
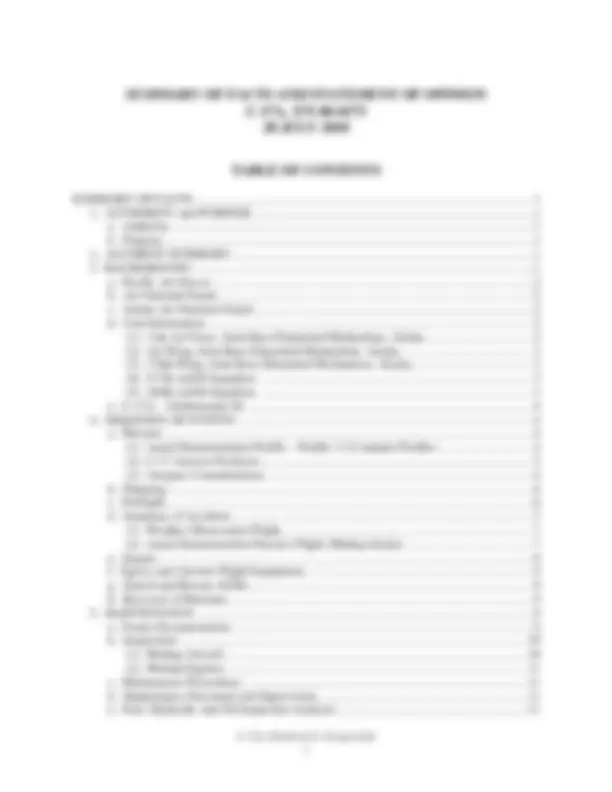
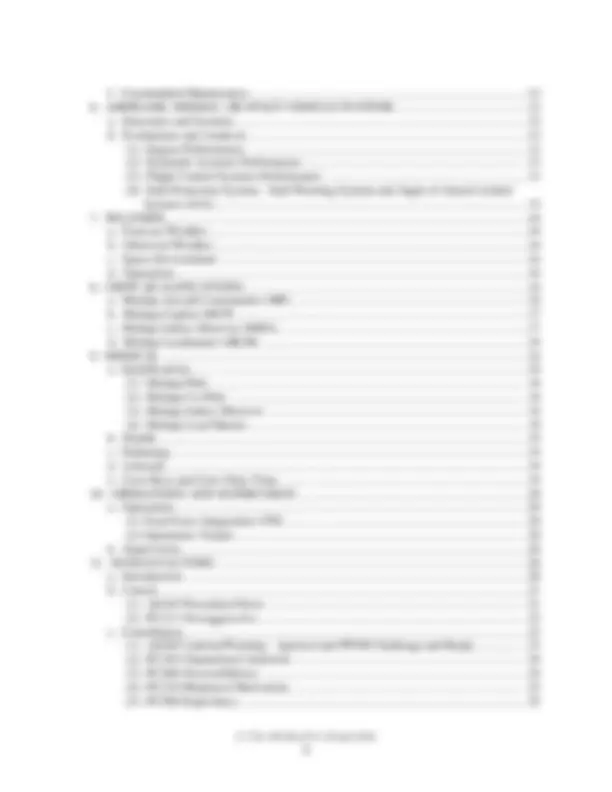
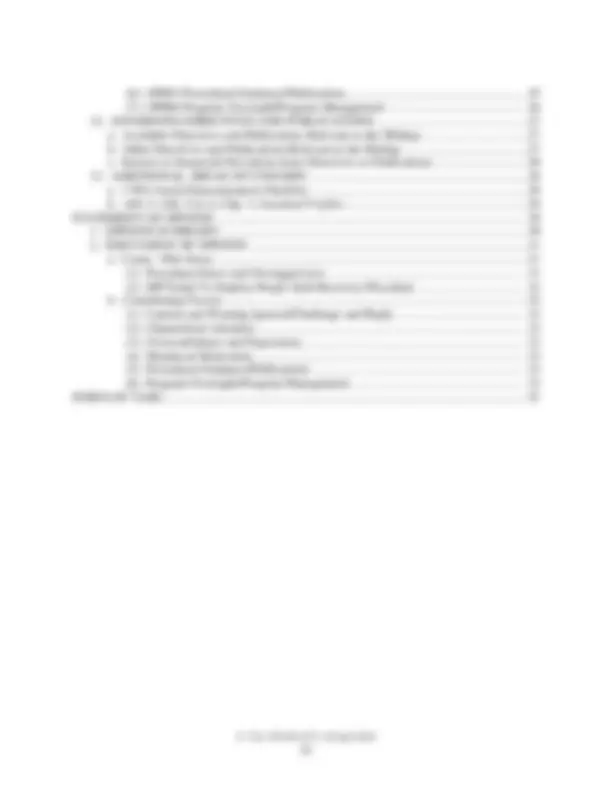
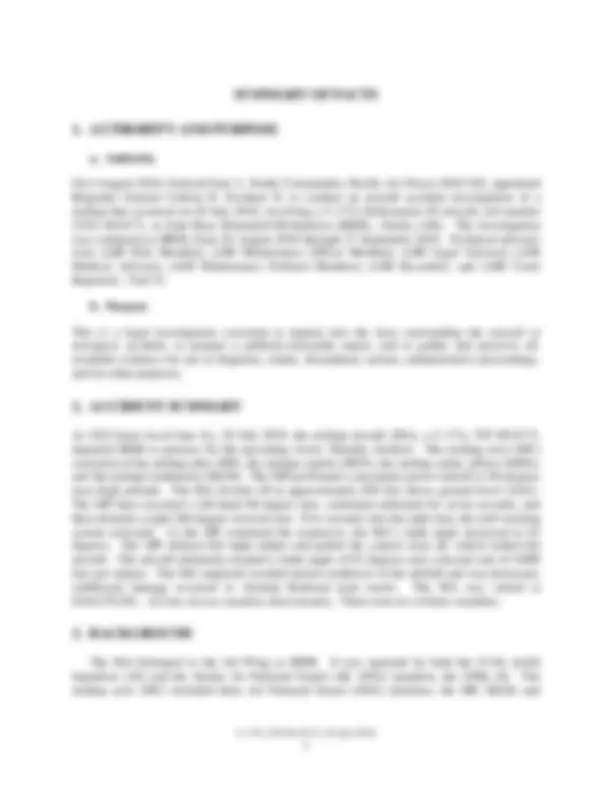
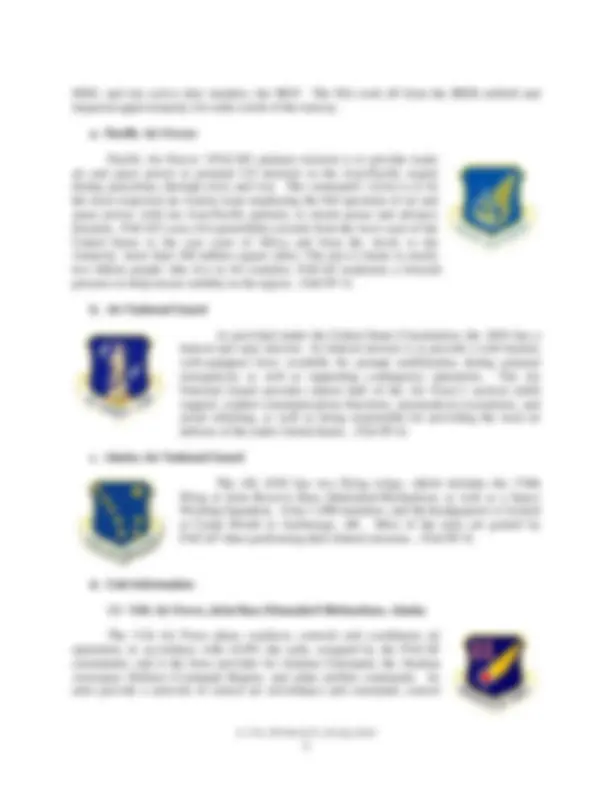
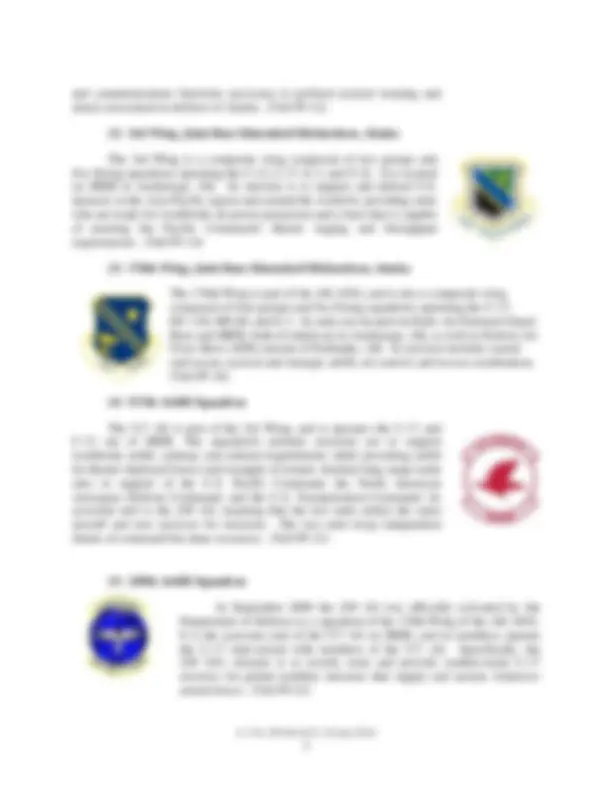
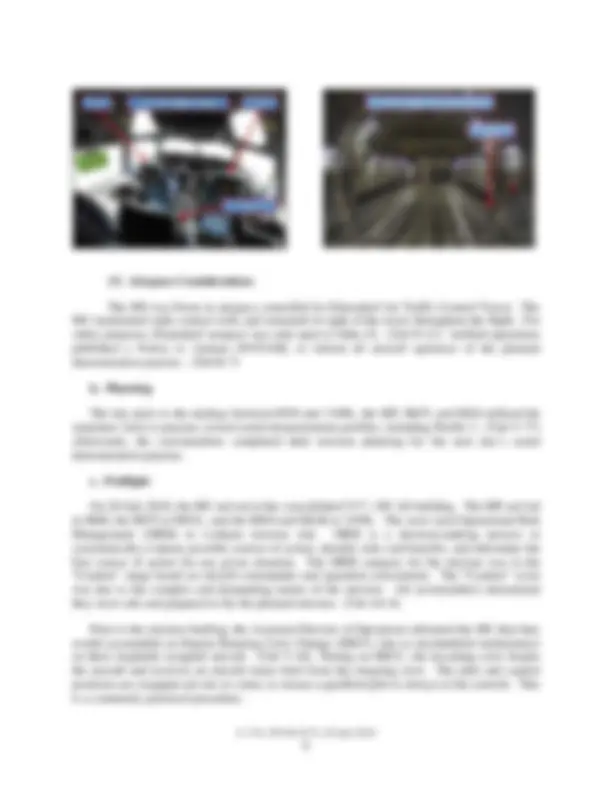
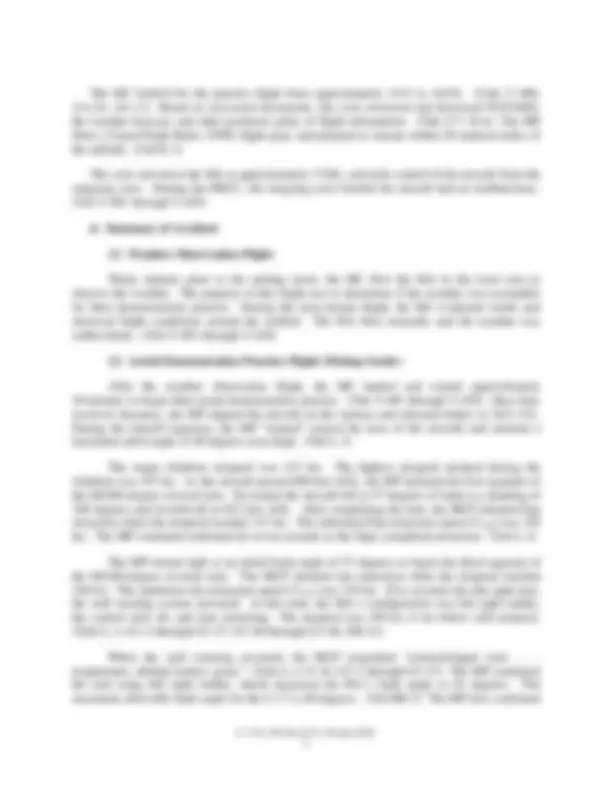
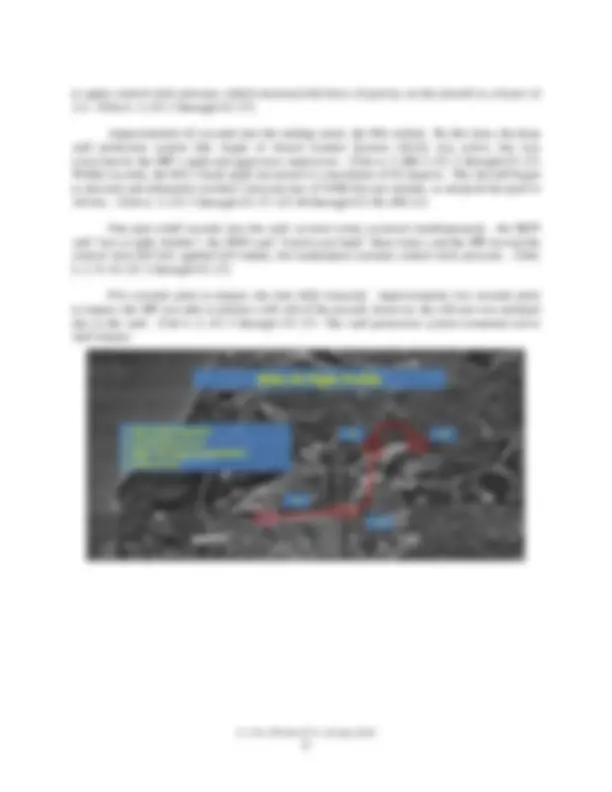
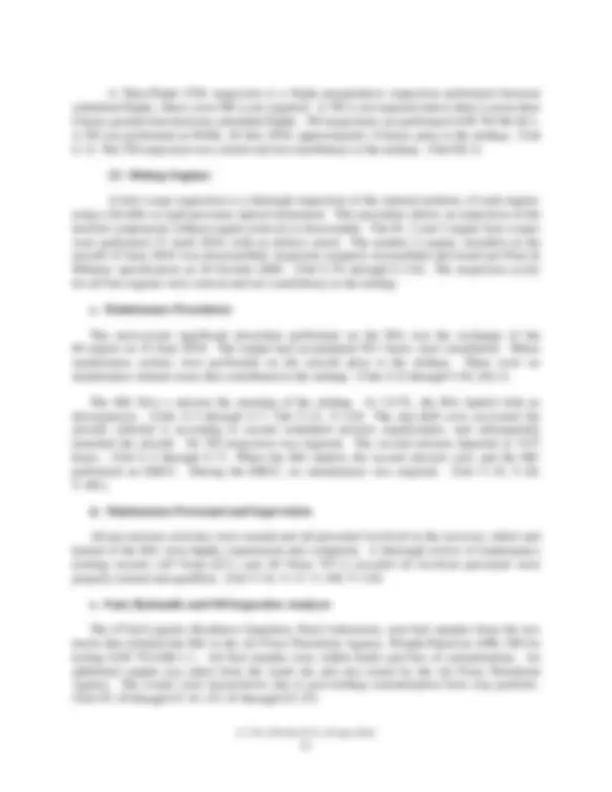
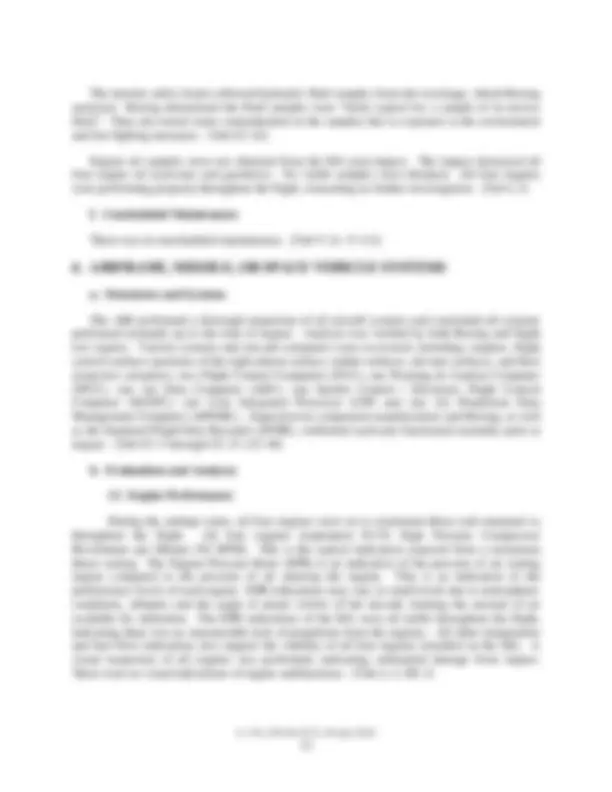
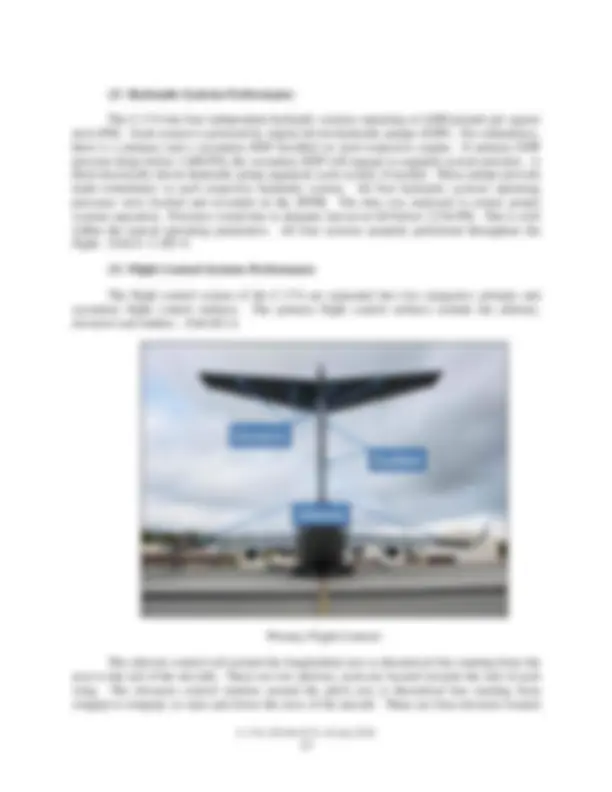
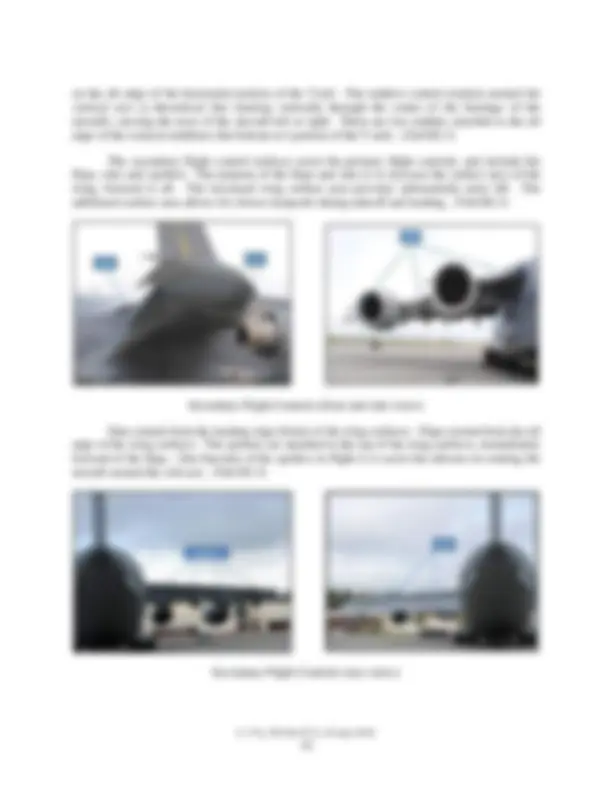
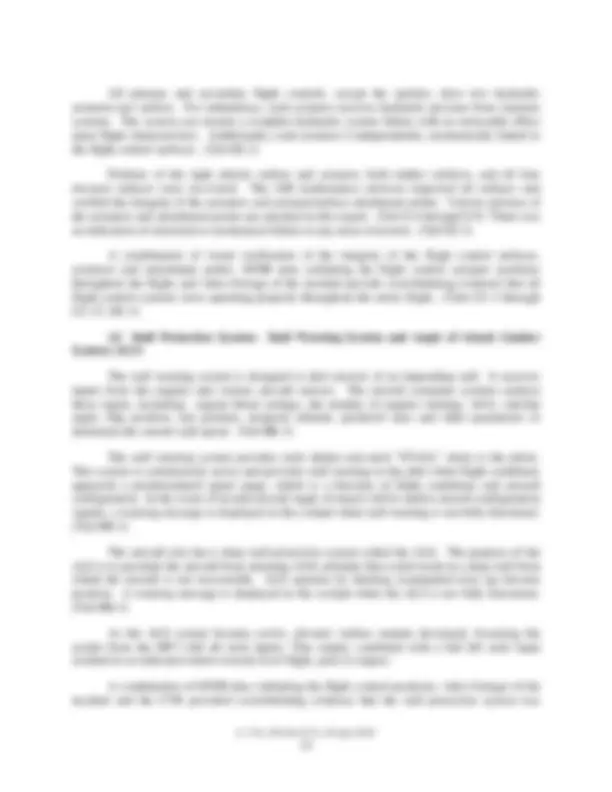
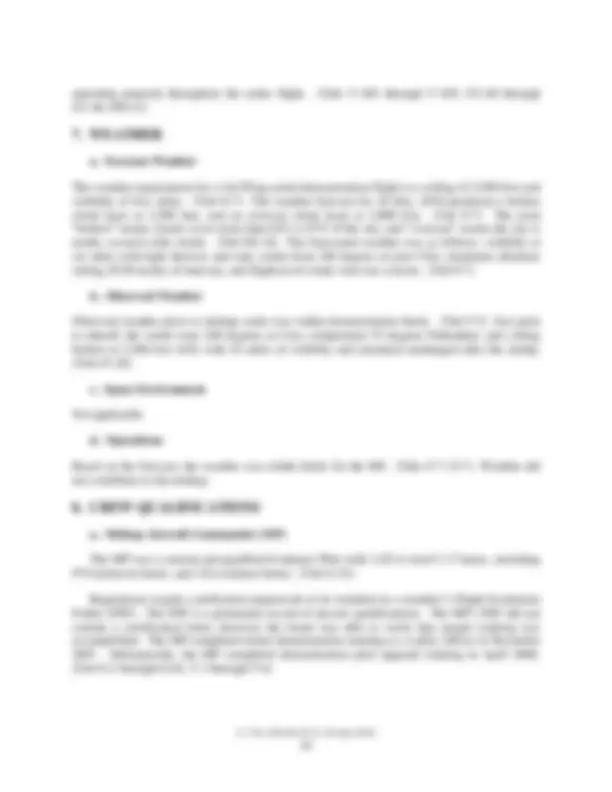
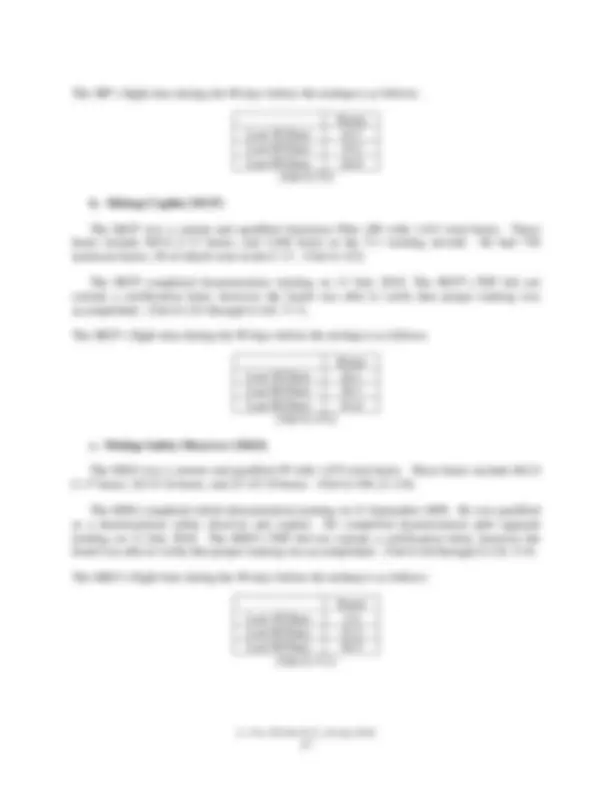
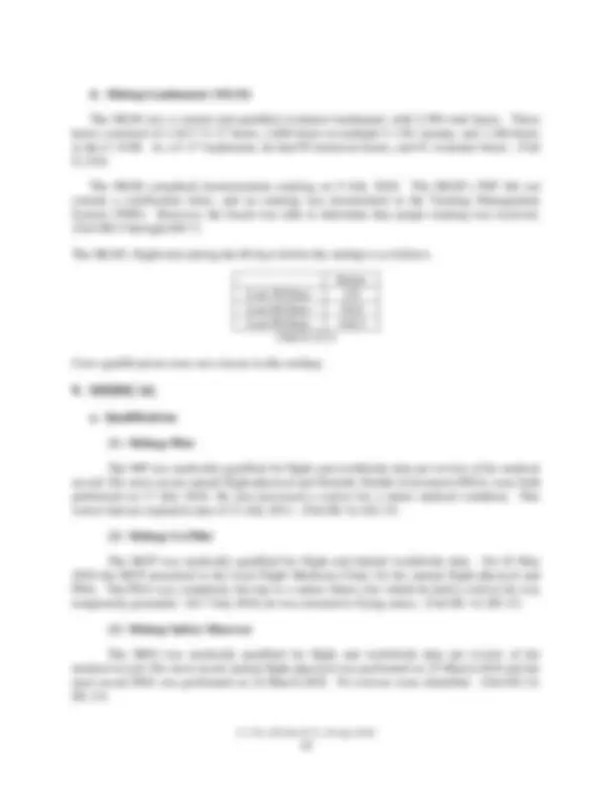
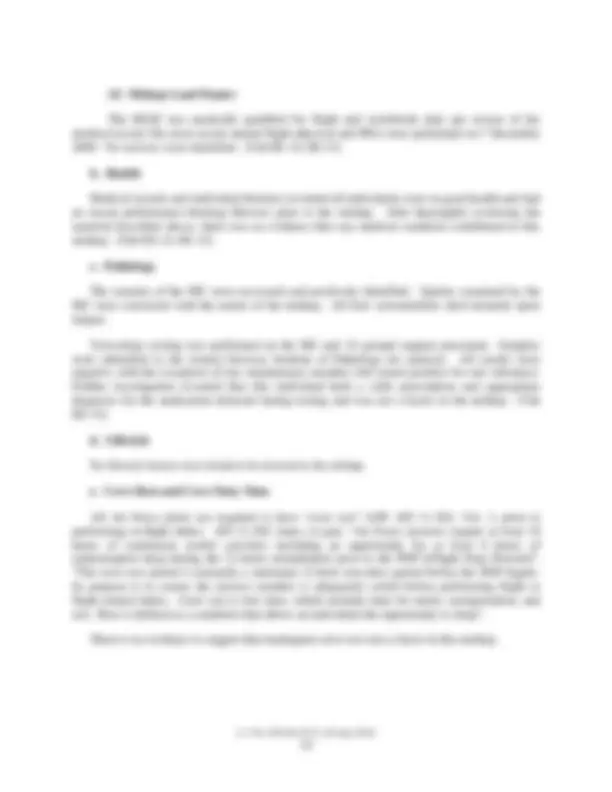
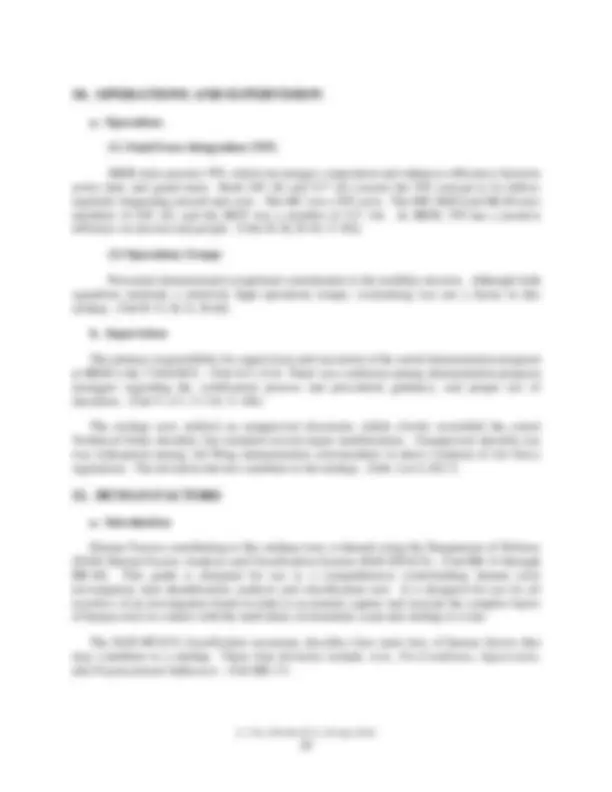
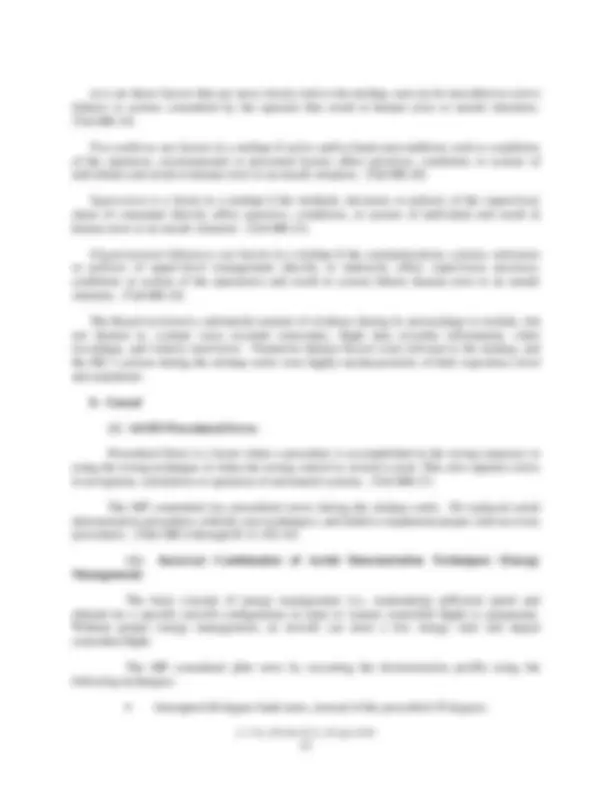
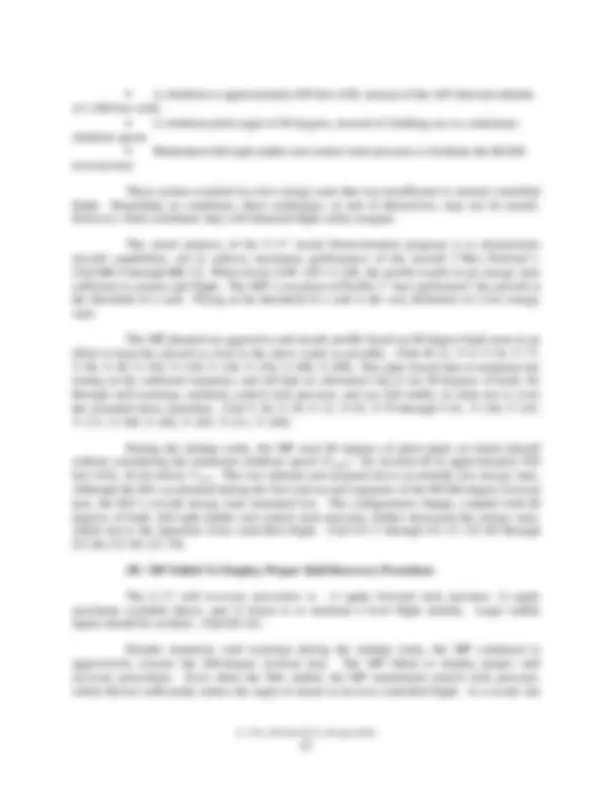
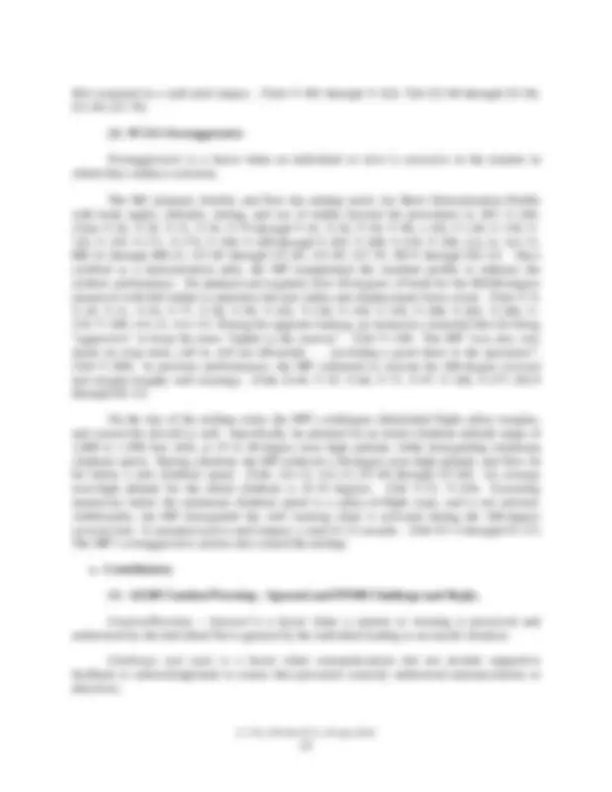
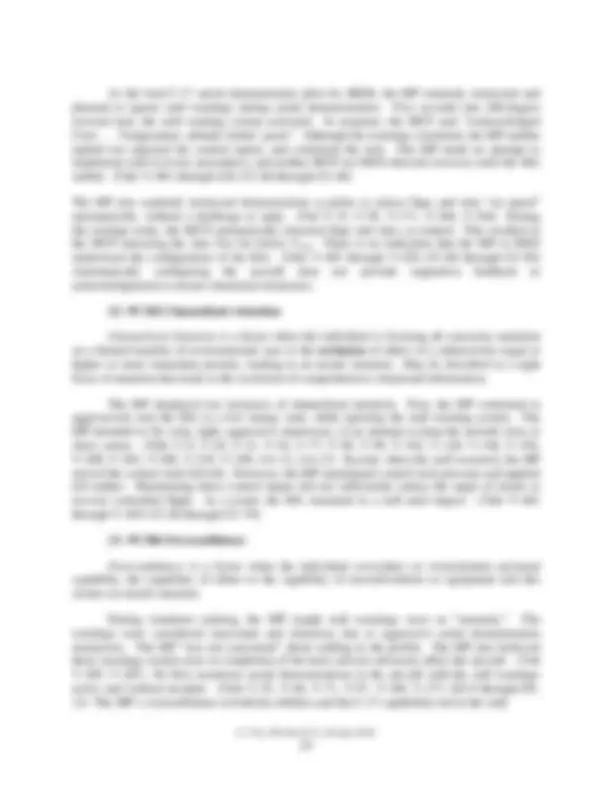
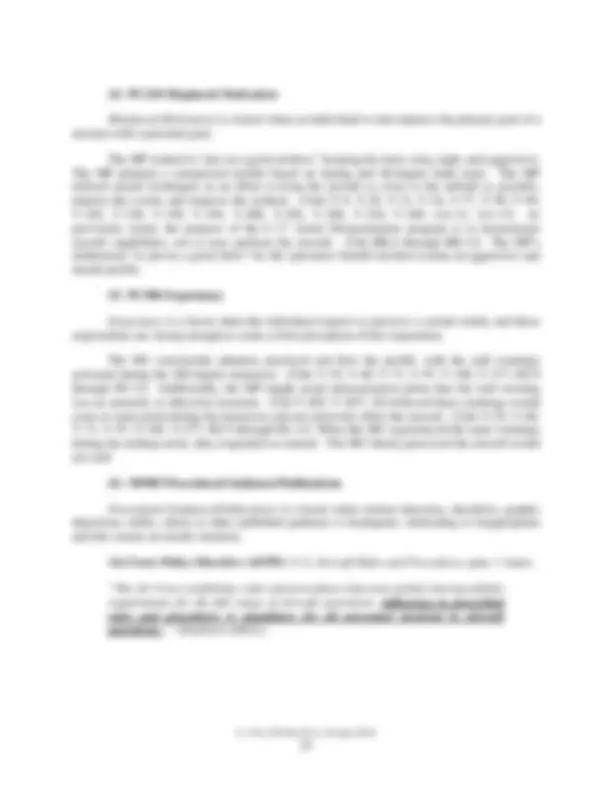
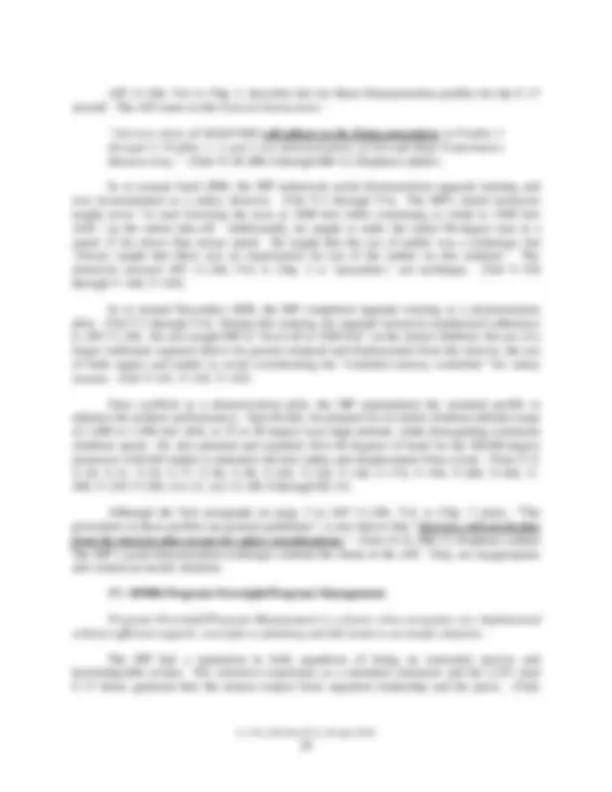
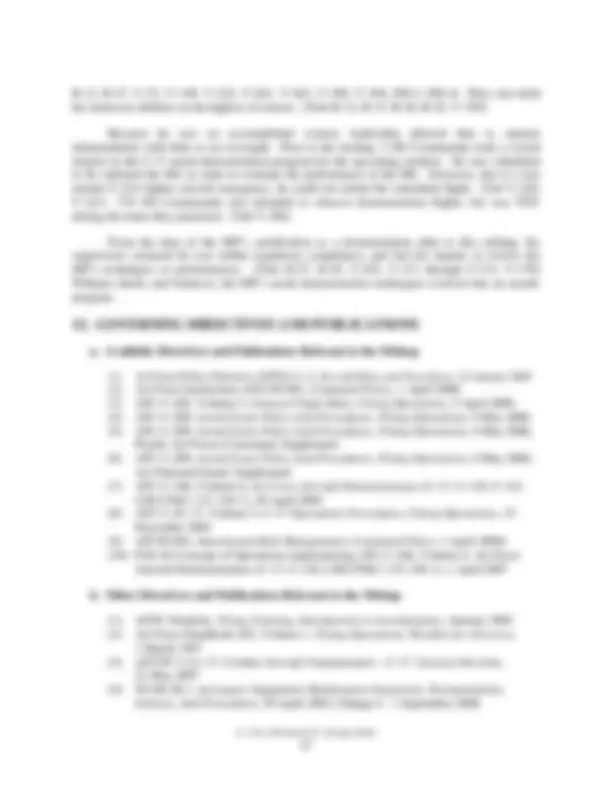
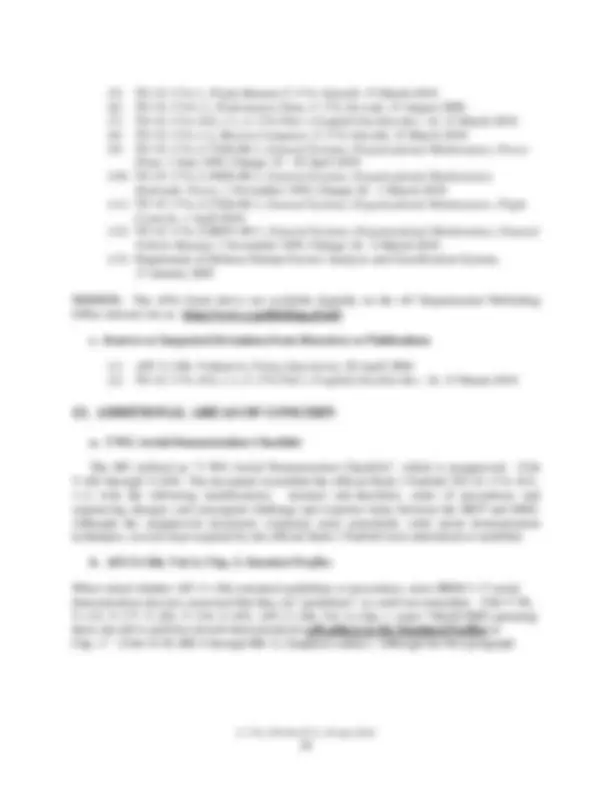
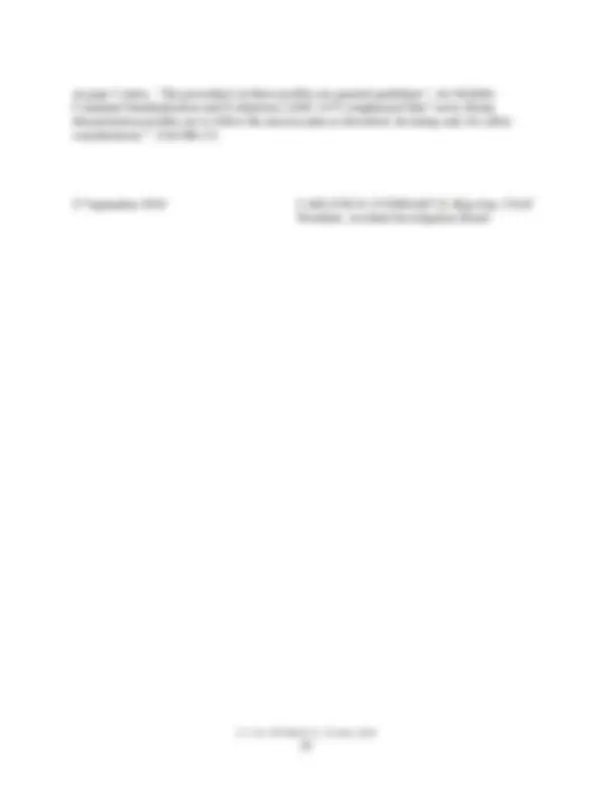
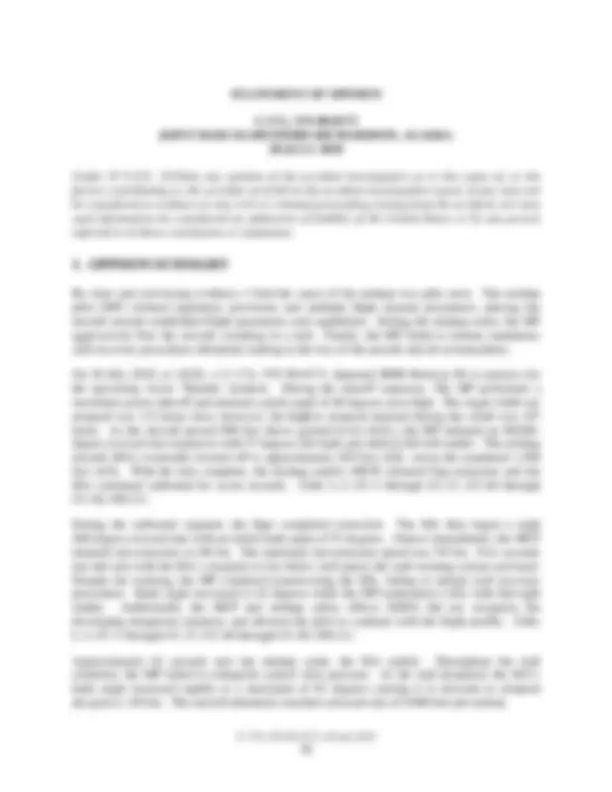
