
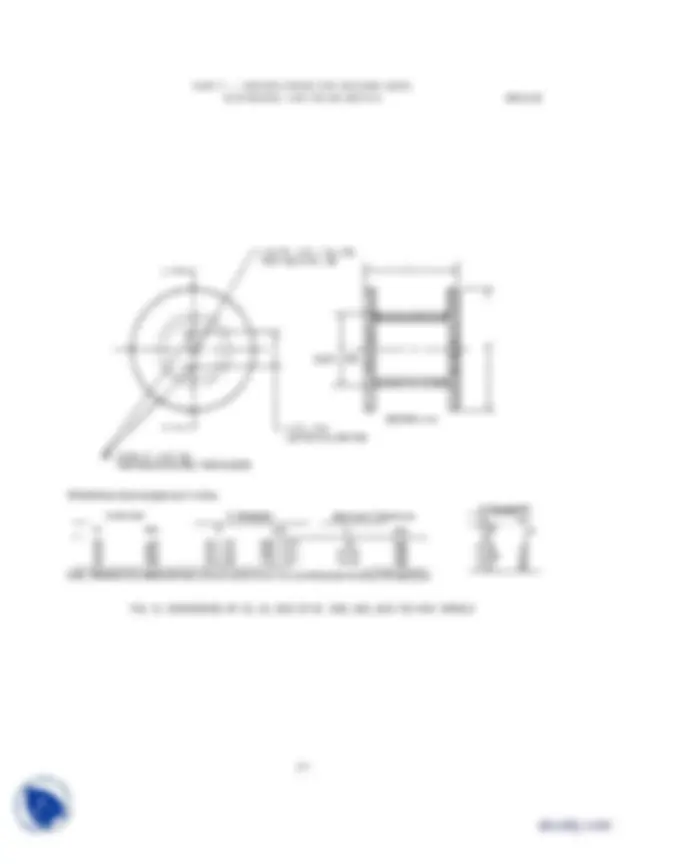
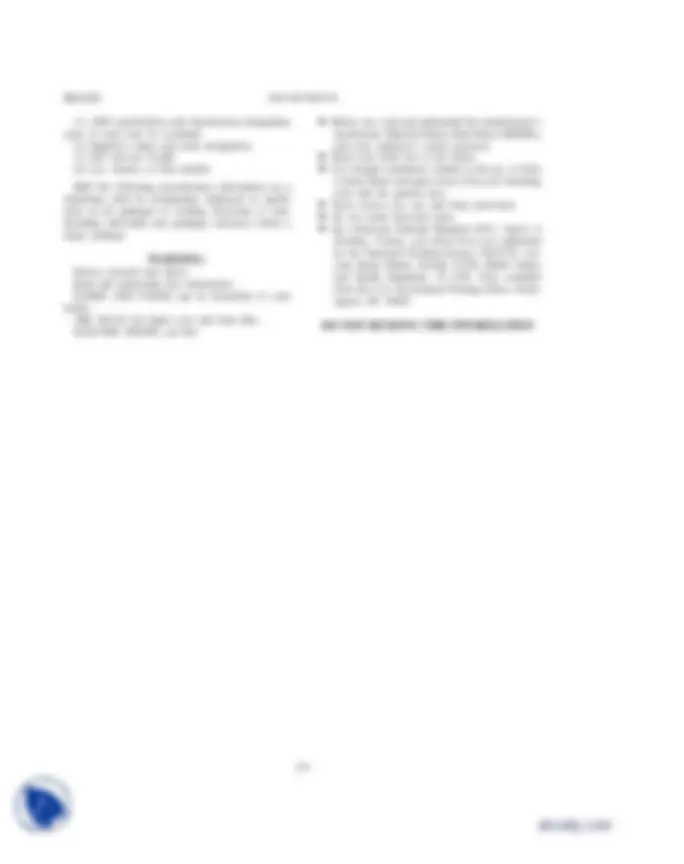
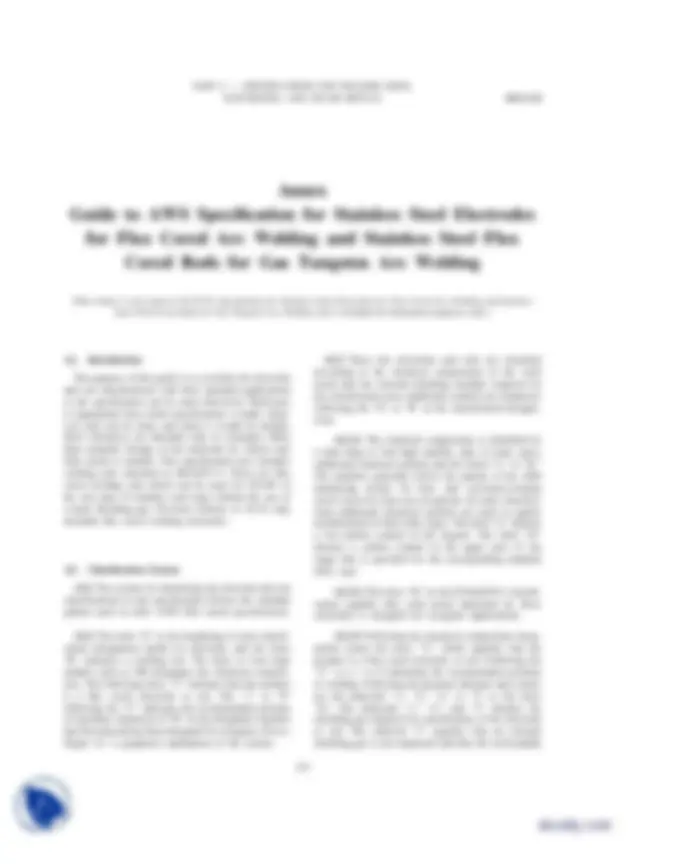
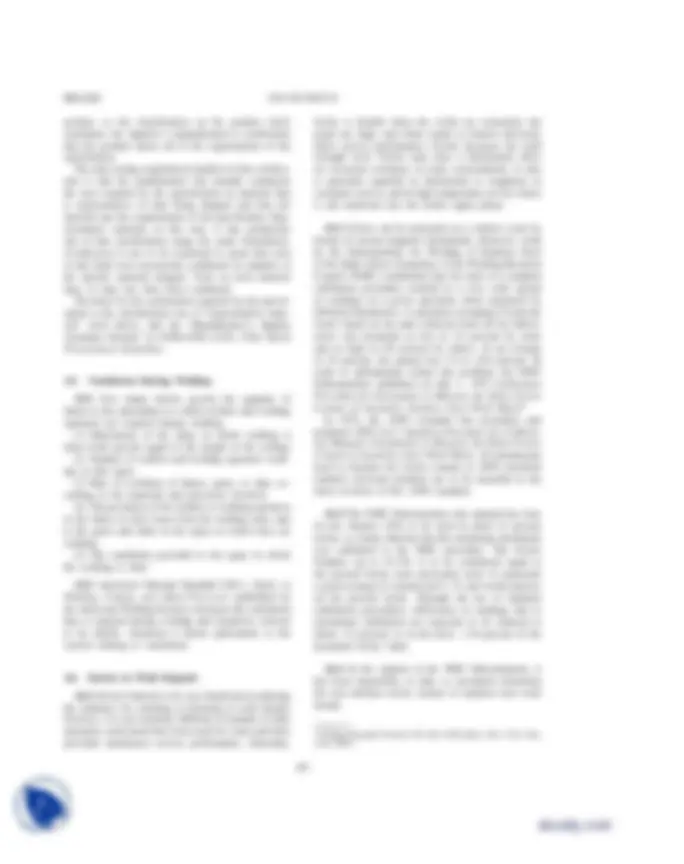
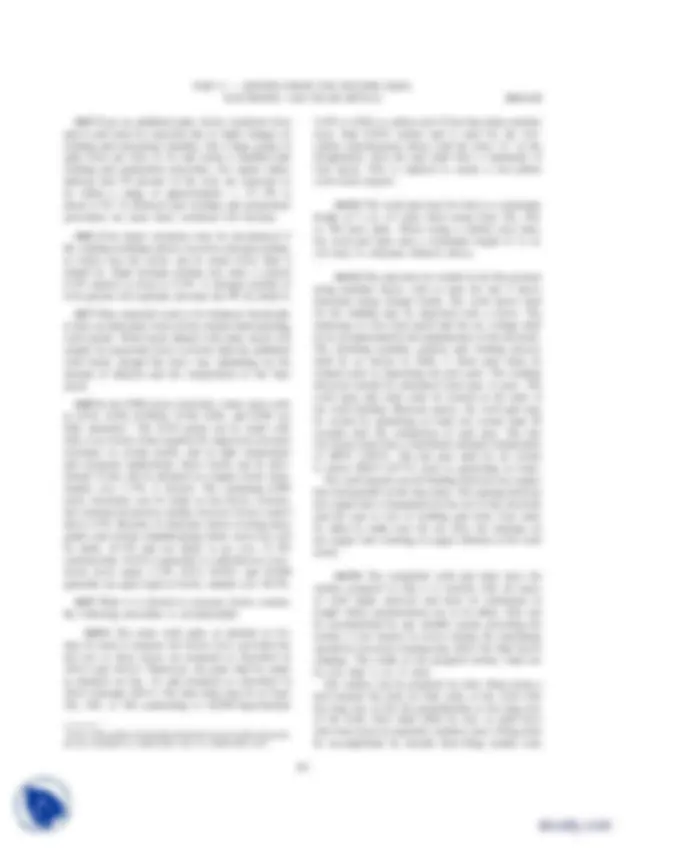
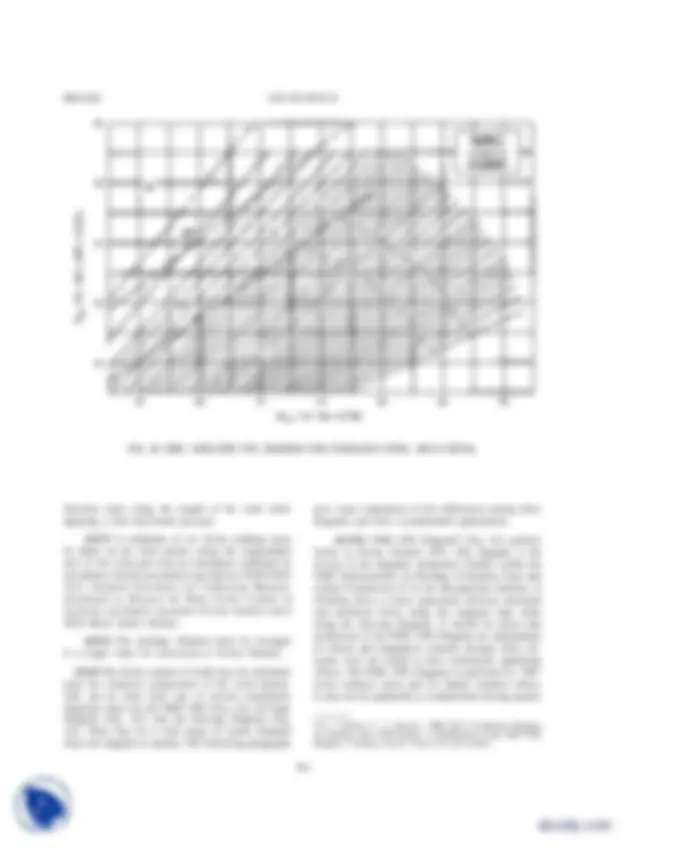
Study with the several resources on Docsity
Earn points by helping other students or get them with a premium plan
Prepare for your exams
Study with the several resources on Docsity
Earn points to download
Earn points by helping other students or get them with a premium plan
Community
Ask the community for help and clear up your study doubts
Discover the best universities in your country according to Docsity users
Free resources
Download our free guides on studying techniques, anxiety management strategies, and thesis advice from Docsity tutors
Dr. Ajitabh Sai delivered this lecture at Baba Farid University of Health Sciences for Mechanical and Materials Engineering Specifications course. It includes: Warning, Fumes, Gases, Electric, Shock, Gas, Tungsten, Arc, Welding, Electrodes
Typology: Exercises
1 / 10
This page cannot be seen from the preview
Don't miss anything!
PART C — SPECIFICATIONS FOR WELDING RODS, ELECTRODES, AND FILLER METALS SFA-5.
FIG. 9 DIMENSIONS OF STANDARD 4 IN. (100 MM) SPOOL
475
SFA-5.22 1998 SECTION II
FIG. 10 DIMENSIONS OF STANDARD 8, 12, AND 14 IN. (200, 300 AND 350 MM) SPOOLS
476
SFA-5.22 1998 SECTION II
(1) AWS specification and classification designation (year of issue may be excluded) (2) Supplier’s name and trade designation (3) Size and net weight (4) Lot, control, or heat number 22.2 The following precautionary information (as a minimum) shall be prominently displayed in legible print on all packages of welding electrodes or rods, including individual unit packages enclosed within a larger package.
