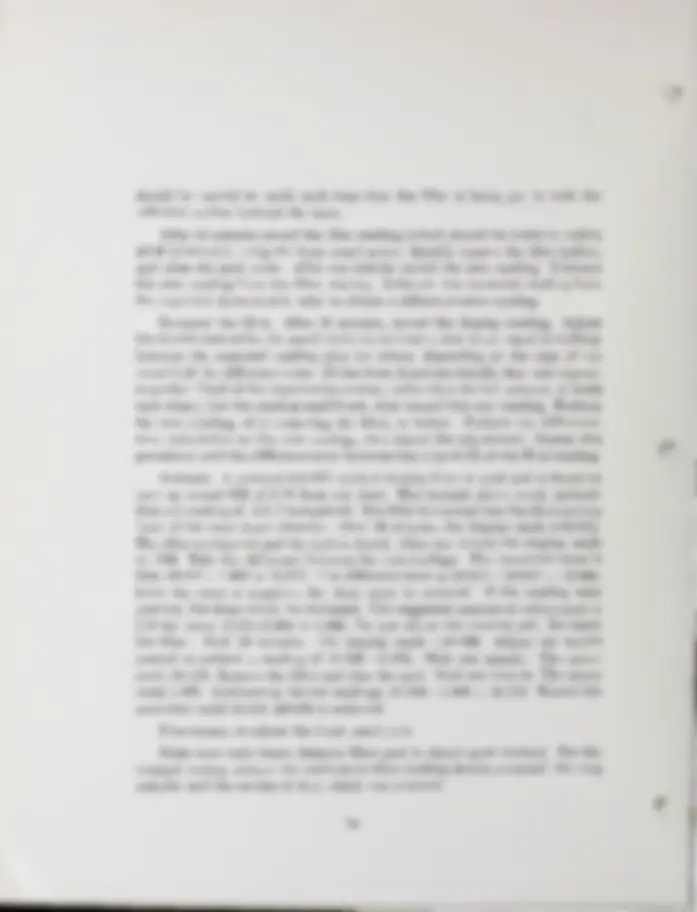
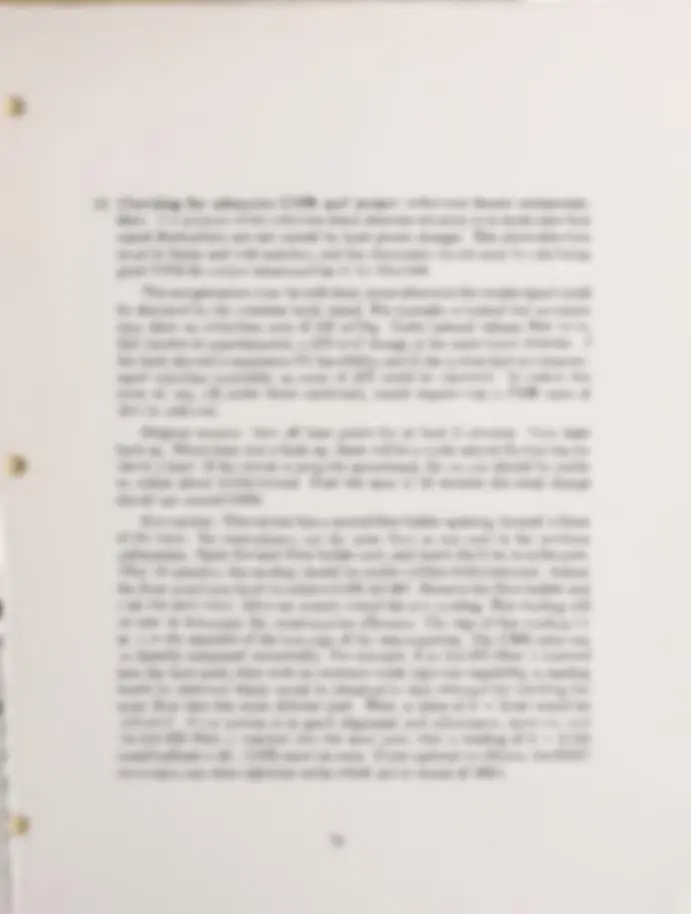
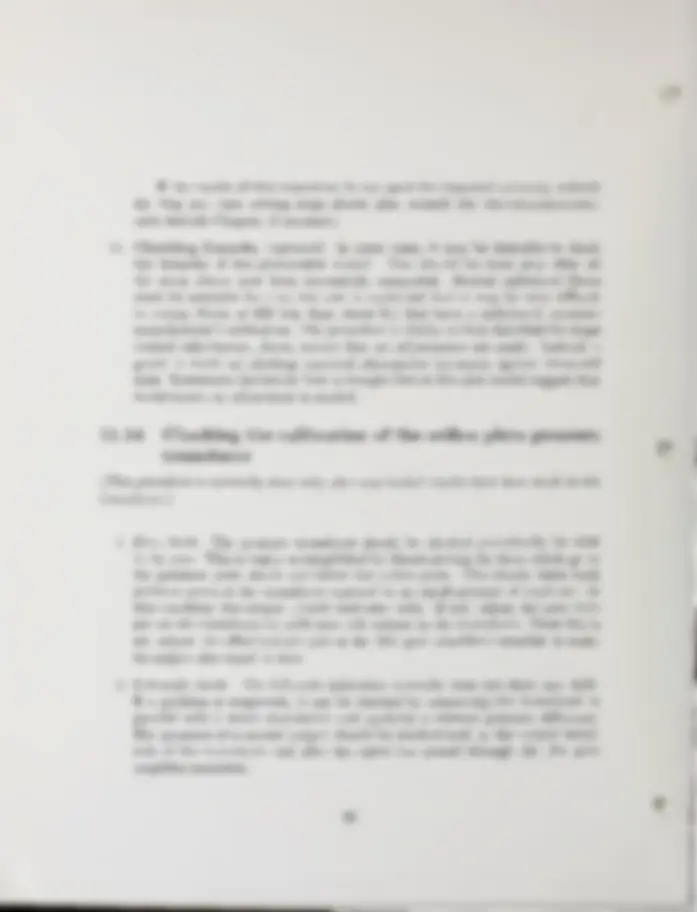
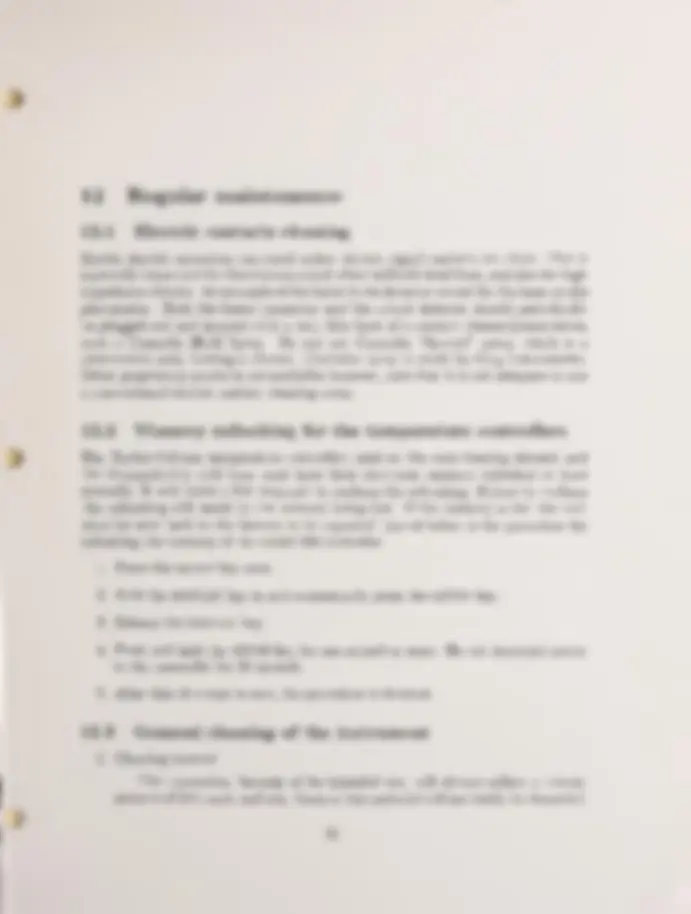
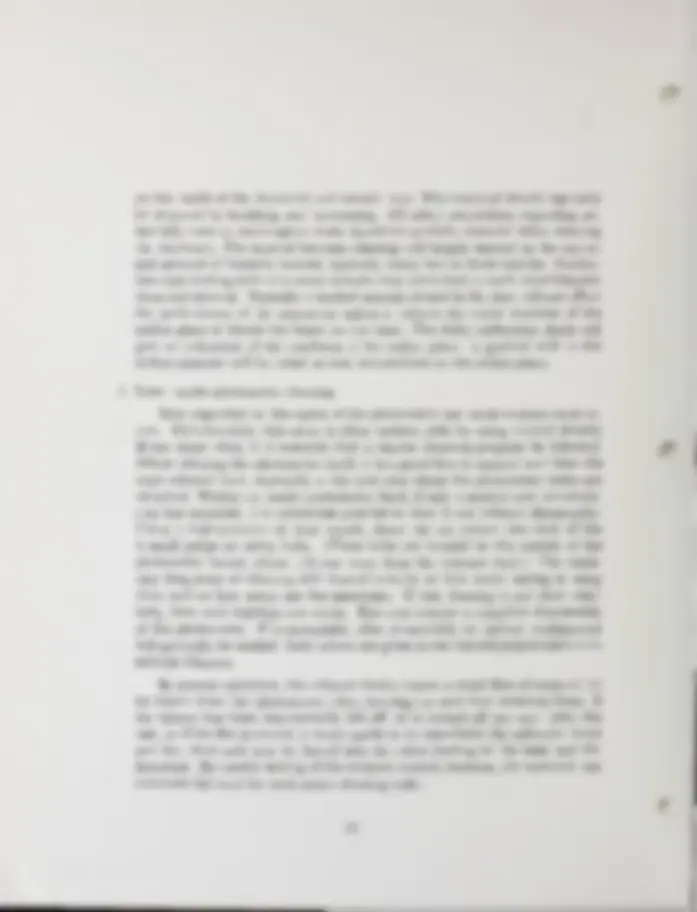
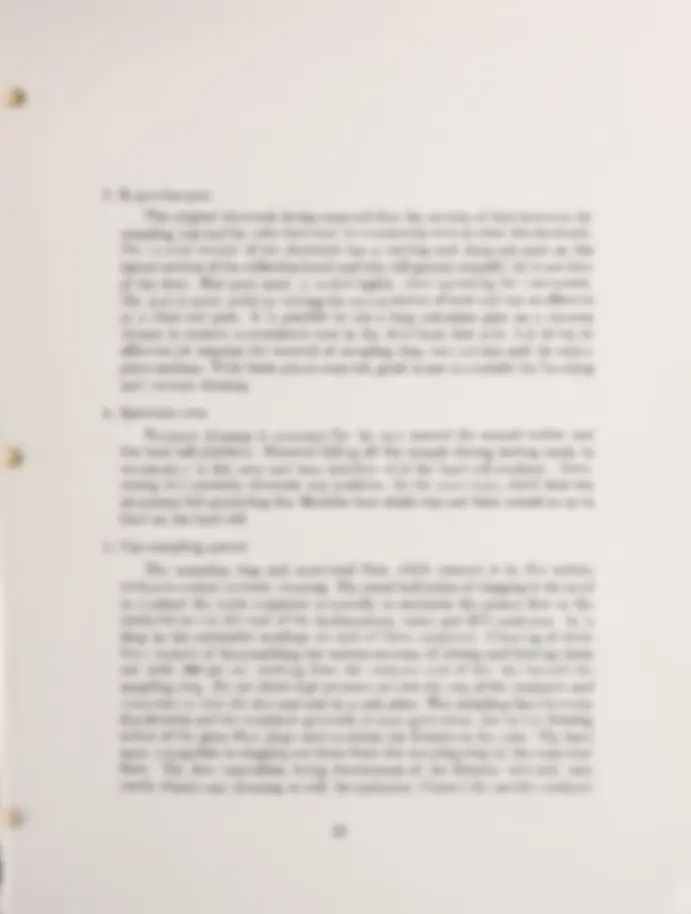
