
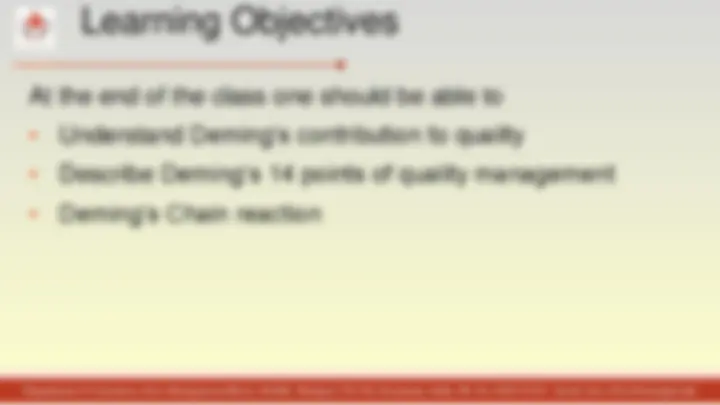
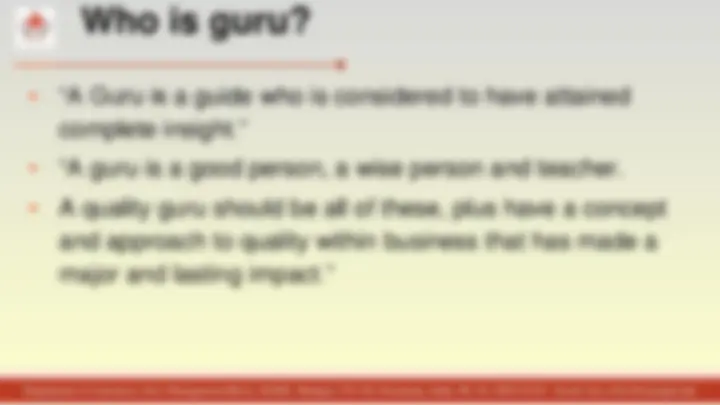
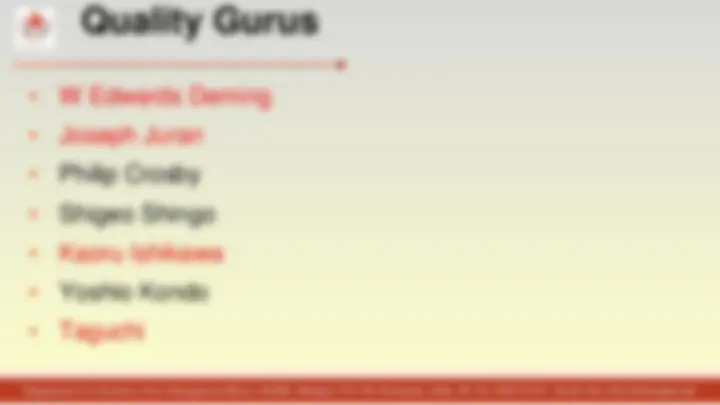
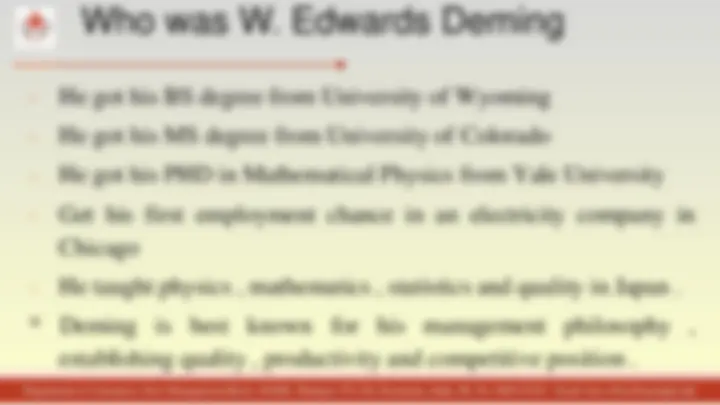
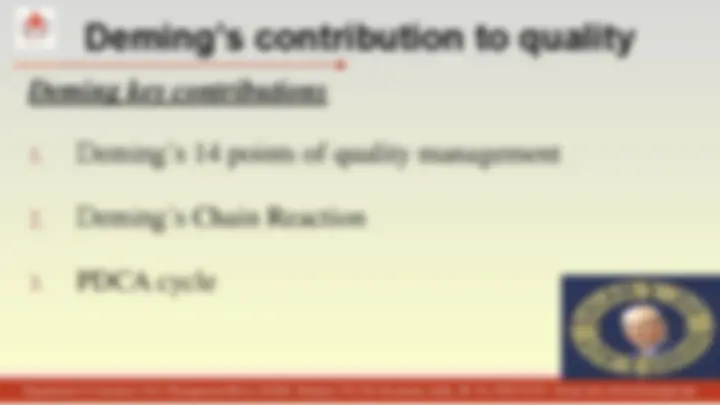
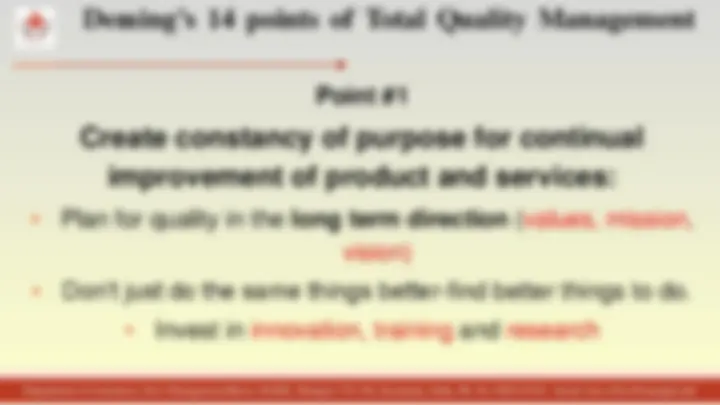
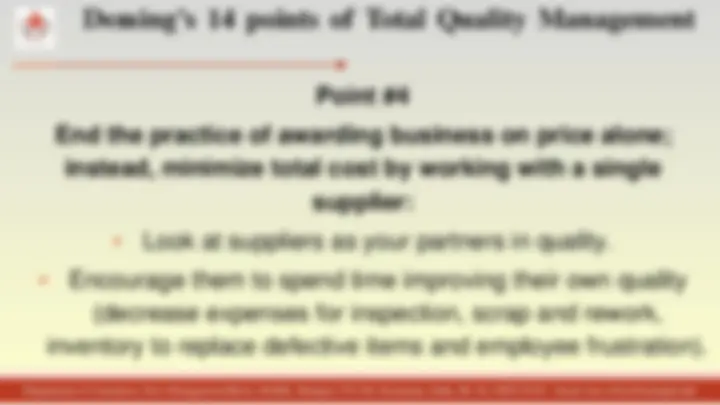
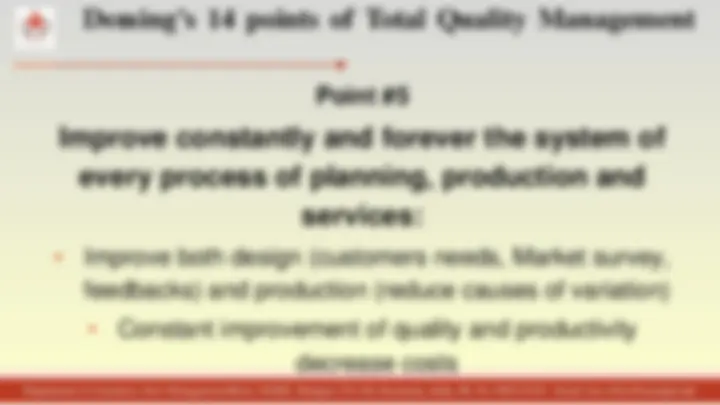
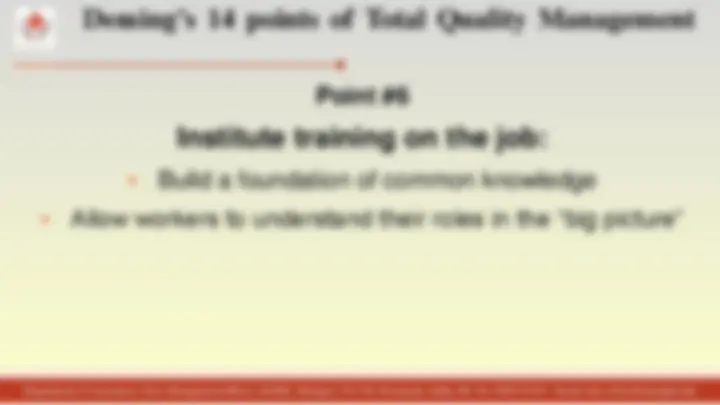
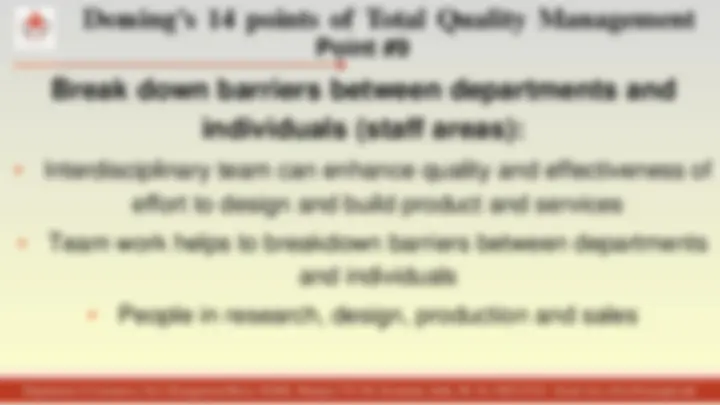
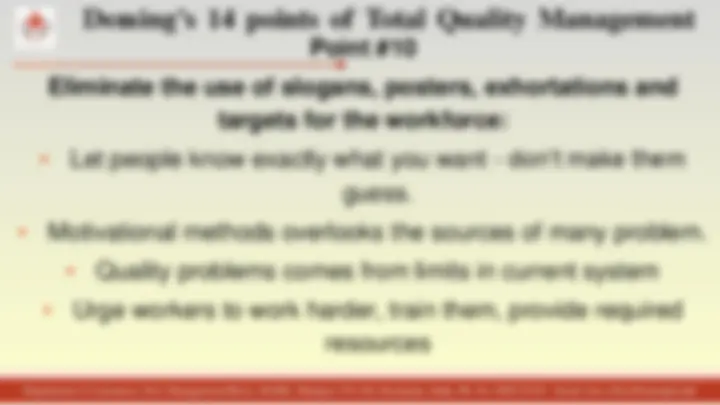
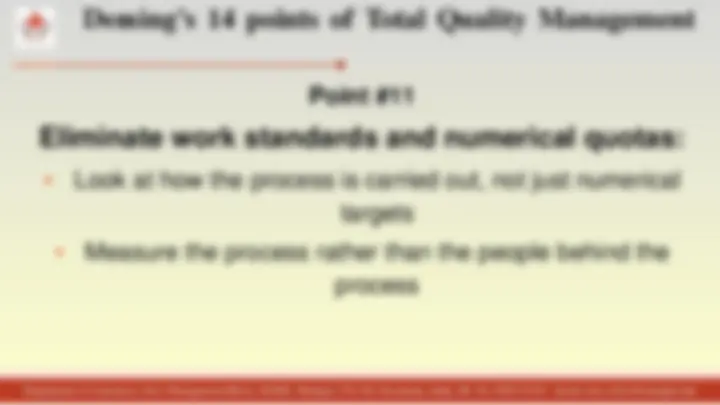
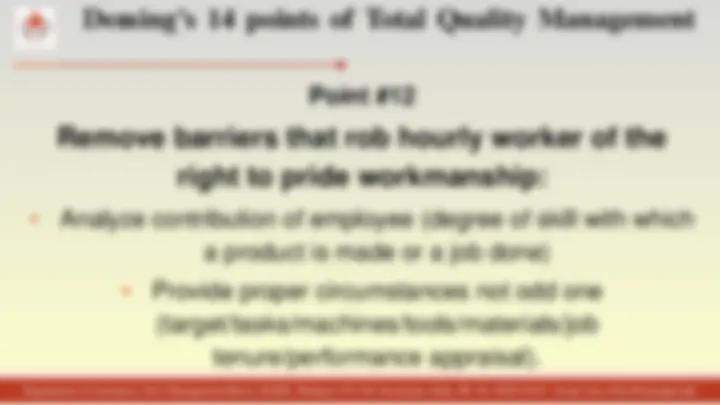
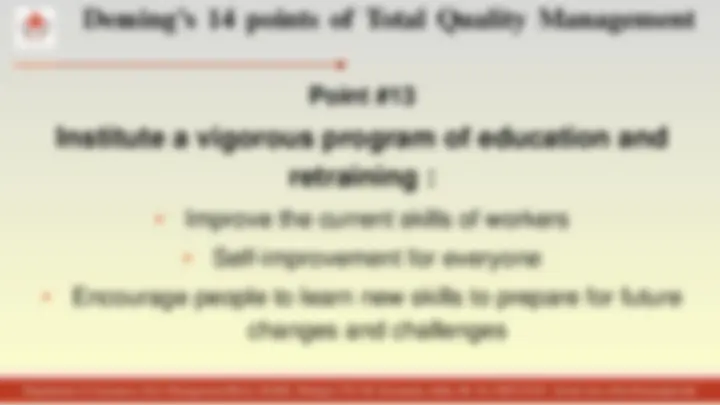
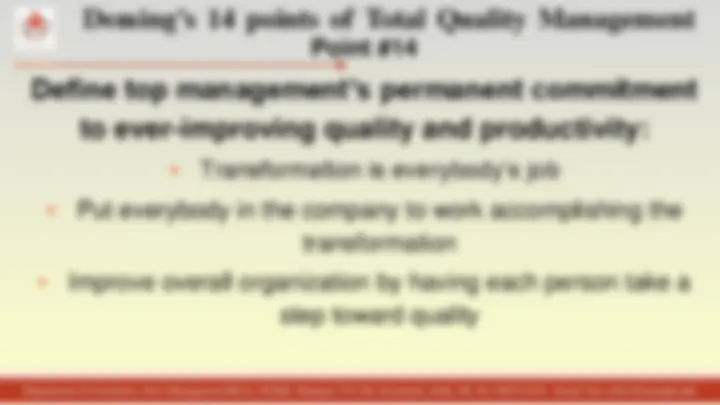
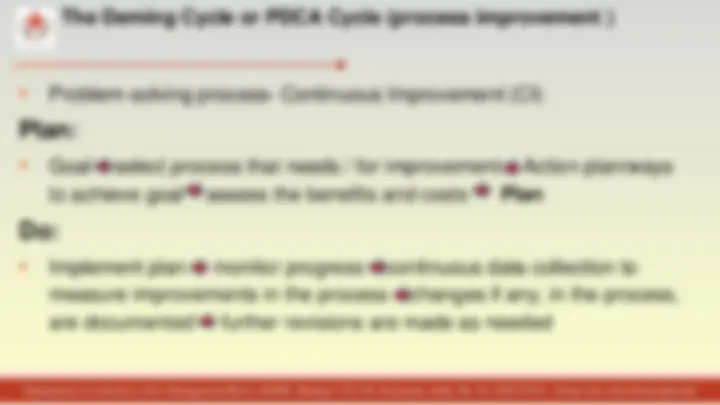
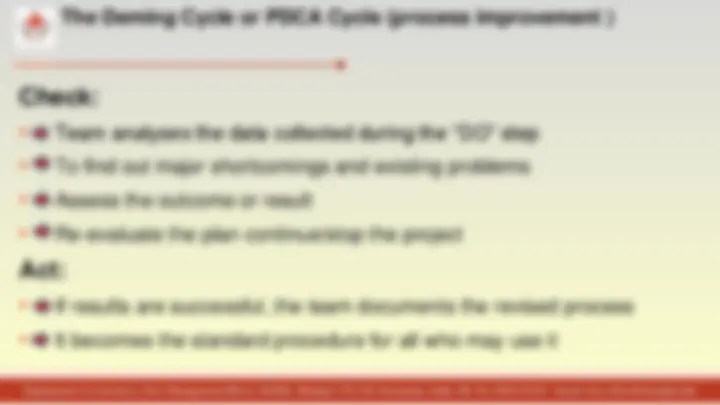
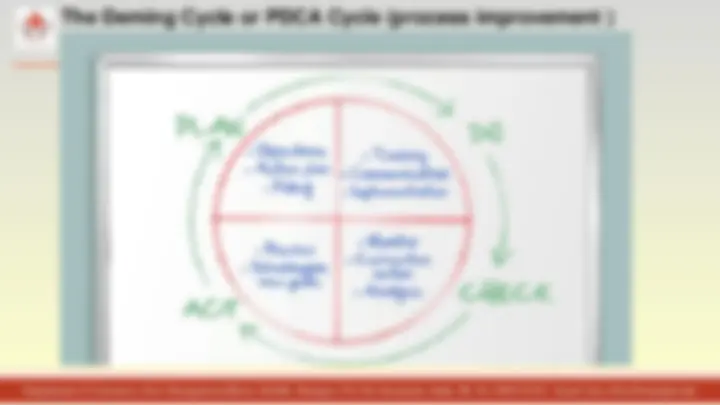
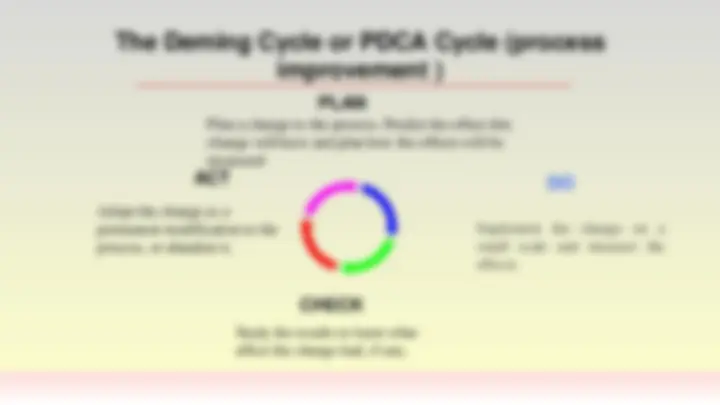
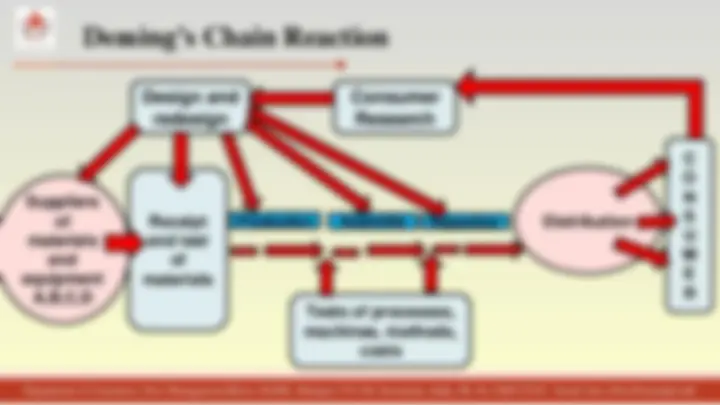
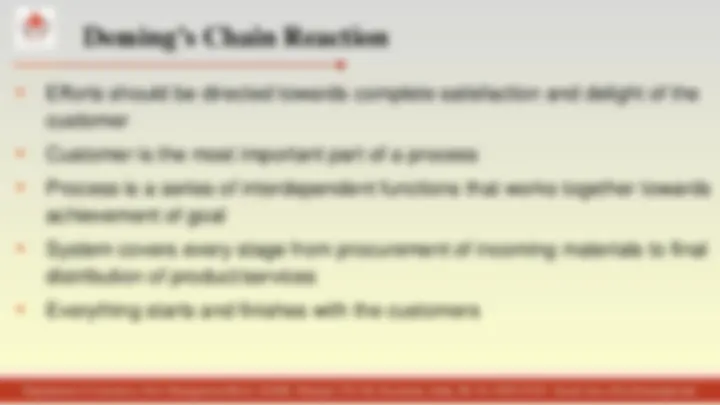
