
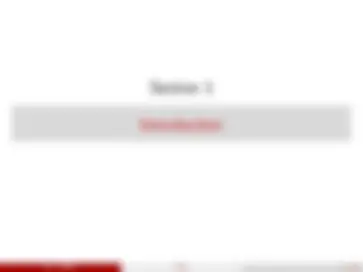
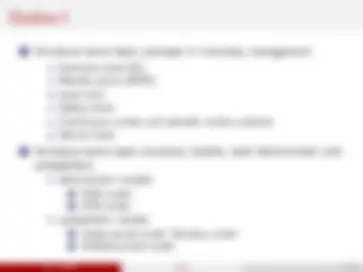
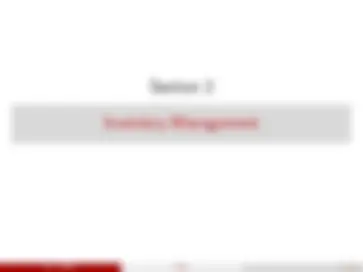
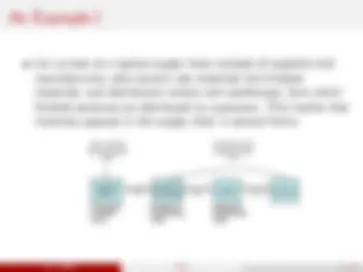
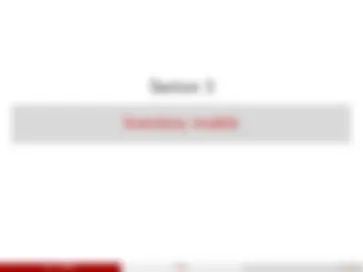
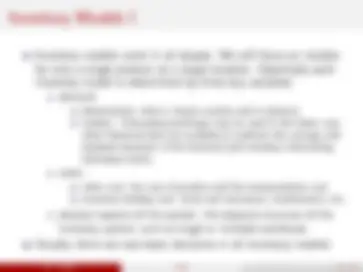

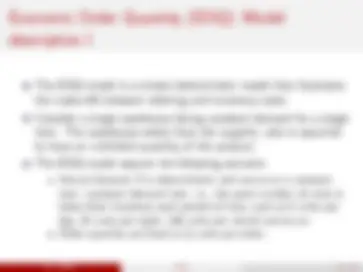
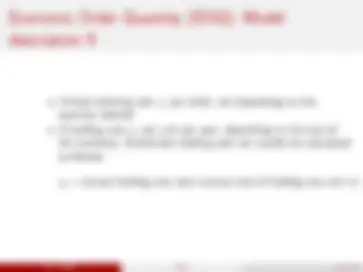
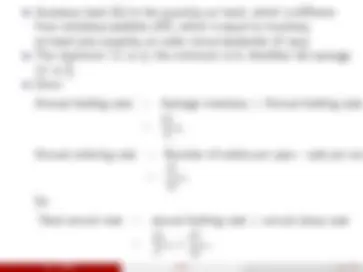
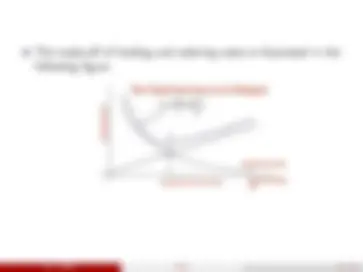
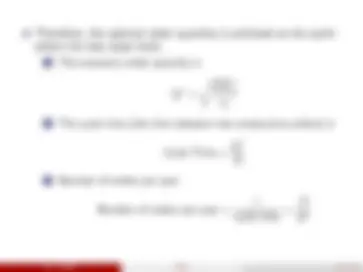
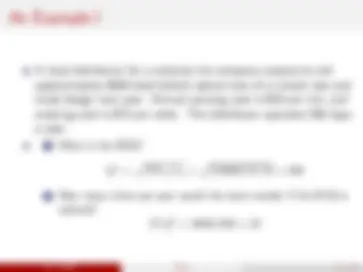
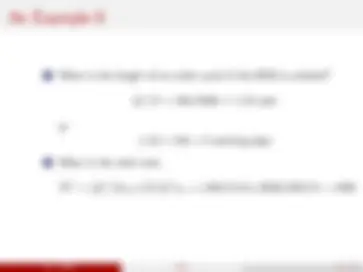
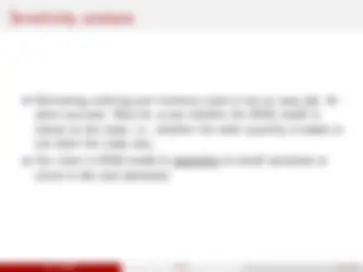
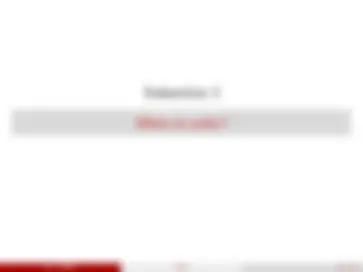