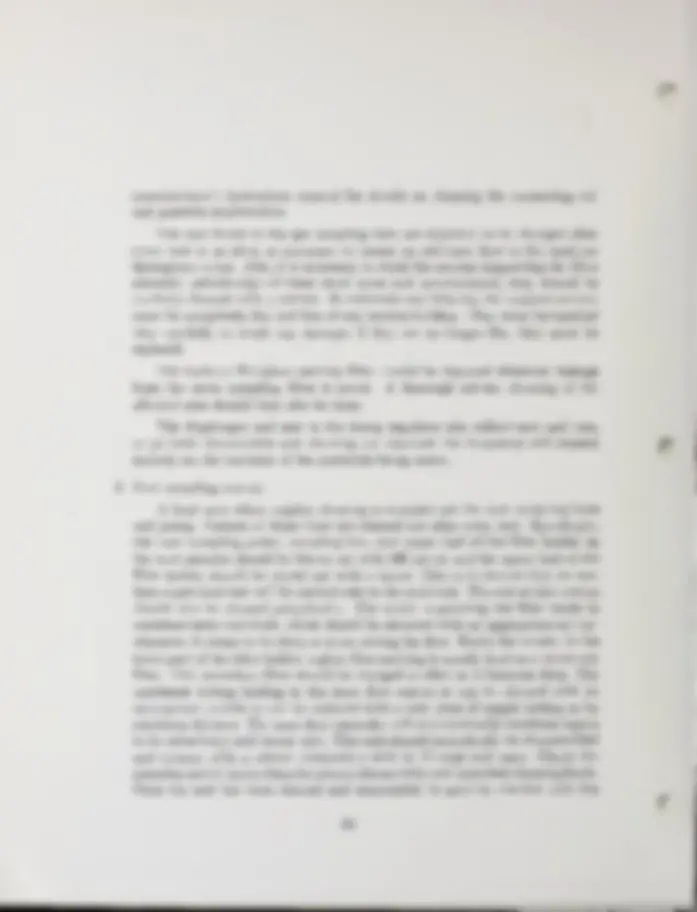
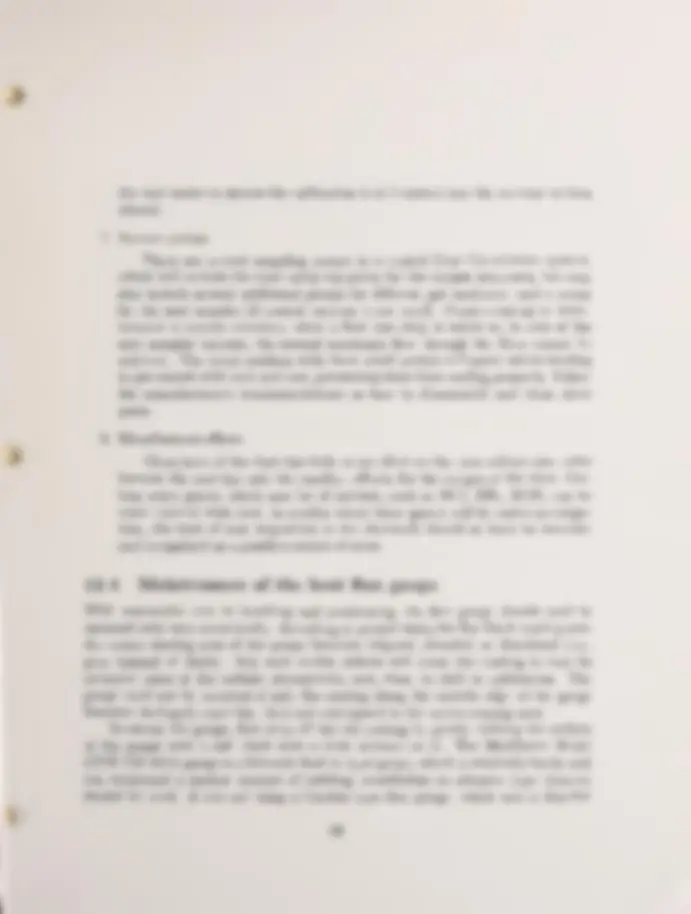
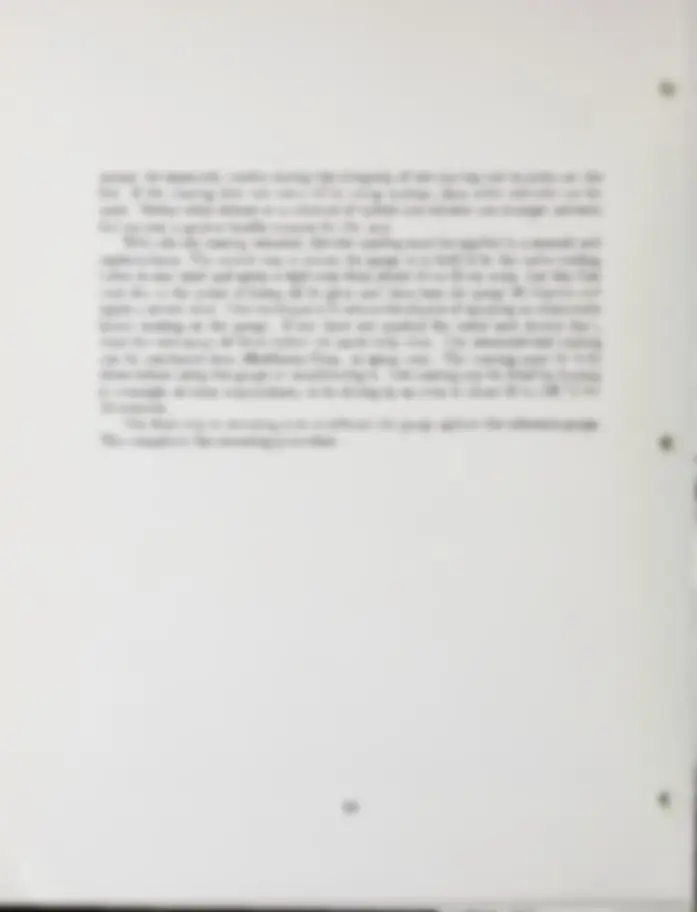
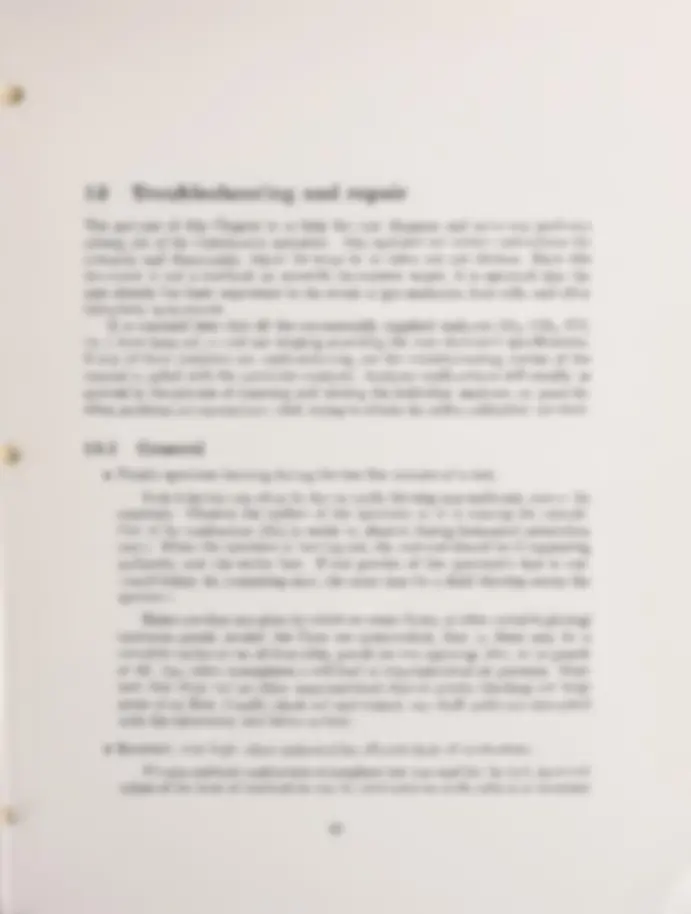
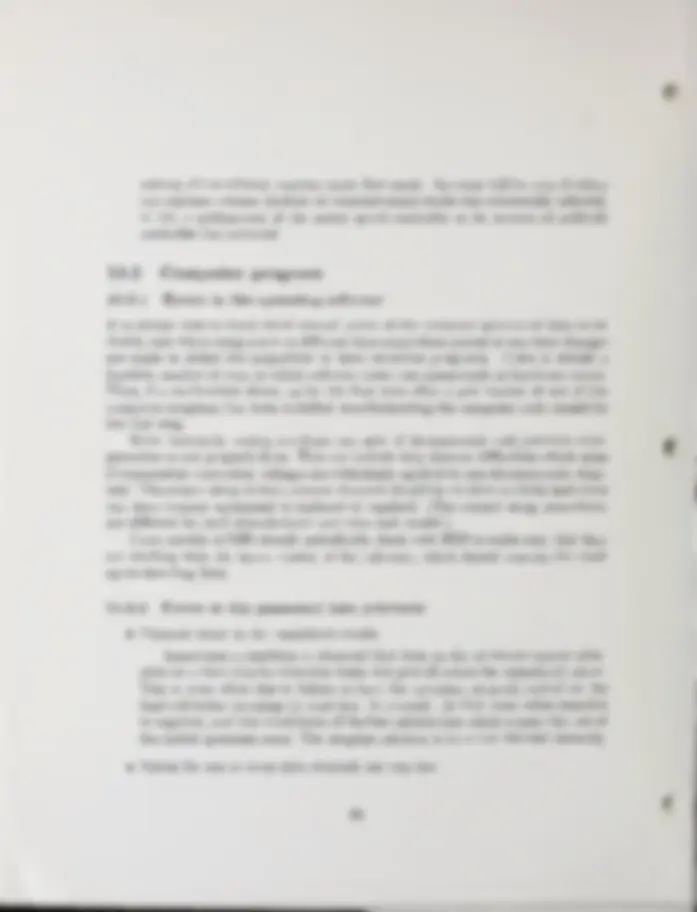
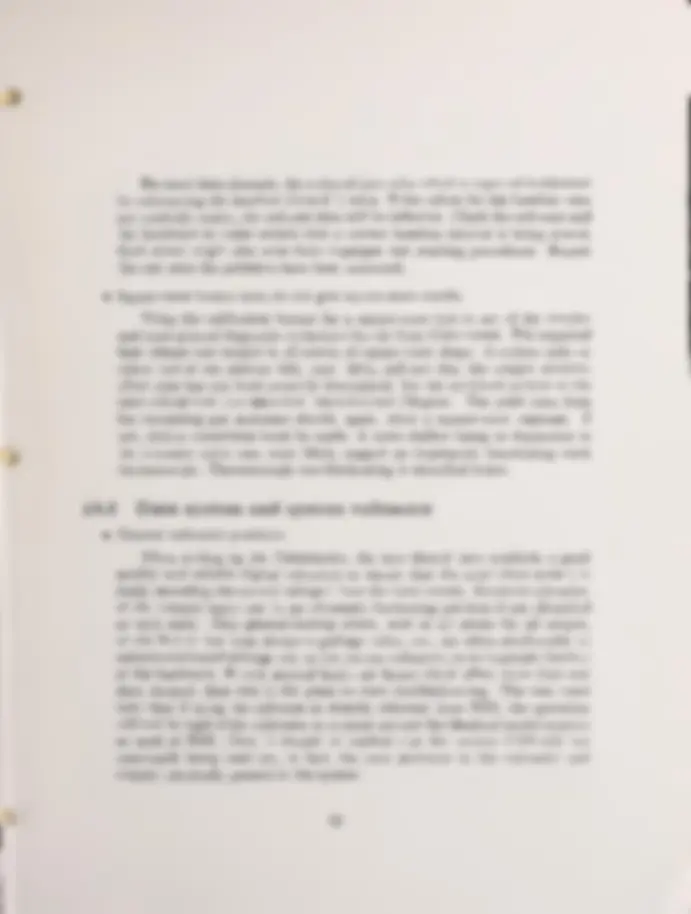