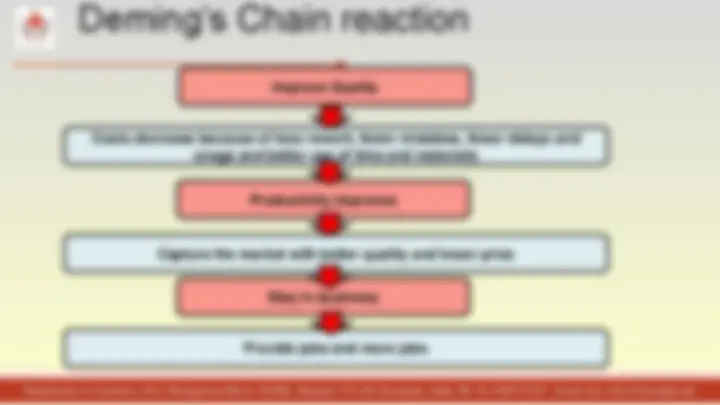
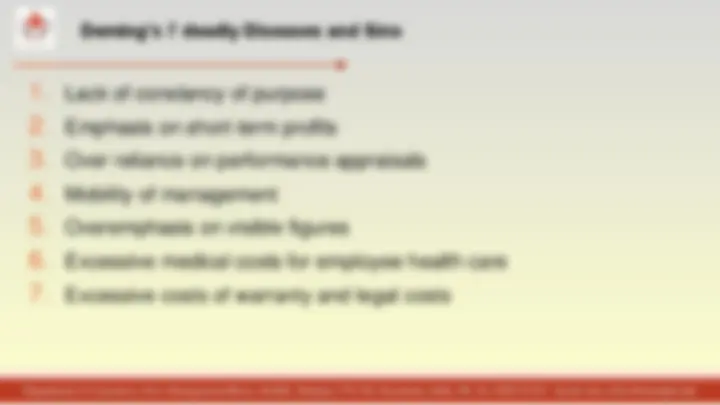

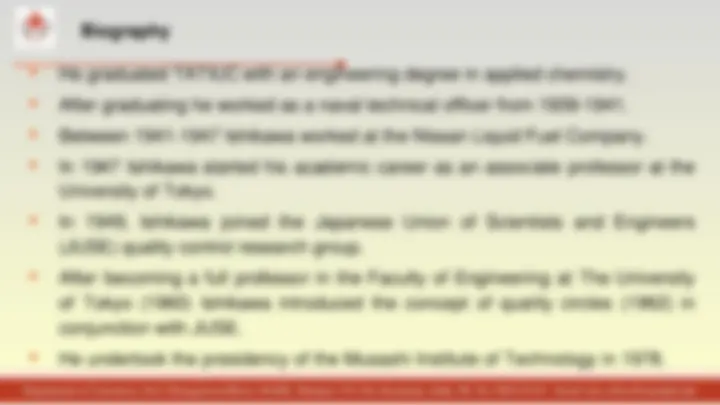
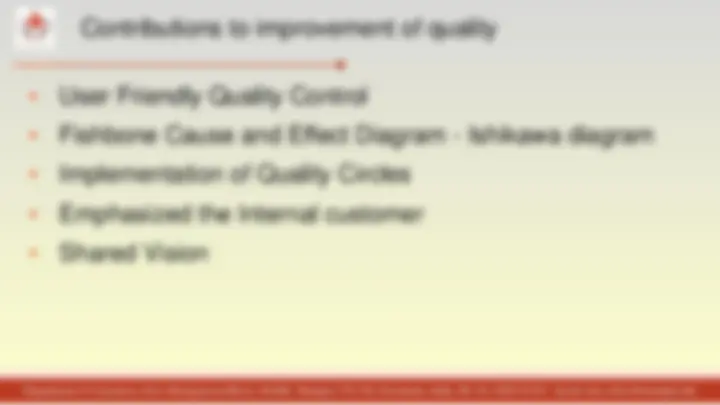
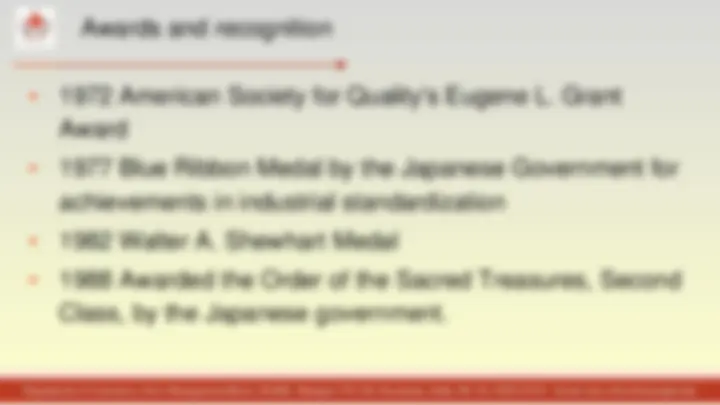
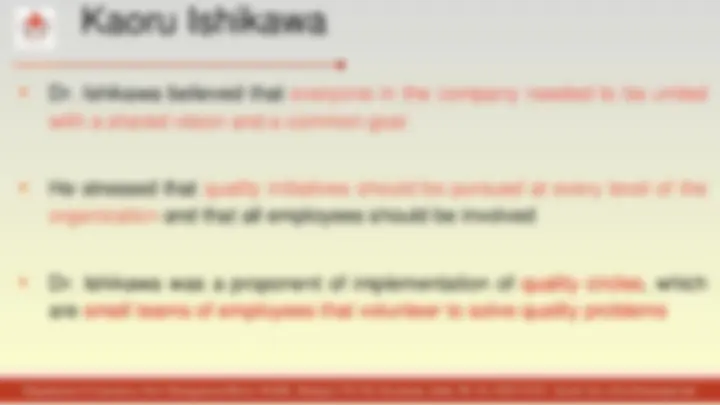
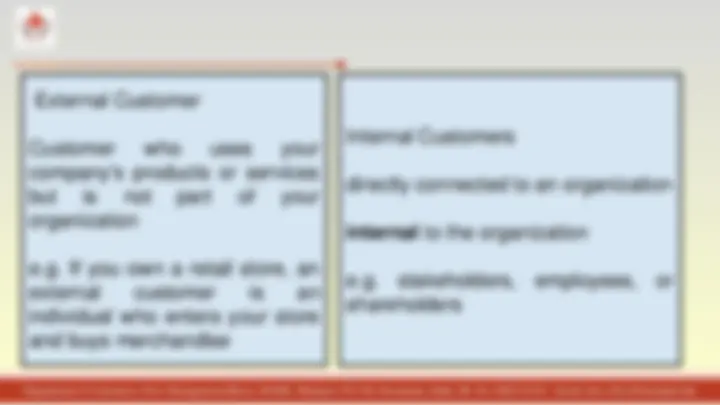
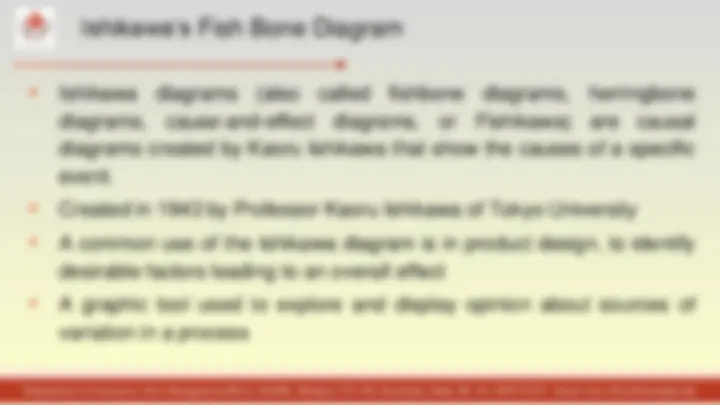
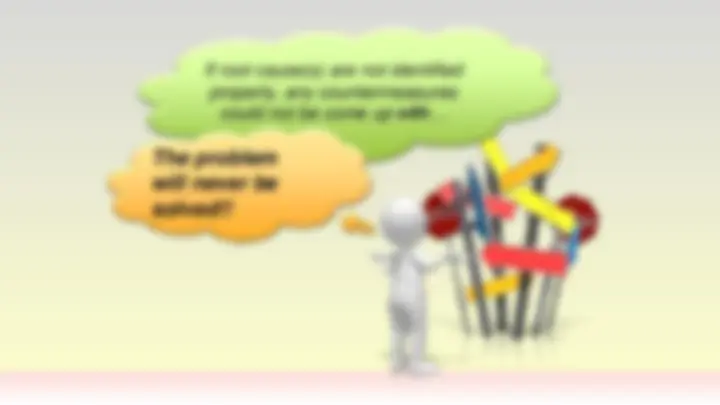
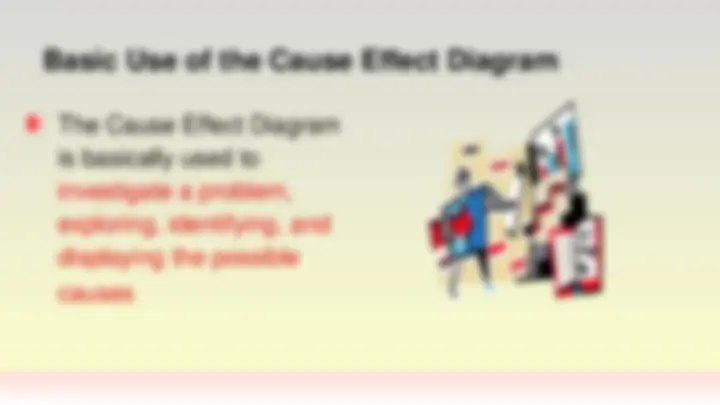
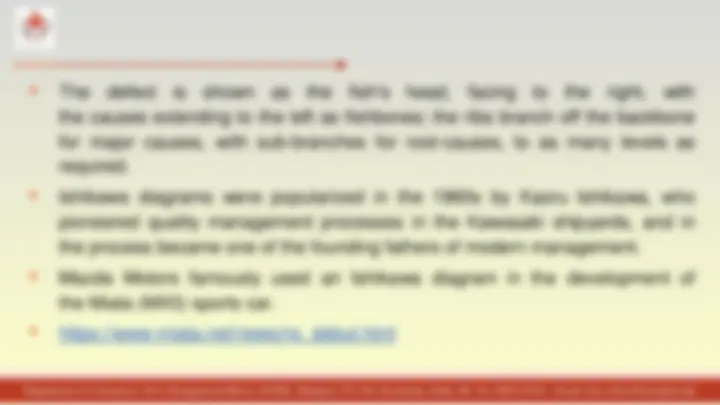
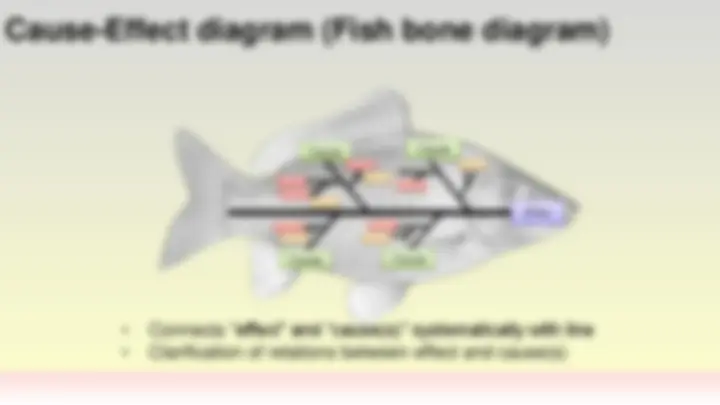
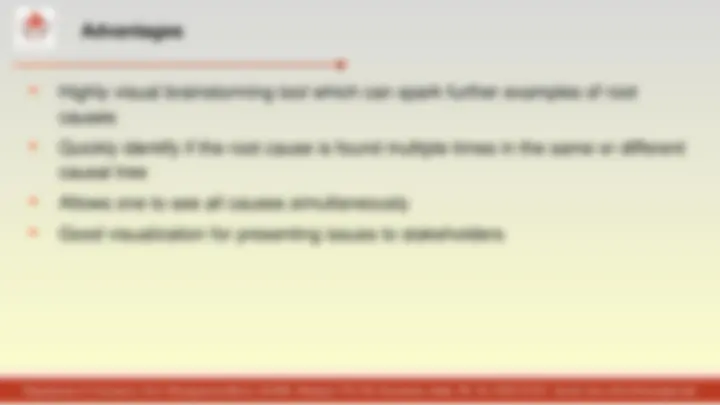
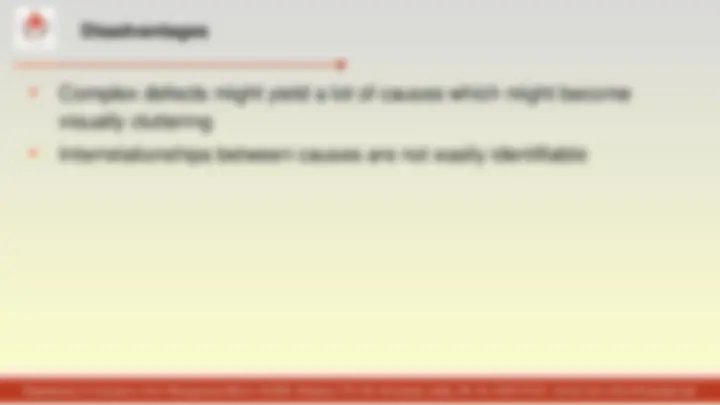
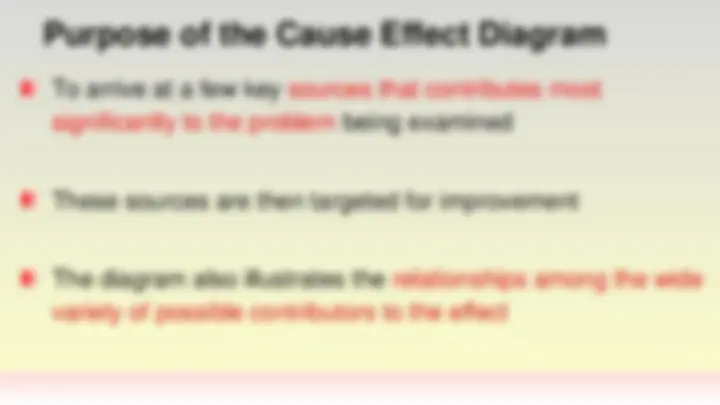
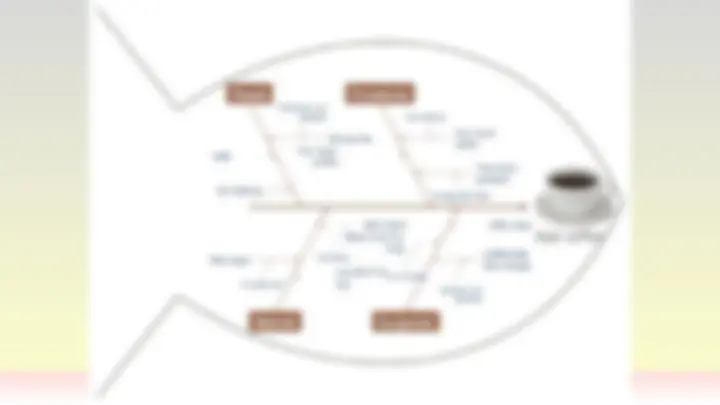
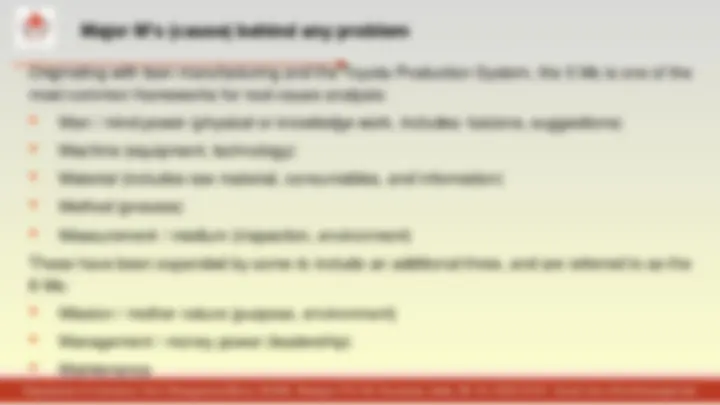

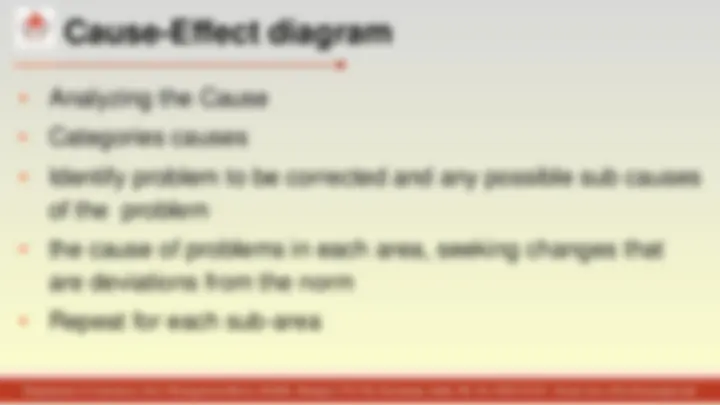
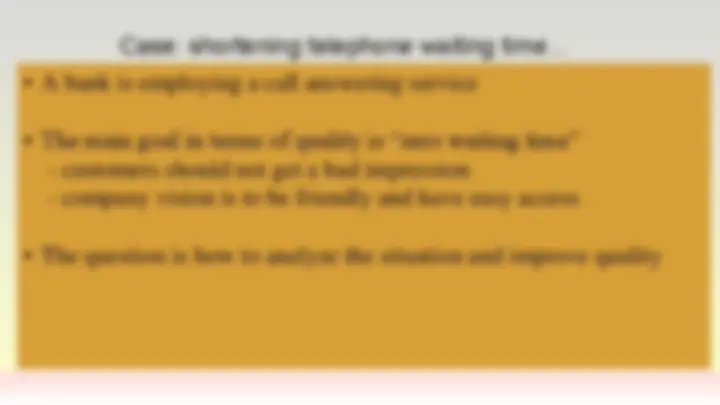
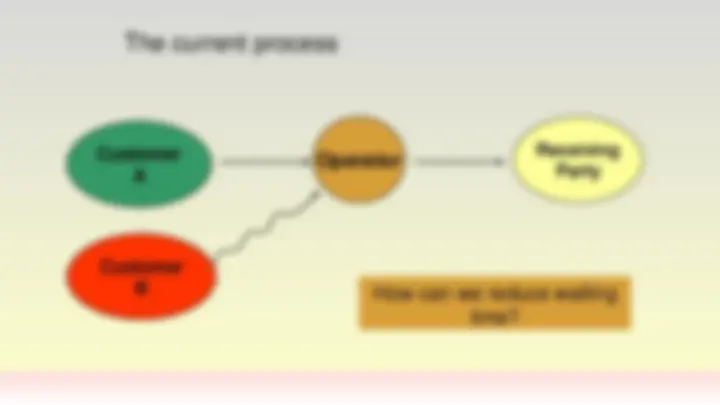
