
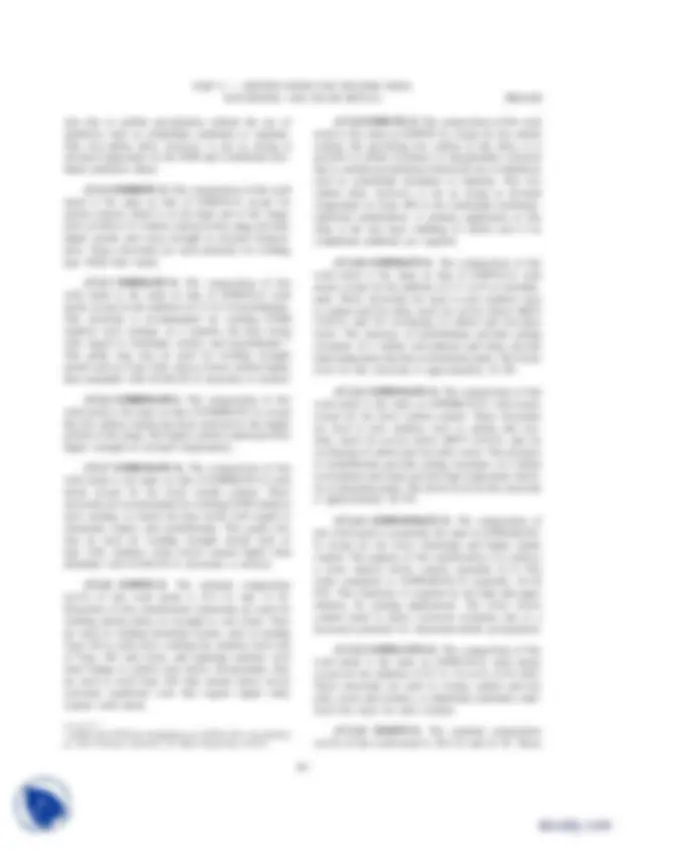
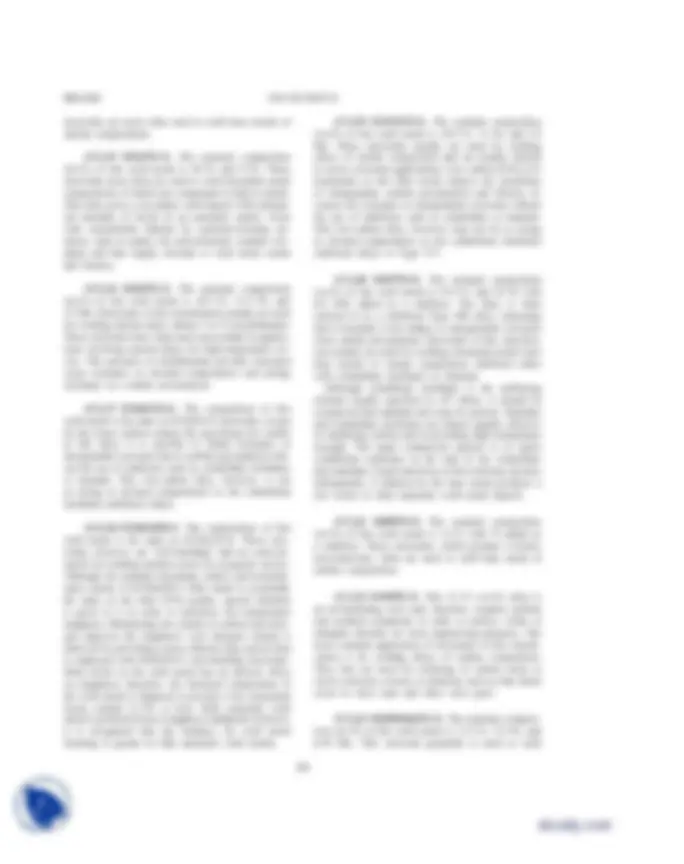
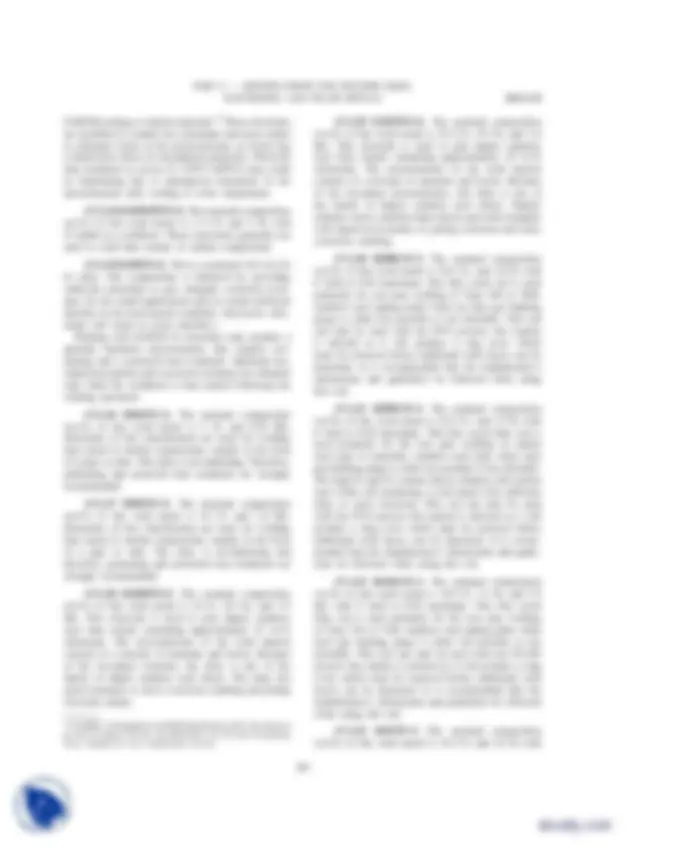
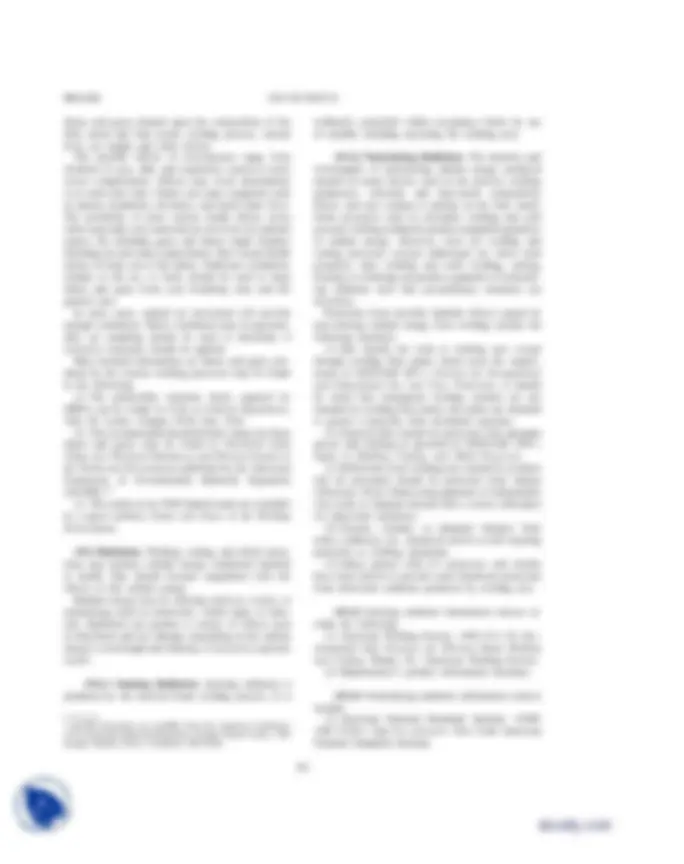
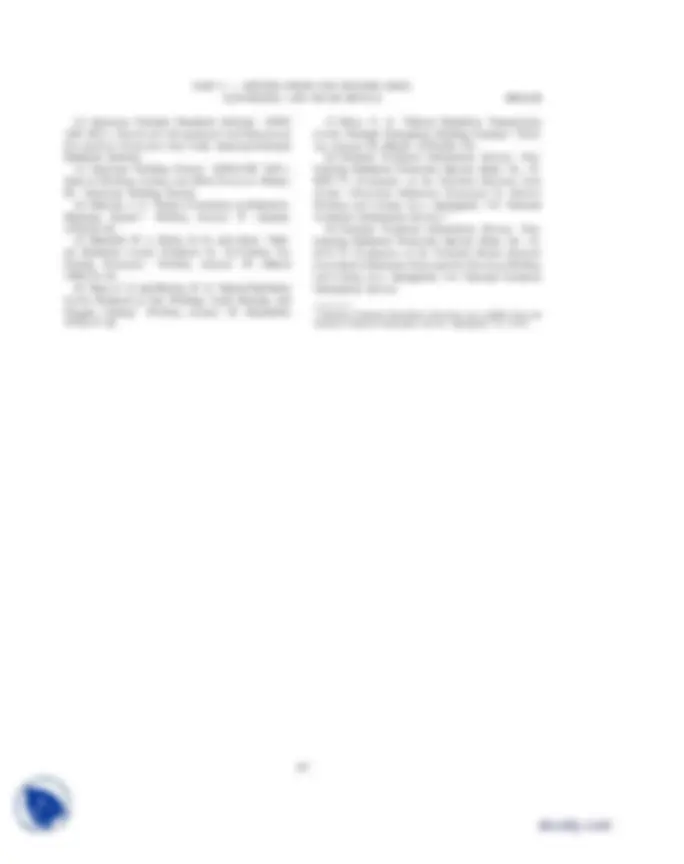
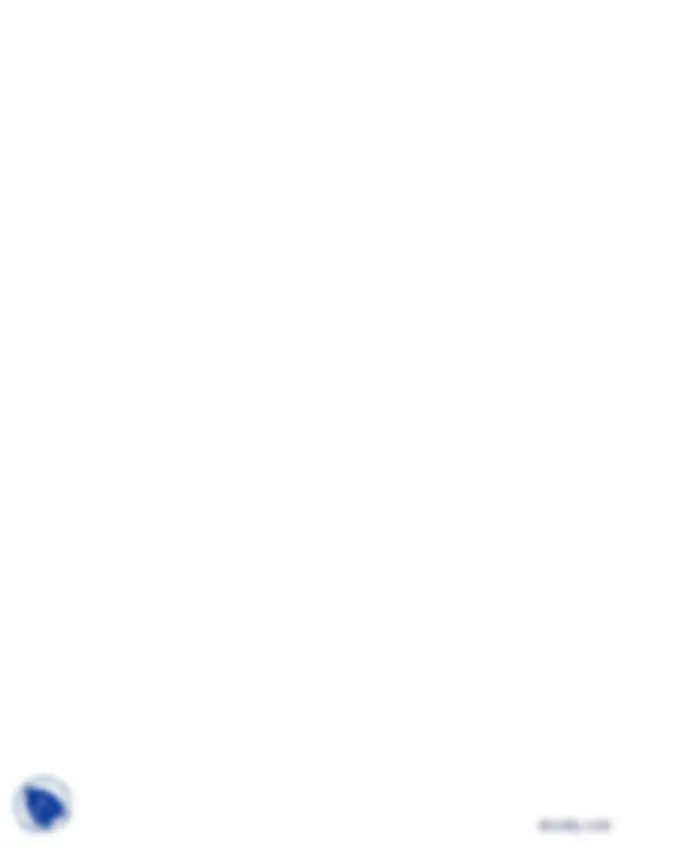
Study with the several resources on Docsity
Earn points by helping other students or get them with a premium plan
Prepare for your exams
Study with the several resources on Docsity
Earn points to download
Earn points by helping other students or get them with a premium plan
Community
Ask the community for help and clear up your study doubts
Discover the best universities in your country according to Docsity users
Free resources
Download our free guides on studying techniques, anxiety management strategies, and thesis advice from Docsity tutors
Dr. Ajitabh Sai delivered this lecture at Baba Farid University of Health Sciences for Mechanical and Materials Engineering Specifications course. It includes: Description, Electrodes, Rods, Composition, COnsiderations, Nominal, Weld, Corrosion, Scaling, Safety, Considerations
Typology: Exercises
1 / 10
This page cannot be seen from the preview
Don't miss anything!
PART C — SPECIFICATIONS FOR WELDING RODS, ELECTRODES, AND FILLER METALS SFA-5.
FIG. A3 ESPY PERCENT FERRITE DIAGRAM FOR STAINLESS WELD METAL
than 0.2 percent of nitrogen and greater than 10 percent of manganese.
