
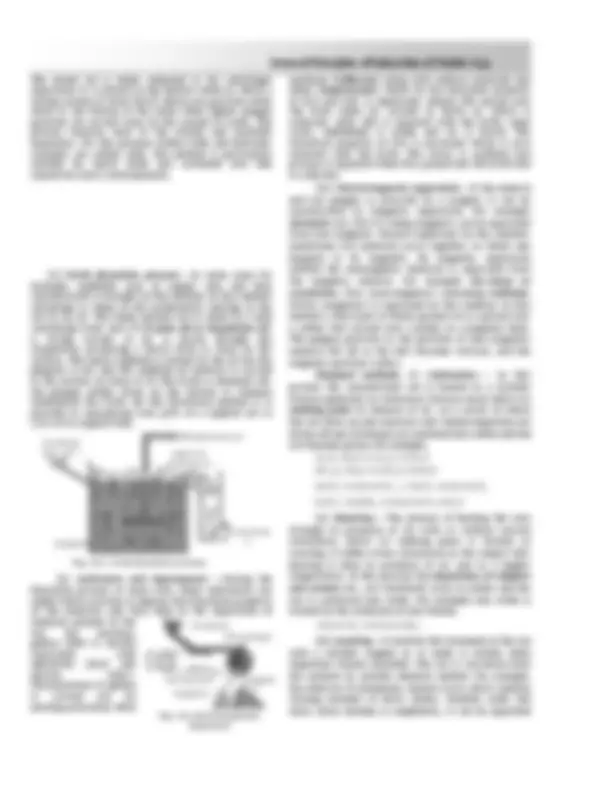
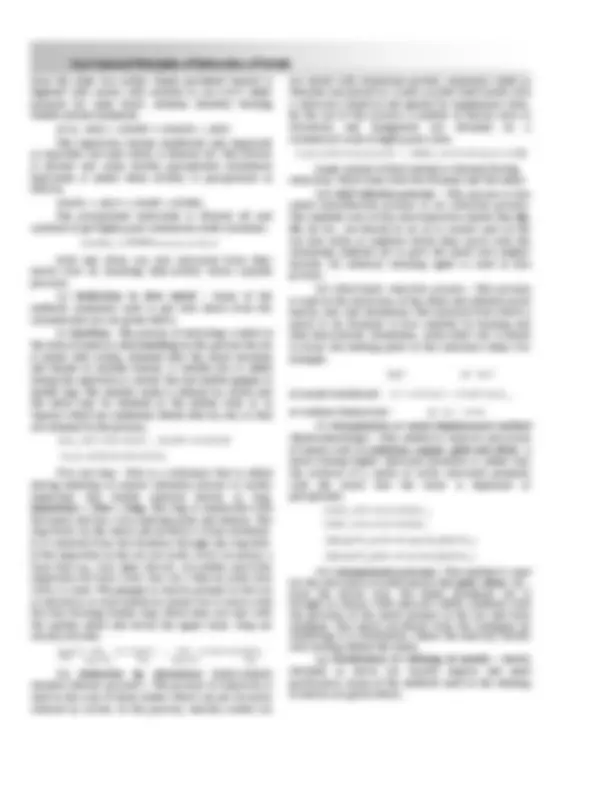
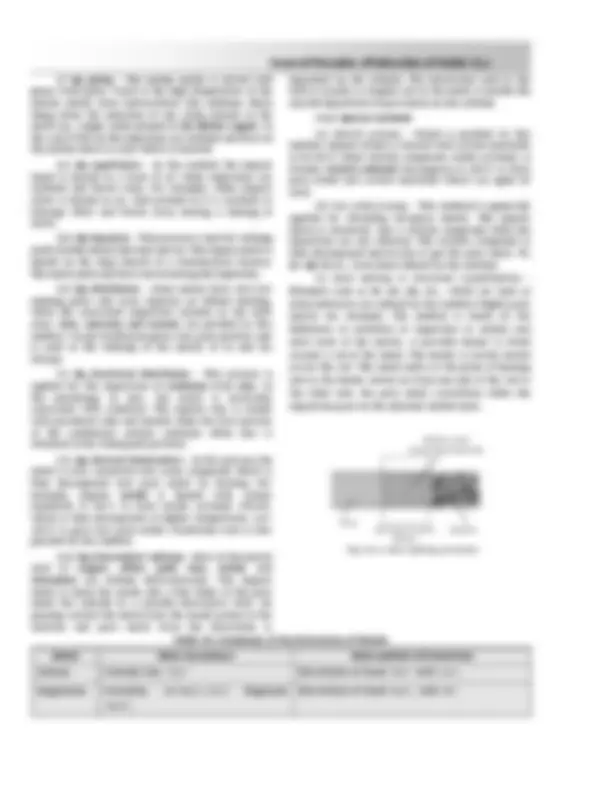
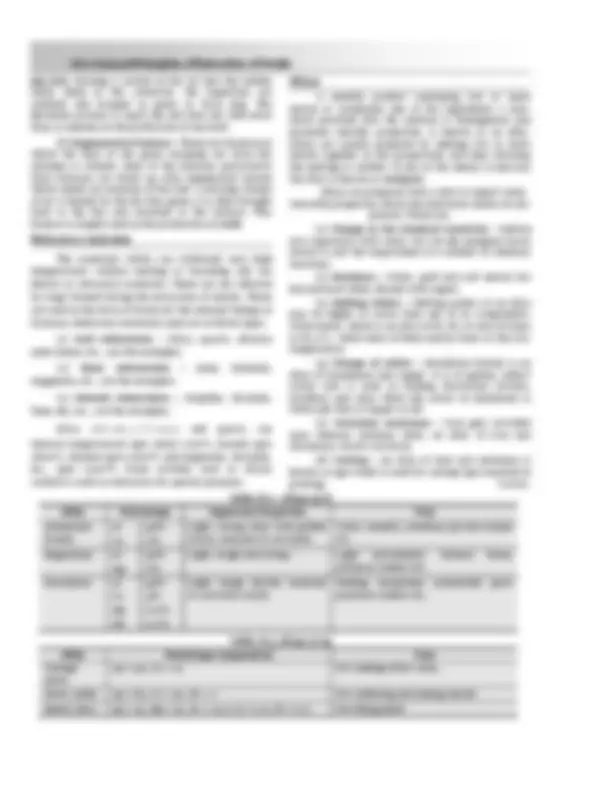
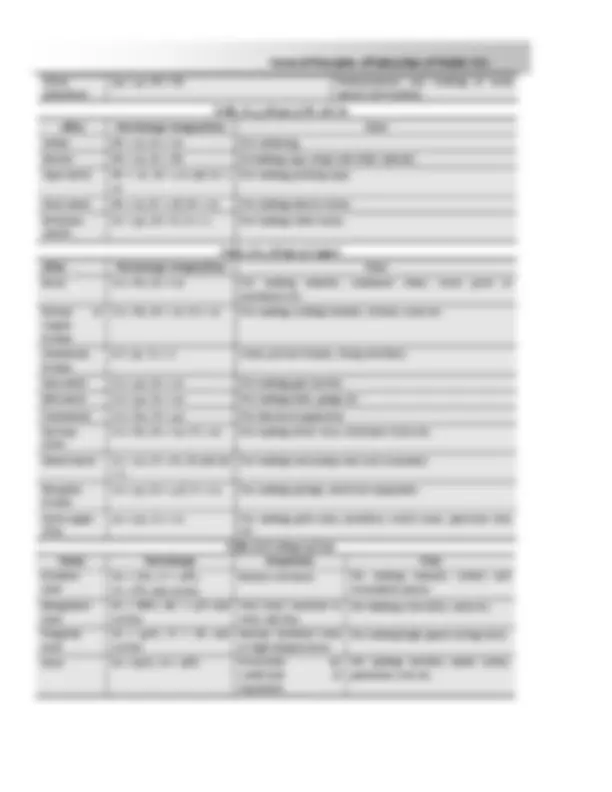

Study with the several resources on Docsity
Earn points by helping other students or get them with a premium plan
Prepare for your exams
Study with the several resources on Docsity
Earn points to download
Earn points by helping other students or get them with a premium plan
Community
Ask the community for help and clear up your study doubts
Discover the best universities in your country according to Docsity users
Free resources
Download our free guides on studying techniques, anxiety management strategies, and thesis advice from Docsity tutors
An overview of the principles of extraction of metals from ores. It explains the occurrence of metals in nature, the types of ores, and the methods used for extraction. The document also discusses the concentration, reduction, and purification of metals. It concludes with a brief discussion of the presence of metals in living organisms.
Typology: Study notes
1 / 10
This page cannot be seen from the preview
Don't miss anything!
