
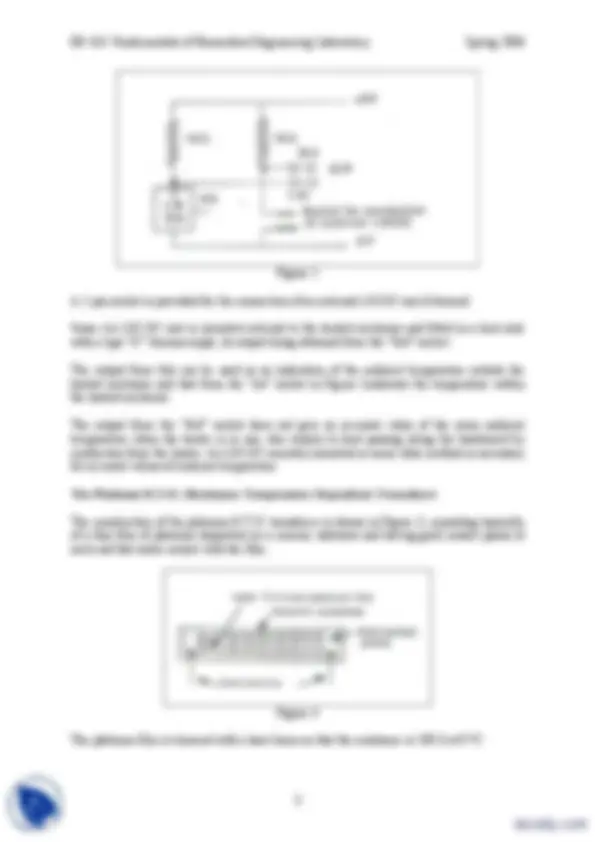
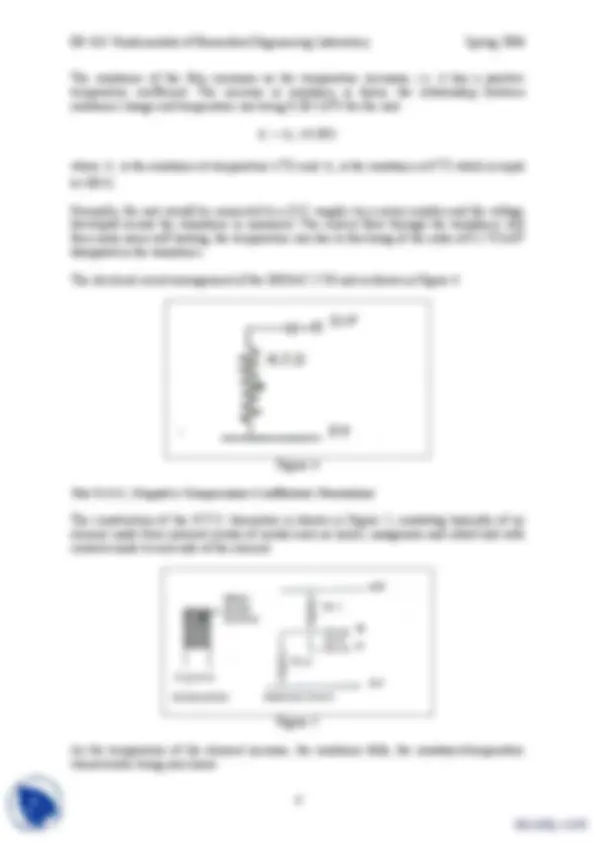
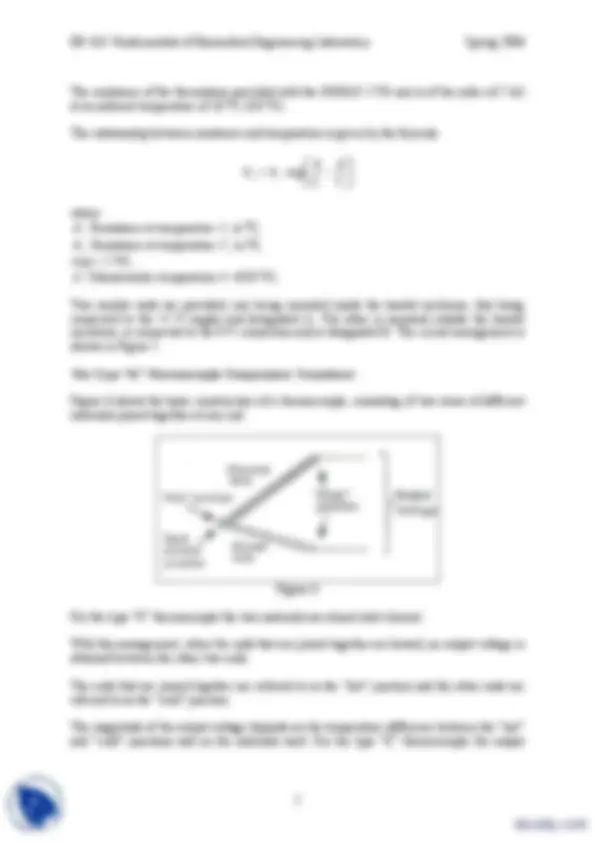
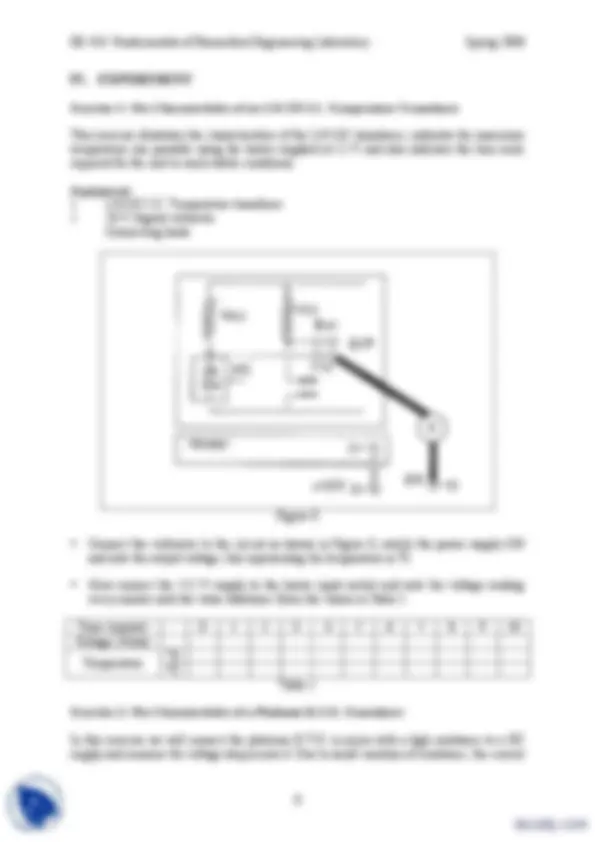
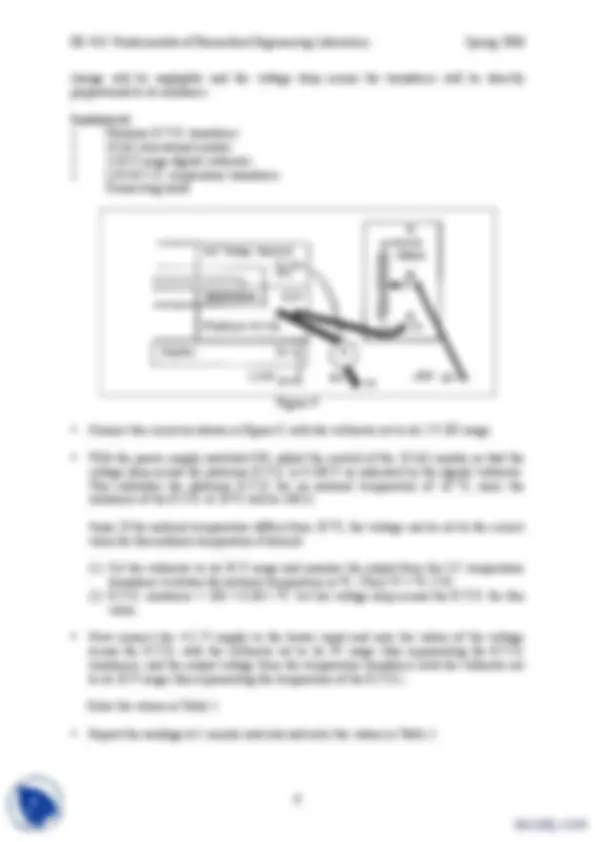
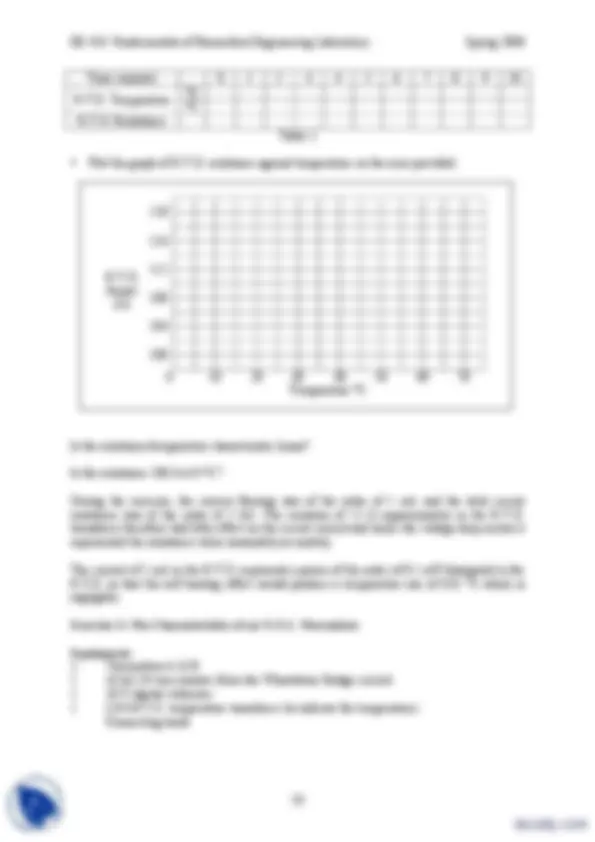
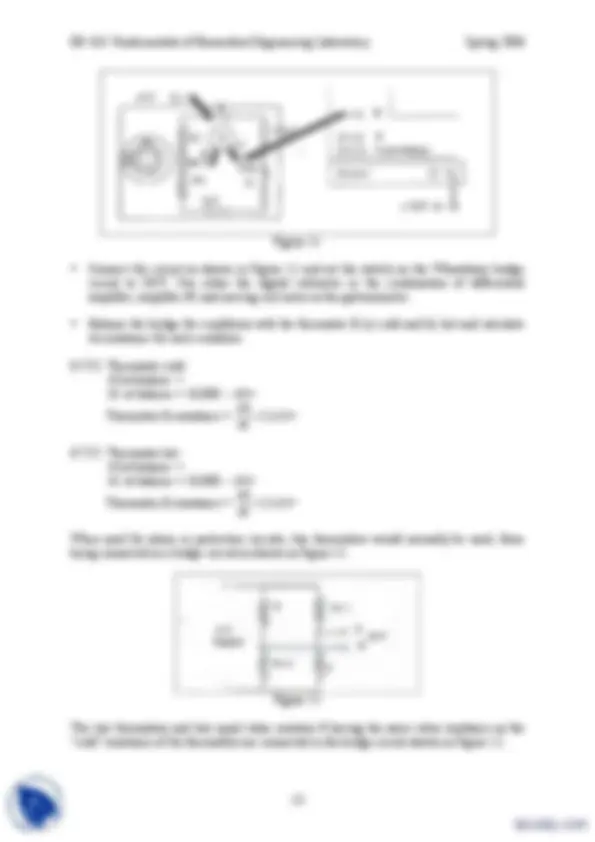
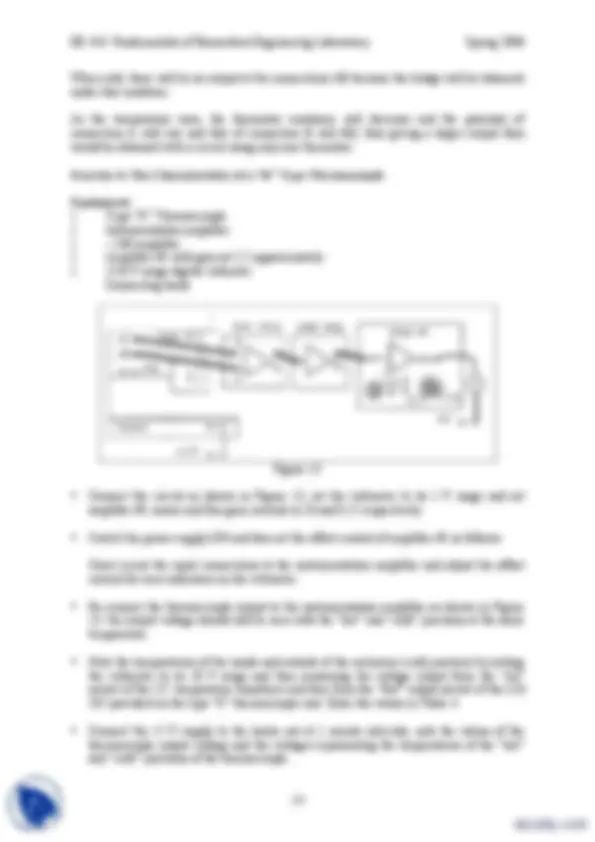
