

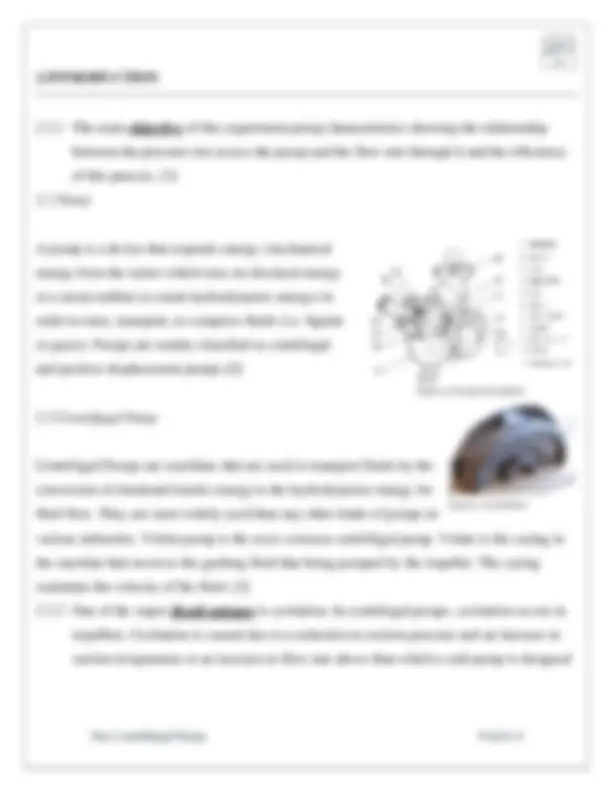
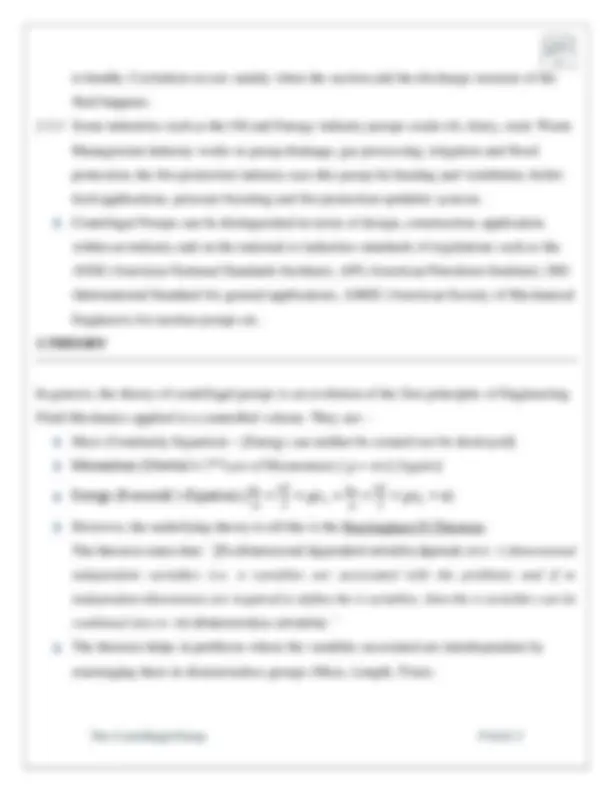
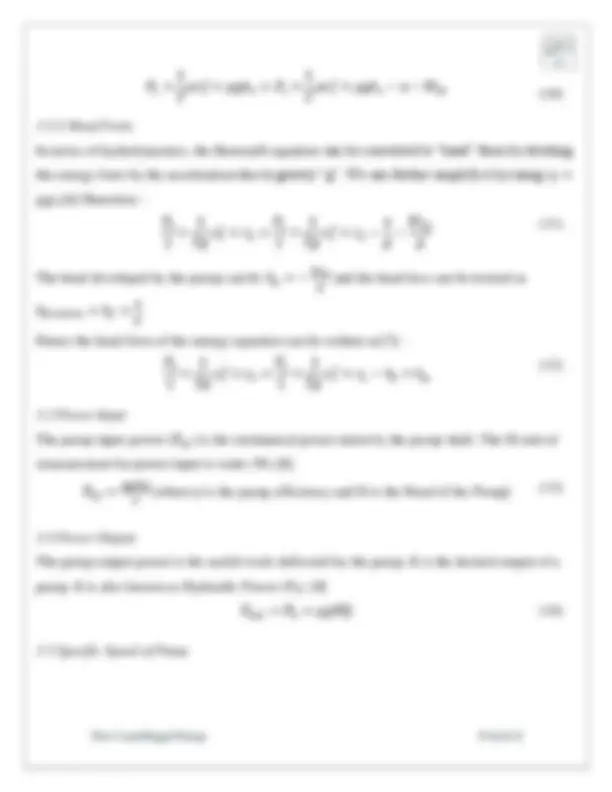

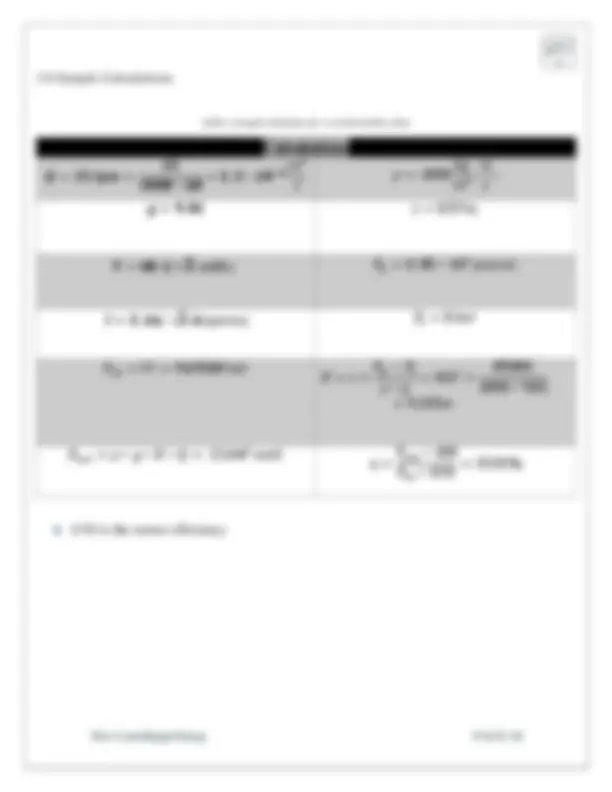
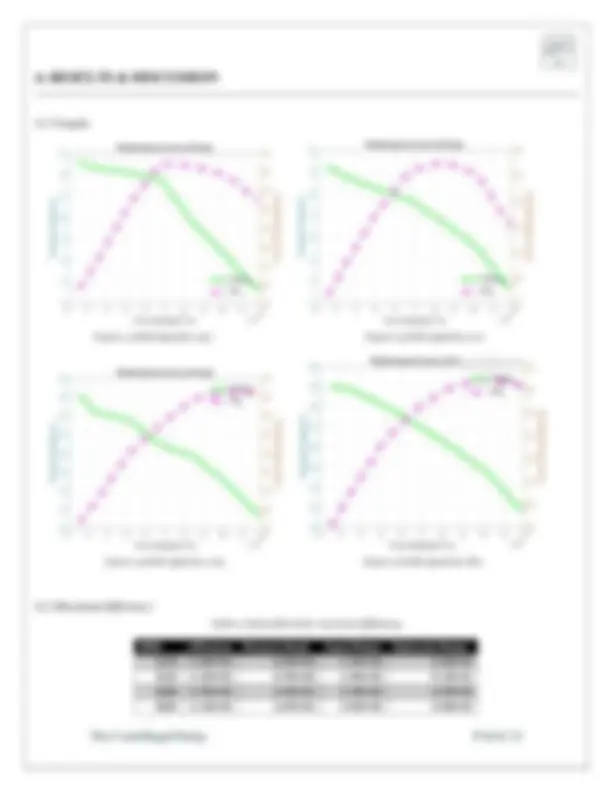
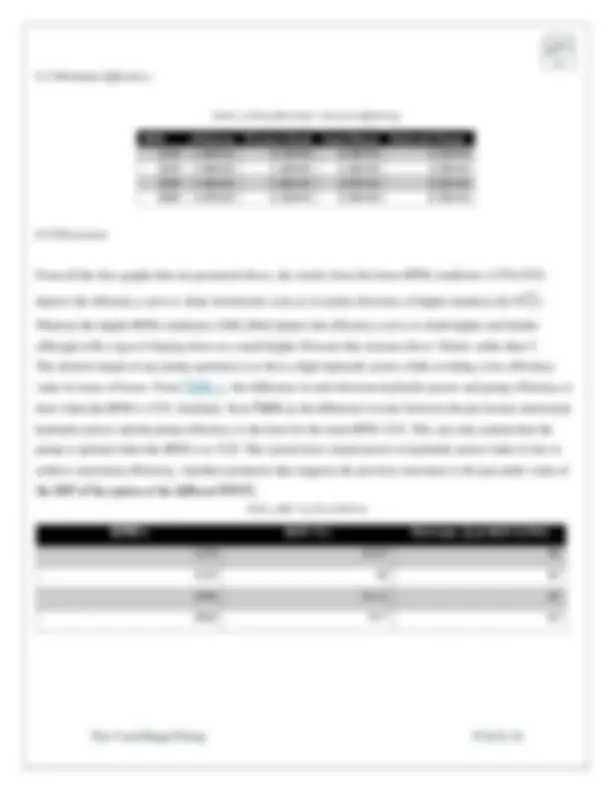
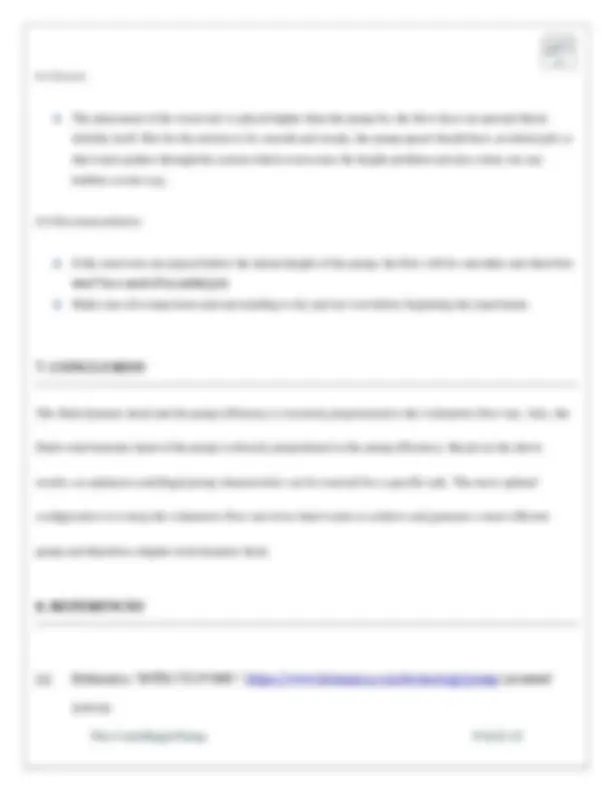

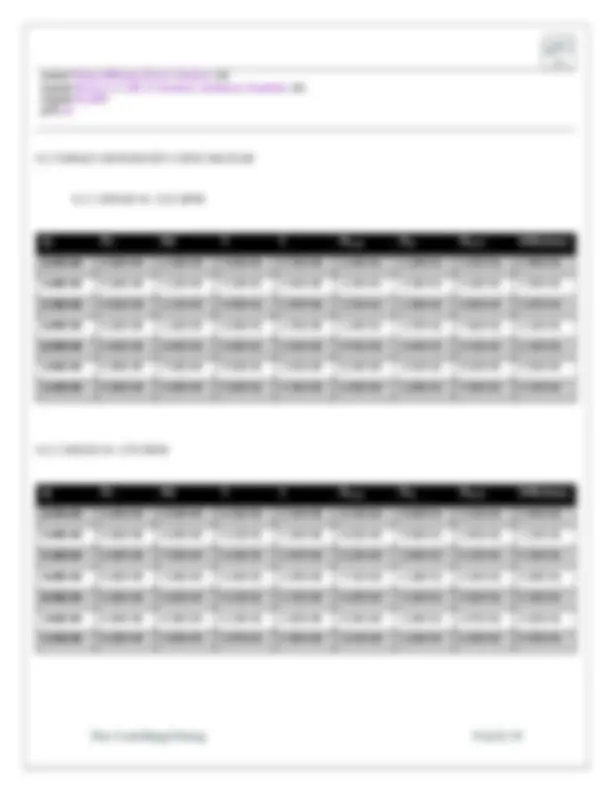

Study with the several resources on Docsity
Earn points by helping other students or get them with a premium plan
Prepare for your exams
Study with the several resources on Docsity
Earn points to download
Earn points by helping other students or get them with a premium plan
Community
Ask the community for help and clear up your study doubts
Discover the best universities in your country according to Docsity users
Free resources
Download our free guides on studying techniques, anxiety management strategies, and thesis advice from Docsity tutors
Mechanical Engineering Lab report on the centrifugal pump
Typology: Lab Reports
1 / 20
This page cannot be seen from the preview
Don't miss anything!
