
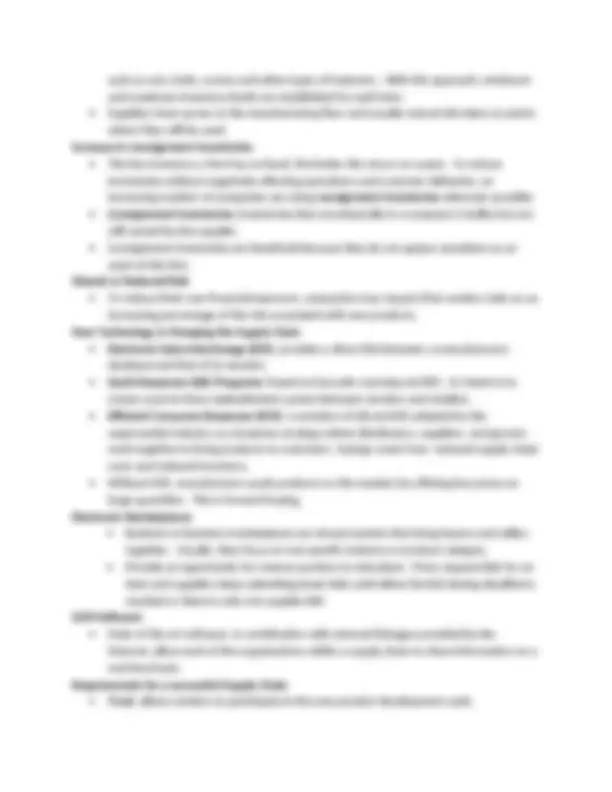
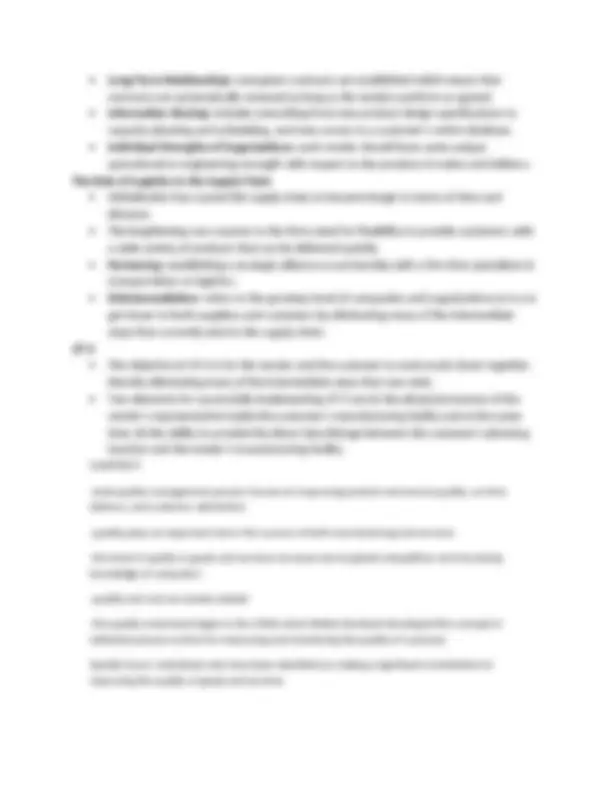
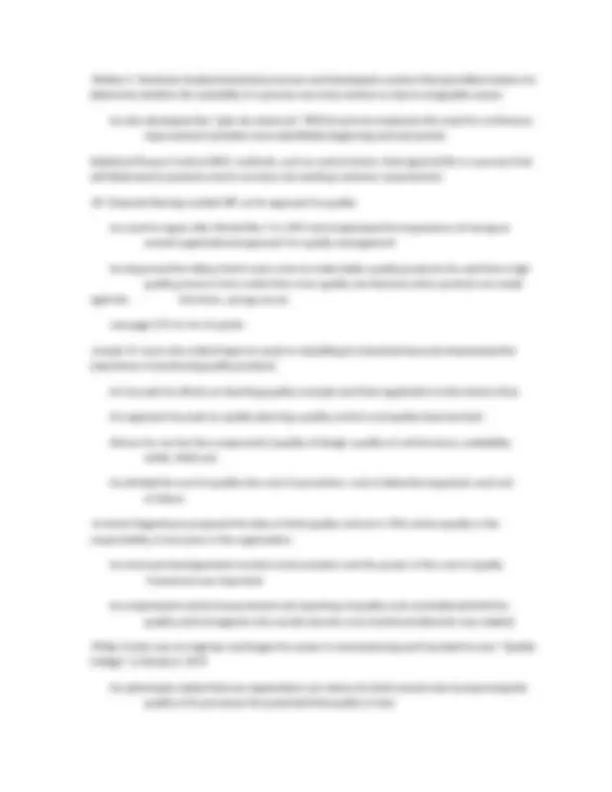
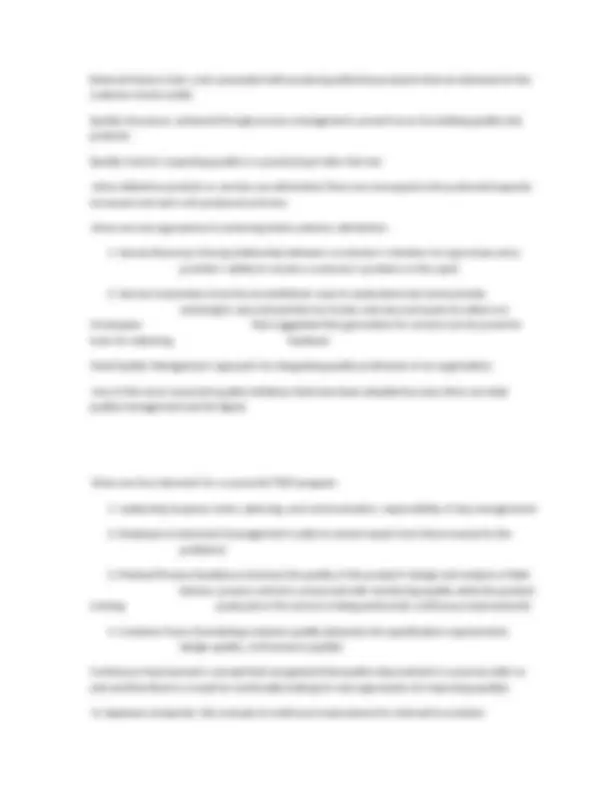
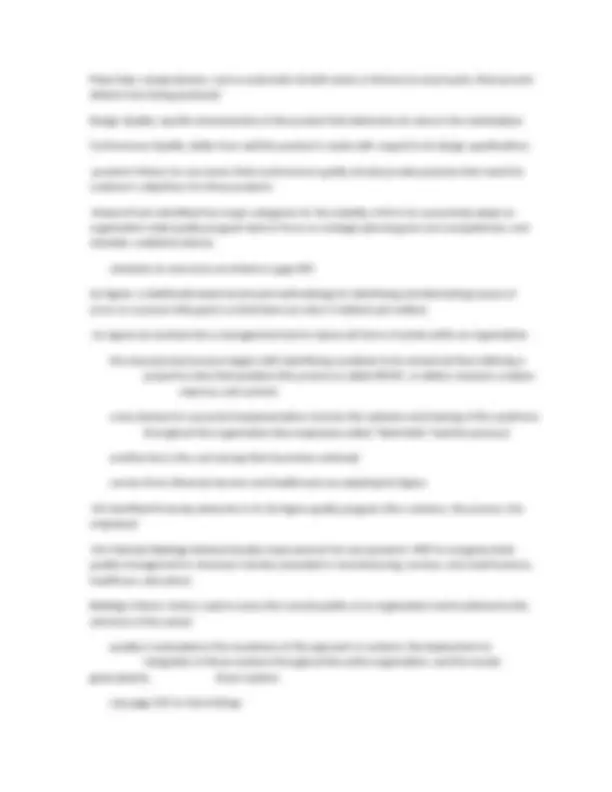
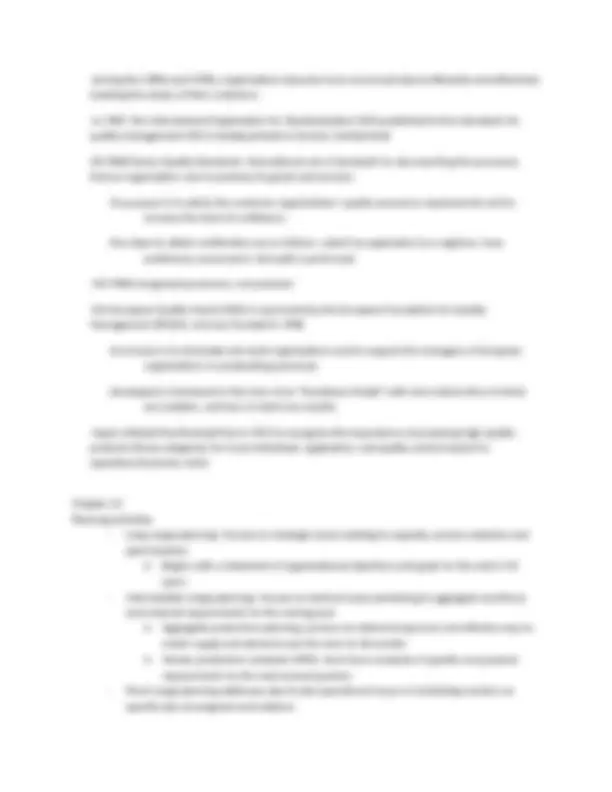
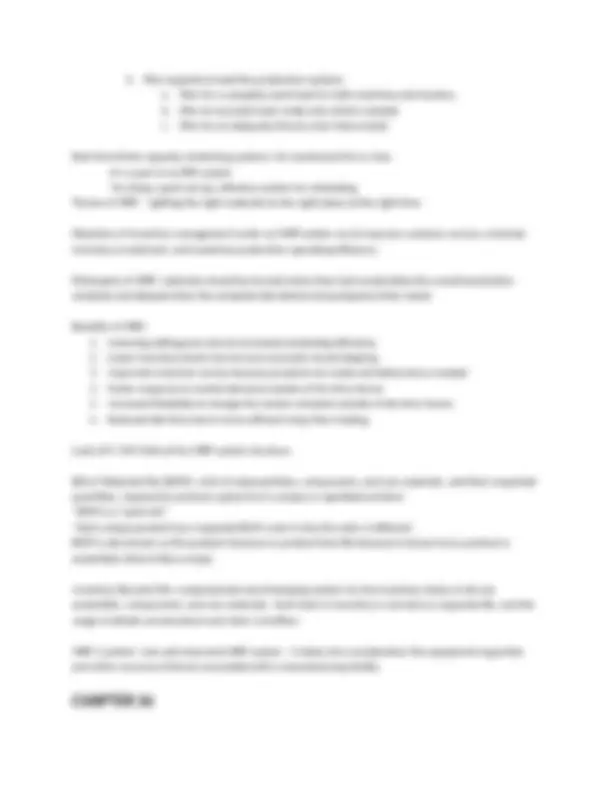
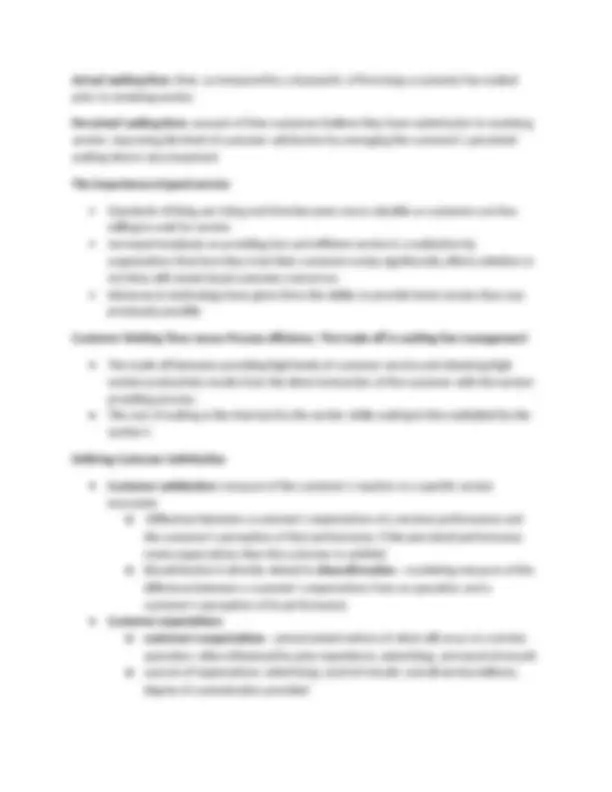
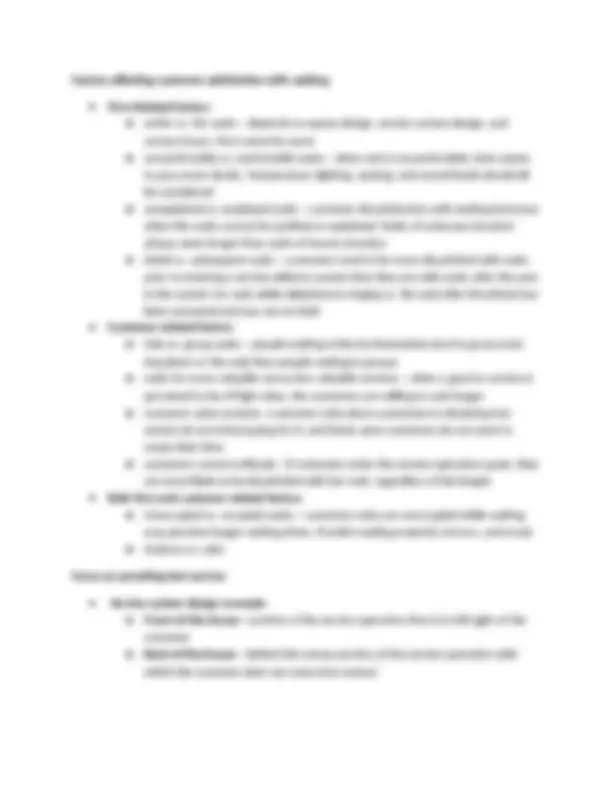
Study with the several resources on Docsity
Earn points by helping other students or get them with a premium plan
Prepare for your exams
Study with the several resources on Docsity
Earn points to download
Earn points by helping other students or get them with a premium plan
Community
Ask the community for help and clear up your study doubts
Discover the best universities in your country according to Docsity users
Free resources
Download our free guides on studying techniques, anxiety management strategies, and thesis advice from Docsity tutors
Material Type: Notes; Professor: Jefferson; Class: Operations Management; Subject: Management; University: Bryant University; Term: Fall 2009;
Typology: Study notes
1 / 16
This page cannot be seen from the preview
Don't miss anything!
