
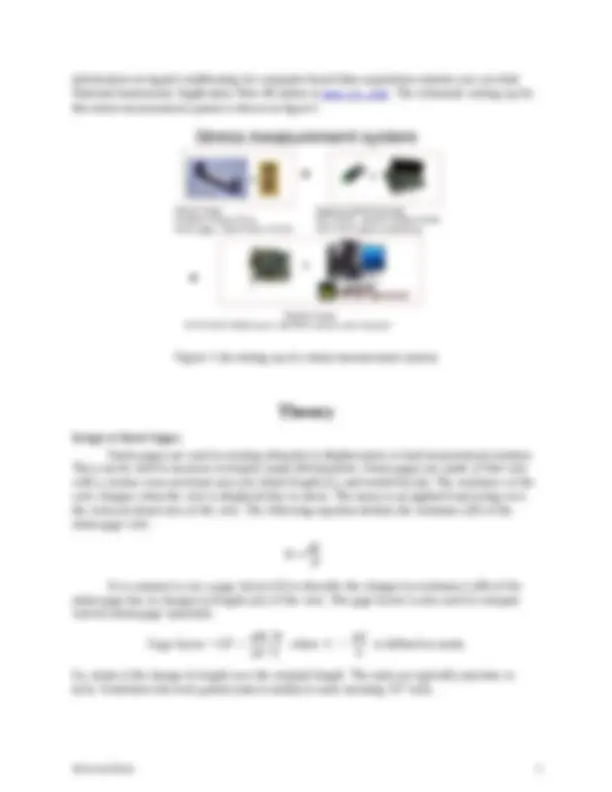
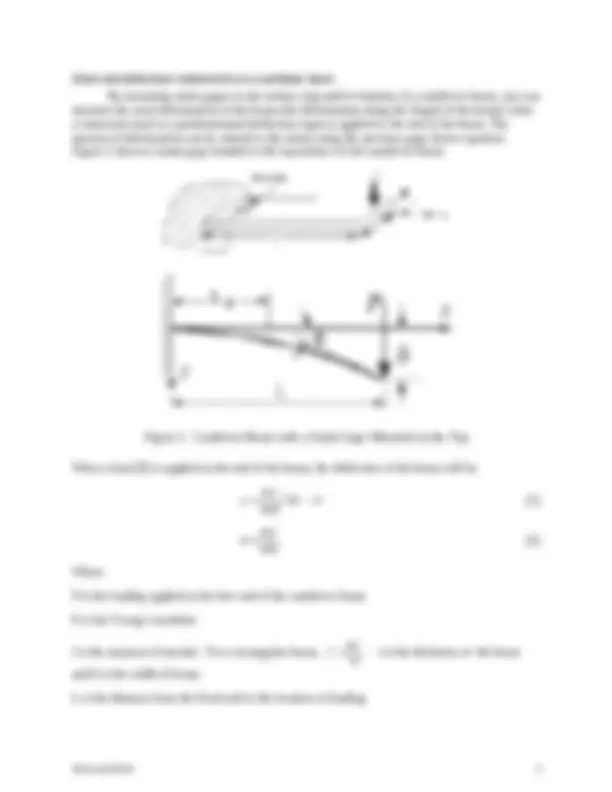
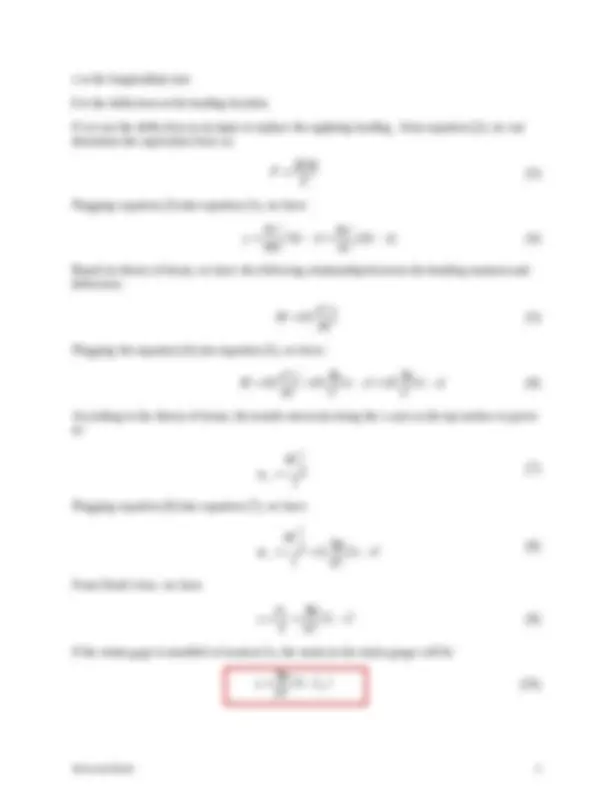
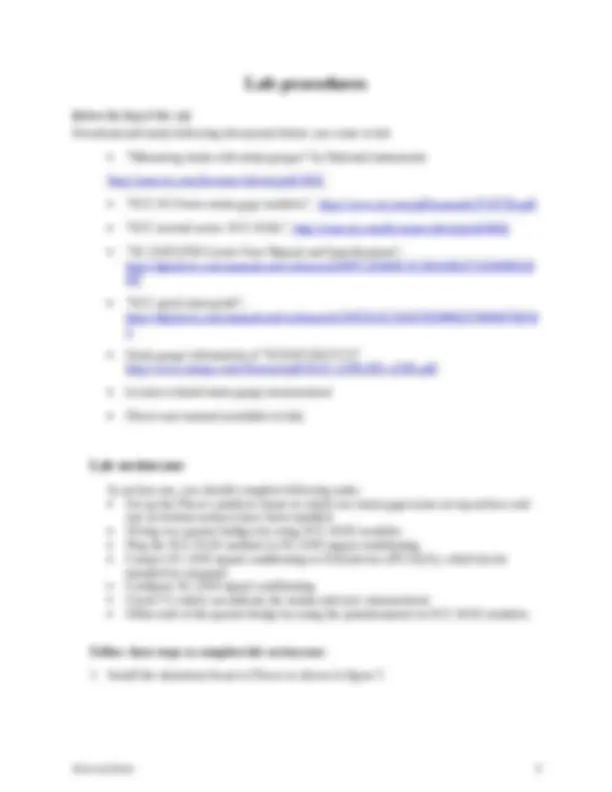
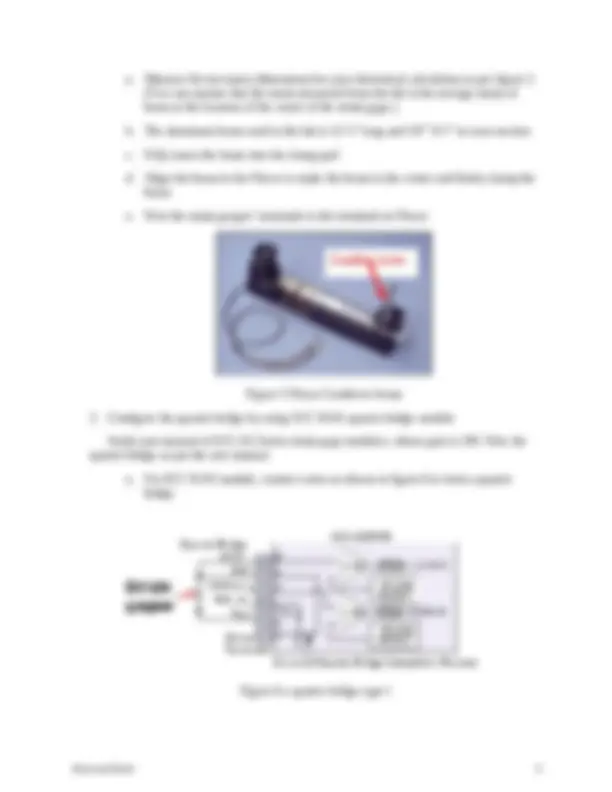
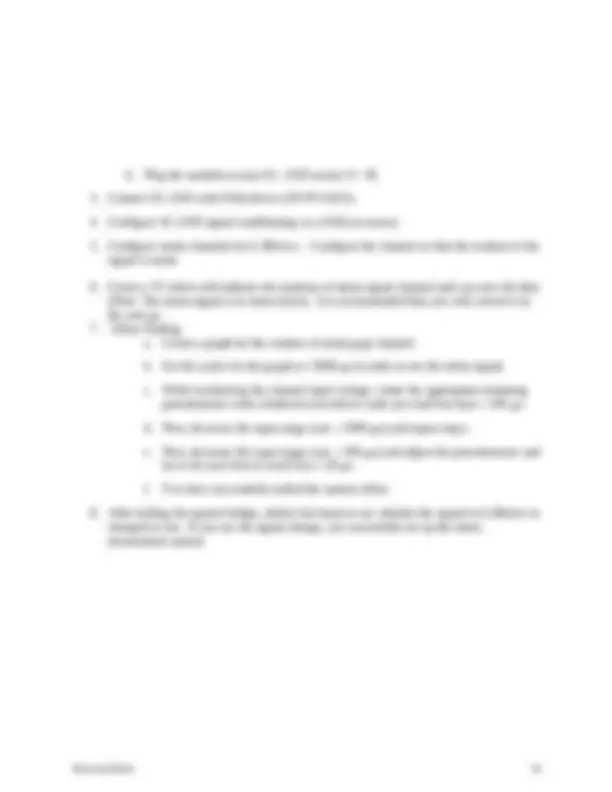
Study with the several resources on Docsity
Earn points by helping other students or get them with a premium plan
Prepare for your exams
Study with the several resources on Docsity
Earn points to download
Earn points by helping other students or get them with a premium plan
Community
Ask the community for help and clear up your study doubts
Discover the best universities in your country according to Docsity users
Free resources
Download our free guides on studying techniques, anxiety management strategies, and thesis advice from Docsity tutors
Instructions and theory for a lab experiment focused on stress and strain measurement using a strain gauge system and finite element analysis (fea). Students will learn to set up the system, calibrate it, and compare results with fea and theoretical calculations. Equipment list, setup instructions, and lab procedures are included.