All the materials found in the earth are composed of elements. There are about 112 elements known which constitute the entire matter on the earth. Therefore, the elements are regarded as the building blocks of the universe. These are distributed in all the three main parts of the earth; atmosphere and lithosphere. Among these, lithosphere constitutes the main source of most of the elements. The elements have been broadly divided into metals and non-metals on the basis of their physical and chemical properties.
Element which have low chemical reactivity generally occur native or free or metallic state. e.g. Au , Pt ,^ noble^ gas^ etc.^ Element^ which^ are^ chemically reactive, generally occur in the combined state. e.g. halogens, chalcogens etc. The natural materials in which the metals occur in the earth are called minerals. The mineral from which the metal is conveniently and economically extracted is called an ore. All the ores are minerals but all minerals cannot be ores. Ores may be divided into four groups, (1) Metallic core (siderophile) of the earth crust contains ( Mn, Fe, Co, Ni, Cu, Ru, Rb, Pd, Ag, Re, Os, Ir, Pt, Au). Entire composition of metals in earth crust may be given as, Al (8.3%); Ca (3.6%); Na (2.8%); K (2.6%); Mg (2.1%); Ti (0.4%); Mn (0.1%); Fe (5.1%) other metals (0.1%). (i) Native ores : These ores contain metals in free state, e.g., silver, gold, platinum, mercury, copper, etc. These are found usually associated with rock or alluvial materials like clay, sand, etc. sometimes lumps
of pure metals are also found. These are termed nuggets. Iron is found in free state as meteroites which also have 20 to 30% nickel. (ii) Sulphurised and arsenical ores : These ores consist of sulphides and arsenides in simple and complex forms of metals. Important ores of this group are Metal Name of the ore Composition Pb Galena PbS Zn Zinc blende ZnS Hg Cinnabar HgS Ag Argentite or silver glance Pyrargyrite or ruby silver
Ag 2 S 3Ag 2 S.Sb 2 S 3 Fe Iron pyrites FeS 2 Ni Kupfer nickel NiAs Cu Copper pyrites Chalcocite or Copper glance
CuFeS 2 Cu 2 S
(iii) Oxidised ores : In these ores, metals are present as their oxides or oxysalts such as carbonates, nitrates, sulphates, phosphates, silicates, etc. Important ores of this group are listed below, Oxides Haematite Fe 2 O 3 Magnetite Fe 3 O 4 Limonite Fe 2 O 3 .3H 2 O Bauxite Al 2 O 3 .2H 2 O Corundum Al 2 O 3 Diaspore Al 2 O 3 .H 2 O Chromite FeO.Cr 2 O 3
Chapter
Chromeochre Cr 2 O 3 Tinstone (Cassiterite) SnO 2 Chrysoberyl BeO.Al 2 O 3 Cuprite (Ruby copper) Cu 2 O Pyrolusite MnO 2 Zincite ZnO Rutile TiO 2 Ilmenite FeO.TiO 2 Carbonates Magnesite MgCO 3 Lime stone CaCO 3 Dolomite CaCO 3 .MgCO 3 Calamine ZnCO 3 Malachite CuCO 3 .Cu(OH) 2 Azurite Cu(OH) 2 .2CuCO 3 Cerussite PbCO 3 Siderite FeCO 3 Nitrates Chile saltpetre NaNO 3 Salt petre KNO 3 Sulphates Epsom salt MgSO 4 .7H 2 O Barytes BaSO 4 Gypsum CaSO 4 .2H 2 O Glauber’s salt Na 2 SO 4 .10H 2 O Anglesite PbSO 4 Kainite KCl.MgSO 4 .3H 2 O Schonite K 2 SO 4 .MgSO 4 .6H 2 O Polyhalite K 2 SO 4 .MgSO 4 .CaSO 4 .2H 2 O Phosphates and Silicates Lepidolite (an ore of lithium)
( Li, Na, K ) 2 Al 2 ( SiO 3 ) 3 ( F,OH ) 2 Petalite (an ore of lithium)
LiAl ( Si 2 O 5 ) 2
Triphylite (an ore of lithium)
( Li, Na ) 3 PO 4 , ( Fe, Mn ) 3 ( PO 4 ) 2 Beryl (an ore of berylium)
3 BeO. Al 2 O 3 .6 SiO 2
Willemite Zn 2 SiO 4 China clay Al 2 O 3 .2 SiO 2 .2 H 2 O Chlor-apatite 3 Ca 3 ( PO 4 ) 2. CaCl 2 Mica K 2 O .3 Al 2 O 3 .6 SiO 2 .2 H 2 O Fluor-apatite 3 Ca 3 ( PO 4 ) 2. CaF 2 Felspar KAlSi 3 O 8 Talc Mg 2 ( Si 2 O 5 ). Mg ( OH ) 2 Asbestos CaMg 3 .( SiO 3 ) 4
(iv) Halide ores : Metallic halides are very few in nautre. Chlorides are most common. For example. Common salt NaCl ; Horn silver AgCl Carnallite KCl. MgCl 2. 6 H 2 O The important fluoride ores are Fluorspar CaF 2 ; Cryolite Na 3 AlF 6
Metals are also found in living organisms, e.g., (1) Magnesium is found in chlorophyll. (2) Potassium is present in plant roots. (3) Manganese, Iron and copper are present in chloroplast. (4) Zinc is present in eyes of cats and cows. (5) Iron is present in haemoglobin. (6) Calcium is present in bones. (7) Vanadium is present in cucumbers. (8) Chromium is present in prown.