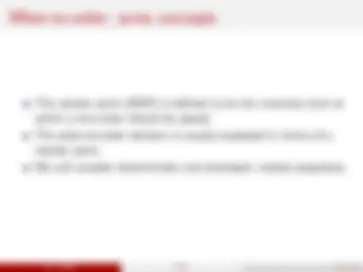
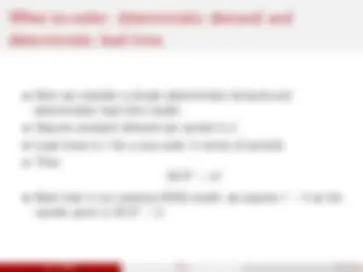
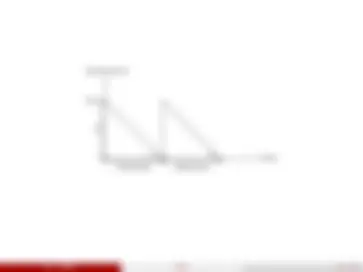
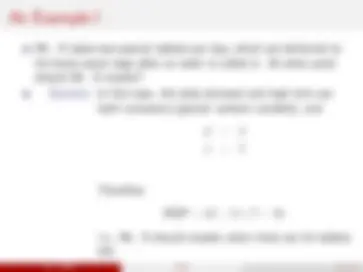
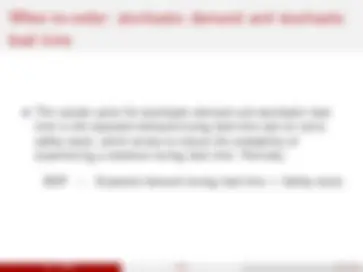
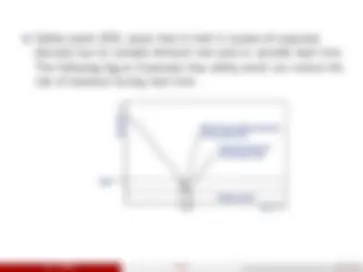
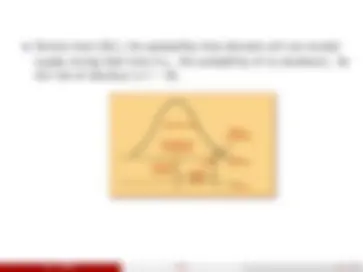
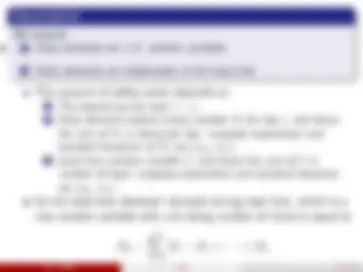
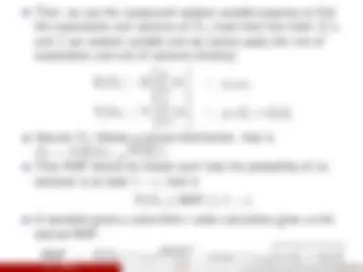
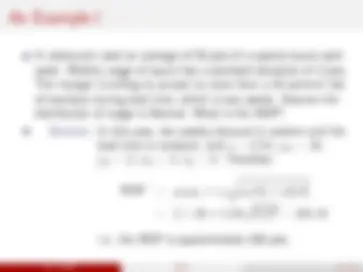
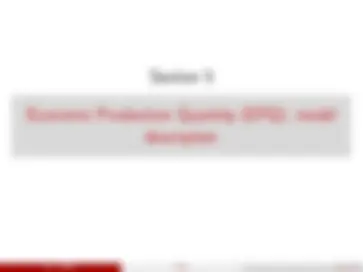
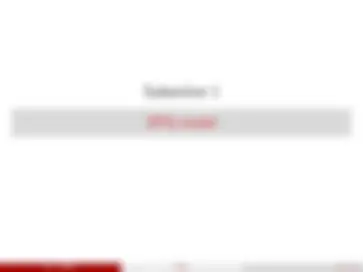
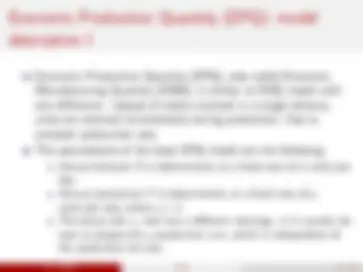
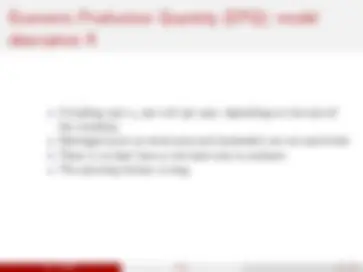
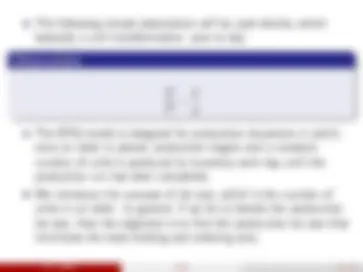