2.2.1 The main objective of this experiment pump characteristics showing the relationship
between the pressure rise across the pump and the flow rate through it and the efficiency
of this process. [1]
2 .1 Pump
A pump is a device that expends energy (mechanical
energy from the motor which runs on electrical energy
or a steam turbine to create hydrodynamic energy) in
order to raise, transport, or compress fluids (i.e. liquids
or gases). Pumps are mainly classified as centrifugal
and positive displacement pumps.[2]
2. 2 Centrifugal Pump
Centrifugal Pumps are machines that are used to transport fluids by the
conversion of rotational kinetic energy to the hydrodynamic energy for
fluid flow. They are more widely used than any other kinds of pumps in
various industries. Volute pump is the most common centrifugal pump. Volute is the casing in
the machine that receives the gushing fluid that being pumped by the impeller. The casing
maintains the velocity of the fluid. [3]
2.2.2 One of the major disadvantages is cavitation. In centrifugal pumps, cavitation occurs in
impellers. Cavitation is caused due to a reduction in suction pressure and an increase in
suction temperature or an increase in flow rate above than which a said pump is designed
Figure 1 Pump Description
Figure 2 Cavitation
to handle. Cavitation occurs mainly when the suction and the discharge moment of the
fluid happens.
2.2.3 Some industries such as the Oil and Energy industry pumps crude oil, slurry, mud. Waste
Management industry works to pump drainage, gas processing, irrigation and flood
protection; the fire protection industry uses this pump for heating and ventilation, boiler
feed applications, pressure boosting and fire protection sprinkler systems.
Centrifugal Pumps can be distinguished in terms of design, construction, application
within an industry and on the national or industries standards of regulations such as the
ANSI (American National Standards Institute), API (American Petroleum Institute), ISO
(International Standard for general application), ASME (American Society of Mechanical
Engineers) for nuclear pumps etc.
In genesis, the theory of centrifugal pumps is an evolution of the first principles of Engineering
Fluid Mechanics applied to a controlled volume. They are: -
Mass (Continuity Equation) – [Energy can neither be created nor be destroyed]
Momentum (Newton’s 2
nd
Law of Momentum) [ p = mv] {kgm/s]
Energy (Bernoulli’s Equation) [
𝑝
1
𝜌
𝑉
1
2
2
1
𝑝
2
𝜌
𝑉
2
2
2
2
However, the underlying theory to all this is the Buckingham Pi Theorem.
The theorem states that: “If a dimensional dependent variable depends on n - 1 dimensional
independent variables (i.e. n variables are associated with the problem) and if m
independent dimensions are required to define the n variables, then the n variables can be
combined into (n - m) dimensionless variables.”
The theorem helps in problems where the variables associated are interdependent by
rearranging them in dimensionless groups (Mass, Length, Time).