The extraction of a pure metal from its ore is called metallurgy****. In order to extract the metal from ores, several physical and chemical methods are used. The method used depending upon chemical properties and nature of the ore from which it is to be extracted. It involves four main steps, (1) Crushing and grinding of the ore. (2) Concentration or dressing of the ore. (3) Reduction to free metal. (4) Purification or refining of the metal. (1) Crushing and grinding of the ore : Those ores occur in nature as huge lumps. They are broken to small pieces with the help of crushers or grinders. These pieces are then reduced to fine powder with the help of a ball mill or stamp mill****. This process is called pulverisation****. (2) Concentration or dressing of the ore : The ore are usually obtained from the ground and therefore contained large amount of unwanted impurities, e.g., earthing particles, rocky matter, sand, limestone etc. These impurities are known collectively as gangue or matrix. It is essential to separate the large bulk of these impurities from the ore to avoid bulk handling and in subsequent fuel costs. The removal of these impurities from the ores is known as concentration. The concentration is done by physical as well as chemical methods. Physical Methods (i) Gravity Separation or levigation : This process of concentration is based on the difference in the specific gravity of the ore and gangue.
Crushed
from the other two oxides. Finely powdered bauxite is digested with caustic soda solution at 150– 170 o C under pressure for some hours. Alumina dissolves forming soluble sodium aluminate. Al 2 O 3_._ 2 H 2 O + 2 NaOH 2 NaAlO 2 + 3 H 2 O The impurities remain unaffected and separated as insoluble red mud which is filtered off. The filtrate is diluted and some freshly precipitated aluminium hydroxide is added when Al ( OH ) 3 is precipitated as follows, NaAlO 2 + 2 H 2 O NaOH + Al ( OH ) 3 The precipitated hydroxide is filtered off and calcified to get highly pure aluminium oxide (alumina). 2 Al ( OH ) 3 calcinatio n Al 2 O 3 3 H 2 O Gold and silver are also extracted from their native ores by Leaching (Mac-Arthur forest cyanide process). (3) Reduction to free metal : Some of the methods commonly used to get free metal from the concentrated ore are given below, (i) Smelting : The process of extracting a metal in the state of fusion is called smelting. In this process the ore is mixed with carbon, obtained after the above reactions and heated in suitable furnace. A suitable flux is added during the operation to convert the non–fusible gangue to fusible slag. The metallic oxide is reduced by carbon and the metal may be obtained in the molten state or as vapours which are condensed. Metals like tin, zinc or lead are obtained by this process. SnO (^) 2 2 C Sn 2 CO ; ZnO C Zn CO Fe (^) 2 O 3 3 CO 2 Fe 3 CO 2 Flux and slag : Flux is a substance that is added during smelting to convert infusible silicons or earthy impurities into fusible material known as slag. Impurities + Flux = Slag. The slag is immiscible with the metal and has a low melting point and density. The slag floats on the metal and protects it from oxidation. It is removed from the furnance through the slag hole. If the impurities in the ore are acidic ( SiO 2 ) in nature, a basic flux e.g., CaO, MgO, FeO etc. are added; and if the impurities are basic ( CaO, FeO , etc.) then on acidic flux ( SiO 2 ) is used. The gangue or matrix present in the ore is refractory or non–fusible in nature but it reacts with the flux forming fusible slag which does not mix with the molten metal and forms the upper layer. Slag are usually silicates.