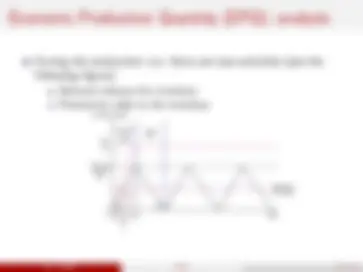
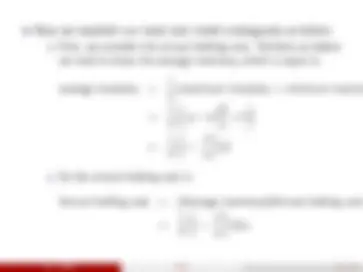
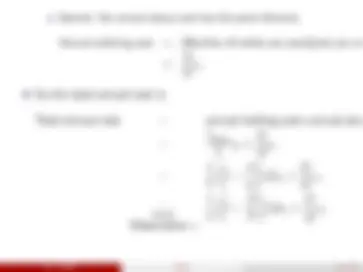
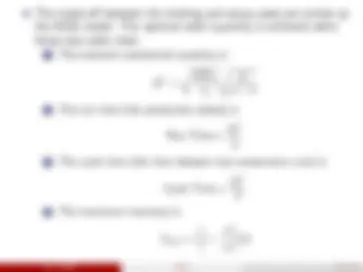
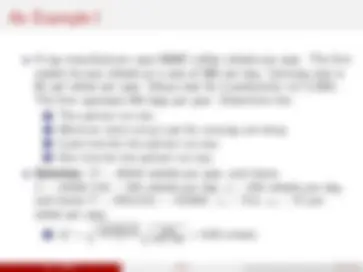
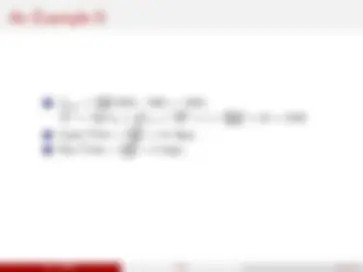
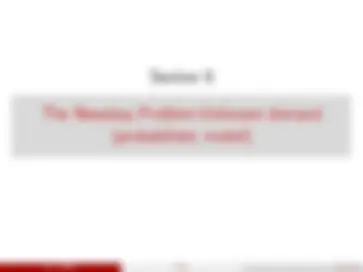
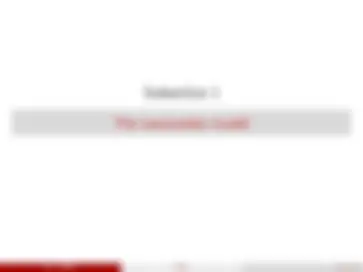
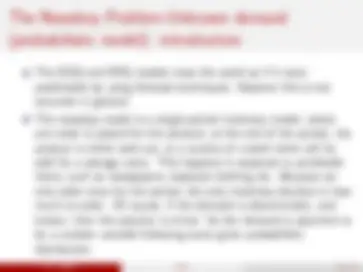
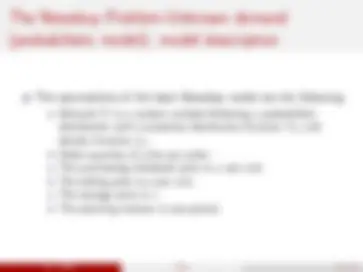
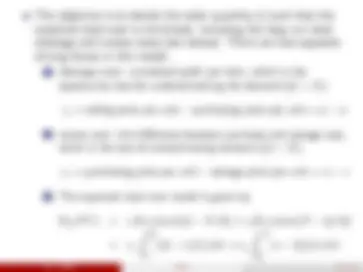
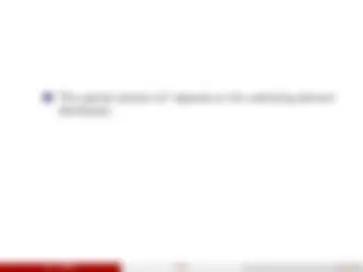
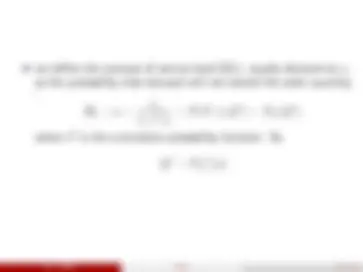
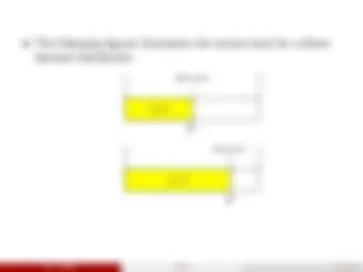
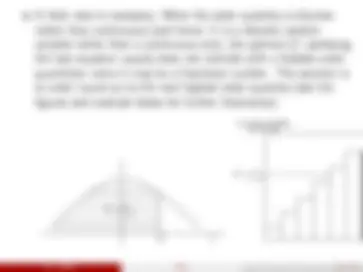
