
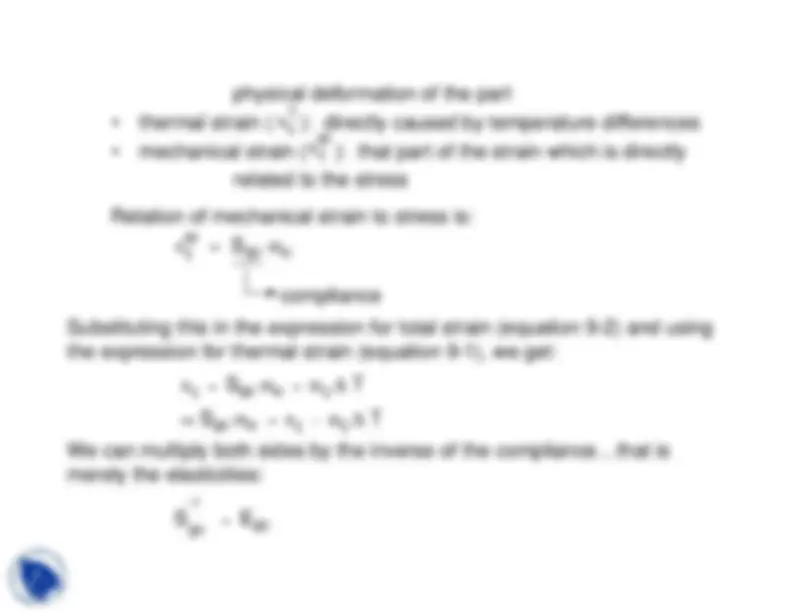
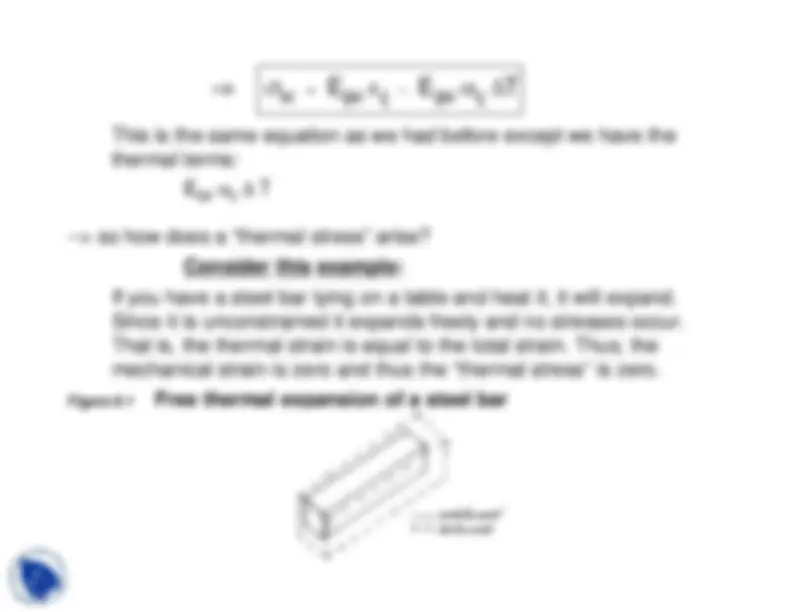
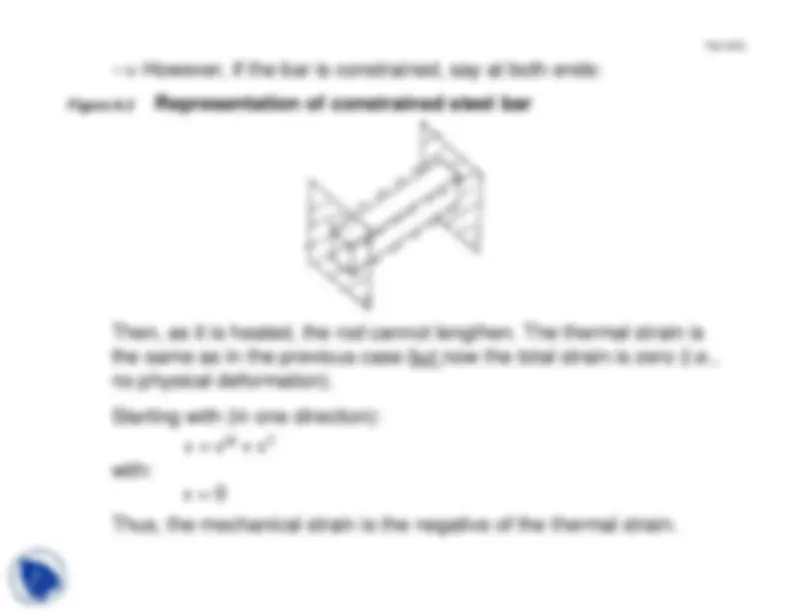
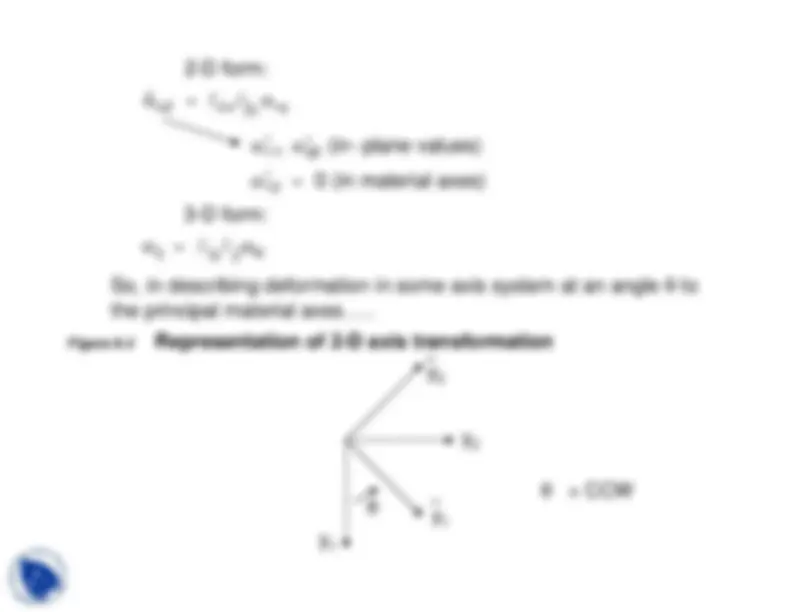
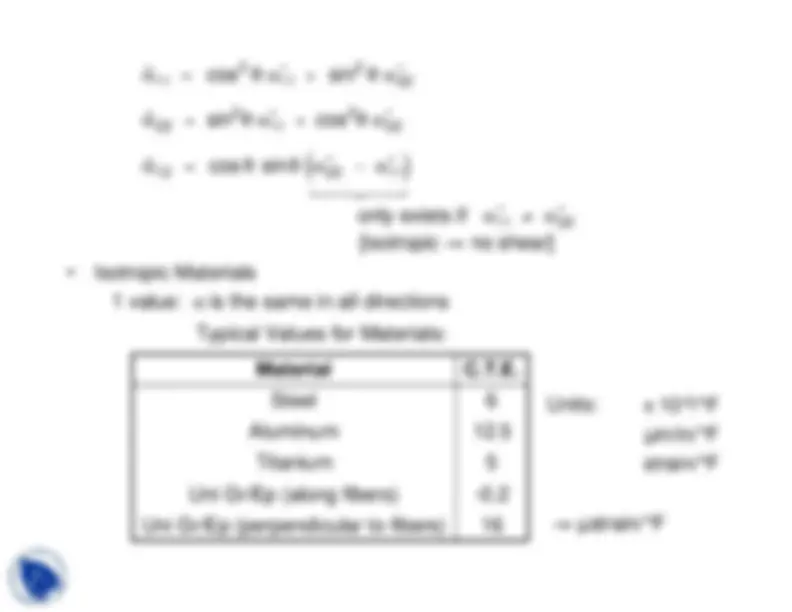
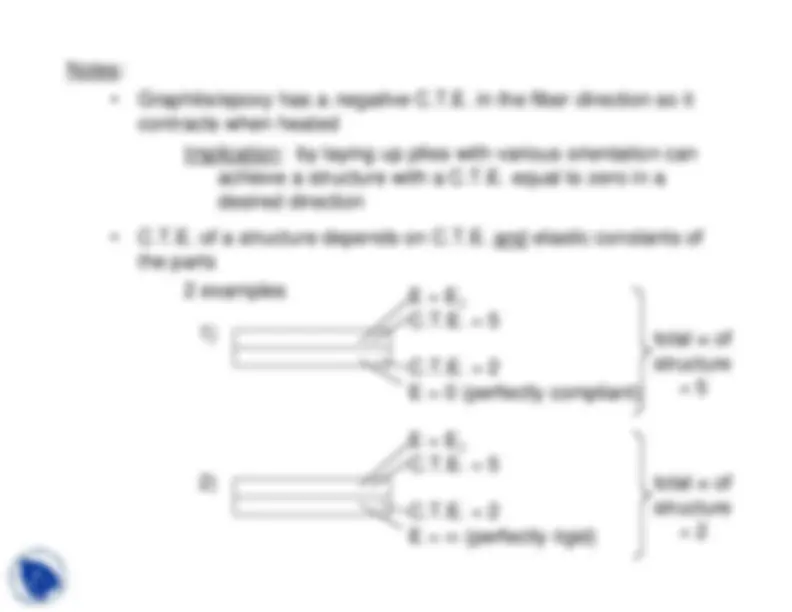
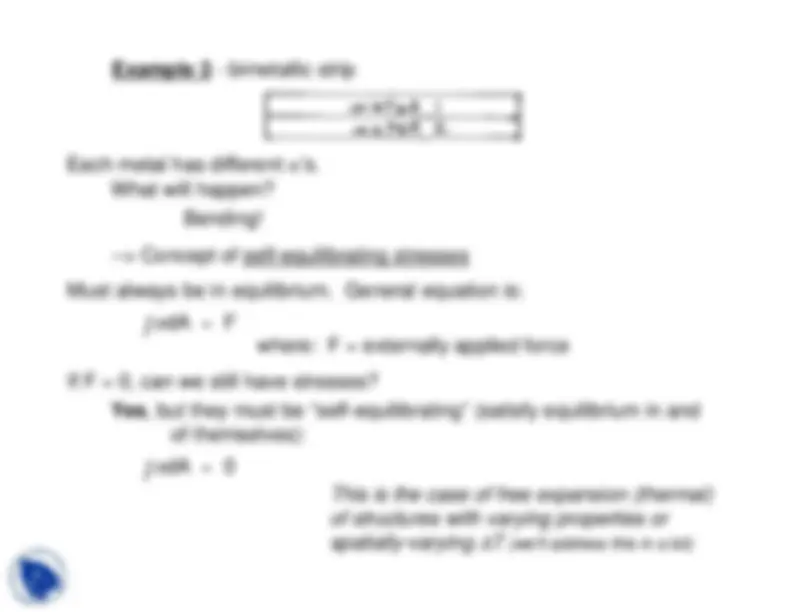
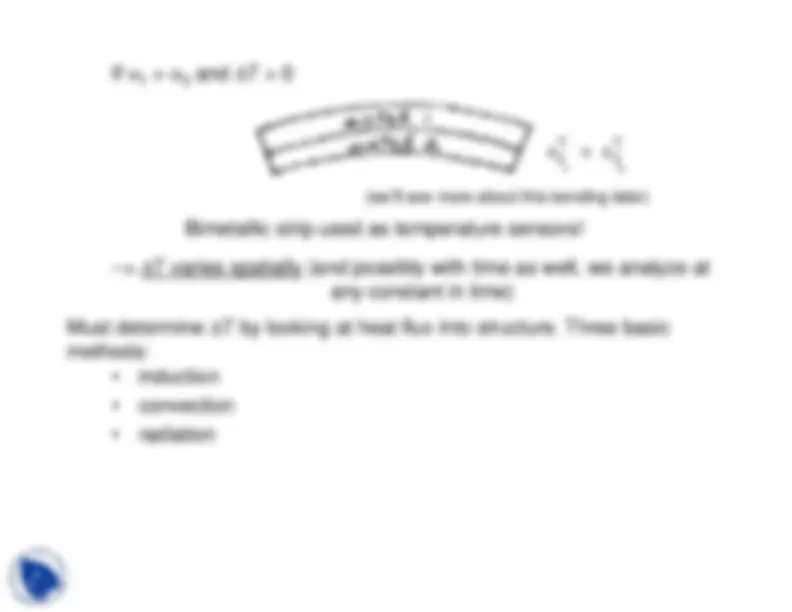
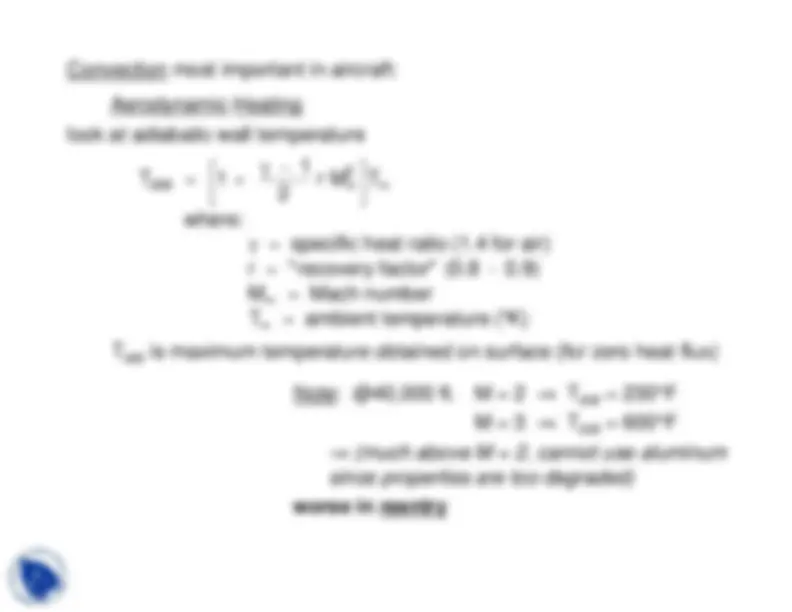
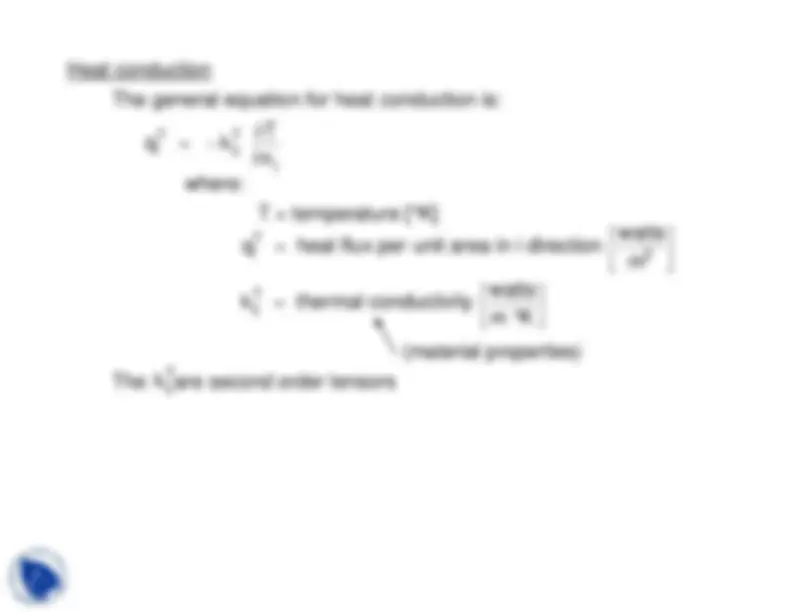
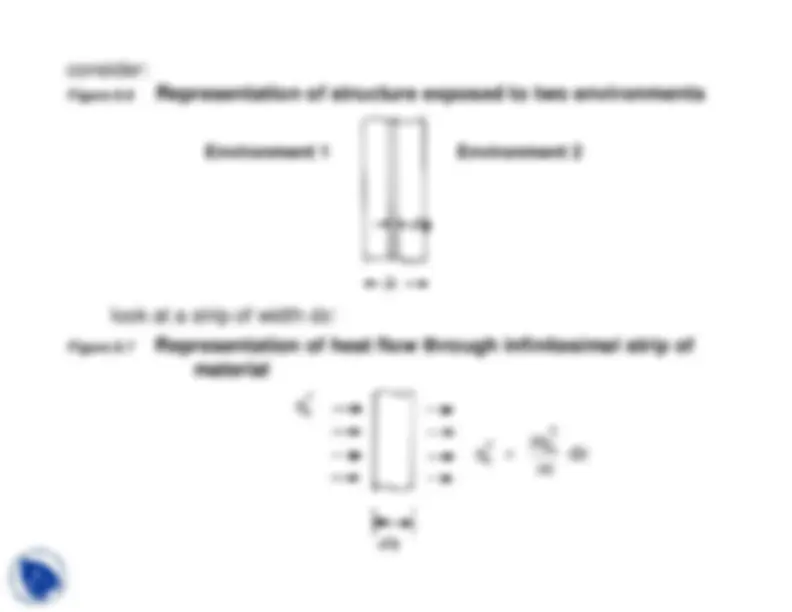
Study with the several resources on Docsity
Earn points by helping other students or get them with a premium plan
Prepare for your exams
Study with the several resources on Docsity