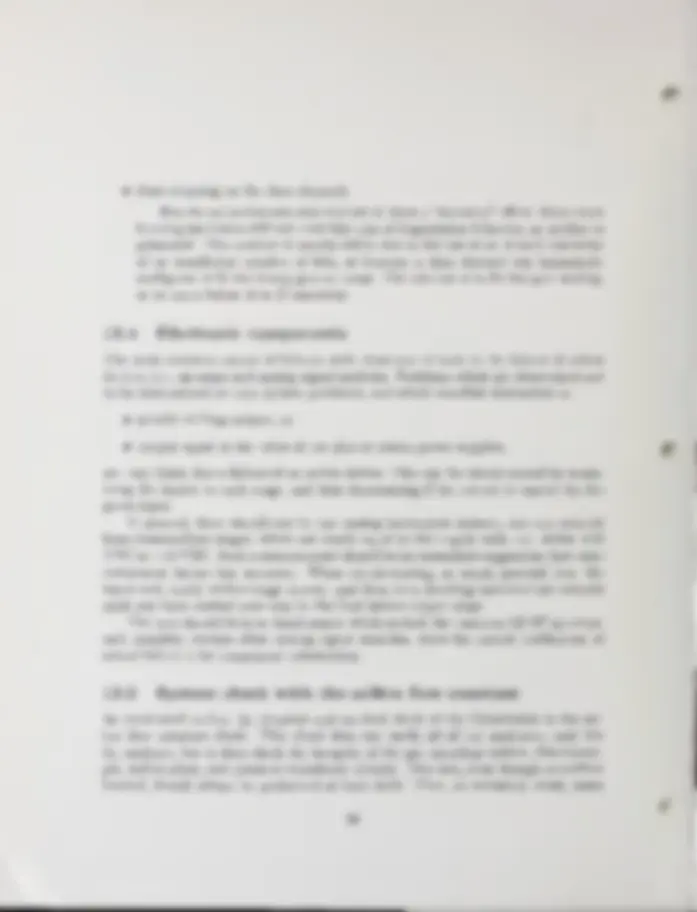
Study with the several resources on Docsity
Earn points by helping other students or get them with a premium plan
Prepare for your exams
Study with the several resources on Docsity
Earn points to download
Earn points by helping other students or get them with a premium plan
Community
Ask the community for help and clear up your study doubts
Discover the best universities in your country according to Docsity users
Free resources
Download our free guides on studying techniques, anxiety management strategies, and thesis advice from Docsity tutors
A comprehensive user guide for operating and maintaining the Cone Calorimeter, a specialized apparatus used for bench-scale rate of heat release measurements. The guide covers preparing weighed soot filters, recording pre-test data, running tests, daily shutdown procedures, and weekly calibration procedures. It also includes a list of essential and additional spare parts.
