
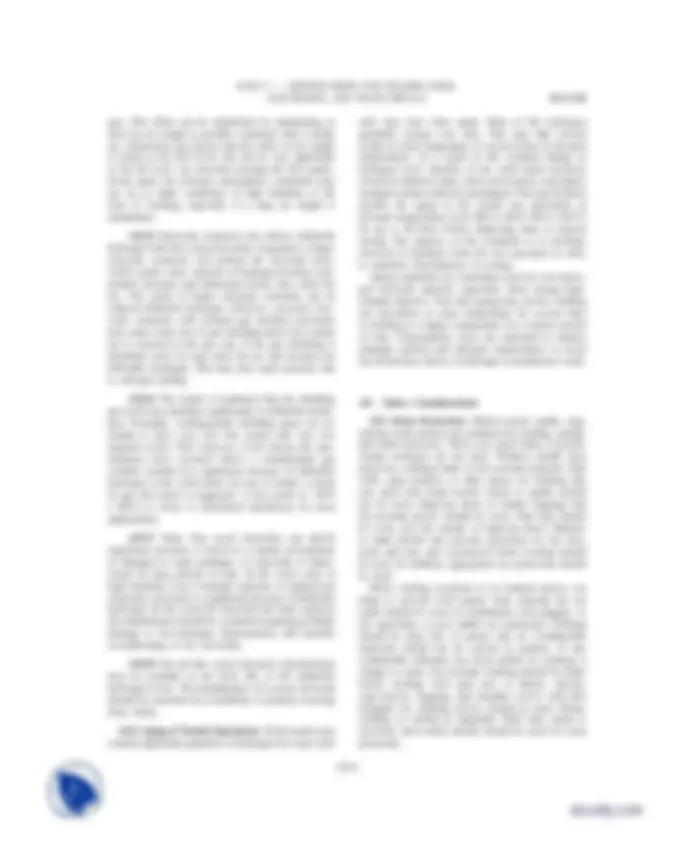
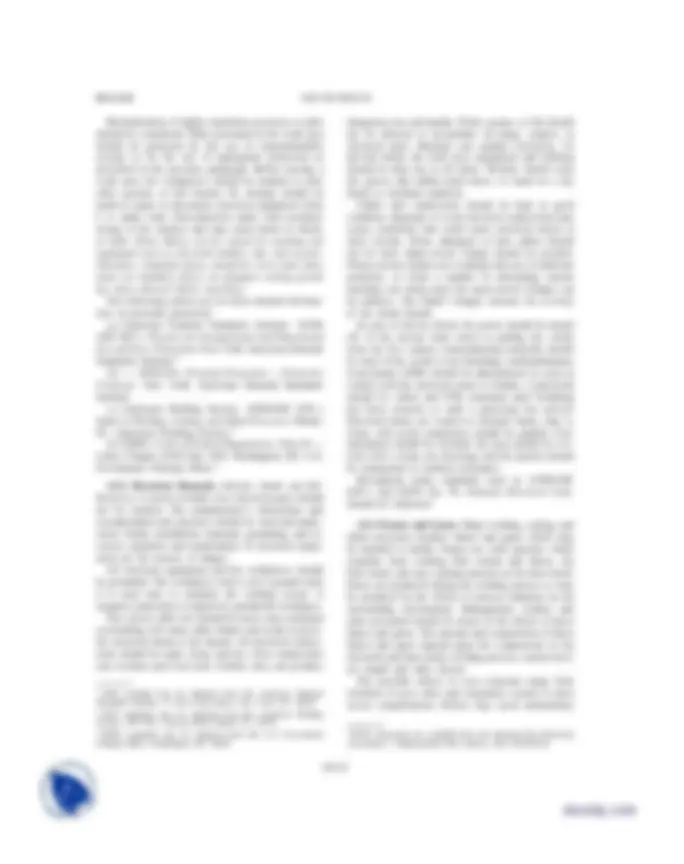
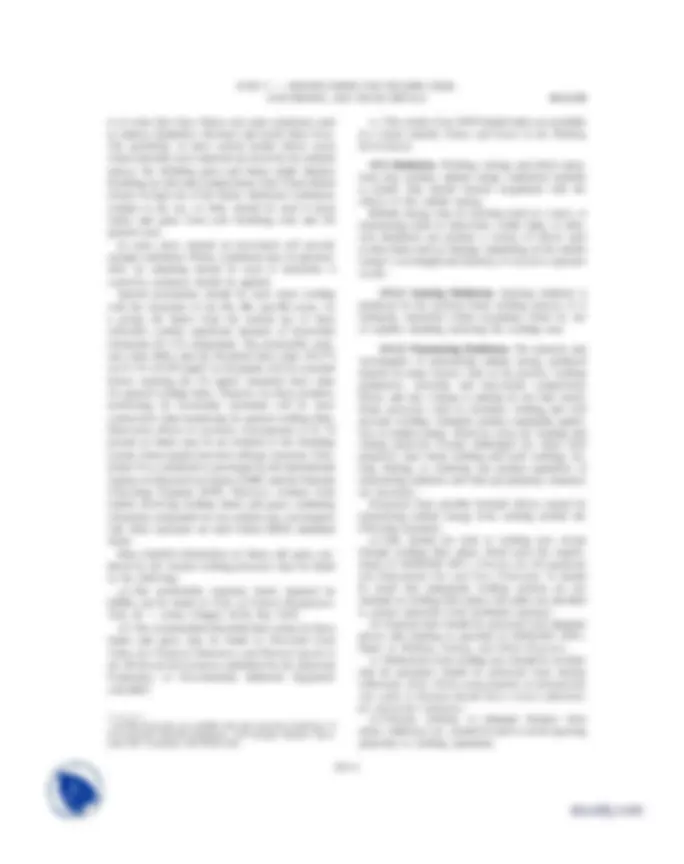
Study with the several resources on Docsity
Earn points by helping other students or get them with a premium plan
Prepare for your exams
Study with the several resources on Docsity
Earn points to download
Earn points by helping other students or get them with a premium plan
Community
Ask the community for help and clear up your study doubts
Discover the best universities in your country according to Docsity users
Free resources
Download our free guides on studying techniques, anxiety management strategies, and thesis advice from Docsity tutors
Dr. Ajitabh Sai delivered this lecture at Baba Farid University of Health Sciences for Mechanical and Materials Engineering Specifications course. It includes: Special, Tests, Diffusible, Hydrogen, Shielding, Gas, Safety, COnsiderations, Burn, Protection
Typology: Exercises
1 / 6
This page cannot be seen from the preview
Don't miss anything!
PART C — SPECIFICATIONS FOR WELDING RODS, ELECTRODES, AND FILLER METALS SFA-5.
(l) EXXTX-B8 — ASTM A 335-P9 pipe For two of these Cr-Mo electrode classifications, low-carbon EXXTX-BXL classifications have been es- tablished. While regular Cr-Mo electrodes produce weld metal with 0.05 percent to 0.12 percent carbon, the ‘‘L-Grades’’ are limited to a maximum of 0.05 percent carbon. While the lower percent carbon in the weld metal will improve ductility and lower hardness; it will also reduce the high-temperature strength and creep resistance of the weld metal. Several of these grades also have had high-carbon grades (EXXTX-BXH) established. In these cases, the electrode produces weld metal with 0.10 percent to 0.15 percent carbon which may be required for high- temperature strength in some applications. Since all Cr-Mo electrodes produce weld metal which will harden in still air, both preheat and postweld heat treatment (PWHT) are required for most applications. No minimum notch toughness requirements have been established for any of the Cr-Mo electrode classifi- cations. While it is possible to obtain Cr-Mo electrodes with minimum toughness values at ambient temperatures down to 32°F (0°C), specific values and testing must be agreed to by the supplier and the purchaser.