Protect yourself and others. Read and understand this information. FUMES AND GASES can be hazardous to your health. ARC RAYS can injure eyes and burn skin. ELECTRIC SHOCK can kill.
478
O Before use, read and understand the manufacturer’s instructions, Material Safety Data Sheets (MSDSs), and your employer’s safety practices. O Keep your head out of the fumes. O Use enough ventilation, exhaust at the arc, or both, to keep fumes and gases away from your breathing zone and the general area. O Wear correct eye, ear, and body protection. O Do not touch electrical parts. O See American National Standard Z49.1, Safety in Welding, Cutting, and Allied Processes published by the American Welding Society, 550 N.W. LeJ- eune Road, Miami, Florida 33126; OSHA Safety and Health Standards, 29 CFR 1910, available from the U.S. Government Printing Office, Wash- ington, DC 20402.
PART C — SPECIFICATIONS FOR WELDING RODS, ELECTRODES, AND FILLER METALS SFA-5.
(This Annex is not a part of A5.22-95, Specification for Stainless Steel Electrodes for Flux Cored Arc Welding and Stainless Steel Flux Cored Rods for Gas Tungsten Arc Welding, but is included for information purposes only.)
A1. Introduction
The purpose of this guide is to correlate the electrode and rod classifications with their intended applications so the specification can be used effectively. Reference to appropriate base metal specifications is made when- ever that can be done and when it would be helpful. Such references are intended only as examples rather than complete listings of the materials for which each filler metal is suitable. This specification now includes welding rods classified as RXXXT1-5. These are flux cored welding rods which can be used for GTAW of the root pass of stainless steel pipe without the use of a back shielding gas. Previous editions of A5.22 only included flux cored welding electrodes.
A2. Classification System
A2.1 The system for identifying the electrode and rod classifications in this specification follows the standard pattern used in other AWS filler metal specifications.
A2.2 The letter “E” at the beginning of each classifi- cation designation stands for electrode, and the letter “R” indicates a welding rod. The three or four digit number such as 308 designates the chemical composi- tion. The following letter “T” indicates that the product is a flux cored electrode or rod. The “1” or “0” following the “T” indicates the recommended position of operation. Inclusion of “K” in the designator signifies that the material has been designed for cryogenic service. Figure A1 is graphical explanation of the system.
479
A2.3 Since the electrodes and rods are classified according to the chemical composition of the weld metal and the external shielding medium required for the classification tests, additional symbols are employed, following the “E” or “R” in the classification designa- tions.
A2.3.1 The chemical composition is identified by a three-digit or four-digit number, and, in some cases, additional chemical symbols and the letters “L” or “H.” The numbers generally follow the pattern of the AISI numbering system for heat- and corrosion-resisting steels; however, there are exceptions. In some classifica- tions additional chemical symbols are used to signify modifications of basic alloy types. The letter “L” denotes a low-carbon content in the deposit. The letter “H” denotes a carbon content in the upper part of the range that is specified for the corresponding standard alloy type.
A2.3.2 The letter “K” in the E316LKT0-3 classifi- cation signifies that weld metal deposited by these electrodes is designed for cryogenic applications.
A2.3.3 Following the chemical composition desig- nation comes the letter “T,” which signifies that the product is a flux cored electrode or rod. Following the “T” is a 1 or 0 indicating the recommended position of welding. Following the position indicator and a dash, are the numerals “1,” “3,” “4,” or “5” or the letter “G.” The numerals “1,” “4,” and “5” identify the shielding gas required for classification of the electrode or rod. The numeral “3” signifies that an external shielding gas is not employed and that the weld puddle
PART C — SPECIFICATIONS FOR WELDING RODS, ELECTRODES, AND FILLER METALS SFA-5.
metal of a “G” classification and filler metal of a similar classification without the “G” (or even with it, for that matter) will be readily apparent from the use of the words “not required” and “not specified” in the specification. The use of these words is as follows: Not Specified is used in those areas of the specification that refer to the results of some particular test. It indicates that the requirements for that test are not specified for that particular classification. Not Required is used in those areas of the specification that refer to the tests that must be conducted in order to classify a filler metal (or a welding material). It indicates that test is not required because the require- ments (results) for the test have not been specified for that particular classification. Restating the case, when a requirement is not speci- fied, it is not necessary to conduct the corresponding test in order to classify a filler metal to that classification. When a purchaser wants the information provided by that test, in order to consider a particular product of that classification for a certain application, the purchaser will have to arrange for that information with the supplier of the product. The purchaser will have to establish with that supplier just what the testing proce- dure and the acceptance requirements are to be, for that test. The purchaser may want to incorporate that information (via ANSI/AWS A5.01, Filler Metal Pro- curement Guidelines ) in the purchase order.