𝑠𝑦𝑠𝑡𝑒𝑚
2
2
1
1
The two pressures at both ends of the pipe are P 1
and P
The water at P 1
will do positive work
since the force points in the same direction as the motion of the fluid. The water at P 2
will do
negative work since it pushes in the opposite direction as the motion of the fluid.
Work can be found with, W = F*d (where, d is the length of the water
displaced by the pressure).
The force from the pressure, F= P*A ( 4 )
So, from (3) and (4), we can say that;
W=PAd ( 5 )
At the initial phase of the pipe, F 1
1
1
and at the final phase of the pipe, F 2
2
2
) as it is
in the opposite direction.
So, the work done at both ends will be W 1
1
1
*d 1
and W 2
2
2
*d 2
Substituting these equations in (1); we get 𝑃
1
1
1
2
2
2
𝑠𝑦𝑠𝑡𝑒𝑚
Since the volume flow rate (Q) must be maintained for an incompressible fluid, A 1
*d
1
2
*d
2
V. This further simplifies the above equation to
1
2
𝑠𝑦𝑠𝑡𝑒𝑚
Therefore, from equations (6) and (2);
1
2
2
2
1
1
If we substitute in the formulas for kinetic and gravitational potential energy, we get: -
1
2
2
2
2
1
2
1
1
As we rearrange the formula and simplify it further by noting that the density, ρ =
𝑚
𝑣
; we get: -
1
1
2
ρv
1
2
1
2
1
2
ρv
2
2
2
3.2.1 Energy Form
When this equation is applied to a fluid contained in a control volume fixed in space,
mechanical work is irreversibly transformed by fluid friction into heat, leading to “losses” (ɛ).
Also, the pump performs work on the fluid which runs on an input power (𝑊
𝐼𝑁
). Both losses
and input power are included in the energy form of the Bernoulli equation. [5] Therefore: -
2
2
2
2
1
1
2
1
− ɛ − 𝑊
𝐼𝑁
3.2.2 Head Form
In terms of hydrodynamics, the Bernoulli equation can be converted to “head” form by dividing
the energy form by the acceleration due to gravity “g”. We can further simplify it by using (γ =
𝜌𝑔).[6] Therefore: -
2
γ
2
2
2
1
γ
1
2
1
ɛ
𝐼𝑁
The head developed by the pump can be ℎ
𝑝
𝑊
𝐼𝑁
𝑔
and the head loss can be termed as
𝑓𝑟𝑖𝑐𝑡𝑖𝑜𝑛
𝑓
ɛ
𝑔
Hence the head form of the energy equation can be written as[7]: -
2
γ
2
2
2
1
γ
1
2
1
𝑓
𝑝
3.3 Power Input
The pump input power (𝑃
𝐼𝑁
) is the mechanical power taken by the pump shaft. The SI unit of
measurement for power input is watts (W).[8]
𝐼𝑁
𝜌𝑔𝐻𝑄
𝜂
[where 𝜂 is the pump efficiency and H is the Head of the Pump]
3.4 Power Output
The pump output power is the useful work delivered by the pump. It is the desired output of a
pump. It is also known as Hydraulic Power (P h
𝑜𝑢𝑡
ℎ
3.5 Specific Speed of Pump
3.6 Sample Calculations
Table 1 Sample Calulation for a random RPM value
−𝟒
3
3
𝐷
5
𝑠
𝐼𝑁
𝐷
𝑠
𝑜𝑢𝑡
𝑜𝑢𝑡
𝐼𝑁
0.92 is the motor efficiency
Figure 3 VFD Control
Panel
Figure 4 Voltage
Response Analyzer Figure 5 Rotameter
Figure 6 Wilo Pump
Figure 7 Tachometer
Drive control panel
with external control.
It’s a frequency
conversion device to
control any three
phase AC motor
under 1.5KW
Power Analyzer
to measure the
volt and ampere
that is used by
the pump.
flowmeter or rotameter
to measure the single-
phase flow of liquid or
gas.
pump with Q max =
14
𝒎
𝟑
ℎ
= 3. 89
𝒎
𝟑
𝑠
And H max
=47m
the RPM on the impeller
of the pump.