Typology: Lecture notes
1 / 136
This page cannot be seen from the preview
Don't miss anything!
User's Guide for the Cone Calorimeter
rhe National^ Bureau^ of^ Standards'^ was^ established^ by^ an^ act^ of^ Congress^ on^ March^ 3,^ 1901.^ The Bureau's overall goal is to strengthen and advance the Nation's science and technology and facilitate (^) their
tiveness and leadership of U.S. industry, science and technology. NBS work involves development and transfer of measurements, standards^ and^ related^ science^ and^ technology,^ in^ support^ of^ continually^ improving^ U.S. productivity, product quality and reliability, innovation and underlying science and engineering. The Bureau's technical work is performed by the National Measurement Laboratory, the National Engineering Laboratory, the Institute for Com- puter Sciences and Technology, and the Institute for^ Materials^ Science^ and Engineering. The National Measurement^ Laboratory Provides the national system of physical and chemical measurement; coordinates the^ system^ with^ measurement^ systems^ of^ other^ nations and furnishes essential services leading to accurate and uniform physical and chemical measurement throughout the Nation's scientific community, industry, and commerce; provides advisory and research services to other Government agencies; conducts physical and chemical research; develops, produces, and distributes Standard Reference Materials; provides calibration services; and manages the National Standard Reference Data System. The Laboratory consists of the following centers:
Provides technology and technical services to the public and private sectors to address national needs and to solve national problems; conducts research in engineering and applied science in^ support^ of^ these efforts; builds and maintains competence in the necessary disciplines required to carry out this research and technical service;^ develops^ engi- neering data and measurement capabilities; provides engineering measure- ment traceability services;^ develops^ test methods^ and^ proposes^ engi- neering standards and code changes; develops and proposes new engineering practices; and^ develops^ and^ improves^ mechanisms^ to transfer results of its research to the ultimate user. The Laboratory consists of the following centers: The Institute for Computer Sciences and Technology
relevant Executive Orders, and other directives; carries out this mission by managing the Federal Information Processing Standards Program, developing Federal ADP standards guidelines, and managing Federal participation in ADP^ voluntary^ standardization^ activities;^ provides^ scien- tific and technological advisory services and assistance to Federal agencies; and provides the technical foundation for computer-related policies of the Federal Government. The Institute consists of the following divisions: The Institute (^) for Materials Science and Engineering Conducts research and provides measurements, data, standards, refer- ence materials, quantitative understanding and other technical informa- tion fundamental to the processing, structure, properties and perfor- mance of materials; addresses the scientific basis for new advanced materials technologies; plans research around^ cross-cutting^ scientific themes such as nondestructive evaluation and phase diagram develop- ment; oversees Bureau-wide technical programs^ in^ nuclear^ reactor radiation research and nondestructive evaluation; and broadly dissem- inates generic technical information resulting from its programs. The Institute consists of the following divisions: Information Systems Engineering Systems and Software Technology Computer Security Systems and Network Architecture Advanced Systems
NBS Special Publication 745 IJser^s Guide (^) for the Cone Calorimeter William H. Twilley and Vytenis Babrauskas Fire Measurement and Research Division Center for Fire Research National Bureau of Standards Gaithersburg, (^) MD 20899 Edition 1. Stimulalinp America's Progress i9ij-i9ee August 1988 U.S. Department of Commerce C. William (^) Verity, Secretary National Bureau of Standards Ernest Ambler, Director
1 Introduction In 1982 the National Bureau of Standards (NBS) developed a new type of apparatus for making bench-scale rate of heat release measurements. Rate of heat release was
products, and assemblies. Laboratory instruments for measuring the rate^ of^ heat release had already been available^ at that^ time^ for over a^ decade.^ These^ earlier^ devices, however, were either of a very simple design and subject to serious measurement errors; or, they were capable of good measurement accuracy, but were of extremely complex and costly construction. During the late 1970's an entirely new principle was discovered for making rate
The (^) method required very (^) precise means of measuring oxygen concentrations; given such capability, however, it was shown that highly accurate rate of heat release mea- surements could be made without (^) the greatly complex hardware required for earlier designs. A program was then started at NBS to develop a bench-scale rate of heat release test method which could serve as a standard laboratory test. The appara- tus became known as the Cone Calorimeter (due to the conical shape of the heating element). It has been provisionally (^) published by ASTM as P 190. This Guide is intended to provide supplemental information on installation, set-