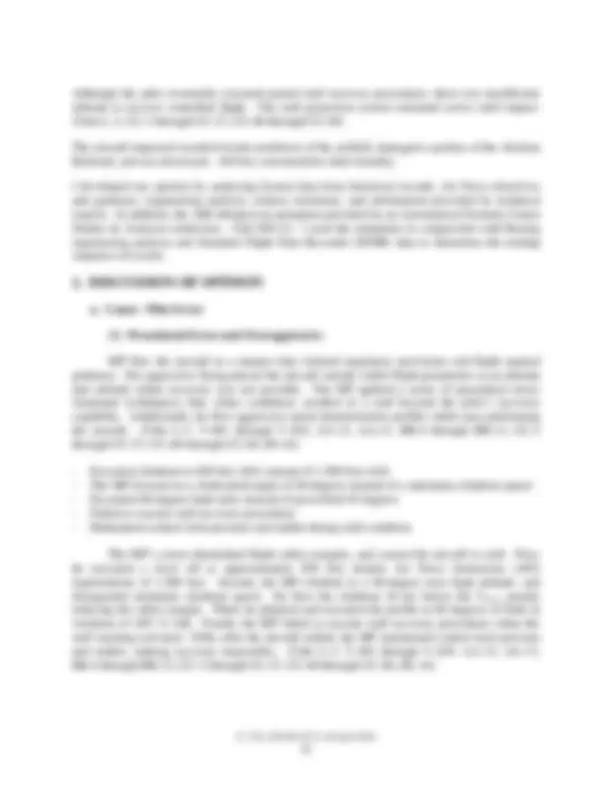
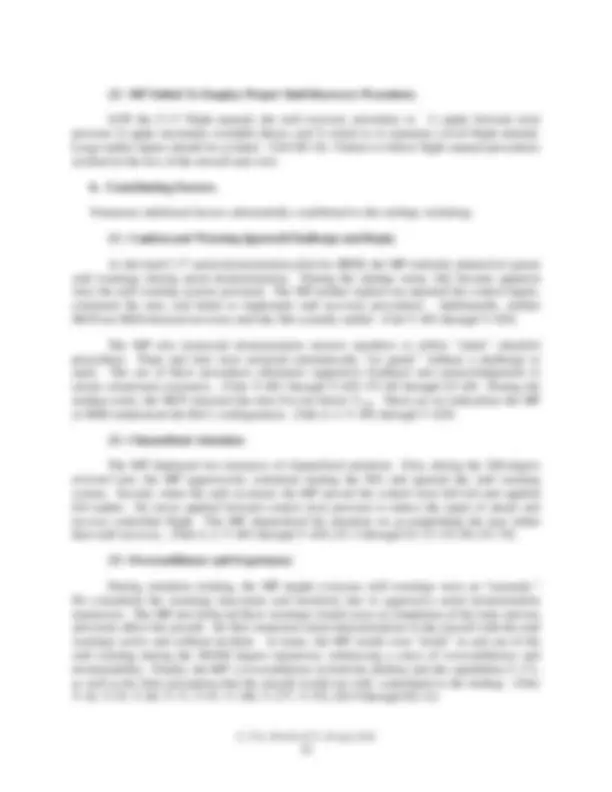
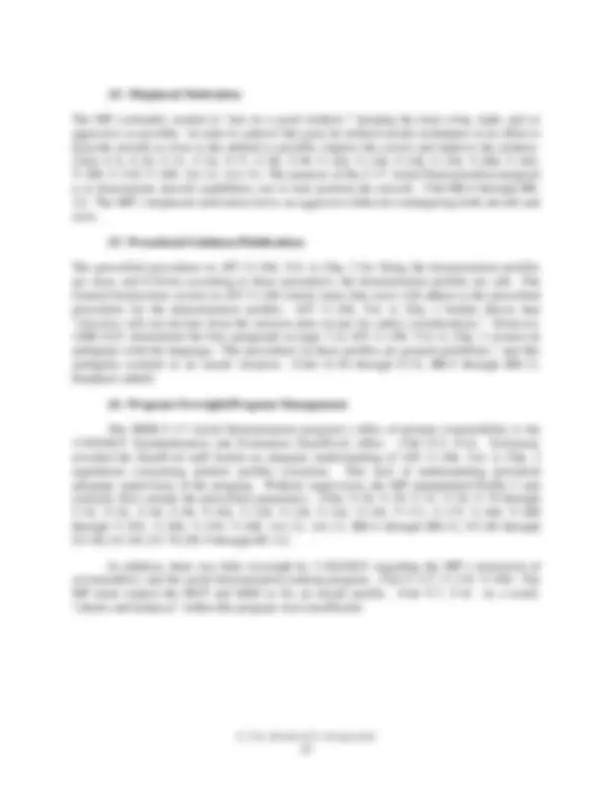
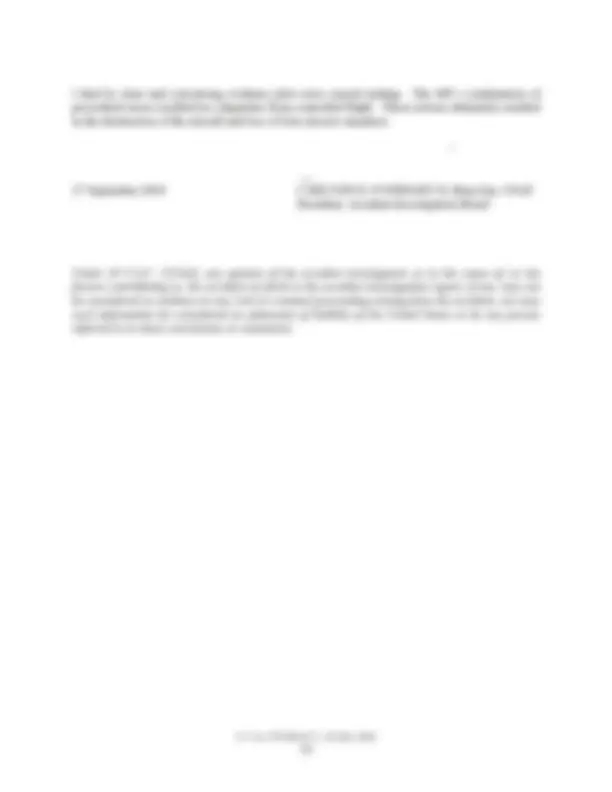
Study with the several resources on Docsity
Earn points by helping other students or get them with a premium plan
Prepare for your exams
Study with the several resources on Docsity
Earn points to download
Earn points by helping other students or get them with a premium plan
Community
Ask the community for help and clear up your study doubts
Discover the best universities in your country according to Docsity users
Free resources
Download our free guides on studying techniques, anxiety management strategies, and thesis advice from Docsity tutors
UNITED STATES AIR FORCE. AIRCRAFT ACCIDENT INVESTIGATION. BOARD REPORT. C-17A, T/N 00-0173. 3. RD. WING. JOINT BASE ELMENDORF-RICHARDSON, ALASKA.
Typology: Exams
1 / 41
This page cannot be seen from the preview
Don't miss anything!
RD
Under 10 U.S.C. 2254(d), any opinion of the accident investigators as to the cause of, or the factors contributing to, the accident set forth in the accident investigation report, if any, may not be considered as evidence in any civil or criminal proceeding arising from the accident, nor may such information be considered an admission of liability of the United States or by any person referred to in those conclusions or statements.