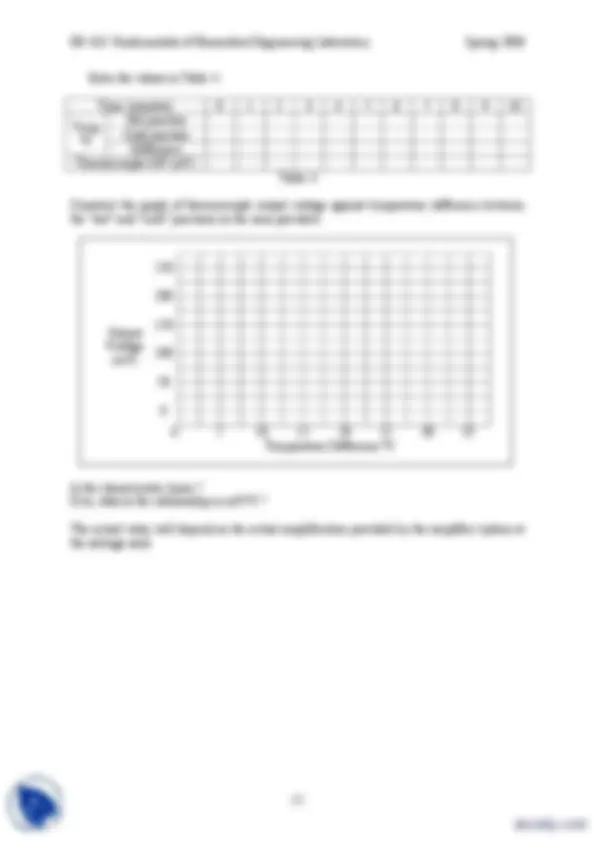
Study with the several resources on Docsity
Earn points by helping other students or get them with a premium plan
Prepare for your exams
Study with the several resources on Docsity
Earn points to download
Earn points by helping other students or get them with a premium plan
Community
Ask the community for help and clear up your study doubts
Discover the best universities in your country according to Docsity users
Free resources
Download our free guides on studying techniques, anxiety management strategies, and thesis advice from Docsity tutors
This lab manual is for Mesaurement and Instrumentation lab. It was provided by Naresh Nair at Kannur University. It includes: Temperature, Transducers, Sensing, Device, Coefficient, Nonlinear, Material, Constant, Wheatstone, Bridge
Typology: Exercises
1 / 15
This page cannot be seen from the preview
Don't miss anything!