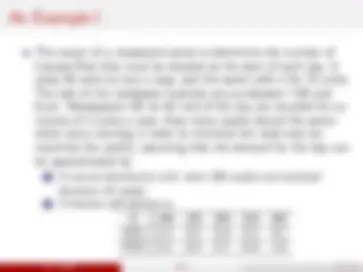
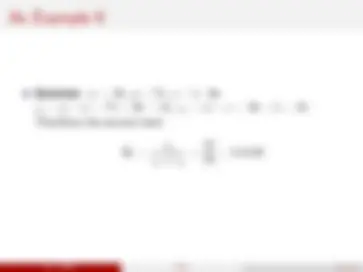
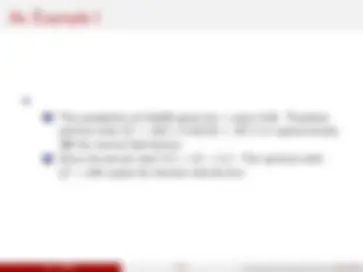
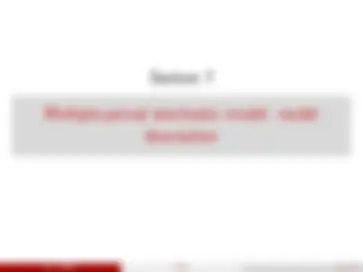
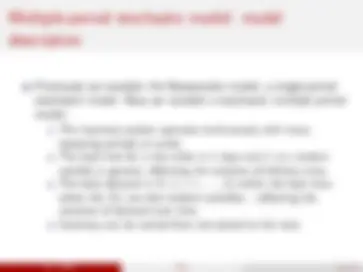
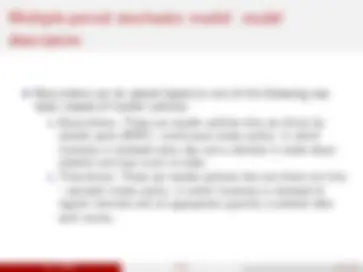
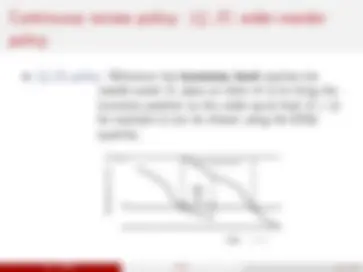
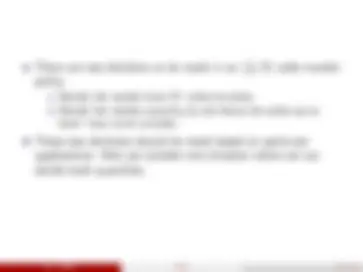
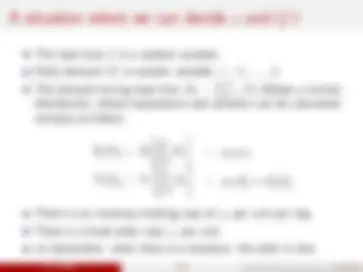
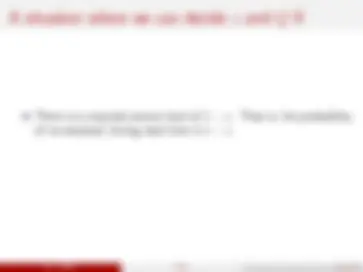
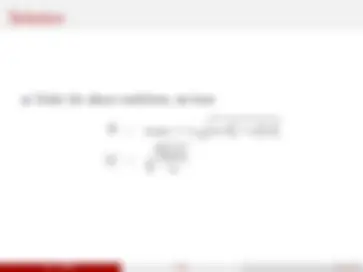
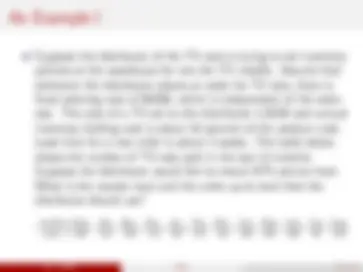
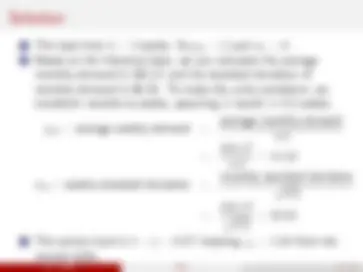
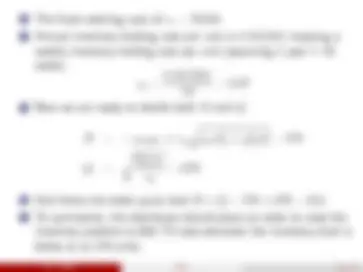
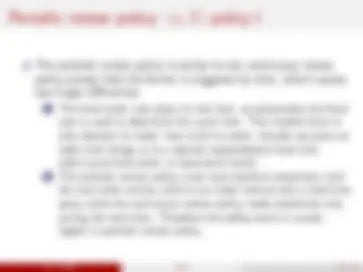
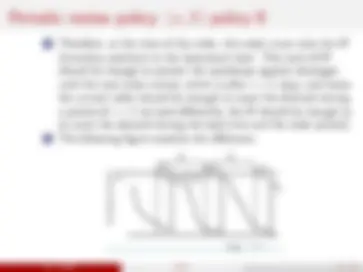