A6.10.2 Espy Diagram^9 (Fig. A3) calculates the percent ferrite rather than FN of deposits of the “200” series (see A2.1) having manganese levels up to 15 percent and nitrogen contents up 0.35 percent (i.e., nitrogen-strengthened austenitic stainless steels).
A6.10.3 DeLong Diagram^10 (Fig. A4) is a modified Schaeffler Diagram^11 predicting the Ferrite Number (FN) up to a maximum of 18 FN. The diagram includes the nitrogen level in the calculation to predict the FN. The DeLong modifications to the Schaeffler Diagram provide a better correlation between the calculated and measured ferrite content of the weld metal; therefore, the Schaeffler Diagram is not shown in this specification. The new WRC 1992 Diagram (see Fig. A2) is the most accurate and preferred diagram for predicting the ferrite in “300” series stainless steel weld metals. Future
(^9) R. H. Espy, “Weldability of Nitrogen-Strengthened Stainless Steels.” Welding Journal 61[5] 149s–156s, 1982. (^10) W. T. DeLong, 1974 Adams Lecture; “Ferrite in Austenitic Stainless Steel Weld Metal.” Welding Journal 53[7] 273-s to 286-s (1974). (^11) A. E. Schaeffler, Metal Progress, 56, 680–680B.
485
publications of this specification may not include the DeLong Diagram.
A6.10.4 The differences between measured and calculated ferrite are somewhat dependent on the ferrite level of the deposit, increasing as the ferrite level increases. The agreement between the calculated and measured ferrite values is also strongly dependent on the quality of the chemical analysis. Variations in the results of the chemical analyses encountered from laboratory to laboratory can have significant effects on the calculated ferrite value, changing it as much as 4 to 8 FN.
A7. Description and Intended Use of Electrodes and Rods A7.1 Composition Considerations
A7.1.1 The chemical composition requirements for these electrodes and rods are patterned after those of ANSI/AWS A5.4, Specification for Stainless Steel Electrodes for Shielded Metal Arc Welding, and ANSI/ AWS A5.9, Specification for Bare Stainless Steel Elec- trodes and Rods.
SFA-5.22 1998 SECTION II
FIG. A4 DeLONG (FN) DIAGRAM FOR STAINLESS STEEL WELD METAL
A7.1.2 The chemical composition requirements of the EXXXTX-1 and EXXXTX-4 classifications are very similar. The requirements of the EXXXT0-3 classifica- tions are different from those of the previous two because self-shielding with a slag system alone is not as effective as shielding with a combination of a slag system and an external shielding gas. The EXXXT0- 3 deposits, therefore, usually have a higher nitrogen content. This means that, in order to control the ferrite content of the weld metal, the chemical compositions of the EXXXT0-3 deposits must have different Cr/Ni ratios than those of EXXXTX-1 and EXXXTX- 4 deposits. Since the atmosphere generated by E316LKT0- electrodes more efficiently shield the arc from nitrogen pickup than that produced by other EXXXT0-3 elec- trodes, the Cr/Ni ratio can be the same as for EXXXTX- 1 deposits without a loss of ferrite control.
486
A7.2 Intended Use of Electrodes and Rods
A7.2.1 E307TX-X. The nominal composition (wt.%) of this weld metal is 19 Cr, 9.7 Ni, 1.0 Mo and 4 Mn. These electrodes are used primarily for moderate strength welds with good crack resistance between dissimilar steels, such as welding austenitic manganese steel to carbon steel forgings or castings.
A7.2.2 E308TX-X. The nominal composition (wt.%) of this weld metal is 19.5 Cr and 10 Ni. Electrodes of this classification are most often used to weld base metal of similar composition such as AISI Types 301, 302, 304, 305, and 308.
A7.2.3 E308LTX-X. The composition of this weld metal is the same as that of E308TX-X, except for carbon content. By specifying low carbon in this alloy, it is possible to obtain resistance to intergranular corro-
SFA-5.22 1998 SECTION II
electrodes are most often used to weld base metals of similar compositions.
A7.2.15 E312TX-X. The nominal composition (wt.%) of this weld metal is 30 Cr and 9 Ni. These electrodes most often are used to weld dissimilar metal compositions of which one component is high in nickel. This alloy gives a two-phase weld deposit with substan- tial amounts of ferrite in an austenitic matrix. Even with considerable dilution by austenite-forming ele- ments, such as nickel, the microstructure remains two- phase and thus highly resistant to weld metal cracks and fissures.