Earn points to download
Earn points by helping other students or get them with a premium plan
Community
Ask the community for help and clear up your study doubts
Discover the best universities in your country according to Docsity users
Free resources
Download our free guides on studying techniques, anxiety management strategies, and thesis advice from Docsity tutors
This lecture note is part of Material and Structures course. It was provided by Prof. Aparijita Singh at Andhra University. It includes: Temperature, Effects, Expansion, Contraction, Change, properties, Coefficient, Thermal, Strain, Mechanical, Elasticity, Compliance, Unconstrained, Deformation
Typology: Exercises
1 / 19
This page cannot be seen from the preview
Don't miss anything!
Temperature and Its Effects
2 basic effects:
expansion / contraction
change of material properties
Look, first, at the former:
Concept of Thermal Stresses and Strains
changes. Thus: Materials and structures expand and contract as the temperature
ε T
= (^) α (^) ( ∆ T)
thermal
temperature change
strain
coefficient of thermal expansion (C.T.E.)
units:
degrees
then “thermal stresses” can arise.If these thermal expansions / contractions are resisted by some means,
However
, “thermal stresses” is a
misnomer, they are really…
“stresses due to thermal effects”
-- stresses are
always
“mechanical”
(we’ll see this via an example)
--> Consider a 3-D generic material.
Then we can write:
T
ε ij
=
α ij ∆ T
i, j = 1, 2, 3
(as before)
α ij (^) = 2nd order tensor
The
(^) total strain
of a material is the sum of the
mechanical strain
(^) and the
thermal strain
mechanical
thermal
M
T
ε ij =
ε ij
ε ij
total
Unit 9 - p. 3
σ kl
=
ijkl
ij −
ijkl
ij
thermal terms: This is the same equation as we had before except we have the
ijkl
α ij ∆ (^) T
--> so how does a “thermal stress” arise?
Consider this example
mechanical strain is zero and thus the “thermal stress” is zero.That is, the thermal strain is equal to the total strain. Thus, theSince it is unconstrained it expands freely and no stresses occur. If you have a steel bar lying on a table and heat it, it will expand.
Figure 9.
Free thermal expansion of a steel bar
Fall, 2002
--> However, if the bar is constrained, say at both ends:
Figure 9.
Representation of constrained steel bar
the same as in the previous case Then, as it is heated, the rod cannot lengthen. The thermal strain is
but
(^) now the total strain is zero (i.e.,
Starting with (in one direction):no physical deformation).
ε M
(^) ε T
with:
ε (^) = 0
Thus, the mechanical strain is the negative of the thermal strain.