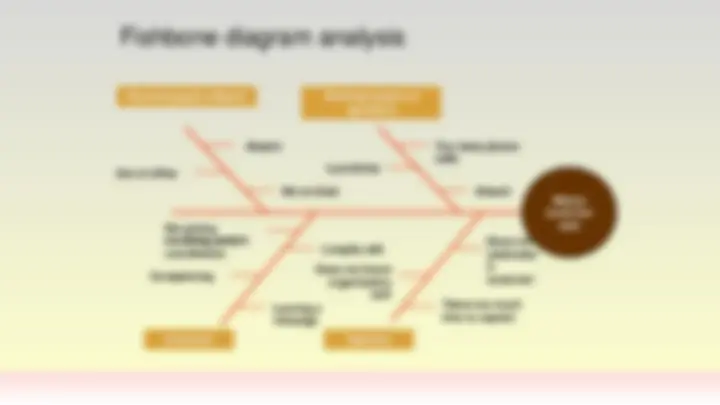
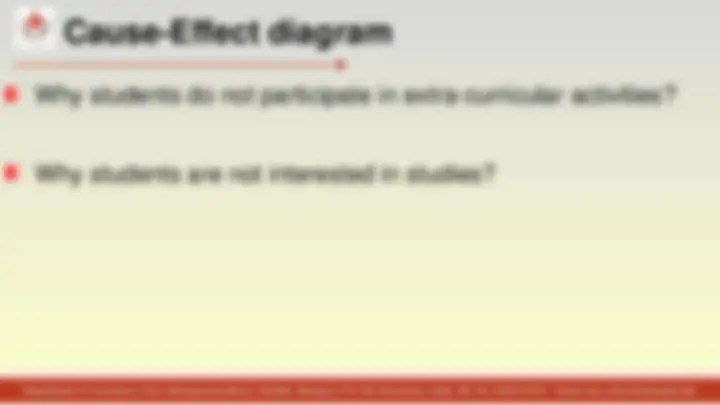
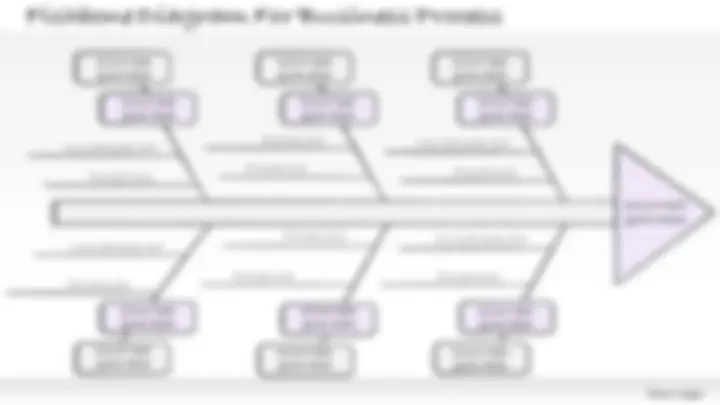
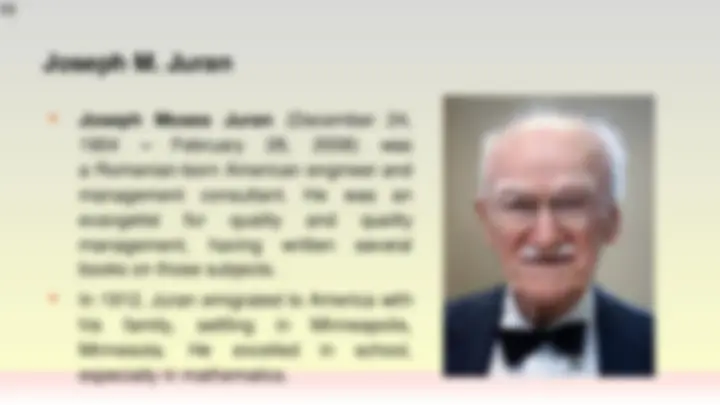
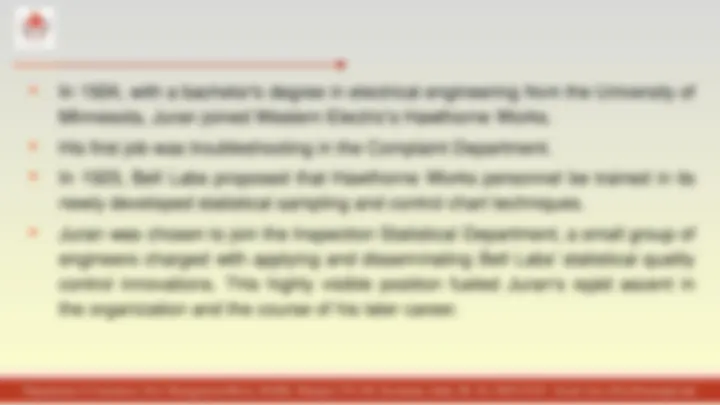
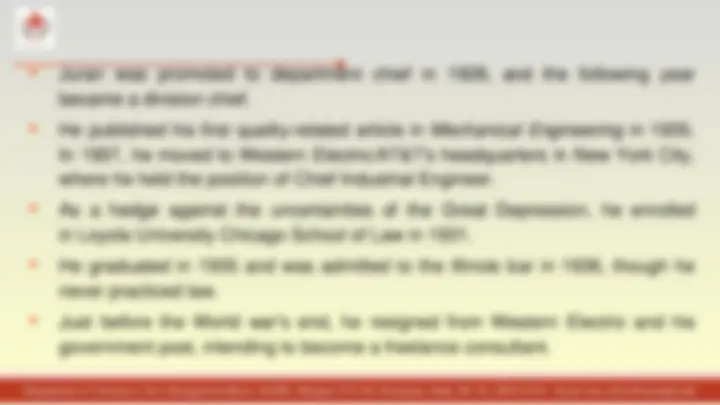
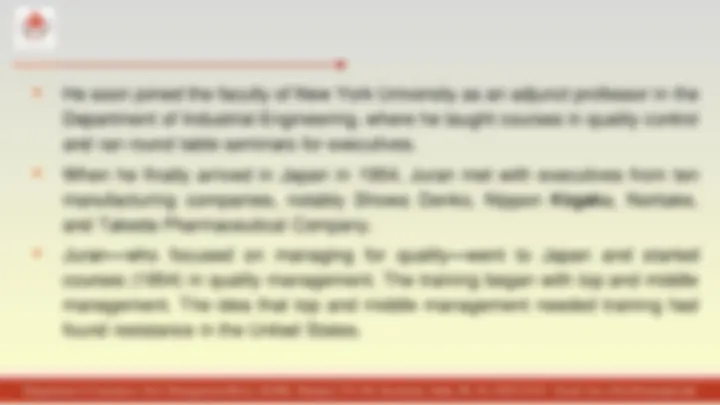
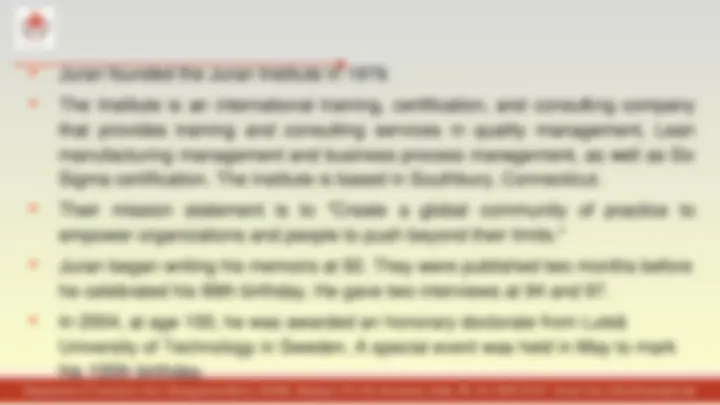
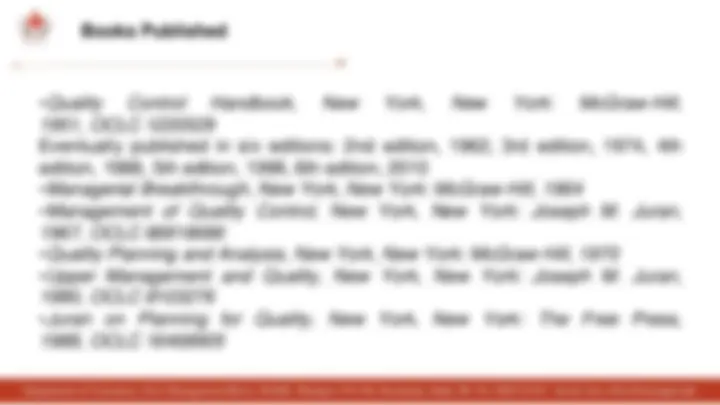
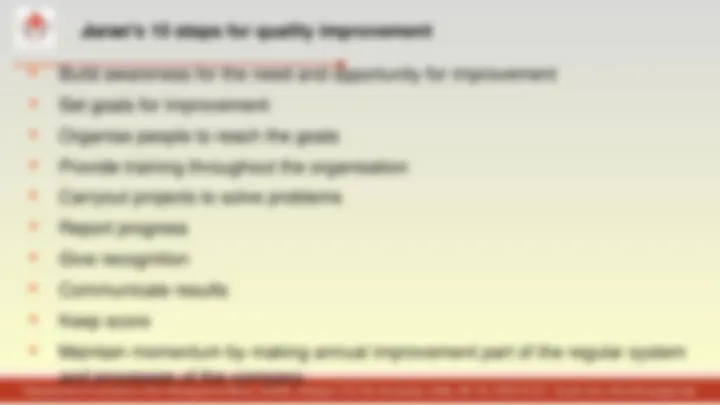
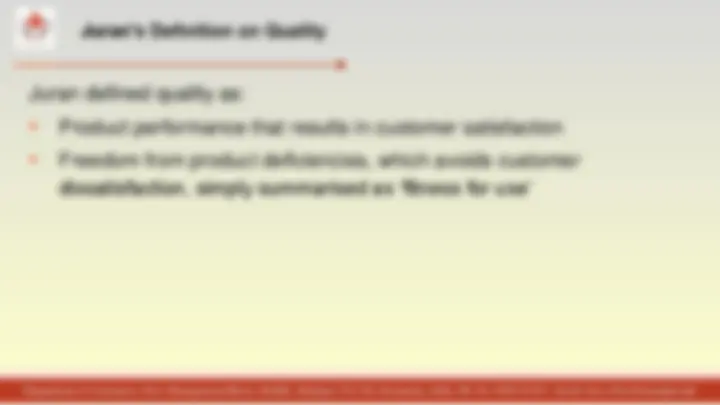
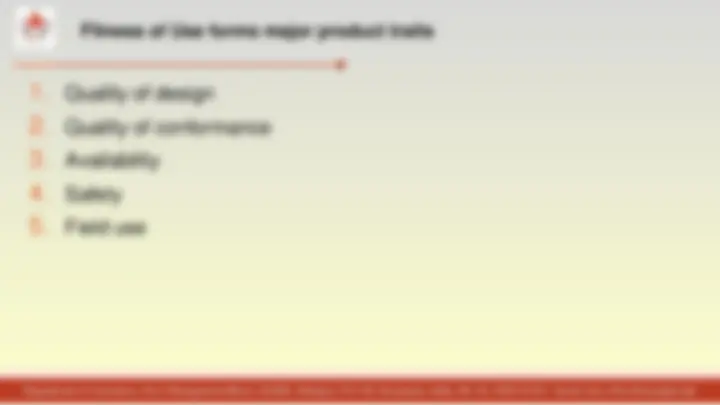
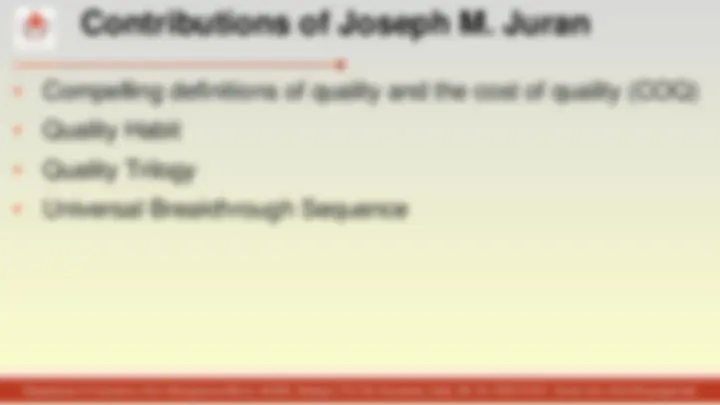
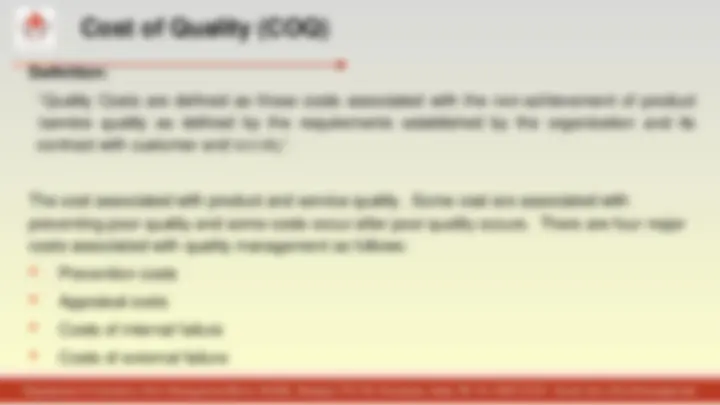
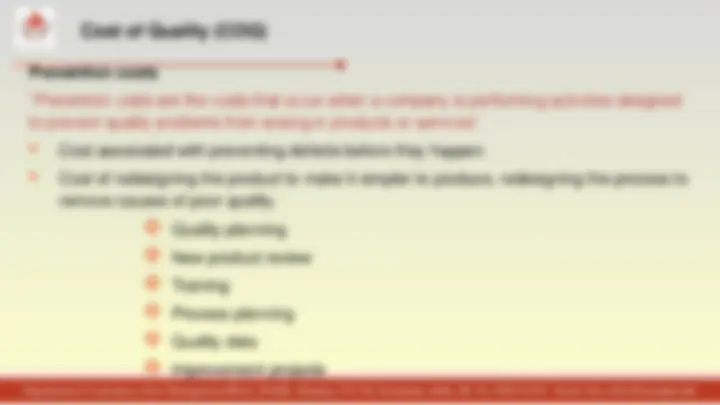
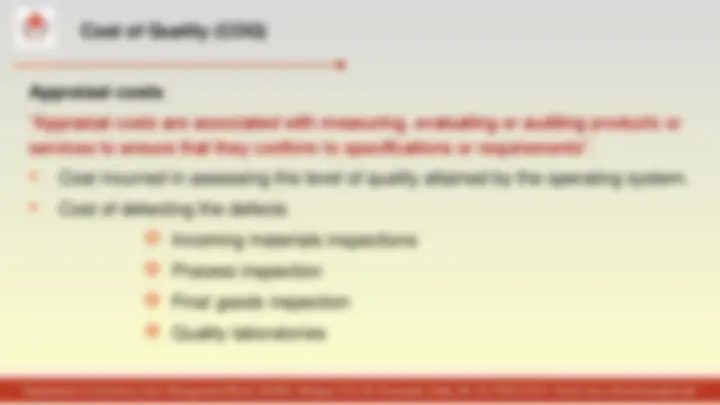
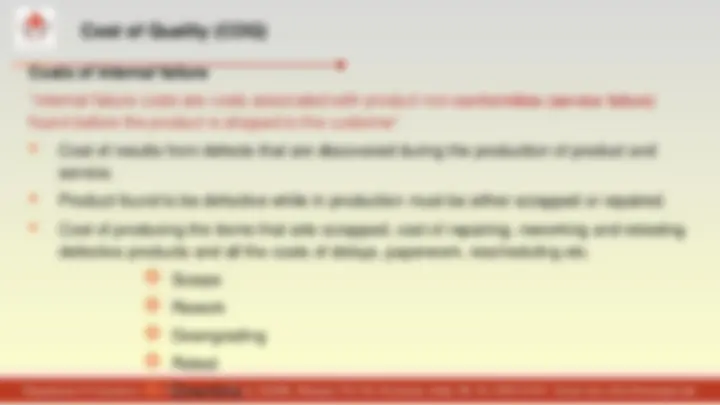
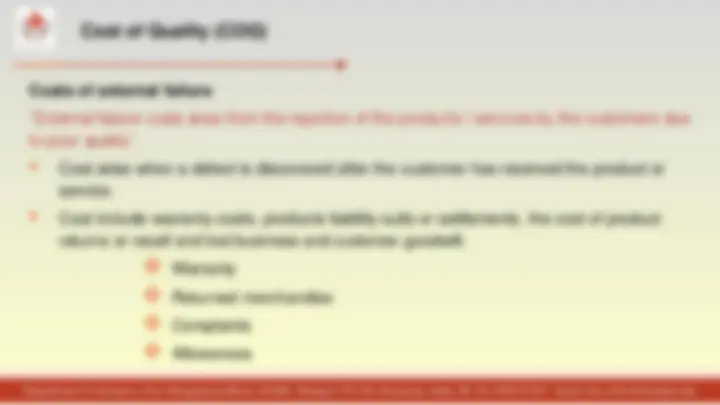
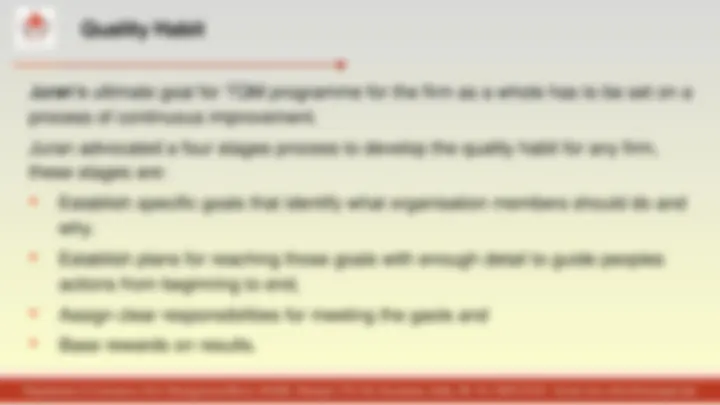
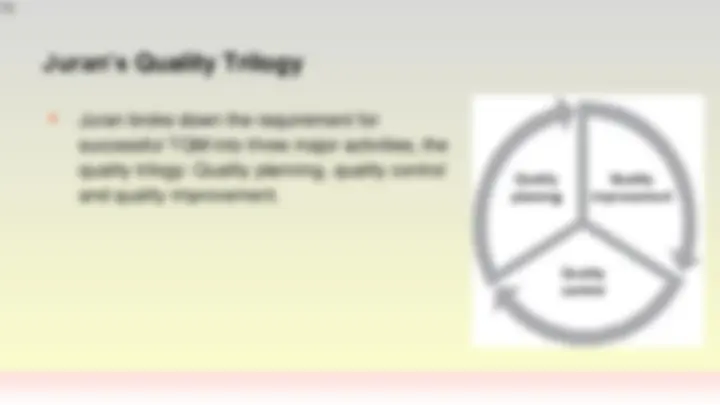
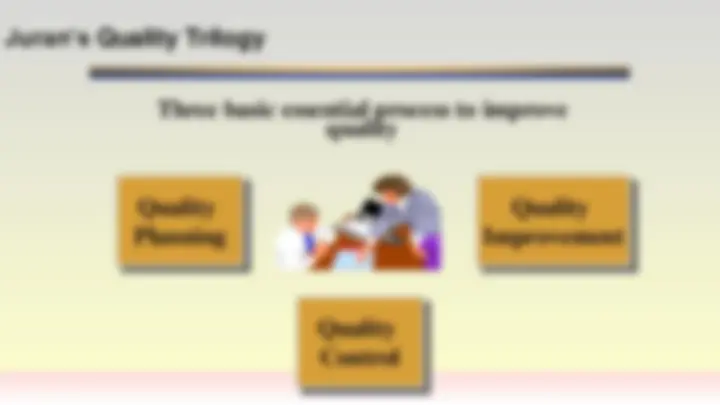