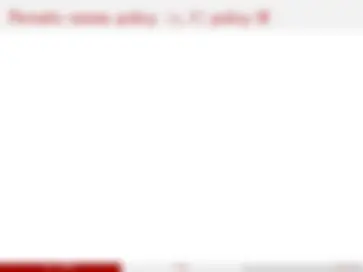
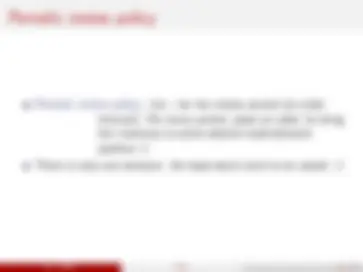
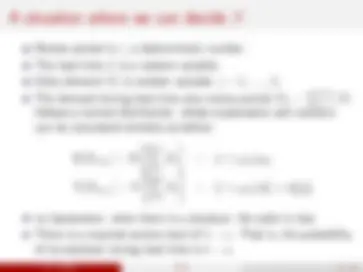
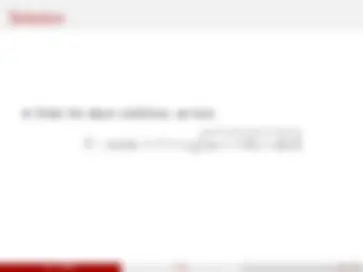
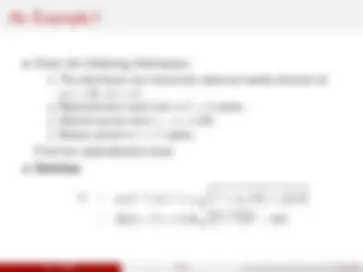
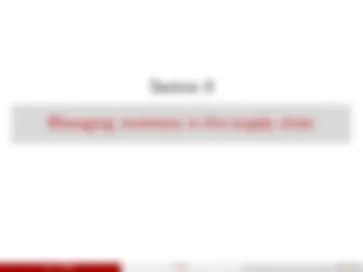
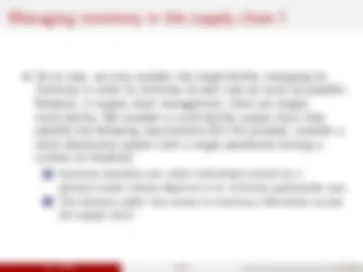
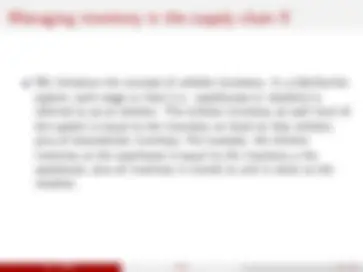
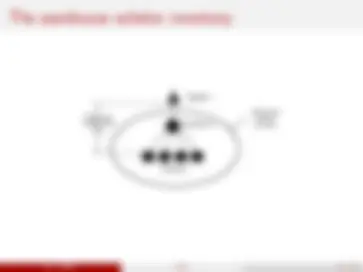
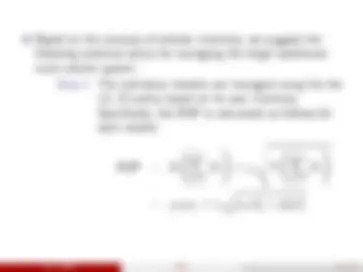
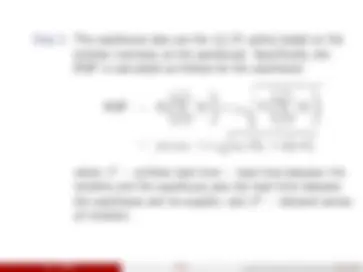
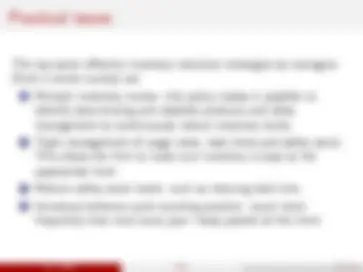
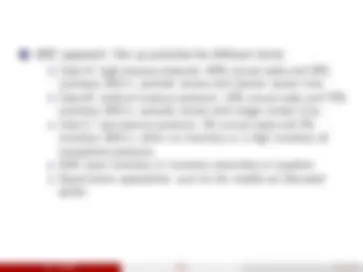
Study with the several resources on Docsity
Earn points by helping other students or get them with a premium plan
Prepare for your exams
Study with the several resources on Docsity
Earn points to download
Earn points by helping other students or get them with a premium plan
Community
Ask the community for help and clear up your study doubts
Discover the best universities in your country according to Docsity users
Free resources
Download our free guides on studying techniques, anxiety management strategies, and thesis advice from Docsity tutors
Tables of content: introduction, inventory management, inventory models, economic order quantity and managing inventory in the supply chain.