Flux (^) Impurities^2 Slag^3 CaO SiO CaSiO ; Impurities^2 Slag^3 SiO FeO FeSiO (ii) Reduction by Aluminium (Gold-schmidt alumino thermic process) : The process of reduction is used in the case of those oxides which can not be easily reduced by carbon. In this process, metallic oxides ore
are mixed with aluminium powder commonly called as thermite and placed in a steel crucible lined inside with a refractory material and ignited by magnesium ribon. By the use of this process a number of metals such as chromium and manganese are obtained on a commercial scale in highly pure state. Cr (^) 2 O 3 2 Al Al 2 O 3 2 Cr^ ; 2 MnO (^) 2 4 Al 2 Al 2 O 3 3 Mn Large amount of heat energy is released during reduction, which fuses both the alumina and the metal. (iii) Self reduction process : This process is also called autoreduction process or air reduction process. The sulphide ores of less electropositive metals like Hg, Pb, Cu etc., are heated in air as to convert part of the ore into oxide or sulphate which then reacts with the remaining sulphide ore to give the metal and sulphur dioxide. No external reducing agent is used in this process. (iv) Electrolytic reduction process : This process is used in the extraction of the alkali and alkaline earth metals, zinc and aluminium. The material from which a metal to be obtained is first smelted by heating and then electrolysed. Sometimes, some other salt is mixed to lower the melting point of the substance taken. For example, NaCl Na ^ Cl At anode (Oxidation) : Cl e Cl ; Cl Cl Cl 2 , At cathode (Reduction) : Na e Na (v) Precipitation or metal displacement method (Hydrometallurgy) : This method is used for extraction of metals such as cadmium, copper, gold and silver. A metal having higher electrode potential is added into the solution of a metal of lower electrode potential with the result that the latter is displaced or precipitated. CuSO (^) 4 Fe Cu FeSO 4 ; CdSO (^) 4 Zn Cd ZnSO 4 2 K [ Ag ( CN ) 2 ] Zn 2 Ag K 2 [ Zn ( CN ) 4 ] 2 K [ Au ( CN ) 2 ] Zn 2 Au K 2 [ Zn ( CN ) 4 ] (vi) Amalgamation process : This method is used for the extraction of noble metals like gold, silver , etc., from the native ores. the finely powdered ore is brought in contact with mercury which combines with the particles of the metal present in the ore and form amalgam. The metal recovered from the amalgam by subjecting it to distillation, where the mercury distills over leaving behind the metal. (4) Purification or refining of metals : Metals obtained as above are usually impure and need purification. Some of the methods used in the refining of metals are given below,
(i) By poling : The molten metals is stirred with green wood poles. Wood at the high temperature of the molten metals form hydrocarbons like methane which being about the reduction of any oxide present in the metal e.g., copper oxide present in the blister copper. In the case of the tin the impurities are oxidised and float on the molten metal as scum which is removed. (ii) By cupellation : In this method the impure metal is heated in a blast of air when impurities are oxidised and blown away. For example, when impure silver is heated in air, lead present in it is oxidised to litharge ( PbO ) and blown away leaving a shining of silver. (iii) By liquation : This process is used for refining easily fusible metals like lead and tin. The impure metal is heated on the slopy hearth of a reverberatory furnace. The metal melts and flows down leaving the impurities. (iv) By distillation : Some metals have very low melting point and soon vaporize on behind heating, while the associated impurities remains in the solid state. Zinc, mercury and arsenic are purified by this method. Vacum distillation gives very pure product and is used in the refining of the metals of IA and IIA Groups. (v) By fractional distillation : This process is applied for the separation of cadmium from zinc. In the metallurgy of zinc, the metal is invariably associated with cadmium. The impure zinc is mixed with powdered coke and heated when the first portion of the condensate contain cadmium while zinc is obtained in the subsequent portions. (vi) By thermal dissociation : In this process the metal is first converted into some compound which is then decomposed into pure metal by heating. For example, impure nickel is heated with carbon monoxide at 60 o C to form nickel carbonyl Ni ( CO ) 4 which is then decomposed at higher temperature, 150- 180 o C to give very pure nickel. Sometimes iron is also purified by this method. (vii) By Electrolytic refining : Most of the metals such as copper, silver, gold, zinc, nickel , and chromium are refined electrolytically. The impure metal is made the anode and a thin sheet of the pure metal the cathode in a suitable electrolytic bath. On passing current the metal from the anode passes in the solution and pure metal from the electrolyte is
