
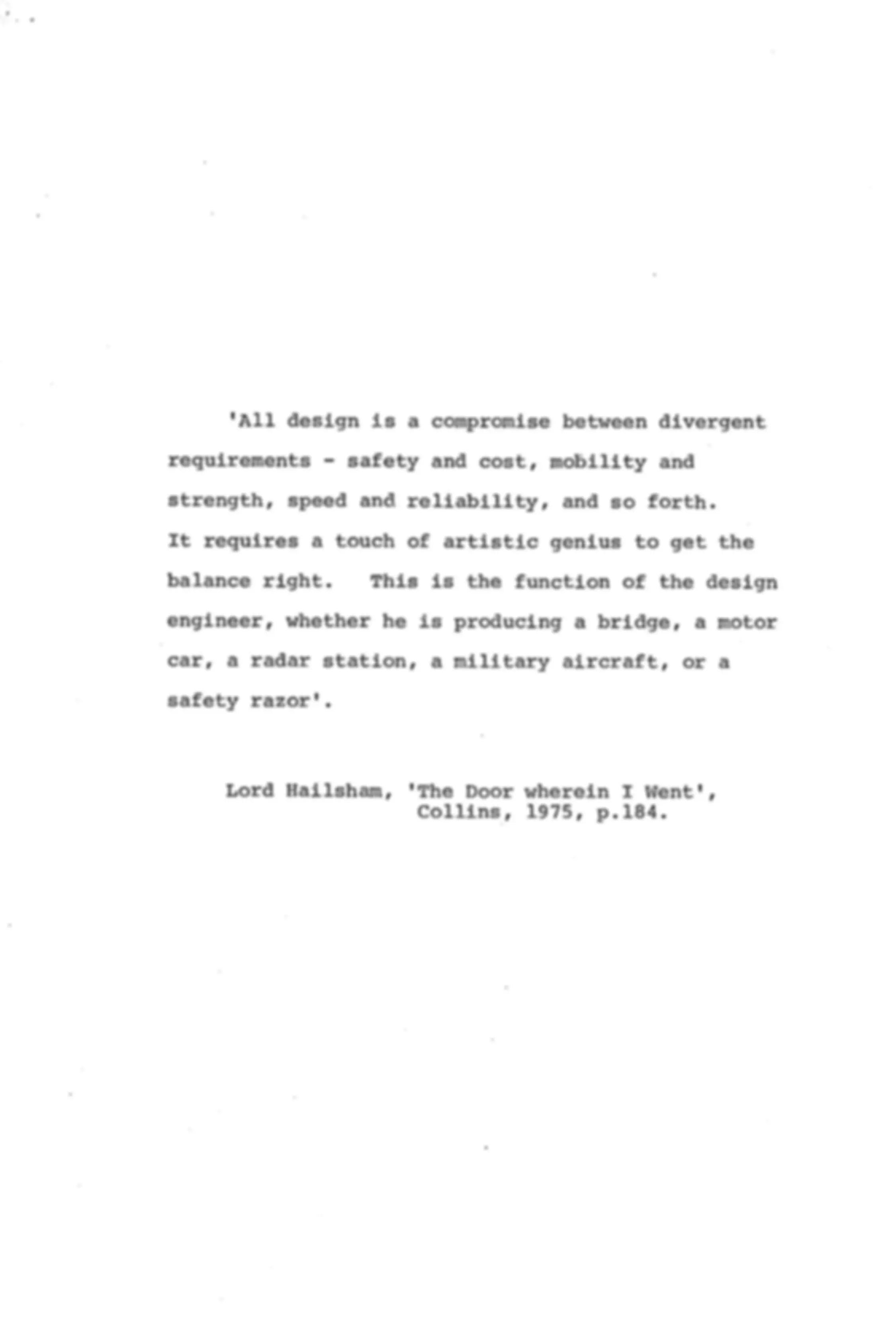
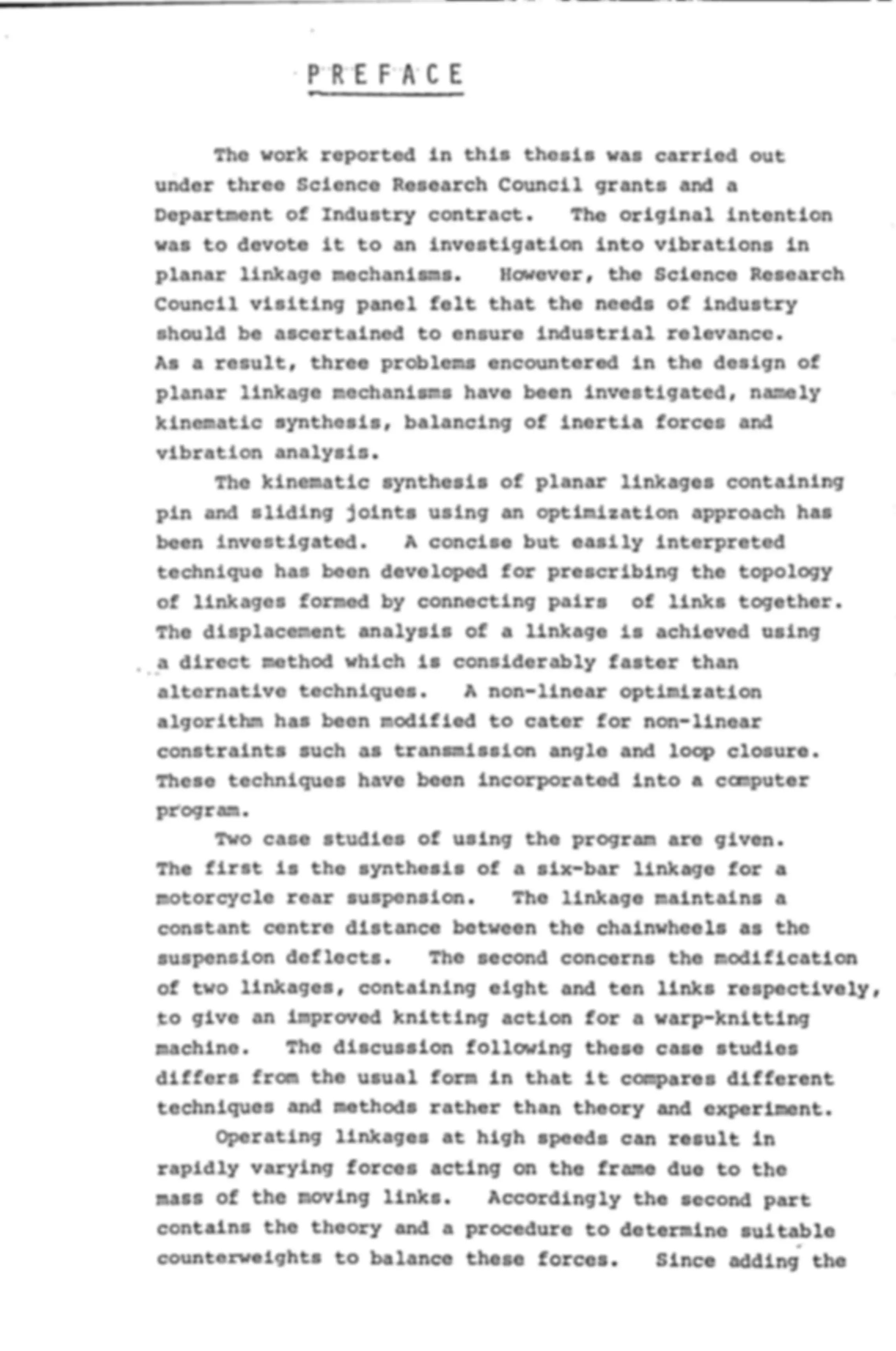
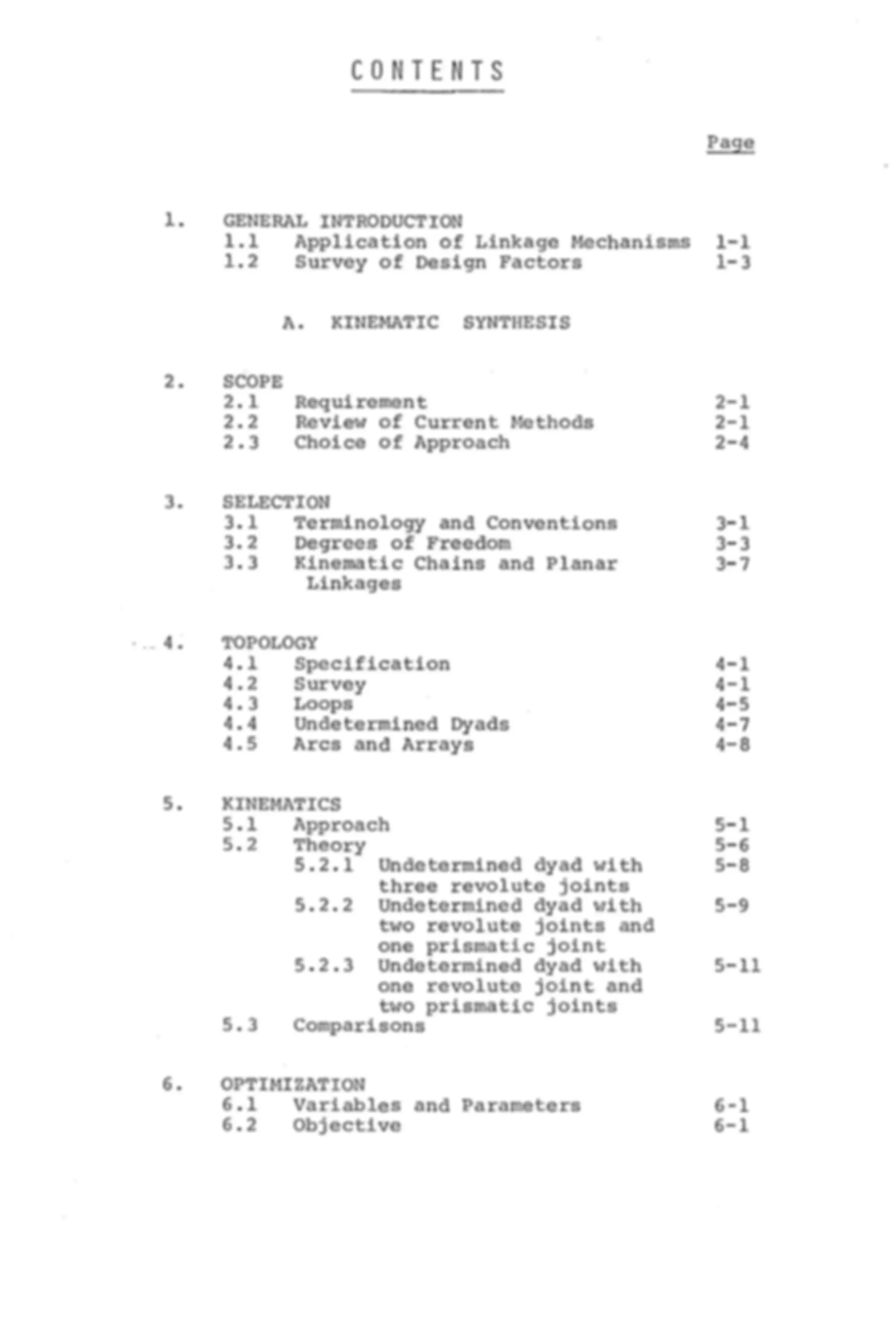
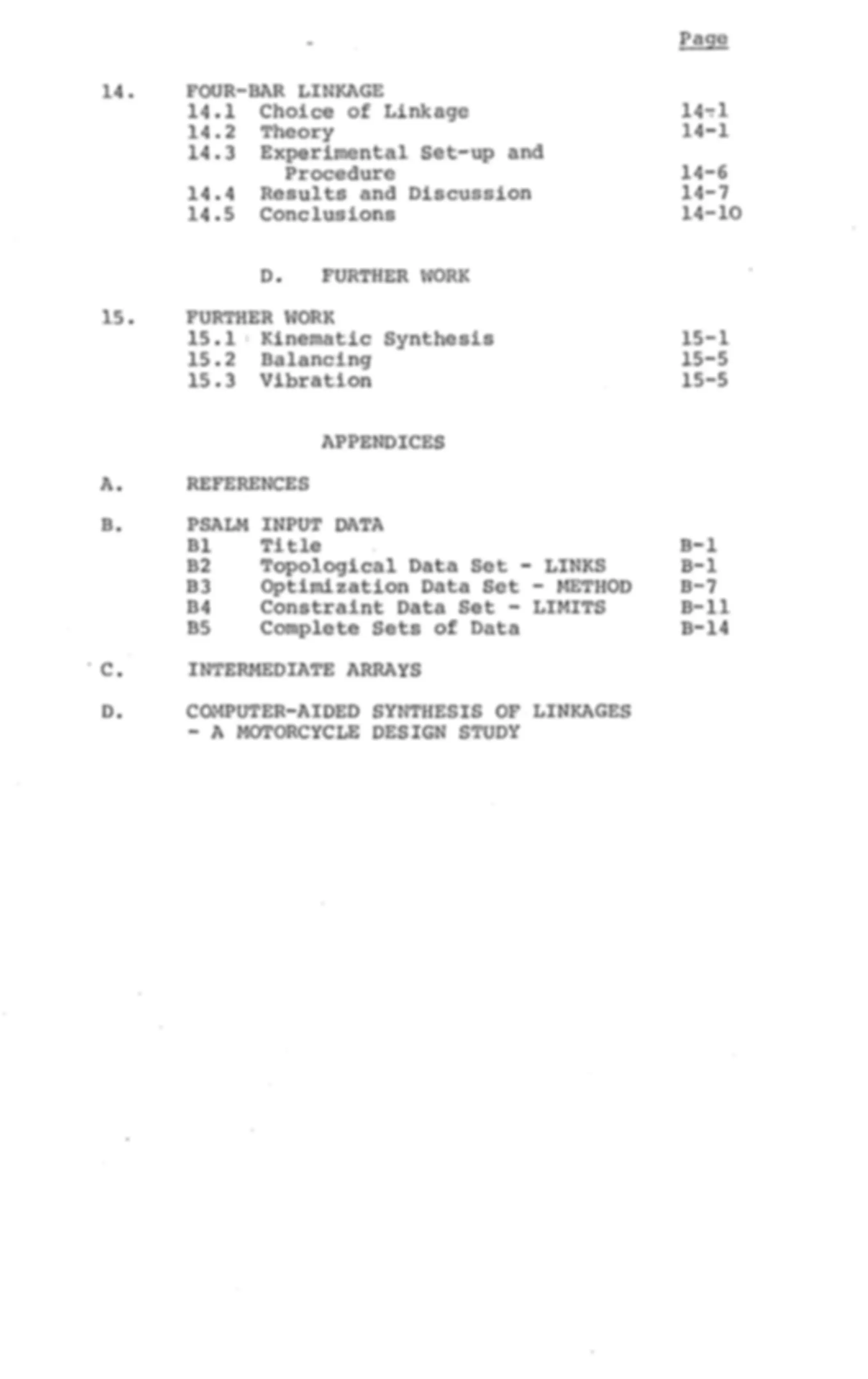
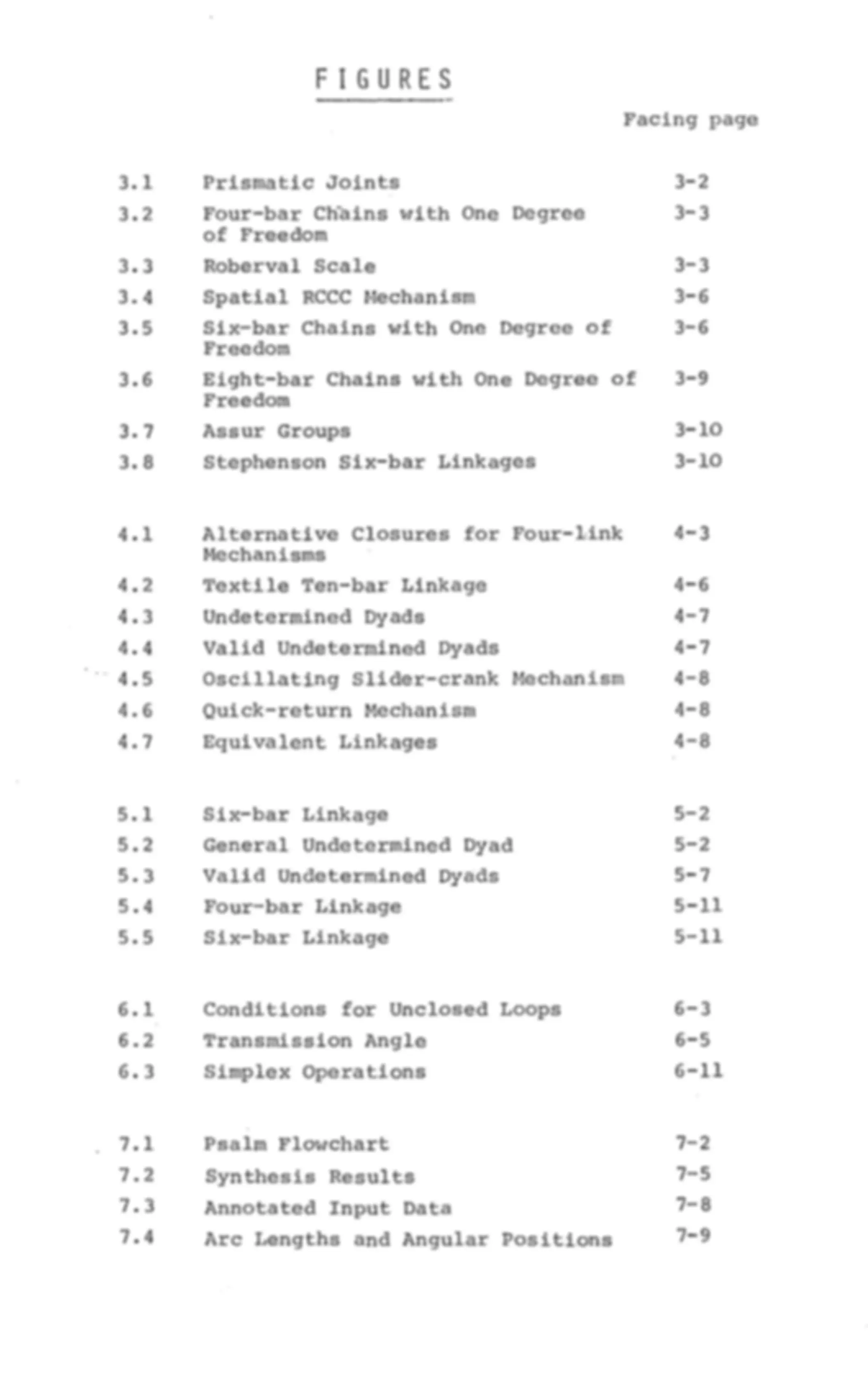
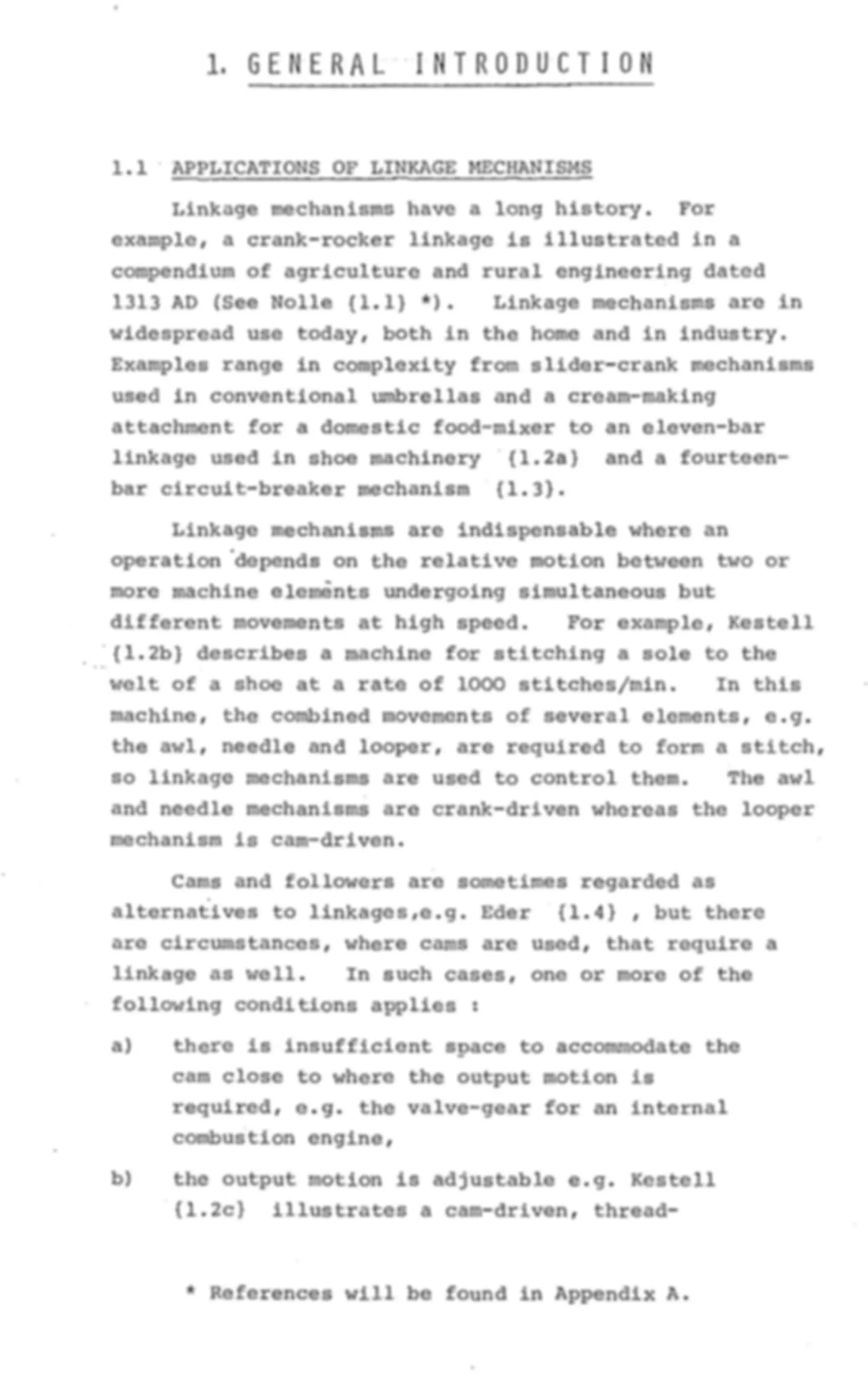
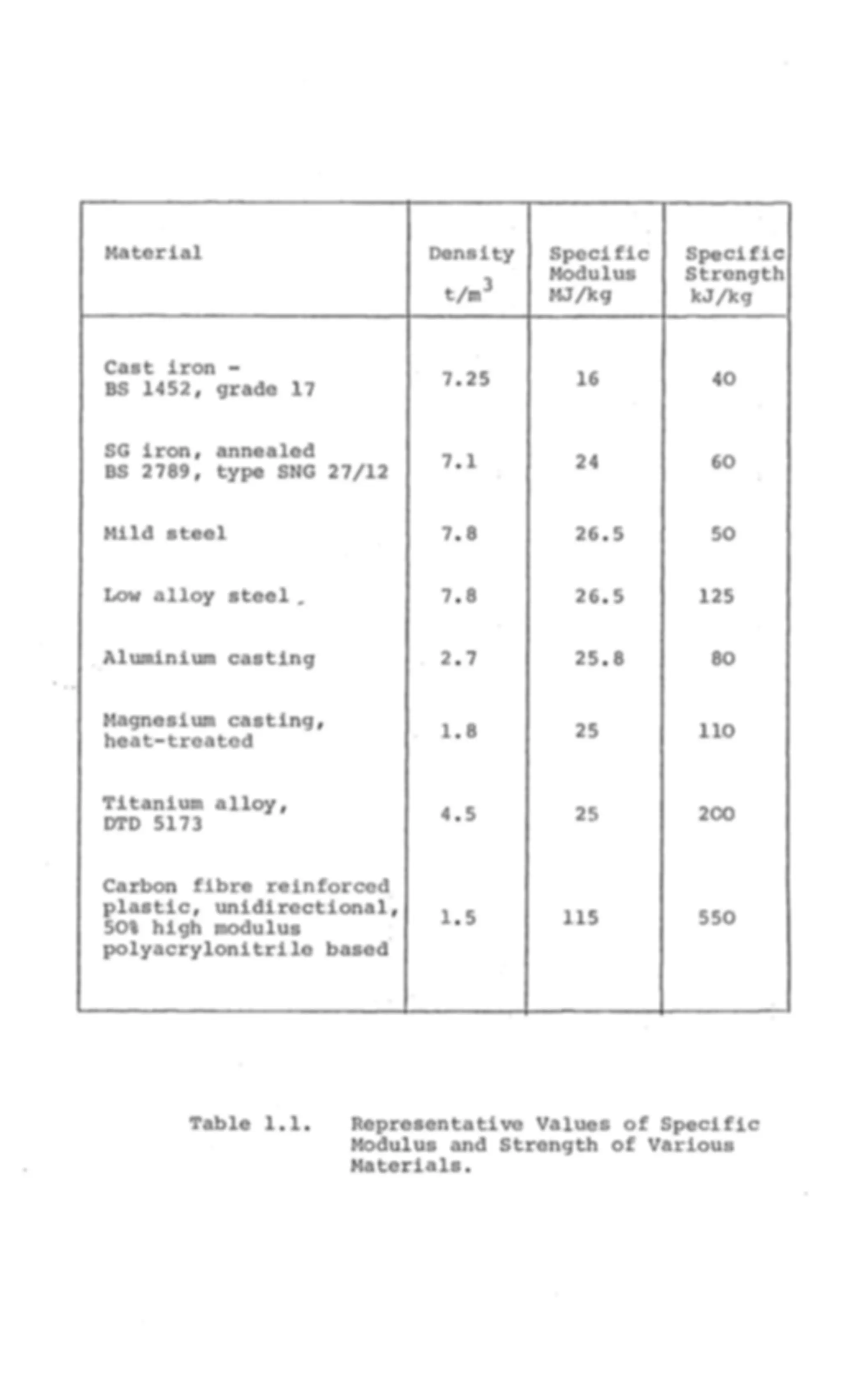
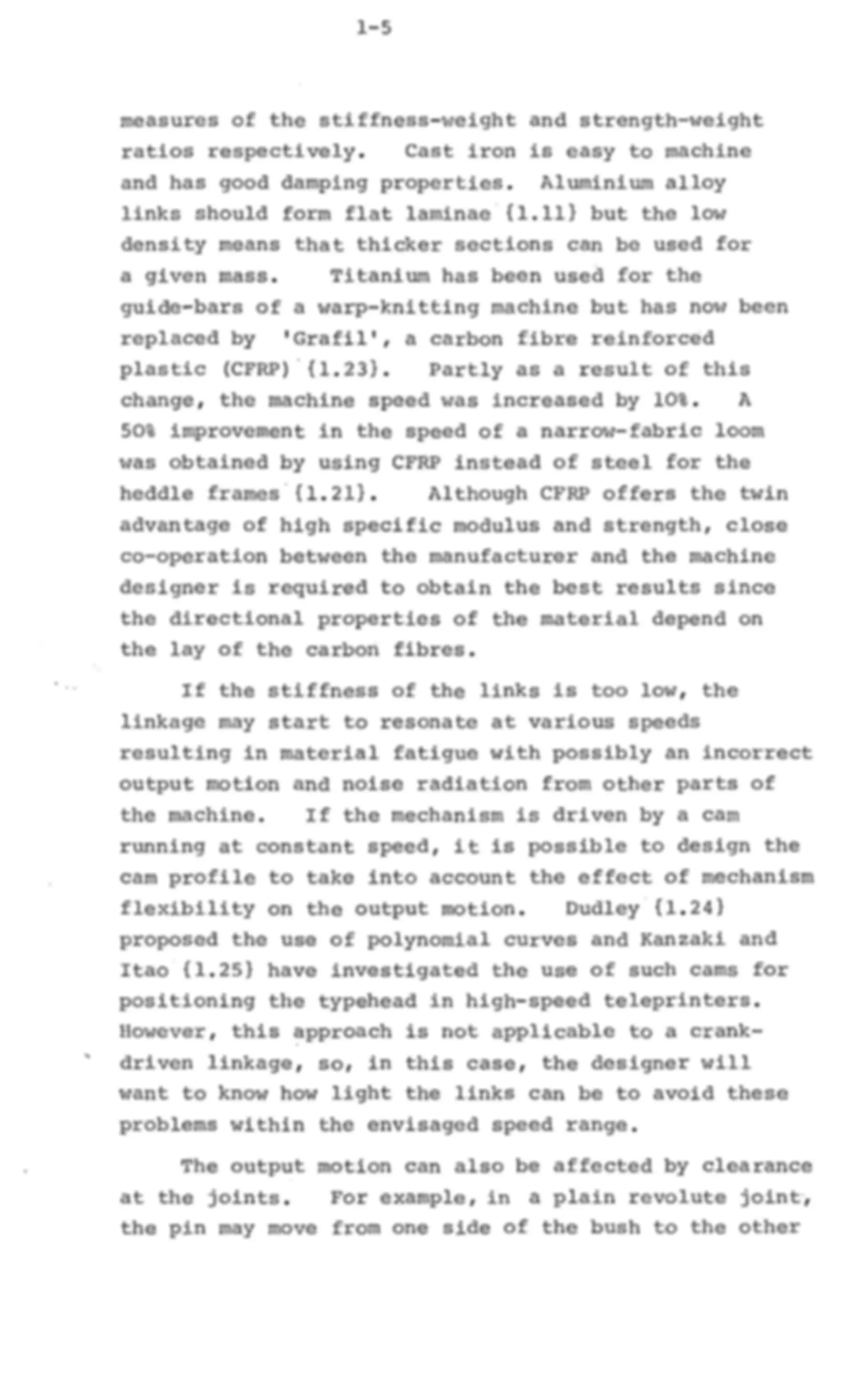
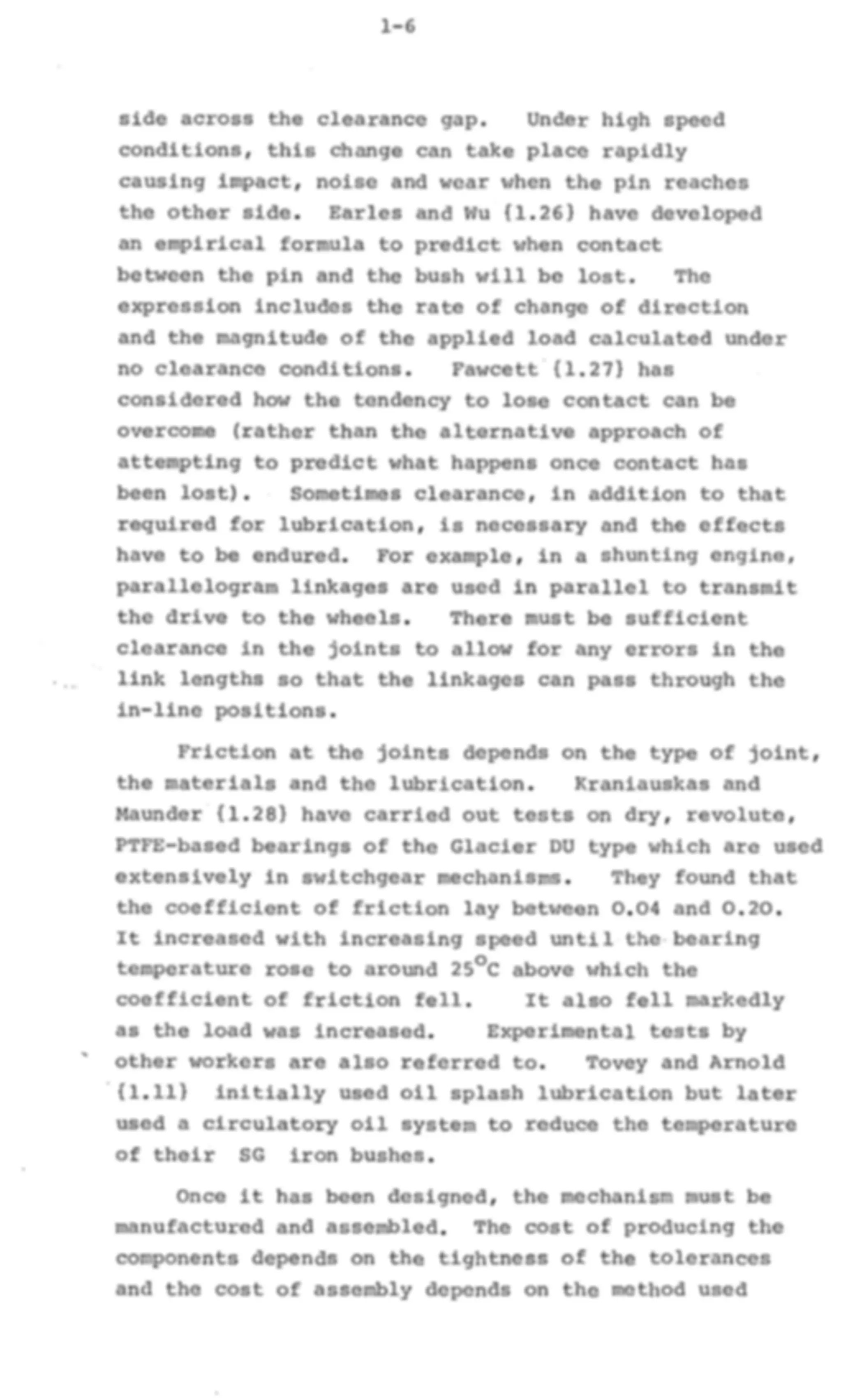
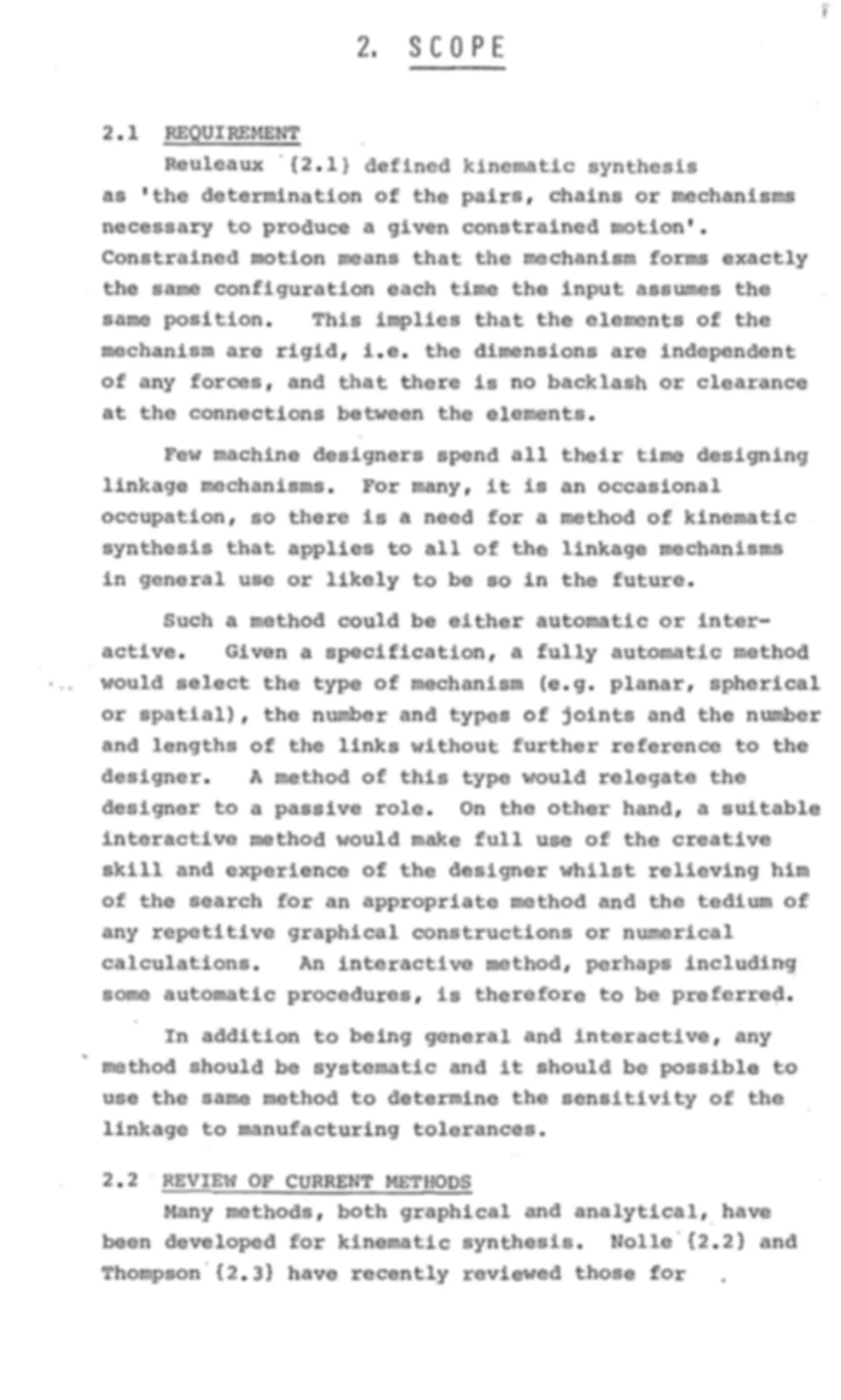
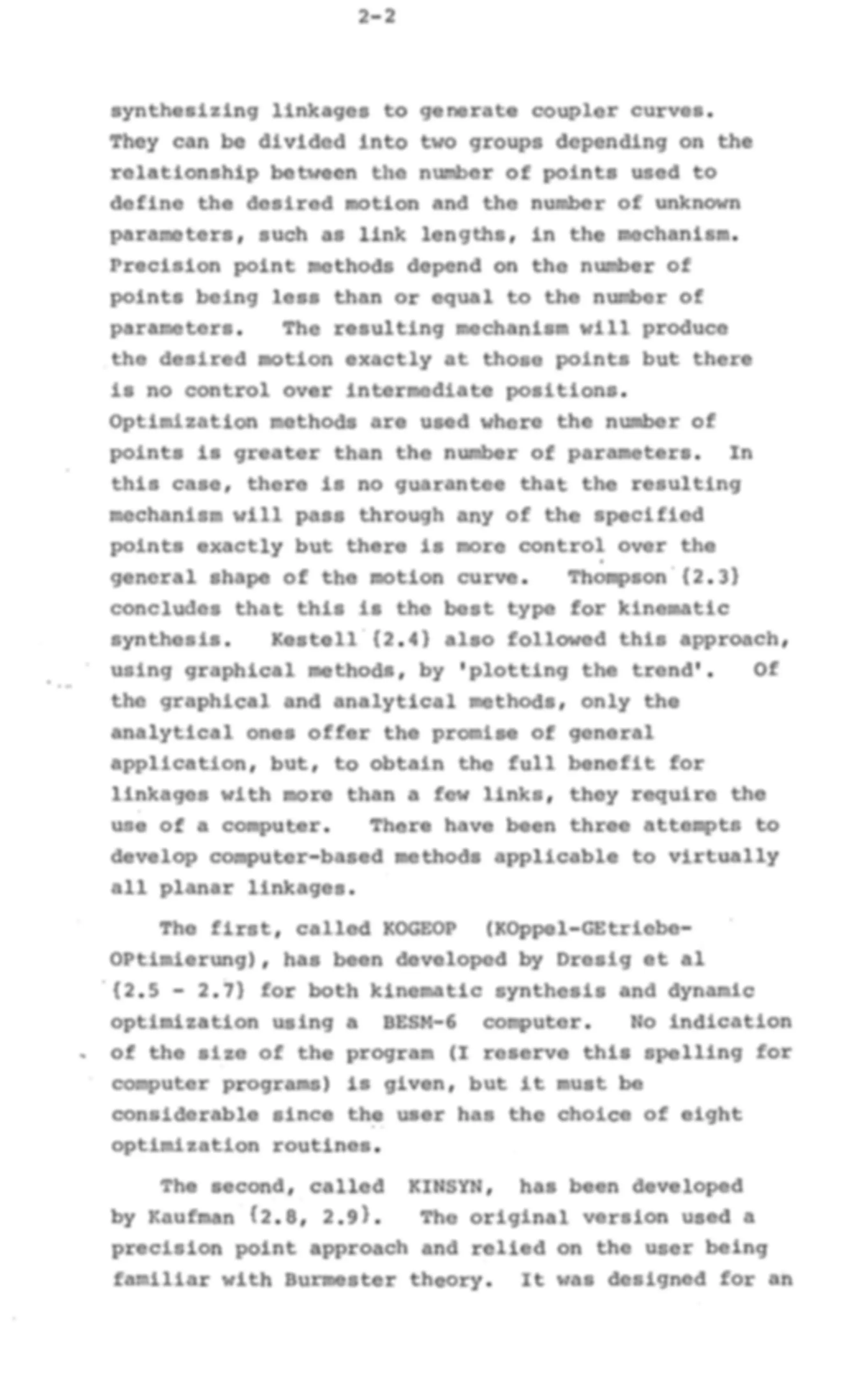
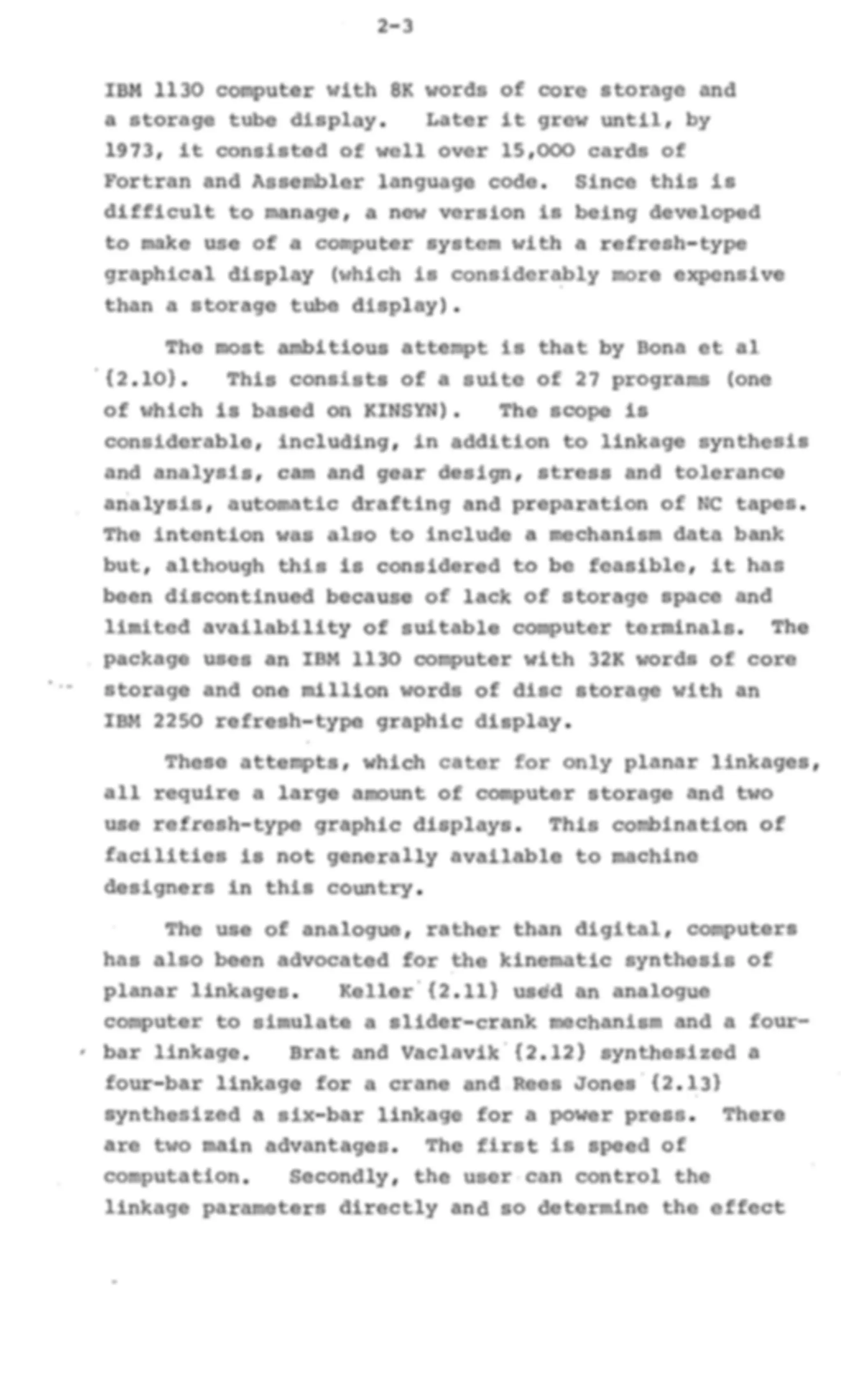
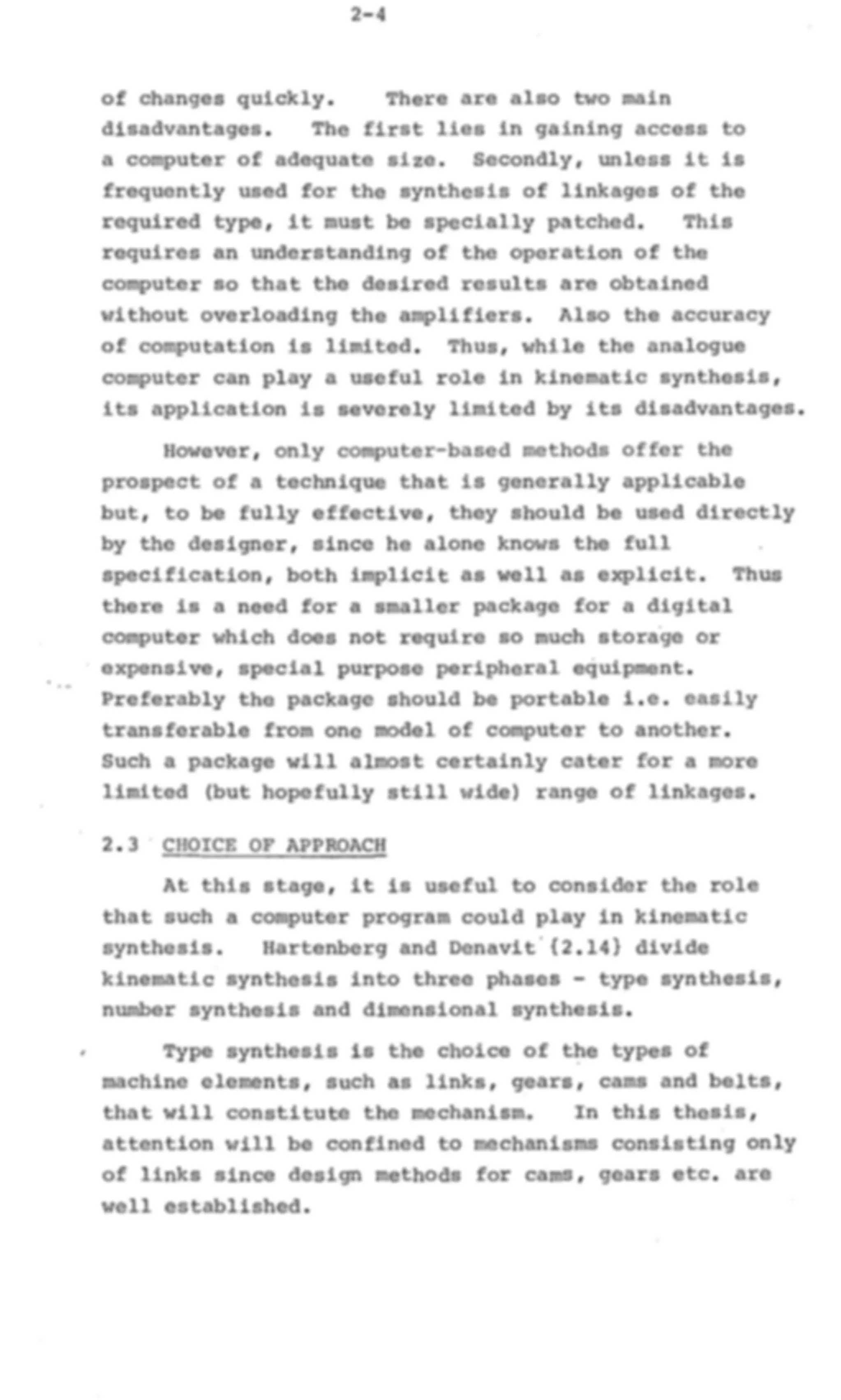
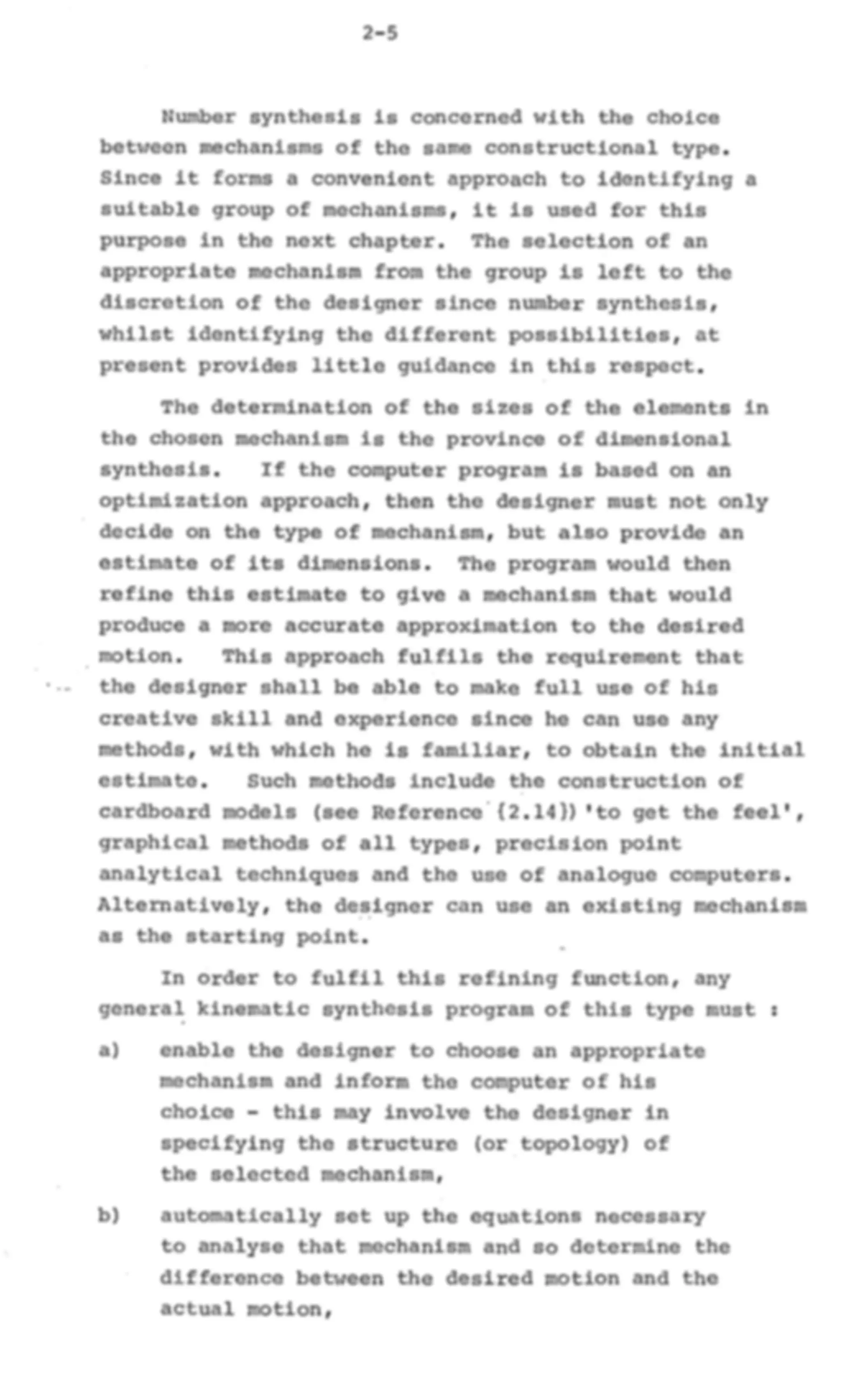
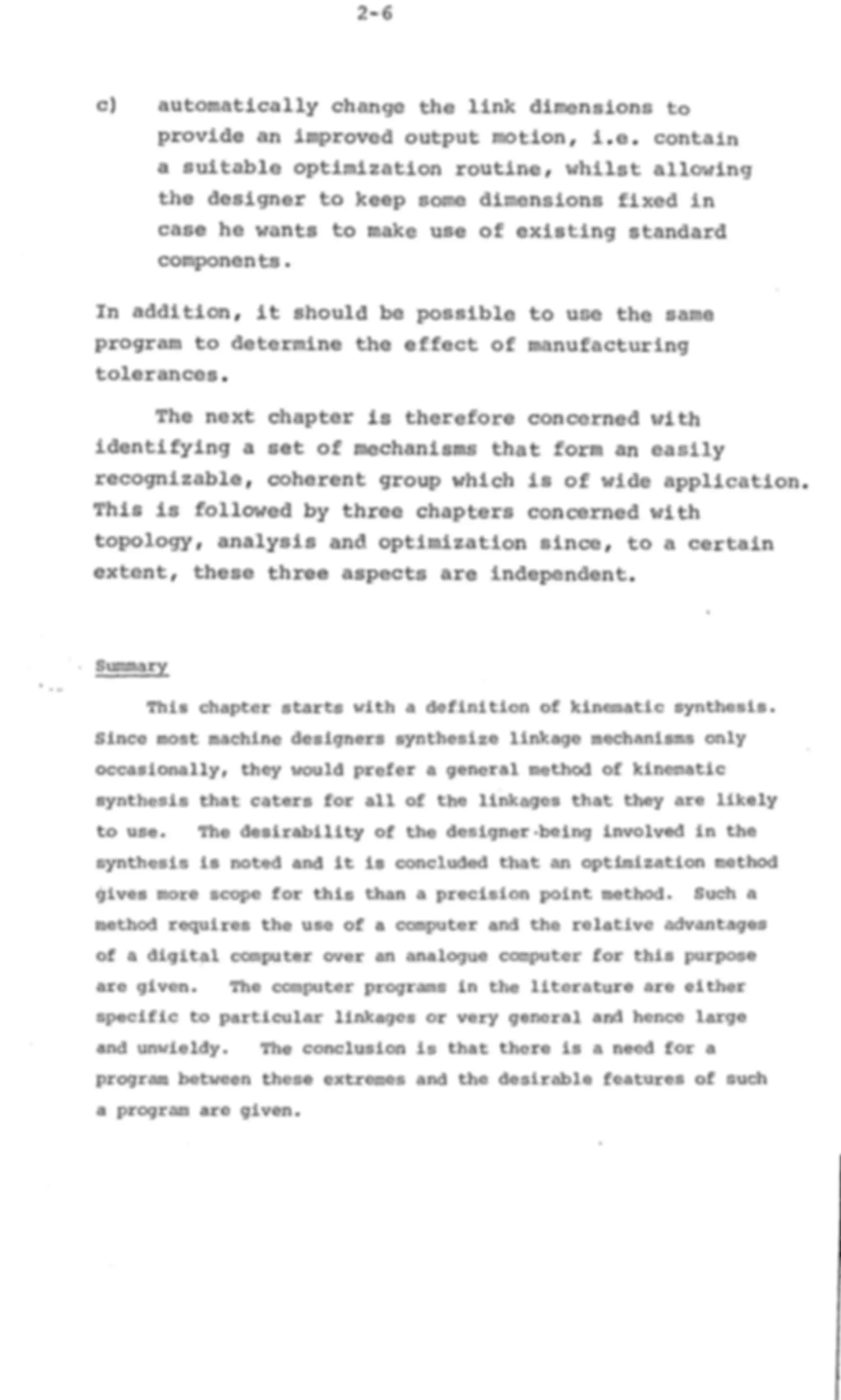
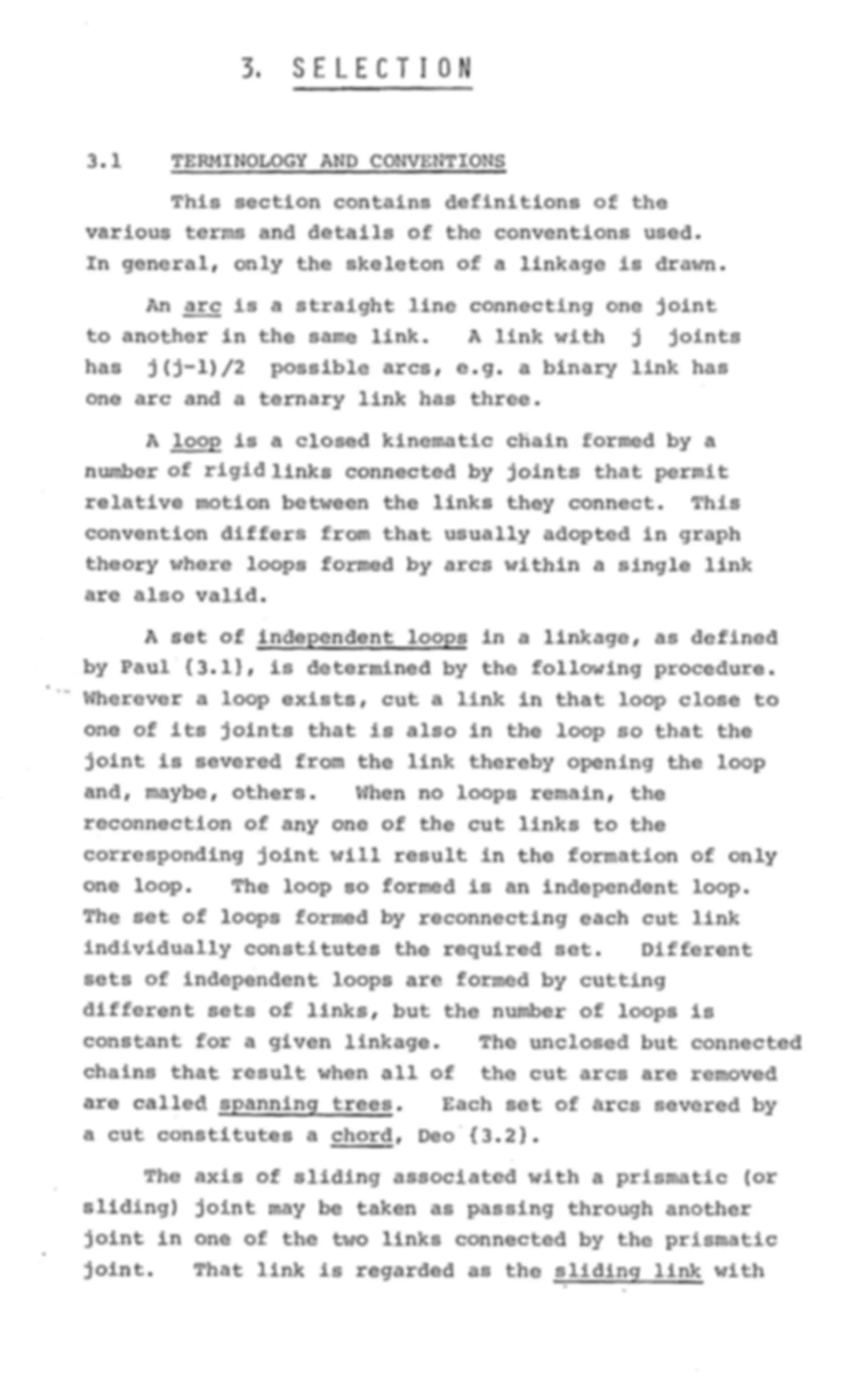
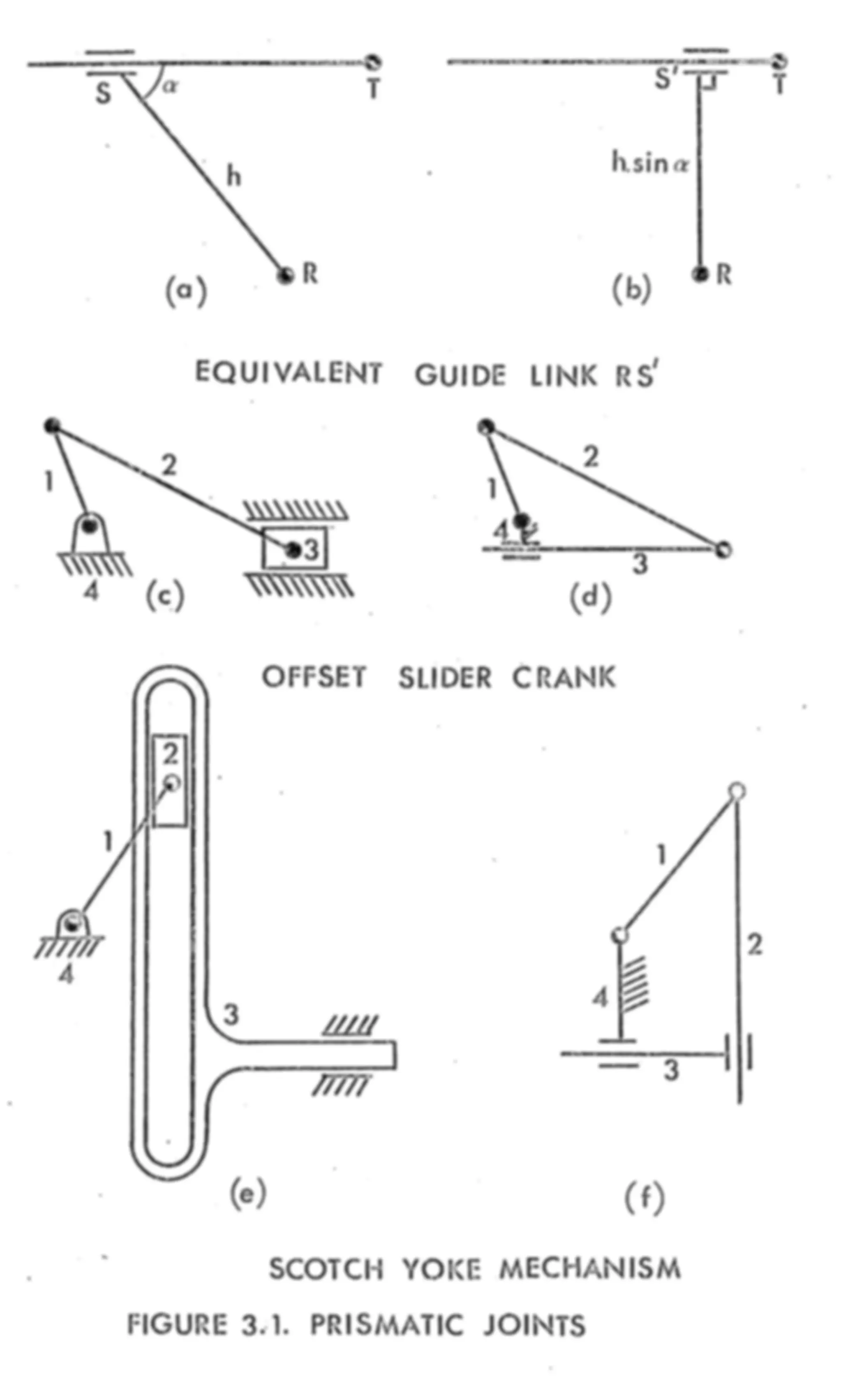
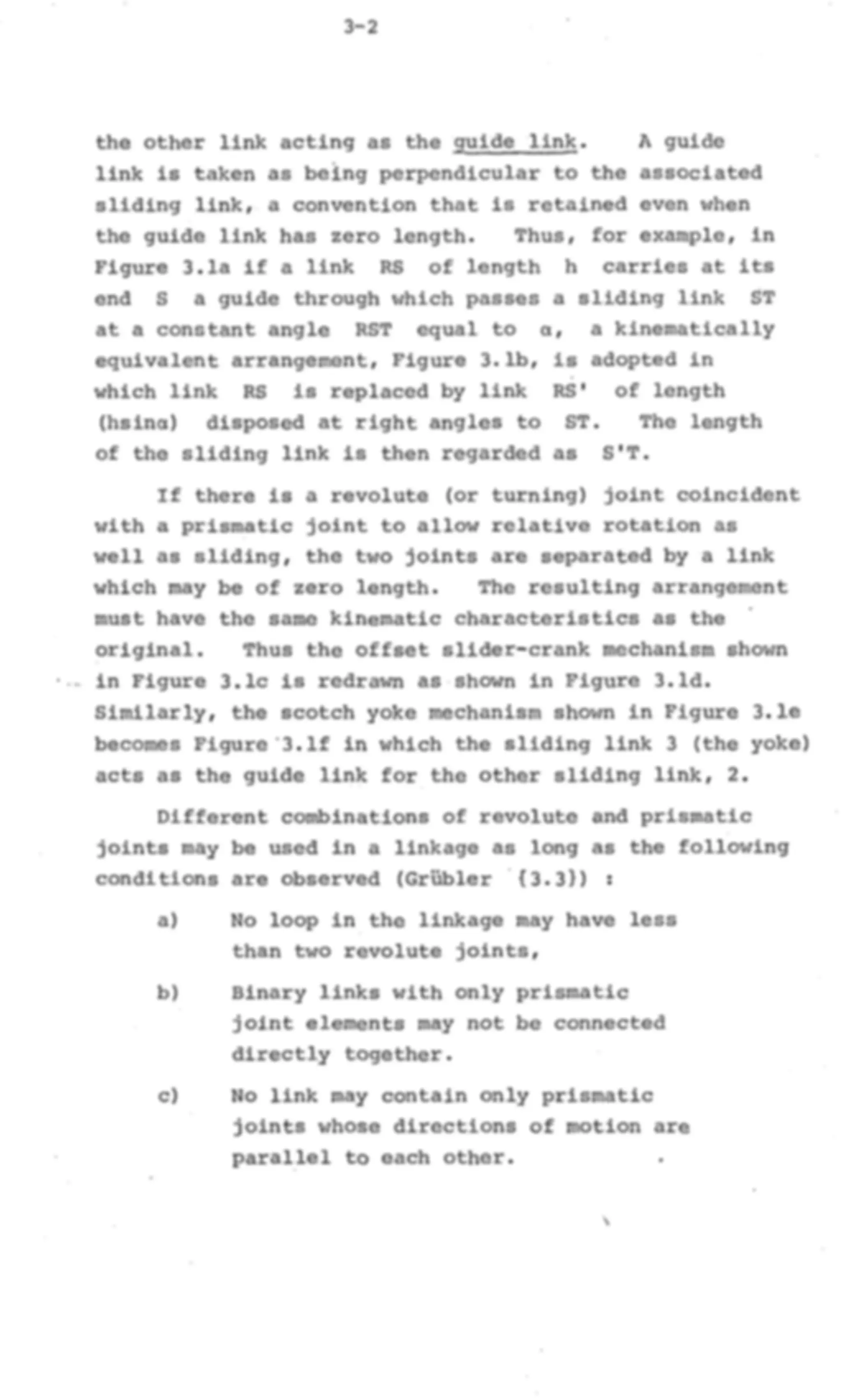
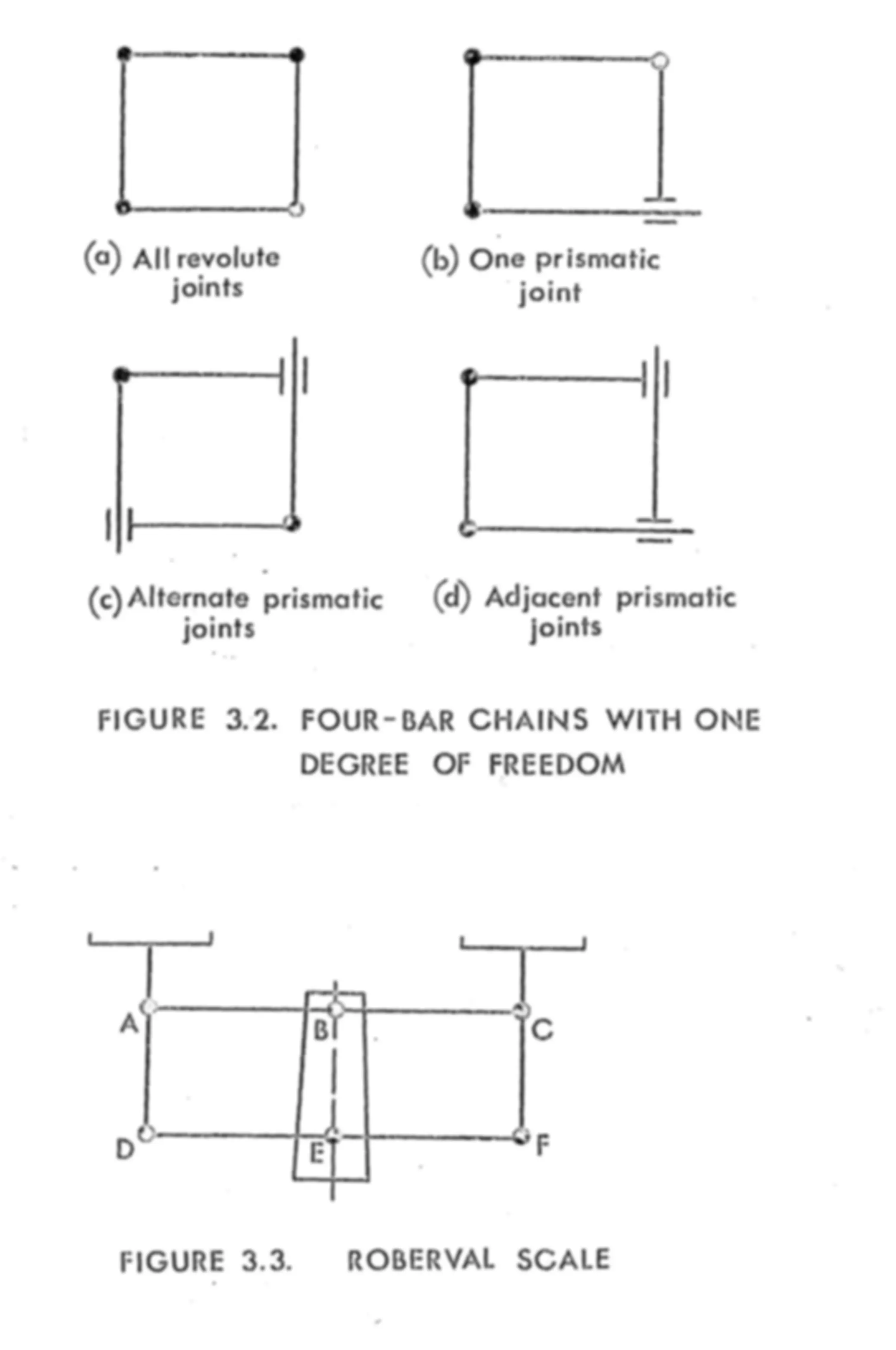
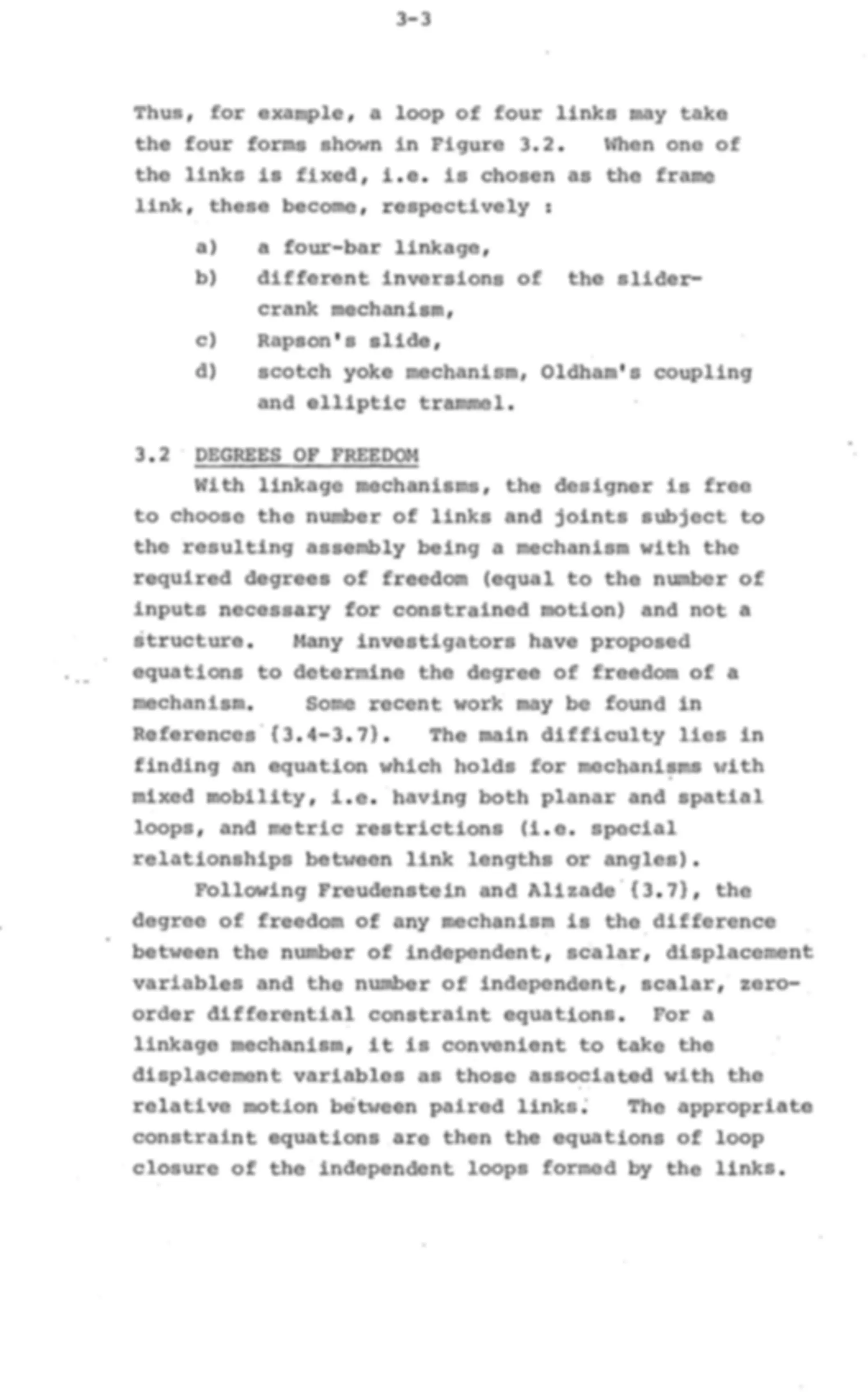
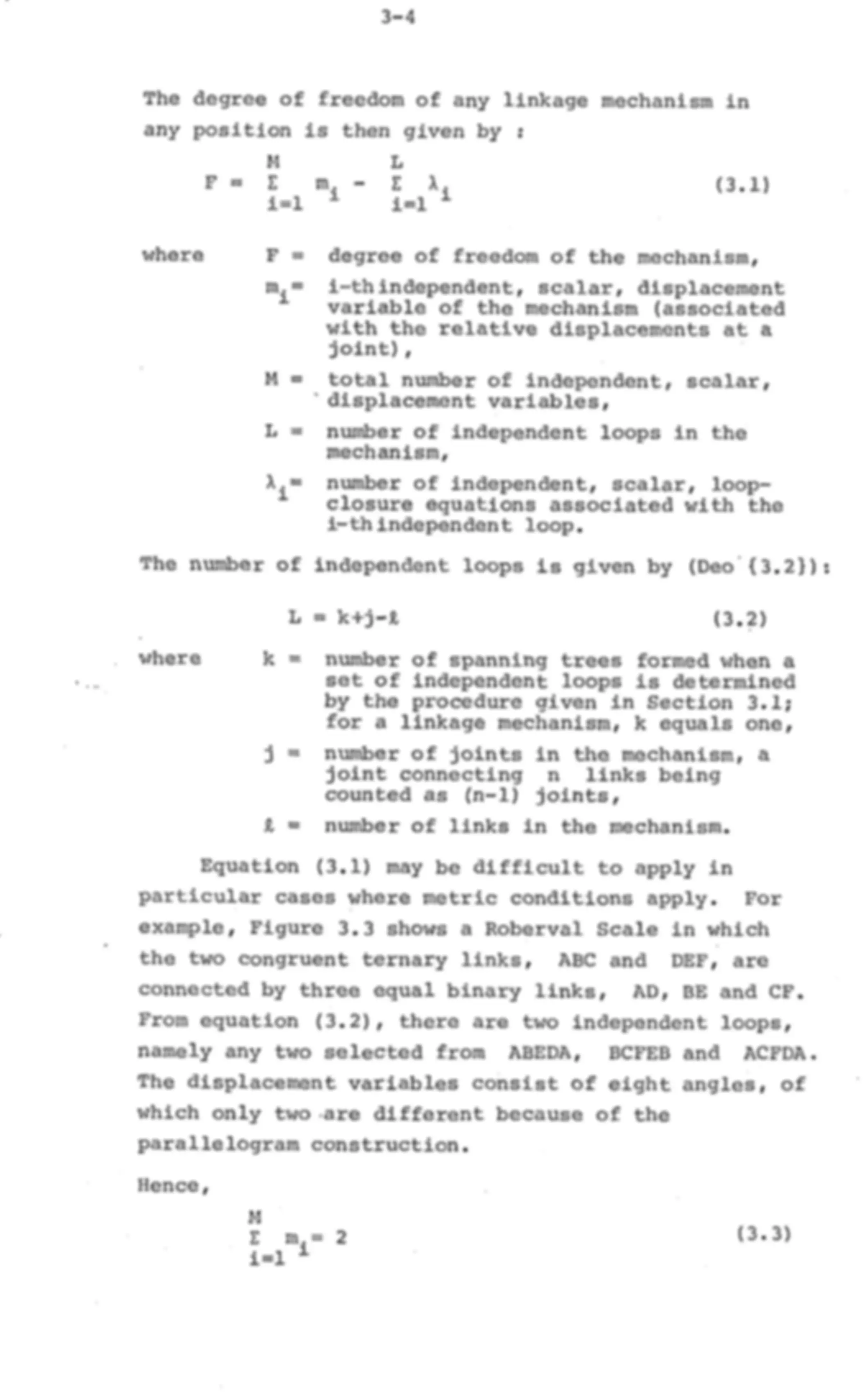
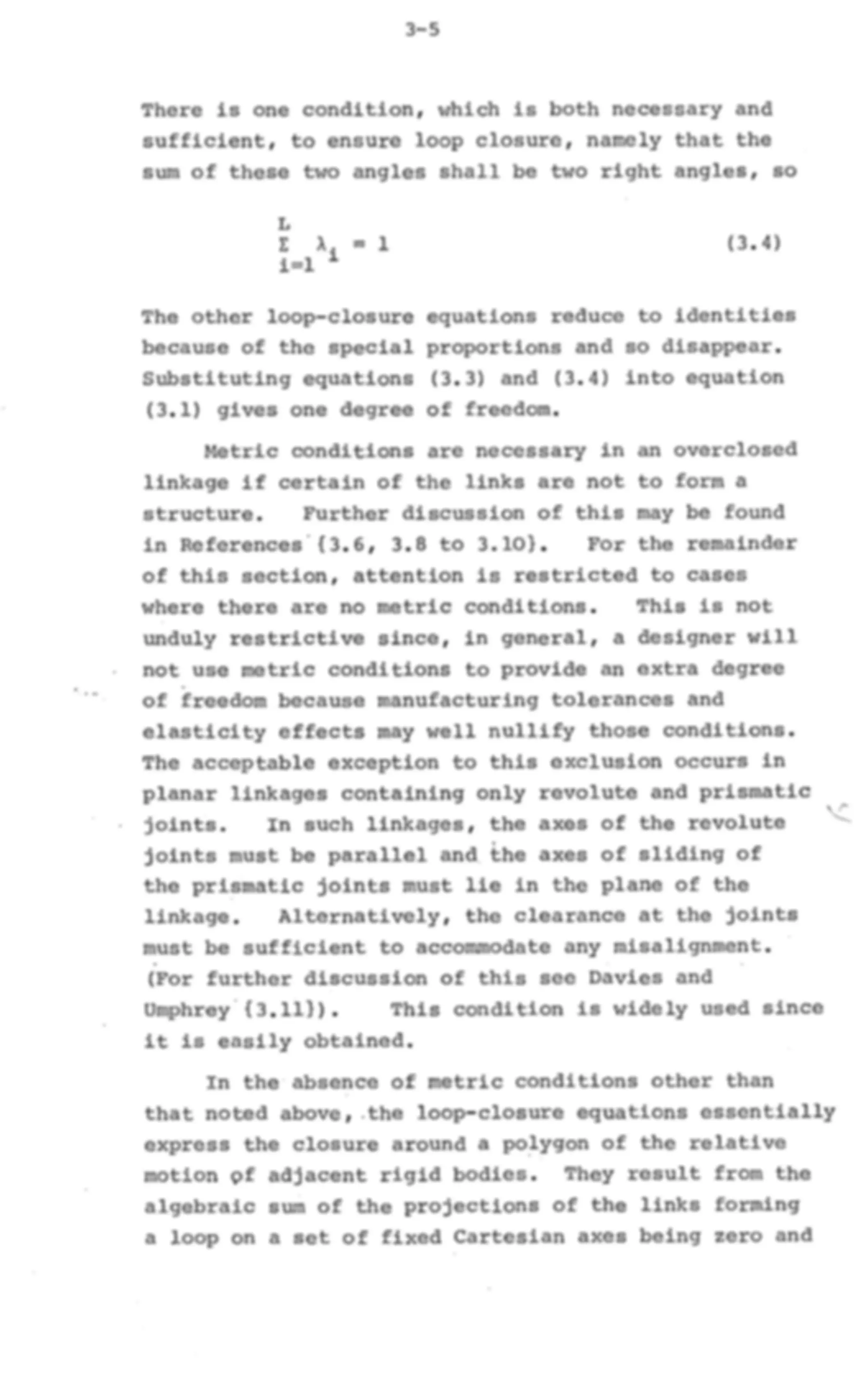
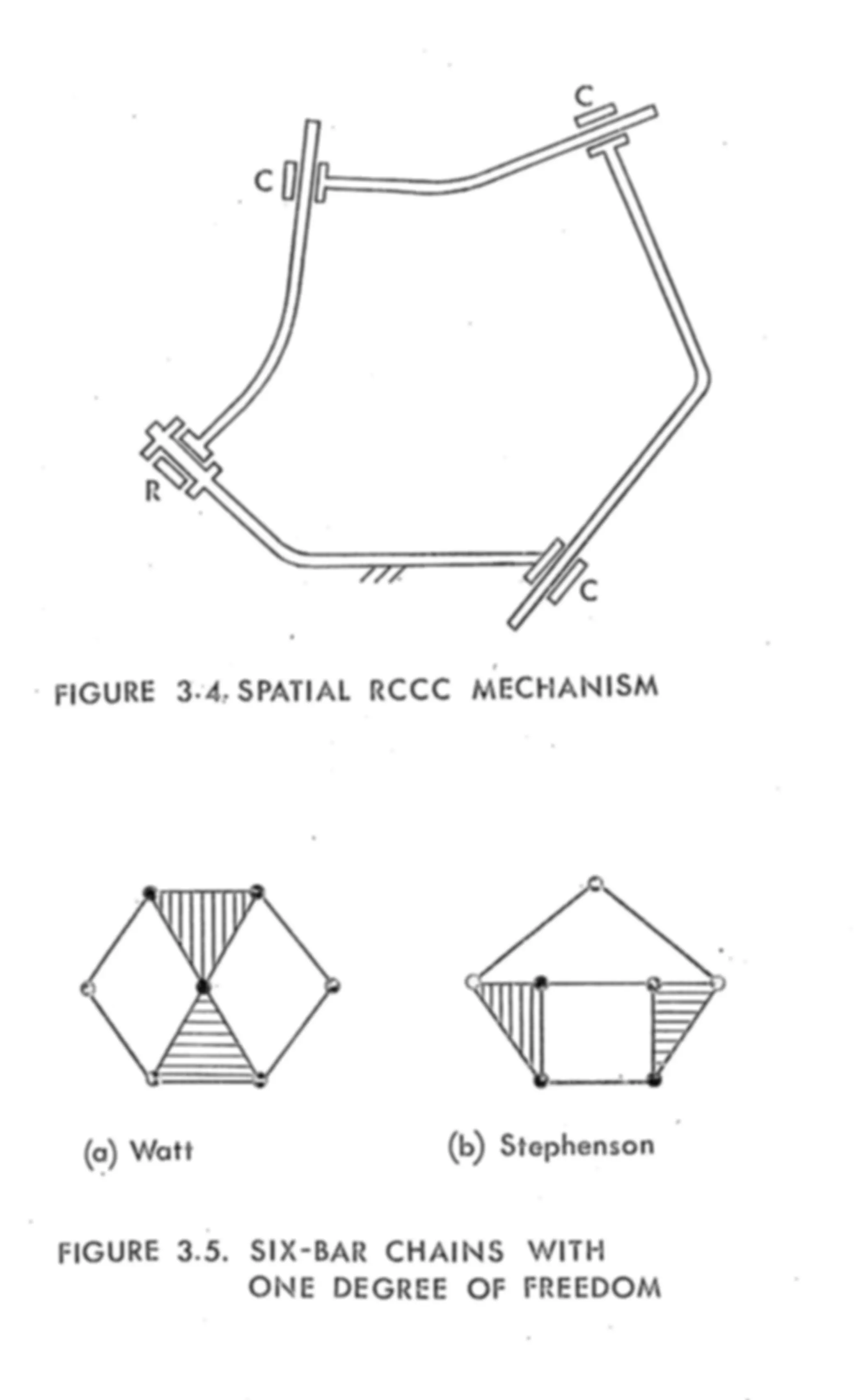
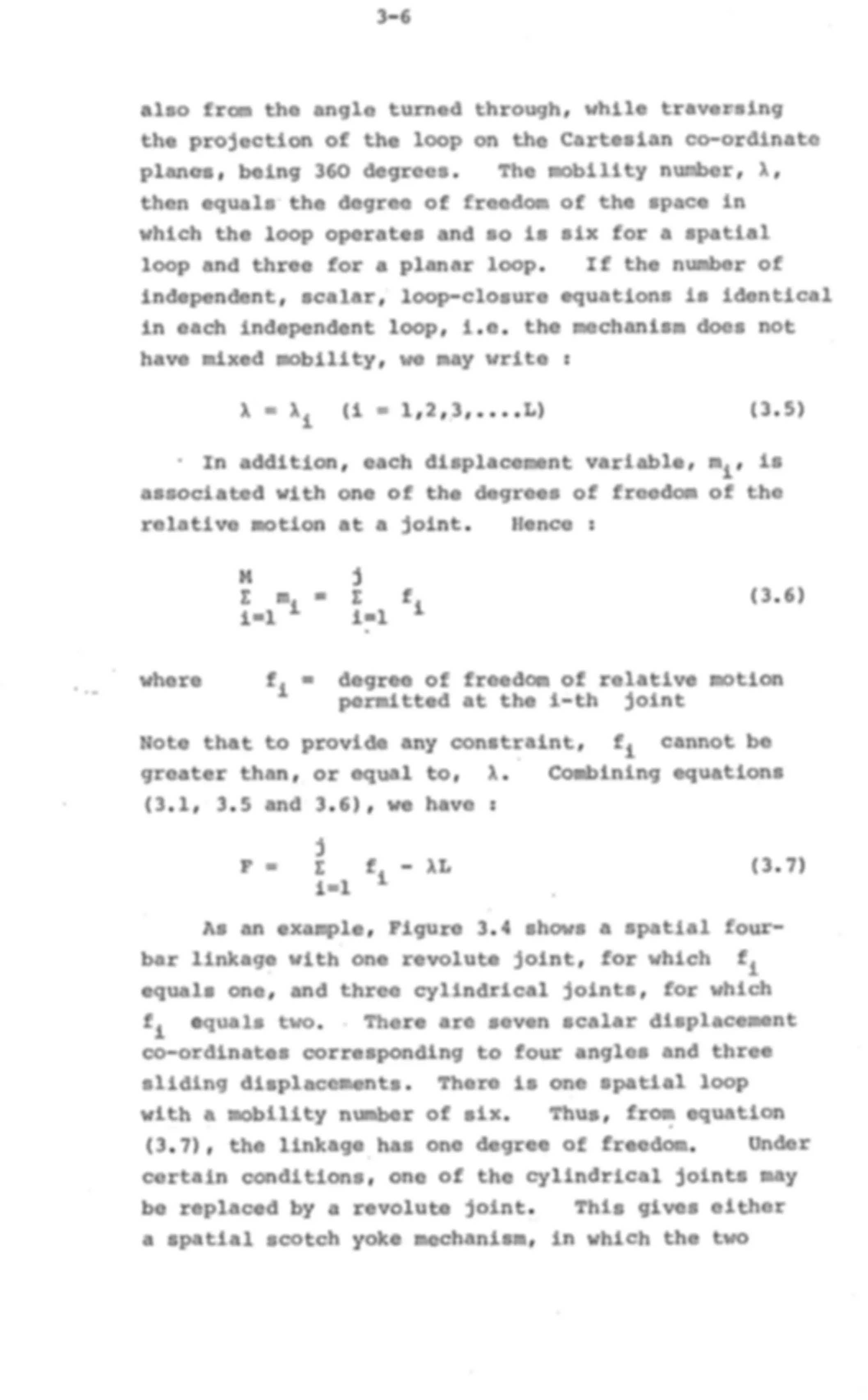
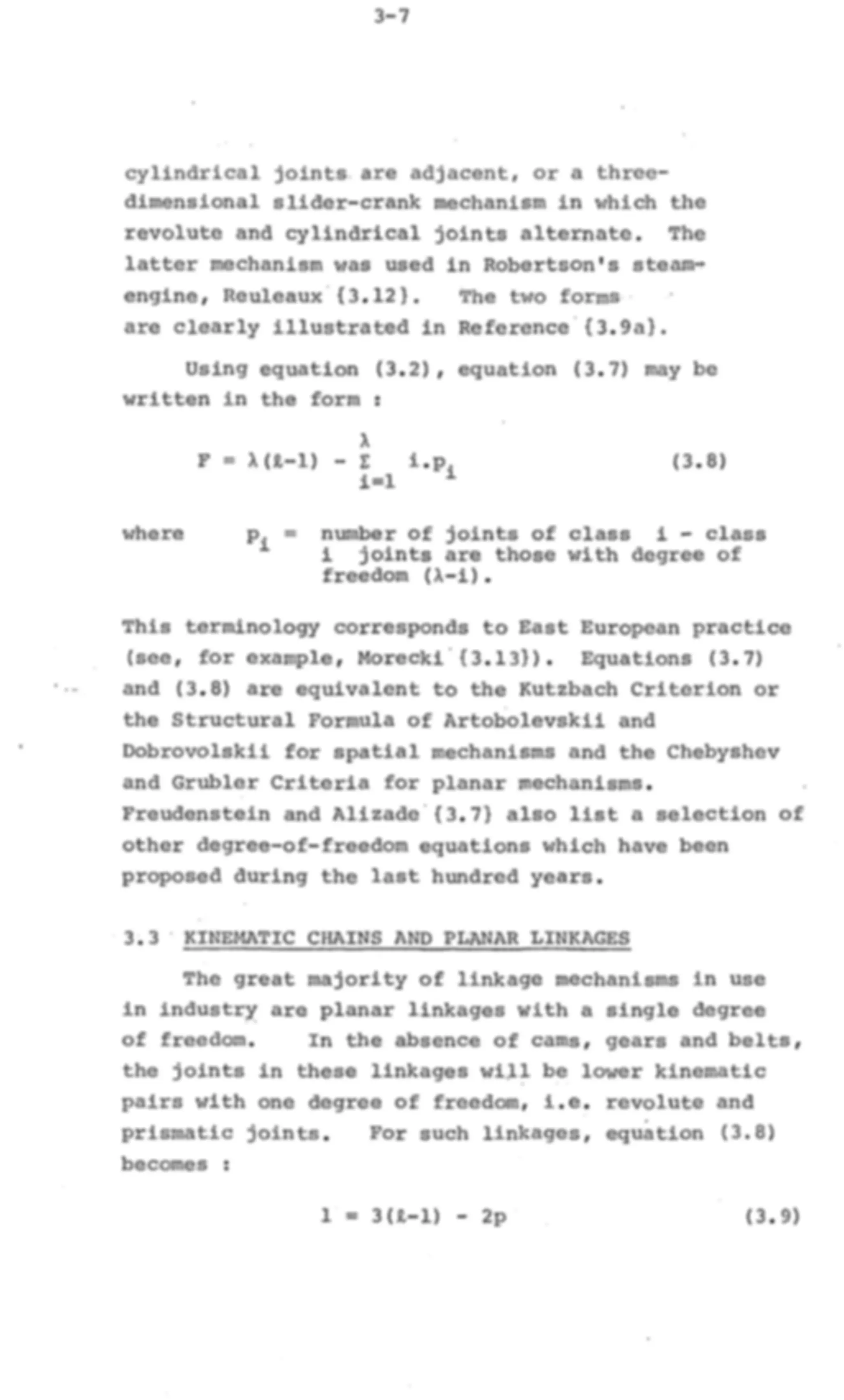
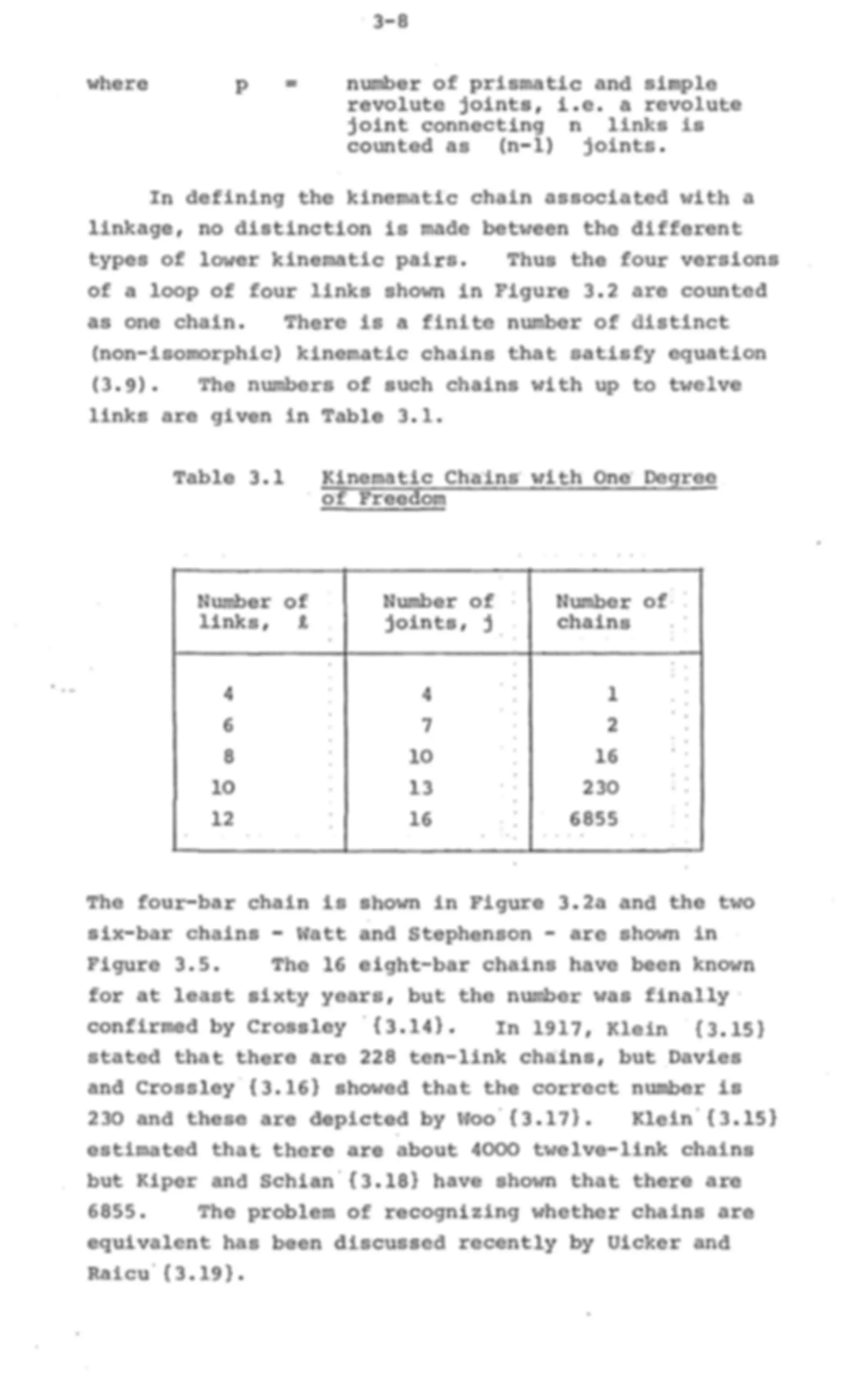
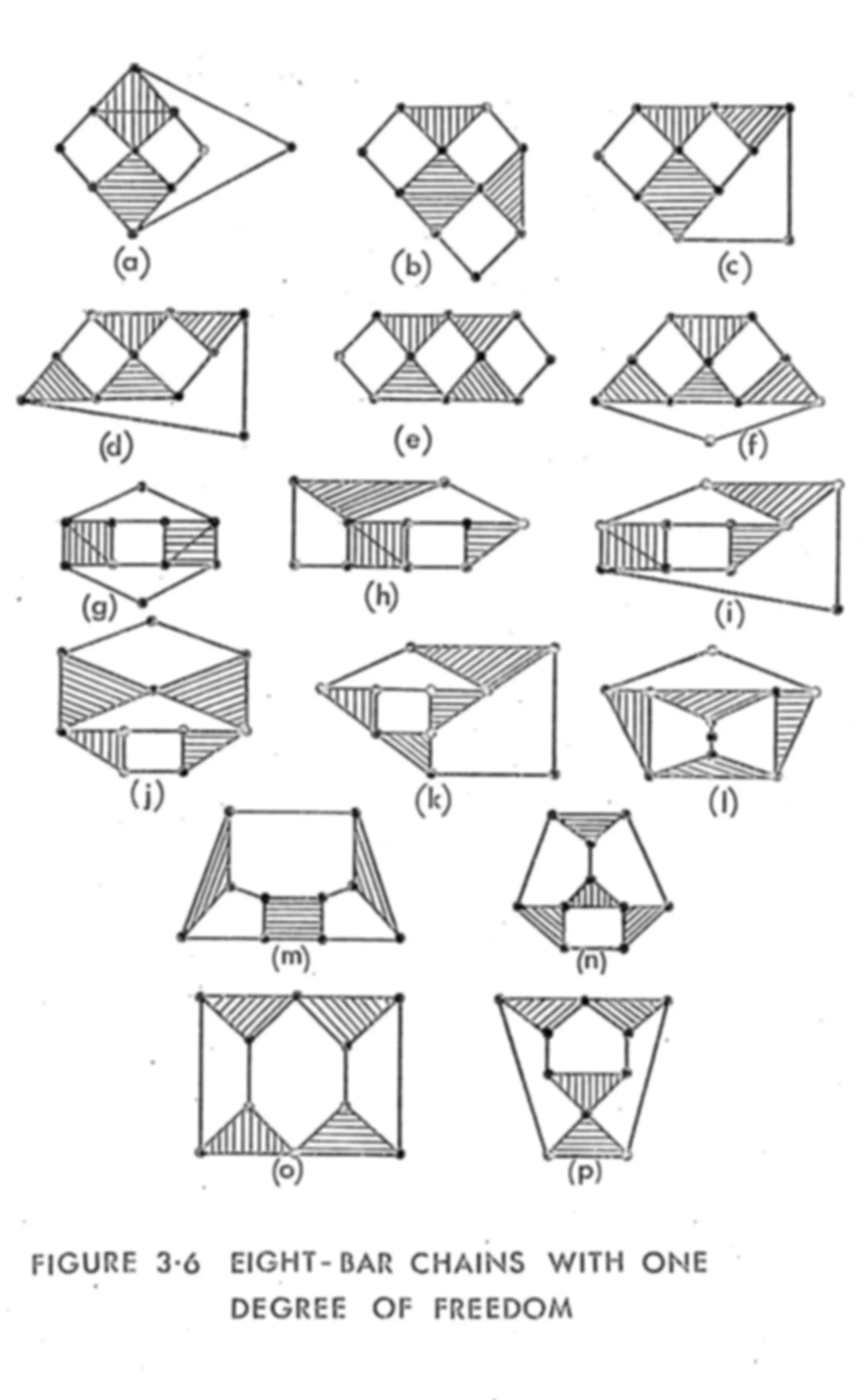
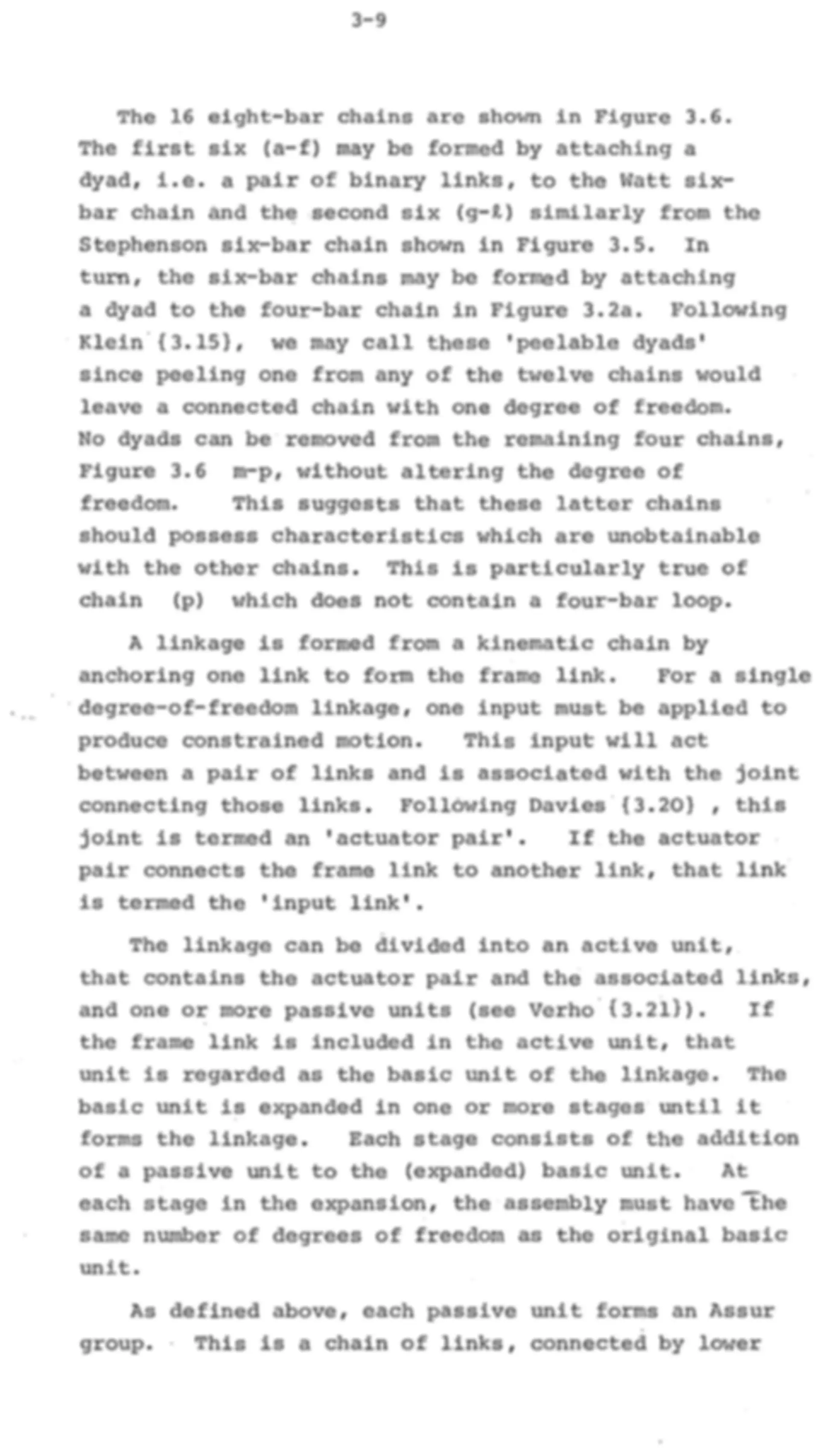
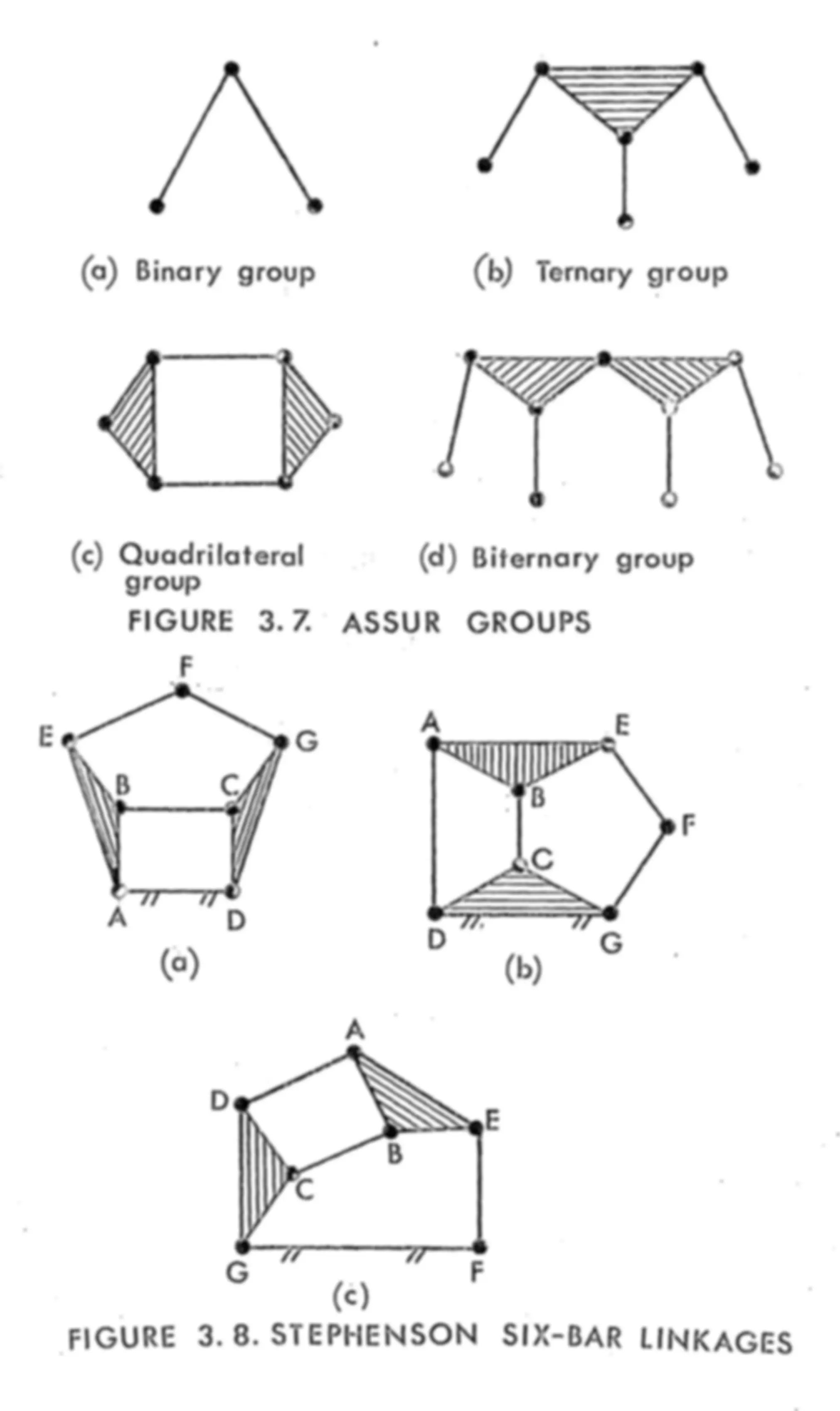
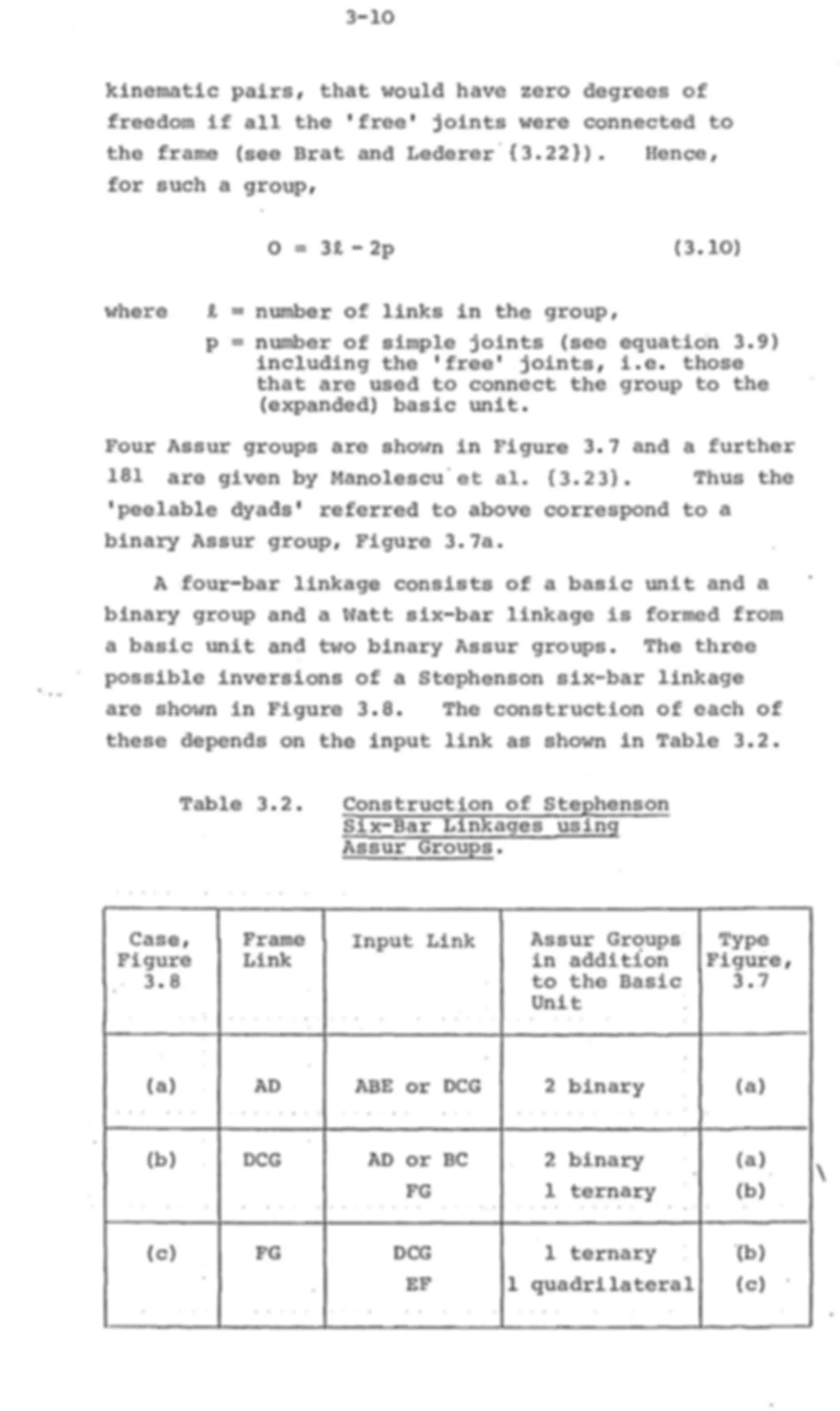
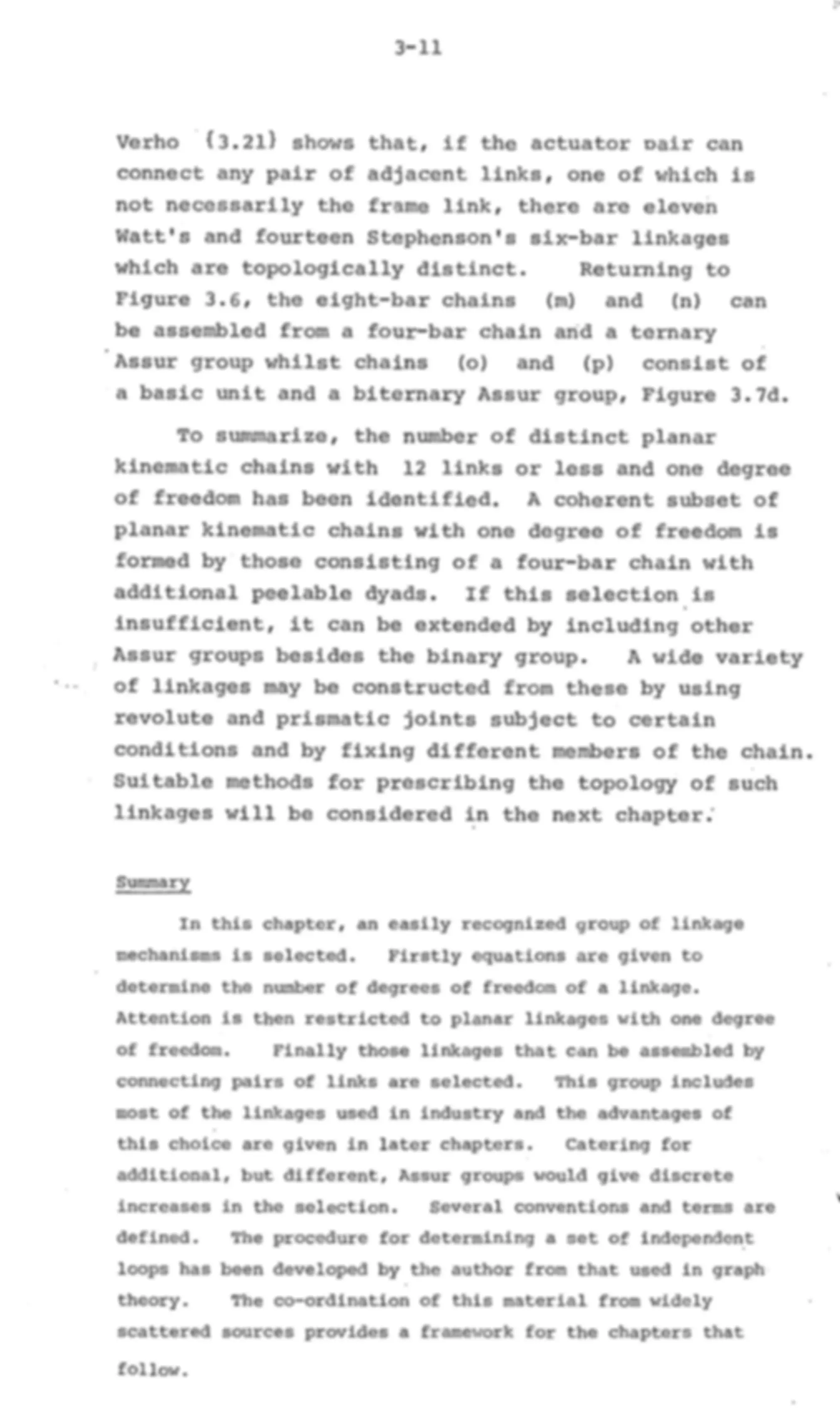
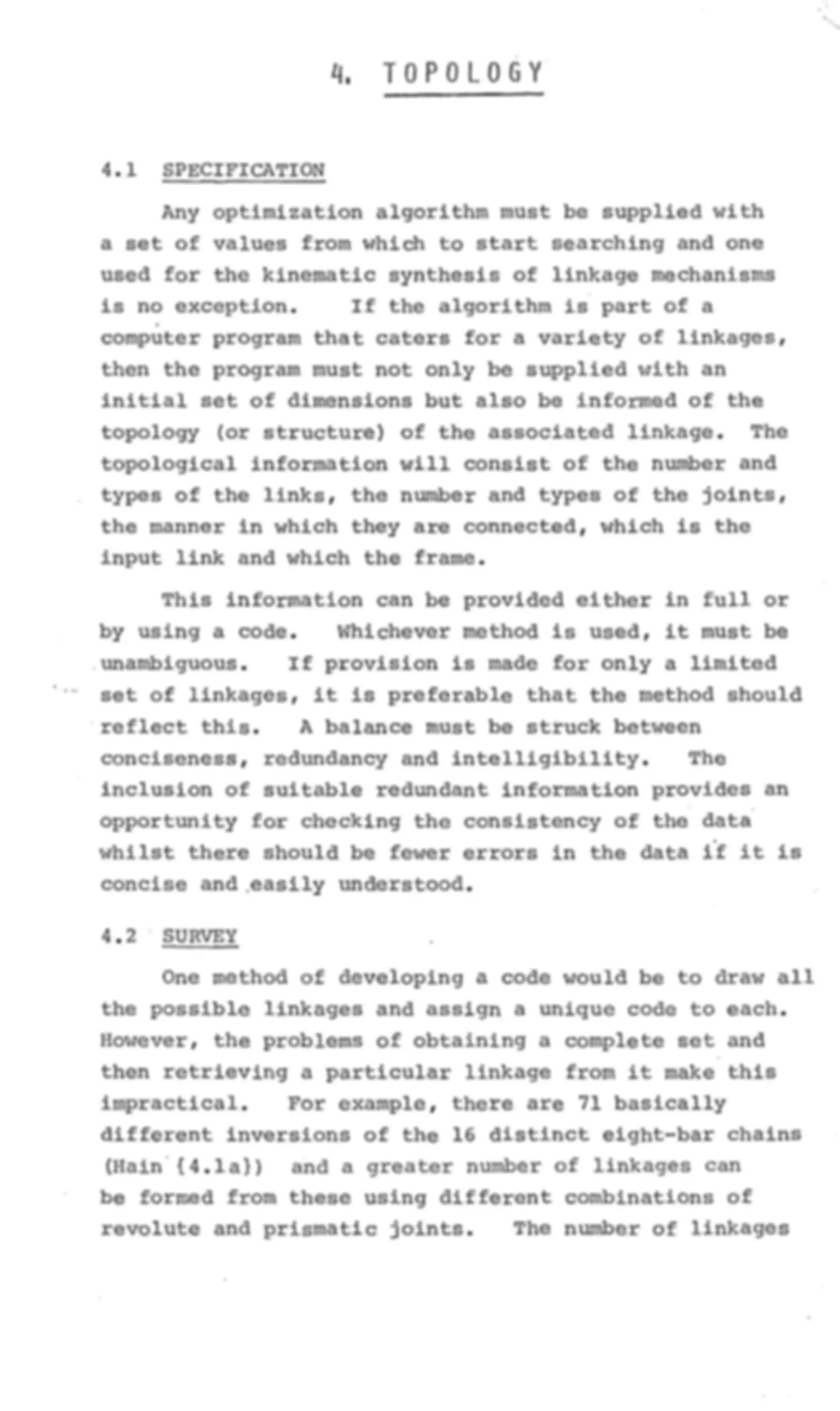
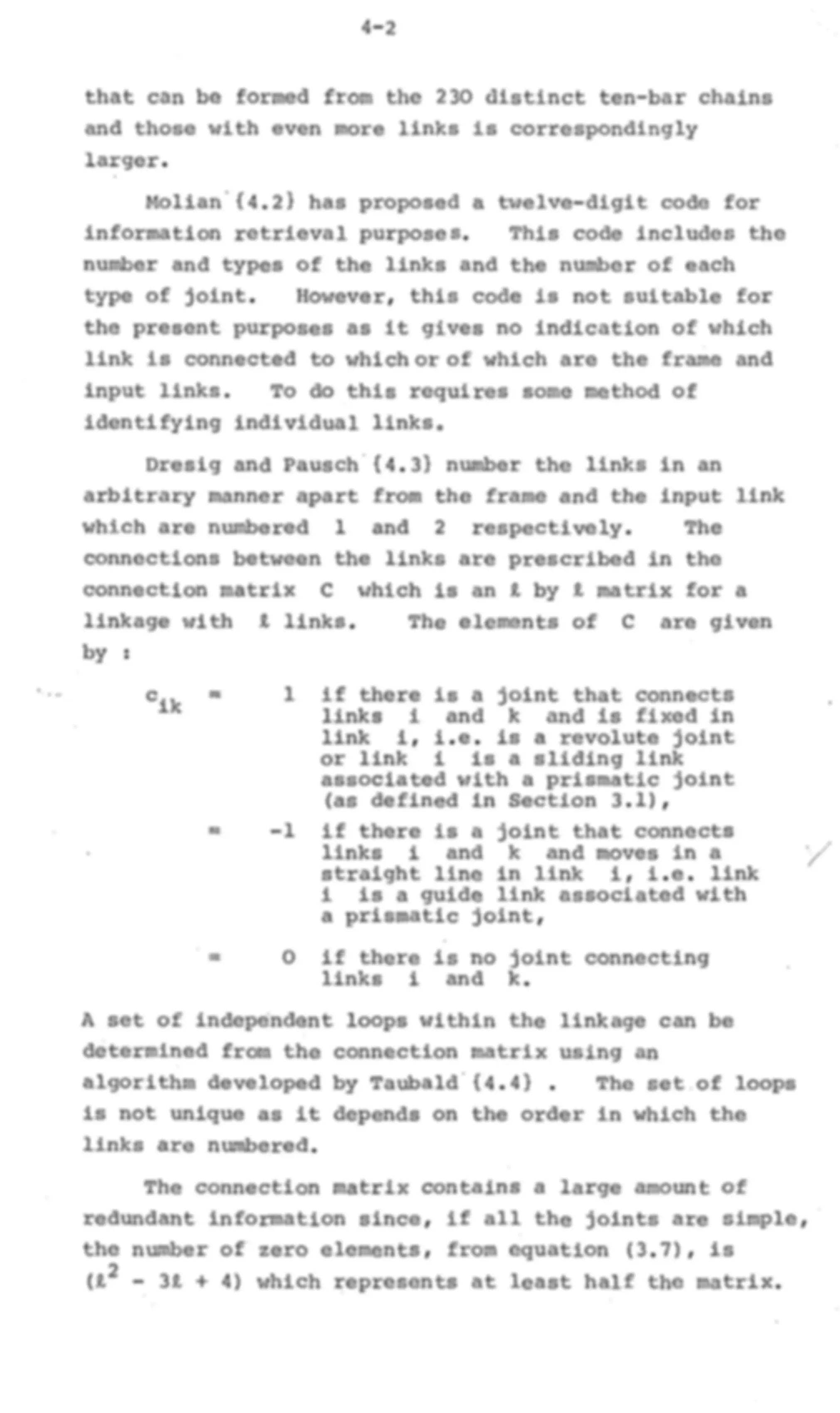
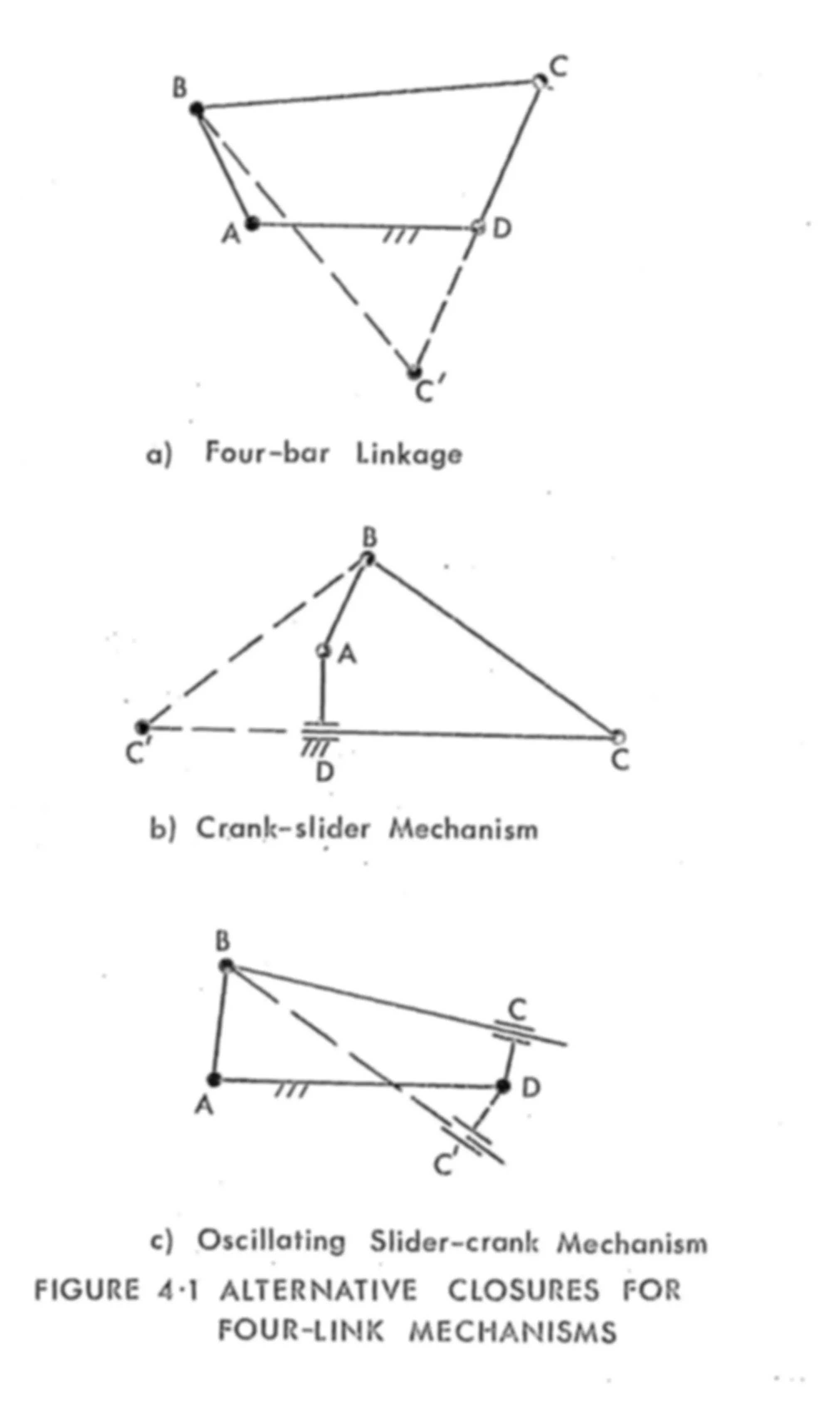
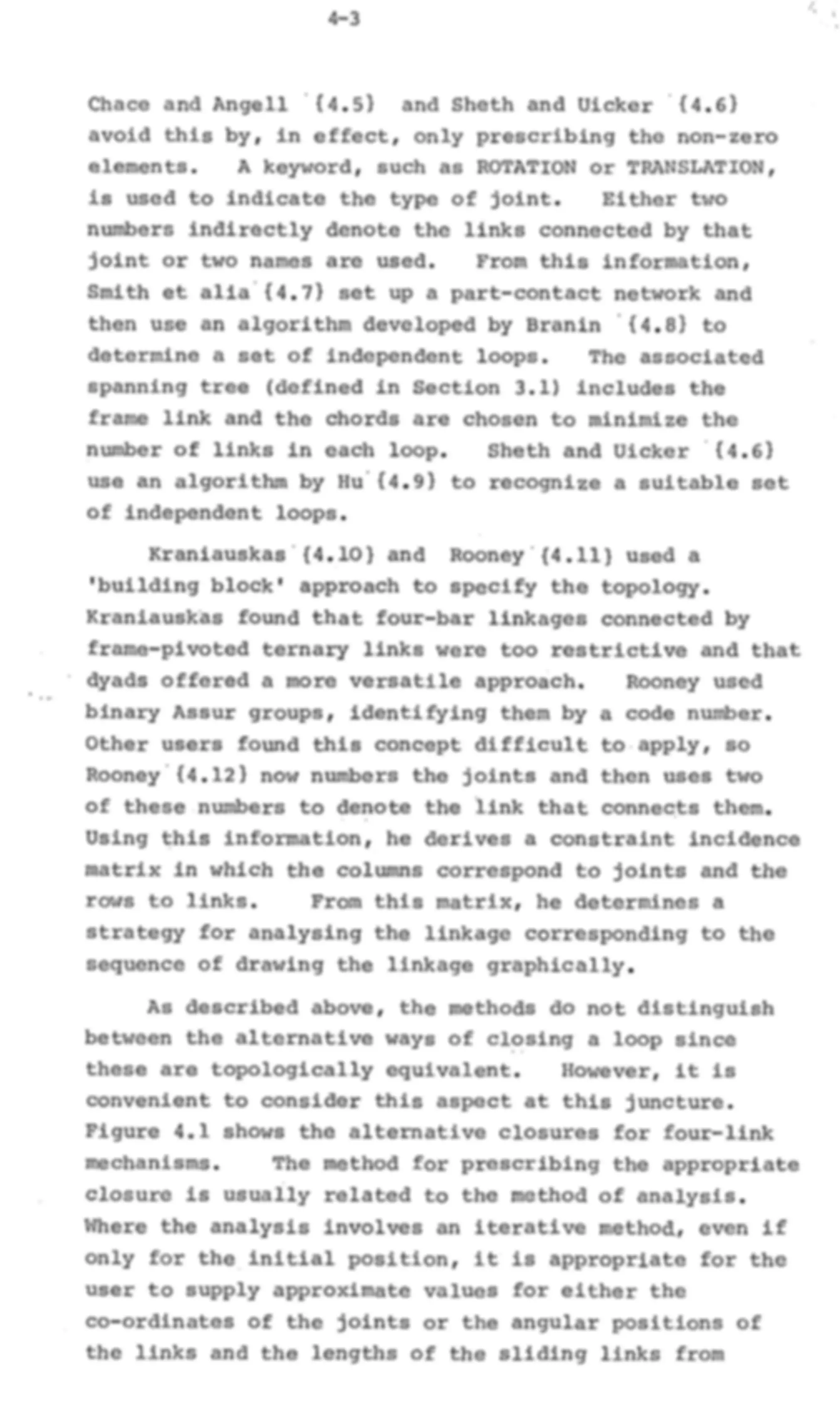
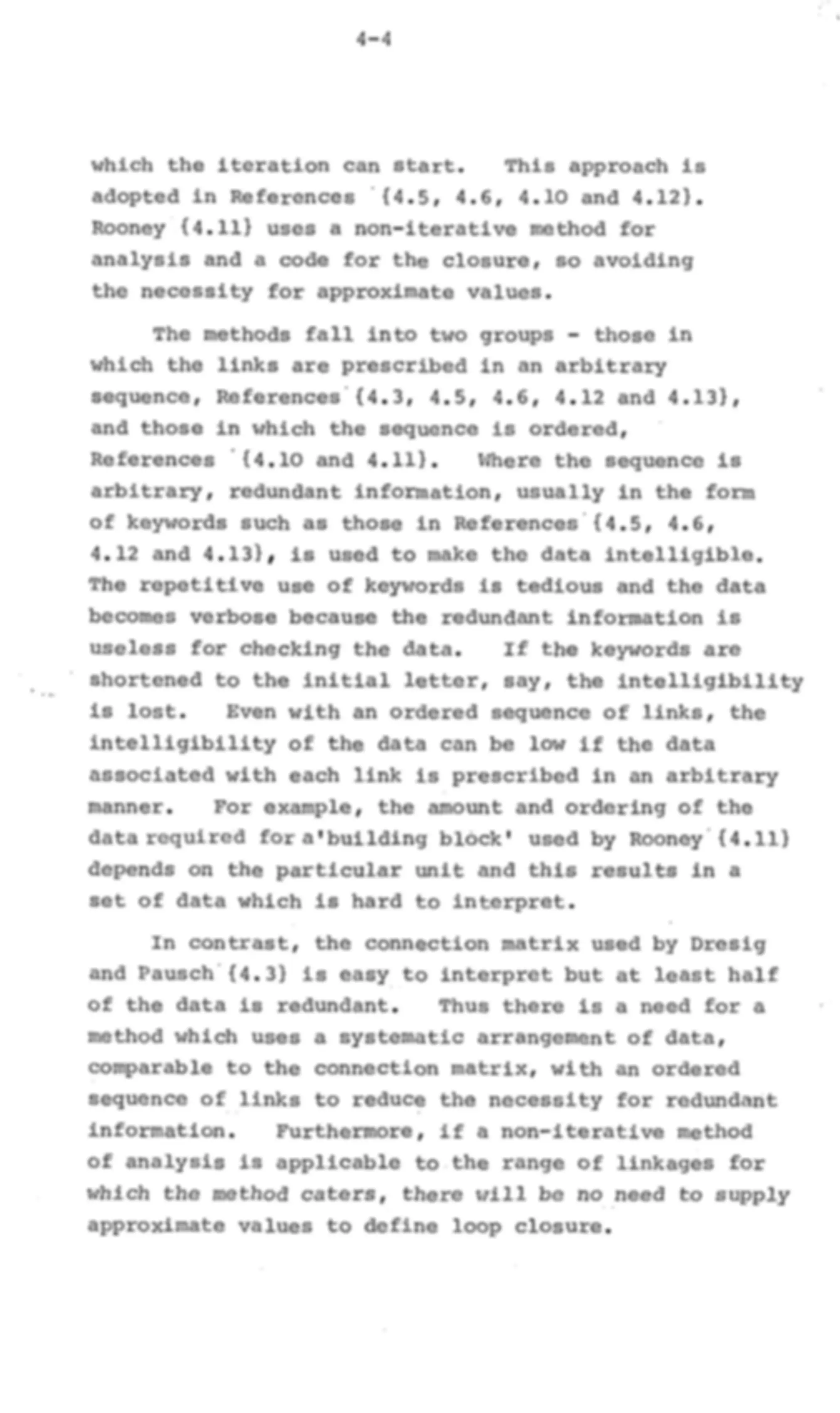
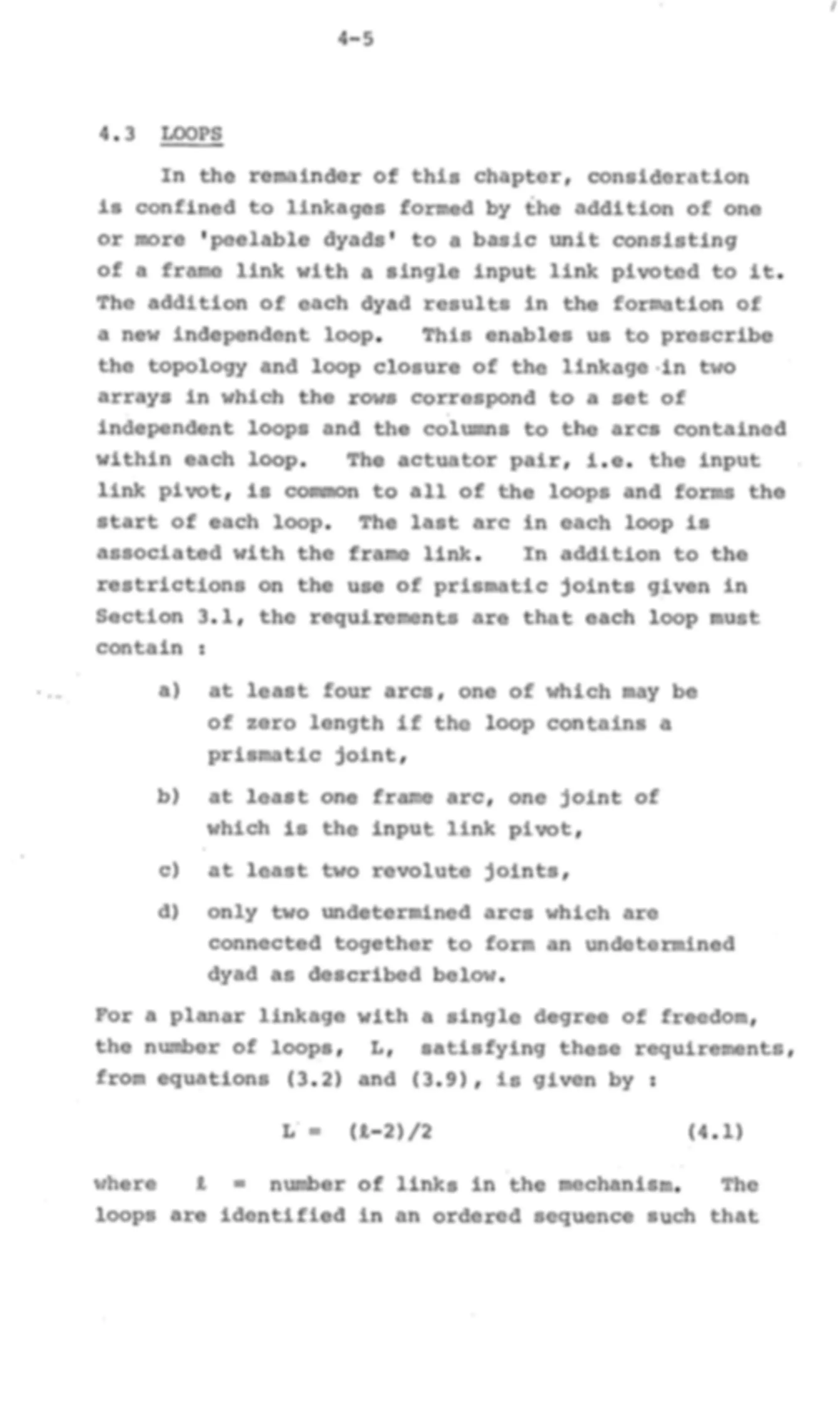
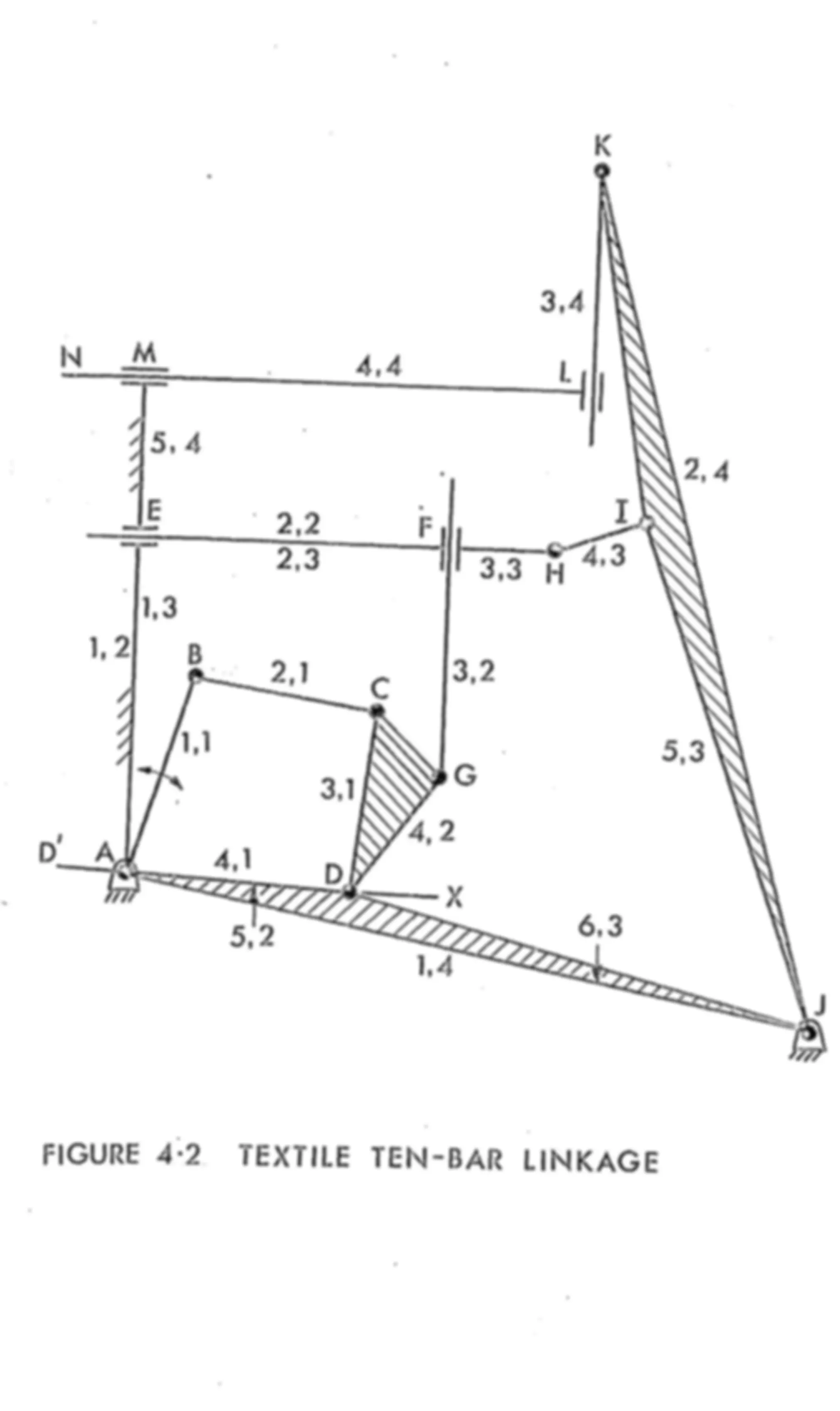
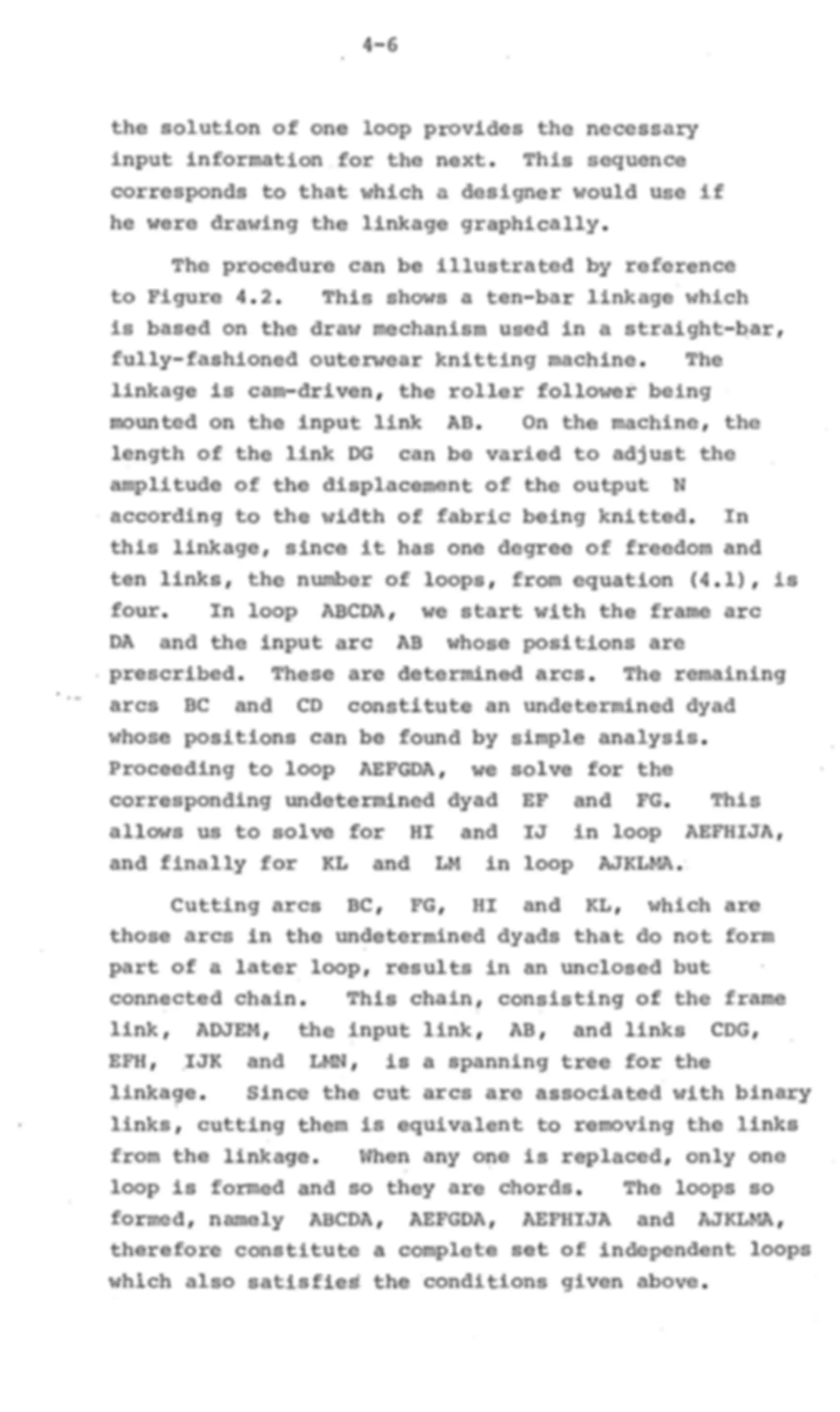
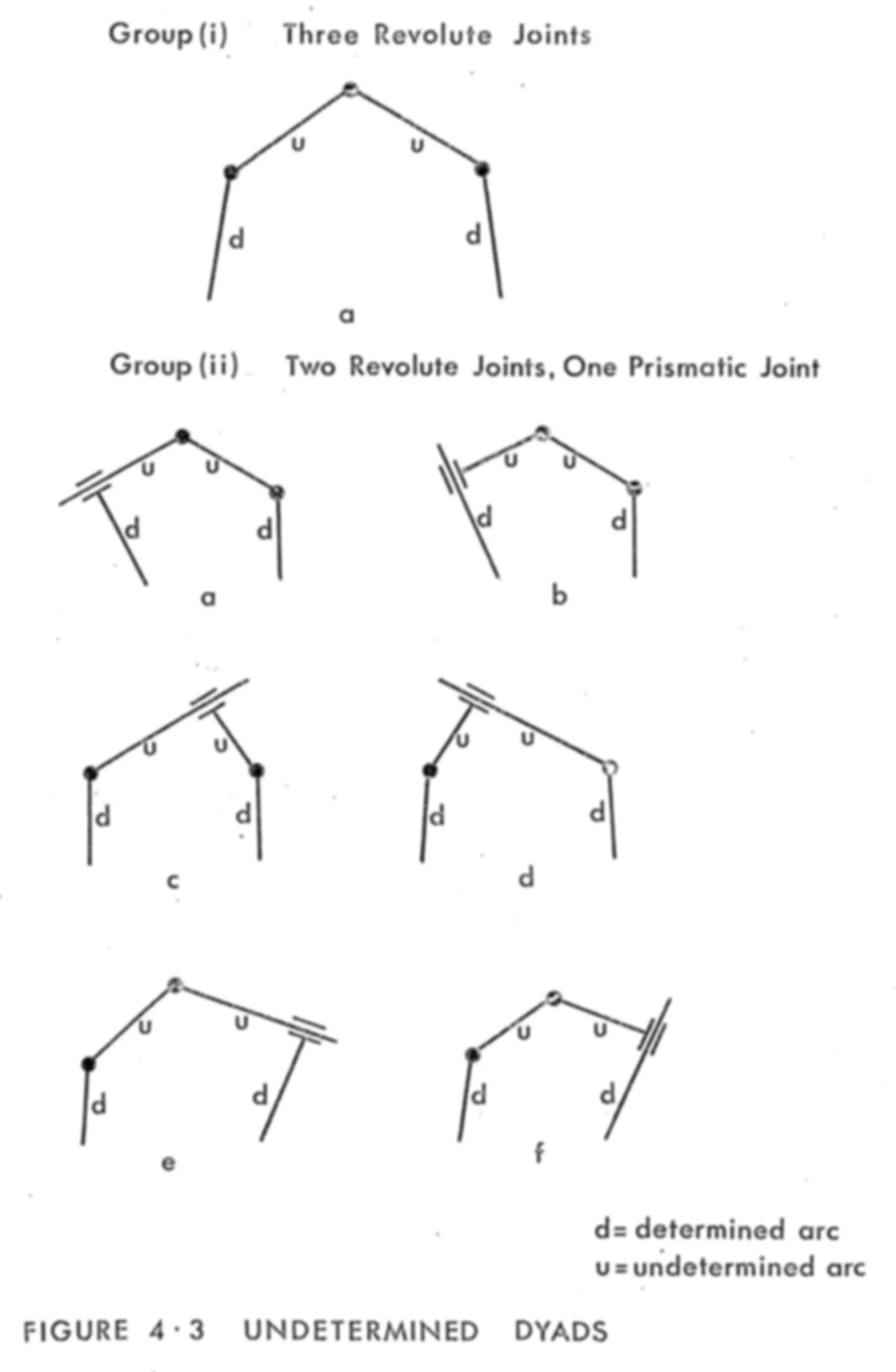
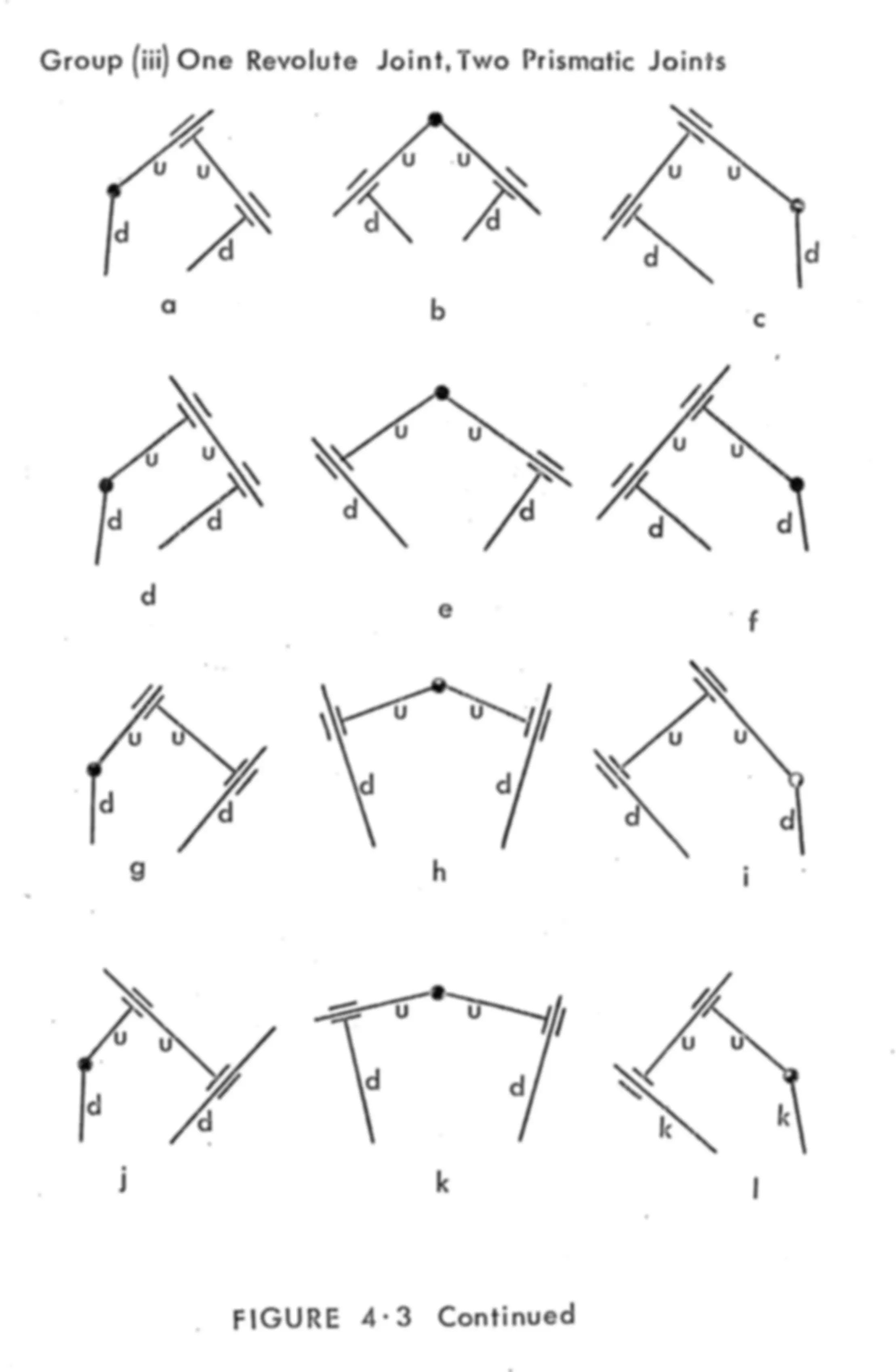
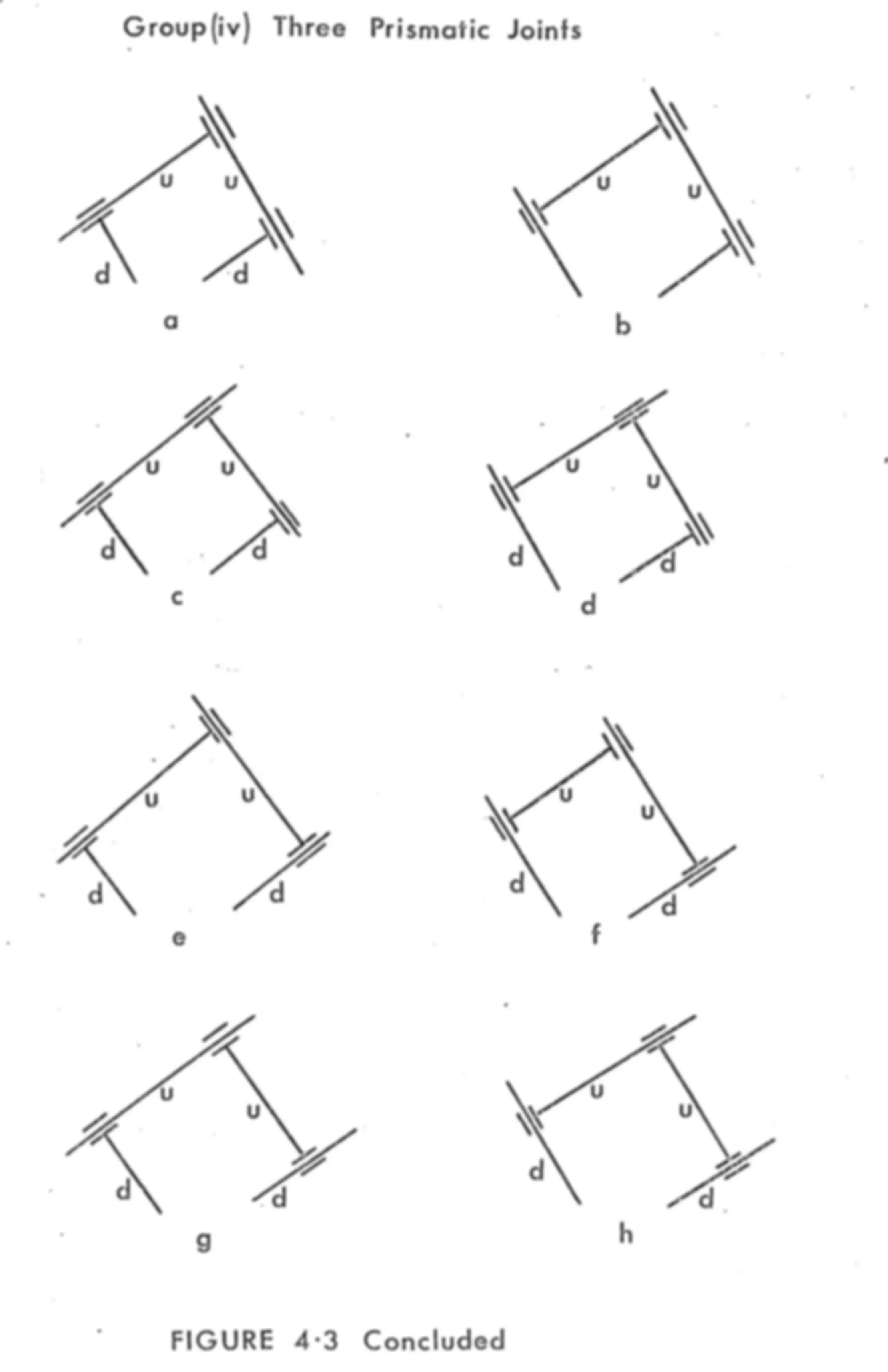
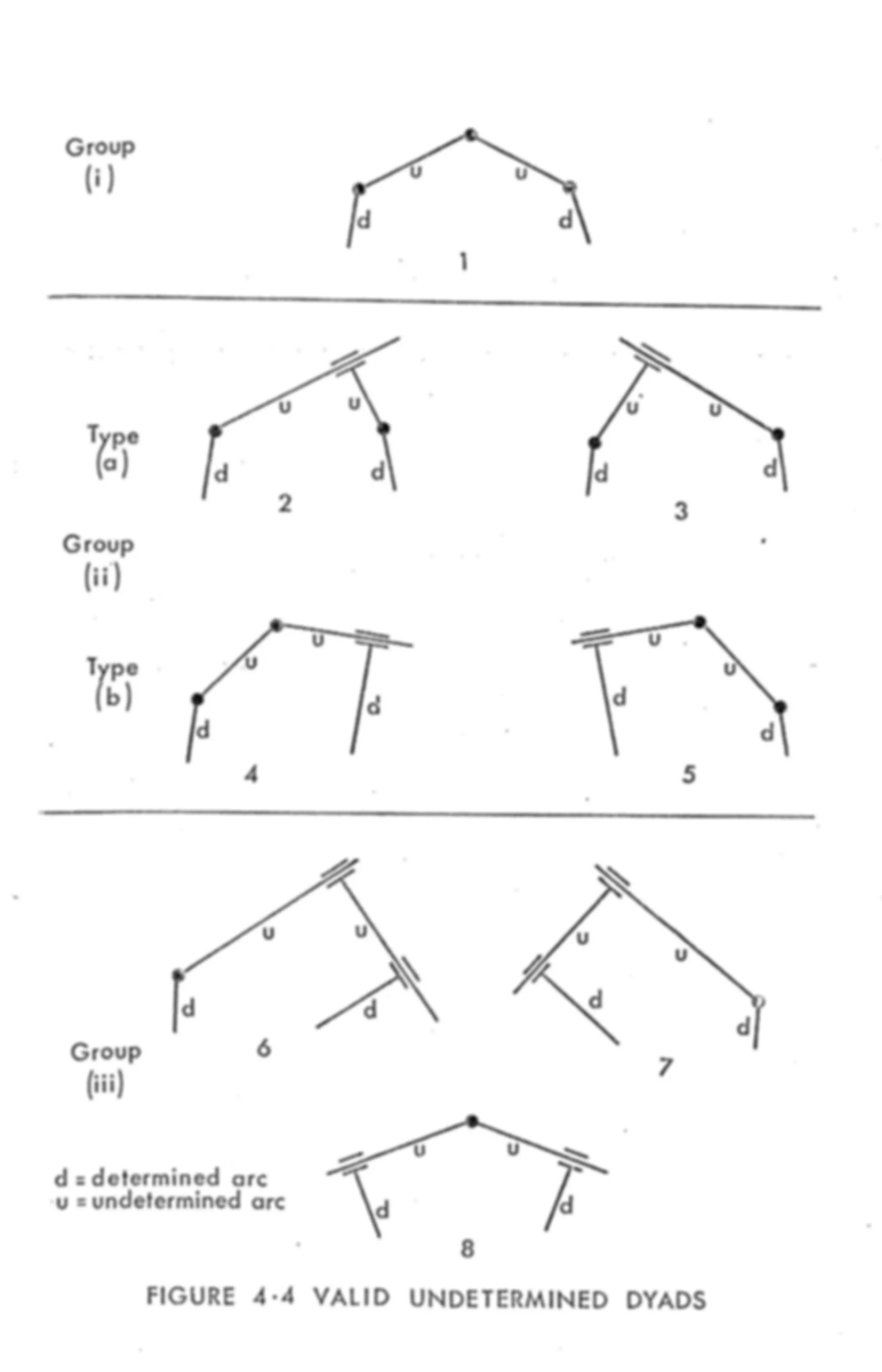
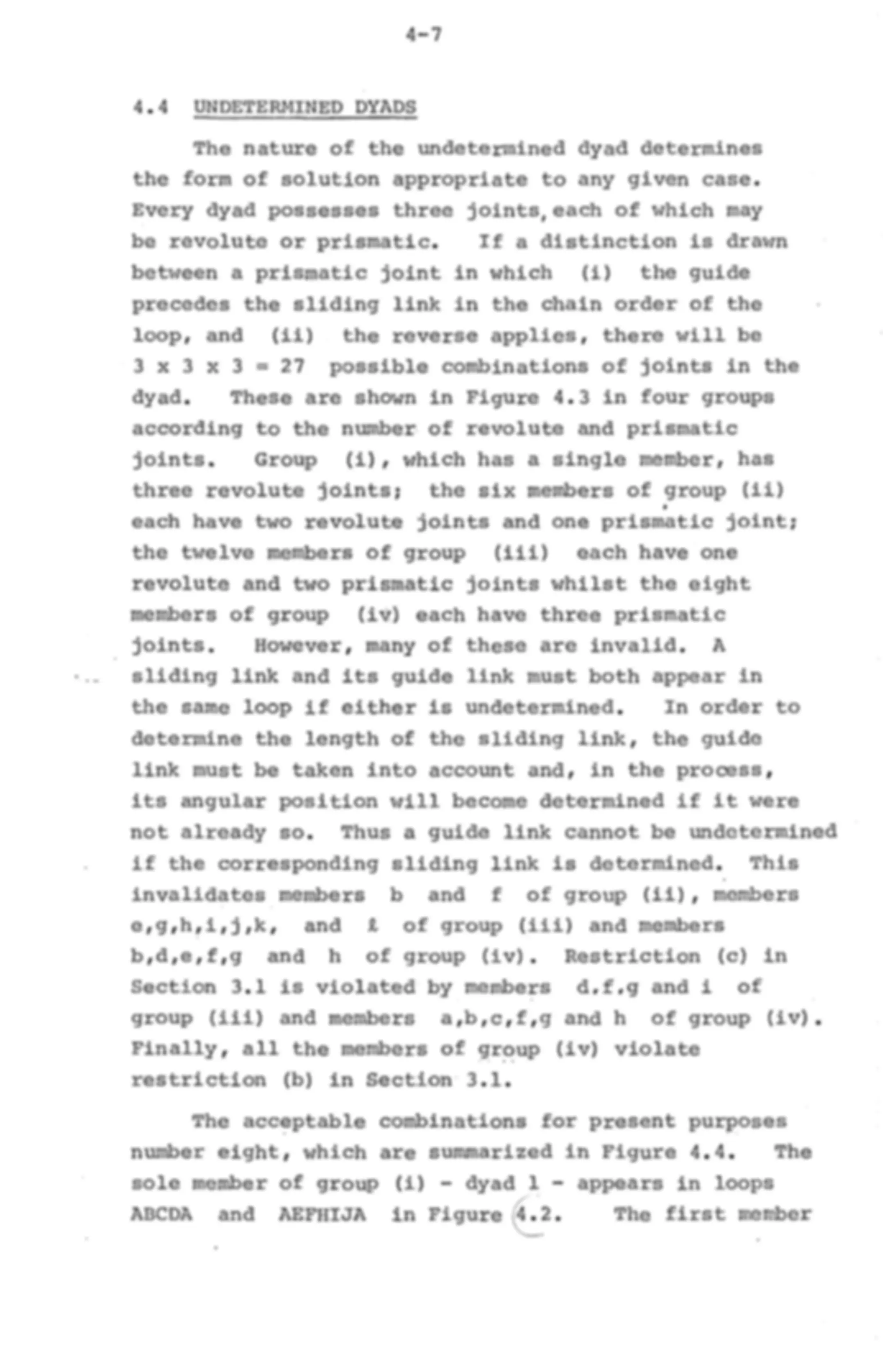
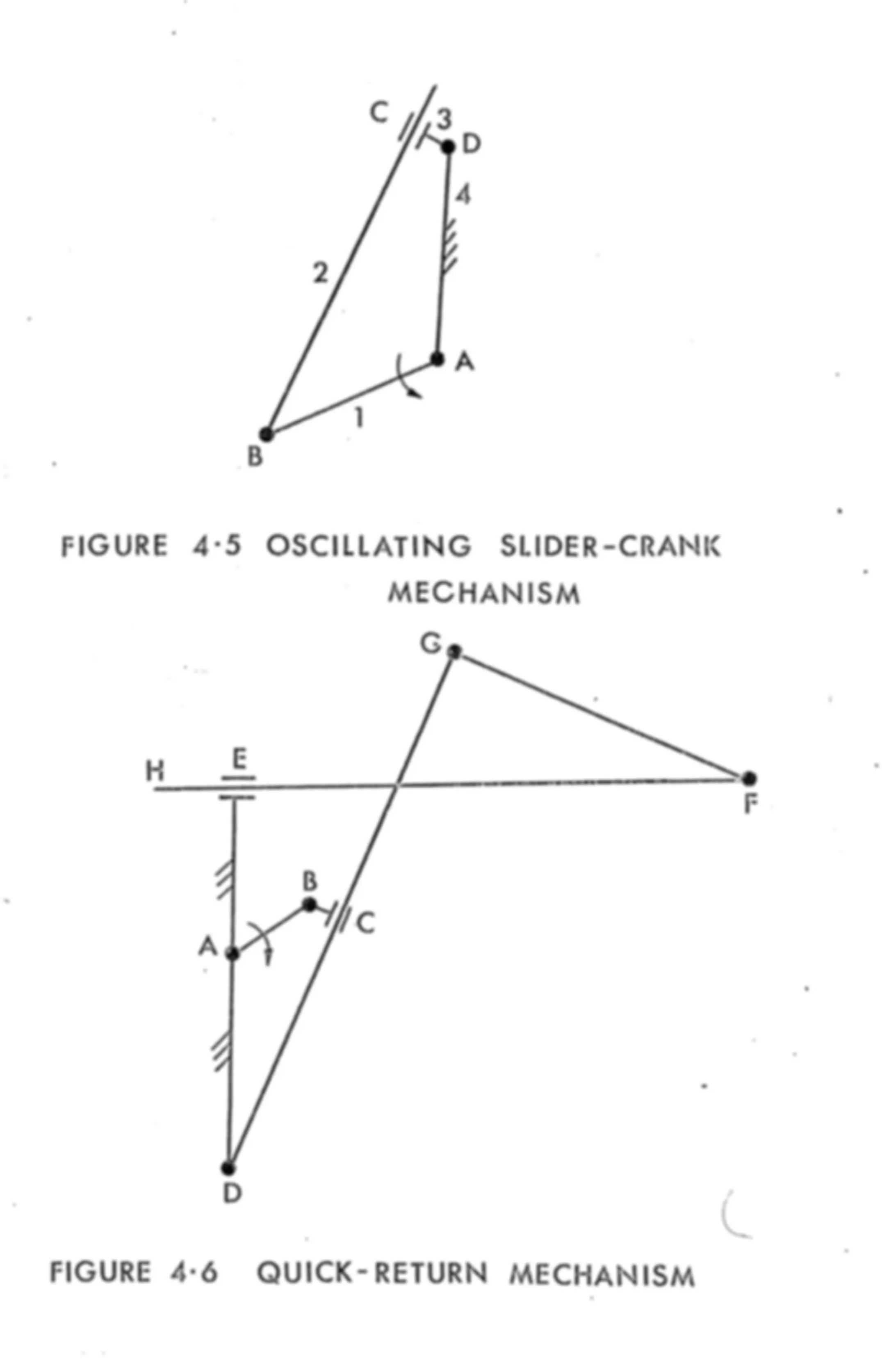
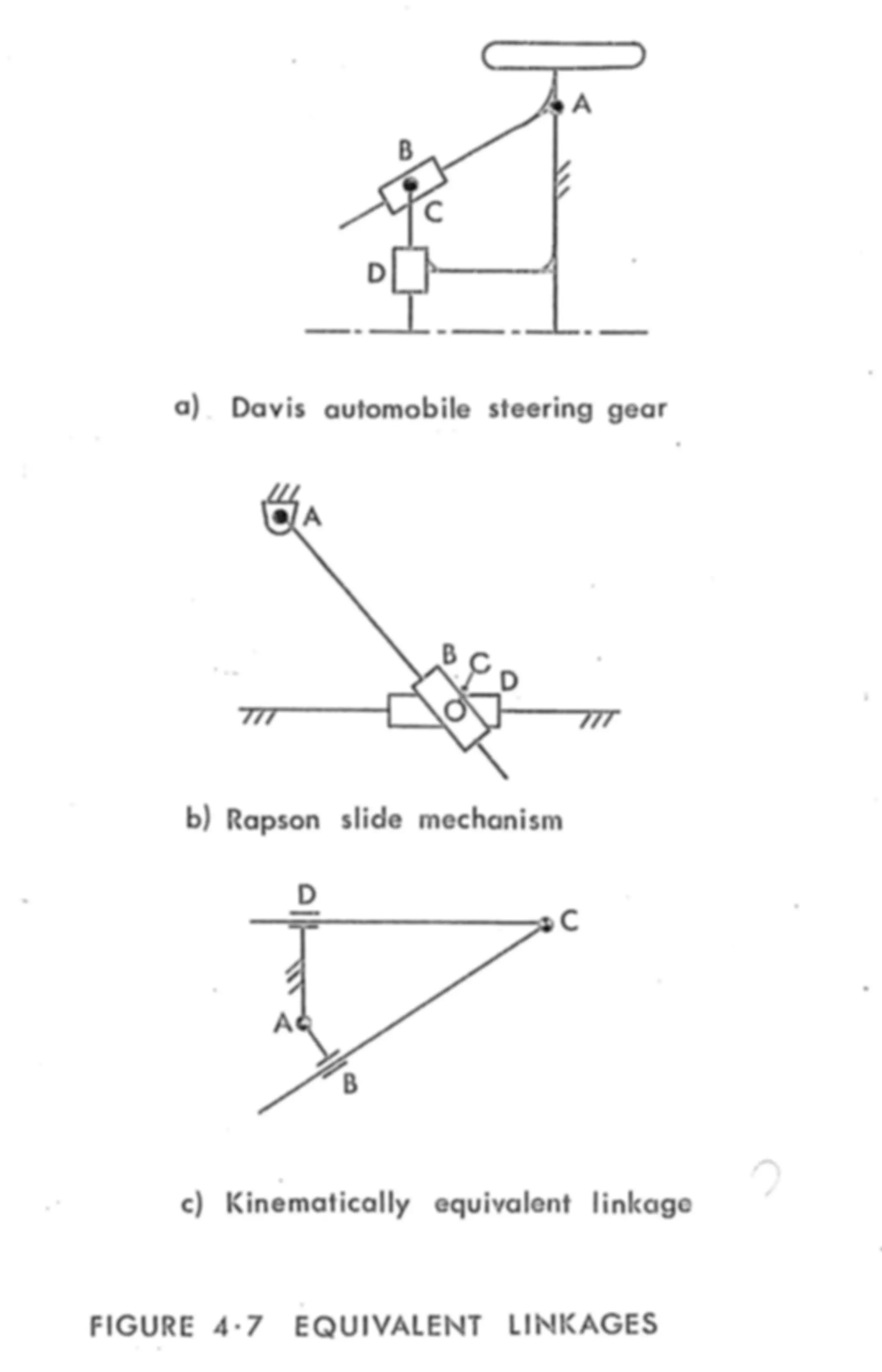

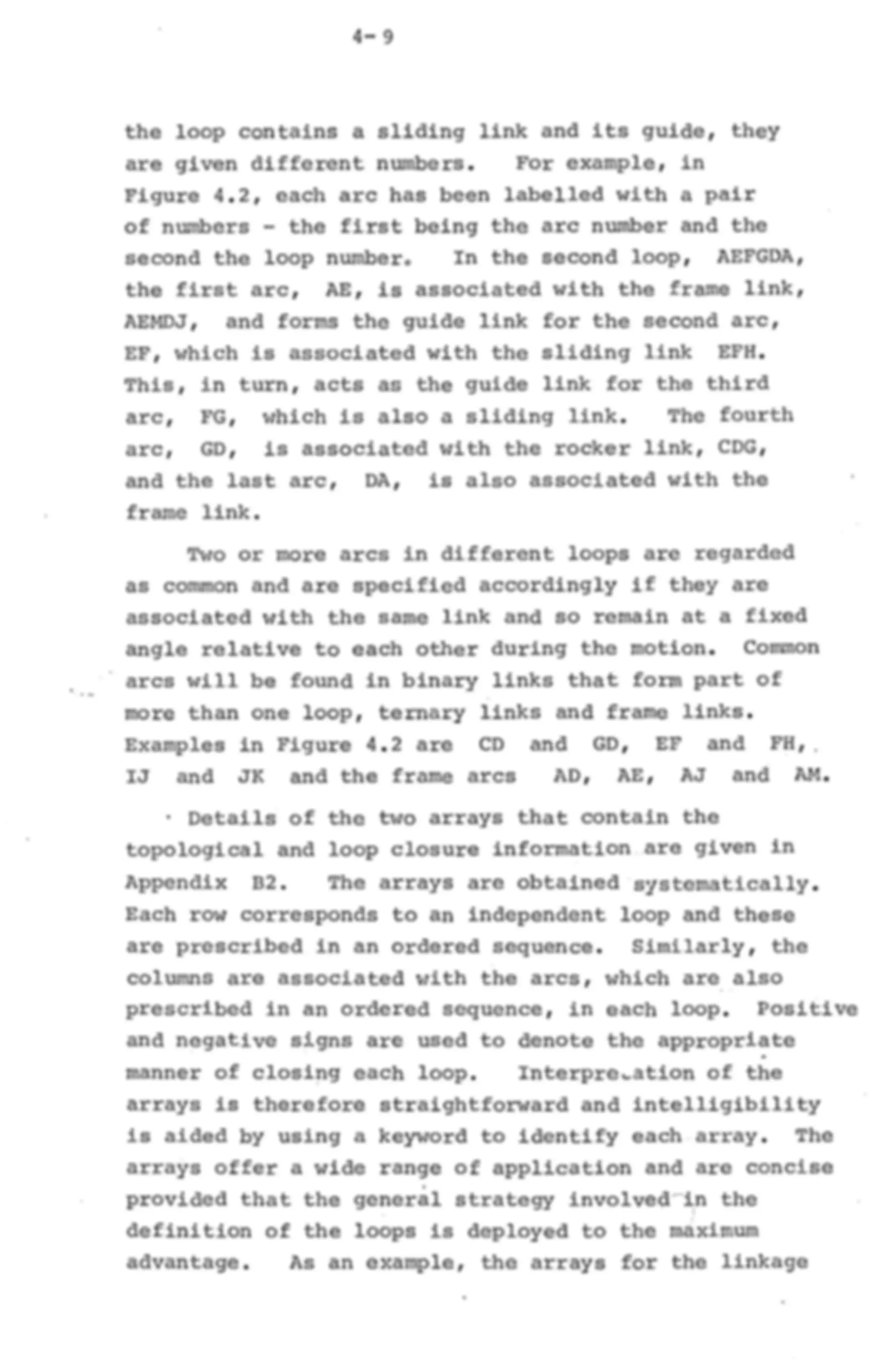
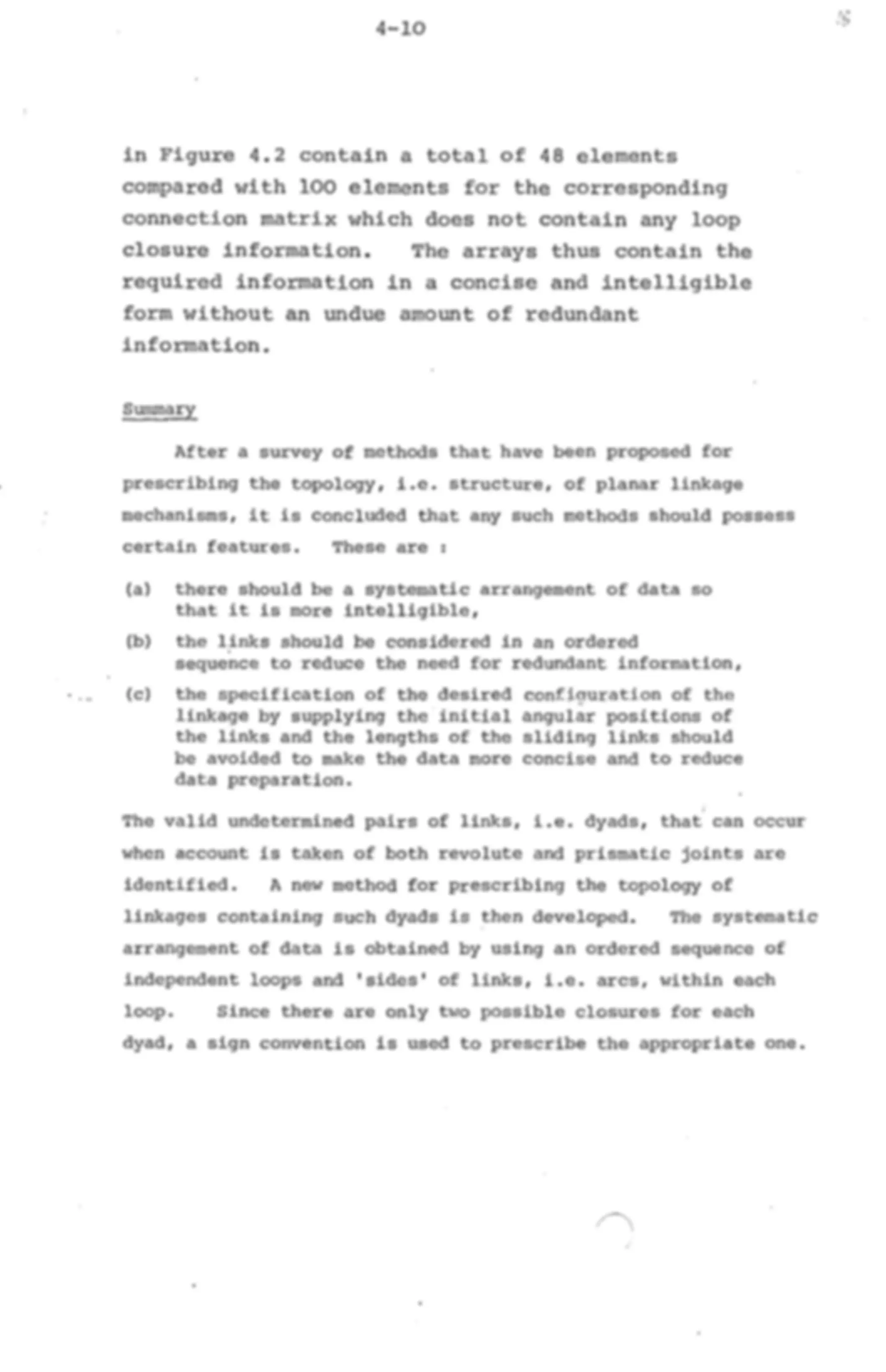
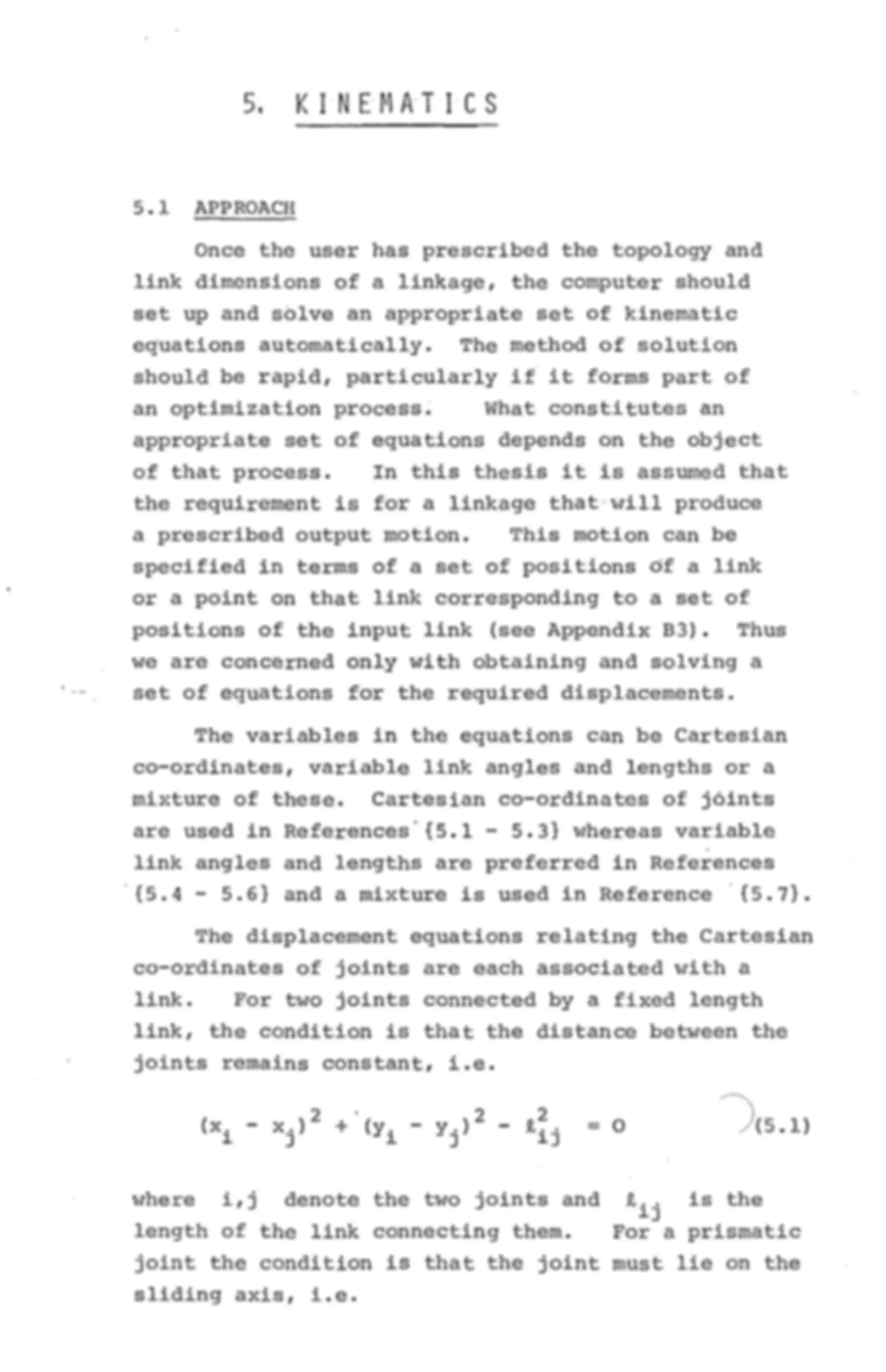
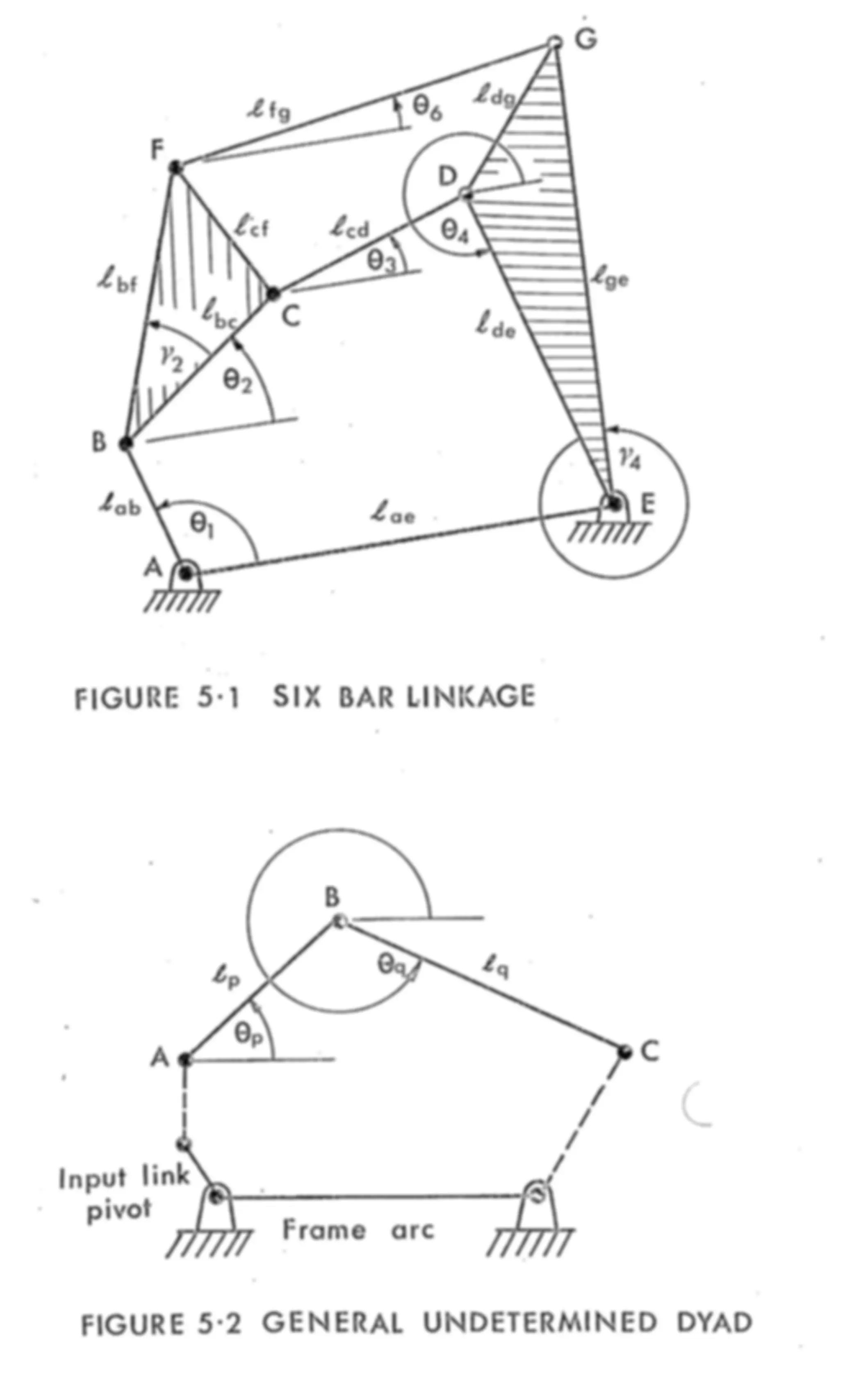
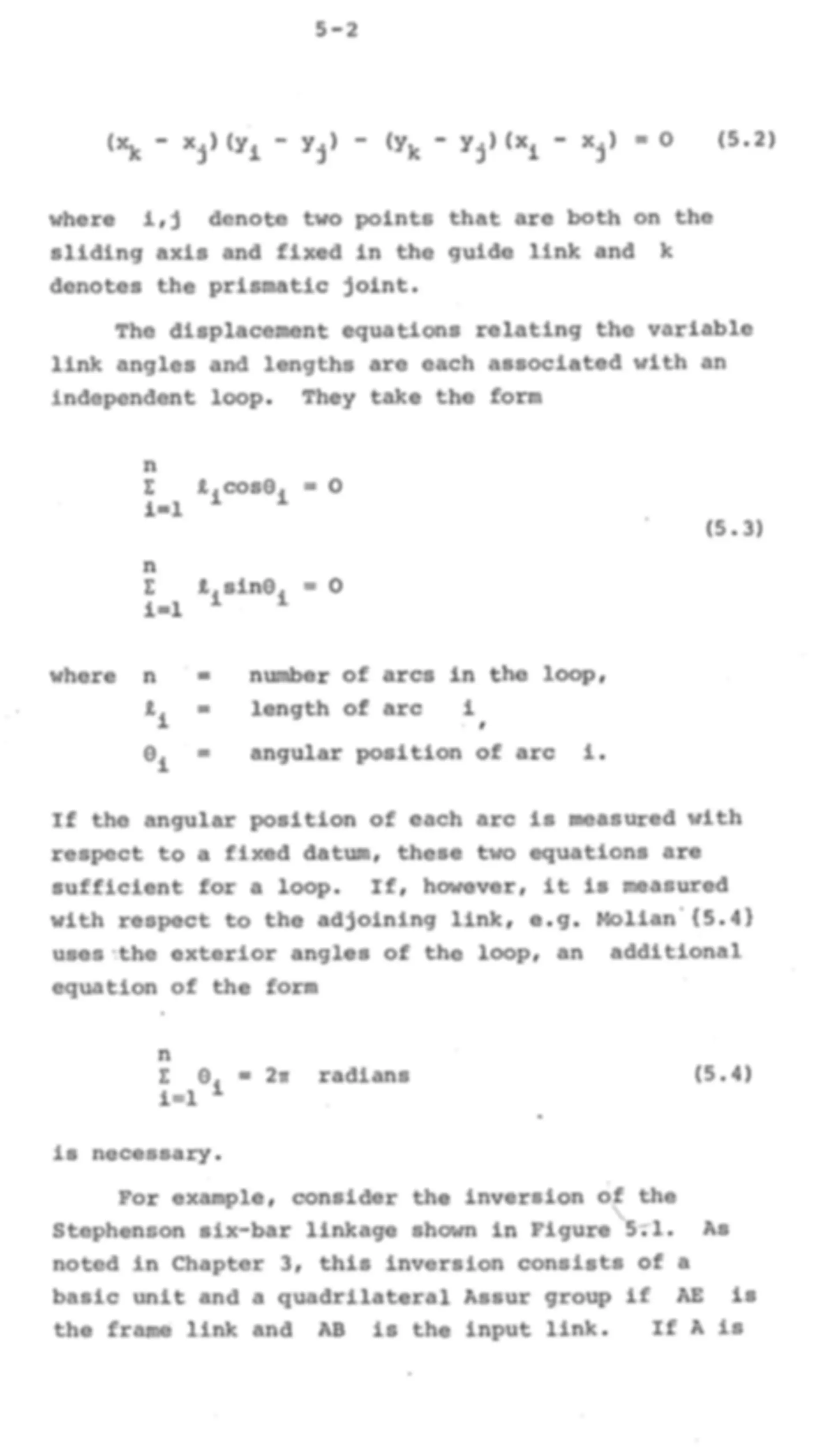
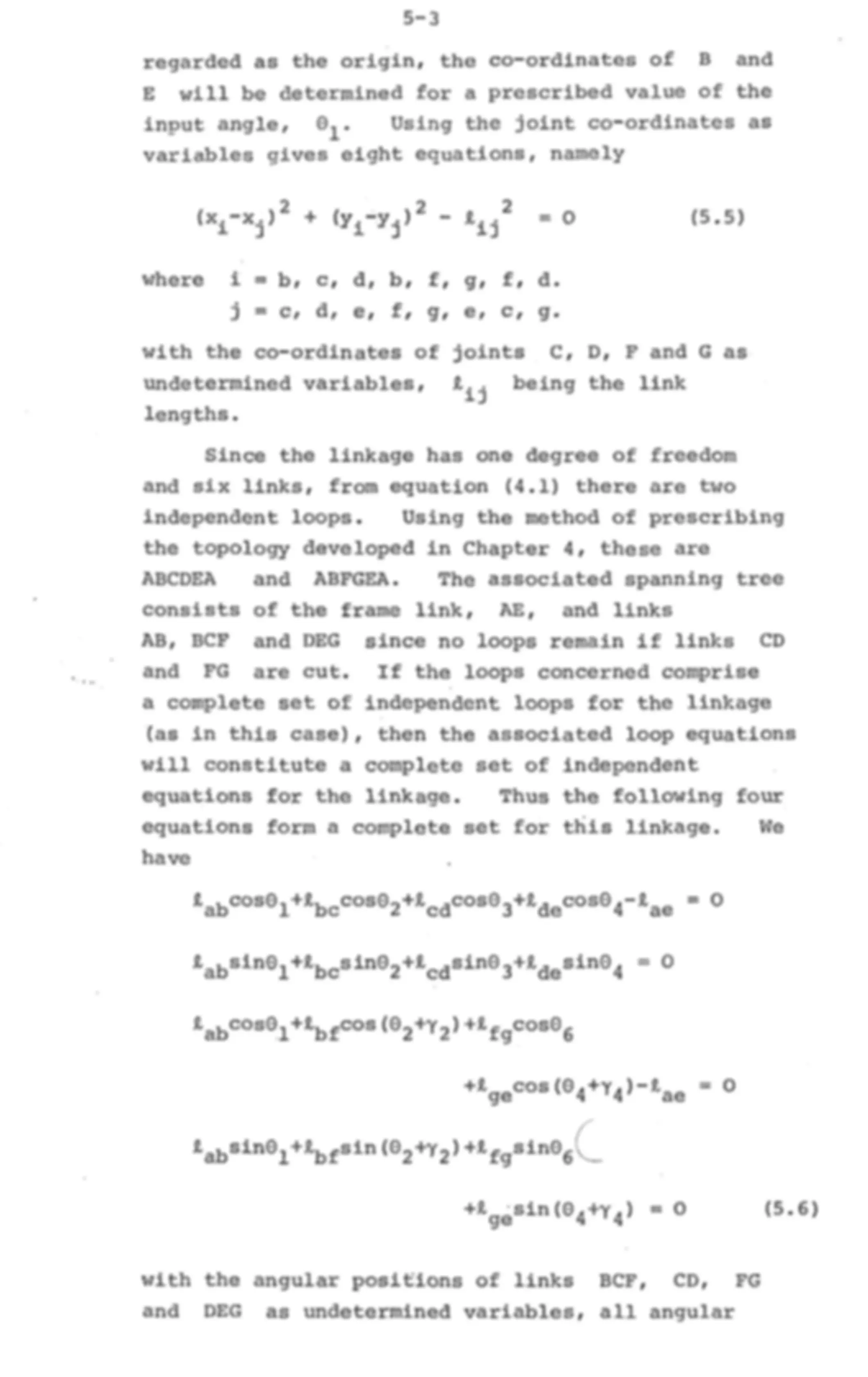
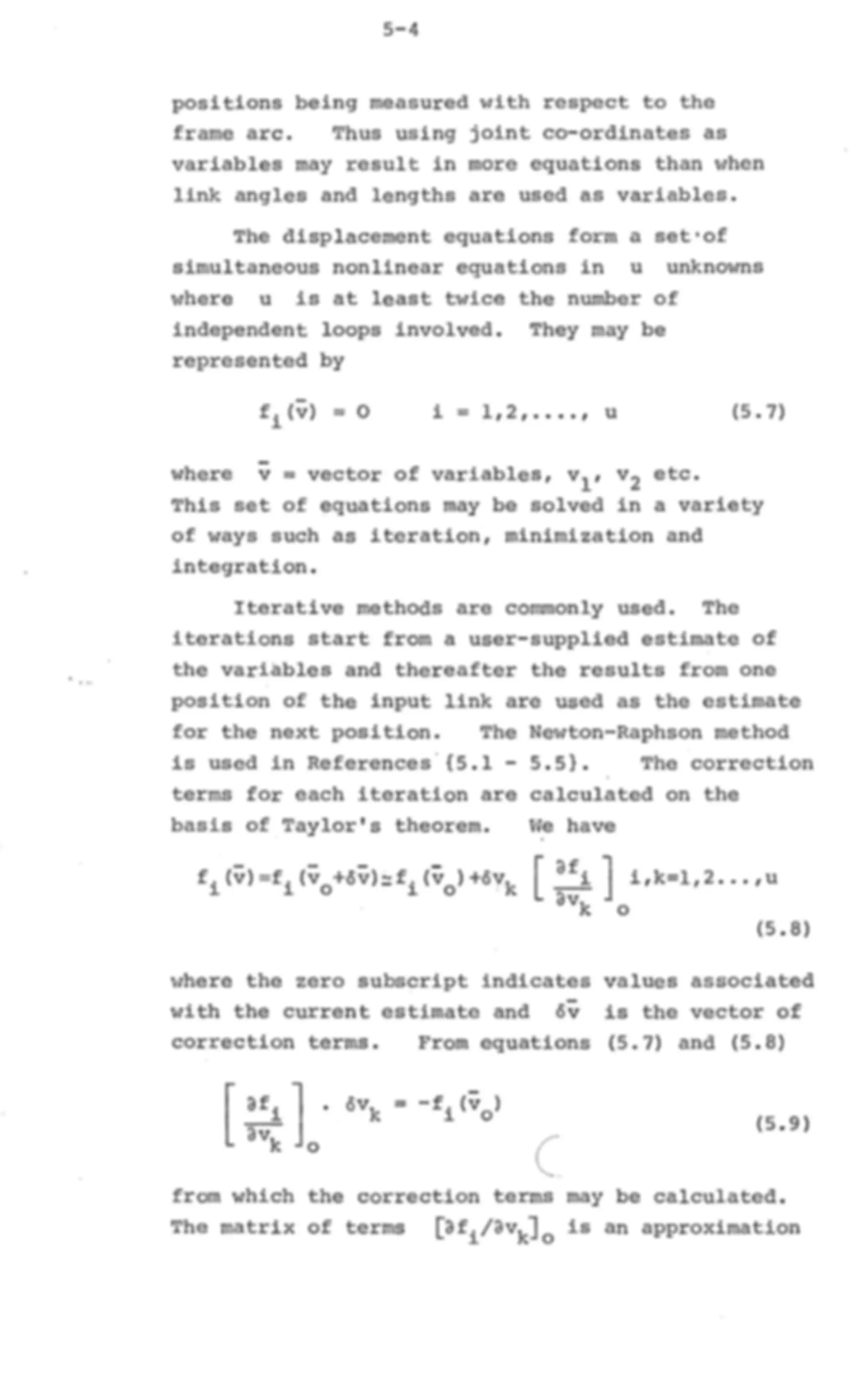
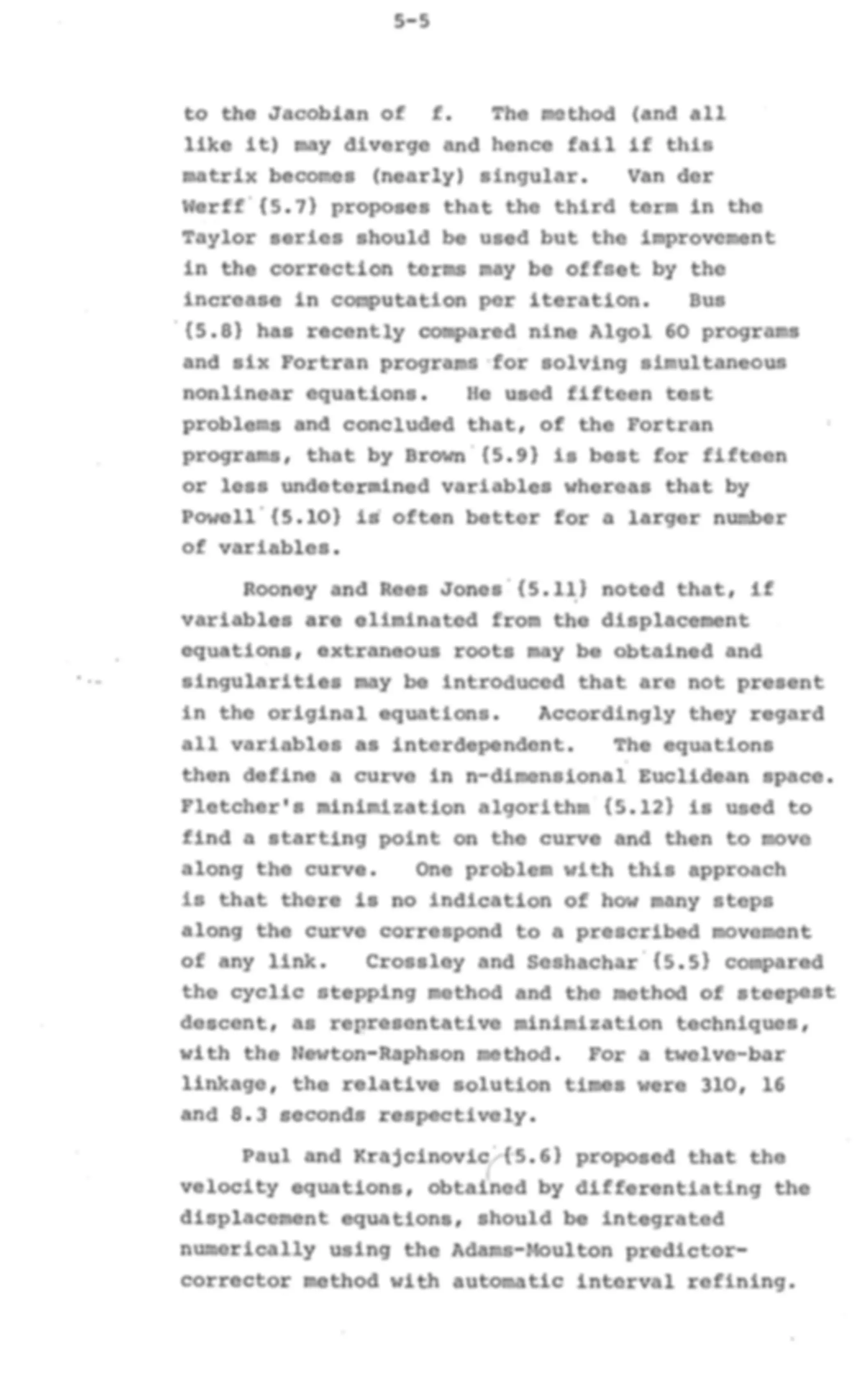
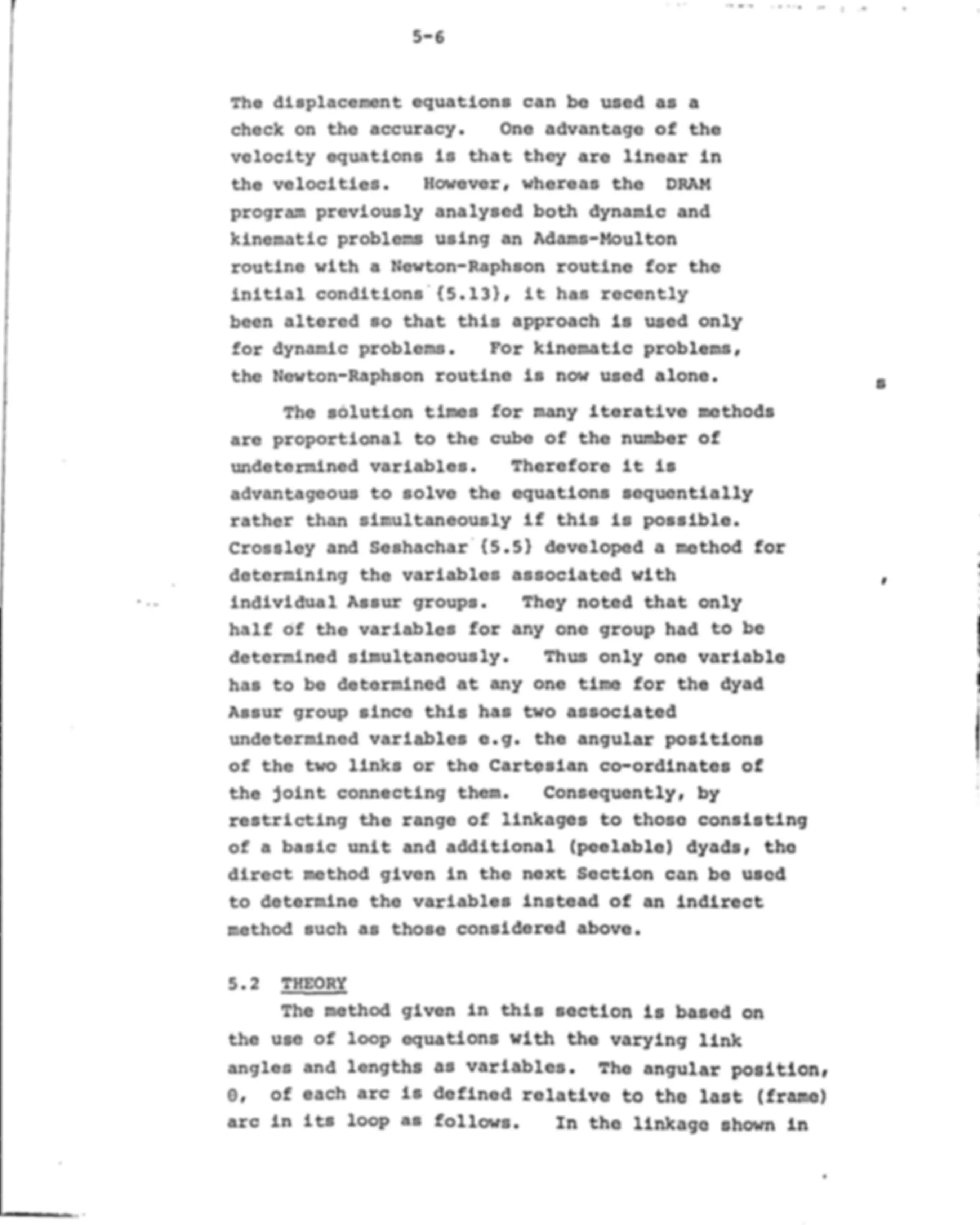
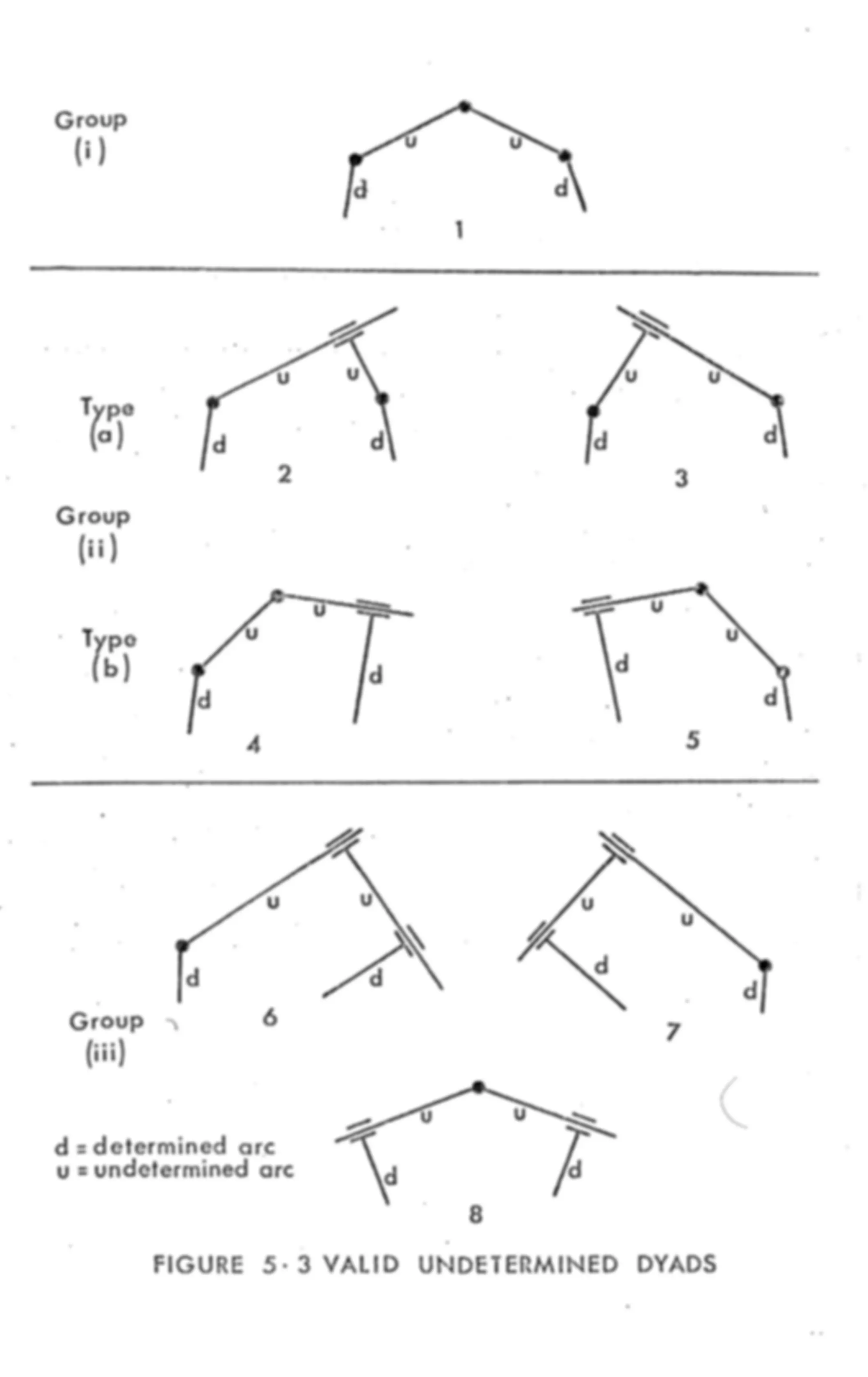
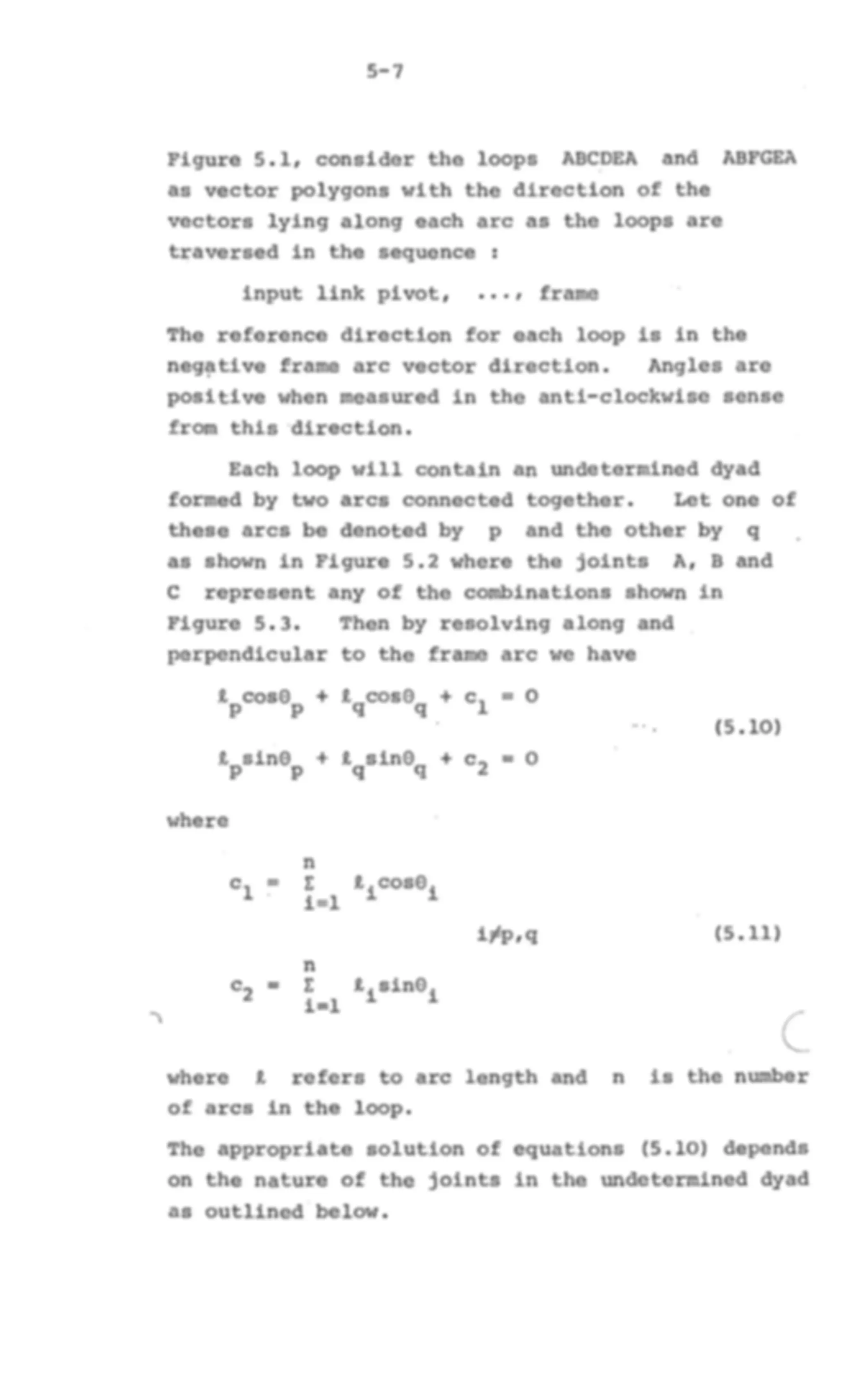
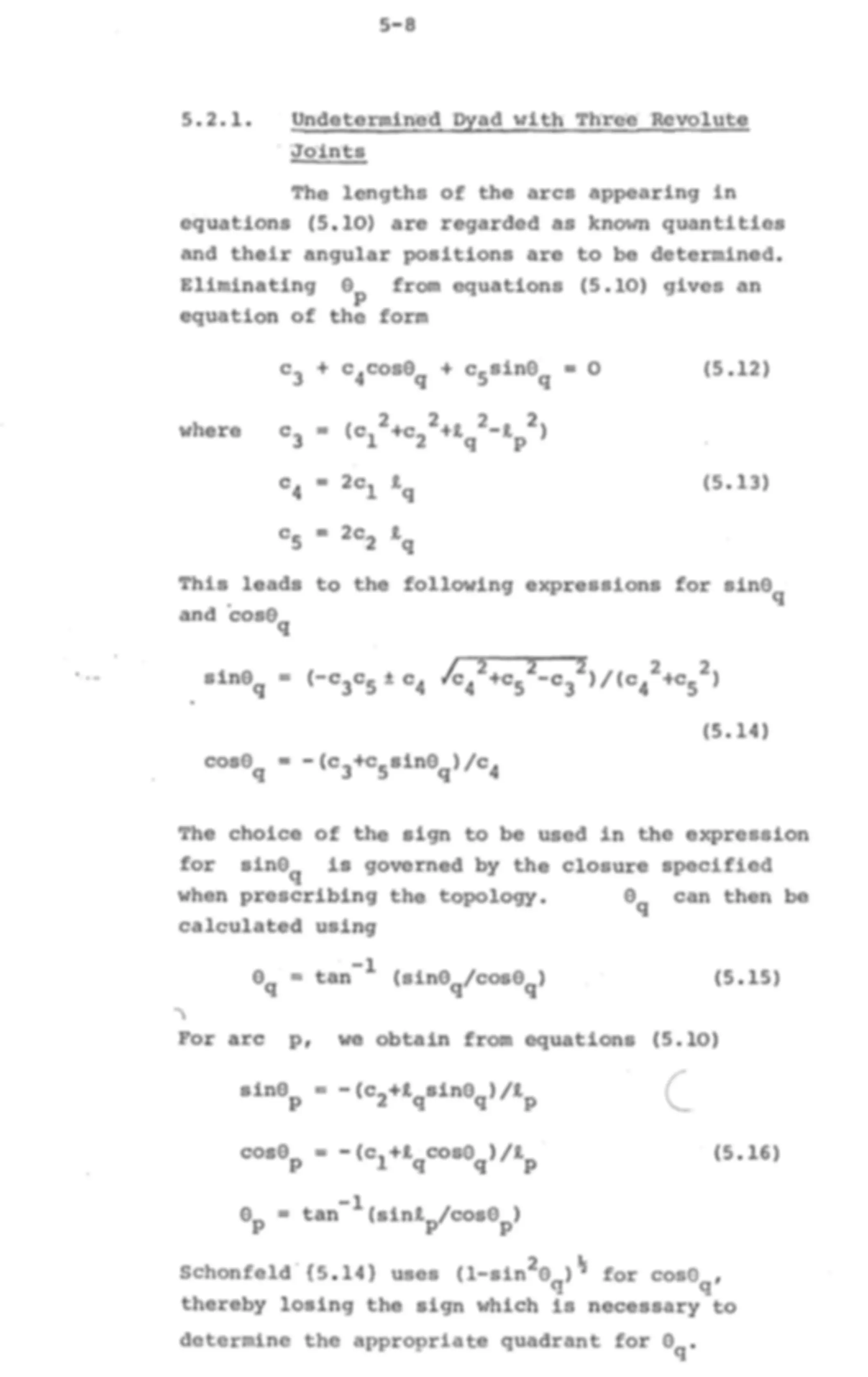
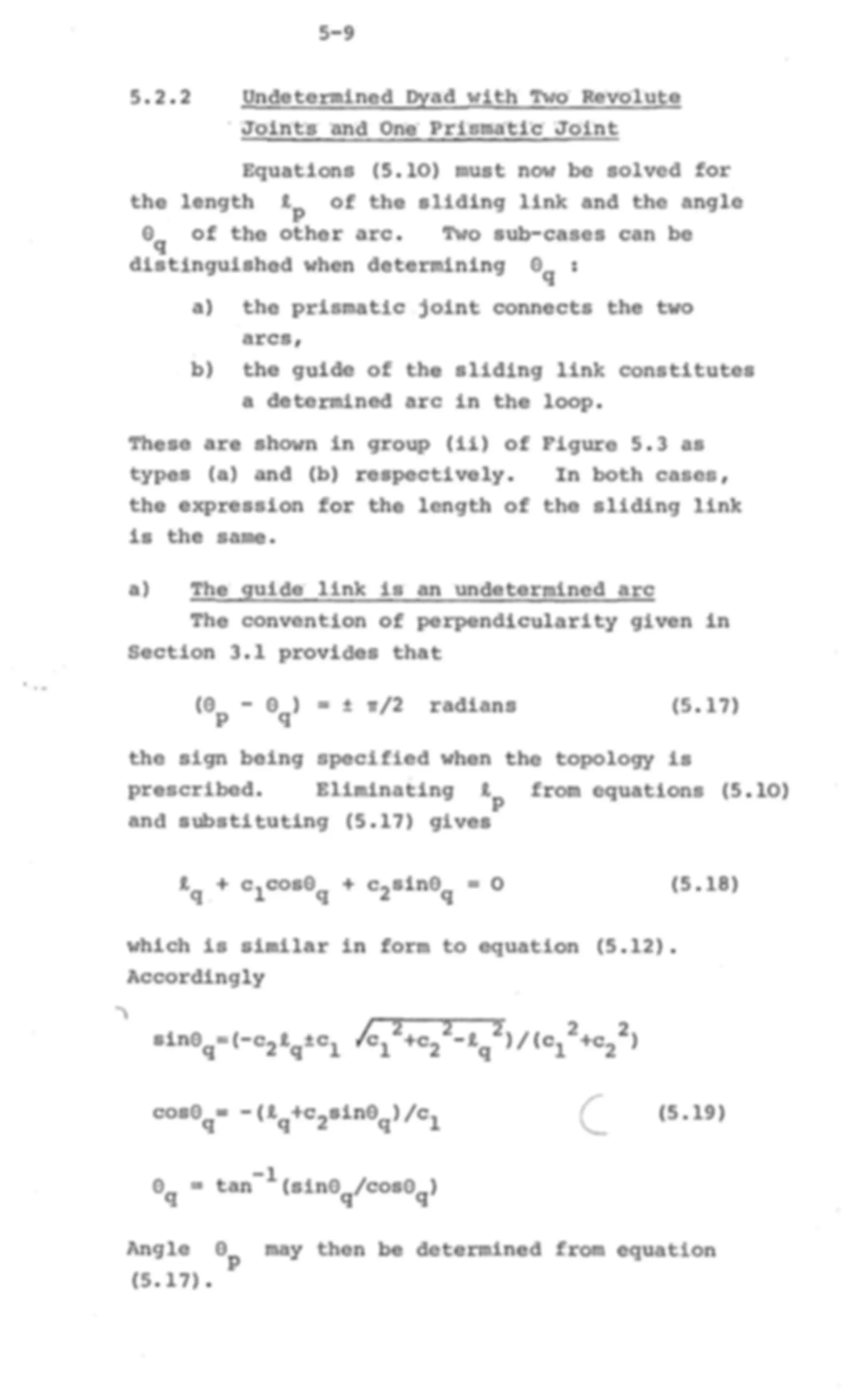
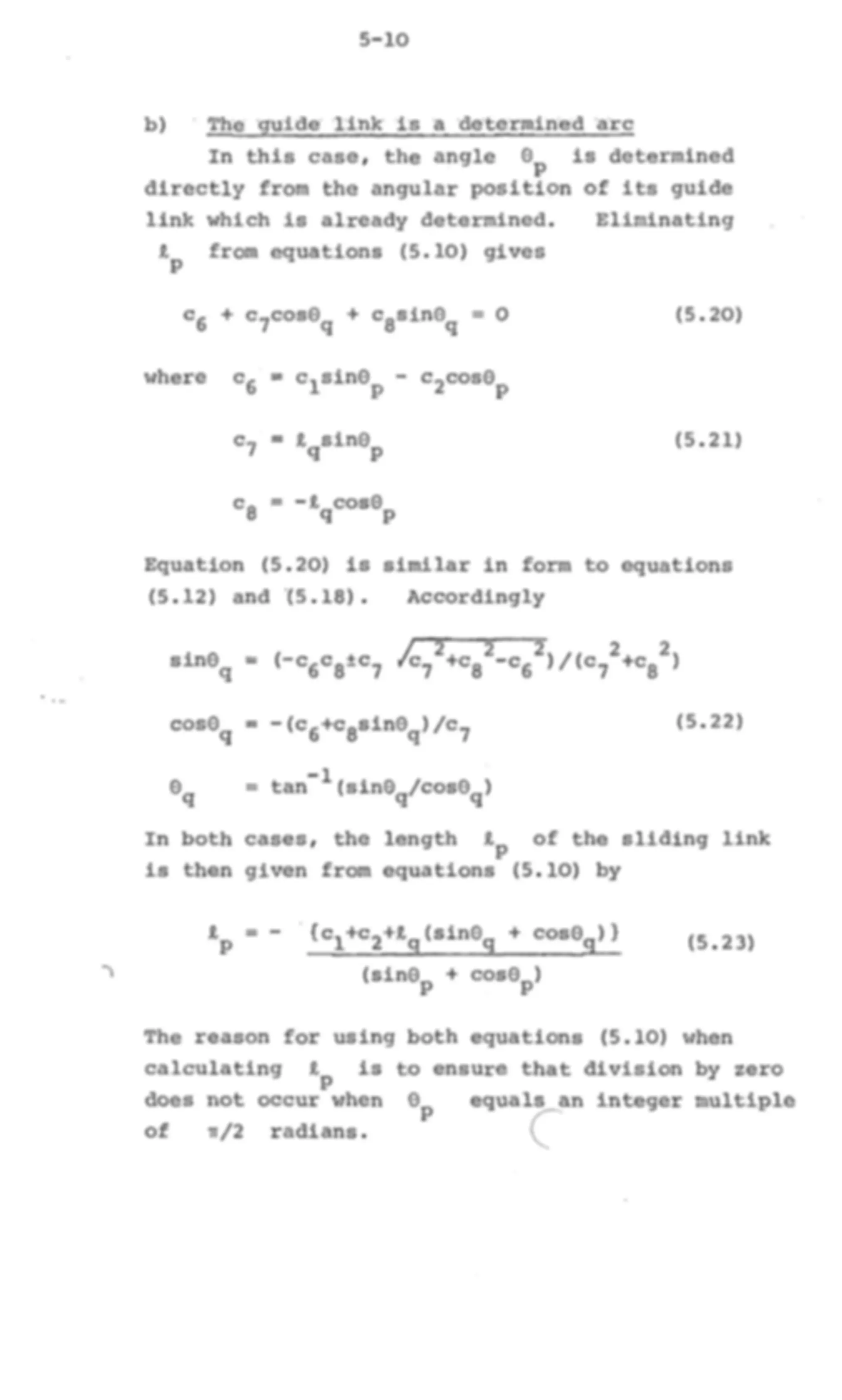
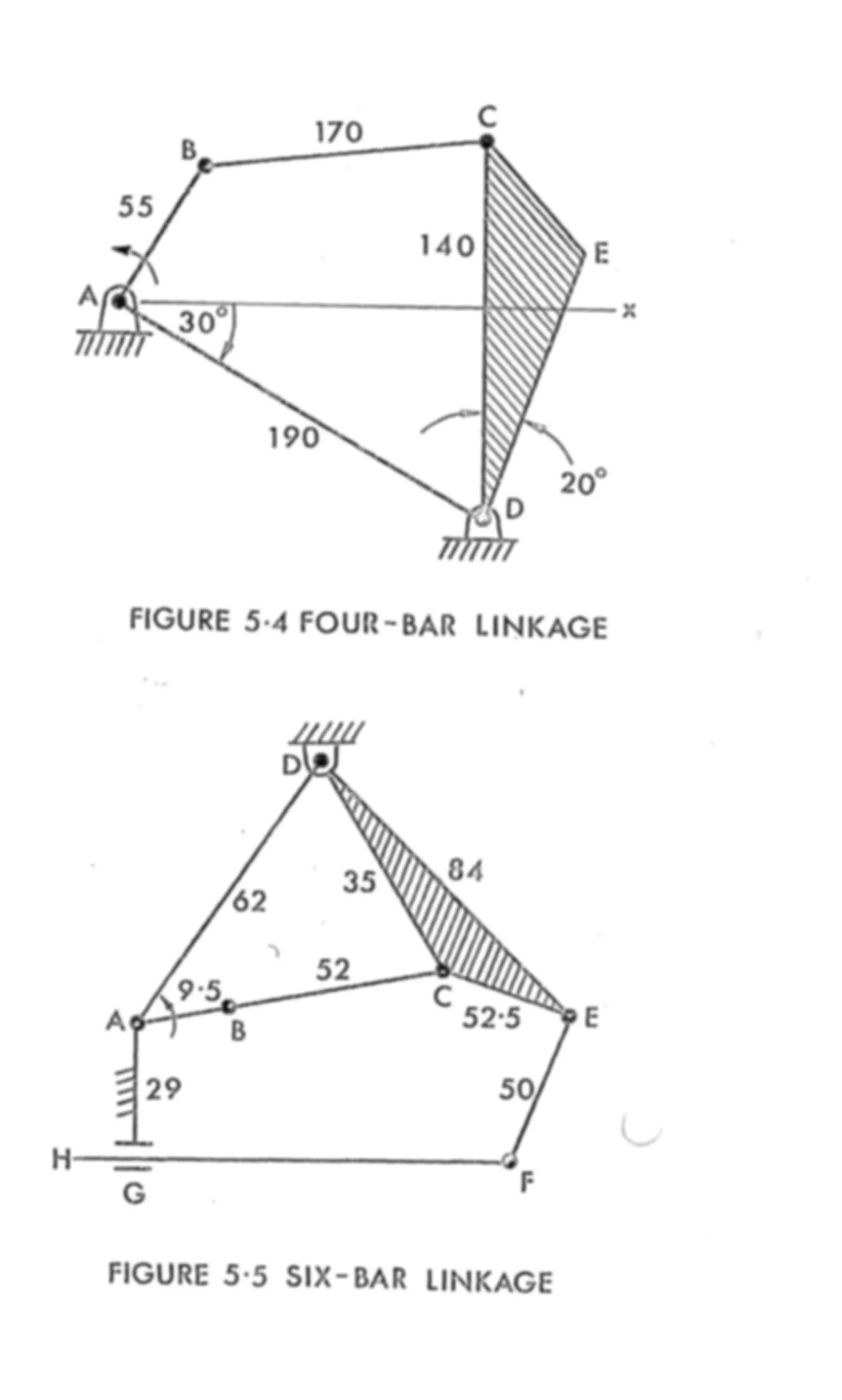
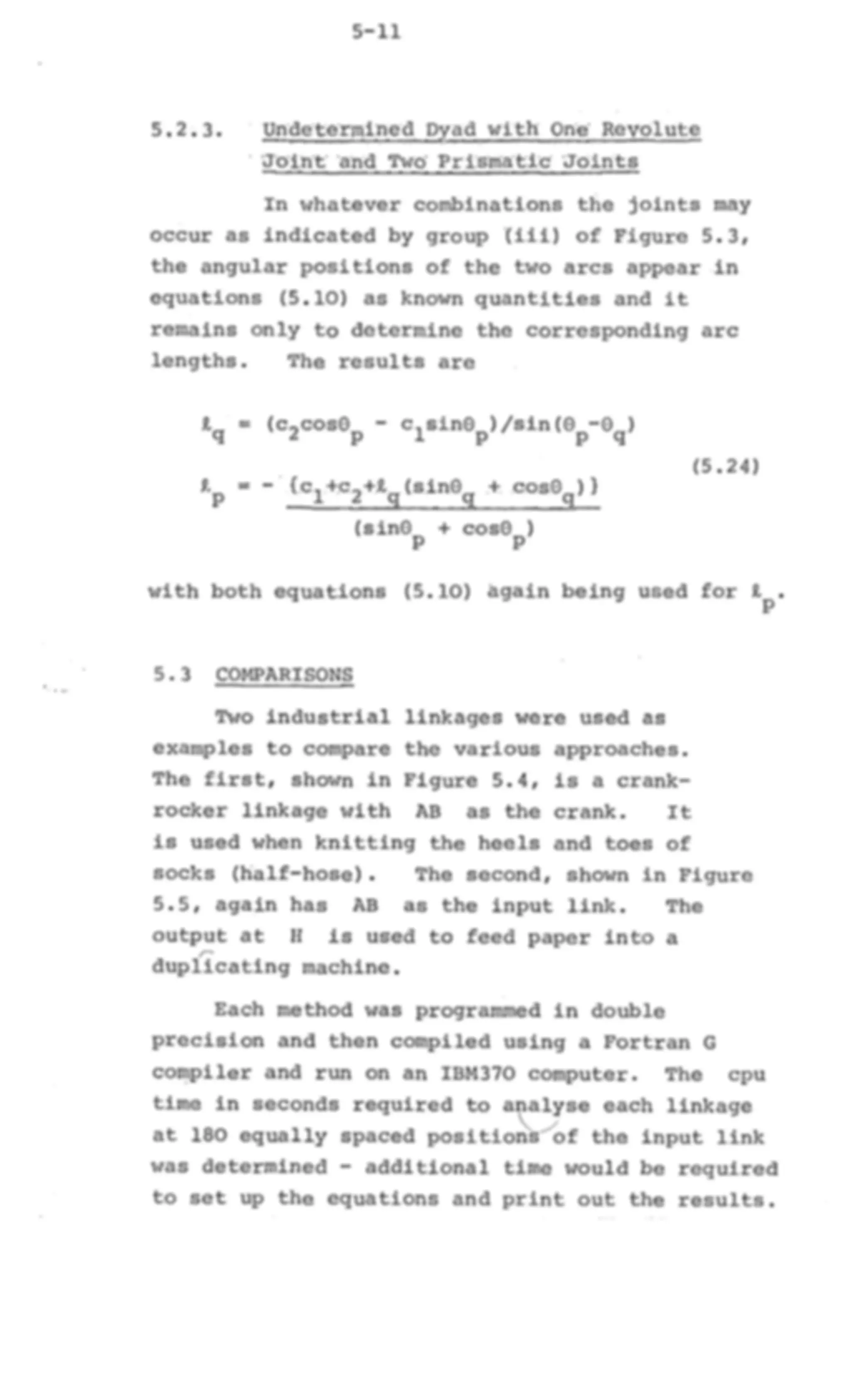
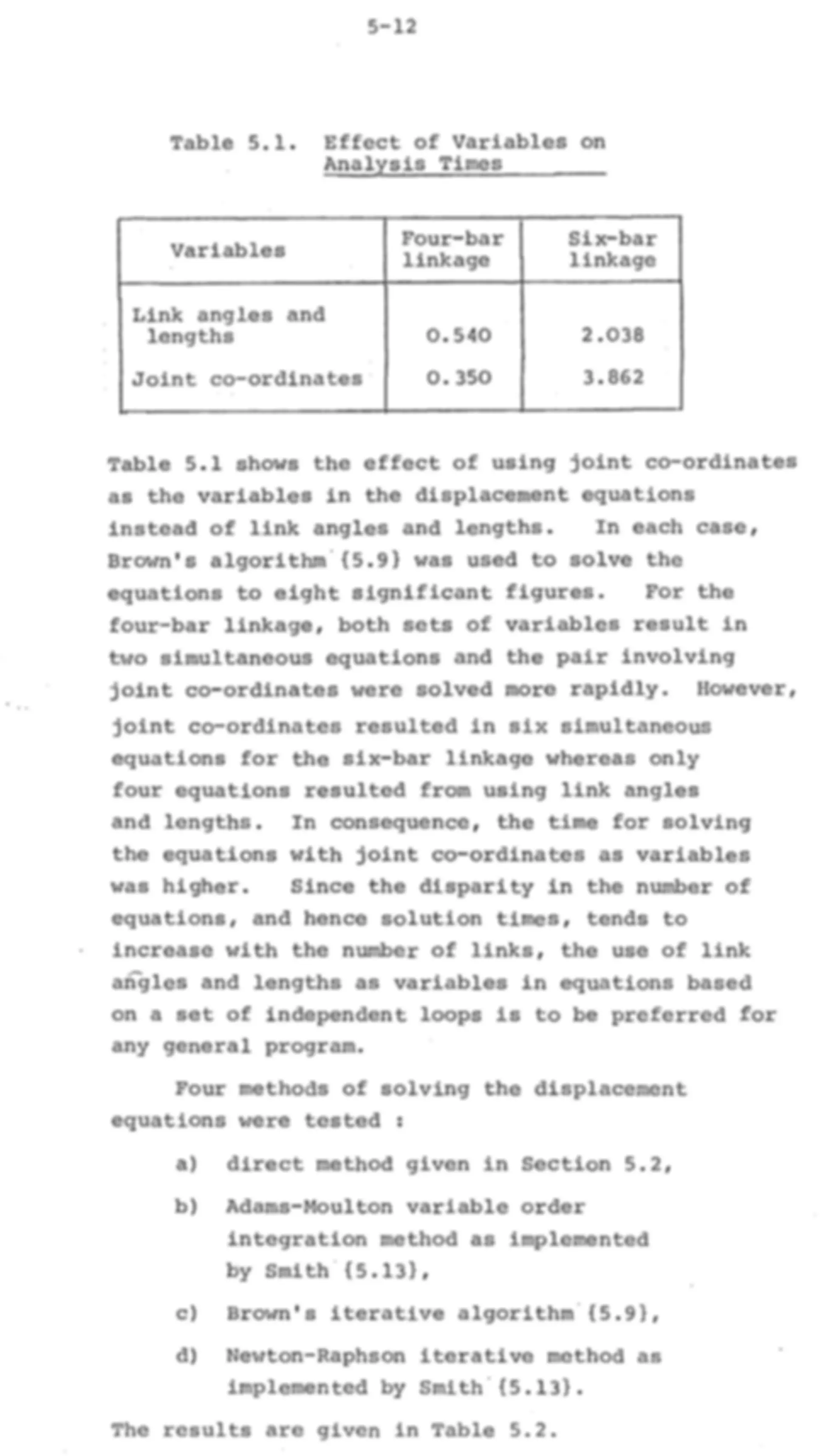
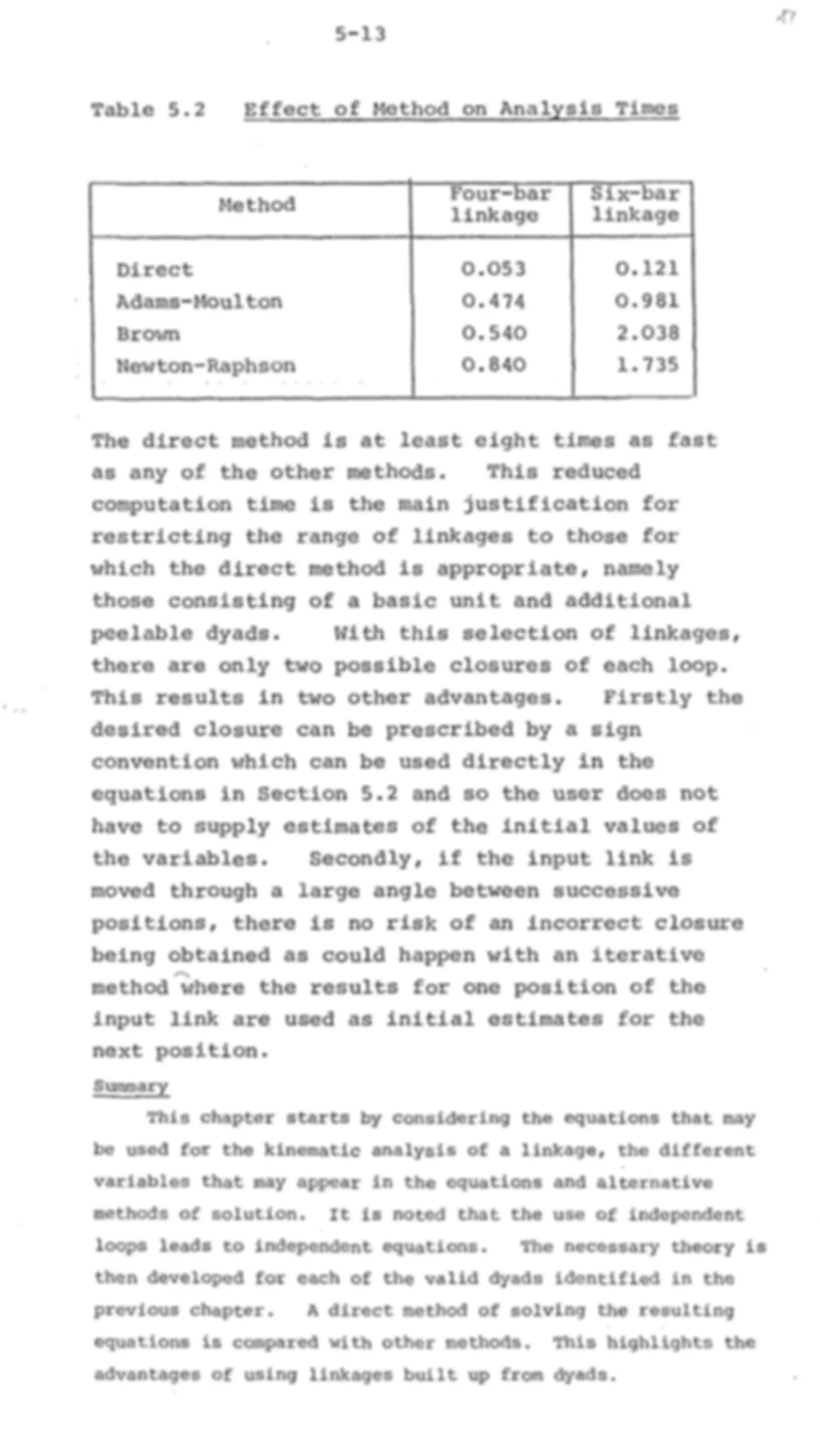
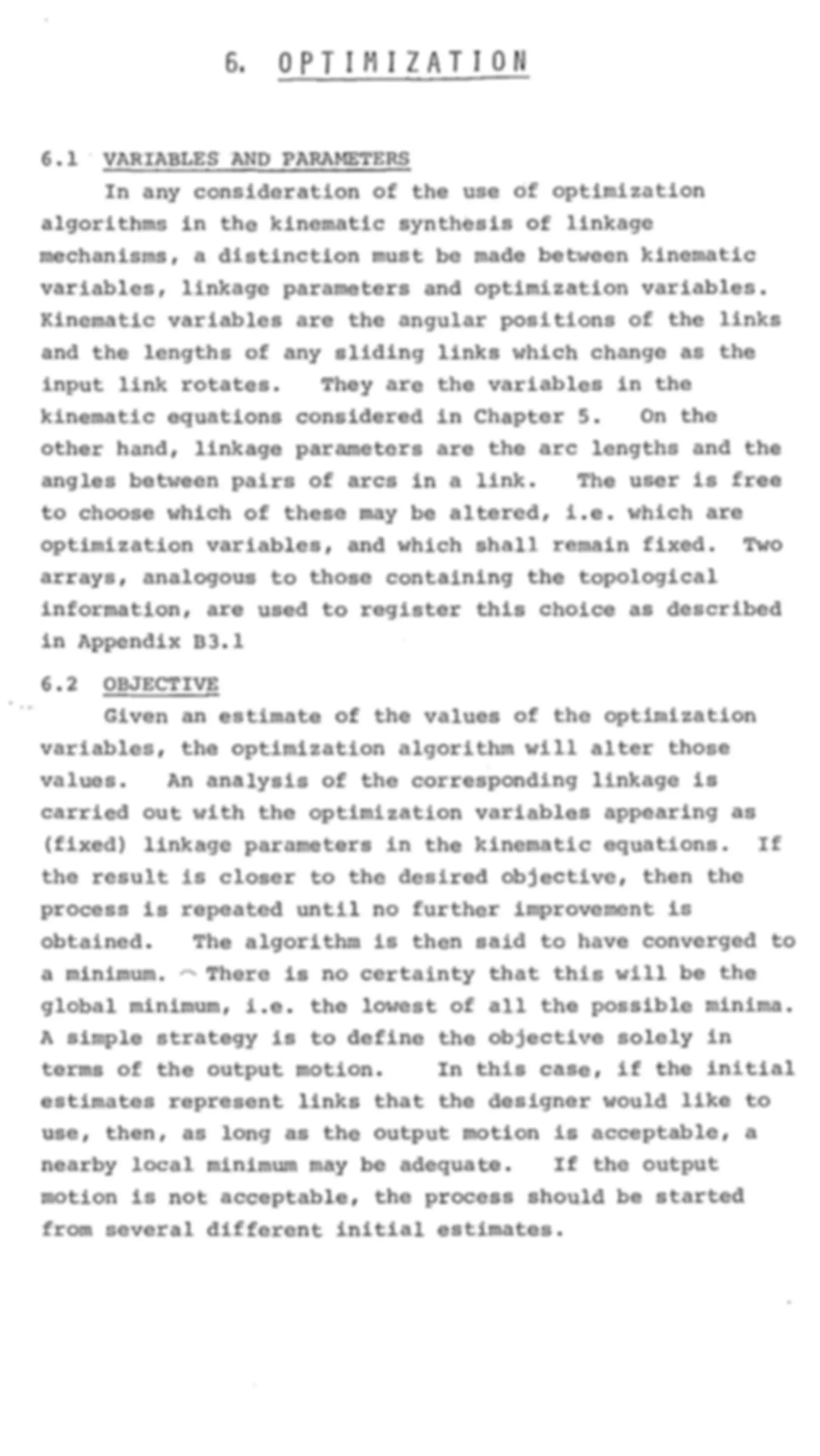
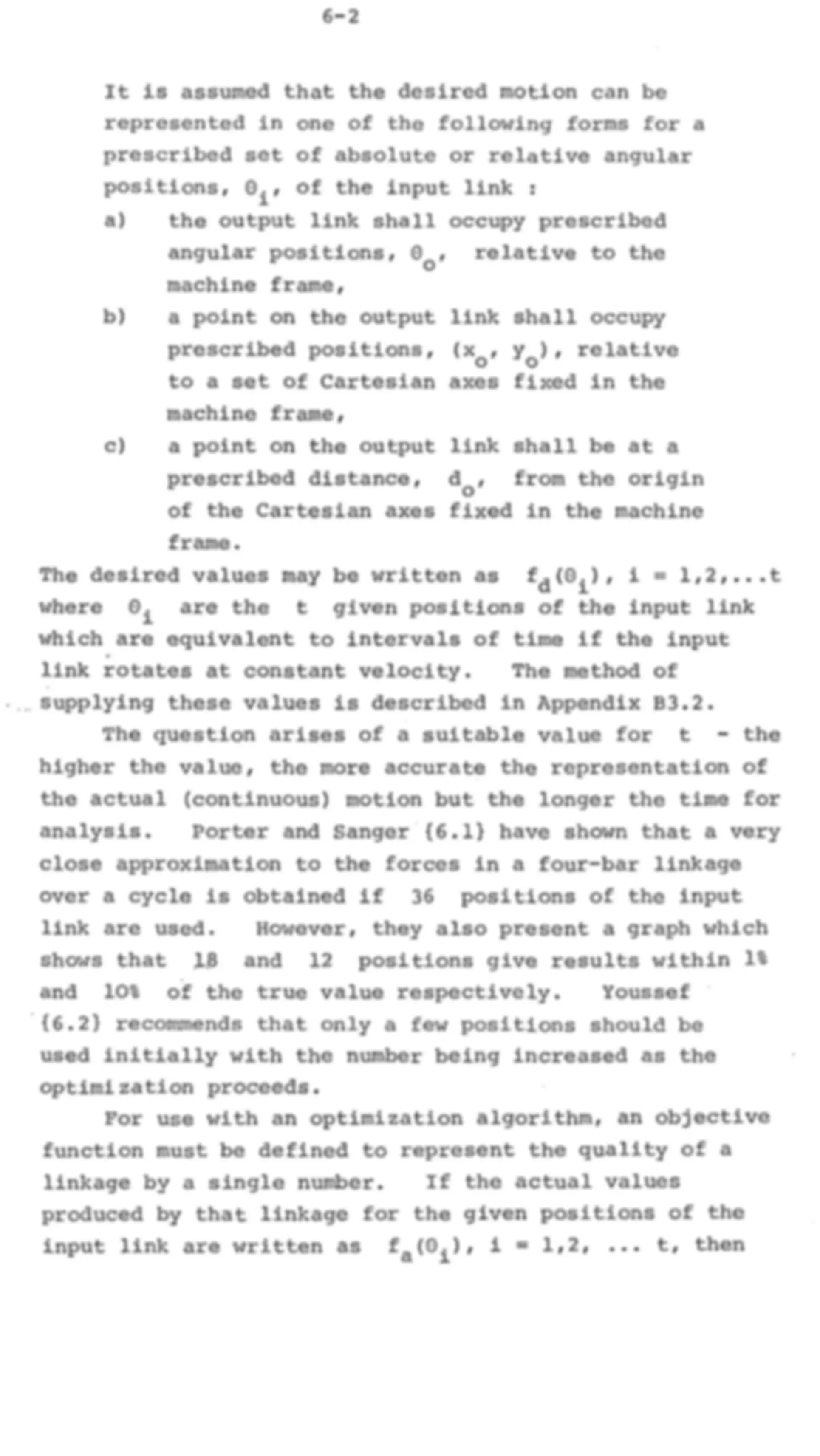
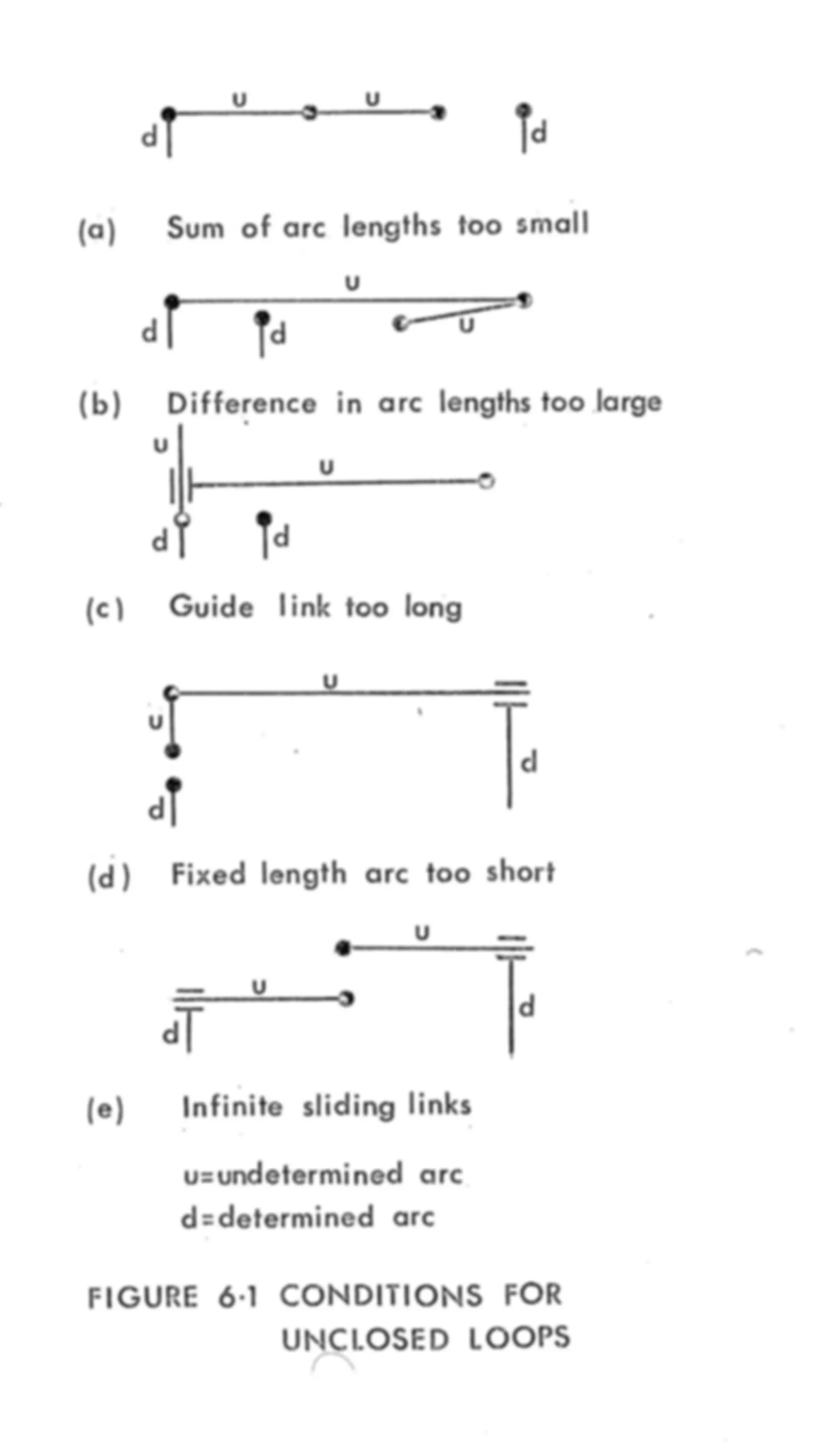
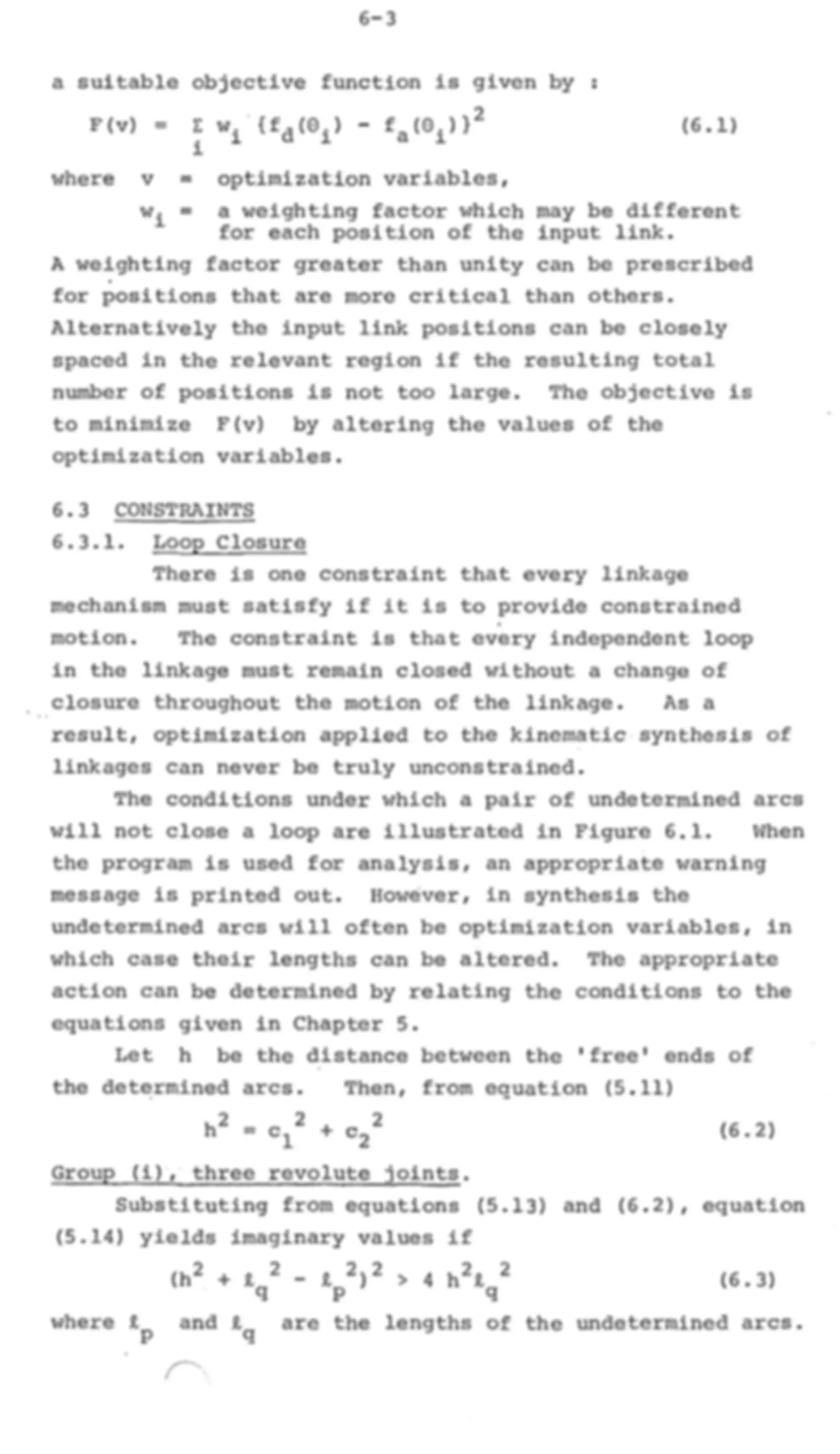
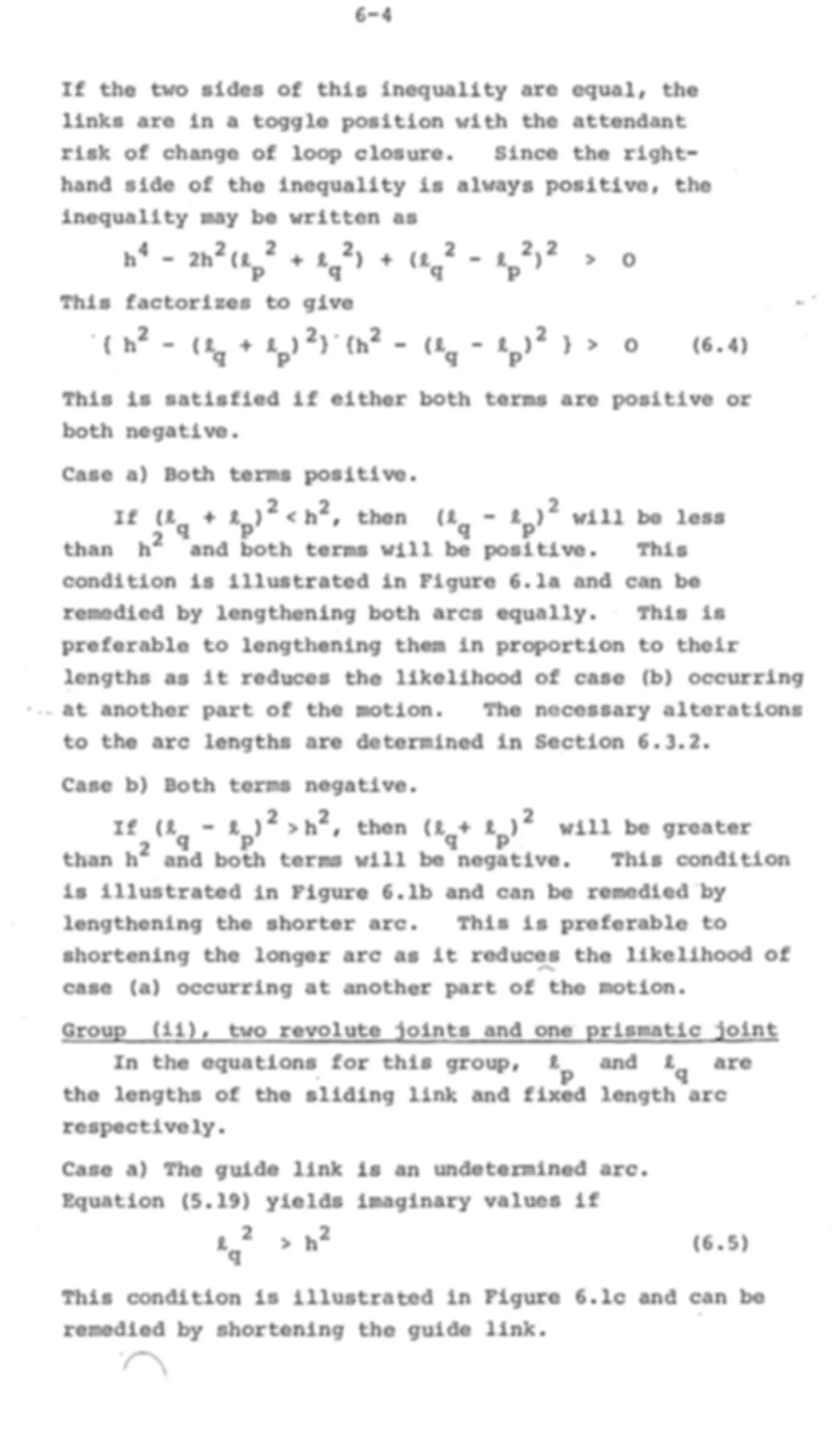
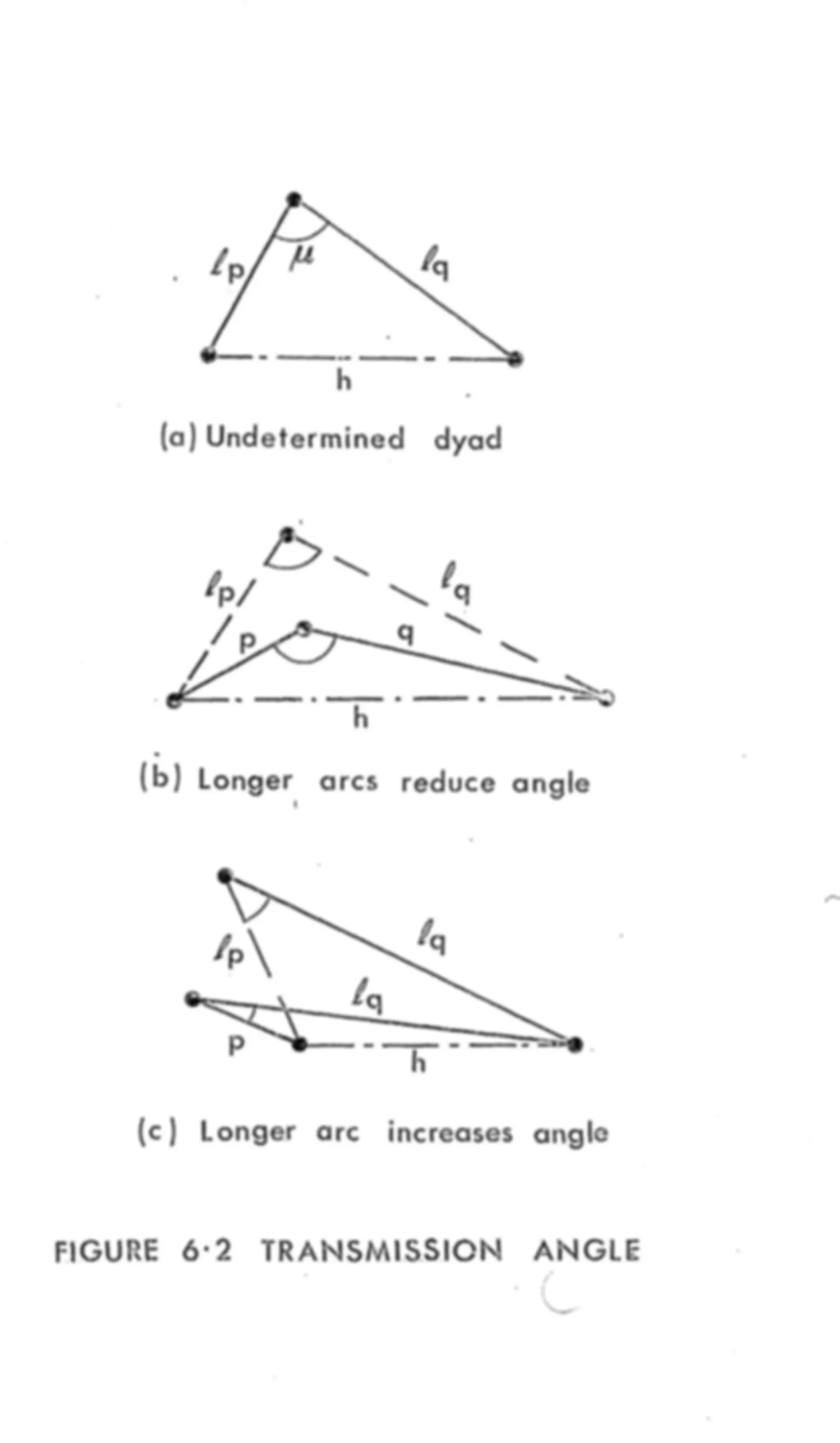
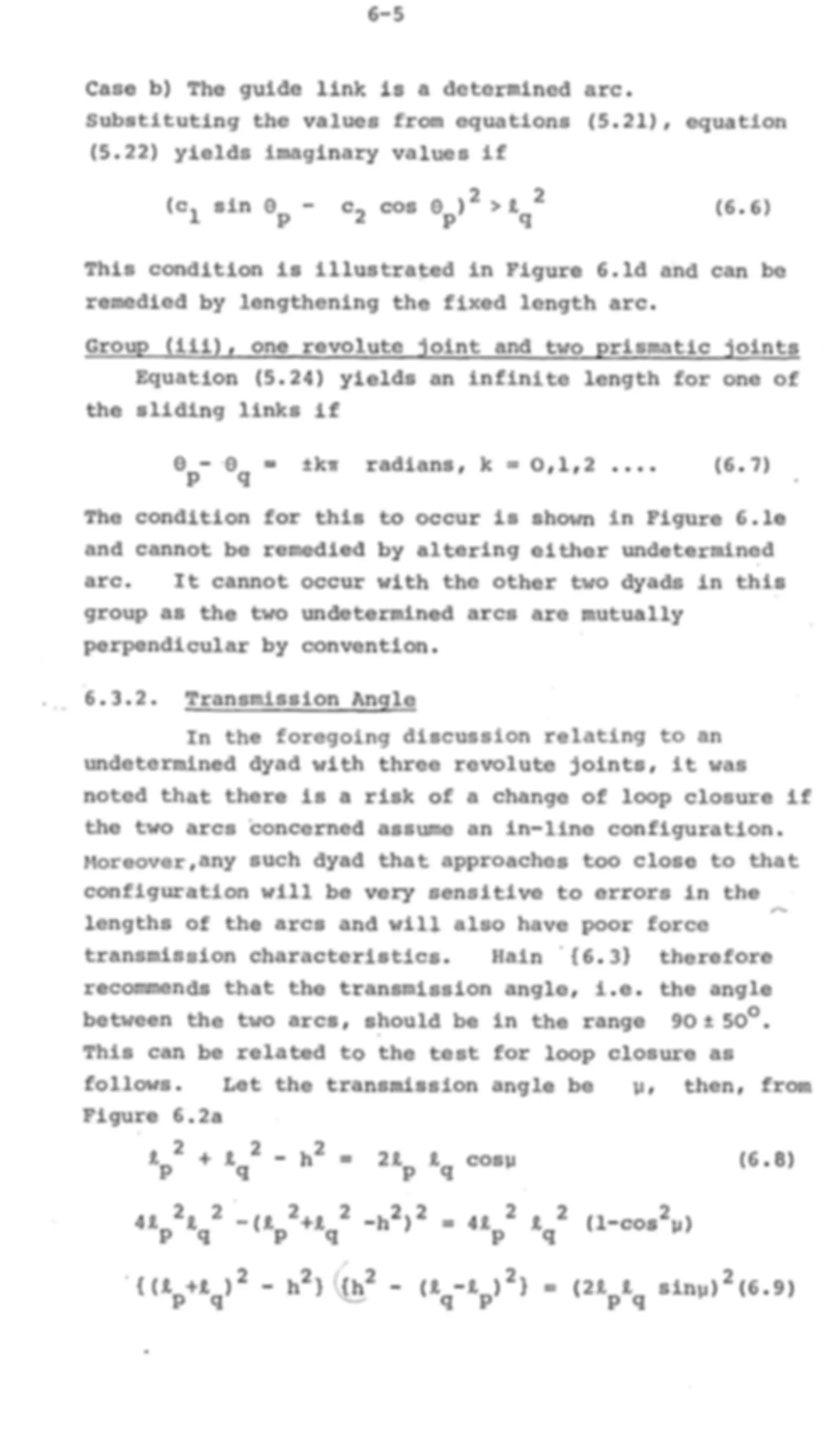