A7.9.3 EXXTX-DX (Mn-Mo Steel) Electrodes. These electrodes produce weld metal which contains about 1- 1 ⁄ 2 percent to 2 percent manganese and between (^1) ⁄ 3 percent and^
3 percent molybdenum. This weld metal provides higher strength and better notch toughness than the C 1 ⁄ 2 percent Mo and 1 percent Ni- 1 ⁄ 2 percent Mo steel weld metal discussed in A7.9.1 and A7.9.4. How- ever, the weld metal from these Mn-Mo steel electrodes is quite air-hardenable and usually requires preheat and PWHT. The individual electrodes classified under this electrode group have been designed to match the me- chanical properties and corrosion resistance of the high- strength, low-alloy pressure vessel steels, such as ASTM A 302 Gr. B and HSLA steels and manganese molybde- num castings such as ASTM A 49, A 291 and A 735.
A7.9.4 EXXTX-K(X) (Various Low-Alloy Steel Type) Electrodes. This group of electrodes produces weld metal of several different chemical compositions. These electrodes are primarily intended for as-welded applications. See Table 2 for a comparison of the toughness levels obtained for each classification.
A7.9.4.1 EXXTX-K1 Electrodes. Electrodes of this classification produce weld metal with nominally 1 percent nickel and 1 ⁄ 2 percent molybdenum. These electrodes can be used for long-term stress-relived applications or for welding low-alloy, high-strength steels, in particular 1 percent nickel.
A7.9.4.2 EXXTX-K2 Electrodes. Electrodes in this classification produce weld metal which will have a chemical composition of 1- 1 ⁄ 2 percent nickel and up to 0.35 percent molybdenum. These electrodes are used on many high-strength applications ranging from 80 to 110 ksi (550 to 760 MPa) minimum yield strength. Typical applications would include the welding of submarines, aircraft carriers, and many structural appli- cations where excellent low-temperature toughness is required. Steels welded would include HY-80, HY-100, ASTM A 710, A 514, and other similar high-strength steels.
A7.9.4.3 EXXTX-K3 Electrodes. Electrodes of this type produce weld deposits with higher levels of Mn, Ni, and Mo than the EXXTX-K2 types. They are usually higher strength than the -K1 and -K2 types. Typical applications include the welding of HY- and A 514 steels.
A7.9.4.4 EXXTX-K4 Electrodes. Electrodes of this classification deposit weld metal similar to that of the -K3 electrodes, with the addition of approximately 0.5 percent chromium. The additional alloy provides the higher strength needed for many applications needing in excess of 120 000 psi (830 MPa) tensile, such as armor plate.
A7.9.4.5 EXXTX-K5 Electrodes. Electrodes of this classification produce weld metal which is designed to match the mechanical properties of steels such as SAE 4130 and 8630 after the weldment is quenched and tempered. The classification requirements stipulate only as welded mechanical properties; therefore, the end user is encouraged to perform qualification testing.
A7.9.4.6 EXXTX-K6 Electrodes. Electrodes of this classification produce weld metal which utilizes less than 1 percent nickel to achieve excellent toughness in the 60 000 and 70 000 psi (410–480 MPa) tensile- strength ranges. Applications include structural, offshore construction, and circumferential pipe welding.
A7.9.4.7 EXXTX-K7 Electrodes. This electrode classification produces weld metal which has similarities to that produced with EXXTX-Ni2 and EXXTX-Ni electrodes. This weld metal has approximately 1- 1 ⁄ 2 percent manganese and 2- 1 ⁄ 2 percent nickel.
A7.9.4.8 EXXTX-K8 Electrodes. This classifi- cation was designed for electrodes intended for use in circumferential girth welding of line pipe. The weld deposit contains approximately 1- 1 ⁄ 2 percent manganese, 1.0 percent nickel, and small amounts of other alloys.
SFA-5.29 1998 SECTION II
It is especially intended for use on API 5LX80 pipe steels.
A7.9.4.9 EXXT1-K9 Electrodes. This electrode produces weld metal similar to that of the -K2 and -K3 type electrodes, but is intended to be similar to the military requirements of MIL-101TM and 101TC electrodes in MIL-E-24403/2C. The electrode is de- signed for welding HY-80 steel.