A2.3.9 Request for Filler Metal Classification (1) When a filler metal cannot be classified according to some classification other than a “G” classification, the manufacturer may request that a classification be established for that filler metal. The manufacturer may do this by following the procedure given here. When the manufacturer elects to use the “G” classification, the Filler Metal Committee recommends that the manu- facturer still request that a classification be established for that filler metal, as long as the filler metal is of commercial significance. (2) A request to establish a new filler metal classifi- cation must be a written request and it needs to provide sufficient detail to permit the Filler Metal Committee or the Subcommittee to determine whether a new classification or the modification of an existing classifi- cation is more appropriate, and whether either is neces- sary to satisfy the need. The request needs to state the variables and their limits, for such a classification or modification. The request should contain some indica- tion of the time by which completion of the new classification or modification is needed. (3) The request should be sent to the Secretary of the Filler Metal Committee at AWS Headquarters.
481
Upon receipt of the request, the Secretary will do the following: (a) Assign an identifying number to the request. This number will include the date the request was received. (b) Confirm receipt of the request and give the identification number to the person who made the request. (c) Send a copy of the request to the Chairman of the Filler Metal Committee and the Chairman of the particular Subcommittee involved. (d) File the original request. (3) Add the request to the log of outstanding requests. (4) All necessary action on each request will be completed as soon as possible. If more than 12 months lapse, the Secretary shall inform the requestor of the status of the request, with copies to the Chairman of the Committee and the Subcommittee. Requests still outstanding after 18 months shall be considered not to have been answered in a “timely manner” and the Secretary shall report these to the Chairman of the Filler Metal Committee, for the Chair’s action. (5) The Secretary shall include a copy of the log of all requests pending and those completed during the preceding year with the agenda for each Filler Metal Committee meeting. Any other publication of requests that have been completed will be at the option of the American Welding Society, as deemed appropriate.
A3. Acceptance Acceptance of all welding materials classified under this specification is in accordance with ANSI/AWS A5.01, Filler Metal Procurement Guidelines, as the specification states. Any testing a purchaser requires of the supplier, for material shipped in accordance with this specification, shall be clearly stated in the purchase order, according to the provisions of ANSI/AWS A5.01. In the absence of any such statement in the purchase order, the supplier may ship the material with whatever testing he normally conducts on material of that classifi- cation, as specified in Schedule F, Table 1, of ANSI/ AWS A5.01. Testing in accordance with any other Schedule in that Table must be specifically required by the purchase order. In such cases, acceptance of the material shipped will be in accordance with those requirements.
A4. Certification The act of placing the AWS specification and classi- fication designations on the packaging enclosing the
SFA-5.22 1998 SECTION II
product, or the classification on the product itself, constitutes the supplier’s (manufacturer’s) certification that the product meets all of the requirements of the specification. The only testing requirement implicit in this certifica- tion is that the manufacturer has actually conducted the tests required by the specification on material that is representative of that being shipped and that the material met the requirements of the specification. Rep- resentative material, in this case, is any production run of that classification using the same formulation. Certification is not to be construed to mean that tests of any kind were necessarily conducted on samples of the specific material shipped. Tests on such material may, or may not, have been conducted. The basis for the certification required by the specifi- cation is the classification test of “representative mate- rial” cited above, and the “Manufacturer’s Quality Assurance System” in ANSI/AWS A5.01, Filler Metal Procurement Guidelines.
A5. Ventilation During Welding
A5.1 Five major factors govern the quantity of fumes in the atmosphere to which welders and welding operators are exposed during welding: (1) Dimensions of the space in which welding is done (with special regard to the height of the ceiling) (2) Number of welders and welding operators work- ing in that space (3) Rate of evolution of fumes, gases, or dust, ac- cording to the materials and processes involved (4) The proximity of the welders or welding operators to the fumes as they issue from the welding zone, and to the gases and dusts in the space in which they are working (5) The ventilation provided to the space in which the welding is done
A5.2 American National Standard Z49.1, Safety in Welding, Cutting, and Allied Processes (published by the American Welding Society), discusses the ventilation that is required during welding and should be referred to for details. Attention is drawn particularly to the section relating to ventilation.