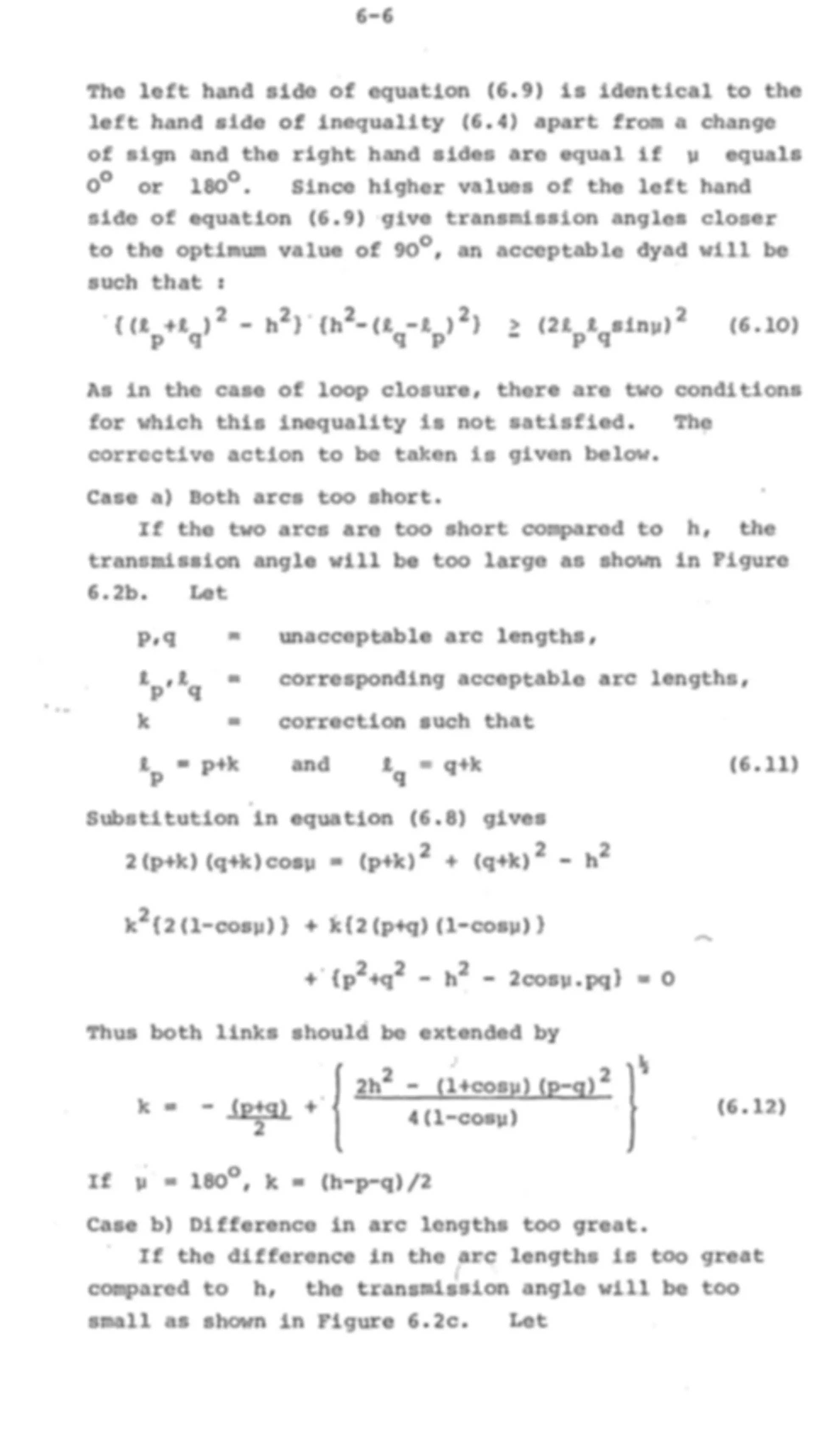
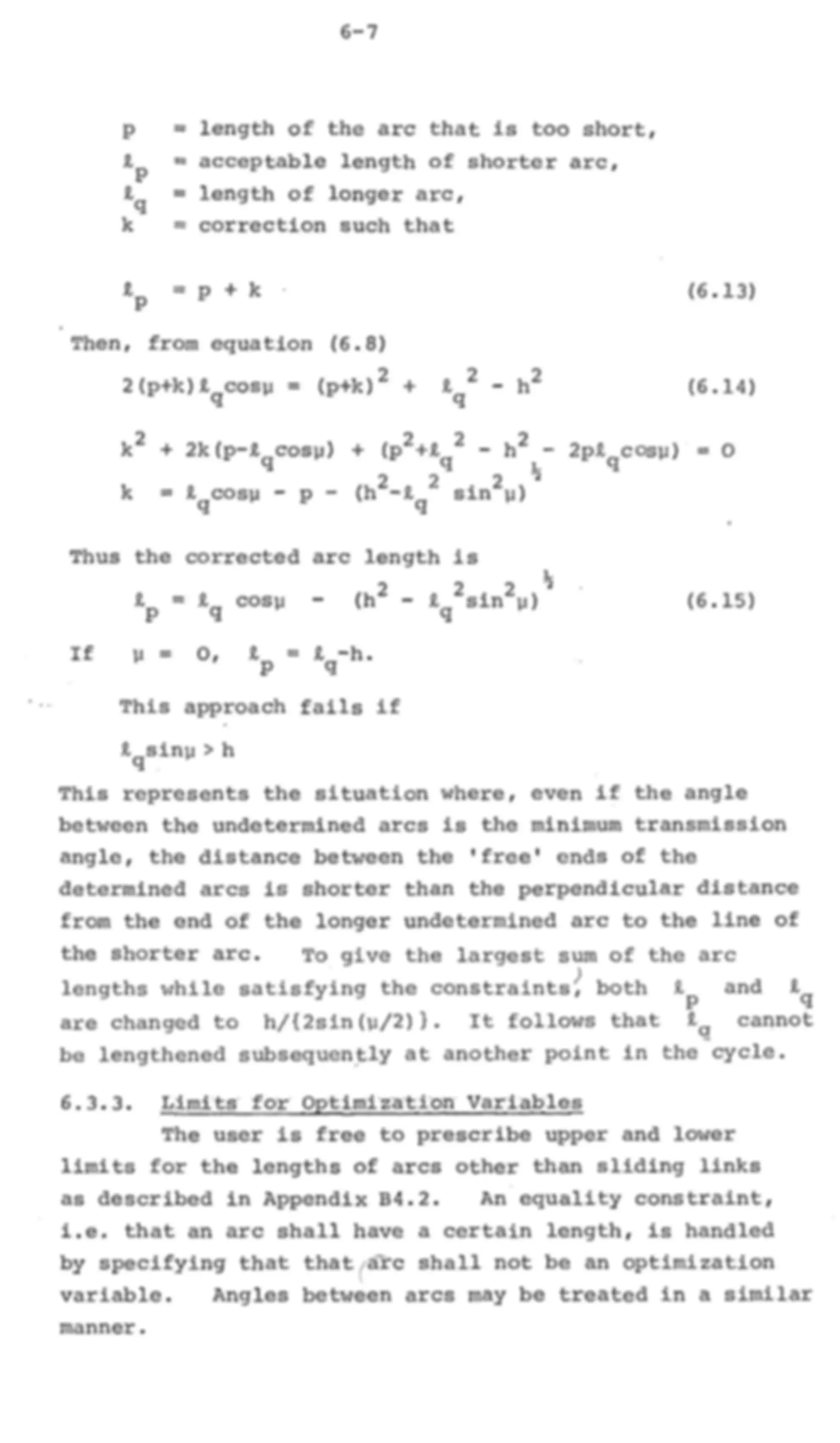
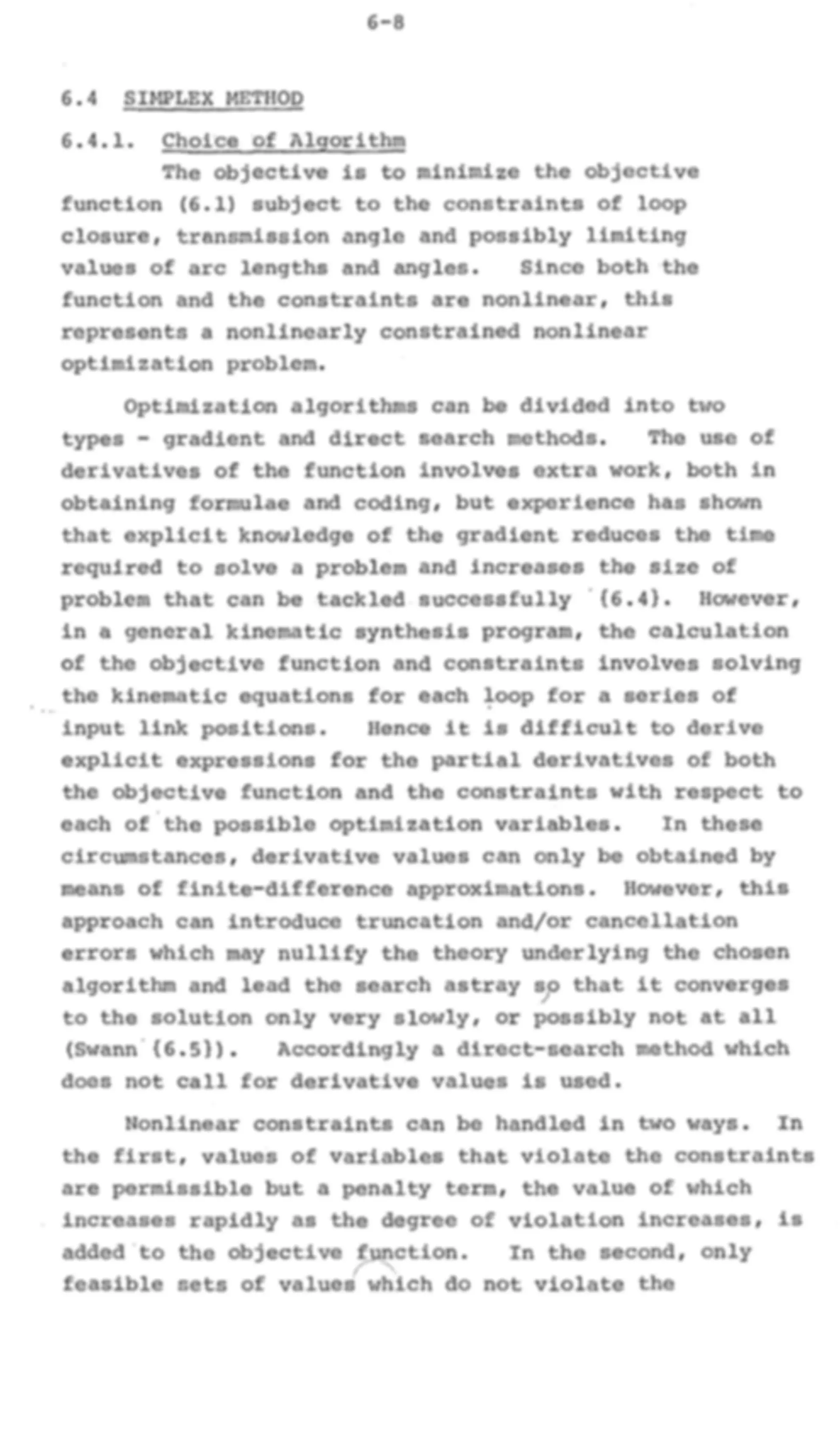
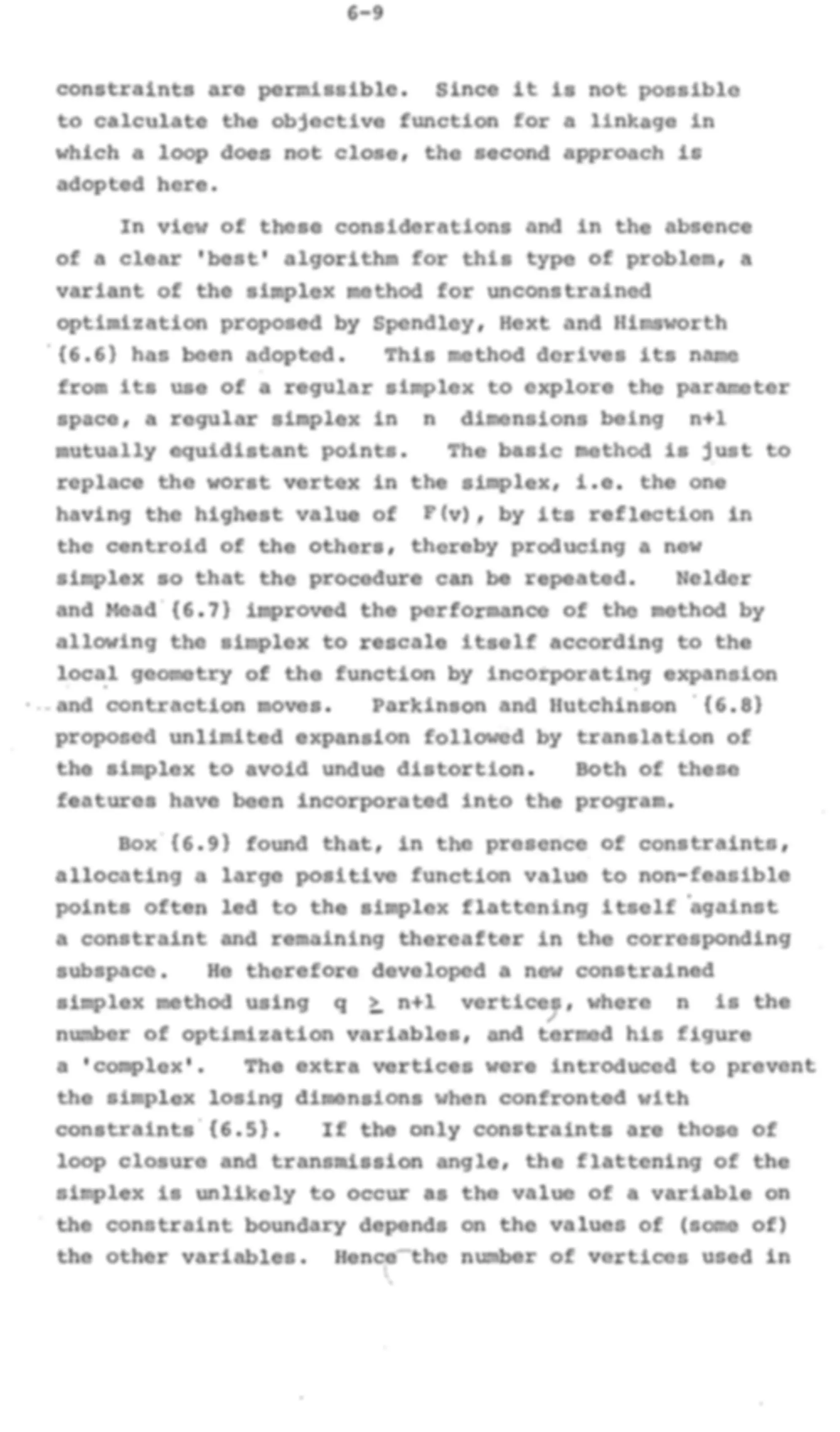
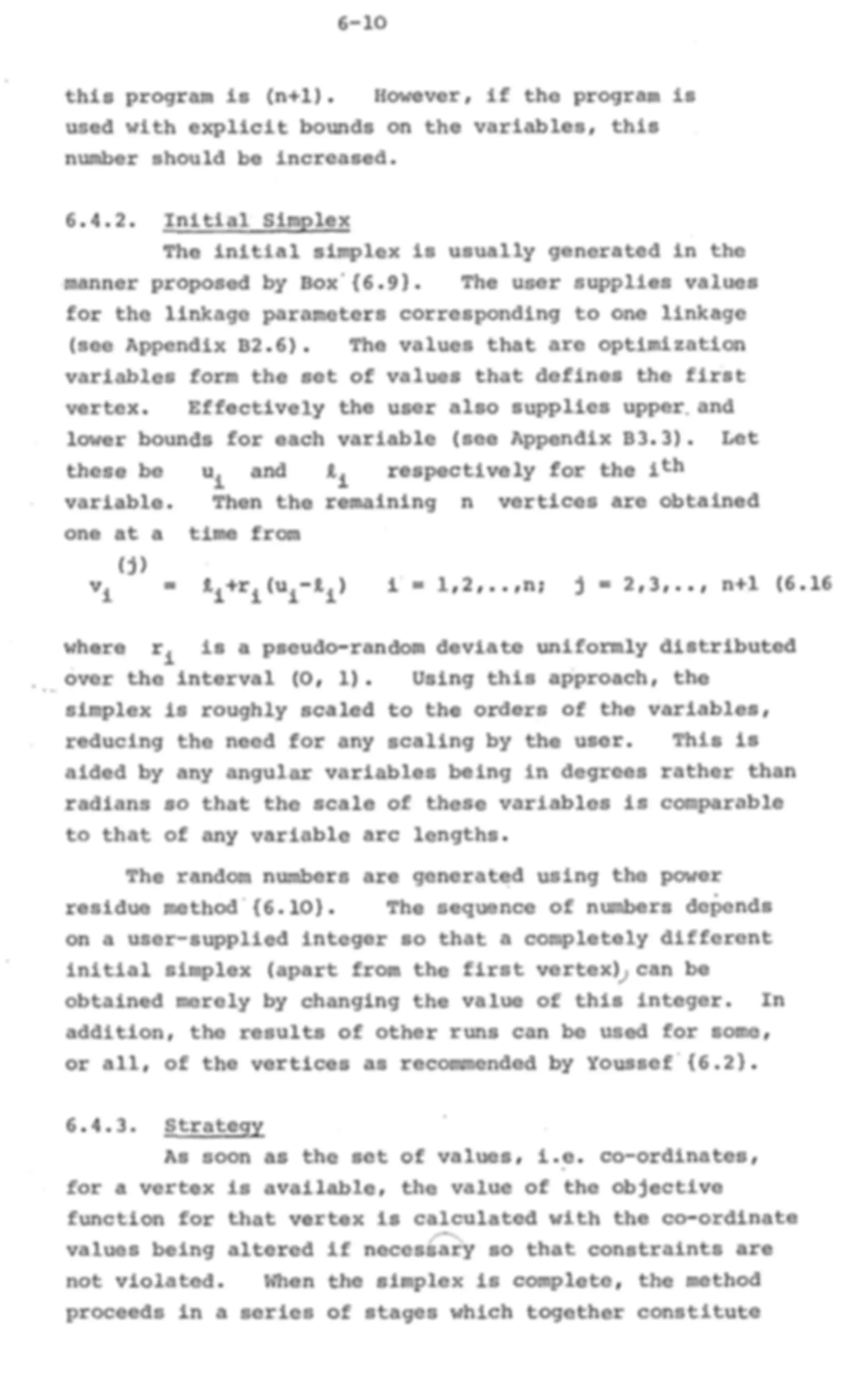
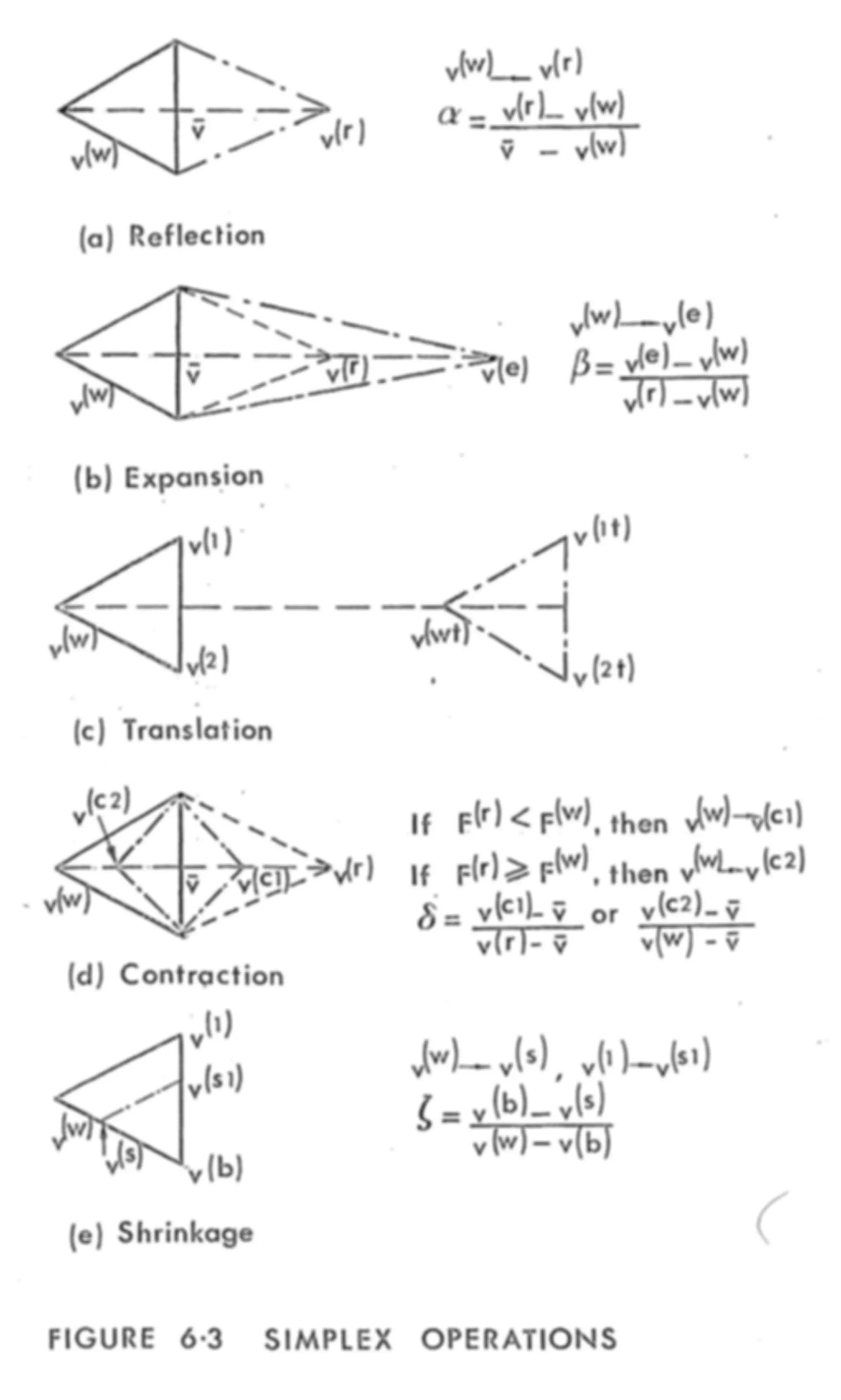
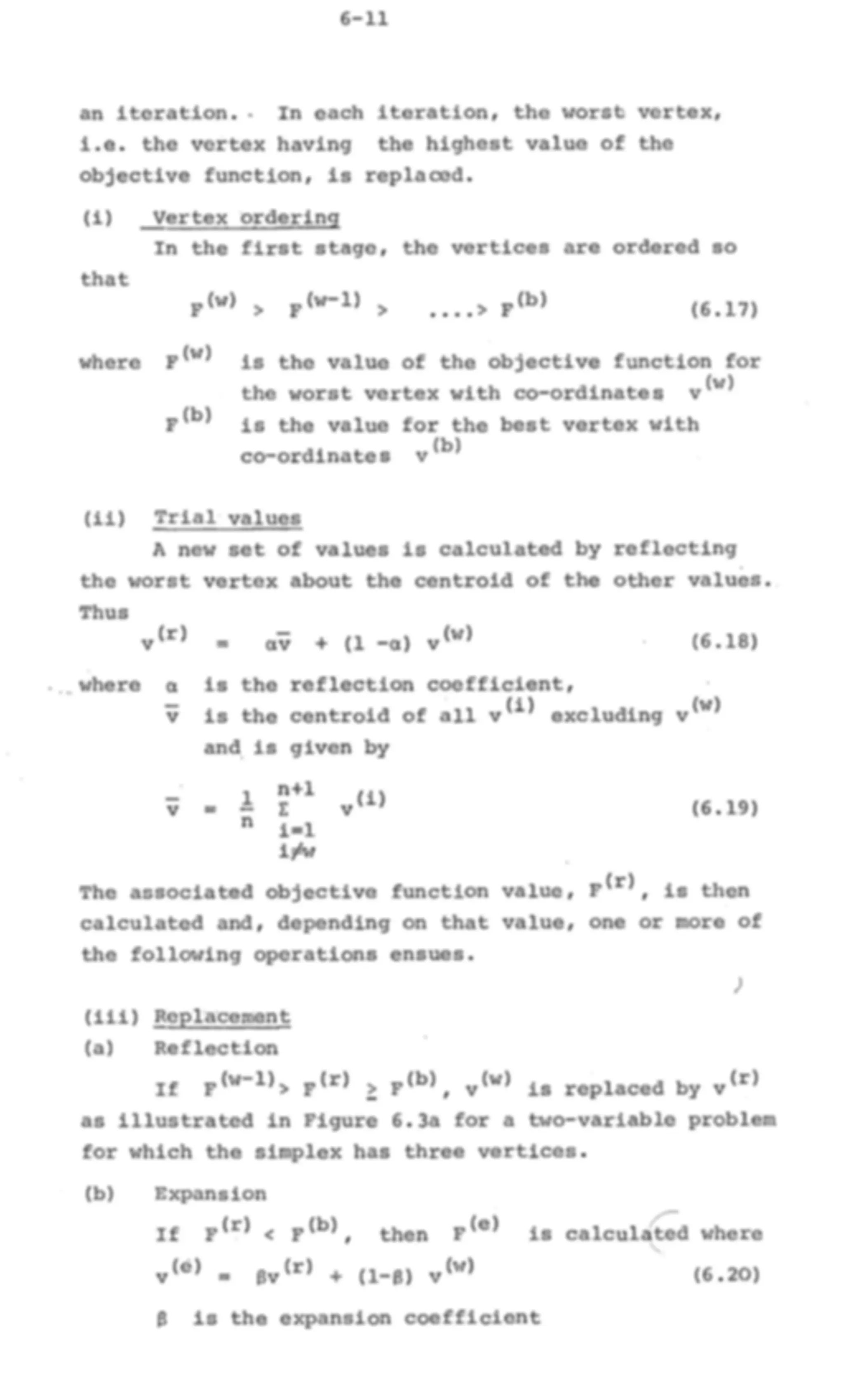
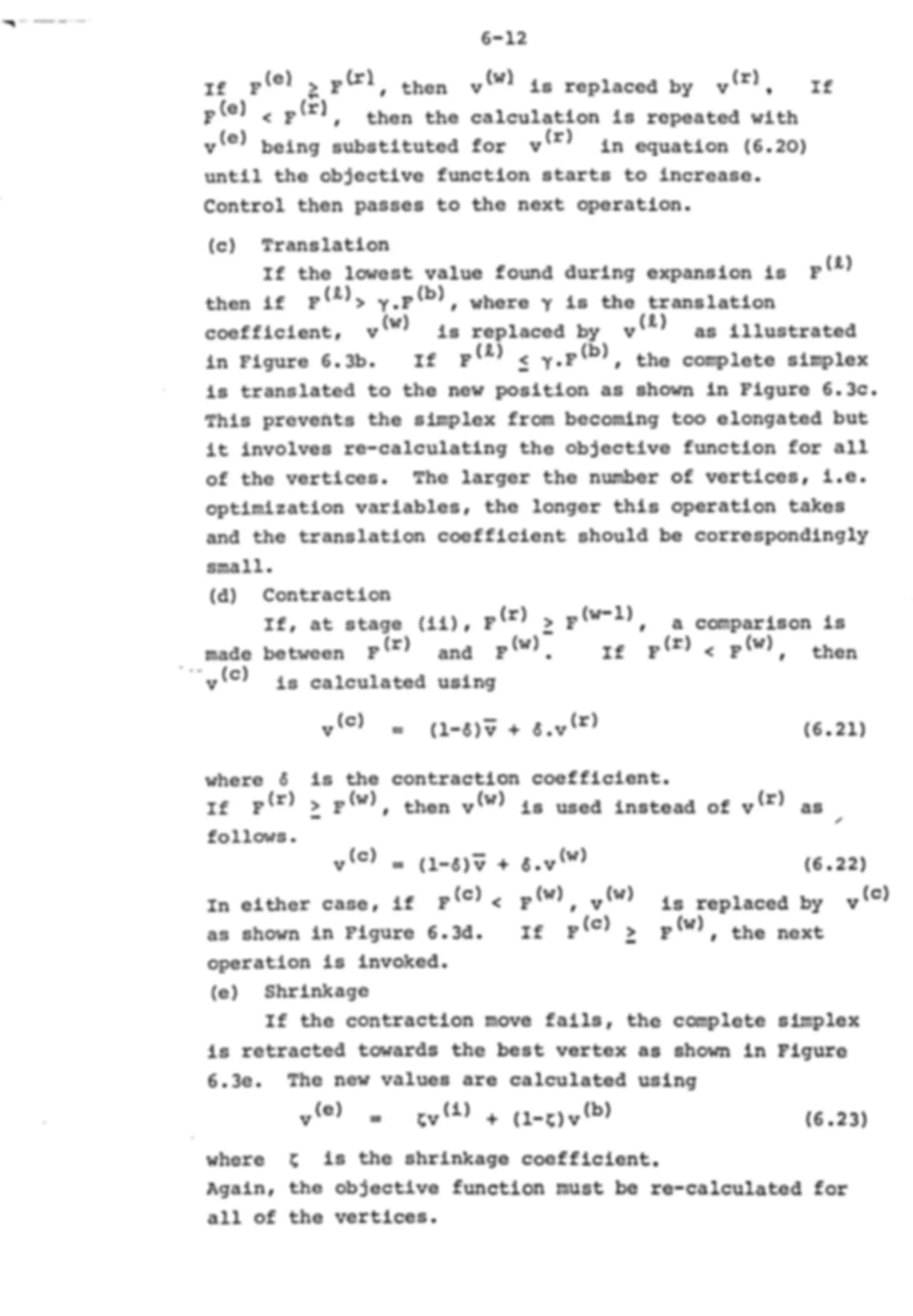
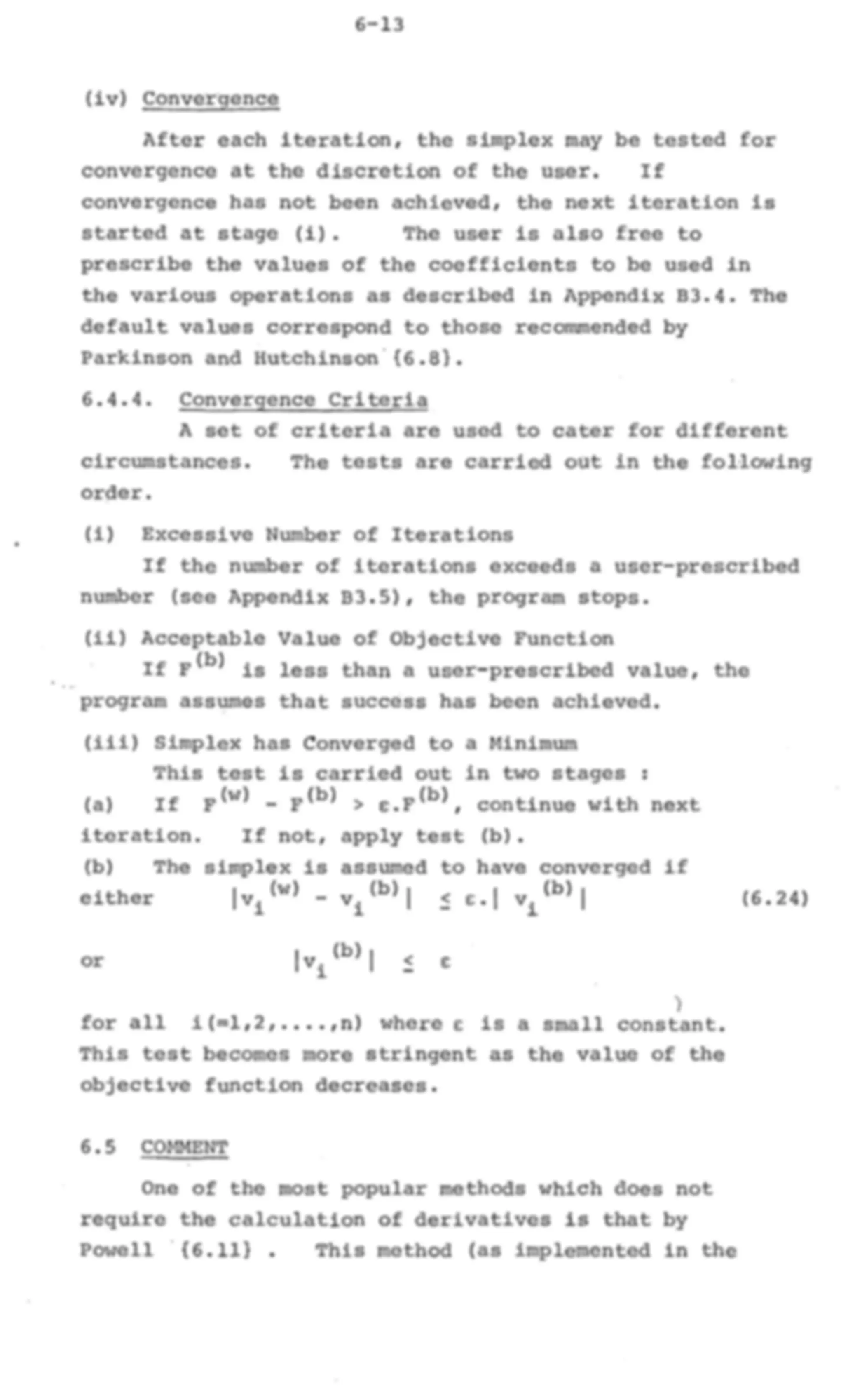
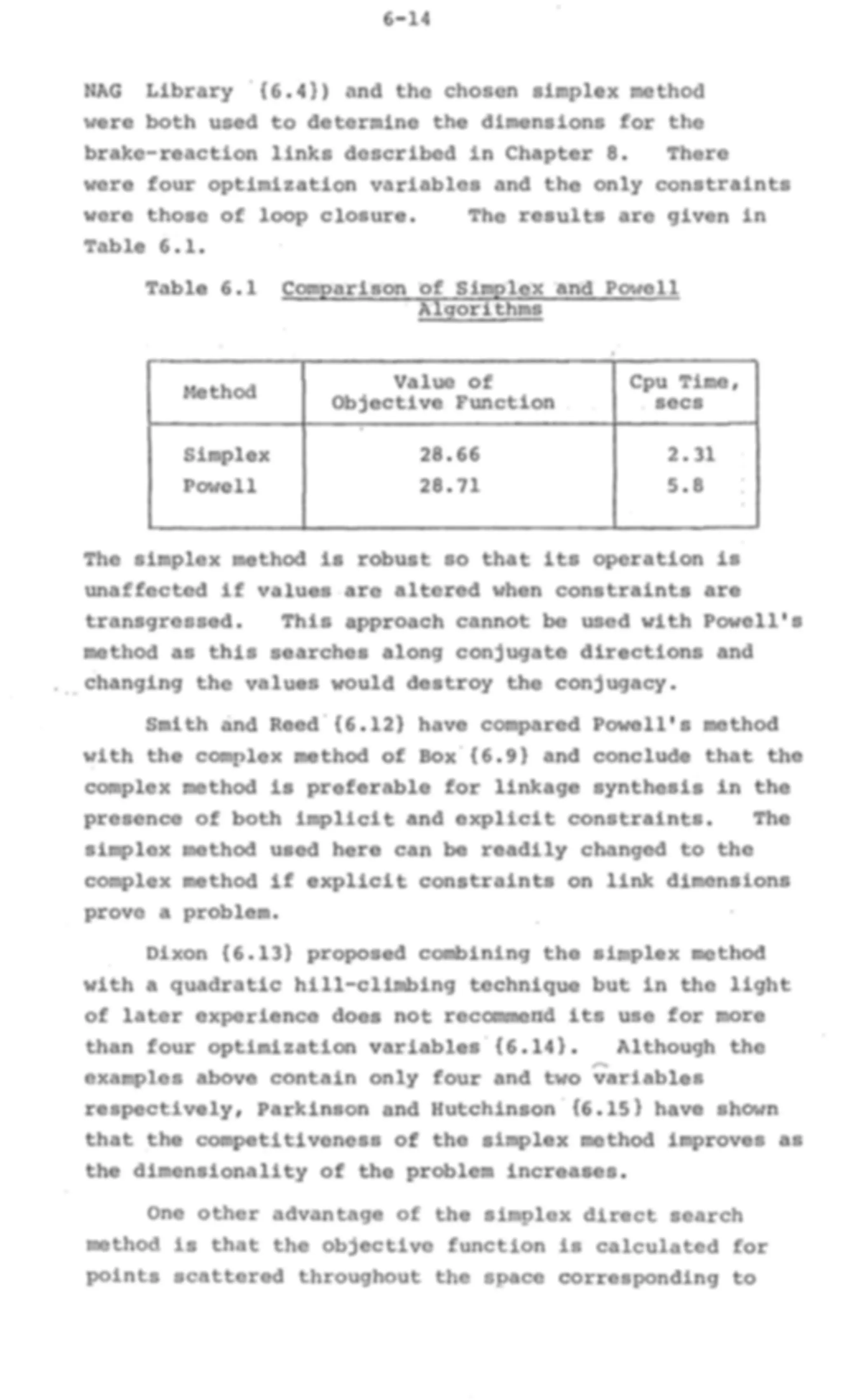
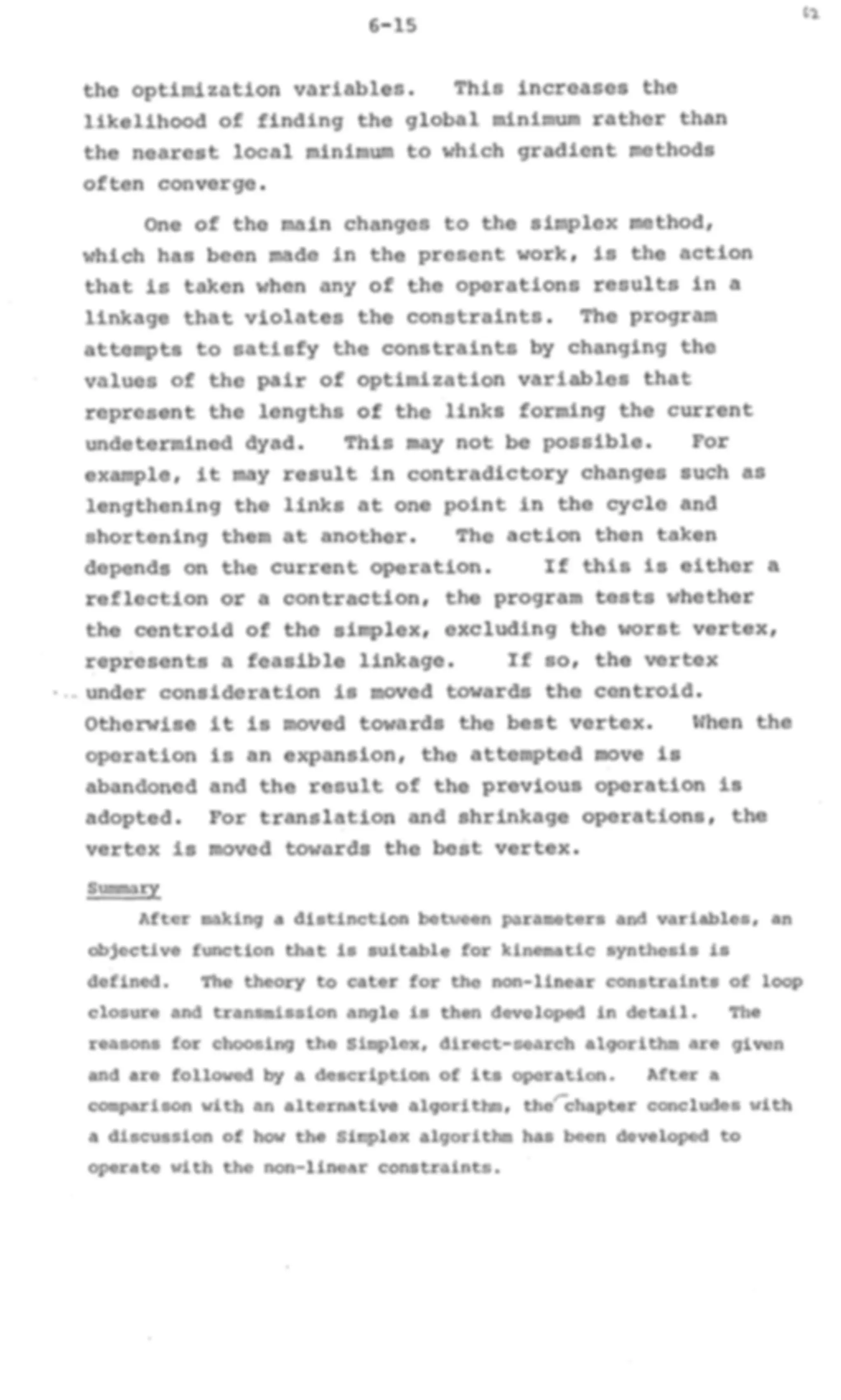
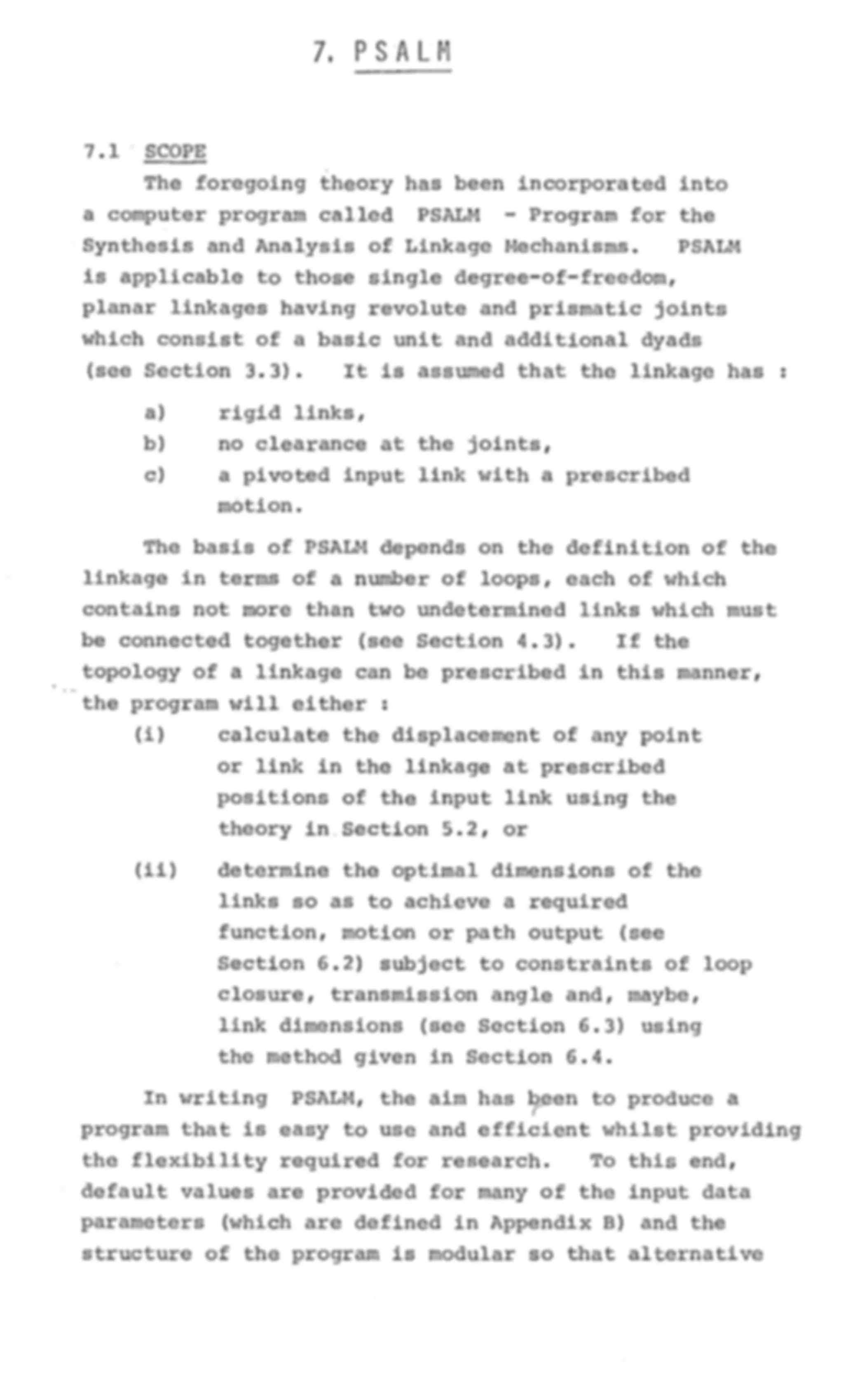
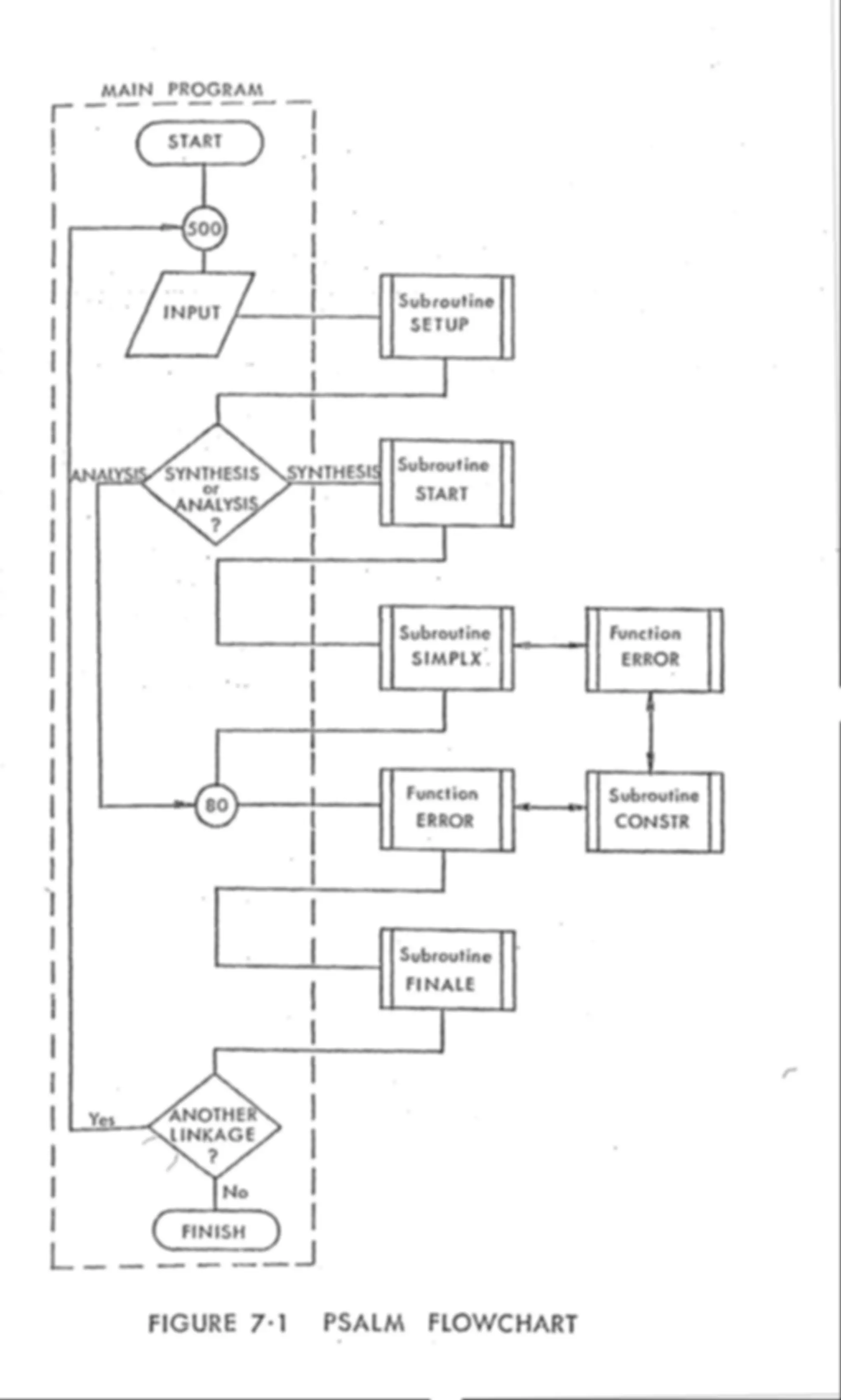
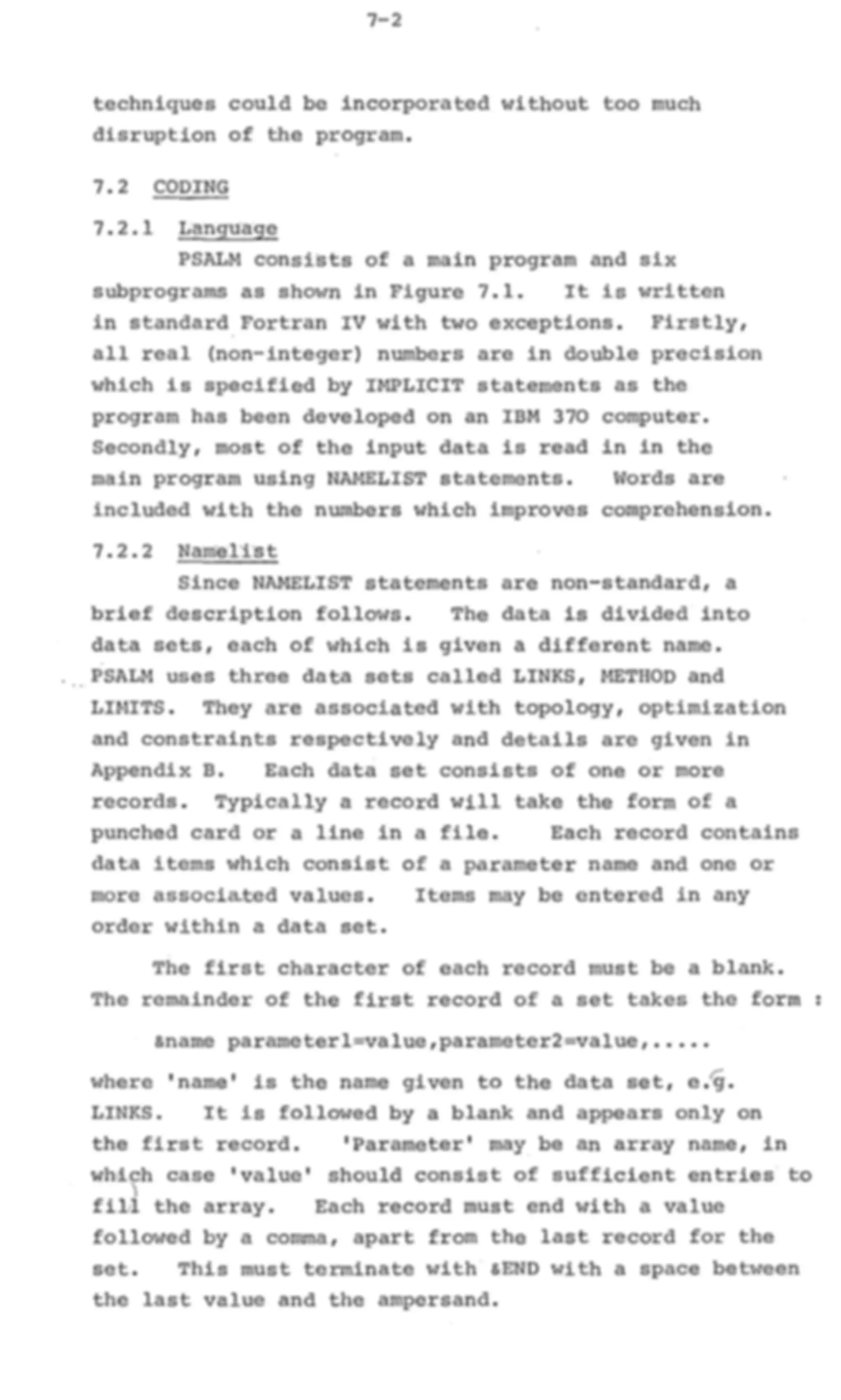
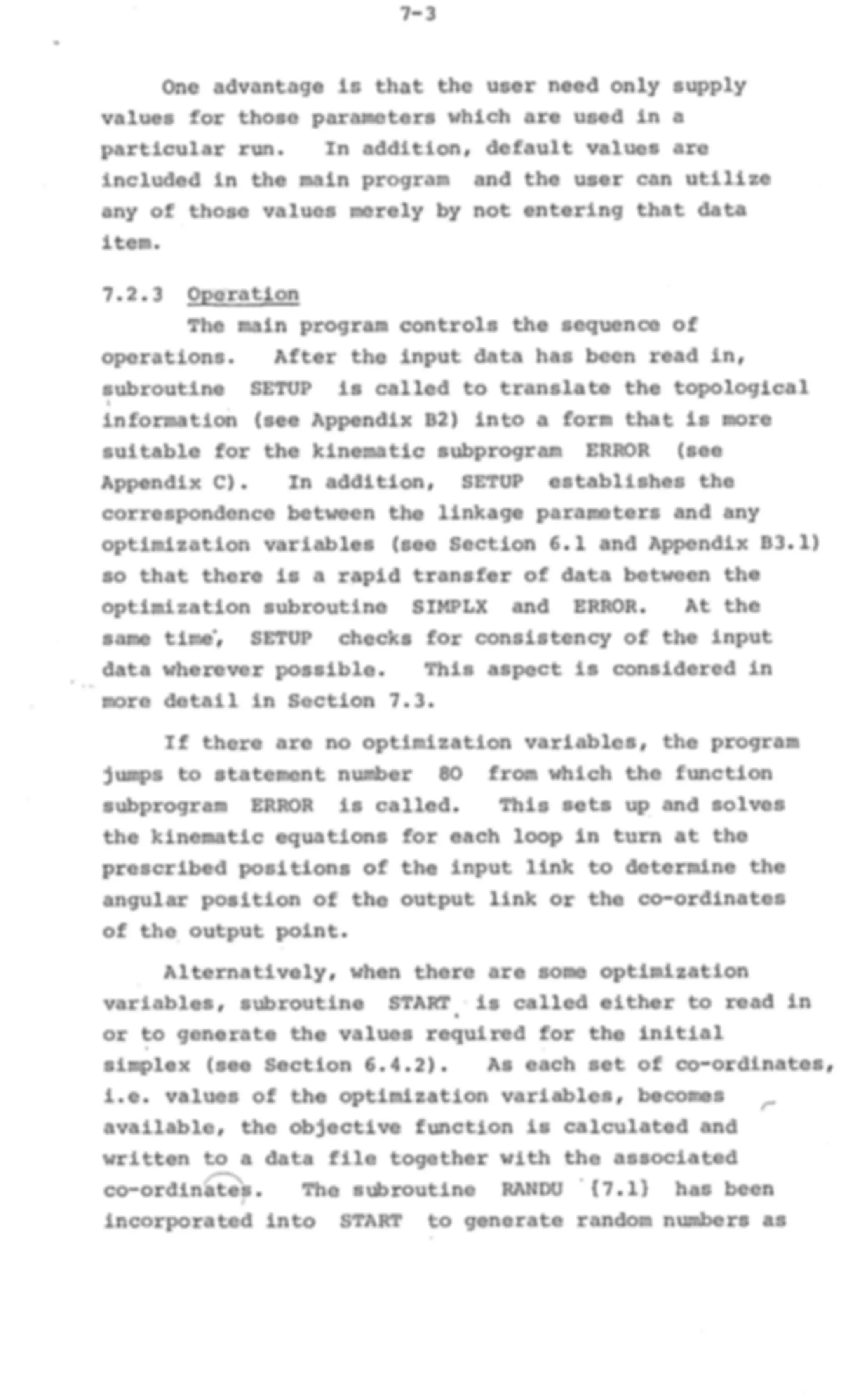
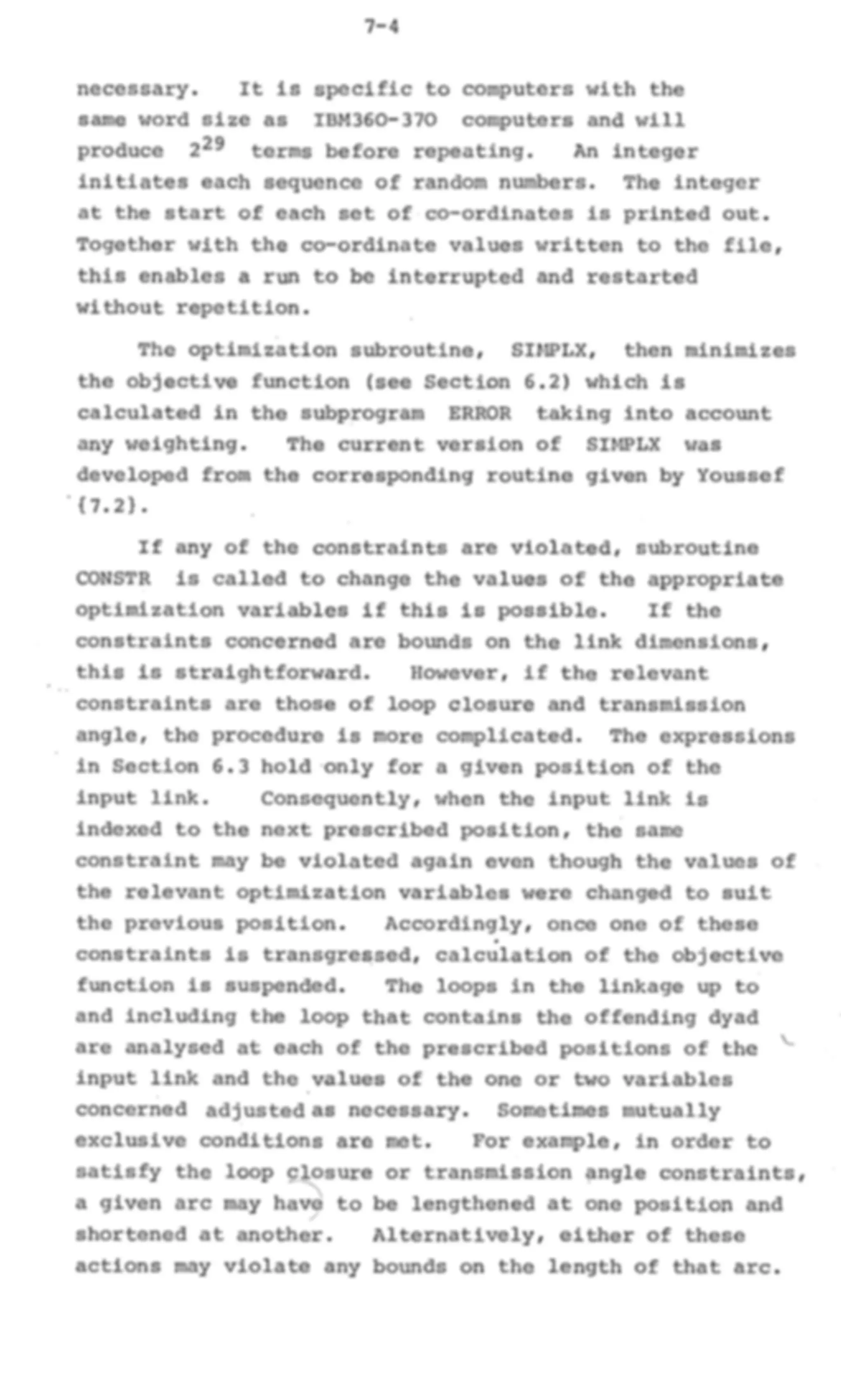
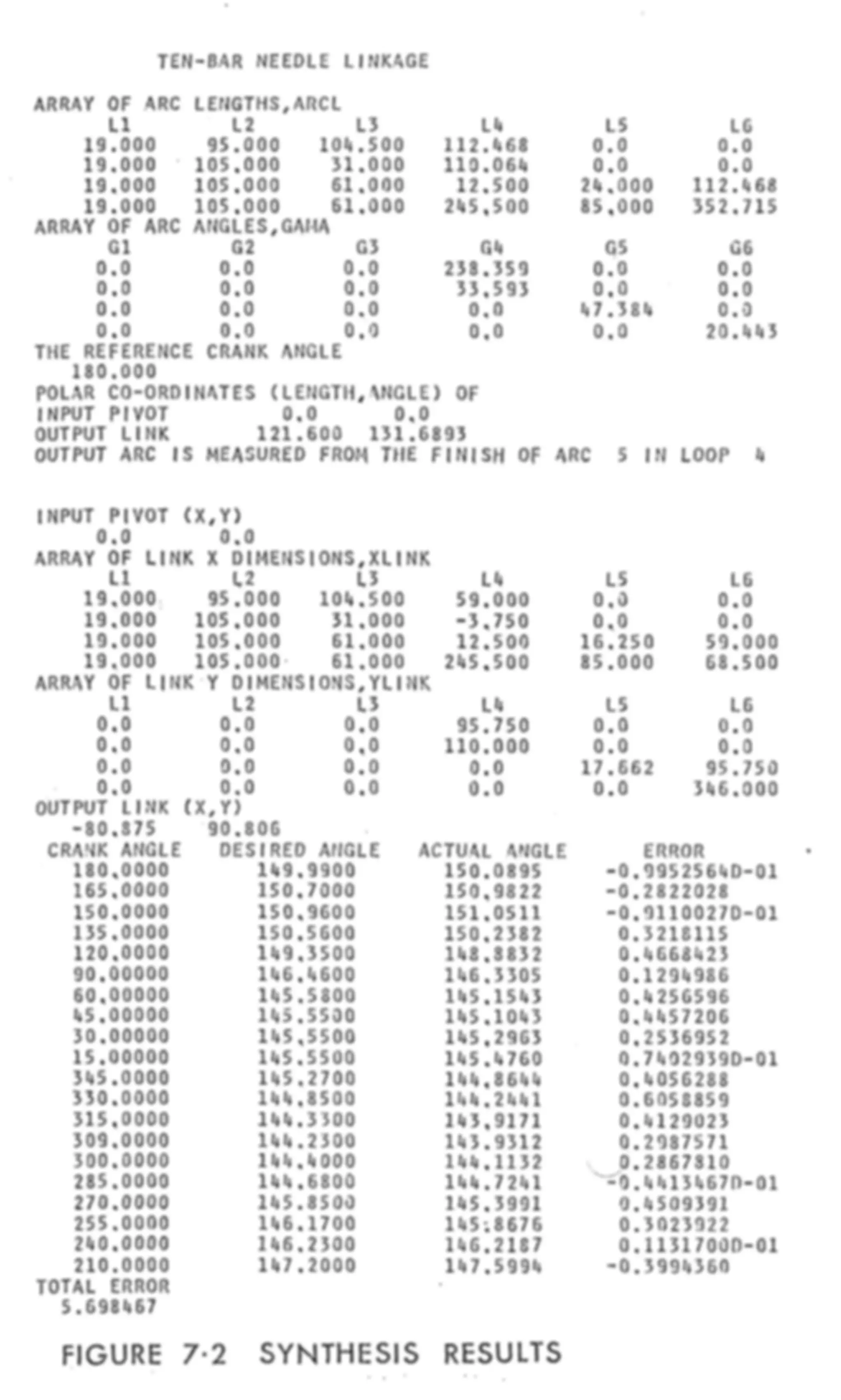
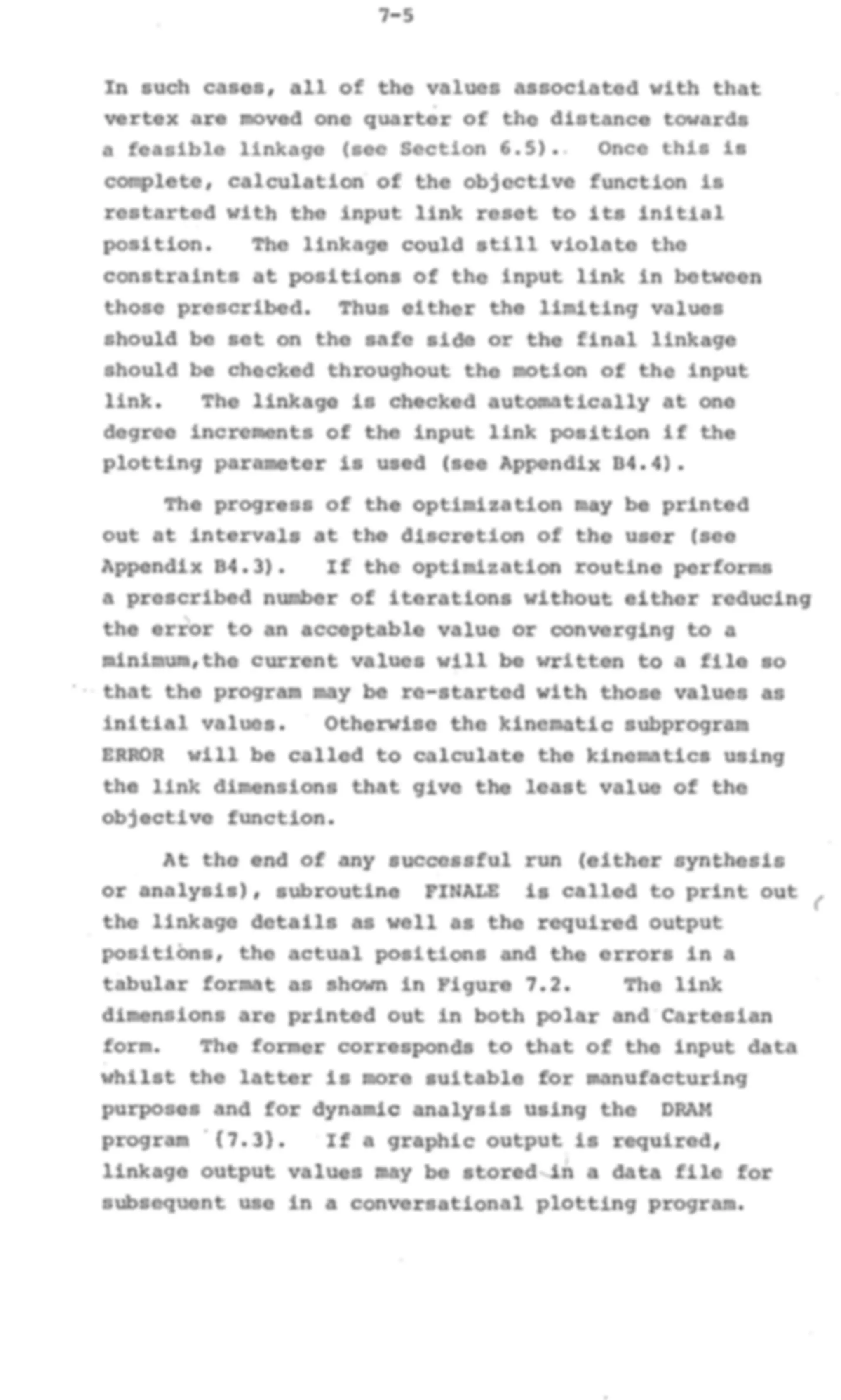
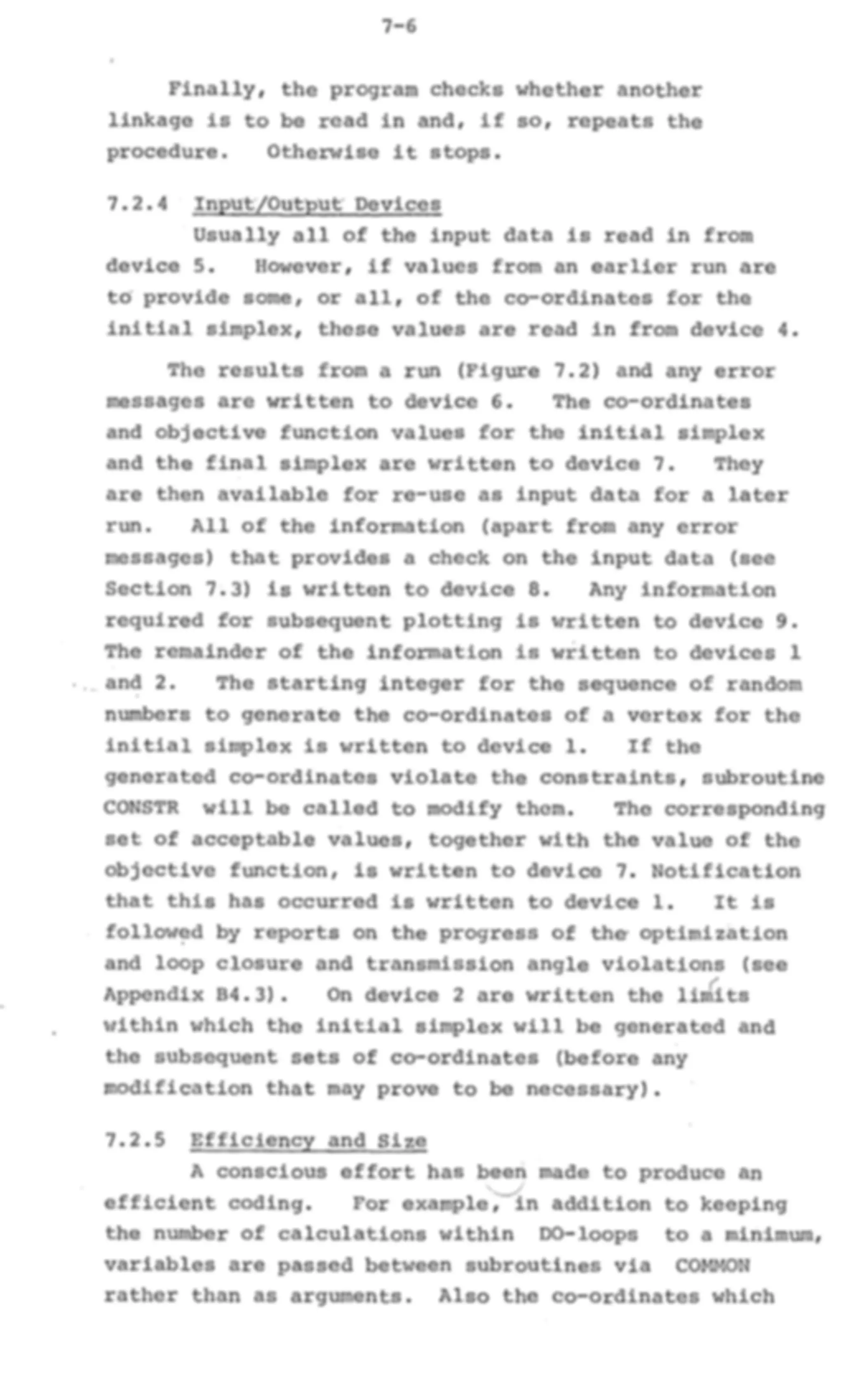
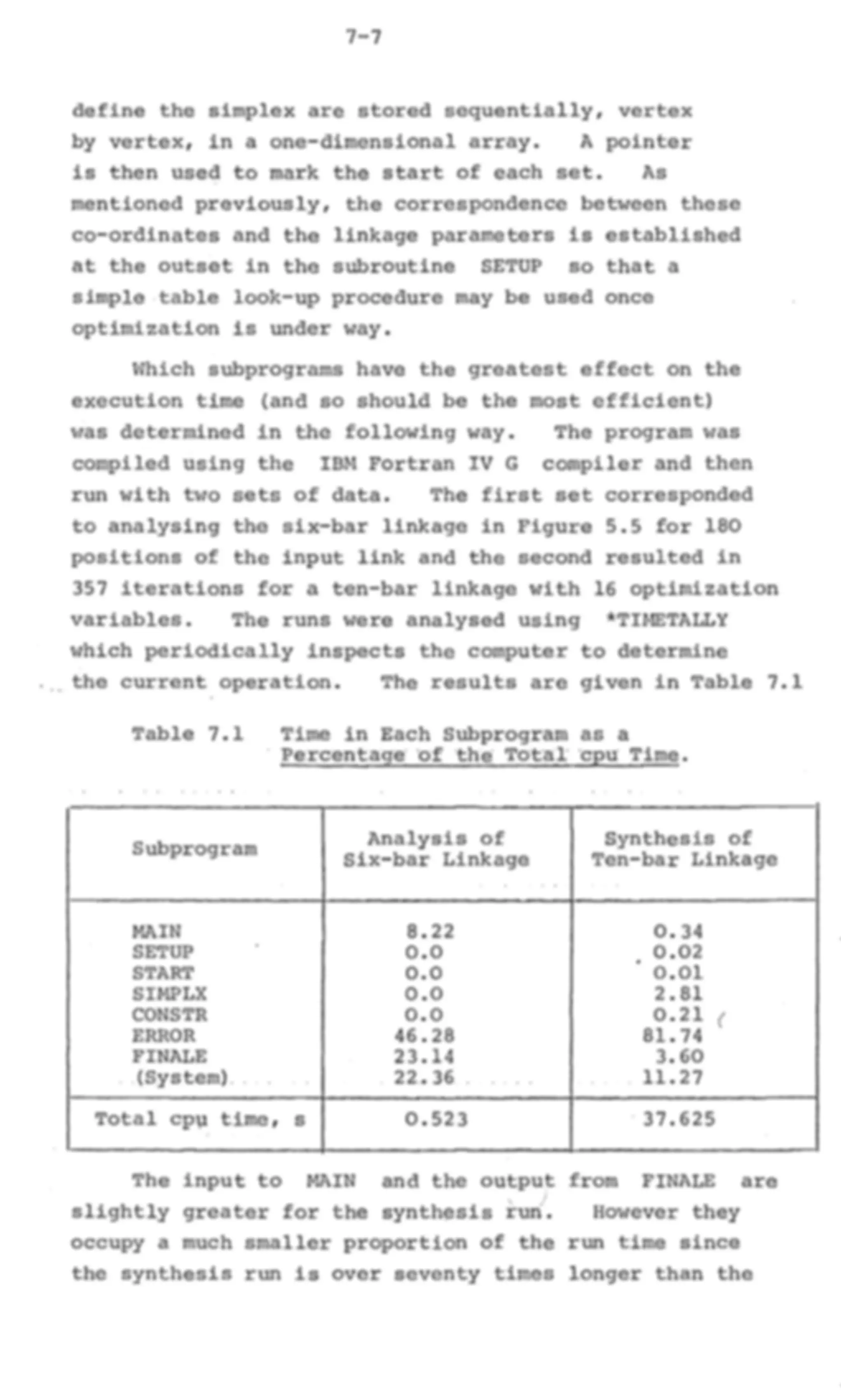
Study with the several resources on Docsity
Earn points by helping other students or get them with a premium plan
Prepare for your exams
Study with the several resources on Docsity
Earn points to download
Earn points by helping other students or get them with a premium plan
Community
Ask the community for help and clear up your study doubts
Discover the best universities in your country according to Docsity users
Free resources
Download our free guides on studying techniques, anxiety management strategies, and thesis advice from Docsity tutors
A technique for prescribing the topology of linkages formed by connecting pairs of links together. It covers topics such as degrees of freedom, kinematic synthesis, optimization, and force balancing. The technique is applicable to various types of linkages and mechanisms, and the document includes examples and case studies.
Typology: Lecture notes
1 / 271
This page cannot be seen from the preview
Don't miss anything!
THE KINEMATICS (^) AND (^) VIBRATION OF PLANAR (^) LINKAGE (^) MECHANISMS
Abstract
This (^) thesis (^) reports (^) an investigation (^) into three (^) problems encountered in^ the^ design^ of linkage^ mechanisms, namely kinematic (^) synthesis, balancing (^) of inertia forces (^) and vibration analysis. A (^) general (^) method of (^) synthesizing (^) planar linkages (^) with (^) pin and sliding joints^ using (^) an Optimization^ approach has^ been investigated. (^) A (^) concise but (^) easily interpreted (^) technique for (^) prescribing the topology (^) of linkages formed by (^) connecting pairs of links^ together^ has^ been^ developed.^ The^ displacement analysis (^) of (^) a linkage^ is^ achieved (^) using a direct^ method which is (^) considerably faster (^) than (^) alternative techniques. A (^) non- linear (^) optimization (^) algorithm has been (^) modified to (^) cater for non-linear constraints (^) such as transmission^ angle. These techniques have^ been (^) incorporated into (^) a computer program. Two (^) case-studies (^) of using the (^) program are given. The first (^) is (^) the (^) synthesis (^) of a (^) six-bar linkage (^) for (^) a motorcycle rear (^) suspension (^) such that^ a constant centre distance^ is
