
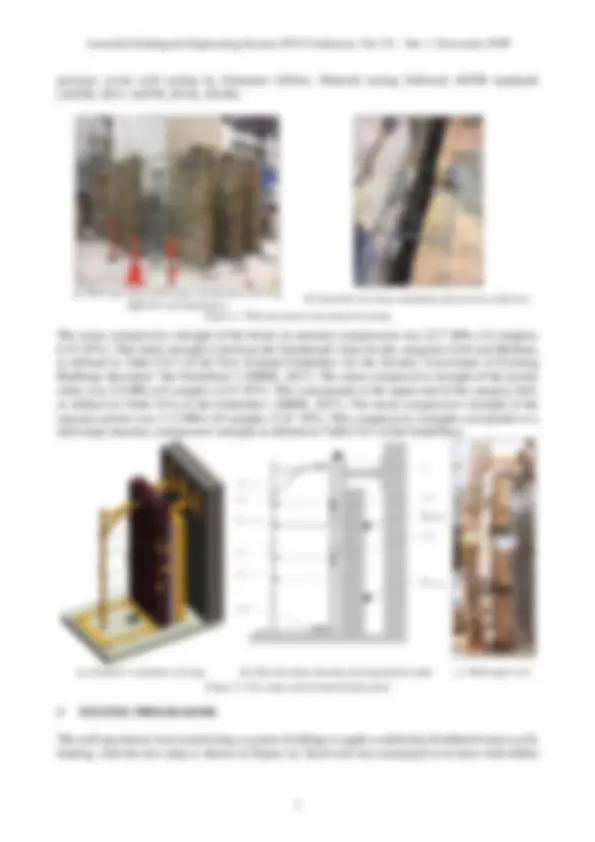
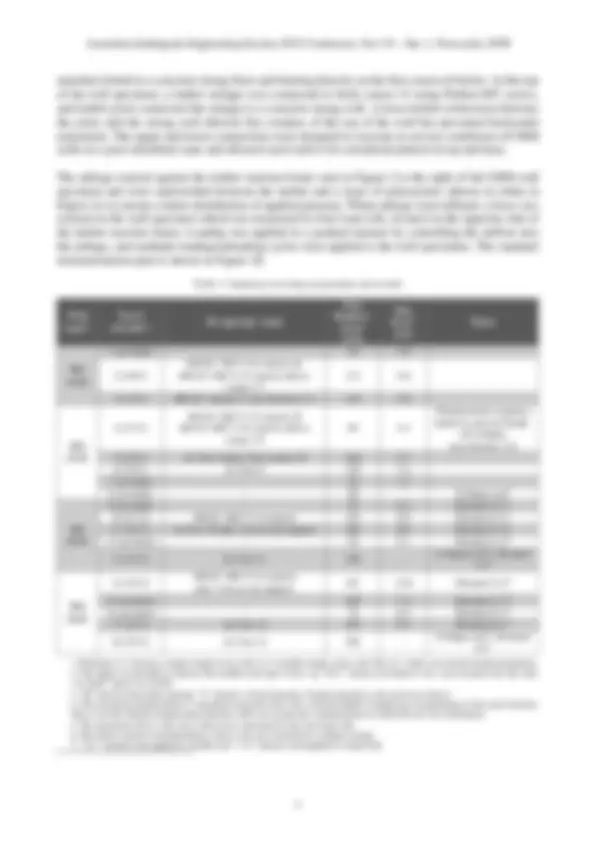
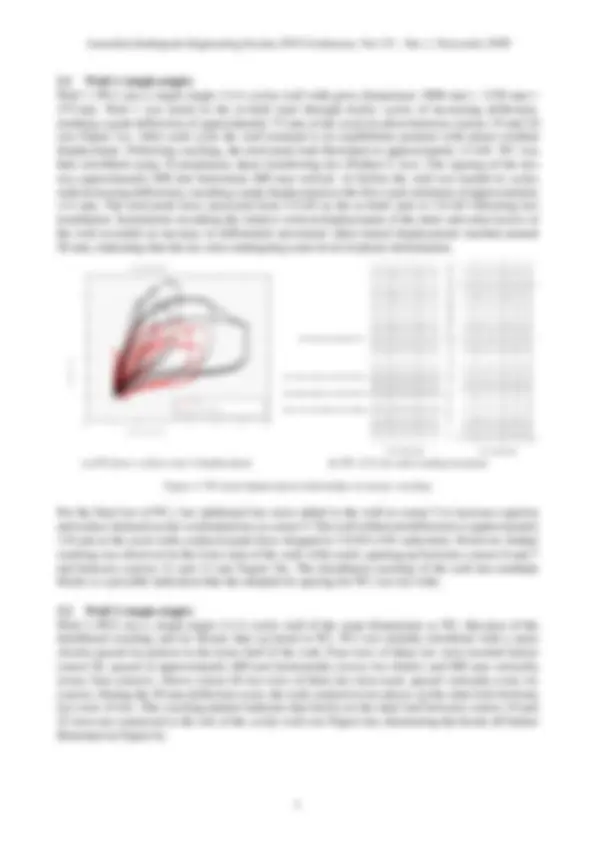
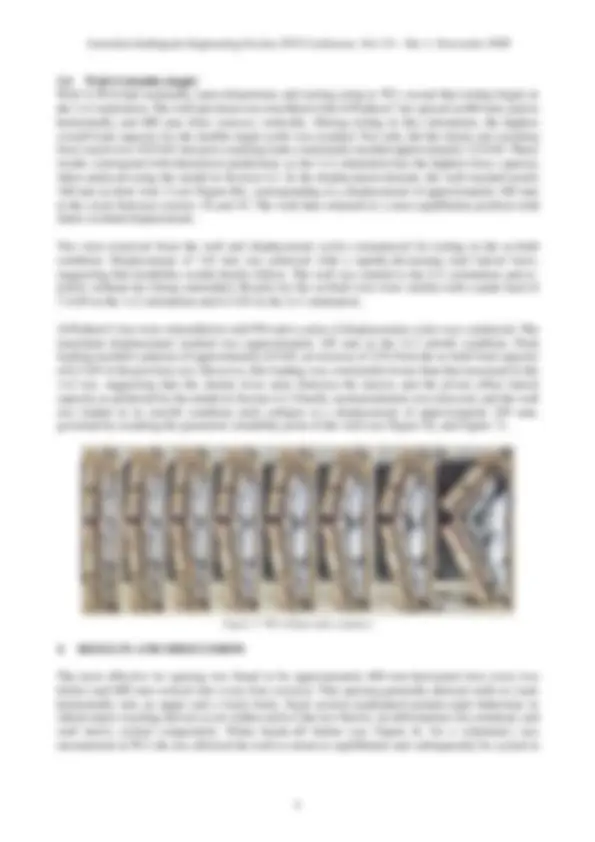
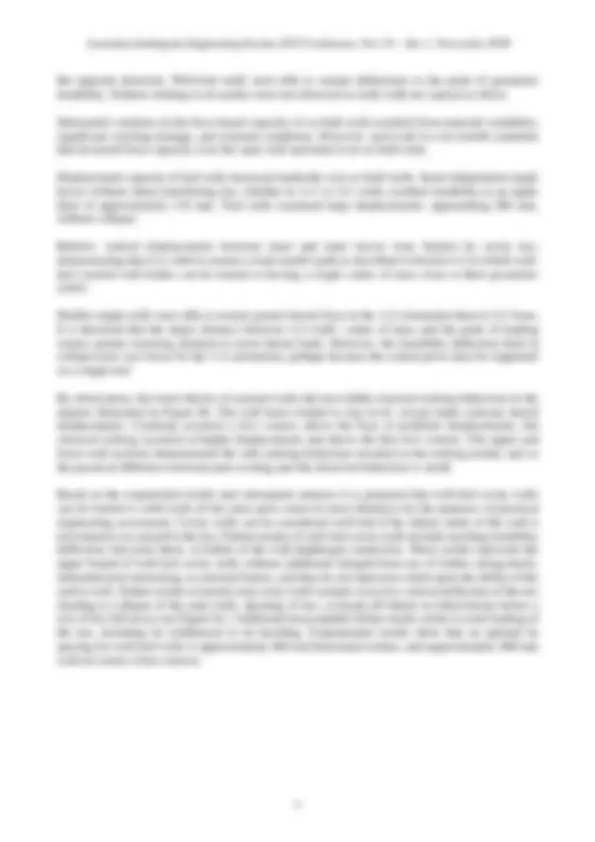
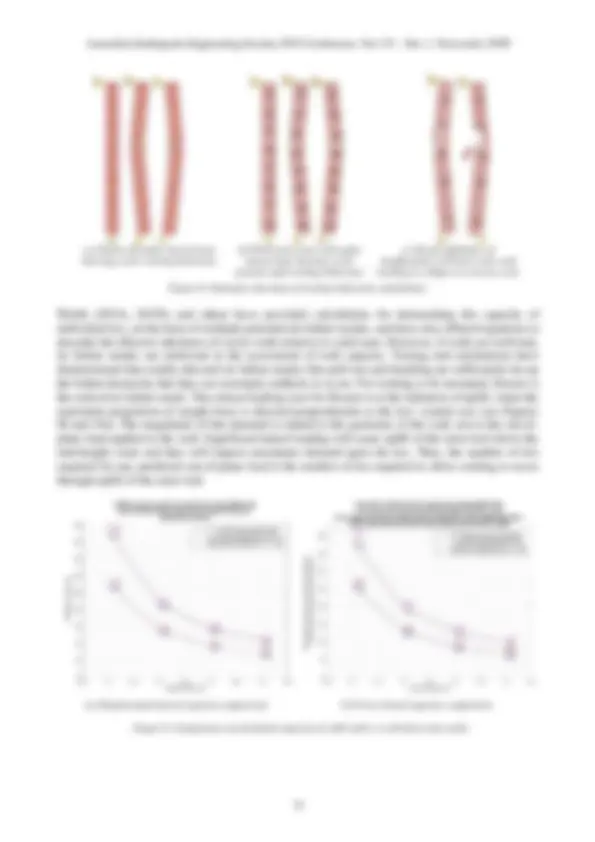
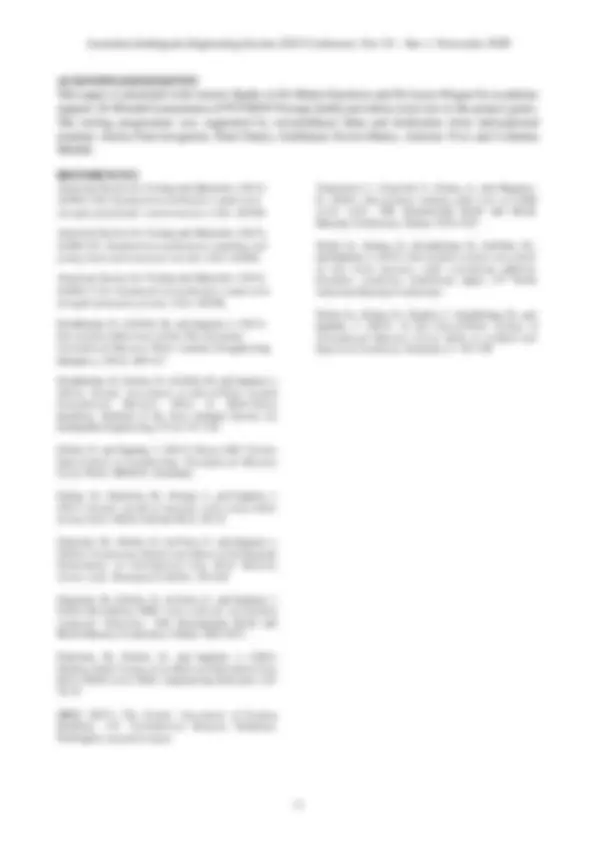
Study with the several resources on Docsity
Earn points by helping other students or get them with a premium plan
Prepare for your exams
Study with the several resources on Docsity
Earn points to download
Earn points by helping other students or get them with a premium plan
Community
Ask the community for help and clear up your study doubts
Discover the best universities in your country according to Docsity users
Free resources
Download our free guides on studying techniques, anxiety management strategies, and thesis advice from Docsity tutors