Typology: Lab Reports
1 / 12
This page cannot be seen from the preview
Don't miss anything!
One critial, primary, must-satisfied design criteria for mechanical engineering is that the
actual stress in part or components during operations must be less than allowable stress specified
by the design engineering. The allowable stress of the materials is generally specified by the
material manufacturer and is a known variable for design engineers. The key issue is how to
find out the actual stress of the components.
Generally, three approaches are equally used in mechanical engineering, which are
theoretical prediction (calculation), finite element analysis (FEA) and strain & stress
measurement (testing).
When the geometry of components and loading conditions are simple, design engineers
can provide very acuurate theretical prediction of the actutal stresses in the components. When,
the geometry and loading conditions are complicated, design engineers can implement different
approaches to simplify the actual models into a handable models, the theroreticla pridction of
which can still be provided. In words, design engineers can always provide therotical prediction
of the actual stresses and use these as a starting point.
Finite element analysis (FEA) is a very powerful tool for predicting the sctual stresses,
which is a numeraical techniques and acquire to use computers, which is one of common tools
availabe for every design engineering. FEA can deal with very complicated geometry and
loading conditions. FEA can also provide relative accurate results acceptable by mose of design
engineers supposed that loading conditions, boundary conditions and initial conditions are
correctly considered.
In reality, both the theroretical prediction and FEA results of the actual stress of the
compoments must be verified by testing if components are critical components in the machine
or equipment. If the testing is properly carried out, the testing results will be results design
engineers must trust and use.
In this strain & stress lab, we will try to use three of approaches mentined above to carry
out the strain & stress evaluation. This lab illustrates the use of a strain gage. The gage is
bonded near the clamped end of a cantilever beam. Predetermined deflections are applied to the
free end of the beam. The strain gage measures the axial elongation of the beam. The therotical
caculation and FEA on the cantilever beam will also part of the lab. Three results will be
compared and discussed.
signal conditioning, configuring DAQ channel and compiling a strain VI.
cantilever beam. The maximum allowable deflection in this lab will be less than 0.5”.
beam.
using Solidworks.
Understand the strain measurement system and be able to set up this system for strain
measurement.
Be able to calibrate the system and properly interpret the measurement results
Comparison measurement with FEA and theoretical calculation
Computer running Windows
LabVIEW version 8.
SCC-SG01 quarter bridge module
SC-2345 signal conditioning with cable for connection between SC-2345 and DAQ device
NI PCI 6221 DAQ device
Strain Gage (SGD-6/120-LY13)
Flexor - Cantilever beam
Computer-based measurement systems are used in a wide variety of applications. In
laboratories, in field services and on manufacturing plant floors, these systems act as general-
purpose measurement tools well-suited for measuring voltage signals. However, many real-world
sensors and transducers require signal conditioning before a computer-based measurement
system can effectively and accurately acquire the signal. The front-end signal conditioning
system can include functions such as signal amplification, attenuation, filtering, electrical
isolation, simultaneous sampling, and multiplexing. In addition, many transducers require
excitation currents or voltages, bridge completion, linearization, or high amplification for proper
and accurate operation. Therefore, most computer-based measurement systems include some
form of signal conditioning in addition to plug-in data acquisition (DAQ) devices. For more
Strain and deflectiuon relationshin on a cantilever beam
By mounting strain gages to the surface (top and/or bottom) of a cantilever beam, you can
measure the axial deformation of the beam (the deformation along the length of the beam) when
a transverse load or a predetermined deflection input is applied to the end of the beam. The
amount of deformation can be related to the strain using the previous gage factor equation.
Figure 2 shows a strain gage bonded to the top surface of the cantilever beam.