maintained between^ the^ chain-wheels as the^ suspension deflects. The (^) second (^) concerns the (^) modification of two linkages, (^) containing eight (^) and ten^ links^ respectively, to^ give (^) an improved^ knitting action for^ a warp-knitting (^) machine. Operating linkages^ at high^ speeds can result in^ rapidly varying forces^ acting (^) on the^ frame^ due^ to^ the^ mass of the^ moving links. (^) A (^) procedure to determine (^) suitable counterweights to balance (^) these forces (^) has been (^) developed. (^) Since (^) adding the counterweights (^) may double^ the^ total^ mass of the^ linkage,^ the links (^) should have (^) minimum mass. If (^) the (^) mass (^) of a link^ is^ reduced too far,^ the link^ may vibrate (^) and so detrimentally^ affect the^ performance of the linkage. (^) Accordingly (^) the final (^) part reports an investigation into (^) the forced (^) vibration, assuming (^) stability, of a 'Uniform, pin-jointed, binary^ link.^ The^ equations of motion are derived and stability boundaries^ determined.^ The^ theoretical^ predictions are (^) compared with (^) experimental results from^ the^ coupler of (^) a four-bar (^) linkage. e
UNIVERSITY (^) OF (^) NEWCASTLE (^) UPON (^) TYNE
0FPLANARLINKAGEMECHANISMS,
by
K. OLDHAM,^ M. A., (^) C. Eng., (^) M. I. Mech. (^) E., A. T. I.
A (^) Thesis (^) submitted for (^) the (^) Degree (^) of Doctor (^) of Philosophy (^) in
the Faculty (^) of Applied (^) Science, (^) University (^) of Newcastle (^) upon Tyne.
November 1977
The (^) work reported in^ this thesis (^) was (^) carried out under three^ Science^ Research^ Council^ grants^ and^ a Department (^) of Industry^ contract. The^ original intention
was to^ devote^ it^ to^ an^ investigation^ into^ vibrations^ in
planar linkage^ mechanisms.^ However,^ the^ Science^ Research Council (^) visiting (^) panel felt^ that^ the^ needs of industry should be^ ascertained^ to^ ensure industrial^ relevance. As (^) a result, three (^) problems encountered in^ the design^ of
planar linkage^ mechanisms^ have^ been^ investigated,^ namely kinematic (^) synthesis, balancing^ of inertia^ forces^ and vibration analysis. The kinematic^ synthesis of planar linkages^ containing pin and^ sliding^ joints^ using^ an^ optimization^ approach^ has been investigated.^ A (^) concise but^ easily interpreted technique has^ been^ developed^ for^ prescribing the^ topology of linkages^ formed^ by^ connecting^ pairs^ of^ links^ together. The displacement^ analysis of (^) a linkage^ is^ achieved using a direct^ method^ which^ is^ considerably^ faster^ than alternative techniques.