assumed that the user has available the following documents:
1.2 Sequence (^) of events The sequence of events listed below, in most cases, is not of specific importance. In
1.3 (^) User comments
not described in the documentation are urged to contact the National Bureau of Standards. User comments are specifically invited, and will be incorporated into
3
2 Installation (^) and initial set-up 2.1 Laboratory environment The apparatus has been designed to operate satisfactorily only in a draft-free environ- ment. While adequate ventilation must be ensured, as described below, it is essential
2.2 (^) Services required
Calorimeter exhaust stack should empty into a collection hood, rather than being directly plumbed into the building exhaust]; (b) remove any smoke drifting up due to specimen insertion or removal; and (c) allow burned specimens to be temporarily placed in a (^) safe location. (^) The requirement for a decoupled
rated capacity will have to be, possibly, ten times the maximum 50 ^|s coming
the end of the main photometer tube, farthest away from the laser). This plug
or of the "new" design (details are given in the LESS-FREQUENT CALIBRATION PROCEDURES (^) Chapter). For units of the original design, the user has to con- struct a filter-positioning device, which can be inserted into the beam inside the
must be able to position a filter nearly, but not quite perpendicularly to the laser beam. Two (^) glass neutral density filters are required, typically at values of approximately 0.3 and 0.8 optical density ("OD") units, calibrated^ at^ the laser wavelength of 623.8 nm. For units of the new design, filter positioning
only to have a calibration filter already mounted in a filter holder^ which^ mates
6
2.4 Calibration samples The user should procure and regularly use the normal calibration sample for the Cone Calorimeter. This sample is PMMA (polymethylmethacrylate) cast sheet stock. It can be obtained as Polycast^ black, 25 mm thick^. [The prior manufacturer for these specimens had been Rohm & Haas. They are no longer producing^ this^ plastic^ in^ the required thickness, and, therefore, Polycast is now specified as the supplier. The new data obtained from (^) Polycast will not (^) be identical (^) to any old measurements obtained from Rohm &: Haas stock.] These samples are not prepared in the standard way, as described in ASTM P (^) 190, but rather are to be prepared in the following special way: Cut the specimens to be 100 mm by 100 mm in area. Obtain cardboard stock, approximately (^) 0.5 mm thick. Prepare from (^) the cardboard strips (^25) mm wide by 100 mm long. Use a thin layer of adhesive to attach the strips to each edge of the specimens. Cure for at least 24 hours. The adhesive used must hold the cardboard strips firmly during the burning process. Note that no aluminum foil is used with these specimens, and that the protective paper sheets (^) on the top and bottom faces of the plastic must be removed prior to testing. The purpose of the cardboard strips is to
The user should retain test data from previous PMMA calibration runs, and compare against those, when necessary in the process of troubleshooting. The flux values are normally chosen to (^) be (^) 25, 50, 75 kW/m^. Note that since these calibration runs are for the purpose of diagnostic testing within one laboratory only, ASTM P 190 does not standardize this procedure. ^Certain commercial (^) products and materials are identified in this document in order to adequately specify the experimental (^) procedure. In no case does such identification imply recommendation or endorsement by the National (^) Bureau of Standards, nor does it imply that the product or material identified is the best available for the purpose. ^Type Cellcast BK2025, from Polycast Co., 69 Southfield Avenue, Stamford, CT 06902. Tele- phone: (^) (800) 243-9002. 7
Oxygen analyzer 0 to 2.5 V Load cell 0 to 1.0 V Stack thermocouple 0 to 50 mV Pressure transducer 0 to 2.5 V Laser smoke photometer 0 to 5.0 V Photometer thermocouple 0 to 50 mV Soot mass flow indicator 0 to 2.0 V
(and linearization) can be done by hardware, by software, or by a combination
laboratory to laboratory, but may also be changed to a different type within one laboratory, specific set-up steps cannot be given for general advice. The operator must make certain, however, once the hookup has been made and the
computer, (^) that the proper operation is checked out. (^) To do this, prepare the computer software to output the necessary temperature channels (there will be at least two—the stack (^) thermocouple and the smoke photometer thermocouple). Make sure the instrument has not been heated and all temperatures are at ambient. Measure the laboratory air temperature with a thermometer. Then scan the temperature (^) channels on the data system and record their readings in degrees (^) C. A reading close to that obtained from the room thermometer should
or correct the computer program routines. It may also be desirable to make a
used.
NBS drawings. For units with different duct dimensions, different blowers, etc., a different orifice flow constant will be expected. Once it has been verified
anywhere in the gas sampling system, the operator should record the constant
shown excellent linearity in the 0 to 12 kW region. 10