A7.9.5 EXXTX-NiX (Ni-Steel) Electrodes. These electrodes have been designed to produce weld metal with increased strength without being air-hardenable or with increased notch toughness at temperatures as low as −100°F (−73°C). They have been specified with nickel contents which fall into three nominal levels of 1 percent Ni, 2- 1 ⁄ 4 percent Ni, and 3- 1 ⁄ 4 percent Ni in steel. With carbon levels of up to 0.12%, strength increases and permits some of these Ni-steel electrodes to be classified as E8XTX-NiX and E9XTX-NiX. However, some classifications may produce low-temperature notch toughness to match the base-metal properties of nickel steels, such as ASTM A 203 Gr. A, ASTM A 352 Grade LC1 and LC2. The manufacturer should be consulted for specific Charpy V-notch impact properties. Typical base metals would also include ASTM A 302, A 572, A 575, and A 734. Many low-alloy steels require postweld heat treatment to stress relieve the weld or temper the weld metal and heat-affected zone (HAZ) to achieve increased ductility. It is often acceptable to exceed the PWHT holding temperatures shown in Table 8. However, for many applications, nickel-steel weld metal can be used without (PWHT). If PWHT is to be specified for a nickel-steel weldment, the holding temperature should not exceed the maximum temperature given in Table 8 for the classification considered, since nickel steels can be embrittled at higher temperatures. Electrodes of the EXXTX-Ni(X) type are often used in structural applications where excellent toughness (Charpy V-notch or CTOD) is required.
A7.9.6 EXXTX-WX (Weathering Steel) Elec- trodes. These electrodes have been designed to produce weld metal that matches the corrosion resistance and the coloring of the ASTM weathering-type structural steels. These special properties are achieved by the addition of about 1 ⁄ 2 percent copper to the weld metal. To meet strength, ductility, and notch toughness in the weld metal, some chromium and nickel additions are also made. These electrodes are used to weld typical weathering steel, such as ASTM A 242 and A 588.
A7.9.7 EXXTX-G (General Low-Alloy Steel) Electrodes. These electrodes are described in A2.4. These electrode classifications may be either modifica- tions of other discrete classifications or totally new classifications. The purchaser and user should determine the description and intended use of the electrode from the supplier.
A8. Special Tests A8.1 It is recognized that supplementary tests may need to be conducted to determine the suitability of these welding electrodes for applications involving properties such as hardness, corrosion resistance, mechanical prop- erties at higher or lower service temperatures, wear resistance, and suitability for welding combinations of dissimilar metals. Supplemental requirements as agreed between purchaser and supplier may be added to the purchase order following the guidance of ANSI/AWS A5.01.
A8.2 Diffusible Hydrogen Test A8.2.1 Hydrogen-induced cracking of weld metal or the HAZ generally is not a problem with carbon steels containing 0.3 percent or less carbon, nor with lower-strength alloy steels. However, the electrodes classified in this specification are used to join higher- carbon steels or low-alloy, high-strength steels where hydrogen-induced cracking may be a serious problem.
A8.2.2 Most flux cored electrodes deposit weld metal having diffusible hydrogen levels of less than 16 mL/100 grams of deposited metal. For that reason, flux cored electrodes are generally considered to be low hydrogen. However, some commercially available products will, under certain conditions, produce weld metal with diffusible hydrogen levels in excess of 16 mL/100 grams of deposited metal. Therefore, it may be appropriate for certain applications to utilize the optional supplemental designators for diffusible hydro- gen when specifying the flux cored electrode to be used.
A8.2.3 The user of this information is cautioned that actual fabrication conditions may result in different diffusible hydrogen values than those indicated by the designator.