^ A^ non-linear^ optimization algorithm has^ been^ modified^ to^ cater^ for^ non-linear constraints such^ as^ transmission^ angle^ and^ loop^ closure. These techniques^ have^ been^ incorporated^ into^ a (^) computer program. Two (^) case studies of (^) using the^ program (^) are given. The first^ is^ the^ synthesis of (^) a six-bar linkage^ for^ a motorcycle rear^ suspension.^ The^ linkage^ maintains^ a constant centre^ distance^ between^ the^ chainwheels^ as^ the suspension deflects.^ The^ second^ concerns^ the^ modification of two^ linkages,^ containing^ eight^ and ten^ links^ respectively, to (^) give an improved^ knitting^ action for^ a warp-knitting machine. The^ discussion^ following^ these^ case studies differs from^ the^ usual form^ in^ that it^ compares different techniques (^) and (^) methods (^) rather than^ theory^ and (^) experiment. operating linkages^ at high^ speeds (^) can result in rapidly varying^ forces^ acting^ on^ the^ frame^ due^ to^ the mass of^ the^ moving^ links.^ Accordingly^ the^ second (^) part contains the^ theory^ and^ a procedure to^ determine^ suitable counterweights to^ balance^ these^ forces.^ Since^ adding the
Paqe
GENERAL (^) INTRODUCTION 1.1 (^) Application (^) of Linkage Mechanisms 1- 1.2 (^) Survey (^) of Design Factors 1-
A. KINEMATIC SYNTHESIS
SELECTION 3.1 (^) Terminology (^) and Conventions (^) 3- 3.2 (^) Degrees (^) of Freedom 3- 3.3 (^) Kinematic (^) Chains (^) and Planar 3- Linkages
4.1 (^) Specification 4- 4.2 (^) Survey 4- 4.3 (^) Loops 4- 4.4 (^) Undetermined (^) Dyads 4- 4.5 (^) Arcs (^) and Arrays 4-
KINEMATICS 5.1 (^) Approach (^) 5- 5.2 (^) Theory 5- 5.2.1 (^) Undetermined dyad (^) with 5- three (^) revolut e joints 5.2.2 (^) Undetermined dyad (^) with 5- two (^) revolute joints^ and one (^) prismatic joint 5.2.3 (^) Undetermined dyad (^) with 5- one revolute joint^ and two (^) prismatic joints 5.3 (^) Comparisons 5-
6.1 (^) Variables (^) and Parame ters 6- 6.2 (^) Objective 6-
B. FORCE (^) BALANCING
VIBRATION (^) ANALYSIS
Paqe
D. FURTHER^ WORK
APPENDICES
A. REFERENCES
B. PSALM^ INPUT^ DATA Bl (^) Title B- B2 Topological^ Data Set (^) - LINKS B- B3 Optimization (^) Data Set (^) - METHOD (^) B- B4 (^) Constraint (^) Data Set (^) - LIMITS B- B5 Complete Sets (^) of Data (^) B- C. INTERMEDIATE ARRAYS D. COIAPUTER-AIDED^ SYNTHESIS^ OF^ LINKAGES -A MOTORCYCLE^ DESIGN^ STUDY
1.1 (^) 'APPLICATIONS OF LINKAGE MECHANISMS Linkage (^) mechanisms have^ a long^ history.^ For example, a (^) crank-rocker linkage^ is^ illustrated^ in^ a compendium of^ agriculture and rural engineering dated (^1313) AD (See^ Nolle {1.11 (^) Linkage (^) mechanisms are in widespread use today,^ both^ in^ the^ home^ and in^ industry. Examples (^) range in^ complexity from^ slider-crank mechanisms used in^ conventional^ umbrellas and a cream-making attachment for^ a domestic^ food-mixer^ to^ an (^) eleven-bar linkage (^) used in (^) shoe machinery '11.2a)^ and (^) a fourteen- bar (^) circuit-breaker (^) mechanism {1.31. Linkage (^) mechanisms are indispensable^ where an operation'depends (^) on the^ relative motion between^ two^ or more (^) machine elements (^) undergoing simultaneous but different (^) movements (^) at high (^) speed. For (^) example, Kestell {1.2b} (^) describes (^) a (^) machine for (^) stitching a (^) sole to (^) the