A7.2.16 E316TX-X. The nominal composition (wt.%) of this weld metal is 18.5 Cr, 12.5 Ni, and 2.5 Mo. Electrodes of this classification usually are used for welding similar alloys (about 2 wt.% molybdenum). These electrodes have been used successfully in applica- tions involving special alloys for high-temperature ser- vice. The presence of molybdenum provides increased creep resistance at elevated temperatures and pitting resistance in a halide environment.
A7.2.17 E316LTX-X. The composition of this weld metal is the same as E316TX-X electrodes, except for the lower carbon content. By specifying low carbon in this alloy, it is possible to obtain resistance to intergranular corrosion due to carbide precipitation with- out the use of stabilizers such as columbium (niobium) or titanium. This low-carbon alloy, however, is not as strong at elevated temperatures as the columbium (niobium)-stabilized alloys.
A7.2.18 E316LKT0-3. The composition of this weld metal is the same as E316LTX-X. These elec- trodes, however, are “self-shielding” and are used pri- marily for welding stainless steels for cryogenic service. Although the nominal chromium, nickel, and molybde- num content of E316LKT0-3 filler metal is essentially the same as the other E316 grades, special attention is given to it in order to maximize low-temperature toughness. Minimizing the content of carbon and nitro- gen improves the toughness. Low nitrogen content is achieved by providing a more efficient slag system than is employed with EXXXT0-3 self-shielding electrodes. Delta ferrite in the weld metal has an adverse effect on toughness; therefore, the chemical composition of the weld metal is balanced to provide a low maximum ferrite content (3 FN or less). Fully austenitic weld metal is preferred from a toughness standpoint; however, it is recognized that the tendency for weld metal fissuring is greater in fully austenitic weld metals.
488
A7.2.19 E317LTX-X. The nominal composition (wt.%) of this weld metal is 19.5 Cr, 13 Ni, and 3. Mo. These electrodes usually are used for welding alloys of similar composition and are usually limited to severe corrosion applications. Low carbon (0.03 wt.% maximum) in this filler metal reduces the possibility of intergranular carbide precipitation and thereby in- creases the resistance to intergranular corrosion without the use of stabilizers such as columbium or titanium. This low-carbon alloy, however, may not be so strong at elevated temperatures as the columbium (niobium) stabilized alloys or Type 317.
A7.2.20 E347TX-X. The nominal composition (wt.%) of this weld metal is 19.5 Cr and 10 Ni with Cb (Nb) added as a stabilizer. The alloy is often referred to as a stabilized Type 308 alloy, indicating that it normally is not subject to intergranular corrosion from carbide precipitation. Electrodes of this classifica- tion usually are used for welding chromium-nickel steel base metals of similar composition stabilized either with columbium (niobium) or titanium. Although columbium (niobium) is the stabilizing element usually specified in 347 alloys, it should be recognized that tantalum also may be present. Tantalum and columbium (niobium) are almost equally effective in stabilizing carbon and in providing high-temperature strength. The usual commercial practice is to report columbium (niobium) as the sum of the columbium plus tantalum. Crack sensitivity of the weld may increase substantially, if dilution by the base metal produces a low ferrite or fully austenitic weld metal deposit.
A7.2.21 E409TX-X. The nominal composition (wt.%) of this weld metal is 12 Cr with Ti added as a stabilizer. These electrodes, which produce a ferritic microstructure, often are used to weld base metal of similar composition.
A7.2.22 E410TX-X. This 12 Cr (wt.%) alloy is an air-hardening steel and, therefore, requires preheat and postheat treatments in order to achieve welds of adequate ductility for most engineering purposes. The most common application of electrodes of this classifi- cation is for welding alloys of similar composition. They also are used for surfacing of carbon steels to resist corrosion, erosion, or abrasion, such as that which occur in valve seats and other valve parts.
A7.2.23 E410NiMoTX-X. The nominal composi- tion (wt.%) of this weld metal is 11.5 Cr, 4.5 Ni, and 0.55 Mo. This electrode generally is used to weld
PART C — SPECIFICATIONS FOR WELDING RODS, ELECTRODES, AND FILLER METALS SFA-5.
