
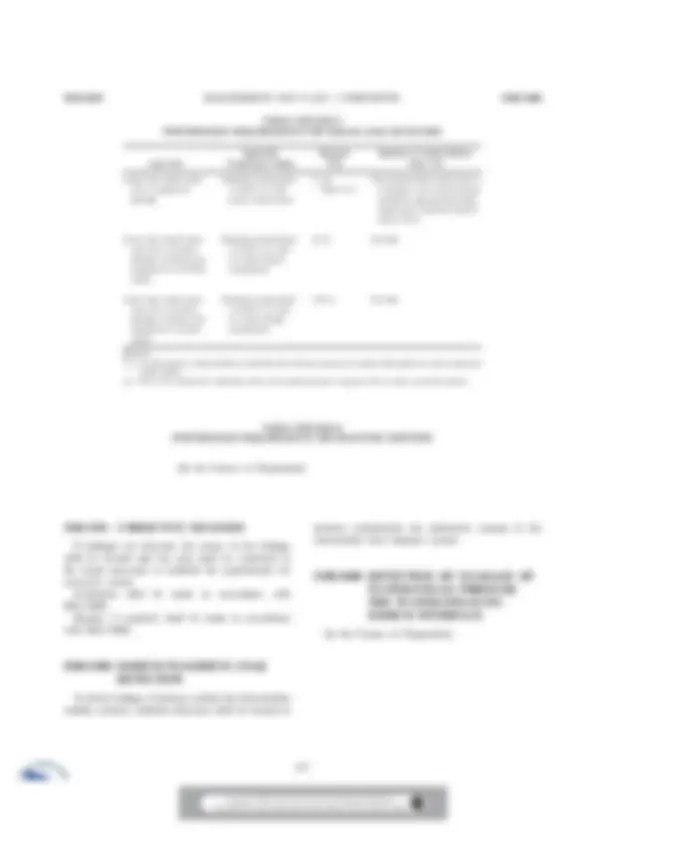
Study with the several resources on Docsity
Earn points by helping other students or get them with a premium plan
Prepare for your exams
Study with the several resources on Docsity
Earn points to download
Earn points by helping other students or get them with a premium plan
Community
Ask the community for help and clear up your study doubts
Discover the best universities in your country according to Docsity users
Free resources
Download our free guides on studying techniques, anxiety management strategies, and thesis advice from Docsity tutors
The requirements for leak detection systems in class 1 liquid metal and cover gas systems, including the installation of diverse, redundant leak detection devices, monitoring for liquid metal to gas leakage and radiation leakage, operability and calibration tests, and leakage monitoring and testing requirements. The document also covers corrective measures for detected leakages and the use of radiation detectors for sodium-to-sodium leak detection.
Typology: Exercises
1 / 2
This page cannot be seen from the preview
Don't miss anything!
(a) As part of the inservice inspection equipment for Class 1 liquid metal systems, diverse, redundant leak detection devices shall be installed to monitor each component and liquid metal appurtenance of the system to monitor for liquid metal to gas leakage. These leak detection systems shall have sensitivities and response times to prevent the following conditions from occurring: (1) substantial weakening of a component due to corrosion resulting from small leaks; (2) damage to other components and cells resulting from large leaks.
Table IMB-5110-1 outlines the required minimum de- tectable leak rates, response times, and operating condi- tions. (b) As part of the inservice inspection equipment for Class 1 cover gas systems, radiation monitors shall be installed to monitor for leakage from the radioactive gas spaces. Performance requirements for radiation mon- itors are shown in Table IMB-5110-2 (in the course of preparation).
Each leak detector system shall be designed to contain self-monitoring provisions to detect failure or degrada- tion of function, except for actual response to aerosol vapors while installed. Procedures shall be established and facilities shall be provided to calibrate the detectors periodically as required in Appendix I for required response to specific concentrations (e.g., radioactivity level, sodium aerosol concentration, hydrogen level, etc.). A number of each type of leak detector systems shall be calibrated at each outage so that all detectors will have been calibrated at least twice each inspection
636
interval. Each leak detector channel shall have provi- sions for in-place calibration of the readout components.
The Class 1 system shall be monitored continuously for leakage of liquid metal and radioactive gases.
In addition, prior to nuclear operation above 5% of rated power, subsequent to shutdown for refueling, maintenance, or inservice inspection, the pressure of the system shall be raised such that the pressure in all points of the system is not less than that seen at 100% of full power operation. The data from each leakage monitor shall be collected and evaluated for a period sufficiently long to detect any trend prior to nuclear operation.
All leakage tests of Class 1 systems required by IMB-5220 shall be conducted while the liquid metal is at a temperature of 600°F or above.
The system pressure shall be increased to the level of the test pressure and test temperature at a rate in accordance with the limitations specified for the system.
IMB-5250 REQUIREMENTS FOR CLASS 1 COMPONENTS IMB-
TABLE IMB-5110- PERFORMANCE REQUIREMENTS FOR SODIUM LEAK DETECTORS
Applicable Response Quantity of Leaked Sodium Leak Size Temperature Range Time [Note (1)] Large leak would cause Shutdown temperature 5 min That amount that would result in cell or equipment (^400°F) to full [Note (2)] a change in cell environmental damage power temperature conditions approaching estab- lished plant Technical Specifi- cation limits
Small leak would cause Shutdown temperature 20 hr 100 g/hr long term corrosion (^400°F) to reac- damage of piping and tor outlet design equipment in air-filled temperature vaults
Small leak would cause Shutdown temperature 250 hr 100 g/hr long term corrosion (^400°F) to reac- damage of piping and tor outlet design equipment in inerted temperature vaults NOTES: (1) It is the Owner’s responsibility to identify the minimum amount of sodium detectable for each component (IMA-1400). (2) The 5 min allowed for detection does not include operator response time to take corrective action.
TABLE IMB-5110- PERFORMANCE REQUIREMENTS FOR RADIATION MONITORS
(In the Course of Preparation)
If leakages are detected, the source of the leakage shall be located and the area shall be examined to the extent necessary to establish the requirements for corrective action. Evaluation shall be made in accordance with IMA-3000. Repairs, if required, shall be made in accordance with IMA-4000.
To detect leakage of primary sodium into intermediate sodium systems, radiation detectors shall be located to
637
monitor continuously the radioactive content of the intermediate heat transport system.
(In the Course of Preparation)
docsity.com