Figure 8 Pressure
Gauge
Figure 9 Suction
Reservoirs
Figure 10 Discharge
Reservoir
Figure 11 Pipelines Figure 12 Centrifugal Pump
Setup
Pressure gauge
reader
where the
returns
towards after
the initial
discharge
reservoir where the
water enters after it
leaves the
flowmeter.
and outlet
connections
for water onto
a reservoir
when connected
together as one setup.
6.1 Graphs
Figure 13 RPM Speed @ 1525 Figure 14 RPM Speed @ 1270
Figure 15 RPM Speed @ 2064 Figure 16 RPM Speed @ 1880
6.2 Maximum Efficiency
Table 2 Values filtered for maximum Efficiency
RPM efficiency Pressure Head Input Power Hydraulic Power
1270 5.28E+01 6.69E+00 1.15E+02 5.58E+
1525 6.22E+01 9.74E+00 1.44E+02 8.13E+
1880 5.74E+01 1.47E+01 2.79E+02 1.47E+
2064 6.13E+01 1.67E+01 3.45E+02 1.95E+
6.3 Minimum Efficiency
Table 3 Values filtered for minimum Efficiency
RPM efficiency Pressure Head Input Power Hydraulic Power
1270 2.64E+01 9.23E+00 9.50E+01 2.31E+
1525 2.90E+01 1.26E+01 1.18E+02 3.15E+
1880 2.50E+01 1.90E+01 2.07E+02 4.76E+
2064 2.67E+01 2.31E+01 2.35E+02 5.78E+
6.4 Discussion
From all the four graphs that are presented above, the results from the lower RPM conditions (1270,1525)
depicts the efficiency curve to slope downwards soon as it reaches flowrates of higher numbers (Q> 5
𝑚
3
𝑠
).
Whereas the higher RPM conditions (1880,2064) depicts the efficiency curve to climb higher and farther
although with a sign of sloping down at a much higher flowrate that streams above 10units rather than 5.
The desired output of any pump operation is to have a high hydraulic power while avoiding a low efficiency
value in terms of losses. From Table 2 , the difference in ratio between hydraulic power and pump efficiency is
least when the RPM is 1525. Similarly, from Table 3 , the difference in ratio between the previously mentioned
hydraulic power and the pump efficiency is the least for the same RPM 1525. This can only explain that the
pump is optimal when the RPM is at 1525. The system loses output power or hydraulic power when it tries to
achieve maximum efficiency. Another parameter that supports the previous statement is the percentile value of
the BEP of the system at the different RPM’S,
Table 4 BEP's of all conditions
RPM’s BEP (%) Flowrate, Q at BEP (LPM)
1270 23.67 60
1525 26 65
1880 19.12 65
2064 19.7 65
[2] Tuthill. "Pump Types." https://www.tuthillpump.com/dam/2525.pdf (accessed 5.12.19.
[3] Thermal_Engineering. "intro to centrifugal pumps." https://www.thermal-
engineering.org/what-is-centrifugal-pump-definition/ (accessed 5.12.19.
[4] Khan_Academy. "Bernoulli's Equation."
https://www.khanacademy.org/science/physics/fluids/fluid-dynamics/a/what-is-bernoullis-
equation (accessed 5.12.19.
[5] Science_Direct. https://www.sciencedirect.com/topics/engineering/bernoulli-equation
(accessed 5.12.19.
[6] Clarkson. "Bernoulli for Hydrodynamics."
https://web2.clarkson.edu/projects/subramanian/ch330/notes/Engineering%20Bernoulli%
0Equation.pdf (accessed 5.12.19.
[7] Energy_Education. "Bernoulli Equation."
https://energyeducation.ca/encyclopedia/Bernoulli%27s_equation (accessed 5.12.19.
[8] ksb. "Power Input Centrifugal Pump." https://www.ksb.com/centrifugal-pump-lexicon/power-
input/191088/ (accessed.
[9] thermexcel. "pumps." https://www.ksb.com/centrifugal-pump-lexicon/power-input/191088/
(accessed 5.12.19.
[10] neutrium. "pump power calculation." https://neutrium.net/equipment/pump-power-
calculation/ (accessed 5.12.19.