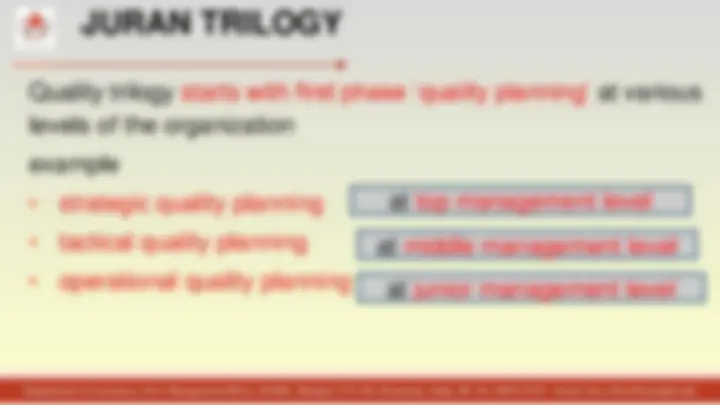
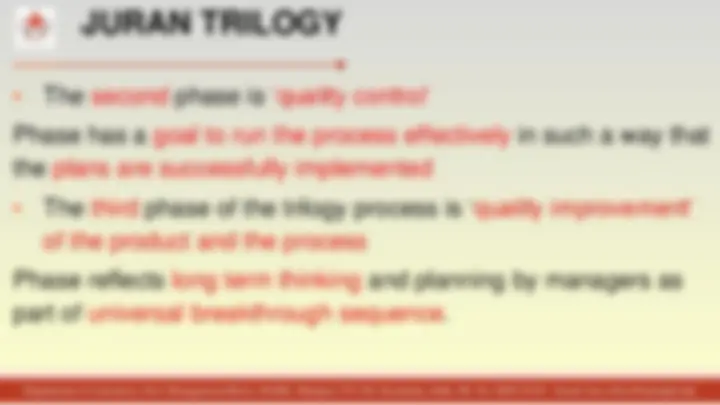
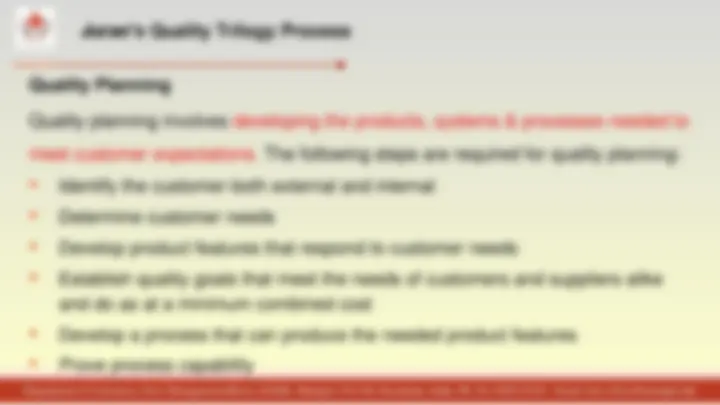
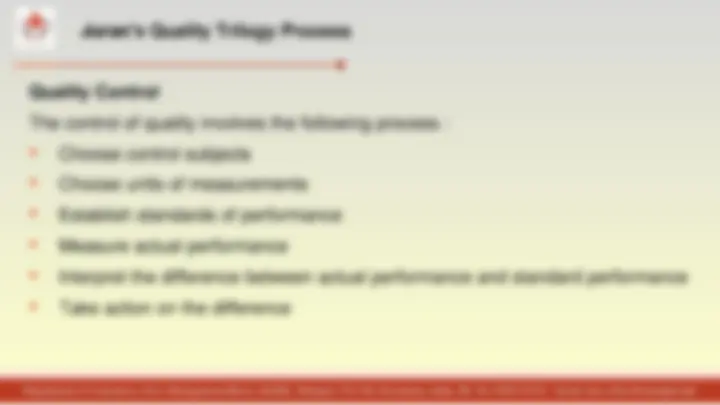
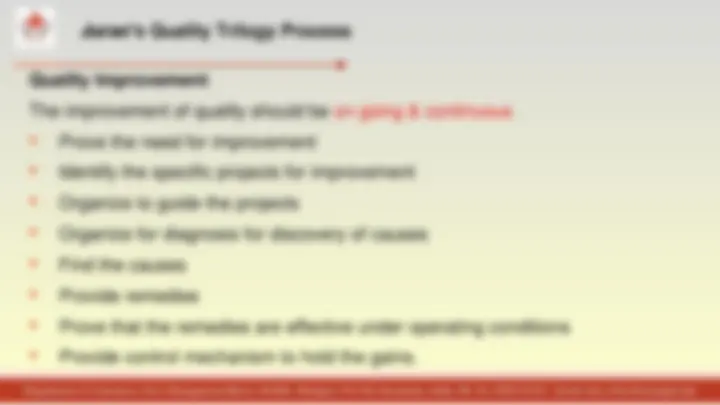
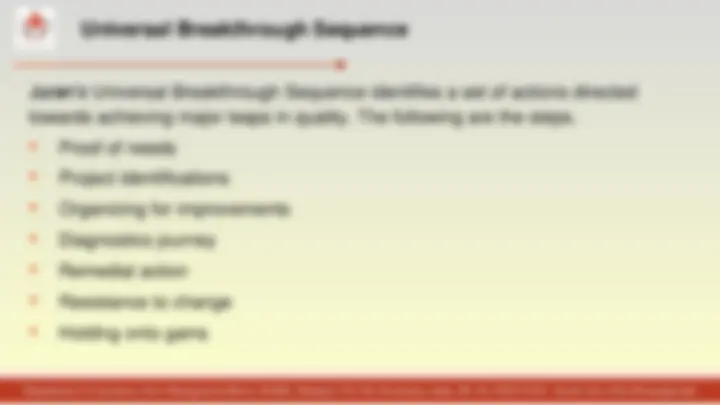
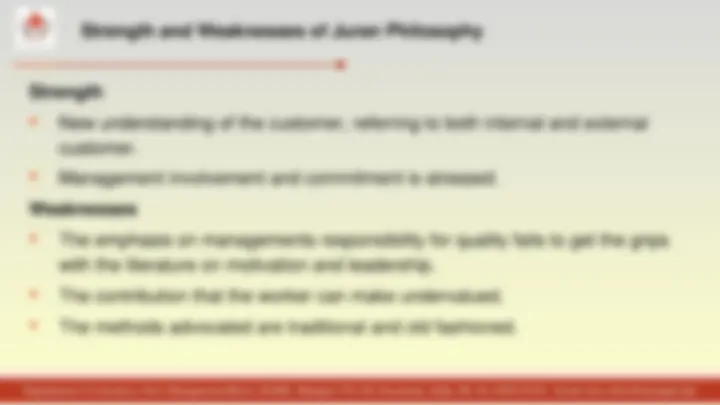
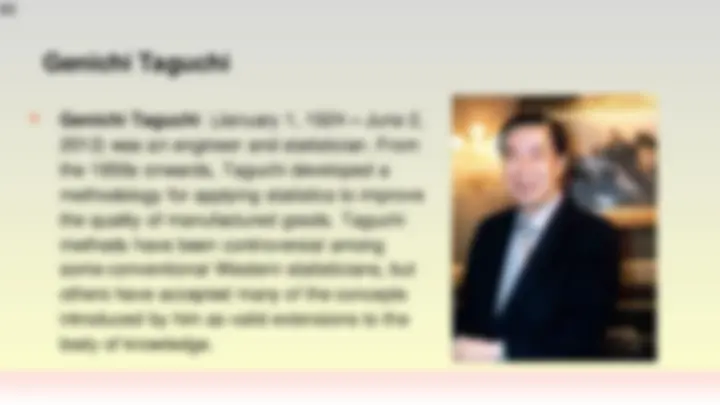
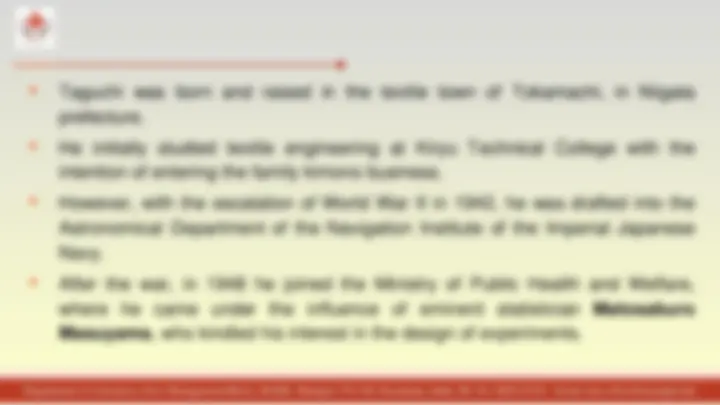
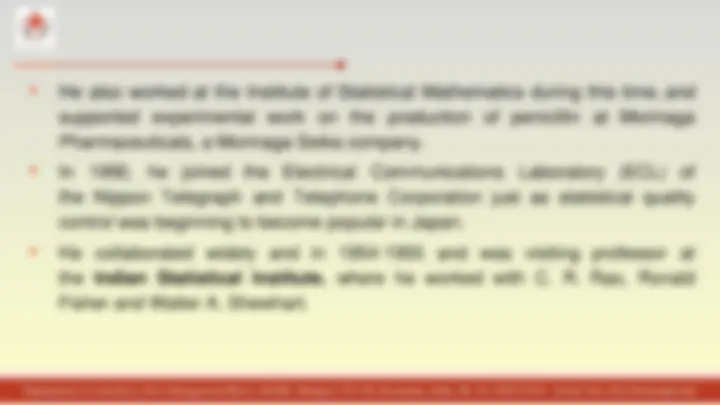
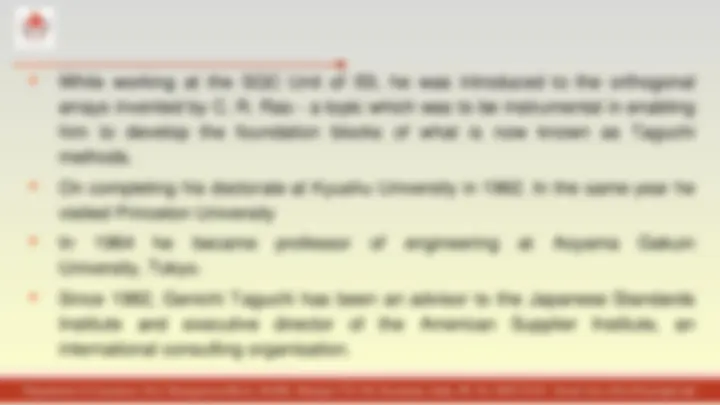
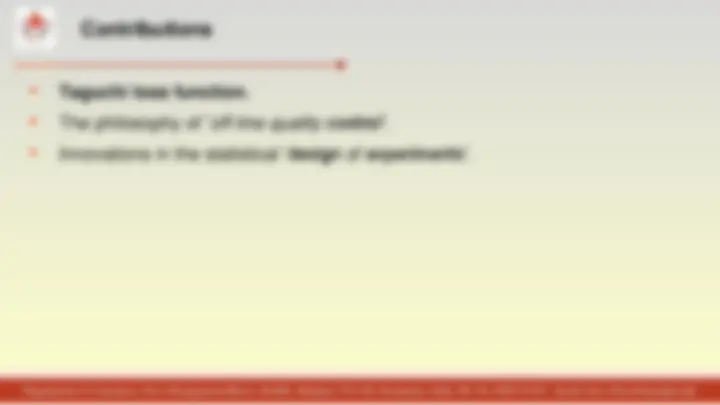
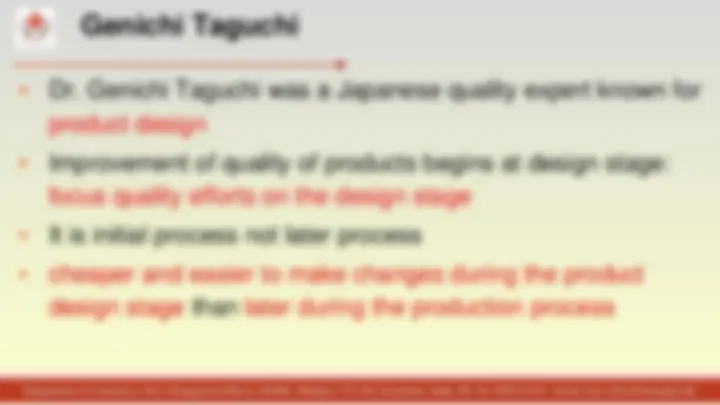
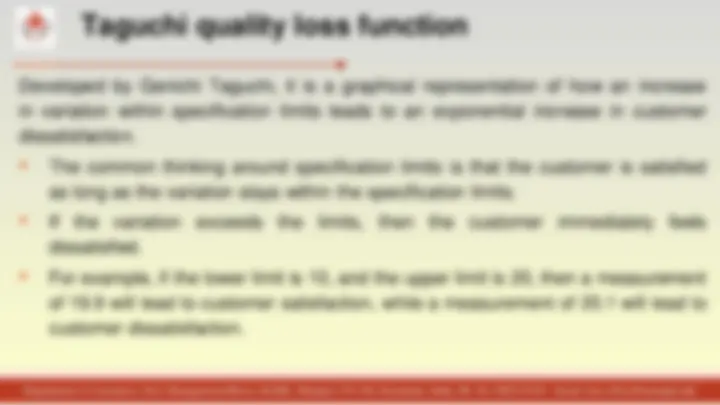
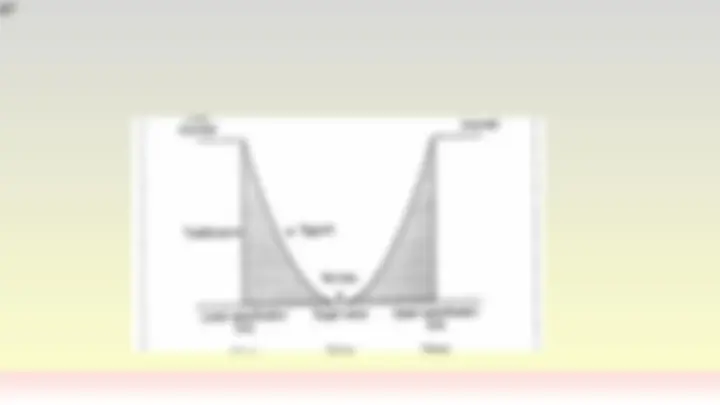
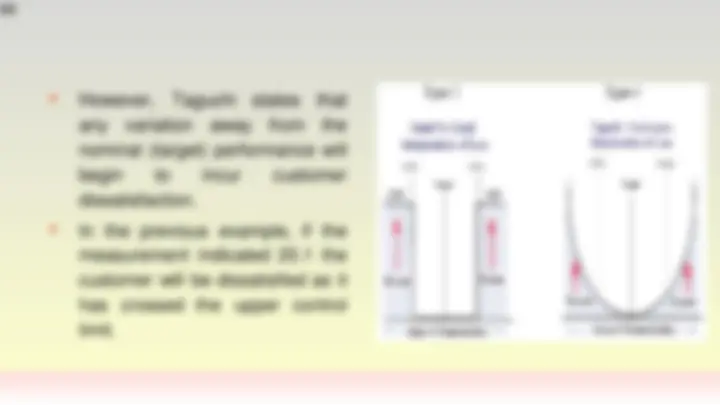
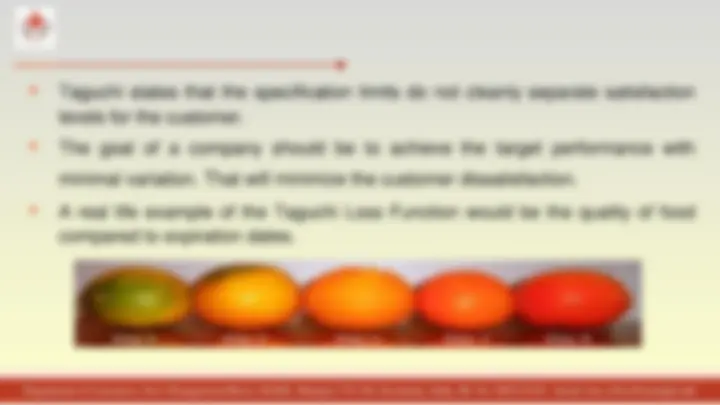
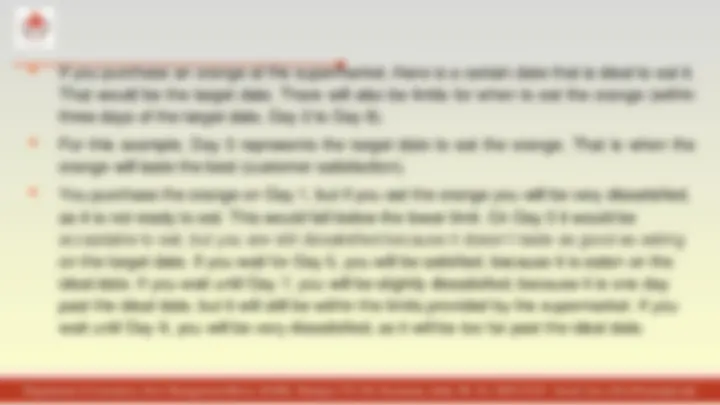
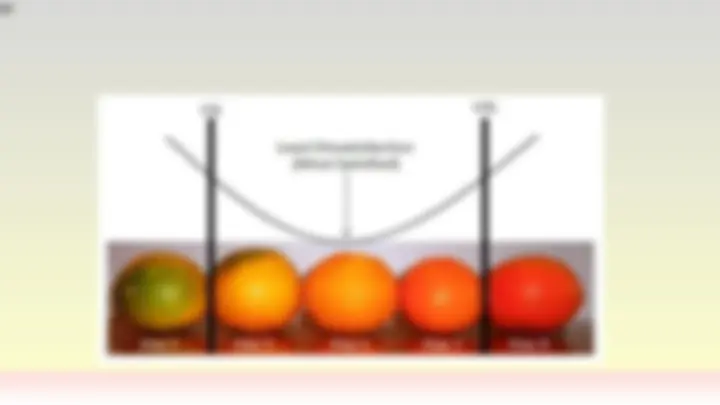
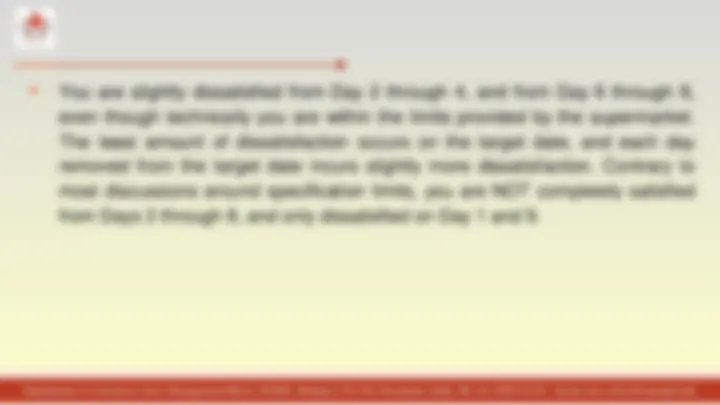
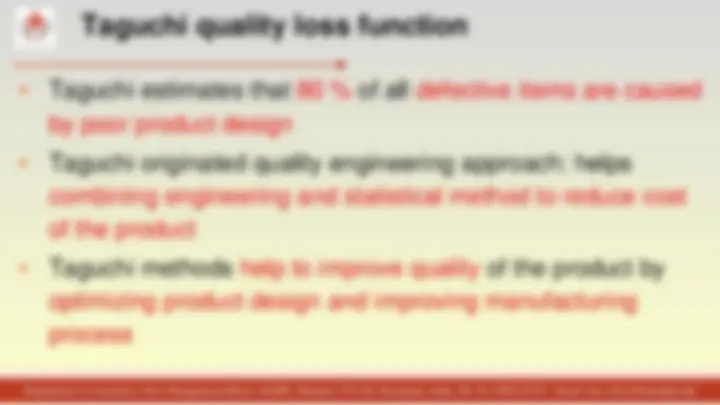