The results of an experimental campaign aimed at improving the out-of-plane performance of unreinforced masonry (URM) cavity walls through seismic retrofitting. The study involved testing full-scale URM walls with varying cross-sections and retrofit arrangements using airbags to simulate earthquake loading. Key findings include the importance of cavity ties in enhancing composite action between wall layers, the difference in performance between as-built and retrofitted walls, and the proposal that well-tied cavity walls can be treated as solid walls for practical engineering assessment. Keywords: earthquake loading, airbag loading, URM, seismic retrofit, cavity wall, cavity tie, clay brick masonry.
Typology: Study notes
1 / 13
This page cannot be seen from the preview
Don't miss anything!
Hamish Tocher^1 , Nicholas Slavin^2 , Anton Stanišić^3 and Dmytro Dizhur 4
Email: hamish.tocher@holmesconsulting.co.nz
Unreinforced clay brick masonry (URM) cavity-wall construction is common in seismically active parts of the world. This construction type incorporates a continuous air gap that separates the inner and outer brick leaves of the wall cross-section. Many past earthquakes (including the 1989 Newcastle, Australia earthquake) have highlighted that cavity-wall URM buildings perform poorly particularly in the out-of-plane loading direction due to their slender aspect and inadequate connections between masonry layers. An experimental campaign was initiated to develop a simple solution to substantially increase the out-of-plane performance of such walls by inducing composite action between the wall layers. Full scale URM cavity walls with varying cross-sections and retrofit arrangements were tested using a system of airbags to simulate earthquake loading. Wall construction details, retrofit procedures, test set-up, comparison with solid walls, and quantification of the improvement in seismic capacity from using the proposed retrofit techniques are presented herein.