CA6NM castings or similar materials.^13 These electrodes are modified to contain less chromium and more nickel to eliminate ferrite in the microstructure, as ferrite has a deleterious effect on mechanical properties. Postweld heat treatment in excess of 1150°F (620°C) may result in rehardening due to untempered martensite in the microstructure after cooling to room temperature.
A7.2.24 E410NiTiTX-X. The nominal composition (wt.%) of this weld metal is 11.5 Cr and 4 Ni with Ti added as a stabilizer. These electrodes generally are used to weld base metals of similar composition.
A7.2.25 E430TX-X. This is a nominal 16.5 (wt.%) Cr alloy. The composition is balanced by providing sufficient chromium to give adequate corrosion resist- ance for the usual applications and yet retain sufficient ductility in the heat-treated condition. (Excessive chro- mium will result in lower ductility.) Welding with E430TX-X electrodes may produce a partially hardened microstructure that requires pre- heating and a postweld heat treatment. Optimum me- chanical properties and corrosion resistance are obtained only when the weldment is heat treated following the welding operation.
A7.2.26 E502TX-X. The nominal composition (wt.%) of this weld metal is 5 Cr and 0.55 Mo. Electrodes of this classification are used for welding base metal of similar composition, usually in the form of a pipe or tube. This alloy is air-hardening. Therefore, preheating and postweld heat treatment are strongly recommended.
A7.2.27 E505TX-X. The nominal composition (wt.%) of this weld metal is 9.2 Cr and 1.0 Mo. Electrodes of this classification are used for welding base metal of similar composition, usually in the form of a pipe or tube. The alloy is air-hardening and therefore, preheating and postweld heat treatment are strongly recommended.
A7.2.28 E2209TX-X. The nominal composition (wt.%) of this weld metal is 22 Cr, 8.5 Ni, and 3. Mo. This electrode is used to join duplex stainless steel base metals containing approximately 22 wt.% chromium. The microstructure of the weld deposit consists of a mixture of austenite and ferrite. Because of the two-phase structure, the alloy is one of the family of duplex stainless steel alloys. The alloy has good resistance to stress corrosion cracking and pitting corrosion attack.
(^13) CA6NM is a designation of ASTM Specification A352, Specification for Steel Castings, Ferritic and Martensitic, for Pressure Containing Parts, Suitable for Low Temperature Service.
489
A7.2.29 E2553TX-X. The nominal composition (wt.%) of this weld metal is 25.5 Cr, 9.5 Ni, and 3. Mo. This electrode is used to join duplex stainless steel base metals containing approximately 25 wt.% chromium. The microstructure of the weld deposit consists of a mixture of austenite and ferrite. Because of the two-phase microstructure, this alloy is one of the family of duplex stainless steel alloys. Duplex stainless steels combine high tensile and yield strengths with improved resistance to pitting corrosion and stress corrosion cracking. A7.2.30 R308LT1-5. The nominal composition (wt.%) of this weld metal is 18.5 Cr, and 10 Ni with C held to 0.03 maximum. This flux cored rod is used primarily for root pass welding of Type 304 or 304L stainless steel piping joints when an inert gas backing purge is either not possible or not desirable. This rod can only be used with the GTA process, but caution is advised as it will produce a slag cover which must be removed before additional weld layers can be deposited. It is recommended that the manufacturer’s instructions and guidelines be followed when using this rod. A7.2.31 R309LT1-5. The nominal composition (wt.%) of this weld metal is 23.5 Cr. and 13 Ni with C held to 0.03 maximum. This flux cored filler rod is used primarily for the root pass welding of carbon steel pipe to austenitic stainless steel pipe when inert gas backing purge is either not possible or not desirable. The high Cr and Ni content allows dilution with carbon steel while still producing a weld metal with sufficient alloy to resist corrosion. This rod can only be used with the GTA process but caution is advised as it will produce a slag cover which must be removed before additional weld layers can be deposited. It is recom- mended that the manufacturer’s instructions and guide- lines be followed when using this rod. A7.2.32 R316LT1-5. The nominal composition (wt.%) of this weld metal is 18.5 Cr, 13 Ni, and 2. Mo with C held to 0.03 maximum. This flux cored filler rod is used primarily for the root pass welding of Type 316 or 316L stainless steel piping joints when inert gas backing purge is either not possible or not desirable. This rod can only be used with the GTAW process but caution is advised as it will produce a slag cover which must be removed before additional weld layers can be deposited. It is recommended that the manufacturer’s instructions and guidelines be followed when using this rod. A7.2.33 R347T1-5. The nominal composition (wt.%) of this weld metal is 19.5 Cr and 10 Ni with
PART C — SPECIFICATIONS FOR WELDING RODS, ELECTRODES, AND FILLER METALS SFA-5.