A6. Ferrite in Weld Deposits
A6.1 Ferrite is known to be very beneficial in reducing the tendency for cracking or fissuring in weld metals; however, it is not essential. Millions of pounds of fully austenitic weld metal have been used for years and have provided satisfactory service performance. Generally,
482
ferrite is helpful when the welds are restrained, the joints are large, and when cracks or fissures adversely affect service performance. Ferrite increases the weld strength level. Ferrite may have a detrimental effect on corrosion resistance in some environments. It also is generally regarded as detrimental to toughness in cryogenic service, and in high-temperature service where it can transform into the brittle sigma phase.
A6.2 Ferrite can be measured on a relative scale by means of various magnetic instruments. However, work by the Subcommittee for Welding of Stainless Steel of the High Alloys Committee of the Welding Research Council (WRC) established that the lack of a standard calibration procedure resulted in a very wide spread of readings on a given specimen when measured by different laboratories. A specimen averaging 5.0 percent ferrite based on the data collected from all the labora- tories was measured as low as 3.5 percent by some and as high as 8.0 percent by others. At an average of 10 percent, the spread was 7.0 to 16.0 percent. In order to substantially reduce this problem, the WRC Subcommittee published on July 1, 1972 Calibration Procedure for Instruments to Measure the Delta Ferrite Content of Austenitic Stainless Steel Weld Metal.^6 In 1974, the AWS extended this procedure and prepared AWS A4.2, Standard Procedure for Calibrat- ing Magnetic Instruments to Measure the Delta Ferrite Content of Austenitic Steel Weld Metal. All instruments used to measure the ferrite content of AWS classified stainless electrode products are to be traceable to the latest revision of this AWS standard.
A6.3 The WRC Subcommittee also adopted the term Ferrite Number (FN) to be used in place of percent ferrite, to clearly indicate that the measuring instrument was calibrated to the WRC procedure. The Ferrite Number, up to 10 FN, is to be considered equal to the percent ferrite term previously used. It represents a good average of commercial U. S. and world practice on the percent ferrite. Through the use of standard calibration procedures, differences in readings due to instrument calibration are expected to be reduced to about 6 5 percent, or at the most, 6 10 percent of the measured ferrite value.
A6.4 In the opinion of the WRC Subcommittee, it has been impossible, to date, to accurately determine the true absolute ferrite content of stainless steel weld metals.
(^6) Welding Research Council, 345 East 47th Street, New York, New York 10017
SFA-5.22 1998 SECTION II
FIG. A2 WRC—WRC-1992 (FN) DIAGRAM FOR STAINLESS STEEL WELD METAL
direction only) along the length of the weld while applying a firm downward pressure.
A6.9.5 A minimum of six ferrite readings must be taken on the filed surface along the longitudinal axis of the weld pad with an instrument calibrated in accordance with the procedures specified in ANSI/AWS A4.2, Standard Procedures for Calibrating Magnetic Instruments to Measure the Delta Ferrite Content of Austenitic and Duplex Austenitic-Ferritic Stainless Steel Weld Metal (latest edition).
A6.9.6 The readings obtained must be averaged to a single value for conversion to Ferrite Number.
A6.10 The ferrite content of welds may be calculated from the chemical composition of the weld deposit. This can be done from one of several constitution diagrams; these are the WRC-1992 (Fig. A2), the Espy Diagram (Fig. A3), and the DeLong Diagram (Fig. A4). There may be a wide range of results obtained from one diagram to another. The following paragraphs
484
give some explanation of the differences among these diagrams and their recommended applications.
A6.10.1 WRC-1992 Diagram^8 (Fig. A2) predicts ferrite in Ferrite Number (FN). This diagram is the newest of the diagrams mentioned. Studies within the WRC Subcommittee on Welding of Stainless Steel and within Commission II of the International Institute of Welding show a closer agreement between measured and predicted ferrite using this diagram than when using the DeLong Diagram. It should be noted that predictions of the WRC-1992 Diagram are independent of silicon and manganese contents because these ele- ments were not found to have statistically significant effects. The WRC-1992 Diagram is preferred for “300” series stainless steels and for duplex stainless alloys. It may not be applicable to compositions having greater
(^8) D. J. Kotecki, T. A. Siewert, “WRC-1992 Constitution Diagram for Stainless Steel Weld Metals: A Modification of the WRC- Diagram.” Welding Journal 71[5] 171s–178s (1992).