
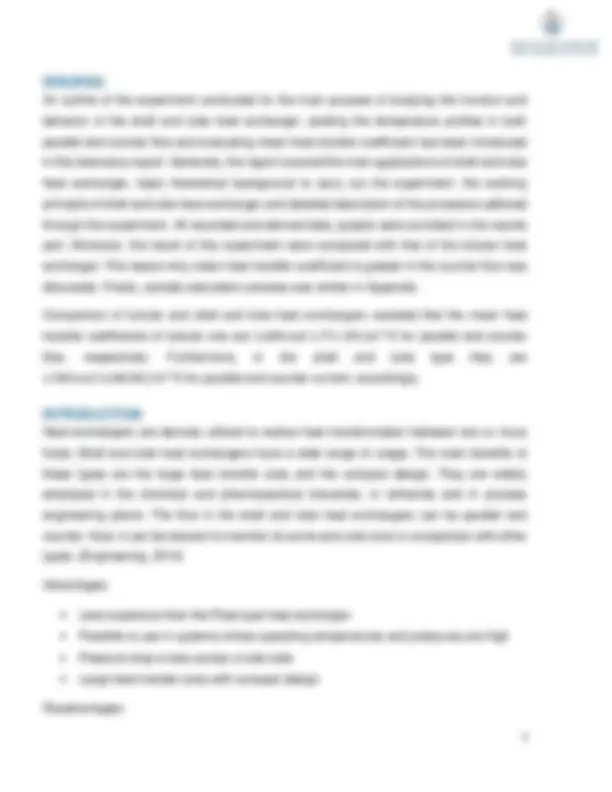
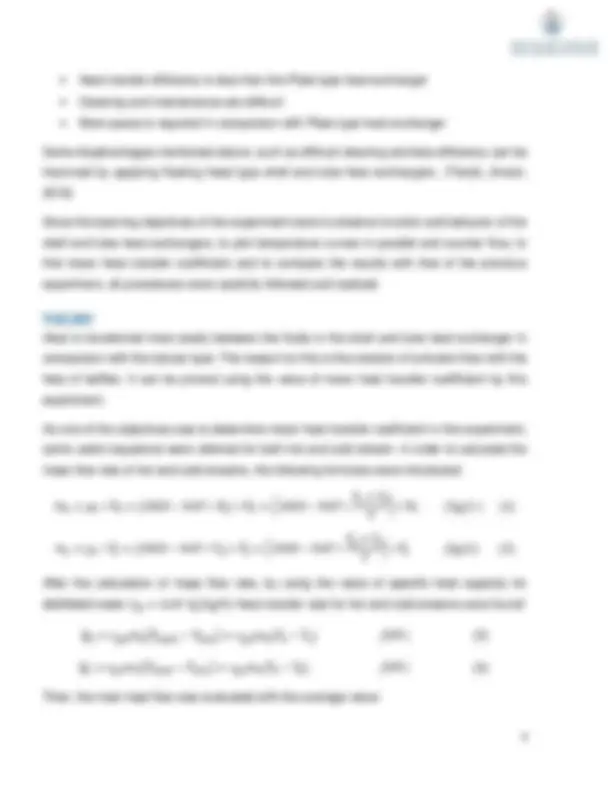
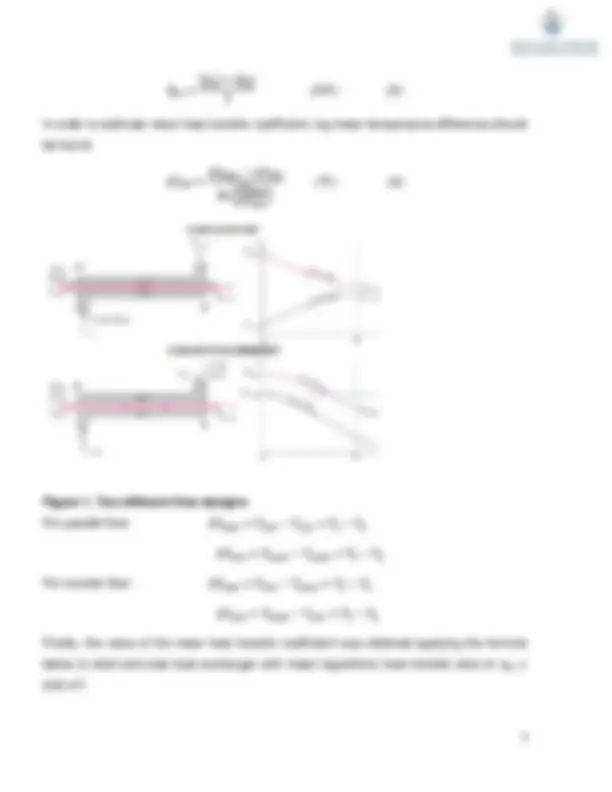

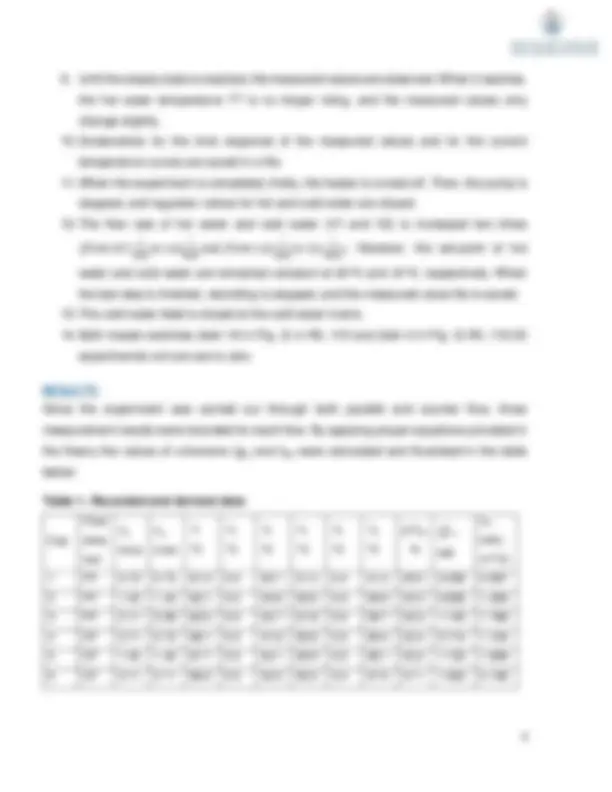
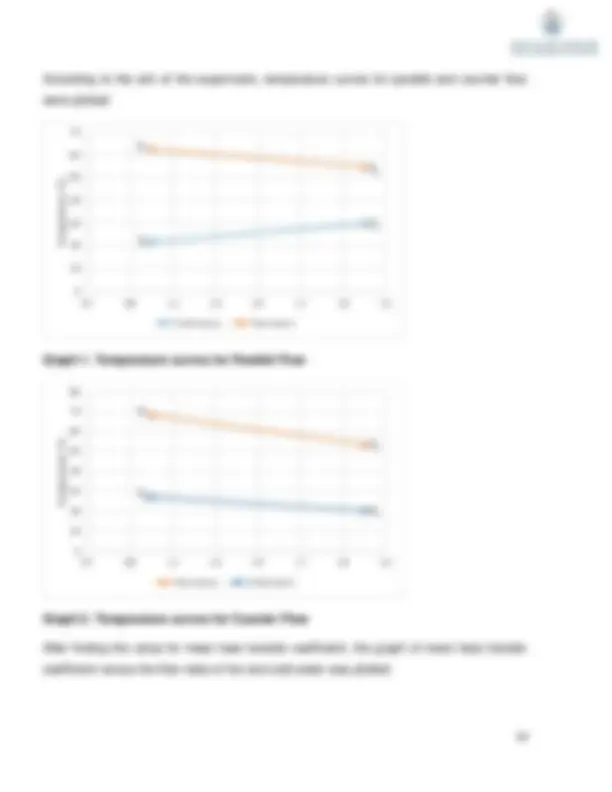
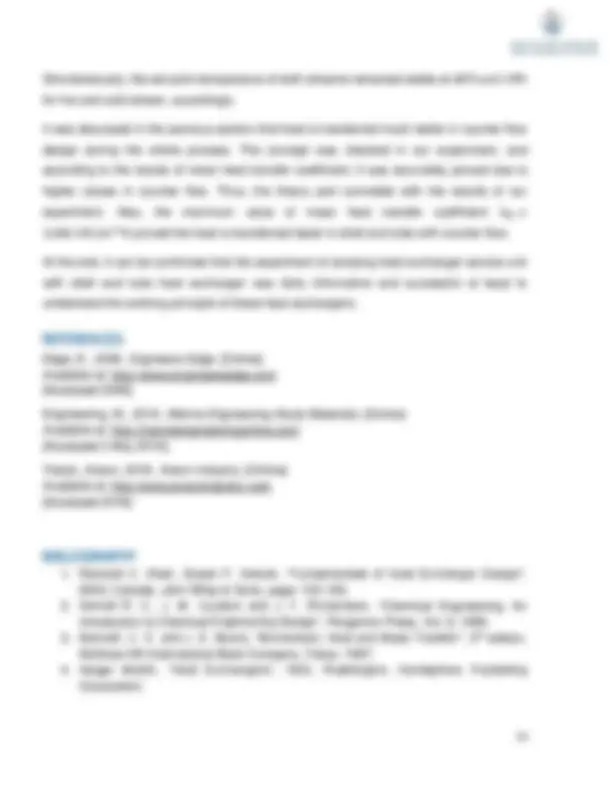
Study with the several resources on Docsity
Earn points by helping other students or get them with a premium plan
Prepare for your exams
Study with the several resources on Docsity
Earn points to download
Earn points by helping other students or get them with a premium plan
Community
Ask the community for help and clear up your study doubts
Discover the best universities in your country according to Docsity users
Free resources
Download our free guides on studying techniques, anxiety management strategies, and thesis advice from Docsity tutors
An outline of the experiment conducted for the main purpose of studying the function and behavior of the shell and tube heat exchanger, plotting the temperature profiles in both parallel and counter flow and evaluating mean heat transfer coefficient has been introduced in this laboratory report. Generally, the report covered the main applications of shell and tube heat exchanger, basic theoretical background to carry out the experiment, and the working principle of shell and tube heat exchanger.