A8.2.4 The use of a reference atmospheric condi- tion during welding is necessitated because the arc is subject to atmospheric contamination when using either self-shielded or gas shielded flux cored electrodes. Moisture from the air, distinct from that in the electrode, can enter the arc and subsequently the weld pool, contributing to the resulting observed diffusible hydro-
SFA-5.29 1998 SECTION II
Mechanization of highly hazardous processes or jobs should be considered. Other personnel in the work area should be protected by the use of noncombustible screens or by the use of appropriate protection as described in the previous paragraph. Before leaving a work area, hot workpieces should be marked to alert other persons of this hazard. No attempt should be made to repair or disconnect electrical equipment when it is under load. Disconnection under load produces arcing of the contacts and may cause burns or shock, or both. (Note: Burns can be caused by touching hot equipment such as electrode holders, tips, and nozzles. Therefore, insulated gloves should be worn when these items are handled, unless an adequate cooling period has been allowed before touching.) The following sources are for more detailed informa- tion on personal protection: (a) American National Standards Institute. ANSI/ ASC Z87.1, Practice for Occupational and Educational Eye and Face Protection. New York: American National Standards Institute. 5 (b) —. ANSI Z41, Personal Protection — Protective Footwear. New York: American National Standards Institute. (c) American Welding Society. ANSI/ASC Z49.1, Safety in Welding, Cutting, and Allied Processes. Miami, FL: American Welding Society. 6 (d) OSHA. Code of Federal Regulations , Title 29 — Labor, Chapter XVII, Part 1910. Washington, DC: U.S. Government Printing Office. 7
A9.2 Electrical Hazards. Electric shock can kill. However, it can be avoided. Live electrical parts should not be touched. The manufacturer’s instructions and recommended safe practices should be read and under- stood. Faulty installation, improper grounding, and in- correct operation and maintenance of electrical equip- ment are all sources of danger. All electrical equipment and the workpieces should be grounded. The workpiece lead is not a ground lead; it is used only to complete the welding circuit. A separate connection is required to ground the workpiece. The correct cable size should be used, since sustained overloading will cause cable failure and result in possi- ble electrical shock or fire hazard. All electrical connec- tions should be tight, clean, and dry. Poor connections can overheat and even melt. Further, they can produce
(^5) ANSI standard may be obtained from the American National Standards Institute, 11 West 42nd Street, New York, NY 10036. (^6) AWS standards may be obtained from the American Welding Society, 550 N.W. LeJeune Road, Miami, FL 33126. (^7) OSHA standards may be obtained from the U.S. Government Printing Office, Washington, DC 20402.
dangerous arcs and sparks. Water, grease, or dirt should not be allowed to accumulate on plugs, sockets, or electrical units. Moisture can conduct electricity. To prevent shock, the work area, equipment, and clothing should be kept dry at all times. Welders should wear dry gloves and rubber-soled shoes, or stand on a dry board or insulated platform. Cables and connections should be kept in good condition. Improper or worn electrical connections may create conditions that could cause electrical shock or short circuits. Worn, damaged, or bare cables should not be used. Open-circuit voltage should be avoided. When several welders are working with arcs of different polarities, or when a number of alternating current machines are being used, the open-circuit voltages can be additive. The added voltages increase the severity of the shock hazard. In case of electric shock, the power should be turned off. If the rescuer must resort to pulling the victim from the live contact, nonconducting materials should be used. If the victim is not breathing, cardiopulmonary resuscitation (CPR) should be administered as soon as contact with the electrical source is broken. A physician should be called and CPR continued until breathing has been restored, or until a physician has arrived. Electrical burns are treated as thermal burns; that is, clean, cold (iced) compresses should be applied. Con- tamination should be avoided; the area should be cov- ered with a clean, dry dressing; and the patient should be transported to medical assistance. Recognized safety standards such as ANSI/ASC Z49.1, and NFPA No. 70, National Electrical Code, should be followed. 8
A9.3 Fumes and Gases. Many welding, cutting, and allied processes produce fumes and gases which may be harmful to health. Fumes are solid particles which originate from welding filler metals and fluxes, the base metal, and any coatings present on the base metal. Gases are produced during the welding process or may be produced by the effects of process radiation on the surrounding environment. Management, welders and other personnel should be aware of the effects of these fumes and gases. The amount and composition of these fumes and gases depend upon the composition of the electrode and base metal, welding process, current level, arc length and other factors. The possible effects of over exposure range from irritation of eyes, skin, and respiratory system to more severe complications. Effects may occur immediately
(^8) NFPA documents are available from the National Fire Protection Association, 1 Batterymarch Park, Quincy, MA 02269-9101.