Objectives: To understand the operation of thermistors and realization of a temperature sensing device, to study the basic characteristics of an I.C. temperature transducer, platinum R.T.D. resistance transducer, N.T.C. thermistor and a thermocouple.
Equipment: Digiac 1750, digital voltmeter.
Average Time to Complete: 2.5 hrs.
Prerequisites: Familiarity with thermistors.
Thermistors are essentially semiconductor devices which behave as thermal resistors having a high negative temperature coefficient of resistance. The sensors are made of sintered ceramics, usually from mixtures of oxides iron, manganese, nickel, cobalt and copper in the form of beads or discs. The resistance value at ambient temperature may range from 100 Ω to 100 kΩ. The variation of resistance with temperature is nonlinear, decreasing with temperature.
The resistance R (^) t of a thermistor at a temperature T can be expressed by the equation
where β is the material constant for the thermistor (K) and is the standard reference
temperature (K).
as,
dT
dR R
t t
The resistance vs. temperature characteristics of the thermistors, can be linearized by shunting it with a proper resistor R (^) p. The value of Rp for a desired temperature can be
Because of its small size, thermistors are ideally suited for measuring temperature distributions or gradients. The measurement of the change in resistance can be carried out with a standard Wheatstone bridge.
The DIGIAC 1750 Temperature Transducer Facilities
Figure 1 shows the layout of the temperature transducer facilities of the DIGIAC 1750 unit.
The active transducers are contained within a clean plastic container which includes a heater.
In the case of the N.T.C. thermistors and the thermocouples, a separate unit is mounted outside the heated enclosure.
Figure 1
The I.C. Temperature Transducer
This is an integrated circuit containing 16 transistors, 9 resistors and 2 capacitors contained in a transistor type package.
The device reference number is LM 335 and it provides an output of 10 mV/oK. A measurement of the output voltage therefore indicates the temperature directly in oK. For example, at a temperature of 20 oC (293 oK), the output voltage will be 2.93 V.
The circuit arrangement provided with the DIGIAC 1750 unit is shown in Figure 2.
The resistance of the film increases as the temperature increases, i.e. it has a positive temperature coefficient. The increase in resistance is linear, the relationship between resistance change and temperature rise being 0.385 Ω/oC for the unit.
Rt = R 0 + 0. 385 t
where Rt is the resistance at temperature t (oC) and R 0 is the resistance at 0oC which is equal
to 100 Ω.
Normally, the unit would be connected to a D.C. supply via a series resistor and the voltage developed across the transducer is measured. The current flow through the transducer will then cause some self heating, the temperature rise due to this being of the order of 0.2 oC/mW dissipated in the transducer.
The electrical circuit arrangement of the DIGIAC 1750 unit is shown in Figure 4.
Figure 4
The N.T.C. (Negative Temperature Coefficient) Thermistor
The construction of the N.T.C. thermistor is shown in Figure 5, consisting basically of an element made from sintered oxides of metals such as nickel, manganese and cobalt and with contacts made to each side of the element.
Figure 5
As the temperature of the element increase, the resistance falls, the resistance/temperature characteristic being non-linear.
The resistance of the thermistors provided with the DIGIAC 1750 unit is of the order of 5 kΩ at an ambient temperature of 20 oC (293 oK).
