
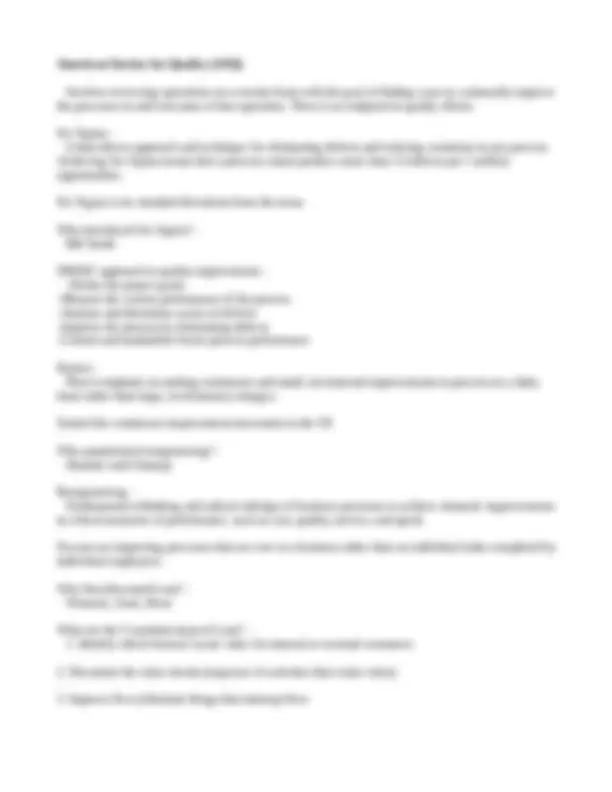
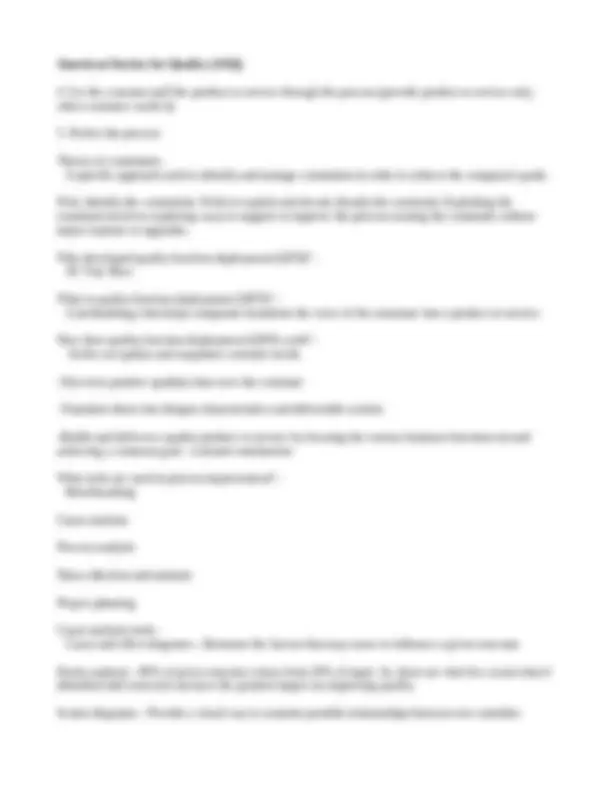
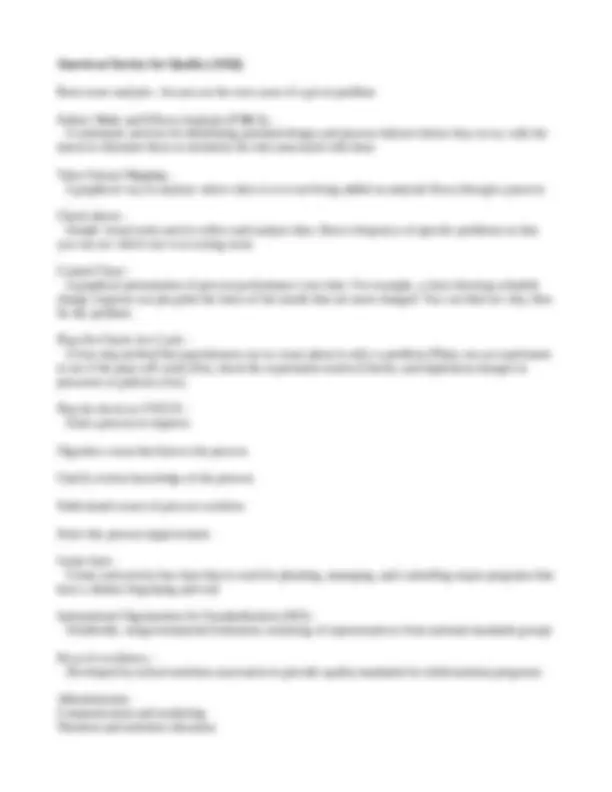
Study with the several resources on Docsity
Earn points by helping other students or get them with a premium plan
Prepare for your exams
Study with the several resources on Docsity
Earn points to download
Earn points by helping other students or get them with a premium plan
Community
Ask the community for help and clear up your study doubts
Discover the best universities in your country according to Docsity users
Free resources
Download our free guides on studying techniques, anxiety management strategies, and thesis advice from Docsity tutors
An overview of Total Quality Management (TQM) and Quality Assurance (QA). It explains the difference between the two and the components of TQM. The document also discusses Deming's 14 point system for TQM and the Plan-Do-Check-Act Cycle. Additionally, it covers various tools and techniques used in quality management such as Root cause analysis, Failure Mode and Effects Analysis (FMEA), Value Stream Mapping, Check sheets, Control Chart, Gantt chart, and FOCUS. The document also mentions the International Organization for Standardization (ISO) and the Malcolm Baldrige National Quality Improvement Act of 1987.
Typology: Exams
1 / 6
This page cannot be seen from the preview
Don't miss anything!
The American Society for Quality (ASQ) description of quality - -Quality is not a program; it is an approach to business -Quality is defined by the customer through his or her satisfaction -Quality is aimed at the performance excellence; anything less is an improvement opportunity
b. Eliminate management by objective. Eliminate management by numbers, numerical goals. Substitute leadership.
Root cause analysis - focuses on the root cause of a given problem Failure Mode and Effects Analysis (FMEA) - A systematic process for identifying potential design and process failures before they occur, with the intent to eliminate them or minimize the risk associated with them Value Stream Mapping - A graphical way to analyze where value is or is not being added as material flows through a process Check sheets - Simple visual tools used to collect and analyze data. Shows frequency of specific problems so that you can see which one is occurring most. Control Chart - A graphical presentation of process performance over time. For example, a chart showing schedule change requests can pin point the times of the month that are most changed. You can find out why, then fix the problem. Plan-Do-Check-Act Cycle - A four-step method that practitioners use to create plans to solve a problem (Plan), run an experiment to see if the plan will work (Do), check the experiment results (Check), and implement changes to processes or policies (Act). Plan do check act FOCUS - Find a process to improve Organize a team that knows the process Clarify current knowledge of the process Understand causes of process variation Select the process improvement Gantt chart - A time and activity bar chart that is used for planning, managing, and controlling major programs that have a distinct beginning and end. International Organization for Standardization (ISO) - Worldwide, nongovernmental federation consisting of representatives from national standards groups Keys of excellence - Developed by school nutrition association to provide quality standards for child nutrition programs Administration Communication and marketing Nutrition and nutrition education