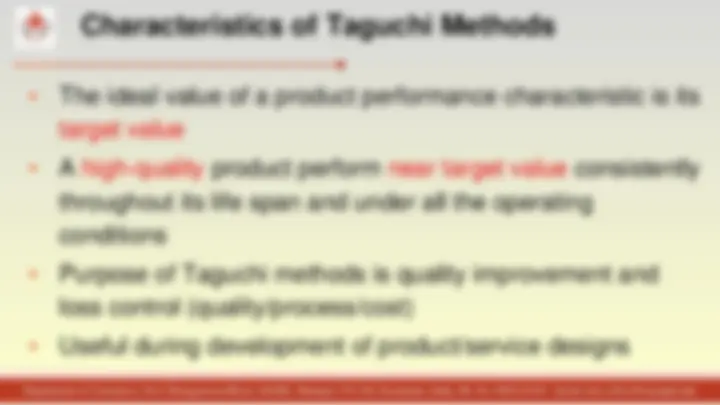
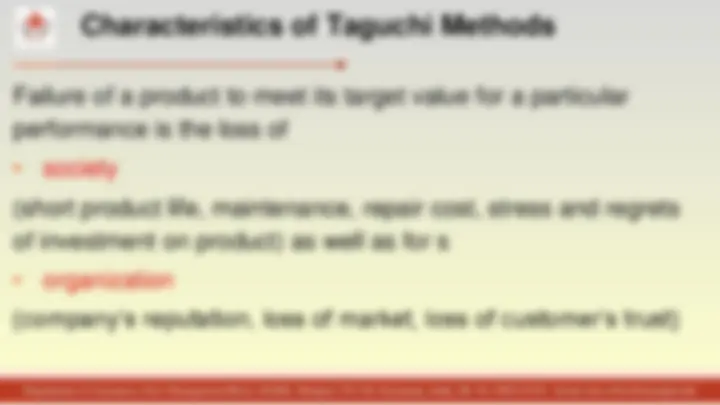
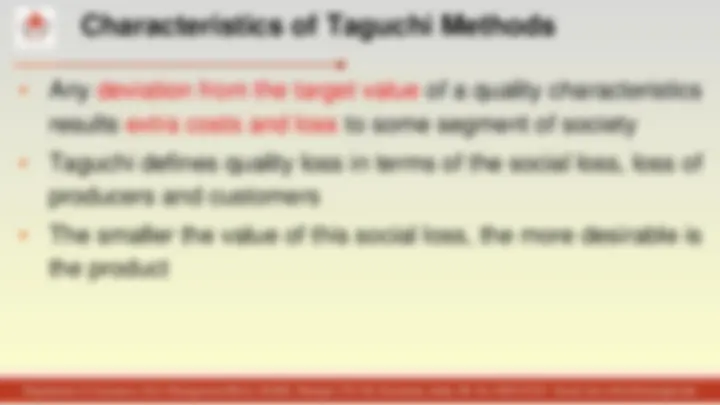
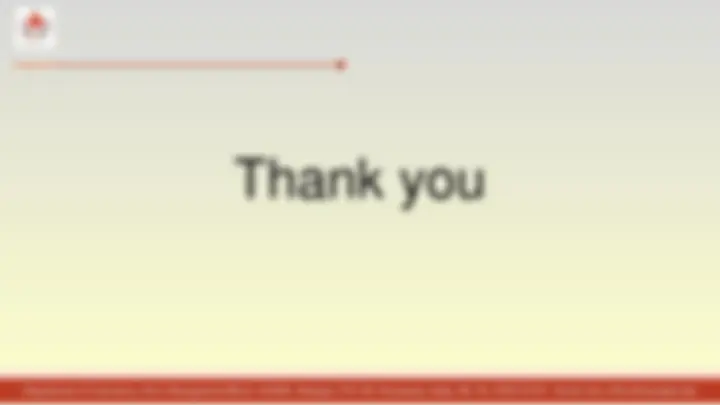
Study with the several resources on Docsity
Earn points by helping other students or get them with a premium plan
Prepare for your exams
Study with the several resources on Docsity
Earn points to download
Earn points by helping other students or get them with a premium plan
Community
Ask the community for help and clear up your study doubts
Discover the best universities in your country according to Docsity users
Free resources
Download our free guides on studying techniques, anxiety management strategies, and thesis advice from Docsity tutors
Running class notes in the form of pdf
Typology: Lecture notes
1 / 97
This page cannot be seen from the preview
Don't miss anything!