deposited on the cathode. The electrolyte used in the bath is usually a complex salt of the metal to enable the smooth deposition of pure metal on the cathode. (viii) Special methods (a) Mond's process : Nickel is purified by this method. Impure nickel is treated with carbon monoxide at 60-80° C when volatile compound, nickel carbonyl, is formed. Nickel carbonyl decomposes at 180° C to form pure nickel and carbon monoxide which can again be used. (b) Van Arkel process : This methods is generally applied for obtaining ultrapure metals. The impure metal is converted into a volatile compound while the impurities are not affected. The volatile compound is then decomposed electrically to get the pure metal. Ti, Zr, Hf, Si etc., have been refined by this method. (c) Zone refining or fractional crystallisation : Elements such as Si, Ge, Ga, etc., which are used as semiconductors are refined by this method. Highly pure metals are obtained. The method is based on the difference in solubility of impurities in molten and solid state of the metals. A movable heater is fitted around a rod of the metal. The heater is slowly moved across the rod. The metal melts at the point of heating and as the heater moves on from one end of the rod to the other end, the pure metal crystallises while the impurities pass on the adjacent melted zone.
Table 16.1 Summary of the Extraction of Metals Metal Main Occurrence Main method of Extraction Sodium Common Salt, NaCl Electrolysis of fused NaCl with CaCl 2 Magnesium Carnallite, KCl. MgCl 2. 6 H 2 O Magnesite MgCO 3
Electrolysis of fused MgCl 2 with KCl
Fig. 16.4. Zone refining of metals
Molten zone containing impurity
Pure metal Moving circular heater^ Impure metal
(2) Reverberatory Furnace : In this furnace fuel burns in a separate part and does not mix with the charge. The furnace may be divided into 3 parts, (i) Fire Grate : It is on one side where the fuel burns. (ii) Flue or Chimney : It is on the other side of the fire grate. The waste gases escape through it. (iii) Hearth : It is the middle part of the furnace where the charge is heated with the flames and hot gases. The material to be heated is placed on the hearth or bed of the furnace and is heated by the hot gases or flames produced by the burning of fuel. The waste gases escape out of the chimney. Since the fuel does not come in contact with the charge, the furnace is very suitable for calcination and roasting and is employed for both oxidising and reducing purposes. For oxidation, the material is heated by the current of hot air while for reduction the material is mixed with coke and heated. The furnace find wide application in the extractive metallurgy.
(3) Electric Furnace : The fuel burnt furnaces described in this chapter produce temperature in the range of 1000 - 1500 o C. Although these furnaces have the great utility in the extraction of metals yet these
are unsuitable where higher temperatures are needed. One commonly used electric furnace is Heroult’s furnace shown in fig. It consists of a steel shell lined inside with dolomite or magnesite. It is provided with movable water jacketed electrodes suspended from the roof or from the sides. Heat is generated by striking an arc between the electrodes, thereby, a temperature of over 3000 o C may be reached. The charge melts and the impurities e.g., Si, Mn, P and S etc. present in the ore combine with the basic lining to form slag, which is free from sulphur or gas bubbles. Steel of very fine quality is prepared by this method. Electric furnaces are largely used where, (i) Cheap power supply is available. (ii) High temperature are required. (iii) Pure product are required. As such they find wide applicability in a number of industries such as metallurgy, ceramices plastics chemical and also in the research laboratories. These furnaces are easily operated and involve the problem of the storage of fuel and disposal of fuel waste. (4) Muffle Furnace : In this furnace the material to be heated does not come in the contact with the fuel or flames. A muffle is a chamber made of refractory material and is surrounded by flames and hot gases on all sides. The products of combustion are removed through a door provided in the furnace. Muffle furnace is used for the extraction of zinc , preparation of red lead, Pb 3 O 4 and for testing the purity of precious metals like silver and gold. In an electric muffle furnace the chamber is surrounded by resistance coils.