Typology: Lab Reports
1 / 13
This page cannot be seen from the preview
Don't miss anything!
On special offer
๏ท Heat transfer efficiency is less than the Plate type heat exchanger ๏ท Cleaning and maintenance are difficult ๏ท More space is required in comparison with Plate type heat exchanger
Some disadvantages mentioned above, such as difficult cleaning and less efficiency can be improved by applying floating head type shell and tube heat exchangers. (Tianjin_Anson,
Since the learning objectives of the experiment were to observe function and behavior of the shell and tube heat exchangers, to plot temperature curves in parallel and counter flow, to find mean heat transfer coefficient and to compare the results with that of the previous experiment, all procedures were carefully followed and realized.
Heat is transferred more easily between the fluids in the shell and tube heat exchanger in comparison with the tubular type. The reason for this is the creation of turbulent flow with the help of baffles. It can be proved using the value of mean heat transfer coefficient by this experiment.
As one of the objectives was to determine mean heat transfer coefficient in the experiment, some useful equations were referred for both hot and cold stream. In order to calculate the mass flow rate of hot and cold streams, the following formulas were introduced:
๐ฬ (^) โ = ๐โ โ ๐ฬโ = ( 1010 โ 0. 47 โ ๐โ) โ ๐ฬโ = ( 1010 โ 0. 47 โ ๐^1 + 2 ๐^3 ) โ ๐ฬโ (๐๐/๐ ) ( 1 )
๐ฬ (^) ๐ = ๐๐ โ ๐๐ฬ = ( 1010 โ 0. 47 โ ๐๐) โ ๐๐ฬ = ( 1010 โ 0. 47 โ ๐^4 + 2 ๐^6 ) โ ๐๐ฬ (๐๐/๐ ) ( 2 )
After the calculation of mass flow rate, by using the value of specific heat capacity for distillated water (๐๐ = 4. 19 ๐๐ฝ โ๐๐ โ) heat transfer rate for hot and cold streams were found:
๐ฬโ = ๐๐,โ๐โ(๐โ,๐๐ข๐ก โ ๐โ,๐๐) = ๐๐,โ๐โ(๐ 3 โ ๐ 1 ) (๐๐) ( 3 )
๐ฬ๐ = ๐๐,๐๐โ(๐๐,๐๐ข๐ก โ ๐๐,๐๐) = ๐๐,๐๐๐(๐ 6 โ ๐ 4 ) (๐๐) ( 4 )
Then, the main heat flow was evaluated with the average value:
In order to estimate mean heat transfer coefficient, log mean temperature difference should be found:
โ๐๐ฟ๐ = โ๐๐๐๐ฅ^ โ^ โ๐๐๐๐ ln (โ โ๐๐๐๐๐ฅ๐๐๐ )
Figure 1. Two different flow designs For parallel flow: โ๐๐๐๐ฅ = ๐โ,๐๐ โ ๐๐,๐๐ = ๐ 1 โ ๐ 4
โ๐๐๐๐ = ๐โ,๐๐ข๐ก โ ๐๐,๐๐ข๐ก = ๐ 3 โ ๐ 6
For counter flow: โ๐๐๐๐ฅ = ๐โ,๐๐ โ ๐๐,๐๐ข๐ก = ๐ 1 โ ๐ 6
โ๐๐๐๐ = ๐โ,๐๐ข๐ก โ ๐๐,๐๐ = ๐ 3 โ ๐ 4
Finally, the value of the mean heat transfer coefficient was obtained applying the formula below to shell and tube heat exchanger with mean logarithmic heat transfer area of ๐ด๐ =
Figure 3. WL 110.20 Water chiller experimental unit
1 โElectronic controller for cold water temperature, 2โSwitch for refrigeration system, 3 โSwitch for Pump, 4โMaster switch with emergency stop function
As it is shown in figure 2, the hot and cold water is circulated through small-diameter pipes which have been insulated to prevent heat loss. After cooling process in the water chiller unit, cold water is sent to heat exchanger service unit with the help of pump and pipes. For the purpose of reaching the desired temperature of hot water, in the tank of heat exchanger service unit heater has been installed.