▪ Deming’s Contribution to quality ▪ Deming’s 14 points of quality Management ▪ Deming’s chain reaction ▪ Ishikawas fish bone diagram ▪ Taguchi’s loss function ▪ Jurans contribution ▪ Jurans quality trilogy ▪ Future of TQM
▪ “A Guru is a guide who is considered to have attained complete insight.” ▪ “A guru is a good person, a wise person and teacher. ▪ A quality guru should be all of these, plus have a concept and approach to quality within business that has made a major and lasting impact.”
▪ W Edwards Deming ▪ Joseph Juran ▪ Philip Crosby ▪ Shigeo Shingo ▪ Kaoru Ishikawa ▪ Yoshio Kondo ▪ Taguchi
Point #
▪ Plan for quality in the long term direction (values, mission, vision) ▪ Don’t just do the same things better-find better things to do. ▪ Invest in innovation, training and research
Point #
▪ Embrace quality throughout the organization ▪ Create your quality vision, and implement it
Point # End the practice of awarding business on price alone; instead, minimize total cost by working with a single supplier: ▪ Look at suppliers as your partners in quality. ▪ Encourage them to spend time improving their own quality (decrease expenses for inspection, scrap and rework, inventory to replace defective items and employee frustration).
Point #
▪ Improve both design (customers needs, Market survey, feedbacks) and production (reduce causes of variation) ▪ Constant improvement of quality and productivity decrease costs
Point #
▪ Don’t simply supervise - provide support and resources so that each staff member can do his or her best. ▪ Be a coach, provide guidance instead of just overseeing them
Point # Drive out fear: ▪ Fear: Obstacle to improve efficiency and effectiveness (failure, unknown, weakness, losing control, change) ▪ Create an environment that encourages people to ask questions, report problems, can share their ideas and try new ideas ▪ Allow people to perform at their best by ensuring that they’re not afraid to express ideas or concerns. ▪ Make workers feel valued, and encourage them to look for better ways to do things.
Point # Eliminate the use of slogans, posters, exhortations and targets for the workforce: ▪ Let people know exactly what you want - don’t make them guess. ▪ Motivational methods overlooks the sources of many problem. ▪ Quality problems comes from limits in current system ▪ Urge workers to work harder, train them, provide required resources
Point #
▪ Look at how the process is carried out, not just numerical targets ▪ Measure the process rather than the people behind the process