Keywords: earthquake loading, airbag loading, unreinforced masonry, URM, seismic retrofit, cavity wall, cavity tie, clay brick masonry
The critical engineering challenge when dealing with unreinforced clay brick masonry (URM) cavity walls is their stability when loaded out-of-plane. Each leaf of the wall is usually slender and is unable to sustain mid-height displacements beyond geometric instability of the single leaf without collapsing. It is now commonplace in current engineering practice to retrofit such walls with stiff
(shear transferring) steel ties which span between the leaves of the wall, crossing the internal cavity. A number of investigations have sought to verify and measure the performance improvement delivered by cavity ties. The focus of this research was on establishing an equivalent thickness of cavity walls by calculating the thickness of a solid wall which would perform nominally similar to a given cavity wall. Walsh et al (2015a, 2015b) undertaken in-situ testing of cavity walls found in existing buildings. It was concluded that ‘cavity tie retrofits… can substantially improve the out-of- plane capacity of URM walls’. Following this work, provisional equations to quantify the equivalent solid thickness of cavity walls were proposed. Giaretton et al (2016a, 2016b) undertaken dynamic testing of cavity walls using a shake table. The testing showed that the slender as-built wire ties common to most cavity walls added no additional deflection capacity to the walls, resulting in the walls performing similarly to independent single leaf walls. Cavity walls retrofitted with shear transferring ties demonstrated ‘composite rigid-body behaviour’, supporting the theory that a rocking model could be applied to tied cavity walls.
Although researchers have observed that cavity wall typologies extend beyond walls of two single leaves (Dizhur, (2015); Giaretton, (2016a)), to the authors’ knowledge there were no experimental testing of asymmetrical leaf arrangements in URM cavity walls. The research programme presented herein includes the testing of walls with a solid double leaf URM wall connected to a single leaf. This arrangement is common on lower floors of URM buildings and can also be found on upper floors.
2 WALL TEST SPECIMENS
The experimental testing programme was conducted using four purpose-built full-scale URM walls (see Figure 1a). The walls were 3000 mm high and 1150 mm wide, with wall height chosen to approximate a typical upper storey in a URM building. Two of the walls were single-single cavity walls, meaning two single leaves of bricks separated by a 55 mm wide air cavity. The other two walls were double-single cavity walls, meaning a double leaf of brick, a 55 mm air cavity, and a single leaf of brick. These walls were denoted “1+1” and “2+1” respectively. These type of wall configurations are frequently found in New Zealand URM buildings, with the double-single cavity walls commonly but not exclusively found on lower floors. The cavity width in all the walls was specified as 50 mm, or approximately half the thickness of a brick. As was common practice in historical URM construction, the outer faces of the walls were made flush. As a result, there was minor variability in the cavity thickness over the height of the wall.
In typical URM cavity wall construction, flexible wire ties were inserted into the walls to connect the leaves across the cavities. Following the methodology employed by Giaretton (2016c), these as-built wire ties were simulated in the specimen walls using 4.0 mm steel wire bent into open hoops. Deterioration of the as-built ties was simulated by notching the wire hoops which were built into the specimen walls (see Figure 1b). Wire hoops were inserted every six courses, alternating between a pair of hoops and a single hoop to create an offset pattern. In retrofitted wall specimens, Python C ties were used to transfer shear and improve composite action between the leaves. The retrofit ties were 6 mm diameter screws with a length of approximately 240 mm and have significantly higher axial and flexural capacity than as-built ties. Python C tie spacing was varied for each retrofit test.
The bricks from which the wall specimens were constructed were sourced from the demolition of a vintage URM building. The bricks are approximately 100 years old, and made from reddish-orange clay, typical of New Zealand URM buildings. Material testing was undertaken on single bricks and three brick high masonry prisms. The mortar used to construct the walls was mixed to a cement:lime:sand ratio of 1:2:9 by volume. This ratio was chosen to follow a mortar mix used in
members bolted to a concrete strong floor and bearing directly on the first course of bricks. At the top of the wall specimen, a timber stringer was connected to brick course 31 using Python MT screws, and timber joists connected the stringer to a concrete strong wall. A loose bolted connection between the joists and the strong wall allowed free rotation of the top of the wall but prevented horizontal translation. The upper and lower connections were designed to recreate in-service conditions of URM walls in a post-retrofitted state and allowed each wall to be considered pinned at top and base.