combustible substance has been spilled on clothing, a change to clean, fire-resistant clothing should be made before working with open arcs or flames. Aprons, cape sleeves, leggings, and shoulder covers with bibs designed for welding service should be used. Where welding or cutting of unusually thick base metal is involved, sheet metal shields should be used for extra protection. Mechanization of highly hazardous processes or jobs should be considered. Other personnel in the work area should be protected by the use of noncombustible screens or by the use of appropriate protection as described in the previous paragraph. Before leaving a work area, hot work pieces should be marked to alert other persons of this hazard. No attempt should be made to repair or disconnect electrical equipment when it is under load; disconnection under load produces arcing of the contacts and may cause burns or shock, or both. (Note: Burns can be caused by touching hot equipment such as electrode holders, tips, and nozzles. Therefore, insulated gloves should be worn when these items are handled, unless an adequate cooling period has been allowed before touching.) The following references are for more detailed infor- mation on personal protection: (1) American National Standards Institute. ANSI/ ASC Z87.1, Practice for Occupational and Educational Eye and Face Protection. New York: American National Standards Institute. (2) American National Standards Institute. ANSI/ ASC Z41.1, Safety-Toe Footwear. New York: American National Standards Institute. (3) American Welding Society. ANSI/ASC Z49.1, Safety in Welding, Cutting, and Allied Processes. Miami, FL: American Welding Society. (4) OSHA, Code of Federal Regulations, Title 29— Labor, Chapter XVII, Part 1910. Washington, D.C.: U. S. Government Printing Office.^14
A9.2 Electrical Hazards. Electric shock can kill. However, it can be avoided. Live electrical parts should not be touched. The manufacturer’s instructions and recommended safe practices should be read and under- stood. Faulty installation, improper grounding, and in- correct operation and maintenance of electrical equip- ment are all sources of danger. All electrical equipment and workpieces should be grounded. The workpiece lead is not a ground lead; it is used only to complete the welding circuit. A separate connection is required to ground the workpiece.
(^14) OSHA standards may be obtained from the U. S. Government Printing Office, Washington, D.C. 20402.
491
The correct cable size should be used since sustained overloading will cause cable failure and can result in possible electrical shock or fire hazard. All electrical connections should be tight, clean, and dry. Poor connec- tions can overheat and even melt. Further, they can produce dangerous arcs and sparks. Water, grease, or dirt should not be allowed to accumulate on plugs, sockets, or electrical units. Moisture can conduct elec- tricity. To prevent shock, the work area, equipment, and clothing should be kept dry at all times. Welders should wear dry gloves and rubber-soled shoes, or stand on a dry board or insulated platform. Cables and connections should be kept in good condition. Improper or worn electrical connections may create conditions that could cause electrical shock or short circuits. Worn, damaged, or bare cables should not be used. Open circuit voltage should be avoided. When several welders are working with arcs of different polarities, or when a number of alternating current machines are being used, the open circuit voltages can be additive. The added voltages increase the severity of the shock hazard. In case of electric shock, the power should be turned OFF. If the rescuer must resort to pulling the victim from the live contact, nonconducting materials should be used. If the victim is not breathing, cardiopulmonary resuscitation (CPR) should be administered as soon as contact with the electrical source is broken. A physician should be called and CPR continued until breathing has been restored, or until a physician has arrived. Electrical burns are treated as thermal burns; that is, clean, cold (iced) compresses should be applied. Con- tamination should be avoided; the area should be cov- ered with a clean, dry dressing; and the patient should be transported to medical assistance. Recognized safety standards such as ANSI/ASC Z49.1, Safety in Welding, Cutting, and Allied Processes and NFPA No. 70, The National Electrical Code should be followed.^15
A9.3 Fumes and Gases. Many welding, cutting, and allied processes produce fumes and gases which may be harmful to health. Fumes are solid particles which originate from welding filler metals and fluxes, the base metal, and any coatings present on the base metal. Gases are produced during the welding process or may be produced by the effects of process radiation on the surrounding environment. Management, welders, and other personnel should be aware of the effects of these fumes and gases. The amount and composition of these
(^15) NFPA documents are available from the National Fire Protection Association, Batterymarch Park, Quincy, MA 02269.