9 .1 CALCULATIONS MADE IN MATLAB
%% Exerimental Results and Calculations %%
% General Data Required %
g = 9.81 ; % gravitational acceleration (m/s^2) %
rho = 1000; % Water Density (kg/m^3)%
zd = .57 ; % Outlet above the Datum (m) %
zs = 0 ; % Inlet on the Datum (m) %
Ps = [0,0,0,0,0,0,0]'; % Suction Pressure (Pa) %
Q = [15,20,30,40,50,60,70]'.0.000017; %Flow Rate Values%*
Eff_motor = 0.92; % Motor Efficiency (92%) %
% Results for set conditions%
% At N_1 = 1525 RPM %
Pd_1 = [1.18,1.15,1.13,1.1,0.9,0.75,0.59]'.10e4;*
V_1 = [71.93,72.82,72,71.9,71.8,71.02,71.95]'./sqrt(2);
I_1 = [3.29,3.45,3.602,3.82,4.0, 4.26,4.44]'/sqrt(2);
Head_P_1 = (((Pd_1-Ps))./(rhog))+(zd-zs);*
P_in_1 = V_1.I_1;*
Hyd_P_1 = rho.g.Head_P_1.Q;*
Eff_1 = ((Hyd_P_1)./(P_in_1.0.92))100;**
T1 = table(Q,Ps,Pd_1,V_1,I_1,Head_P_1,P_in_1,Hyd_P_1,Eff_1);
% At N_2 = 1270 RPM %
Pd_2 = [0.85,0.809,0.75,0.7,0.6,0.49,0.3]'.10e4;*
V_2 = [60.1,59.84,59.96,59.95,59.82,59.79,54.8]'./sqrt(2);
I_2 = [3.16,3.31,3.47,3.66,3.84,4.03,4.17]'./sqrt(2);
Head_P_2 = (((Pd_2-Ps))/(rhog))+(zd-zs);*
P_in_2 = V_2.I_2;*
Hyd_P_2 = rho.g.Head_P_2.Q;*
Eff_2 = ((Hyd_P_2)./(P_in_20.92))100;**
T2 = table(Q,Ps,Pd_2,V_2,I_2,Head_P_2,P_in_2,Hyd_P_2,Eff_2);
% At N_3 = 2064 RPM %
Pd_3 = [2.21,2.12,2.08,1.95,1.89,1.75,1.58]'.10e4;*
V_3 = [136.51,136.4,136.38,136.28,136.19,136.1,135.98]'./sqrt(2);
I_3 = [3.45,3.686,3.871,4.128,4.445,4.819,5.076]'./sqrt(2);
Head_P_3 = (((Pd_3-Ps))./(rhog))+(zd-zs);*
P_in_3 = V_3.I_3;*
Hyd_P_3 = rho.g.Head_P_3.Q;*
Eff_3 = ((Hyd_P_3)./(P_in_3.0.92))100;**
T3 = table(Q,Ps,Pd_3,V_3,I_3,Head_P_3,P_in_3,Hyd_P_3,Eff_3);
ylabel('Pump Efficiency[Eeta]','fontsize',12)
legend('Head_P_3','Eff_3','location','northeast','FontSize',12)
legend('boxoff')
grid on
9 .2 TABLES GENERATED USING MATLAB
9 .2.1 SPEED @ 1525 RPM
Q Ps Pd V I P head
P IN
P HYD
Efficiency
2.55E- 04 0.00E+00 1.18E+05 5.09E+01 2.33E+00 1.26E+01 1.18E+02 3.15E+01 2.90E+
3.40E- 04 0.00E+00 1.15E+05 5.15E+01 2.44E+00 1.23E+01 1.26E+02 4.10E+01 3.55E+
5.10E- 04 0.00E+00 1.13E+05 5.09E+01 2.55E+00 1.21E+01 1.30E+02 6.05E+01 5.07E+
6.80E- 04 0.00E+00 1.10E+05 5.08E+01 2.70E+00 1.18E+01 1.37E+02 7.86E+01 6.22E+