On 28 July 2010, at approximately 1822 hours local time (L), a C-17A, Tail Number 00-0173, executed a takeoff from Runway 06 to practice maneuvers for the upcoming 31 Jul 10 Arctic Thunder Airshow at Joint Base Elmendorf-Richardson. After the initial climbout and left turn, the mishap pilot executed an aggressive right turn. As the aircraft banked, the stall warning system activated to alert the crew of an impending stall. Instead of implementing stall recovery procedures, the pilot continued the turn as planned, and the aircraft entered a stall from which recovery was not possible. Although the pilot eventually attempted to recover the aircraft, he employed incorrect procedures, and there was not sufficient altitude to regain controlled flight. The aircraft impacted wooded terrain northwest of the airfield, damaged a portion of the Alaskan Railroad, and was destroyed.
The mishap aircraft was assigned to the 3rd Wing based at Joint Base Elmendorf-Richardson, Alaska. The mishap crew was an integrated crew with members from both the 249th and 517th Airlift Squadrons. The mishap crew consisted of the mishap pilot, the mishap copilot, the mishap safety observer and the mishap loadmaster. All four aircrew members died instantly. The mishap aircraft was valued at $184,570,581. The impact also damaged Alaskan Railroad train tracks that transect the base. There were no civilian casualties.
The board president found clear and convincing evidence that the cause of the mishap was pilot error. The mishap pilot violated regulatory provisions and multiple flight manual procedures, placing the aircraft outside established flight parameters at an attitude and altitude where recovery was not possible. Furthermore, the mishap copilot and mishap safety observer did not realize the developing dangerous situation and failed to make appropriate inputs. In addition to multiple procedural errors, the board president found sufficient evidence that the crew on the flight deck ignored cautions and warnings and failed to respond to various challenge and reply items. The board also found channelized attention, overconfidence, expectancy, misplaced motivation, procedural guidance, and program oversight substantially contributed to the mishap.