SFA-5.22 1998 SECTION II
fumes and gases depend upon the composition of the filler metal and base metal, welding process, current level, arc length, and other factors. The possible effects of overexposure range from irritation of eyes, skin, and respiratory system to more severe complications. Effects may occur immediately or at some later time. Fumes can cause symptoms such as nausea, headaches, dizziness, and metal fume fever. The possibility of more serious health effects exists when especially toxic materials are involved. In confined spaces, the shielding gases and fumes might displace breathing air and cause asphyxiation. One’s head should always be kept out of the fumes. Sufficient ventilation, exhaust at the arc, or both, should be used to keep fumes and gases from your breathing zone and the general area. In some cases, natural air movement will provide enough ventilation. Where ventilation may be question- able, air sampling should be used to determine if corrective measures should be applied. More detailed information on fumes and gases pro- duced by the various welding processes may be found in the following: (1) The permissible exposure limits required by OSHA can be found in Code of Federal Regulations, Title 29—Labor, Chapter XVII, Part 1910. (2) The recommended threshold limit values for these fumes and gases may be found in Threshold Limit Values for Chemical Substances and Physical Agents in the Workroom Environment published by the American Conference of Governmental Industrial Hygienists (ACGIH).^16 (3) The results of an AWS-funded study are available in a report entitled, Fumes and Gases in the Welding Environment.
A9.4 Radiation. Welding, cutting, and allied opera- tions may produce radiant energy (radiation) harmful to health. One should become acquainted with the effects of this radiant energy. Radiant energy may be ionizing (such as x-rays), or nonionizing (such as ultraviolet, visible light, or infra- red). Radiation can produce a variety of effects such as skin burns and eye damage, depending on the radiant energy’s wavelength and intensity, if excessive exposure occurs.
A9.4.1 Ionizing Radiation. Ionizing radiation is produced by the electron beam welding process. It is
(^16) ACGIH documents are available from the American Conference of Governmental Industrial Hygienists, Kemper Woods Center, 1330 Kemper Meadow Drive, Cincinnati, OH 45240.
492
ordinarily controlled within acceptance limits by use of suitable shielding enclosing the welding area.
A9.4.2 Nonionizing Radiation. The intensity and wavelengths of nonionizing radiant energy produced depend on many factors, such as the process, welding parameters, electrode and base-metal composition, fluxes, and any coating or plating on the base metal. Some processes such as resistance welding and cold pressure welding ordinarily produce negligible quantities of radiant energy. However, most arc welding and cutting processes (except submerged arc when used properly), laser welding and torch welding, cutting, brazing, or soldering can produce quantities of nonioniz- ing radiation such that precautionary measures are necessary. Protection from possible harmful effects caused by non-ionizing radiant energy from welding include the following measures: (1) One should not look at welding arcs except through welding filter plates which meet the require- ments of ANSI/ASC Z87.1, Practice for Occupational and Educational Eye and Face Protection. It should be noted that transparent welding curtains are not intended as welding filter plates, but rather are intended to protect a passerby from incidental exposure. (2) Exposed skin should be protected with adequate gloves and clothing as specified in ANSI/ASC Z49.1, Safety in Welding, Cutting, and Allied Processes. (3) Reflections from welding arcs should be avoided, and all personnel should be protected from intense reflections. (Note: Paints using pigments of substantially zinc oxide or titanium dioxide have a lower reflectance for ultraviolet radiation.) (4) Screens, curtains, or adequate distance from aisles, walkways, etc., should be used to avoid exposing passersby to welding operations. (5) Safety glasses with UV protective side shields have been shown to provide some beneficial protection from ultraviolet radiation produced by welding arcs.
A9.4.3 Ionizing radiation information sources in- clude the following: (1) American Welding Society. AWS F2.1-78, Rec- ommended Safe Practices for Electron Beam Welding and Cutting. Miami, FL: American Welding Society. (2) Manufacturer’s product information literature.
A9.4.4 Nonionizing radiation information sources include: (1) American National Standards Institute. ANSI/ ASC Z136.1, Safe Use of Lasers. New York: American National Standards Institute.