8.50E- 04 0.00E+00 9.00E+04 5.08E+01 2.83E+00 9.74E+00 1.44E+02 8.13E+01 6.15E+
1.02E- 03 0.00E+00 7.50E+04 5.02E+01 3.01E+00 8.22E+00 1.51E+ 02 8.22E+01 5.91E+
1.19E- 03 0.00E+00 5.90E+04 5.09E+01 3.14E+00 6.58E+00 1.60E+02 7.69E+01 5.23E+
9 .2. 2 SPEED @ 1 270 RPM
Q Ps Pd V I P head
P IN
P HYD
Efficiency
2.55E- 04 0.00E+00 8.50E+04 4.25E+01 2.23E+00 9.23E+00 9.50E+01 2.31E+01 2.64E+
3.40E- 04 0.00E+00 8.09E+04 4.23E+01 2.34E+00 8.82E+00 9.90E+01 2.94E+01 3.23E+
5.10E- 04 0.00E+00 7.50E+04 4.24E+01 2.45E+00 8.22E+00 1.04E+02 4.11E+01 4.29E+
6.80E- 04 0.00E+00 7.00E+04 4.24E+01 2.59E+00 7.71E+00 1.10E+02 5.14E+01 5.09E+
8.50E- 04 0.00E+ 00 6.00E+04 4.23E+01 2.72E+00 6.69E+00 1.15E+02 5.58E+01 5.28E+
1.02E- 03 0.00E+00 4.90E+04 4.23E+01 2.85E+00 5.56E+00 1.20E+02 5.57E+01 5.02E+
1.19E- 03 0.00E+00 3.00E+04 3.87E+01 2.95E+00 3.63E+00 1.14E+02 4.24E+01 4.03E+
9 .2. 3 SPEED @ 2064 RPM
Q Ps Pd V I P head
P IN
P HYD
Efficiency
2.55E- 04 0.00E+00 2.21E+05 9.65E+01 2.44E+00 2.31E+01 2.35E+02 5.78E+01 2.67E+
3.40E- 04 0.00E+00 2.12E+05 9.64E+01 2.61E+00 2.22E+01 2.51E+02 7.40E+01 3.20E+
5.10E- 04 0.00E+00 2.08E+05 9.64E+01 2.74E+00 2.18E+01 2.64E+02 1.09E+02 4.49E+
6.80E- 04 0.00E+00 1.95E+05 9.64E+01 2.92E+00 2.04E+01 2.81E+02 1.36E+02 5.27E+
8.50E- 04 0.00E+00 1.89E+05 9.63E+01 3.14E+00 1.98E+01 3.03E+02 1.65E+02 5.94E+
1.02E- 03 0.00E+00 1.75E+05 9.62E+01 3.41E+00 1.84E+01 3.28E+02 1.84E+02 6.11E+
1.19E- 03 0.00E+00 1.58E+05 9.62E+01 3.59E+00 1.67E+01 3.45E+02 1.95E+02 6.13E+
9 .2. 4 SPEED @ 1 880 RPM
Q Ps Pd V I P head
P IN
P HYD
Efficiency
2.55E- 04 0.00E+00 1.81E+05 8.49E+01 2.43E+00 1.90E+01 2.07E+02 4.76E+01 2.50E+
3.40E- 04 0.00E+00 1.80E+05 8.48E+01 2.56E+00 1.89E+01 2.17E+02 6.31E+01 3.16E+
5.10E- 04 0.00E+00 1.72E+05 8.47E+01 2.68E+00 1.81E+01 2.27E+02 9.06E+01 4.34E+
6.80E- 04 0.00E+00 1.62E+05 8.46E+01 2.87E+00 1.71E+01 2.42E+02 1.14E+02 5.11E+
8.50E- 04 0.00E+00 1 .51E+05 8.46E+01 3.07E+00 1.60E+01 2.60E+02 1.33E+02 5.57E+
1.02E- 03 0.00E+00 1.39E+05 8.45E+01 3.30E+00 1.47E+01 2.79E+02 1.47E+02 5.74E+
1.19E- 03 0.00E+00 1.20E+05 8.45E+01 3.45E+00 1.28E+01 2.91E+02 1.49E+02 5.57E+