- C-17A, T/N 00-0173, 28 July - C-17A, T/N 00- SUMMARY OF FACTS AND STATEMENT OF OPINION - 28 JULY
C-17A, T/N 00-0173, 28 July 2010 v
PF Pilot Flying PHA Physical Health Assessment PIT Pilot Instructor Training PM Pilot Monitoring PR Preflight Inspection PRO SUPER Production Supervisor PSI Pounds Per Square Inch PT Physical Training QA Quality Assurance QC Quality Check QUAL Qualification RACM Right Additional Crewmember RAP Ready Aircrew Program RED X Safety of Flight RPM Revolutions per Minute SAR Search and Rescue SCEFC Spoiler Controller/Electronic Flap Computer SEFE Standardization Evaluation Flight Examiner SFDR Standard Flight Data Recorder SIM Simulator S/N Serial Number
SOF Supervisor of Flying Sortie Flight STAN EVAL Standardization and Evaluation TACAN Tactical Air Navigation TCTO Time Compliance Technical Order TDY Temporary Duty Tech School Technical School TFI Total Force Integration TH Thru-Flight T/N Tail Number TO Technical Order TMS Training Management System TSgt Technical Sergeant U.S. United States USAF United States Air Force VFR Visual Flight Rules V (^) mco Minimum Climbout Speed V (^) mfr Minimum Flap Retract Speed V (^) msr Minimum Slat Retract Speed Vol. Volume WCC Warning & Caution Computer Z Zulu or Greenwich Mean Time
The above list was compiled from the Summary of Facts, the Statement of Opinion, the Index of Tabs, and Witness Testimony (Tab V).
C-17A, T/N 00-0173, 28 July 2010 1
a. Authority
On 4 August 2010, General Gary L. North, Commander, Pacific Air Forces (PACAF), appointed Brigadier General Carlton D. Everhart II, to conduct an aircraft accident investigation of a mishap that occurred on 28 July 2010, involving a C-17A Globemaster III aircraft, tail number (T/N) 00-0173, at Joint Base Elmendorf-Richardson (JBER), Alaska (AK). The investigation was conducted at JBER, from 28 August 2010 through 27 September 2010. Technical advisors were [AIB Pilot Member], [AIB Maintenance Officer Member], [AIB Legal Advisor], [AIB Medical Advisor], [AIB Maintenance Enlisted Member], [AIB Recorder], and [AIB Court Reporter]. (Tab Y)
b. Purpose
This is a legal investigation convened to inquire into the facts surrounding the aircraft or aerospace accident, to prepare a publicly-releasable report, and to gather and preserve all. available evidence for use in litigation, claims, disciplinary actions, administrative proceedings, and for other purposes.