The airbags reacted against the timber reaction frame seen in Figure 2 to the right of the URM wall specimen and were sandwiched between the timber and a layer of polystyrene (shown in white in Figure 2c) to ensure a better distribution of applied pressure. When airbags were inflated, a force was exerted on the wall specimen which was measured by four load cells, located on the opposite side of the timber reaction frame. Loading was applied in a gradual manner by controlling the airflow into the airbags, and multiple loading/unloading cycles were applied to the wall specimens. The standard instrumentation plan is shown in Figure 2b.
Table 1: Summary of testing programme and results
Wall (type^1 )
Test # (retrofit^2 ) Tie spacing
(^3) (mm)
Max displace- ment^4 (mm)
Max force^5 (kN)
Notes
W (1+1)
1 (as-built) - 76 3.
2 (10 C)
690 H / 700 V (8 courses) & 690 H / 500 V (5 courses) above course 17
112 5.
3 (12 C) 690 H / various V (see Section 3.1) 118 5.
W (1+1)
4 (21 C)
460 H / 400 V (4 courses) & 460 H / 600 V (6 courses) above course 19
84 4.
Displacement sequence halted to prevent break- off collapse (see Section 3.2) 5 (23 C) As Test 4 plus 2 ties course 22 104 2. 6 (23 C) As Test 5 149 3. 7 (as-built) - 54 1. 8 (as-built) - 90 - Collapse test^6
W (2+1)
9 (as-built) - 53 8.4 Oriented 2+1^7 10 (21 C) 460 H / 400 V (4 courses) 153 6.9 Oriented 2+1^7 11 (24 C) As Test 10 plus 3 ties at top support 193 8.6 Oriented 1+2^7 12 (as-built) - 52 5.1 Oriented 1+2^7 13 (24 C) As Test 11 230 - Collapse test
(^6). Oriented 1+2 7
W (2+1)
14 (24 C) 460 H / 400 V (4 courses)plus 3 ties at top support 181 12.0 Oriented 1+2 7 15 (as-built) - 109 7.4 Oriented 1+2 7 16 (as-built) - 74 6.5 Oriented 2+1 7 17 (24 C) As Test 14 103 9.2 Oriented 2+1 7 18 (24 C) As Test 14 350 - Collapse test
(^6). Oriented 2+1 7
3.1 Wall 1 (single-single) Wall 1 (W1) was a single-single (1+1) cavity wall with gross dimensions 3000 mm × 1150 mm × 275 mm. Wall 1 was tested in the as-built state through twelve cycles of increasing deflection, reaching a peak deflection of approximately 75 mm at the crack location between courses 19 and 20 (see Figure 3a). After each cycle the wall returned to its equilibrium position with minor residual displacement. Following cracking, the total peak load fluctuated at approximately 3.5 kN. W1 was then retrofitted using 10 proprietary shear transferring ties (Python C ties). The spacing of the ties was approximately 690 mm horizontal, 600 mm vertical. As before the wall was loaded in cycles with increasing deflections, reaching a peak displacement at the first crack initiation of approximately 112 mm. The total peak force increased from 3.9 kN in the as-built state to 5.8 kN following ties installation. Instruments recording the relative vertical displacement of the inner and outer leaves of the wall recorded an increase in differential movement when lateral displacement reached around 50 mm, indicating that the ties were undergoing some level of plastic deformation.
Figure 3: W1 Load-displacement relationship, tie layout, cracking
For the final test of W1, two additional ties were added to the wall at course 5 to increase capacity and reduce demand on the overloaded ties at course 9. The wall withstood deflection to approximately 118 mm at the crack with a reduced peak force dropped to 5.0 kN (14% reduction). However, further cracking was observed in the lower part of the wall, with cracks opening up between courses 6 and 7 and between courses 12 and 13 (see Figure 3b). The distributed cracking of the wall into multiple blocks is a possible indication that the adopted tie spacing for W1 was too wide.
3.2 Wall 2 (single-single) Wall 2 (W2) was a single-single (1+1) cavity wall of the same dimensions as W1. Because of the distributed cracking and tie flexure that occurred in W1, W2 was initially retrofitted with a more closely-spaced tie pattern in the lower half of the wall. Four rows of three ties were inserted below course 20, spaced at approximately 460 mm horizontally (every two bricks) and 400 mm vertically (every four courses). Above course 20 two rows of three ties were used, spaced vertically every six courses. During the 30 mm deflection cycle, the wall cracked in two places on the outer leaf, between two rows of ties. This cracking pattern indicates that bricks on the outer leaf between courses 19 and 25 were not connected to the rest of the cavity wall (see Figure 4a), threatening the break-off failure illustrated in Figure 8c.