welt (^) of (^) a shoe at a rate of (^1000) stitches/min. In^ this
machine, the^ combined movements of several (^) elements, e. g. the (^) awl, needle (^) and looper,^ are required to form (^) a stitch, so linkage^ mechanisms are (^) used to^ control them.^ The^ awl and (^) needle mechanisms are crank-driven (^) whereas the^ looper mechanism is^ cam-driven. Cams (^) and followers^ are (^) sometimes regarded as alternatives to^ linkages,^ e. g. Eder^ {1-4}^ , but^ there are (^) circumstances, (^) where cams (^) are used, that^ require a linkage (^) as well. In (^) such cases, one or more of the following (^) conditions (^) applies (^) : a) there^ is^ insufficient^ space to^ accommodate the cam close to^ where the^ output motion is required, (^) e. g. the^ valve-gear for^ an internal combustion (^) engine, b) (^) the (^) output (^) motion is (^) adjustable (^) e. g. Kestell fl. (^) 2c} illustrates (^) a (^) cam-driven, thread-
1-
measure mechanism^ in^ which^ the^ length^ of thread (^) paid out depends^ on the^ thickness^ of the (^) work being^ stitched,
C) the^ amplitude of^ the^ output^ motion^ is different from^ that (^) of the (^) cam follower;^ the output amplitude^ may^ be^ larger,^ as^ in^ the^ case of a draw^ mechanism^ for^ a^ weft-knitting machine (one^ version^ of^ which^ is^ given^ by Wignall '11.5})^ in^ which the^ output amplitude is (^) adjustable and may be^ a maximum of 42 in. compared with a^ cam^ throw^ of^9 in.,^ or^ smaller, as in^ a^ copying^ machine^ where a^ negative magnification, to^ reduce errors, is^ obtained using a^ pantograph mechanism,
d) (^) two (^) cams are (^) used to (^) generate a two-dimensional
output motion, the^ linkage^ being^ required^ to combine the^ motions,^ e. g.^ Bloom'{1.6)^ and^ Wray et al.^ 11.71^ where one^ component^ of^ the^ output is adjustable^ to^ provide different^ spacings^ of^ the loops in^ a looped^ pile fabric^ machine, e) a^ positive drive^ is^ required^ from^ a^ single^ cam profile using swinging followers^ e. g.^ Jackowski and Dubil'fl.^ 8}^ , an early example^ of^ its^ use^ is illustrated by^ Willkomm'{1.91. There is^ a continual demand^ made on industrial designers for^ machines that (^) will run (^) faster and yet be simpler to^ manufacture.^ If^ cams^ are^ used^ at^ higher speeds, greater attention^ must^ be^ paid^ to^ producing^ a profile that^ gives^ the^ desired^ dynamic^ performance^ as this is^ significantly (^) affected by^ local^ profile errors. In (^) addition, if^ a (^) spring-loaded follower^ is^ used, high spring forces^ will be^ necessary to^ maintain contact and these forces^ will cause high^ contact stresses and possible surface^ failure.^ A^ closed-track^ cam^ with^ a single roller follower^ suffers from^ impact^ and^ skidding, causing noise and^ wear,^ when^ the^ roller^ changes^ from one side of the^ track^ to^ the^ other.^ To^ overcome^ these