At 1822 hours local time (L), 28 July 2010, the mishap aircraft (MA), a C-17A, T/N 00-0173, departed JBER to practice for the upcoming Arctic Thunder Airshow. The mishap crew (MC) consisted of the mishap pilot (MP), the mishap copilot (MCP), the mishap safety officer (MSO), and the mishap loadmaster (MLM). The MP performed a maximum power takeoff at 40 degrees nose high attitude. The MA leveled off at approximately 850 feet above ground level (AGL). The MP then executed a left-hand 80-degree turn, continued outbound for seven seconds, and then initiated a right 260-degree reversal turn. Five seconds into the right turn, the stall warning system activated. As the MP continued the maneuver, the MA’s bank angle increased to 62 degrees. The MP utilized full right rudder and pulled the control stick aft, which stalled the aircraft. The aircraft ultimately reached a bank angle of 82 degrees and a descent rate of 9, feet per minute. The MA impacted wooded terrain northwest of the airfield and was destroyed. Additional damage occurred to Alaskan Railroad train tracks. The MA was valued at $184,570,581. All four aircrew members died instantly. There were no civilian casualties.
The MA belonged to the 3rd Wing at JBER. It was operated by both the 517th Airlift Squadron (AS) and the Alaska Air National Guard (AK ANG) squadron, the 249th AS. The mishap crew (MC) included three Air National Guard (ANG) members, the MP, MLM, and
C-17A, T/N 00-0173, 28 July 2010 3
and communications functions necessary to perform tactical warning and attack assessment in defense of Alaska. (Tab FF-12)
(2) 3rd Wing, Joint Base Elmendorf-Richardson, Alaska
The 3rd Wing is a composite wing composed of two groups and five flying squadrons operating the C-12, C-17, E-3, and F-22. It is located on JBER in Anchorage, AK. Its mission is to support and defend U.S. interests in the Asia Pacific region and around the world by providing units who are ready for worldwide air power projection and a base that is capable of meeting the Pacific Command's theater staging and throughput requirements. (Tab FF-14)
(3) 176th Wing, Joint Base Elmendorf-Richardson, Alaska
The 176th Wing is part of the AK ANG, and is also a composite wing composed of four groups and five flying squadrons operating the C-17, HC-130, HH-60, and E-3. Its units are located on Kulis Air National Guard Base and JBER, both of which are in Anchorage, AK, as well as Eielson Air Force Base (AFB) outside of Fairbanks, AK. Its mission includes search and rescue, tactical and strategic airlift, air control, and rescue coordination. (Tab FF-18)
(4) 517th Airlift Squadron
The 517 AS is part of the 3rd Wing, and it operates the C-17 and C-12 out of JBER. The squadron's primary missions are to support worldwide airlift, airdrop, and airland requirements while providing airlift for theater deployed forces and resupply of remote Alaskan long-range radar sites in support of the U.S. Pacific Command, the North American Aerospace Defense Command, and the U.S. Transportation Command. Its associate unit is the 249 AS, meaning that the two units utilize the same aircraft and mix aircrews for missions. The two units keep independent chains of command but share resources. (Tab FF-21)
(5) 249th Airlift Squadron
In September 2009 the 249 AS was officially activated by the Department of Defense as a squadron of the 176th Wing of the AK ANG. It is the associate unit of the 517 AS on JBER, and its members operate the C-17 inter-mixed with members of the 517 AS. Specifically, the 249 AS's mission is to recruit, train and provide combat-ready C- aircrews for global mobility missions that supply and sustain America's armed forces. (Tab FF-23)
C-17A, T/N 00-0173, 28 July 2010 4
e. C-17A – Globemaster III
The C-17 is capable of rapid strategic delivery of troops and all types of cargo to main operating bases or directly to forward bases in the deployment area. The aircraft can perform tactical airlift and airdrop missions and can also transport litters and ambulatory patients during aeromedical evacuations when required. (Tab FF-24)
The C-17 is approximately 174 feet long and has a wingspan of 169 feet, 10 inches, and its maximum takeoff weight is 585,000 pounds. It is powered by four, fully reversible F117-PW- (Pratt & Whitney PW2040) engines, each producing 40,440 pounds of thrust. The C-17 can cruise at 450 knots (kts), and its range is global with in-flight refueling. The C-17 is crewed by a pilot, copilot, and loadmaster. The aircraft can perform missions as diverse as airdrop of 102 paratroopers or aeromedical transport of 54 patients. (Tab FF-24)
a. Mission
The mishap sortie (MS) was a practice flight for the JBER Arctic Thunder Airshow, scheduled for the weekend of 31 July 2010. (Tab AA-5, AA-6) The sortie was authorized by the 176th Wing, in coordination with the 3rd Wing, and involved ANG and active duty Airmen from JBER. It was planned and briefed as an aerial demonstration proficiency and currency flight, involving one C-17A aircraft, Callsign Sitka 43. (Tab K-4) C-17 aerial demonstration flights typically consists of a single aircraft, which conducts a series of practice demonstration maneuvers, defined by Air Force Instruction (AFI) 11-246, Vol. 6, as “profiles”. There are four distinct profiles, the first three ranging from six to twelve minutes in length. The fourth incorporates an airdrop demonstration, where personnel or cargo are released from the aircraft via parachutes. For this particular flight, the mishap crew (MC) planned to fly the Profile 3, known as the 12-minute profile. (Tab BB-4 through BB-12)
(1) Aerial Demonstration Profile – Profile 3 (12-minute Profile)
The relevant components of Profile 3 as related to this mishap were: maximum performance climb to 1,500 feet AGL, 80/260-degree reversal turn, and the 500-foot AGL high- speed pass. (Tab BB-6)
The maximum performance climb requires the pilot to pitch the aircraft nose upward to achieve minimum climbout speed, defined as V (^) mco. V (^) mco is the speed required to clear an
C-17A, T/N 00-0173, 28 July 2010 6
(3) Airspace Considerations
The MS was flown in airspace controlled by Elmendorf Air Traffic Control Tower. The MC maintained radio contact with, and remained in sight of the tower throughout the flight. For safety purposes, Elmendorf airspace was only open to Sitka 43. (Tab N-21) Airfield operations published a Notice to Airman (NOTAM), to inform all aircraft operators of the planned demonstration practice. (Tab K-7)
b. Planning
The day prior to the mishap, between 0930 and 1100L, the MP, MCP, and MSO utilized the simulator (sim) to practice several aerial demonstration profiles, including Profile 3. (Tab V-77) Afterwards, the crewmembers completed their mission planning for the next day’s aerial demonstration practice.
c. Preflight
On 28 July 2010, the MC arrived at the consolidated 517 / 249 AS building. The MP arrived at 0800, the MCP at 0901L, and the MSO and MLM at 1430L. The crew used Operational Risk Management (ORM) to evaluate mission risk. ORM is a decision-making process to systematically evaluate possible courses of action, identify risks and benefits, and determine the best course of action for any given situation. The ORM category for the mission was in the “Caution” range based on aircraft commander and squadron assessments. The “Caution” score was due to the complex and demanding nature of the mission. All crewmembers determined they were safe and prepared to fly the planned mission. (Tab AA-8)
Prior to the mission briefing, the Assistant Director of Operations informed the MC that they would accomplish an Engine Running Crew Change (ERCC) due to unscheduled maintenance on their originally assigned aircraft. (Tab V-44) During an ERCC, the incoming crew boards the aircraft and receives an aircraft status brief from the outgoing crew. The pilot and copilot positions are swapped-out one at a time, to ensure a qualified pilot is always at the controls. This is a commonly practiced procedure.