The relationship between resistance and temperature is given by the formula:
2 1
2 1 exp^ T
where R 1 : Resistance at temperature T 1 in oK,
R (^) 2 : Resistance at temperature T 2 in oK, exp = 2. 718 , B : Characteristic temperature (= 4350 oK).
Two similar units are provided, one being mounted inside the heated enclosure, this being connected to the +5 V supply and designated A. The other is mounted outside the heated enclosure, is connected to the 0 V connection and is designated B. The circuit arrangement is shown in Figure 5.
The Type “K” Thermocouple Temperature Transducer
Figure 6 shows the basic construction of a thermocouple, consisting of two wires of different materials joined together at one end.
Figure 6
For the type “K” thermocouple the two materials are alumel and chromel.
With this arrangement, when the ends that are joined together are heated, an output voltage is obtained between the other two ends.
The ends that are joined together are referred to as the “hot” junction and the other ends are referred to as the “cold” junction.
The magnitude of the output voltage depends on the temperature difference between the “hot” and “cold” junctions and on the materials used. For the type “K” thermocouple the output
III. PRELIMINARY WORK
R p oC.
a. 0 oC. b. 50 oC. c. -20 oC.
a. What would be its resistance 50 oC? b. What temperature would be represented by a resistance of 115.2 Ω?
a. 4 kΩ b. 3 kΩ c. 1.8 kΩ
Cold Hot a. 0 oC 50 oC b. 20 oC 70 oC c. 50 oC 50 oC d. -20 oC 60 oC
What amplifier gain would be required to enable the thermocouple to produce an output of 1V for a temperature difference of 100 oC between the “hot” and “cold” junctions?
IV. EXPERIMENT
Exercise 1: The Characteristics of an LM 335 I.C. Temperature Transducer
This exercise illustrates the characteristics of the LM 335 transducer, indicates the maximum temperature rise possible using the heater supplied at 12 V and also indicates the time scale required for the unit to reach stable conditions.
Equipment: 1 LM 335 I.C. Temperature transducer 1 20 V Digital voltmeter Connecting leads
Figure 8
Connect the voltmeter to the circuit as shown in Figure 8, switch the power supply ON and note the output voltage, this representing the temperature in oK.
Now connect the +12 V supply to the heater input socket and note the voltage reading every minute until the value stabilizes. Enter the values in Table 1.
Time (minute) 0 1 2 3 4 5 6 7 8 9 10 Voltage (Volts) oK Temperature (^) o C Table 1
Exercise 2: The Characteristics of a Platinum R.T.D. Transducer
In this exercise we will connect the platinum R.T.D. in series with a high resistance to a DC supply and measure the voltage drop across it. Due to small variation of resistance, the current
Time (minute) 0 1 2 3 4 5 6 7 8 9 10 oK R.T.D. Temperature (^) o C R.T.D. Resistance Table 2
Plot the graph of R.T.D. resistance against temperature on the axes provided.
Resist. (Ω)
Temperature oC
Is the resistance/temperature characteristic linear?
Is the resistance 100 Ω at 0 oC?
During the exercise, the current flowing was of the order of 1 mA and the total circuit resistance was of the order of 5 kΩ. The variation of 12 Ω approximately in the R.T.D. transducer therefore had little effect on the circuit current and hence the voltage drop across it represented the resistance value reasonably accurately.
The current of 1 mA in the R.T.D. represents a power of the order of 0.1 mW dissipated in the R.T.D. so that the self heating effect would produce a temperature rise of 0.02 oC which is negligible.
Exercise 3: The Characteristics of an N.T.C. Thermistor
Equipment: 2 Thermistors A & B 1 10 kΩ 10 turn resistor (from the Wheatstone Bridge circuit) 1 20 V digital voltmeter 1 LM 335 I.C. temperature transducer (to indicate the temperature) Connecting leads
Resistance measurement method
The resistance of the N.T.C. thermistor varies over the range 5 kΩ to 1.5 kΩ approximately for the temperature range available within the heated enclosure for an ambient temperature of 20 oC. For this large range we cannot use the method we used in exercise 2 to measure the resistance. Also if readings are to be taken at regular intervals of 1 minute, the readings of resistance must be obtained with the minimum of time.