(a) W1 force vs draw-wire 2 displacement (b) W1 12 C ties and cracking locations
-20 0 20 40 60 80 100 120 Draw Wire 2 Displacement (mm)
0
1
2
3
4
5
6
Out-of-Plane Force (kN)
W1 - Force vs Displacement
As-Built 10 Python C Ties Retrofit
3.3 Wall 3 (double-single) Wall 3 (W3) was a double-single (2+1) cavity wall with gross dimensions 3000 mm × 1150 mm × 395 mm. Double-single walls are necessarily asymmetrical, and it was predicted that their response would be anisotropic. As a result, the testing programme included turning each wall specimen so that it could be tested from both out-of-plane directions. Load applied to the double leaf orientation is herein denoted as “2+1”. When loading is applied to the single leaf, the orientation is denoted “1+2” (see Figure 5a-b).
W3 was first tested as-built in the 2+1 orientation. Following initial cracking, the wall was cycled through increasing displacements up to approximately 50 mm, returning to near equilibrium position at the end of the as-built test. An LVDT measured high relative vertical displacement of the leaves of the upper block, with a peak displacement exceeding 20 mm (see Figure 6a). The wall specimen was retrofitted using 21 Python C ties at 460 mm horizontal centres and 400 mm vertical centres, corresponding to a row of ties every four courses. With ties in place, the crack from as-built testing between courses 17 and 18 did not initially reopen, but a new crack formed between courses 21 and 22 during testing. The wall reached approximately 155 mm at the mid-height crack and returned to an equilibrium position with minor residual displacement. During the 155 mm displacement cycle, the crack between courses 17 and 18 which had occurred in the as-built test reopened, and the block between course 18 and 21 moved semi-independently of the upper block, at a separate angle. The wall was able to return to a stable equilibrium, and it was subsequently able to sustain displacements in the opposite loading direction. Additionally, the upper LVDT measured a peak interleaf vertical displacement of approximately 4 mm (see Figure 6a) during the tie retrofit test, suggesting that the cavity wall leaves acted compositely as a semi-rigid body and relative displacement was limited.
The wall W3 was rotated 180 degrees and a new row of ties was inserted in course 31 to ensure a load path between the outer leaf and the upper restraint. The wall sustained high levels of displacement during the 1+2 retrofit test, peaking at approximately 165 mm for draw wire 2. Draw wire 3, connected at course 15 on the lower part of the wall, measured a peak displacement over 190 mm. For these large displacements to occur, the inner single leaf lifted and fully support the outer leaf via the retrofit ties (see Figure 5c). To establish a directional difference between performance of as-built double-single cavity walls, the wall specimen was tested again with ties removed, for comparison with the as-built test in the 2+1 orientation. The peak loading in both directions was similar at approximately 5.0 kN. Lastly, ties were reinstalled in wall 3 and it was loaded to collapse. The wall withstood displacement to 350 mm at the mid-height crack before collapsing, which represents a geometrically-determined instability failure rather than a tie failure.
(a) W 3 2+1 force vs relative vertical leaf displacement (b) W 4 1+2 force vs draw wire 2 displacement Figure 6: Force vs displacement plots for double-single walls
-5 0 5 10 15 20 25 Upper LVDT Displacement (mm)
0
1
2
3
4
5
6
7
8
9
Out-of-Plane Force (kN)
W3 2+1 - Force vs Upper Interleaf Displacement
As-Built 21 Python C Ties Retrofit -20 0 20 40 60 80 100 120 140 160 Draw Wire 2 Displacement (mm)
0
2
4
6
8
10
12
14
Out-of-Plane Force (kN)
W4 1+2 - Force vs Displacement
As-Built 24 Python C Ties Retrofit
3.4 Wall 4 (double-single) Wall 4 (W4) had nominally same dimensions and testing setup as W3, except that testing began in the 1+2 orientation. The wall specimen was retrofitted with 24 Python C ties spaced at 460 mm centres horizontally and 400 mm (four courses) vertically. During testing in this orientation, the highest overall load capacity for the double-single walls was reached. Not only did the elastic pre-cracking force reach over 10.0 kN, but post-cracking loads consistently reached approximately 12.0 kN. These results correspond with theoretical predictions as the 1+2 orientation has the highest force capacity when analysed using the model in Section 4.2. In the displacement domain, the wall reached nearly 160 mm at draw wire 2 (see Figure 6b), corresponding to a displacement of approximately 180 mm at the crack between courses 18 and 19. The wall then returned to a near equilibrium position with minor residual displacement.