Material (^) Density t/m^3
Specific Modulus MJ/kg
Specific Strength kJ/kg
Cast iron^ 7.2 5 16 40 BS 1452,^ grade 17
SG iron,^ annealed (^7 1 24 ) BS 2789,^ type SNG 27/^.
Mild (^) steel 7.8 26.5 50
Low (^) alloy (^) steel- 7.8 (^) 26.5 125
. Aluminium.^ casting^.^ 2.7^ 25.8^80
Magnesium (^) casting, (^1 8 25 ) heat-treated (^).
Titanium (^) alloy, (^4 5 25) 2CO DTD 5173.
Carbon fibre^ reinforced plastic, unidirectional, (^1 5 115 ) 50% high^ modulus. polyacrylonitrile based
Table 1.1.^ Representative Values (^) of Specific Modulus (^) and Strength (^) of Various Materials.
measures of^ the^ stiffness-weight^ and^ strength-weight ratios respectively.^ Cast^ iron^ is^ easy^ to^ machine and has^ good^ damping^ properties.^ Aluminium^ alloy links (^) should form flat^ laminae^ {1.111^ but^ the low density (^) means that thicker (^) sections can be (^) used for a given mass. Titanium^ has^ been^ used for^ the guide-bars of^ a^ warp-knitting machine but^ has^ now^ been replaced by^ 'Grafil',^ a carbon fibre^ reinforced plastic (CFRP)'{1.23}.^ Partly^ as a result of^ this change, the^ machine^ speed was increased^ by^ 10%.^ A 50% improvement in (^) the (^) speed (^) of a narrow-fabric loom was obtained^ by^ using CFRP^ instead^ of^ steel for^ the heddle frames'{1.211.^ Although CFRP (^) offers the twin advantage (^) of high^ specific (^) modulus and strength, close co-operation between^ the^ manufacturer and the^ machine designer is^ required to (^) obtain the best (^) results since the directional (^) properties of the (^) material depend^ on the lay^ of the^ carbon fibres. If the (^) stiffness of the links^ is^ too low,^ the linkage (^) may (^) start to (^) resonate at various (^) speeds resulting in^ material fatigue^ with possibly an^ incorrect output (^) motion and noise (^) radiation from^ other parts of the (^) machine. If the (^) mechanism is^ driven^ by^ a cam running (^) at constant speed, it^ is^ possible^ to^ design^ the cam (^) profile to^ take^ into^ account the^ effect of^ mechanism flexibility (^) on the (^) output (^) motion. Dudley {1. proposed the^ use^ of^ polynomial curves^ and^ Kanzaki^ and Itao {1.251^ have^ investigated^ the (^) use of (^) such cams for positioning the^ typehead^ in^ high-speed^ teleprinters. However, this (^) approach is^ not (^) applicable to (^) a crank- driven linkage,^ so, in (^) this (^) case, the designer^ will
want to^ know^ how^ light^ the^ links^ can be^ to^ avoid these
problems (^) within the^ envisaged speed range. The (^) output (^) motion can (^) also be^ affected by^ clearance at the^ joints.^ For^ example, in^ a^ plain revolute^ joint', the (^) pin (^) may move from^ one side of the^ bush^ to^ the^ other