-total quality management process focuses on improving product and service quality, on time delivery, and customer satisfaction -quality plays an important role in the success of both manufacturing and services -the level of quality in goods and services increases due to global competition and increasing knowledge of computers -quality and cost are closely related -the quality movement began in the 1920s when Walter Shewhart developed the concept of statistical process control for measuring and monitoring the quality of a process Quality Gurus: individuals who have been identified as making a significant contribution to improving the quality of goods and services
-Walter A. Shewhart studied industrial processes and developed a system that permitted workers to determine whether the variability of a process was truly random or due to assignable causes -he also developed the “plan-do-check-act” (PDCA) cycle to emphasize the need for continuous improvement (activities have identifiable beginning and end points) Statistical Process Control (SPC): methods, such as control charts, that signal shifts in a process that will likely lead to products and/or services not meeting customer requirements -W. Edwards Deming created SPC as his approach to quality -he went to Japan after World War II in 1947 and emphasized the importance of having an overall organizational approach for quality management -he disproved the fallacy that it costs more to make better quality products (he said that a high quality process is less costly than a low quality one because when products are made right the first time, savings occur) -see page 275 for his 14 points -Joseph M. Juran also visited Japan to assist in rebuilding its industrial base and emphasized the importance of producing quality products -he focused his efforts on teaching quality concepts and their application to the factory floor -his approach focused on quality planning, quality control, and quality improvement -fitness for use has five components (quality of design, quality of conformance, availability, safety, field use) -he divided the cost of quality into cost of prevention, cost of detection/appraisal, and cost of failure -Armand Feigenbaum proposed the idea of total quality control in 1956 where quality is the responsibility of everyone in the organization -he stressed interdependent mental communication and the power of the cost of quality framework was important -he emphasized careful measurement and reporting of quality costs and believed that the quality control engineer who would oversee cross functional elements was needed -Philip Crosby was an engineer and began his career in manufacturing and founded his own “Quality College” in Florida in 1979 -his philosophy stated that any organization can reduce its total overall costs by improving the quality of its processes (he preached that quality is free)
External Failure Costs: costs associated with producing defective products that are delivered to the customer (most costly) Quality Assurance: achieved through process management, prevent error by building quality into products Quality Control: inspecting quality in a product/part after the fact -when defective products or services are eliminated, there are more good units produced (capacity increases) and each unit produced costs less -there are two approaches to achieving total customer satisfaction:
-during the 1980s and 1990s, organizations became more concerned about efficiently and effectively meeting the needs of their customers -in 1987, the International Organization for Standardization (ISO) published its first standards for quality management (ISO is headquartered in Geneva, Switzerland) ISO 9000 Series Quality Standards: international set of standards for documenting the processes that an organization uses to produce its goods and services -its purpose is to satisfy the customer organizations’ quality assurance requirements and to increase the level of confidence -the steps to obtain certification are as follows: submit an application to a registrar, have preliminary assessment, full audit is performed -ISO 9000 recognized processes, not products -the European Quality Award (EQA) is sponsored by the European Foundation for Quality Management (EFQM), and was founded in 1988 -its mission is to stimulate and assist organizations and to support the managers of European organizations in accelerating processes -developed a framework in the form of an “Excellence Model” with nine criteria (five of which are enablers, and four of which are results) -Japan initiated the Deming Prize in 1951 to recognize the importance of producing high quality products (three categories for it are individuals, application, and quality control award for operations/business units) Chapter 13 Planning activities
Aggregate production planning