Figure 2. Cantilever Beam with a Strain Gage Mounted on the Top
When a load (P) is applied at the end of the beam, the deflection of the beam will be:
L x
EI
Px y 3
6
2
3
3
EI
PL δ (2)
Where
P is the loading applied at the free end of the cantilever beam
E is the Young’s modules
I is the moment of inertial. For a rectangular beam,
12
3 bt I . t is the thickness of the beam
and b is the width of beam.
L is the distance from the fixed end to the location of loading
x is the longitudinal axis
is the deflection at the loading location.
If we use the deflection as an input to replace the applying loading, from equation (2), we can
determine the equivalent force as:
3
EIδ
P (^) (3)
Plugging equation (3) into equation (1), we have:
(^) ( 3 )
2
3
2 2
L x
L
x
L x
EI
Px
y
Based on theory of beam, we have the following relationship between the bending moment and
deflection:
2
2
dx
d y M EI (5)
Plugging the equation (4) into equation (5), we have:
L x
L
L x EI
L
dx
d y
M EI
2 3 3
2 3 3
(6)
According to the theory of beam, the tensile stress () along the x-axis at the top surface is given
as:
t M
x
Plugging equation (6) into equation (7), we have:
t E
I
t
M
x
3 2
From Hook’s law, we have
t
x
3 2
If the strain gage is installed at location Ls, the strain in the strain gauge will be
S
t
3 2
Figure 4 A quarter Wheatstone Bridge
If R 1 =R 2 , and R 3 =R 4 , But we replace R 4 with an active strain gauge. Then any change in
the strain gauge resistance will unbalance the bridge and produce a nonzero output voltage. If
the nominal resistance of the strain gage is designated as RG, then the strain-induced change in
resistance R can be expressed as R=RG ×GF×. We have
4
GF
2
GF 1
1
4
0 GF
EX
V
V
Before the Day of the Lab
Download and study following documents before you come to lab
“Measuring strain with strain gauges” by National instruments
http://zone.ni.com/devzone/cda/tut/p/id/
“SCC-SG Series strain gage modules”, http://www.ni.com/pdf/manuals/371073b.pdf
“SCC tutorial series: SCC-SG0x”, http://zone.ni.com/devzone/cda/tut/p/id/
“SC-2345/2350 Carrier User Manual and Specifications”,
http://digital.ni.com/manuals.nsf/websearch/09FC2D464C3C38A1862571850066A
“SCC quick start guide”,
http://digital.ni.com/manuals.nsf/websearch/5587D12C545D7ED9862570600070E
Strain gauge information of “SGD-6/120-LY13”
http://www.omega.com/Pressure/pdf/SGD_LINEAR1-AXIS.pdf
Lectures related strain gauge measurement
Flexor user manual (available in lab)
Lab section one
In section one, you should complete following tasks:
Set up the Flexor cantilever beam in which two strain gages (one on top surface and
one on bottom surface) have been installed
Wiring two quarter bridges by using SCC-SG01 modules
Plug the SCC-SG01 modules in SC-2345 signal conditioning
Connect SC-2345 signal conditioning to DAQ device (PCI 6221), which has be
installed in computer.
Configure SC-2345 signal conditioning
Create VI which can indicate the strains and save measurement
Offset null of the quarter bridge by using the potentiometers in SCC-SG01 modules.
Follow these steps to complete lab section one:
b. Plug the modules in any SC- 2345 socket J1 ~J8.
signal is strain
(Note: The strain signal is in strain (in/in). It is recommended that you will convert it in
the unit .
a. Create a graph for the readout of strain gage channel.
b. Set the scales for the graph at ±5000 in order to see the strain signal.
c. While monitoring the channel input voltage, rotate the appropriate trimming
potentiometer with a flathead screwdriver until you read less than ± 100 .
d. Next, decrease the input range (use ± 1000 ) and repeat step c.
e. Next, decrease the input range (use ± 100 ) and adjust the potentiometer and
try to do your best to reach less ± 20 .
f. You have successfully nulled the system offset.
changed or not. If you see the signal change, you sucessfully set up the strain
measurment system.
Lab section two
In section two, you should complete following tasks:
Conduct 8 strain measurements under the predetermined defection at the free end of
the cantilever beam. The maximum allowable deflection in this lab will be less than
Conduct the theoretical prediction of strain for the cantilever beam at the
predetermined deflection.
Compare the measurement with theoretical prediction.
Do analyze the data to check whether results are reasonable or not. If not, try to
figure out what is wrong and prepare to rerun it in lab three section.
Deflection
(^) (or (^) )
Measurement on top
strain gage
or
Measurement on bottom
strain gage
or
Theoretical prediction
Note: Create your own table to show the relative error.