1-
which, again, is^ affected by^ the^ tolerances^ on^ the link dimensions. (^) There (^) are five (^) assembly methods from (^) which to (^) choose (^) :
a) (^) random assembly with total^ interchangeability
Further development (^) of design (^) methods is (^) both possible (^) and desirable.^ Contacts^ with industry have (^) shown that (^) machine designers (^) would appreciate assistance (^) with the^ determination^ of the link^ lengths and the^ anticipation (^) of linkage^ vibration. Reflecting these (^) requirements, the (^) thesis is (^) divided into (^) three parts (^) entitled Kinematic^ Synthesis,^ Force^ Balancing and Vibration^ Analysis^ respectively.
. 'Suwznary
After (^) noting some applications of linkage (^) mechanisms, the conditions (^) where linkages^ are (^) necessary are listed.^ Their relationship (^) with, and their^ advantages over, (^) cam-driven mechanisms (^) are then^ considered. This^ is^ followed^ by^ a survey of factors^ to^ be^ taken^ into^ account in^ the^ design^ of linkage mechanisms. These^ factors^ include^ material selection, force balancing (^) and vibration in (^) addition to (^) clearance and friction (^) at the joints.^ As (^) well (^) as determining (^) the (^) nominal dimensions (^) of the links, (^) the designer^ must decide (^) on suitable tolerances for manufacture (^) and assembly. In^ conclusion, the^ need for^ further work in^ kinematic^ synthesis, force^ balancing^ and (^) vibration is emphasized.
synthesizing linkages^ to^ generate^ coupler curves. They (^) can be^ divided^ into^ two (^) groups depending^ on the relationship between^ the^ number of points used^ to define (^) the desired (^) motion and the (^) number of unknown parameters, (^) such as link^ lengths,^ in^ the^ mechanism. Precision (^) point methods depend^ on the (^) number of points being^ less^ than^ or (^) equal to^ the^ number of parameters. The^ resulting mechanism will produce the desired^ motion exactly (^) at those (^) points but^ there is (^) no control over intermediate (^) positions. Optimization (^) methods are (^) used (^) where the (^) number of points is^ greater than^ the^ number^ of parameters. In this (^) case, there^ is^ no guarantee that^ the^ resulting mechanism (^) will pass through^ any of the^ specified points exactly but^ there^ is^ more control^ over^ the general shape of the^ motion curve. Thompson*{2. concludes that^ this^ is^ the^ best^ type^ for^ kinematic synthesis. Kestell'{2.41^ also followed^ this^ approach, using (^) graphical methods, by^ 'plotting^ the^ trend'.