T2 T
Figure 4. Schematic diagram for the whole process in the parallel flow
After the water is heated in the tank B with the heater H, it is pumped to shell and tube heat exchanger with the adjusted flow rate. Simultaneously, cold water is pumped to this heat exchanger after the cooling process with the same flow rate in parallel flow. Finally, heat is exchanged between hot and cold streams in parallel flow, and liquids are returned to their location. Thus, until the aim is achieved, the streams are circulated. The same processes occur in the counter flow design with opposite direction of cold water stream.
Since water and electricity are used in the experiment, careful operation is firmly required. All electrical appliances must be kept away from water, which is an excellent conductor.
In our experiment, electrical connections are revealed when the rear panel is opened. To avoid risk of electric shock, rear panel must be protected against humidity.
In addition, as the hot water circuit can even reach up to 70ยฐC, contact with water can lead to scalding.
According to the aim of the experiment, temperature curves for parallel and counter flow were plotted:
Graph 1. Temperature curves for Parallel Flow
Graph 2. Temperature curves for Counter Flow
After finding the value for mean heat transfer coefficient, the graph of mean heat transfer coefficient versus the flow rates of hot and cold water was plotted:
0
10
20
30
40
50
60
70
0,7 0,9 1,1 1,3 1,5 1,7 1,9 2,
Temperature (
ยฐC)
Cold stream Hot stream
๐ 1 ๐ 3
๐ 4
๐ 6
0
10
20
30
40
50
60
70
80
0,7 0,9 1,1 1,3 1,5 1,7 1,9 2,
Temperature (
ยฐC)
Hot stream Cold stream
๐ 1
๐ 3
๐ 4
๐ 6
Graph 3. Mean heat transfer coefficient against hot and cold water flow rates
Table 2. Comparison of heat transmission for tubular and shell and tube heat exchangers
Type of Heat Exchanger
Flow direction
V ๏ฆ h , l/min
V ๏ฆ c , l/min
SP( T 7 ) ยฐC
SP( Tc ) ยฐC
km kW/(m^2 ยฐC) Tubular PF 2.1 2.1 65 19 1. Shell and tube
PF (^) 2.1 2.1 65 19 1.
Tubular CF^ 2.1 2.1 65 19 1. Shell and tube
CF (^) 2.1 2.1 65 19 2.
According to the aim of the experiment, both parallel and counter flow were applied to the shell and tube heat exchanger. By following all procedures carefully temperature profiles were plotted for co-current and counter-current design. Thanks to the equations provided in theory, all unknowns were found and as a result, it was shown how mean coefficient of heat transfer depends on the flow rate of hot and cold streams by plotting the graph. In order to
0
0,
1
1,
2
2,
0 0,5 1 1,5 2 2,
k_mean (kW/m^
ยฐC)
Flow rate (l/min) Counter Flow Paralel Flow
Simultaneously, the set-point temperature of both streams remained stable at 65โ ๐๐๐ 19โ for hot and cold stream, accordingly.
It was discussed in the previous section that heat is transferred much better in counter flow design during the whole process. The concept was checked in our experiment, and according to the results of mean heat transfer coefficient, it was accurately proved due to higher values in counter flow. Thus, the theory part coincided with the results of our experiment. Also, the maximum value of mean heat transfer coefficient ๐๐ = 2.106 ๐๐ ๐โ 2 โ proved the heat is transferred faster in shell and tube with counter flow.
At the end, it can be confirmed that the experiment of studying heat exchanger service unit with shell and tube heat exchanger was fairly informative and successful at least to understand the working principle of these heat exchangers.
Edge, E., 2000. Engineers Edge. [Online] Available at: http://www.engineersedge.com [Accessed 2000].
Engineering, M., 2014. Marine Engineering Study Materials. [Online] Available at: http://marineengineeringonline.com [Accessed 2 May 2014].
Tianjin_Anson, 2016. Anson Industry. [Online] Available at: http://www.ansonindustry.com [Accessed 2016].