PART C — SPECIFICATIONS FOR WELDING RODS, ELECTRODES, AND FILLER METALS SFA-5.
or at some later time. Fumes can cause symptoms such as nausea, headaches, dizziness and metal fume fever. The possibility of more serious health effects exists when especially toxic materials are involved. In confined spaces, the shielding gases and fumes might displace breathing air and cause asphyxiation. One’s head should always be kept out of the fumes. Sufficient ventilation, exhaust at the arc, or both, should be used to keep fumes and gases from your breathing zone and the general area. In some cases, natural air movement will provide enough ventilation. Where ventilation may be question- able, air sampling should be used to determine if corrective measures should be applied. Special precautions should be used when welding with the electrodes of the B3, B6, and B8 series. As a group, the fumes from the normal use of these electrodes contain significant amounts of hexavelant chromium (Cr VI) compounds. The permissible expo- sure limit (PEL) and the threshold limit value (TLV ®) for Cr VI of 0.05 mg/m 3 as chromium will be exceeded before reaching the 5.0 mg/m 3 threshold limit value for general welding fume. Therefor, for these products, monitoring for hexavelant chromium will be more conservative than monitoring for general welding fume. Short-term effects of excessive overexposure to Cr VI present in fumes may be an irritation to the breathing system. Some people may have allergic reactions. Chro- mium VI is considered a carcinogen by the International Agency for Research on Cancer (IARC) and the National Toxicology Program (NTP). However, evidence from studies involving welding fumes and gases containing chromium compounds do not confirm any carcinogenic risk when exposures are held within OSHA mandated limits. More detailed information on fumes and gases pro- duced by the various welding processes may be found in the following: (a) The permissible exposure limits required by OSHA can be found in Code of Federal Regulations , Title 29 — Labor, Chapter XVII, Part 1910. (b) The recommended threshold limit values for these fumes and gases may be found in Threshold Limit Values for Chemical Substances and Physical Agents in the Workroom Environment , published by the American Conference of Governmental Industrial Hygienists (ACGIH) 9.
(^9) ACGIH documents are available from the American Conference of Governmental Industrial Hygienists, 1330 Kemper Meadow Drive, Suite 600, Cincinnati, OH 45240-
(c) The results of an AWS-funded study are available in a report entitled, Fumes and Gases in the Welding Environment.
A9.4 Radiation. Welding, cutting, and allied opera- tions may produce radiant energy (radiation) harmful to health. One should become acquainted with the effects of this radiant energy. Radiant energy may be ionizing (such as x-rays), or nonionizing (such as ultraviolet, visible light, or infra- red). Radiation can produce a variety of effects such as skin burns and eye damage, depending on the radiant energy’s wavelength and intensity, if excessive exposure occurs.
A9.4.1 Ionizing Radiation. Ionizing radiation is produced by the electron beam welding process. It is ordinarily controlled within acceptance limits by use of suitable shielding enclosing the welding area.
A9.4.2 Nonionizing Radiation. The intensity and wavelengths of nonionizing radiant energy produced depend on many factors, such as the process, welding parameters, electrode and base-metal composition, fluxes, and any coating or plating on the base metal. Some processes, such as resistance welding and cold pressure welding, ordinarily produce negligible quanti- ties of radiant energy. However, most arc welding and cutting processes (except submerged arc when used properly), laser beam welding and torch welding, cut- ting, brazing, or soldering can produce quantities of nonionizing radiation such that precautionary measures are necessary. Protection from possible harmful effects caused by nonionizing radiant energy from welding include the following measures: (a) One should not look at welding arcs except through welding filter plates which meet the require- ments of ANSI/ASC Z87.1, Practice for Occupational and Educational Eye and Face Protection. It should be noted that transparent welding curtains are not intended as welding filter plates, but rather are intended to protect passersby from incidental exposure. (b) Exposed skin should be protected with adequate gloves and clothing as specified in ANSI/ASC Z49.1, Safety in Welding, Cutting, and Allied Processes. (c) Reflections from welding arcs should be avoided, and all personnel should be protected from intense reflections. (Note: Paints using pigments of substantially zinc oxide or titanium dioxide have a lower reflectance for ultraviolet radiation.) (d) Screens, curtains, or adequate distance from aisles, walkways, etc., should be used to avoid exposing passersby to welding operations.