Typology: Slides
1 / 83
This page cannot be seen from the preview
Don't miss anything!
On special offer
Donglei Du
Faculty of Business Administration, University of New Brunswick, NB Canada Fredericton E3B 9Y2 (ddu@umbc.edu)
(^1) Introduction (^2) Inventory Management (^3) Inventory models (^4) Economic Order Quantity (EOQ) EOQ model When-to-order? (^5) Economic Production Quantity (EPQ): model description EPQ model (^6) The Newsboy Problem-Unknown demand (probabilistic model) The newsvendor model (^7) Multiple-period stochastic model: model description (^8) Managing inventory in the supply chain
(^1) Introduce some basic concepts in inventory management Inventory level (IL) Reorder point (ROP) Lead time Safety stock Continuous review and periodic review systems Service level (^2) Introduce some basic inventory models, both deterministic and probabilistic. deterministic models (^1) EOQ model (^2) EPQ model probabilistic models (^1) Single-period model: Newsboy model (^2) Multiple-period model
The objective of inventory is to achieve satisfactory levels of customer service while keeping inventory costs within reasonable bounds. Level of customer service: (1) in-stock (fill) rate (2) number of back orders (3) inventory turnover rate: the ratio of average cost of goods sold to average inventory investment Inventory cost: cost of ordering and carrying trade-off
Let us look at a typical supply chain consists of suppliers and manufacturers, who convert raw materials into finished materials, and distribution centers and warehouses, form which finished products are distributed to customers. This implies that inventory appears in the supply chain in several forms:
suppliers plants distributors warehouses retailers^ customers Inventory &warehousing costs
Transportationcost Transportationcost Transportationcost
Raw materials Work-in-process(WIP) Finished product Goods-in-transit(GIP)
Inventory & warehousing costs
Production/ purchase costs
Inventory models come in all shapes. We will focus on models for only a single product at a single location. Essentially each inventory model is determined by three key variables: demand: deterministic, that is, known exactly and in advance. random. Forecasting technique may be used in the latter case when historical data are available to estimate the average and standard deviation of the demand (will introduce forecasting techniques later). costs: order cost: the cost of product and the transportation cost inventory holding cost: taxes and insurances, maintenance, etc. physical aspects of the system: the physical structure of the inventory system, such as single or multiple-warehouse. Usually, there are two basic decisions in all inventory models:
(^1) How much to order? (^2) When to order?
The EOQ model is a simple deterministic model that illustrates the trade-offs between ordering and inventory costs. Consider a single warehouse facing constant demand for a single item. The warehouse orders from the supplier, who is assumed to have an unlimited quantity of the product. The EOQ model assume the following scenario: Annual demand D is deterministic and occurs at a constant rate—constant demand rate: i.e., the same number of units is taken from inventory each period of time, such as 5 units per day, 25 units per week, 100 units per month and so on. Order quantity are fixed at Q units per order.
Shortages (such as stock-outs and backorder) are not permitted.
There is no lead time or the lead time is constant.
The planning horizon is long
The objective is to decide the order quantity Q per order so as to minimize the total annual cost, including holding and setting-up costs.
The following graph illustrates the inventory level as a function of time—a saw-toothed inventory pattern. Quality on hand Q
place^ time order receiveorder placeorder
lead time
receive order
The trade-off of holding and ordering costs is illustrated in the following figure.
Order Quantity(Q)
The Total-Cost Curve is U-Shaped
Ordering Costs QO
Annual Cost
( optimal order quantity)
TC = Q 2 H + D Q S
Therefore, the optimal order quantity is achieved at the point where the two costs meet. (^1) The economic order quantity is
Q∗^ =
√ 2 Dco ch (^2) The cycle time (the time between two consecutive orders) is
Cycle Time = Q∗ D (^3) Number of orders per year
Number of orders per year =
1 cycle time =
D Q∗