C-17A, T/N 00-0173, 28 July 2010 7
The MC briefed for the practice flight from approximately 1515 to 1615L. (Tabs V-400, AA-10, AA-11) Based on recovered documents, the crew reviewed and discussed NOTAMS, the weather forecast, and other pertinent safety of flight information. (Tabs F-7, K-6) The MP filed a Visual Flight Rules (VFR) flight plan, and planned to remain within 20 nautical miles of the airfield. (Tab K-3)
The crew arrived at the MA at approximately 1720L, and took control of the aircraft from the outgoing crew. During the ERCC, the outgoing crew briefed the aircraft had no malfunctions. (Tab V-401 through V-429)
d. Summary of Accident
(1) Weather Observation Flight
Thirty minutes prior to the mishap sortie, the MC flew the MA in the local area to observe the weather. The purpose of this flight was to determine if the weather was acceptable for their demonstration practice. During the nine-minute flight, the MC evaluated winds and observed flight conditions around the airfield. The MA flew normally and the weather was within limits. (Tab V-401 through V-429)
(2) Aerial Demonstration Practice Flight (Mishap Sortie)
After the weather observation flight, the MC landed and waited approximately 30 minutes to begin their aerial demonstration practice. (Tab V-401 through V-429) Once they received clearance, the MP aligned the aircraft on the runway and released brakes at 1821:31L. During the takeoff sequence, the MP “rotated” (raised the nose of the aircraft) and attained a maximum pitch angle of 40 degrees nose-high. (Tab L-3)
The target climbout airspeed was 133 kts. The highest airspeed attained during the climbout was 107 kts. As the aircraft passed 800 feet AGL, the MP initiated the first segment of the 80/260-degree reversal turn. He turned the aircraft left at 57 degrees of bank to a heading of 340 degrees and leveled-off at 852 feet AGL. After completing the turn, the MCP initiated flap retraction when the airspeed reached 151 kts. The minimum flap retraction speed (Vmfr) was 150 kts. The MP continued outbound for seven seconds as the flaps completed retraction. (Tab L-3)
The MP turned right at an initial bank angle of 53 degrees to begin the third segment of the 80/260-degree reversal turn. The MCP initiated slat retraction when the airspeed reached 188 kts. The minimum slat retraction speed (V (^) msr) was 193 kts. Five seconds into the right turn, the stall warning system activated. At this time, the MA’s configuration was full right rudder, the control stick aft, and slats retracting. The airspeed was 199 kts, 6 kts below stall airspeed. (Tabs L-3, CC-3 through CC-27, CC-60 through CC-68, DD-21)
When the stall warning occurred, the MCP responded “acknowledged crew... temperature, altitude lookin’ good.” (Tabs L-3, N-18, CC-3 through CC-27) The MP continued the turn using full right rudder, which increased the MA’s bank angle to 62 degrees. The maximum allowable bank angle for the C-17 is 60 degrees. (Tab BB-3) The MP also continued
C-17A, T/N 00-0173, 28 July 2010 9
e. Impact
The MA impacted wooded terrain northwest of the airfield at 63.6 degrees of right bank, 16. degrees nose-low at 184 kts on 28 July 2010 at 1822L. (Tabs L-3, CC-15) The MA exploded, burned for approximately 36 hours and was destroyed. (Tab H-4)
f. Egress and Aircrew Flight Equipment
All life support equipment on board the MA was inspected prior to takeoff and deemed serviceable by both aircrews. (Tab V-401) Due to the immediate destruction of the aircraft upon impact, there was no opportunity for the MC to use survival gear or life support equipment. (Tab H-6)
g. Search and Rescue (SAR)
At 1822L, JBER Fire Dispatch Center received notification of a C-17 crash. Emergency vehicles responded immediately. Battalion 2 (Command & Control Vehicle) and Engine 3 were the first units to arrive. Access to the site was extremely limited, with debris and fire scattered over a large area. Battalion 2 took initial command and directed other arriving vehicles into the crash area. Rescue personnel arrived in seven minutes and immediately began searching for potential survivors. No survivors were found. (Tab DD-8)
h. Recovery of Remains
Crash, fire, and rescue personnel were pivotal to recovery efforts. Remains were recovered from 30 July 2010 to 1 August 2010 and transferred to JBER Mortuary Affairs. (Tab DD- through DD-20)
a. Forms Documentation
The 3rd Maintenance Group, 703rd Aircraft Maintenance Squadron, JBER, maintained the aircraft forms for the MA. All maintenance was documented on Air Force Technical Order (AFTO) 781 forms and in GO81 (Core Automated Maintenance System for Mobility). The purpose of AFTO 781 series forms is to document various maintenance actions. They are maintained in a binder specifically assigned to each aircraft. GO81 is an automated database of aircraft discrepancies, maintenance repair actions and flying history. The current AFTO 781 series forms were aboard the MA and destroyed in the crash. The historical AFTO 781 series forms revealed minor documentation errors, commonly found in maintenance forms. These minor errors were previously reconciled. A detailed 90-day review of records and forms revealed no evidence of mechanical, structural or electrical failure, which could have contributed to the mishap. (Tabs D-3, U-8 through U-82, U-111)
A comprehensive review of all AFTO 781 series forms and GO81 was accomplished to determine airworthiness of the MA. (Tab EE-3)
C-17A, T/N 00-0173, 28 July 2010 10
Time Compliance Technical Orders (TCTOs) are inspections or maintenance procedures required before specific dates or flight. The AFTO 781 series forms and GO81 track compliance times and dates. No TCTO’s restricted the MA from flying. Historical records showed all TCTOs were accomplished IAW applicable guidance. TCTO non-compliance did not contribute to the accident. (Tabs D-3, U-8 through U-82, U-116)
Prior to the mishap sortie, the MA’s total aircraft time was 13,361.6 hours. All four engines were Pratt and Whitney (P&W) F117-PW-100 turbofan engines. The #1 engine (left outboard engine), serial number (S/N) 00PW170316, had 11,619.7 hours total engine operating time with 9,836 operating cycles. The #2 engine (left inboard engine), S/N 00PW170333, had 9,523. hours total engine operating time with 7,883 operating cycles. The #3 engine (right inboard engine), S/N 00PW170049, had 14,300.2 hours total engine operating time with 10, operating cycles. The #4 engine (right outboard engine), S/N 00PW170348, had 11,276.7 hours total engine operating time with 5,875 operating cycles. (Tabs D-3, U-93, U-110)
The MA flew 126 flights, for a total of 302.9 hours, within 90 days of the mishap. There were no major maintenance discrepancies that would have prevented the MA from accomplishing the aerial demonstration mission on 28 July 2010. Also, historical records did not reveal any recurring maintenance problems. (Tabs D-3, U-3 through U-82)
b. Inspections
(1) Mishap Aircraft
Global Reach Improvement Program / Heavy Fleet Maintenance (GRIP) is a periodic cycle of in-depth inspections. These inspections usually coincide with the paint cycle of the aircraft. The C-17A GRIP cycle is every five years. The GRIP inspections are performed IAW Technical Order (TO) 00-20-1. The most recent GRIP inspection was completed 21 September
Home Station Checks (HSC) are periodic inspections performed in 180-day increments, encompassing a 720-day cycle. The HSC inspections are performed IAW TO 00-20-1. These on-site inspections are performed to ensure the airworthiness of the aircraft. The most recent HSC performed was completed on 15 April 2010. The next scheduled HSC was due on 12 October 2010. (Tab D-3) The HSC inspection was current and not contributory to the mishap. (Tab EE-3)
A Pre-Flight (PR) is a flight preparedness inspection performed prior to flight and is a valid inspection for 72 hours once completed. The PR inspections are performed IAW TO 00- 20-1. The purpose of this inspection is to visually inspect and operationally checkout various areas and systems of the aircraft in preparation for a flying period. The most recent PR was performed on 26 July 2010, at 2200L, approximately 45 hours and 30 minutes prior to the incident. (Tab D-3) The PR inspection was current and not contributory to the mishap. (Tab EE-3)
C-17A, T/N 00-0173, 28 July 2010 12
The interim safety board collected hydraulic fluid samples from the wreckage, which Boeing analyzed. Boeing determined the fluid samples were “fairly typical for a sample of in-service fluid.” They also noted water contamination in the samples due to exposure to the environment and fire fighting measures. (Tab CC-42)
Engine oil samples were not obtained from the MA post-impact. The impact destroyed all four engine oil reservoirs and gearboxes. No viable samples were obtained. All four engines were performing properly throughout the flight, warranting no further investigation. (Tab L-3)
f. Unscheduled Maintenance
There was no unscheduled maintenance. (Tab V-21, V-112)
a. Structures and Systems
The AIB performed a thorough inspection of all aircraft systems and concluded all systems performed normally up to the time of impact. Analysis was verified by both Boeing and flight test experts. Various systems and aircraft computers were recovered, including: engines, flight control surfaces (portions of the right aileron surface, rudder surfaces, elevator surfaces, and their respective actuators), two Flight Control Computers (FCC), one Warning & Caution Computer (WCC), one Air Data Computer (ADC), one Spoiler Control / Electronic Flight Control Computer (SCEFC), one Core Integrated Processor (CIP) and one Air Propulsion Data Management Computer (APDMC). Inspection by component manufacturers and Boeing, as well as the Standard Flight Data Recorder (SFDR), confirmed each unit functioned normally prior to impact. (Tab CC-3 through CC-27, CC-48)
b. Evaluations and Analyses
(1) Engine Performance
During the mishap sortie, all four engines were set to maximum thrust and remained so throughout the flight. All four engines maintained 92.5% High Pressure Compressor Revolutions per Minute (N2 RPM). This is the typical indication expected from a maximum thrust setting. The Engine Pressure Ratio (EPR) is an indication of the pressure of air exiting engine compared to the pressure of air entering the engine. This is an indication of the performance levels of each engine. EPR indications may vary in small levels due to atmospheric conditions, altitudes and the angle of attack (AOA) of the aircraft, limiting the amount of air available for utilization. The EPR indications of the MA were all stable throughout the flight, indicating there was no measureable lack of propulsion from the engines. All other temperature and fuel flow indications also support the viability of all four engines installed on the MA. A visual inspection of all engines was performed, indicating substantial damage from impact. There were no visual indications of engine malfunctions. (Tabs L-3, EE-3)
C-17A, T/N 00-0173, 28 July 2010 13
(2) Hydraulic Systems Performance
The C-17A has four independent hydraulic systems operating at 4,000 pounds per square inch (PSI). Each system is powered by engine driven hydraulic pumps (EDP). For redundancy, there is a primary and a secondary EDP installed on each respective engine. If primary EDP pressure drops below 3,400 PSI, the secondary EDP will engage to augment system pressure. A third electrically driven hydraulic pump augments each system, if needed. These pumps provide triple redundancy in each respective hydraulic system. All four hydraulic systems operating pressures were tracked and recorded on the SFDR. The data was analyzed to ensure proper systems operation. Pressures varied due to demand, but never fell below 3,536 PSI. This is well within the typical operating parameters. All four systems properly performed throughout the flight. (Tabs L-3, EE-3)
(3) Flight Control Systems Performance
The flight control system of the C-17A are separated into two categories: primary and secondary flight control surfaces. The primary flight control surfaces include the ailerons, elevators and rudders. (Tab EE-3)
Primary Flight Controls
The ailerons control roll around the longitudinal axis (a theoretical line running from the nose to the tail of the aircraft). There are two ailerons, each one located towards the end of each wing. The elevators control rotation around the pitch axis (a theoretical line running from wingtip to wingtip), to raise and lower the nose of the aircraft. There are four elevators located