Ties were removed from the wall and displacement cycles commenced for testing in the as-built condition. Displacement of 110 mm was achieved with a rapidly-decreasing total lateral force, suggesting that instability would shortly follow. The wall was rotated to the 2+1 orientation and re- tested, without ties being reinstalled. Results for the as-built tests were similar with a peak load of 7.4 kN in the 1+2 orientation and 6.5 kN in the 2+1 orientation.
24 Python C ties were reinstalled in wall W4 and a series of displacement cycles was conducted. The maximum displacement reached was approximately 105 mm in the 2+1 retrofit condition. Peak loading reached a plateau of approximately 8.0 kN, an increase of 23% from the as-built load capacity of 6.5 kN in the previous test. However, this loading was consistently lower than that measured in the 1+2 test, suggesting that the shorter lever arms between the masses and the pivots affect lateral capacity as predicted by the model in Section 4.2. Finally, instrumentation was removed, and the wall was loaded in its retrofit condition until collapse at a displacement of approximately 350 mm, governed by reaching the geometric instability point of the wall (see Figure 5d, and Figure 7).
Figure 7: W4 collapse time sequence
4 RESULTS AND DISSCUSSION
The most effective tie spacing was found to be approximately 460 mm horizontal (ties every two bricks) and 400 mm vertical (ties every four courses). This spacing generally allowed walls to crack horizontally into an upper and a lower body. Each section maintained pseudo-rigid behaviour in which major cracking did not occur within each of the two blocks, tie deformation was minimal, and wall leaves rocked compositely. When break-off failure (see Figure 8c for a schematic) was encountered in W3, the ties allowed the wall to return to equilibrium and subsequently be cycled in
(a) Solid wall under lateral load showing cyclic rocking behaviour
(b) Well-tied cavity wall under lateral load showing cyclic pseudo-rigid rocking behaviour
(c) Break-off failure of insufficiently well-tied cavity wall leading to collapse in reverse cycle Figure 8: Schematic drawings of rocking behaviour and failures
Walsh (2015a, 2015b) and others have provided calculations for determining the capacity of individual ties, on the basis of multiple potential tie failure modes, and have also offered equations to describe the effective thickness of cavity walls relative to solid ones. However, if walls are well-tied, tie failure modes are irrelevant in the assessment of wall capacity. Testing and calculations have demonstrated that axially-directed tie failure modes like pull-out and buckling are sufficiently far up the failure hierarchy that they are extremely unlikely to occur. For rocking to be sustained, flexure is the critical tie failure mode. The critical loading case for flexure is at the initiation of uplift, when the maximum proportion of weight force is directed perpendicular to the ties’ central axis (see Figures 8b and 10a). The magnitude of this demand is related to the geometry of the wall, not to the out-of- plane load applied to the wall. Significant lateral loading will cause uplift of the outer leaf above the mid-height crack and thus will impose maximum demand upon the ties. Thus, the number of ties required for any predicted out-of-plane load is the number of ties required to allow rocking to occur through uplift of the outer leaf.
(a) Displacement-based capacity comparison (b) Force-based capacity comparison
Figure 9: Comparison of calculated capacity of solid walls vs well-tied cavity walls
4.1 Displacement-based analysis of wall capacity Part C8 of the Guidelines defines the out-of-plane capacity of walls as their ability to reach a limiting displacement before instability causes collapse. Using a modified version of the Parts and Components loading in NZS1170.5, C8 defines the probable deflection response of walls to the lateral loading that is predicted for their location. Analysis has been conducted regarding displacement-based response of well-tied cavity walls using the calculation method given in Part C8, assuming pseudo- rigid behaviour of the walls. This response was compared to the predicted response of solid walls of the same total thickness as the cavity walls. Because cavity walls are lighter than solid walls, they have less rotational inertia and generate less restoring force to resist instability. However, as a result of their lower mass they also incur a lower load than solid walls for a given acceleration. The following analysis shows that the net result of the lower capacity and lower loading of well-tied cavity walls is that if pseudo-rigid behaviour is assumed, they are predicted to perform approximately the same as solid walls. Figure 9a shows a maximum difference of three percentage points in % New Building Standard (NBS) scores of solid walls and well-tied cavity walls at low seismic loading, decreasing to approximately one percentage point at higher loads. Evidence for well-tied cavity walls’ displacement-based equivalence to solid walls is found in the deflections they sustained before collapse during experimentation (see Table 1). Based on the attained experimental results, it appears that well-tied cavity walls behaved the same as solid walls for practical purposes, when considered in a displacement paradigm. Therefore, well-tied cavity walls could simply be assessed for displacement capacity by engineers familiar with C8 by assuming that they are solid.
