
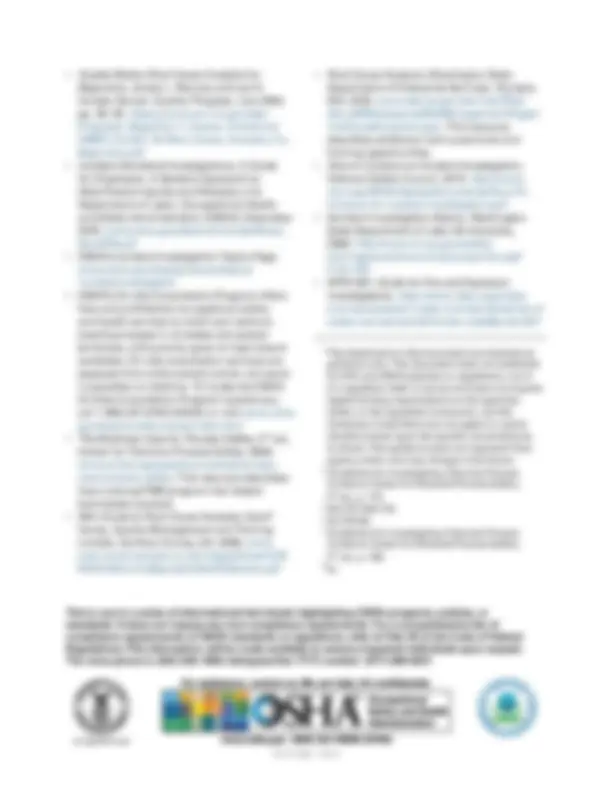
Study with the several resources on Docsity
Earn points by helping other students or get them with a premium plan
Prepare for your exams
Study with the several resources on Docsity
Earn points to download
Earn points by helping other students or get them with a premium plan
Community
Ask the community for help and clear up your study doubts
Discover the best universities in your country according to Docsity users
Free resources
Download our free guides on studying techniques, anxiety management strategies, and thesis advice from Docsity tutors
In this study, Employers covered by OSHA’s Process Safety Management (PSM) standard are required to investigate incidents that resulted in, or could reasonably have resulted in, catastrophic releases of highly hazardous chemicals.
Typology: Study notes
1 / 3
This page cannot be seen from the preview
Don't miss anything!
Employers covered by OSHA’s Process Safety Management (PSM) standard are required to investigate incidents that resulted in, or could reasonably have resulted in, catastrophic releases of highly hazardous chemicals.^3 Similarly, owners or operators of facilities regulated under EPA’s Risk Management Program (RMP) regulations must conduct incident investigations.^4 During an incident investigation, an employer must determine which factors contributed to the incident, and both OSHA and the EPA encourage employers to go beyond the minimum investigation required and conduct a root cause analysis. A root cause analysis allows an employer to discover the underlying or systemic , rather than the generalized or immediate , causes of an incident. Correcting only an immediate cause may eliminate a symptom of a problem, but not the problem itself.
A successful root cause analysis identifies all root causes—there are often more than one. Consider the following example: A worker slips on a puddle of oil on the plant floor and falls. A traditional investigation may find the cause to be “oil spilled on the floor” with the remedy limited to cleaning up the spill and instructing the worker to be more careful.^5 A root cause analysis would reveal that the oil on the floor was merely a symptom of a more basic, or fundamental problem in the workplace. An employer conducting a root cause analysis to determine whether there are systemic reasons for an incident should ask:
incident investigations on the non-lethal inci- dents and determined that operator error was the cause of the overfills and subsequent leaks. However, a proper root cause investigation would have looked deeper into the incident, and determined that funding cuts—which resulted in a deficient mechanical integrity program and malfunctioning instrumentation—led to a dangerous situation that operators could not have prevented. Had these root causes been previously identified, the employer could have taken action to improve the mechanical integrity program and repair the instrumentation system, preventing the fatal incident.
Conducting a thorough investigation that identifies root causes will help to prevent similar events from happening again. In this way, employers will reduce the risk of death and/or injury to workers or the community or environmental damage. By using root cause analysis to prevent similar events, employers can avoid unnecessary costs resulting from business interruption, emergency response and clean-up, increased regulation, audits, inspections, and OSHA or EPA fines. Regulatory fines can become costly, but litigation costs can often substantially exceed OSHA and EPA fines. Employers may find that they are spending money to correct immediate causes of incidents that could have been prevented, or reduced in severity or frequency, by identifying and correcting the underlying system management failure. Finally, when an employer focuses on prevention by using root cause analysis, public trust can be earned. Employers with an incident free record may be more likely to attract and retain high performing staff. A robust process safety program, which includes root cause analysis, can also result in more effective control of hazards, improved process reliability, increased revenues, decreased production costs, lower maintenance costs, and lower insurance premiums.
Below is a list of tools that may be used by employers to conduct a root cause analysis. The tools are not meant to be used exclusively. Ideally, a combination of tools will be used.