(5) Bessemer Converter : A Bassemer converter is a pear–shaped 10 or more feet high, open at the top, lined with a refractory material such as silica or magnesia which also acts as a flux. The converter is mounted on trunnions, so that it can be tilted to collect the products formed. There is an arrangement of introducing a hot blast of air from a number of small openings in the bottom of the furnace. The converter is used mostly for manufacturing of copper of steel from
Fig. 16.6. Modern reverberatory furnace
Hangers^ Tie-rod
Charge hopper
Air and oil Furnace charge Silica Magnesite
Fig. 16.7. Muffle furnace
Flames and hot gases Muffle
Fire place
pig iron. Passing a current of hot air into the molten metal taken in the converter, the impurities are oxidised and escaped as gases or from slag. The Bessemer process is rapid one and does not take more than 15 minutes in the production of one bath. (6) Regenerative Furnace : These are furnaces in which the heat of the gases escaping out from the chimney is utilized. Most of the furnaces particularly blast furnaces are fitted up with regenerated system which means an economy of the fuel. A flowing column of air is heated by the hot flue gases, it is then brought back to the fire and returned to the furnace. This furnace is largely used in the production of steel.
The materials which can withstand very high temperatures without melting or becoming soft are known as refractory materials. These are not affected by slags formed during the extraction of metals. These are used in the form of bricks for the internal linings of furnaces. Refractory materials used are of three types, (1) Acid refractories : Silica, quartz, silicious sand stones, etc., are the examples. (2) Basic refractories : Lime, dolomite, magnesite, etc., are the examples. (3) Neutral refractories : Graphite, chromite, bone ash, etc., are the examples.
Silica ( 92 % SiO 2 , 2. 7 % Al 2 O 3 ) and quartz, can tolerate temperatures upto about 1750° C , bauxite upto 1800° C , alumina upto 2000° C and magnesite, chromite, etc., upto 2200° C. Some carbides such as silicon carbide is used as refractory for special purposes.
A metallic product containing two or more metals or sometimes one of the ingredients a non– metal provided that the mixture is homogenous and possesses metallic properties, is known as an alloy. Alloys are usually prepared by melting two or more metals together in the proportions and then allowing the melting to solidify. If one of the metals is mercury the alloy is known as amalgam. Alloys are prepared with a view to impart some desirable properties which the individual metals do not possess. These are, (1) Change in the chemical reactivity : Sodium acts vigorously with water, but Na–Hg amalgam reacts slowly to suit the requirement of a number of chemical reactions. (2) Hardness : Silver, gold and soft metals but become hard when alloyed with copper. (3) Melting Points : Melting points of an alloy may be higher or lower than any of its components. Wood-metal, which is an alloy of Bi, Pb, Sn and Cd fuses at 60.5o C ., while none of these metals fuses at this low temperature. (4) Change of colour : Aluminium bronze is an alloy of aluminium and copper. It is of golden, yellow colour and is used in making decoration articles, jewellery and coins while the colour of aluminium is white and that of copper is red. (5) Corrosion resistance : Iron gets corroded soon whereas stainless Steel, an alloy of iron and chromium, resists corrosion. (6) Casting : An alloy of lead and antimony is known as type metal is used for casting type required in printing works. Table 16.2 Alloys of Al Alloy Percentage Important Properties Uses Aluminium bronze
Al Cu
Light, strong alloy with golden lustre, resistant to corrosion
Coins, utensils, jewellary picture frames etc. Magnalium Al Mg
Light, tough and strong Light instruments, balance beam, pressure cookers etc. Duralumin Al Cu Mg Mn
Light, tough, ductile, resistant to corrosive action
Making aeroplanes automobile parts pressure cookers etc.
Table 16.3 Alloys of Ag Alloy Percentage composition Uses Coinage silver
Ag = 90, Cu = 10 For making silver coins.
Silver solder Ag = 63, Cu = 30, Zn = 7 For soldering and joining metals Dental alloy Ag = 33, Hg = 52, Sn = 12.5, Cu = 2.0, Zn = 0.5 For filling teeth
Nickel steel Fe = 98–96%, Ni = 2–4% Resistant to corrosion, hard and elastic.
For making wire cables, gears, drive shafts etc. Permalloy Fe = 21%, Ni = 78% and carbon
Strongly magnetised by electric current, loses magnetism when current is cut off.
For making electromagnets, ocean cables etc.
Chrome steel Fe = 98–96%, Cr = 2–4% High tensile strength For making axles, ball bearings and cutting tools such as files. Alnico Fe = 60%, Al =12%, Ni = 20%, Co = 8%
Highly magnetic For making permanent magnents.