^ Of the (^) graphical (^) and analytical methods, only the analytical (^) ones (^) offer the^ promise of general application, but,^ to^ obtain the^ full^ benefit^ for linkages (^) with more than (^) a few links, (^) they (^) require the use of (^) a computer. There^ have^ been^ three^ attempts to develop (^) computer-based methods applicable to (^) virtually all planar linkages. The first,^ called KOGEOP (KOppel-GEtriebe- OPtimierung), has^ been^ developed^ by^ Dresig (^) et al 12.5 (^) - 2. ý)^ for both (^) kinematic (^) synthesis and dynamic optimization (^) using a BESM-6^ computer. No^ indication of the^ size of the^ program (I^ reserve this^ spelling for computer (^) programs) is^ given, but^ it^ must be considerable (^) since the^ user has^ the^ choice of (^) eight optimization (^) routines. The (^) second, called KINSYN, has^ been^ developed by (^) Kaufman {2.8,2.91.^ The (^) original version used a precision point approach and (^) relied on^ the^ user^ being familiar (^) with Burmester theory. It (^) was designed^ for^ an
2-
IBM (^1130) computer with 8K^ words of core storage and a (^) storage tube^ display.^ Later^ it^ grew (^) until, by 1973, (^) it (^) consisted of (^) well over 15,000 (^) cards Of Fortran (^) and Assembler language (^) code. Since this is difficult (^) to (^) manage, a new version is being (^) developed to (^) make use (^) of a computer system with a (^) refresh-type graphical display^ (which^ is^ considerably (^) more expensive than (^) a storage tube display). The (^) most (^) ambitious attempt is^ that by^ Bona (^) et al {2.10). (^) This (^) consists of a (^) suite of (^27) programs (one of which is^ based^ on KINSYN).^ The^ scope is considerable, including,^ in^ addition to^ linkage^ synthesis and analysis, (^) cam and (^) gear design,^ stress and tolerance analysis, (^) automatic drafting^ and preparation of NC^ tapes. The intention^ was also to include^ a mechanism data^ bank but, (^) although this is (^) considered to be (^) feasible, it has been (^) discontinued (^) because (^) of lack (^) of storage space and
limited (^) availability (^) of suitable computer terminals. The package (^) uses (^) an IBM^1130 computer with 32K^ words of core storage (^) and (^) one million words (^) of disc^ storage (^) with an IBM (^2250) refresh-type graphic display. These (^) attempts, (^) which cater for^ only (^) planar linkages, all (^) require a large^ amount of computer (^) storage and two use refresh-type (^) graphic displays.^ This^ combination of facilities (^) is (^) not (^) generally available to (^) machine designers (^) in (^) this (^) country. The (^) use (^) of analogue, rather than digital,^ computers has (^) also been (^) advocated for (^) the kinematic (^) synthesis of planar linkages.^ Keller'f2^.^111 usdd an analogue computer to^ simulate a slider-crank mechanism and a four- bar (^) linkage. (^) Brat (^) and Vaclavik'f2.12) (^) synthesized a four-bar (^) linkage for (^) a crane (^) and Rees Jones'{2. synthesized (^) a (^) six-bar linkage^ for^ a power (^) press. There are two^ main (^) advantages. The^ first^ is^ speed of computation. Secondly,^ the^ user-can control the linkage (^) parameters directly (^) and (^) so determine (^) the (^) effect