4.2 Force-based analysis of wall capacity A simplified model of wall behaviour from a force-based perspective is presented in Figure 10a. In the model, the wall cracks into two bodies, which rock cyclically, one atop the other. The model assumes that maximum lateral load capacity occurs at first displacement, when the lever arms are longest between the weight forces in the wall and the pivots. Based on this assumption, a theoretical maximum out-of-plane load capacity for the cavity walls can be calculated. When this theoretical maximum is compared to loads generated by the New Zealand Loadings Standard, a force/capacity ratio can be found which is analogous to the %NBS score generated in the displacement realm. Comparing theoretical capacity/demand ratios of solid walls and cavity walls, analysis shows that they are predicted to perform very similarly, supporting the proposition that if cavity walls are well- tied they can be assessed as solid walls of the same gross thickness (see Figure 9b). When these theoretical loads are compared to experimental results, there is good agreement, with theoretical loads appearing somewhat conservative (see Figure 10b).
This paper is presented with sincere thanks to Dr Marta Giaretton and Dr Lucas Hogan for academic support. Dr Ronald Lumantarna of PYTHON Fixings kindly provided cavity ties to the project gratis. The testing programme was supported by extraordinary help and dedication from international students Alexia Fam-lavignotte, Paul Chatry, Guillaume Scriva-Marty, Antoine Yves and Uchenna Maduh.
REFERENCES American Society for Testing and Materials, (2013). ASTM C109. Standard test method for compressive strength of hydraulic cement mortars. USA: ASTM.
American Society for Testing and Materials, (2014). ASTM C67. Standard test methods for sampling and testing brick and structural clay til e. USA: ASTM.
American Society for Testing and Materials, (2014). ASTM C1314. Standarsd test method for compressive strength of masonry prisms. USA: ASTM.
Derakhshan, D., Griffith, M., and Ingham, J. (2013). Out-of-plane Behaviour of One-Way Spanning Unreinforced Masonry Walls. Journal of Engineering Mehanics, 139(4): 409-
Derakhshan, H., Dizhur, D., Griffith, M. and Ingham, J. (2014). Seismic Assessment of Out-of-Plane Loaded Unreinforced Masonry Walls in Multi-Storey Buildings. Bulletin of the New Zealand Society for Earthquake Engineering, 47(2):119–138.
Dizhur, D. and Ingham, J. (2015). Report ER3. Seismic Improvement of Loadbearing Unreinforced Masonry Cavity Walls. BRANZ: Auckland.
Dizhur. D., Giaretton, M., Giongo, I., and Ingham, J. (2017) Seismic retrofit of masonry walls using timber strong-backs. SESoc Journal 30(2): 30-
Giaretton, M., Dizhur, D., da Porto, F., and Ingham, J. (2016) Construction Details and Observed Earthquake Performance of Unreinforced Clay Brick Masonry Cavity-walls. Structures 6 (2016): 159-
Giaretton, M., Dizhur, D., da Porto, F., and Ingham, J. (2016) Retrofitting URM cavity walls for out-of-plane composite behaviour. 16th International Brick and Block Masonry Conference, Padua: 2063-2071.
Giaretton, M., Dizhur, D., and Ingham, J. (2016). Shaking Table Testing of As-Built and Retrofitted Clay Brick URM Cavity-Walls. Engineering Structures 125: 70-
MBIE (2017). The Seismic Assessment of Existing Buildings. C8: Unreinforced Masonry Buildings. Wellington: eq-assess.org.nz
Tomassetti, U., Graziotti, F., Penna, A., and Magenes, G. (2016). Out-of-plane shaking table tests on URM cavity walls. 16th International Brick and Block Masonry Conference, Padua: 1939-1947.
Walsh, K., Dizhur, D., Derakhshan, H., Griffiths, M., and Ingham, J. (2015). Out-of-plane seismic assessment of clay brick masonry walls considering different boundary conditions. Conference paper, 12 th^ North American Masonry Conference.
Walsh, K., Dizhur, D., Shafaei, J., Derakhshan, H., and Ingham, J. (2015). In Situ Out-of-Plane Testing of Unreinforced Masonry Cavity Walls in As-Built and Improved Conditions. Structures 3: 187-