Fall, 2002
Values of C.T.E.
’s
Note
α ij (^) = (^) α ji
Anisotropic Materials 6 possibilities:
α 11 , α 22 , α 33 , α 12 , (^) α 13 , (^) α 23
T can cause shear strains
not true in “engineering” materials
Orthotropic Materials 3 possibilities:
α 11 , (^) α 22 , (^) α 33
T only causes
extensional
(^) strains
Notes
are interested only inGenerally we deal with planar structures and
α 11
and
α 22
principal material axes, we can “have” anIf we deal with the material in other than the
α 12
Transformation obeys same law as strain (it’s a tensor).
2-D form:
α˜ αβ^
l
l βγ (^) α σγ
ασ
˜
˜
∗
∗
α 11 , α 22
(in - plane values)
∗
α 12
0 (in material axes)
3-D form:
α ij =
l
l j l˜ α kl
i k˜
So, in describing deformation in some axis system at an angle
(^) θ (^) to
the principal material axes…..
Figure 9.
Representation of 2-D axis transformation
y^ ~ 1 y^2
θ
y 2
θ
y 1
Notes
Graphite/epoxy has a
negative
C.T.E. in the fiber direction so it
contracts when heated
Implication
: by laying up plies with various orientation can
desired directionachieve a structure with a C.T.E. equal to zero in a
C.T.E. of a structure depends on C.T.E.
(^) and
elastic constants of
the parts
E = 0 (perfectly compliant) E = E
1
2 examples
total
α (^) of
structure
1
total
α (^) of
structure
(perfectly rigid)
Fall, 2002
α (^) =
α (T)
C.T.E. is a function of temperature (see MIL HDBK 5 for metals). Can be large difference.
Implication
: a zero C.T.E. structure may not truly be
attainable since it may be C.T.E. at T
1 but not at T
2 (^)!
(^) Sources of temperature differential (heating)
shadow, tropics, etc.)ambient environment (engine, polar environment, earth
aerodynamic heating
radiation (black-body)
(^) Constant
(with respect to spatial locations)
In many cases, we are interested in a case where
T (from some reference
temperature) is constant through-the-thickness, etc.
thin structures
structures in ambient environment for long periods of time
Relatively easy problem to solve. Use:
equations of elasticity
equilibrium
stress-strain
Example 3
Each metal has different
α ’s.
What will happen?
Bending!
--> Concept of
(^) self-equilibrating stresses
Must always be in equilibrium. General equation is:
σ dA
where: F = externally applied force
If F = 0, can we still have stresses?
Yes
, but they must be “self-equilibrating” (satisfy equilibrium in and
of themselves):
σ dA
spatially-varyingof structures with varying properties or This is the case of free expansion (thermal)
(^) (we’ll address this in a bit)
If α 1 (^) > (^) α 2 and
T
T
ε ij
ε ij
(^1)
2
(we’ll see more about this bending later)
Bimetallic strip used as temperature sensors!
T varies spatially
(and possibly with time as well, we analyze at
any constant in time)
Must determine
T by looking at heat flux into structure. Three basic
methods:
induction
convection
radiation
Source of heat here is from air boundary layer:
q = h
AW
(^) - T
s ) surface temperature of body
heat flux
heat transfer
[watts/M
2 ]
(convective constant)coefficient
(h is determined from boundary layer theory)
--> 2 considerationsatmosphere). Always important but especially in space (or at high temperature in Radiation
Emissivity
--> surface emits heat
q = -
ε σ
s 4
surface temperature
fluxheat
Stefan-Boltzmann constant
(a material property) emissivity
Absorptivity
heat
q =
α (^) I s (^) λ
angle factor
flux
intensity of source
(a material property)absorptivity
Figure 9.
Representation of heat flux impinging on structure
structure angle of
like the sun
I s (^) (intensity of source)
Figure 9.6 consider:
Representation of structure exposed to two environments
Environment 1
Environment 2
look at a strip of width dz:
Figure 9.
Representation of heat flow through infinitesimal strip of
material
T
q z
T
T
q z + ∂ q z
dz
∂ z