The method used connects the thermistor in series with a calibrated resistor to the +5 V supply. For each reading, the variable resistor is adjusted until the voltage at the junction of the thermistor and the resistor is half the supply value. For this setting, there will be the same voltage drop across the thermistor and the resistor and their resistances will be equal, and hence the value of the resistance read from the calibrated resistor scale represents the resistance of the thermistor.
Figure 10
Connect the circuit as shown in Figure 10, set the switch on the Wheatstone bridge circuit to OUT to disconnect the 12 kΩ and Rx resistors from the circuit and set the resistor dial reading to 500 approximately.
Switch the power supply ON, adjust the resistor control until the voltage indicated by the voltmeter is 2.5 V and then note the dial reading and the temperature, by connecting the voltmeter temporarily to the “Int” socket of the I.C. temperature transducer.
Note: Since there is a 1 kΩ resistor in the output lead of the resistance, the total resistance in the resistance circuit will be of value (10 × Dial reading + 1 kΩ).
Enter the values of dial reading and temperature in Table 3.
Now connect the 12 V supply to the heater input socket and, at 1 minute intervals, note the values of the dial reading to produce 2.5 V across the resistance and also the temperature. Enter the values in Table 3.
Figure 11
Connect the circuit as shown in Figure 11 and set the switch on the Wheatstone bridge circuit to OUT. Use either the digital voltmeter or the combination of differential amplifier, amplifier #1 and moving coil meter as the galvanometer.
Balance the bridge for conditions with the thermistor B (a) cold and (b) hot and calculate its resistance for each condition.
N.T.C. Thermistor cold: R 3 at balance = R 1 at balance = 10,000 – R 3 =
Thermistor B resistance = × k Ω R
N.T.C. Thermistor hot: R 3 at balance = R 1 at balance = 10,000 – R 3 =
Thermistor B resistance = × k Ω R
When used for alarm or protection circuits, two thermistors would normally be used, these being connected in a bridge circuit as shown in Figure 12.
Figure 12
The two thermistors and two equal value resistors R having the same value resistance as the “cold” resistance of the thermistors are connected in the bridge circuit shown in Figure 12.
When cold, there will be no output at the connections AB because the bridge will be balanced under this condition.
As the temperature rises, the thermistor resistance will decrease and the potential of connection A will rise and that of connection B will fall, thus giving a larger output than would be obtained with a circuit using only one thermistor.
Exercise 4: The Characteristics of a “K” Type Thermocouple
Equipment: 1 Type “K” Thermocouple 1 Instrumentation amplifier 1 ×100 amplifier 1 Amplifier #1 with gain set 2.5 approximately 1 2/20 V range digital voltmeter Connecting leads
Figure 13
Connect the circuit as shown in Figure 13, set the voltmeter to its 2 V range and set amplifier #1 coarse and fine gain controls to 10 and 0.25 respectively.
Switch the power supply ON and then set the offset control of amplifier #1 as follows:
Short circuit the input connections to the instrumentation amplifier and adjust the offset control for zero indication on the voltmeter.
Re-connect the thermocouple output to the instrumentation amplifier as shown in Figure
Note the temperatures of the inside and outside of the enclosure (cold junction) by setting the voltmeter to its 20 V range and then measuring the voltage output from the “Int” socket of the I.C. temperature transducer and then from the “Ref” output socket of the LM 335 provided on the type “K” thermocouple unit. Enter the values in Table 4.
Connect the 12 V supply to the heater ant at 1 minute intervals, note the values of the thermocouple output voltage and the voltages representing the temperatures of the “hot” and “cold” junctions of the thermocouple.